- 1State Grid Xiongan New Area Electric Power Supply Company, Xiongan New Area, China
- 2Huzhou Power Supply Company of State Grid Zhejiang Electric Power Company Limited, Huzhou, China
With the motivation of electricity marketization, the demand for large-capacity electrochemical energy storage technology represented by prefabricated cabin energy storage systems is rapidly developing in power grids. However, the designs of prefabricated cabins do not initially fit for the requirement of grid energy storage in terms of manufacturing and implementation, resulting in difficulties in condition monitoring and having high risks of fire failures. It is necessary to develop a modularized and intelligent integration technology for cabin-type energy storge in MW ∼ GW for the deep embeddedness in power grid. With the core objective of improving the long-term performance of cabin-type energy storages, this paper proposes a collaborative design and modularized assembly technology of cabin-type energy storages with capabilities of thermal runaway detection and elimination in early stage, classified alarm of system operation status based on big data analysis, and risk-informed safety evaluation of cabin-type energy storage. Research in this paper can be guideline for breakthrough in the key technologies of enhancing the intrinsic safety of lithium-ion battery energy storage system based on big data analysis, proposing a prototype of novel energy storage system suitable for applications in power grid with high proportion of renewable energy.
Introduction
In recent years, electrochemical battery type energy storage has flourished all around the world, particularly huge demands are raised for applications in power plants, substations and on the user side (Faisal et al., 2018; Li and Han, 2016). With increasing penetration of renewable energies and gradually formation of electricity market-based mechanisms in developing countries, the demand for energy storage in power grid would be further expanded (Faisal et al., 2018). Among all the available types of large-scale energy storage technologies, electrochemical batteries are the primary choice for power grids, since they are relatively low in cost, easy to produce in large-scale and the technical feasibility is mature (Horiba, 2014; Din et al., 2017; Hannan et al., 2018). However, at present the electrochemical batteries are directly refitted from the one used in electric vehicle industries, problems such as inadequate preparation of procurement standards, mismatched control systems and failure to keep up with operation and maintenance technology have already emerged in the practical applications (Gavriluta et al., 2014). Most of the manufacturers continued to design energy storages for power industries based on electric vehicle technologies. There are significant differences in the working conditions and potential threats when the batteries are embedded to power grid, leading to the onerous situations of difficult power quality control, huge maintenance investment and high thermal runaway risks. It is necessary to develop a modular and universal integrated technology to promote and standardize the development of grid energy storage technology and achieve the core goal of improving the intrinsic safety of energy storage devices.
The earliest application of prefabricated cabin type energy storage in power grids is originated in Europe and North America, where the energy storage container (ESC) technology was used early on to facilitate on-site applications. Battery packs and ancillary measures are formed as separated energy storage units for peak shaving and frequency regulation (Qi et al., 2018; Zhu et al., 2019). At present, prefabricated cabins used in power network can mainly be divided into two types, i.e., integrated cabin-type and split-arranged cabin-type energy storages (Fioravanti et al., 2020). The former integrates battery packs, power conversion system (PCS) and transformers in one cabin for applications with small capacity and low voltage, which are often commonly used for user-side energy storage projects (Cassani and Williamson, 2010). The latter is generally used for energy storage devices with relatively high voltage and large capacity, which are often installed intensively near the generation and transmission networks. At present, prefabricated cabin type energy storge is still only a kind of customized products, which are generally designed, manufactured, and debugged by battery manufacturers according to characteristics of their signature products. The technical problems including poor compatibility with different battery types and lack of standardization retard the further development of cabin-type energy storges in power grid. What is more, due to the large arbitrariness of the internal functions and complex layout of the prefabricated cabin, the automatic operation and control cannot be realized. The lack of precise condition monitoring and remedial measures results in high thermal runaway risks. In fact, serious fire failures leading to the destructions of the entire energy storage power stations have occurred all around the world, such as the ruining of 25 MWh energy storage power station in Jimei, Beijing, occurred in April 2021 (May et al., 2018).
To address the above problems, the paper intends to study the thermal runaway evolutionary disaster-causing mechanism and safety rating method applicable to lithium-ion battery-based cabin-type energy storage system, as well as the risk perception, multi-level protection and safety linkage technology, and build a whole-life safety performance evaluation and certification system to comprehensively improve the safety and reliability of energy storage system operation. The expected results of this paper include heat accumulation state assessment technology for lithium-ion batteries of different levels, thermal runaway segmentation barrier technology for energy storage batteries based on thermal spread characteristics, thermal runaway sign capture technology for lithium-ion batteries under massive working conditions, advanced fire extinguishing technology based on lithium-ion battery fire characteristics, and safety risk probability rating technology for full-size energy storage battery systems (ESBS) under diversified working conditions. The optimal design proposed in this paper can be applied in the field of energy storage system operation and energy storage equipment development to continuously promote the technological innovation of intelligent energy storage and support the clean transformation of energy structure and energy consumption revolution with the target of “double carbon”.
Structure and Working Principle of Prefabricated Cabin Type Energy Storage System
Large-scale energy storage installations generally consist of two components, ESBS and PCS. For indoor projects, they can be deployed in dedicated rooms or basements, whereas for most outdoor projects, prefabricated cabin technology is used, which can contain the entire energy storage system. The cabins are directly modified from freight containers and are divided into small chambers with cabinets on the floor. Sliding rails are installed on the top, which are equipped with power distribution, heating ventilation and air-conditioning (HVAC), fire protection and monitoring systems. For energy storage system with small capacities, PCS and ESBS can be arranged in the same compartment, whereas for battery systems with large capacity and high voltage, PCS needs to be arranged in a separate compartment.
An ESBS is generally composed of multiple battery clusters. Each cluster includes multiple battery modules, and each battery module is composed of multiple single batteries in series or parallel, commonly known as battery packs. The charging and discharging of the battery are controlled by the battery management systems (BMS). BMS is the core of the battery system (Sylvestrin et al., 2021). It is usually divided into multiple levels. The host can be deployed in a separate cabinet. The second-level control and the third-level control correspond to the battery clusters and batteries, respectively. The common structure of a 500-kW cabin-type energy storage system is shown in Figure 1.
It can be seen from Figure 1 that in the energy storage system, the prefabricated cabin is the carrier of the energy storage devices, the most basic component of the energy storage system, and most importantly the basic guarantee to ensure the reliable operation of the battery pack (Degefa et al., 2014). Its interior can be divided into six subsystems, namely battery system, converter system, power distribution system, control system, monitoring system and fire-extinguishing system. The prefabricated cabin energy storage system has standardized size, compact structure, relatively small occupied area, and convenient transportation and installation, so it has been generally accepted by power grid users (Zhang et al., 2021). However, in recent years, some technical problems in terms of safe control and operation have also been discovered, which are described as following.
1) High risk of battery fire
Batteries are the core of energy storage. Due to their vulnerable internal structure and high energy density, fire failure is almost an unavoidable risk for ESBS (Lyu et al., 2021). However, research on fire failure orientations and early detections is very few at present, with a lack of mature technologies for the improvements in mechanism understanding and protective measures for fire accidents.
2) Inadequate safeguards of energy storage devices
The safety guarantee system of energy storage devices is not yet refined. The sensitivity of defects detection and warning system is not sufficient, intelligent monitoring of life-cycle performance is not in place, and the fire protection as well as safety measurement system is not effective, resulting in frequent operation safety problems, which seriously limits the promotion and application of cabin-type energy storage technology (Liang et al., 2017).
3) Insufficient detection capability and automation of the monitoring system
The monitoring and automatic control system is the guarantee for the safe operation of energy storage devices, but at present the automation level of prefabricated cabin type energy storage devices is relatively low, the monitoring system is not perfect, it is not yet possible to achieve automatic condition diagnosis and risk warning, unmanned operations cannot be achieved and result in huge costs in condition monitoring.
4) Insufficient standardization level of prefabricated cabin design
In engineering practice, equipment versatility, standardization and modularity are among the main features that ensure high product maturity, quality, and reliability, which not only facilitate operation and maintenance and asset management for the user, but also improve the degree of specialization and manufacturing level of the manufacturer. However, due to a number of factors such as battery type, technical route and cost control, the actual configuration of energy storage prefabricated modules is often highly individualized and the level of monitoring and automation is weak, thus causing inconvenience to operation and maintenance and safety management, as well as being a source of many potential problems.
It is therefore necessary to develop a modular and universal prefabricated module energy storage technology system for different battery types and different operational requirements, in order to improve the safety and stability of electrochemical energy storage equipment.
Theoretical and Practical Basis for the Optimal Design of Prefabricated Cabins
Basic Theory of Lithium Battery Failure
The main cause of lithium-ion battery failure is the thermal runaway accident of the battery (Hammar et al., 2010). Thermal runaway is caused by the fact that the rate of heat generation in a battery is much higher than the rate of heat dissipation, resulting in a large amount of heat accumulations and cannot be dissipated in time. In essence, thermal runaway is a positive energy feedback loop, i.e., an increase in temperature causes the system to get hotter, which in turn causes the system to get hotter. Battery thermal runaway can be divided into three stages, as shown in Figure 2.
In stage 1, internal battery thermal runaway occurs. Due to internal short circuit, external heating, or the battery itself in the high current charging and discharging of its own heat, the internal temperature of the battery rose to about 90–100°C, the lithium salt began to decompose. The charging of carbon anode chemical activity is very high, which is close to the lithium metal. Meanwhile, the surface of the SEI film begins to decompose under the high temperature, lithium ions embedded in graphite also react with electrolyte and binder, which further push the temperature of battery to approximately 150°C. At this temperature, new violent exothermic reactions take place, such as the massive decomposition of the electrolyte to generate more by-products, which would further catalyze the decomposition of organic solvents. In stage 2, battery bulge stage occurs. When the battery temperature reaches above 200°C, the cathode material decomposes, releases a large amount of heat and gas, and continues to warm up. At 250–350°C, the embedded lithium state negative electrode begins to react with the electrolyte. In stage 3, battery thermal runaway begins. Cathode materials in charging state begins to react by violent decomposition, the electrolyte undergoes a violent oxidation reaction, releasing a large amount of heat, generating high temperatures and large amounts of gas, and the battery combusts and explodes.
Several characteristic temperatures, i.e., self-generated thermal onset temperature Tonset, thermal runaway temperature TTR and maximum temperature Tmax can be used to assess the thermal runaway characteristics of the battery. Tonset is the onset temperature of self-generation, i.e., the temperature at which the self-generation rate of the battery is higher than 0.02°C/min. Above this temperature, the battery would experience significant self-generation; TTR is the thermal runaway temperature of the battery, generally defined as the temperature at which the self-generation rate of the battery is higher than 1°C/min. After this temperature is reached, the battery would experience a violent temperature rise, which may be as high as 105°C/min. Tmax is the maximum temperature in the thermal runaway process, which can be as high as 1,000°C.
Basic Theory of Battery Ageing
The ageing of lithium-ion batteries is externally manifested by capacity decay and increased internal resistance, and its internal ageing mechanism includes the loss of positive and negative active materials and the loss of available lithium ions, as shown in Figure 3.
Under different ageing paths, the battery ageing process and changing trends of external characteristics are different, and the consequent changes in safety performance of the batteries are also different. The ageing paths can be divided into two types: cyclic ageing and storage ageing (Šeruga et al., 2021). The effects of these two types of ageing paths on the safety performance of batteries are discussed as following. The relationship between battery ageing mechanisms and safety performance is described in Table 1.
1) The effects of cyclic ageing on battery safety performance
Under ambient/high temperature cyclic ageing conditions, the battery’s resistance to electrical abuse such as overcharging and short-circuiting deteriorates. The main reason for this deterioration is due to the increase in battery internal resistance, which leads to an increase in joule heat production under electrical abuse and makes it easier for thermal runaway to occur. Previous research shows that the safety performance of the battery under mechanical abuse such as pinning and squeezing does not change much before and after the cyclic ageing, indicating that the mechanical characteristics of the battery basically do not change with cyclic ageing. The changes in thermal stability of the battery under ambient/high temperature cyclic ageing conditions are related to the material system. Some studies show that after ambient/high temperature cyclic ageing, Tonset and TTR of the battery both decrease to a certain extent, and the self-generated heat rate also increases slightly, indicating that the battery after cyclic ageing is more prone to self-generation and thermal runaway under abnormal temperature shock. Meanwhile, some other studies show that once ambient/high temperature cycling ageing occurs, the rate of self-heat generation decreases and the thermal stability of the battery improves. The main reason for this difference is the change in the negative SEI film during cycling ageing, where the non-stable components of the SEI film on the surface of the negative electrode of some batteries gradually transform into stable components, and the SEI film gradually becomes stable, which can better protect the graphite negative electrode and improve the thermal stability of the battery. Meanwhile the SEI film on the surface of the negative electrode of some batteries continuously breaks down during cycling and regenerates a new unstable SEI film, which gradually weakens the protective effect on the graphite negative electrode. The negative electrode starts to react with the electrolyte at a lower temperature, and the thermal stability of the battery decreases. Some batteries would experience lithium precipitation from the negative electrode under high-rate charging, resulting in a decrease in the thermal stability of the whole ESBS.
Even low temperature cyclic ageing has significant effects on the safety performance of the battery. Studies have shown that once low temperature cyclic ageing occurs, Tonset would drop significantly, and within the normal range of use, which is generally within 50°C, self-generation of heat may occur, and the rate of heat generation increases significantly, leading to the sharply decreased thermal stability of the battery. The main reason for the decrease in the thermal stability of the battery by low temperature cycling ageing is the precipitation of lithium on the surface of the negative electrode, which is very active and can react with the electrolyte at a lower temperature, causing a decrease in the starting temperature of the battery and a sharp increase in the rate of heat production, which seriously endangers the safety of the battery.
(2) The effects of storage aging on battery safety performance
Previous studies show that Tonset increases and the self-generated thermal rate decreases to a certain extent by batteries aged in storage at ambient/high temperature, and the increase in Tonset and the decrease in self-generated thermal rate become more obvious with the increase in storage time, indicating that the thermal abuse performance of the batteries after storage aging improves. The increase in thermal stability of the battery by storage ageing is mainly due to the gradual stabilization of the SEI film on the surface of the negative electrode. Under storage conditions, the SEI film of the negative electrode does not rupture and regenerate, and the non-stable components gradually transform into stable components during long storage. However, the battery may generate gas during storage ageing, causing the battery to swell and affecting its safety. Under electrical abuse such as overcharging and short-circuiting, similar to cyclic ageing, the joule heat production of the battery increases due to the increase in internal resistance, resulting in a potentially decrease in the electrical abuse resistance of the battery after storage ageing.
Characteristics, Testing Methods and Principles of Battery Management Systems
For cabin-type energy storage, batteries are bound to change in performance over the course of their life, so battery condition and prediction methods are essential for safe and reliable long-term trials of energy storage units in power grid. Battery management systems (BMS) use battery state of health (SOH) to measure the performance of individual cells or whole batterie packs, defining the initial factory SOH of the battery as 100% and expressing the gradual decay of battery health as a percentage. Based on the battery test method and test data, and combined with the decay mechanism of the battery material, a decay model with a high degree of agreement with the measured data can be established, so as to make accurate prediction of the battery health status and life. At present, key parameters such as internal resistance or impedance, charging/discharging capacity, multiplier and cycle times are mainly used for battery life state assessment, either using a single parameter or as a combination of parameters.
Commonly used testing methods of BMS include charging/discharging curve analysis method, Equivalent circuit model parameter method, electrochemical impedance spectroscopy and diffusion coefficient analysis method (Subburaj et al., 2016). In addition, the extended Kalman filter are generally used to identify the equivalent circuit model, and the battery capacitance parameters are used to derive SOH estimates. The voltage response curve of double pulse discharge is used to study the amount of voltage change with the battery cycle life and SOH decay law, and the polarization curve parameters of the pulse can be better used to estimate the SOC and SOH of the battery (Cao and Qahouq 2021).
In summary, SOH prediction methods have their own advantages and disadvantages. Prediction methods based on the differentials in voltage and capacity, electrochemical AC impedance spectrum and diffusion coefficient of the battery can obtain the internal battery ageing state with accuracy, but need to use battery calendar life and cycle life data to build a battery life model, and the testing cost and time of the ageing test are considerable. For extended Kalman filter, adaptive control, neural network can get SOH in high resolution. However, the accuracy of SOH estimation is low because the parameters used in the estimation, such as internal resistance, polarization or capacity, can only represent the battery life state well, but do not fully reflect the battery health state. This shows that the accurate prediction of SOH, which reflects the important characteristics of batteries, is still a difficult problem in battery management technology research, and it is urgent to further improve and innovate battery testing techniques and analysis and evaluation methods to establish a more accurate model to reflect the health status of batteries. An intelligent and accurate condition monitoring system for the batteries embed in the modularized design of cabin-type energy storage system will be discussed in the following sections.
Specific Implementation Programmes
Technical Route for the Modularized Assembly Scheme
The technical roadmap for the modularized assembly proposed in this study is shown in Figure 4. Overall, four main tasks are aimed to be achieved by this novel design, i.e., energy storage system disaster evolution and risk perception, multi-level protection and safety linkage of energy storage system, and whole life cycle safety classification and state risk control of energy storage system. In order to achieve these goals, this design can be divided into four parts, i.e., evolutionary disaster-causing mechanism confirmation and safety evaluation of thermal runaway of lithium-ion batteries for full-size cabin-type energy storage system, thermal runaway barrier technology and performance evaluation for lithium-ion batteries, fault detection and diagnosis based on big data analysis and whole life cycle classification warning, and safety performance evaluation level certification and practical applications of cabin-type energy storage. The detailed implementations of these four parts will be described in the following sections.
Intrinsically Safe Technologies for Cabin-Type Energy Storage Based on Fire Protection
This paper takes lithium-ion batteries as a typical research object and proposes to carry out corresponding technical research on the characteristics of this kind of battery.
Fire Failure Mechanism and Safety Rating of Cabin-Type Energy Storage
The complex and changing conditions of large-scale grid energy storage applications impose higher requirements on the thermal stability of lithium-ion batteries at different device levels. In order to guarantee the safety performance of ESBS in severe working conditions, a safety evaluation and rating of cabin-type energy storage based on understanding of the mechanisms behind fire failures is proposed, as shown in Figure 5. Key technologies involved in this module are described as following.
1) Measurement technology of thermal runaway state under diversified working conditions
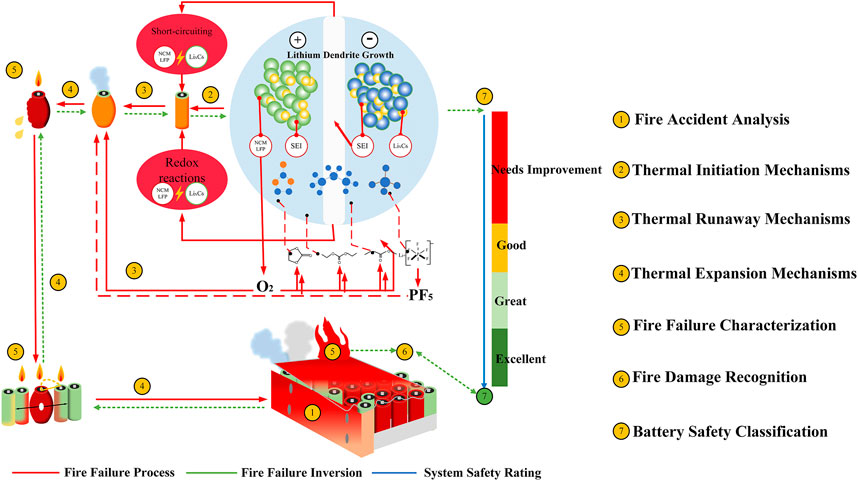
FIGURE 5. Safety evaluation and rating scheme of cabin-type energy storage based on fire failure mechanisms.
The extended adiabatic accelerated calorimetry technique is used to accurately obtain the thermodynamic properties of materials based on the heat accumulation state of lithium-ion batteries of different layers. The data are obtained by using the extended adiabatic accelerated calorimetry technique, and the electrochemical data such as voltage, current and impedance during the thermal runaway process are obtained by an external circuit. The thermal properties including initial decomposition fraction, exothermic rate, heat of reaction, activation energy, temperature and pressure curves with time are obtained. The accuracy of this measurement technology is expected to be up to ±1°C for the temperature measurement and 0.005°C min−1 for the temperature rise rate measurement at each stage of the safety threshold. At the same time, the external circuitry collects real-time battery test operation data (such as voltage, current and impedance), measures battery breakage pressure limit, and analyze the composition of leaking explosive gas, to establish a full-size cabin-type energy storage system to establish a scientific thermal failure timing model for full-size energy storage systems.
2) Equivalent circuit algorithm for internal short-circuit induced thermal runaway
Based on the simulation of the internal electrochemical behavior of the battery, the equivalent internal short circuit (IS) resistance can be quantitatively evaluated. The smaller the ISC equivalent resistance is, the higher the probability and severity of thermal runaway generation. The spontaneous ISC progressive evolution mechanism of the full life-cycle is investigated by simulated alternative ISC test method, and the internal short-circuit identification rate is expected to be higher than 99%. The short-circuit recognition rate is expected to be higher than 99.5%, and the internal short-circuit faults that may cause serious thermal runaway can be detected 30 min in advance.
3) Evaluation of fire hazard level by mixed measurement of multiple time scales
Based on the fire failure characteristics from battery cells, modules, and soft packs to prefabricated module, study the transformation rate between the expected fire path of the system to the accidental fire path, evaluate techniques for self/reciprocal acceleration hazard levels of different functional modules.
Thermal Barrier Technology and Performance Evaluation for Lithium-Ion Batteries
In order to stop the thermal runaway of batteries from becoming a disaster and to slow down the spread rate of thermal runaway, the key is to fully understand the electrochemical mechanism of thermal abuse, the establishment of three-dimensional model of the thermal spread state, involving electrochemical reactions, aerodynamics and explosion kinetic theory. In addition, the selection of safe and efficient thermal barrier materials and technologies also needs to be considered. Eventually, based on the optimal configuration of high-voltage high-power DC power fuse, relay and other relay protection circuit topology, comprehensive consideration of the battery module safety isolation design reliability, effectiveness and costs, balance system specific energy, specific power and safety margin requirements, an optimized battery module architecture with different barrier forms and methods, matching the modular management system with active safety control is proposed in this paper, as shown in Figure 6. Key technologies involved in this module are described as following.
Firstly, we study the characteristics of combustible gas injection, flame characteristics and heat diffusion paths during thermal runaway of battery, and establish the dynamic model of combustible gas injection and heat diffusion under thermal runaway of battery. Secondly, based on the behavior and characteristics of battery thermal runaway diffusion, study the barrier effect of various materials on gas, fire and heat and design barrier devices; construct a three-in-one barrier technology of thermal barrier, heat release and valve leakage channel to effectively control the spread of battery thermal runaway and open flame generation. Again, we study the active isolation protection technology, and then complete the development of corresponding battery modules and battery clusters. Combining electrical barrier technology and thermal barrier technology, we design efficient, active and safe battery modules and clusters to reduce the risk of total thermal runaway generated by single battery thermal runaway. Finally, based on the system topology architecture and thermal runaway defense technology, the impact of battery arrangement on the overall safety of the energy storage system will be studied to improve the safety of the energy storage battery system.
Thermal Runaway Fault Diagnosis Based on Feature Migration and Big Data Analysis
Due to the progressive coupling concurrent correlations of the lithium-ion battery thermal runaway faults, and weak signs in the early stage, detections of high-value signs in thermal runaway become extremely difficult. Fault detection and diagnosis accuracy is also low, resulting in the poor hierarchical warning reliability for full life-cycle monitoring. In order to solve the above problems. this paper focuses on lithium-ion battery thermal runaway signs set construction, fault detection and diagnosis technology development. A big data monitoring system for the full life cycle hierarchical warning and early fault detection is proposed in this paper. Details of the system are presented in the following sections.
The intelligent fault diagnosis method based on big data analysis is shown in Figure 7. A deep residual separable convolution based on “thermal-mechanical-electrical-aging” multimodal data is proposed. The construction of a thermal runaway sign set for lithium-ion batteries is carried out by using deep residual separable convolution and attentional statistical pooling network. Based on aging, overcharge/discharge Based on collected data of aging, overcharging/discharging, internal short-circuit, high/low temperature thermal abuse, extrusion and deformation, and large rate charging, a multimodal training set is created with battery capacity, power, voltage, temperature, current, internal resistance, chemical gas concentration, battery deformation image and near-infrared (NIR) spectra. Further, the multi-batch data organization is achieved by normalization, stitching, alignment and scaling. The deep residual separable convolution module and the “squeeze-expansion” module are used to build multi-channel stacked deep convolutional neural networks, create attention statistical pooling operators, and embed high-dimensional multi-channel abstraction of lithium battery. The loss function with metric feature interval is designed to achieve semi-supervisory learning of the network to capture the thermal runaway signs with high recognition and strong correlation.
After the “thermal-mechanical-electrical-aging” multimodal dataset is successfully created, with the help of deep residual separable convolution and attention statistical pooling network, the thermal runaway fault diagnosis of lithium-ion battery can be carried out. The source domain dataset consists of experimental test thermal runaway signs, and the target domain dataset consists of a small number of actual operational thermal runaway signs are created. The loss function with the maximum mean difference index is designed to reduce the distribution difference between the source and target data features, and to realize the migration from the source to the target data features. Based on the same distribution of fault features after migration, the bi-directional long- and short-term neural network is used to realize the multi-fault diagnosis of thermal runaway such as aging, overcharging/discharging and internal short circuit of Li-ion battery under actual operating conditions. The detailed implementation of the fault diagnosis method is shown in Figure 8.
Universal Application Architecture of Proposed Collaborative Design and Modularized Assembly Scheme for Cabin-Type Energy Storage System
With intrinsic safety enhancement as the core objective of the modularized design of prefabricated cabin type energy storage, this section discusses the requirements of hardware and software modules of prefabricated chambers based on the key technologies proposed previously, forming a generalized technical solution for the collaborative design.
Safety Design of Cabin-Type Energy Storage
The first task for the practical application of cabin-type energy storage is the safety design for inspection and installation. For the optimal design, the selection principles and guidance for the overall structure, internal layout and facility foundation design of the prefabricated module are proposed for the classification of the application scenarios on site. The protection standards for the prefabricated module, the battery cluster, the control cabinet and the monitoring system are proposed to match the guidelines according to the application needs. Further, the installation process and process guidance for the energy storage prefabricated module are developed to ensure the safe handover of the energy storage system. The detailed process for the design and selection of the prefabricated module body are shown in Figure 9.
The design of battery module integration also needs to be carried out, which mainly includes the condition sensor module, thermal management module and monitoring software module. The condition monitoring module is mainly evaluating BMS management, whereas thermal management module is mainly evaluating heat flow detection and thermal field detection analysis. The optimization of the thermal balance design of the battery module is one of the key technologies for thermal management. It is proposed to study the relationship between the forced convection control means and the overall temperature difference, to improve the homogenization of the battery temperature and to avoid the rapid ageing caused by the difference in working conditions due to the large temperature difference and thus the imbalance of the battery working conditions.
Eventually, modularized design is achieved. Based on intrinsic safety, prefabricated cabin design module plan is proposed, including the design ideas of electrochemistry, structure, thermal management, BMS, safety, application system and other necessary modules. Classification of the designs is conducted based on the application requirements and application scenarios of the energy storage system. The selection principles and typical integration schemes of the hardware composition, coordination system, interface standard and other modules of the energy storage system are carried out, finally the generalized design scheme is formed. The preliminary idea of the module design is shown in Figure 10.
Prefabricated Cabin Safety Design Performance Test and Safety Assessment
Prior to practical application of the novel design of prefabricated cabin type energy storage, a series of performance tests need to be carried out, which include optimization of the operating system, routine tests of equipment and system circuits of the battery management system, checking the measurement accuracy and analysis capabilities of electrical signals such as voltage, charge and discharge status. In addition, a thermal management test system is also necessary including reasonably distributed temperature sensing devices, with the ability to sense, detect, analyze and process the temperature in the cabin. A humidity control system is embedded with reasonably arranged humidity sensors and dehumidification devices. Various abnormal signs of gas contents before and after the battery burns are monitored continually with a corresponding gas and smoke detection and analysis platform, particularly carbon dioxide, organic solvents, and solid particles need to be investigated. An optical sensing system by using advanced flame sensors with high sensitivity to weak lights and open flames is also established. Through the analysis and comparison of the above technologies for key signal parameters such as electricity, temperature, gas, humidity, and optics, the relationship and complementarity between those parameters can be clarified, and eventually a safety evaluation system for prefabricated cabin performance testing with strong complementarity, high precision and good stability can be proposed, as shown in Figure 11.
The constant performance of BMS is the guarantee for cabin-type energy storage system safety assessment. This paper establishes an advanced BMS test platform, as shown in Figure 12, which includes installation test bench, constant current source, constant voltage source, control cabinet, simulated battery, monitoring station and other components. The hardware, software, function, and reliability of the BMS can be checked through simulation of different temperature, humidity, charge and discharge conditions. It is also able to check the actual working conditions of the BMS in the prefabricated cabin by using high-precision electrical sensors to measure the voltage, current, resistance, capacity and other electrical signals of some cells in the prefabricated cabin, and compare them with the prefabricated cabin BMS test results. By judging the detection sensitivity and accuracy of BMS; use some “questionable cells” to replace the batteries in the prefabricated cabin, and observe the fault detection and responding abilities of BMS when these “questionable cells” are used under abnormal conditions such as overcharging and overheating. The detection effect of the prefabricated cabin BMS on each cell is also tested, and serve as an important criterion for judging the performance of the BMS. The analysis results of the above two aspects are used as the main criteria for evaluating the performance of the prefabricated cabin BMS, and a reasonable and complete BMS evaluation system is established to provide a good guarantee for the safety of the prefabricated cabin storage system.
In practical, a big data monitoring system based on multi-tier microservice architecture is also proposed for cabin-type energy storage, as shown in Figure 13. For precision fault detection and diagnosis and efficient and reliable full-life cycle hierarchical warning needs of ESBS, big data monitoring system for Megawatt-hour-level energy storage based on multi-layer microservice is constructed. The research is based on multi-layer cloud, multi-source heterogeneous industrial big data integration mode, and the construction of multi-process data collection and transmission network based on iot communication gateway and time-sensitive network, to realize standardization of multi-protocol, multi-source heterogeneous and time-sensitive lithium-ion battery data. Eventually the modular on-demand reuse of data and functions and real-time fusion interaction is achieved.
Conclusion
In order to solve the key technical problems that existing in large-capacity prefabricated cabin type energy storage, and meet the grid energy storage requirements in terms of process, technology and quality, a collaborative design and modularized assembly for the cabin-type energy storage is proposed to improve the intrinsic safety of cabin-type energy storage devices, and theoretical analysis is used to aid design optimization. Eventually a safety-centric modular and universal energy storage prefabricated cabin integration technology is achieved. The main contributions of this article are presented as the following.
The dynamic evolution time sequence mechanism of thermal trigger, thermal diffusion and thermal spread of full-size lithium-ion battery system is figured out, under the accident process of energy storage power plant. The graded hazard evaluation technology of multi-time scale heat accumulation causing disaster is developed, comprehensively improving the analysis method of energy storage battery system safety performance level, and proposing the concept of inherent battery safety design.
Battery thermal runaway spreading mechanism, efficient thermal barrier materials and technologies are proposed, which improves battery active safety from thermal spreading level, improves energy storage battery system safety through battery thermal management, as well as achieves electrical topology optimization and structure optimization, and achieves comprehensive improvement of full-size battery, which is upgraded from passive safety to active safety and system safety.
An automatic machine learning and “thermal-mechanical-electrical-aging” multimodal data-based lithium-ion battery life-cycle fault diagnosis and hierarchical early warning method can be realized in the design, which can discover the signs of thermal runaway fault in lithium-ion battery with long and short-term dependence on time series, and reveal its fault characterization evolution and hierarchical early warning mechanism at the big data level.
The risk modeling and evaluation method of energy storage battery system is proposed in this paper, which can significantly improve the inherent safety design concept of the battery. The system is designed to improve the inherent battery safety design concept, rehearse hypothetical battery accidents, set up targeted preventive measures, and implement a “risk aware” energy storage system reliability control system.
Data Availability Statement
The original contributions presented in the study are included in the article/supplementary materials, further inquiries can be directed to the corresponding author.
Author Contributions
The individual contributions of the authors are as follows: data curation, CC; formal analysis, JL; writing (original draft), MG. All authors have read and agreed to the published version of the manuscript.
Funding
This study received funding from Collective Enterprise Science and Technology Project of State Grid Zhejiang Electric Power Co., LTD. (No.2019-HUZJTKJ-19). The funder was not involved in the study design, collection, analysis, interpretation of data, the writing of this article or the decision to submit it for publication.
Conflict of Interest
Author CC was employed by State Grid Xiongan New Area. Electric Power Supply Company. Authors JL and MG were employed by Huzhou. Power Supply Company of State Grid Zhejiang Electric Power Company Limited.
Publisher’s Note
All claims expressed in this article are solely those of the authors and do not necessarily represent those of their affiliated organizations, or those of the publisher, the editors, and the reviewers. Any product that may be evaluated in this article, or claim that may be made by its manufacturer, is not guaranteed or endorsed by the publisher.
References
Cao, Y., and Qahouq, J. A. (2021). Hierarchical SOC Balancing Controller for Battery Energy Storage System. IEEE Trans. Ind. Electro. 68, 9386–9397. doi:10.1109/TIE.2020.3021608
Cassani, P. A., and Williamson, S. S. (2010). Design, Testing, and Validation of a Simplified Control Scheme for a Novel Plug-In Hybrid Electric Vehicle Battery Cell Equalizer. IEEE Trans. Ind. Electro. 57, 3956–3962. doi:10.1109/TIE.2010.2050750
Degefa, M. Z., Millar, R. J., Lehtonen, M., and Hyvönen, P. (2014). Dynamic Thermal Modeling of MV/LV Prefabricated Substations. IEEE Trans. Power Deliv. 29, 786–793. doi:10.1109/TPWRD.2013.2276941
Din, E., Schaef, C., Moffat, K., and Stauth, J. T. (2017). A Scalable Active Battery Management System with Embedded Real-Time Electrochemical Impedance Spectroscopy. IEEE Trans. Power Electro. 32, 5688–5698. doi:10.1109/TPEL.2016.2607519
Faisal, M., Hannan, M. A., Ker, P. J., Hussain, A., Mansor, M. B., and Blaabjerg, F. (2018). Review of Energy Storage System Technologies in Microgrid Applications: Issues and Challenges. IEEE Access 6, 35143–35164. doi:10.1109/ACCESS.2018.2841407
Fioravanti, R., Kumar, K., Nakata, S., Chalamala, B., and Preger, Y. (2020). Predictive-Maintenance Practices: For Operational Safety of Battery Energy Storage Systems. IEEE Power Energ. Mag. 18, 86–97. doi:10.1109/MPE.2020.3014542
Gavriluta, C., Candela, J. I., Citro, C., Rocabert, J., Luna, A., and Rodríguez, P. (2014). Decentralized Primary Control of MTDC Networks with Energy Storage and Distributed Generation. IEEE Trans. Industry Appl. 50, 4122–4131. doi:10.1109/TIA.2014.2315715
Hammar, A., Venet, P., Lallemand, R., Coquery, G., and Rojat, G. (2010). Study of Accelerated Aging of Supercapacitors for Transport Applications. IEEE Trans. Ind. Electro. 57, 3972–3979. doi:10.1109/TIE.2010.2048832
Hannan, M. A., Hoque, M. M., Hussain, A., Yusof, Y., and Ker, P. J. (2018). State-of-the-Art and Energy Management System of Lithium-Ion Batteries in Electric Vehicle Applications: Issues and Recommendations. IEEE Access 6, 19362–19378. doi:10.1109/ACCESS.2018.2817655
Horiba, T. (2014). Lithium-Ion Battery Systems. Proc. IEEE 102, 939–950. doi:10.1109/JPROC.2014.2319832
Li, Y., and Han, Y. (2016). A Module-Integrated Distributed Battery Energy Storage and Management System. IEEE Trans. Power Electron. 1, 8260–8261. doi:10.1109/TPEL.2016.2517150
Liang, Y., Su, J., Xi, B., Yu, Y., Ji, D., Sun, Y., et al. (2017). Life Cycle Assessment of Lithium-Ion Batteries for Greenhouse Gas Emissions. Resour. Conservation Recycling 117, 285–293. doi:10.1016/j.resconrec.2016.08.028
Lyu, N., Jin, Y., Miao, S., Xiong, R., Xu, H., Gao, J., et al. (2021). Fault Warning and Location in Battery Energy Storage Systems via Venting Acoustic Signal. IEEE J. Emerging Selected Top. Power Electro., 1. doi:10.1109/JESTPE.2021.3101151
May, G. J., Davidson, A., and Monahov, B. (2018). Lead Batteries for Utility Energy Storage: A Review. J. Energ. Storage 5, 145–157. doi:10.1016/j.est.2017.11.008
Qi, J., Lai, C., Xu, B., Sun, Y., and Leung, K. -S. (2018). Collaborative Energy Management Optimization toward a Green Energy Local Area Network. IEEE Trans. Ind. Inform. 14, 5410–5418. doi:10.1109/TII.2018.2796021
Šeruga, D., Gosar, A., Sweeney, C. A., Jaguemont, J., Mierlo, J. V., and Nagode, M. (2021). Continuous Modelling of Cyclic Ageing for Lithium-Ion Batteries. Energy 215, 119079. doi:10.1016/j.energy.2020.119079
Subburaj, A. S., Bayne, S. B., Giesselmann, M. G., and Harral, M. A. (2016). Analysis of Equivalent Circuit of the Utility Scale Battery for Wind Integration. IEEE Trans. Industry Appl. 52, 25–33. doi:10.1109/TIA.2015.2463794
Sylvestrin, G. R., Scherer, H. F., and Hideo Ando Junior, O. (2021). Hardware and Software Development of an Open Source Battery Management System. IEEE Latin America Trans. 19, 1153–1163. doi:10.1109/TLA.2021.9461844
Zhang, K., Zhou, B., Or, S. W., Li, C., Chung, C. Y., and Voropai, N. I. (2021). Optimal Coordinated Control of Multi-Renewable-To-Hydrogen Production System for Hydrogen Fueling Stations. IEEE Trans. Industry Appl., 1. doi:10.1109/TIA.2021.3093841
Keywords: optimal desgin, energy storage, safety management, battery failure model, panoramic monitoring
Citation: Chen C, Lai J and Guan M (2022) A Collaborative Design and Modularized Assembly for Prefabricated Cabin Type Energy Storage System With Effective Safety Management. Front. Energy Res. 10:846741. doi: 10.3389/fenrg.2022.846741
Received: 31 December 2021; Accepted: 07 February 2022;
Published: 04 April 2022.
Edited by:
Jian Zhao, Shanghai University of Electric Power, ChinaReviewed by:
Yu Guan, Xi’an Jiaotong University, ChinaMinghe Chi, Harbin University of Science and Technology, China
Copyright © 2022 Chen, Lai and Guan. This is an open-access article distributed under the terms of the Creative Commons Attribution License (CC BY). The use, distribution or reproduction in other forums is permitted, provided the original author(s) and the copyright owner(s) are credited and that the original publication in this journal is cited, in accordance with accepted academic practice. No use, distribution or reproduction is permitted which does not comply with these terms.
*Correspondence: Chen Chen, Y2N4YXNnQDEyNi5jb20=