- 1Biosystems and Agricultural Engineering, University of Kentucky, Lexington, KY, United States
- 2College of Chemical Engineering, Nanjing Forestry University, Nanjing, China
Lignin is an integral part of the plant cell wall, which provides rigidity to plants, also contributes to the recalcitrance of the lignocellulosic biomass to biochemical and biological deconstruction. Lignin is a promising renewable feedstock for aromatic chemicals; however, an efficient and economic lignin depolymerization method needs to be developed to enable the conversion. In this study, we investigated the depolymerization of alkaline lignin in aqueous 1-ethyl-3-methylimidazolium acetate [C2C1Im][OAc] under oxidizing conditions. Seven different transition metal catalysts were screened in presence of H2O2 as oxidizing agent in a batch reactor. CoCl2 and Nb2O5 proved to be the most effective catalysts in degrading lignin to aromatic compounds. A central composite design was used to optimize the catalyst loading, H2O2 concentration, and temperature for product formation. Results show that lignin was depolymerized, and the major degradation products found in the extracted oil were guaiacol, syringol, vanillin, acetovanillone, and homovanillic acid. Lignin streams were characterized by Fourier transform infrared spectroscopy and gel permeation chromatography to determine effects of the experimental parameters on lignin depolymerization. The weight-average molecular weight (Mw) of liquid stream lignin after oxidation, for CoCl2 and Nb2O5 catalysts were 1,202 and 1,520 g mol−1, respectively, lower than that of Kraft lignin. Polydispersity index of the liquid stream lignin increased as compared with Kraft lignin, indicating wide span of the molecular weight distribution as a result of lignin depolymerization. Results from this study provide insights into the role of oxidant and transition metal catalysts and the oxidative degradation reaction sequence of lignin toward product formation in presence of aqueous ionic liquid.
Introduction
Lignin is the second most abundant terrestrial biopolymer on earth and is one of the three main building blocks of lignocellulosic biomass (Das et al., 2012). Depending on the biomass source, lignin accounts for approximately 10–30% of the biomass together with cellulose, hemicellulose, and other minor components (Chatel and Rogers, 2013). Lignin is a three dimensional polyphenolic biopolymer synthesized in plants mainly from coniferyl, sinapyl, and p-coumaryl alcohol (Brandt et al., 2015). These monomers give rise to guaiacyl (G), syringyl (S), and p-hydroxyphenyl (H) subunits via free radical polymerization (Brandt et al., 2015). As projected by the 2009 Renewable Fuel Standard (RFS2) on basis of the 2007 Energy Independence and Security Act, the US alone will generate approximately 60 million dry tons of lignin annually from the capacity of cellulosic biorefineries by year 2022 (Tilman et al., 2009; Somerville et al., 2010; Brown and Brown, 2013). This quantity will add on top of the existing ~100 million dry tons of lignin from paper and pulping industry (Chakar and Ragauskas, 2004; Ragauskas et al., 2014). Despite its great potential to a wide range of chemicals, lignin is yet an underutilized substrate, and under the current biorefinery concept, lignin is commonly burned to generate steam and electricity. It is critical to convert lignin waste streams to high value-added chemicals to enable cost-competitive biofuels and chemicals production in a biorefinery (Ragauskas et al., 2014; Beckham et al., 2016; Mottiar et al., 2016).
Lignin’s full potential as a renewable source for aromatic compounds can be, in part, unlocked only if an efficient and economic method for lignin depolymerization and valorization is developed (Prado et al., 2016a). The heterogeneity of lignin (both in its varied bond chemistry and its variability between plants), however, is the major hurdle to its targeted upgrading and reuse as a feedstock for chemicals and advanced materials (Das et al., 2012). The type and abundance of the inter-unit linkages (β-O-4, β-β, β-5, 5-5, and 5-O-4), as combinations of carbon–oxygen and carbon–carbon bonds, vary largely based on the plant type (Zakzeski et al., 2010a). Several lignin conversion methods are currently under investigation, inlcuding hydrolysis, hydrogenolysis, pyrolysis, catalytic oxidation, and biological depolymerization (Stärk et al., 2010). Among those, catalytic oxidation is one of the suitable routes as the side-chain aliphatic OH, the terminal phenolic OH groups, and the reactive benzylic positions in lignin can be selectively modified via oxidation. Lignin oxidation produces a suite of platform compounds with added functionalities, which can be subsequently separated through filtration or extraction (Crestini et al., 2010; Pandey and Kim, 2011).
Ionic liquids (ILs) have received increasing interest because of their high efficacy in fractionating and pretreating lignocellulosic biomass. ILs are defined as salts consisting of cations and anions, which typically melt at or below 100°C. ILs have wide range of applications due to their unique properties including negligible vapor pressure, thermal, electrochemical, and chemical stability, and versatile solvent power (Marszałł and Kaliszan, 2007). Several ILs, such as 1-ethyl-3-methylimidazolium acetate [C2C1Im][OAc], 1-butyl-3-methylimidazolium chloride [C4C1Im][Cl] (Kilpeläinen et al., 2007), 1,3-dimethylimidazolium methylsulfate [C2C1Im][MeSO4] (Tan et al., 2009), and 1-butyl-3-methylimidazolium methylsulfate [C4C1Im][MeSO4] (Pu et al., 2007) have proven their efficacy toward delignification of plant biomass and lignin depolymerization. The solvent property of an IL is the key for lignin solvation. It was suggested that the anion of IL is the dominating factor influencing lignin dissolution as compared with cation. The affinity in which anions intereacting with lignin is in the order of sulfate > lactate > acetate > chloride > phosphate (Prado et al., 2016a).
Despite the effectiveness of [C2C1Im][OAc] and similar ILs at reducing the recalcitrance of lignocellulosic biomass and solubilizing lignin, the challenges associated with product recovery and IL recycling hinder the commercial scale-up of an IL-based technology (Datta et al., 2010; Klein-Marcuschamer et al., 2011; Gladden et al., 2014). In an aqueous IL pretreatment system, the majority of the lignin is extracted to the liquid phase (black liquor) and separation of lignin form this liquid system is however challenging. Hence, direct lignin valorization in aqueous (liquor) IL could offer a new strategy for selective lignin depolymerization meanwhile help to tackle the challenges associated with IL recycle and product recovery, thus improving the economics of an IL-based biorefining process.
Catalytic oxidation of lignin and lignin model compounds into aromatic chemicals in various solvent systems has been explored (Behling et al., 2016). Oxidative catalysts including inorganic metal-based catalysts, organocatalysts, and metallo-based complexes have been investigated for lignin oxidation to produce high value chemicals (Crestini et al., 2010). Transitional metals are known catalysts for oxidation reaction with several transition metals such as CuII, FeIII, MnII,III, CoII, and ZrIV identified in enhancing product yields of lignin oxidation (Zakzeski et al., 2010a). Side-chain cleavage and ether bond hydrolysis are the predominant reactions during the oxidation of lignin model compounds (Zhang et al., 2016).
A few oxidizing agents such as H2O2 and oxygen have been demonstrated effective in lignin depolymerization when combined with metal oxide-based catalysts; however, most of the studies were carried out in organic solvents or water under basic/acidic conditions (Zakzeski et al., 2010b; Behling et al., 2016). Several studies have explored catalysis of lignin model compounds and technical lignin in 100% IL medium (Zakzeski et al., 2010b; Chatel and Rogers, 2013; Xu et al., 2014). Delignification of miscanthus and willow in [HC4Im][HSO4] and [Et3NH][HSO4] and subsequent lignin depolymerization in the black liquor using H2O2 in presence of TiO2 catalyst were reported recently (Prado et al., 2016a,b). Despite many reports of using [C2C1Im][OAc] for biomass delignification, catalytic lignin depolymerization in aqueous [C2C1Im][OAc] has not been explored. There is a gap in our understanding of the interplay of catalyst, oxidizing agent, and product formation in an aqueous IL system (Zhang et al., 2016). Hence, the objectives of this study are to: (1) screen transition metal catalysts in aqueous [C2C1Im][OAc] IL system; (2) investigate the effects of catalyst loading, temperature, and H2O2 concentration on the production of aromatic compounds from alkaline (Kraft) lignin; (3) characterize the lignin before and after oxidation reaction. Results from this study provide insights into the oxidative degradation pathway of lignin in the presence of aqueous IL and the selectivity of catalyst/oxidizing agent toward the formation of desirable products.
Materials and Methods
Materials
Transition metal salts Nb2O5 (99.9%), CoCl2⋅6H2O (98%), CuSO4 (99%), MnN2O6⋅4H2O (97%), TiO2 (99.8%), CrKO8S2⋅12H2O (98%), and NiCl2⋅XH2O (99.9%) were obtained from Sigma Aldrich (St. Louis, MO, USA). The IL ([C2C1Im][OAc]), alkaline (Kraft) lignin, 2-methyltetrahydrofuran (MeTHF, 99%), H2O2 (30%), guaiacol (98%), syringol (98%), vanillin (99%), acetovanillone (98%), and homovanillic acid (98%) were also procured from Sigma Aldrich (St. Louis, MO, USA).
Lignin Depolymerization, Extraction, and Analytical Method
Lignin oxidation reactions were performed in batch reactors. Prior to the reaction, lignin (10 wt%) was treated in [C2C1Im][OAc] for 3 h at 140°C by following a typical IL pretreatment condition shown elsewhere (Li et al., 2010); subsequently the IL–lignin mixtures were diluted by adding water at a mass ratio of 1:1 to a 2 mL total volume. To the above mixture, a predetermined amount of catalyst and H2O2 were added and the reaction was conducted at different temperatures (74–126°C) for 3 h with constant mixing by a magnetic stir bar at 200 rpm. The catalyst and hydrogen peroxide (commercially available 30% H2O2 solution) loadings were based on the total weight of IL and lignin. After reaction, residual lignin was precipitated by addition of 2 mL of water followed by centrifugation at 4,000 rpm for 15 min to separate solids from liquid stream. The liquid stream was subjected to a liquid–liquid extraction using MeTHF for three times. Finally, the MeTHF was evaporated to leave thick oil in a vacuum oven at 30°C for 24 h. The oil was re-dissolved in 750 µL of ethyl acetate and analyzed by GC/MS for monomeric compounds.
The solid stream (residual lignin) was washed by 5 mL warm water for four times and subsequently oven dried for 24 h at 70°C. Lignin conversion was calculated using Eq. 1
Identification and quantification of the monomeric products from the depolymerization reaction were performed by Agilent 7890B GC coupled 5977B MS with an HP-5ms (60 m × 0.32 mm) capillary column. The temperature program started at 50°C and increased to 120°C at 10°C min−1 with a holding time of 5 min; then it was raised to 280°C at 10°C min−1 with a holding time of 8 min and to 300°C at 10°C min−1 with holding time of 2 min (Prado et al., 2016a). Helium was used as a carrier gas at a flow rate of 1.2 mL min−1. Calibration curves were created using commercially available pure compounds: guaiacol, syringol, vanillin, acetovanillone, and homovanillic acid (Sigma Aldrich, St. Louis, MO, USA).
Screening of Catalysts
In a series of preliminary screening experiments, various transition metal catalysts including Nb2O5, CoCl2⋅6H2O, CuSO4, MnN2O6⋅4H2O, TiO2, CrKO8S2⋅12H2O, and NiCl2⋅XH2O were tested in batch reactors. Catalyst and H2O2 were both loaded at 5 wt% loading (IL + lignin); the screening experiments were conducted at 120°C and a reaction time of 3 h (Prado et al., 2016a). Identification and determination of product formation and concentration were performed according to the batch experiments mentioned in the Section “Lignin Depolymerization, Extraction, and Analytical Method.”
Experimental Design
An orthogonal central composite design (CCD) (Table 1) was used to study the effect of H2O2 concentration, catalyst loading, and temperature on product concentration for selected catalysts. Levels for independent variables were selected to be, 1–5%, 1–5%, and 80–120°C for H2O2 concentration, catalyst loading, and temperature, respectively.
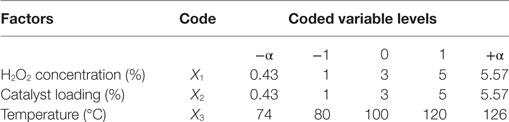
Table 1. Experimental factors and their coded levels of independent variables for central composite design.
A CCD consists of 2p factorial runs with 2p axial runs and Pc center runs. In this study, the independent variables were H2O2 concentration (X1), catalyst loading (X2), and temperature (X3). For each independent variable, a 23 full factorial CCD for the three variables consisting of 8 factorial points, 6 axial points, and 3 replicates at the center points were employed, which accounted for a total of 17 experiments.
The center points were used to determine the experimental error and reproducibility of the data. Low and high levels of the independent variable were coded as −1 and +1. Axial points were located at (±α, 0, 0), (0, ±α, 0), and (0, 0, ±α) where α is the distance of the axial point. In this study, α value was fixed at 1.287. The experimental sequence was randomized to minimize the effects of uncontrolled errors. The response variable for this study was product concentration (Y1). Response was used to develop an empirical model corresponding to product concentration using a second-degree polynomial equation as given in Eq. 2:
where is the response, β0 is the intercept, βi the linear coefficients, βii the quadratic coefficients, βij the interaction coefficients, and xixj are the coded values.
Lignin Characterization
Gel Permeation Chromatographic (GPC) Analysis
The weight-average molecular weight (Mw) and number-average molecular weight (Mn) of the residual lignin were measured by GPC after acetylation (Samuel et al., 2014). An Ultimate 3000 HPLC system (Dionex Corporation, Sunnyvale, CA, USA) equipped with an ultra violet (UV) detector was used. Separation was accomplished with a Mixed-D PLgel column (5 µm particle size, 300 mm × 7.5 mm i.d., linear molecular weight range of 200–400,000 µm, Polymer Laboratories, Amherst, MA, USA) at 80°C using a mobile phase of THF at a flow rate of 0.5 mL min−1. Elution profile of materials eluting from the column was monitored by UV absorbance at 280 nm and calibrated using a polystyrene standards kit (Sigma-Aldrich).
Fourier Transform Infrared (FTIR)
Changes in the chemical structure of untreated lignin and residual lignin were performed using a Thermo Nicolet Nexus 870 FTIR-ATR spectroscopy. Spectra of the lignin samples were obtained using an average of 64 scans in the range of 700 and 4,000 cm−1 with a spectral resolution of 1.928 cm−1.
Results and Discussion
Catalyst Selection and Model Development
Catalysts were screened based on the total product concentration and conversion. Results obtained from the screening experiments show that out of the seven catalysts used CoCl2 and Nb2O5 gave the highest product concentration and conversion compared to the other catalysts (Figure 1). Subsequently, optimization of batch experiments was performed using these two catalysts. Cobalt (Co)-based catalysts have been used for oxidation of lignin model compounds and alcohols in 1-ethyl-3-methylimidazolium diethylphosphate ([C2C1Im][DEP]) (Zakzeski et al., 2010b, 2011). Co species facilitate the oxidation reaction by readily catalyzing the disproportionation of H2O2 to form O2 and H2O (Pokutsa et al., 2009). In addition, several studies reported niobium oxide as a selective and effective oxidation catalyst for a wide range of oxidation reactions (Wachs et al., 2000). Apart from acting as a strong Lewis acid, niobium oxide also has the capability to stabilize oxidation cation species, which could assist in the electrophilic attack of H2O2 on lignin (Fielicke et al., 2003; Nakajima et al., 2011).
Concentrations (mg L−1) of five products: guaiacol, syringol, vanillin, acetovanillone, and homovanillic acid were determined by GC/MS for all the reaction conditions based on the central composite design. Results illustrate that the total product concentrations for CoCl2 catalyst were in the range of 545.3–1,200.5 mg L−1; whereas for Nb2O5 catalyst the total product concentrations fell into 340.7–1,325.6 mg L−1 range (Table 2). In addition, obtained data were fitted to a polynomial model to optimize the reaction parameters for the formation of products from lignin using a desirability approach (JMP 12, SAS Institute, Inc., Cary, NC, USA). The suggested optimum levels for CoCl2 catalyst were temperature of 120°C, catalyst loading of 1%, and H2O2 concentration of 1%, corresponding to a predicted total product concentration of 1,079.5 mg L−1 at 95% confidence interval (989.0, 1,169.9). For Nb2O5 catalyst, the optimum reaction parameters were temperature of 120°C, catalyst loading of 4.45%, and H2O2 concentration of 3.08%, corresponding to a predicted total product concentration of 1,262.6 mg L−1 at 95% confidence interval (1,182.8, 1,342.3). The quadratic regression models for the CoCl2 and Nb2O5 catalysts were shown below:
where, X1, X2, and X3 are H2O2 concentration, catalyst loading, and temperature, respectively. The linear effects were represented by the coefficients of one factor (X1, X2, X3), while the coefficients of the second-order term and two-factor term (X1 X2, X1 X3, X2 X3) represent the quadratic effects and interaction effects, respectively.
Lignin Breakdown Product Identification
Products obtained from the catalytic oxidation process were identified and quantified using GC/MS. Figure 2 shows a GC chromatography representing the mixture of aromatic products derived from lignin after catalytic oxidation in aqueous IL. Several lignin derived monomers of commercial interest such as guaiacol, syringol, vanillin, acetovanillone, and homovanillic acid were determined quantitatively for both catalysts. Guaiacol was the major oxidation product followed by homovanillic acid, acetovanillone, vanillin, and syringol. For CoCl2 catalyst, the concentration of guaiacol was in a range of 265.0–536.9 mg L−1 whereas for Nb2O5 catalyst the concentration was in a range of 235.4–649.4 mg L−1. The concentrations of homovanillic acid were in the range of 25.5–314.3 and 45.1–361.7 mg L−1, for CoCl2 and Nb2O5 catalysts, respectively. Other products such as syringol, vanillin, and acetovanillone were also present at small proportions. The alkaline lignin used in this study was derived from softwood, which contains primarily G-lignin and a small quantity of S-lignin in the original feedstock (Sigma-Aldrich, 2016). The fact that products obtained from oxidation reactions were mainly G-lignin derived compounds corroborates the G-lignin rich source. Similar profile of compounds were reported in a previous study using [C2C1Im][OAc] IL for the pretreatment of switchgrass, eucalyptus, and Kraft lignin (Varanasi et al., 2013). In another study, Stärk et al. (2010) reported similar product profiles from the catalytic oxidation of organosolv beech wood lignin with guaiacol as the main product probably due to the cleavage of β-aryl ether bond.
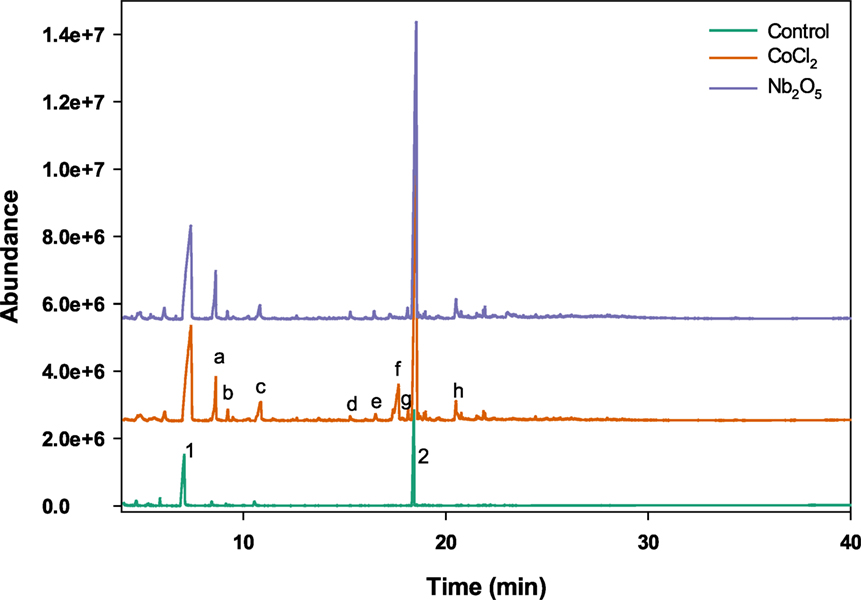
Figure 2. Representative GC chromatography [peaks representing a: guaiacol, b: 4-methoxy-1,3-benzenediamine, c: 1,3,5-benzenetriol, d: syringol, e: vanillin, f: 1-methyl-4-thiouracil, g: acetovanillone, h: homovanillic acid, 1: 1-ethyl imidazole, and 2: butylated hydroxytoluene (stabilizer for MeTHF)]. Experimental conditions: temperature: 120°C, catalyst loading: 1%, and H2O2 concentration: 1%.
Product formation during a catalytic oxidation process is partially dependent on the basicity or acidity of the reaction system. Formation of vanillin from Kraft lignin by different oxidants such as H2O2, O2, and nitrobenzene in NaOH medium has been reported (Xiang and Lee, 2000; Rodrigues Pinto et al., 2010; Pandey and Kim, 2011). It was reported that the IL, [C2C1im][OAc] possesses dual basic and acidic characteristics as a function of temperature (Varanasi et al., 2012). The hydrogen bond basicity (β) decreased by 1.4% with an increase in temperature from 120 to 160°C (Varanasi et al., 2012). In an aqueous IL system, the hydrogen bond basicity (β value) can be correlated with the disruption of the inter- and intramolecular hydrogen bondings in cellulose, hemicellulose, and lignin (Shi et al., 2014). It is likely that the G-lignin monomeric products obtained in this study were phenolic moieties of G-lignin caused by losing phenolic proton under alkaline conditions at low reaction temperatures (Varanasi et al., 2012). These results lead to the hypothesis that the temperature-dependent dual basic and acidic characteristics of an IL could serve as a design basis to tune the aqueous IL system for better lignin solubility and product selectivity (Park and Kazlauskas, 2003; Shi et al., 2014).
Effect of Reaction Parameters on Product Concentration and Yield
H2O2 Loading
The effect of H2O2 loading on total product concentration was optimized for both catalysts. Figures 3A,C illustrate the effect of H2O2 loading coupled with interactions of catalyst loading and reaction temperature for CoCl2 catalyst. From the 3D response surface plot, it appeared that the overall product concentrations increased with the decrease in H2O2 loading, with 1% H2O2 giving the highest concentration. In addition, results from ANOVA (Tables S1 and S3 in Supplementary Material) indicate that H2O2 loading had a significant effect (p = 0.020) whereas interaction effect of H2O2 with catalyst loading and temperature were not significant (p = 0.096 and p = 0.055). Figures 4A,C illustrate the combined effect of H2O2 concentration with catalyst loading and temperature on product concentration for Nb2O5 catalyst. Results from ANOVA (Tables S1 and S4 in Supplementary Material) illustrate that H2O2 had less significant effect (p = 0.064) on product formation in the experimental design specified levels. Furthermore, the interaction effects of H2O2 with catalyst loading and temperature were not significant (p = 0.772 and p = 0.058), which explain the lack of any particular trend in the 3D response surface plot.
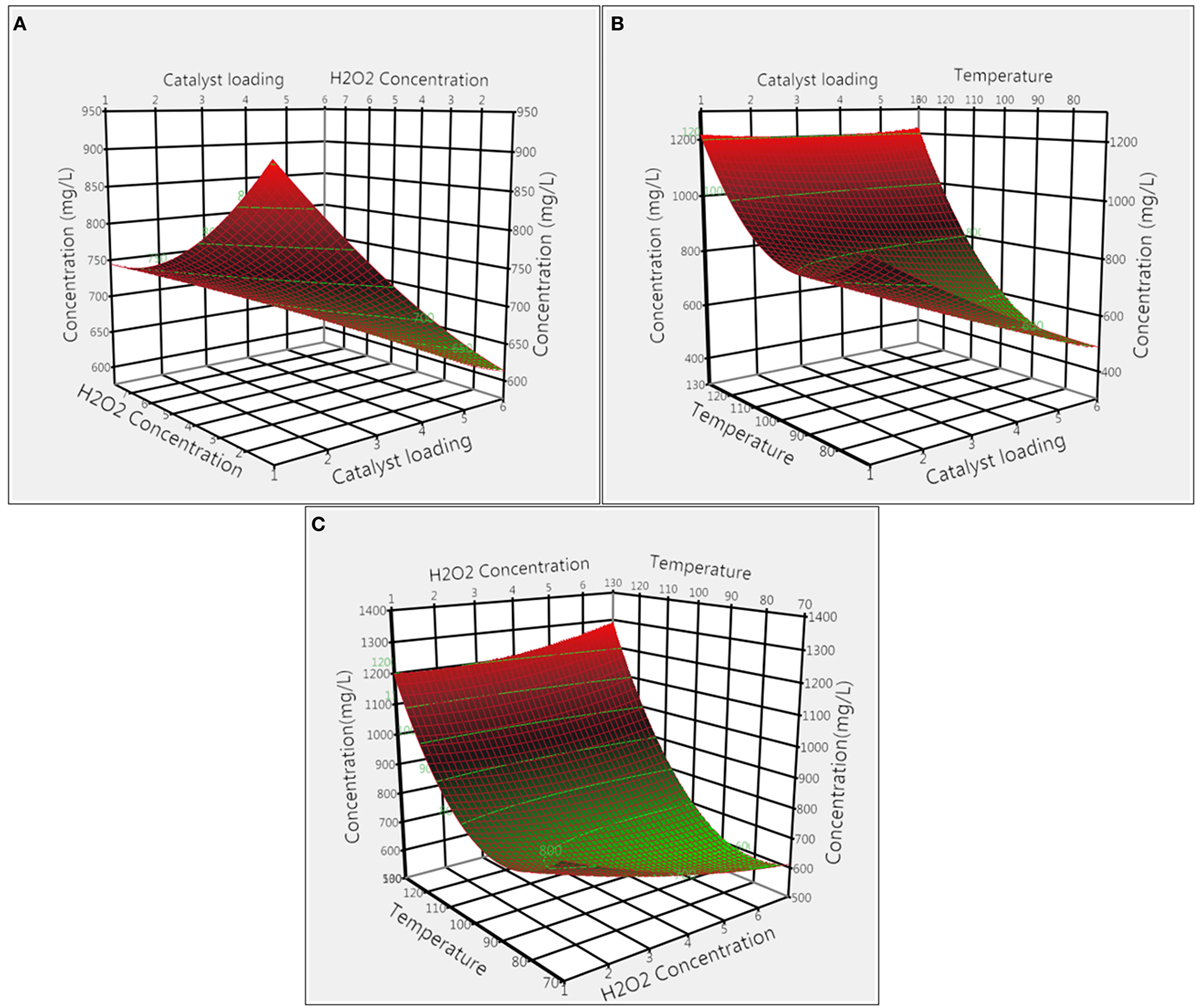
Figure 3. Surface response plots showing the effect of CoCl2 catalyst on product concentration: (A) catalyst loading and H2O2 concentration, (B) catalyst loading and temperature, and (C) temperature and H2O2 concentration.
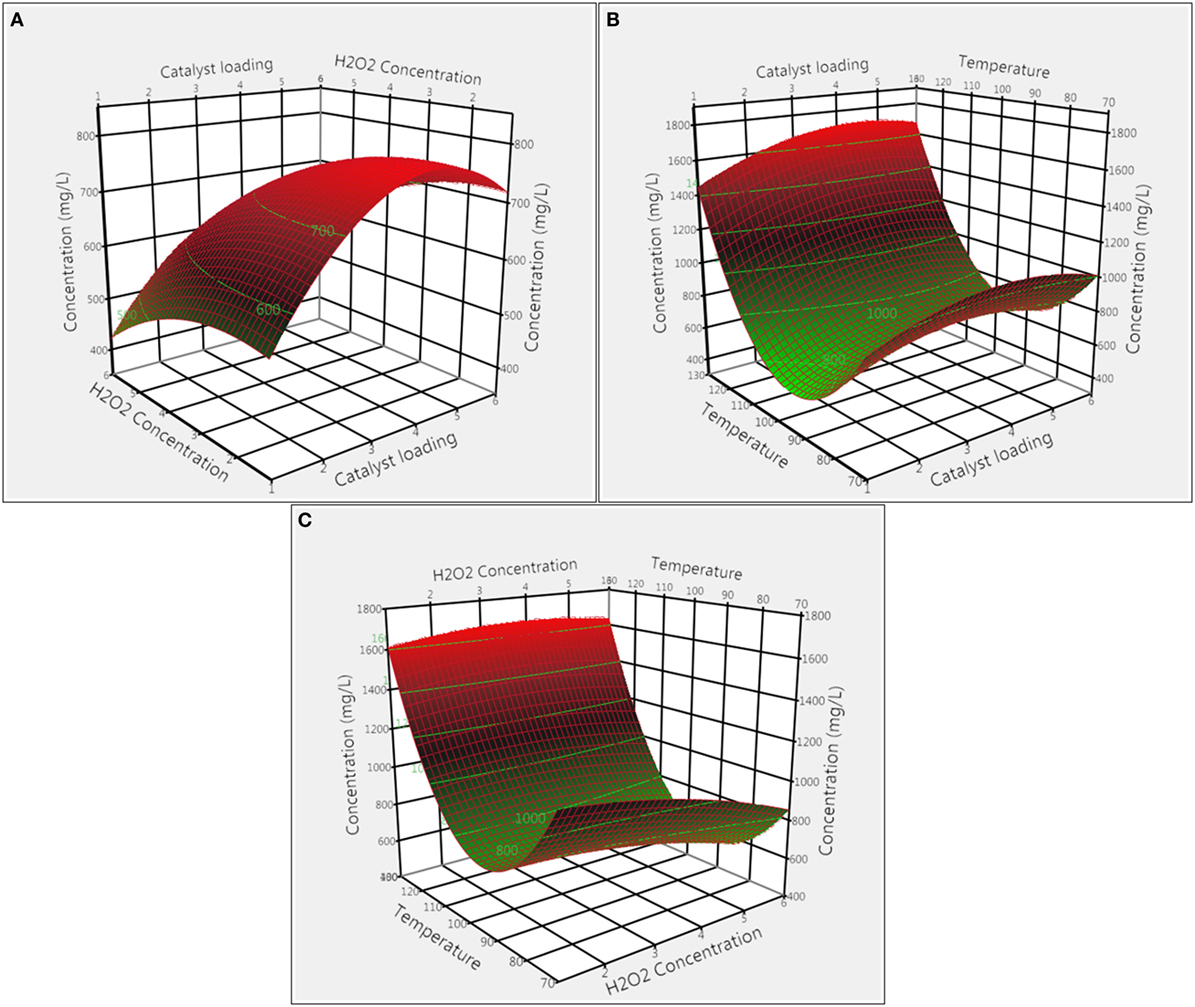
Figure 4. Surface response plots showing the effect of Nb2O5 catalyst on product concentration: (A) catalyst loading and H2O2 concentration, (B) catalyst loading and temperature, and (C) temperature and H2O2 concentration.
For both catalysts, H2O2 concentration (in the design specified range) did not have a significant effect on product concentration. Results obtained from this study corroborate the findings by Das et al., using niobium oxalate catalyst in presence of H2O2 in an aqueous system where increasing H2O2 loading from 3 to 7% did not change the concentrations of vanillin and syringaldehyde significantly. In another study, Xiang and Lee (2000) demonstrated that doubling H2O2 loading from 0.56 to 1.12 g resulted in a total aromatics yield of 9.8 and 8.3%, respectively. The decrease in product yield could be explained by the decomposition of excess H2O2 before its reaction with lignin or over-oxidization to other intermediate compounds (Xiang and Lee, 2000).
Catalyst Loading
The effects of CoCl2 catalyst loading combined with H2O2 concentration and temperature on the total quantified product concentration are shown in Figures 3A,B. From the 3D surface plots, it is evident that 1% of CoCl2 catalyst loading gave the highest product concentration. ANOVA results (Tables S1 and S3 in Supplementary Material) demonstrate that catalyst loading alone and its interaction with temperature were significant (p < 0.0001 and p = 0.003, respectively); however, the interaction effect of catalyst loading with H2O2 concentration was not significant (p = 0.096). The effect of Nb2O5 catalyst loading was also evaluated for total product concentrations. The combined effects of catalyst loading with H2O2 concentration and temperature on total product concentration were illustrated in Figures 4A,B, respectively. Catalyst loading had a significant (p < 0.0001) effect, but the interaction effect of catalyst loading on H2O2 concentration and temperature were not significant (p = 0.772 and p = 0.393, respectively). Optimal catalyst loading was 4.48%, leading to a maximum predicted product concentration of 1,262.6 mg L−1. Similar trends were reported for degradation of pine wood lignin using vanadium-based polyoxometalate (POM) in presence of an acidic IL, 1-butylimidazolium hydrogen sulfate, and H2O2 (Prado et al., 2016b). Increasing POM loading from 1 to 20% led to increases in vanillin yield from 0.01 to 0.22%, and the authors speculated that with increase in catalyst loading, more active sites became available for breaking down lignin to products. Taking together, results from this study suggest that catalyst loading is catalyst-dependent and critical to both lignin conversion and product yield.
Reaction Temperature
The combined effects of temperature with CoCl2 catalyst loading and H2O2 concentration are illustrated in Figures 3B,C. Both temperature and temperature/catalyst loading interaction had significant (p < 0.0001 and p = 0.003) effects on total product concentration. Product concentration increased with increase in temperature and the highest product concentration was achieved at 120°C. Similarly, the combined effects of temperature with Nb2O5 catalyst loading and H2O2 concentration are shown in Figures 4B,C. Only temperature had significant (p < 0.0001) effect on product concentration whereas its interactions with H2O2 concentration and catalyst loading were not significant. Pokutsa et al. (2009) reported that elevation of temperature from 80 to 120°C improved the conversion of precipitated hardwood lignin from 84.6 to 97.8% using H2O2 in a NaOH medium. In this study, for both catalysts, increasing temperature led to increases in product concentration, probably due to the formation of active hydroxyl and superoxide ions at higher temperatures as a result of hydrogen peroxide disintegration (Rodrigues Pinto et al., 2010).
Characterization of Lignin Streams
FTIR-ATR
The ATR-IR spectra of alkaline lignin and residual lignin (after oxidation) are shown in Figure 5A. All lignin samples showed a wide absorption band at 3,400 cm−1, which is assigned to the O–H stretching vibrations in aromatic and aliphatic O–H groups (Tejado et al., 2007). Bands around 2,930 and 2,840 cm−1 can be assigned to C–H vibrations of CH2 and CH3 groups; while signals between 1,700 and 1,400 cm−1 can be attributed to the aromatic skeletal vibrations (Cachet et al., 2014). The C=C of aromatic skeletal vibrations were reflected by peaks at 1,595 and 1,510 cm−1 (Prado et al., 2016b); these two stretches showed decrease in intensity when compared to unreacted alkaline lignin, indicating the oxidation of lignin at tested conditions. The bands found at 1,460 and 1,420 cm−1 can be assigned to the C–H deformation in CH2 and CH3 groups and C–H aromatic ring vibrations, respectively. Notable decreases in peak intensity at 1,420 cm−1 for both catalysts were observed when compared to unreacted alkaline lignin, indicating possible breakdown of the CH2 and CH3 groups by oxidation. The bands associated with guaiacyl (G) and syringyl (S) units of lignin were detected at 1,220, 1,110, and 1,030 cm−1 (García et al., 2012; Gordobil et al., 2016). The band at 1,220 cm−1 corresponding to C–C, C–O, and C=O stretching (G) showed a decrease in intensity from untreated lignin compared to catalyzed lignin. The band at 1,110 cm−1 corresponding to aromatic C–H in plane deformation (S) also showed decrease in intensity as compared with unreacted alkaline lignin, possibly due to the reduced proportion of S-lignin in the residual lignin. Meanwhile, the band at 1,030 cm−1 assigning to aromatic C–H in plane deformation (G > S) remained constant for all the three peaks. Collectively, these observations supported the general fact that the lignin used in this study is dominated by G-units and indicated possible preferential breakdown of S-lignin as a result of its high chemical reactivity (Shi et al., 2016).
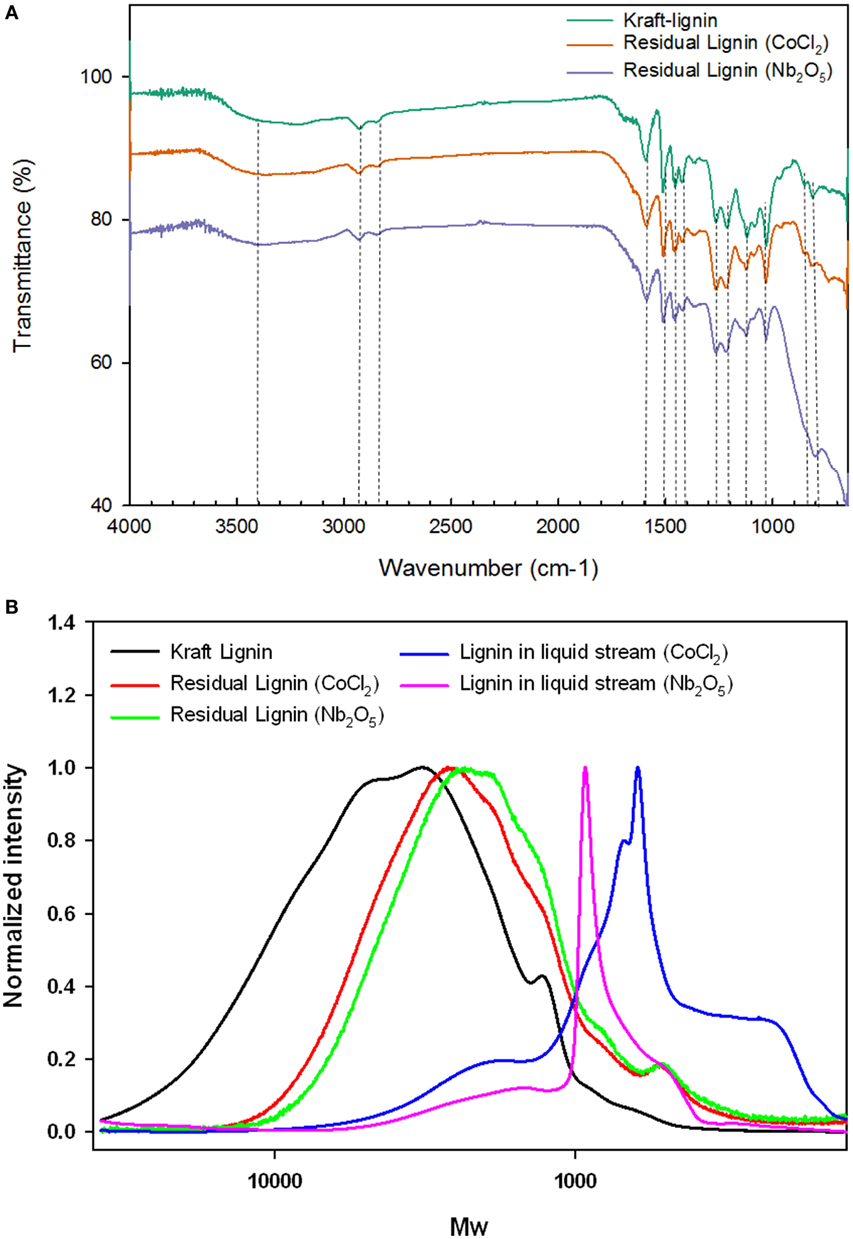
Figure 5. (A) Fourier transform infrared spectra and (B) gel permeation chromatography of lignin streams before and after oxidation.
GPC Analysis
The Mw (weight-average molecular weight) and Mn (number-average molecular weight) of the alkaline lignin and residual lignin after oxidation reaction are shown in Table 3 and the molecular weight distribution (MWD) profiles are depicted in Figure 5B. Comparing the MWD profiles of the unreacted alkaline lignin with residual lignins, the MWD curves of the residual lignins shifted to the right (translating to late elution time and lower Mw as shown in Table 3), indicating lignin depolymerization caused by oxidation. The extent of depolymerization was greater for Nb2O5 catalyst, as indicated by the slightly lower Mw and Mn when compared with that of CoCl2 catalyst. This observation was further supported by the higher products concentration and greater conversion when comparing Nb2O5 catalyst with CoCl2 catalyst. Mw of the lignin in liquid streams for CoCl2 and Nb2O5 catalysts were 1,201.9 and 1,520.2 g mol−1, respectively; both were lower than the corresponding solids residues and untreated lignin. However, the Mn showed to be much lower as compared to solids residues and untreated lignin; this is in accordance to the increased polydispersity index, indicating a wide span of MW after oxidation. Taken together, these results suggest that lignin underwent significant depolymerization during the catalytic oxidation; however, the dissolved and depolymerized lignin might have underwent repolymerization (Li et al., 2007; El Hage et al., 2009; Toledano et al., 2014).
Possible Reaction Sequence
Temperature and catalyst loading were the significant factors for both catalysts. Guaiacol, syringol, vanillin, acetovanillone, and homovanillic acid were the main compounds of the total quantified products (Figure 6). Yields of the total quantified products are detailed in Table S2 in Supplementary Material. Nb2O5 catalyst led to higher yield of products than that of CoCl2 catalyst. Yield (%) with respect to the loaded lignin ranged from 0.26 to 0.99 for Nb2O5 catalyst and from 0.41 to 0.90 for CoCl2 catalyst, respectively, under the tested conditions. The product yields obtained from this study were comparable with results from previous studies using vanadium-based POM in presence of IL 1-butylimidazolium hydrogen sulfate and H2O2 with a product (vanillin, syringaldehyde, and guaiacol) yield of 0.055% (De Gregorio et al., 2016; Prado et al., 2016a). Low product yield in this study may be due to repolymerization of depolymerized lignin and/or over-oxidization products to other intermediates which were not detected in the GC/MS. Based on the insight gained from this study, a few possible approaches to improve product yield could be (a) a better control of the reaction time and temperature of the oxidation reaction; (b) selection of more selective catalysts; and (c) in situ product recovery such as using a biphasic system or via continuous product separation.
Complexity of lignin structure hindered the understanding of the reaction mechanisms of the substrate under catalytic oxidation. Lignin model compounds (monomeric and oligomeric) have been investigated to understand the cleavage mechanism and parameters effecting the depolymerization product and yield (Xu et al., 2014). Depolymerization of organosolv lignin in ILs [C2C1Im][OTf] and [C2C1Im][Cl] under reductive conditions using Lewis and Brønsted acid catalysts showed low conversion despite the high yields obtained on lignin model compounds (Behling et al., 2016). On the other hand, catalytic oxidation of Kraft lignin, soda lignin, Alcell/organosolv lignin in ILs [C2C1Im][DEP], [C2C1Im][MeSO4], [C2C1Im][CF3SO3], and [C2C1Im][EtSO4] involving various metal oxides such as Ni, Co, V, Cu, Fe, and Mn coupled with oxidants such as O2 and H2O2 were effective on lignin conversion, however, did not lead to high product yield (Chatel and Rogers, 2013; Xu et al., 2014). Zakzeski et al. (2010b) studied the oxidation of organosolv lignin and soda lignin with 1-ethyl-3-methylimidazilium diethylphosphate, [C2C1Im][DEP] IL in presence of transition metal catalysts; however, the study failed to detect any monomeric products via GC/MS. In another study, oxidation of lignin model compounds and lignin was investigated using dispersed metal nanoparticle catalyst in [C4C1Im][MeSO4] or [C4C1Im][PF6] (Zhu et al., 2012). It was postulated that there was insufficient disruption of lignin linkages to yield monomeric products or over-oxidation of monomeric product in the latter case.
Oxidation of lignin is a complex process, involving various kinds of reaction pathways. On the basis of previous literature (Zakzeski et al., 2011) and results obtained for the current study, we proposed a plausible reaction sequence for lignin oxidation in aqueous [C2C1Im][OAc]. Anion [OAc] from the IL coordinates to the Co or Nb, forming Co[OAc] or Nb[OAc] species. We hypothesize that at 120°C IL behaves as an alkaline medium and under these conditions hydrogen peroxide dissociates to perhydroxyl anion (HOO–), an extremely strong nucleophile (Xiang and Lee, 2000; Pokutsa et al., 2009). Perhydroxyl anion (HOO–) combines with Co[OAc] or Nb[OAc] species to cleave the aryl ether bonds of the phenolic moieties of the lignin to form lignin monomers (Varanasi et al., 2012).
Conclusion
The alkaline lignin was oxidized to aromatic compounds using transition metal catalysts in presence of H2O2 in an aqueous IL, [C2C1Im][OAc]. Among the seven tested transition metal catalysts, Nb2O5 and CoCl2 proved to be the most effective catalysts. From the batch experiment results, catalyst loading and temperature were significant factors affecting lignin conversion and product yield. The highest product concentrations were obtained using Nb2O5 catalyst with the main lignin depolymerization products identified and quantified in the extracted oil as guaiacol, syringol, vanillin, acetovanillone, and homovanillic acid. For both catalysts, guaiacol was the major compound, and the formation of guaiacol can be attributed to the cleavage of β-aryl ether bond of the alkaline lignin derived from softwood. Molecular weights of the residual lignin (both Mw and Mn) were lower than untreated alkaline lignin indicating depolymerization of lignin to aromatic products via oxidation. Product yield could be further improved by selecting catalyst/IL pairs for better conversion efficacy and selectivity and by applying in situ product recovery to minimize lignin repolymerization or product over-oxidation.
Author Contributions
LD and JS conceptualized the work, designed experiment, analyzed data, and wrote the manuscript. LD and SX conducted the experiment. All authors have approved the manuscript and agreed with submission to Frontiers in Energy Research.
Conflict of Interest Statement
The authors declare that the research was conducted in the absence of any commercial or financial relationships that could be construed as a potential conflict of interest.
Acknowledgments
The information reported in this paper (17-05-073) is part of a project of the Kentucky Agricultural Experiment Station and is published with the approval of the Director.
Funding
This work was supported by the National Science Foundation under Cooperative Agreement No. 1632854 and 1355438 and the National Institute of Food and Agriculture, U.S. Department of Agriculture, Hatch-Multistate project under accession number 1003563.
Supplementary Material
The Supplementary Material for this article can be found online at http://journal.frontiersin.org/article/10.3389/fenrg.2017.00021/full#supplementary-material.
References
Beckham, G. T., Johnson, C. W., Karp, E. M., Salvachúa, D., and Vardon, D. R. (2016). Opportunities and challenges in biological lignin valorization. Curr. Opin. Biotechnol. 42, 40–53. doi: 10.1016/j.copbio.2016.02.030
Behling, R., Valange, S., and Chatel, G. (2016). Heterogeneous catalytic oxidation for lignin valorization into valuable chemicals: what results? What limitations? What trends? Green Chem. 18, 1839–1854. doi:10.1039/C5GC03061G
Brandt, A., Chen, L., van Dongen, B. E., Welton, T., and Hallett, J. P. (2015). Structural changes in lignins isolated using an acidic ionic liquid water mixture. Green Chem. 17, 5019–5034. doi:10.1039/C5GC01314C
Brown, T. R., and Brown, R. C. (2013). A review of cellulosic biofuel commercial-scale projects in the United States. Biofuels Bioprod. Biorefin. 7, 235–245. doi:10.1002/bbb.1387
Cachet, N., Camy, S., Benjelloun-Mlayah, B., Condoret, J.-S., and Delmas, M. (2014). Esterification of organosolv lignin under supercritical conditions. Ind. Crops Prod. 58, 287–297. doi:10.1016/j.indcrop.2014.03.039
Chakar, F. S., and Ragauskas, A. J. (2004). Review of current and future softwood kraft lignin process chemistry. Ind. Crops Prod. 20, 131–141. doi:10.1016/j.indcrop.2004.04.016
Chatel, G., and Rogers, R. D. (2013). Review: oxidation of lignin using ionic liquids – an innovative strategy to produce renewable chemicals. ACS Sustainable Chem. Eng. 2, 322–339. doi:10.1021/sc4004086
Crestini, C., Crucianelli, M., Orlandi, M., and Saladino, R. (2010). Oxidative strategies in lignin chemistry: a new environmental friendly approach for the functionalisation of lignin and lignocellulosic fibers. Catalysis Today 156, 8–22. doi:10.1016/j.cattod.2010.03.057
Das, L., Kolar, P., and Sharma-Shivappa, R. (2012). Heterogeneous catalytic oxidation of lignin into value-added chemicals. Biofuels 3, 155–166. doi:10.4155/bfs.12.5
Datta, S., Holmes, B., Park, J. I., Chen, Z. W., Dibble, D. C., Hadi, M., et al. (2010). Ionic liquid tolerant hyperthermophilic cellulases for biomass pretreatment and hydrolysis. Green Chem. 12, 338–345. doi:10.1039/B916564a
De Gregorio, G. F., Prado, R., Vriamont, C., Erdocia, X., Labidi, J., Hallett, J. P., et al. (2016). Oxidative depolymerization of lignin using a novel polyoxometalate-protic ionic liquid system. ACS Sustainable Chem. Eng. 4, 6031–6036. doi:10.1021/acssuschemeng.6b01339
El Hage, R., Brosse, N., Chrusciel, L., Sanchez, C., Sannigrahi, P., and Ragauskas, A. (2009). Characterization of milled wood lignin and ethanol organosolv lignin from miscanthus. Polym. Degrad. Stab. 94, 1632–1638. doi:10.1016/j.polymdegradstab.2009.07.007
Fielicke, A., Meijer, G., and von Helden, G. (2003). Infrared spectroscopy of niobium oxide cluster cations in a molecular beam: identifying the cluster structures. J. Am. Chem. Soc. 125, 3659–3667. doi:10.1021/ja0288946
García, A., Erdocia, X., Alriols, M. G., and Labidi, J. (2012). Effect of ultrasound treatment on the physicochemical properties of alkaline lignin. Chem. Eng. Process. Process Intensif. 62, 150–158. doi:10.1016/j.cep.2012.07.011
Gladden, J. M., Park, J. I., Bergmann, J., Reyes-Ortiz, V., D’haeseleer, P., Quirino, B. F., et al. (2014). Discovery and characterization of ionic liquid-tolerant thermophilic cellulases from a switchgrass-adapted microbial community. Biotechnol. Biofuels 7, 15. doi:10.1186/1754-6834-7-15
Gordobil, O., Moriana, R., Zhang, L., Labidi, J., and Sevastyanova, O. (2016). Assessment of technical lignins for uses in biofuels and biomaterials: structure-related properties, proximate analysis and chemical modification. Ind. Crops Prod. 83, 155–165. doi:10.1016/j.indcrop.2015.12.048
Kilpeläinen, I., Xie, H., King, A., Granstrom, M., Heikkinen, S., and Argyropoulos, D. S. (2007). Dissolution of wood in ionic liquids. J. Agric. Food Chem. 55, 9142–9148. doi:10.1021/jf071692e
Klein-Marcuschamer, D., Simmons, B. A., and Blanch, H. W. (2011). Techno-economic analysis of a lignocellulosic ethanol biorefinery with ionic liquid pre-treatment. Biofuels Bioprod. Biorefin. 5, 562–569. doi:10.1002/bbb.303
Li, C., Knierim, B., Manisseri, C., Arora, R., Scheller, H. V., Auer, M., et al. (2010). Comparison of dilute acid and ionic liquid pretreatment of switchgrass: biomass recalcitrance, delignification and enzymatic saccharification. Bioresour. Technol. 101, 4900–4906. doi:10.1016/j.biortech.2009.10.066
Li, J., Henriksson, G., and Gellerstedt, G. (2007). Lignin depolymerization/repolymerization and its critical role for delignification of aspen wood by steam explosion. Bioresour. Technol. 98, 3061–3068. doi:10.1016/j.biortech.2006.10.018
Marszałł, M. P., and Kaliszan, R. (2007). Application of ionic liquids in liquid chromatography. Crit. Rev. Anal. Chem. 37, 127–140. doi:10.1080/10408340601107847
Mottiar, Y., Vanholme, R., Boerjan, W., Ralph, J., and Mansfield, S. D. (2016). Designer lignins: harnessing the plasticity of lignification. Curr. Opin. Biotechnol. 37, 190–200. doi:10.1016/j.copbio.2015.10.009
Nakajima, K., Baba, Y., Noma, R., Kitano, M., Kondo, J. N., Hayashi, S., et al. (2011). Nb2O5·nH2O as a heterogeneous catalyst with water-tolerant Lewis acid sites. J. Am. Chem. Soc. 133, 4224–4227. doi:10.1021/ja110482r
Pandey, M. P., and Kim, C. S. (2011). Lignin depolymerization and conversion: a review of thermochemical methods. Chem. Eng. Technol. 34, 29–41. doi:10.1002/ceat.201000270
Park, S., and Kazlauskas, R. J. (2003). Biocatalysis in ionic liquids-advantages beyond green technology. Curr. Opin. Biotechnol. 14, 432–437. doi:10.1016/S0958-1669(03)00100-9
Pokutsa, A., Makitra, R., Maksim, D., and Pal’chikova, E. Y. (2009). Quantitative accounting for the medium effect at the catalytic decomposition of H2O2 in hydrophilic solvents. Russ. J. Gen. Chem. 79, 1425–1429. doi:10.1134/S1070363209070032
Prado, R., Brandt, A., Erdocia, X., Hallet, J., Welton, T., and Labidi, J. (2016a). Lignin oxidation and depolymerisation in ionic liquids. Green Chem. 18, 834–841. doi:10.1039/C5GC01950H
Prado, R., Erdocia, X., De Gregorio, G. F., Labidi, J., and Welton, T. (2016b). Willow lignin oxidation and depolymerization under low cost ionic liquid. ACS Sustain Chem. Eng. 4, 5277–5288.
Pu, Y., Jiang, N., and Ragauskas, A. J. (2007). Ionic liquid as a green solvent for lignin. J. Wood Chem. Technol. 27, 23–33. doi:10.1080/02773810701282330
Ragauskas, A. J., Beckham, G. T., Biddy, M. J., Chandra, R., Chen, F., Davis, M. F., et al. (2014). Lignin valorization: improving lignin processing in the biorefinery. Science 344, 1246843. doi:10.1126/science.1246843
Rodrigues Pinto, P. C., Borges da Silva, E. A., and Rodrigues, A. E. (2010). Insights into oxidative conversion of lignin to high-added-value phenolic aldehydes. Ind. Eng. Chem. Res. 50, 741–748. doi:10.1021/ie102132a
Samuel, R., Pu, Y., Jiang, N., Fu, C., Wang, Z.-Y., and Ragauskas, A. (2014). Structural characterization of lignin in wild-type versus COMT down-regulated switchgrass. Front. Energy Res. 1:14. doi:10.3389/fenrg.2013.00014
Shi, J., Balamurugan, K., Parthasarathi, R., Sathitsuksanoh, N., Zhang, S., Stavila, V., et al. (2014). Understanding the role of water during ionic liquid pretreatment of lignocellulose: co-solvent or anti-solvent? Green Chem. 16, 3830–3840. doi:10.1039/c4gc00373j
Shi, J., Pattathil, S., Parthasarathi, R., Anderson, N. A., Im Kim, J., Venketachalam, S., et al. (2016). Impact of engineered lignin composition on biomass recalcitrance and ionic liquid pretreatment efficiency. Green Chem. 18, 4884–4895. doi:10.1039/C6GC01193D
Sigma-Aldrich. (2016). Certification of Origin. Available at: http://www.sigmaaldrich.com/catalog/CertOfOriginPage.do?symbol=471003&brand=ALDRICH&LotNo=04414PEV&brandTest=ALDRICH
Somerville, C., Youngs, H., Taylor, C., Davis, S. C., and Long, S. P. (2010). Feedstocks for lignocellulosic biofuels. Science 329, 790–792. doi:10.1126/science.1189268
Stärk, K., Taccardi, N., Bösmann, A., and Wasserscheid, P. (2010). Oxidative depolymerization of lignin in ionic liquids. ChemSusChem 3, 719–723. doi:10.1002/cssc.200900242
Tan, S. S., MacFarlane, D. R., Upfal, J., Edye, L. A., Doherty, W. O., Patti, A. F., et al. (2009). Extraction of lignin from lignocellulose at atmospheric pressure using alkylbenzenesulfonate ionic liquid. Green Chem. 11, 339–345. doi:10.1039/b815310h
Tejado, A., Pena, C., Labidi, J., Echeverria, J., and Mondragon, I. (2007). Physico-chemical characterization of lignins from different sources for use in phenol-formaldehyde resin synthesis. Bioresour. Technol. 98, 1655–1663. doi:10.1016/j.biortech.2006.05.042
Tilman, D., Socolow, R., Foley, J. A., Hill, J., Larson, E., Lynd, L., et al. (2009). Beneficial biofuels – the food, energy, and environment trilemma. Science 325, 270–271. doi:10.1126/science.1177970
Toledano, A., Serrano, L., and Labidi, J. (2014). Improving base catalyzed lignin depolymerization by avoiding lignin repolymerization. Fuel 116, 617–624. doi:10.1016/j.fuel.2013.08.071
Varanasi, P., Singh, P., Arora, R., Adams, P. D., Auer, M., Simmons, B. A., et al. (2012). Understanding changes in lignin of Panicum virgatum and Eucalyptus globulus as a function of ionic liquid pretreatment. Bioresour. Technol. 126, 156–161. doi:10.1016/j.biortech.2012.08.070
Varanasi, P., Singh, P., Auer, M., Adams, P. D., Simmons, B. A., and Singh, S. (2013). Survey of renewable chemicals produced from lignocellulosic biomass during ionic liquid pretreatment. Biotechnol. Biofuels 6, 1. doi:10.1186/1754-6834-6-14
Wachs, I. E., Briand, L. E., Jehng, J.-M., Burcham, L., and Gao, X. (2000). Molecular structure and reactivity of the group V metal oxides. Catalysis Today 57, 323–330. doi:10.1016/S0920-5861(99)00343-0
Xiang, Q., and Lee, Y. (2000). Oxidative cracking of precipitated hardwood lignin by hydrogen peroxide. Appl. Biochem. Biotechnol. 84, 153–162. doi:10.1385/ABAB:84-86:1-9:153
Xu, C., Arancon, R. A. D., Labidi, J., and Luque, R. (2014). Lignin depolymerisation strategies: towards valuable chemicals and fuels. Chem. Soc. Rev. 43, 7485–7500. doi:10.1039/c4cs00235k
Zakzeski, J., Bruijnincx, P. C., Jongerius, A. L., and Weckhuysen, B. M. (2010a). The catalytic valorization of lignin for the production of renewable chemicals. Chem. Rev. 110, 3552–3599. doi:10.1021/cr900354u
Zakzeski, J., Jongerius, A. L., and Weckhuysen, B. M. (2010b). Transition metal catalyzed oxidation of Alcell lignin, soda lignin, and lignin model compounds in ionic liquids. Green Chem. 12, 1225–1236. doi:10.1039/c001389g
Zakzeski, J., Bruijnincx, P. C., and Weckhuysen, B. M. (2011). In situ spectroscopic investigation of the cobalt-catalyzed oxidation of lignin model compounds in ionic liquids. Green Chem. 13, 671–680. doi:10.1039/c0gc00437e
Zhang, Z., Song, J., and Han, B. (2016). Catalytic transformation of lignocellulose into chemicals and fuel products in ionic liquids. Chem. Rev. 117, 6834–6880. doi:10.1021/acs.chemrev.6b00457
Zhu, Y., Chuanzhao, L., Sudarmadji, M., Hui Min, N., Biying, A. O., Maguire, J. A., et al. (2012). An efficient and recyclable catalytic system comprising nanopalladium (0) and a pyridinium salt of iron bis (dicarbollide) for oxidation of substituted benzyl alcohol and lignin. ChemistryOpen 1, 67–70. doi:10.1002/open.201100014
Keywords: catalyst, depolymerization, ionic liquids, lignin, oxidation
Citation: Das L, Xu S and Shi J (2017) Catalytic Oxidation and Depolymerization of Lignin in Aqueous Ionic Liquid. Front. Energy Res. 5:21. doi: 10.3389/fenrg.2017.00021
Received: 03 June 2017; Accepted: 17 July 2017;
Published: 10 August 2017
Edited by:
Chang Geun Yoo, Oak Ridge National Laboratory (DOE), United StatesReviewed by:
Xianzhi Meng, University of Tennessee, Knoxville, United StatesMarcus Foston, Washington University in St. Louis, United States
Copyright: © 2017 Das, Xu and Shi. This is an open-access article distributed under the terms of the Creative Commons Attribution License (CC BY). The use, distribution or reproduction in other forums is permitted, provided the original author(s) or licensor are credited and that the original publication in this journal is cited, in accordance with accepted academic practice. No use, distribution or reproduction is permitted which does not comply with these terms.
*Correspondence: Jian Shi, ai5zaGlAdWt5LmVkdQ==