- 1Department of Architecture, Built Environment and Construction Engineering - DABC, Politecnico di Milano, Milan, Italy
- 2Department of Civil, Environmental, Architectural Engineering and Mathematics - DICATAM, Università degli Studi di Brescia, Brescia, Italy
The research aims at analyzing the integration of Waste Management (WM) strategies and Information management in the construction procurement process. The application of Building information modelling (BIM) methodologies for a Most Economically Advantageous Tender could address the digital transition in order to adopt environmentally sustainable practices. Despite the wide regulation regarding waste minimization, an overview of which is provided, AECO is still one of the most polluting industrialized sector. Drivers and barriers to the method, and a literature review are provided: BIM approaches to enable WM practices have been analyzed from the designer and constructor’s point of view, but few studies investigated the role of the Client, in particular the Public Client. The goal of the study was to evaluate the efficiency of Most Economically Advantageous Tender and a BIM methodology to promote WM strategies during the tender phase. Design Build (DB) and Design Bid Build (DBB) procurement models are tested through three case studies of Italian schools' calls for proposals: the BIM model enabled to verify the bids in terms of WM strategies implementation. Blockchain and Smart contract future applications are also investigated in order to ensure transparency of the whole process. The Public Client could trigger a change in the construction sector regarding the integration of WM practices, as a central and active actor of the construction process, through the application of Green Public Procurement and BIM methodologies.
Introduction
Increasing global urbanization has resulted in high levels of waste. The built environment consumes more natural resources than necessary. The World Resource Institute study (Matthews et al. 2000) shows that “one half to three quarters of the annual material input was returned to the environment as waste within 1 year in industrialized countries like Austria, Germany, Japan, The Netherlands and United States.” International organizations, likewise European Union (EU) have realized and are claiming that resources are finite and that nature can no longer absorb the vast quantities of waste produced by humankind. However, the famous Earth Overshoot Day, the date when humanity’s demand for resources in a year exceeds what the Earth can regenerate, passed from October to July 29th (in 2019) in just 30 years. In 2019 waste production was still increasing. In order to contrast the waste phenomenon, European initiatives involving municipalities, companies and citizens’ groups are encouraging its members to commit to the elimination of residual waste, thereby ending landfill and incineration as waste management (Waste Managemen) practices. EU targets of zero waste to landfill.
It is estimated that waste produced on a construction site accounts for up to 30% of the total weight of materials delivered (Fishbein, 1998). Data about waste in constructions and demolitions activities and their environmental and economic impacts cannot be further ignored. Construction WM (CWM) processes must be reengineered to reduce construction waste at source. Rethinking WM in construction requires adopting “cyclic” rather than “linear” approach to design and construction (Osmani, 2011). This requires re-engineering current practice to contribute to a cleaner environment through efficient and cost effective sustainable waste minimization strategies. Waste minimization strategies must be adopted during the whole process of design, construction, operation and demolition of a building.
The present work would initially provide a review of the definition of waste and the European regulation framework, in order to introduce the context for the application of sustainable strategies and green procurement based processes, with a specific focus on AECO (Architecture, Engineering, Construction, and Operations) sector. Existing barriers and drivers to waste minimization practices in the construction sector are then presented, that lead to the integration between sustainable strategies and green procurement, and Building information modelling (BIM) methods, as provided in the literature review section. The method proposed implies the integration of these methods and strategies in order to introduce and encourage a change in the construction sector. In particular, both the method presented and the subsequent case studies are part of the Italian context, with the application of an innovative tender process implementing waste minimization strategies. In order to introduce the Italian context, the adoption of the European regulation in the Italian legislation framework is presented, and the proposed innovative tender processes are investigated. Three Italian case studies of tendering and construction processes at different levels of completion are then introduced and analyzed in order to identify advantages and disadvantages of the method proposed. Some future implementation to improve transparency and traceability, such as the application of Blockchain technology and Smart contracts, are finally provided, followed by conclusions and possible further developments.
Waste Definition
Zero waste strategy could be the only solution for a world in an environmental crisis; however, this is really challenging in AECO industry. In order to reach the goal it will be necessary to involve and commit all stakeholders and develop efficient WM strategies taking the industry closer to a “zero waste” vision (Osmani, 2011). The new common sustainable approach involves a redefinition of the concept and the idea of “waste”; various interpretations and definitions of waste can be found in construction waste related literature. From a waste by-product of a process, the concept of waste has been redefined as a factor adding costs but not value (Koskela, 1992). Similarly, waste can be classified as “unavoidable,” when the costs to reduce it are higher than the producible value, “avoidable,” when the investment needed to manage the waste is higher than the costs to prevent or reduce it (Formoso et al., 1999). Otherwise, Ekanayake and Ofori (2000) defined construction waste as “any material, apart from earth materials, which needs to be transported elsewhere from the construction site or used within the construction site itself for the purpose of land filling, incineration, recycling, reusing or composting, other than the intended specific purpose of the project due to material damage, excess, non-use, or non-compliance with the specifications or being a by-product of the construction process.” Mossman (2009) also defined material waste as anything that is not needed to generate value for the end-user.
It is possible to claim that there is no generally accepted definition of waste. As a result, the European Council revised the Waste Framework Directive in October 2008, which should have been fully implemented within all EU member states by December 2010. The European Waste Framework Directive 2008/98/EC define waste as “any substance or object which the holder discards or intends or is required to discard” (EU). Reuse and recycling of waste are encouraged, whereas the sorting out measures are aimed at simplifying the fragmented legal frame-work that has regulated the waste sector to date.
European Regulation Framework Developments
In order to analyze the context of WM is necessary to provide a review of the major regulations in terms of WM strategies with a specific focus regarding construction and demolition waste. The main regulation framework in the European context is defined by the European Directives, since the common interest in the context of sustainability and the attempt of the UE to achieve common objectives among the Member States.
In the paragraphs below construction and demolition waste main regulations are presented, focusing on the aspects with major effects and interests for AECO sector. The following paragraphs, then, summarizes the specific regulation framework of packaging waste, and, finally, some considerations and the analysis of Eurostat data regarding the evolution of construction and demolition wastes production are provided.
Construction and Demolition Waste Regulation Framework
The regulation framework in the field of WM, and in particular in the context of AECO sector is presented below. The major evolution of the legislation starts from 1975, with the definition of waste and WM activities, up to the definition of specific categories of construction and demolition wastes in the early 2000s, as shown in Table 1.
In 2008 Directive 2008/98/EC stressed the attention on the possible uses and treatments of waste, with the definition of the waste treatment hierarchy. Recycling and recovery targets are also introduced for the construction sector. The attention started to focus on the production phases of products, with an increasing responsibility of the producer on wastes.
Around 2015 a significant step forward can be seen in the approach to the phenomenon, as the focus shifts from waste and how to manage it, to the phases in which wastes are produced and how they could be reduced; in 2014 there was a first introduction of sustainability criteria in procurement legislation. Also, major and important integrations to the Directive 2008/98/EC were introduced in 2018, as shown in Table 2.
In 2014 the procurement legislation, i.e., Directive 2014/24/EU, highlighted the need of minimize waste generation and increase resource efficiency, thus introducing the possibility to include tender clauses related to WM and minimization. In 2015 with COM (2015) 614 final of December 2, 2015 a real turning point emerged as the focus extended to the whole process, from the design phase to product disposal stage. As a result, the interest changed from the only phase in which waste already exists, to the whole process, with the aim of avoiding or reducing waste production through the definition of environmentally sustainable design processes. Regarding the construction sector, this approach turned the attention from the only phase of construction and demolition to the design phase, with major attention to a responsible choice of construction materials.
The European Commission also pointed out that a large amount of materials resulting from the demolition of buildings could be recycled, but as they are not properly identified and separated they cannot be treated and are landfilled. This leads to considerable environmental damage, both because of the amount of waste that could have been recycled and used as secondary raw materials or energetically recovered, and because the mix of demolition waste materials often contain hazardous substances and can be highly polluting to the environment. As a consequence, the aim would be to maximize the homogeneous portions of valuable materials so that they could be properly recycled.
Finally, one of the most important aspects of this document is a new approach to wastes as resources as “secondary raw materials” in the circular economy cycle. The major consequence is the possible profit of construction companies in selling recycled products, such as metals, and, also, ensure savings with the re-use of demolition wastes into the next building cycle.
Later, in 2018, with Directive 2018/851 the attentions is highly stressed on the design phase, and, as regards AECO sector, the following consequences are expected: conscious choice of materials during the design phase, e.g. avoiding waste strategies, recyclable, recycled, durable materials, using raw materials produced in sustainable ways and use of the least possible quantity of hazardous substances; implying local workforce and materials, reducing transport pollution; focus on the quantity of waste produced during the construction phase, due to the preparation process of the products before they are installed and quantity of packaging wastes; possibility of recovering the building at the end of its life and, when no longer possible, focus on the possibility of re-use, recycling or recovery of materials and debris resulting from the demolition of the building. A clearer definition of selective demolition reflects the need to integrate this phase into standard practice, so as to increase the proportion of materials actually recycled at the end of building life cycle. Also, the introduction of electronic records is a main aspect of the regulation since wastes must be properly treated and consequently they must be traceable, avoiding as much as possible illegal transportation of wastes. The definition of backfilling introduced the possibility of replacing the excavated soil in the same location, ensuring landfilling savings for construction companies.
Packaging Waste Regulation Framework
This paragraph shows a brief summary of the main regulation specifically focused on packaging (Table 3), as this represent a large part of construction wastes.
The main objective of the regulation development is the increasing attention to the separation of different types of packaging ensuring to recycle the most part of them. In addition, the increasingly detailed sorting of materials, e.g. the distinction between “ferrous metals” and “aluminum”, ensures high quality recycling, increasing the profit from selling them as secondary raw materials. Therefore, one of the final aims is, once again, to increase the willingness of companies to sort and recycle waste, turning it from a burden to a profit.
Waste Statistics in European Union
EUROSTAT study is presented in order to provide an overview of waste production divided by EU countries and industrial sectors (Figure 1). In 2016, the total waste generated in the EU-28 by all economic activities and households amounted to 2,538 million tons.
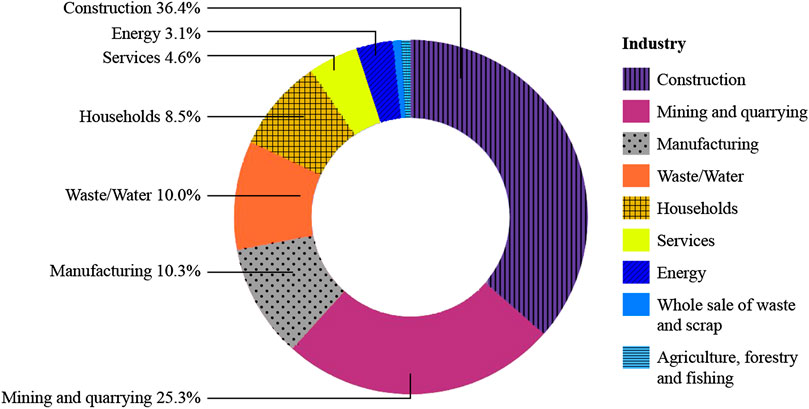
FIGURE 1. Waste generation by economic activities and households, EU-28, 2016. Data source: Eurostat (env_wasgen).
In the EU-28, construction contributed 36.4% of the total in 2016 and was followed by mining and quarrying (25.3%), manufacturing (10.3%), waste and water services (10.0%), and households (8.5%). The data collected underline that AECO sector is responsible of 924 million tons of waste out of the total of 2,539 million tons.
Figure 2 shows the data for Construction, Mining and quarrying, and Manufacturing sectors in the period 2004–2016 for EU-28 countries. The three sectors produce 72% of total waste in EU (Figure 1). Figure 2 excludes major mineral wastes that are more easily reused and recycled, and shows how Mining and quarrying and Manufacturing sectors have reported a decreasing trend in waste generation equal to −31.4 and −29.6% respectively since the introduction of Directive 2008/98/EC. On the contrary, AECO sector shows an increasing trend in waste production in the period 2004–2016 equal to +3.9%.
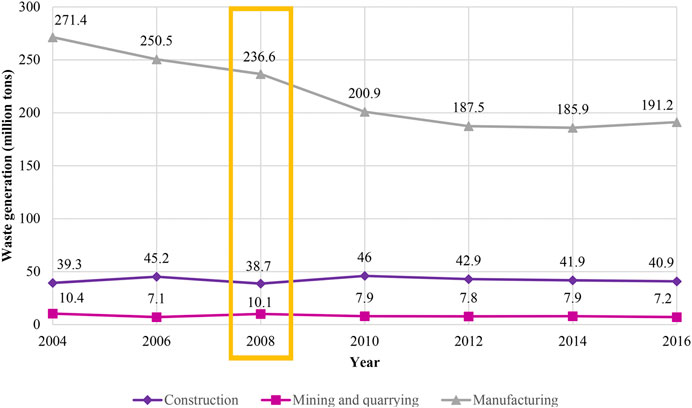
FIGURE 2. Waste generation graph and current trends for waste production in industrialized sectors, excluding major mineral wastes, EU-28, 2004–2016 (million tons). Data source: Eurostat (env_wasgen).
Given the annual amount of waste produced by AECO sector more effort seems to be needed. In order to analyze the possible factors that prevent proper WM in the Construction sector, barriers and possible drivers for waste minimization are presented in the following section.
Construction Waste Minimization Drivers and Barriers
Socio-Economical Barriers
As stated, despite the adoption of several WM strategies, and the introduction of various legislative measures reducing waste generated by AECO industry remains challenging. In fact, increasing waste intensiveness of the industry is not only as a result of ineffectiveness of the existing WM strategies; waste intensiveness of the industry is enhanced by certain cultural and socio-economical values that support construction waste generation (Teo and Loosemore, 2001). In their study Ajayi et al. (2016) examine cultural profile of United Kingdom AECO sector in order to understand cultural factors contributing to waste intensiveness. Five waste inducing cultural factors have been identified:
• “Make-do understanding” that usually result in “make-do waste”:
most error and rework at construction stage is usually due to incomplete design document or contractors’ poor knowledge of the design and its documentation (Dainty et al., 2007). The process which generates this kind of waste is called make-do waste (Koskela, 2004). The whole process and provisions that allows construction activities with incomplete documentation is termed make-do understanding (Ajayi et al., 2016). Documents and design specifications uncompleted or with unresolved design issues are cause of reworks and subsequent waste generation increasing the risks of cost and time projects overrun.
• Non-collaborative culture, which results in reworks and wasteful activities:
inadequate collaboration between designers, procurement team and contractors is a key feature that compromises profitability and effectiveness of AECO industry (Deborah et al., 2012). It has been proved that the major causes of construction waste are ineffective communication and coordination, inconsistent procurement documentation, unclear allocation of responsibilities (Osmani, 2012), document delay, and non-involvement of contractors in design decisions (Arain et al., 2004).
• Blame culture, which encourages shifting of waste preventive responsibilities between designers and contractors:
AECO industry is known for its inadequate interdisciplinary communication. Specialists deal with their own discipline and are not interested and prepared to take responsibility for choices that affect other disciplines or which have impacts during a different phase of the construction process. The whole design and construction process is interested in passing blame to another party (Fewings and Henjewele, 2019). This shifting of blame is one of the major cause contributing to waste production and inefficiencies in terms of WM strategies; contractors believe that designers contribute to waste generation and designers posit that their activities have nothing to do with waste (Osmani et al., 2008).
• Culture of waste behavior, which encourages belief in waste inevitability:
waste inevitability is evident in the concept of waste allowance, which is the potential proportion of waste that is added to the required quantity of materials. The allowance is usually in the range of 2.5–10% of the quantity of materials (Buchan et al., 1991). It is a belief that a certain proportion of waste is inevitable in construction. As a result, optimization strategies to reduce the amount of scrap materials are not applied in the design phase. Off-site construction processes and the use of products with a wide dimensional range, that would help overcoming the waste issue, have not been implemented as standard practice yet.
In addition, this is a common approach since in the standard practice the owners and the construction company have already paid for packaging, construction and demolition wastes, and landfilling, so they are not encouraged to recycle, and selective demolition and waste separation are seen as a burden. In order to change this way of thinking and acting, the European regulation introduced the concept of waste as a resource and possible source of income with the COM (2015) 614 final of December 2, 2015 and related European packaging regulation. This enables to change owners and construction companies’ view of wastes as a resources and ensuring that sustainable practices become part of the standard practice.
• Conservatism, which hinders diffusion of innovation across the industry:
the project-based nature of AECO industry and its temporary relationship among parties makes it difficult to get innovation across to the industry. Although, it is usually claimed that little innovation occurs within the construction industry (Blayse and Manley, 2004), it is clear that innovation occurs within projects but there are problems with institutional learning required to capture them for future projects (Tatum, 1989, Fairclough, 2002). The temporary work relationship among parties hinders further exploration or repetition of innovative approach in other projects (Fairclough, 2002).
A similar study conducted by Osmani (2011) has identified and highlighted the vision of designers and construction companies on the main barriers to the introduction of WM in the UK construction sector. Some considerations are made by the author (Osmani, 2011):
• Architects consider “lack of interest from clients” as the major constraint, followed by “waste accepted as inevitable” shared by contractors’ vision; it underlines the pervasive culture of waste behavior, which encourages belief in waste inevitability.
• “Poor defined individual responsibilities” underlines the non-collaborative culture of AECO sector.
• Contractors see in “waste accepted as inevitable” the major barrier to waste minimization, followed by “lack of training” highlighting the need of more efficient tools and method of WM.
The public Client introducing incentives that promote the adoption of waste minimization methods could trigger a change in AECO industry. As a result, companies would be encouraged to implement sustainable strategies to maintain competitiveness.
Architecture, Engineering, Construction, and Operations Waste Minimization Drivers
Considerable efforts have been made over the last years to understand the factors driving the sustainability of AECO sector in terms of WM. Government legislation is one of the most critical success factors for ensuring the sustainability of the sector (Osmani et al., 2008). A study conducted on the critical success factors for WM in construction projects highlights that WM legislation; WM system, low-waste building technologies, fewer design changes and research and development in WM process are the most critical in ensuring waste is sustainably managed (Adjei et al., 2018). The key drivers for waste reduction strategy in AECO industry could be categorized into three main groups which are:
• Legislative drivers;
• Business drivers;
• Managerial and technological drivers.
Legislative Drivers: Green Procurement
Previous paragraph Socio-Economical Barriers identified the socio-economic barriers of AECO sector, ranging from the culture of waste to the idea of its inevitability, and the sector’s reluctance to integrate sustainable strategies into common practice. In order to trigger a change in the current way of thinking, the Client can encourage its implementation during the tendering phase through clauses in the tender contract. As regards the public construction sector, it is possible to introduce contract clauses in the tendering phase requiring the implementation of sustainable design and construction strategies and waste minimization. Therefore, the public sector can lead the construction market towards environmentally sustainable practices. This aspect has been introduced by the procurement legislation with the European Directive 2014/24/EU, stating that public purchasers must allow public procurement to be opened up to competition as well as the achievement of sustainability objectives. As a matter of fact, by using their purchasing power to opt for environmentally friendly goods, services and works, public Clients can significantly contribute to sustainable consumption and production, which is the idea behind the concept of Green Public Procurement (GPP). Furthermore, the European Commission, through the COM (2015) 614 final of December 2, 2015, attempted to change the concept of waste, from items to be disposed of, to resources in the broader context of circular economy. This paradigm shift aimed to highlight the potential income from proper separation of construction and demolition wastes, in particular by identifying materials for high quality recycling, such as aluminum. As a result, wastes could become secondary raw materials for the construction sector or other sectors and, at the same time, not resulting in costs, such as landfill costs, but in an economic benefit, as well as for the environment.
Business Drivers: Sector Performance
In the previous paragraph the legislative pressure on the implementation of sustainable practices has been presented, and public Clients are placing ever increasing attention on environmentally sustainable practices to be implemented in their tender and construction processes. In addition, both private and public clients are increasingly demanding for enhanced sustainable project performances and are exerting more influence on the industry to reduce onsite waste and cut costs. As a consequence, a direct effect on construction companies is the need to adopt sustainable practices, including waste minimization, in order to improve their performances and remain competitive. Thus, in response to such pressures, businesses are abandoning their narrow theory of value in favor of a broader approach, which not only seeks increased economic value but also considers corporate social responsibilities and stakeholders’ engagement and commitment (Osmani, 2011).
Managerial and Technological Drivers: Information Modelling and Management
Waste minimization practices have for years focused on physical minimization of construction waste and identification of site waste streams. Tools, models and techniques have been developed to manage waste on site. Although these tools facilitate auditing, assessment and benchmarking, their approach to the assessment of waste sources is limited and fragmented, as it fails to effectively address the causal issues of waste generation at all stages of a construction project. As stated in paragraph Socio-Economical Barriers a barrier pointed out by contractors is the lack of training and methods to handle the waste stream during the whole construction process. In addition, in EU regulation the attentions in WM is highly stressed on the design phase; the main objective of the standard is to implement waste minimization strategies in the early design phases in accordance with the waste hierarchy pyramid.
The waste hierarchy pyramid (Figure 3) is divided into different level of WM strategy (EPA, US Environmental Protection Agency):
• Avoidance: the highest priority strategy to adopt in the design phase in order to reduce the amount of waste generated, in a construction project waste generation must be avoided or reduced during the preliminary phases of planning and design.
• Reducing source use, reuse, recovery: reuse, recycling, reprocessing and energy recovery strategies must be the second priority in the design phase. Designers should consider the use of construction technologies with a high level of reusability such as prefabricated and off-site products and the use of materials with a high percentage of recycled materials.
• Disposal: waste hierarchy recognizes that some types of waste, such as hazardous chemicals or asbestos, cannot be safely recycled and direct treatment or disposal is the most appropriate management option.
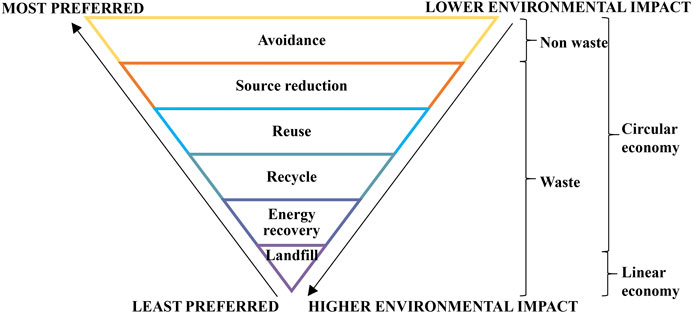
FIGURE 3. Sustainable Materials Management: Non-Hazardous Materials and Waste Management Hierarchy. Information source: EPA, US Environmental Protection Agency.
Regarding previous statements the current challenge is to provide methods, tools and techniques to identify and solve the root causes and origins of construction waste (Osmani, 2011). The basis for such an approach could be BIM and related technologies.
In addition, BIM methodology could overcome the barriers stated in paragraph Socio-Economical Barriers (Ajayi et al., 2016) by:
• Reducing design errors and lack of information resulting from incomplete and incoherent documentation;
• Improving collaboration among actors and anticipating the involvement of key stakeholders in the process;
• Enabling the shift from a traditional procurement route to a more collaborative system;
• Overcoming the waste inevitability culture since the possibility of computing actual quantities of wastes in a rapid and efficient way.
In order to investigate the state of art of Information Modelling and Management method in AECO sector a concise literature review about applications and case studies of combined Information Modelling and WM is provided.
Literature Review
Information Modelling and Waste Management
As introduced, BIM could help to minimize the amount of Construction and Demolition (C&D) waste. Therefore, several previous studies have proposed BIM-based systems to handle C&D waste (Cheng and Ma, 2013; Hamidi et al., 2014) and have introduced potential use of BIM to minimize waste in AECO sector (Liu et al., 2011; Ahankoob et al., 2012; Porwal and Hewage, 2012; Rajendran and Pathrose, 2012). In the following paragraphs, several applications and methodologies of information modeling for WM are presented.
BIM-Based Planning and Estimating System of Construction and Demolition Waste
Several studies have stressed that the lack of benchmarking is an obstacle to the implementation of sustainable practices in AECO industry and that decision making should be based on the most accurate data, information and estimations possible (Yuan and Shen, 2011). Therefore, the quantification of C&D waste is essential for effective WM. The results of the estimations can provide key data to assess the real waste dimension and support decision making for minimization and sustainable WM (Jalali, 2007). The authors Cheng and Ma (2013) propose a BIM-based system for estimating and planning Demolition and Reconstruction waste. Existing tools and methods are not convenient for contractors, too much time and effort are needed since information such as material volume needs to be either measured or retrieved from available documents manually. The BIM-based approach proposed by the authors aims to fill this gap. Authors claim that their system “could extract and process the component information of each building element in a digital virtual BIM model for waste estimation,” providing an automated, fast and accurate waste estimation trough a BIM-model.
A similar and subsequent study proposed by Cheng et al. (2015) investigates how BIM can be implemented to minimize and manage C&D waste on a construction site. Typical BIM uses that can be implemented in planning, design, and construction phases have been identified by the authors through literature review. The study also investigates BIM-based approaches to manage C&D waste in design, construction, and demolition phases, linking BIM uses with hierarchy of WM strategy. The study highlights the potential of information modelling to support integrated building design and construction processes to eliminate the main causes of C&D waste generation and manage waste production. Specifically, the study explores the possibility to reduce and manage waste during the design phase performing design reviews, clash detection, quantity take-off, phase planning, site utilization, and digital prefabrication trough a BIM approach. Considering that C&D waste can be reused and easily recycled if divided into homogeneous fractions, information modelling could help designers and contractors to maximize mono-material fractions minimizing heterogeneous waste. Moreover, authors conclude that the minimized and disposed wastes could be monitored by BIM-based WM planning and execution system (Cheng et al., 2015).
BIM and Design for Deconstruction
The study conducted by Akinade et al. (2015) aims to develop a BIM-based Deconstructability Assessment Score (BIM-DAS) to predict if and how difficult a building can be deconstructed from the early design phase. Critical design principles influencing effectual building deconstruction and key features for assessing the performance of Design for Deconstruction (DfD) have been found to develop BIM-DAS using mathematical modelling approach based on efficient material requirement planning (Akinade et al., 2015). Deconstruction is defined as the whole or partial disassembly of buildings to facilitate component reuse and recycling (Kibert, 2016), DfD could lead the sector to reach the long-term aim of attaining a zero-waste economy (Addis and Jenkins, 2008). Despite the disagreement on the possibility of completely avoiding construction, demolition and excavation waste (Yuan and Shen, 2011; Zaman and Lehmann, 2013), studies show that the application of DfD could lead AECO industry towards a zero waste strategy (Guy et al., 2002; Tingley and Davison, 2012; Akbarnezhad et al., 2014). The study highlights the role and potential of BIM systems for assessing the deconstruction of buildings during the design phase (Akinade et al., 2015). Authors also claim that the results help to understand how BIM functionalities could be employed to improve the effectiveness of existing Construction, Demolition and Excavation Waste management tools and BIM software.
Computational BIM for Construction and Demolition Waste Management
As said, BIM systems could be used to support designers to compare different design options, or contractors to evaluate different construction schemes, both with the objective to avoid or minimize construction waste. The management of a construction project involves the use of available data, information and knowledge to make a series of highly interdisciplinary decisions (Flanagan and Lu, 2008). Considering that the main objective of Information modelling and management is to support decision making by ensuring accurate and available information (Chen et al., 2015), BIM can provide this decision support information for Construction WM (CWM). However, Lu et al. (2017) conducted a study that demonstrates how the digital representation of a building itself cannot manipulate information to enable informed decision making for CWM; BIM systems and models must be based on algorithms tailored for this purpose; in order to achieve an efficient use of BIM for CWM authors identify two necessary pre-requisites (Lu et al., 2017):
• Information readiness;
• Computational algorithms.
Lu et al. (2017) aim to demonstrate the importance of organizing data, information and knowledge in a structured form to efficiently apply Information modeling to C&D management. The study explores computational algorithms that can process data and product information and knowledge to assist decision-making process for CWM. In addition, the authors propose a framework for computational BIM by linking it to prevalent procurement models, e.g., Design Bid Build (DBB) and Design Build (DB) (Lu et al., 2017).
The literature review highlighted the wide use of BIM methodologies to handle the waste related data and information and to manage a waste minimization process. Also, the case studies presented in the literature showed positive results from the application of such methods during the design and construction phase. However, the studies mainly focused on the promising use of BIM approaches for process optimization from the designer and constructor’s point of view. The application of BIM methodology in the preliminary stages of the design and construction process could be more efficient, as the strategies are anticipated at a preliminary stage (Di Giuda et al., 2020a). Therefore, the case studies presented in this work, and described in the next section, focus on the implementation of BIM methodologies for Green procurement. The aim is to anticipate sustainable WM strategies during the design and procurement phases and, at the same time, manage the information flow throughout the whole process.
Methodology: Digitalization for Waste Management and Green Procurement
The main drivers defined in the previous section, legislative and information technology’s once, can direct the contractors’ bid towards a more sustainable WM process. Green procurement and BIM methodology seem to be the key factors to implement sustainable practices in the Construction industry. In this section, the authors present the method developed for the evaluation and comparison of bids submitted in tender phase for public school projects in the Italian context from 2015 to date. A focus is kept on aspects concerning environmental impact and WM. A first part is dedicated to the Italian regulatory framework. Then, the method of evaluation of the bids in tender phase is presented, with specific criteria following the best practices and indications of the EU. Also, the use of BIM methodology for the information management process, promotes the collaboration among stakeholders.
The Italian Regulation Framework
Within the Italian regulatory framework concerning the environment protection and sustainability, the main legislation until 2016 was the Decreto Ministeriale (D.M.) (Ministerial Decree) 203/2003, defined as the “30% Decree.” On the basis of the D.M., Public Clients were required to purchase recycled products for at least 30% of their annual needs in the provision of goods and services. The decree, however, had various rigidities, especially with respect to its application in the construction sector.
In 2016, the Decreto Legislativo (D.Lgs.) (Legislative Decree) 50/2016 on procurement marked a turning point through the requirement of applying GPP in public tenders, according to European indications. Article 34 of the D.Lgs. requires all Public Clients to purchase products that comply with the Criteri Ambientali Minimi (CAM) (Minimum Environmental Criteria) issued by the Ministero dell’Ambiente (Ministry of Environment), for all classes of products and services and for the total amount of the tender (with exceptions only for construction, that has specific criteria for different construction waste types). In addition, the D.Lgs. 50/2016 includes an invalidation clause for a contract concluded between a Public Client and a company based on a “GPP non-compliant” tender. As a result, the GPP requirement caught the attention of both Public Clients and companies; the process needs, indeed, guarantees at all levels. This aspect is mostly important regarding the quality of “green” products and services offered during the tendering phase and awarded “forcibly.” The aim would be to ensure that the objectives of GPP application, i.e., environment care and “green” products diffusion and promotion, are not only a possibility on paper.
The case studies tried to apply the criteria according to Italian and European regulations in order to promote sustainable processes and introduce waste minimization strategies in Italian AECO industry.
An Innovative Tender Process Implementing Sustainable Waste Strategies
This section regards the types of tenders mainly used in Italian context, with their features and peculiarities. A focus is kept on the evaluation systems of Most Economically Advantageous Tender (MEAT) used during the tender phase in the case studies, and in particular on the criteria related to environmental impact and WM. The potential integration of this information in BIM models is presented.
Tender Process Types
Contract management models currently present in the construction market are: Design Bid Build (DBB), Design Build (DB), Construction Management at Risk and Integrated Project Delivery (IPD). The latter two models represent the most integrated and virtuous forms of design, but they are rarely applied in Italy and are not taken into account. The most common models and their peculiarities are here presented, also in relation to BIM methodology.
The DBB approach is used for almost 90% of public buildings and 40% of private buildings (Di Giuda and Villa, 2016). In this procurement model, two sequential phases are identified without direct reciprocal influences: a design tender to realize all levels of the project until the construction design, and a construction tender to identify the construction company with the best bid for the realization of the building. In the context of Building information modelling, this method generates slowdowns and limited exchanges of information due to the proprietary know-how of each company that causes re-processing of information.
The Design Build (DB), increasingly adopted to replace the Design Bid Build (DBB), stands out thanks to the merging of design and construction in a single operator. In this way, the Client dialogues with a single actor, increasing the efficiency of information transfer. Thanks to the presence of a unique actor in the building construction process management, this approach represents an excellent scenario in which to exploit BIM methodology and carry out a coordinated management of information, also considering the entire life cycle.
Given the current possibilities in terms of collaboration made by cloud services and Common Data Environments, along with the diffusion of Information modeling methods, the efficiency gap between the two procurement models is reducing. In order to evaluate the actual efficiency of the procurement models for waste minimization strategies, the two models were tested with real case studies, presented in Application on Three Case Studies. A deep explanation of the waste minimization strategies implemented in a DB procurement model is provided in the following paragraphs, since the DB model has proved to be the most promising in terms of collaboration and efficiency.
Method and Criteria for Bid Evaluation
One of the main innovations introduced by D.Lgs. 50/2016 is the introduction of the reward criterion with Most Economically Advantageous Tender (MEAT), based on the quality/price ratio calculated on the life cycle of the building (Art. 95, c. 2, D.Lgs. 50/2016). In order to properly implement this evaluation system, a breakdown of the building’s elements and of the phases involved in the building life cycle, and a detailed definition of their evaluation must be carried out. This process leads to the definition of guidelines, schemes and annexes to be shared with the participants in the call for proposals. These documents identify criteria, sub-criteria, methods and specific formulas for the evaluation of the MEAT. Defining a detailed set of objective criteria and their evaluation systems allows an objective, non-discriminatory and transparent comparison between all the bids received during the tender process.
Table 4 shows the scheme used for the evaluation of the case study set out below. A number of aspects that could be improved were identified at a general level: building envelope performance, building services performance, management and safety in construction phase, and maintenance. The evaluation of the bids is based on the definition of quantitative and qualitative criteria, that can be linked to quantitative classes, or to qualitative classes (when requiring a subjective assessment, e.g., in the case of aesthetical features). In such a way, the evaluation system is based on objective alpha-numerical criteria to define the quality of the bids. In conclusion, the rankings are determined based on linear interpolations for the quantitative criteria and on the compensatory aggregative method on the whole bid. This method also allows an automation of the evaluation process.
Table 4 highlights all the criteria and sub-criteria that contribute to the general assessment of the environmental impact of WM. It should be noted that C&D WM is evaluated directly through the individual criterion C.2.3 within the management phases of the building site, but also indirectly by considering construction materials, their degree of maintenance, distance of production site and process certifications for contractors and manufacturing companies. Among others, the contractor’s EMS (Environmental Management Systems) certifications (UNI EN ISO 14001) are rewarded, in order to promote the adoption of voluntary performance targets, and environmental certifications of the building construction products. Considering the goal of this research, indirect aspects have been omitted to focus on those strictly related to WM. As presented in the previous sections, GPP tenders are stressing the attention on the minimization of the environmental impacts throughout the entire building life cycle, as introduced by European and Italian regulations. The fulfilment of the environmental criteria can increase the ranking of the participant to the tender. As a matter of fact, regulatory imposition and, above all, reward criteria are a valuable method of promoting the implementation of environmental aspects in AECO sector.
Regarding the category C–Construction site, the construction phase focuses on technical solutions that guarantee an increased in durability, maintenance, construction ease, safety, and WM. The sub-criterion C.2.3–WM is used for detailed forward-looking analyses of qualitative and quantitative waste production during the building construction.
The measures outlined in C&D WM planning consists in reducing, reusing, and recycling the waste, where the reduction and, if possible, avoidance, of waste production is the most effective solution. C&D waste that can not be reused or recycled can only be landfilled. According to this approach, some priorities are defined among waste categories, used to provide compensations and assign additional points during the competition phase: reduction waste strategies are promoted with higher rankings. On the other hand, to evaluate qualitative aspects, the competitors are asked to provide a report that describes processes and methods adopted to manage waste on site. The presence of a quantitative definition of WM combined with a technical report makes it possible to carry out detailed controls during the execution phase, verifying the application of the methods proposed by the contractor and comparing them with site and transport documents. The linear interpolation used to obtain the final score on this specific sub-criterion is described in detail below, using an extract from the guidelines of the tender.
Extract From Guidelines for Tenders’ Preparation: Sub-Criterion C.2.3 - Waste Management
What Was Evaluated
It is requested to formulate an offer to define the amount of waste that will be produced. It is necessary to underline the amount of non-hazardous waste from construction activities (excluding excavated soil and debris) that will not be sent to landfills or incinerators, reusing the recyclable resources recovered in the production process and redirecting the materials to specific collection sites, according to one of the following alternatives:
• Re-use of waste materials on site: indicate the quantities of waste expected to be reused on the same site, the methods of use and any necessary treatment for reuse.
• Recycling of waste materials: indicate the methods of separation of the waste on site in a differentiated manner to be collected by an authorized company, which will carry out the differentiated storage and recycling directly and/or transfer the differentiated waste to third parties.
• Disposal: indicate the quantity and type of special hazardous waste (EWC code) that will be produced on site and the disposal methods envisaged with an indication of the companies and sites envisaged for treatment and controlled disposal.
A technical report must therefore be produced, indicating: the quantity of waste (with suitable units of measurement) for each material and divided by processing (Table 5); the methods and checks that will be carried out for the reuse of the materials.

TABLE 5. Example of table to define percentages of wastes to be reused, recycled, or landfilled, with the proper EWC code.
In addition, for each waste material, it is necessary to fill:
• EWC codes;
• A description of construction activities involving those materials;
• Total quantity
• Percentage of non-hazardous waste material that will be re-used in the construction site;
• Percentage of non-hazardous waste material, excluding excavated land and tillage waste (
• Percentage of non-hazardous waste material, excluding excavated land and tillage waste, that will be sent to landfills or incinerators
• Percentage of hazardous waste material, as defined by directive 2008/98/CE, that will be disposed of in authorized landfills (
For each EWC code, the following verification will be done: for non-hazardous materials the sum of percentages (
Evaluation
The evaluation will be performed on the percentage, related to the quantity, of recycled, reused, and disposed of waste material. The score will be based on the following formulas:
Where
The total amount (in kg) of waste materials to be reused (
Where N is the number of materials of Table 5.
The total amount of waste/scrap material is equal to the sum of the quantities related to recycle, reuse, dispose of, both for non-hazardous (with subscript Nper) and for hazardous materials (subscript per).
This value allows calculating the percentage of materials to reuse, recycle, and dispose of:
It is necessary to define a WM coefficient, as shown in Table 6.
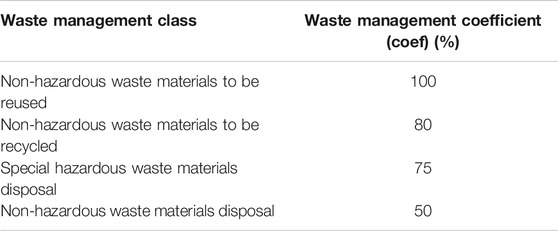
TABLE 6. Waste management coefficients for non-hazardous and hazardous waste materials related to waste treatments.
For each offer (i), it will be necessary to calculate the value of
For each offer (i), it will be necessary to evaluate the score with the following formula:
Where
The score of the sub-criterion will be adjusted following the methodology provided in the Determinazione AVCP n. 7 del 24 Novembre 2011, “Linee guida per l’applicazione dell’offerta economicamente più vantaggiosa nell’ambito dei contratti di servizi e forniture”.»
Once the evaluation is described, the following paragraph will underline how BIM methods and BIM authoring software provide quantitative evaluations based on the use of parameters, resulting in faster and more efficient processes, and guaranteeing the consistency of the information flow during the whole building life-cycle.
The Information Modelling Method and the Implementation of Waste Management Strategies
One of the main problems of MEAT tenders is the lack of consistency among project drawings and, in general, among the tender-based documentation. In this sense, Guidelines of the Autorità Nazionale Anticorruzione for contracting authority, that are administrative law documents drawn up by the Italian national anti-corruption authority, suggest “to develop templates, also in electronic format, which facilitate the preparation and submission of bids, both technical and economic, by competitors.”
The adoption of BIM methodology is highly suitable to meet this indication and to partially overcome the above-mentioned problems. The Building information model represents, in fact, a single source of all the drawings and information, both graphic and non-graphic, of all the disciplines involved in a construction project, allowing to maintain consistency throughout the preparation of the tender and consequently in the preparation of bids. It is therefore possible to extract all the project outputs - such as building plans, sections, documents like quantity take-off or also performance specifications - as well as the bid sheets, directly from the BIM model. To make efficient use of Information modelling methods, it is essential to organize data, information and knowledge in a structured form. Parameters are set for each object and organized in easily recognizable homogeneous sections, so that they are also ordered and easily manageable for the creation of tables and the extraction/import operations.
As introduced earlier in the literature review, BIM could help to manage and minimize the amount of Construction and Demolition waste. It could enable the management, the reduction and, in the best situations, avoidance of waste by means of design reviews, clash detection, quantity take-off, phase planning, site utilization, and digital prefabrication. Some relevant example of these activities are presented in the case studies.
These applications are possible when the BIM model is properly set with the goal of quantity and WM, both in the design phase and in the construction phase. The proposed method implies that each type of material in the BIM library is identified with a parameter that specifies the EWC code of the waste material related (Figure 4). This approach allows the evaluation of C&D WM based on quantities of waste materials. During the tender, it could be possible to identify materials producing the higher quantity of waste, and therefore structure criteria for the evaluation of bids that will promote a better second-life management of these materials.
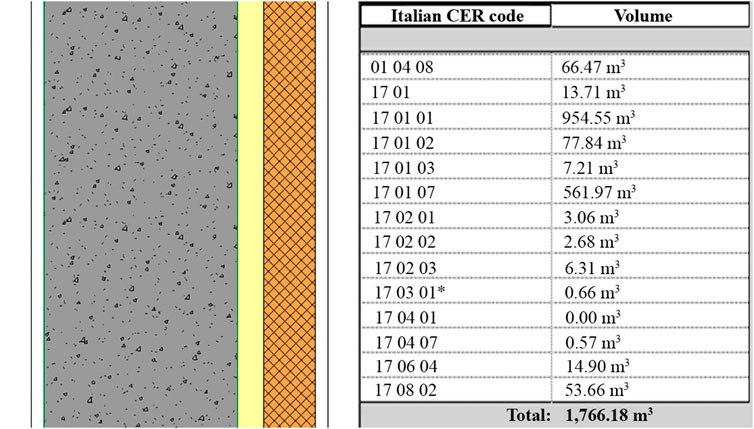
FIGURE 4. Information regarding EWC (Italian CER) codes assigned to building materials in the BIM model.
As previously stated, considering the current state of art regarding BIM-based software, an interaction between different tools is required to provide detailed analysis on waste information management. Waste generated by the packaging of building construction materials, and scraps deriving from construction activities, are difficult to manage and quantify within the BIM model. To overcome these issues, the proposed framework combines the use of BIM models with external data sheets to support the elaboration and analysis of the bids during the tender phase. These spreadsheets allow comparisons among data, and the customization of criteria and calculation methods. The information contained in the spreadsheets can be linked with the BIM models helping information management and storage during the entire building life cycle. This information could be valuable also to manage tender processes of building disposal and demolition.
Application on Three Case Studies
Three case studies of Design Build and DBB tenders are presented. All projects are related to public schools in Italy designed using BIM methodology. The first project is a DB tender process for a primary school in Melzo (MI). The construction was completed in 2017; the tender process implied the criteria of the MEAT method set out above, before the introduction of C&D WM EU directives and the Italian regulations. The second case study presented is a DBB tender process regarding the project of a secondary school in Liscate (MI). A comparison with the DB tender is also provided. Finally, the ongoing DB tender process for a primary and secondary school in Inveruno (MI) is introduced focusing on the evolution of the environmental management system of the construction site. This represents a work in progress that will be implemented and monitored throughout the design and construction process, in order to analyze further advantages and disadvantages of the method. This project is based on current legislation, and especially on the CAM (Minimum Environmental Criteria), which integrate many aspects of environmental management of the building process illustrated so far.
Primary School in Melzo: Design Build
This case study concerns the detailed design and construction of the new primary school for 500 students in Melzo (MI) and has a €5 M construction budget. This project was developed in 2015 therefore the CAM are not applied. The Italian legislation related to environmental sustainability was defined by D.M. 152/2006 “Norme in materia ambientale (Environmental standards),” which also regulates WM, and by D.M. 203/2003, which defines the minimum quantities of recycled materials to be guaranteed in public contracts. This regulatory framework demanded only a control on hazardous waste. This control was carried-out by means of site-specific instructions and loading register for transport to other sites. For all other materials, it was not mandatory to draw up documents for WM on site and, above all, the selection of materials with recycling rates was not required.
To improve the environmental impact value, BIM methodology framework was used in this case both in the project design phase and in the tender process drafting. Considering the design phase, the main advantages resulting from the application of the proposed methodology are the possibility to avoid and reduce waste production during design reviews and clash detection between disciplines, processing of quantity take-off and digital prefabrication for walls and facade systems. For instance, the finishing panels of the main facade of the building were optimized in terms of size, quantity and colors of each individual panels in relation to the client’s requirements, to reduce the amount of waste on site. During the tendering phase, the possibility of making further improvements in site management and C&D WM was promoted. Each company illustrated in the offer how it could manage environmental factors affecting the construction also in relation to other aspects.
The drafting of the tender documents was carried out as previously described in An Innovative Tender Process Implementing Sustainable Waste Strategies, but the use of the BIM model was not mandatory for the submission of tenders. The procurement systems used in Melzo process is detailed in Di Giuda et al. (2016); data reported in the received bids are congruent, complete and unequivocal. The analyses provided can therefore count on valid and unambiguous proposals.
Since the use of BIM in the tender phase was not required, the entire process was conducted in parallel with the traditional management of documentation both in the tender phase and in the construction phase. The model was a verification tool for companies and designers to verify and validate their project and documentations. Also, it allowed to test the defined method from the research point of view. Since the use of an information exchange platform has not been contractually agreed upon, the procedure for acceptance and approval of materials by the Works Management was carried out in a traditional way. In parallel, the same documents are placed on an experimental platform connected to the modelled elements, in order to deliver to the client an as-built BIM model, containing all the information and documents regarding the construction.
Data Analysis and Discussion
Regarding the first case study, environmental criteria regarded more than 40 points and, within these, WM criteria involved directly and indirectly 15 of the 100 total points. In particular, the previously illustrated sub-criterion C.2.3–WM (Extract From Guidelines for Tenders’ Preparation: Sub-Criterion C.2.3 - Waste Management) allowed to collect a maximum score of 3 points.
Considering the nine technical bids admitted to tender, all the construction companies filled the quantitative table and attached the specific report for WM, as required in the sub-criterion “C.2.3–WM”. This result shows that the presence of WM among the improvement criteria has succeeded in stimulating interest on this subject (Figure 5). Most of the proposals developed a good degree of detail on the issue, but only half of the proposals described how the most virtuous waste reduction and reuse activities are carried out on site. Moreover, compared to the average 2.35 of the points obtained, only two offers showed significantly lower results, due to the high quantity of material classified as general mixed waste. In general, the bids with the highest scores appear to be directly related to the detail in analyzing and separating at the highest level the types of waste in relation to the planned site operations. Both these observations show that the majority of the companies have interest in proper WM. Due to their own technical background and thanks to the requests of the call for tenders, the companies have integrated the organizational and technical skills for a proper WM.
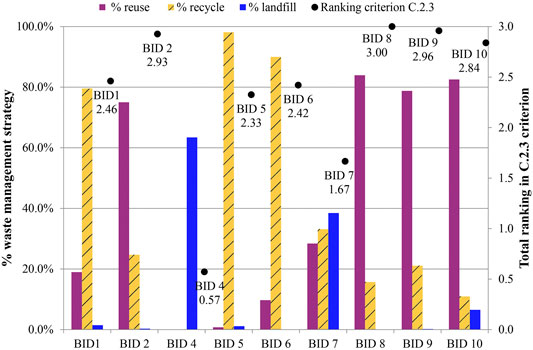
FIGURE 5. Comparison between percentages of waste management strategies and rankings in sub-criterion C.2.3.
All seven offers performing above average included high quantities of material for reuse and recycling. Based on these two types of treatments, it is also possible to identify a second important split linked to the quality of WM and selective demolition. These offers show percentages that exceed 75% on one of these two possible activities related to waste (reuse and recycling). Companies that manage to obtain a greater quantity of material to be reused -compared to that to be sent for recycling-, that results in a lower environmental impact, can be distinguished.
Considering EWC codes (Italian CER) used in the four bids with reuse percentages of waste materials around 80%, including the winning bid, the prevailing materials to be reused are cement, bricks, tiles and ceramics (Figure 6). These materials are used for the construction of the sub-bases of the pitches and roadways on site, or as filler for the planned embankments, or as recovered aggregates for concrete mixes. In the background, partial reuses of wood-based and gypsum-based materials, bituminous mixtures or insulating materials can be highlighted: in these cases, it is certainly necessary to investigate the procedures of reuse adopted by the contractor. In fact, for these materials there is a lack of homogeneity in the methods of waste treatment implemented in the four offers. Finally, considering recycling, materials deriving from packaging and metal alloys play a predominant role.
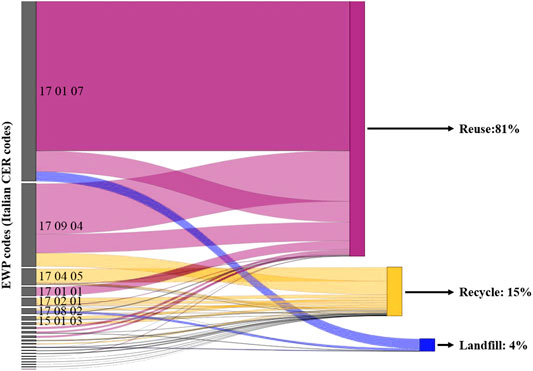
FIGURE 6. Percentages of reused, recycled and landfilled materials of the four bids with higher rankings.
It is generally observed how the Design Build (DB) contract allows the contractor to obtain greater awareness and integration of WM strategies. The possibility for the constructor to manage the information, documentation and the process flow since the final design phase, minimizes the production of wastes, that in a traditional process would have been linked to project incompleteness or rework. Moreover, thanks to all these aspects, the waste produced in the operational phase can be better managed guaranteeing high reuse and recycling percentages.
Secondary School in Liscate: Design Bid Build
The project concerns the construction of a secondary school in Liscate (MI) for 150 students and €5 M of construction costs. The school was developed in 2017 through a BIM approach and applies the Framework Alliance Contract (FAC-1) as part of the project, showing a high level of complexity. The project development was carried out through a Document Management System (DMS) linked to a BIM-based data management, as detailed in Di Giuda et al. (2020b).
This second case study, only related to construction tender, was carried out in an advanced scenario due to the introduction of the CAM. For the DBB tendering phase, the CAM legislative framework only provide for the application of the contractual clauses according to point “2.7 Conditions of execution.” The design requirements imposed by CAM, previously defined by the appointing party during the design tender, should in this phase only be applied and guaranteed by the Contractor. The use of a bid evaluation system based on reward criteria is suggested, but still optional.
For the project tender, the contractor has requested the total application of CAM without specific prescriptions. Therefore, quantitative criteria for the evaluation of participants regarding environmental aspects, including WM, were not integrated. In the second phase of the construction contract, a variant of the MEAT evaluation system set out in this paper was applied and adapted to the needs of a DBB contract.
Compared to the first case study of Melzo, a relevant difference can be underlined, regarding the role of the contractor and of the appointing party. In this case, the evaluation of WM was based only on certifications concerning the production of prevailing products, and on the management of the building site and its impact on the surrounding area. In general, the entire bid evaluation system reflected the greater attention on the construction phase, since the Contractor could not intervene on the purely design aspects. As a result of the separation of the two phases of the design and construction tender processes, data on quantities of reused, recycled, and landfilled materials are not available, since the Contractor could not intervene in the design phase.
Primary and Secondary School in Inveruno: Design Build
This third case study concerns the construction of a school complex in the municipality of Inveruno (MI) by means of a DB call for design and construction for a total amount of €15 M. The setting of the call for tenders is currently under development. The appointing party is proceeding with the application of CAM on the whole process, realizing a total integration of their requirements in the tender documentation. Unlike the DBB process, the DB tender involves the mandatory compliance with all the technical specifications of CAM and all the related methods. The reward criteria required by CAM will be integrated with additional ones, including the quantitative criteria related to WM exposed in this paper.
Within this project, WM plays a fundamental role. The project includes selective demolition of old school buildings. In addition, the building site hosted parts of a disused industrial building, not yet demolished. Detailed plans regarding the management of materials, and of excavated soils will be required to encourage the processing of waste for local reuse or the regeneration of by-products. Both the Client, and the Contractor aim at developing with the best methods these regeneration activities of materials included in the DB tender. The Client will obtain a correct environmental management of the common good and can exploit in advance the economic value of the waste to be reconverted to resources, by compensating other economic items of the initial investment. At the same time, as the Contractor owns excavated soil and regenerated products resulting by the selective demolition activities, an important form of incentive for the correct management of the waste is created. This approach represents in a clear way the shift from waste to resource to be applied to materials derived from demolition and excavation, as promoted by the European Directives.
As previously stated, this project is still under development; the whole project is being carried out through a BIM approach. Design review, quantity take-off, phase planning, site utilization, and digital prefabrication options will be detailed and developed through the BIM model. These will be joined by other aspects that participate in improving the environmental impact of design and execution development. Given the importance of collaboration, BIM methodology will be applied and combined with a Common Data Environment platform. This platform will facilitate the verification phases of the on-site WM. Dashboards would be set for the graphical visualization and comparison of the quantitative results expected during the tender phase and those achieved during the construction. The commitment to environmental protection will be guaranteed by a specific criterion to be included in the tender phase, requiring LEED certification. As a result, a guarantee method for the Client developed by a third party will be applied.
Blockchain for Green Procurement: A Theoretical Analysis of the Benefits
In Construction and Demolition Waste Regulation Framework, the introduction by the European Directive 2018/851 of electronic registers for the homogeneous collection of data on waste has been highlighted. The use of electronic register aims at guaranteeing the reliability and accuracy of data on recycled materials. The creation, maintenance and sharing of such register improves both the clarity on products or components designed and prepared for re-use and the understanding of what has actually been recycled as a result. The electronic register therefore makes it possible to set recycling targets for all components used in the process, bearing the final WM and subsequent treatment in accordance with the principles of circular economics.
The presence of an electronic database created and enriched from the design phase enhances the activities of recording, collection and traceability of data, promoting a lean development of the life cycle of materials. In addition, the electronic sharing of information relating to waste makes it easier for designers, companies and suppliers to record all data relating to the life cycle of materials and products, improving the related control activities and, consequently, increasing collaboration among them.
The process based on the creation of the electronic registers becomes truly beneficial when the data it contains are reliable, transparent and immutable. For these reasons, this section introduces Blockchain technology to support the WM process in the construction industry. Thanks to the immutability and transparency offered, the development of sustainable processes and green procurements can benefit from the use of the technology. The potential benefits and the theoretical implementation of the technology in the construction process are presented in order to encourage further researches and real case studies of green supply chains development through the use of Blockchain platforms.
Reliability of Waste Information Issue
As in many other industries, the research shows that also in the construction sector the WM represents a relevant challenge that affects the environment and the pursuit of a sustainable and green supply chain. The possibility to pursuit a green procurement addressed issues such as WM, carbon footprint, packaging and transportation and in this way guarantees a high efficiency of the process and low pollution levels (Rane and Thakker, 2019). For these reasons, in the recent years many regulations have been laid down to manage these procedures. The main goal is to close the circle that characterizes the life cycle of the product, from its production to the management of waste or secondary raw materials.
In order to be able to close, i.e., make circular, the life cycle of a product, its correct design becomes fundamental. Since buildings in the built environment have a long-life span, improving the design of materials, products and components is essential to reduce the building environmental impact and improve the durability and recyclability of its parts, with consequent reduction of waste production.
There is no doubt that technological advancements have caused a revisiting of sustainability practices inside the construction sector. Thanks to its nature as an integrated design system that allows all participants, such as designers, contractors and suppliers, to operate in a concerted manner by managing all information on the same platform, Building Information Modeling contributes directly to the implementation of the circular economy. Unfortunately, due to the large number of participants and the information created and exchanged, the platform used in the BIM process does not always ensure the reliability, traceability, origin and ownership of the information, hindering the effective pursuit of sustainable procedures due to the scarcity or lack of data. These BIM issues could be resolved through the vertical and horizontal integration of Blockchain inside the circular and sustainable construction processes (Di Giuda et al., 2020c).
Blockchain as an Enabler for Waste Management Optimization
Despite first uses of Blockchain lies in banking and finance sectors, recently other industries such as energy and supply chains have realized its potential. Indeed, Blockchain technology, thanks to its structure, is consider as a technology that could disrupt every industry in the world. Since it belongs to Distributed Ledger Technologies, the distributed nature of Blockchain guarantees the shift form a centralized storage database to a distributed ledger shared among all the process participants. The procedures used by Blockchain to store, link and transact data assure the information of avoiding any attempt of manipulation or counterfeiting. In addition, the programmable nature of Blockchain enables some applications such as Smart Contracts that represent self-executing computer codes that perform specified actions (releases funds, sends information, makes purchase, etc.) when certain conditions are met, in the real world (a payment is received, the outcome of an event is determined, etc.) (Kouhizadeh and Sarkis, 2018). Due to their structure and functioning these contracts reduce the amount of human involvement required to create, execute and enforce a contract, thereby lowering its cost while raising the assurance of execution and enforcement processes. The European Regulation EIDaS–Electronic Identification, Authentication and Trust Services Regulation (EU Regulation no. 910/2014) recognizes the Blockchain validity and functions, based on distributed ledger that legally guarantees the identity, as well as the electronic time validation of document stored on the platform.
In view of the legal recognition of Blockchain, it can improve and be integrated with the BIM platform in two ways. A vertical integration would allow the creation of a combined platform for the digitalization of the entire process, with a guarantee about the identity of participants, the immutability of the documents entered and the consequent possibility to provide for the adoption of Smart Contracts. A horizontal integration would allow to trace the entire life cycle of the product used during construction until its reduction to the state of waste would extend the radius of the circular economy, ensuring evidence from the design phase until the waste of construction and demolition. The latter integration is fundamental to support an efficient development of a green procurement based on a Blockchain-based BIM process through which is possible to track the product right from its raw material phase to the end of its life, such as recycle or reuse (Figure 7). The tracking of items from supplier to customer is characterized by all the information about the processing, the location and the quality of the items, giving a transparent development of the process and improving its control.
The distributed system provides the needed trust and transparency within the information exchange among all the participants of the construction process. Blockchain technology can potentially improve the transparency and traceability issues within the supply chain through the use of immutable record of data, distributed storage, and controlled user accesses. Blockchain can overcome BIM barriers related to lack of data, lack of trust in data and the gap in regulatory framework supporting the implementation of circular economy principles (Bolier, 2018). Blockchain indeed promises tamper-proof recording of data related to materials, products or component supporting the improvement of information management for the entire supply chain enabling the development of sustainable business (Vogel et al., 2019).
Smart Contracts Supporting the Green Procurement Process
In order boost the WM and the circular economy principles inside the construction industry, a novel approach based on Blockchain is proposed as a further development. The presence of a distributed ledger that stores information in an immutable and transparent manner is beneficial to all participants in the process. In addition, the ability to define and execute the various contractual tasks through Smart Contracts not only streamlines procedures but also provides incentives for the contracting parties to perform their tasks in accordance with the contractual terms. All information produced and exchanged during the design phase of the building, including the life cycle planning of materials, products and components and the prediction of their reuse, recycling and disposal, are recorded on the Blockchain. This data is accessible at all times in order to understand the correct pre-design of the construction waste and its impact on the environment.
On the basis of the design, the client may request in the invitation to tender specific WM methods and include reward clauses for the choice of reusable or recyclable materials. The reward clauses can be translated in computer codes of a Smart Contract that releases automatically the reward when the request is satisfied. All communication between companies and suppliers is recorded on Blockchain and allows transparent observation and access to the complete life cycle of materials and products chosen and used in construction. The ability to have this information recorded on Blockchain allows to create a truthful identity card of the materials used, useful not only for those involved in the construction of the building, but also for those who will use the building and especially for those who will have to demolish or break it down. Thanks to the registration of the entire life cycle of the product and the planning of its reuse, recycling or disposal, it is easy to guarantee the circularity of all components of the building.
For these reasons, the distributed database offered by Blockchain can transform the traditional supply chain in a green one, supporting the reduction of energy usage and efficient waste disposal. The development and management of product life cycle based on Blockchain could result in a positive impact on construction resources and materials utilization and recycle. Since that Blockchain archived the identity card of every material from the design phase to the demolition one, the information flow could be more effective and it could maintain the value of products and services during its whole life.
In conclusion, Blockchain can be considered as a useful technology, able to offer ecological and economic benefits. The distributed ledger promotes both a better integration among the participants network and a suitable monitor of the materials and waste cycle, by recording all information or actions (Abeyratne and Monfared, 2016).
Conclusions
Increasing global urbanization has resulted in high levels of waste. The construction sector is one of the most polluting industrial sector, with an estimated waste production of about 36%. Also, AECO sector shows a still increasing trend in waste production, especially in comparison with other industries. An overview regarding European and Italian regulations showed the attention on the need to reduce the production of wastes and to perform environmentally sustainable processes. In this sense regulations promote the adoption of waste minimization strategies. In addition, waste is no longer seen as a burden but as a resource and a profit for all actors and stakeholders involved in the whole construction process.
Several drivers for the implementation of waste minimization strategies in AECO industry and to overcome the barriers identified, can be summarized as follows:
• Promotion by regulations and public Clients’ requirements of sustainable strategies;
• Competitiveness for construction companies is strongly intertwined with the implementation of sustainable strategies into their own business models;
• Information modelling methods could allow the avoidance of waste production since the preliminary phases of the construction process, enabling the collaboration among parties, the integration of WM strategies and an easier definition of waste quantities to be reused and recycled.
Previous applications in the literature investigated efficiency of BIM methodology for waste minimization strategies from the designer and constructor’s point of view.
The present work analyzed by means of three case studies the integration of waste minimization and management strategies during the tender phase. The application of BIM methodology to handle the tender phase is also tested from the public Client’s point of view. Two types of procurement models, i.e. DB and DBB, have been applied in order to identify the related feasibility to promote sustainable practices in the construction sector. The collaboration between Client and constructor and a less fragmented information flow, enabled by the DB procurement model, allow a better implementation of waste minimization and management strategies. The DB model seems to be the most promising in terms of collaboration and efficiency. In particular:
• Environmental reward criteria led the participants at the tender phase to integrate sustainable practices in their procedures;
• Sustainable requirements as reward criteria in the tender phase promoted the participants to apply and extend their know-how in the field of waste management;
• BIM approaches in a MEAT framework allowed the Client to verify the compliance of the bids with the requirements in terms of sustainability, and the participants to more easily apply waste minimization strategies.
• Almost a half of the participants, including the winning one, proposed a reuse strategy for about the 80% of wastes.
The case studies showed the possibility for the public Clients to trigger a change in the construction sector regarding the integration of waste minimization and management practices, through the application of GPP and BIM methodologies.
Furthermore, a distributed ledger technology, i.e. the application of Blockchain for the implementation of Smart contracts, could promote both a better integration among the participants’ network and a suitable monitor of the materials and waste cycle. The information recorded on the Blockchain can be accessed at any time in order to monitor the correct planning of the construction waste and its impact on the environment, recording all information or actions in a full transparent way.
Data Availability Statement
The original contributions presented in the study are included in the article/Supplementary Material, further inquiries can be directed to the corresponding author/s.
Author Contributions
LT: ideation, management, editing. LP: workflow definition and organization. SC: data analysis and investigation. ML: data collection and preparation. GP: regulation and introduction. GD: methodology and conclusions.
Funding
This work was supported by the BIM Group, a research unit of ABC Lab for the Digital Transition in AECO sector, of the Department of Architecture, Built Environment and Construction Engineering, Politecnico di Milano.
Conflict of Interest
The authors declare that the research was conducted in the absence of any commercial or financial relationships that could be construed as a potential conflict of interest.
Acknowledgments
The authors want to thank Francesco Paleari, Marco Schievano, and Elena Seghezzi for the development of the three case studies and for the support to this research project.
References
Abeyratne, S., and Monfared, R. (2016). Blockchain ready manufacturing supply chain using distributed ledger. Int. J. Renew. Energy Technol. 5 (9), 1–10. doi:10.15623/ijret.2016.0509001
Addis, B., and Jenkins, O. (2008). Briefing: design for deconstruction. Waste Resource Manag. 161, 9–12. doi:10.1680/warm.2008.161.1.9
Adjei, S. D., Ankrah, N. A., Ndekugri, I., and Searle, D. (2018). “Sustainable construction and demolition waste management: comparison of corporate and project level drivers,” in Proceeding of the 34th annual ARCOM conference, ARCOM, Belfast, UK, September 3–5, 2018, 99–108.
Ahankoob, A., Khoshnava, S. M., Rostami, R., and Preece, C. (2012). “BIM perspectives on construction waste reduction,” in Management in construction research association, Malaysia, January, 195–199.
Ajayi, S. O., Oyedele, L. O., Akinade, O. O., Bilal, M., Owolabi, H. A., Alaka, H. A., et al. (2016). Reducing waste to landfill: a need for cultural change in the UK construction industry. J. Build. Eng. 5, 185–193. doi:10.1016/j.jobe.2015.12.007
Akbarnezhad, A., Ong, K. C. G., and Chandra, L. R. (2014). Economic and environmental assessment of deconstruction strategies using building information modeling. Autom. ConStruct. 37, 131–144. doi:10.22260/isarc2014/0051
Akinade, O. O., Oyedele, L. O., Bilal, M., Ajayi, S. O., Owolabi, H. A., Alaka, H. A., et al. (2015). Waste minimisation through deconstruction: a BIM based deconstructability assessment score (BIM-DAS). Resour. Conserv. Recycl. 105, 167–176. doi:10.1016/j.resconrec.2015.10.018
Arain, F. M., Assaf, S., and Pheng, L. S. (2004). Causes of discrepancies between design and construction. Architect. Sci. Rev. 47 (3), 237–249. doi:10.1080/00038628.2000.9697530
Blayse, A. M., and Manley, K. (2004). Key influences on construction innovation. Construct. Innovat. 4 (3), 143–154. doi:10.1108/14714170410815060
Bolier, M. (2018). Blockchain technology to accelerate the transition towards a circular economy. Delft University of Technology.
Buchan, R. D., Kelly, J. R., and Fleming, F. W. (1991). Estimating for builders and quantity surveyors. London, UK: Newnes.
Chen, K., Lu, W., Peng, Y., Rowlinson, S., and Huang, G. Q. (2015). Bridging BIM and building: from a literature review to an integrated conceptual framework. Int. J. Proj. Manag. 33 (6), 1405–1416. doi:10.1016/j.ijproman.2015.03.006
Cheng, J. C. P., and Ma, L. Y. H. (2013). A BIM-based system for demolition and renovation waste estimation and planning. Waste Manag. 33 (6), 1539–1551. doi:10.1016/j.wasman.2013.01.001
Cheng, J. C. P., Won, J., and Das, M. (2015). “Construction and demolition waste management using BIM technology,” in Proceedings of IGLC 23 - 23rd annual conference of the international group for lean construction: global knowledge - global solutions, Perth, Australia, January 2015, 381–390.
Dainty, A., Green, S., and Bagilhole, B. (2007). People and culture in construction: a reader. Abingdon, UK: Routledge.
Deborah, H., Trefor, W., and Zhaomin, R. (2012). Differing perspectives on collaboration in construction. Construct. Innovat. 12 (3), 355–368. doi:10.1108/14714171211244613
Di Giuda, G. M., Giana, P. E., Paleari, F., Schievano, M., Seghezzi, E., and Villa, V. (2020a). “A BIM-based process from building design to construction: a case study, the school of Melzo,” in Research for development. Berlin, Germany, Springer International Publishing, 163–173.
Di Giuda, G. M., Giana, P. E., Schievano, M., and Paleari, F. (2020b). “A collaborative approach for AEC industry digital transformation: a case study, the school of liscate,” in Research for development. Berlin, Germany, Springer International Publishing, 175–184.
Di Giuda, G. M., Pattini, G., Seghezzi, E., Schievano, M., and Paleari, F. (2020c). “The construction contract execution through the integration of blockchain technology,” in Digital transformation of the design, construction and management processes of the built environment. Berlin, Germany, Springer International Publishing, 309–318.
Di Giuda, G. M., and Villa, V. (2016). Il BIM. Guida completa al Building Information Modeling per committenti, architetti, ingegneri, gestori immobiliari e imprese. Milano, Italy: Hoepli.
Di Giuda, G. M., Villa, V., Tagliabue, L. C., and Ciribini, A. L. C. (2016). Process innovation: the use of BIM-oriented model for most economically advantageous tender. Matera, Italy: Colloqui.AT.e.
Ekanayake, L., and Ofori, G. (2000). “Construction material waste source evaluation,” in Proceedings of the strategies for a sustainable built environment, Pretoria, South Africa, August 23-25, 2000.
Fairclough, J. (2002). Rethinking construction innovation and research-a review of the government’s R&D policies and practices. London, UK: DTI.
Fewings, P., and Henjewele, C. (2019). Construction project management: an integrated approach. Oxford, UK: Taylor & Francis.
Fishbein, B. K. (1998). Building for the future: strategies to reduce construction and demolition waste in municipal projects. New York, NY: INFORM, Inc.
Flanagan, R., and Lu, W. (2008). “Making informed decisions in product-service systems,” in IMechE conference, knowledge and information management through-life, London, UK, June 24, 2008.
Formoso, C. T., Luís Isatto, E., and Hitomi Hirota, E. (1999). “Method for waste control in the building industry,” in 7th annual conference of the international group for lean construction, Berkeley, CA, July 26–28, 1999, 325–334.
Guy, B., Shell, S., and Homsey, E. (2002). “Design for Deconstruction and Materials Reuse”, in Design for Deconstruction and Materials Reuse. Rotterdam, Netherlands, Inhouse publishing, 21.
Hamidi, B., Bulbul, T., Perace, A., and Thabet, W. (2014). “Potential application of BIM in cost-benefit analysis of demolition waste management,” in Construction research congress, 2014, Atlanta, GA, May 19–21, 2014, 140–149.
Kibert, C. J. (2016). Sustainable construction: green building design and delivery. Hoboken, NJ: John Wiley & Sons.
Koskela, L. (1992). Application of the new production philosophy to construction. CIFE Technical Report No. 72.
Koskela, L. (2004). “Making-do the eighth category of waste,” in 12th annual conference of the international group for lean construction, Helsingor, Denmark, August 3–5, 2004.
Kouhizadeh, M., and Sarkis, J. (2018). Blockchain practices, potentials, and perspectives in greening supply chains. Sustainability 10, 1–16. doi:10.3390/su10103652
Liu, Z., Osmani, M., Demian, P., and Baldwin, A. N. (2011). “The potential use of BIM to aid construction waste minimalisation,” in Proceedings of the CIB W78-W102 2011: international conference, Sophia Antipolis, France, 26–28 October.
Lu, W., Webster, C., Chen, K., Zhang, X., and Chen, X. (2017). Computational Building Information Modelling for construction waste management: moving from rhetoric to reality, Renew. Sustain. Energy Rev. 68, 587–595. doi:10.1016/j.rser.2016.10.029
Matthews, E., Amann, C., Bringezu, S., Fischer-Kowalski, M., Huttler, W., Kleijn, R., et al. (2000). The weight of nations. Material outflows from industrial economies. Washington, DC:World Resources Institute.
Mossman, A. (2009). Creating value: a sufficient way to eliminate waste in lean design and lean production. Lean Constr. J. 13–23.
Osmani, M. (2012). Construction waste minimization in the UK: current pressures for change and approaches. Procedia Soc. Behav. Sci. 40, 37–40. doi:10.1016/j.sbspro.2012.03.158
Osmani, M., Glass, J., and Price, A. D. F. (2008). Architects' perspectives on construction waste reduction by design. Waste Manag. 28 (7), 1147–1158. doi:10.1016/j.wasman.2007.05.011
Porwal, A., and Hewage, K. N. (2012). Building information modeling–based analysis to minimize waste rate of structural reinforcement. J. Construct. Eng. Manag. 138 (8), 943–954. doi:10.1061/(ASCE)CO.1943-7862.0000508
Rajendran, P., and Pathrose, C. P. (2012). “Implementing BIM for waste minimisation in the construction industry,” in Proceedings of the 2nd international conference on management, Malaysia, June 11–12, 2012, 557–570.
Rane, S. B., and Thakker, S. V. (2019). Green procurement process model based on blockchain–IoT integrated architecture for a sustainable business. Manag. Environ. Qual. Int. J. 31 (3), 741–763. doi:10.1108/MEQ-06-2019-0136
Tatum, C. B. (1989). Organizing to increase innovation in construction firms. J. Construct. Eng. Manag. 115 (4), 602–617. doi:10.1061/(asce)0733-9364(1989)115:4(602)
Teo, M. M. M., and Loosemore, M. (2001). A theory of waste behaviour in the construction industry. Construct. Manag. Econ. 19 (7), 741–751. doi:10.1080/01446190110067037
Tingley, D. D, and Davison, B. (2012). Developing an LCA methodology to account for the environmental benefits of design for deconstruction. Build Environ. 57, 387–395. doi:10.1016/j.buildenv.2012.06.005
Vogel, J., Hagen, S., and Thomas, O. (2019). “Discovering blockchain for sustainable product-service systems to enhance the circular economy,” in 14th international conference on wirtschaftsinformatik, February 24-27, 2019, 1493–1507.
Yuan, H., and Shen, L. (2011). Trend of the research on construction and demolition waste management. Waste Manag. 31 (4), 670–679. doi:10.1016/j.wasman.2010.10.030
Keywords: Waste minimization strategies, Construction Waste Management (CWM), Building Information Management (BIM), Green Public Procurement (GPP), Most Economically Advantageous Tender (MEAT), Blockchain, Smart Contract
Citation: Pellegrini L, Campi S, Locatelli M, Pattini G, Di Giuda GM and Tagliabue LC (2020) Digital Transition and Waste Management in Architecture, Engineering, Construction, and Operations Industry. Front. Energy Res. 8:576462. doi: 10.3389/fenrg.2020.576462
Received: 26 June 2020; Accepted: 29 September 2020;
Published: 20 November 2020.
Edited by:
Massimiliano Manfren, University of Southampton, United KingdomReviewed by:
May M. Wu, Argonne National Laboratory (DOE), United StatesMarco Beccali, University of Palermo, Italy
Copyright © 2020 Pellegrini, Campi, Locatelli, Pattini, Di Giuda and Tagliabue. This is an open-access article distributed under the terms of the Creative Commons Attribution License (CC BY). The use, distribution or reproduction in other forums is permitted, provided the original author(s) and the copyright owner(s) are credited and that the original publication in this journal is cited, in accordance with accepted academic practice. No use, distribution or reproduction is permitted which does not comply with these terms.
*Correspondence: Lavinia Chiara Tagliabue, Y2hpYXJhLnRhZ2xpYWJ1ZUBwb2xpbWkuaXQ=