- Department of Energy Engineering, Universidad de La Ciénega del Estado de Michoacán de Ocampo, Sahuayo, Michoacán, Mexico
Seeking energy alternatives that are friendly to the environment without compromising the growth of society is becoming more widespread. Biofuels from biomass processing are a promising path toward the development of a biomass industry and the early replacement of fossil fuels. The purpose of this work is to determine the feasibility of generating biofuels through the use of agro-industrial waste through a mathematical model for the optimization of the supply chain for the production of biofuels from waste generated by the food processors in the municipality of Zamora, Michoacán, Mexico. This case study considers the available raw material, waste from the food industries, the period of time in which these are available, as well as the possible places for processing and obtaining biofuels. The results establish that it is possible to obtain 7.27 × 107 l/year of bioethanol through the processing of 3.27 × 106 tons/year of organic waste, which generates a profit of 4.37 × 107 USD/year.
1 Introduction
Global warming is a central problem worldwide, originating in the high concentration of greenhouse gases, mostly from fossil fuel combustion. The use of biomass has a large potential benefit at the environmental level, as it is the most promising path to the development of a biomass industry and the mitigation of environmental impact. The use of biomass makes it possible to produce biofuels and other products with high added value; in addition to this, biomass is found in residual form. The industrial sector generates high amounts of waste, such as the large amount of organic waste created by agro-industry, which has the potential to be used in producing other products. Thus, it is important to evaluate the amount of waste generated by agro-industry and how it can be reused for efficient and sustainable disposal (Singh et al., 2021), as well as the various alternatives for the use of agro-industrial waste to improve environmental quality (Corredor and Pérez, 2018), such as in the estimation of the potential for the production of high value-added products, such as the reduction of processing costs through the production of biosurfactants (Gaur et al., 2022) that represent the production of new high added value products. This area of research calls for special attention to establish alternatives for the production of high value-added products involving the residual biomass of different materials and the various available transformation routes (Mehmood et al., 2021) and to determine the potential use of environmentally friendly technologies for the production of high value-added products due to increase waste from agro-industries (Freitas et al., 2021). The composition of agro-industrial residues and the content of lignocellulosic components present in this type of biomass offer a wide range of products with high added value, among which the main ones are biofuels. Thanks to their chemical composition, it is possible to use agro-industrial waste in the generation of biofuels, and they have a high potential for use due to the favorable conversion factor for this use (Muoz-Muoz et al., 2014). Further, study of the use of biorefineries for the processing of agro-industrial waste, an environmental option for zero waste, has also been studied (Dhanya 2022). Koul et al. (2022) and other studies reviewed the potential for generating biofuels through agro-industrial waste due to its content of cellulose, lignin, and lignocellulose, as well as the obtaining of by-products with high added value. Sarangi and Nayak (2021) considered different processing alternatives for the production of the main biofuels from the residual biomass produced by agro-industry. Among the processes most commonly used for the production of biofuels through agro-industrial waste are anaerobic digestion processes for the production of biogas, pellets for the production of bioenergy, and catalytic and enzymatic processes for liquid biofuels. For the production of biogas, anaerobic digestion process refers to the stage in which the treatment of food waste is carried out, and a system has been proposed that takes into account the type of microorganism and the optimization parameters (Cremonez et al., 2021). Biogas can be obtained that incorporates agro-industrial waste, mainly fruit waste (Suhartini et al., 2021), and some studies have found that the best scenario for the production of biogas takes into account the techno-economic analysis and costs associated with the life cycle (Ugwu et al., 2022). For pellet production, Murillo et al. (2021) studied the feasibility of pellet production through residual biomass, taking into account efficiency in the combustion reaction and performance in terms of energy content. The production of liquid biofuels from agro-industrial waste presents a greater potential for biomass reuse, as there is currently high demand for these biofuels, mainly in the transportation sector. Elyamny et al. (2022) analyzed the catalytic process for the transformation of agro-industrial waste to bioethanol in the pre-treatment stage, adopting the production of bioethanol from the concept of biorefinery, taking into account the processes that are carried out in the ago-industrial sector (Melendez et al., 2022). Adiya et al. (2022) determined the production of bioethanol through various agro-industrial residues and compared its properties, biofuel production potential, and biochemicals from fruit waste, taking the composition of the waste and the high production of fruit waste into account (Stanisić et al., 2022). The generation of energy or biofuels from agro-industrial waste can bring economic and environmental benefits, as it is possible to reduce energy consumption in the industry itself using optimization techniques. Research has been developed to address the problem in terms of the circular economy, in addition to reducing CO2 emissions by reducing the consumption of fossil energy sources. Fernández-Puratich et al. (2021) proposed an optimization model for heating and energy generation involving agro-industrial waste, and the reduction of CO2 in these systems was analyzed. Sanjuan-Acosta et al. (2021) determined the best processing route for the production of bioethanol from the agro-industrial residues of African palm taking into account technical-economic and sustainability aspects. This research proposal considers the generation of waste by food processing agro-industries, which, due to their composition, have high potential for the production of bioethanol due to their high content of sugars and lignocellular compounds. A linear integer mixed-optimization mathematical model is proposed to determine the best processing route for agro-industrial waste, considering the amount of waste generated annually, as well as the demand for bioethanol. The proposed model considers the feasibility of installing waste processing plants for the generation of bioethanol, as well as the maximization of annual economic benefit. The potential for bioethanol production is evaluated considering the reduction of CO2 emissions due to the use of biomass by waste, as well as a comparison with the use of fossil fuels, which allows the environmental feasibility for the reduction of emissions and the reduction of organic pollutants to be identified.
2 Methodology
The first stage consists of identifying the agro-industrial residues available for the production of biofuels. In Mexico, the food industry generates among the highest rates of biomass waste, and it is generally discarded into the environment, causing a serious problem of contamination of soil, air and water due to decomposition. The composition of this residues are mostly lignocellulosic compounds. Bioethanol is mainly produced from hydrolysis, as shown in Figure 1. Hydrolysis is considered here because it is commonly used and has economic advantages. Two stages of distillation are proposed, the first of which considers the common distillation process and the second stage the dehydrated process to increase the purity of the product. The bioethanol obtained in this processing plant is sent to cities with high demand for fuel for the transportation sector. This biofuel, like fossil fuels, during its combustion, generates CO2 emissions; however, as it is produced from biomass throughout the supply chain, the net generation may be less than that seen with fossil fuels. A superstructure is proposed to determine the mathematical model for the case study, as shown in Figure 2, and we indicate a proposal of two types of process plants, namely, distributed and centralized plants; the main difference between these two types of plants is that centralized plants have greater processing capacity and are closer to the cities that demand bioethanol, whereas distributed plants are located near waste extraction sites. Thus, we seek to determine the optimal route for processing agro-industrial waste with the greatest economic benefit, taking into account the amount of biomass available, the bioethanol produced, and the CO2 emissions compared to the use of fossil fuels.
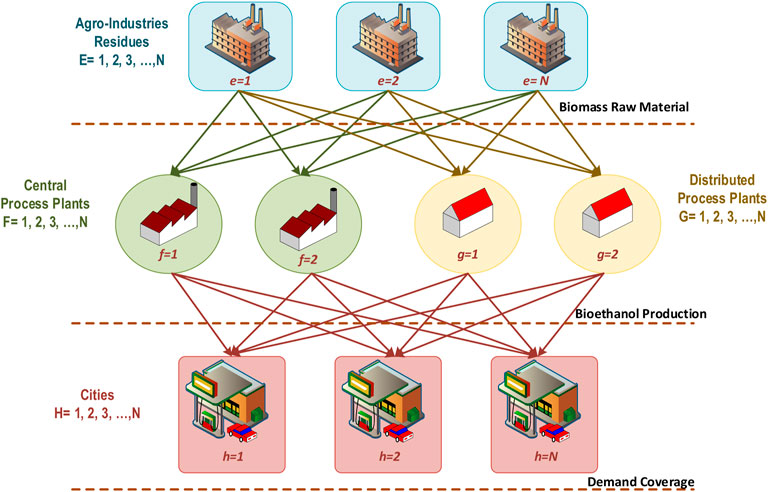
FIGURE 2. Superstructure for the case study for optimal production of bioethanol from agro-industrial residues.
2.1 Model formulation
Previous authors, such as Murillo-Alvarado et al. (2015), have investigated optimization techniques for the conversion of lignocellular residues for the production of bioethanol. The optimization model for the bioethanol production from agro-industrial wastes takes into account the superstructure shown in Figure 2, the optimization model proposed for this case study defined the followings sets: set e represents the agro-industry that provides the waste biomass that will be converted into bioethanol, set f represents the possible central process that will be considered for the production of bioethanol, set g represents the distributed process plant, set h represents the cities that demand bioethanol, and finally, set t represents the time period. The formulation of the mathematical model takes the following equations into account:
- Constraint on the distribution of the amount of waste available cannot exceed the maximum obtained from agro-industry; the balance to quantify the availability of water is determined through the following equation:
- Mass balance in the distribution of the residues available from agro-industry sent to the processing plants for bioethanol production:
- This balance determines the total amount of biomass (
- The biomass conversion that arrives at each processing plant for transformation into bioethanol, so that the
- The bioethanol obtained is then sent to the cities that demand this fuel, for which the following mass balance is proposed:
- This mass balance determines the total amount of bioethanol that is distributed by the processing plants to each of the cities.
- Along the processing route, from the point when the biomass is available until the final product is distributed, costs are incurred, such as processing, capital, and transportation costs. Processing costs are calculated with the following equation:
-The modeling and optimization stage appears before the start-up of the project, and it is where the feasibility of generating bioethanol from agroindustry residues is determined, so that within the model, the process that will be carried out is a black box, but if the total cost for this plant is determined, all stages of bioethanol production considering must be involved. The capital costs refer to the costs involved in the installation of the processing plants considered, reflecting investments. Therefore, the following disjunction with a Boolean variable is proposed; if the variable is true, this means that there is a feasible processing flow, considered a capital cost, and if the variable is false, this means that there is no flow for process, so the plant cannot be installed and has a zero capital value:
- In the optimization for the mathematical model, it is necessary to establish an objective minimizing or maximizing function; the objective is to maximize the economic benefit that represent the overall profit in the supply chain founded, which is given by the sales of the products obtained, here bioethanol, minus the total costs (including operation, capital, and transportation):
The total sales are calculated through the following equation:
- Finally, the total amount of CO2 emissions along the processing route is calculated, including the emissions that are released by the processing activities in plants, transport of biomass and bioethanol, and due to the combustion of fuel are considered. The bioethanol obtained and the amount of CO2 that is absorbed by the biomass used during the photosynthesis process are subtracted.
According to SAGARPA 2018, 10,120 ha of strawberries are cultivated in Michoacán, and other crops that provide the raw material to agribusinesses that generate around 3 million kg waste. In the state of Michoacán in Mexico are the cities of Jacona and Zamora, which are characterized by the concentration of a large number of food processing industries, which mainly export frozen foods of fruits and vegetables, highlights the production of frozen product of strawberries, berries, blueberries, mangoes, and broccoli, so that annually, due to this processing, a large amount of waste is generated, which is dumped into the environment, generating great problems of environmental pollution. These residues present in their composition mainly sugars and lignocellulosic compounds, which can be transformed into bioethanol. Therefore, the proposed mathematical model was used in this case study. For the solution of the proposed model, the availability of biomass from 30 agro-industries that process strawberries, mangoes and broccoli was considered, for which the surplus of these fruits is considered as waste. The possible installation of five distributed processing plants for the production of bioethanol was considered, which are close to the places where the waste is generated, four possible central processing plants with possible location near the points of demand for bioethanol and four cities that demand fuel. The optimization model proposed is a mixed integer lineal program (MILP) was coded in the software GAMS using the solver CPLEX (Brooke et al., 2012). The addressed case study has 4,344 continuous variables, 9 binary variable and 1,248 constraints, the model was solved in a computer with Intel® Core™ i7 processor at 2.80 GHz with 12.0 GB of Memory RAM with a 0.289 s of CPU time in each scenario.
3 Results and discussion
To present the applicability of the model, two scenarios are solved, in the first of which the optimal solution is defined without constraints in the bioethanol production, and in the second of which CO2 quantification is considered in the overall route for the bioethanol generation from agro-industrial residues.
3.1 Scenario A1. Optimal solution for the bioethanol production by agro-industries waste
This scenario presents the number of processing plants for the production of bioethanol that would be feasible to install considering the amount of waste generated in the agro-industries of the region. For this solution, the model is solved without restrictions; that is, there is no restriction on how many processing plants must be installed and how much bioethanol has to be produced, so the model determines the optimal processing route taking the maximization of economic benefit into consideration. In this sense, the optimal route for this solution is shown in Figure 3, which considers the installation of two central processing plants of the four considered and no distributed processing plants of the five considered. The processing of waste from the 30 considered agro-industries is considered. Processing plant 1 processes 1.8 × 106 tons/year of residues, and processing plant 2 processes 1.47 × 106 tons/year of residues. This configuration present production of bioethanol of 3.99 × 107 l/year for plant 1 and 3.27 × 107 l/year for plant 2, and this bioethanol obtained is sent to two of the four cities considered, the economic profit for this optimal configuration is 4.37 × 107 USD/year.
3.1.1 Scenario A2. Constraint on the demand for bioethanol in cities
The previous scenario presents the optimal solution to process the agro-industrial residues for the bioethanol production without constraints; however, this shows that the distribution of bioethanol is only for two cities of the four considered; that is, in this scenario it is established as a restriction that the four cities considered have a demand for bioethanol. The values of this solution are presented in Table 1, and a configuration where the agro-industrial residues are taken from 30 agro-industries, the installation of four central process plants is feasible, and bioethanol is sent to four cities is considered. This configuration process 3.6 × 106 tons/year of residues, 7.24 × 107 l/year of bioethanol obtained, and 4.21 × 107 USD/year of economic profit, calculated with Eq. (9).

TABLE 1. Configuration for Scenario A2, total flow of residues processed and total bioethanol obtained in each plant.
3.2 Scenario B, CO2 quantification in the processing of agro-industrial waste for the generation of bioethanol
This scenario presents CO2 quantification along the overall route for bioethanol generation from agro-industrial waste. Bioethanol, like gasoline, generates CO2 emissions during the combustion process, as well as during the processing of biomass, and the processes used for the production of bioethanol generate CO2 due to the energy requirements, whether thermal or electrical; however, the effect that the advantage that bioethanol has relative to gasoline is that bioethanol comes from a biomass source that captures CO2 during its growth through photosynthesis process. Thus, CO2 is quantified in the biomass processing stage, during the stage of transportation of raw material and products, during combustion, and finally as captured by the amount of biomass used. The CO2 emitted for the processing of residues in all process plants is 8.1 × 105 tons/year, the CO2 emitted for the transport of residues to process plants is 2.93 × 104 tons/year, the CO2 emitted for the transport of bioethanol to cities is 2.32 × 104 tons/year, the CO2 emitted for combustion of the bioethanol obtained is 1.11 × 105 tons/year, and the CO2 captured for biomass used for the bioethanol production is 1.65 × 107 tons/year.
4 Conclusion
In this paper, a mathematical optimization model was presented to determine the feasibility of bioethanol production taking into account the waste generated by agro-industry in the state of Michoacán, Mexico. The results obtained show that in the economic aspect, the generation of bioethanol is feasible, as a feasible economic benefit is obtained. In scenario A1, it was observed that it is preferable to operate under a centralized model because in both sub-scenarios the installation of central processing plants is preferentially obtained, because in this type of plant, processing costs are reduced due to the processing of the larger flow, and in a distributed system, despite the fact that it is possible to reduce transportation costs due to the proximity of the places where the raw material is available but processing costs are higher. The economic benefit obtained is around of 4.21 × 107 USD/year, and this benefit represents the profit from the sales of bioethanol obtained less the total costs, in terms of the operation, capital, and transportation costs. Finally, the results at the environmental level show that the production of bioethanol from agro-industrial waste is feasible, as it is possible to reduce CO2 emissions compared to the use of gasoline.
Data availability statement
The original contributions presented in the study are included in the article and the Supplementary Material, further inquiries can be directed to the corresponding author.
Author contributions
PM-A proposed the idea and carried out the conceptualization, writing of the original draft, and formal analysis. EF was responsible for the proposed coded model, analysis of the data, and design of the case studies.
Funding
Universidad de la Ciénega del Estado de Michoacan de Ocampo. Financing is being sought from the Institute of Science and Technology of the State of Michoacan.
Conflict of interest
The authors declare that the research was conducted in the absence of any commercial or financial relationships that could be construed as a potential conflict of interest.
Publisher’s note
All claims expressed in this article are solely those of the authors and do not necessarily represent those of their affiliated organizations, or those of the publisher, the editors and the reviewers. Any product that may be evaluated in this article, or claim that may be made by its manufacturer, is not guaranteed or endorsed by the publisher.
References
Adiya, Z. I. S. G., Adamu, S. S., Ibrahim, M. A., Okoh, E. V. C., and Ibrahim, D. (2022). Comparative study of bioethanol produced from different agro-industrial biomass residues. Earthline J. Chem. Sci. 7 (2), 143–152. doi:10.34198/ejcs.7222.143152
Brooke, A., Kendrick, D., Meeraus, A., and Raman, R. (2012). GAMS A user’s guide. Washington, D.C.: GAMS Development Corporation. Available in: http://www.gams.com/dd/docs/bigdocs/GAMSUsersGuide.pdf.
Corredor, Y. A. V., and Pérez, L. I. P. (2018). Aprovechamiento de residuos agroindustriales en el mejoramiento de la calidad del ambiente. Rev. Fac. Ciencias Básicas 14, 59–72. doi:10.18359/rfcb.3108
Cremonez, P. A., Teleken, J. G., Meier, T. R. W., and Alves, H. J. (2021). Two-stage anaerobic digestion in agroindustrial waste treatment: A review. J. Environ. Manag. 281, 111854. doi:10.1016/j.jenvman.2020.111854
de Agricultura, Secretaría (2022). Ganadería, desarrollo rural, pesca y alimentación (SAGARPA, méxico 2018). Available at: https://www.gob.mx/agricultura/michoacan/articulos/michoacan-se-mantiene-en-primer-lugar-a-nivel-nacional-en-produccion-de-fresa?idiom=es (Accessed February, 2022).
Dhanya, M. S. (2022). “Perspectives of agro-waste biorefineries for sustainable biofuels,” in Zero waste biorefinery (Singapore: Springer), 207–232.
Elyamny, S., Hamdy, A., Ali, R., and Hamad, H. (2022). Role of combined Na2HPO4 and ZnCl2 in the unprecedented catalysis of the sequential pretreatment of sustainable agricultural and agro-industrial wastes in boosting bioethanol production. Int. J. Mol. Sci. 23 (3), 1777. doi:10.3390/ijms23031777
Fernández-Puratich, H., Rebolledo-Leiva, R., Hernández, D., Gómez-Lagos, J. E., Armengot-Carbo, B., and Oliver-Villanueva, J. V. (2021). Bi-objective optimization of multiple agro-industrial wastes supply to a cogeneration system promoting local circular bioeconomy. Appl. Energy 300, 117333. doi:10.1016/j.apenergy.2021.117333
Freitas, L. C., Barbosa, J. R., da Costa, A. L. C., Bezerra, F. W. F., Pinto, R. H. H., and de Carvalho Junior, R. N. (2021). From waste to sustainable industry: How can agro-industrial wastes help in the development of new products? Resour. Conservation Recycl. 169, 105466. doi:10.1016/j.resconrec.2021.105466
Gaur, V. K., Sharma, P., Sirohi, R., Varjani, S., Taherzadeh, M. J., Chang, J. S., et al. (2022). Production of biosurfactants from agro-industrial waste and waste cooking oil in a circular bioeconomy: An overview. Bioresour. Technol. 343, 126059. doi:10.1016/j.biortech.2021.126059
Koul, B., Yakoob, M., and Shah, M. P. (2022). Agricultural waste management strategies for environmental sustainability. Environ. Res. 206, 112285. doi:10.1016/j.envres.2021.112285
Mehmood, T., Nadeem, F., Qamar, S. A., Bilal, M., and Iqbal, H. (2021). “Bioconversion of agro-industrial waste into value-added compounds,” in Sustainable bioconversion of waste to value added products (Cham: Springer), 349–368.
Melendez, J. R., Mátyás, B., Hena, S., Lowy, D. A., and El Salous, A. (2022). Perspectives in the production of bioethanol: A review of sustainable methods, technologies, and bioprocesses. Renew. Sustain. Energy Rev. 160, 112260. doi:10.1016/j.rser.2022.112260
Muoz-Muoz, D., Pantoja-Matta, A. J., and Cuatin-Guarin, M. F. (2014). Aprovechamiento de residuos agroindustriales como biocombustible y biorefinería. Biotecnol. el Sect. Agropecu. agroindustrial 12 (2), 10–19.
Murillo, H. A., Díaz-Robles, L. A., Santander, R. E., and Cubillos, F. A. (2021). Conversion of residual biomass into valuable biofuels by co-hydrothermal carbonization for utilization in household pellet stoves. Biomass Bioenergy 151, 106153. doi:10.1016/j.biombioe.2021.106153
Murillo-Alvarado, P. E., Guillén-Gosálbez, G., Ponce-Ortega, J. M., Castro-Montoya, A. J., Serna-González, M., and Jiménez, L. (2015). Multi-objective optimization of the supply chain of biofuels from residues of the tequila industry in Mexico. J. Clean. Prod. 108, 422–441. doi:10.1016/j.jclepro.2015.08.052
Sanjuan-Acosta, M. J., Tobón-Manjarres, K., Sánchez-Tuirán, E., Ojeda-Delgado, K. A., and González-Delgado, Á. D. (2021). An optimization approach based on superstructures for bioethanol production from african palm kernel shells. Pol. J. Environ. Stud. 30 (3), 2293–2300. doi:10.15244/pjoes/127554
Sarangi, P. K., and Nayak, M. M. (2021). “Agro-waste for second-generation biofuels,” in Liquid biofuels: Fundamentals, characterization, and applications (Hoboken, New Jersey, United States: John Wiley & Sons), 697–709.
Singh, R., Das, R., Sangwan, S., Rohatgi, B., Khanam, R., Peera, S. K. P. G., et al. (2021). Utilisation of agro-industrial waste for sustainable green production: A review. Environ. Sustain. 4, 619–636. doi:10.1007/s42398-021-00200-x
Stanisić, D., Tasić, M., Stamenković, O., and Tasić, L. (2022). “Prospects and perspectives for producing biodiesel, bioethanol and bio-chemicals from fruit waste: Case studies in Brazil and Serbia,” in Production of biofuels and chemicals from sustainable recycling of organic solid waste (Singapore: Springer), 415–452.
Suhartini, S., Nurika, I., Paul, R., and Melville, L. (2021). Estimation of biogas production and the emission savings from anaerobic digestion of fruit-based agro-industrial waste and agricultural crops residues. Bioenergy Res. 14 (3), 844–859. doi:10.1007/s12155-020-10209-5
Ugwu, S. N., Harding, K., and Enweremadu, C. C. (2022). Comparative life cycle assessment of enhanced anaerobic digestion of agro-industrial waste for biogas production. J. Clean. Prod. 345, 131178. doi:10.1016/j.jclepro.2022.131178
Nomenclature
Indexes
e Index for agro-industries that provide the biomass waste
f Index for central process for the production of bioethanol
g Index for distributed process for the production of bioethanol
h Index for cities with demand of bioethanol
t Index for time periods
Sets
E Set for agro-industries that provide the biomass waste e
F Set for central process for the production of bioethanol f
G Set for distributed process for the production of bioethanol g
H Set for cities with demand of bioethanol h
T Set for time periods
Parameters
Variables
FBf,h,t Flow of bioethanol supplied in cities from distributed plants
FBg,h,t Flow of bioethanol supplied in cities from central plants
FBCCg,t Total flow of bioethanol obtained in central plants
FBCDf,t Total flow of bioethanol obtained in distributed plants
FMAe,t Flow of biomass waste supplied for the agro-industries
Keywords: biofuels, agro-industrial waste, optimization, emission depletion, bioethanol
Citation: Murillo-Alvarado PE and Flores Russell E (2022) Optimization approach for bioethanol production from agro-industrial waste. Front. Energy Res. 10:975133. doi: 10.3389/fenrg.2022.975133
Received: 22 June 2022; Accepted: 08 September 2022;
Published: 30 September 2022.
Edited by:
Sachin Kumar, Sardar Swaran Singh National Institute of Renewable Energy, IndiaReviewed by:
Pratibha Dheeran, Maharaj Singh College, IndiaMuhammad Waqas, Kohat University of Science and Technology, Pakistan
Copyright © 2022 Murillo-Alvarado and Flores Russell. This is an open-access article distributed under the terms of the Creative Commons Attribution License (CC BY). The use, distribution or reproduction in other forums is permitted, provided the original author(s) and the copyright owner(s) are credited and that the original publication in this journal is cited, in accordance with accepted academic practice. No use, distribution or reproduction is permitted which does not comply with these terms.
*Correspondence: Pascual Eduardo Murillo-Alvarado, cGVtdXJpbGxvQHVjZW1pY2guZWR1Lm14