- 1Department of Mechanical Engineering, Marwadi University, Rajkot, India
- 2Blockchain Project Manager, MGL Group, Rajkot, India
- 3Communication Theory and Networking, College of Computer Science, King Khalid University, Abha, Saudi Arabia
- 4Department of Mathematics, Marwadi University, Rajkot, India
Metal casting is among humanity’s most ancient manufacturing methods in which, molten metal is poured into a mold of a desired shape. Despite its long history, this field has not fully embraced cutting-edge technologies like IIoT, AR/VR, and the metaverse. Emerging technologies like AR/VR and Metaverse have become popular and offer exciting possibilities for metal casting applications. A physical set up of metal casting integrated with IIoT is designed and developed in immersive interactive environment to utilise the most recent technology in manufacturing. The goal is to reinforce research, stimulate innovation, and develop technical expertise, for which a conceptual framework is designed to create Immersive Interactive Environment for metal casting, specifically for Vertical Centrifugal Casting (VCC). In this process, metal is poured in to the rotating mold to produce cylindrical components. The present work focuses on development of young and emerging talent to build their skills in traditional processes like casting through experimental learning and develop the learning environment for the young and curios minds. Ultimate aim is to nurture innovation and to bridge the gap that exists between traditional manufacturing methodologies and contemporary technological enhancements.
Introduction
Metal casting It is considered an ancient manufacturing method. It represents humanity’s first strides in crafting metallic parts. Intense heat, capable of melting metals and alloys, achieves this. It is an orchestrating process to control the solidification of molten metal. Metal is poured into a mold. The mold shapes the metal into the desired metallic form. This part is known as a pattern. Metal casting has dramatically increased over the past 100–150 years. This increase spans various industrial domains. The process of metal casting makes a significant contribution to societal development. Demand for various shapes, sizes, and strengths has given rise to numerous metal casting processes. Each process differs in aspects such as pattern-making, mold formation, melting, pouring, and solidification. Centrifugal casting is a distinctive variation of these methods, especially because it rotates the mold. Metal is poured into the mold. As it is being rotated. This method allows the creation of cylinder-shaped objects. For instance, you can use it to create pipes, tubes, pistons, and aluminum alloy cylinders. This technique has evolved further into Vertical Centrifugal Casting (VCC). This technique enables the mold to rotate along the vertical axis. Figure 1 is a depiction of the VCC process. It’s a representation of a two-dimensional VCC process. As mentioned before, vertical centrifugal casting (VCC) includes pouring molten metal into a mold that’s spinning. The centrifugal force pushes the molten metal towards the mold’s outer edges. The centrifugal force achieves this. The result is castings that are uniformly dense. They possess minimal porosity and defects. The procedure demands meticulous control of parameters. The variables include the mold temperature, the pour temperature, and the rotation speed. In essence, metal casting is about crafting a mold. We crafted it to resemble the shape of the desired metal object. We then pour molten metal into the mold. We do this to forge the final product.
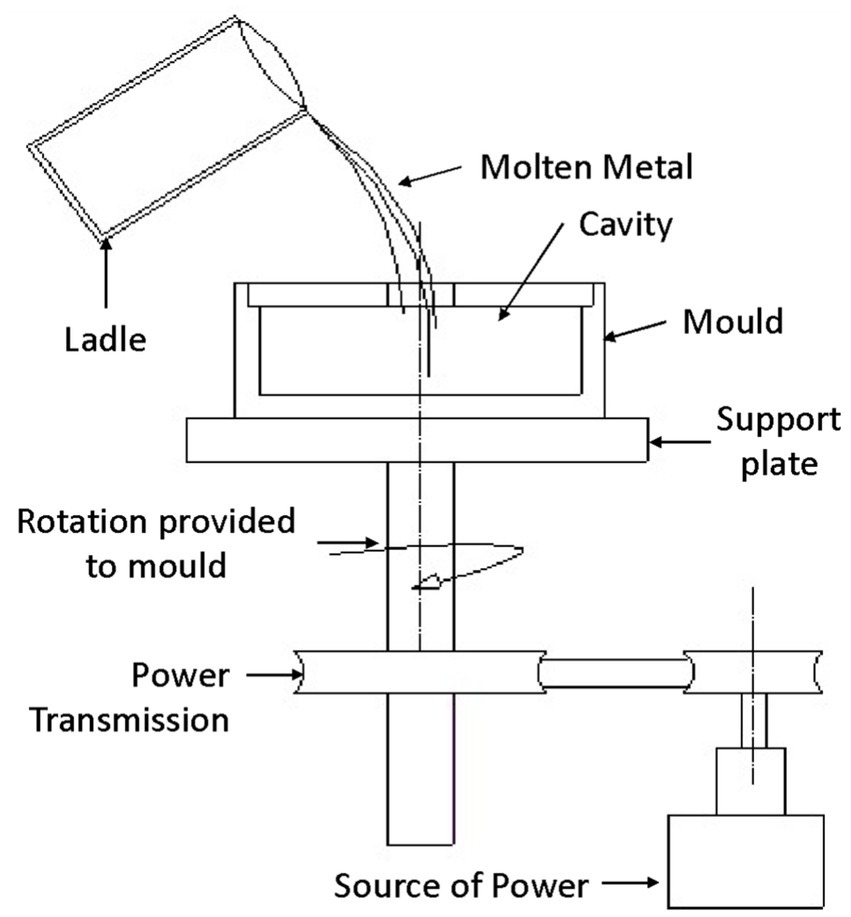
Figure 1. Two-dimensional representation of VCC (Mazloum and Sata, 2022).
This determines the quality of the metallic parts produced. Control of this level necessitates specific skill sets and deep domain expertise. Numerous iterations are also required. Young professionals aspire to excel in the realm of metal casting. To become domain experts, they must possess specialized skills. Industry often views metal casting as an art rather than a pure engineering discipline. The industry has been slow in embracing recent technological advancements like industrial artificial intelligence, IIoT, the digital twin, AR, VR, and the metaverse. There’s an urgent need to bridge the gap between this age-old manufacturing process and modern technologies. This will attract a diverse pool of young talent to this domain.
Immersive environments in metal casting demonstrate the potential. This falls under the manufacturing sector. Taking advantage of immersive technology might streamline metal casting. Immersion technology can also enhance this process. Designers and engineers find virtual reality helpful. They create digital images of desired metal objects. It facilitates visualization. The model allows for precise control. Digital models lay the groundwork for virtual molds. This fosters thorough testing. We can optimize digital models before starting physical production. In addition, there are virtual simulations. These simulations can pinpoint possible problems. These simulations identify the mold’s issues. We can make changes ahead of time to reduce risks. By doing so, you can enhance the quality of the final product (LeFebvre et al., 2020). Metal casting could incorporate immersive technology. It shows promise for better efficiency. It can bring down expenses. Furthermore, it may improve product quality. Metal casting may incorporate immersive technology. It promises efficiency improvements. Costs could be lessened. The potential exists for an enhancement of product quality.
While domains now acknowledge the benefits of immersive and interactive environments, their application is still in its infancy. Metal casting is still in its infancy. A thorough examination of the literature reveals that we have yet to fully explore the potential of immersive interactive technology. Especially in vertical centrifugal casting setups. Nonetheless, lots of research studies cite the potential benefits of using this technology in the casting process. Extensive exploration of immersive interactive spaces has produced useful technologies. These technologies have applications in many sectors (Bansal et al., 2022). These include simulations (Zhang et al., 2022; Rahman et al., 2023), gaming (Trunfio and Rossi, 2022), office utilities (Liu et al., 2020), social interactions (Li, 2020), marketing methods (Kye et al., 2021), and healthcare procedures (Go et al., 2021). The impact also extends to educational techniques (Lee et al., 2021; Lin et al., 2022) and advanced research (Richter and Richter, 2023). The literature on metal casting, however, remains scarce. Research engagement in various fields is ongoing. The aim is to understand the implementation of immersive environments. The impact on various sectors is also under scrutiny. Studies in additive manufacturing (AM) and design for additive manufacturing (DfAM) exist. They draw comparisons between the impacts of immersive (VR) and non-immersive surroundings on design procedures. The impact on AM competency training and development is considered important (Mathur et al., 2023). The idea of There exists an immersive interactive cyber-physical system (I2CPS). It is part of a structure that aims to improve human involvement in smart manufacturing. It accomplishes this by utilizing human abilities such as quick understanding and decision-making. This structure has a purpose. It aims to tackle issues such as incorrect accuracy and human errors. It also addresses the complicated analysis of big data (Yun and Jun, 2022). Expanding immersive environments to unmanned aerial vehicles (UAVs) holds enormous promise. This is particularly true in environments that are hazardous or remote. In such settings, UAVs can help with tasks, offering support effectively and safely. This carries many benefits for novice training. Adding digital twin technology to the Flexible Printed Circuit Board (FPCB) etching process has proven to be effective. Enhancing production precision and yield (Sheng et al., 2023). The approach fine-tunes process parameters. It combines real-time data acquisition with online control systems. This brings product reliability and consistency. Implementing FPCB etching has a significant impact. It marks a notable improvement in smart manufacturing for FPCB applications. The market for immersive and virtual reality is growing fast. However, there is persistent confusion about their distinctions. However, some researchers (Korżel and Łupkowski, 2023) delve into the core disparities between these technologies, exploring their causes and effects. Beyond manufacturing and technical domains, immersive VR technologies are rapidly proving beneficial, such as in training for non-verbal communication (Xenakis et al., 2022). The Digital Immersive Environment, also known as the Metaverse, has been extensively discussed, defined, and studied for its diversity, equity, accessibility, safety, and inclusion of various terms during its design (Zallio and Clarkson, 2022).
The integration of the metaverse involves numerous parameters that require careful consideration and thorough discussion, encompassing both positive and negative impacts. Similarly, digital twins assume a crucial role in visual representation, significantly enhancing communication efficiency for project managers beyond mere process simulation. They serve as pivotal information hubs for all personnel involved in constructing, operating, and maintaining production processes, leveraging historical data for future advancements (Yan et al., 2017). Integrating a digital twin alongside physical products or processes can prove invaluable for project managers, particularly in lean project implementation focused on process enhancement.
Synergy between immersive interaction and digital twin environments is crucial. It necessitates a systematic approach to bridge information between the real and virtual worlds. This is accomplished through appropriate channels or systems. Office spaces and building areas are ideal places to review this integration. We can assess comfort, productivity, and adaptive behavior (Latini et al., 2023). Furthermore, they have an impact on work-life balance. Their influence on geographical experience and satisfaction is crucial. A single study looked into the potential of metaverse technology. We specifically conducted the study within a particular domain. It focused on optimizing the casting process for greater efficiency. It also aimed to enhance quality (Anadkat and Sata, 2023). This research was successful. It involved a blend of metaverse technology. Machine learning algorithms were also key. This investigation managed to optimize casting process parameters. The findings were clear. Substantial improvements were noted. They exhibited both efficiency and quality. Innovative technologies made all of this possible. We also conducted another study. This one examined the use of metaverse technology. It was used to simulate and optimize the casting process. Dual goals were in mind. These were to increase efficiency and lower costs (Authors, 2023a). The study made use of strong synergy. This synergy was between metaverse technology and virtual reality. This inquiry simulated the casting process. It further fine-tuned some process parameters. Most importantly, results were obtained. A significant drop was observed. We significantly reduced both the time and money typically required for physical prototyping and testing. It proved that technological interventions work. It was convincing. Results were conclusive. Thus the technological interventions work. The metaverse constitutes a 3D virtual reality environment where daily interactions occur through avatars, presenting themselves as authentic representations (Authors, 2023b). The utilization of avatars and the integration of the digital and physical realms signify the coexistence of physical and virtual realities, ultimately forming a 3D virtual cyberspace (Authors, 2021).
Diverse sectors are increasingly embracing immersive environments, with education emerging as a leading and rapidly evolving arena for their incorporation. Within this domain, they function as adaptable instruments for instructing employees, students, and workers, as well as providing demonstrations of machinery operations within controlled spaces (Sata, 2016). The Immersive Interactive Environment creates a collaborative setting where multiple users can seamlessly navigate between the physical and virtual realms, addressing the inherent constraints of conventional 2D online learning platforms (Sata and Ravi, 2014).
Through virtual reality, various researchers have demonstrated the use and implementation of immersive interactive environments in the educational sector. While virtual reality provides immersive experiences, the concept of immersive interactive environments is broader, encompassing both virtual reality and user engagement in diverse activities, connectivity, and integration with the real world. The experimental setup combines physical components with immersive environments that are operable in both physical and virtual worlds, with results visible on both platforms, giving users the flexibility to work from any location. Furthermore, it serves as a tool for training individuals in machine operation when a physical setup is inaccessible.
Experts have explored the realms of AR/VR/Metaverse and other ground-breaking technologies across various sectors, where advancements are still in their infancy and predominantly at a foundational level.
Several more years may be required to fully bring these technologies to life. Several more years may be required. These tools promise significant potential in the manufacturing sector. Casting especially stands out. These technologies may be of use in training simulations. They could play a role in hazardous environments, too. They could pave the way to reduce the risk to human life. They can streamline operations. However, they may need further perfection. They might benefit from more development. In metal casting, an immersive, interactive environment is emerging. It is a sphere with strong links to manufacturing and industrial processes. Here are the advantages of using immersive environments in metal casting:
1. Training and skill development: Immersive environments can serve as a realistic and secure training atmosphere. These immersive environments can help new personnel train. They can also boost the skills of experienced metal-casting workers. Trainees interact with virtual or simulated casting equipment. Or with processes and materials. This lets them learn and practice without risking damage to machinery or injury.
2. Process Optimization. Engineers and technicians can conduct tests by simulating the metal casting process in an immersive environment. They can test different variables. Variables include temperature materials and casting techniques. They aim to optimize efficiency and quality. The quality of the casting process. This can save costs. It can also improve product quality and reduce waste.
3. Prototyping and design evaluation. Before creating physical prototypes, engineers and designers can use immersive environments. Engineers and designers can use them. These environments are used by engineers and designers to visualize and evaluate cast designs. They interact with virtual prototypes. This helps them to identify potential problems and make improvements. It happens early in the design process. Such steps save time and resources. Physical prototyping and production occur.
4. Safety Training and Hazard Identification. Metal casting environments can pose significant safety hazards. The hazards include high temperatures, molten metal, and heavy machinery. Immersive environments can simulate these hazards. They do this in a controlled setting. This allows workers to undergo safety training. They can practice emergency procedures too. They can accomplish all this without putting themselves at risk of injury.
5. Remote Collaboration and Communication. Immersive environments can help with remote collaboration and communication. Team members who are involved in metal casting projects can use them for this purpose. Virtual reality (VR) or augmented reality (AR) technologies may be helpful. These technologies allow team members to interact. They can interact with virtual representations of casting equipment and products. Real-time collaboration is possible regardless of the geographical location.
6. Enhanced Visualization and Analysis. Immersive environments are great. They can provide advanced visualization tools. These tools may include 3D modeling and simulation. Both can help engineers and technicians understand complex casting processes. They also help identify areas for improvement. Interactive data visualization tools are helpful. These tools can enable real-time analysis of casting performance metrics. This allows for more informed decision-making.
In summary, immersion environments can offer a multitude of advantages within the metal casting industry. These include upgraded training and optimized process evaluation of design safety instruction. Other benefits include increased remote collaboration. Visualization analysis capabilities. These can lead to more efficient, cost-effective, and safe metal casting operations. Indeed, prior research has uncovered both the attractive advantages and the current limitations. Their study focused on the use of immersive interactive environments. The vertical centrifugal casting process utilized these environments. Though the field is still in its infancy, multiple research projects highlight an optimistic picture. They show how immersive interactive environments can enhance casting processes. This leads to improved efficiency, reduced expenses, and better quality. Nonetheless, additional investigation is mandatory. The goal is to completely unpack the potential of immersive interactive environments within the vertical centrifugal casting setup. Another goal is to identify any constraints on their use.
Framework for implementing an immersive interactive environment in metal casting
Figure 2 serves to depict the overall structure of an immersive interactive space for metal casting. This structure primarily entails the development of Internet of Things (IoT)-enabled metal casting. It also entails synergic integration with virtual metal casting setups.
The IIoT-enabled Metal casting can be a multi-step process. Initially, we need a physical metal casting setup, complete with sensors. This setup also requires a data acquisition system. This system needs to be built. The next step involves streaming the data. This activity should occur on a cloud-based server. We do this to enable online monitoring and process control. Furthermore, we can use relevant predictions and analytics to enhance quality. You can also seamlessly integrate this system with a virtual metal casting setup. In this case, it would serve as a replica. It would also serve as a digital twin of the physical setup. The cloud-based server streams data. This data comes from sensors and an embedded data acquisition system. Both of these are present on the physical casting setup. This procedure enables process monitoring in a virtual environment. Additionally, the cloud-based server allows the entire virtual setup to interact with the physical setup. The cloud-based server then uses this collected data. The collected data is used to monitor online processes. It also utilizes the collected data for prognosis and analytics. These, in turn, improve quality. The following sections will provide a detailed discussion of the various elements that contribute to an immersive interactive environment for IoT-enabled metal casting. In this discussion, the topic of focus will be Vertical Centrifugal Casting (VCC). The main aim is to ensure clarity and understanding in implementation.
Setup development by embedding sensor, data acquisition system, and controllers
Vertical Centrifugal Casting (VCC), as previously mentioned, primarily fabricates cylindrical metallic parts from aluminium alloys, characterized by a specific aspect ratio (the ratio of height to diameter; Bhoraniya et al., 2022). We have engineered the physical configuration of the VCC setup (Figure 3) to accommodate various mold sizes, enabling the casting of molten aluminium alloys with minor adjustments to clamps mounted on the adapter plate. Additionally, we have developed a specific array of molds to produce metallic parts with diverse aspect ratios ranging from 1 to 3, specifically tailored for industrial applications. The structure of the VCC setup integrates a 3-phase induction motor with an alternating current frequency drive control unit to ensure operational versatility. This configuration enables a broader range of mold rotation (from 25 to 200 revolutions per minute) within a vibration-free environment.
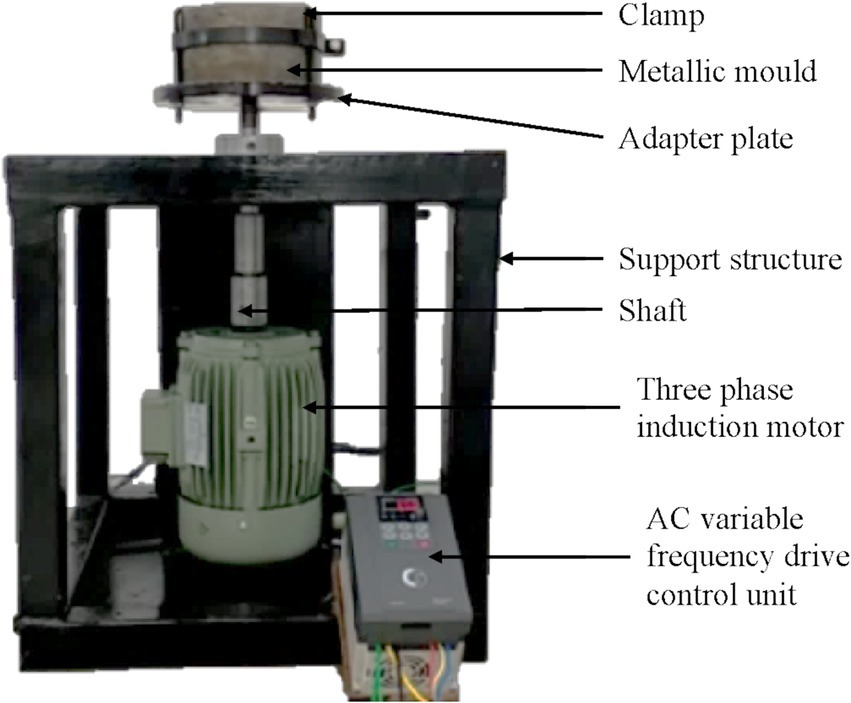
Figure 3. Physical setup of VCC (Sata, 2016).
We have designed and developed a specialized melting furnace that can melt alloys up to 3 kg, with a melting point ranging between 1,050°C, within a prescribed time frame of 50 to 55 min. This furnace also includes a bottom-pouring feature to ensure safe handling of molten metal. We have devised a unique stopper rod mechanism to ensure precise pouring of molten metal from the melting furnace onto the rotating mold within the VCC setup. During the pouring process, we maintain careful alignment between the bottom-pouring furnace and the center of rotation of the mold. Other technical literature (Bhoraniya et al., 2018) elaborates further on the design of the VCC setup and the resistance bottom-pouring furnace. Figure 4 depicts the VCC setup and the resistance bottom-pouring melting furnace.
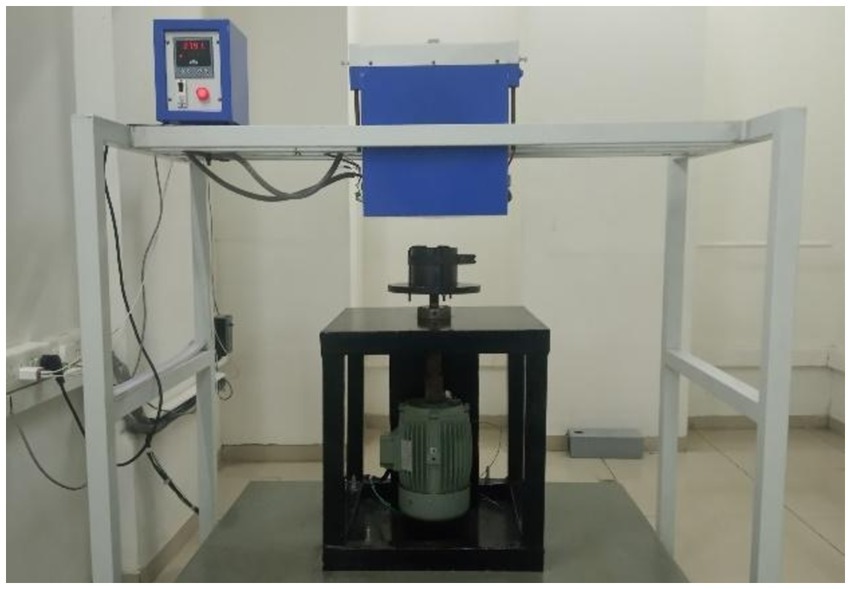
Figure 4. Physical setup of VCC and bottom pouring melting furnace (Sata and Ravi, 2014; Sata and Ravi, 2015).
Various sensors and microcontrollers equip both the physical VCC setup and the melting furnace. Microcontrollers integrate these sensors, which monitor environmental conditions within the casting zone (such as temperature and relative humidity), air quality (measuring CO2 and O2 levels), rotation of the mold, and temperature of the crucible and molten metal. The Message Queuing Telemetry Transport (MQTT) protocol can stream the acquired data to a cloud-based server. Additionally, the microcontrollers incorporate specific relays (ranging up to 10A) to execute various functionalities necessary for controlling the VCC setup and bottom-pouring furnace.
Process monitoring and controlling
The data obtained from the cloud-based server can initially be used for real-time process monitoring and comprehensive control of various functionalities linked to both the VCC setup and the bottom-pouring melting furnace. The system then transmits this acquired data to smart devices and dashboards for visualization, often presenting it in chart form. Both the VCC and the bottom-pouring melting furnace can be used with this system. It can turn the power on and off and fine-tune parameters like the VCC’s rotation speed (from 25 to 200 rotations per minute, with the option of clockwise or counter clockwise rotation) and the melting furnace’s temperature control (from 700 to 1,050°C). Figure 5 illustrates the user interface and other functionalities. The cloud-based server stores data collected from various sensors, which it then uses to enhance quality through a quality prognosis system and data analytics.
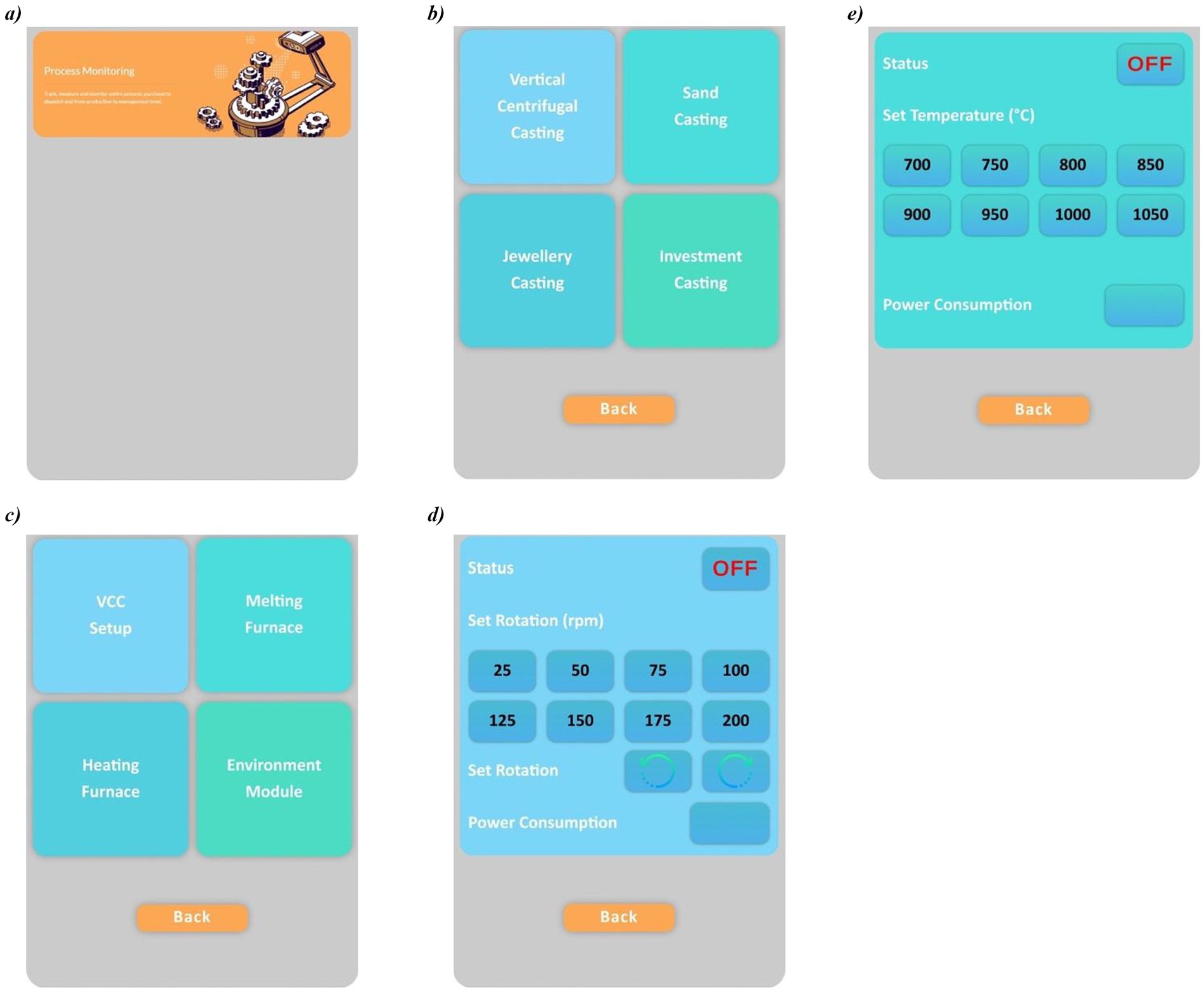
Figure 5. Controlling of VCC and bottom pouring furnace using SMART device. (a) User interface – SMART device. (b) Different modules – SMART device. (c) Interaction with VCC using SMART device. (d) Tuning of VCC setup using a SMART device. (e) Tuning of bottom pouring melting furnace using a SMART device.
Quality prognosis and data analytics system
Analyzing data from various sensors and microcontrollers stored on a cloud-based server is crucial for enhancing the quality of castings, ensuring they are defect-free and possess the desired mechanical properties. We can perform data analytics in two ways: prognosis of quality, which predicts quality based on acquired data, and analytics of quality, which provides answers to questions about how to improve quality. We pre-processed the stored data for both prognosis and analytics purposes. We developed cloud-based quality prognosis and data analytics modules (Figure 6) to optimize the use of stored data.
Quality Prognosis uses the fundamentals of artificial neural networks (ANN) to predict the quality of casting using data stored on a cloud-based server. The system enables users to forecast the quality for the subsequent stage of the production cycle. QPS (Sata and Ravi, 2015) facilitates the selection of parameters that impact accuracy and prediction time, including the transfer function, number of hidden layers, number of neurons in each layer, and training algorithm. Technical literature (Authors, 2019; Sata and Ravi, 2016; Sata and Ravi, 2017a) elaborately explains the development of QPS.
Another important aspect of data analytics is finding out how to improve casting quality. As several parameters drive the overall quality of casting, it is equally important to know a specific range of values for responsible parameters affecting the overall quality of castings (Sata and Ravi, 2017b). For instance, the deviation in pouring temperature drives shrinkage porosity, but it’s crucial to pinpoint the precise pouring temperature range to prevent its occurrence on the shop floor. We develop the Data Analytics System using the fundamentals of Bayesian inference to address these concerns, but due to space constraints, we do not include details on its overall development in this work.
Furthermore, the developed systems are categorized as Internet of Things (IoT)-enabled metal casting. This includes the development of a physical setup, the integration of sensors and microcontrollers, the streaming of data to a cloud-based server, the use of stored data for real-time monitoring, and the implementation of prognosis and analytics systems to enhance the overall quality of castings. We will discuss the integration of this IoT-enabled system with a virtual setup to create an immersive interactive environment.
Creating an immersive interactive environment for VCC
Typically, we develop an immersive interactive environment by creating a virtual setup and integrating it with a physical setup. Furthermore, the virtual setup involves selecting suitable hardware and software, developing a VR environment, incorporating interactive features, and then testing and refining the immersive environment. The developed VR setup will be integrated with the physical setup discussed in earlier sections to create an immersive interactive environment for VCC. This development specifically needs a multidisciplinary approach that involves knowledge of 3D modelling, manufacturing processes, and software development.
Three-dimensional models of VCC as well as bottom-pouring furnaces have been developed using a well-known three-dimensional modelling tool (CREO®), and aesthetic aspects as well as rendering were provided using an open-source tool (Blender®). We also created specific avatars to enhance interaction. We further imported the rendered model into the well-known Unity Hub® game engine to add interactive features. We tested and validated the entire VR setup using a specific set of VR headsets (Oculus Quest 2.0®). We also connected the entire VR setup to a cloud-based server to establish an interface with the physical setup. This integration enables interaction with the physical configuration of the VCC and bottom pouring furnace, enabling the execution of various functions discussed in the section on process monitoring and control. Figure 7 illustrates rendered views of the VCC setup and the bottom pouring furnace. Immersive virtual environments for VCC and bottom-pouring melting furnaces have been developed (Figure 8) and can be compared with the physical environment demonstrated in Figure 4. We further integrated the immersive virtual environment with a cloud-based server by scripting a C# program, compiling it, and executing it on the game engine to interact with the physical setup. We bundle and store the entire environment for future use.
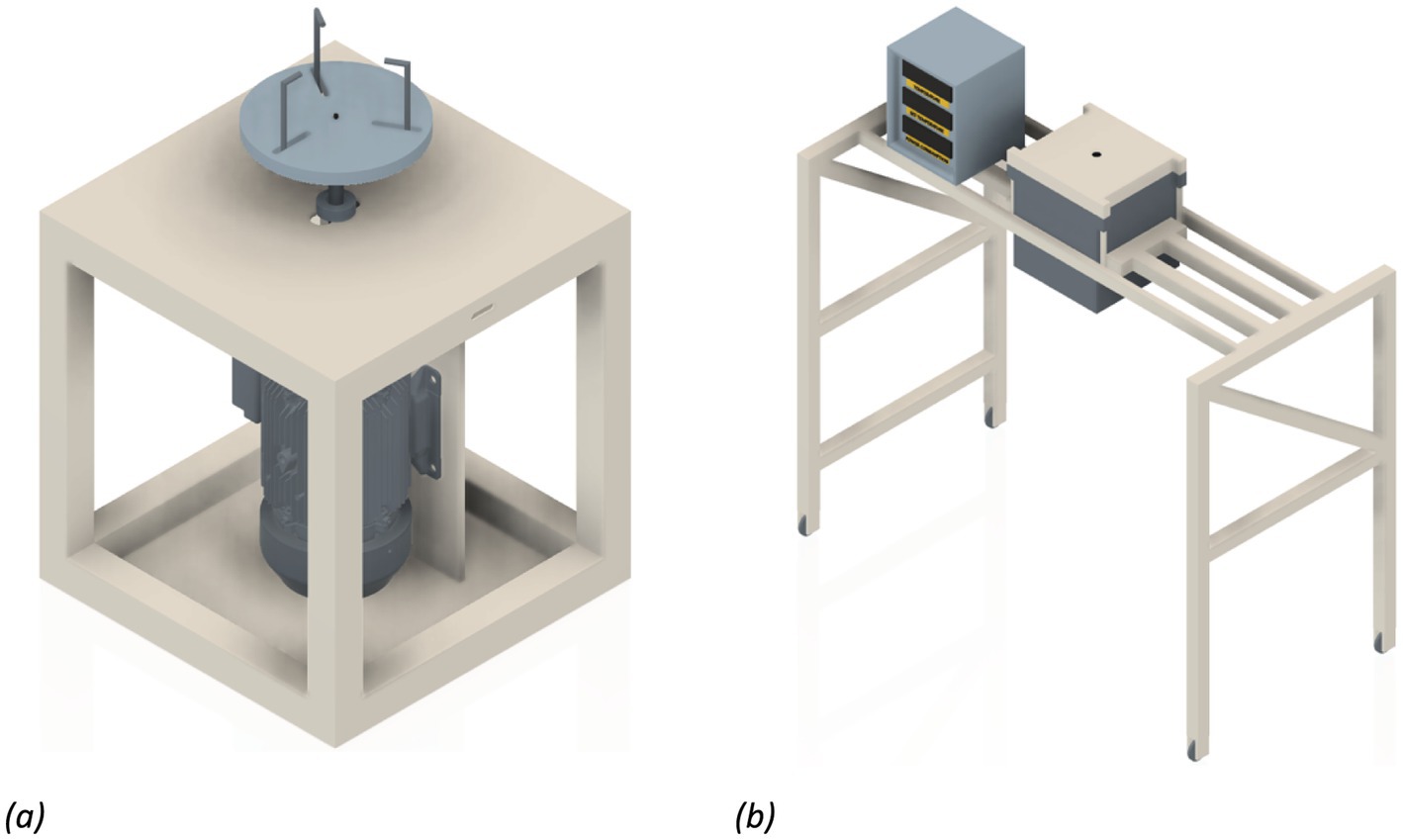
Figure 7. Rendered views of VCC and bottom pouring melting furnace. (a) Rendered VCC setup. (b) Rendered bottom pouring melting furnace.
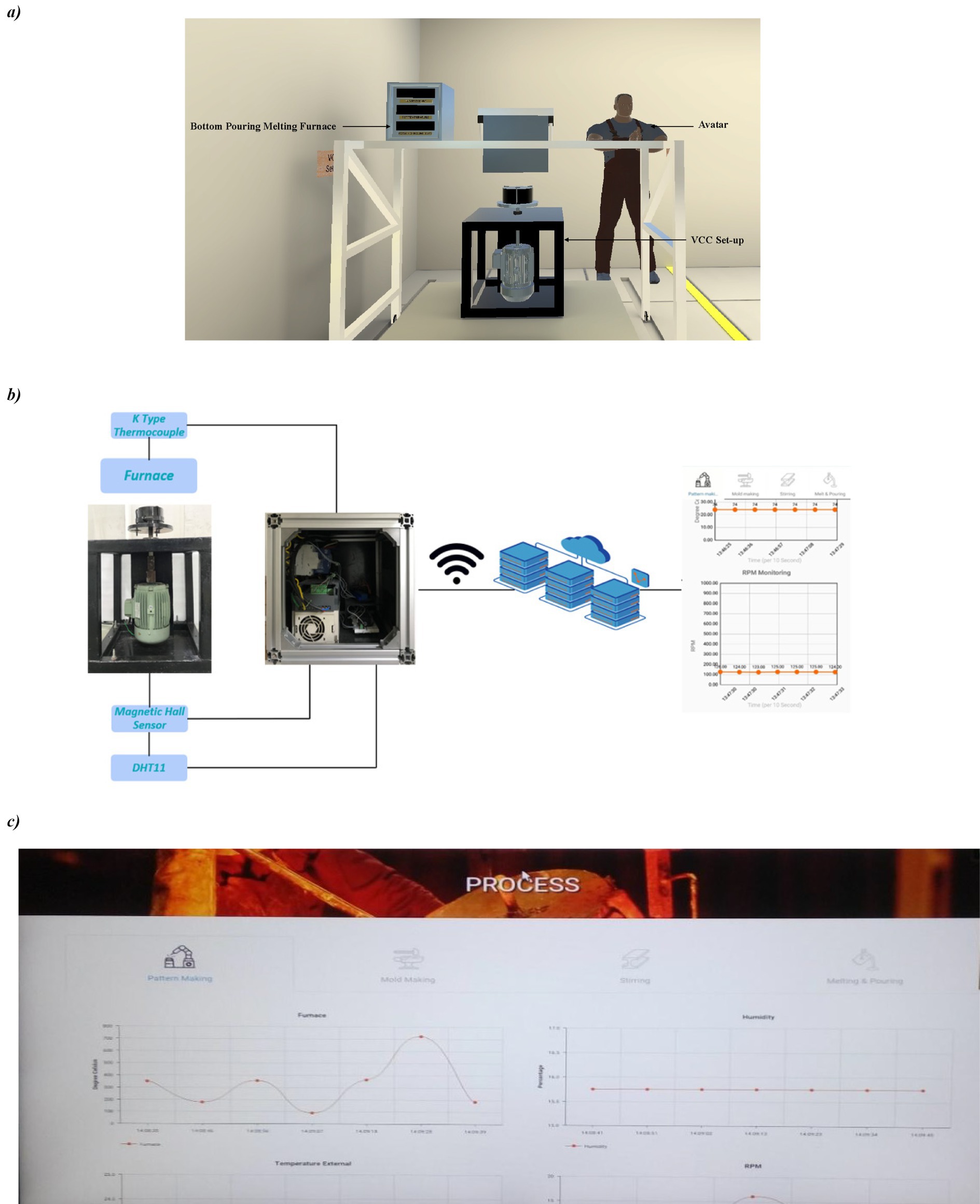
Figure 8. (a) Immersive virtual environment for VCC and melting furnace. (b) Schematic diagram of integration of VCC with DAQ system. (c) Real time monitoring of the process parameters.
A demonstration of an immersive interactive environment for VCC
Researchers have developed and demonstrated an immersive interactive environment-enabled VCC setup at the university level. Researchers have developed an immersive interactive environment for metal casting, specifically for the VCC process, which any interested user can experience. Using a VR headset (of any popular brand), the user can immerse themselves in an immersive environment, which necessitates an internet connection.
overall experience. An avatar that has been specifically prepared interacts further with the user of the Immersive Interactive Environment for metal casting. The setup in the interactive environment (Figure 9) allows the user to interact in similar ways as described in the process monitoring and controlling section. We conducted a few experiments using the immersive interactive environment of an IoT-enabled VCC setup, and Figure 10 shows the resulting metal castings.
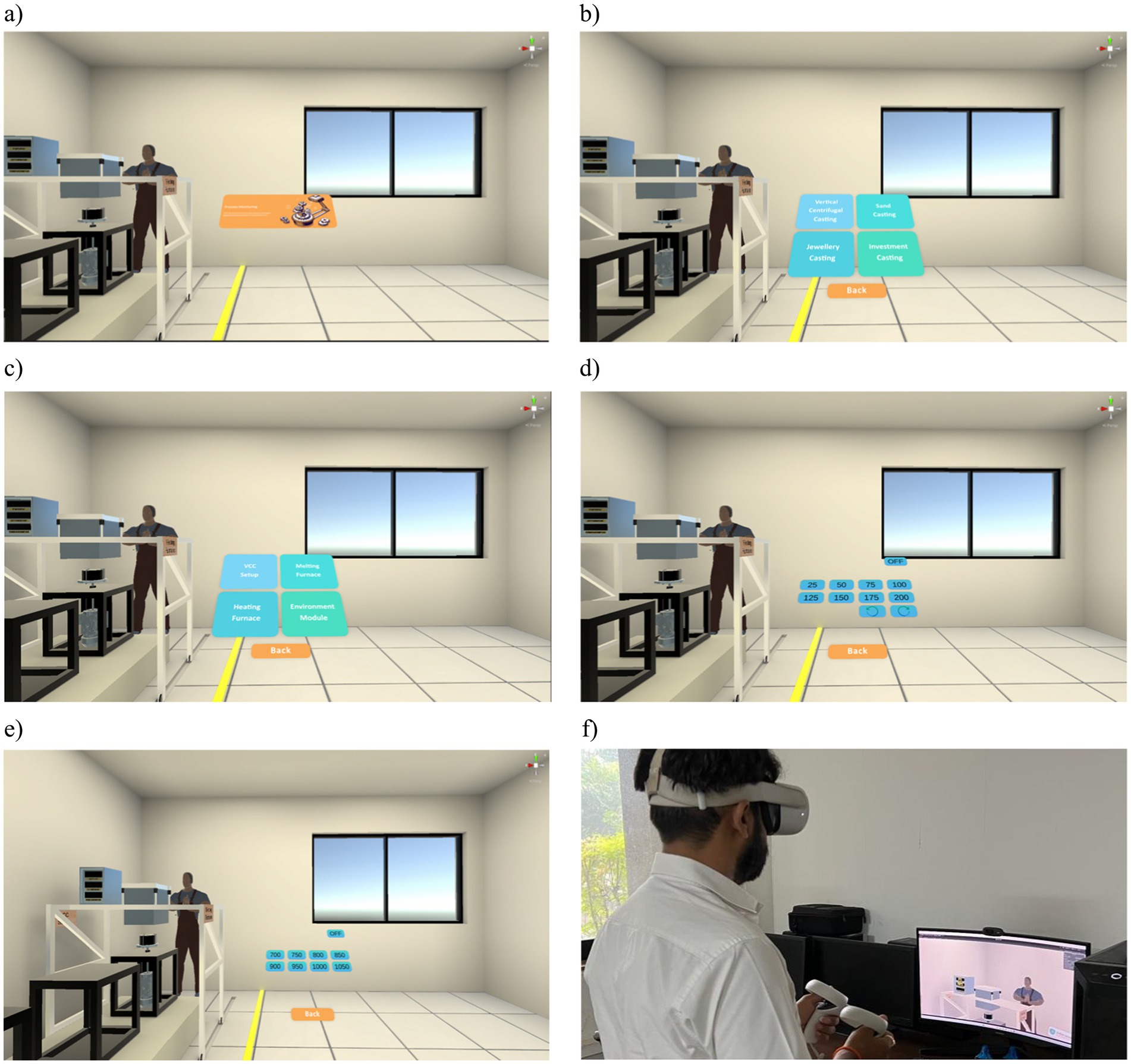
Figure 9. Interaction with VCC and Bottom Pouring Melting Furnace. (a) User interface. (b) Different modules. (c) Interaction with VCC. (d) Tuning of VCC setup. (e) Tuning of bottom pouring melting furnace. (f) Tuning of bottom pouring melting furnace.
The immersive interactive environment of IoT-enabled metal casting offered valuable insights into the metal casting process, enhanced skill sets, and ignited the creative minds of young professionals. This setup really helped in demonstrating multi-disciplinary capabilities, as well as in creating a bridge between the oldest manufacturing process and technology of recent times.
Conclusion
This work aims to create a bottom-pouring melting furnace and an immersive interactive environment for an IoT-enabled VCC setup. An overall framework for development has proposed a comprehensive development framework. Additionally, we have integrated the IoT-enabled VCC with a VR-based setup, enabling interaction with the VCC setup in an immersive interactive setting. We conducted a few experiments using the immersive interactive environment to explore its capabilities on the developed setup (Figure 4). This was done with the help of a mobile application (Figure 5) or web application designed for operation, monitoring, and control from anywhere in the world. The main experiment involved pouring molten metal at different temperatures into a mold that rotates at a specific speed in either a clockwise or anticlockwise direction. We create a digital twin of the setup and develop an immersive environment for interaction with it (Figure 9). We conduct experiments with the current setup and present the results (Figure 10), enabling the identification and prediction of defects.
The present work was primarily focused on extending an Immersive Interactive Environment application to the domain of VCC, as a relatively smaller number of variables are required to be handled in the early phase of development; however, this can also be extended to more complex casting processes, such as the investment casting process, where a large number of variables need to be handled.
The immersive interactive environment of the IoT-enabled VCC has significantly enhanced the learning experience, improved skill sets, and ignited creativity and innovation among young minds. It also provides a great multi-disciplinary platform to include the fundamentals of several domains of engineering, including manufacturing, computers, and electronics. This implementation has demonstrated that we can extend the advanced technology of recent times to metal casting. The immersive interactive environment of IoT-enabled metal casting will undoubtedly transform the metal casting learning experience and inspire young minds to pursue careers in this field.
However, the implementation of an immersive interactive environment for VCC has also revealed several challenges, including the lack of standardization and interoperability of platforms, the high cost of development, and potential security and privacy concerns associated with its use. We can overcome the high-cost concern by developing low-cost hardware and peripheral requirements, and we can address privacy and security-related challenges by extending Blockchain technology into an immersive interactive environment of IoT-enabled metal casting.
Data availability statement
The data that support the findings of this study are available on request from the corresponding author. The data are not publicly available due to containing information that could compromise the privacy of research participants.
Author contributions
DA: Writing – original draft, Methodology, Software. AS: Supervision, Writing – original draft, Writing – review & editing, Data curation. MS: Supervision, Writing – original draft, Writing – review & editing, Resources. SJ: Funding acquisition, Project administration, Resources, Supervision, Validation, Writing – original draft, Writing – review & editing. DM: Data curation, Methodology, Project administration, Software, Writing – original draft, Writing – review & editing.
Funding
The author(s) declare that financial support was received for the research and/or publication of this article. Authors extend their appreciation to the Deanship of Research and Graduate Studies at King Khalid University for funding this work through Large Research Project under grant number RGP2/508/45.
Conflict of interest
The authors declare that the research was conducted in the absence of any commercial or financial relationships that could be construed as a potential conflict of interest.
Generative AI statement
The authors declare that no Gen AI was used in the creation of this manuscript.
Publisher’s note
All claims expressed in this article are solely those of the authors and do not necessarily represent those of their affiliated organizations, or those of the publisher, the editors and the reviewers. Any product that may be evaluated in this article, or claim that may be made by its manufacturer, is not guaranteed or endorsed by the publisher.
References
Anadkat, D., and Sata, A., (2023). "IoT enabled vertical centrifugal casting – Experimental setup." in Proceedings of National Conference on foundry 4.0 – Opportunities and challenges, CSIR (CMERI) - Durgapur (India), 2022. Indian design on internet of things enabled vertical centrifugal casting setup (351952–001).
Authors (2021). Copyright on Software on Quality Prognosis System (QPS) for Manufacturing (SW-14972/2021).
Authors (2023a). Indian design on internet of things enabled vertical centrifugal casting setup (351952001).
Authors (2023b). Indian design on internet of things enabled bottom pouring resistance melting furnace. pp. 351953–351001.
Bansal, G., Rajgopal, K., Chamola, V., Xiong, Z., and Niyato, D. (2022). Healthcare in metaverse: a survey on current metaverse applications in healthcare. IEEE Access 10, 119914–119946. doi: 10.1109/ACCESS.2022.3219845
Bhoraniya, D., Dharaiya, V., and Sata, A. (2022). Application of Niyama criterion to predict shrinkage porosity in vertical centrifugal casting (VCC) of ASTM A356 alloy. Int. J. Process Manag. Benchmark. 12, 395–406. doi: 10.1504/IJPMB.2022.122231
Bhoraniya, D., Kanzaria, P., Anadkat, D., and Sata, A., (2018). "Development of vertical centrifugal casting (VCC) experimental setup," in Proceedings of National Conference on Excellence in Design, Manufacturing & Automation (NCEDMA-2018)/ pp. 26–27.
Chirita, G., Soares, D., and Silva, F. S. (2008). Advantages of the centrifugal casting technique for the production of structural components with Al–Si alloys. Mater. Des. 29, 20–27. doi: 10.1016/j.matdes.2006.12.011
Go, S. Y., Jeong, H. G., Kim, J. I., and Sin, Y. T., (2021). "Concept and developmental direction of metaverse," Korea information process society.
Hosseini, S., Abbasi, A., Magalhaes, L. G., Fonseca, J. C., da Costa, N. M. C., Moreira, A. H. J., et al. (2024). Immersive interaction in digital factory: Metaverse in manufacturing. Proc. Comp. Sci. 232, 2310–2320. doi: 10.1016/j.procs.2024.02.050
Korżel, K., and Łupkowski, P. (2023). The phenomenon of presence in virtual reality is mistakenly equated with immersion. PRESENCE Virt. Augment. Reality 32, 117–127. doi: 10.1162/pres_a_00404
Kye, B., Han, N., Kim, E., Park, Y., and Jo, S. (2021). Educational applications of metaverse: possibilities and limitations. J. Educ. Eval. Health Prof. 18. doi: 10.3352/jeehp.2021.18.32
Latini, A., Di Giuseppe, E., and D'Orazio, M. (2023). Immersive virtual vs real office environments: a validation study for productivity, comfort and behavioural research. Build. Environ. 230:109996. doi: 10.1016/j.buildenv.2023.109996
Lee, L. H., et al. (2021). All one needs to know about metaverse: a complete survey on technological singularity, virtual ecosystem, and research agenda. J. Latex Class Files 14.
LeFebvre, L., LeFebvre, L. E., and Allen, M. (2020). Virtual environment presentations: a qualitative exploration of user perceptions. PRESENCE Virt. Augment. Reality 29, 241–259. doi: 10.1162/pres_a_00367
Li, Z. (2020). Application of metaverse technology in the simulation and optimization of the casting process for improved efficiency and reduced costs. Mater. Sci. Forum 1007, 207–212.
Lin, H., Wan, S., Gan, W., Chen, J., and Chao, H. C., (2022). Metaverse in education: vision, opportunities, and challenges. In 2022 IEEE International Conference on Big Data. pp. 2857–2866.
Liu, Z., Han, S., Chen, Y., Zhang, C., and Liu, X. (2020). Optimization of casting process based on metaverse technology. Adv. Mech. Eng. 12, 1–9.
Mathur, J., Miller, S. R., Simpson, T. W., and Meisel, N. A. (2023). Designing immersive experiences in virtual reality for design for additive manufacturing training. Addit. Manuf. 78:103875. doi: 10.1016/j.addma.2023.103875
Mazloum, K., and Sata, A., (2022). "Quality prediction in vertical centrifugal casting using criterion function," in Industrial transformation: Implementation and Essential Components and Processes Of Digital Systems.
Rahman, K. R. R., Khan Shitol, S., Islam, M. S., and Iftekhar, K. T. (2023). Use of metaverse technology in education domain. J. Metaverse 3, 79–86. doi: 10.57019/jmv.1223704
Richter, S., and Richter, A. (2023). What is novel about the metaverse? Int. J. Inf. Manag. 73:102684. doi: 10.1016/j.ijinfomgt.2023.102684
Sata, A. (2016). Investment casting defect prediction using neural network and multivariate regression along with principal component analysis. Int. J. Manuf. Res. 11, 356–373. doi: 10.1504/IJMR.2016.082819
Sata, A., and Ravi, B. (2014). Comparison of some neural network and multivariate regression for predicting mechanical properties of investment castings. Int. J. Mat. Eng. Perform. 23, 2953–2964. doi: 10.1007/s11665-014-1029-1
Sata, A., and Ravi, B., (2015). "Mechanical property prediction of investment castings using artificial neural network and multivariate regression analysis," in Proceedings of 63rd Indian Foundry Congress, Institute of Indian Foundrymen, Greater Noida.
Sata, A., and Ravi, B., (2016). "Novel Bayesian inference-based approach to identify critical parameters affecting mechanical properties of investment castings," in Proceedings of 72nd World Foundry Congress, Nagoya, Japan, May 22–24.
Sata, A., and Ravi, B. (2017a). Bayesian inference-based investment casting defects analysis system for industrial application. Int. J. Adv. Manuf. Technol. 90, 3301–3315. doi: 10.1007/s00170-016-9614-0
Sata, A., and Ravi, B., (2017b). "Foundry data analytics to identify critical parameters affecting mechanical properties of investment castings," in Proceedings of ASME 2017 IMECE, Florida, USA, pp. 3-9.
Seabra, E. A. R., Barbosa, J., Barbosa, J., Puga, H., and Puga, H., (2009). "Design and development of a centrifugal casting machine for pistons production," in Selected Proceedings from the 13th International Congress on Project Engineering. pp. 401–408.
Sheng, J., Zhang, Q., Li, H., Shen, S., Ming, R., Jiang, J., et al. (2023). Digital twin driven intelligent manufacturing for FPCB etching production line. Comput. Ind. Eng. 186:109763. doi: 10.1016/j.cie.2023.109763
Trunfio, M., and Rossi, S. (2022). Advances in metaverse investigation: streams of research and future agenda. Int. J. Virtual Worlds 1, 103–129. doi: 10.3390/virtualworlds1020007
Xenakis, I., Gavalas, D., Kasapakis, V., Dzardanova, E., and Vosinakis, S. (2022). Nonverbal communication in immersive virtual reality through the lens of presence: a critical review. PRESENCE Virt. Augment. Reality 31, 147–187. doi: 10.1162/pres_a_00387
Yan, H., Hua, Q., Wang, Y., Wei, W., and Imran, M. (2017). Cloud robotics in smart manufacturing environments: challenges and countermeasures. Comput. Electr. Eng. 63, 56–65. doi: 10.1016/j.compeleceng.2017.05.024
Yun, H., and Jun, M. B. G. (2022). Immersive and interactive cyber-physical system (I2CPS) and virtual reality interface for human involved robotic manufacturing. J. Manuf. Syst. 62, 234–248. doi: 10.1016/j.jmsy.2021.11.018
Zallio, M., and Clarkson, P. J. (2022). Designing the metaverse: a study on inclusion, diversity, equity, accessibility and safety for digital immersive environments. Telematics Inform. 75:101909. doi: 10.1016/j.tele.2022.101909
Keywords: metal casting, vertical centrifugal casting, Industrial Internet of Things (IIoT), Augmented Reality (AR), Virtual Reality (VR), metaverse
Citation: Anadkat D, Sata A, Shukla M, Jarboui S and Mobarsa D (2025) Designing an immersive interactive environment for IIoT-enhanced vertical centrifugal casting. Front. Educ. 9:1507851. doi: 10.3389/feduc.2024.1507851
Edited by:
Fezile Özdamlı, Near East University, CyprusReviewed by:
Seren Başaran, Near East University, CyprusMayurkumar Sutaria, Charotar University of Science and Technology, India
Copyright © 2025 Anadkat, Sata, Shukla, Jarboui and Mobarsa. This is an open-access article distributed under the terms of the Creative Commons Attribution License (CC BY). The use, distribution or reproduction in other forums is permitted, provided the original author(s) and the copyright owner(s) are credited and that the original publication in this journal is cited, in accordance with accepted academic practice. No use, distribution or reproduction is permitted which does not comply with these terms.
*Correspondence: Amit Sata, YW1pdC5zYXRhQG1hcndhZGllZHVjYXRpb24uZWR1Lmlu