- Center for Transportation and Logistics, Massachusetts Institute of Technology, Cambridge, MA, United States
Circular supply chains comprise the industrial production and supply chain systems used by companies to eliminate waste and recover value in products and materials. There are a variety of circular strategies including recycling in waste management, returns and repair in consumer-facing industries, and reusable packaging in supply chains. Successful implementation and management of these circular strategies requires the ability to measure and report on progress across different functions and processes. In this paper, we propose a new set of metrics to measure the performance of reusing items in a circular supply chain. We review the literature on metrics in circular supply chain management and reusable packaging in supply chains. We then classify the proposed metrics based on whether they measure the circularity of a circular supply chain initiative or impact of implementing the initiative. They also are segmented based on the level of detail they incorporate from the product level to the system level. We then demonstrate the use of the proposed metrics through a case study with an omnichannel retail company. We find that product-level metrics facilitate the comparison of different types of reusable and single-use packages with the potential to reduce lifecycle greenhouse gas emissions. We also find that measuring system-level Total Logistics Costs helps identify potential challenges with the feasibility of a reusable packaging system including the implications of not recovering packages and amortizing initial costs across multiple use cycles. Our aim in this paper is to address the gap in circularity and impact metrics focused on reuse strategies in supply chains. This new set of metrics provides companies with a tool to measure and report on progress toward a circular economy. It also suggests future avenues for research to assess the economic, environmental, and social dimensions of sustainability.
Introduction
Supply chains are the backbone of the modern economy. They also play a central role in the emission of greenhouse gases (Scott et al., 2018), depletion of critical material resources (Sovacool et al., 2020), accumulation of waste in the environment (Geyer et al., 2017; Tisserant et al., 2017), and other pressures on the natural environment (Hoekstra and Wiedmann, 2014). One solution that has been proposed to address these challenges is the concept of a circular economy (CE), which decouples economic growth from material depletion and waste generation by encouraging the reduction and reuse of products and materials (Stahel, 2016; Geissdoerfer et al., 2017). The concept of a CE was first introduced in Pearce and Turner (1990), and has gained increasing attention over the last two decades from governments, scholars, companies, and consumers (Ghisellini et al., 2016; Schöggl et al., 2020). CE is seen as a new business model that operationalizes sustainable development (Kirchherr et al., 2017). This requires balancing consideration of the economic, environmental, and social (EES) aspects of the economy, sector, or individual industrial process (Ghisellini et al., 2016). There are now national and international policies related to CE in China, the European Union, Norway, the United Kingdom, and other countries (Fan and Fang, 2020; Mhatre et al., 2021). Ellen MacArthur Foundation (2013), WBCSD (2021), WEF (2021), and other organizations have raised awareness of CE concepts at consumer, corporate, and policy levels. There is also a growing body of research that has been published on the topic of CE (Schöggl et al., 2020; De Pascale et al., 2021; Sarja et al., 2021).
By definition, the concept of a CE refers to the industrial production and supply chain systems that are designed to eliminate waste and recover value in products and materials (Batista et al., 2018). Once products are made, reverse logistics operations recover them from consumers and bring them back into the forward supply chain (Govindan and Soleimani, 2017). Closed-loop supply chains integrate both forward and reverse supply chains, but do not account for open-loop flows of by-products and wastes (Govindan and Soleimani, 2017). Circular supply chains (CSC) comprise both closed-loop and open-loop flows of products and materials in a CE (Batista et al., 2018; Geissdoerfer et al., 2018). In this paper, we embrace the definition of circular supply chain management (CSCM) proposed by (Farooque et al., 2019, p. 884): “Circular supply chain management is the integration of circular thinking into the management of the supply chain and its surrounding industrial and natural ecosystems. It systematically restores technical materials and regenerates biological materials toward a zero-waste vision through system-wide innovation in business models and supply chain functions from product/service design to end-of-life and waste management, involving all stakeholders in a product/service life cycle including parts/product manufacturers, service providers, consumers, and users.”
CSCM is characterized by a variety of performance objectives including: minimizing waste, inventory, and the use of materials, water, and energy; and maximizing the availability of products, the number of recovery flows, and the efficient use of supply chain assets (Vegter et al., 2020). To achieve these objectives, nine circular strategies (called “R's” or “R-strategies”) have been proposed Van Buren et al. (2016) including: Refuse (preventing raw material use), Reduce (increase efficiency in production or use), Reuse (secondhand or sharing), Repair (and maintenance), Refurbish (restoring an old product), Remanufacture (new product from old parts), Repurpose (reuse with different purpose), Recycle (reuse materials), and Recover (energy from incineration). A 10th R is sometimes added to the framework for Rethinking product use (Kirchherr et al., 2017). These strategies form closed loops for product and material flows in a CE with product life extension and reuse strategies referred to as “inner circles” or “inner loops,” and end-of-life (EOL) management and recycling forming “outer circles” or “outer loops” (Ellen MacArthur Foundation, 2013).
Given the variety of CE strategies, efforts have been made to prioritize them based on application within the value chain and the impact on critical materials, waste generation, and other CE objectives (Ellen MacArthur Foundation, 2013; Kirchherr et al., 2017; Kalmykova et al., 2018). Shorter loop strategies focused on product use and life extension (e.g., reuse, repair, and refurbish) are considered to hold the greater potential to reduce environmental impact and create economic value than the outer loops focused on EOL management (e.g., remanufacturing and recycling; Ellen MacArthur Foundation, 2013; Stahel, 2013). And though many of the concepts of CE came from the waste management sector, there is a long history of sharing, reusing, and repairing products in the consumer segment as well as reusable packaging in supply chains (Hazen et al., 2021).
In the consumer segment, Kalmykova et al. (2018) found that short loop strategies are one of the most active areas of implementation. Out of the over 100 implementation cases they sampled across the full value chain from materials sourcing and product design to recycling and disposal, ~10% of the cases were focused on reuse, sharing, and product-as-a-service or pay-per-use strategies. However, they found almost 50% of the cases were implemented in the collection, disposal, recovery, and recycling segments of the value chain. These outer loops are also where there is the most institutional support in China, the EU, and Japan, which can have the greatest impact on successful implementation of CE strategies in supply chains (Govindan and Hasanagic, 2018; Kalmykova et al., 2018).
In this research we focus on key metrics to measure the impact of reusable packaging in circular supply chains. Packaging plays an important role in supply chains, enabling the safe and efficient storage, handling, transportation, and sale of goods (Meherishi et al., 2019). And while reusable packaging is a well-known strategy, most packaging is designed to be disposed of after a single use (Escursell et al., 2021). As a result, packaging also uses large quantities of material resources and is a significant source of municipal and industrial solid wastes. In Europe, for example, packaging uses 40% of plastics and 50% of paper while contributing 36% of solid municipal waste (Coelho et al., 2020). Globally, plastic packaging accounts for roughly half of all plastic waste generated (Geyer et al., 2017). Reusable packaging, such as glass milk containers or fabric grocery bags, can replace single-use packaging throughout the supply chain resulting in lower life cycle greenhouse gas (GHG) emissions and reducing post-consumer waste (Goellner and Sparrow, 2014; Zimmermann and Bliklen, 2020; Fashion for Good, 2021). However, these benefits depend on the characteristics and performance of the reusable packaging system (Goudenege et al., 2013; Accorsi et al., 2014; Zimmermann and Bliklen, 2020).
Successful implementation and management of reusable packaging and other CE strategies in supply chains requires the ability to measure and report on progress across different functions and processes (Vegter et al., 2021). Metrics provide information for decision making, controlling the execution of strategy, and reporting to a variety of stakeholders (Neely et al., 1995; Maestrini et al., 2017). Supply chain metrics typically focus on economic performance (Maestrini et al., 2017). However, Dai and Tang (2021) argue that supply chain operations should be incorporated into environmental, social, and governance (ESG) measures, and ESG measures should play a central role in supply chain management (SCM) practices (Sarja et al., 2021). The literature on metrics in CSCM is sparse, but Vegter et al. (2021) found that performance metrics in CSCM expand on the economic focus in SCM by incorporating elements of circularity, environmental and, currently to a lesser degree, social considerations. Most of these metrics are in early stages of development (Acampora et al., 2017; Walker et al., 2018; Vegter et al., 2021), and despite the variety of R-strategies in a CE, product and enterprise-level metrics currently focus on recycling, remanufacturing, and other EOL strategies rather than reuse and other short-loop strategies (Kristensen and Mosgaard, 2020).
Reuse, and more specifically reusable packaging in supply chains, is a strategy to make progress toward reducing pressure on critical resources, reducing waste generation, and realizing the vision of a CE. In order to do so, key metrics are needed to manage the performance of a CSC with reusable packages or other items. However, the literature on metrics in CSCM is sparse (Vegter et al., 2021) and primarily focuses on recycling and other EOL management strategies rather than reuse and product life extension (Saidani et al., 2019; Kristensen and Mosgaard, 2020; De Pascale et al., 2021). Thus, the objectives of this paper are to:
• Review the literature on metrics in circular supply chain management and reusable packaging in supply chains.
• Propose a new set of metrics to measure the performance of reusing items in a circular supply chain.
• Demonstrate, through a case study, the use of these new metrics with an omnichannel retail company.
In the next section we review the literature on metrics used to measure circularity and EES impact in a CE and for CSCM. We also review the literature on metrics used to manage the performance of reusable packaging in supply chains. Building on this background, we then propose a new set of metrics to measure circularity and impact of reusable packaging in circular supply chains. We also demonstrate the use of these metrics with a case study and conclude with a discussion of what we found in this study and future research directions.
Literature review
There is a growing body of research on developing and testing metrics for supply chains in a CE. This paper will focus on research related to measuring the performance of reusing items in a circular supply chain. Google Scholar and MIT Library databases were used to find relevant publications including early works on topics related to circular economy and a focus on publications from the last 5 years. The primary search terms used were “circular economy,” “circular supply chain,” and “reusable packaging.”
This paper will not provide a comprehensive or systematic review of this literature. Several existing literature reviews aim to do this and provide further guidance for this paper. Corona et al. (2019) reviewed 19 circularity metrics and assessment frameworks. They define criteria that a set of metrics should meet including the degree to which it measures what it intends to (validity), the consistency and robustness of the metric (reliability), and how practical it is (utility). The focus of their review is on the validity of metrics based on eight CE goals. They classify metrics into three groups: metrics measuring the degree of circularity (“circularity indices”), metrics that assess the effects of circularity (“CE assessment indicators”), and assessment frameworks such as Life Cycle Assessment (LCA) and Material Flow Analysis (MFA). For each category, they identified metrics focused on the product/enterprise level and/or at the sector/region/global level. They found there is a trade-off between scope (R-strategies) and practical usability with most indicators focused on a narrow aspect of CE. Assessment frameworks like LCA, in contrast, were more comprehensive in scope, but more complex to apply and interpret in practice. They also found that all 19 metrics accounted for environmental considerations, seven for economic considerations, and one for social considerations.
Saidani et al. (2019) conducted a similar review of 55 indicators across 10 dimensions including levels (micro, meso, and macro), loops (three of the R's), performance (circularity or impacts), perspective (actual or potential), uses, traversability (generic or sector-specific), dimension, units, format, and sources. They found the majority (>90%) of the indicators at all levels consider recycling while less than half consider reuse. Of the 20 indicators focused on the product or enterprise level (micro), a majority (80%) measure circularity while 40% measure EES impacts and 20% consider both. They also found that only three micro-level indicators were sector-specific. Previous work has found micro-level indicators are still in early stages of development with a low degree of adoption in industrial practices (Acampora et al., 2017; Walker et al., 2018), and Saidani et al. (2019) suggest that more work may be needed to advance the development of new indicators adapted to more specific contexts.
More recently, De Pascale et al. (2021) found similar results in their review of 61 CE indicators across levels, loops (six of the R's), sustainability impact (EES), and other dimensions. The majority (26 of 29) of micro-level indicators considered outer loop strategies (recycling and remanufacturing) while half take reuse strategies into account and none focused on reuse. They also found the majority (19 of 29) of the micro-level indicators focus on environmental and economic impacts, five focus on economic, and two on environmental. No micro-level indicators were focused on social considerations alone, although seven considered all three EES impacts.
Kristensen and Mosgaard (2020) found similar results in their review of thirty CE indicators focused at the micro-level. The majority of the indicators (19) include economic considerations, 12 directly and five indirectly include environmental considerations, and only four include social considerations. They also found that the majority of indicators (21) had a narrow focus on a single aspect of a CE, which may present an overly simplified measure of circularity and risks hindering sustainability more broadly by sub-optimizing. Conversely, they conclude that multidimensional indicators covering CE principals more broadly lack practical usability at the enterprise-level and prioritization of CE principals. While more narrow indicators may avoid these limitations, the indicators Kristensen and Mosgaard (2020) review all focused on recycling, remanufacturing, and other EOL strategies rather than reuse and product life extension strategies. However, reuse may present a more sustainable option than remanufacturing, which in turn may be more sustainable than recycling (Stahel, 2013), and so the lack of prioritization with multidimensional indicators, and the lack of focus on reuse and life extension strategies, misses the potential hierarchy for value creation and sustainability in a CE.
Vegter et al. (2021) conducted a review of 18 performance measurement systems, each consisting of a set of metrics, for CSCM. The authors propose different criteria than Corona et al. (2019) for an effective measurement system in CSCM including:
• Considering multiple dimensions of performance.
• The perspectives of multiple relevant stakeholders.
• The dimensions of circularity (reducing, maintaining, and recovering resources).
• The economic, environmental, and social dimensions of sustainable development.
• Limiting the range of measures to only the critical performance measures.
• Connecting performance on strategic, tactical, and operational levels (vertical integration).
• Aligning measures along processes (horizontal integration) including plan, source, make, deliver, use, return, recover, and enable.
• Recognizing and allowing for trade-offs and synergies with insight into the interdependencies among measures.
They find that social considerations are underrepresented and only two measurement systems provide insight into the interdependencies between circularity and sustainable development. They also find the literature on metrics in CSCM sparse with most in early stages of development that have not been tested in practice. And while the authors assess the level of integration horizontally, vertically, and across the forward and reverse chains, they do not assess the circular strategies (e.g., the 9 R's) each measurement system considers.
Few CE and CSCM metrics focus on the reuse CE strategy, however, reusable packaging is a well-known strategy in supply chains and there is a robust literature discussing packaging materials, reuse operations, and indicators used to manage operations with reusable packaging. Meherishi et al. (2019) conducted a broad review of packaging sustainability in SCM and CE, and found that reuse and return practices are one of the most popular topics studied (22 out of 59). For studies that looked at the EES impacts of packaging in supply chains (35), they found that environmental impacts (22) are studied more than twice as often as economic impacts (10) with only three considering social impacts. Mahmoudi and Parviziomran (2020) focused on reusable packaging and reviewed 86 studies on the environmental and economic impacts, system design, and operations management including performance measurement. They found reusable packaging has been studied in the food and beverage, cold-chain, and automotive industries as well as generic studies applied to any logistic system. Almost half (37) of the studies focused on performance measurements or criteria for measuring, and factors affecting, the environmental and economic impact of reusable packaging. And many of these propose new indices and metrics systems. They also found that more studies looking at environmental and economic impact were published in the last decade compared to decades prior, in contrast to the trend seen for operations management and logistics system design.
Building on these recent reviews, we focus our literature review on metrics in CSCM to identify patterns and common metrics that can be used for reusable items in supply chains. As shown by Corona et al. (2019), Vegter et al. (2021), metrics can be classified based on whether they measure circularity or the EES impact with some measurement systems combining both assessments. Since few CE and CSCM metric systems focus on reuse, we draw on other multidimensional indicators and indicators focused on other R strategies. Additionally, Ghisellini et al. (2016) and subsequent authors classify CE into micro, meso, and macro levels. The assessment of reusable items in supply chains is primarily focused at the micro level, so we use a new classification based on product or supply chain system level of analysis. This classification connects the metrics found in the literature on CE with the literature on SCM where SC problems are focused on the systems level (Choi et al., 2001; Chan and Chan, 2005). It also extends the definition of a supply chain proposed by Stevens (1989) as “a system whose constituent parts include material suppliers, production facilities, distribution services and customers linked together via the feed-forward flow of materials and the feedback flow of information” with the concept of a closed-loop supply chain integrating both forward and reverse flows (Govindan and Soleimani, 2017).
Measuring circularity and impact
Product-level metrics
One of the first circularity indicators that received attention in both practice and academia was the Material Circularity Indicator (MCI) developed by Ellen MacArthur Foundation and Granta Design (2015). The MCI is based on Material Flow Analysis (MFA; Ayres and Simonis, 1994) and focuses on quantifying a single indicator for the circularity of material flows based on a product's bill of materials. The metric is based on a linear flow factor calculated with the quantity (by weight) of materials and components that come from recycled or reused (remanufacture/repurpose loop) sources, and recycling efficiency. It also uses a utility factory based on an estimated lifespan. By focusing on material flows in a production process, the MCI focuses on outer-loop circularity with remanufacturing, repurposing, and recycling strategies. It measures circularity at the product level, which can be aggregated to the company-level based on a weighted average. The MCI focuses on a single circularity metric; however, it also provides complementary risk and impact indicators such as price variation, toxicity, scarcity, energy use, and CO2 emissions. These complementary indicators allow for consideration of EES impacts.
Linder et al. (2017) argued that potential drawbacks with the MCI are the difficulty differentiating recovery pathways based on mass (e.g., recycled material vs. a remanufactured part) and estimating product lifespan, which often can't be measured easily. Instead, Linder et al. (2017) proposed a new product-level circularity (PLC) metric based on MFA for the relative embedded cost of recirculated parts and materials. Their rationale is that costs are more readily available and distinguishable by source. An economic value metric based on market prices can account for material scarcity as well. Linder et al. (2020) then evaluated the relationship between the PLC score and environmental impacts (measured using LCA) for 18 different products. They found a strong and significant negative correlation between product circularity and all three environmental impact measures (global warming potential, abiotic depletion potential, and environmental priority strategy), meaning that as product circularity increases, its environmental impact decreases.
Mesa et al. (2018) extended the product-level assessment to product families, a group of related products that are derived from a common set of components, with a set of six circularity metrics. In the product development process, the product family approach is a widely-used strategy to satisfy a variety of customer requirements with a more efficient manufacturing process. The six metrics they proposed measure material flows (by mass), component reusability (for remanufacturing/repurposing), reconfigurability, and functional performance. Similar to the MCI and PLC, Mesa et al. (2018) focused on outer-loop circularity. They also didn't assess the EES impacts of their circularity metrics, but they did evaluate the use of their metrics in the product development process with a case study (prosthetic fingers) and found circularity metrics can be used to optimize product design for circularity and functionality.
More recently, Bracquené et al. (2020) proposed a product circularity indicator (PCI) taking into account different recovery pathways using an MFA for mass at the material and component level rather than the product level like the MCI and PLC. They proposed a utility factor similar to MCI as well. By accounting for material losses in feedstock and component production, the PCI better reflects the benefits of using remanufactured parts compared to recycled materials. Bracquené et al. (2020) demonstrated the application of the PCI with a case study (washing machines) and a LCA to measure the environmental impacts of different circularity scenarios. They found that the PCI was an effective measure for primary material flows and impacts from the production phase. However, it was not able to effectively account for the production impacts of complex components like printed circuit boards nor impacts during the use phase, which are significant for an energy-intensive product like a washing machine. Similar to the MCI and other product circularity metrics, the PCI focuses on outer-loop circularity.
Product reuse is the shortest loop in the 9R framework involving the flow of products and materials and highlighted as a key strategy in CE (Korhonen et al., 2018). As mentioned above, however, few indicators focus on product reuse. One tool that attempts to address this discrepancy is the Circularity Calculator (CC) developed by IDEAL & CO (de Pauw et al., 2021). The CC provides four separate product-level metrics. Circularity (1) is measured using mass flows similar to the MCI. Value capture (2) assesses the economic impact of product design and production strategies based on the economic value of the materials from open, closed, remanufactured, and refurbished loops. Cycled content (3) assesses the percentage of a product's mass that comes from recycled and/or rapidly renewable resources. Finally, reuse is assessed based on the potential number of cycles a product can be used compared to a single-use product (one use cycle).
System-level metrics
Similar to product-level indicators, system-level indicators focus on outer loop circularity. Graedel et al. (2011) defined metrics that measure the circularity of metal production and scrap supply chains including the collection rate, process efficiency, recovery rate for scrap metal, and the recycled content and quantity of metal from EOL products. These metrics are used to estimate global recycling statistics, but would scale by redefining system boundaries to a more specific metal production, scrap, and recycling chain.
Brown and Bajada (2018) proposed two performance indicators for a recycling network that incorporate multiple stakeholder effects with multi-stakeholder collaboration including the impact of the speed of recycling and the effectiveness of collection and conversion of recycled material on production, and the upper bound of production for a given amount of recyclable material in the system. Based on a theoretical analysis, they found that cycle velocity, a factor not considered by other indicators, is positively related to production performance and recycling activity among stakeholders is driven by stakeholder collaboration and engagement.
Olugu et al. (2011) developed a set of sixteen circularity and EES performance measures for the automotive supply chain. While the lifespan of automobiles is frequently extended with reuse and repair strategies, Olugu et al. (2011) focused on the circular production supply chain which involves disassembly of EOL vehicles for remanufacturing or repurposing parts, then shredding the remaining vehicle for material recycling. They considered both the forward and backward chain. They then validated the set of metrics with thirty-three experts from academia and industry and found customer commitment to be the most important metric for the forward chain followed by quality, supplier commitment, and management commitment. Management was found to be the most important metric for the reverse chain followed by material features and recycling efficiency.
Some studies at the system-level focus on the EES impacts of a circular supply chain. Haghighi et al. (2016) proposed a balanced scorecard of indicators that measure EES performance in a recycling supply chain. They combined both quantitative and qualitative indicators in a multi-echelon network model, and tested it with data from 40 plastic recycling companies. They found that at the supplier echelon, the model is most sensitive to eliminating hazardous materials, flexibility was the most important indicator for the manufacturer echelon, and delivery cost was the most important factor for the distributor and retailer echelons. The model was almost equally sensitive to delivery time and customer satisfaction at the retailer echelon as well.
Ansari et al. (2020) focused on measuring EES impact as well. They identified 20 different indicators classified along the management processes of the supply chain operations reference (SCOR) model for a remanufacturing supply chain. They tested the complex relationships between indicators using a case study (remanufacturing business), and found that indicators for consumer awareness, technological compatibility, and workforce skill-level may be the most important in remanufacturing supply chains.
Measuring the performance of reusable packaging in supply chains
Out of all of the general CSCM metrics we reviewed, only the Circularity Calculator (de Pauw et al., 2021) included a direct measure of strategies that extend product life (maintenance, reuse, and repair). However, reusable packaging is a well-known strategy in supply chains. It is also one of the most popular topics studied related to packaging sustainability with many focused on performance measurements or criteria for measuring, and factors affecting, the environmental and economic impact of reusable packaging (Meherishi et al., 2019; Mahmoudi and Parviziomran, 2020).
Packaging can be classified based on its proximity to a product and functionality in the supply chain (Pålsson, 2018). Primary packaging (e.g., a shampoo bottle) surrounds a product, and provides convenience and protection, until the product is used by the end consumer. A secondary package (e.g., a corrugated box used for e-commerce shipping) is used to protect primary packages and bundle products into case quantities. Finally, tertiary packages (e.g., pallets) are used for bulk handling.
One of the first studies to look at the environmental impact of reuse and recycling in packaging systems was Tsiliyannis (2005). They developed a combined reuse/recycle model that measured the environmental performance of packaging systems based on virgin material demand and discarded waste. Using a theoretical analysis, they found that the total amount of packaging material that flows to consumers was a better indicator than the total number of reuse cycles, reuse rate, and recycling rate.
Goudenege et al. (2013) later developed a network model to compare the total costs and life cycle GHG emissions CO2-equivalent or (CO2e) for reusable (plastic cartons) and single-use (cardboard) secondary packages. The model was applied to a retail supply chain with forward and reverse flows between retail stores and distribution warehouses. They found that both total cost and life cycle emissions were lower for reusable packages if the backhaul between stores and warehouses is utilized with transportation costs negotiated lower than for the forward flow. If the backhaul is not utilized then costs and life cycle emissions are higher.
Goellner and Sparrow (2014), in contrast, found that environmental impacts are not as sensitive to backhaul transportation costs in cold chain logistics. They used a LCA to evaluate the global warming potential, acidification emission, eutrophication emissions, photochemical ozone emissions, human toxicity emissions, and post-consumer waste of single-use and reusable secondary packages for pharmaceutical and biological materials. Given the thermal control requirements of secondary packages in the cold chain, the impact of packaging manufacturing (cradle-to-gate) was significantly higher than the use and EOL phases.
Single-use packaging is common in the food industry as well including plastic bags and plastic or cardboard boxes that serve as primary packages as well as the cardboard boxes, wooden boxes, and disposal plastic crates used as secondary and tertiary packages. Accorsi et al. (2014) evaluated the economic and environmental impact of using a reusable plastic container (RPC) to carry fresh produce between farms and caterers in a food catering supply chain. They used LCA to measure the carbon footprint of packages and Life Cycle Costing (LCC) to measure infrastructure, storage, manufacturing, transportation, operating, and disposal costs. Compared to single-use packages, they found the RPCs would reduce life cycle GHG emission but increase overall costs. Within the supply chain, farmers would likely benefit from lower costs with distributors bearing the net cost increase.
Zimmermann and Bliklen (2020) conducted a similar study for secondary packages used in e-commerce shipping. Using a LCA of CO2e emissions, they found that the majority of emissions for a reusable plastic bag and a reusable plastic box come from the initial production of the package followed by the forward transportation from retailer to customer. This life cycle footprint is then translated into the number of times a reusable package has to be used in order to achieve a lower footprint compared to the single-use package it would replace (the breakeven point). They found that the breakeven point for a reusable plastic box was 61 cycles compared to a standard cardboard box, 81 cycles compared to a cardboard box made from post-consumer fiber, and 32 cycles if the reusable box is made from post-consumer plastic. For a reusable plastic bag, the breakeven point was 20 cycles compared to a single-use plastic bag and only three cycles if the reusable bag was made from post-consumer plastic. This suggests that the number of reuse cycles, and factors that affect it such as the return rate by customers, has a significant impact on the environmental performance of reusable secondary packages in e-commerce.
Similar factors can affect the economic impact of reusable packaging as well. Mollenkopf et al. (2005) showed that reusable packaging is more economical for larger, bulk packaging with a high daily demand. Return rate, transportation costs, cycle times, delivery distance, fluctuation in maximum daily volume, and other factors can affect the economic impact as well (Mollenkopf et al., 2005; Breen, 2006; Cobb, 2016).
Proposed set of metrics
As discussed in the previous section, we found that few CE and CSCM metrics systems take into account reuse, repair, and other CE strategies that extend product lifespans. There is, however, a robust literature discussing strategies and operations including performance metrics for reusable packaging in supply chains. The focus of this section will be to connect these two bodies of work with a new set of key performance indicators for reusable packaging in circular supply chains.
In this paper, we embrace the definition of CSCM proposed by Farooque et al. (2019) and discussed earlier. That definition is grounded in the goal of systematically restoring technical materials and regenerating biological materials toward a zero-waste vision. Achieving this goal requires engaging all stakeholders from initial product or service design to EOL and waste management. A key activity in circular supply chains is the reverse logistics connecting forward chains with the reverse flow of products and materials. The metrics we propose are designed to help managers and organizations work toward the vision of a CE by measuring the circularity and EES impact of the supply chains they engage with.
Similar to our review of CE and CSCM metrics, we categorize this new set of metrics based on whether they measure the circularity of SC initiatives or the impact of implementing a circular SC initiative. Within each of these groups, a hierarchy starting with the aim of zero waste (level 1) then classifies metrics based on whether the analysis is focused on the product or supply chain system (level 2). Each of the product or system metrics (level 3) are then often a composite of more granular indicators (level 4) focused on components of the product or system. An illustration of this hierarchy can be seen in Figure 1. The hierarchy is meant to clarify the design intent for each of these metrics.
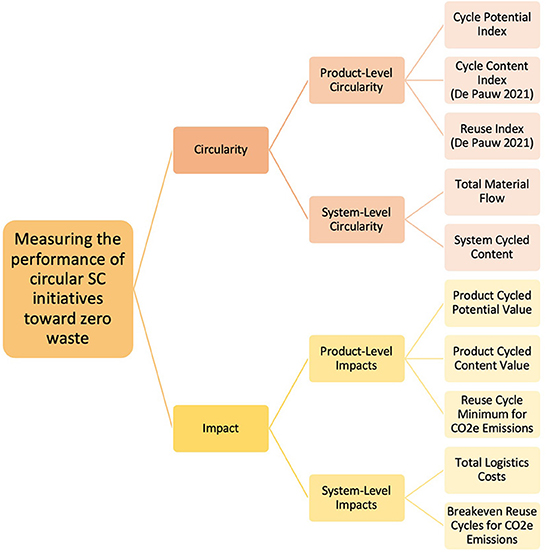
Figure 1. Proposed set of metrics to measure the circularity and impact of reusable packaging in a circular supply chain.
Measuring supply chain circularity
The first set of metrics are focused on measuring the circularity of SC initiatives. As seen in Table 1, we propose three product-level and two system-level composite metrics for the circularity of reusable items in SCM. Each of these metrics is meant to be measured for a fixed period. Previous MFA-based studies have used either mass (Ellen MacArthur Foundation and Granta Design, 2015; Bracquené et al., 2020; de Pauw et al., 2021) or economic value (Linder et al., 2017; de Pauw et al., 2021) for the unit of measure for circularity metrics. There are advantages and limitations to both strategies. In this paper we will define metrics in such a way that either unit of measure could be used. This allows the user to select the unit that best suits their circumstances such as the availability of data. We refer the reader to Bracquené et al. (2020) for additional methodological details on mass-based MFA and Linder et al. (2017) for a cost-based approach.
Product-level metrics
Product Reuse Index
The Product Reuse Index (CRP) is a metric designed to help supply chain managers compare single-use products with reusables whose life can be extended with maintenance, reuse, repair, and similar strategies. In contrast to the CPP and CCP which assess outer loop (EOL) strategies, the CRP is focused on inner loop strategies. It was proposed by de Pauw et al. (2021), and given by,
where N is the number of potential use cycles for a given product.
Product Cycle Potential Index
The Product Cycle Potential Index (CPP) is a metric designed to help supply chain managers assess the potential of a product without knowing future material flows. It is forward-looking and assesses the degree to which components within a product can be put to use in future products as components, materials, or nutrients through remanufacturing, repurposing, recycling, composting, and other EOL strategies. Based on many similar circularity metrics proposed by Ellen MacArthur Foundation and Granta Design (2015), Bracquené et al. (2020), de Pauw et al. (2021) and others, the CPP is defined as the ratio of the mass (or economic value) of materials or components within a product that are potentially reusable and the total product mass (or economic value) given by,
where MPUM is the mass (or economic value) of components that could be remanufactured or repurposed for future products, MPRM is the mass (or economic value) of materials that could be recycled, MPCM is the mass (or economic value) of materials that could be composted, and MTP is the total mass (or economic value) of the product. Additional elements (Mi) could be considered if there are other material flow strategies within the CSCN.
There are three elements of the CPP and the applicability of each depends on the characteristics of a particular product.
Percent of reusable (remanufacture/repurpose) components: CPUM is the ratio of the mass (or economic value) of components within a product that are potentially reusable and the total product mass (or economic value). This metric assesses the degree to which components within a product can be put to use in future products through remanufacturing, in which case new products are made from components of the same product, or repurposing, where new products are made from components of other products. Considerations for the reusability of components include durability, disassemble-ability, and refurbish-ability. Closed-loop systems for reusable components require reverse flows, disassembly processes, and production processes for new products with inputs of remanufactured or repurposed components. This metric is given by,
Percent of recyclable materials: CPRM is defined as the ratio of the mass (or economic value) of materials within a product that are potentially recyclable and the total product mass (or economic value). This metric assesses the degree to which the materials within a product can be put to use in future products by recycling those materials. Considerations for the recyclability of materials include accessibility of the material through efficient disassembly or material extraction processes and existing market capabilities to recycle the specific material. This metric is given by,
Percent of compostable materials: CPCM is defined as the ratio of the mass (or economic value) of materials within a product that are potentially compostable and the total product mass (or economic value). This metric assesses the degree to which the materials within a product will biodegrade with residential or industrial composting processes. Considerations for the compostability of materials include the conditions under which the material biodegrades, accessibility of the material through efficient disassembly or material extraction processes, and existing market capabilities to compost the specific material. This metric is given by,
Combining these three elements gives,
Product Cycled Content Index
The Product Cycled Content Index (CCP) is a backward-looking metric designed to help supply chain managers assess the content used in a product that came from post-consumer, EOL sources. It is based on similar circularity metrics as the CPP. The CCP is defined as the ratio of the mass (or economic value) of materials or components within a product that came from post-consumer sources and the total product mass (or economic value) given by,
where MPUU is the mass (or economic value) of components from post-consumer remanufactured or repurposed sources, MPRU is the mass (or economic value) from post-consumer recycled (PCR), and MTP is the total mass (or economic value) of the product.
There are two elements of the CCP and the applicability of each depends on the characteristics of a particular product. Similar to CPP, additional elements (Mi) could be considered if there are other material flow strategies within the CSCN.
Percent of used (remanufacture/repurpose) components in a product: CPUU is defined as the ratio of the mass (or economic value) of post-consumer components within a product and the total product mass (or economic value). This metric assesses the degree to which the components within a product came from post-consumer remanufactured or repurposed sources. This metric is given by,
Percent of recycled materials used in a product: CPRU is defined as the ratio of the mass (or economic value) of PCR materials within a product and the total product mass (or economic value). This metric assesses the degree to which the materials within a product came from PCR sources. This metric is given by,
Combining these two elements gives,
System-level metrics
System Reuse Index
Similar to the product level, a system level metric focused on inner loop strategies can help supply chain actors compare supply chains with single-use products to reusables where processes bring products back to the system and extend product life with maintenance, reuse, repair, and similar strategies. The System Reuse Index (CRS) is similar to the product-level metric (CRP) and given by,
where N is the average number of use cycles for the reusable products within the system. If the system only contains a single reusable product (e.g., a single type of reusable secondary package) then,
In other cases, the system may be defined for multiple (p) products where n is the number of use cycles for a given (i) product and,
Total material flow
There are two metrics that are designed to help supply chain actors assess the materials that circulate and are disposed of by a circular supply chain network (CSCN) and the materials that are not recovered by the system from end consumers.
Percent of material brought back to the system: CBACK is defined as the ratio of the mass (or economic value) of materials that return back to the CSCN in which they were produced after at least one use cycle by an end consumer and the total mass (or economic value) of production within the system. The boundaries of the CSCN should be clearly defined to identify production output, and closed-loops which return products and materials back to the system. If the end consumer is considered within the boundary of the system then these materials circulate within the system without leaving. This metric is given by,
where MBACK is the mass (or economic value) of materials that return back to the system after one or more uses by an end consumer or circulate within the system, and MTS is the total mass (or economic value) of production within the system.
Percent of material not recovered from end consumers: COUT is defined as the ratio of the mass (or economic value) of materials not recovered from end consumers and the total mass (or economic value) of production within the system. Since these materials are not recovered by the system, their fate will not be known to actors within the CSCN, and so from a systems perspective these are materials lost to the system. Similar to CBACK, the boundaries of the CSCN should be clearly defined. This metric is given by,
where MOUT is the mass (or economic value) of materials not recovered from end consumers.
Combining these two elements gives,
where MIN is the mass (or economic value) of material inputs to the systems from non-recovered sources (e.g., virgin materials).
System cycled content
While the pathway of materials that are not recovered by the system (COUT) will not be known, the pathways for recovered materials (CBACK) are important indicators of the circularity of material flows including recyclable materials and components that can be remanufactured or repurposed.
Percent of components recovered that can be remanufactured/repurposed: CRU is defined as the ratio of the mass (or economic value) of components that return back to the CSCN which can be remanufactured or repurposed for future products and the total mass (or economic value) of production within the system. The system boundary considerations described for CBACK should be considered for this metric as well. This metric is given by,
where MRU is the mass (or economic value) of components that return back to the CSCN which can be remanufactured or repurposed for future products.
Percent of recyclable material recovered: CRR is defined as the ratio of the mass (or economic value) of materials that return back to the CSCN which can be recycled within the system for future products and the total mass (or economic value) of production within the system. The system boundary considerations described for CBACK should be considered for this metric as well. This metric is given by,
where MRR is the mass (or economic value) of materials that return back to the CSCN which can be recycled within the system for future products.
Combining these two elements gives,
and
Measuring the impact of reusable packaging
Given the complexity of EES systems for different products and CSC configurations, the metrics proposed for the assessment of EES impact are more specific to packaging in supply chains. As seen in Table 2, there are three product-level and two system-level composite metrics for measuring the impact of packaging in supply chains. Similar to the previous section on circularity, these metrics are defined with a hierarchy that may include more granular indicators for components of the product or system. These metrics also are based on existing research discussed previously on the performance indicators used to manage reusable packaging in supply chains and the use of LCA to assess environmental impacts. The metrics we propose are not meant to be used as an alternative to, rather as a complement to, LCA. In fact, LCA may be the best methodology to determine the CO2e emissions associated with the metrics proposed below. We did not address the gap in literature on social dimension for reusable packaging and CE assessment more broadly. This is a limitation with this study and opportunity for future research. In the following subsections, we will define each of these metrics and highlight methodological and other considerations.
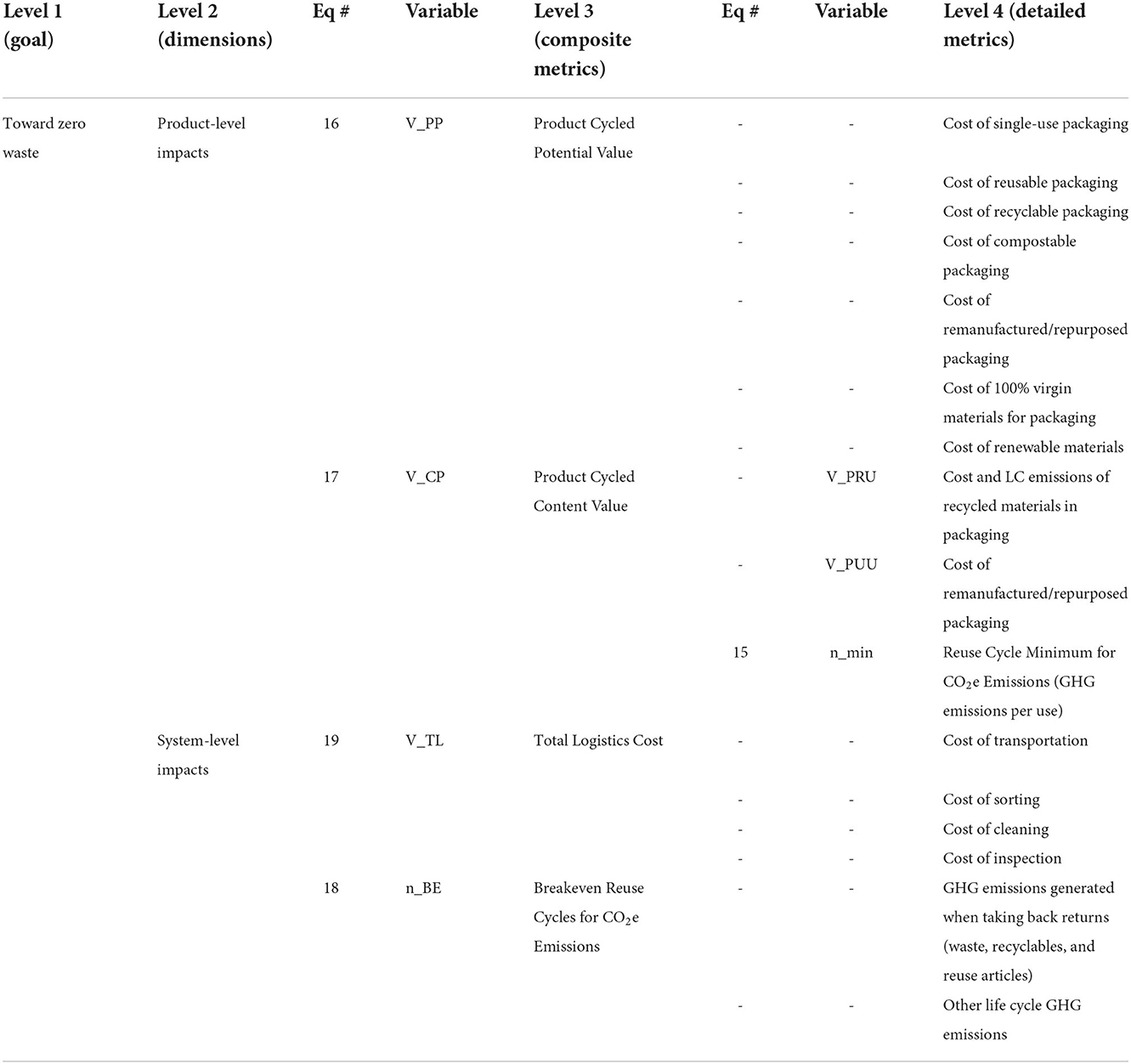
Table 2. Proposed set of metrics to measure the impact of implementing circular supply chain initiatives.
Product-level metrics
Reuse Cycle Minimum for CO2e Emissions
At the product level, there are many approaches to assessing the environmental impact of packages in supply chains. The Reuse Cycle Minimum for CO2e Emissions indicator is designed to help supply chain managers compare the embedded life cycle GHG emissions of reusable and single-use packages at the product level without knowing characteristics of the reusable packaging system. For a single use, CO2e emissions from the upstream fabrication and manufacturing (F&M) life cycle of a reusable package is typically higher due to more durable construction than for a disposable, single-use package (Coelho et al., 2020; Mahmoudi and Parviziomran, 2020; Zimmermann and Bliklen, 2020). However, the F&M emissions for a reusable package can be amortized over multiple use cycles. Therefore, one way to compare the F&M emissions footprint of a reusable package and a single-use package is to identifying the minimum number of use cycles a specific reusable package product will have to be used before the amortized emissions for a reusable package are equal to or lower than for a single-use package (Zimmermann and Bliklen, 2020). This metric is given by,
where is the minimum number of use cycles for the reusable package, is the upstream F&M life cycle CO2e emissions for the single-use package, and is the upstream F&M life cycle CO2e emissions for the reusable package. This metric is related to the system-level Breakeven Reuse Cycles for CO2e Emissions indicator.
Product Cycled Potential Value
Similar to the CPP, the Product Cycled Potential Value (VPP) is a forward-looking metric designed to help supply chain managers assess the potential value of a product without knowing future material flows. If economic value is used as the unit of measure for CPP then,
otherwise VPP is defined as the ratio of the economic value of materials or components within a product that are potentially reusable and the total product economic value given by,
where VPUM is the economic value of components that could be remanufactured or repurposed for future products, VPRM is the economic value of materials that could be recycled, VPCM is the economic value of materials that could be composted, and VTP is the total economic value of the product. Similar to CPP, additional elements (Vi) could be considered if there are other material flow strategies within the CSCN.
Product Cycled Content Value
Similar to the CCP, the Product Cycled Content Value (VCP) is a backward-looking metric designed to help supply chain managers assess the value of content used in a product that came from post-consumer, EOL sources. If economic value is used as the unit of measure for CCP then,
otherwise VCP is defined as the ratio of the economic value of materials or components within a product that came from post-consumer sources and the total product economic value given by,
where VPUU is the economic value of components from post-consumer remanufactured or repurposed sources, VPRU is the economic value from PCR, and VTP is the total economic value of the product. Similar to CCP, additional elements (Vi) could be considered if there are other material flow strategies within the CSCN.
System-level metrics
Breakeven Reuse Cycles for CO2e Emissions
Related to the product-level , the Breakeven Reuse Cycles for CO2e Emissions indicator is designed to help supply chain managers compare the life cycle GHG emissions of reusable and single-use packages. This metric accounts for the full life cycle of packages in a reusable packaging system including F&M, forward and reverse transportation between the actors in the system, and processing packages between uses (Zimmermann and Bliklen, 2020). The life cycle emissions for a single-use package only includes F&M and forward transportation to the customer. This metric is given by,
which is evaluated iteratively and where is the breakeven number of use cycles, is the life cycle CO2 equivalent (CO2e) emissions for the single-use package at use cycle i, is the life cycle CO2e emissions for the reusable package at use cycle i.
Total Logistics Costs
Total Logistics Costs is a well-known metric designed to help supply chain managers assess the costs associated with the flow of products within a supply chain network. While accounting for materials considered flows outside of the system (e.g., MOUT), cost accounting for reusable packaging is typically focused within the system (Mollenkopf et al., 2005). For a reusable packaging system, this metric is given by,
where is the variable costs associated with each package (i) cycle (ni) including sorting, inspecting, cleaning, storage, and any transportation and handling associated with managing the pool (p) of reusable packages in the system. is the non-packaging variable costs associated with fulfilling and delivering a customer order including picking, packing, and transportation. Finally, Vfixed is the fixed costs associated with operating this system such as purchasing the reusable packages and the equipment and facilities needed to fulfill and deliver orders. Details for these costs will depend on the specific characteristics and configuration of a reusable packaging system.
Case study: Reusable packaging at an omnichannel retailer
To demonstrate the use of the proposed metrics for supply chain circularity and the impact of reusable packaging, we apply the metrics to a real case study. The purpose is to demonstrate the practical application of these metrics including testing different outcomes from decisions based on the metrics. This case study is based on an omnichannel retail company with hundreds of physical retail outlets and a growing fulfillment network for e-commerce. We interviewed subject matter experts at the company, reviewed internal strategy and operational documents, and analyzed internal data on sales, returns, packaging, products, and customers. The company name and related information will be anonymized and no proprietary information will be discussed in this paper.
The focus of this case is secondary packaging used for orders received online and either delivered to customer's homes by a local courier or picked up at stores by customers. Omnichannel retail refers to the sale of goods and services to end consumers through multiple sales channels that bridge digital and physical customer experiences. At the case company, online orders can be delivered to customer's homes or picked up at stores. Orders placed for same-day delivery are delivered by local couriers. Cardboard boxes are used to package products for these same-day deliveries to protect products during delivery. The same boxes can be used (at the customer's discretion) for orders picked up at stores. The company has ambitious goals to reduce the environmental impact of their supply chain including packaging. This case assesses the feasibility of replacing single-use cardboard boxes with reusable packages to work toward the company's goals. The two reusable packages that are considered in this assessment are a polypropylene box and a woven-polypropylene bag.
Operational considerations
Packaging is an important part of product value chains. It can be an integral feature of a product and protects products from damage, contamination, and other exposures prior to use. It also supports the efficient flow of products through supply chains from production to end consumers. The secondary packages used for local delivery and store pick up support the final leg of this journey. Cardboard boxes are assembled at stores and protect products in route to customer's homes. Once an order is delivered, how the cardboard box is disposed of is at the discretion of the customer. Replacing these single-use cardboard boxes with reusable packages has a number of important operational considerations. In order to close the loop, the packages need to be collected from customers and returned back to stores and other locations where they can be redeployed for future orders. This reverse flow includes transportation between customers and the company's facilities. It also includes processes to receive, inspect, repair (if needed), clean, and prepare the package for reuse. We will assess the circularity of this supply chain using the proposed metrics applicable to inner loop strategies including product-level and system-level indicators.
Measuring circularity
Selection of metrics for a specific application depends on the characteristics and configuration of the system as well as the availability of data. Data for total material flows were not available, but the focus for this case organization is a reusable packaging system and so all three product-level metrics can be used to support the assessment.
The Product Reuse Index (CRP) assesses durability and other characteristics of a specific package product that influence the number of cycles it could be used for. Since a single reusable package is being considered for this system, the product-level and system-level reuse indexes are equivalent. The CRP for a single-use cardboard box would be,
In contrast, CRP = 99 for a polypropylene box that could be used for 100 cycles and CRP = 95 for a reusable woven-polypropylene bag that could be used for 20 cycles.
The Product Cycle Potential Index (CPP) and Product Cycled Content Index (CCP) can be used to inform selection of packaging type as well. There are many types of reusable packages used for e-commerce fulfillment including reusable plastic or fabric bags, semi-rigid totes, and plastic boxes (Coelho et al., 2020; Escursell et al., 2021). Specific package products can be evaluated based on the potential circularity for materials it is made with. For example, a 100-gram box made from polypropylene (90% post-consumer) could be recycled by the company. The Product Cycle Potential Index for this package would be,
Since the box is made from 90% post-consumer polypropylene, Product Cycled Content Index would be,
Similar calculations could be made for other types of reusable packages, including packaging with more complex construction mixing reused components and different recycled materials, providing standardized metrics to compare material circularity and support package selection by the company.
Measuring impact
The focus for this assessment is on the system-level economic and environment impacts of the reusable packaging system, but at the product level the Reuse Cycle Minimum for CO2e Emissions indicator can be used to assess the viability of a reusable package before data is available to evaluate the Reusable Index. In this case, the F&M emissions for a single-use cardboard box, polypropylene box, and woven-polypropylene bag are ~6 kg CO2e, 0.3 kg CO2e, and 0.4 kg CO2e (Zimmermann and Bliklen, 2020). This means that the polypropylene box will have to be used for at least 15 use cycles before the amortized emissions are equal to or lower than for the single-use cardboard box while the woven-polypropylene bag has a F&M emissions. This minimum, however, does not take into account the full life cycle emissions of a reusable packaging system.
At the system level, we can use the Breakeven Reuse Cycles for CO2e Emissions indicator to compare the full life cycle GHG emissions of reusable and single-use packages. This assessment takes into account the emissions from F&M as well as forward and reverse transportation between the actors in the system, and processing packages between uses. Life cycle emissions for a single-use package only includes F&M and forward transportation to the customer. For the logistics system considered by Zimmermann and Bliklen (2020), the breakeven point for a polypropylene box is 61 cycles compared to a standard cardboard box, 81 cycles compared to a cardboard box made from post-consumer fiber, and 32 cycles if the reusable box is made from post-consumer plastic. For the woven-polypropylene bag, the breakeven point is only two cycles and one cycle if the reusable bag is made from post-consumer polypropylene. Since the polypropylene box and woven-polypropylene bag can be used for up to 100 and 20 use cycles, the cumulative CO2e emissions for the logistics system would be lower with either of these reusable packages than for single-use cardboard boxes.
In addition to the environmental impacts, we can use the Total Logistics Costs indicator to assess the system-level economic impacts. Cost details depend on the specific characteristics and configuration of the logistics system. In this case (Figure 2), retail stores serve as e-commerce fulfillment locations where orders are picked, packed, and staged for delivery. Orders are then picked up by customers at the store or delivered to customer's homes by a local courier. When customers pick up an order and/or shop in the store they can drop off any reusable packages they have from previous orders. Couriers can bring back reusable packages to the store from prior orders when they deliver new orders as well. At the store, reusable packages are sorted and inspected. A separate cleaning service is used.
To evaluate the Total Logistics Costs, the variable costs for each reusable package use cycle include cleaning, handling, storage, and replacing any reusable packages that are damaged or lost. Transportation is the other variable cost associated with each order. Approximately 90% of retail sales for this case organization occur at physical retail stores, and so we assume that the local courier will incur costs to return packages to the store for only 10% of orders. Finally, since the case organization built and operates retail stores independently of the e-commerce orders delivered within this reusable packaging system, the only fixed cost is purchasing the inventory of reusable packages needed to meet demand for online orders fulfilled at stores. The full set of parameters used for the simulation model can be found in Table 3.
We calculated the Total Logistics Costs for nine different scenarios including: one store for 1 month of operations, one store for 12 months, and 400 stores for 12 months, each for three different reusable package purchase prices. As seen in Table 4, the Total Logistics Costs for operating a circular supply chain with reusable packages could range from $2.8 million to $8.7 million in 400 stores over 12 months. The total cost per order is between $1.10 and $3.50, depending on the type of package used.
To determine the most important factors influencing the Total Logistics Costs of this reusable packaging system, we evaluated the sensitivity to several key parameters used in the model including the loss rate (reusable packages not recovered from customers), reusable package purchase price, and the cost and rate for transportation from customer's homes back to retail stores (backhaul).
As seen in Figure 3, we found that the total cost increases as the loss rate increases indicating total cost is sensitive to loss rate. Moreover, the sensitivity rate (indicated by the slope of the line) increases as the price of the package increases indicating that total cost is sensitive to both the loss rate and package price. For $1 packages, the total cost is insensitive or possibly inversely sensitive to the loss rate. For packages costing $2 or more, the sensitivity rate increases with the price of the package. However, while the cost sensitivity to the loss rate increases with package price, the slope of the sensitivity curves tapers as package price increases (Figure 4). This tapering suggests that other parameters are buffering cost sensitivity as package price increases.
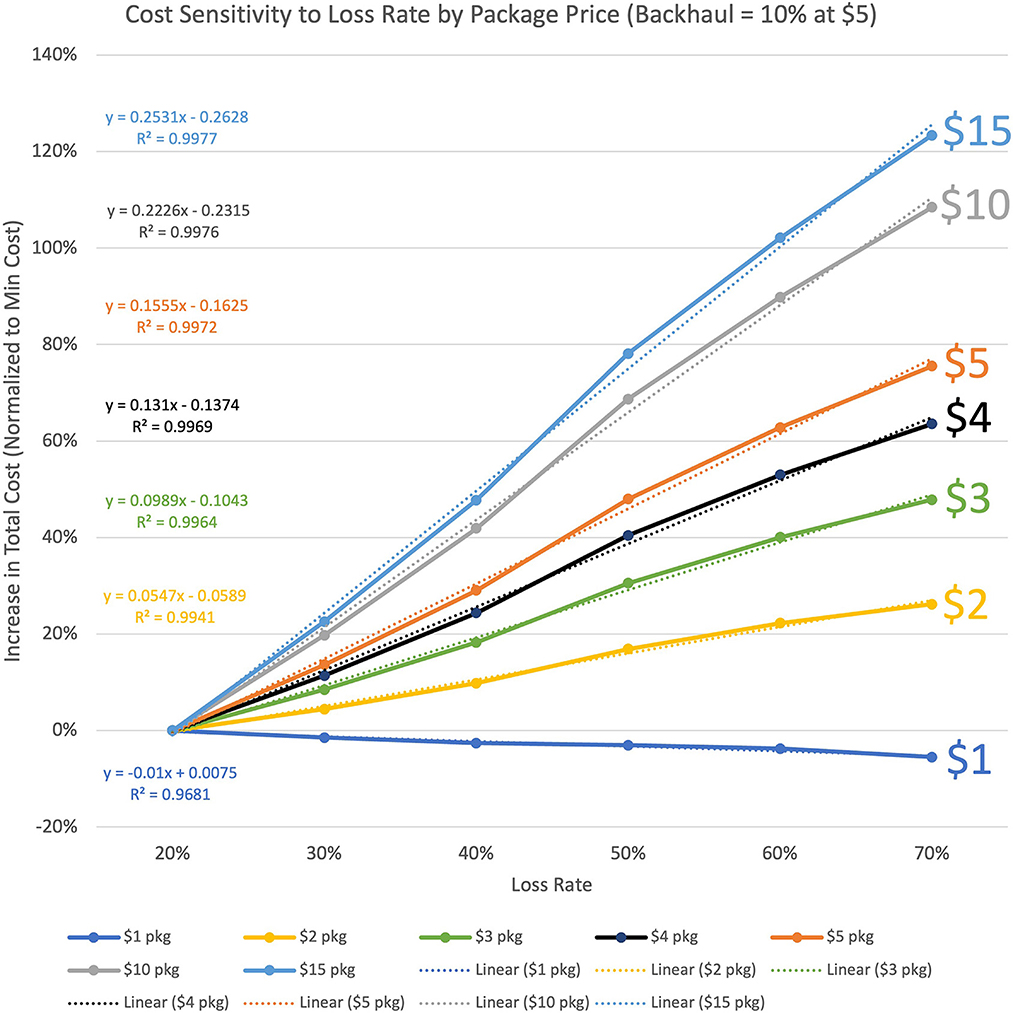
Figure 3. Cost sensitivity to loss rate for packages priced (color) between $1 and $15, and for 10% of packages subject to an extra backhaul cost of $5, showing total cost is sensitive to higher priced packages at a higher rate (slope of the line).
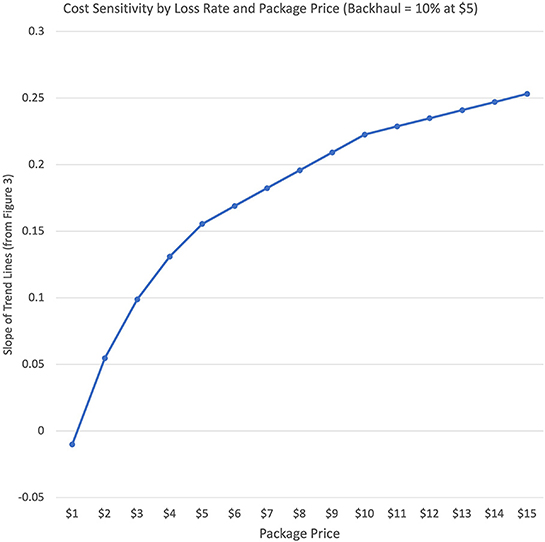
Figure 4. The trend in cost sensitivity rate to loss rate by package price showing that the rate of cost sensitivity decreases as package price increases, and suggesting other parameters influence cost sensitivity.
Two other key parameters (Table 3) used in the model are the extra backhaul cost and the number of packages subject to the extra backhaul cost (backhaul rate). As seen in Figure 5, the sensitivity pattern for backhaul costs of $5 and $10 are similar. Packages >$2 are sensitive to the loss rate, and the sensitivity rate increases with package price. However, when we increase the number of packages subject to the backhaul cost from 10% to 50%, the additional backhaul costs buffer sensitivity to loss rate. As seen in Figure 6, the higher extra backhaul rate results in packages almost as much as $5 being insensitive to the loss rate—in which case it would be cheaper to accept the loss and purchase a new package.
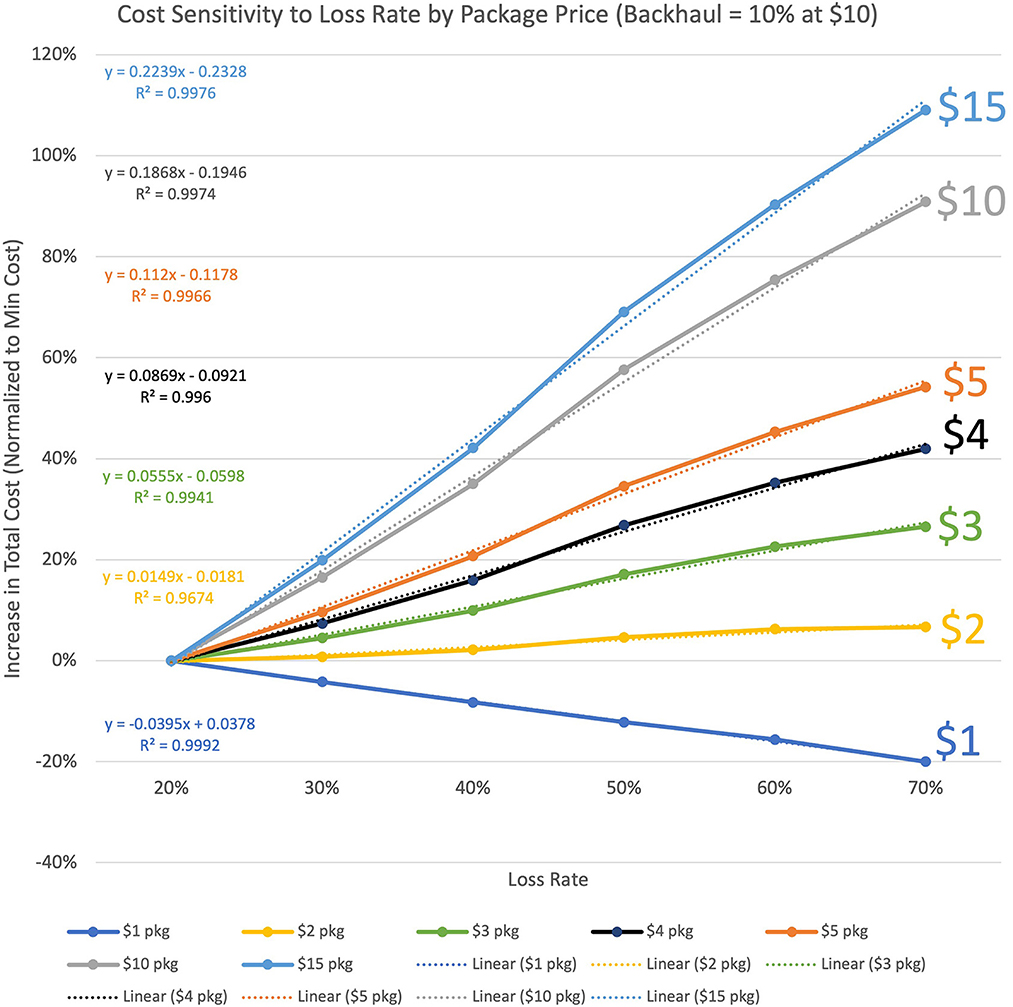
Figure 5. Cost sensitivity to loss rate for packages priced (color) between $1 and $15, and for 10% of packages subject to an extra backhaul trip cost of $10. Compared to Figure 3 ($5 backhaul trip cost) the sensitivity pattern did not change suggesting total cost is not sensitive to the backhaul trip cost when only 10% of packages are subject to the cost.
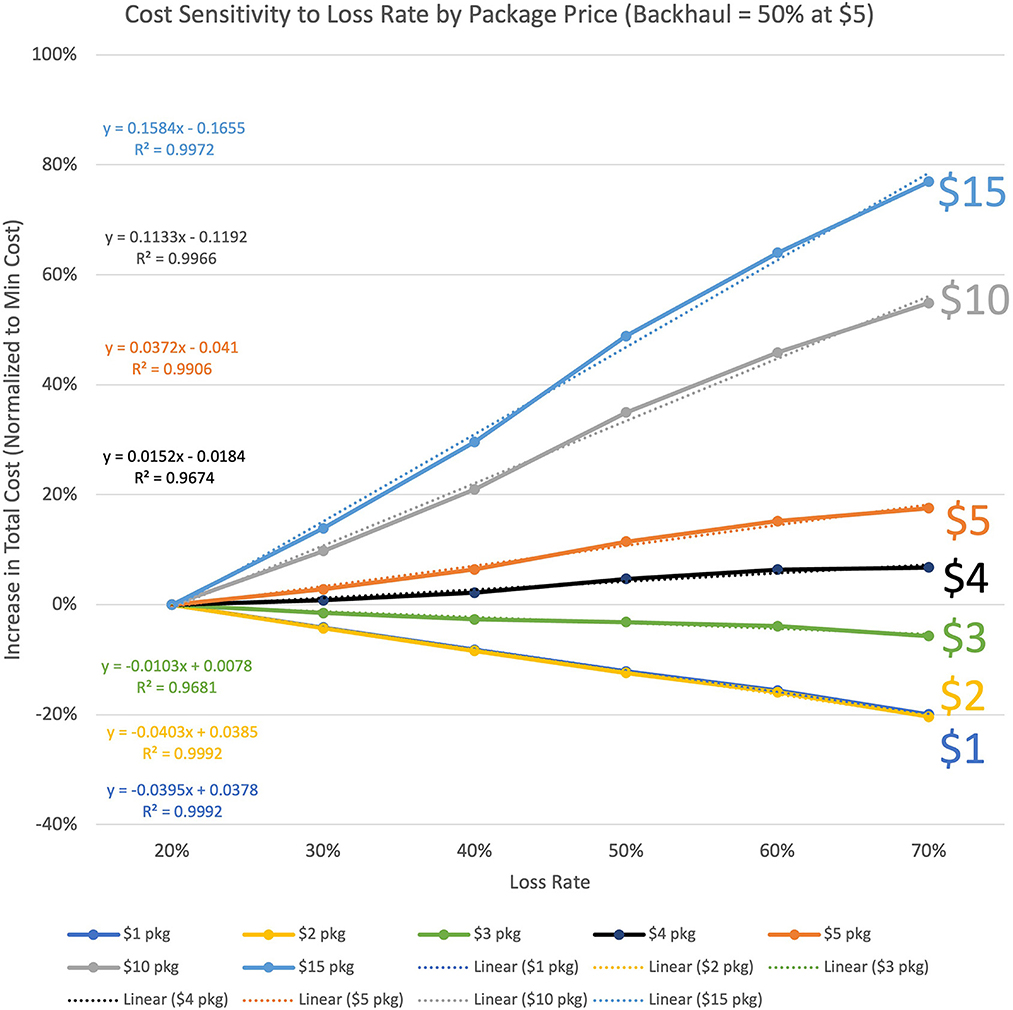
Figure 6. Cost sensitivity to loss rate for packages priced (color) between $1 and $15, and for 50% of packages subject to an extra backhaul cost of $5. Compared to Figure 3 (10% backhaul rate), the sensitivity pattern changed significantly suggesting that total cost is sensitive to the number of packages subject to a backhaul cost (backhaul rate).
Discussion and conclusion
In this paper, we propose a new set of metrics to measure the circularity and impact of reusable packages in supply chains. Packaging plays an important role in supply chains, protecting products from production to end consumers. There is also a growing awareness that packaging uses material resources and results in waste that enters our environment. Reusable packaging is one solution that may address these challenges, and successful implementation and management of this and other CE strategies requires the ability to measure and report on progress across different functions and processes.
There is a growing body of research on metrics for circularity and the impact of CE strategies and CSCM. We found these studies focus on outer-loop circular strategies including remanufacturing and recycling with less attention to reuse strategies. At the same time, reusable packaging is a well-known strategy in supply chains. The contribution in this paper is a new set of metrics to measure circularity and the economic and environmental impacts of reusable items by connecting the existing research on CE metrics with reuse strategies in supply chains. We categorize these metrics as product-level or system-level based on the level of detail they incorporate. We also demonstrate their application with a case study from an omnichannel retail company.
With the case study, we found that the Product Reuse Index, Reuse Cycle Minimum for CO2e Emissions, and Breakeven Reuse Cycles for CO2e Emissions indicators facilitate the comparison of different types of reusable and single-use packages. They show, for example, that a reusable system with either a polypropylene box and reusable woven-polypropylene bag would result in lower cumulative life cycle emissions than shipping with single-use cardboard boxes. The reusable box, however, would have to be used between 32 and 81 times before cumulative emissions are an improvement over cardboard. This has important implications for the durability of the box and recovery from customers. Some studies have found that recovery of reusable packages in a business-to-consumer system can be low (Accorsi et al., 2014; Zimmermann and Bliklen, 2020).
We also found that Total Logistics Costs is sensitive to the rate at which reusable packages are lost, and the impact grows with package cost. Packages can be recovered by asking customers to return them to physical retail locations. They also can be recovered using an owned or third-party transportation service such as local couriers. However, use of transportation services comes with a cost and we found Total Logistics Costs is more sensitive to the number of packages that have to be brought back rather than the unit transportation cost. This suggests that as the rate of package recovery using a transportation service increase, it may be more cost effective to accept a higher loss rate—recovery fewer packages—for higher priced packages, which would then reduce the environmental benefits of reusable packaging.
This case study demonstrates that the new set of metrics we propose for reusable items in SCM shed light on key financial and operational considerations for reusable packaging in an omnichannel retail environment. The same methodology could be applied to a wide range of business models considering SC initiatives for reusable items. Performance metrics inherently rely on the use of data, however, and the primary limitation that may be encountered is the availability of information about specific products and business operations. This limitation can be mitigated in some cases through the use of more general industry data, which may be more readily available in some cases while also reducing the specificity of the results.
While our aim was to address the gap in circularity and impact metrics focused on reuse strategies in supply chains, there are limitations to the new metrics we propose and the case study we used that provide opportunities for further research. The literature and our metrics are focused on economic and/or environmental impacts with limited consideration of the social dimension of sustainability. Further research could evaluate potential social considerations of a reusable packaging system including upstream impacts during the F&M of packages, the impacts on retail store employees and local delivery drivers, and the customer experience.
Another avenue for further research could be implementation and empirical testing of the metrics we propose. Vegter et al. (2021) found that the majority of metrics systems for CSCM are still in early phases of development with only 20% in implementation and 10% in use. We evaluated the application of the metrics within the constraints of a real organization, and found they provide insight into the potential impact of package recovery and other considerations. Further research could evaluate the implementation and effectiveness of these metrics for managing an operational reusable packaging system.
Data availability statement
The original contributions presented in the study are included in the article/supplementary material, further inquiries can be directed to the corresponding author.
Author contributions
KB: conceptualization, methodology, investigation, and writing—original draft. EG-F and EP-C: conceptualization, methodology, investigation, and writing—review and editing. All authors contributed to the article and approved the submitted version.
Conflict of interest
The authors declare that the research was conducted in the absence of any commercial or financial relationships that could be construed as a potential conflict of interest.
Publisher's note
All claims expressed in this article are solely those of the authors and do not necessarily represent those of their affiliated organizations, or those of the publisher, the editors and the reviewers. Any product that may be evaluated in this article, or claim that may be made by its manufacturer, is not guaranteed or endorsed by the publisher.
References
Acampora, A., Preziosi, M., Merli, R., and Lucchetti, M. C. (2017). Environmental management systems in the wine industry: identification of best practices toward a circular economy. In Proceedings of the 23rd International Sustainable Development Research Society Conference (Bogotá, Colombia), p. 14–16.
Accorsi, R., Cascini, A., Cholette, S., Manzini, R., and Mora, C. (2014). Economic and environmental assessment of reusable plastic containers: a food catering supply chain case study. Int. J. Prod. Econ. 152, 88–101. doi: 10.1016/j.ijpe.2013.12.014
Ansari, Z. N., Kant, R., and Shankar, R. (2020). Remanufacturing supply chain: an analysis of performance indicator areas. Int. J. Product. Perform. Manag. 2020, 38. doi: 10.1108/IJPPM-01-2020-0038
Ayres, R. U., and Simonis, U. E. (1994). Industrial Metabolism: Restructuring for Sustainable Development. Vol. 376. Tokyo: United Nations University Press.
Batista, L., Bourlakis, M., Smart, P., and Maull, R. (2018). In search of a circular supply chain archetype – a content-analysis-based literature review. Product. Plan. Control 29, 438–451. doi: 10.1080/09537287.2017.1343502
Bracquené, E., Dewulf, W., and Duflou, J. R. (2020). Measuring the performance of more circular complex product supply chains. Resour. Conserv. Recycl. 154, 104608. doi: 10.1016/j.resconrec.2019.104608
Breen, L. (2006). Give me back my empties or else! A preliminary analysis of customer compliance in reverse logistics practices (UK). Manag. Res. News 29, 532–551. doi: 10.1108/01409170610708989
Brown, P. J., and Bajada, C. (2018). An economic model of circular supply network dynamics: toward an understanding of performance measurement in the context of multiple stakeholders. Bus. Strategy Environ. 27, 643–655. doi: 10.1002/bse.2069
Chan, F. T., and Chan, H. K. (2005). The future trend on system-wide modelling in supply chain studies. Int. J. Adv. Manufact. Technol. 25, 820–832. doi: 10.1007/s00170-003-1851-3
Choi, T. Y., Dooley, K. J., and Rungtusanatham, M. (2001). Supply networks and complex adaptive systems: control versus emergence. J. Operat. Manag. 19, 351–366. doi: 10.1016/S0272-6963(00)00068-1
Cobb, B. R. (2016). Estimating cycle time and return rate distributions for returnable transport items. Int. J. Prod. Res. 54, 4356–4367. doi: 10.1080/00207543.2016.1162920
Coelho, P. M., Corona, B., ten Klooster, R., and Worrell, E. (2020). Sustainability of reusable packaging - current situation and trends. Resour. Conserv. Recycl. 6, 100037. doi: 10.1016/j.rcrx.2020.100037
Corona, B., Shen, L., Reike, D., Carreón, J. R., and Worrell, E. (2019). Towards sustainable development through the circular economy—a review and critical assessment on current circularity metrics. Resour. Conserv. Recycl. 151, 104498. doi: 10.1016/j.resconrec.2019.104498
Dai, T., and Tang, C. S. (2021). Integrating ESG Measures and Supply Chain Management: Research Opportunities in the Post-Pandemic Era. SSRN Scholarly Paper ID 3939968. Rochester, NY: Social Science Research Network. doi: 10.2139/ssrn.3939968
De Pascale, A., Arbolino, R., Szopik-Depczyńska, K., Limosani, M., and Ioppolo, G. (2021). A systematic review for measuring circular economy: the 61 indicators. J. Clean. Prod. 281, 124942. doi: 10.1016/j.jclepro.2020.124942
de Pauw, I., van der Grinten, B., Flipsen, B., and Alvarez-Mendez, L. (2021). The Circularity Calculator, a Tool for Circular Product Development with Circularity and Potential Value Capture Indicators. Available online at: https://hdl.handle.net/10344/10207 (accessed December 2, 2021).
Ellen MacArthur Foundation Granta Design (2015). Circularity Indicators. An Approach to Measuring Circularity. Methodology. Available online at: https://ellenmacarthurfoundation.org/material-circularity-indicator (accessed December 12, 2021).
Ellen MacArthur Foundation. (2013). Towards the Circular Economy, Vol. 1: An Economic and Business Rationale for an Accelerated Transition. Available online at: https://ellenmacarthurfoundation.org/towards-the-circular-economy-vol-1-an-economic-and-business-rationale-for-an (accessed December 11, 2021).
Escursell, S., Llorach-Massana, P., and Roncero, M. B. (2021). Sustainability in E-commerce packaging: a review. J. Clean. Prod. 280, 124314. doi: 10.1016/j.jclepro.2020.124314
Fan, Y., and Fang, C. (2020). Circular economy development in china-current situation, evaluation and policy implications. Environ. Impact Assess. Rev. 84, 106441. doi: 10.1016/j.eiar.2020.106441
Farooque, M., Zhang, A., Thürer, M., Qu, T., and Huisingh, D. (2019). Circular supply chain management: a definition and structured literature review. J. Clean. Prod. 228, 882–900. doi: 10.1016/j.jclepro.2019.04.303
Fashion for Good (2021). The Rise of Reusable Packaging: Understanding the Impact & Mapping a Path to Scale. Available online at: https://reports.fashionforgood.com/report/the-rise-of-reusable-packaging/ (accessed December 2, 2021).
Geissdoerfer, M., Morioka, S. N., de Carvalho, M. M., and Evans, S. (2018). Business models and supply chains for the circular economy. J. Clean. Prod. 190, 712–721. doi: 10.1016/j.jclepro.2018.04.159
Geissdoerfer, M., Savaget, P., Bocken, N. M., and Hultink, E. J. (2017). The circular economy – a new sustainability paradigm? J. Clean. Prod. 143, 757–768. doi: 10.1016/j.jclepro.2016.12.048
Geyer, R., Jambeck, J. R., and Law, K. L. (2017). Production, use, and fate of all plastics ever made. Sci. Adv. 3, 25–29. doi: 10.1126/sciadv.1700782
Ghisellini, P., Cialani, C., and Ulgiati, S. (2016). A review on circular economy: the expected transition to a balanced interplay of environmental and economic systems. J. Clean. Prod. Toward Post Fossil Carbon Soc. 114, 11–32. doi: 10.1016/j.jclepro.2015.09.007
Goellner, K. N., and Sparrow, E. (2014). An environmental impact comparison of single-use and reusable thermally controlled shipping containers. Int. J. Life Cycle Assess. 19, 611–619. doi: 10.1007/s11367-013-0668-z
Goudenege, G., Chu, C., and Jemai, Z. (2013). Reusable containers management: from a generic model to an industrial case study. Supply Chain For. 14, 26–38. doi: 10.1080/16258312.2013.11517313
Govindan, K., and Hasanagic, M. (2018). A systematic review on drivers, barriers, and practices towards circular economy: a supply chain perspective. Int. J. Prod. Res. 56, 278–311. doi: 10.1080/00207543.2017.1402141
Govindan, K., and Soleimani, H. (2017). A review of reverse logistics and closed-loop supply chains: a journal of cleaner production focus. J. Clean. Prod. 142, 371–384. doi: 10.1016/j.jclepro.2016.03.126
Graedel, T. E., Allwood, J., Birat, J. P., Buchert, M., Hagelüken, C., Reck, B. K., et al. (2011). What do we know about metal recycling rates? J. Indus. Ecol. 15, 355–366. doi: 10.1111/j.1530-9290.2011.00342.x
Haghighi, S. M., Torabi, S. A., and Ghasemi, R. (2016). An integrated approach for performance evaluation in sustainable supply chain networks (with a case study). J. Clean. Prod. 137, 579–597. doi: 10.1016/j.jclepro.2016.07.119
Hazen, B. T., Russo, I., Confente, I., and Pellathy, D. (2021). Supply chain management for circular economy: conceptual framework and research agenda. Int. J. Logist. Manag. 32, 510–537. doi: 10.1108/IJLM-12-2019-0332
Hoekstra, A. Y., and Wiedmann, T. O. (2014). Humanity's unsustainable environmental footprint. Science 344, 1114–1117. doi: 10.1126/science.1248365
Kalmykova, Y., Sadagopan, M., and Rosado, L. (2018). Circular economy – from review of theories and practices to development of implementation tools. Resour. Conserv. Recycl. Sustain. Resour. Manag. Circul. Econ. 135, 190–201. doi: 10.1016/j.resconrec.2017.10.034
Kirchherr, J., Reike, D., and Hekkert, M. (2017). Conceptualizing the circular economy: an analysis of 114 definitions. Resour. Conserv. Recycl. 127, 221–232. doi: 10.1016/j.resconrec.2017.09.005
Korhonen, J., Honkasalo, A., and Seppäl,ä, J. (2018). Circular economy: the concept and its limitations. Ecol. Econ. 143, 37–46. doi: 10.1016/j.ecolecon.2017.06.041
Kristensen, H. S., and Mosgaard, M. A. (2020). A review of micro level indicators for a circular economy – moving away from the three dimensions of sustainability? J. Clean. Prod. 243, 118531. doi: 10.1016/j.jclepro.2019.118531
Linder, M., Boyer, R. H., Dahllöf, L., Vanacore, E., and Hunka, A. (2020). Product-level inherent circularity and its relationship to environmental impact. J. Clean. Prod. 260, 121096. doi: 10.1016/j.jclepro.2020.121096
Linder, M., Sarasini, S., and van Loon, P. (2017). A metric for quantifying product-level circularity. J. Indus. Ecol. 21, 545–558. doi: 10.1111/jiec.12552
Maestrini, V., Luzzini, D., Maccarrone, P., and Caniato, F. (2017). Supply chain performance measurement systems: a systematic review and research agenda. Int. J. Prod. Econ. 183, 299–315. doi: 10.1016/j.ijpe.2016.11.005
Mahmoudi, M., and Parviziomran, I. (2020). Reusable packaging in supply chains: a review of environmental and economic impacts, logistics system designs, and operations management. Int. J. Prod. Econ. 228, 107730. doi: 10.1016/j.ijpe.2020.107730
Meherishi, L., Narayana, S. A., and Ranjani, K. S. (2019). Sustainable packaging for supply chain management in the circular economy: a review. J. Clean. Prod. 237, 117582. doi: 10.1016/j.jclepro.2019.07.057
Mesa, J., Esparragoza, I., and Maury, H. (2018). Developing a set of sustainability indicators for product families based on the circular economy model. J. Clean. Prod. 196, 1429–1442. doi: 10.1016/j.jclepro.2018.06.131
Mhatre, P., Panchal, R., Singh, A., and Bibyan, S. (2021). A systematic literature review on the circular economy initiatives in the European Union. Sustain. Prod. Consumpt. 26, 187–202. doi: 10.1016/j.spc.2020.09.008
Mollenkopf, D., Closs, D., Twede, D., Lee, S., and Burgess, G. (2005). Assessing the viability of reusable packaging: a relative cost approach. J. Bus. Logistic. 26, 169–197. doi: 10.1002/j.2158-1592.2005.tb00198.x
Neely, A., Gregory, M., and Platts, K. (1995). Performance measurement system design. Int. J. Operat. Prod. Manag. 15, 80–116. doi: 10.1108/01443579510083622
Olugu, E. U., Wong, K. Y., and Shaharoun, A. M. (2011). Development of key performance measures for the automobile green supply chain. Resour. Conserv. Recycl. 55, 567–579. doi: 10.1016/j.resconrec.2010.06.003
Pålsson, H. (2018). Packaging Logistics: Understanding and Managing the Economic and Environmental Impacts of Packaging in Supply Chains. London: Kogan Page Publishers.
Pearce, D. W., and Turner, R. K. (1990). Economics of Natural Resources and the Environment. Baltimore, MD: JHU Press.
Saidani, M., Yannou, B., Leroy, Y., Cluzel, F., and Kendall, A. (2019). A taxonomy of circular economy indicators. J. Clean. Prod. 207, 542–559. doi: 10.1016/j.jclepro.2018.10.014
Sarja, M., Onkila, T., and Mäkelä, M. (2021). A systematic literature review of the transition to the circular economy in business organizations: obstacles, catalysts and ambivalences. J. Clean. Prod. 286, 125492. doi: 10.1016/j.jclepro.2020.125492
Schöggl, J. P., Stumpf, L., and Baumgartner, R. J. (2020). The narrative of sustainability and circular economy - a longitudinal review of two decades of research. Resour. Conserv. Recycl. 163, 105073. doi: 10.1016/j.resconrec.2020.105073
Scott, K., Roelich, K., Owen, A., and Barrett, J. (2018). Extending European energy efficiency standards to include material use: an analysis. Climate Pol. 18, 627–641. doi: 10.1080/14693062.2017.1333949
Sovacool, B. K., Ali, S. H., Bazilian, M., Radley, B., Nemery, B., Okatz, J., et al. (2020). Sustainable minerals and metals for a low-carbon future. Science 367, 30–33. doi: 10.1126/science.aaz6003
Stahel, W. R. (2013). Policy for material efficiency—sustainable taxation as a departure from the throwaway society. Philos. Trans. Royal Soc. A 371, 20110567. doi: 10.1098/rsta.2011.0567
Stevens, G. C. (1989). Integrating the supply chain. Int. J. Phys. Distribut. Mater. Manag. 19, 3–8. doi: 10.1108/EUM0000000000329
Tisserant, A., Pauliuk, S., Merciai, S., Schmidt, J., Fry, J., Wood, R., et al. (2017). Solid waste and the circular economy: a global analysis of waste treatment and waste footprints. J. Indus. Ecol. 21, 628–640. doi: 10.1111/jiec.12562
Tsiliyannis, C. A. (2005). A new rate index for environmental monitoring of combined reuse/recycle packaging systems. Waste Manag. 23, 304–313. doi: 10.1177/0734242X05056757
Van Buren, N., Demmers, M., Van der Heijden, R., and Witlox, F. (2016). Towards a circular economy: the role of dutch logistics industries and governments. Sustainability 8, 647. doi: 10.3390/su8070647
Vegter, D., van Hillegersberg, J., and Olthaar, M. (2020). Supply chains in circular business models: processes and performance objectives. Resour. Conserv. Recycl. 162, 105046. doi: 10.1016/j.resconrec.2020.105046
Vegter, D., van Hillegersberg, J., and Olthaar, M. (2021). Performance measurement systems for circular supply chain management: current state of development. Sustainability 13, 12082. doi: 10.3390/su132112082
Walker, S., Coleman, N., Hodgson, P., Collins, N., and Brimacombe, L. (2018). Evaluating the environmental dimension of material efficiency strategies relating to the circular economy. Sustainability 10, 666. doi: 10.3390/su10030666
WBCSD (2021). Circular economy. World Business Council for Sustainable Development. (2021). Available online at: https://www.wbcsd.org/CE (accessed December 11, 2021).
WEF (2021). Circular Economy. World Economic Forum. Available online at: https://www.weforum.org/projects/circular-economy/ (accessed December 11, 2021).
Keywords: circular supply chain (CSC), reusable packaging, sustainability, performance indicator (PI), retailer
Citation: Betts K, Gutierrez-Franco E and Ponce-Cueto E (2022) Key metrics to measure the performance and impact of reusable packaging in circular supply chains. Front. Sustain. 3:910215. doi: 10.3389/frsus.2022.910215
Received: 29 April 2022; Accepted: 24 November 2022;
Published: 15 December 2022.
Edited by:
Shutaro Takeda, Kyoto University, JapanCopyright © 2022 Betts, Gutierrez-Franco and Ponce-Cueto. This is an open-access article distributed under the terms of the Creative Commons Attribution License (CC BY). The use, distribution or reproduction in other forums is permitted, provided the original author(s) and the copyright owner(s) are credited and that the original publication in this journal is cited, in accordance with accepted academic practice. No use, distribution or reproduction is permitted which does not comply with these terms.
*Correspondence: Eva Ponce-Cueto, ZXBvbmNlQG1pdC5lZHU=