- 1Lee Kong Chian Faculty of Engineering and Science, UTAR, Kajang, Malaysia
- 2School of Engineering and The Built Environment, Edinburgh Napier University, Edinburgh, United Kingdom
- 3Department of Mechanical Engineering, University of Malaya, Kuala Lumpur, Malaysia
- 4Department of Forestry and Natural Resources, National I-Lan University, Yilan City, Taiwan
Global energy demand is rising due to the rapid development and adoption of new technologies in every sector. Hence, there is a need to introduce a clean energy source that does not cause damage to the environment. Aluminium-air battery with its high theoretical specific volumetric capacity is an exciting alternative for post-lithium energy storage and has been at the forefront of energy research for years. However, the conventional aqueous electrolyte-based aluminium-air battery with bulky liquid storage, parasitic corrosion of aluminium in contact with the electrolyte, and formation of a passive oxide or hydroxide layer has precluded its widespread application. In order to achieve successful simplification and cost-effectiveness, a novel idea of a polypropylene-based aluminium-air battery is proposed. In this work, a polypropylene-based aluminium-air battery was constructed using aluminium foil as an anode, carbon fiber cloth as an air-cathode, and Polypropylene and Kimwipes as the separator. The effects of the electrolyte concentration on the aluminium-air battery were investigated and analyzed using various discharge currents. The study showed that the performance of the polypropylene separator is better than that of the Kimwipes separator. The battery capacity is negatively correlated with the concentrations of the electrolyte. At a discharge current of 30 mA, the aluminium-air battery has a specific capacity of 375 mAh g−1 when 1 M of potassium hydroxide was used as electrolyte.
Introduction
Rapid growth of the world economy has led to an increase in energy demand in daily lives and industries. It is projected that the world energy consumption will grow by 50% between 2018 to 2050, particularly in the Asiatic region. On the other hand, global energy-related CO2 emissions will grow by 0.6% per year from 2018 to 2050. As a result, human-induced climate change is also increasing steadily. Hence, renewable energy sources are being explored to minimize the burning of fossil fuel and creation of environmental pollution. One of the alternative solutions is using electrochemical energy storage systems to replace conventional internal combustion engines to generate electricity for vehicles. There are several advantages associated with electrochemical energy storage systems on fuel-cell-powered vehicles, such as reductions in harmful emissions, less noise pollution, and reduced dependence on fossil fuels (Clark et al., 2018).
The primary energy source of Electrical Vehicles (EVs) is electrochemical energy storage systems such as lead-acid battery, Li-ion battery, NiCd, and NiMH. Among the various batteries used in EVs, the Li-ion battery with its high energy density (7,900 Wh/L) and power density (3,460 Wh/kg) is a popular choice (Clark et al., 2018). Apart from that, Li-ion battery has a longer cycle life and depth of discharge as compared to other types of energy storage systems (Abdin and Khalilpour, 2018). However, the Li-ion battery is very sensitive to operating temperatures and prone to thermal runaway (Tan et al., 2011). On the other hand, EVs equipped with a rechargeable battery will require the construction of a new charging facility. Fast charging of the electric vehicle during peak hours will certainly increase the electric load of the existing electricity networks. In addition, disposal of used Li-ion batteries is also one of the issues that remains unsolved. Hence, research on the energy storage system has been conducted to search for an alternative solution to replace the Li-ion battery; one of the potential solutions is using a metal-air battery.
Metal-air batteries with high energy density are projected as one of the clean energy solutions for the post-Li-ion battery era (Li and Lu, 2017). The operating principle of the metal-air batteries is very simple; the electrochemical reaction occurs when the battery consumes oxygen from the air at the cathode and forms hydroxide ion. At the anode, the metal being oxidized to metal oxide generates the electricity. There are various types of metal electrodes being used, such as zinc, aluminium, magnesium, iron, lithium (Xiang et al., 2020), and sodium (Jiang et al., 2018). Among various types of metal, aluminium is considered to be an attractive candidate because of its unique characteristics such as high specific energy, high conversion rate, low operating cost, good stealth performance, and it being environmentally friendly (Liu et al., 2017). Moreover, aluminium is the most abundant metal element in the world, and it is easy to handle, transport, and recycle through industrial treatment. Aluminium-air battery has the highest theoretical voltage and energy density among various types of batteries, which were recorded at 2.7 V and 8,100 Wh kg−1, respectively (Nestoridi et al., 2008; Schwarz, 2014). However, there are several drawbacks associated with the aluminium-air battery, such as the need to mechanically recharge the battery by replacing the aluminium. Additionally, parasitic corrosion of the anode will further affect the performance of the batteries (Zhang et al., 2018).
The performance of aluminium anode in the aluminium-air battery has been extensively studied worldwide by prominent researchers. Wang et al. set up an experiment to investigate the corrosion of aluminium anode in the aluminium-air battery. In this work, aluminium foil was used as the anode and sodium hydroxide (NaOH) was used as the electrolyte (Wang et al., 2013). The result showed that, as the concentration of the electrolyte increased, the utilization efficiency of the aluminium reduced. Besides, the aluminium anode can be infused with other metals to reduce the self-discharge of aluminium (Liu et al., 2017). Other than the aluminium anode factor, the electrolytes in the aluminium-air battery are also an important factor affecting the performance of the battery. Based on previous research, the alkaline electrolyte has shown remarkable results and works well with aluminium-air batteries, such as potassium hydroxide (KOH) and sodium hydroxide (NaOH), which can optimize the performance of aluminium-air batteries (Mori, 2020). In addition, the selection of the air cathode, anode, and electrolyte can affect the cycle life of the batteries (Pei et al., 2014; Xu et al., 2015). Despite all the advantages in the properties of aqueous electrolytes, it also faced some shortcomings, such as corrosion of the carbon-based air cathode which can occur due to the reaction of the highly concentrated alkaline electrolyte in the metal-air batteries. This can cause the electrolyte to change to a brown color from the oxidation of the carbon ion in the air cathode, resulting in the formation of carboxylic acids. Thus, reducing the pH of the electrolyte could be the solution to improve the metal-air battery performance. Sumboja et al. (2016) investigated the durability of zinc-air batteries using neutral salt and manganese oxide catalyst. It was found that the electrolytes with a pH value of 7 can stabilize and produce an acceptable result by reducing the occurrence of carbon corrosion in the air cathode. On top of that, a non-aqueous electrolyte is also one of the solutions to overcome the problem in the aqueous-based metal-air battery system. Other than that, alloying the aluminium anode may also help to improve battery performance. Ou et al. (2020) conducted an experiment by using pre-alloy LiAl alloy as the anode of the battery. It was found that capacity retention of about 79% was achieved in LiAl alloy as compared to 51% achieved by pristine Al foil. Wang and Tang (2020) applied artificial solid electrolyte interphase on the surface of the aluminium anode. The findings showed that the artificial solid electrolyte interphase layer is able to passivate the aluminium anode and prevent the aluminium anode from corroding.
The anode and cathode of the battery are usually separated by a porous separator which is one of the key elements in determining the effectiveness of the battery. The separator separates the anode and cathode to prevent short circuiting and allows the crossing of ions to the other side. The commonly used separators are produced from a polymer, such as olefin which has a low melting point. However, this type of thermally unstable separator could suffer thermal shrinkage when the operating temperature exceeds the melting point, which would further lead to thermal runaway and safety issues of the battery (Song et al., 2019). Therefore, the separator of the battery should have a good porosity property but not affect the thermal stability and mechanical strength at a certain level (Moon et al., 2019). To satisfy these requirements, a cellulose-based separator was introduced for the aluminium-air battery (Pan et al., 2018; Pan et al., 2019b). Pan et al. (2019a) studied the double-sided conductive separator using carbon nanotubes and cellulose nano-fiber composite layers coated with fiberglass. From the experiment, a more stable and longer cycle life has been observed due to the decrease in the local current density provided by the porous and conductive layer. It can be concluded that the double-sided conductive separator can be used for the aluminium-air battery and promote the development of the aluminium-air battery. However, the cellulose-based separator may face several drawbacks, such as swelling when immersed in an electrolyte causing strength weakening and a change of material properties as compared with polymer separators. Xie et al. (2019) investigated the tensile properties of a cellulose separator under the electrolyte-immersed condition and discovered that Young’s modulus of the separator is reduced and the expansion coefficient is increased. This further proved that the strength of the separator is weakening and swelling occurs in electrolyte-immersed conditions (Xie et al., 2019). Although the mechanical properties of the cellulose separator deteriorated in aqueous electrolyte, the swelling of cellulose separators will improve the performance of the separators as well as the electrochemical properties. Hence, the issues of strength weakening need to be overcome to produce a battery with longer life cycles.
Recently, a novel structure of aluminium-air batteries has been developed using a solid electrolyte. It is fabricated using water-absorbing polymers immersed in an alkaline solution to produce a semisolid gel. This method will simplify the battery structure design and eliminate the electrolyte leakage problems (Wang et al., 2019b). Many researchers used a gelling agent as a corrosion inhibitor in the alkaline electrolyte. This will enhance the performance of the solid-state aluminium-air and generate a high power output. However, most of the solid electrolytes exist in bulk and possess rigid physical properties which reduce the energy density of the battery. Therefore, it is necessary to search for a more suitable solid electrolyte for the aluminium-air battery (Zhang et al., 2014; Pino et al., 2015; Di Palma et al., 2017). In view of this, Wang et al. (2019a) introduced the paper-based solid electrolyte to produce low-cost aluminium-air batteries. It was found that a paper-based solid electrolyte aluminium-air battery with mechanical rechargeable capability can power a mini watt device. The battery is capable of producing a power density of 21 mW cm−2 with a specific capacity of 1,273 mAh g−1. By connecting the batteries in series, it can form a battery pack with open circuit voltage of 13.2 V (Wang et al., 2019a). The power output is comparable with the studies from Liu et al. (2016) and Xu et al. (2016) which showed 254.6 mAh g−1 and 935 mAh g−1, respectively. Avoundjian et al. (2017) designed a small paper-based aluminium battery that was only 9 cm2 in size. This small battery can generate a power of 3 mW. By connecting three batteries in series, it can be used to power LED lights and flashlights. On the other hand, Katsoufis et al. analyzed the performance of thin-film aluminium-air battery (Katsoufis et al., 2020). In the study, a maximum power of 28 mW cm−2 is generated by the thin-film aluminium-air battery with 1 cm−2 of the aluminium anode. Shen et al. investigated a paper-based microfluidic aluminium-air battery and measured its electrical performance (Shen et al., 2019). It was found that the battery has an energy density of 2,900 Wh kg−1 and specific capacity of 2,750 Ah kg−1, which is better than that of the non-fluidic configuration battery. All these studies suggested that a paper-based aluminium-air battery is well suitable to be applied in miniature applications.
In view of the above, a low-cost polypropylene-based aluminium-air battery is proposed in this study. Compared to the conventional aqueous aluminium-air battery system, a polypropylene pad is used as a natural microfluidic channel to deliver the electrolyte through capillary action. This design enables the compact design of the aluminium-air battery and reduces the self-corrosion of aluminium. Furthermore, the effect of alkaline electrolyte concentrations is investigated. The performance of the polypropylene-based aluminium-air battery is then compared with the paper-based aluminium-air battery using Kimwipes. Lastly, SEM and XRD analyses are performed to examine the microstructure and composition change on the aluminium anode. The rest of the paper is organized as follows: Section Methodology describes the operation of the aluminium-air battery, battery design, and experimental setup. Following that, Section Results and Discussion presents the performance of the aluminium-air under different concentrations of the alkaline solutions and discharge currents. Finally, conclusions are drawn in Section Conclusion based on the findings obtained.
Methodology
Discharge Mechanism of Al-Air Battery
The essential components in the aluminium-air battery are the aluminium anode, air cathode, separator, and electrolyte. A separator is used to isolate the anode and cathode to prevent short circuiting. The oxygen reduction reaction (ORR) is the main cathodic reaction at the air cathode. Oxygen is reduced in the alkaline medium to form hydroxyl ions (OH−) as shown in Eq. 1. On the other hand, the aluminium anode will react with OH− to produce Al (OH)4− and electricity is generated (Eq. 2). The overall reaction in the Aluminium-air battery is shown in Eq. 3. There is another reaction taking place in conjunction with the reaction at the anode side, which is known as parasitic loss. This reaction will consume electrons as a side reaction to generate hydrogen, as shown in Eq. 4. A parasitic reaction is a critical issue for aqueous-based aluminium-air batteries that have infinite contact with the aluminium anode and electrolyte. The corrosion of the aluminium anode will seriously affect the efficiency and performance of the battery.
Cathode reaction:
Anode reaction:
Overall reaction:
Parasitic reaction at anode:
Al-Air Battery Design
The design of the polypropylene-based aluminium-air battery is illustrated in Figure 1. The battery reaction area is about 5 cm × 5 cm. The battery consists of four major parts: two acrylic plates used as the enclosure of the aluminium-air battery, an anode which is made of aluminium foil (98.2% Al and 0.01 mm thick), an air cathode which is made of carbon fiber cloth (0.167 mm), and the separator of the battery which is made of a polypropylene absorbent pad (100% Polypropylene, 2 mm thick, Crisben). An acrylic-based material is chosen as the enclosure of the battery due to its inert properties that do not affect the reaction of the aluminium-air battery. An air-breathing window of 5 cm × 5 cm was cut on the air cathode side of the enclosure to facilitate oxygen transport. Wire mesh was cut into the desired size to provide support for the air cathode and ensure tight contact of the air cathode with the separator. Potassium hydroxide (KOH) was used as the electrolyte in this study with concentrations varying from 1 to 3 M. The electrolyte is prepared by dissolving the KOH pellet into deionized water and 1.5 ml of KOH solution is injected into the polypropylene separator. The aluminium foil was also cut into the reaction area of 5 cm × 5 cm and inserted into the enclosure. The advantages of this type of battery are its low-cost and simple fabrication process. Moreover, the parasitic reaction at the anode can be controlled by limiting the amount of electrolytes present in the battery and does not require a bulky electrolyte recirculation system.
Experimental Analysis
Three different concentrations of KOH electrolyte—1, 2, and 3 M—were prepared in this study. 1.5 ml of electrolyte was dropped on the absorbent pad (polypropylene) to activate the battery. The battery open circuit was recorded when the reaction area was fully wetted with the electrolyte. An electrochemical workstation (ZIVE SP1) was used to analyze the battery. Linear sweep voltammetry was used to obtain the polarization curve of the battery. A scan rate of 5 mV s−1 was used to sweep the open-circuit voltage to 0 V of the battery. Characterization of the performance of the Aluminium-air battery was conducted by discharging the battery under a constant current. Various discharge currents in the range of 10 mA to 50 mA were used to discharge the battery with various concentrations of KOH electrolyte.
Next, Kimwipes was used to replace polypropylene as the separator. The performance of the paper-based aluminium-air battery was recorded and compared with a polypropylene-based aluminium-air battery. All tests were repeated three times to obtain an average value. All the tests were conducted under room temperature of 25°C. After the cyclic performance test, the battery was disassembled to measure the weight loss of the aluminium anode. Then, scanning electron microscope was used to observe the surface morphologies of the anode and separator before and after the experiment. In addition, X-Ray diffraction analysis was also conducted; the scan range was set from 10 to 90 degrees with a scan speed of 2 degrees per minute. The XRD patterns were then interpreted using X’Pert HighScore Plus.
A wettability test was conducted to analyze the hydrophobic properties of the separator by dropping 1, 2, and 3 M KOH solution on the surface of the separator. The contact angle was measured to study the wettability performance. ImageJ was used to measure the contact angle. Figure 2 showed the contact angle of the separator. The results showed that the contact angle tends to increase as the concentration of electrolyte increases from 1 to 3 M. The contact angles were 70.1°, 76.5°, and 97.6° for 1, 2, and 3 M respectively. This suggested that, as the concentration increases, the hydrophobic properties of the separator improves. However, only the 3 M electrolyte achieved true hydrophobic potential as the contact angle was greater than 90° (Doshi et al., 2018). The hydrophobicity properties of the separator can limit the flow of water molecules from the cathode to the anode which helps to prevent corrosion.
Results and Discussion
Activation Test
An activation test was performed before a full-scale experiment was conducted. Activation tests are important because they can help to improve the performance of the battery. In the activation test, a multiple polarization test for the battery was conducted. In each polarization test, the carbon fibre cloth remained unchanged while the Al anode and the polypropylene were changed. The concentration of KOH used is 1 M. Figure 3 shows the polarization test for the study. As shown in Figure 3, the battery performance improved each subsequent test. At 10 cycles of the polarization test, the maximum power achieved was 4 mW. This value was improved to 7.3 mW at 20 cycles of the polarization test. The test was continued until the maximum power increased to 25.6 mW at 30 cycles of the polarization test. There was a sharp increase in power density after 30 cycles of the activation test. However, further continuing the experiment to 40 cycles did not show a significant improvement as the power density reached 26.9 mW at 40 cycles. There was about 6.7 times improvement in power density when comparing the test result at 10 cycles and 40 cycles. There was also no significant change of the open-circuit voltage of the battery. The open-circuit voltage remained constant at 1.45 V for all the polarization tests. The improvement in power density suggested that an activation test is necessary to improve the performance of the battery. This improvement occurs mainly on the air-cathode. As the polarization test continued, the PTFE coating at the carbon fibre cloth was removed due to the electrochemical process as suggested in the work by Wang et al. (2019a). Furthermore, the study also suggested that a hydrophilic cathode is favourable to enhance the liquid-electrode contact and increase the performance of the battery.
Battery Performance Under the 1 M of KOH
The performance of the aluminium-air battery was investigated with different discharge currents and concentrations of KOH electrolyte. The Aluminium-air battery was tested until the voltage of the battery dropped to 0 V to capture the battery capacity. The discharge currents used in this study were 10, 20, 30, and 50 mA. Figure 4 shows the discharge performance of the Aluminium-air battery with 1 M of KOH. It indicated that the battery discharge with 10 mA took a longer time to become completely exhausted. It could last for about 1 h and 36 min before the battery dried out. The discharge duration is inversely proportional to the discharge current. At a discharge current of 50 mA, the battery could last for about 20 min only. During the discharge process, the aluminium and hydroxyl ions will be consumed and lead to a reduction of battery voltage. When the remaining hydroxyl and aluminium ions are fully consumed and unable to fulfill the required discharging current, the battery voltage will drop to 0 V. This phenomenon is more obvious when a high current is used to discharge the battery and leads to a quicker drop in battery voltage. Based on the result, an aluminium-air battery with a small current load will produce a higher initial cell voltage and longer discharge period as compared to high discharge current loads. The initial voltage achieved by 10, 20, 30, and 50 mA of discharge current is about 1.1, 1.0, 0.8, and 0.3 V, respectively. This is because the electrochemical reaction at the battery is positively correlated with the discharge current and more ions are involved in the reaction. Rapid consumption of ions available in the battery will cause a sudden drop in the battery voltage. Therefore, increasing the amount of electrolyte present in the battery or increasing the size of the aluminium anode can further increase the capacity of the battery and prolong the discharge period. Besides, increasing the thickness of the polypropylene is directly proportional to increasing the amount of electrolyte stored in the polypropylene separator. Using a better electrocatalyst to enhance the oxygen reduction reaction will also help to improve the performance of the battery.
Battery Performance with Different Concentrations of Electrolyte
The performance of the battery discharging characteristics were compared with different concentrations of electrolytes. In this study, the discharge current was fixed at 20 mA. Strong alkaline solution will certainly reduce the performance of the battery. As shown in Figure 5, as the concentration of the electrolyte increases, the capacity of the battery is reduced. For high concentrations of KOH, the battery takes a shorter time to discharge. The discharge time was about 28 min for 3 M of electrolyte. On the other hand, the discharge time was improved to about 59 and 64 min for 2 and 1 M of electrolyte, respectively. The concentration of electrolyte is negatively correlated with the discharge performance of the aluminium-air battery. This observation is coherent with the work by Mohammad (2008) The reduction of discharge time is due to the corrosion rate of the battery. As the concentration of the electrolyte increases, the concentration of OH− ions increased as well. This will favor the formation of aluminium hydroxide, Al (OH)3, and hydrogen as a by-product, as shown in Eq. 4. Most of the aluminium at the anode was consumed in the side reaction rather than used in the electrochemical reaction. As the discharging process continues, the aluminium will be covered by the aluminium hydroxide during the electrochemical process and reduce the battery performance. The evidence of the formation of aluminium hydroxide will be presented in Section XRD and SEM Results. Hence, using a high concentration of electrolytes will increase the frequency of replacing the anode in the aluminium-air battery.

FIGURE 5. Discharge performance of Al-air battery with different KOH concentration with discharge current of 20 mA.
Although a high concentration limits the discharge capacity of the aluminium-air battery, the voltage stabilizes at a higher value for high concentrations of electrolytes. At 20 mA, the voltage stabilized at 0.8 V when 3 M electrolyte was used in the study, whereas it dropped to about 0.5 V when 1 M of electrolyte was used. This is because a strong alkaline has better ionic conductivity and facilitates better ionic movement. Higher amounts of OH− ions are available in the electrolyte solution and react with the aluminium at the anode to produce electricity. It also helps to reduce the resistance of ion movement in the separator. Hence, there exists a compromise between the concentrations of electrolyte, discharge capacity, and operating voltage of the aluminium-air battery. However, increasing the concentration of the electrolyte does not affect the open-circuit voltage of the battery. As shown in Figure 5, the open-circuit voltage tends to remain the same at about 1.1 V for 1, 2, and 3 M of KOH whereas the effect of concentration of the electrolyte on open circuit voltage is insignificant.
Specific Discharge Capacity of Aluminium-Air Battery
Figure 6 showed the specific capacity of the aluminium-air battery for different concentrations and discharge currents. As shown in the figure, 1 M of the electrolyte always showed the highest specific capacity for discharge currents of 10, 20, 30, and 50 mA. Due to the low corrosion rate of 1 M electrolyte, most of the aluminium was consumed in the electrochemical reaction rather than the parastitic loss in the side reaction. Hence, the specific capacity increased as the anode utilization improved. Specific discharge capacities of 228 and 375 mAh g−1 were obtained for discharge currents of 10 and 30 mA respectively. However, this improvement is not observed at a discharge current of 50 mA. The specific capacity for 1 M electrolyte tends to reduce at 50 mA. This is due to the limitation of OH− ions in the 1 M electrolyte. There was insufficient OH− supplied to the anode and, hence, the electrochemical reaction reduced and led to a drop in specific capacity.
In 2 and 3 M electrolytes, the specific capacities were always lower than 1 M. As the concentration increases, the corrosion rate increases which leads to poor anode utilization. Some of the aluminium was consumed by reacting with OH− ions to form aluminium hydroxide, causing a reduction in anode utilization which led to the specific capacities dropping. 3 M electrolyte always showed the lowest specific capacity. This suggested that the effect of corrosion is very serious for the battery using 3 M of electrolyte.
Among all the tests, the best performance was achieved by 1 M electrolyte at a discharge capacity of 30 mA in which a specific capacity of 375 mAh g−1 was recorded. The performance is better than previous research on the aluminium-air battery: 65 mAh g−1 (Elia et al., 2017), 239 mAh g−1 (Yu et al., 2018), and 350 mAh g−1 (Wang et al., 2016).
Performance of Polypropylene Against a Paper-Based Separator
This study compared the discharge performance of the aluminium-air battery using a polypropylene separator and paper-based separator-Kimwipes. In this study, 1 M KOH was used as the electrolyte. Kimwipes was cut into a square with 5 cm × 5 cm and used as the separator in the aluminium-air battery. From the results shown in Figure 7, it can be seen that the polypropylene separator performed better than the paper-based separator for all discharge currents. At a discharge current of 10 mA, the polypropylene separator maintained a discharge duration of about 97 min while the paper-based separator was only able to maintain a discharge duration of about 33 min. There was about a 3 times improvement for the polypropylene separator as compared to the paper-based separator. There was a sharp drop of voltage in the paper-based aluminium-air battery. At 10 mA, the open circuit voltage dropped from 1.18 V to about 0.82 V, and maintained a constant discharge voltage at about 0.8 V. On the other hand, the polypropylene-based separator showed an initial voltage drop from 1.1 to 0.9 V and was able to provide a constant discharge voltage of 0.9 V before a sudden drop in voltage due to the electrolyte drying out. This suggested that the electrical performance of the polypropylene separator is better than the kimwipes. At a higher discharge current of 20 and 30 mA, a paper-based separator does not produce a good stability in voltage output. The voltage tends to fluctuate, as shown in Figure 7. The discharge duration also tends to reduce as the discharge current increases. At 30 mA, the paper-based aluminium-air battery can only survive for 18 min. There is no obvious constant discharge voltage plateau in the discharging curve. On the other hand, using polypropylene as a separator can achieve a discharge duration of 52 min while keeping a constant discharge voltage of about 0.4 V. The discharge duration was improved 3-fold.
The performance of the paper-based aluminium-air battery at a discharge current of 20 mA is similar to the performance of the polypropylene-based aluminium-air battery at a discharge current of 30 mA. Both the batteries showed a constant discharge voltage of 0.4 V. However, the discharge duration of the paper-based aluminium-air battery was about 28 min and shorter than the polypropylene-based aluminium-air battery which was recorded at 52 min. The discharge performance indicates that the polypropylene separator was able to provide a better battery performance at a higher discharge current as compared to the paper-based separator at a lower discharge current.
Besides that, the polypropylene separator did not suffer a severe sharp drop in voltage as compared to kimwipes for all discharge currents. The sharp drop in the initial voltage of the kimwipes separator will produce a lower discharge voltage. The effects of fluctuation in voltage and the large drop in initial voltage suggested that kimwipes does not provide a stable electrical performance. This may be due to the higher internal resistance of the paper-based separator. A polypropylene separator can provide a stable discharge performance for a longer period of time. Although kimwipes possess a better chemical absorbent property than the polypropylene, it does not show a good performance when used as a separator in aluminium-air battery. This may be due to the physical microstructure of the Kimwipes. Kimwipes is a cellulose-based material while polypropylene is a fiber-based material. When a cellulose-based material is used as a separator in the battery, it can cause swelling when immersed in the electrolyte. This will alter the material properties of the separator. Nevertheless, the geometry of the fiber-based polypropylene does not distort when it is immersed in the electrolyte. Hence, the polypropylene separator will produce a better battery performance. This observation agrees with the work by Xie et al. (2019).
Weight of the Aluminium Foil
During the electrochemical reaction, an aluminium anode was consumed to generate energy and aluminium hydroxide was produced as a by-product. Measuring the weight of the aluminium anode before and after the electrochemical process can help to understand the corrosion rate of the aluminium anode. Since the density of the aluminium hydroxide (2.42 g cm−3) is lighter than that of the aluminium (2.70 g cm−3), the weight loss can be attributed to the formation of aluminium hydroxide during the electrochemical process. The corrosion rate is positively correlated with the weight loss of the aluminium anode. The initial weight of the aluminium anode was measured before the experiment and after the discharge process. Table 1 shows the weight of the aluminium anode before and after the experiment with 12.50 mA of discharging current.
Based on the difference between the weights of the aluminium anode, it was shown that more aluminium is consumed as the concentration of KOH is increased. This is due to the large amount of OH− ion present in the electrolyte, promoting the parasitic reaction and causing severe corrosion on the aluminium anode. In addition, this also suggested that more aluminium hydroxide is formed during the process. The aluminium hydroxide will block the surface of the aluminium anode, preventing the pristine aluminium from involving in the electrochemical process. The removal of aluminium hydroxide is necessary before fresh aluminium is ready for electrochemical reaction again. As a result, there is a need to replace aluminium anodes more frequently when higher electrolyte concentrations are used.
XRD and SEM Results
SEM was performed to characterize the aluminium anode surface morphology. The change of the microstructure before and after the experiment was observed. The physical observation of the aluminium anode after the experiment for different concentrations of electrolytes are shown in Figure 8. The aluminium anode tends to undergo corrosion after the discharge test. The severity of the corrosion increases as the concentration of the electrolyte is increased. Powder was observed in the aluminium anode with 2 and 3 M of electrolyte. For 1 M of electrolyte, no obvious powdery structure was formed after the discharge process.
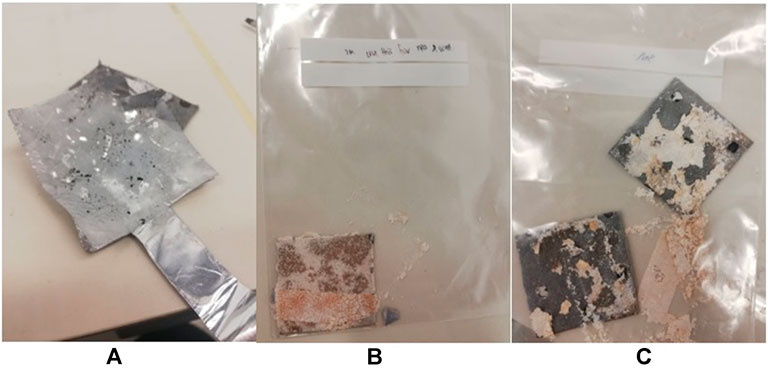
FIGURE 8. Images of aluminum anode after more than 2 hours of discharging with 1 M (A), 2M (B), and 3M (C) of KOH concentration respectively.
Figure 9 shows the SEM images of the aluminium anode after discharging the battery for more than 2 h with different concentrations of KOH. For the aluminium anode with 1 M of KOH, there were minor changes in the microstructure. Pits were observed and the surfaces tend to be coarse. This showed that aluminium is consumed and there is no obvious formation of aluminium hydroxide. This observation was further analyzed using XRD analysis. The XRD pattern of the aluminium anode after testing with 1 M of KOH solution is shown in Figure 10. The XRD pattern indicated that aluminium was the sole candidate in the test, hence it can be concluded that corrosion of the aluminium anode is not severe and formation of aluminium hydroxide is not apparent.
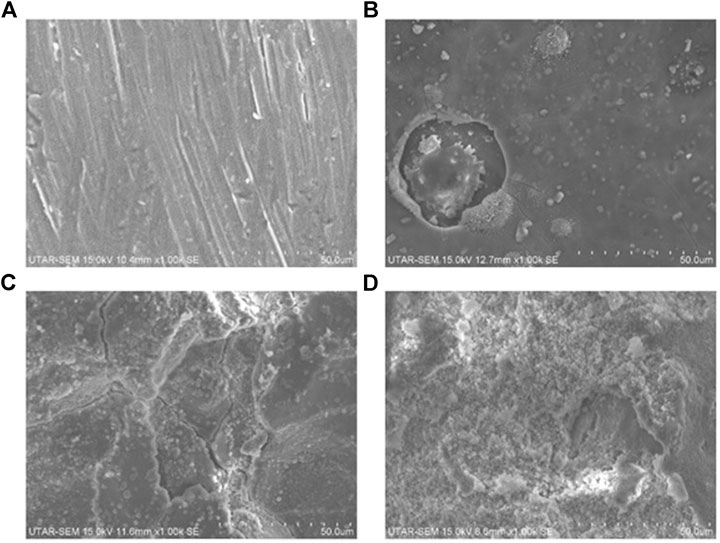
FIGURE 9. SEM images 1000x magnification of (A) aluminium before discharging (B) aluminum after discharging over 2 hours using 1 M KOH (C) aluminum after discharging over 2 hours using 2 M KOH (D) aluminium.
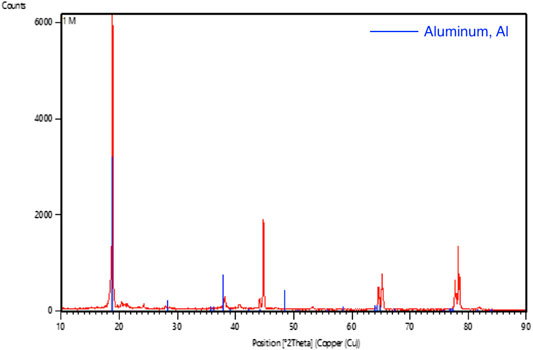
FIGURE 10. Graphic comparing the XRD pattern (red line) on aluminum foil after tested with 1 M of KOH solution with the standard aluminum XRD pattern (blue line).
For the study involving 2 and 3 M of KOH, it was observed that the aluminium anode undergoes severe corrosion as shown in Figure 8. Powdery structure was formed on the surface of the aluminium anode. This can be proved by SEM and XRD tests. Figure 9 shows the SEM images of the aluminium anode after the test and that the surface of the aluminium anode was severely damage. The surface of the aluminium anode was coarse and there were impurities formed. The formation of the impurities was more severe for the battery using 3 M of KOH electrolyte as compared to 2 M of KOH electrolyte. Hence, a high concentration of KOH promotes the growth of impurity substances. XRD was then conducted to identify the content of the impurity’s substance formed on the surface.
The XRD pattern of the aluminium anode after testing with 2 and 3 M of KOH electrolyte were shown in Figures 11, 12, respectively. In the analysis, it was found that aluminium hydroxide is the main component in the powder formed after the discharging test, suggesting that aluminium was consumed and reacted with hydroxyl to form aluminium hydroxide. High concentrations of KOH will accelerate the corrosion of the aluminium anode.
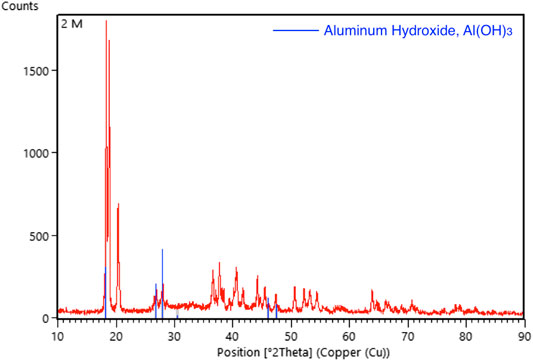
FIGURE 11. Graphic comparing the XRD pattern (red line) of aluminum foil after tested with 2 M of KOH solution with the standard aluminum hydroxide XRD pattern (blue line).
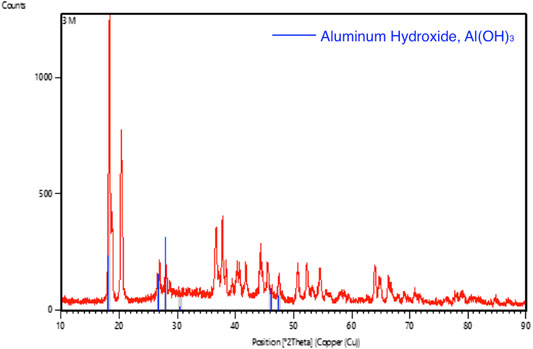
FIGURE 12. Graphic comparing the XRD pattern (red line) of aluminum foil after tested with 3 M of KOH solution with the standard aluminum hydroxide XRD pattern (blue line).
Conclusion
The performance of the polypropylene separator and paper-based separator in the aluminium-air battery was benchmarked with different discharge currents and different concentrations of KOH electrolyte. An aluminium-air battery was designed and constructed using aluminium foil as the anode, carbon fiber cloth as the air cathode, polypropylene pad and Kimwipes as the separator, and potassium hydroxide (KOH) as the electrolyte. An open circuit test was conducted and the results showed that the Aluminium-air battery with a polypropylene separator is able to generate an open circuit voltage of 1.1 V. The concentration of electrolytes used in the separator is important in determining the performance of the battery. High concentration will cause a higher corrosion rate at the aluminium anode which deteriorates the performance of the battery. The best specific discharge capacity for the battery equipped with a polypropylene separator is about 375 mAh g−1 for 30 mA of discharge current at 1 M electrolyte. The study also reveals that polypropylene is a suitable candidate to be used as a separator as compared to Kimwipes. Compared to a paper-based separator, a fiber-based separator is more suitable for the aluminium-air battery. Extensive research is required to promote the polypropylene-based separator as one of the key solutions in future energy storage systems.
Data Availability Statement
The original contributions presented in the study are included in the article/Supplementary Material, further inquiries can be directed to the corresponding author.
Author Contributions
All authors listed have made a substantial, direct, and intellectual contribution to the work and approved it for publication.
Funding
This work is supported by Fundamental Research Grant Scheme (Grant No. FRGS/1/2018/TK07/UTAR/02/4) from Ministry of Higher Education Malaysia and University Malaya RU grant (Grant No. ST024-2019).
Conflict of Interest
The authors declare that the research was conducted in the absence of any commercial or financial relationships that could be construed as a potential conflict of interest.
Acknowledgments
We would like to thank Nor Haziq Naquiddin for their help in testing some of the battery performances.
References
Abdin, Z., and Khalilpour, K. R. (2018). “Single and polystorage technologies for renewable-based hybrid energy systems,” in Polygeneration with polystorage: for Chemical and energy hubs. (Amsterdam, Netherlands: Elsevier Sciences), doi:10.1016/B978-0-12-813306-4.00004-5
Avoundjian, A., Galvan, V., and Gomez, F. A. (2017). An inexpensive paper-based aluminum-air battery. Micromachines 8 (7), 222. doi:10.3390/mi8070222
Clark, S., Latz, A., and Horstmann, B. (2018). A review of model-based design tools for metal-air batteries. Batteries 4, 5. doi:10.3390/batteries4010005
Di Palma, T. M., Migliardini, F., Caputo, D., and Corbo, P. (2017). Xanthan and κ-carrageenan based alkaline hydrogels as electrolytes for Al/air batteries. Carbohydr. Polym. 157, 122. doi:10.1016/j.carbpol.2016.09.076
Doshi, B., Sillanpää, M., and Kalliola, S. (2018). A review of bio-based materials for oil spill treatment. Water Res. 135, 262. doi:10.1016/j.watres.2018.02.034
Elia, G. A., Hasa, I., Greco, G., Diemant, T., Marquardt, K., Hoeppner, K., et al. (2017). Insights into the reversibility of aluminum graphite batteries. J. Mater. Chem. A. 5, 9682. doi:10.1039/c7ta01018d
Jiang, C., Fang, Y., Zhang, W., Song, X., Lang, J., Shi, L., et al. (2018). A multi-ion strategy towards rechargeable sodium-ion full batteries with high working voltage and rate capability. Angew. Chem. Int. Ed. 57, 16370. doi:10.1002/anie.201810575
Katsoufis, P., Katsaiti, M., Mourelas, C., Andrade, T. S., Dracopoulos, V., Politis, C., et al. (2020). Study of a thin film aluminum-air battery. Energies 13, 1447. doi:10.3390/en13061447
Li, Y., and Lu, J. (2017). Metal-air batteries: will they Be the future electrochemical energy storage device of choice? ACS Energ. Lett. 2, 1370. doi:10.1021/acsenergylett.7b00119
Liu, Y., Li, J., Li, W., Li, Y., Zhan, F., Tang, H., et al. (2016). Exploring the nitrogen species of nitrogen doped graphene as electrocatalysts for oxygen reduction reaction in Al-air batteries. Int. J. Hydrogen Energ. 41, 10354. doi:10.1016/j.ijhydene.2015.10.109
Liu, Y., Sun, Q., Li, W., Adair, K. R., Li, J., and Sun, X. (2017). A comprehensive review on recent progress in aluminum-air batteries. Green. Energ. Environ. 2, 246. doi:10.1016/j.gee.2017.06.006
Mohammad, A. A. (2008). Electrochemical properties of aluminum anodes in gel electrolyte-based aluminum-air batteries. Corrosion Sci. 50, 3475–3479. doi:10.1016/j.corsci.2008.09.001
Moon, J., Jeong, J. Y., Kim, J. I., Kim, S., and Park, J. H. (2019). An ultrathin inorganic-organic hybrid layer on commercial polymer separators for advanced lithium-ion batteries. J. Power Sourc. 416, 89. doi:10.1016/j.jpowsour.2019.01.075
Mori, R. (2020). Recent developments for aluminum-air batteries. Electrochem. Energ. Rev. 3, 344–369. doi:10.1007/s41918-020-00065-4
Nestoridi, M., Pletcher, D., Wood, R. J. K., Wang, S., Jones, R. L., Stokes, K. R., et al. (2008). The study of aluminium anodes for high power density Al/air batteries with brine electrolytes. J. Power Sourc. 178, 445. doi:10.1016/j.jpowsour.2007.11.108
Ou, X., Zhang, G., Zhang, S., Tong, X., and Tang, Y. (2020). Simultaneously pre-alloying and artificial solid electrolyte interface towards highly stable aluminum anode for high-performance Li hybrid capacitor. Energ. Storage Mater. 28, 357. doi:10.1016/j.ensm.2020.03.021
Pan, R., Sun, R., Wang, Z., Lindh, J., Edström, K., Strømme, M., et al. (2019a). Double-sided conductive separators for lithium-metal batteries. Energ. Storage Mater. 21, 464. doi:10.1016/j.ensm.2019.06.025
Pan, R., Sun, R., Wang, Z., Lindh, J., Edström, K., Strømme, M., et al. (2019b). Sandwich-structured nano/micro fiber-based separators for lithium metal batteries. Nano Ener. 55, 316. doi:10.1016/j.nanoen.2018.11.005
Pan, R., Xu, X., Sun, R., Wang, Z., Lindh, J., Edström, K., et al. (2018). Nanocellulose modified polyethylene separators for lithium metal batteries. Small 14, 1704371. doi:10.1002/smll.201704371
Pei, P., Wang, K., and Ma, Z. (2014). Technologies for extending zinc-air battery’s cyclelife: a review. Appl. Energ. 128, 315. doi:10.1016/j.apenergy.2014.04.095
Pino, M., Chacón, J., Fatás, E., and Ocón, P. (2015). Performance of commercial aluminium alloys as anodes in gelled electrolyte aluminium-air batteries. J. Power Sourc. 299, 195. doi:10.1016/j.jpowsour.2015.08.088
Schwarz, H. G. (2014). “Aluminum production and energy,” in Encyclopedia of Energy. (Amsterdam, Netherlands: Elsevier Sciences), doi:10.1016/B0-12-176480-X/00372-7
Shen, L. L., Zhang, G. R., Biesalski, M., and Etzold, B. J. M. (2019). Paper-based microfluidic aluminum-air batteries: toward next-generation miniaturized power supply. Lab. Chip. 19, 3438. doi:10.1039/c9lc00574a
Song, Q., Li, A., Shi, L., Qian, C., Feric, T. G., Fu, Y., et al. (2019). Thermally stable, nano-porous and eco-friendly sodium alginate/attapulgite separator for lithium-ion batteries. Energ. Storage Mater. 22, 48. doi:10.1016/j.ensm.2019.06.033
Sumboja, A., Ge, X., Zheng, G., Goh, F. W. T., Hor, T. S. A., Zong, Y., et al. (2016). Durable rechargeable zinc-air batteries with neutral electrolyte and manganese oxide catalyst. J. Power Sourc. 332, 330. doi:10.1016/j.jpowsour.2016.09.142
Tan, Y. K., Mao, J. C., and Tseng, K. J. (2011). “Modelling of battery temperature effect on electrical characteristics of Li-ion battery in hybrid electric vehicle,” in Proceedings of the international conference on power electronics and drive systems, Singapore, December 5–8, 2011. doi:10.1109/PEDS.2011.6147318
Wang, H., and Tang, Y. (2020). Artificial solid electrolyte interphase acting as “Armor” to protect the anode materials for high-performance lithium-ion battery. Chem. Res. Chin. Univ. 36, 402. doi:10.1007/s40242-020-0091-5
Wang, L., Wang, W., Yang, G., Liu, D., Xuan, J., Wang, H., et al. (2013). A hybrid aluminum/hydrogen/air cell system. Int. J. Hydrogen Energ. 38, 14801. doi:10.1016/j.ijhydene.2013.09.036
Wang, S., Yu, S., Tu, J., Wang, J., Tian, D., Liu, Y., et al. (2016). A novel aluminum-ion battery: Al/AlCl3-[EMIm]Cl/Ni3S2@Graphene. Adv. Energ. Mater. 6, 1600137. doi:10.1002/aenm.201600137
Wang, Y., Kwok, H. Y. H., Pan, W., Zhang, H., Lu, X., and Leung, D. Y. C. (2019a). Parametric study and optimization of a low-cost paper-based Al-air battery with corrosion inhibition ability. Appl. Energ. 251, 113342. doi:10.1016/j.apenergy.2019.113342
Wang, Y., Pan, W., Kwok, H., Lu, X., and Leung, D. Y. (2019b). Low-cost Al-air batteries with paper-based solid electrolyte. Energ. Proced. 158, 522. doi:10.1016/j.egypro.2019.01.146
Xiang, L., Ou, X., Wang, X., Zhou, Z., Li, X., and Tang, Y. (2020). Highly concentrated electrolyte towards enhanced energy density and cycling life of dual‐ion battery. Angew. Chem. Int. Ed. 59, 17924. doi:10.1002/anie.202006595
Xie, W., Liu, W., Dang, Y., Tang, A., Deng, T., and Qiu, W. (2019). Investigation on electrolyte-immersed properties of lithium-ion battery cellulose separator through multi-scale method. J. Power Sourc. 417, 150. doi:10.1016/j.jpowsour.2019.02.002
Xu, M., Ivey, D. G., Xie, Z., and Qu, W. (2015). Rechargeable Zn-air batteries: progress in electrolyte development and cell configuration advancement. J. Power Sourc. 283, 358. doi:10.1016/j.jpowsour.2015.02.114
Xu, Y., Zhao, Y., Ren, J., Zhang, Y., and Peng, H. (2016). An all-solid-state fiber-shaped aluminum-air battery with flexibility, stretchability, and high electrochemical performance. Angew. Chem. Int. Ed. Engl. 55, 7979. doi:10.1002/anie.201601804
Yu, Y., Chen, M., Wang, S., Hill, C., Joshi, P., Kuruganti, T., et al. (2018). Laser sintering of printed anodes for Al-air batteries. J. Electrochem. Soc. 165, A584. doi:10.1149/2.0811803jes
Zhang, Y., Liu, S., Ji, Y., Ma, J., and Yu, H. (2018). Emerging nonaqueous aluminum-ion batteries: challenges, status, and perspectives. Adv. Mater. 30, 1706310. doi:10.1002/adma.201706310
Keywords: battery, aluminum-air battery, polypropylene, separator, alkaline solution
Citation: Tan WC, Saw LH, Yew MC, Sun D, Cai Z, Chong WT and Kuo P-Y (2021) Analysis of the Polypropylene-Based Aluminium-Air Battery. Front. Energy Res. 9:599846. doi: 10.3389/fenrg.2021.599846
Received: 28 August 2020; Accepted: 19 January 2021;
Published: 03 March 2021.
Edited by:
Joni Jupesta, Research Institute of Innovative Technology for the Earth, JapanReviewed by:
Liqiang Mai, Wuhan University of Technology, ChinaYongbing Tang, Chinese Academy of Sciences (CAS), China
Copyright © 2021 Tan, Saw, Yew, Sun, Cai, Chong and Kuo. This is an open-access article distributed under the terms of the Creative Commons Attribution License (CC BY). The use, distribution or reproduction in other forums is permitted, provided the original author(s) and the copyright owner(s) are credited and that the original publication in this journal is cited, in accordance with accepted academic practice. No use, distribution or reproduction is permitted which does not comply with these terms.
*Correspondence: Lip Huat Saw, c2F3bGhAdXRhci5lZHUubXk=, YmVybmFyZHNhdzgxQHlhaG9vLmNvbQ==