- 1Key Lab of Industrial Fluid Energy Conservation and Pollution Control (Qingdao University of Technology), Ministry of Education, Qingdao, China
- 2School of Mechanical and Automotive Engineering, Qingdao University of Technology, Qingdao, China
- 3College of Computer Science and Technology, Qingdao University, Qingdao, China
The life test of a complex electromechanical system (CEMS) is restricted by many factors, such as test time, test cost, test environment, test site, and test conditions. It is difficult to realize system reliability synthesis and prediction of a CEMS which consists of units with different life distributions. Aiming at the problems, a numerical analysis method based on the computer simulation and the Monte Carlo (MC) method is proposed. First, the unit’s life simulation values are simulated using the MC method with the given each unit’s life distribution and its distribution parameter point estimation. Next, using the unit’s life simulation values, the CEMS life simulation value can be obtained based on the CEMS reliability model. A simulation test is realized instead of the life test of the CEMS when there are enough simulation values of the CEMS life. Then, simulation data are analyzed, and the distribution of the CEMS life is deduced. The goodness-of-fit test, point estimation and confidence interval of the parameters, and reliability measure are estimated. Finally, as a test example of the wind turbine, the practicability and effectiveness of the method proposed in this paper are verified.
Introduction
Complex electromechanical systems (CEMSs) have been used in industry, civil machinery, aerospace, and so on (Mi et al., 2016; Wang et al., 2022). Reliability synthesis and prediction of CEMSs have long been critical issues within the field of reliability engineering. CEMSs are usually composed of optics, machinery, and electricity (Tang et al., 2021). Some CEMSs have very complex structures, some have huge volumes, some have long service life, and some are expensive (Han et al., 2021). Thus, reliability synthesis and prediction of CEMSs only relying on life testing are limited by multiple factors such as test scheme, test site, test time, test cost, and test conditions. However, at the stage of the project demonstration and initial design of CEMSs, reliability synthesis and prediction of CEMSs are necessary (Fuqiu et al., 2020). Therefore, it challenges the realization of reliability synthesis and prediction of CEMSs.
Since Buehler proposed a reliability synthesis method for a series system with two binomial components (Buehler, 1957), scholars from classical, Bayes, and fiducial schools have conducted a lot of research on reliability synthesis and prediction of systems. The classical school put forward the maximum likelihood estimation (MLE) method, modified maximum likelihood estimation (MML) method, sequential reduction (SR) method, combined MML and SR method (CMSR), and so on (Yu et al., 2013). The MLE method is only applicable to large sample tests, and the failure distribution is an unbounded symmetric normal distribution. The MML method is only applicable to binomial (pass–fail) component systems (Fo and Xiong, 2009). The disadvantage of the SR method is that successive compression of test data leads to information loss, resulting in large estimation variance and a more conservative confidence limit of system reliability (Zhu and J Sh, 1990). The algorithm of the CMSR method is complex, and it is not suitable for the system with zero failure number of unit test data. The Bayes method only solves the reliability interval estimation of binomial or exponential approximation for complex systems (Guo and Wilson, 2013). The fiducial method has been proved unsuitable for system reliability evaluation (Zhou and Weng, 1990). Therefore, it is difficult to use the abovementioned methods to synthesize and predict the CEMSs’ reliability, and reliability synthesis and prediction of CEMSs are still problems in reliability engineering (Peng et al., 2013). Although the Monte Carlo method can easily deal with the reliability synthesis problem of systems with different unit distributions (Yeh et al., 2010), the simple Monte Carlo method, bootstrap method, double Monte Carlo method, and asymptotic method introduced in many studies can only solve the lower confidence limit of system reliability, and the interval estimation problem of system life distribution types and parameters are unsolved (Meng and Wen-Tao, 2021). Despite decades of research, there is still no general method to realize the reliability synthesis and prediction of CEMSs (Kovacs et al., 2019).
It is well known that a CEMS is composed of several units (subsystems), and the system reliability depends on the reliability of its constituent units (subsystems) (Negi and Singh, 2015), (Liu et al., 2015). When the constituent units’ life of CEMS follows different distributions, it is difficult to synthesize and predict the CEMS reliability from units’ reliability data information (Weiyan et al., 2009). Hence, some scholars have conducted a lot of correlational research. For example, Guo et al. (2014) analyzed some theories and methods for system reliability synthesis, and the new idea was proposed for the problem aiming at specific engineering backgrounds. Considering that some CEMSs contain outsourced components, Sun et al. (2018) computed system reliability and component importance measures. According to the equal-principle first and second moment of reliability, Yu et al. (2013) investigated Bayes reliability confidence limit for a series-parallel system consisting of different distribution units. Graves and Hamada (2016) evaluated the likelihood for simultaneous failure time data when monitoring was stopped. In view of the lack of reliability data information of CEMSs, Wilson et al. (2006) and Yuan et al. (2019) discussed how to make full use of limited reliability data information of CMESs to synthesize and predict system reliability. Although scholars have discussed the reliability synthesis and prediction of CEMS from many aspects, there are still challenges by many factors such as difficulty in establishing a reliability model for CMES, lack of reliability data information, high test cost, and so on. It is necessary to be studied further.
In order to solve the above problems and realize the reliability synthesis and prediction of CEMS, a numerical analysis method based on the computer simulation and the Monte Carlo (MC) method is proposed in this article. The remainder of this article is organized as follows: In Section 2, we propose a method to obtain the life simulation values for the constituent units of CEMS when the life distribution types and distribution parameters of constituent units are known. In Section 3, we take a method to obtain the system life simulation value from the units’ life simulation values. One system life simulation value represents a reliability test of CEMS. Computer simulation can be realized instead of life test when there are enough system life simulation values. In Section 4, we carry out the initial selection of CMES life distribution types and goodness-of-fit test. In Section 5, a case study of a CMES is presented to demonstrate the effectiveness of our proposed method. Finally, conclusions are made in Section 6.
Life Simulation Values for the Constituent Units of Complex Electromechanical Systems
It is assumed that a CEMS is composed of n different life distribution units, and the life distribution and the appropriate parameters of each constituent unit are known. The life simulation values for n units are generated using the random variable simulation conversion equation and through Monte Carlo simulation (Yoshida and Akiyama, 2011; Wang et al., 2012; Zhang et al., 2014). According to the common distributions in engineering, such as the exponential distribution, Weibull distribution, normal distribution, logarithmic normal distribution, extreme value distribution, Gamma distribution etc., the respective random variable simulation conversion equations
In order to ensure that all units are independent of each other, the pseudo-random number is computer-generated for each unit and subject to 0-1uniform distribution.
According to the life distribution and parameters of each constituent unit, the life simulation value
In this way, a set of life simulation values of n units can be obtained, and the first simulation values are completed. The m groups of life simulation values are obtained after m cycles.
Life Simulation Values for the Complex Electromechanical Systems
For the CEMS composed of n units, the life simulation value for each unit can be obtained through each simulation, and they are denoted by
where S denotes the CEMS, q denotes the number of the minimum path sets in the CEMS,
Therefore, the life simulation value
where
The minimal path sets of the typical system are shown in Figure 1, and the system has four minimum path sets:
In general, the CEMS is usually considered to be composed of several simple serial or parallel subsystems, and the following equations are established:
where
For any CEMS, the simulation value array
Each simulation can yield a set of life simulation values for the units, and one life simulation value for the system can be obtained by Eq. 2. If r simulations are performed, r life simulation values can be obtained, namely,
Initial Selection of Life Distribution Types for the Complex Electromechanical Systems and Goodness-of-Fit Test
In order to determine the life distribution types for the system, this thesis makes use of the probability graph estimation method and goodness-of-fit test method. First, the probability graph for common distributions is designed and constructed on the computer, and
Data Processing and Initial Selection of Distribution Types
The basic principle for the probability idea design is to linearize the distribution function, and Table 2 shows the linearized conversion equations for seven common distributions. The system life data are drawn in the new coordinate system, respectively. According to the discretization of the fitting line, the life distribution types for the system are initially decided.
To improve the accuracy of statistical inference, the value of
Then
where
The median
The frequency number of the life simulation value for the system in the kth interval
Each scattered data pair
where aj and bj are the linear parameters of the fitting line, and q is the number of the selected probability graphs.aj and bj and the residual sum of squares
where
The values of
Pearson Goodness-of-Fit Test
The goodness-of-fit test should be performed after the initial distribution is determined.
The initial distribution function as
1) The hypotheses are established.
The original hypothesis
2) The point estimate value
The probability for p intervals is calculated as follows:
3) The Pearson
4) When the confidence probability
where v is the degree of freedom,
If
To facilitate the computer analysis, the Fisher approximation of
where
where a0 = 2.3075; a1 = 0.2706; b1 = 0.9922; b2 = 0.0448; and
Engineering Application–System Reliability Prediction on Wind Turbine
An MW wind turbine unit is mainly composed of impeller, gearbox, generator, yaw system, pitch system, brake system, lubrication system, electrical system, and frequency converter in serial connection, and its reliability block diagram (RBD) is shown in Figure 2.
The given life distributions and parameters for all components in the wind power generator unit are listed in Table 3 (Tavner et al., 2007; Spinato et al., 2009; Guo et al., 2012).
According to the relevant parameters of each unit listed in Table 3, the life simulation value for each unit is generated using the simulation conversion equation in Table 1. We set
1) Initial selection of the life distribution types for the wind turbine.
The characteristic data in Table 5 are processed using probability graph estimation to get the residual sum of squares under different distributions,
It is shown in Table 6 that the residual sum of squares for the two-parameter Weibull distribution was the least, and it can be used as the initial distribution.
2) Goodness-of-fit test for the initial distribution.
According to the probability graph estimation,
Given the confidence probability
We can obtain
The hypothesis test is passed at a high probability, and then the life data of this wind turbine follows the two-parameter Weibull distribution, the distribution parameters, the point estimation and the interval estimation of reliability measures can be further solved.
We set
The logarithm is taken from
The constraint conditions are set as
The likelihood equations are established and arranged as
Therefore,
where
As
If
With the given t value, the maximum likelihood estimation for the reliability function
Therefore, the maximum likelihood estimation for the failure rate function
If the confidence probability is set as
where
To simplify the calculation, the shape parameter m can be taken as its maximum likelihood estimation, and it is taken as
When the given confidence probabilities
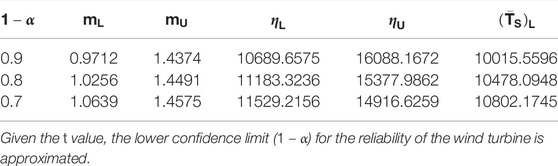
TABLE 7. The confidence interval for the distribution parameter and lower confidence limit for the average life of the wind turbine under different confidence probabilities.
The upper confidence limit (
when t is 1000, 1500, 2000, 2500, and 3000h, and the confidence probabilities
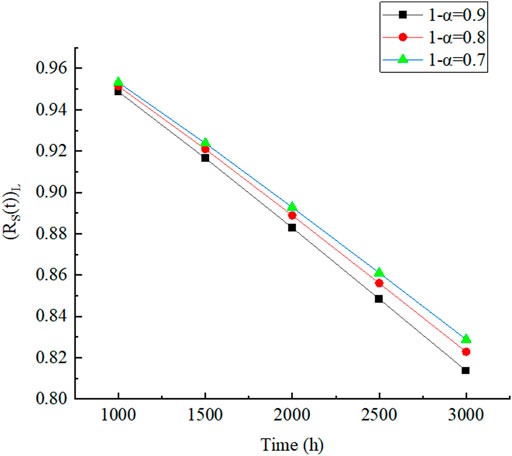
FIGURE 3. Reliability lower confidence limit (
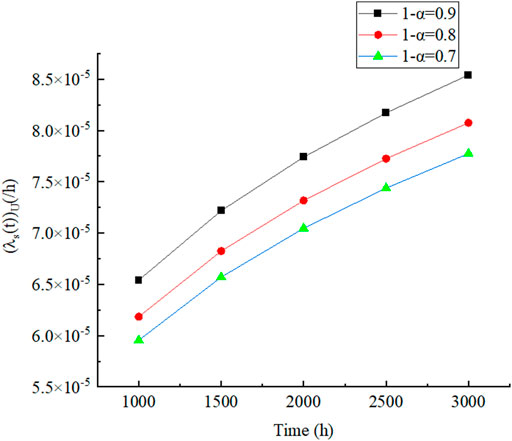
FIGURE 4. Failure rate upper confidence limit (
It can be seen from Figure 3 and Figure 4 that all lower limits of reliability
Conclusion
For the CEMS with many limiting factors, this article presented a method of replacing life test with computer analog simulation for CEMS. The life simulation values of system constituent units of CEMS could be obtained by their life distribution types and relevant distribution parameters. The life simulation values of CEMS were obtained according to the reliability logic relationship and reliability logic block diagram of the CEMS, and the simulation was instead of the life test of CEMS when the simulation times were enough. The method proposed in this thesis was of great significance to save test time and test cost, especially for the CEMSs that could not carry out reliability life test.
The method proposed in this thesis could solve the problems of system reliability synthesis and prediction of CEMS with different distributions of units. When the “pyramid model” was used for system reliability level by level synthesis and prediction. Compared with the traditional life test method of CMES, it could save a lot of test cost, test time, test site, and so on. This approach could be applied to the early program design, prototype development, trial production, and other stages of production. In engineering applications, the CMES reliability logic block diagram could be drawn by computer, and all the smallest path sets could be obtained by the node traversal optimization algorithm. Therefore, it has obvious application value in engineering.
Finally, the proposed method was applied to the wind turbine, and the reliability lower confidence limit (
Data Availability Statement
The raw data supporting the conclusions of this article will be made available by the authors, without undue reservation.
Author Contributions
CY: writing, reviewing, and editing, YG: reviewing and drawing, and XY: funding acquisition.
Funding
This work was supported by the project of the Natural Science Foundation of Shandong Province, China (No. ZR2019PEE018) and Shandong Province Science and Technology SMES Innovation Ability Enhancement Project (No. 2021TSGC1063).
Conflict of Interest
The authors declare that the research was conducted in the absence of any commercial or financial relationships that could be construed as a potential conflict of interest.
Publisher’s Note
All claims expressed in this article are solely those of the authors and do not necessarily represent those of their affiliated organizations, or those of the publisher, the editors, and the reviewers. Any product that may be evaluated in this article, or claim that may be made by its manufacturer, is not guaranteed or endorsed by the publisher.
Acknowledgments
The authors thank all the editors and referees for their helpful suggestions.
References
Aguwa, J. I., and Sadiku, S. (2012). Reliability Studies on Timber Data from Nigerian Grown Iroko Tree (Chlorophora Excelsa) as Bridge Beam Material. Jera 8 (12), 17–35. doi:10.4028/www.scientific.net/jera.8.17
Buehler, R. J. (1957). Confidence Intervals for the Product of Two Binomial Parameters. J. Am. Stat. Assoc. 52 (280), 482–493. doi:10.1080/01621459.1957.10501404
Cancela, B., Ortega, M., Penedo, M. G., Novo, J., and Barreira, N. (2013). On the Use of a Minimal Path Approach for Target Trajectory Analysis. Pattern Recognition 46 (7), 2015–2027. doi:10.1016/j.patcog.2013.01.013
Fo, X. C., and Xiong, H. L. (2009). MML Method and its Application in the Reliability Analysis of Navigating System. Electron. Product. Reliability Environ. Test. 27 (1), 16–19. doi:10.3969/j.issn.1672-5468.2009.01.005
Fuqiu, L., Wang, Z., Xiaopeng, L., and Zhang, W. (2020). A Reliability Synthesis Method for Complicated Phased Mission Systems[J]. IEEE Access 8, 193681–193685. doi:10.1109/ACCESS.2020.3028303
Graves, T. L., and Hamada, M. S. (2016). A Note on Incorporating Simultaneous Multi-Level Failure Time Data in System Reliability Assessments. Qual. Reliab. Engng. Int. 32, 1127–1135. doi:10.1002/qre.1820
Guo, J., Sun, Y., and Wang, M. (2012). System Reliability Synthesis of Wind Turbine Based on Computer Simulation[J]. J. Mech. Eng. 48 (2), 1–7. doi:10.3901/JME.2021.02.002
Guo, J., Sun, Y., Yu, C., Yuan, H., and Su, Z. (2014). Some Theory and Method for Complex Electromechanical System Reliability Prediction[J]. J. Mech. Eng. 50 (4), 1–13. doi:10.3901/jme.2014.14.001
Guo, J., and Wilson, A. G. (2013). Bayesian Methods for Estimating System Reliability Using Heterogeneous Multilevel Information. Technometrics 55 (4), 461–472. doi:10.1080/00401706.2013.804441
Han, S.-Y., Zhou, J., Chen, Y.-H., Zhang, Y.-F., Tang, G.-Y., and Wang, L. (2021). Active Fault-Tolerant Control for Discrete Vehicle Active Suspension via Reduced-Order Observer. IEEE Trans. Syst. Man. Cybern, Syst. 51 (11), 6701–6711. doi:10.1109/tsmc.2020.2964607
Hong-Bo, Z., and Guo, J. (2009). Method of System Reliability Synthesis Based on Minimal Path Sets[J]. Transducer Microsystem Tech. 28 (8), 20–23. doi:10.13873/j.100-97872009.08.14
Kovacs, Z., Orosz, A., and Friedler, F. (2019). Synthesis Algorithms for the Reliability Analysis of Processing Systems. Cent. Eur. J. Oper. Res. 27, 573–595. doi:10.1007/s10100-018-0577-0
Liu, Y., Zuo, M. J., Li, Y.-F., and Huang, H.-Z. (2015). Dynamic Reliability Assessment for Multi-State Systems Utilizing System-Level Inspection Data. IEEE Trans. Rel. 64 (4), 1287–1299. doi:10.1109/tr.2015.2418294
Meng, J., and Wen-Tao, Z. (2021). Research on the Reliability of Differential Protection Based on Monte Carlo[J]. Computer Simulation 38 (11), 112–116. doi:10.3969/j.issn.1006-9348.2021.11.023
Mi, J., Li, Y. F., Yang, Y. J., Peng, W., and Huang, H. Z. (2016). Reliability Assessment of Complex Electromechanical Systems under Epistemic Uncertainty. Reliability Eng. Syst. Saf. 152 (8), 1–15. doi:10.1016/j.ress.2016.02.003
Negi, S., and Singh, S. B. (2015). Reliability Analysis of Non-repairable Complex System with Weighted Subsystems Connected in Series. Appl. Math. Comput. 262 (262), 79–89. doi:10.1016/j.amc.2015.03.119
Peng, W., Huang, H., Xie, M., Yang, Y., and Liu, Y. (2013). A Bayesian Approach for System Reliability Analysis with Multilevel Pass-Fail, Lifetime and Degradation Data Sets. IEEE Trans. Rel. 62 (3), 689–699. doi:10.1109/tr.2013.2270424
Praks, P., and Gono, R. (2011). “Uncertainty Analysis of Failure Rate of Selected Transformers in a Power Distribution Network[C],” in Proceedings of the 12th International Scientific Conference Electric Power Engineering 2011, EPE 2011, 645–648.
Schallert, C. (2014). A Safety Analysis via Minimal Path Sets Detection for Object-Oriented Models. ESREL, 2019–2027. doi:10.1201/b17399-277
Spinato, F., Tavner, P. J., Bussel Van, G. J. W., and Koutoulakos, E. (2009). Reliability of Wind Turbines Subassemblies [J]. IET Renew. Power Generator 3 (4), 1–15. doi:10.1049/iet-rpg.2008.0060
Sun, Y., Sun, T., Pecht, M. G., and Yu, C. (2018). Computing Lifetime Distributions and Reliability for Systems with Outsourced Components: A Case Study. IEEE Access 6, 31359–31366. doi:10.1109/access.2018.2843375
Tang, S., Zhu, Y., and Yuan, S. (2021). An Improved Convolutional Neural Network with an Adaptable Learning Rate towards Multi-Signal Fault Diagnosis of Hydraulic Piston Pump. Adv. Eng. Inform. 50, 101406. doi:10.1016/j.aei.2021.101406
Tavner, P. J., Xiang, J., and Spinato, F. (2007). Reliability Analysis for Wind Turbines. Wind Energy 10, 1–18. doi:10.1002/we.204
Wang, H., Gong, Z., Huang, H. Z., Xiaoling, Z., and Zhiqiang, Lv. (2012). “System Reliability Based Design Optimization with Monte Carlo Simulation[C],” in 2012 International Conference on Quality, Reliability, Risk, Maintenance, and Safety Engineering, Chengdu, China, 15-18 June 2012, 1143–1147.
Wang, Y., Zhou, J., Wang, R., Chen, L., Zhang, T., Han, S., et al. (2022). Transfer Collaborative Fuzzy Clustering in Distributed Peer-To-Peer Networks[J]. IEEE Trans. Fuzzy Syst. 30 (2), 500–514. doi:10.1109/TFUZZ.2020.3041191
Weiyan, M., Xingzhong, X., and Shifeng, X. (2009). Inference on System Reliability for Independent Series Components[J]. Commun. Statistics-Theory Methods 38 (3), 409–418. doi:10.1080/03610920802220793
Wilson, A. G., Graves, T. L., Hamada, M. S., and Reese, C. S. (2006). Advances in Data Combination, Analysis and Collection for System Reliability Assessment[J]. Stat. Sci. 21 (4), 514–531. doi:10.1214/088342306000000439
Yeh, W., Lin, Y., Chung, Y., and Mingchang, C. (2010). A Particle Swarm Optimization Approach Based on Monte Carlo Simulation for Solving the Complex Network Reliability Problem. IEEE Trans. Rel. 59 (1), 212–221. doi:10.1109/tr.2009.2035796
Yoshida, I., and Akiyama, M. (2011). “Reliability Estimation of Deteriorated RC-Structures Considering Various Observation Data[C],” in 11th International Conference on Applications of Statistics and Probability in Civil Engineering, 1231–1239. doi:10.1201/b11332-187
Yu, C., Guo, J., Sun, Y., Su, Z., and Yuan, H. (2013). Bayes Confidence Limit of Reliability for Series-Parallel System Consisting of Different Distribution Units[J]. Chin. J. Scientific Instrument 34 (2), 428–433. doi:10.19650/j.cnki.cjsi.2013.02.028
Yuan, R., Tang, M., Wang, H., and Li, H. (2019). A Reliability Analysis Method of Accelerated Performance Degradation Based on Bayesian Strategy. IEEE Access 7, 169047–169054. doi:10.1109/ACCESS.2019.2952337
Zhang, M., Hu, Q., Xie, M., and Yu, D. (2014). Lower Confidence Limit for Reliability Based on Grouped Data Using a Quantile-Filling Algorithm. Comput. Stat. Data Anal. 75 (75), 96–111. doi:10.1016/j.csda.2014.01.010
Keywords: Monte Carlo simulation, computer simulation, system reliability prediction, system reliability synthesis, complex electromechanical system
Citation: Yu C, Guan Y and Yang X (2022) Reliability Synthesis and Prediction for Complex Electromechanical System: A Case Study. Front. Energy Res. 10:865252. doi: 10.3389/fenrg.2022.865252
Received: 29 January 2022; Accepted: 03 March 2022;
Published: 30 March 2022.
Edited by:
Ling Zhou, Jiangsu University, ChinaReviewed by:
Shiyuan Han, University of Jinan, ChinaTong Ruipeng, China University of Mining and Technology, China
Copyright © 2022 Yu, Guan and Yang. This is an open-access article distributed under the terms of the Creative Commons Attribution License (CC BY). The use, distribution or reproduction in other forums is permitted, provided the original author(s) and the copyright owner(s) are credited and that the original publication in this journal is cited, in accordance with accepted academic practice. No use, distribution or reproduction is permitted which does not comply with these terms.
*Correspondence: Chunyu Yu, aG9uZXljaHVueXVAMTI2LmNvbQ==; Yuanlin Guan, Z3Vhbnl1YW5saW5AcXV0LmVkdS5jbg==