- Department of Materials Science and Engineering, Stanford University, Stanford, CA, United States
We report high throughput open-air processing techniques for the scalable production of all device and barrier layers for perovskite photovoltaics (PV). This work discusses and resolves some of the most formidable barriers to module-level scaling that the perovskite community has been facing. Our advanced technoeconomic manufacturing analysis indicates that vacuum-based processes with high capital expenditures (CapEx) and low throughputs dominate the cost of production. Open-air fabrication methods offer low CapEx routes to manufacturing, but achieving reproducibility in ambient conditions with varying relative humidity has been a persistent challenge. The use of rapid processing methods with plasma curing to convert films from the solution-state enables reproducibility, moisture immunity, and the highest perovskite PV efficiency produced in open-air. These methods are readily translatable to in-line processing where layers are sequentially deposited without the need for lengthy post-annealing steps that reduce throughput and involve additional equipment. Significant progress is demonstrated in reduced manufacturing costs as perovskites contend as a commercially viable next-generation thin film PV technology.
Introduction
Organic–inorganic metal halide perovskites are at a crossroads with commercialization due to compatibility with solution processing and remarkable gains in power conversion efficiency (PCE) up to 25.5% (National Renewable Energy Laboratory, 2019) on lab-scale devices. However, the fact that these PCE values are widely lauded despite on areas that are a fraction of a cm2 with minimal operational lifetimes is nothing short of legerdemain. Demonstrating a high-performance stable and scalable metal halide perovskite PV technology at low-cost represents the remaining grand challenge for cost-effective perovskite field operations.
Perovskites are prone to degradation from many stressors including moisture, heat, mechanical stress, light and electrical bias. Moisture ingress can cause rapid degradation of perovskite films due to hygroscopic organic cations that form hydrogen bonds with water leading to a hydrated perovskite phase which compromises the crystal’s structural stability. Exposure to elevated temperatures causes degradation from the rapid formation of PbI2, volatilization of the organic component, diffusion of halide species, and corrosion of metal contacts. Residual tensile stress resulting from coefficient of thermal expansion (CTE) mismatch between the perovskite film and substrate (Bush et al., 2018) generates a driving force for cracking and delamination, which negatively impacts environmental stability (Zhao et al., 2017; Rolston et al., 2018). Finally, the migration of vacancies and perovskite phase segregation has been attributed to light exposure (Bertoluzzi et al., 2020). In all cases, a combination of stressors accelerates the perovskite degradation process.
Scaling processes to enable production of thin-film devices at the manufacturing scale is a critical challenge that must be faced before emerging technologies can successfully reach the market. Deposition processes in open-air with high throughput are paths to significantly reduce capital expenditures by eliminating the need for expensive vacuum-based chambers and pumps while requiring fewer tools to produce a given number of devices based on increased production speeds. Recent work in the field has focused on developing scalable printing processes for the perovskite using blade coating (Deng et al., 2019), slot-die coating (Di Giacomo et al., 2018), and related scalable methods beyond spin coating (Priyadarshi et al., 2016) to produce large-area modules with respectable performance. Other work has focused on increasing throughput with rapid thermal processing (Ouyang et al., 2020), photonic curing (Troughton et al., 2016), or reduced annealing times (Deng et al., 2020). Our recent work combined both rapid deposition and curing with an open-air process by spray coating the perovskite precursor followed by an open-air plasma treatment that enabled continuous, in-line processing at 12 m/min without any post-anneal (Rolston et al., 2020).
Atmospheric pressure or open-air plasmas are used extensively in industry to clean surfaces and to functionalize substrates. These systems do not require any reaction vessel or chamber to maintain pressure at a fixed level and as a result can be directly integrated with in-line production. The plasma jet is commercially available and requires nothing more than a gas source (typically compressed air or N2) and high voltage. In one such configuration, the gas is ionized as it passes through the high-voltage region—which generates an arc with the grounded wall of the plasma system—and the resulting discharge is blown out of a nozzle and directed onto the substrate (Figure 1A). The uniqueness of the plasma system is the combination of energy sources which are generated. Reactive species (ions, radicals, metastables, and photons) are produced in combination with convective heat to rapidly transfer energy to enable ultrafast precursor conversion. No additional annealing or post-deposition processing is required to form high-quality device layers.
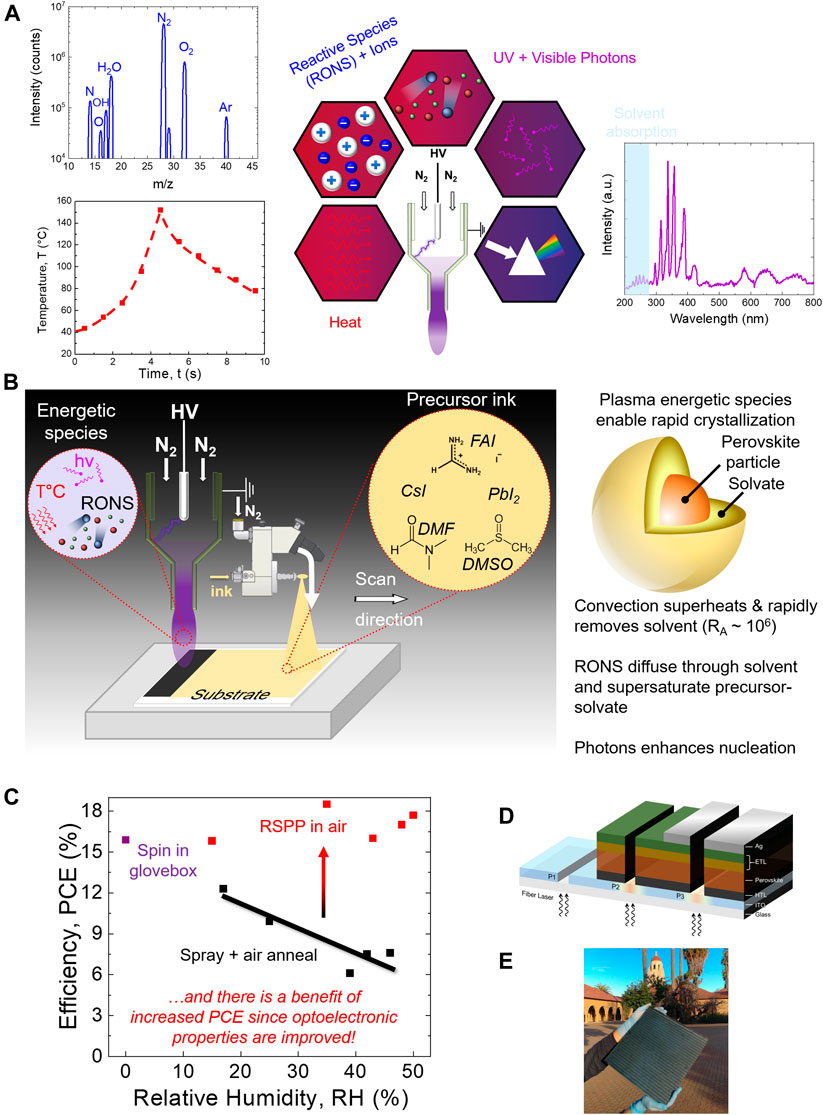
FIGURE 1. (A) Schematic of an open-air plasma system with the various energy sources generated that enable rapid curing of thin films. (B) Rapid spray plasma processing (RSPP), where the energetic species from the open-air plasma curing enables complete perovskite crystallization in <1 s and the highest throughput of any PV technology. (C) RSPP enables the highest perovskite efficiency for a scalable process in open-air and can produce manufacturing-scale perovskite PV modules. (D) Single-source laser scribing for perovskite module production. (E) Panel-scale perovskite deposited in open-air with RSPP on a 940 cm2 area.
We have demonstrated that open-air plasmas are effective at converting high-quality single, double, and triple cation compositions with a range of bandgaps into high-quality perovskite films (Hilt et al., 2018; Hovish et al., 2020; Rolston et al., 2020) and dense organosilicate barrier films (Rolston et al., 2017). This patented open-air Rapid Spray Plasma Process (RSPP) is a new scalable method for the ultra-fast deposition and cure of both efficient and mechanically robust thin films (Figures 1B,C) and PV modules (Figures 1D,E).
Cost Modeling for Utility Scale and Lab Scale Pilot Lines
Our scaling work initially focused on an inverted p–i–n structure with an ITO/NiO/Cs0.17FA0.83PbI3/C60/BCP/Ag layer stack. We have demonstrated rapid open-air processing of manufacturable device layers by developing a robust and stable spray coated NiO HTL (Scheideler et al., 2019) and perovskite active layer with RSPP. The top ETL and electrode were thermally evaporated in vacuum. A complete cost model for the full manufacturing process was developed to determine the annual costs for module production in a 9-step process were each calculated based for the entire process (Figure 2A) and amounted to $36.50/m2 or $0.23/W. Technoeconomic analysis was previously reported for a pilot line for a 2.46 m2 module produced in a factory generating 100 MW of annual production, which represents a significant investment on the order of tens of millions of dollars and was aimed at targeting utility-scale energy production.
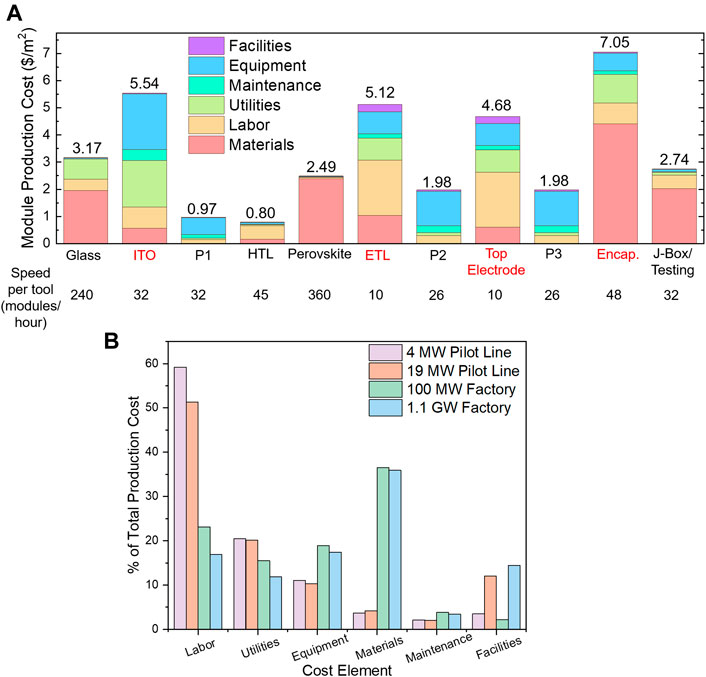
FIGURE 2. (A) Complete cost model for the entire, 9-step module production process for RSPP assuming a linear processing speed of ∼1 m/min (32 modules/hour) for the entire process with 100 MW of annual production. The vacuum-based steps (listed in red) are the most expensive. (B) Cost breakdown by percentage for a lab-scale pilot line producing 0.1 m2 modules compared to a factory producing 2.46 m2 modules. The green bars indicate the breakdown for the cost model shown in (A).
Here, we extend the analysis for the identical module architecture using a pilot line that could be currently achieved in a lab setting, a more practical situation relevant to the current state-of-the-art facilities employed by academic and industrial perovskite processing. This line consists of 0.1 m2 modules, with total annual production of either 4 or 19 MW of annual production, and the cost model estimates prices of $1.80/W or $1.65/W respectively, with the majority of the cost being driven by the ITO sputtering as well as the ETL and top electrode evaporation steps. These steps represent 58% of the total production cost per module, with their costs being elevated primarily due to low throughputs because of their reliance on vacuum conditions. Slower processing speeds necessitate more tools to keep pace with the other production steps, thus multiplying the labor, utility, and floorspace required to accommodate the tools. In addition, the cost of these three vacuum steps is disproportionately exacerbated by the scaling down of the production line; they only represent 44% of production costs in the 100 MW factory. Labor costs experience the largest relative growth when downsizing, as the number and cost of human workers do not adjust as naturally as other inputs such as precursor and utility usage. Surprisingly, the materials cost drops precipitously for the smaller pilot line, comprising just 4% of manufacturing costs compared to 44% for the 100 MW factory (Figure 2B). All labor costs were based on US manufacturing, and this trend illustrates the challenges that US-based perovskite start-ups often encounter since labor costs can be exorbitant in R&D facilities until reaching factory-scale production. This transition has not yet been reached for perovskites due to continued challenges regarding module reliability and operational lifetimes.
Our cost model has proven particularly useful because of the specificity of the material and equipment quotes we have garnered from industry suppliers. In addition, the model calculates cost as a function of throughput, meeting a user-input target of modules per hour by automatically adjusting the number of tools required, changing the other dependent variables such as materials and power usage accordingly. This greatly facilitated our analysis of production bottlenecks and optimal output levels. Moving forward, more exact direct labor data would help to increase the accuracy of our cost model; there is some uncertainty about labor intensity, the number of operators required per tool, and how much room there is for automation. Other recent cost models for perovskite modules were useful for comparison as we financed our own production line, and they also show disproportionate expenses from rate-limiting vacuum steps (Chang et al., 2017; Li et al., 2018). However, it is unclear based on these reports if our method of increasing tool numbers to meet desired throughput is the industry standard. Future work is therefore needed to address how to either reduce the adverse speeds and costs associated with vacuum steps or to sidestep them altogether. Increased transparency regarding low throughput steps would likely be a boon to the perovskite field.
Our analysis clearly indicates that the vacuum-based processes dominate the cost of production, with sputtered ITO, thermally evaporated electron transport layer (ETL) and the top electrode, and the vacuum processed encapsulation as the largest contributions. Clearly, vacuum deposition both poses a challenge for integrated linear production and dominates the overall cost of module production. Therefore, a significant opportunity exists to develop open-air spray-based capabilities for fully open-air manufactured perovskite modules with scalable methods.
Prospects for Open-Air Processing of ETL, Electrodes, and Barriers for Modules
Ironically, the costly ETL, top electrode, and encapsulation are also implicated in perovskite degradation mechanisms leading to metal diffusion/metal halide formation that currently dictates cell stability and lifetimes.
Open-Air ETL
Inorganic ETLs have excellent stability, mechanical robustness, and barrier properties, but are not easily processed on perovskite films in p-i-n architectures due to high energy deposition or annealing temperatures required (Figure 3A). Also, they rely on sol-gel spin-coating or vacuum-based deposition not amenable to large-scale inline production. We have developed a low-temperature TiOx ETL produced directly on top of perovskite using open-air chemical vapor deposition (Figure 3B) to form a fully inorganic, conformal, and compact TiOx film with >30X fracture resistance than commonly used fullerene-based ETLs and improved ambient stability (Chen et al., 2020a), although the lower conductivity of the amorphous layer has motivated efforts to explore different inorganic materials with improved electrical properties. This work established a path for open-air deposition of inorganic transport layers on top of perovskite without degrading the underlying film.
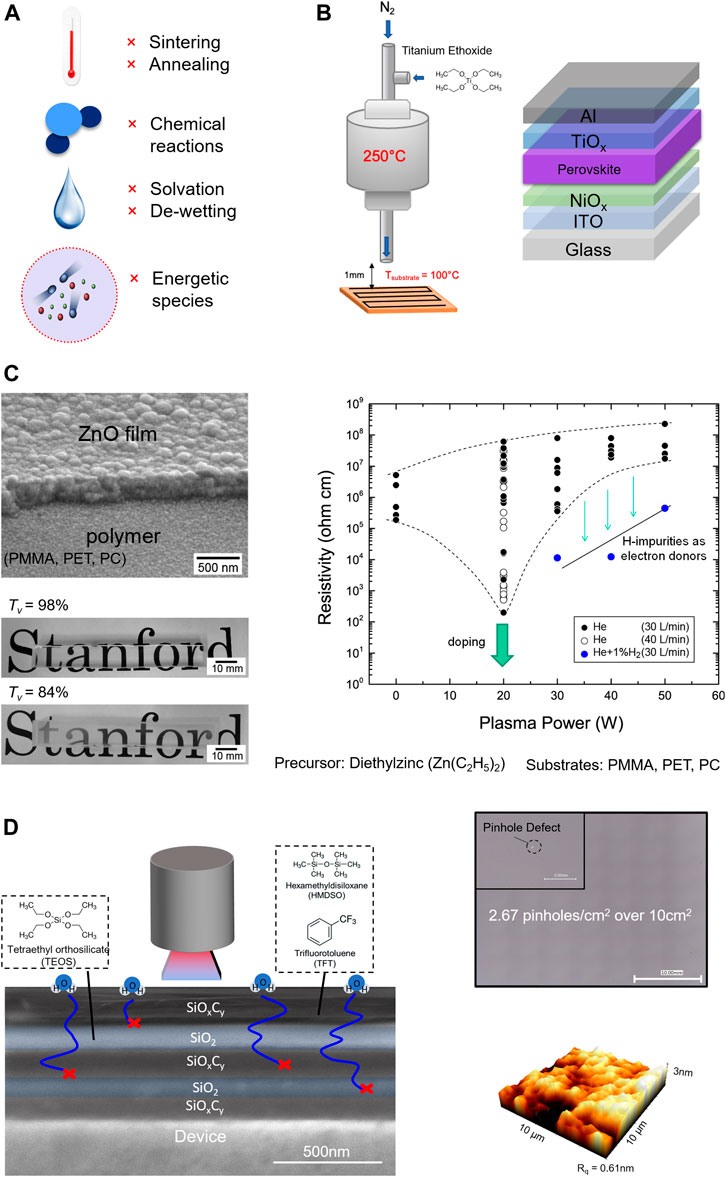
FIGURE 3. (A) Processing constraints for depositing films on top of the sensitive perovskite. (B) Open-air chemical vapor deposition of TiOx electron transport layer directly on the perovskite. (C) Open-air plasma deposition of transparent conducting ZnO thin films at low temperatures on plastic substrates. (D) Open-air deposited multilayer thin film moisture barriers using RSPP for improved environmental stability.
Our recent work has involved scalable methods for depositing SnO2 in open-air with scalable spray or chemical vapor deposition techniques. SnO2 is potentially a more promising inorganic candidate that TiO2 due to faster charge extraction, higher electron mobility, and improved stability under UV illumination. One strategy involves a sprayed composite of nanocrystalline SnO2 nanoparticles in an amorphous SnOx matrix, the latter of which is deposited from a SnCl2-based chemistry. The conversion of SnCl2 to SnOx can occur through a UV-ozone or plasma treatment, although the dose must be determined carefully to ensure the underlying perovskite is not degraded in the process. The nanoparticles serve as a buffer layer for the treatment, and any microscopic voids in the nanoparticle films are infiltrated with the matrix.
Open-Air TCO
We have also previously developed open-air processes for TCO films without damage on plastic substrates using rapid thermal processing (RTP) or plasma curing (Figure 3C) (Watanabe et al., 2014). Implementing a transparent conducting oxide (TCO) top electrode eliminates the concern of metal diffusion through the ETL and reacting with the halide in the perovskite (Bush et al., 2016). Current state-of-the-art architectures with the best reported stability under operational conditions thus involve a TCO or carbon-based top electrode. The requirement that the ETL serve as an effective buffer layer to prevent perovskite damage from RTP or plasma exposure is fulfilled by the fact that inorganic-based ETLs are effective buffer layers against plasma sputtering damage (Bush et al., 2017). In contrast, there are no requirements for minimizing thermal and plasma exposure for the bottom electrode, which enables more conventional spray pyrolysis for TCO formation. TCO-based top and bottom electrodes utilizing scalable deposition methods including near-infrared rapid thermal processing (NIR-RTP) and RSPP offer advantages over conventional electrode materials both in terms of cost and stability.
For the bottom electrode, open-air, solution-processed TCO formation typically employs high-temperature spray pyrolysis of metal chlorides with a high degree of composition and dopant flexibility. To reduce the required thermal load, delayed ignition combustion oxidation (DICO) modifies the precursor chemistry to utilize the metal nitrate hydrate coupled with an organic fuel (acetylacetone or urea) and shows significant promise to form uniform TCOs at lower temperatures (<300 °C) over short timescales (minutes) in open-air (Yu et al., 2015). Aa combination of spray-coated DICO chemistries for ITO, indium-doped zinc oxide (IZO), and aluminum-doped zinc oxide (AZO) with RSPP, NIR-RTP curing, and traditional annealing enables exploration of scalable TCO possibilities unparalleled by conventional methods. RSPP replaces the thermal curing requirement of spray pyrolysis while introducing a flexible chemical environment (reductive, oxidative, or neutral) with charged species to yield high quality TCOs.
Similar material systems can be adapted to the top electrode with non-aqueous solvent chemistries and lower processing temperatures. Replacing a traditionally thermally evaporated metal film with a TCO eliminates the concern of metal diffusing through the ETL and reacting with the halide in the perovskite. Current state-of-the-art architectures with the best reported stability under operational conditions employ TCO (Cheacharoen et al., 2018) or carbon-based top electrodes (Grancini et al., 2017). NIR-RTP and RSPP have already been used by our group to deposit TCO films without damaging plastic substrates (Watanabe et al., 2014), though a technological challenge is the requirement that the ETL serve as an effective buffer layer to perovskite damage from RTP or plasma exposure.
TCO films, with their superior operational stability, serve as the foundation toward achieving high conductivity top electrode films without the constraint of optical transparency. Challenges with the top electrode conductivity primarily involve low substrate deposition temperatures, thus optimization of a pure TCO top electrode will work in tandem with TCO-metal composite electrodes, utilizing the operational stability and barrier properties of TCOs as metal diffusion barriers. Efforts toward enhancing conductivities through composite electrodes have involved metal nanowire networks (Lee et al., 2018a), though these electrode networks consistently lack the process temperature for fused-junction formation to achieve high conductivity. Our group has previously demonstrated spray-deposition of metal-based nanoparticles and nanofibrils (Ansari et al., 2018), enabling the exploration of additional TCO-metal composite electrode systems. The unique multimodal curing capabilities offered by NIR-RTP and RSPP at low substrate temperatures enable a unique enhancement of TCO-metal multilayer top electrodes, allowing for top electrode development and conductivity optimization with unmatched process throughput and stability improvements.
Open-Air Barriers
Encapsulation is the largest individual contribution to the module cost (Figure 2A), and despite being a vacuum-based process, the materials are expensive due to the combination of polymeric encapsulation, butyl edge seal, and top glass for lamination. This encapsulation structure is comparable to the industrial standard processes for commercialized c-Si and CdTe solar modules for preventing moisture ingress or weather damage over the course of multiple decades. The bulky structure plays a key role in ensuring the long service lifetimes achieved by these technologies and is even more important for perovskites given the inherent instabilities in the presence of environmental stressors such as heat and moisture. However, the development of a thin, micron-scale barrier film structure would be game-changing from a cost perspective. Notwithstanding the potential need for additional structural stability, this strategy would enable flexible, lightweight perovskite solar modules if appropriately low water vapor transmission rates and pinhole/defect densities are achieved.
We have used RSPP to deposit submicron flexible barrier films directly on completed perovskite devices with significant improvements in stability under accelerated testing (combinations of 85°C and/or 85% RH) for more than 3,000 h along with improved resistance to degradation under continuous exposure to light, heat, and moisture (Rolston et al., 2017). Organosilicate precursors such as hexamethyldisiloxane in combination with fluorinated aromatic compounds resulted in higher contact angles (decreased water wettability) and improved film morphology. A slight modification of the RSPP experimental setup spraying the precursor incident to the leading edge of the plasma afterglow increased interactions with the precursor and resulted in dense organosilicate films with a tunable composition. The combination of these industrially relevant precursor chemistries in combination with the low CapEx from RSPP provides significant opportunity compared to commercial barriers on adhesive substrates—such as 3M’s ultrabarrier films—which are extremely expensive at ∼$50/m2.
We have also developed a similar process to deposit a dense SiO2 thin film on thermally sensitive substrates using plasma deposition. By combining this inorganic SiO2 layer with the RSPP organosilicate barrier, we have created multilayer barrier films to protect perovskites from moisture (Figure 3D) (Zhao et al., 2020). Such structures with alternating layers of inorganic and organic layers represent an effective strategy because the inorganic layer effectively blocks moisture or oxygen while the organic layer passivates defects like pinholes in the inorganic layer.
We have assessed the effectiveness of our multilayer barrier design by an optical calcium test in 38°C and 90% RH conditions. Both single layer barriers exhibited little protection from moisture with high WVTR on the order of 0.8–4 g/m2/day (Zhao et al., 2020). However, by combining these two layers, there is a significant improvement in an approximately two order of magnitude decrease in WVTR to 1.1 × 10−2 g/m2/day. This large increase in barrier property is likely explained by the multilayer design decoupling defects in one layer from another. Further improvement to 5.0 × 10−3 g/m2/day was accomplished by depositing a 5-layer barrier, which is comparable to WVTR of thin film barriers deposited using comparatively more expensive ALD and CVD processes in vacuum. The total thickness of this 5-layer barrier is still under 1 micron, and work is ongoing to map water ingress into the film to visualize the sources of film defectivity that are leading to eventual degradation.
The Bottom-Line: Design for Reliability and Module Stability
A key innovation with broader application to the perovskite community is a comprehensive module investigation strategy that focuses on high-throughput degradation monitoring of devices with a focus on targeting interfaces for improving module stability. There is a dearth of fundamental understanding for statistical analyses of degradation modes in perovskite modules under operational conditions. Our group employs a full suite of optoelectronic, structural, and mechanical characterization including color-normalized images, large-area optical microscopy, X-ray diffraction, time resolved photoluminescence, and detailed photoluminescence mapping at length scales from nm to cm to understand the fundamental degradation pathways due to each individual stressor and combinations of stressors. This holistic approach including multiple synergistic environmental stressors and in-situ characterization capabilities represents a significant advance over existing stability studies.
Detecting early-onset of degradation streamlines the design iteration process toward achieving stable perovskite cells Comprehensive studies are necessary to understand and mitigate degradation mechanisms in perovskite solar cells and modules. These need to be validated by adherence to consensus IEC standards and ISOS protocols (Khenkin et al., 2020) for accelerated aging and characterized by tracking device performance under specific combinations of heat, light, humidity, and electrical bias. Including multiple synergistic stressors and in-situ characterization capabilities over a wide range of length scales represents a significant advance over existing stability studies and will allow for determination of the spatial distribution of surface defects, grain boundaries, phase segregation, and interfacial reactions. Each individual stressor and combinations of stressors for both unencapsulated (intrinsic material stability) and fully encapsulated (extrinsic device stability) devices informs our iterative design process. Additionally, there is a critical need to establish relationships between optoelectronic properties and device performance together with film morphology/structure and stability. The ability to predict degradation and evaluate stability with rapid characterization such as in-situ imaging and will streamline the design iteration process toward the critical requirement of stable perovskite solar cells and modules.
The role of mechanical properties has been largely overlooked until recently. Perovskites have been identified as a mechanically fragile PV technology (Rolston et al., 2016), and several recent reports have explored strain engineering as a concept to improve optoelectronic properties (Zhu et al., 2019; Chen et al., 2020b; Kim et al., 2020) and reduce perovskite degradation (Zheng et al., 2016; Xiao et al., 2017; Zhao et al., 2017; Rolston et al., 2018; Li et al., 2019). The prospects of this effort are impactful since typical thermal processing generates large residual tensile perovskites film strain from the CTE mismatch compared to the typically stiff substrates used (i.e. glass and silicon). Approaches for reduction of such mismatch strains from processing and during operation involve the use of higher CTE substrates and lower temperature processing. This includes open-air plasma processing which has been demonstrated to result in significantly lower perovskite film stress (Hovish et al., 2020).
Recent studies have also examined more exotic methods such as compositional tailoring through the replacement of ions in the perovskite lattice and interfacial management through the insertion of thin layers either above or below the perovskite to apparently modulate the perovskite film strain. However, there are some misunderstandings of the fundamental mechanics of these approaches in the literature that have led to incorrect conclusions. As an initial matter, there are conflicting reports of the substitution of smaller (Saidaminov et al., 2018) and larger cations (Lee et al., 2018b) to reduce strain. Additionally, the concept of interfacial management is unfounded as a mechanism to reduce CTE mismatch film strains since it is the CTE mismatch between the film and the substrate that dominates the film strains, neither the interface nor the insertion of intermediate films has a role on film stresses. This is particularly true regarding work that claims that a higher CTE HTL can offset the residual tensile strain in the perovskite (Xue et al., 2020). There are also similar claims of other methods for reducing tensile strain (Wu et al., 2019) and minimizing CTE mismatch with interlayers or 2D perovskite layers (Wang et al., 2019). This is simply not founded in well-established thin-film mechanics where intermediate or top layers play no role on CTE elastic stresses (unless very close to the film edge). This topic needs further elucidation in the field to avoid incorrect conclusions with undue attention being placed on the role of contact/buffer layers and interfacial management to relieve CTE mismatch stress.
In addition to educating the broader community on the importance of mechanics and its application to thin film PV devices, the primary goal of our efforts is to develop fully open-air manufactured perovskite cells with scalable processing that eliminates the remaining vacuum-based processes (Figure 4) and concomitantly improves cell stability. In addressing this remaining grand challenge, we focus on robust materials integration with a fundamental understanding of degradation mechanisms to produce commercially competitive and stable perovskite solar modules.
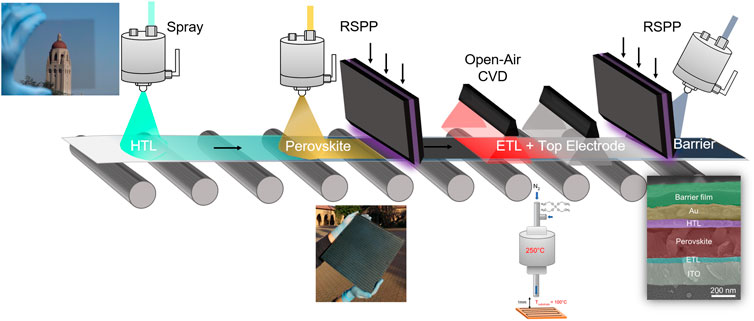
FIGURE 4. Schematic of high-throughput open-air production for in-line, fast and scalable manufacturing of perovskite solar modules.
Data Availability Statement
The original contributions presented in the study are included in the article/Supplementary Material, further inquiries can be directed to the corresponding author.
Author Contributions
All authors contributed to the writing of this manuscript.
Funding
This work was supported by the U.S. Department of Energy’s Office of Energy Efficiency and Renewable Energy (EERE) under Solar Energy Technologies Office (SETO) Agreement Number DE-EE0008559. Part of this work was performed at the Stanford Nano Shared Facilities (SNSF), supported by the National Science Foundation under award ECCS-1542152. Additional support was provided by the National Science Foundation Graduate Research Fellowship, awarded to OZ and JC under award DGE-1656518.
Conflict of Interest
The authors declare that the research was conducted in the absence of any commercial or financial relationships that could be construed as a potential conflict of interest.
The handling editor declared a past collaboration with several of the authors NR, OZ, RHD.
Acknowledgments
This work was supported by the U.S. Department of Energy’s Office of Energy Efficiency and Renewable Energy (EERE) under Solar Energy Technologies Office (SETO) Agreement Number DE-EE0008559. Part of this work was performed at the Stanford Nano Shared Facilities (SNSF), supported by the National Science Foundation under award ECCS-1542152. Additional support was provided by the National Science Foundation Graduate Research Fellowship, awarded to OZ and JC under award DGE-1656518.
References
Ansari, F., Ding, Y., Berglund, L. A., and Dauskardt, R. H. (2018). Toward Sustainable Multifunctional Coatings Containing Nanocellulose in a Hybrid Glass Matrix. ACS Nano 12, 5495–5503. doi:10.1021/acsnano.8b01057
Bertoluzzi, L., Boyd, C. C., Rolston, N., Xu, J., Prasanna, R., O’Regan, B. C., et al. (2020). Mobile Ion Concentration Measurement and Open-Access Band Diagram Simulation Platform for Halide Perovskite Solar Cells. Joule 4, 109–127. doi:10.1016/j.joule.2019.10.003
Bush, K. A., Bailie, C. D., Chen, Y., Bowring, A. R., Wang, W., Ma, W., et al. (2016). Thermal and Environmental Stability of Semi-Transparent Perovskite Solar Cells for Tandems Enabled by a Solution-Processed Nanoparticle Buffer Layer and Sputtered ITO Electrode. Adv. Mater. 28, 3937–3943. doi:10.1002/adma.201505279
Bush, K. A., Palmstrom, A. F., Yu, Z. J., Boccard, M., Cheacharoen, R., Mailoa, J. P., et al. (2017). 23.6%-efficient monolithic perovskite/silicon tandem solar cells with improved stability. Nat. Energy 2, 17009. doi:10.1038/nenergy.2017.9
Bush, K. A., Rolston, N., Gold-Parker, A., Manzoor, S., Hausele, J., Yu, Z. J., et al. (2018). Controlling Thin-Film Stress and Wrinkling during Perovskite Film Formation. ACS Energy Lett. 3, 1225–1232. doi:10.1021/acsenergylett.8b00544
Chang, N. L., Yi Ho-Baillie, A. W., Basore, P. A., Young, T. L., Evans, R., and Egan, R. J. (2017). A manufacturing cost estimation method with uncertainty analysis and its application to perovskite on glass photovoltaic modules. Prog. Photovolt: Res. Appl. 25, 390–405. doi:10.1002/pip.2871
Cheacharoen, R., Rolston, N., Harwood, D., Bush, K. A., Dauskardt, R. H., and McGehee, M. D. (2018). Design and understanding of encapsulated perovskite solar cells to withstand temperature cycling. Energy Environ. Sci. 11, 144–150. doi:10.1039/C7EE02564E
Chen, J. P., Hilt, F., Rolston, N., and Dauskardt, R. H. (2020a). Scalable open-air deposition of compact ETL TiOx on perovskite for fullerene-free solar cells. J. Mater. Chem. A 8, 22858–22866. doi:10.1039/D0TA08554E
Chen, Y., Lei, Y., Li, Y., Yu, Y., Cai, J., Chiu, M.-H., et al. (2020b). Strain engineering and epitaxial stabilization of halide perovskites. Nature 577, 209–215. doi:10.1038/s41586-019-1868-x
Deng, Y., Ni, Z., Palmstrom, A. F., Zhao, J., Xu, S., Van Brackle, C. H., et al. (2020). Reduced Self-Doping of Perovskites Induced by Short Annealing for Efficient Solar Modules. Joule 4, 1949–1960. doi:10.1016/j.joule.2020.07.003
Deng, Y., Van Brackle, C. H., Dai, X., Zhao, J., Chen, B., and Huang, J. (2019). Tailoring solvent coordination for high-speed, room-temperature blading of perovskite photovoltaic films. Sci. Adv. 5, eaax7537. doi:10.1126/sciadv.aax7537
Di Giacomo, F., Shanmugam, S., Fledderus, H., Bruijnaers, B. J., Verhees, W. J. H., Dorenkamper, M. S., et al. (2018). Up-scalable sheet-to-sheet production of high efficiency perovskite module and solar cells on 6-in. substrate using slot die coating. Solar Energy Materials and Solar Cells 181, 53–59. doi:10.1016/j.solmat.2017.11.010
Grancini, G., Roldán-Carmona, C., Zimmermann, I., Mosconi, E., Lee, X., Martineau, D., et al. (2017). One-Year stable perovskite solar cells by 2D/3D interface engineering. Nat. Commun. 8, 15684. doi:10.1038/ncomms15684
Hilt, F., Hovish, M. Q., Rolston, N., Brüning, K., Tassone, C. J., and Dauskardt, R. H. (2018). Rapid route to efficient, scalable, and robust perovskite photovoltaics in air. Energy Environ. Sci. 11, 2102–2113. doi:10.1039/C8EE01065J
Hovish, M. Q., Rolston, N., Brüning, K., Hilt, F., Tassone, C., and Dauskardt, R. H. (2020). Crystallization kinetics of rapid spray plasma processed multiple cation perovskites in open air. J. Mater. Chem. A 8, 169–176. doi:10.1039/C9TA07980G
Khenkin, M. V., Katz, E. A., Abate, A., Bardizza, G., Berry, J. J., Brabec, C., et al. (2020). Consensus statement for stability assessment and reporting for perovskite photovoltaics based on ISOS procedures. Nat. Energy 5, 35–49. doi:10.1038/s41560-019-0529-5
Kim, G., Min, H., Lee, K. S., Lee, D. Y., Yoon, S. M., and Seok, S. I. (2020). Impact of strain relaxation on performance of α-formamidinium lead iodide perovskite solar cells. Science 370, 108–112. doi:10.1126/science.abc4417
Lee, E., Ahn, J., Kwon, H.-C., Ma, S., Kim, K., Yun, S., et al. (2018a). All-Solution-Processed Silver Nanowire Window Electrode-Based Flexible Perovskite Solar Cells Enabled with Amorphous Metal Oxide Protection. Adv. Energy Mater. 8, 1702182. doi:10.1002/aenm.201702182
Lee, J.-W., Dai, Z., Han, T.-H., Choi, C., Chang, S.-Y., Lee, S.-J., et al. (2018b). 2D perovskite stabilized phase-pure formamidinium perovskite solar cells. Nat. Commun. 9, 3021. doi:10.1038/s41467-018-05454-4
Li, X., Luo, Y., Holt, M. V., Cai, Z., and Fenning, D. P. (2019). Residual Nanoscale Strain in Cesium Lead Bromide Perovskite Reduces Stability and Shifts Local Luminescence. Chem. Mater. 31, 2778–2785. doi:10.1021/acs.chemmater.8b04937
Li, Z., Zhao, Y., Wang, X., Sun, Y., Zhao, Z., Li, Y., et al. (2018). Cost Analysis of Perovskite Tandem Photovoltaics. Joule 2, 1559–1572. doi:10.1016/j.joule.2018.05.001
Ouyang, Z., Yang, M., Whitaker, J. B., Li, D., and van Hest, M. F. A. M. (2020). Toward Scalable Perovskite Solar Modules Using Blade Coating and Rapid Thermal Processing. ACS Appl. Energy Mater. 3, 3714–3720. doi:10.1021/acsaem.0c00180
Priyadarshi, A., Haur, L. J., Murray, P., Fu, D., Kulkarni, S., Xing, G., et al. (2016). A large area (70 cm2) monolithic perovskite solar module with a high efficiency and stability. Energy Environ. Sci. 9, 3687–3692. doi:10.1039/C6EE02693A
Rolston, N., Bush, K. A., Printz, A. D., Gold-Parker, A., Ding, Y., Toney, M. F., et al. (2018). Engineering Stress in Perovskite Solar Cells to Improve Stability. Adv. Energy Mater. 8, 1802139. doi:10.1002/aenm.201802139
Rolston, N., Printz, A. D., Hilt, F., Hovish, M. Q., Brüning, K., Tassone, C. J., et al. (2017). Improved stability and efficiency of perovskite solar cells with submicron flexible barrier films deposited in air. J. Mater. Chem. A 5, 22975–22983. doi:10.1039/C7TA09178H
Rolston, N., Scheideler, W. J., Flick, A. C., Chen, J. P., Elmaraghi, H., Sleugh, A., et al. (2020). Rapid Open-Air Fabrication of Perovskite Solar Modules. Joule 4, 2675–2692. doi:10.1016/j.joule.2020.11.001
Rolston, N., Watson, B. L., Bailie, C. D., McGehee, M. D., Bastos, J. P., Gehlhaar, R., et al. (2016). Mechanical integrity of solution-processed perovskite solar cells. Extreme Mechanics Letters 9, 353–358. doi:10.1016/j.eml.2016.06.006
Saidaminov, M. I., Kim, J., Jain, A., Quintero-Bermudez, R., Tan, H., Long, G., et al. (2018). Suppression of atomic vacancies via incorporation of isovalent small ions to increase the stability of halide perovskite solar cells in ambient air. Nat. Energy 3, 648–654. doi:10.1038/s41560-018-0192-2
Scheideler, W. J., Rolston, N., Zhao, O., Zhang, J., and Dauskardt, R. H. (2019). Rapid Aqueous Spray Fabrication of Robust NiO x : A Simple and Scalable Platform for Efficient Perovskite Solar Cells. Adv. Energy Mater. 9, 1803600. doi:10.1002/aenm.201803600
Troughton, J., Carnie, M. J., Davies, M. L., Charbonneau, C., Jewell, E. H., Worsley, D. A., et al. (2016). Photonic flash-annealing of lead halide perovskite solar cells in 1 ms. J. Mater. Chem. A 4, 3471–3476. doi:10.1039/C5TA09431C
Wang, H., Zhu, C., Liu, L., Ma, S., Liu, P., Wu, J., et al. (2019). Interfacial Residual Stress Relaxation in Perovskite Solar Cells with Improved Stability. Adv. Mater. 31, 1904408. doi:10.1002/adma.201904408
Watanabe, M., Cui, L., and Dauskardt, R. H. (2014). Atmospheric plasma deposition of transparent semiconducting ZnO films on plastics in ambient air. Organic Electronics 15, 775–784. doi:10.1016/j.orgel.2014.01.007
Wu, J., Cui, Y., Yu, B., Liu, K., Li, Y., Li, H., et al. (2019). A Simple Way to Simultaneously Release the Interface Stress and Realize the Inner Encapsulation for Highly Efficient and Stable Perovskite Solar Cells. Adv. Funct. Mater. 29, 1905336. doi:10.1002/adfm.201905336
Xiao, Z., Kerner, R. A., Zhao, L., Tran, N. L., Lee, K. M., Koh, T.-W., et al. (2017). Efficient perovskite light-emitting diodes featuring nanometre-sized crystallites. Nature Photon 11, 108–115. doi:10.1038/nphoton.2016.269
Xue, D.-J., Hou, Y., Liu, S.-C., Wei, M., Chen, B., Huang, Z., et al. (2020). Regulating strain in perovskite thin films through charge-transport layers. Nat. Commun. 11, 1514. doi:10.1038/s41467-020-15338-1
Yu, X., Smith, J., Zhou, N., Zeng, L., Guo, P., Xia, Y., et al. (2015). Spray-combustion synthesis: Efficient solution route to high-performance oxide transistors. Proc Natl Acad Sci USA 112, 3217–3222. doi:10.1073/pnas.1501548112
Zhao, J., Deng, Y., Wei, H., Zheng, X., Yu, Z., Shao, Y., et al. (2017). Strained hybrid perovskite thin films and their impact on the intrinsic stability of perovskite solar cells. Sci. Adv. 3, eaao5616. doi:10.1126/sciadv.aao5616
Zhao, O., Ding, Y., Pan, Z., Rolston, N., Zhang, J., and Dauskardt, R. H. (2020). Open-Air Plasma-Deposited Multilayer Thin-Film Moisture Barriers. ACS Appl. Mater. Interfaces 12, 26405–26412. doi:10.1021/acsami.0c01493
Zheng, X., Wu, C., Jha, S. K., Li, Z., Zhu, K., and Priya, S. (2016). Improved Phase Stability of Formamidinium Lead Triiodide Perovskite by Strain Relaxation. ACS Energy Lett. 1, 1014–1020. doi:10.1021/acsenergylett.6b00457
Keywords: photovoltaics, module, spray coating, scalable, stability, cost modeling, lifetime, transparent conducting oxide
Citation: Rolston N, Sleugh A, Chen JP, Zhao O, Colburn TW, Flick AC and Dauskardt RH (2021) Perspectives of Open-Air Processing to Enable Perovskite Solar Cell Manufacturing. Front. Energy Res. 9:684082. doi: 10.3389/fenrg.2021.684082
Received: 22 March 2021; Accepted: 17 May 2021;
Published: 28 May 2021.
Edited by:
Jinbao Zhang, Xiamen University, ChinaReviewed by:
Karthick Alagar, KPR Institute of Engineering and Technology, Coimbatore, IndiaDillip K. Panda, Clemson University, United States
Copyright © 2021 Rolston, Sleugh, Chen, Zhao, Colburn, Flick and Dauskardt. This is an open-access article distributed under the terms of the Creative Commons Attribution License (CC BY). The use, distribution or reproduction in other forums is permitted, provided the original author(s) and the copyright owner(s) are credited and that the original publication in this journal is cited, in accordance with accepted academic practice. No use, distribution or reproduction is permitted which does not comply with these terms.
*Correspondence: Reinhold H. Dauskardt, ZGF1c2thcmR0QHN0YW5mb3JkLmVkdQ==