- 1Department of Chemical Engineering, University of South Carolina, Columbia, SC, United States
- 2Department of Chemistry, University of South Carolina, Columbia, SC, United States
Bio-oils produced from torrefaction or pyrolysis of biomass constitute an under-utilized product that generally requires complicated processing. The high acidity and water content pose storage and transportation issues, and the complex nature of the organic species makes utilization as a chemical feedstock troublesome. Most methodologies to separate and upgrade bio-oils involve multiple distinct steps and solvent-based extractions, complicating the process and adding cost. In this work, we demonstrate a simple one-step solution using ammonia to separate the aqueous and organic phases of a model bio-oil. This process produces an aqueous phase that contains ammonium species that could be utilized as a fertilizer and an organic phase that can be used as an additive for transportation fuels or could be burned to produce electricity.
1 Introduction
Biomass torrefaction is a promising way to upgrade biomass to improve physical properties such as grindability and storability as well as increase the heating value of the produced biomass (Shankar Tumuluru et al., 2011; Chen et al., 2018; Matyjewicz et al., 2020). However, during torrefaction (or pyrolysis), condensable amounts of bio-oil and CO are produced (Ren et al., 2013; Biswas et al., 2017). If CO is not utilized for syngas or other applications, a pollutant control technology such as catalytic oxidation can be used to produce CO2. However, bio-oil is currently underutilized due to unfavorable properties resulting from its composition. Due to the high water content, it is not cost-effective to transport and poses issues for combustion. The high acid content also poses problems for storage as it can corrode low alloy steel containers (Wigley et al., 2017). Finally, utilization as a chemical feedstock is difficult as bio-oil contains a large mixture of chemicals, and separability is an issue (Wang et al., 2014; Panwar and Paul, 2021).
Various processes exist to upgrade bio-oil to more valuable products. Still, the separability of the organic and aqueous fractions can be problematic, and the variability in composition with different feedstocks can complicate processing (Kim, 2015; Drugkar et al., 2022). Some work has been done to separate the two phases by adjustment of the pH of the bio-oil via the addition of bases such as sodium hydroxide, however, they also generally require multiple steps such as various pH adjustments or additional solvent extractions (Park et al., 2016). These extra steps increase processing costs, and a simple one-step methodology could prove to be advantageous. To address these shortcomings, this work seeks to develop a simple one-step process to upgrade bio-oil using gaseous ammonia. Utilizing ammonia instead of other bases also expands the potential use cases for the process as bio-oil could potentially be used as an industrial scrubbing medium for ammonia instead of conventional acids such as sulfuric or nitric acid (Melse and Ogink, 2005). Additionally, the neutralization of acetic acid with ammonia also produces ammonium acetate which can be utilized as a fertilizer, deicer, or as a precursor to acetamide (Rosanoff et al., 1911; Liu et al., 1997; Frolova et al., 2013). Finally, work is currently underway to use coal combustion flue gas for on-site torrefaction of waste biomass, and power plants have ammonia available for selective catalytic reduction units (Wilburn and Wright, 2004). Therefore, the co-location of the bio-oil feedstock and ammonia would allow for potential on-site treatment with existing rail transport routes.
Alternatively, for production sites with no ammonia infrastructure, on-site ammonia generation could be a potential solution. With research focusing on lower-pressure ammonia synthesis (Humphreys et al., 2021) and a possible desire to create a more modular setup for hydrogen as a fuel source (MacQueen, 2020; Humphreys et al., 2021), ammonia could be produced from hydrogen from electrolysis, nitrogen from pressure swing adsorption, effectively only requiring access to water and electricity. Additionally, if the bio-oil effectively scrubs ammonia from the reactor effluent, it could eliminate the need for separation before recycling unreacted H2 and N2 back into the ammonia synthesis reactor system. This approach requires less energy for ammonia production due to ammonia production pressures, the elimination of cryogenic product separation, as well as the elimination of storage and transportation costs for the required ammonia.
2 Experimental
Synthetic bio-oil was created by blending pure analogue components for each class of functional group and mixing until homogenous. A detailed composition of the synthetic bio-oil is shown below in Table 1. The composition of the synthetic bio-oil is similar to what is documented in previous literature, although with a high acid content, to validate the process in a highly acidic environment (Ren et al., 2013; Zhai et al., 2014; Wahid et al., 2017; Ukaew et al., 2018; Abdul Samad and Saleh, 2022).
Bubbling of ammonia was conducted via flowing 500 ml/min of 5 vol.% NH3 diluted in argon through a Synthware mineral oil bubbler filled with 20 ml of the synthetic bio-oil, as shown in Figure 1. In order to reduce the evaporation of water, the bubbler was submerged in an ice bath at ∼0°C. Bubbling was conducted until breakthrough occurred in which the concentration of ammonia flowing through the bio-oil matched the concentration of ammonia flowing through the system without bio-oil. After breakthrough occurred, the mixture was added to a centrifuge set at 6,900 rpm for 5 min to expedite separation, although the mixture will also gravitationally separate. Here, the aqueous phase was able to be poured out, leaving the organic phase in the centrifuge tube. The ammonia concentration was determined via a mass spectrometer system. This system consisted of a Kurt J. Lesker Series 979 Atm to Vacuum Transducer, MDC ULV-150 variable leaking valve, Stanford Research Systems RGA 200, and pumped with a Varian V-250 turbopump backed by an Alcatel 2021-SD mechanical pump. A portion of the process effluent gas was introduced to the leaking valve with a Lenox Laser 100 μm orifice plate and differentially pumped via another roughing pump.
Analysis was also conducted utilizing an ammonia synthesis reactor as the ammonia source. Hydrogen (Airgas, UHP) and nitrogen (Airgas, UHP) flowed at 240 ml/min total (at a 50:50 ratio) through a 3/8” 316 Stainless Steel reactor tube inside of an MTI OTF-1200X furnace with an ammonia synthesis catalyst. This catalyst was a 5% Ru/CeO2 which produced an effluent gas containing approximately 5.47% ammonia (as determined using a Shimadzu GC-2014), with the balance being the fed hydrogen and nitrogen. Bubbling through the bio-oil and analysis of breakthrough of ammonia was conducted as above.
The composition of the products was determined utilizing a Shimadzu GC-2010 gas chromatograph–mass spectrometer (GC/MS) equipped with a 30 m RTX-1701 column held at 40°C for 4 min and then ramped at 5°C/min to 260°C where it was held for 15 min. The aqueous phase was diluted 10:1 in DI water and the organic phase was similarly diluted with acetone and filtered through a 0.2 μm PVDF filter before injecting 0.3 μL of solution for analysis.
Heating values of the organic phase from the bio-oil were determined using a Parr model 1,108 bomb calorimeter that was calibrated with benzoic acid. The system was charged with 30 bar of oxygen and approximately 1 g of sample was combusted to determine the heating value.
3 Results and discussion
Upon initial exposure of the bio-oil mixture to ammonia, essentially no ammonia slip occurs, as shown in Figure 2A. The point at which breakthrough begins to occur (at ∼120–150 min) generally corresponds roughly to the third and fourth images in Figure 2B, indicating that the bubbling could potentially be stopped before full breakthrough while still maintaining adequate separation of the two phases of the bio-oil, requiring less ammonia. Distinct color changes are noted as separation begins to occur. Initially, the mixture starts as a homogenous black solution and briefly turns partly cloudy before a dark organic phase, and a lighter aqueous phase begins to develop. As ammonia slip begins, distinct droplets of the organic phase begin to develop. Near complete breakthrough, the phases completely separated, and the organic phase consists of spherical droplets that will gravitationally settle to the bottom of the experimental apparatus, as seen in the images in Figure 2B. Quantification of the ammonia consumption was accomplished by integrating the signal above the breakthrough curve, and the result of this integration is shown in Figure 3A. Consistency exists from experiment to experiment with an average uptake of 8.0 mmol NH3/mL of bio-oil. Based solely on the reaction of acetic acid and ammonia, the expected uptake of 5.5 mmol of NH3/mL of bio-oil is much lower than what was experimentally observed. However, other mildly acidic components exist in the model bio-oil, such as phenol, and aqueous ammonia can react with other organic components (Baekeland, 1909). Further, the remaining ammonia would also lead to the resulting basic solution observed due to dissolution in the liquid.
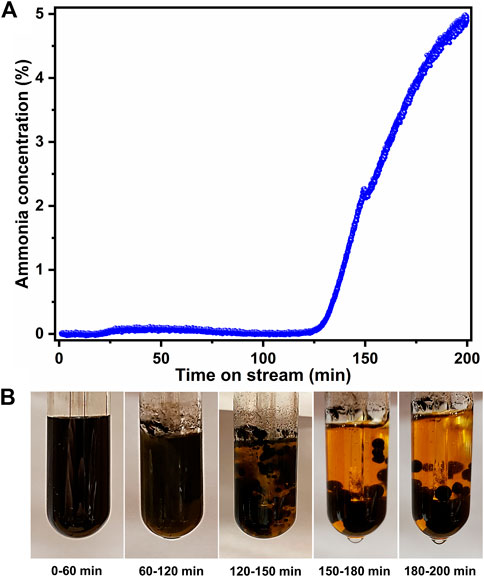
FIGURE 2. (A) ammonia concentration after bubbling through bio-oil as a function of time (B) digital photographs showing the separation trend of organic and aqueous phases.
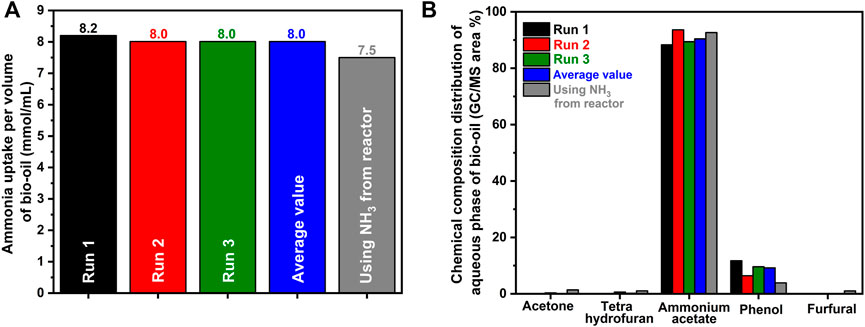
FIGURE 3. (A) Normalized uptake of ammonia by bio-oil and (B) yields and distribution of the separated aqueous phase of bio-oil.
To determine the quality of the separation and determine where the additionally consumed ammonia had reacted, the composition of both the organic and aqueous phase was analyzed, and the results are summarized below. As shown in Figure 3B, most of the aqueous phase is composed of ammonium acetate with some phenol and trace chemicals such as acetone and tetrahydrofuran. In contrast, the organic phase is essentially free of acetic acid/ammonium acetate, as shown in Figure 4. Additionally, this phase is insoluble in water but readily dissolves in acetone or ethanol and partially dissolves in cyclohexane. However, the utilization of ethanol as a solvent resulted in the reaction of part of the organic phase with ethanol (replacement of -OH groups with -OCH2CH3); thus, acetone was used as the solvent for the GC/MS analysis of the organic phase. In general, the organic phase consists mainly of phenol and a variety of monocyclic and polycyclic nitrogen-containing species. The concentration of phenol in the organic phase is consistent run to run; however, despite the sums of the areas of the various nitrogen-heterocycles being consistent, the yield of each of the nitrogen-containing species varied run to run as seen in Figure 4.
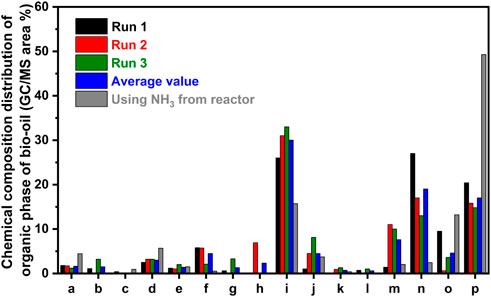
FIGURE 4. Yields and distribution of the quantified species in the separated organic phase of bio-oil. (A) tetrahydrofuran (B) acetic acid/ammonium acetate (C) ethylbenzene (D) O-xylene (E) furfural (F) 1H-pyrrole-2-carboxaldehyde (G) aziridine, 2-isopropyl-1,3-dimethyl-, trans- (H) 4-piperidinone, 2,2,6,6-tetramethyl-, oxime (I) phenol (J) tricyclo [3.3.1.1 (3,7)]decan-1-amine (K) acetamide, N-(3H-[1,2,3]triazolo [4,5-day]pyrimidin-7-yl)- (L) 1H-pyrrole, 1-(2-furanylmethyl)- (M) 2-methyl-2-azatricyclo [4.3.1.0 (3,8)] decane (N) pyrazolo [5,1-c]1,2,4-triazine-3-carbonitrile, 4,7-dimethyl- (O) adamantane-1-carboxamide, N-(1-methylbenzimidazol- and (P) other polycyclic N species.
While this process succeeds in separating acetic acid from the organic fraction of the bio-oil and concentrating the organics by the formation of a hydrophobic phase, it does, however, create a substantially larger mix of chemicals than what was originally present in the model bio-oil. This result poses an issue for the utilization of this mixture as a chemical feedstock, however, due to the removal of water and acetic acid, the mixture is readily combustible and is capable of dissolving in materials already used as fuels, such as ethanol. The organic mixture was readily ignitable and had a heating value of 29.0 MJ/kg, as seen in Figure 5, which is slightly higher than that of ethanol (Turner et al., 2011) and approximately two-thirds that of gasoline (Cataluña et al., 2008; Turner et al., 2011), making this a potential fuel additive to ethanol for gasoline, however, we do note the potential NOx hazards that do play a possible risk due to the nitrogen containing ringed hydrocarbons that would require a catalyst for decomposition post-combustion. Additionally, the low content of unburned material, as shown in Figure 5, means this is a relatively clean-burning fuel.
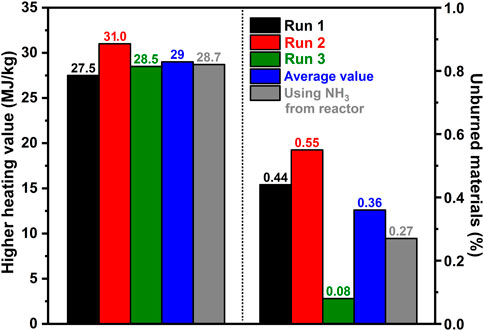
FIGURE 5. Heating value of the organic phase of the separated bio-oil and the unburned residue post combustion.
Previous literature examining reactions of organics and aqueous ammonia/ammonia gas had documented the creation of nitrogen-containing rings from various feedstocks. Furfural has previously been reported to react with ammonia to form a variety of compounds with nitrogen-substituted rings (Mariscal et al., 2016). Additionally, ammonia or amines can react with aldehydes and ketones to produce imines (Chichibabin synthesis) which can further react with themselves or other aldehydes or ketones to produce azines such as pyridine and pyrimidine (and their derivatives) as well as non-aromatic nitrogen containing rings similar to those detected in the GC/MS (Frank and Seven, 1949; Weiss, 1952; Mcgill and Rappa, 1988). The formation of larger polymer chains has also been previously documented as Bakelite, an early polymer, was synthesized from ammonium hydroxide solution and aldehydes (Baekeland, 1909). Potential reactions of furfural with ammonia are shown in Figure 6 and result in the formation of polycyclic nitrogenous compounds.
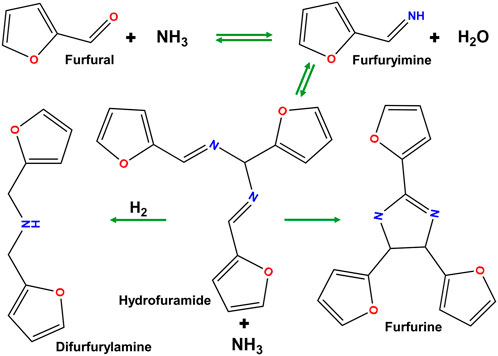
FIGURE 6. Chemicals formed during ammonia exposure to furfural adapted from (Mariscal et al., 2016).
Further exploration was conducted to determine the effect of using effluent gas from an ammonia synthesis reactor. Currently, ammonia is primarily synthesized using the Haber-Bosch process, which requires liquefication under low temperatures or under pressure to separate the produced ammonia from the remaining hydrogen and nitrogen. Here, an ammonia synthesis reactor was used to produce the ammonia, and therefore the balance of the gas flow was hydrogen and nitrogen instead of argon. A similar breakthrough curve was determined, with ammonia uptake being slightly lower than when ammonia was sourced from a tank (approximately 7.5 mmol NH3/mL compared to 8.0 mmol NH3/mL). Further, the phase separation occurred once again, with ammonium acetate being the major component (92.7%) once again in the aqueous phase and only in trace amounts (0.07%) in the non-aqueous phase. In fact, as shown in Figure 3B, similar concentrations of compounds in the aqueous phase can be seen using both NH3 from a reactor and from a tank of ammonia, which highlights the lack of effect of hydrogen and nitrogen in the effluent in comparison to a balance of argon. In addition, as shown in Figure 5, the heating value of the organic phase of this experiment produced an almost identical heating value, and percent burned compared to the original runs. Further, as the bio-oil removed the ammonia from the gas flow, an almost pure mixture of hydrogen and nitrogen was measured, resulting in the ability to recycle this gas through the reactor without the need for any further mechanism of separation; thus, resulting in a possible one-step ammonia synthesis (for ammonium acetate) and bio-fuel reactor.
4 Conclusion
Highly acidic bio-oils can be successfully upgraded via the separation of the organic and aqueous phases via bubbling with ammonia. In addition, this method also removes acetic acid from the organic phase and produces ammonium acetate, which can be utilized as a fertilizer. Although the complex nature of the organic phase (even when utilizing a model bio-oil) makes utilization as a chemical feedstock difficult, the organic phase is readily ignitable. It has a greater heating value than ethanol, a common fuel additive. Therefore, this process valorizes both the aqueous and organic fractions. Further, the bio-oil could also be utilized as a scrubbing medium for controlling ammonia slip, potentially using another waste stream to upgrade the bio-oil. Finally, the ability to utilize ammonia from an ammonia synthesis reactor would, in turn, create a less energetic process for ammonia synthesis and would reduce the need for transportation of ammonia to the upgrading facility, therefore increasing the flexibility of the facility.
Data availability statement
The raw data supporting the conclusion of this article will be made available by the authors, without undue reservation.
Author contributions
Conceptualization: MR, SD, and JL; Methodology: MR, SD, and JL; Formal analysis and investigation: MR, SD, and JB; Writing—Original Draft: MR; Writing—Review and Editing: MR, JL, and SD; Graphics: SG; Funding acquisition: JL; Resources: JL; Supervision: JL.
Funding
This work was funded by the South Carolina Smartstate Center for Strategic Approaches to the Generation of Electricity (SAGE).
Conflict of interest
The authors declare that the research was conducted in the absence of any commercial or financial relationships that could be construed as a potential conflict of interest.
Publisher’s note
All claims expressed in this article are solely those of the authors and do not necessarily represent those of their affiliated organizations, or those of the publisher, the editors and the reviewers. Any product that may be evaluated in this article, or claim that may be made by its manufacturer, is not guaranteed or endorsed by the publisher.
References
Abdul Samad, N. A. F., and Saleh, S. (2022). Analysis of volatile composition released from torrefaction of empty fruit bunch. Mater Today Proc. 57, 1202–1207. doi:10.1016/j.matpr.2021.10.462
Baekeland, L. H. (1909). The synthesis, constitution, and uses of bakelite. J. Industrial Eng. Chem. 1, 149–161. doi:10.1021/ie50003a004
Biswas, B., Pandey, N., Bisht, Y., Singh, R., Kumar, J., and Bhaskar, T. (2017). Pyrolysis of agricultural biomass residues: Comparative study of corn cob, wheat straw, rice straw and rice husk. Bioresour. Technol. 237, 57–63. doi:10.1016/j.biortech.2017.02.046
Cataluña, R., da Silva, R., de Menezes, E. W., and Ivanov, R. B. (2008). Specific consumption of liquid biofuels in gasoline fuelled engines. Fuel 87, 3362–3368. doi:10.1016/j.fuel.2008.04.041
Chen, Z., Wang, M., Ren, Y., Jiang, E., Jiang, Y., and Li, W. (2018). Biomass torrefaction: A promising pretreatment technology for biomass utilization IOP Conf. Ser. Earth Environ. Sci., 113. Bristol, UK: IOP Publishing, 12201.
Drugkar, K., Rathod, W., Sharma, T., Sharma, A., Joshi, J., Pareek, V. K., et al. (2022). Advanced separation strategies for up-gradation of bio-oil into value-added chemicals: A comprehensive review. Sep. Purif. Technol. 283, 120149. doi:10.1016/j.seppur.2021.120149
Frank, R. L., and Seven, R. P. (1949). Pyridines. IV. A study of the Chichibabin synthesis. J. Am. Chem. Soc. 71, 2629–2635. doi:10.1021/ja01176a008
Frolova, E. A., Kondakov, D. F., Orlova, V. T., Avdyushkina, L. I., Bykov, A. V., and Danilov, V. P. (2013). Design of deicing reagents based on alkali and alkaline-earth metals and ammonium formates, acetates, and nitrates. Theor. Found. Chem. Eng. 47, 422–427. doi:10.1134/s0040579513040076
Humphreys, J., Lan, R., and Tao, S. (2021). Development and recent progress on ammonia synthesis catalysts for Haber–Bosch process. Adv. Energy Sustain. Res. 2, 2000043. doi:10.1002/aesr.202000043
Kim, J.-S. (2015). Production, separation and applications of phenolic-rich bio-oil–a review. Bioresour. Technol. 178, 90–98. doi:10.1016/j.biortech.2014.08.121
Liu, A., Jones, R. J., Malzer, G. L., and Rehm, G. M. (1997). Effect of zinc ammonia acetate on germination and early seedling growth of three maize genotypes. J. Plant Nutr. 20, 1551–1566. doi:10.1080/01904169709365356
Mariscal, R., Maireles-Torres, P., Ojeda, M., Sádaba, I., and Granados, M. L. (2016). Furfural: A renewable and versatile platform molecule for the synthesis of chemicals and fuels. Energy Environ. Sci. 9, 1144–1189. doi:10.1039/c5ee02666k
Matyjewicz, B., Świechowski, K., Koziel, J. A., and Białowiec, A. (2020). Proof-of-Concept of high-pressure torrefaction for improvement of pelletized biomass fuel properties and process cost reduction. Energies (Basel) 13, 4790. doi:10.3390/en13184790
Mcgill, C. K., and Rappa, A. (1988). Advances in heterocyclic chemistry. Amsterdam, The Netherlands: Elsevier, 1–79. Advances in the chichibabin reaction.
Melse, R. W., and Ogink, N. W. M. (2005). Air scrubbing techniques for ammonia and odor reduction at livestock operations: Review of on-farm research in The Netherlands. Trans. ASAE 48, 2303–2313. doi:10.13031/2013.20094
Panwar, N. L., and Paul, A. S. (2021). An overview of recent development in bio-oil upgrading and separation techniques. Environ. Eng. Res. 26, 200382–200390. doi:10.4491/eer.2020.382
Park, L. K.-E., Ren, S., Yiacoumi, S., Ye, X. P., Borole, A. P., and Tsouris, C. (2016). Separation of switchgrass bio-oil by water/organic solvent addition and pH adjustment. Energy & Fuels 30, 2164–2173. doi:10.1021/acs.energyfuels.5b02537
Ren, S., Lei, H., Wang, L., Bu, Q., Chen, S., Wu, J., et al. (2013). The effects of torrefaction on compositions of bio-oil and syngas from biomass pyrolysis by microwave heating. Bioresour. Technol. 135, 659–664. doi:10.1016/j.biortech.2012.06.091
Rosanoff, M. A., Gulick, L., and Larkin, H. K. (1911). The preparation of acetamide. J. Am. Chem. Soc. 33, 974–977. doi:10.1021/ja02219a018
Shankar Tumuluru, J., Sokhansanj, S., Hess, J. R., Wright, C. T., and Boardman, R. D. (2011). Review: A review on biomass torrefaction process and product properties for energy applications. Ind. Biotechnol. 7, 384–401. doi:10.1089/ind.2011.7.384
Turner, D., Xu, H., Cracknell, R. F., Natarajan, V., and Chen, X. (2011). Combustion performance of bio-ethanol at various blend ratios in a gasoline direct injection engine. Fuel 90, 1999–2006. doi:10.1016/j.fuel.2010.12.025
Ukaew, S., Schoenborn, J., Klemetsrud, B., and Shonnard, D. R. (2018). Effects of torrefaction temperature and acid pretreatment on the yield and quality of fast pyrolysis bio-oil from rice straw. J. Anal. Appl. Pyrolysis 129, 112–122. doi:10.1016/j.jaap.2017.11.021
Wahid, F. R. A. A., Harun, N. H. H. M., Rashid, S. R. M., Samad, N. A. F. A., and Saleh, S. (2017). Physicochemical property changes and volatile analysis for torrefaction of oil palm frond. Chem. Eng. Trans. 56, 199–204. doi:10.3303/CET1756034
Wang, S., Wang, Y., Cai, Q., Wang, X., Jin, H., and Luo, Z. (2014). Multi-step separation of monophenols and pyrolytic lignins from the water-insoluble phase of bio-oil. Sep. Purif. Technol. 122, 248–255. doi:10.1016/j.seppur.2013.11.017
Weiss, M. (1952). Acetic acid—ammonium acetate reactions. An improved chichibabin pyridine synthesis1. J. Am. Chem. Soc. 74, 200–202. doi:10.1021/ja01121a051
Wigley, T., Yip, A. C. K., and Pang, S. (2017). A detailed product analysis of bio-oil from fast pyrolysis of demineralised and torrefied biomass. J. Anal. Appl. Pyrolysis 123, 194–203. doi:10.1016/j.jaap.2016.12.006
Wilburn, R. T., and Wright, T. L. (2004). SCR ammonia slip distribution in coal plant effluents and dependence upon SO {sub 3. Power Plant Chem. 6.
Keywords: bio-oil upgrading, ammonia scrubbing, bio-fuel production, torrefaction, bio-oil separation
Citation: Royko MM, Drummond SM, Boyt J, Ghoreishian SM and Lauterbach J (2022) Novel process for the upgrading of model torrefaction bio-oils using ammonia. Front. Energy Res. 10:1088902. doi: 10.3389/fenrg.2022.1088902
Received: 03 November 2022; Accepted: 09 December 2022;
Published: 22 December 2022.
Edited by:
Haiping Yang, Huazhong University of Science and Technology, ChinaCopyright © 2022 Royko, Drummond, Boyt, Ghoreishian and Lauterbach. This is an open-access article distributed under the terms of the Creative Commons Attribution License (CC BY). The use, distribution or reproduction in other forums is permitted, provided the original author(s) and the copyright owner(s) are credited and that the original publication in this journal is cited, in accordance with accepted academic practice. No use, distribution or reproduction is permitted which does not comply with these terms.
*Correspondence: Jochen Lauterbach, bGF1dGVyYWpAY2VjLnNjLmVkdQ==