- 1The Harold and Inge Marcus Department of Industrial and Manufacturing Engineering, University Park, PA, United States
- 2Department of Biomedical Engineering, University Park, PA, United States
- 3Department of Mechanical Engineering, The University of TX, Edinburg, TX, United States
- 4Department of Mechanical Aerospace and Nuclear Engineering, Rensselaer Polytechnic Institute, Troy, NY, United States
- 5Materials Research Institute (MRI), The Pennsylvania State University, University Park, PA, United States
The cold sintering process (CSP) is a low-temperature consolidation method used to fabricate materials and their composites by applying transient solvents and external pressure. In this mechano-chemical process, the local dissolution, solvent evaporation, and supersaturation of the solute lead to “solution-precipitation” for consolidating various materials to nearly full densification, mimicking the natural pressure solution creep. Because of the low processing temperature (<300°C), it can bridge the temperature gap between ceramics, metals, and polymers for co-sintering composites. Therefore, CSP provides a promising strategy of interface engineering to readily integrate high-processing temperature ceramic materials (e.g., active electrode materials, ceramic solid-state electrolytes) as “grains” and low-melting-point additives (e.g., polymer binders, lithium salts, or solid-state polymer electrolytes) as “grain boundaries.” In this minireview, the mechanisms of geomimetics CSP and energy dissipations are discussed and compared to other sintering technologies. Specifically, the sintering dynamics and various sintering aids/conditions methods are reviewed to assist the low energy consumption processes. We also discuss the CSP-enabled consolidation and interface engineering for composite electrodes, composite solid-state electrolytes, and multi-component laminated structure battery devices for high-performance solid-state batteries. We then conclude the present review with a perspective on future opportunities and challenges.
1 Introduction
Sintering refers to a process that combines particulate materials into dense solids through diffusion-assisted densification and coarsening. Extensive research has been conducted on processing ceramics and ceramic-based composites to promote multifunctional properties (e.g., mechanical, electrical, thermal properties, etc.) (Lóh et al., 2016; Qian, 2017). Ceramic manufacturing has progressed along a path with the continuous development of sintering techniques. In this regard, manufacturing methods of interest include hot pressing (HP), flash, microwave, spark plasma (SPS), laser, and cold sintering process (CSP). The pressure and heat coupling in the HP, high thermal ramp rates by microwave heating, and electrical field-assisted rapid ramp rates by SPS, present respective advantages and disadvantages of these processes (Biesuz et al., 2019). Among these techniques, cold sintering is a low-temperature sintering process that involves two phases: a main component of powder from which to form a matrix body and a transient phase which is often liquid or liquid mixer to facilitate mass transport. Liquid phases can be acids, alkalis, polar solvents, or mixtures with polymer or salt additives (Grasso et al., 2020). A combination of capillarity at the two-phase interface and the applied uniaxial pressure provides the driving force to facilitate mass transport and densification (Guo et al., 2019).
As an emerging densification method, the CSP has been used to process a large variety of materials at high density (>90% of relative density), such as metals (Fe, Cu, etc.) (de Beauvoir et al., 2019), binary compounds (V2O5, ZnO, etc.) (Gonzalez-Julian et al., 2018; Zhao N et al., 2019), ternary compounds (K2Mo2O7, BaTiO3, etc.) (Guo J et al., 2016; Sada et al., 2021), quaternary compounds (LiFePO4, KH2PO4, etc.) (Guo H et al., 2016; Seo et al., 2017) and quinary compounds (Li1.5Al0.5Ge1.5(PO4)3, Li1.3Al0.3Ti1.7(PO4)3, Li7La3Zr2O12, etc.) (Berbano et al., 2017; Liu et al., 2019; Seo et al., 2020). The low-temperature sintering can integrate different materials, such as ceramic, polymers, and metals, that can open opportunities for composite manufacturing in many applications. For example, in battery electrode processing, electrode materials usually include metals (Al and/or Cu) as the current collector, ceramics as the active material, carbon as the conductive additive, and polymer as the binder (Huang et al., 2015). When introducing the CSP, the low-temperature sintering process can achieve dense composite electrodes to improve volumetric battery performance compared to the low-calendered electrode density fabricated by the conventional process (Sun et al., 2019). The cold-sintered solid-state electrolytes can also mitigate the lithium volatilization and interface side reactions that usually occur under high-temperature sintering (>1000°C) (Zhao Y et al., 2019).
In fact, CSP shows many advantages for battery processing compared to other electrode fabrication methods. This mini-review discusses the concept of the cold sintering process concept, including the process evolution, sintering mechanism, and energy dissipation. Then, the applications of cold sintering in the manufacturing/production of battery electrodes and solid-state electrolytes, as well as the integration of laminated all-solid-state devices, are discussed. Perspectives and outlooks on future opportunities and challenges of the cold sintering process for battery material selection and manufacturing field are also given.
2 Mechanism and process physics
Based on the early diagenesis in sedimentary basins (Figure 1A), the sediments consolidate upon weathering pressure solution. The non-hydrostatic dissolution around the intergranular contact surface occurs and assists diffusive transport into the pores outside the contacts and possible secondary mineral precipitation (Gundersen et al., 2002; Lu et al., 2021). Inspired by the geological consolidation process, CSP was designed with similar attributes to consolidate the materials or composites. The combination of capillary forces applied uniaxial pressure, and dissolution-based mass transport presumably forms the basis for the densification mechanism. It involves primary stages with dissolution, mass transport, and precipitation during the CSP. In these stages, due to the mechanical-chemical coupling and the hydrothermal-assisted crystal growth, the free energy barrier is relatively lower (Figure 1B) (Guo H et al., 2016). The heating profile and the applied pressure generally follow an initial rapid increase and then a plateau period (Funahashi et al., 2017; Haug et al., 2020). Assisted by the transient solvent, the sintering temperature (typically <300°C) of CSP is much lower than that of the conventional sintering process. Specifically, the shrinkage difference shows that more linear shrinkage occurs in the CSP at a temperature lower than 65°C (Figure 1C). Also, the heating rate affects the existing period of the transient phase, which presents a heating rate-dependent kinetic process (e.g., 2.0ºC–15.0°C/min) (Bang et al., 2020a). Regarding the different attributes of the sintering process, increasing the ramping rate, applying an electric field, and using sintering aid can lower energy consumption. In Figures 1D,E, the addition of sintering aids is the simplest approach to reduce energy consumption, which makes CSP one of the most energy-efficient techniques to consolidate powder materials and composites (Sohrabi Baba Heidary et al., 2018). Across multiple material sintering systems, CSP with significantly decreased energy dissipation shows a low normalized excess energy indicator versus power density compared to the furnace-based sintering. Thus, the CSP of ceramics and their composites saves considerable energy in production.
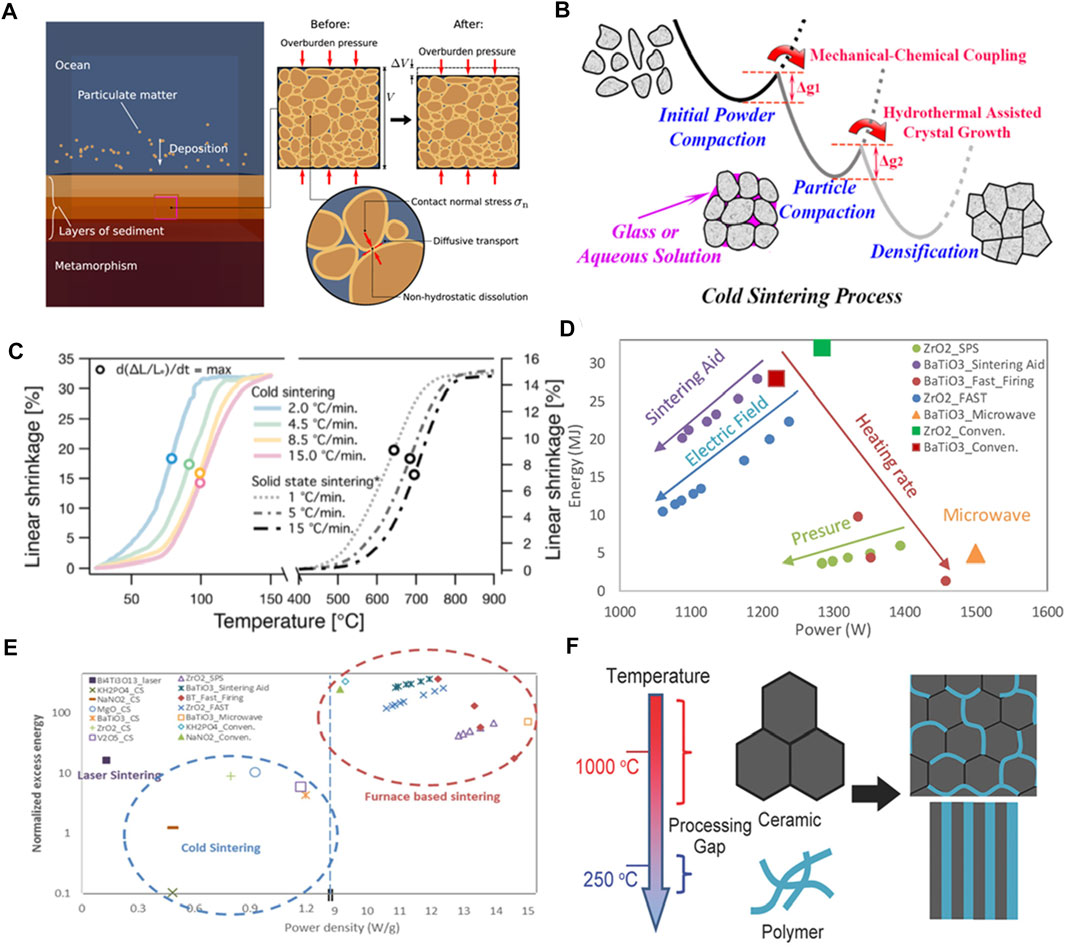
FIGURE 1. Geomimetics inspired cold sintering process (CSP). (A) The geology diagenesis in sedimentary basins (Gundersen et al., 2002). (B) The schematic of the cold sintering mechanism (Guo H et al., 2016). (C) The sample shrinkage difference between the CSP and solid-state sintering (Bang et al., 2020a). (D and E) The comparison of energy dissipations and conditions for different sintering methods (Sohrabi Baba Heidary et al., 2018). (F) The co-sintering ability for ceramic-polymer composite designs at a low temperature (Guo et al., 2018). All reproduced with permission, Copyright.
Due to the low sintering temperature, CSP can co-sinter dissimilar materials to integrate their composites. Specifically, with the addition of the polymer phase, it is possible to prepare dense polymer-in-ceramic composites where polymers can fill in the ceramic matrix or laminated structures between the ceramic layers (Figure 1F). Interface engineering of polymers, ceramics, and other additives into a composite allows novel composite designs for battery electrodes, electrolytes, and multi-component devices (Guo et al., 2018).
3 Cold sintering enabled battery material and device manufacturing
Cold sintering features a mechanically and thermally driven mass transport process that enables a low-temperature integration of various materials, such as ceramics, polymers, and metals (Figure 2A) (Dursun et al., 2020). Particularly, it attracts great attention to the advanced manufacturing of solid-state batteries with high energy density, safe operation, low processing cost, and energy consumption. Specifically, it enables interface engineering to readily address many fundamental issues associated with chemical/physical/mechanical properties occurring at various interfaces. These defects may cause an increased resistance as a barrier to prevent fast electron and ion transports in the electrochemical battery system, dramatically deteriorating the battery performance (Banerjee et al., 2020). To this end, the CSP enables an effective strategy to engineer intimate contact between dissimilar phases or components for composite electrodes, solid electrolytes, and the integration of multi-layered structures (Figure 2B). In fact, the CSP offers many advantages, including: 1) integration of additive phases to aid conductive interfaces and mechanical integration; 2) mitigation of volatility with Li-salts to reduce depletion zones at interfaces; 3) consolidation of high-density composite electrodes for high volumetric performance; 4) facile integration of anodes, cathodes, electrolytes, and metallic current collectors for multi-component battery devices; and 5) good compatibility with lamination and tape-casting approaches for potential scale-up batch and continuous processes.
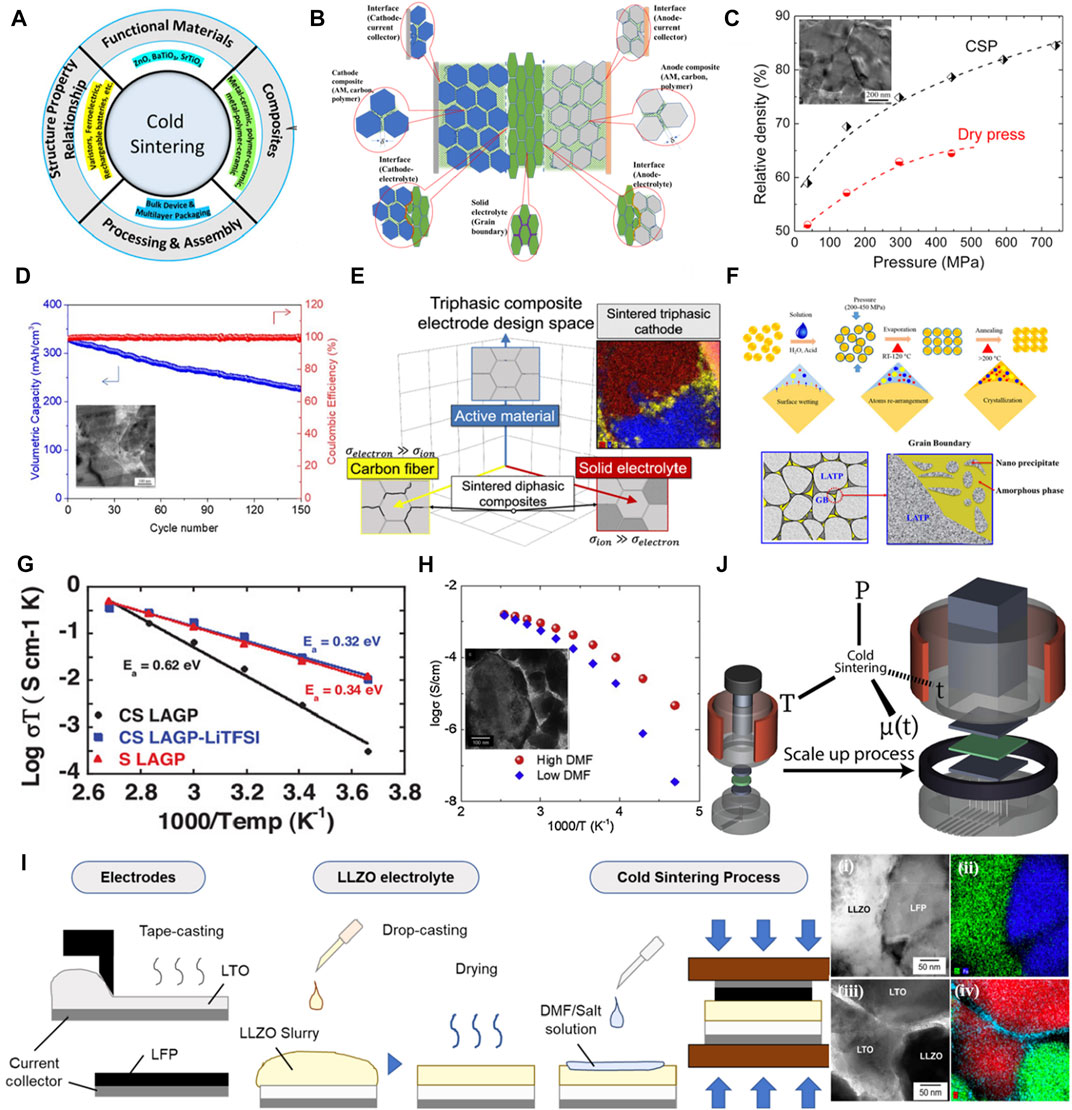
FIGURE 2. Cold sintering of composite electrodes, electrolytes, and multi-component layered-structure battery devices. (A) The process of CSP and its applications (Dursun et al., 2020). (B) The schematic of the CSP-assisted interface engineering for the integration of solid-state battery devices. (C) The pressure-dependent density of cold-sintered LiFePO4 cathodes (Seo et al., 2017). Inset: an SEM image showing the morphology of the cold-sintered cathodes. (D) The charge-discharge cycling performance of a cold-sintered Li4Ti5O12 anode (Seo et al., 2019). (E) The NASICON structured triphasic composite electrode (Grady et al., 2021). (F) The CSP of the Li1.3Al0.3Ti1.7(PO4)3 (Liu et al., 2019). (G) The ionic conductivity of the cold-sintered LAGP-LiTFSI solid-state composite electrolyte (Lee et al., 2019). (H) The ionic conductivity of the cold-sintered LLZO-SM electrolyte. Insert: A TEM image showing the sintered particles (Seo et al., 2020). (I) The interface illustrations of the multi-component layered-structure solid-state battery device via STEM and elemental mappings (Seo et al., 2021). (J) The scale-up configuration of the cold sintering system (Bang et al., 2020b). All reproduced with permission, Copyright.
3.1 CSP of composite electrodes
Different phases and components in composites underpin the electrochemical battery performance inside an electrochemical system. LiFePO4, as a commercial cathode material for LIBs, has a low density of 3.6 g cm-3, which is very difficult to achieve high volumetric capacity in a roll-to-roll slurry coating process. CSP was demonstrated to densify LiFePO4 composite electrodes consisting of carbon and PVDF polymer additives at a low temperature of 240°C. In Figure 2C, the cold-sintered composite cathode exhibited a relative density of ∼89% and higher physical density (2.7 g cm-3) than electrodes manufactured by conventional sintering (1.9 g cm-3). It is suggested that employing the liquid phase of LiOH solution benefits the dissolution-precipitation for the compaction and sintering. For example, LiFePO4 cathode in a lithium-ion half-cell delivered a high volumetric capacity of ∼340 mAh cm-3 at 0.1C (Seo et al., 2017). In addition to the sintering aids, the transient phase of the LiOH solution was also demonstrated to promote the LiCO3 removal from the air-exposed LiMn2O4 cathode for improved battery performance (Nur et al., 2022). On the anode side, a binder-free Li4Ti5O12 (LTO)/carbon nanofiber (CNF) composite was co-sintered to achieve a relative density of 87%, which delivered a high volumetric capacity of 225 mA h cm-3 after 150 cycles at 0.2 C (Figure 2D) (Seo et al., 2019). More importantly, electrical and ionic conducting phases are necessary to be co-sintered into composite electrodes for rapid charge delivery. For example, a NASICON-structured composite electrode (>90% density) with interface engineering of Na3V2(PO4)3 (NVP) active material, Na3Zr2Si2PO12 (NZSP) ionic conductor, and electrically conductive carbon nanofibers (CNFs) was co-sintered by CSP, which demonstrated improved total conductivity from 3.8 × 10−8 S cm-1 to 1.31 × 10−5 S cm-1 (Figure 2E) (Grady et al., 2021). The optimized interface engineering through cold sintering of dissimilar materials illustrates enhanced volumetric capacity and improved charge transports for battery composite electrodes. The CSP enables to the production of thick and dense composite electrodes with high areal mass loading and high electrode density, which shows great potential to achieve high areal and high volumetric battery performance. However, the thick and dense electrodes usually severely degrade the battery performance due to insufficient charge transports. Therefore, novel structured electrode designs with optimized charge transport pathways are highly desirable to address the intrinsic limitation for efficient charge transport kinetics. For the solid-state battery system, CSP can readily integrate inorganic and organic conducting phases into the co-sintered thick electrodes (Wu et al., 2019), but the large interface resistances cause the degradation for high-energy-density battery performance, especially at the elevated current density. In addition, liquid electrolyte additives are still used to further reduce interface resistances and improve the charge transport kinetics.
3.2 CSP of composite electrolytes
CSP enables the effective consolidation of solid-state electrolytes to improve ionic conductivity and stability. For the solid-state oxide-based electrolyte, the side reactions at a high sintering temperature limit its application in all-solid-state batteries. Recently, cold sintering has been used to sinter oxide-based electrolytes with good ionic conductivity. For example, NASICON structured electrolytes, such as Li1.5Al0.5Ge1.5(PO4)3 (LAGP) (Takashima et al., 2021) and Li1.3Al0.3Ti1.7(PO4)3 (LATP) (Liu et al., 2019), were prepared by CSP at 120°C. The sintered LATP pellet with a relative density of 93% showed a high ionic conductivity of 8.04 × 10−5 S cm-1 at room temperature. As shown in Figure 2F, the particles in the pellet are interconnected with nanocrystal-enriched “grain boundaries.” The regular CSP with water as the transient solvent remains challenging in the amorphous, low-conductivity grain boundaries for the oxide-based electrolyte. More importantly, the lithium salts (LiTFSI and LiClO4) with moisture can be used as the sintering aids to replace water as the transient solvent (Lee et al., 2019; Jiang et al., 2021). As a result, the 130°C sintered LAGP-LiTFSI composite electrolyte exhibited nearly 90% relative density and around 10–4 S cm-1 ionic conductivity at 20°C (Figure 2G). The assembled Li//LAGP-LiTFSI//Li symmetric cell can be charged/discharged over 1800 h at 0.2 mA cm-2. The transient solvent, LiTFSI with moisture, can lower the sintering energy and improve the ionic conductivity across the artificial “grain boundaries.” Besides lithium salts, polymer additives were co-sintered to consolidate the LAGP-(PVDF-HFP) composite electrolyte, which delivered a high ionic conductivity of 1.0 × 10−4 S cm-1 at 25°C (Berbano et al., 2017). Another type of oxide-based electrolyte, Li6.25Al0.25La3Zr2O12 (LLZO) garnet ceramic, was cold-sintered with PEO polymer, resulting in stable charge/discharge cycles over 550 h at a current density of 0.3 mA cm-2 (Hu et al., 2022). Furthermore, mixing lithium salts and polymer with the transient solvent mixture of acetone and DMF was used as the sintering aids for the co-sintering of LLZO ceramic-based electrolytes. The addition of solvent during the process was found to benefit the charge transport across the interfaces at grain boundaries (Figure 2H) (Seo et al., 2020). Therefore, the sintering temperature, applied pressure, dwell time, and the sintering transient solvent play significant roles in the densification and conductivity of the cold-sintered solid-state electrolytes (Seo et al., 2020; Wang et al., 2020; Zhang J et al., 2022; Zhang Y et al., 2022). With the above applications of solid-state composite electrolytes, the CSP enables to co-sinter dense composite electrolytes with strong bonding between powder particles as “grains” for improved ionic conductivity. Moreover, the chemical composition and phase of the constituent in the “grain boundaries” need further studies to reduce the depletion of ion transport across the “grain boundaries”.
3.3 CSP of multi-component solid-state battery devices
In all-solid-state batteries, the interfaces across the current collector, electrode, and electrolyte may cause large resistances leading to charge transport depletions and performance degradation. To tackle this challenge, cold sintering can integrate multiple components (e.g., electrodes, solid-state electrolytes, and metal current collectors) into a laminated structure in a battery cell, which is compatible with a tap-casting process (Figure 2I). The scanning transmission electron microscopy (STEM) and elemental mapping of energy dispersive X-ray spectroscopy (EDS) images of the triple point region showed that the grains and grain boundaries were intimately joined by CSP (Figure 2I), resulting in fast ion transport through the polymer-salt interfaces as artificial grain boundaries. Ascribed to the co-sintering with the metal current collector, the intimate interface between the metal and the ceramic-based composite enabled good electric contact. Integrating multi-components into solid-state battery cells via CSP enabled excellent interface engineering underpinning mechanical stability and high electrochemical performance simultaneously (Seo et al., 2021). Moreover, a customized cold sintering apparatus with a large-sized sintering die can be developed for a potential scale-up production (Figure 2J). Four densification process variables: applied uniaxial pressure (p), sintering temperature (T), dwell time (t), and transient chemistry (μ(t)) can be investigated to correlate the sintering conditions to microstructural evolution and property (Bang et al., 2020b). One major challenge of large sample sintering is that the microstructure and property homogeneity across the sample need to be better understood and well-controlled. Because transient chemistry drives the cold sintering process in an open system, the stochastic localized evaporation, a key factor, may lead to a major processing issue that limits sample homogeneity. Such a challenge was not obvious in laboratory-scale cold sintering due to the small amount of the transient chemistry and high pressure that yielded homogeneous samples (Hérisson de Beauvoir et al., 2020).
4 Conclusions and perspectives
This mini-review summarized the mechanism of cold sintering and its recent progress in interface engineering for battery material and manufacturing. Based on the merits of the cold sintering process, composite electrodes, solid-state electrolytes, and laminated cell devices can be consolidated into a dense form, which significantly can improve the conductivities and volumetric battery performance. Furthermore, the interface engineering between different phases and components offers a possible solution to enhance the charge transports across the interfaces, such as “grain boundaries.” In fact, cold sintering is an energy-efficient manufacturing process that enables the consolidation and densification of dissimilar materials, including polymers, ceramics, and metals, due to the low processing temperature. However, the electrochemical performance of the sintered electrodes, electrolytes, and laminated devices is still far behind the demands for real applications, especially the high-rate performance and long cycling stability. Therefore, it’s desirable to provide insight into interface engineering for more efficient charge transport kinetics across various interfaces. The studies of the interaction between transient solvents and powder particles will provide more insights into the cold sintering mechanism to further lower the energy dissipation. Moreover, it will require a further fundamental understanding to explore the possible scale-up cold sintering process. Specifically, the challenges associated with scale-up include: dispersion of transient phase throughout the particles; uniform re-arrangement and compactions of powders; minimization of stress gradients under uniaxial pressure; uniform loss of transient chemistries throughout the sintering process; homogeneous heat transfer to drive the sintering uniformly through the components. To this end, methodology approaches for in-line monitoring and closed-loop quality control need to be developed for aiding the scale-up processing. In addition, low-temperature sintering is crucial to enable re-processing and prevent side reactions that might occur between components at high temperature. Thus, cold sintering provides a unique opportunity for recycling composites. Overall, the CSP is a low-energy-consumption sintering process, which impacts composite manufacturing and many energy-related applications such as energy storage.
Author contributions
BN, HS, TL wrote the first draft of the manuscript, JL, MA, SK, SB, ML reviewed and edited the manuscript. All authors contributed to manuscript revision, read, and approved the submitted version.
Funding
NSF FMSG (2134643), NSF PREM program under Award DMR (2122178).
Acknowledgments
HS would like to thank NSF FMSG (2134643) and Pennsylvania State University start-up fund for partial support of this work. MA acknowledges the partial support received from the NSF PREM program under Award DMR-2122178: UTRGV-UMN Partnership for Fostering Innovation by Bridging Excellence in Research and Student Success.
Conflict of interest
The authors declare that the research was conducted in the absence of any commercial or financial relationships that could be construed as a potential conflict of interest.
Publisher’s note
All claims expressed in this article are solely those of the authors and do not necessarily represent those of their affiliated organizations, or those of the publisher, the editors and the reviewers. Any product that may be evaluated in this article, or claim that may be made by its manufacturer, is not guaranteed or endorsed by the publisher.
References
Banerjee, A., Wang, X., Fang, C., Wu, E. A., and Meng, Y. S. (2020). Interfaces and interphases in all-solid-state batteries with inorganic solid electrolytes. Chem. Rev. 120, 6878–6933. doi:10.1021/acs.chemrev.0c00101
Bang, S. H., Ndayishimiye, A., and Randall, C. A. (2020). Anisothermal densification kinetics of the cold sintering process below 150 °C. J. Mater. Chem. C 8, 5668–5672. doi:10.1039/D0TC00395F
Bang, S. H., Tsuji, K., Ndayishimiye, A., Dursun, S., Seo, J.-H., Otieno, S., et al. (2020). Toward a size scale-up cold sintering process at reduced uniaxial pressure. J. Am. Ceram. Soc. 103, 2322–2327. doi:10.1111/jace.16976
Berbano, S. S., Guo, J., Guo, H., Lanagan, M. T., and Randall, C. A. (2017). Cold sintering process of Li1.5Al0.5Ge1.5(PO4)3 solid electrolyte. J. Am. Ceram. Soc. 100, 2123–2135. doi:10.1111/jace.14727
Biesuz, M., Saunders, T. G., Grasso, S., Speranza, G., Sorarù, G. D., Campostrini, R., et al. (2019). Flash joining of conductive ceramics in a few seconds by flash spark plasma sintering. J. Eur. Ceram. Soc. 39, 4664–4672. doi:10.1016/j.jeurceramsoc.2019.07.036
de Beauvoir, T. H., Dursun, S., Gao, L., and Randall, C. (2019). New opportunities in metallization integration in cofired electroceramic multilayers by the cold sintering process. ACS Appl. Electron. Mater. 1, 1198–1207. doi:10.1021/acsaelm.9b00184
Dursun, S., Tsuji, K., Bang, S. H., Ndayishimiye, A., and Randall, C. A. (2020). A route towards fabrication of functional ceramic/polymer nanocomposite devices using the cold sintering process. ACS Appl. Electron. Mater. 2, 1917–1924. doi:10.1021/acsaelm.0c00225
Funahashi, S., Guo, J., Guo, H., Wang, K., Baker, A. L., Shiratsuyu, K., et al. (2017). Demonstration of the cold sintering process study for the densification and grain growth of ZnO ceramics. J. Am. Ceram. Soc. 100, 546–553. doi:10.1111/jace.14617
Gonzalez-Julian, J., Neuhaus, K., Bernemann, M., Pereira da Silva, J., Laptev, A., Bram, M., et al. (2018). Unveiling the mechanisms of cold sintering of ZnO at 250 °C by varying applied stress and characterizing grain boundaries by Kelvin Probe Force Microscopy. Acta Mater. 144, 116–128. doi:10.1016/j.actamat.2017.10.055
Grady, Z., Fan, Z., Ndayishimiye, A., and Randall, C. A. (2021). Design and sintering of all-solid-state composite cathodes with tunable mixed conduction properties via the cold sintering process. ACS Appl. Mater. Interfaces 13, 48071–48087. doi:10.1021/acsami.1c13913
Grasso, S., Biesuz, M., Zoli, L., Taveri, G., Duff, A. I., Ke, D., et al. (2020). A review of cold sintering processes. Adv. Appl. Ceram. 119, 115–143. doi:10.1080/17436753.2019.1706825
Gundersen, E., Renard, F., Dysthe, D. K., Bjørlykke, K., and Jamtveit, B. (2002). Coupling between pressure solution creep and diffusive mass transport in porous rocks. J. Geophys. Res. Solid Earth 107, ECV 19-21–ECV 19-19. ECV 19-1-ECV 19-19. doi:10.1029/2001JB000287
Guo, H., Baker, A., Guo, J., and Randall, C. A. (2016). Cold sintering process: A novel technique for low-temperature ceramic processing of ferroelectrics. J. Am. Ceram. Soc. 99, 3489–3507. doi:10.1111/jace.14554
Guo, J., Floyd, R., Lowum, S., Maria, J.-P., Herisson de Beauvoir, T., Seo, J.-H., et al. (2019). Cold sintering: Progress, challenges, and future opportunities. Annu. Rev. Mater. Res. 49, 275–295. doi:10.1146/annurev-matsci-070218-010041
Guo J, J., Guo, H., Baker, A. L., Lanagan, M. T., Kupp, E. R., Messing, G. L., et al. (2016). Cold sintering: A paradigm shift for processing and integration of ceramics. Angew. Chem. Int. Ed. Engl. 55, 11457–11461. doi:10.1002/anie.201605443
Guo, J., Zhao, X., Herisson De Beauvoir, T., Seo, J.-H., Berbano, S. S., Baker, A. L., et al. (2018). Recent progress in applications of the cold sintering process for ceramic–polymer composites. Adv. Funct. Mater. 28, 1801724. doi:10.1002/adfm.201801724
Haug, M., Bouville, F., Adrien, J., Bonnin, A., Maire, E., and Studart, A. R. (2020). Multiscale deformation processes during cold sintering of nanovaterite compacts. Acta Mater. 189, 266–273. doi:10.1016/j.actamat.2020.02.054
Hérisson de Beauvoir, T., Tsuji, K., Zhao, X., Guo, J., and Randall, C. (2020). Cold sintering of ZnO-PTFE: Utilizing polymer phase to promote ceramic anisotropic grain growth. Acta Mater. 186, 511–516. doi:10.1016/j.actamat.2020.01.002
Hu, Q., Sun, Z., Nie, L., Chen, S., Yu, J., and Liu, W. (2022). High-safety composite solid electrolyte based on inorganic matrix for solid-state lithium-metal batteries. Mater. Today Energy 27, 101052. doi:10.1016/j.mtener.2022.101052
Huang, S., Wu, H., Chen, P., Guo, Y., Nie, B., Chen, B., et al. (2015). Facile pH-mediated synthesis of morphology-tunable MnCO3 and their transformation to truncated octahedral spinel LiMn2O4 cathode materials for superior lithium storage. J. Mater. Chem. A 3, 3633–3640. doi:10.1039/C4TA06522K
Jiang, P., Guo, P., Shi, Y., Li, S., Li, K., Lu, X. Y., et al. (2021). Solid-state Li metal battery enabled by cold sintering at 120 °C. Mater. Today Phys. 20, 100476. doi:10.1016/j.mtphys.2021.100476
Lee, W., Lyon, C. K., Seo, J.-H., Lopez-Hallman, R., Leng, Y., Wang, C.-Y., et al. (2019). Ceramic–salt composite electrolytes from cold sintering. Adv. Funct. Mater. 29, 1807872. doi:10.1002/adfm.201807872
Liu, Y., Liu, J., Sun, Q., Wang, D., Adair, K. R., Liang, J., et al. (2019). Insight into the microstructure and ionic conductivity of cold sintered NASICON solid electrolyte for solid-state batteries. ACS Appl. Mater. Interfaces 11, 27890–27896. doi:10.1021/acsami.9b08132
Lóh, N. J., Simão, L., Faller, C. A., De Noni, A., and Montedo, O. R. K. (2016). A review of two-step sintering for ceramics. Ceram. Int. 42, 12556–12572. doi:10.1016/j.ceramint.2016.05.065
Lu, R., Cheng, C., Nagel, T., Milsch, H., Yasuhara, H., Kolditz, O., et al. (2021). What process causes the slowdown of pressure solution creep. Geomechanics Geophys. Geo-Energy Geo-Resources 7, 57. doi:10.1007/s40948-021-00247-4
Nur, K., Roitzheim, C., Finsterbusch, M., Bram, M., and Guillon, O. (2022). Cold sintered LiMn2O4 for high-rate capability electrodes. J. Electrochem. Soc. 169, 020556. doi:10.1149/1945-7111/ac5348
Sada, T., Tsuji, K., Ndayishimiye, A., Fan, Z., Fujioka, Y., and Randall, C. A. (2021). High permittivity BaTiO3 and BaTiO3-polymer nanocomposites enabled by cold sintering with a new transient chemistry: Ba(OH)2∙8H2O. J. Eur. Ceram. Soc. 41, 409–417. doi:10.1016/j.jeurceramsoc.2020.07.070
Seo, J.-H., Fan, Z., Nakaya, H., Rajagopalan, R., Gomez, E. D., Iwasaki, M., et al. (2021). Cold sintering, enabling a route to co-sinter an all-solid-state lithium-ion battery. Jpn. J. Appl. Phys. 60, 037001. doi:10.35848/1347-4065/abdd4c
Seo, J.-H., Guo, J., Guo, H., Verlinde, K., Heidary, D. S. B., Rajagopalan, R., et al. (2017). Cold sintering of a Li-ion cathode: LiFePO4-composite with high volumetric capacity. Ceram. Int. 43, 15370–15374. doi:10.1016/j.ceramint.2017.08.077
Seo, J.-H., Nakaya, H., Takeuchi, Y., Fan, Z., Hikosaka, H., Rajagopalan, R., et al. (2020). Broad temperature dependence, high conductivity, and structure-property relations of cold sintering of LLZO-based composite electrolytes. J. Eur. Ceram. Soc. 40, 6241–6248. doi:10.1016/j.jeurceramsoc.2020.06.050
Seo, J.-H., Verlinde, K., Rajagopalan, R., Gomez, E. D., Mallouk, T. E., and Randall, C. A. (2019). Cold sintering process for fabrication of a high volumetric capacity Li4Ti5O12 anode. Mater. Sci. Eng. B 250, 114435. doi:10.1016/j.mseb.2019.114435
Sohrabi Baba Heidary, D., Lanagan, M., and Randall, C. A. (2018). Contrasting energy efficiency in various ceramic sintering processes. J. Eur. Ceram. Soc. 38, 1018–1029. doi:10.1016/j.jeurceramsoc.2017.10.015
Sun, H., Zhu, J., Baumann, D., Peng, L., Xu, Y., Shakir, I., et al. (2019). Hierarchical 3D electrodes for electrochemical energy storage. Nat. Rev. Mater. 4, 45–60. doi:10.1038/s41578-018-0069-9
Takashima, K., Iwazaki, Y., and Randall, C. A. (2021). Cold sintering for Li1.5Al0.5Ge1.5(PO4)3 using LiNO3-LiOH as a transient solvent. Jpn. J. Appl. Phys. 60, 126505. doi:10.35848/1347-4065/ac33cf
Wang, X., Wang, J., Li, F., Zhu, F., and Ma, C. (2020). Influence of cold sintering process on the structure and properties of garnet-type solid electrolytes. Ceram. Int. 46, 18544–18550. doi:10.1016/j.ceramint.2020.04.160
Wu, X., Xia, S., Huang, Y., Hu, X., Yuan, B., Chen, S., et al. (2019). High-performance, low-cost, and dense-structure electrodes with high mass loading for lithium-ion batteries. Adv. Funct. Mater. 29, 1903961. doi:10.1002/adfm.201903961
Zhang, J., Wang, L., Liu, A., Zhang, Y., Li, Z., Chen, H., et al. (2022). Effect of LiOH solution additives on ionic conductivity of Li6.25Al0.25La3Zr2O12 electrolytes prepared by cold sintering. J. Mater. Sci. Mater. Electron. 33, 19187–19194. doi:10.1007/s10854-022-08756-y
Zhang, Y., Liu, A., Shi, Z., Ge, S., and Zhang, J. (2022). Microstructure and ion conductivity of Al-LLZO solid electrolyte prepared by molten salt and cold sintering process. Int. J. Appl. Ceram. Technol. 19, 320–331. doi:10.1111/ijac.13873
Zhao N, N., Khokhar, W., Bi, Z., Shi, C., Guo, X., Fan, L.-Z., et al. (2019). Solid garnet batteries. Joule 3, 1190–1199. doi:10.1016/j.joule.2019.03.019
Keywords: cold sintering, interface engineering, composites, solid state battery (SSB), manufacturing
Citation: Nie B, Liu T, Alcoutlabi M, Basu S, Kumara S, Li M, Lian J and Sun H (2023) Cold sintering-enabled interface engineering of composites for solid-state batteries. Front. Energy Res. 11:1149103. doi: 10.3389/fenrg.2023.1149103
Received: 21 January 2023; Accepted: 13 February 2023;
Published: 21 February 2023.
Edited by:
Sheng S. Zhang, United States Army Research Laboratory, United StatesReviewed by:
Wei Liu, ShanghaiTech University, ChinaCopyright © 2023 Nie, Liu, Alcoutlabi, Basu, Kumara, Li, Lian and Sun. This is an open-access article distributed under the terms of the Creative Commons Attribution License (CC BY). The use, distribution or reproduction in other forums is permitted, provided the original author(s) and the copyright owner(s) are credited and that the original publication in this journal is cited, in accordance with accepted academic practice. No use, distribution or reproduction is permitted which does not comply with these terms.
*Correspondence: Hongtao Sun, aG9uZ3Rhby5zdW5AcHN1LmVkdQ==