- 1Cooperative Innovation Center of Unconventional Oil and Gas (Ministry of Education and Hubei Province), Yangtze University, Wuhan, China
- 2Key Laboratory of Drilling and Production Engineering for Oil and Gas, Wuhan, Hubei, China
- 3School of Urban Construction, Yangtze University, Jingzhou, China
- 4College of Civil and Transportation Engineering, Hohai University, Nanjing, China
1 Introduction
With the rapid development of global economy, the demand for oil and gas resources keeps rising, unconsolidated sandstone reservoirs occupy a very important position in China’s oil and gas resources (Wang et al., 2010) (Zhang, 2021) (Yan et al., 2021). In the process of drilling and producing oil in unconsolidated sandstone reservoir, the stress and pore pressure around the oil production cavity will be redistributed, which will cause serious problems such as sand production in the production stage (Wang et al., 2022). Sand production not only damages borehole integrity, but also leads to reduced oil and gas production, equipment corrosion and impact on production safety during production (Ahad et al., 2020) (Song et al., 2021). Due to the existence of the above negative effects, the exploitation cost of unconsolidated sandstone reservoir is further improved, so it is particularly important to conduct reliable sand production prediction research (Shabdirova et al., 2019) (Zivar et al., 2019).
At present, the research on sand production prediction of unconsolidated sandstone mainly focuses on two aspects, namely laboratory experimental research and numerical simulation research. Laboratory experimental studies mostly use a single large cylindrical artificial sandstone specimen for diagenesis and combine electrorheological probes (ER Probes) or high-pressure consolidation system (HPCS) to simulate the sand behavior, from the overall or macro perspective to simulate the sand law, but it is difficult to reveal the microscopic nature and mechanism of particle migration and sand production process (Zhang et al., 2015; Kozhagulova et al., 2020a; Kozhagulova et al., 2020b). Meanwhile, sand production in oil wells is closely related to mechanical behavior and rock properties of sandstone reservoir (Fattahpour et al., 2012). Because of the complex mineral composition and low cementation strength of unconsolidated sandstone reservoir, it is more difficult to predict sand production by laboratory experiments.
To better simulate and predict sand production, many scholars have shifted their research focus to numerical simulation methods (Cao et al., 2021; Liu et al., 2022). Therefore, this article discussed the current research status of numerical simulation methods for prediction of sand production in unconsolidated sandstone, analyzes the shortcomings of various methods, and puts forward suggestions for further research, so as to provide reference and theoretical support for sand production prediction and sand control design in the development of unconsolidated sandstone reservoirs.
2 Numerical simulation methods for sand production prediction
The accurate prediction of unconsolidated sandstone sand production in the production process plays a significant role in the level of oil and gas production. There are four kinds of numerical simulation methods, namely finite element method, finite difference method, discrete element method and discrete element-finite element hybrid method.
2.1 Finite element method
The finite element method mainly includes critical drawdown pressure difference evaluation, equivalent plastic strain analysis, thick wall cylinder calculation and prediction of sand production (Papamichos et al., 2010; Liu and Liu, 2018) (Garolera et al., 2020; Li et al., 2018).
2.1.1 Critical drawdown pressure difference evaluation
This method uses the true triaxial stress chamber (TTSC) to simulate the single-hole sanding behavior under true triaxial stress and fluid flow conditions and is verified by the finite element software ABAQUS (Younessi et al., 2013). Studies suggest that there is a critical drawdown pressure difference to induce sand production in the sand producing area around the borehole (Song et al., 2022). The failure prediction under true triaxial stress state is more accurate than Drucker-Prager (Al-Ajmi and Zimmerman, 2005; Al-Ajmi and Zimmerman, 2006) and has a stronger correlation with the experimental results. However, the numerical model does not consider the plastic strain law, and the sample is in an ideal state after yielding, which deviates from the actual value.
2.1.2 Equivalent plastic strain analysis
Since the 1990s, some scholars have introduced the equivalent plastic strain to analyze the sand production conditions and sand production, thereby improving the accuracy of sand production prediction, Figure 1B. (Morita et al., 1989; Bai et al., 2012). Volonte et al. established a reliable workflow through finite element modeling to estimate the actual sanding conditions (Volonté et al., 2010). As shown in Figure 1A, the rock failure around the perforation is evaluated by analyzing the distribution of equivalent plastic strain, and the Cosserat continua is introduced to simulate the slit type of failure around the borehole, so as to achieve the purpose of sand production prediction (Muller et al., 2011; Saski et al., 2021). Gui et al. (2016) further improved the accuracy of this method by combining core experiment and field experiment.
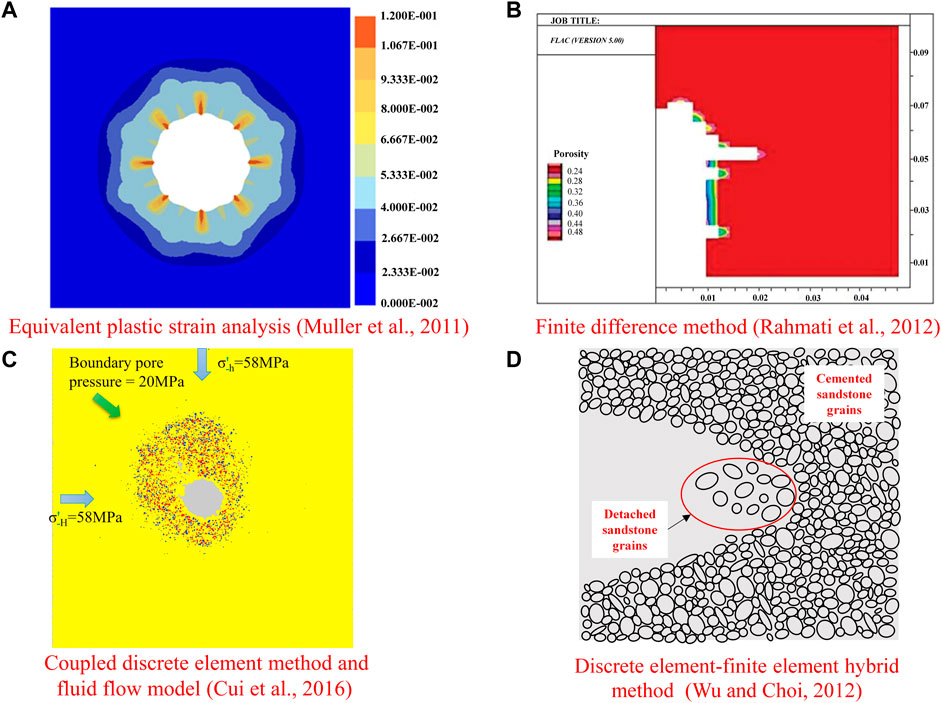
FIGURE 1. Numerical simulation methods for sand production prediction of unconsolidated sandstone. (A) corresponds to the numerical simulation results of equivalent plastic strain analysis, (B) corresponds to the numerical simulation results of finite difference method, (C) corresponds to the coupled discrete element method and fluid flow model, and (D) corresponds to the discrete element-finite element hybrid method.
2.1.3 Thick wall cylinder calculation
Santana and Likrama proposed a workflow for optimal matching between laboratory tests and finite element model simulation results (Santana and Likrama, 2016). In this method, the finite element model under the same test is developed by testing the experimental curve of thick-walled cylinder (TWC) to calibrate the strength and plasticity of the material. When the numerical test values match the experimental results, the failure threshold is determined according to the critical equivalent plastic strain to simulate the failure near the wellbore during production (Deng et al., 2019).
2.1.4 Prediction of sand production
Prediction of sand production is by considering the erosion process of coupling finite element method, by simulating the fluid flow phenomenon, to observe the sand erosion process, and then to predict the amount of sand in the wellbore (Servant et al., 2006). This method can reproduce the process of an erosion front, and the proposed finite element numerical model does not depend on specific erosion pattern, which is reproducible. The amount of sand is mainly affected by the degree of erosion and finite element time step and mesh refinement (Liu, 2012; Pak and Pak, 2020).
2.2 Finite difference method
Based on erosion criterion (Vardoulakis et al., 1996) (Papamichos et al., 2001), Detournay et al. (2006) proposed a sand production prediction to study the onset and rate of sand production by using the finite difference model. Rahmati et al. (2012) extended Detournay’s mechanical-erosion model with strain hardening/softening Mohr-Coulomb yield surface and fracture energy regularization technique (Nouri et al., 2009), which reduced the mesh dependence of strain results to a certain extent, and introduced erosion coefficient K to improve the accuracy of sand production prediction, as shown in Figure 1B. Shahsavari et al. (2021) further reduced the negative impact of mesh size on sand production prediction by combining hollow cylinder sand production experiment and finite difference program on the basis of predecessors.
2.3 Discrete element method
The discrete element method includes three aspects: Coupled Lattice-Boltzmann and Method Discrete Element Method (LBM-DEM), Coupled Computational Fluid Dynamic and Discrete Element Method (CFD-DEM), Coupled Discrete Element Method and Fluid Flow Model (DEM-FFM) (Wang et al., 2016; Rakhimzhanova et al., 2021; Zhang et al., 2022).
2.3.1 Coupled Lattice-Boltzmann and method-discrete element method
LBM code in LBM-DEM coupling method simulates fluid flow in each time step, and DEM is used to determine the particle position. Through the two-dimensional numerical simulation of fluid flow in deformable particulate media comprising of movable circular particles, the sand production phenomenon in weakly cemented sandstone reservoirs can be simulated. Also, can be used to study the basic mechanism of sand production on an experimental scale (Ghassemi and Pak, 2015; Han and Cundall, 2017) and analyze the permeability before and after sand production and the evolution process of the complex force chain network inside the model (Xia et al., 2022). On the basis of predecessors, Honari et al. simulated different stages of sand production by integrating Immersion Moving Boundary (IMB) method, including scale effect, extension of failure zone under incremental stress, and stress change during particle erosion (Honari and Hosseininia, 2021). The study believed that the smaller the pore diameter and the greater the stress value, the easier the sand production.
2.3.2 Coupled computational fluid dynamic and discrete element method
The coupling CFD-DEM model is used to study the sand production time, sand production amount and particle migration in the perforation damage zone of weakly cemented sand body under different fluid flow condition (Song et al., 2020; Khamitov et al., 2021). Then, the sand production of different fluid types is coupled (Khamitov et al., 2022). It is found that the stripped sand particles are mostly clustered or blocky, and the strength of sand body and fluid velocity are the key factors to determine whether to produce sand. Under the influence of fluid flow, the compacted core will release particles to the perforation location, and then produce transient sand retention. Ismail et al. extended the CFD-DEM coupling model to the study of screen sand consolidation and analyzed the influence of key parameters such as fluid velocity and particle size ratio on sand retention effect. The research results show that the method can better predict the sand production observed in the experiment (Ismail et al., 2021; Ismail et al., 2022).
2.3.3 Coupled discrete element method and fluid flow model
The DEM-FFM coupling model uses the particle flow code (PFC) developed by ITACSA to calculate by the discrete element method. The particles in the software are rigid and can overlap. The time steps calculated by the discrete element method correspond to the boundary conditions in PFC3D. The influence of boundary stress and fluid pressure on the spalling and sand production of sandstone particles is simulated by updating the variations of permeability and porosity change (Cui et al., 2016), as shown in Figure 1C. The research shows that the high boundary stress and seepage force plays a major role in the sand production process, and lead to the redistribution of stress, which makes the plastic area near the wellbore asymmetrically distributed and aggravates the sand production behavior. After that, Zhao et al. (2020) built a discrete element model based on the PFC3D platform and made a quantitative analysis of sand production.
2.4 Discrete element-finite element hybrid method
Wu and Choi based on the hybrid discrete element-finite model (DE-FE), use the strength of cementing materials, the degree of cementation between particles, and the property of pore fluid to evaluate the formation of pore types, the evolution of sand production volume and sand production rate, and whether the sand production is continuous (Wu and Choi, 2012). When the cementation between particles is destroyed, particles will separate from sandstone and flow out from the tip of the cavity through the fluid, as shown in Figure 1D. If the degree of cementation is poor, the toughness and permeability are high enough, the drag force of pore fluid is enough to cause bond failure, and the detached sandstone particles gather toward the borehole center, resulting in continuous sanding (Zhou et al., 2011).
3 Analysis and discussion
1) Finite element method and finite difference method are based on continuum mechanics. The strength and elastic properties of the numerical model can be obtained by laboratory tests, which is suitable for large-scale sand production prediction, but cannot capture local sand production phenomena.
2) The discrete element method can capture the motion, interaction and micro-failure mechanism of a single sand particle in the dynamic process, but it cannot be used for large-scale calculation and the calibration of model parameters is difficult. The calibration of parameters is not unique, and the micro properties cannot be determined by laboratory specimens.
3) The discrete element-finite element hybrid method can use the continuum theory to simulate the small deformation away from the wellbore, and the sand production behavior near the wellbore can be analyzed by using the discontinuous characteristics of discrete element. This method increases the accuracy of sand production prediction, but there are few related studies, most of which are still based on finite element method or discrete element method.
4) Discrete software PFC can simulate the discontinuous characteristics of rock and reproduce the separation phenomenon of single sand particle from rock matrix. The establishment of numerical model and parameter calibration are relatively simple, and the calculation amount is small, which has high sand production prediction accuracy (Cui et al., 2016; Zhao et al., 2020) (Rahmati et al., 2013) (Shirinabadi et al., 2016).
4 Conclusion
1) Accurate prediction of loose sandstone sand production has always been the focus of domestic and foreign scholars. From the perspective of numerical simulation, this paper summarizes the current research progress of numerical simulation methods, and analyzes the advantages and disadvantages of various methods, in order to provide research direction for future sand production prediction.
2) The finite element method may consider developing special numerical elements to characterize the effect of perforation geometry on sand production during perforation. The finite difference method uses the fracture energy regularization technique to extend the mechanical-erosion criterion and reduce the dependence of the fluid on the grid. In the future, the sand deposition after compression can be considered to further improve the prediction accuracy of sand production. The discrete element method can correlate the microscopic parameters of rock with macroscopic properties and realize the calibration of microscopic parameters of 3D DEM models. Due to the poor applicability of fluid flow at the perforation tip in the current 3D discrete element perforation test simulation, the reliability of the fluid simulation results at the perforation tip can be improved by introducing the discrete element-finite element hybrid method, considering the cementation state between particles, and providing reference for sand production prediction.
3) Although the discrete software PFC has high precision in sand prediction, there are still some calculation errors. In the future, based on the interface provided by the discrete software PFC, combined with the C++ language, a discrete contact model suitable for unconsolidated sandstone is established to further improve the accuracy of sand production prediction.
Author contributions
HS: mainly responsible for research literature and writing manuscript. GJ: mainly responsible for framework adjustment and thesis guidance. ZL and DH: mainly responsible for literature research.
Funding
This work was supported by the National Natural Science Foundation of China (No. 51804042), Open Fund of Key Laboratory of Exploration Technologies for Oil and Gas Resources (Yangtze University), and Ministry of Education (No. PI2021-04), and Open Fund of Cooperative Innovation Center of Unconventional Oil and Gas (Yangtze University), and Ministry of Education and Hubei Province (No. UOG2022-38).
Conflict of interest
The authors declare that the research was conducted in the absence of any commercial or financial relationships that could be construed as a potential conflict of interest.
Publisher’s note
All claims expressed in this article are solely those of the authors and do not necessarily represent those of their affiliated organizations, or those of the publisher, the editors and the reviewers. Any product that may be evaluated in this article, or claim that may be made by its manufacturer, is not guaranteed or endorsed by the publisher.
References
Ahad, N. A., Jami, M., and Tyson, S. (2020). A review of experimental studies on sand screen selection for unconsolidated sandstone reservoirs. J. Pet. Explor. Prod. Technol. 10 (4), 1675–1688. doi:10.1007/s13202-019-00826-y
Al-Ajmi, A. M., and Zimmerman, R. W. (2005). Relation between the mogi and the coulomb failure criteria. Int. J. Rock Mech. Min. Sci. 42 (3), 431–439. doi:10.1016/j.ijrmms.2004.11.004
Al-Ajmi, A. M., and Zimmerman, R. W. (2006). Stability analysis of vertical boreholes using the mogi–coulomb failure criterion. Int. J. Rock Mech. Min. Sci. 43 (8), 1200–1211. doi:10.1016/j.ijrmms.2006.04.001
Bai, M., Santana, C., and Shen, X. (2012). “A comprehensive approach in predicting excessive sand production,” in 2012 harmonising rock engineering and the environment–qian & zhou (London: Taylor & Francis Group) (978-0-415-80444-8.
Cao, C., Cheng, L. S., Zhang, X. Y., and Shi, J. J. (2021). Numerical simulation investigation on well performance integrated stress sensitivity and sand production. Geofluids 2021, 1–11. doi:10.1155/2021/9925866
Cui, Y. F., Nouri, A., Chan, D., and Rahmati, E. (2016). A new approach to DEM simulation of sand production. J. Petroleum Sci. Eng. 147, 56–67. doi:10.1016/j.petrol.2016.05.007
Deng, F. C., Yan, C. L., Jia, S. P., Chen, S. H., Wang, L. H., and He, L. (2019). Influence of sand production in an unconsolidated sandstone reservoir in a deepwater gas field. J. Energy Resour. Technol. 141 (9), 092904. doi:10.1115/1.4043132
Detournay, C., Tan, C., and Wu, B. (2006). “Modeling the mechanism and rate of sand production using FLAC,” in Numerical modeling in geo-mechanics-2006. Paper No. 08-10. Minne-Apolis. Editors R. Hart, and P. Varona (Minnesota: Itasca Consulting Group).
Fattahpour, V., Moosavi, M., and Mehranpour, M. (2012). An experimental investigation on the effect of grain size on oil-well sand production. Pet. Sci. 9 (3), 343–353. doi:10.1007/s12182-012-0218-5
Garolera, D., Carol, I., and Papanastasiou, P. (2020). Application of zero-thickness interface elements to sanding prediction analysis. J. Petroleum Sci. Eng. 190, 107052. doi:10.1016/j.petrol.2020.107052
Ghassemi, A., and Pak, A. (2015). Numerical simulation of sand production experiment using a coupled Lattice Boltzmann–Discrete Element Method. J. Petroleum Sci. Eng. 135, 218–231. doi:10.1016/j.petrol.2015.09.019
Gui, F., Khaksar, A., Zee, W. V. D., Hughes, B., and Cadogan, P. (2016). “Improving the sanding evaluation accuracy by integrating core tests, field observations and numerical simulation,” in Proceedings of the SPE asia pacific oil & gas conference and exhibition (Perth, Australia. doi:10.2118/182499-MS
Han, Y. H., and Cundall, P. (2017). Verification of two-dimensional LBM-DEM coupling approach and its application in modeling episodic sand production in borehole. Petroleum 3 (2), 179–189. doi:10.1016/j.petlm.2016.07.001
Honari, S., and Hosseininia, E. S. (2021). Particulate modeling of sand production using coupled DEM-LBM. Energies 14 (4), 906. doi:10.3390/en14040906
Ismail, N. I., Kuang, S. B., Tang, Y. C., and Yu, A. B. (2022). CFD-DEM evaluation of screen types for sand control applications. Powder Technol. 404, 117496. doi:10.1016/j.powtec.2022.117496
Ismail, N. I., Kuang, S. B., and Yu, A. B. (2021). CFD-DEM study of particle-fluid flow and retention performance of sand screen. Powder Technol. 378, 410–420. doi:10.1016/j.powtec.2020.10.012
Khamitov, F., Minh, N. H., and Zhao, Y. (2021). Coupled CFD-DEM numerical modelling of perforation damage and sand production in weak sandstone formation. Geomechanics Energy Environ. 28, 100255. doi:10.1016/j.gete.2021.100255
Khamitov, F., Minh, N. H., and Zhao, Y. (2022). Numerical investigation of sand production mechanisms in weak sandstone formations with various reservoir fluids. Int. J. Rock Mech. Min. Sci. 154, 105096. doi:10.1016/j.ijrmms.2022.105096
Kozhagulova, A., Minh, N. H., Zhao, Y., and Fok, S. C. (2020). Experimental and analytical investigation of sand production in weak formations for multiple well shut-ins. J. Petroleum Sci. Eng. 195, 107628. doi:10.1016/j.petrol.2020.107628
Kozhagulova, A., Shabdirova, A., Minh, N. H., and Zhao, Y. (2020). An integrated laboratory experiment of realistic diagenesis, perforation and sand production using a large artificial sandstone specimen. J. Rock Mech. Geotechnical Eng. 13 (1), 154–166. doi:10.1016/j.jrmge.2020.09.004
Li, X. R., Feng, Y. C., and Gray, K. E. (2018). A hydro-mechanical sand erosion model for sand production simulation. J. Petroleum Sci. Eng. 166, 208–224. doi:10.1016/j.petrol.2018.03.042
Liu, C., Zhou, W. S., Jiang, J. Z., Shang, F. J., He, H., and Wang, S. (2022). Remaining oil distribution and development strategy for offshore unconsolidated sandstone reservoir at ultrahigh water-cut stage. Geofluids 2022, 1–11. doi:10.1155/2022/6856298
Liu, Z. J., and Liu, R. J. (2018). Depletion-induced extreme plasticity across multiple horizontal wellbores in reservoirs with soft formations. Extreme Mech. Lett. 18, 70–78. doi:10.1016/j.eml.2017.11.004
Liu, Z. W. (2012). Sand prediction model and its application in offshore unconsolidated sandstone reservoirs. Special Oil Gas Reservoirs 19 (3), 136–139+158. doi:10.3969/j.issn.1006-6535.2012.03.036
Morita, N., Whitfill, D. L., Massle, I., and Kundsen, T. W. K. (1989). Realistic sand-production prediction: Numerical approach. SPE Prod. Eng. 4 (1), 15–24. doi:10.2118/16989-PA
Muller, A. L., Jr, E. D. A. V., Vaz, L. E., Figueiredo, R. P., and Goncalves, C. J. (2011). Numerical analysis of sand/solids production in boreholes considering fluid-mechanical coupling in a Cosserat continuum. Int. J. Rock Mech. Min. Sci. 48, 1303–1312. doi:10.1016/j.ijrmms.2011.09.012
Nouri, A., Kuru, E., and Vaziri, H. (2009). Elastoplastic modelling of sand production using fracture energy regularization method. J. Can. Petroleum Technol. 48 (4), 64–71. doi:10.2118/09-04-64
Pak, M. F. A., and Pak, A. (2020). Numerical simulation of sanding using a coupled hydro-mechanical sand erosion model. J. Rock Mech. Geotechnical Eng. 12 (4), 811–820. doi:10.1016/j.jrmge.2019.12.017
Papamichos, E., Tronvoll, J., Skjærstein, A., and Unander, T. E. (2010). Hole stability of red wildmoor sandstone under anisotropic stresses and sand production criterion. J. Petroleum Sci. Eng. 72, 78–92. doi:10.1016/j.petrol.2010.03.006
Papamichos, E., Vardoulakis, I., Tronvoll, J., and Skjærstein, A. (2001). Volumetric sand production model and experiment. Int. J. Numer. Anal. Methods Geomech. 25 (8), 789–808. doi:10.1002/nag.154
Rahmati, H., Jafarpour, M., Azadbakht, S., Nouri, A., Vaiziri, H., Chan, D., et al. (2013). Review of sand production prediction models. J. Petroleum Eng. 2013, 1–16. doi:10.1155/2013/864981
Rahmati, H., Nouri, A., Vazir, H., and Chan, D. (2012). Validation of predicted cumulative sand and sand rate against physical-model test. J. Can. Petroleum Technol. 51 (5), 403–410. doi:10.2118/157950-PA
Rakhimzhanova, A., Thornton, C., Amanbek, Y., and Zhao, Y. (2021). Numerical simulations of sand production in oil wells using the CFD-DEM-IBM approach. J. Petroleum Sci. Eng. 208, 109529. doi:10.1016/j.petrol.2021.109529
Santana, C., and Likrama, F. (2016). “Workflow on incorporating thick-walled cylinder test results in finite element models of near wellbore for sanding prediction studies,” in 50th US rock mechanics/geomechanics symposium (American Rock Mechanics Association), 16–514.
Saski, T., Shao, B., Elshafie, M., Papadopoulou, M., Yamamoto, K., and Soga, L. (2021). Simulation of axial tensile well deformation during reservoir compaction in offshore unconsolidated methane hydrate-bearing formation. Comput. Geotechnics 129, 103894. doi:10.1016/j.compgeo.2020.103894
Servant, G., Marchina, P., Peysson, Y., Bemer, E., and Nauroy, J. F. (2006). Sand erosion in weakly consolidated reservoirs: Experiments and numerical modeling. SPE 100023. doi:10.2118/100023-MS
Shabdirova, A., Minh, N. H., and Zhao, Y. (2019). A sand production prediction model for weak sandstone reservoir in Kazakhstan. J. Rock Mech. Geotechnical Eng. 11 (4), 760–769. doi:10.1016/j.jrmge.2018.12.015
Shahsavari, M. H., Khamehchi, E., Fattahpour, V., and Molladavoodi, H. (2021). Investigation of sand production prediction shortcomings in terms of numerical uncertainties and experimental simplifications. J. Petroleum Sci. Eng. 207, 109147. doi:10.1016/j.petrol.2021.109147
Shirinabadi, R., Moarefvaand, P., Goshtasbi, K., and Ahangari, K. (2016). The physical and numerical modeling of sand production and gravel pack in oil wells by designing and manufacturing the machine and presenting a relation estimating sand production rate. J. Min. Sci. 52 (2), 300–312. doi:10.1134/s1062739116020453
Song, R., Zhang, P., Tian, X. M., Huang, F. M., Li, Z. W., and Liu, J. N. (2022). Study on critical drawdown pressure of sanding for wellbore of underground gas storage in a depleted gas reservoir. Energies 15 (16), 5913. doi:10.3390/en15165913
Song, Y. Q., Ranjith, P. G., and Wu, B. L. (2020). Development and experimental validation of a computational fluid dynamics-discrete element method sand production model. J. Nat. Gas Sci. Eng. 73, 103052. doi:10.1016/j.jngse.2019.103052
Song, Y. Q., Ranjith, P. G., Wu, B. L., and Song, Z. L. (2021). A microscopic study of sand arches and sand skeletons under hydrodynamic force based on the CFD-DEM model. J. Nat. Gas Sci. Eng. 92, 104017. doi:10.1016/j.jngse.2021.104017
Vardoulakis, I., Stavropoulou, M., and Papanastasiou, P. (1996). Hydro-mechanical aspects of the sand production problem. Transp. Porous Media 22 (2), 225–244. doi:10.1007/bf01143517
Volonté, G., Scarfato, F., and Brignoli, M. (2010). Sand prediction: A practical finite-element 3D approach for real field applications. SPE, 134464. doi:10.2118/134464-ms
Wang, M., Feng, Y. T., and Wang, C. Y. (2016). Coupled bonded particle and lattice Boltzmann method for modelling fluid-solid interaction. Int. J. Numer. Anal. Methods Geomech. 40 (10), 1383–1401. doi:10.1002/nag.2481
Wang, X. Z., Wang, J. Y., Wang, C. F., Zeng, L. F., and Liu, X. W. (2010). Quantitative description of characteristics of high-capacity channels in unconsolidated sandstone reservoirs using in situ production data. Pet. Sci. 7 (1), 106–111. doi:10.1007/s12182-010-0013-0
Wang, Y., Cheng, K., Yang, Y. F., Tao, Y. C., and Li, Y. W. (2022). Microscopic mechanical analysis of sand production using a new arbitrary resolved-unresolved CFD-DEM model. Int. J. Multiph. Flow 149, 103979. doi:10.1016/j.ijmultiphaseflow.2022.103979
Wu, B., and Choi, S. K. (2012). Effect of mechanical and physical properties of rocks on post-failure cavity development-experimental and numerical studies. ARAM, 12–489.
Xia, T., Feng, Q. H., Wang, S., Zhang, J. Y., Zhang, W., and Zhang, X. M. (2022). Numerical study and force chain network analysis of sand production process using coupled LBM-DEM. Energies 15 (5), 1788. doi:10.3390/en15051788
Yan, Z. H., Yang, Y., Li, W., Wang, Y. H., Xie, M. Y., and Xiong, Q. (2021). Analysis of sand production law and key factors of offshore weakly cemented unconsolidated sandstone reservoirs. Fresenius Environ. Bull. 30 (6A), 6574–6580.
Younessi, A., Rasouli, V., and Wu, B. (2013). Sand production simulation under true-triaxial stress conditions. Int. J. Rock Mech. Min. Sci. 61, 130–140. doi:10.1016/j.ijrmms.2013.03.001
Zhang, F. S., Wang, T., Liu, F., Peng, M., Bate, B., and Wang, P. (2022). Hydro-mechanical coupled analysis of near-wellbore fines migration from unconsolidated reservoirs. Acta Geotech. 17, 3535–3551. doi:10.1007/s11440-021-01396-2
Zhang, P., Zheng, S. J., Jing, J. Q., Zhou, Y. N., Li, Q. P., Wang, K., et al. (2015). Surface erosion behavior of an intrusive probe in pipe flow. J. Nat. Gas Sci. Eng. 26, 480–493. doi:10.1016/j.jngse.2015.05.037
Zhang, X. Y. (2021). Experimental study on stress sensitivity of permeability and elastic parameters of unconsolidated sandstone reservoirs. Fresenius Environ. Bull. 30 (7), 8467–8475.
Zhao, B., Su, Y. Z., Cong, W., Sun, H. B., Dong, X. Y., Hu, M. H., et al. (2020). Discrete element analysis on sand production risk and mechanism in unconsolidated sandstone oil and gas reservoir. J. Saf. Sci. Technol. 16 (11), 59–65. doi:10.11731/j.issn.1673-193x.2020.11.009
Zhou, Z. Y., Yu, A. B., and Choi, S. K. (2011). Numerical simulation of the liquid-induced erosion in a weakly bonded sand assembly. Powder Technol. 211 (2-3), 237–249. doi:10.1016/j.powtec.2011.04.029
Keywords: unconsolidated sandstone, sand production prediction, finite element method, finite difference method, discrete element method, discrete element-finite element hybrid method
Citation: Sun H, Ji G, Liu Z and Huang D (2023) Research advance of numerical simulation methods for sand production prediction of unconsolidated sandstone. Front. Energy Res. 10:1071320. doi: 10.3389/fenrg.2022.1071320
Received: 17 October 2022; Accepted: 07 November 2022;
Published: 17 January 2023.
Edited by:
Qi Zhang, China University of Geosciences Wuhan, ChinaReviewed by:
Zhegwen Zhu, Wuhan University, ChinaJian Xiong, Southwest Petroleum University, China
Yanjun Lu, Yanshan University, China
Copyright © 2023 Sun, Ji, Liu and Huang. This is an open-access article distributed under the terms of the Creative Commons Attribution License (CC BY). The use, distribution or reproduction in other forums is permitted, provided the original author(s) and the copyright owner(s) are credited and that the original publication in this journal is cited, in accordance with accepted academic practice. No use, distribution or reproduction is permitted which does not comply with these terms.
*Correspondence: Guofa Ji, amlndW9mYUAxNjMuY29t