- 1Guangdong Technion Israel Institute of Technology (GTIIT), Shantou, Guangdong, China
- 2Department of Chemistry, Shantou University, Shantou, China
- 3Technion-Israel Institute of Technology (IIT), Haifa, Israel
Heterogeneous catalytic hydrogenation of carbon dioxide (CO2) to methanol is a practical approach to mitigating its greenhouse effect in the environment while generating good economic profits. Though applicable on the industrial scale through the syngas route, the catalyst of Cu/ZnO/Al2O3 suffers from a series of technical problems when converting CO2 to methanol directly, which include low single-pass conversion, low methanol selectivity, requiring high pressure and fast deactivation by the reverse water gas shift reaction. Over the years, intensive research efforts have been devoted to proffering solutions to these problems by modifying the existing catalyst or developing new active catalysts. However, the open question is if this type of widely used industrial catalyst still promising for CO2 methanolizing reaction or not? This paper reviews the history of the methanol production in industry, the impact of CO2 emission on the environment, and analyzes the possibility of the Cu/ZnO-based catalysts for the direct hydrogenation of CO2 to methanol. We not only address the theoretical and technical aspects but also provide insightful views on catalyst development.
Introduction
Carbon dioxide (CO2) is a greenhouse gas emitted into the atmosphere via the combustion of fossil fuels (oil, coal, natural gas) in vehicles and power plants, from many industrial processes, and household operations, etc. (Karl and Trenberth, 2003; Hansen et al., 2006; Lim, 2015). On receiving the CO2 from these sources, the earth heats up, resulting in global warming. A recent report shows that as of 2017, the global average concentration of CO2 in the atmosphere was 405 ppm, and it is expected to reach 410 ppm by 2020, which shows a clear increasing level in the atmosphere. Therefore, it is urgent to develop and establish practical and reliable emission reduction technologies and CO2 control approaches. In recent times, this has been one of the reasons why discussion of CO2 emission reduction tops agenda in most environmental pollution control submits, globally.
The reduction of CO2 to economically relevant products represents an eco-friendly and green route toward value-added CO2 emissions mitigation for environmental sustainability. For example, converting CO2 to liquid fuels and chemicals is essential to cushion the shortage of fossil fuels and to provide cheap availability of chemical feedstock (Kattel et al., 2017a). This kind of conversions can be successfully implemented by heterogeneous catalytic processes using cheaply available hydrogen, e.g., H2 from natural gas and shale gas, or renewable sources of energy (Dang et al., 2018; Ouda et al., 2019). The catalytic reduction of CO2 can produce carbon monoxide (CO), methanol, or hydrocarbons. CO is a feedstock in the Fischer–Tropsch process, while the applications of methanol and hydrocarbon are diversified.
Methanol is an essential industrial commodity chemical, with a global production capacity higher than 100 MTY (Bertau et al., 2014; Jadhav et al., 2014; Wang et al., 2014; Sehested, 2019). In 2018, the demand for methanol was approximately 80–90 million tons and will exceed 110 MTY by 2023. Methanol can be directly used as a clean-burning biodegradable fuel in combustion engines and fuel cells, and can be transformed by various chemical processes into a wide range of useful chemicals (Figure 1). The latter can be subsequently applied to produce a broad range of daily products—fuel additives, resins, plastics, paints, polyester, and building materials (Goeppert et al., 2014; Sehested, 2019). With the increasing use of these products, more methanol is required to meet the large-scale precursor chemical production and other applications. Hence, the catalytic conversion of CO2 to methanol is highly desirable to meet the high demand and to ensure a cleaner environment by reducing the burden of global warming caused by CO2 emission, with associated potential economic benefits.
Generally, conversion to methanol and other value-added products is an effective strategy for CO2 valorization. Some literature reports in the past have reviewed the CO2 reduction with hydrogen over heterogeneous catalysts focusing on the different aspect of the field, including the CO2 reduction to CO, methanol and hydrocarbons, their challenges and prospects (Porosoff et al., 2016; Yang H. et al., 2017; Whang et al., 2019; Zhou et al., 2019). According to the thermodynamics, the most stable reaction path for CO2 hydrogenation yields methane as the product. The pathway to a particular reaction can be selectively controlled by selecting appropriate catalysts and reaction conditions (Porosoff et al., 2016). Owning to a low equilibrium conversion of CO2 to methanol at high temperatures, the development of efficient catalysts to break the thermodynamics barriers is of extreme importance. Thus, a selective catalyst is required to optimize methanol synthesis.
Although new catalysts have been developed in the last five years, the conventional Cu-based catalysts for CO2 hydrogenation to methanol are still extensively investigated for further improvements. Considering the significant progress achieved in this area, we will discuss and focus on the recent advancements in the application of Cu/ZnO-based catalysts for the direct synthesis of methanol from CO2, i.e., using CO2 as the sole feed. We will also retrospect and review the history of the methanol production in industry, the reaction thermodynamics, mechanism, and kinetics, as well as the catalyst structures and suitable conditions for surpassing the equilibrium catalyst activity.
Thermodynamics and Reaction Mechanism
Thermodynamics
In the hydrogenation of CO2 feedstock to a desirable product, the performance of a catalyst will be determined by the thermodynamics of the reaction. Thus, the maximum conversion of CO2 at a given pressure and temperature is defined by the thermodynamic equilibrium conversion under the given reaction conditions (Mutschler et al., 2018). The transformation of CO2 to methanol is an exothermic reaction (Eq. 1), and therefore, favored at low reaction temperature and high pressure. Consequently, elevated pressure and reduced temperature favor an increased methanol yield. However, considering the reaction kinetics and the inert nature of CO2, a high reaction temperature greater than 240°C is often applied (Ma et al., 2009). In addition, this reaction often accompanies the reverse water gas shift (RWGS) reaction, that is endothermically (Eq. 2) favorable at high temperatures and low pressures, generating CO, which lowers the selectivity to methanol, and H2O that deactivates the catalyst. These factors reduce catalyst activity and increase the difficulty in process design (Grabow and Mavrikakis, 2011; Graciani et al., 2014; Hartadi et al., 2015). Thus, the overall process is limited by the thermodynamic equilibrium, and the equilibrium-shift chemistry plays out to control the conversion and selectivity of the products.
Breaking the thermodynamics/kinetics limitation by increasing one-pass CO2 conversion (CO2 conversion at a single step) can tune the selectivity away from CO and toward methanol (Stangeland et al., 2018). One way to actualize this is by applying high pressure. The high-pressure approach using a conventional Cu/ZnO/Al2O3 methanol synthesis catalyst was applied to CO2 hydrogenation to methanol (Figure 2). Under the specified reaction conditions, methanol selectivity, and productivity were remarkably boosted at high pressure by increasing H2 partial pressure to enhance the reaction rate and thermodynamically favor high CO2 conversion and methanol selectivity (Bansode and Urakawa, 2014). As reported by Stangeland et al. (2018), both temperature and pressure have considerable effects on the equilibrium conversion. The methanol synthesis reaction becomes less favored, and the RWGS reaction more favored as the temperature is increased. On the other hand, increasing the pressure strongly enhances the CO2 conversion at low temperatures. Moreover, lowering the concentration of CO2 in the feed stream can increase the CO2 conversion, and this can be achieved by using excess H2 to shift the equilibrium to the products side. Thus, a high H2/CO2 ratio leads to high methanol and low CO selectivity. The selection of the appropriate H2/CO2 ratio, therefore, depends on the requirements of the methanol synthesis system. For example, if high conversions are targeted, it is preferable to work at high H2 concentrations (Stangeland et al., 2018). Irrespective of the pressure, increasing the H2/CO2 ratio will lead to an increase in the CO2 conversion to methanol owing to the sensitivity of H2 partial pressure to the methanol synthesis (Jia et al., 2016; Stangeland et al., 2018). It was demonstrated that product condensation could be utilized to circumvent thermodynamic restrictions on the product yield. Thus, significant improvements in CO2 conversion can be achieved by operating at conditions favorable for product condensation (Stangeland et al., 2018). Also, the thermodynamic limitation can be overcome with reactors, which can recycle the waste CO2 from methanol combustion, and this can increase the conversion to almost 100% (Goeppert et al., 2014; Huš et al., 2017a). Thus, performing multiple separation/recycling loops can produce high conversion under practical temperature and pressure. The use of microstructured catalytic reactors with transverse diameter channels on a millimeter-scale has advantages over larger systems of better heat management, more efficient use of catalysts and controlled operation at high pressure (Renken and Kiwi-Minsker, 2010).
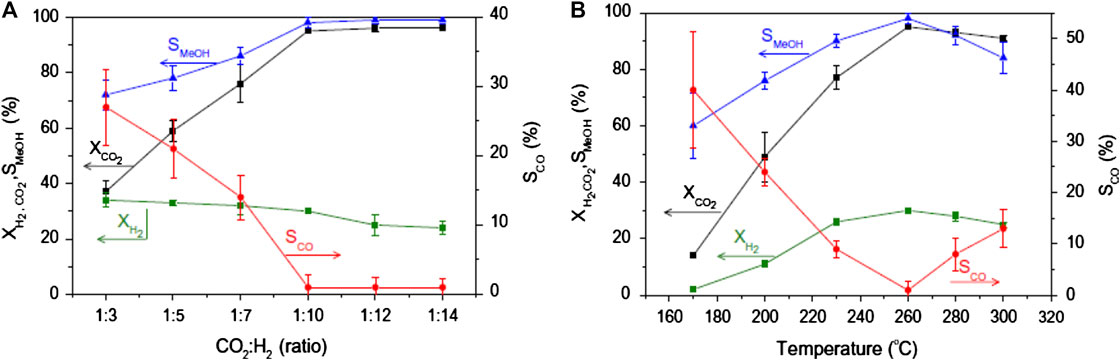
FIGURE 2. Effects of (A) CO2/H2 feed ratio and (B) temperature on conversion of CO2
Reaction Mechanism
Knowledge of the mechanistic details is a decisive catalyst design criterion for CO2 hydrogenation catalysts. Generally, two mechanistic pathways have been proposed from many studies for CO2 hydrogenation to methanol over Cu-based catalysts, as shown in Figure 3 (Kattel et al., 2016; Huš et al., 2017a; Huš et al., 2017b; Yang B. et al., 2017;Karelovic et al., 2019). The first pathway features the CO intermediate, which is produced from RWGS: CO2 + H2 → CO + H2O reaction via carboxyl (*HOCO) species and is further hydrogenated to methanol; the other pathway is associated with the formate (*HCOO) intermediate formed by CO2 hydrogenation which eventually produces methanol via the C–O bond cleavage and *HCO or *H2CO intermediates (Liu and Liu, 2015). According to the density functional theory (DFT) calculations, CO2 hydrogenation prefers the formate pathway on ZnCu(211) via *HCOOH, *H2COOH, and *CH3O intermediates over the RWGS + CO-hydro pathway for methanol synthesis (Kattel et al., 2017b). On the same ZnCu(211) surface, hydrogenation of CO2 can proceed through the Eley–Rideal mechanism, as with pure Cu catalysts, as a result of the unfavorable CO2 binding at the Zn–Cu interfacial site. CO is the main product along the RWGS pathway, and only a relatively small proportion of *HCO could further be hydrogenated to *CH3OH. The direct dissociation of *CO2 to *CO and *O was also evident, and the strong oxygen affinity for Zn sites kinetically favored the formation of *O more than hydrogenation to *HOCO. On unsupported or unalloyed Cu catalysts, *HCOO species act as spectators for methanol synthesis (Yang et al., 2015; Kattel et al., 2017b). The addition of Zn or ZnO stabilized the *HCOOH intermediates via direct Zn–O interaction and by activating *HCOO via hydrogenation. Chances to suppress the undesired CO formation for an increased methanol yield are high, and different strategies can be applied if the two reactions are known to proceed independently via parallel pathways (and on various surface sites). In turn, it will be a hard task to suppress CO formation for a catalyst that produces methanol by a mechanism that shares a common intermediate with CO formation or even uses CO as a reactant (Kunkes et al., 2015). For the industrial Cu/ZnO/Al2O3 catalyst, the Fourier-transform infrared spectroscopy analysis has shown that the hydrogenation of both formate and methoxy species is the rate-determining step in the methanol synthesis over Cu-based catalysts (Ojelade and Zaman, 2019). Formates are the dominant species when CO2 is used as the feed, whereas methoxy species would result in the case with CO as the main reactant.
Theoretical studies deciphered that the WGS reaction followed the carboxyl mediated mechanism, and the methanol synthesis followed both CO and CO2 hydrogenation pathways (Grabow and Mavrikakis, 2011). Under conditions typical of the industrial methanol synthesis, CO2 hydrogenation was responsible for about 65% of the methanol produced from the intermediates *HCOO, *HCOOH, *CH3O2, *CH2O, and *CH3O (Grabow and Mavrikakis, 2011; Kattel et al., 2016). The formation of *HCOO species from *CO2 and *H on Cu(111) involved no intermediate carbonate species and the hydrogenation of *HCOO led to *HCOOH instead of *H2CO2 (Grabow and Mavrikakis, 2011). However, the direct hydrogenation of formate over Cu(111) is not a feasible pathway for methanol production under dry hydrogen conditions (Zhao et al., 2011). Thus, the presence of small amounts of water is essential in methanol synthesis from CO2 hydrogenation on Cu-based catalysts (Yang et al., 2013). It is shown that direct formate hydrogenation does not lead to methanol due to the high hydrogenation barriers of HCOO and H2COO. Formate, formaldehyde, and methoxy radicals are unlikely to be reaction intermediates for methanol synthesis. CO is also hydrogenated in significant amounts to *HCO, *CH2O, *CH3O, and *CH3OH, and plays a promotional role in methanol synthesis, which include two possibilities: a) removal of *OH via *COOH to form CO2 and hydrogen via WGS, and b) assisted hydrogenation of various surface intermediates (Grabow and Mavrikakis, 2011). Route a) also contributes to methanol production, although its effect is minute compared with the direct hydrogenation of CO to methanol. However, the rates of methanol synthesis are limited by the formation of *CH3O at low CO2/(CO + CO2) ratios and by its hydrogenation in CO2-rich feeds. Thus, the *CH3O hydrogenation is a slow step during methanol synthesis from both the CO and CO2 routes. Factors such as their rate-determining steps, feed composition, and reaction conditions influence the relative contribution of each route (Grabow and Mavrikakis, 2011).
Methanol Synthesis Catalysts
Historical Development of the Industrial Catalysts for CO2 Conversion to Methanol
The use of Cu-based catalysts for methanol synthesis via the CO2 dehydrogenation route is as old as the process itself. In 1921, the first patent for methanol synthesis on Cu-based catalyst was filed by Patart (1922), but the catalyst failed to get attention for commercial use due to its susceptibility to sulfur poisoning. The Imperial Chemical Industries developed the Cu/ZnO catalyst in the late 1960s, which was operative at pressure and temperature of 50–100 bar and 200–300°C, respectively, and using syngas (CO + H2) as feedstock (Din et al., 2019). Following the successful industrialization of the process and development of gas purification system, which freed the syngas produced from coal, natural gas and crude oil from poisoning by sulfur (Supp, 1973), interest in Cu-based catalysts revived with a ternary Cu-based catalyst—copper oxide, zinc oxide, and chromium oxide (synthesized by in situ reductions) (Davies and Snowdon, 1967). Subsequent studies found that replacing chromium oxide with alumina prolonged the catalyst life. The copper–zinc–alumina catalysts were prepared by co-precipitation of soluble zinc and copper salts (usually the nitrates) with an alkali carbonate solution. The resulting mixture of carbonates was heated to form a mixture of oxides, which were then mixed with aluminum oxide (Casey and Chapman, 1974).
To improve the activity, selectivity, thermal stability, and resistance to poisoning, the Raney copper catalysts consisting of 50% aluminum and 50% copper–zinc mixture by precipitation with NaOH (Marsden et al., 1980). These catalysts were active for methanol production comparable to that of the commercial copper-based methanol synthesis catalyst, but selective to small amounts of dimethyl ether (DME) by-product.
As early as 1930, the possibility of synthesizing methanol from CO2 as the sole feedstock was known. As then known, methanol catalysts produced CO2 or H2O or both along with methanol. It was proposed that the formation of methanol from CO and hydrogen may not be direct, especially when approaching a steady state. Smith and Hirst (1930) observed that hydrogen and CO2 formed CO and H2O over methanol catalysts at atmospheric pressure. In the like manner, CO and H2O react over the Cu-based catalysts to form CO2 and hydrogen, and equilibrium could be closely approached in the water-gas shift reaction. In 1932, the reaction was confirmed in addition to the regular methanol formation over the unsupported zinc–copper–aluminum catalyst under a certain pressure at high temperatures (Boomer and Morris, 1932). Although the catalyst was not particularly active, it indicated the course of the reaction. In 1945, it was found that methanol from CO2 could be produced over copper–alumina catalysts in the temperature range of 282–487°C and the pressure range of 117–410 atm. Catalysts consisting of Cu or Al2O3 alone had no catalytic activity. The most active catalyst had a Cu content of 8–25% and gave a conversion of 94% under 410 atm at a temperature of 285°C. With CO as the carbon source, similar experiments gave 39–43% conversions, with about 15 and 41% of the CO charge converted to methane and DME, respectively (Ipatieff and Monroe, 1945). In the reaction gas mixture (CO/CO2/H2) with CO:CO2 of 3.1:1, the methanol conversion was 64%, and the formation of DME reduced to about 1%. The results led to the postulation that the formation of methanol from CO2 and hydrogen under pressure may proceed along two paths. The developmental milestone of the Cu-based catalysts for the direct CO2 to methanol conversion is presented in Figure 4. Ren et al. provided the evidence than Cu species promoted by Zn were essential for the hydrogenation of CO2 in the CO2 promoted CO–H2 gas system. They observed that CO2 inhibited the CO hydrogenation over Pd/Al2O3, and ZnO–Cr2O3 catalysts, but promoted it over Cu–ZnO/A12O3, at their respective optimum temperatures and under pressures that ensured low conversions (Ren et al., 1989).
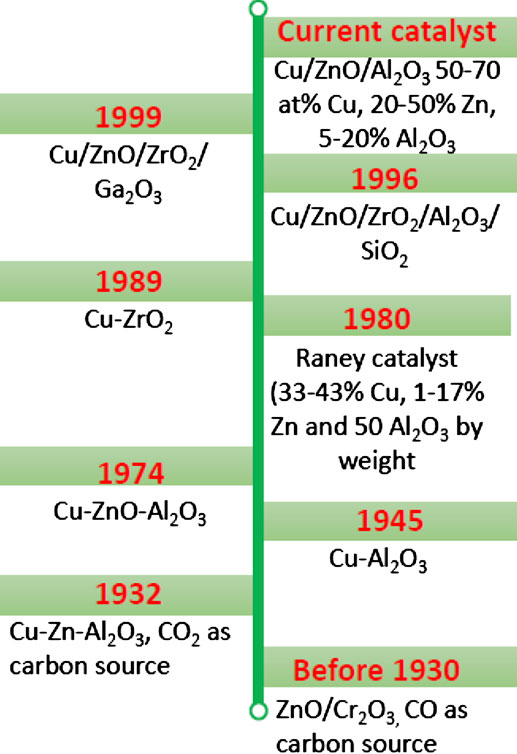
FIGURE 4. Evolution of Cu-based catalysts for conversion of CO2 to methanol (CO2 as the sole carbon source).
Intensive research on the methanol synthesis from CO2 and the active catalysts started growing in the 1980s. Currently, the ternary copper-based catalyst (Cu/ZnO/A12O3) is still used for the industrial synthesis of methanol from CO2 in the gas phase from a mixture of syngas and CO2 under the operations conditions: temperature and pressure of 220–300°C and 50–100 bar, respectively (Din et al., 2019; Sehested, 2019). In this process, methanol formation is believed to originate mainly from CO2, whereas CO acts as a scavenger of surface oxygen. Due to the availability of CO2 in large volumes from emissions into the atmosphere and the need for environmental cleaning to reduce the incidence of global warming and demand for clean fuel, research efforts are devoted to the use of CO2 as the sole reactant gas which is challenged by the unavailability of efficient catalysts (Din et al., 2019).
The Present Commercial Catalyst (Cu–Zn–Al)
At the commercial scale, methanol is synthesized over Cu/ZnO/Al2O3 catalyst at a pressure of 50–100 bar and temperature of 220–300°C. This catalyst contains 50–70 atomic% CuO, 20–50% ZnO, and 5–20% of the Al2O3 promoter. These combinations allow the formation of stabilized Zn-incorporated Cu surfaces, which are highly defective, and enable the maximization or optimization of the density of the active sites. The resulting oxide catalyst is activated with diluted hydrogen at 190–250°C, at which CuO is completely reduced to metallic crystallites interspersed by ZnO/Al2O3 (Behrens et al., 2013). It should be noted that the commercial Cu/ZnO/Al2O3 catalysts for methanol synthesis are not a “supported system” although researchers often mistake it as one because neither ZnO nor Al2O3 component is classical porous oxide support to qualify it as such, and the active phase has a high loading in the system (Behrens et al., 2013). The Cu-rich composition of the industrial catalyst possesses a peculiar microstructure, which is composed of spherical copper nanoparticles of sizes 5–15 nm and even smaller ZnO nanoparticles arranged in a regular pattern (Lunkenbein et al., 2015). In the catalyst, ZnO affords typical promoting functions, partakes in active sites creation, and supports and stabilizes the mesostructure of the Cu phase. In the Cu/ZnO/Al2O3 catalyst, there is a strong metal–support interaction layer of metastable “graphitic-like” ZnO after reductive activation, which was kinetically stabilized by interacting with the defective and Cu surface (Lunkenbein et al., 2015). The defects are crucial for the stability of the ZnO overlayer and may lead to the presence of some ZnOx species that act as co-catalysts in the methanol synthesis. The overlayer growth protects the Cu from particle size growth and reshaping. ZnO can also act as a spacer, avoiding the direct contact of the Cu particles with the Al2O3, enabling dispersion of the Cu particles and preventing them from sintering (Kasatkin et al., 2007). The Al2O3 component, although it can interact with the ZnO phase, does not generally change the evolution of the Cu/ZnO binary phase. It helps to modify the ZnO surface, introducing defective sites by doping (Schumann et al., 2014; Mota et al., 2018). Al2O3 incorporation into the catalyst is necessary to enhance catalyst stability and resistance to thermal sintering of the Cu crystallites. In addition, studies suggest that alumina also acts as a promoter, though there is evidence of Al3+ doping into ZnO, which specifically tailors the reduction properties of the latter. Also, Al2O3 surface acidity affects the byproducts’ selectivity (Xiao K. et al., 2017). Table 1 summaries the performance of the Cu/ZnO/Al2O3 catalysts investigated in recent years.
The catalyst must fulfill three important technical requirements (Figure 5) for high catalytic activity, which can be ensured by the nanoparticulate and porous Cu/ZnO aggregates (Zander et al., 2013). Different methods have been investigated for the preparation of the commercial catalysts by researchers, including solid-state combustion, solid-state reaction, reduction–precipitation, reversed co-precipitation and deposition precipitation (Natesakhawat et al., 2012; Dong et al., 2016; Dasireddy and Likozar, 2019); however, desirable properties for the industrial applications are more often achieved by the co-precipitation method. Initially developed by the Imperial Chemical Industries in the 1960s, the method involves co-precipitation, aging of the mixed metal Cu, Zn, and (Al) hydroxyl-carbonate precursor materials, thermal decomposition and finally activation by reduction of Cu component to active species as shown in Figure 6 (Waller et al., 1989; Fierro et al., 1996; Spencer, 1999; Whittle et al., 2002; Kniep et al., 2004; Behrens et al., 2011). During the synthesis, the initially formed solids from co-precipitation of Cu, Zn and Al precursors are amorphous hydroxycarbonates, which evolve during aging in contact with the mother liquor to crystalline forms with different composition, morphology, and structure as a result of Ostwald ripening dissolution/re-precipitation or agglomeration (Mota et al., 2018). Aging can increase the exposed Cu surface area, ZnO crystallite size, the stability of ZnO, and the Cu–ZnO contacts due to the change in the structure of precipitates with a strong influence on the microstructure of the final Cu/ZnO–Al catalysts (Mota et al., 2018). Calcination influences the precursor decomposition and the CuO structure of the catalyst (Zhang et al., 2010). The average CuO crystallite size increases with an increase in calcination temperature, whereas the dispersion of Cu species decreases under the same condition (Guo et al., 2011). Usually, the calcination temperatures of 300–400°C are optimum for forming a suitable catalyst. The detailed description of the synthesis of this catalyst can be found in the literature (Behrens and Schlögl, 2013).
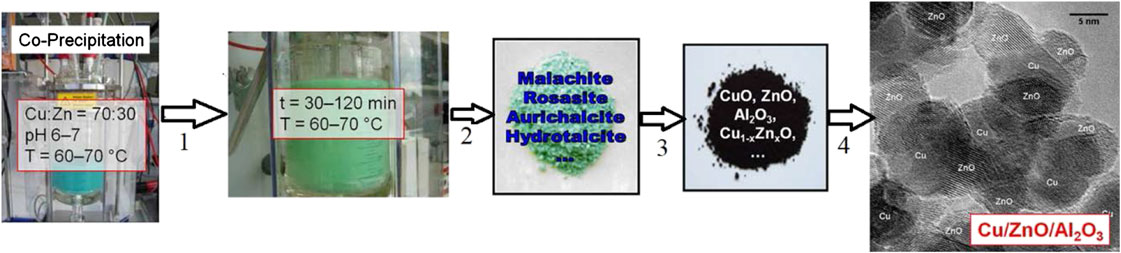
FIGURE 6. Major steps in co-precipitation synthesis of Cu–ZnO–Al2O3 catalyst developed by ICI. Stages 1–4 refer to aging, washing/drying, calcination and reduction, respectively (Behrens and Schlögl, 2013). Reproduced with permission from John Wiley and Sons.
The Cu–ZnO–Al2O3 catalyst system has been optimized to a very high-performance level under relevant industrial conditions. Thus, one may rationally assume that the catalyst is highly active for the direct CO2 hydrogenation to methanol. Although Cu/ZnO/Al2O3 exhibits promising performance (space-time yield up to 7,729 gMeOH kgcat−1 h−1) under 36 MPa and 10:1 H2:CO2 ratio (Bansode and Urakawa, 2014), obviously this pressure is too high from an economic point of view.
Active Sites
Theoretical Modeling of the Cu–ZnO Catalyst Surface
The multiscale modeling techniques adopted for investigating the performance of the traditional Cu-based catalysts include the DFT, kinetic Monte Carlo (kMC), and microkinetic modeling (Li et al., 2015; Huš et al., 2017b;Kopač et al., 2017; Kopač et al., 2019; Park et al., 2020). These models allow for the clarification of the exact reaction pathway, including energetics and kinetics of every reaction step, and help the analysis of catalyst performance over a range of operating conditions and different length and time scales (Park et al., 2020). The DFT can compute ground-state energy and its associated properties using electron density, allowing for the calculation of relatively larger systems such as nanoparticles and periodic surfaces. The atomic configurations, transition states, energetics, energy barriers, and reaction mechanisms derived from first-principles calculations can be used to predict the catalytic activities at an atomic level. The kMC showed how the catalytic surface coverages change with time and conditions on a microscopic scale, and resolve the surface coverage with atomistic detail (Pavlišič et al., 2020). Microkinetic modeling is an important continuum model with even higher accuracy and reliability than DFT and kMC. It is an ideal framework for integrating the data generated by latter. Like the kMC, it avails information on product distribution and estimates the catalyst activity in steady-state kinetics (Li et al., 2015). In many cases, the catalytic performance data form Cu-based catalysts compared qualitatively with those obtained from the experiments in the literature. For example, the results from these theoretical modellings were found to conform well to the experiments over Cu–ZnO–Al2O3 or Cu–MgO–Al2O3. The active sites of the catalysts Cu–ZnO or Cu–MgO were modeled by the DFT. Cu sites were modeled as a Cu(111) surface on top of which ZnO or MgO cluster was placed in the most energetically favorable position. The methanol synthesis was investigated under different temperatures and pressures. Both the microkinetic and kMC modeling indicated high selectivities toward methanol at low temperatures (between 95 and 100%). Cu/Mg and Cu/Zn had different reaction pathways toward methanol production, which depended on the operating conditions and the formate pathway was the energetically most favorable over the Cu/Zn surface.
The DFT calculation found that, on a commercial Cu/ZnO/Al2O3 catalyst, the open Cu surfaces [e.g., Cu(110) and Cu(100)] partially covered by oxygen are active for methanol synthesis, suggesting that Cu species without the effect of support are the active sites for methanol synthesis (Grabow and Mavrikakis, 2011). Different surfaces and the presence or absence of surface defects have shown the ability to catalyze the methanol synthesis. The stepped Cu(533) surface was shown to enhance the selectivity for methanol about four orders of magnitude better than a flat Cu(111) surface (Kopač et al., 2019). The defective surface relative to the Cu(111) surface promoted the H2COH hydrogenation pathway, resulting in higher CH3OH yields. Over (ZrO2)3/Cu(110) interface, the adsorption energies of unsaturated species were observed to increase compared to a pure Cu(110) surface. A similar observation was recorded for the selectivity for methanol (Liu et al., 2020). A comparison between the pure Cu(211) and the Zn-doped Cu(ZnCu(211)) surfaces showed differences in the reaction steps (Zheng et al., 2020). For the ZnCu(211) surface, the methanol formation pathway included the formation of CH3O instead of CH2OH species. The rate-limiting step over Cu(211) was the reaction, CO2 + H → HCOO, whereas that over ZnCu(211) was HCOOH + H → H2COOH, which has been known as the main intermediate for the methanol synthesis over Cu/ZnO catalysts. The kinetics further deviated on Zn-promoted Cu due to the reduced activation energies of several critical reactions, leading to the improved catalytic performance of ZnCu(211).
The simple pure-copper kinetic model can sufficiently describe the catalysts with different supports after modifying the model active site concentrations (Jurković et al., 2020). Such a method can be useful for predicting the activity of the Cu/Al2O3 catalyst and for further reactor designs modeling and scale-up applications. Applying these could guide the rational design of multifaceted Cu catalysts for methanol synthesis by surface defects engineering.
Experimentally Observed Active Sites
Studies have discussed the identity of the catalysts’ active sites, with particular regard to the intermediates and precursors for methanol formation. The reported kind and nature of the active sites are closely linked with the synthesis method and/or the analytical techniques deployed for studying it (Herman et al., 1979). For the Cu-based catalysts, the active sites are considered to be metallic Cu (Cu0) or Cu+, and the activity was shown to be directly related to the Cu surface area (Baltes et al., 2008; Dong et al., 2016; Dasireddy and Likozar, 2019). However, other studies found that the catalytic activity was not certainly correlated linearly with the Cu surface area (Nakamura et al., 2003). The active sites and the activity relations of a reversed co-precipitated prepared Cu-based catalysts were investigated by various characterization techniques (Natesakhawat et al., 2012). The results revealed the presence of metallic Cu on the surface of fresh but reduced and spent catalysts. CuO in the catalyst reduced to Cu0 upon exposure to H2 at 250°C. This state was observed in various kinds of Cu-containing catalysts with different supports/additives, size of Cu particle, and varying degrees of ZnO crystallinity, thus it can be concluded from this study that additives, particles and support crystallite size do not affect the activity of Cu (Natesakhawat et al., 2012).
Tsang and co-workers observed the formation of CuZn alloy particles by X-ray photoelectron spectroscopy (XPS) in the Ga-promoted Cu/ZnO catalyst for CO2 hydrogenation to MeOH. They attributed the effect of incorporation of Ga3+ to the formation of the ZnGa2O4 spinel structure, which created electronic heterojunction with excess ZnO phase that eased the reduction of Zn2+ to Zn0 to form CuZn alloy upon contact with Cu nanoparticle. They also correlated the concentration of Zn0 in the CuZn alloy nanoparticle with the catalytic performance (CO2 conversion and methanol selectivity) and found that the latter could be significantly improved by increasing the Zn0 content in the heterojunction catalysts (Li et al., 2016). With advanced characterization techniques, it is evident that Zn atoms can be reduced on Cu nanoparticles, resulting in a detectable change in the geometry and electronic structure of Cu due to Zn–Cu bimetallic properties (Sanches et al., 2012). As a result, it is concluded that the Zn–Cu alloy is an active catalytic site. On the contrary, other studies found that reactions occur at the atomic interface between ZnO and Cu. Thus, the presence of the ZnO–Cu interface and the synergy of Cu and ZnO are essential for the production of methanol (Li et al., 2018).
The active site of Cu catalysts can also exist in the form of other species. Recent studies have shown that stepped and ZnOx-decorated Cu surfaces are active sites of the industrial catalysts (Studt et al., 2015). Both experimental and theoretical investigations have found that decorated Cu stabilized by bulk defects and surface species participate in the hydrogenation of CO2 to methanol reaction (Behrens et al., 2012). The transmission electron microscopy study revealed the ZnO overlayer was formed on top of the Cu particles in the Cu/ZnO/Al2O3 catalyst under reaction conditions that could create a metal oxide interface with catalytic activity (Figure 7). Evidence is also available for the existence of the Zn–Cu bimetallic sites or ZnO–Cu interfacial sites (Kattel et al., 2017b). Over the ZnCu bimetallic and ZnO/Cu model catalysts for methanol synthesis, it was found that ZnCu surface oxidized in situ such that the surface Zn transforms into ZnO, allowing ZnCu to form ZnO/Cu active surface in a synergistic interaction of Cu and ZnO. Cu–Zn alloy or the Cu/ZnO interface has been proposed to generate the active site responsible for the high methanol selectivity. Generally, as summarized in this section, the active sites for the Cu–ZnO catalysts can be grouped into the following categories: a) Cu species (metallic or oxidized Cu species); b) Cu–ZnO interface; c) defective Cu surface; d) Cu–Zn alloy; and e) ZnO decorated Cu. All these have led to the conclusion that the Cu species and/or Cu–Zn contact is necessary for the activity of the Cu/ZnO-based catalysts.
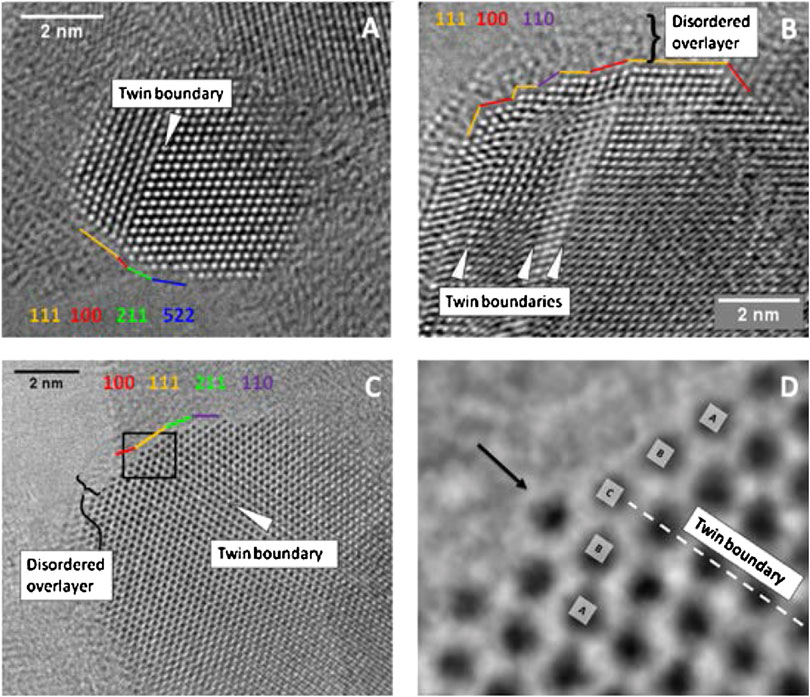
FIGURE 7. (A-C) Aberration-corrected HRTEM images of Cu particles in the commercially active Cu/ZnO/Al2O3 catalyst. (D) is a zoom-in of the marked area in (C) (Behrens et al., 2012). Reproduced with permission from American Association for the Advancement of Science.
Deactivation of Methanol Synthesis Catalysts
The deactivation of heterogeneous catalysts is a severe problem in many reactions. Many studies have reported various deactivation mechanisms of the Cu-based catalyst in the literature; however, the mechanism of deactivation is not entirely clear. One of the major causes of catalysts deactivation is sintering. The sintering of catalytic materials particles results in a decrease in catalyst activity. Catalyst particles sinter in the early stages by a coalescence mechanism, which involves the migration and coalescence of particles, while the Ostwald ripening mechanism is operative in the end phase of the process (Bartholomew, 2001). The Ostwald ripening is caused by the surface diffusion of catalytic material and the higher thermodynamic stability of larger particles (Fichtl et al., 2015). The initial and rapid deactivation is due to loss of surface area when some of the finely dispersed Cu crystallites agglomerate (Roberts et al., 1993; Twigg and Spencer, 2001). The later pathway, which is slow and approaches the steady-state, is caused by the surface coverage of some reaction products and intermediates, especially water, and carbonated species (Roberts et al., 1993). It was found that the cause of catalyst deactivation was sintering of both Al2O3 and Cu with water due to the decreasing Al2O3 surface, and Cu particle size with increasing content of H2O (Prašnikar et al., 2019).
Figure 8A shows that all phases exhibit a reduction in surface area (or increase of particle size) with an increasing amount of steam. The Cu particle growth was fitted to a coalescence model for sintering (Figure 8B), which confirms coalescence as the operating mechanism. The increased particle migration is due to weak contact between the metal and support or increased surface diffusion of catalytic material (Prašnikar et al., 2019). The structures of ZnO and Al2O3 species and metallic Cu can be stabilized to improve the catalyst lifetime, which can be accomplished by forming stable Cu interface with support material, and by stabilizing the dynamic nature of ZnO under working conditions using hydrophobic or hydrothermally stable materials. A promising approach is to confine the growth of Cu species in a porous oxide to stabilize and maximize Cu–support interface (Chen et al., 2019).
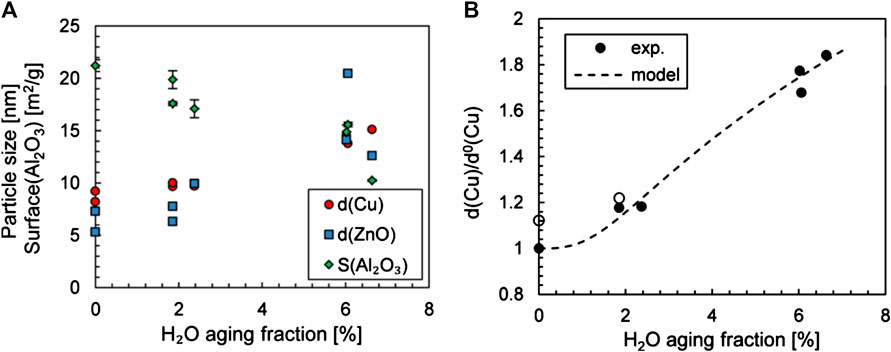
FIGURE 8. (A) H2O impact on the Cu and ZnO particle size and on the Al2O3 surface. (B) Growth factor for Cu(dCu/dCu0) depending on the molar fraction of the water and model results for 48 h (Prašnikar et al., 2019). Reproduced with permission from American Chemical Society.
The water generated in the RWGS during CO2 reduction to methanol deactivates the catalyst, causing speciation of Cu active phase and phase separation (Kung, 1992; Liang et al., 2019; Prašnikar et al., 2019). Sahibzada et al. observed a lower rate of methanol production in the presence of water in the H2/CO2 feed (Sahibzada et al., 1998). Another possible effect of water in the deactivation of the methanol synthesis catalyst is the crystallization of ZnO and Cu particles (Lunkenbein et al., 2016). Water produced can speed up the crystallization of particles, leading to deactivation observed for the Cu/ZnO/ZrO2/Al2O3 catalyst. The inhibiting effect of water during CO2 reduction to methanol was caused by the adsorption on and blocking of the active sites for CO2 hydrogenation (Liu et al., 1985). Water reacts with CO2, forming carbonate species that have been proven to block the active sites for CO2 hydrogenation. The deactivation of Cu-based catalysts by water could also result from blocking of hydrogen adsorption sites, morphology changes of Cu, and the oxidation of the active Cu-phase (Clausen et al., 1994; Omata et al., 2004). These can be explained by recrystallization and an enhanced tendency for sintering of the Cu particles in the presence of water (Wu et al., 2001); however, this mechanism is not always true as no deactivation was observed by Omata et al. (2004) in their study in the presence of water.
Improvements to the Conventional Cu–ZnO–Al2O3 Catalyst
Use of Promoters
To further increase the activity and stability of the Cu–ZnO or Cu–ZnO–Al2O3 catalysts, modifiers such as K, Ba Zr, Ce, Mn, La, Si, Pd, Ga, Mg, and Y were incorporated to promote the catalytic performance (Iizuka et al., 1983; Inoue and Iizuka, 1986; Denize et al., 1989; Toyir et al., 2009; Sanches et al., 2012; Zhang L. et al., 2012; Gao et al., 2013; Zhan et al., 2014; Gao et al., 2015; Zohour et al., 2016; Larmier et al., 2017; Xiao S. et al., 2017;Zhang F. et al., 2017; Hu et al., 2018). An effective promoter should be able to achieve large Cu surface area, high Cu dispersion, and to ease the reducibility of CuO to metallic Cu (Sanches et al., 2012). Modification to the basicity, methanol selectivity, CO2 conversion, and temperature and pressure have been reportedly observed (Gao et al., 2013). A series of Cu/Zn/Al catalysts promoted with Mn, La, Ce, Zr, and Y were synthesized by the co-precipitation method and tested for the CO2 hydrogenation to methanol, and effect of the promoters on the physicochemical properties of the base catalysts was investigated (Gao et al., 2013). The results showed that the specific surface area, Cu surface area, Cu dispersion and number of basic sites increase in the order: Cu/Zn/Al < Cu/Zn/Al/Mn < Cu/Zn/Al/La Cu/Zn/Al/Ce < Cu/Zn/Al/Zr < Cu/Zn/Al/Y, whereas the CH3OH selectivity increases in the order of Cu/Zn/Al < Cu/Zn/Al/Mn < Cu/Zn/Al/La < Cu/Zn/Al/Ce < Cu/Zn/Al/Y < Cu/Zn/Al/Zr. The Zr-modified Cu/Zn/Al catalyst exhibited the highest density and proportion of strong basic sites. The addition of Mn, La, Ce, Zr, and Y enhanced the production of methanol; however, the Y- and Zr-modified Cu/Zn/Al catalysts exhibited the highest CO2 conversion and methanol selectivity, respectively (Gao et al., 2013).
Lee et al. (2020) investigated the effect of adding Zr, Mg, and Ga on the conventional Cu/ZnO/Al2O3. The incorporation of Zr enhanced the performance for methanol synthesis by improving conversion and methanol yield, but the occurrence of intensified WGS reaction reduced CO2 conversion. On the other hand, the addition of Ga and Mg further lowered catalytic performance (Table 2), attributed to reducibility difficulties and the increased crystalline size of Cu particles (Xiao et al., 2015). These catalysts were evaluated using a feed composed of both CO and CO2.
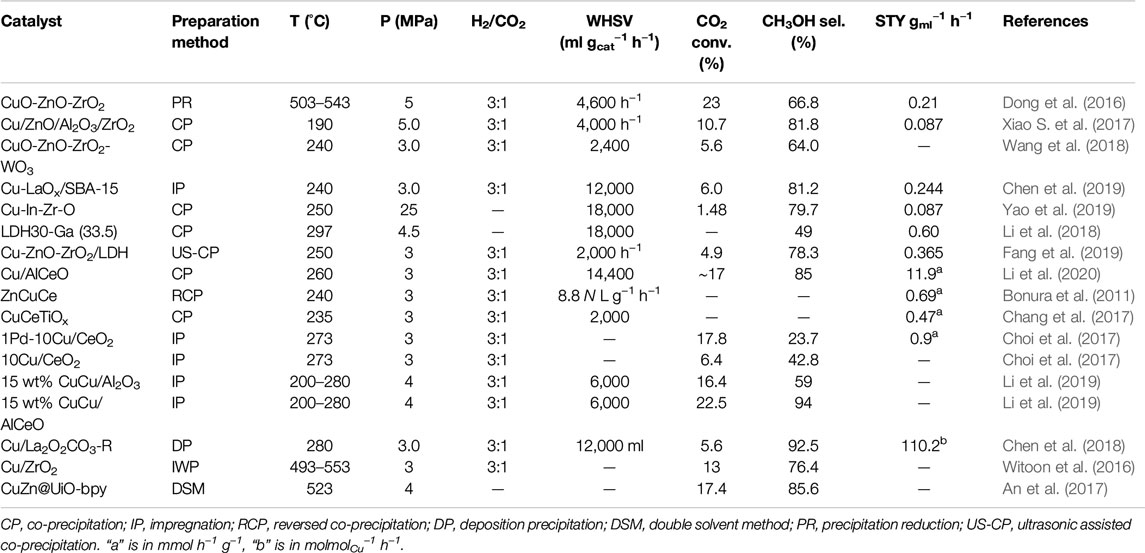
TABLE 3. Catalytic activities of recently studied Cu-catalysts for methanol synthesis from CO2 hydrogenation in fixed bed reactors.
The CuO–ZnO–Al2 catalysts modified with SiO2, TiO2, or SiO2–TiO2 exhibited better catalytic performances than the CuO–ZnO–Al2O3 without any promoter. The conversion of CO2 and methanol yield increased when the promoters were added, and the maximum of CO2 conversion and methanol yield were obtained over 2 wt% SiO2–TiO2/CuO–ZnO–Al2O3 catalyst (Zhang et al., 2012). Both SiO2 and TiO2 eased the reduction and dispersion of CuO, while SiO2–TiO2 made the reduction of CuO slightly difficult. SiO2–TiO2 had the best performance than SiO2 or TiO2 as a result of synergistic interaction between SiO2 and TiO2, leading to a weaker acid strength and a higher acid concentration on the surface of the catalyst. This resulted in weaker adsorption of CO2 but stronger adsorption of H2 and the dissociated H species (Zhang et al., 2012). The catalytic results revealed higher performance for the promoted CuO–ZnO–Al2O3 catalysts. Maximum activity and methanol selectivity were obtained for the catalyst promoted with SiO2–TiO2, giving CO2 conversion of 40.70% and methanol selectivity of 41.17% compared with the catalyst without a promoter (CO2 conversion of 15.81% and methanol selectivity of 23.31%) under similar reaction conditions of temperature = 533 K, pressure = 2.6°MPa, H2:CO2 = 3:1, and space velocity = 3,600 h−1. The introduction of non-metallic ions (e.g., fluoride ion) can drastically promote the basicity of Cu/ZnO/Al2O3 and the adsorption of CO2 and increases the methanol selectivity (Dybbert et al., 2019).
Although the CuO–ZnO–ZrO2 ternary catalysts have exhibited comparative activity with the commercial catalyst, the introduction of promoters such as SiO2, CeO2, Ga2O3, TiO2 can further improve the catalytic performance (Zhang et al., 2012; Larmier et al., 2017; Phongamwong et al., 2017; Hu et al., 2018). A series of CuO–ZnO–ZrO2–SiO2 catalysts were synthesized by the reverse co-precipitation of copper, zinc and zirconium precursors with colloidal silica nanoparticles, and the influence of silica content (0–5 wt%) on the properties of the resulting catalysts as well as their catalytic activity in CO2 hydrogenation were studied. Analysis with various characterization techniques revealed modification of the catalyst structures. A low content of SiO2 was more effective for modifying the geometric structure. The addition of 1 wt% SiO2 led to an increase in methanol synthesis activity (26%) compared to the SiO2-free catalyst system. Phongamwong et al. (2017) concluded that the addition of SiO2 to Cu/ZnO/ZrO2 improves methanol synthesis activity by increasing metallic Cu surface area and surface basicity. Słoczyński et al. (2006) observed an increase in the yield of methanol upon modification of Cu/ZnO/ZrO2 catalyst with B, Ga, In, Gd, Y, Mn, and Mg oxides. The addition of these elements also altered the textural and/or structural properties of the catalyst; Ga2O3 has been particularly useful in promoting methanol yield. Saito et al. (1996) developed a Cu/ZnO/ZrO2/Al2O3/SiO2 catalyst used for methanol synthesis operation in the bench plant. The catalyst was very stable during long-term methanol synthesis (Saito et al., 1996; Toyir et al., 2009). The methanol production capacity of 50 kg d−1 of methanol over Cu/ZnO/ZrO2/Al2O3/SiO2 was also successfully operated (Ushikoshi et al., 1998; Toyir et al., 2001; Toyir et al., 2009).
Improvements in Catalyst Synthesis
A unique microstructure with a proper balance of Cu dispersion and exposure of active Cu–ZnO interface sites at a high total Cu content is essential for achieving methanol selectivity (Behrens and Schlögl, 2013). Thus, the synthesis method that guarantees the structure sensitivity of methanol synthesis over Cu surfaces is appropriate. Varying the specific activity of the active sites and/or the concentration of the sites can be a result of the deployed synthesis method (Table 3). The ternary Cu-based catalysts are prepared by co-precipitation from a mixture of copper, zinc, and aluminum nitrate using a carbonate as a precipitant (Behrens and Schlögl, 2013; Behrens, 2015).
The co-precipitation involves the simultaneous solubilization and solidification of copper and zinc precursors (usually nitrate salts) in the presence of alkaline metal carbonates, forming binary precipitates under suitable conditions (Casey and Chapman, 1974; Kasatkin et al., 2007). The precipitate is aged, dried, and calcined in air to obtain the CuO/ZnO oxides. Finally, the catalyst is reduced under H2 atmosphere during which CuO is reduced to metallic Cu. This method affords the study of hydrolysis of Cu2+ and Zn2+ at different pH relevant to the catalyst preparation. Over the years, many researchers have investigated the synthesis parameters of the co-precipitation route, and have achieved a high degree of optimization, usually by empirically adjusting the synthesis conditions (Li and Inui, 1996; Baltes et al., 2008; Behrens et al., 2011). Even so, further improvement of this catalyst is still needed. The best catalyst is usually obtained by co-precipitation with Na2CO3 solution at a constant pH 6 or 7 and at temperatures ranging from 60–70°C (Li and Inui, 1996; Baltes et al., 2008). The initial precipitate, which is made of hydroxycarbonates (Mota et al., 2018; Ghosh et al., 2019), is aged for around 30 min to a few hours (Li and Inui, 1996; Kniep et al., 2004; Behrens et al., 2011) followed by washing, drying, and calcination at temperatures around 600–700 K to form CuO–ZnO species with some carbonate residues, responsible for the porous microstructure and surface area. The following further reduction of the obtained phases yields the active catalyst phase—usually metallic Cu nanoparticles, although other species of Cu, including Cu+, ZnO decorated Cu, or partially reduced ZnOx, have been reported (Schumann et al., 2016; Mota et al., 2018). The conditions during the precipitation and aging stages, as well as residual Na+ ions in the system and elemental composition (Cu:Zn—65:25), are crucial for the properties of the final catalyst (Zhao et al., 2011; Behrens, 2016; Kondrat et al., 2017; Mota et al., 2018; Ghosh et al., 2019; Guil-López et al., 2019b).
To further improve the microstructural and porous properties of the methanol synthesis catalysts, other synthesis methods have also been studied (Guo et al., 2009; Natesakhawat et al., 2012; Dong et al., 2016; Dasireddy and Likozar, 2019). The precipitation–reduction method involves first the co-precipitation step, followed by a reduction in the second step by a reducing agent such as NaBH4. Typically, a solution of metal nitrates and a solution of Na2CO3 or NaOH precipitant are added dropwise to deionized water simultaneously under stirring at a temperature and a constant pH (∼7.0) during precipitation. Then a reducing agent is added, and the resulting slurry is further aged at a specific temperature for sufficient time, followed by filtration and washing, drying, and calcination. Compared with the conventional co-precipitation method, catalysts with smaller Cu particles are much more easily obtained by using the precipitation–reduction method. By this method, the viewpoint that both Cu+ and Cu0 species contributed to the activity of CO2 hydrogenation to methanol is accepted (Dong et al., 2016).
The sol–gel (SG) method is another way to prepare mixed oxides, especially for M–CeTiOx systems (Chen et al., 2014; Matějová et al., 2014; Bo et al., 2016). In a study utilizing CuCeTiOx as the catalyst, Ce and Ti ions were hydrolyzed to form the framework at low pH during the sol–gel transformation. Then the Cu species were solidified through evaporation of the solvents. These steps can lead to elemental distribution that differs between the bulk and surface, resulting in catalysts with varying composition in CuCeTiOx on their catalytic properties. By this method, a catalyst composite (CuCeTiOx–SG) with the composition (30%CuO35%CeO235%TiO2) was prepared and compared with the co-precipitation method derived catalyst (CuCeTiOx–CP). The preparation methods show an important influence on catalytic performance (Figure 9). The CuCeTiOx–CP catalyst showed a higher CO2 conversion than CuCeTiOx–SG. However, the CuCeTiOx–SG catalyst showed a higher selectivity to methanol than CuCeTiOx–CP at the same CO2 conversion (Chang et al., 2017). Also, Cu/ZnO catalysts were prepared using three different methods (co-precipitation, sequential precipitation, and homogeneous precipitation). The studied preparation methods influenced the surface area of the Cu-based catalysts, which directly impact their catalytic activities. The different preparation methods resulted in various structural changes in the aurichalcite precursors that were transformed into the final catalyst. From the catalytic evaluation results, it was concluded that the preparation methods had noticeable effects on the dispersion of Cu particles and the catalyst structure. These effects were more pronounced for the catalysts prepared by homogeneous precipitation and co-precipitation (Sanches et al., 2012). The hydrogenation of CO2 was conducted over a series of Cu/ZnO/Al2O3 catalysts prepared by different synthesis methods (co-precipitation, ultrasound-assisted, sol–gel, and solid-state). The characterization and catalytic performance showed that the preparation strategy had a strong influence on them (Dasireddy and Likozar, 2019). The ultrasonic synthesis route provided catalysts with increased basic active sites and significant methanol selectivity in comparison with that prepared from the conventional co-precipitation route. This method also improved the dispersion of metallic Cu particles, which altered the intrinsic reactivity of CuO–ZnO. Since the methanol production rate was proportional to the ratio of Cu+/Cu0, it was concluded that the presence of high levels of Cu+ species is essential for high and low selectivity to methanol and CO, respectively (Dasireddy and Likozar, 2019).
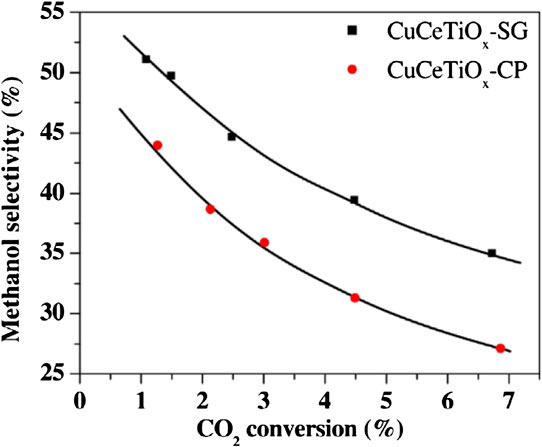
FIGURE 9. Selectivity-conversion relationships of CuCeTiOx–SG and CuCeTiOx–CP (Chang et al., 2017). Reproduced with permission from Elsevier.
Other Cu-Containing Catalysts
Supported and Promoted Cu Catalysts
Until the present, Cu-based catalysts present the most desirable properties for the direct CO2 hydrogenation to methanol at the industrial scale, thus proper to refer it as the methanol synthesis catalyst. However, the low conversion of CO2 below equilibrium and poor selectivity to methanol have necessitated further improvement of these catalysts. Although the methanol synthesis catalyst is not a classical supported catalyst, suitable support not only provides a proper catalyst configuration but modify the interactions between the active component and the support (Liu et al., 2003). It can also alter the surface properties, such as the basicity/acidity and adsorption characteristics of the catalyst. Over the years, various support materials (Figure 10) for the Cu-based catalysts have been studied (Weigel et al., 1996; Tang et al., 2009; Halder et al., 2018; Lin et al., 2019; Yang B. et al., 2019). Metal oxides are the most common supports for the methanol synthesis catalysts, and their properties greatly affect the catalyst activity in several ways. The non-metallic supports, including metal organic frameworks (MOFs), porous silica materials, layered double hydroxides (LDHs), carbon materials, metal carbides, graphene, and porous polymers, have also been investigated (Rodriguez et al., 2015; Wang et al., 2015; Díez-Ramírez et al., 2016; Fan and Wu, 2016; Liu et al., 2016; Din et al., 2018; Sun et al., 2018; Witoon et al., 2018; Mureddu et al., 2019). We discuss the supported Cu-catalysts in a different light from the above discussed ternary catalysts, noting that the commercial methanol synthesis (Cu/ZnO/Al2O3) catalyst, for example, is not a “supported catalyst.” Supported catalysts are generally prepared by the incipient or wet impregnation methods. Of the metal oxide supports investigated in the literature for Cu catalysts, ZnO, ZrO2, Al2O3, Ga2O3, SiO2, and CeO2 have drawn the most attention in methanol synthesis. These metal oxides have also been explored as promoters to the Cu-based methanol synthesis catalysts (Toyir et al., 2009; Zhan et al., 2014; Hu et al., 2018).
Cu/ZnO Catalysts—ZnO as a Support and Co-Catalyst
The Cu/ZnO-based catalysts for the production of methanol from CO or CO2 or a mixture of both have been in existence and applied for nearly six decades. Before the standardization of the ternary Cu/ZnO/Al2O3 catalyst, Cu/ZnO was used as an active catalyst for the hydrogenation of CO. The Cu/ZnO catalyst is typically prepared by the impregnation or co-precipitation method (Lei et al., 2015; Lunkenbein et al., 2015).
In the Cu/ZnO catalyst, ZnO plays several important roles. The presence of ZnO improves the dispersion and stability of Cu (Bonura et al., 2011); also, the lattice oxygen vacancies and the electron pairs in ZnO are active for methanol synthesis. These functions lead to a more active Cu phase and larger surface area, thus preventing agglomeration of Cu particles (Arena et al., 2007). The active Cu surface area of Cu/ZnO catalysts correlated with the degree of Zn incorporated into the precursor phase. The metallic copper surface areas in the reduced catalysts could be determined by the N2O titration technique (Guo et al., 2009; Guo et al., 2011).
Synergism between Cu and ZnO reportedly exists upon the incorporation of ZnO into the Cu based catalysts (Kanai et al., 1996; Chen et al., 1999), and this resulted in the electronic interaction between Cu and Zn(2−δ)+ which created active sites like Cu+–O–Zn (Kanai et al., 1996). The catalytic activity of a Zn-doped Cu(111) surface was much higher than that of the pure Cu(111) as a result that ZnO modified the electronic properties of Cu sites by an electron exchange and interaction with Cu particles (Twigg and Spencer, 2001; Koitaya et al., 2019). The role of ZnO in the reduction of Cu by H2 was studied by Fierro et al. (1996). The temperature programmed reduction investigation of the CuO–ZnO catalyst synthesized by the co-precipitation method revealed ZnO promoted the reducibility of CuO. It is believed that ZnO acts as a reservoir of atomic hydrogen and provides it for the CO2 hydrogenation on the Cu surface, or as a binding site facilitating the adsorption of H2 species and CO2 via a spillover (Chen et al., 1999). The atomic hydrogen then transfers from the Cu onto the ZnO surface and gradually hydrogenates the adsorbed CO2 to methanol (Sun et al., 2003; Dang et al., 2018).
ZnO, as a support, is also suggested to be an active component in the methanol synthesis catalyst (Fujitani and Nakamura, 2000; Choi et al., 2001). In a physical mixture of Cu/SiO2 and ZnO/SiO2, it was found that Zn species could migrate to the Cu surface upon reduction with H2, creating Cu–Zn active sites on the Cu surface (Choi et al., 2001). The formate species were firstly formed on both Cu and ZnO phases, and secondly, they were further hydrogenated to form methoxides located on the ZnO (Lei et al., 2015). Thus, ZnO is actively involved in the synthesis of methanol by creating more stable reaction intermediates, which readily convert to methanol on further hydrogenation (Chen et al., 1999). The absorption strength of reaction intermediates like HCO, H2CO, and H3CO can be enhanced by the incorporation of ZnO, thus decreasing the energy barriers. Consequently, the formation rate of methanol is increased (Behrens et al., 2012).
Sulfur and chlorine species are considered poisons for Cu-based methanol synthesis catalysts, and the addition of ZnO to the catalyst irreversibly scavenges sulfur or chlorine as ZnS or ZnCl2, respectively, militating against deactivation of the catalyst. On the negative, ZnO is a basic oxide that can neutralize the acidity of Al2O3 in the commercial catalyst, preventing the transformation of CO2 to methanol and promoting the agglomeration of active Cu particles (Twigg and Spencer, 2001).
Cu/ZrO2 and Cu/ZnO/ZrO2
ZrO2 is a good support due to its hydrophobicity, and surface basicity. Besides, its high thermal stability is superior to Al2O3 under reducing and oxidizing atmospheres (Li and Chen, 2019). The catalytic activity of ZrO2 as a support is superior to that of Al2O3, SiO2, or ZnO (Li and Chen, 2019). The addition of ZrO2 has been reported to improve the surface area of Cu species and can alter the Cu+/Cu0 ratio in the surface (Fisher et al., 1997; Słoczyński et al., 2003). CuO can be uniformly dispersed on the ZrO2 surface, forming an interface favorable for the methanol synthesis reaction (Li and Chen, 2019).
ZrO2 exists in different crystal structural phases (polymorphs)–amorphous (a)-ZrO2 and tetragonal (t)-ZrO2 and monoclinic (m)-ZrO2 (Figures 11A–C). The a-ZrO2 and t-ZrO2 transform to m-ZrO2 at high temperatures. The calcination of Zr(OH)4 at temperatures greater than 400°C transforms it mainly to m-ZrO2, so Cu species are easily incorporated into a-ZrO2 (Tada et al., 2018). The effects of ZrO2 polymorphs, including -a, -t and -m phases on the structure of Cu, Cu–ZrO2 interaction and adsorption–desorption of H2 and CO2 were systematically investigated, and the catalytic performance of the catalysts, Cu/a-ZrO2, Cu/t-ZrO2, and Cu/m-ZrO2 catalysts explored (Witoon et al., 2016). By a variety of analytical techniques, the Cu surface area followed the trend: Cu/a-ZrO2 > Cu/t-ZrO2 > Cu/m-ZrO2. The increase in the yield of methanol is correlated with the increase in Cu surface area, thus the Cu/a-ZrO2 exhibited the highest methanol yield. However, the methanol turn over frequency (TOFMethanol) of Cu/t-ZrO2 was higher than those of Cu/a-ZrO2 and Cu/m-ZrO2. In general, the high TOFMethanol is due to a strong Cu–ZrO2 interaction and a high surface concentration of atomic hydrogen to CO2 (Witoon et al., 2016). A highly loaded CuO (65.2 wt%) on ZrO2 support prepared by flame spray pyrolysis (FSP), showed a good catalyst activity compared with a commercial catalyst (Figure 11D). The production rate of methanol by CO2 hydrogenation and the selectivity to methanol over FSP-made CuO/ZrO2 catalysts were obviously higher compared with those of commercial CuO/ZnO/Al2O3 (Fujiwara et al., 2019). For all catalysts, the CO2 conversion increased, with increasing contact time, while the selectivity to methanol decreased, but the selectivity to CO increased (Figure 11E). The activity and selectivity of the prepared catalysts depended on the spray pyrolysis rate. They were higher at low feed rates (2–3 ml min−1) than those of the catalysts prepared at higher feed rates (5–10 ml min−1). The former feed rate led to the formation of smaller ZrO2 particles, which provided more surface to stabilize small Cu particles and formed interfacial Cu-ZrO2 active sites. The crystallite size and crystallinity of t-ZrO2 could be controlled by varying the precursor feed rate (Fujiwara et al., 2019).
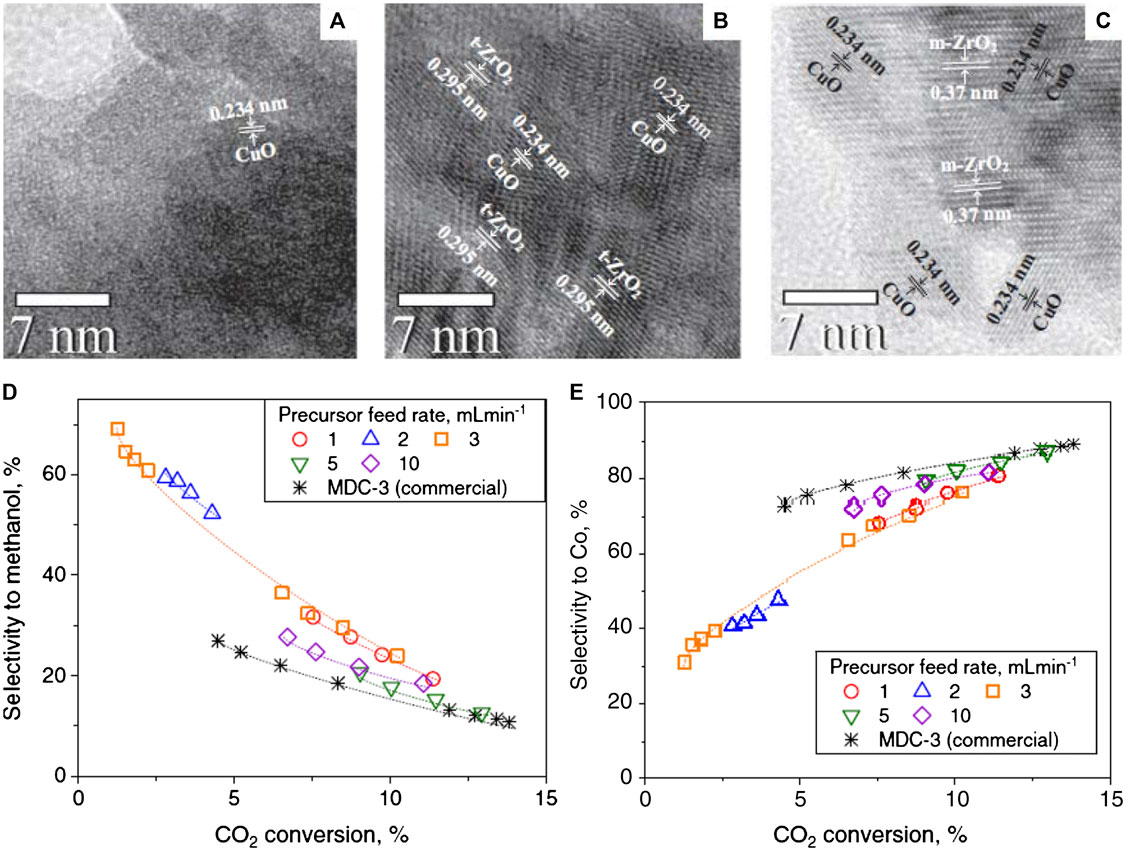
FIGURE 11. TEM of (A) Cu/a-ZrO2, (B) Cu/t-ZrO2 and (C) Cu/m-ZrO2 catalysts (Witoon et al., 2016). (D) The selectivity to methanol as a function CO2 conversion over FSP-made CuO/ZrO2 and commercial CuO/ZnO/Al2O3 at different contact times. (E) The selectivity to CO as a function CO2 conversion over FSP-made CuO/ZrO2 and commercial CuO/ZnO/Al2O3 at different contact times. The contact time of commercial CuO/ZnO/Al2O3 and CuO/ZrO2 prepared at P = 1–10 ml min−1 were 60–1,500
Cu/ZnO/ZrO2 catalyst is more resistant to water deactivation due to the hydrophobic nature of ZrO2 (Li and Chen, 2019). The Cu/ZnO/ZrO2 catalyst contains ZrO2 instead of Al2O3 and exhibits high performance in methanol synthesis from CO2 hydrogenation. Compared with Al2O3, the impressive performance is linked with the possibility of interactions between Cu-species and ZnO–ZrO2 oxides (Li and Chen, 2019). Moreover, ZrO2 exhibits a weaker hydrophilic character than either Al2O3 or CeO2, which promotes the desorption of formed water, and benefits the formation of methanol (Arena et al., 2007). The presence of ZrO2 in the Cu/ZnO catalysts could lower the Cu coordination with oxygen and increase the Cu–O distance, as studied by the extended X-ray absorption fine structure. This indicates the presence of defective Cu structures resulting from the strong Cu–support interaction (Yang et al., 2006). Consequently, the Cu/ZnO catalyst containing ZrO2 exhibited much higher activity and selectivity toward methanol production than the Cu/ZnO catalyst. While it is a proven fact that the impressive performance of the Cu/ZnO/ZrO2 catalyst arises from the structural and surface modifications of the Cu/ZnO by ZrO2, it is important also to note that the crystallinity of ZrO2 strongly affects the Cu–ZrO2 interaction (Baiker et al., 1993). Thus, the co-presence of amorphous ZrO2 and crystalline Cu/ZnO enhances the synergistic effect of Cu/ZnO/ZrO2, facilitating the dissociative adsorption of CO2 and the selective conversion of CO2 to methanol (Słoczyński et al., 2004).
Both experiments and DFT calculations using Cu–ZnO–ZrO2 have provided evidence on the separate functions of the Cu species and ZnO–ZrO2 interface in the catalytic conversion of CO2 to methanol by hydrogenation (Wang Y. et al., 2019). The catalytic evaluation at 220°C under 3.0 MPa showed very high activity (CO2 conversion of 18.2% and selectivity to methanol of 80.2%). The binary oxides of ZnO–ZrO2 showed a higher ability for CO2 adsorption and the hydrogenation of carbonate species to formate and methoxy intermediates than the Cu–ZnO or Cu–ZrO2 systems. Cu/ZrO2 and Cu/ZnO catalysts synthesized by various methods show different catalytic performance. While Cu/ZrO2 is more effective for the selective formation of methanol from CO2, higher activity for CO2 conversion is associated with Cu/ZnO (Li and Chen, 2019).
So far, efforts have been made to enhance the catalytic performance of CuO–ZnO–ZrO2 catalysts further. Modification of CuO–ZnO–ZrO2 catalysts with various additives is a feasible option to alter the physicochemical properties of the catalysts, improving the methanol synthesis activity and preventing the Cu sintering. The CuO–ZnO–ZrO2 catalysts supported on graphene oxide (GO) gave a higher STY in comparison with the GO-free catalyst due to the increased active sites for the adsorption of CO2 and H2. The methanol selectivity of GO supported catalysts was above that of the unsupported catalyst. Specifically, the highest methanol selectivity of 75.88% was obtained over the CuO–ZnO–ZrO2 catalyst prepared with 1 wt% GO (CZZ-1GO) at 200°C and 20 bars. This performance was attributed to a promoting effect of GO nanosheet serving as a bridge between metal oxides, which enhanced a hydrogen spillover from the Cu surface to the carbon-containing species adsorbed on the metal oxide particles (Witoon et al., 2018). The mixed oxides of Cr, Mo, or W and CuO–ZnO–ZrO2 prepared by the co-precipitation method showed better activity for methanol synthesis. The results indicated an improved methanol selectivity and yield of the CuO–ZnO–ZrO2 catalyst upon addition of MoO3 or WO3 but slightly dropped when doped with Cr2O3. The improved methanol yield over these catalysts can be attributed to the differences in their Brunauer-Emmett-Teller surface areas and adsorption capacities for CO2. It was also found that the ratio of surface Zn to Cu, as well as the fraction of strong basic sites, improved the methanol selectivity (Wang G. et al., 2019). A layered double hydroxide (Mg-Al LDH) was used as a carrier for Cu–ZnO–ZrO2 catalyst synthesized by the co-precipitation method. Characterization results revealed CuO–ZnO–ZrO2 nanoparticles were uniformly dispersed and attached to the surface of the LDH, which improved the specific surface area and Cu dispersion compared with a reference catalyst without the support. The catalyst showed a high methanol selectivity of 78.3% at 250°C under a pressure of 3.0 MPa, which is about 50% higher than conventional Cu-based catalysts reported in the literature. Raising the temperature of the CuO-ZnO–ZrO2–LDH catalyst slightly decreased the conversion. Very promising is that the activity of the can be recovered by reduction with H2 (Fang et al., 2019).
Cu/CeO2 and Cu/ZnO/CeO2
CeO2 has also been studied as a support or co-support for the methanol synthesis catalysts via the CO2 hydrogenation route (Hu et al., 1991; Wang et al., 2016; Chang et al., 2017; Li et al., 2019). It has a strong adsorption affinity for CO2 due to its strong basicity and oxygen vacancies. The latter can improve the dispersion of Cu particles and promote the spillover of atomic hydrogen, which benefits the production of methanol (Chang et al., 2017; Li et al., 2020); also, a negative influence on the surface area of catalysts with ceria was observed (Bonura et al., 2011). In 2014, Rodriguez and co-workers published a study that demonstrated the combination of Cu metal and oxide sites in the Cu–CeO2 interface affords favorable reaction pathways for the conversion of CO2 to methanol (Graciani et al., 2014). By theoretical methods, the CO2 hydrogenation over a CeOx/Cu(111) surface was demonstrated. The complementary surface analysis with XPS indicated Ce2O3/Cu(111) as the active phase of the catalyst (Figure 12A). This inverse catalyst was much better for methanol synthesis than either Cu(111) or Cu/ZnO
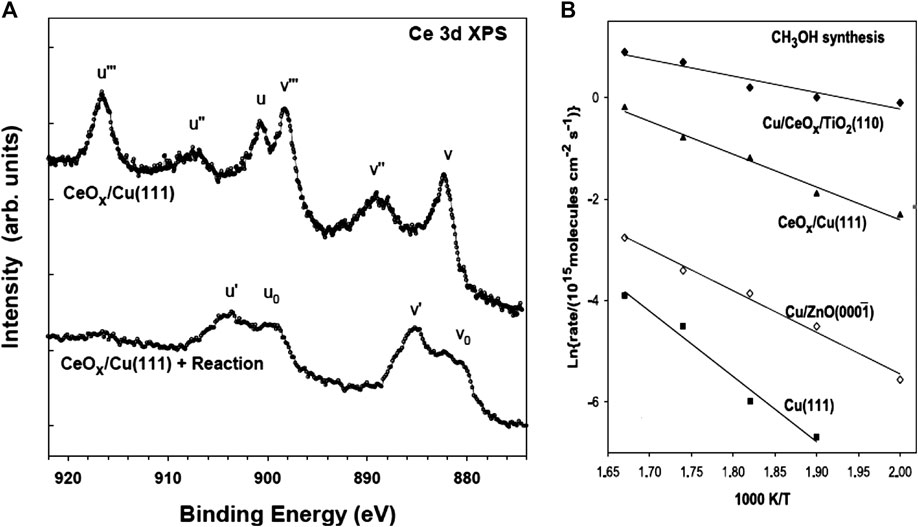
FIGURE 12. (A) Ce 3d XPS spectra collected before and after performing the hydrogenation of CO2 on a CeOx/Cu(111) surface. Reaction conditions: catalyst was exposed to 0.5 atm of CO2 and 4.5 atm of H2, at 500 K, for 15 min. (B) Arrhenius plot for methanol synthesis on Cu(111); Cu/ZnO
In ceria-containing Cu–ZnO oxide catalysts, the presence of CeO2 promoted the surface activity of the Cu–ZnO system, although negatively influenced the catalyst texture and metal surface area in comparison to ZrO2 (Bonura et al., 2011). As discussed earlier, CeOx can improve the dispersion of Cu particles and promote the spillover of atomic hydrogen. On the other hand, ZnO can improve the dispersion of the CeOx nanoparticles. Thus, the ternary CuZnCeOx exhibited higher performance than the binary CuZnOx catalyst (Shi et al., 2019); but had relatively very high selectivity toward CO (Hu et al., 2018). A CuZnCeOx catalyst prepared by a parallel flow co-precipitation technique was evaluated in the hydrogenation of CO2 to methanol and CO. The amount of CeOx in the catalyst controlled the selectivity of the products. Characterization results revealed a significant synergistic effect between Cu and metal oxides (ZnO and/or CeOx) in the catalyst. Cu played a critical role in the activation of H2, and CeOx strongly adsorbed CO2, improved the dispersion of Cu nanoparticles, and promoted the spillover of atomic hydrogen (Shi et al., 2019). The results of these studies suggest that CeO2 in Cu–ZnO catalysts can offer a viable way to produce methanol or CO from CO2 hydrogenation selectively. The selectivity toward the products (methanol and CO) can be regulated by changing the reaction conditions, catalyst formulation, or preparation method (Hu et al., 2018). For example, the CuZnCeTiOx showed significantly enhanced activity in comparison with the CuCeTiOx catalyst and was twice more active than the commercial catalyst as measured by TOF values. However, the stability is still not good enough, with high selectivity toward CO (Chang et al., 2019).
Other Metal Oxides Employed as Promoters or Additives
Magnesium Oxide (MgO)
Mg-containing Cu/Zn/Al industrial catalysts for methanol synthesis were developed in the 1990s (Bozzano and Manenti, 2016). The effect of metal oxides on the Cu/ZnO/Al2O3 catalyst from co-precipitation was investigated. MgO showed a negative impact on the catalytic activity, but a positive effect on the stability of the catalyst (Meshkini et al., 2010). It was concluded that Mg affects the activity of the Cu/Zn/Zr catalyst for methanol synthesis from CO2 by improving the adsorption properties (Słoczyński et al., 2003). Zander et al. (2013) found that the methanol production rate from synthesis gas by Cu/MgO/ZnO was higher than that by Cu/ZnO, ascribed to the higher Cu dispersion caused by Mg addition. Recently, the influence of Mg addition on the performance of Cu/Zn/Al/Mg methanol synthesis catalyst prepared by co-precipitation and fractional-precipitation methods was investigated. In a series on Cu/Zn/Al/Mg catalysts obtained, the preparation method was found to have a significant effect on the properties as well as the catalytic performance. The co-precipitation method resulted in catalysts with higher Brunauer-Emmett-Teller surface area and Cu dispersion, but with decreased catalytic activity. On the other hand, the fractional precipitation facilitated the Cu substitution by Zn in the sub-carbonate precursor, which cushioned the effect resulting from the former method, catalytically performed better than those prepared by the co-precipitation method (Zhang et al., 2017). In these catalysts, there was the formation of Mg–Al hydrotalcite unfavorable for methanol production. Moreover, the formation of CuAl2O4 and MgAl2O4 spinel phases in Cu/MgO/Al2O3 catalysts were observed (Dasireddy et al., 2018).
Gallium Oxide (Ga2O3)
Ga2O3 is reported to increase the activity per unit Cu surface area of methanol synthesis catalyst (Toyir et al., 2009). Ga3+ can modify the hydroxycarbonate precursors during the catalyst synthesis to form the precursors with hydrotalcite structure (An et al., 2007). The catalysts derived from the Ga-modified hydrotalcite showed improvement in the dispersion of Cu particles and the formation of active Cu–ZnOx sites, which enhanced the efficiency of Cu–ZnGa catalyst system for CO2 hydrogenation to methanol (An et al., 2007). One reason for this improvement is that the hydrotalcite derived catalysts could maintain their morphology in ultrafine layers even after heat treatment at high temperatures, which transformed the phase to amorphous (Guil-López et al., 2019a). The amorphous phase is more accessible with better dispersed metallic Cu crystal, and with a large surface area decorated with a small amount of Zn atoms. CuZnGa catalysts derived from the LDH precursor gave good catalytic activity in CO2 hydrogenation to methanol. LDH30Ga (Cu: 33.5 wt%) yielded STY of 0.59 gml−1 h−1, higher than the commercial JM-HiFUEL (50 wt% Cu/ZnO/Al2O3) with a STY of 0.38 gml−1 h−1 after 25 h on stream at 290°C and 4.5 MPa (Li et al., 2018). However, there is an obvious requirement of high temperature and pressure for realizing the high activity.
Titanium Oxide (TiO2)
The incorporation of titanium nanotubes (TNTs) support into CuO–ZnO–CeO2 catalysts can promote CuO reducibility, improve metallic Cu dispersion and increase the specific surface area. The CuO–ZnO–CeO2/TNTs composite catalysts with different TNTs contents prepared by a deposition–precipitation method gave high CO2 conversion and methanol selectivity. The selectivity was positively correlated with the number of basic sites, whereas the CO2 conversion was a function of the specific surface area of Cu. The catalyst prepared with 10 wt% TNTs (CuO–ZnO–CeO2/10 TNTs) possessed high metallic Cu surface area, high CO2 adsorption capacity and a large number of basic sites, translating into excellent catalytic performance (methanol selectivity of 59.8%, CO2 conversion of 23.3% and STY of 9.33 mmolMeOH h−1 gcat−1 at 260°C, H2/CO2 of 3, gas hourly space velocity (GHSV) of 7,500 ml g−1 h−1) (Shi et al., 2019).
Non-Metal Oxide Supports
In general, SiO2 possesses large surface area and porosity, high thermal stability, and good dispersion capacity but weak interaction with metals (Nitta et al., 1994; Sugawa et al., 1995). However, the presence of steam at high temperatures weakens its thermal stability due to its transformation to Si(OH)2. During the methanol synthesis from CO2, the stability of Cu/ZnO-based catalysts was improved by incorporating a small amount of silica, which suppressed the crystallization of ZnO in the catalysts (Toyir et al., 2009). Cu supported on high-purity silica was nearly inactive in methanol synthesis (Fujita et al., 1995; Gotti and Prins, 1998), and the selectivity toward methanol was low. In another study, the Cu/SiO2 catalyst exhibited a low selectivity to methanol (Sugawa et al., 1995). A 10 wt% Cu/SiO2 exhibited higher methanol formation rate (2.1%) than 10 wt% Pd/SiO2 (0.3%) (Kunkes et al., 2015). Some experimental results have reported higher activity and relatively better selectivity for methanol over silica-based than ZnO-based catalysts, due to the higher surface area of the former (Nitta et al., 1994). SiO2 can function better as a support for Cu-catalyst for methanol synthesis in the presence of other metal oxides as a promoter or co-support, or for the copper bimetallic catalysts (Sugawa et al., 1995; Grandjean et al., 2011). Micro-spherical SiO2 prepared by the spray-drying method was investigated as support for Cu/ZnO-based catalysts synthesized with different percentages of Cu and ZnO by the ammonia-evaporation method (Jiang et al., 2018). The results revealed the deposition of Cu and Zn ions in the pores of the SiO2 and high distribution, which depended on the metal loadings. The specific surface area of the catalysts increased with increasing loadings to a critical amount due to the formation of the porous structure of SiO2. Beyond this loading, CO2 conversion slightly reduced due to the blocking of the pores of the support. The combination of X-ray diffraction, XPS, X-ray Auger electron spectroscopy and CO-adsorption in situ Fourier-transform infrared spectroscopy analysis demonstrated that SiO2 facilitated the formation of both Cu+ and Cu0 species on the surface of the reduced Cu/ZnO/SiO2 catalysts (Jiang et al., 2018). Other examples of the SiO2 supported catalysts for methanol synthesis can be found in the literature (Studt et al., 2014; Fiordaliso et al., 2015; Phongamwong et al., 2017; Jiang et al., 2018).
Carbon materials possess a very large surface area, high thermal stability, high hydrogen uptake, mechanical strength, and facilitate H2 dissociation. All these properties contribute to the increasing rate of CO2 hydrogenation to methanol at a lower temperature with high methanol selectivity than the equilibrium when used as supports, but unsuitable for a commercial application due to low conversion. GO as support for the Cu–ZnO catalysts was studied for the CO2 hydrogenation to methanol. The results found that 10 wt% CuZn/rGO catalyst exhibited a good activity for the CO2 hydrogenation, achieving 26 % CO2 conversion, methanol selectivity of 51%, and 424 ± 18 mgmethanol at 250°C under 15 bar after 5 h on a stream (Deerattrakul et al., 2016). With MOF as a support or component of catalyst, very high methanol selectivity (up to 100%) was reported (Rungtaweevoranit et al., 2016; An et al., 2017; Hu et al., 2019). Still, its application suffers from serious challenges that are undesirable for industrial applications—low conversion and instability at high temperatures. GO as support for the Cu–ZnO catalysts was studied for the CO2 hydrogenation to methanol. The results found that 10 wt% CuZn/rGO catalyst exhibited a good activity for the CO2 hydrogenation, achieving 26% CO2 conversion, methanol selectivity of 51%, and 424 ± 18 mgmethanol at 250°C under 15 bar after 5 h on a stream (Deerattrakul et al., 2016).
The promotion of the Cu/Zn catalyst supported on SBA-15 (CZ/SBA-15) with transition metals (Cr, Mn, Fe, Co, Ni) revealed impressive catalytic performances of the modified catalysts. The Mn promoted catalyst (Mn-CZ/SBA-15) was the most active due to the presence of small copper crystallites and strong interaction between CuO and other oxide species in the catalyst. At a reaction temperature of 180°C under 4.0 MPa, WHSV of 60 L/gcat. h and H2/CO2 of 3, the catalyst presented a methanol yield of 10.4%, CO2 conversion of 10.5% and a methanol selectivity of 98.6% (Koh et al., 2019).
Bimetallic Cu-Based Catalysts
Bimetallic Cu-based catalysts also have good catalytic performances in the direct CO2 hydrogenation to methanol. Noble metals such as Pd have proper properties for activating hydrogen, which could spread through a hydrogen spillover mechanism to the neighboring catalytic sites (Melián-Cabrera et al., 2002; Ponce and Klabunde, 2005). The hydrogen spillover can result in a catalyst surface with a highly reduced state that could facilitate the hydrogenation process. In the methanol synthesis application, Pd is reported with good catalyst improvement roles. It is suggested that Pd enhances the activity of Cu sites. Upon the addition of Pd, the Cu dispersion and surface concentration on the catalyst surface were improved. The Cu dispersion and the surface Cu concentration increased with an increase in the amount of loaded Pd to a certain level. It was explained that the interaction between Pd and Cu decreased the Cu–Cu bond distance due to the strong electronic perturbation, resulting in well-dispersed Cu species (Kugai et al., 2016). In this way, the aggregation or agglomeration of Cu particles was suppressed due to the interaction with Pd, which was highly dispersed on CeO2 support (Choi et al., 2017). According to the XPS results, the peaks for Cu 2p electrons in Pd–Cu/CeO2 catalysts appeared at relatively lower binding energy than those in Cu/CeO2 catalyst, meaning that Cu sites in Pd–Cu/CeO2 catalysts were more abundant in electrons and could donate them to Cu, enabling Cu to stabilize in a more reduced state (Fox et al., 2008). Thus, Pd promotion generated more electron-rich Cu sites by electron transfer (Choi et al., 2017). Pd can also improve the reducibility of CuO and enrich the catalyst surface with electrons, enabling the activation of CO2 by interaction with the carbon atom of CO2 (Choi et al., 2017). A strong Pd–Cu bimetallic promoting effect on the formation of methanol from CO2 hydrogenation was observed, which is due to the synergetic effect between Pd and Cu as a result of the Pd–Cu alloy formation (Jiang et al., 2015). Pd–Cu supported on amorphous silica exhibited higher catalytic activity than monometallic Cu/SiO2 or Pd/SiO2 for CO2 hydrogenation to methanol. Some authors attribute the synergistic effect between Pd and Cu, which contributes to the improvement of catalytic activity to the alloy formation, as evidenced by the correlation between catalyst composition, structure and catalytic performance (Jiang et al., 2019a; Jiang et al., 2019b). The Pd–Cu bimetallic catalysts with total metal loadings (2.4–18.7 wt%) and optimal Pd/(Pd + Cu) atomic ratio exhibited a bimetallic effect on promoting CH3OH synthesis at 250°C and 4.1 MPa. The improvement in catalytic performance was realized at lower metal loadings, and Pd–Cu(2.4)/SiO2 catalyst could yield approx. 1.6 times higher methanol than the commercial Cu/ZnO/Al2O3 catalyst as measured with the metal-based STY. At high loadings, Pd–Cu alloy exhibited high selectivity to CO (Nie et al., 2018; Jiang et al., 2019a). The amount of alloy, as determined by quantitative X-ray diffraction, correlated with the observed promotive synergy; and the estimated TOFs, suggesting its involvement in methanol synthesis (Jiang et al., 2019b). A Cu–Zn bimetallic catalyst supported on Al foam (Cu–Zn/Al foam) gave a high methanol yield of 7.81 g gCu−1 h−1 at CO2 conversion of 9.9% and methanol selectivity of 82.7% under reaction conditions of 3 MPa and 250°C at a high WHSV of 20,000 ml gcat−1 h−1. It was found that the support structure played a significant role in the performance of this catalyst. Compared with the other Cu-based catalysts, the Cu–Zn/Al foam catalyst possesses a good heat/mass transferability, and an appropriate amount of basic sites (Liang et al., 2017).
Renewable Energy Storage in and New Processes for Methanol
The chemical recycling of CO2 to renewable fuels and commodity chemicals represents an economic aspect of the CO2 mitigation. Methanol, a primary liquid product derived from the hydrogenation of CO2, aside being used directly as a fuel, can be efficiently processed into other products of high societal needs—DME, ethylene, propylene, gasoline, and other products currently obtained from petroleum and natural gas. The combustion of methanol and its derivatives will release CO2, which can be recycled back effectively, forming a carbon loop (Goeppert et al., 2014). Biomass is a form of recycled CO2 that can be converted into DME, for example. Since CO2 hydrogenation is carried out using hydrogen produced from renewable energy sources—electrical, wind, hydro or solar energy (Goeppert et al., 2014; Patterson et al., 2019), it is required to store it for use at a later time due to the obvious challenges with each of the energy sources. For example, solar and wind are seasonal, intermittent and fluctuating. The storage of electricity on a large scale and transportation at a very long distance are still challenging. The electrical energy can be conveniently stored in chemical compounds such as hydrogen, methanol, methane and higher hydrocarbons that can then be stored, transported and used when needed to produce electricity or for various other applications such as heating, cooking and transportation (Olah, 2005; Goeppert et al., 2014). It has been proposed that the carbon-based liquid fuels will continue to be important energy storage media in the future because of their higher volumetric stored energy density. Methanol has great merits as a storage medium for renewable energy. As an energy storage medium, methanol displays high performance as an additive or substitute for gasoline in internal combustion engines. The direct conversion of the chemical energy in methanol to electrical power at ambient temperature has been demonstrated in methanol fuel cells (McGrath et al., 2004). Methanol is also a feedstock for a number of chemicals such as formaldehyde and acetic acid. It can produce light olefins, including ethylene and propylene, used in the synthesis of various polymers, and any hydrocarbons and products currently obtained from petroleum oil through the methanol-to-olefin process. DME produced from methanol can be easily liquefied at moderate pressure and applied as diesel fuel substitute with high cetane rating, producing little or no soot emissions (Semelsberger et al., 2006; Arcoumanis et al., 2008). It is a good substitute for liquefied petroleum gas in most applications, such as heating and cooking.
The CO2 hydrogenation to methanol can be processed by the thermochemical, electrochemical and photochemical methods. These processes are challenging in several aspects. The thermochemical process applied in the commercial methanol synthesis from natural gas is a two-step process that transforms the energy and molecules in a fossil fuel (Olah, 2013). The first step is the steam-methane reforming into synthesis gas, which subsequently converts to methanol in the second step. A few percent of CO2 is also produced in the first step. Methanol cannot be directly generated electrochemically from CO2 with high selectivities or current densities (Malik et al., 2016; Yang D. et al., 2019).
Researches are continuously seeking new technologies to recycle CO2 to liquid fuel most efficiently and economically. Patterson et al. (2019) developed a new approach integrating the existing conventional chemical catalytic process and energy harvesting methods. They proposed combining solar methanol islands and human-made marine structures that use renewable energy to harvest CO2 from seawater and catalysis to produce methanol. This approach uses clusters of marine-based floating islands on which photovoltaic cells convert sunlight into electrical energy to produce H2 and extract CO2 from seawater, where it is in equilibrium with the atmosphere. H2 and CO2 then react to form methanol. H2 is electrochemically generated and the extraction of CO2 is possible using a series of membrane cells. Methanol is then synthesized using a looped gas-phase heterogeneous catalytic process. They suggested that a single solar methanol island could output up to 15,300 tons/year of methanol. The process is particularly of advantage compared with the direct atmospheric CO2 capture because CO2 in seawater (0.099 kg CO2/m3) is about 125 greater than the amount in the atmosphere (0.00079 kg/m3) (Patterson et al., 2019). This innovative technology for renewable fuel synthesis from the marine environment has attractive features, such as abundant raw materials and large exposure to solar energy, and avoidance of local CO2 depletion. However, this technology relies on previously demonstrated chemical and physical processes to produce the solar methanol island on a significantly large scale. It is suggested that wind could also serve as a power source; thus, analyzing how other energy sources or energy mixture could contribute is expected to further the development of the process. For a practical design of solar-powered artificial marine-islands to recycle CO2 into methanol and other synthetic liquid fuel, some issues must be addressed. These include i) how photovoltaic modules can be deployed on a large-scale in the marine environment, and properly maintained. ii) Is combined technology such as desalination and electrolysis a possibility to efficiently produce H2 from seawater? iii) Can electrodialysis be deployed for large-scale CO2 extraction from seawater? iv) What kind of reactor material and systems engineering are required to realize a large, practical marine installation? If methanol is the end product, there is the need to look into the optimal design, including reactor looping and heat and pressure management, for a marine-based synthetic fuel reactor and separation system. These frontline questions need urgent technological answers.
The integration of direct CO2 air capture with CO2 and H2O as electrolyzers and a traditional methanol synthesis step in a process termed “air-to-barrel” has been proposed (Smith et al., 2019). The process uses CO2 electrolyzers to convert atmospheric CO2 into solar fuels using renewable electricity. This technology has the potential of producing 10,000 tons of methanol/day. The CO2 and water electrolyzers can replace the steam-methane reforming step of current methanol synthesis by producing CO and H2 from CO2 and H2O. Essentially, the carbon and hydrogen content of methane is replaced by CO2, H2O and solar energy.
Conclusion and Outlook
In this review, we have discussed the recent developments in the direct hydrogenation of carbon dioxide to methanol over the Cu/ZnO-based catalysts. No doubt, the Cu-based catalysts are still very promising for the direct hydrogenation of CO2 to methanol in the industry. Still, they need to be improved to overcome a series of technical problems. Many studies have been conducted to understand the catalyst structures and to enhance their functionalities. From the thermodynamical aspect, both low temperature and high pressure are favorable conditions for the methanol synthesis from CO2 reduction with hydrogen; however, low temperature is kinetically unfavorable for breaking the O–C–O bonds in CO2 molecule. High temperature increases the rate of RWGS and other side reactions, whereas high pressure is economically infeasible. It is a challenge to obtain both a high single-pass CO2 conversion and a high methanol selectivity with the current industrial catalyst via the direct CO2 hydrogenation. Consequently, developing Cu-based catalysts with high activity (high single-pass CO2 conversion and high selectivity to methanol) at lower temperatures and pressures are crucial for the CO2 to methanol hydrogenation.
With the Cu/ZnO/Al2O3 catalysts, the sintering of the Cu particles is a crucial problem. Thus, high mechanical strength and thermal stability are essential to maintain a long catalyst life under typical industrial conditions. These may be achieved by 1) use of confined catalysts, such as Cu or Cu/ZnO in porous materials, e.g., mesoporous SiO2 (SBA-15) and porous ZrO2; 2) use of binders in the catalyst composition which can boost both thermal stability and water resistance, and 3) deploying suitable synthesis methods and protocols, such as adding promoters to the base catalyst, forming promoted or multi-metallic catalysts
Besides the conventional methods for catalyst preparation, several other approaches are promising for the development of modified catalysts. These catalysts can be grouped into the following: 1) solid-solution derived catalysts, e.g., the solid solution of ZnZrOx is demonstrated to possess high selectivity and stability. Therefore, opportunities exist for even better performances of some other solid solutions for methanol synthesis from CO2. Several materials acting both as support or co-catalysts are effective as the traditional alumina in the Cu/ZnO/Al2O3. Specifically, ZrO2 is a good substitute for Al2O3 due to its excellent catalytic and surface properties; 2) catalysts derived from complex metal oxide compounds, e.g., hydrotalcite, perovskites, spinel compounds, MOFs, zeolites, etc. The catalysts derived from these compounds can have a high Cu dispersion and intimate contact among various catalyst components. For example, Cu or Cu/ZnO nanoparticles derived from perovskites and hydrotalcites through a proper reduction strategy may have high dispersion of Cu; MOFs and zeolite derived catalysts may have the well-defined component composition and ratio, and precise location, which should be suitable for the reaction and the clarification of the property-structure relations of the catalysts, as the well-defined structures can enable the understanding of how catalyst micro/macrostructure affects conversion and selectivity; 3) core–shell catalysts, e.g., Cu or Cu/ZnO with ZrO2 shells. The core–shell catalysts are highly thermally stable and could form efficient function-selective catalysts; 4) alloy and bi- or tri-metallic catalysts, and 5) metallic–nonmetallic hybrid systems.
It is believed that the CO2 reductive hydrogenation to methanol commonly proceeds mainly through two mechanisms—the RWGS (via *HOCO intermediate species) and the formate (via *HCOO intermediate species) pathways. While the former involves a CO intermediate followed by hydrogenation, in the latter, CO2 is initially hydrogenated to the formate species, further dissociating to methanol. The various active sites reported include metallic Cu, oxidized Cu, Zn decorated Cu, and isolated Cu–Zn interfaces. Although the active sites and reaction mechanisms have been explored and analyzed in the literature, yet, knowledge of the detailed structure of the catalysts is still lacking. Analytical approaches such as the in situ experimental measurements should be deployed to elucidate the active sites and reaction mechanisms. Theoretical calculations using multiscale modeling techniques should complement experiments to elucidate the structures of the traditional catalysts further and to improve the design of new ones. It should be kept in mind that a well-designed catalysts will catalyze the desired reaction but inhibit the side reactions. However, the design of suitable catalysts mainly depends on understanding the reaction mechanism and active site structures, and the advances in the catalyst preparation. Therefore, a comprehensive solution combining a fundamental understanding of catalysis with advanced catalyst preparation and process optimization is necessary.
The recycling of CO2 to renewable fuels and platform chemicals is an important aspect of CO2 mitigation. Methanol, a major liquid product of CO2 hydrogenation with hydrogen from renewable energy sources, can serve as a storage medium for future use of energy in various applications such as heating, cooking and transportation. New processes for renewable fuel production have been developed, such as “solar methanol island” involving CO2 from the marine environment in combination with catalysis, and “air-to-barrel” process, which uses CO2 electrolyzers to convert atmospheric CO2 into solar fuels. It is not yet developed a practical design of solar-powered artificial marine-islands to recycle CO2 into methanol and other synthetic liquid fuels. Several issues, including deployment at marine environment on large-scale, proper maintenance, efficient production of H2 from seawater, and the reactor requirements for practical marine installation need to deal with.
Author Contributions
UJE wrote the manuscript. YS revised the manuscript. ZZ organized, wrote and modified the manuscript.
Funding
This work is financially supported by 2020 Li Ka Shing Foundation Cross-Disciplinary Research Grant (2020LKSFG09A), Guangdong Province Key discipline fund (GTIIT), and Department of Education of Guangdong Province (2018KTSCX063).
Conflict of Interest
The authors declare that the research was conducted in the absence of any commercial or financial relationships that could be construed as a potential conflict of interest.
References
An, B., Zhang, J., Cheng, K., Ji, P., Wang, C., and Lin, W. (2017). Confinement of ultrasmall Cu/ZnOx nanoparticles in metal–organic frameworks for selective methanol synthesis from catalytic hydrogenation of CO2. J. Am. Chem. Soc. 139, 3834–3840. doi:10.1021/jacs.7b00058
An, X., Li, J., Zuo, Y., Zhang, Q., Wang, D., and Wang, J. (2007). A Cu/Zn/Al/Zr fibrous catalyst that is an improved CO2 hydrogenation to methanol catalyst. Catal. Lett. 118, 264–269. doi:10.1007/s10562-007-9182-x
Arcoumanis, C., Bae, C., Crookes, R., and Kinoshita, E. (2008). The potential of di-methyl ether (DME) as an alternative fuel for compression-ignition engines: a review. Fuel. 87, 1014–1030. doi:10.1016/j.fuel.2007.06.007
Arena, F., Barbera, K., Italiano, G., Bonura, G., Spadaro, L., and Frusteri, F. (2007). Synthesis, characterization and activity pattern of Cu–ZnO/ZrO2 catalysts in the hydrogenation of carbon dioxide to methanol. J. Catal. 249, 185–194. doi:10.1016/j.jcat.2007.04.003
Baiker, A., Kilo, M., Maciejewski, M., Menzi, S., and Wokaun, A. (1993). “Hydrogenation of CO2 over copper, silver and gold/zirconia catalysts: comparative study of catalyst properties and reaction pathways,” in Studies in surface science and catalysis. Editors L. Guczi, F. Solymosi, and P. Tétényi (New York, NY: Elsevier), Vol. 75, 1257–1272.
Baltes, C., Vukojevic, S., and Schüth, F. (2008). Correlations between synthesis, precursor, and catalyst structure and activity of a large set of CuO/ZnO/Al2O3 catalysts for methanol synthesis. J. Catal. 258, 334–344. doi:10.1016/j.jcat.2008.07.004
Bansode, A., and Urakawa, A. (2014). Towards full one-pass conversion of carbon dioxide to methanol and methanol-derived products. J. Catal. 309, 66–70. doi:10.1016/j.jcat.2013.09.005
Bartholomew, C. H. (2001). Mechanisms of catalyst deactivation. Appl. Catal. Gen. 212, 17–60. doi:10.1016/s0926-860x(00)00843-7
Behrens, M. (2015). Coprecipitation: an excellent tool for the synthesis of supported metal catalysts - from the understanding of the well known recipes to new materials. Catal. Today 246, 46–54. doi:10.1016/j.cattod.2014.07.050
Behrens, M. (2016). Promoting the synthesis of methanol: understanding the requirements for an industrial catalyst for the conversion of CO2. Angew. Chem. Int. Ed 55, 14906–14908. doi:10.1002/anie.201607600
Behrens, M., Brennecke, D., Girgsdies, F., Kißner, S., Trunschke, A., Nasrudin, N., et al. (2011). Understanding the complexity of a catalyst synthesis: co-precipitation of mixed Cu,Zn,Al hydroxycarbonate precursors for Cu/ZnO/Al2O3 catalysts investigated by titration experiments. Appl. Catal. Gen. 392, 93–102. doi:10.1016/j.apcata.2010.10.031
Behrens, M., Lolli, G., Muratova, N., Kasatkin, I., Hävecker, M., d’Alnoncourt, R. N., et al. (2013). The effect of Al-doping on ZnO nanoparticles applied as catalyst support. Phys. Chem. Chem. Phys. 15, 1374–1381. doi:10.1039/c2cp41680h
Behrens, M., and Schlögl, R. (2013). How to prepare a good Cu/ZnO catalyst or the role of solid state chemistry for the synthesis of nanostructured catalysts. Z. Anorg. Allg. Chem. 639, 2683–2695. doi:10.1002/zaac.201300356
Behrens, M., Studt, F., Kasatkin, I., Kühl, S., Hävecker, M., Abild-Pedersen, F., et al. (2012). The active site of methanol synthesis over Cu/ZnO/Al2O3 industrial catalysts. Science. 336, 893–897. doi:10.1126/science.1219831
Bertau, M., Offermanns, H., Plass, L., Schmidt, F., and Wernicke, H.-J. (2014). Methanol: the basic chemical and energy feedstock of the future. New York, NY: Springer.
Bo, Y., Yuesong, S., Yanwei, Z., Shubao, S., and Shemin, Z. (2016). Promotional effects of copper doping on Ti-Ce-Ox for selective catalytic reduction of NO by NH3 at low temperature. J. Rare Earths. 34, 268–275. doi:10.1016/S1002-0721(16)60024-8
Bonura, G., Arena, F., Mezzatesta, G., Cannilla, C., Spadaro, L., and Frusteri, F. (2011). Role of the ceria promoter and carrier on the functionality of Cu-based catalysts in the CO2-to-methanol hydrogenation reaction. Catal. Today 171, 251–256. doi:10.1016/j.cattod.2011.04.038
Boomer, E. H., and Morris, H. E. (1932). The hydrogen-carbon dioxide reaction. J. Am. Chem. Soc. 54, 407. doi:10.1021/ja01340a509
Bozzano, G., and Manenti, F. (2016). Efficient methanol synthesis: perspectives, technologies and optimization strategies. Prog. Energy Combust. Sci. 56, 71–105. doi:10.1016/j.pecs.2016.06.001
Chang, K., Wang, T., and Chen, J. G. (2017). Hydrogenation of CO2 to methanol over CuCeTiO catalysts. Appl. Catal. B Environ. 206, 704–711. doi:10.1016/j.apcatb.2017.01.076
Chang, K., Wang, T., and Chen, J. G. (2019). Methanol synthesis from CO2 hydrogenation over CuZnCeTi mixed oxide catalysts. Ind. Eng. Chem. Res. 58, 7922–7928. doi:10.1021/acs.iecr.9b00554
Chen, H. Y., Lau, S. P., Chen, L., Lin, J., Huan, C. H. A., Tan, K. L., et al. (1999). Synergism between Cu and Zn sites in Cu/Zn catalysts for methanol synthesis. Appl. Surf. Sci. 152, 193–199. doi:10.1016/s0169-4332(99)00317-7
Chen, K., Duan, X., Fang, H., Liang, X., and Yuan, Y. (2018). Selective hydrogenation of CO2 to methanol catalyzed by Cu supported on rod-like La2O2CO3. Catal. Sci. Technol. 8, 1062–1069. doi:10.1039/c7cy01998j
Chen, K., Fang, H., Wu, S., Liu, X., Zheng, J., Zhou, S., et al. (2019). CO2 hydrogenation to methanol over Cu catalysts supported on La-modified SBA-15: the crucial role of Cu–LaOx interfaces. Appl. Catal. B Environ. 251, 119–129. doi:10.1016/j.apcatb.2019.03.059
Chen, L., Si, Z., Wu, X., and Weng, D. (2014). DRIFT study of CuO–CeO2–TiO2 mixed oxides for NOx reduction with NH3 at low temperatures. ACS Appl. Mater. Interfaces. 6, 8134–8145. doi:10.1021/am5004969
Choi, E. J., Lee, Y. H., Lee, D.-W., Moon, D.-J., and Lee, K.-Y. (2017). Hydrogenation of CO2 to methanol over Pd–Cu/CeO2 catalysts. Mol. Catal. 434, 146–153. doi:10.1016/j.mcat.2017.02.005
Choi, Y., Futagami, K., Fujitani, T., and Nakamura, J. (2001). The role of ZnO in Cu/ZnO methanol synthesis catalysts - morphology effect or active site model? Appl. Catal. Gen. 208, 163–167. doi:10.1016/s0926-860x(00)00712-2
Clausen, B. S., Schiøtz, J., Gråbæk, L., Ovesen, C. V., Jacobsen, K. W., Nørskov, J. K., et al. (1994). Wetting/non-wetting phenomena during catalysis: evidence from in situ on-line EXAFS studies of Cu-based catalysts. Top. Catal. 1, 367–376. doi:10.1007/bf01492289
Dang, S., Yang, H., Gao, P., Wang, H., Li, X., Wei, W., et al. (2018). A review of research progress on heterogeneous catalysts for methanol synthesis from carbon dioxide hydrogenation. Catal. Today 330, 61–75. doi:10.1016/j.cattod.2018.04.021
Dasireddy, V. D. B. C., and Likozar, B. (2019). The role of copper oxidation state in Cu/ZnO/Al2O3 catalysts in CO2 hydrogenation and methanol productivity. Renew. Energy. 140, 452–460. doi:10.1016/j.renene.2019.03.073
Dasireddy, V. D. B. C., Neja, S. Š., and Blaž, L. (2018). Correlation between synthesis pH, structure and Cu/MgO/Al2O3 heterogeneous catalyst activity and selectivity in CO2 hydrogenation to methanol. J. CO2 Util. 28, 189–199. doi:10.1016/j.jcou.2018.09.002
Deerattrakul, V., Dittanet, P., Sawangphruk, M., and Kongkachuichay, P. (2016). CO2 hydrogenation to methanol using Cu-Zn catalyst supported on reduced graphene oxide nanosheets. J. CO2 Util 16, 104–113. doi:10.1016/j.jcou.2016.07.002
Denise, B., Cherifi, O., Bettahar, M. M., and Sneeden, R. P. A. (1989). Supported copper catalysts prepared from copper(II) formate. Appl. Catal 48, 365–372. doi:10.1016/s0166-9834(00)82805-5
Díez-Ramírez, J., Sánchez, P., Rodríguez-Gómez, A., Valverde, J. L., and Dorado, F. (2016). Carbon nanofiber-based palladium/zinc catalysts for the hydrogenation of carbon dioxide to methanol at atmospheric pressure. Ind. Eng. Chem. Res 55, 3556–3567. doi:10.1021/acs.iecr.6b00170
Din, I. U., Shaharun, M. S., Alotaibi, M. A., Alharthi, A. I., and Naeem, A. (2019). Recent developments on heterogeneous catalytic CO2 reduction to methanol. J. CO2 Util 34, 20–33. doi:10.1016/j.jcou.2019.05.036
Din, I. U., Shaharun, M. S., Naeem, A., Tasleem, S., and Rafie Johan, M. (2018). Carbon nanofibers based copper/zirconia catalysts for carbon dioxide hydrogenation to methanol: effect of copper concentration. Chem. Eng. J 334, 619–629. doi:10.1016/j.cej.2017.10.087
Dong, X., Li, F., Zhao, N., Xiao, F., Wang, J., and Tan, Y. (2016). CO2 hydrogenation to methanol over Cu/ZnO/ZrO2 catalysts prepared by precipitation-reduction method. Appl. Catal. B Environ. 191, 8–17. doi:10.1016/j.apcatb.2016.03.014
Dybbert, V., Fehr, S. M., Klein, F., Schaadt, A., Hoffmann, A., Frei, E., et al. (2019). Oxidative fluorination of Cu/ZnO methanol catalysts. Angew. Chem. Int. Ed. 58, 12935–12939. doi:10.1002/anie.201811267
Fan, Y. J., and Wu, S. F. (2016). A graphene-supported copper-based catalyst for the hydrogenation of carbon dioxide to form methanol. J. CO2 Util. 16, 150–156. doi:10.1016/j.jcou.2016.07.001
Fang, X., Men, Y., Wu, F., Zhao, Q., Singh, R., Xiao, P., et al. (2019). Improved methanol yield and selectivity from CO2 hydrogenation using a novel Cu-ZnO-ZrO2 catalyst supported on Mg-Al layered double hydroxide (LDH). J. CO2 Util. 29, 57–64. doi:10.1016/j.jcou.2018.11.006
Fichtl, M. B., Schlereth, D., Jacobsen, N., Kasatkin, I., Schumann, J., Behrens, M., et al. (2015). Kinetics of deactivation on Cu/ZnO/Al2O3 methanol synthesis catalysts. Appl. Catal. Gen. 502, 262–270. doi:10.1016/j.apcata.2015.06.014
Fierro, G., Lo Jacono, M., Inversi, M., Porta, P., Cioci, F., and Lavecchia, R. (1996). Study of the reducibility of copper in CuO–ZnO catalysts by temperature-programmed reduction. Appl. Catal. Gen. 137, 327–348. doi:10.1016/0926-860x(95)00311-8
Fiordaliso, E. M., Sharafutdinov, I., Carvalho, H. W. P., Grunwaldt, J.-D., Hansen, T. W., Chorkendorff, I., et al. (2015). Intermetallic GaPd2 nanoparticles on SiO2 for low-pressure CO2 hydrogenation to methanol: catalytic performance and in situ characterization. ACS Catal. 5, 5827–5836. doi:10.1021/acscatal.5b01271
Fisher, I. A., Woo, H. C., and Bell, A. T. (1997). Effects of zirconia promotion on the activity of Cu/SiO2 for methanol synthesis from CO/H2 and CO2/H2. Catal. Lett. 44, 11–17. doi:10.1023/a:1018916806816
Fox, E. B., Velu, S., Engelhard, M. H., Chin, Y.-H., Miller, J. T., Kropf, J., et al. (2008). Characterization of CeO2-supported Cu–Pd bimetallic catalyst for the oxygen-assisted water–gas shift reaction. J. Catal. 260, 358–370. doi:10.1016/j.jcat.2008.08.018
Fujita, S., Usui, M., Hanada, T., and Takezawa, N. (1995). Methanol synthesis from CO2-H2 and from CO-H2 under atmospheric pressure over Pd and Cu catalysts. React. Kinet. Catal. Lett. 56, 15–19. doi:10.1007/bf02066946
Fujitani, T., and Nakamura, J. (2000). The chemical modification seen in the Cu/ZnO methanol synthesis catalysts. Appl. Catal. Gen. 191, 111–129. doi:10.1016/s0926-860x(99)00313-0
Fujiwara, K., Tada, S., Honma, T., Sasaki, H., Nishijima, M., and Kikuchi, R. (2019). Influences of particle size and crystallinity of highly loaded CuO/ZrO2 on CO2 hydrogenation to methanol. AlChE J. 65, e16717. doi:10.1002/aic.16717
Gao, P., Li, F., Zhao, N., Xiao, F., Wei, W., Zhong, L., et al. (2013). Influence of modifier (Mn, La, Ce, Zr and Y) on the performance of Cu/Zn/Al catalysts via hydrotalcite-like precursors for CO2 hydrogenation to methanol. Appl. Catal. Gen. 468, 442–452. doi:10.1016/j.apcata.2013.09.026
Gao, P., Zhong, L., Zhang, L., Wang, H., Zhao, N., Wei, W., et al. (2015). Yttrium oxide modified Cu/ZnO/Al2O3 catalysts via hydrotalcite-like precursors for CO2 hydrogenation to methanol. Catal. Sci. Technol. 5, 4365–4377. doi:10.1039/c5cy00372e
Ghosh, S., Uday, V., Giri, A., and Srinivas, S. (2019). Biogas to methanol: a comparison of conversion processes involving direct carbon dioxide hydrogenation and via reverse water gas shift reaction. J. Clean. Prod. 217, 615–626. doi:10.1016/j.jclepro.2019.01.171
Goeppert, A., Czaun, M., Jones, J.-P., Surya Prakash, G. K., and Olah, G. A. (2014). Recycling of carbon dioxide to methanol and derived products - closing the loop. Chem. Soc. Rev. 43, 7995–8048. doi:10.1039/c4cs00122b
Gotti, A., and Prins, R. (1998). Basic metal oxides as cocatalysts for Cu/SiO2 catalysts in the conversion of synthesis gas to methanol. J. Catal. 178, 511–519. doi:10.1006/jcat.1998.2167
Grabow, L. C., and Mavrikakis, M. (2011). Mechanism of methanol synthesis on Cu through CO2 and CO hydrogenation. ACS Catal. 1, 365–384. doi:10.1021/cs200055d
Graciani, J., Mudiyanselage, K., Xu, F., Baber, A. E., Evans, J., Senanayake, S. D., et al. (2014). Highly active copper-ceria and copper-ceria-titania catalysts for methanol synthesis from CO2. Science 345, 546–550. doi:10.1126/science.1253057
Grandjean, D., Pelipenko, V., Batyrev, E. D., van den Heuvel, J. C., Khassin, A. A., Yurieva, T. M., et al. (2011). Dynamic Cu/Zn interaction in SiO2 supported methanol synthesis catalysts unraveled by in situ XAFS. J. Phys. Chem. C 115, 20175–20191. doi:10.1021/jp201839s
Guil-López, R., Mota, N., Llorente, J., Millán, E., Pawelec, B., Fierro, J. L. G., et al. (2019a). Methanol synthesis from CO2: a review of the latest developments in heterogeneous catalysis. Materials 12, 3902. doi:10.3390/ma12233902
Guil-López, R., Mota, N., Llorente, J., Millán, E., Pawelec, B., García, R., et al. (2019b). Structure and activity of Cu/ZnO catalysts co-modified with aluminium and gallium for methanol synthesis. Catal. Today. doi:10.1016/j.cattod.2019.03.034
Guo, X., Mao, D., Lu, G., Wang, S., and Wu, G. (2011). CO2 hydrogenation to methanol over Cu/ZnO/ZrO2 catalysts prepared via a route of solid-state reaction. Catal. Commun. 12, 1095–1098. doi:10.1016/j.catcom.2011.03.033
Guo, X., Mao, D., Wang, S., Wu, G., and Lu, G. (2009). Combustion synthesis of CuO–ZnO–ZrO2 catalysts for the hydrogenation of carbon dioxide to methanol. Catal. Commun. 10, 1661–1664. doi:10.1016/j.catcom.2009.05.004
Halder, A., Kilianová, M., Yang, B., Tyo, E. C., Seifert, S., Prucek, R., et al. (2018). Highly efficient Cu-decorated iron oxide nanocatalyst for low pressure CO2 conversion. Appl. Catal. B Environ. 225, 128–138. doi:10.1016/j.apcatb.2017.11.047
Hansen, J., Sato, M., Ruedy, R., Lo, K., Lea, D. W., and Medina-Elizade, M. (2006). Global temperature change. Proc. Natl. Acad. Sci. U.S.A. 103, 14288–14293. doi:10.1073/pnas.0606291103
Hartadi, Y., Widmann, D., and Behm, R. J. (2015). CO2 hydrogenation to methanol on supported Au catalysts under moderate reaction conditions: support and particle size effects. ChemSusChem. 8, 456–465. doi:10.1002/cssc.201402645
Herman, R., Klier, K., Simmons, G., Finn, B., Bulko, J. B., and Kobylinski, T. (1979). Catalytic synthesis of methanol from CO/H2I. Phase composition, electronic properties, and activities of the Cu/ZnO/M2O3 catalysts. J. Catal. 56, 407–429. doi:10.1016/0021-9517(79)90132-5
Hong, Z.-S., Cao, Y., Deng, J.-F., and Fan, K.-N. (2002). CO2 hydrogenation to methanol over Cu/ZnO/Al2O3 catalysts prepared by a novel gel-network-coprecipitation method. Catal. Lett. 82, 37–44. doi:10.1023/a:1020531822590
Hu, B., Yin, Y., Zhong, Z., Wu, D., Liu, G., and Hong, X. (2019). Cu@ZIF-82 derived inverse ZnO/Cu catalyst with sub-5 nm ZnO for efficient CO2 hydrogenation to methanol. Catal. Sci. Technol. 9, 2673–2681. doi:10.1039/c8cy02546k
Hu, X., Qin, W., Guan, Q., and Li, W. (2018). The synergistic effect of CuZnCeOx in controlling the formation of methanol and CO from CO2 hydrogenation. ChemCatChem. 10, 4438–4449. doi:10.1002/cctc.201800668
Hu, Z., Kunimori, K., and Uchijima, T. (1991). Interaction of hydrogen and oxygen with niobia-supported and niobia-promoted rhodium catalysts. Appl. Catal. 69, 253–268. doi:10.1016/s0166-9834(00)83306-0
Huš, M., Dasireddy, V. D., Štefančič, N. S., and Likozar, B. (2017a). Mechanism, kinetics and thermodynamics of carbon dioxide hydrogenation to methanol on Cu/ZnAl2O4 spinel-type heterogeneous catalysts. Appl. Catal. B Environ. 207, 267–278. doi:10.1016/j.apcatb.2017.01.077
Huš, M., Kopač, D., Štefančič, N. S., Jurković, D. L., Dasireddy, V. D., and Likozar, B. (2017b). Unravelling the mechanisms of CO2 hydrogenation to methanol on Cu-based catalysts using first-principles multiscale modelling and experiments. Catal. Sci. Technol. 7, 5900–5913. doi:10.1039/C7CY01659J
Iizuka, T., Kojima, M., and Tanabe, K. (1983). Support effects in the formation of methanol from carbon dioxide and hydrogen over rhenium catalysts. J. Chem. Soc. Chem. Commun. 638–639. doi:10.1039/c39830000638
Inoue, T., and Iizuka, T. (1986). Hydrogenation of carbon dioxide and carbon monoxide over supported platinum catalysts. J. Chem. Soc. Faraday Trans. 1, 1681–1686. doi:10.1039/f19868201681
Ipatieff, V. N., and Monroe, G. S. (1945). Synthesis of methanol from carbon dioxide and hydrogen over copper-alumina catalysts. Mechanism of reaction. J. Am. Chem. Soc. 67, 2168–2171. doi:10.1021/ja01228a032
Jadhav, S. G., Vaidya, P. D., Bhanage, B. M., and Joshi, J. B. (2014). Catalytic carbon dioxide hydrogenation to methanol: a review of recent studies. Chem. Eng. Res. Des. 92, 2557–2567. doi:10.1016/j.cherd.2014.03.005
Jia, C., Gao, J., Dai, Y., Zhang, J., and Yang, Y. (2016). The thermodynamics analysis and experimental validation for complicated systems in CO2 hydrogenation process. J. Energy Chem. 25, 1027–1037. doi:10.1016/j.jechem.2016.10.003
Jiang, X., Jiao, Y., Moran, C., Nie, X., Gong, Y., Guo, X., et al. (2019a). CO2 hydrogenation to methanol on Pd–Cu bimetallic catalysts with lower metal loadings. Catal. Commun. 118, 10–14. doi:10.1016/j.catcom.2018.09.006
Jiang, X., Koizumi, N., Guo, X., and Song, C. (2015). Bimetallic Pd–Cu catalysts for selective CO2 hydrogenation to methanol. Appl. Catal. B Environ. 170–171, 173–185. doi:10.1016/j.apcatb.2015.01.010
Jiang, X., Nie, X., Wang, X., Wang, H., Koizumi, N., Chen, Y., et al. (2019b). Origin of Pd-Cu bimetallic effect for synergetic promotion of methanol formation from CO2 hydrogenation. J. Catal. 369, 21–32. doi:10.1016/j.jcat.2018.10.001
Jiang, Y., Yang, H., Gao, P., Li, X., Zhang, J., Liu, H., et al. (2018). Slurry methanol synthesis from CO2 hydrogenation over micro-spherical SiO2 support Cu/ZnO catalysts. J. CO2 Util. 26, 642–651. doi:10.1016/j.jcou.2018.06.023
Jurković, D. L., Prašnikar, A., Pohar, A., and Likozar, B. (2020). Surface structure-based CO2 reduction reaction modelling over supported copper catalysts. J. CO2 Util. 41, 101234. doi:10.1016/j.jcou.2020.101234
Kanai, Y., Watanabe, T., Fujitani, T., Uchijima, T., and Nakamura, J. (1996). The synergy between Cu and ZnO in methanol synthesis catalysts. Catal. Lett. 38, 157–163. doi:10.1007/bf00806562
Karelovic, A., Galdames, G., Medina, J. C., Yévenes, C., Barra, Y., and Jiménez, R. (2019). Mechanism and structure sensitivity of methanol synthesis from CO2 over SiO2-supported Cu nanoparticles. J. Catal. 369, 415–426. doi:10.1016/j.jcat.2018.11.012
Karl, T. R., and Trenberth, K. E. (2003). Modern global climate change. Science 302, 1719–1723. doi:10.1126/science.1090228
Kasatkin, I., Kurr, P., Kniep, B., Trunschke, A., and Schlögl, R. (2007). Role of lattice strain and defects in copper particles on the activity of Cu/ZnO/Al2O3 catalysts for methanol synthesis. Angew. Chem. Int. Ed. 46, 7324–7327. doi:10.1002/anie.200702600
Kattel, S., Liu, P., and Chen, J. G. (2017a). Tuning selectivity of CO2 hydrogenation reactions at the metal/oxide interface. J. Am. Chem. Soc. 139, 9739–9754. doi:10.1021/jacs.7b05362
Kattel, S., Ramírez, P. J., Chen, J. G., Rodriguez, J. A., and Liu, P. (2017b). Active sites for CO2 hydrogenation to methanol on Cu/ZnO catalysts. Science 355, 1296–1299. doi:10.1126/science.aal3573
Kattel, S., Yan, B., Yang, Y., Chen, J. G., and Liu, P. (2016). Optimizing binding energies of key intermediates for CO2 hydrogenation to methanol over oxide-supported copper. J. Am. Chem. Soc. 138, 12440–12450. doi:10.1021/jacs.6b05791
Kniep, B. L., Ressler, T., Rabis, A., Girgsdies, F., Baenitz, M., Steglich, F., et al. (2004). Rational design of nanostructured copper–zinc oxide catalysts for the steam reforming of methanol. Angew. Chem. Int. Ed. 43, 112–115. doi:10.1002/anie.200352148
Koh, M. K., Zain, M. M., and Mohamed, A. R. (2019). “Exploring transition metal (Cr, Mn, Fe, Co, Ni) promoted copper-catalyst for carbon dioxide hydrogenation to methanol,” in Paper presented at the AIP Conference Proceedings. doi:10.1063/1.5117066
Koitaya, T., Yamamoto, S., Shiozawa, Y., Yoshikura, Y., Hasegawa, M., Tang, J., et al. (2019). CO2 activation and reaction on Zn-deposited Cu surfaces studied by ambient-pressure X-ray photoelectron spectroscopy. ACS Catal. 9, 4539–4550. doi:10.1021/acscatal.9b00041
Kondrat, S. A., Smith, P. J., Carter, J. H., Hayward, J. S., Pudge, G. J., Shaw, G., et al. (2017). The effect of sodium species on methanol synthesis and water–gas shift Cu/ZnO catalysts: utilising high purity zincian georgeite. Faraday Discuss 197, 287–307. doi:10.1039/c6fd00202a
Kopač, D., Huš, M., Ogrizek, M., and Likozar, B. (2017). Kinetic Monte Carlo simulations of methanol synthesis from carbon dioxide and hydrogen on Cu(111) catalysts: statistical uncertainty study. J. Phys. Chem. C 121, 17941–17949. doi:10.1021/acs.jpcc.7b04985
Kopač, D., Likozar, B., and Huš, M. (2019). Catalysis of material surface defects: multiscale modeling of methanol synthesis by CO2 reduction on copper. Appl. Surf. Sci. 497, 143783.
10.1016/j.apsusc.2019.143783CrossRef Full Text | Google Scholar
Kugai, J., Miller, J. T., Fox, E. B., and Song, C. (2016). In-situ X-ray absorption study of ceria-supported Pd-Cu nanoparticles for oxygen-enhanced water gas shift. Appl. Catal. Gen. 528, 67–73. doi:10.1016/j.apcata.2016.09.010
Kung, H. H. (1992). Deactivation of methanol synthesis catalysts - a review. Catal. Today 11, 443–453. doi:10.1016/0920-5861(92)80037-n
Kunkes, E. L., Studt, F., Abild-Pedersen, F., Schlögl, R., and Behrens, M. (2015). Hydrogenation of CO2 to methanol and CO on Cu/ZnO/Al2O3: is there a common intermediate or not? J. Catal. 328, 43–48. doi:10.1016/j.jcat.2014.12.016
Lachowska, M., and Skrzypek, J. (2004). Methanol synthesis from carbon dioxide and hydrogen over Mn-promoted copper/zinc/zirconia catalysts. React. Kinet. Catal. Lett. 83, 269–273. doi:10.1023/b:reac.0000046086.93121.36
Larmier, K., Liao, W.-C., Tada, S., Lam, E., Verel, R., Bansode, A., et al. (2017). CO2 -to-methanol hydrogenation on zirconia-supported copper nanoparticles: reaction intermediates and the role of the metal-support interface. Angew. Chem. Int. Ed. 56, 2318–2323. doi:10.1002/anie.201610166
Lee, J. S., Han, S. H., Kim, H. G., Lee, K. H., and Kim, Y. G. (2000). Effects of space velocity on methanol synthesis from CO2/CO/H2 over Cu/ZnO/Al2O3 catalyst. Kor. J. Chem. Eng. 17, 332–336. doi:10.1007/bf02699049
Lee, W. J., Bordoloi, A., Patel, J., and Bhatelia, T. (2020). The effect of metal additives in Cu/Zn/Al2O3 as a catalyst for low-pressure methanol synthesis in an oil-cooled annulus reactor. Catal. Today 343, 183–190. doi:10.1016/j.cattod.2019.03.041
Lei, H., Nie, R., Wu, G., and Hou, Z. (2015). Hydrogenation of CO2 to CH3OH over Cu/ZnO catalysts with different ZnO morphology. Fuel 154, 161–166. doi:10.1016/j.fuel.2015.03.052CrossRef Full Text |
Li, C., Yuan, X., and Fujimoto, K. (2014). Development of highly stable catalyst for methanol synthesis from carbon dioxide. Appl. Catal. Gen. 469, 306–311. doi:10.1016/j.apcata.2013. doi:10.010
Li, J.-L., and Inui, T. (1996). Characterization of precursors of methanol synthesis catalysts, copper/zinc/aluminum oxides, precipitated at different pHs and temperatures. Appl. Catal. Gen. 137, 105–117. doi:10.1016/0926-860x(95)00284-7
Li, K., and Chen, J. G. (2019). CO2 hydrogenation to methanol over ZrO2-containing catalysts: insights into ZrO2 induced synergy. ACS Catal. 9, 7840–7861. doi:10.1021/acscatal.9b01943
Li, M. M.-J., Chen, C., Ayvalı, T., Suo, H., Zheng, J., Teixeira, I. F., et al. (2018). CO2 hydrogenation to methanol over catalysts derived from single cationic layer CuZnGa LDH precursors. ACS Catal. 8, 4390–4401. doi:10.1021/acscatal.8b00474
Li, M. M.-J., Zeng, Z., Liao, F., Hong, X., and Tsang, S. C. E. (2016). Enhanced CO2 hydrogenation to methanol over CuZn nanoalloy in Ga modified Cu/ZnO catalysts. J. Catal. 343, 157–167. doi:10.1016/j.jcat.2016.03.020
Li, S., Guo, L., and Ishihara, T. (2020). Hydrogenation of CO2 to methanol over Cu/AlCeO catalyst. Catal. Today 339, 352–361. doi:10.1016/j.cattod.2019.01.015
Li, S., Wang, Y., Yang, B., and Guo, L. (2019). A highly active and selective mesostructured Cu/AlCeO catalyst for CO2 hydrogenation to methanol. Appl. Catal. Gen. 571, 51–60. doi:10.1016/j.apcata.2018.12.008
Li, Y., Chan, S. H., and Sun, Q. (2015). Heterogeneous catalytic conversion of CO2: a comprehensive theoretical review. Nanoscale 7, 8663–8683. doi:10.1039/c5nr00092k
Liang, B., Ma, J., Su, X., Yang, C., Duan, H., Zhou, H., et al. (2019). Investigation on deactivation of Cu/ZnO/Al2O3 catalyst for CO2 hydrogenation to methanol. Ind. Eng. Chem. Res. 58, 9030–9037. doi:10.1021/acs.iecr.9b01546
Liang, Z., Gao, P., Tang, Z., Lv, M., and Sun, Y. (2017). Three dimensional porous Cu-Zn/Al foam monolithic catalyst for CO2 hydrogenation to methanol in microreactor. J. CO2 Util. 21, 191–199. doi:10.1016/j.jcou.2017.05.023
Liao, F., Huang, Y., Ge, J., Zheng, W., Tedsree, K., Collier, P., et al. (2011). Morphology-dependent interactions of ZnO with Cu nanoparticles at the materials’ interface in selective hydrogenation of CO2 to CH3OH. Angew. Chem. Int. Ed. 50, 2162–2165. doi:10.1002/anie.201007108
Lin, L., Yao, S., Rui, N., Han, L., Zhang, F., Gerlak, C., et al. (2019). Conversion of CO2 on a highly active and stable Cu/FeOx/CeO2 catalyst: tuning catalytic performance by oxide-oxide interactions. Catal. Sci. Technol. 9, 3735–3742. doi:10.1039/C9CY00722A
Liu, C., and Liu, P. (2015). Mechanistic study of methanol synthesis from CO2 and H2 on a modified model Mo6S8 cluster. ACS Catal. 5, 1004–1012. doi:10.1021/cs501354b
Liu, G., Willcox, D., Garland, M., and Kung, H. H. (1985). The role of CO2 in methanol synthesis on Cu-Zn oxide: an isotope labeling study. J. Catal. 96, 251–260. doi:10.1016/0021-9517(85)90378-1
Liu, L., Su, X., Zhang, H., Gao, N., Xue, F., Ma, Y., et al. (2020). Zirconia-modified copper catalyst for CO2 conversion to methanol from DFT study. Appl. Surf. Sci. 528, 146900. doi:10.1016/j.apsusc.2020.146900
Liu, X., Song, Y., Geng, W., Li, H., Xiao, L., and Wu, W. (2016). Cu-Mo2C/MCM-41: an efficient catalyst for the selective synthesis of methanol from CO2. Catalysts 6, 75. doi:10.3390/catal6050075
Liu, X.-M., Lu, G. Q., Yan, Z.-F., and Beltramini, J. (2003). Recent advances in catalysts for methanol synthesis via hydrogenation of CO and CO2. Ind. Eng. Chem. Res. 42, 6518–6530. doi:10.1021/ie020979s
Liu, Y., Zhang, Y., Wang, T., and Tsubaki, N. (2007). Efficient conversion of carbon dioxide to methanol using copper catalyst by a new low-temperature hydrogenation process. Chem. Lett. 36, 1182–1183. doi:10.1246/cl.2007.1182
Lunkenbein, T., Girgsdies, F., Kandemir, T., Thomas, N., Behrens, M., Schlögl, R., et al. (2016). Bridging the time gap: a copper/zinc oxide/aluminum oxide catalyst for methanol synthesis studied under industrially relevant conditions and time scales. Angew. Chem. Int. Ed. 55, 12708–12712. doi:10.1002/anie.201603368
Lunkenbein, T., Schumann, J., Behrens, M., Schlögl, R., and Willinger, M. G. (2015). formation of a ZnO overlayer in industrial Cu/ZnO/Al2O3 catalysts induced by strong metal-support interactions. Angew. Chem. Int. Ed. 54, 4544–4548. doi:10.1002/anie.201411581
Ma, J., Sun, N., Zhang, X., Zhao, N., Xiao, F., Wei, W., et al. (2009). A short review of catalysis for CO2 conversion. Catal. Today 148, 221–231. doi:10.1016/j.cattod.2009.08.015
Malik, M. I., Malaibari, Z. O., Atieh, M., and Abussaud, B. (2016). Electrochemical reduction of CO2 to methanol over MWCNTs impregnated with Cu2O. Chem. Eng. Sci. 152, 468–477. doi:10.1016/j.ces.2016.06.035
Marsden, W. L., Wainwright, M. S., and Friedrich, J. B. (1980). Zinc-promoted Raney copper catalysts for methanol synthesis. Ind. Eng. Chem. Prod. Res. Dev. 19, 551–556. doi:10.1021/i360076a014
Matějová, L., Kočí, K., Reli, M., Čapek, L., Hospodková, A., Peikertová, P., et al. (2014). Preparation, characterization and photocatalytic properties of cerium doped TiO2: on the effect of Ce loading on the photocatalytic reduction of carbon dioxide. Appl. Catal. B Environ. 152, 172–183. doi:10.1016/j.apcatb.2014.01.015
McGrath, K. M., Prakash, G. S., and Olah, G. A. (2004). Direct methanol fuel cells. J. Ind. Eng. Chem. 10, 1063–1080.Google Scholar
Melián-Cabrera, I., Granados, M. L., and Fierro, J. (2002). Reverse topotactic transformation of a Cu–Zn–Al catalyst during wet Pd impregnation: relevance for the performance in methanol synthesis from CO2/H2 mixtures. J. Catal. 210, 273–284. doi:10.1006/jcat.2002.3676
Meshkini, F., Taghizadeh, M., and Bahmani, M. (2010). Investigating the effect of metal oxide additives on the properties of Cu/ZnO/Al2O3 catalysts in methanol synthesis from syngas using factorial experimental design. Fuel 89, 170–175. doi:10.1016/j.fuel.2009.07.007
Mota, N., Guil-Lopez, R., Pawelec, B. G., Fierro, J. L. G., and Navarro, R. M. (2018). Highly active Cu/ZnO–Al catalyst for methanol synthesis: effect of aging on its structure and activity. RSC Adv. 8, 20619–20629. doi:10.1039/c8ra03291b
Mureddu, M., Ferrara, F., and Pettinau, A. (2019). Highly efficient CuO/ZnO/ZrO2@SBA-15 nanocatalysts for methanol synthesis from the catalytic hydrogenation of CO2. Appl. Catal. B Environ. 258, 117941. doi:10.1016/j.apcatb.2019.117941
Mutschler, R., Moioli, E., Luo, W., Gallandat, N., and Züttel, A. (2018). CO2 hydrogenation reaction over pristine Fe, Co, Ni, Cu and Al2O3 supported Ru: comparison and determination of the activation energies. J. Catal. 366, 139–149. doi:10.1016/j.jcat.2018.08.002
Nakamura, J., Choi, Y., and Fujitani, T. (2003). On the issue of the active site and the role of ZnO in Cu/ZnO methanol synthesis catalysts. Top. Catal. 22, 277–285. doi:10.1023/A:1023588322846
Natesakhawat, S., Lekse, J. W., Baltrus, J. P., Ohodnicki, P. R., Howard, B. H., Deng, X., et al. (2012). Active sites and structure-activity relationships of copper-based catalysts for carbon dioxide hydrogenation to methanol. ACS Catal. 2, 1667–1676. doi:10.1021/cs300008g
Nie, X., Jiang, X., Wang, H., Luo, W., Janik, M. J., Chen, Y., et al. (2018). Mechanistic understanding of alloy effect and water promotion for Pd-Cu bimetallic catalysts in CO2 hydrogenation to methanol. ACS Catal. 8, 4873–4892. doi:10.1021/acscatal.7b04150
Nitta, Y., Suwata, O., Ikeda, Y., Okamoto, Y., and Imanaka, T. (1994). Copper-zirconia catalysts for methanol synthesis from carbon dioxide: effect of ZnO addition to Cu-ZrO2 catalysts. Catal. Lett. 26, 345–354. doi:10.1007/bf00810608
Ojelade, O. A., and Zaman, S. F. (2020). A review on Pd based catalysts for CO2 hydrogenation to methanol: in-depth activity and DRIFTS mechanistic study. Catal. Surv. Asia, 24, 11–37. doi:10.1007/s10563-019-09287-z
Olah, G. A. (2005). Beyond oil and gas: the methanol economy. Angew. Chem. Int. Ed. 44, 2636–2639. doi:10.1002/anie.200462121
Olah, G. A. (2013). Towards oil independence through renewable methanol chemistry. Angew. Chem. Int. Ed. 52, 104–107. doi:10.1002/anie.201204995
Omata, K., Hashimoto, M., Watanabe, Y., Umegaki, T., Wagatsuma, S., Ishiguro, G., et al. (2004). Optimization of Cu oxide catalyst for methanol synthesis under high CO2 partial pressure using combinatorial tools. Appl. Catal. Gen. 262, 207–214. doi:10.1016/j.apcata.2003.11.028
Ouda, M., Hank, C., Nestler, F., Hadrich, M., Full, J., Schaadt, A., et al. (2019). “Power-to-methanol: techno-economical and ecological insights,” in Zukünftige Kraftstoffe: energiewende des Transports als ein weltweites Klimaziel. Editor W. Maus (Berlin, Heidelberg: Springer), 380–409.
Park, J., Kim, H. S., Lee, W. B., and Park, M.-J. (2020). Trends and outlook of computational chemistry and microkinetic modeling for catalytic synthesis of methanol and DME. Catalysts 10, 655. doi:10.3390/catal10060655
Patterson, B. D., Mo, F., Borgschulte, A., Hillestad, M., Joos, F., Kristiansen, T., et al. (2019). Renewable CO2 recycling and synthetic fuel production in a marine environment. Proc. Natl. Acad. Sci. U.S.A 116, 12212–12219. doi:10.1073/pnas.1902335116
Pavlišič, A., Huš, M., Prašnikar, A., and Likozar, B. (2020). Multiscale modelling of CO2 reduction to methanol over industrial Cu/ZnO/Al2O3 heterogeneous catalyst: linking ab initio surface reaction kinetics with reactor fluid dynamics. J. Clean. Prod. 275, 122958. doi:10.1016/j.jclepro.2020.122958
Phongamwong, T., Chantaprasertporn, U., Witoon, T., Numpilai, T., Poo-Arporn, Y., Limphirat, W., et al. (2017). CO2 hydrogenation to methanol over CuO–ZnO–ZrO2–SiO2 catalysts: effects of SiO2 contents. Chem. Eng. J 316, 692–703. doi:10.1016/j.cej.2017.02.010
Ponce, A. A., and Klabunde, K. J. (2005). Chemical and catalytic activity of copper nanoparticles prepared via metal vapor synthesis. J. Mol. Catal. Chem. 225, 1–6. doi:10.1016/j.molcata.2004.08.019
Porosoff, M. D., Yan, B., and Chen, J. G. (2016). Catalytic reduction of CO2 by H2 for synthesis of CO, methanol and hydrocarbons: challenges and opportunities. Energy Environ. Sci. 9, 62–73. doi:10.1039/c5ee02657a
Prašnikar, A. E., Pavlišič, A., Ruiz-Zepeda, F., Kovač, J., and Likozar, B. (2019). Mechanisms of copper-based catalyst deactivation during CO2 reduction to methanol. Ind. Eng. Chem. Res. 58, 13021–13029. doi:10.1021/acs.iecr.9b01898
Ren, Z.-X., Wang, J., Jia, J.-J., and Lu, D.-S. (1989). Effect of carbon dioxide on methanol synthesis over different catalysts. Appl. Catal. 49, 83–90. doi:10.1016/s0166-9834(00)81424-4
Renken, A., and Kiwi-Minsker, L. (2010). “Microstructured catalytic reactors,” in Advances in catalysis. Editors B. C. Gates, and H. Knözinger (New York, NY: Elsevier), Vol. 53, 47–122.
Roberts, G. W., Brown, D. M., Hsiung, T. H., and Lewnard, J. J. (1993). Deactivation of methanol synthesis catalysts. Ind. Eng. Chem. Res. 32, 1610–1621. doi:10.1021/ie00020a012
Rodriguez, J. A., Liu, P., Stacchiola, D. J., Senanayake, S. D., White, M. G., and Chen, J. G. (2015). Hydrogenation of CO2 to methanol: importance of metal–oxide and metal–carbide interfaces in the activation of CO2. ACS Catal. 5, 6696–6706. doi:10.1021/acscatal.5b01755
Rungtaweevoranit, B., Baek, J., Araujo, J. R., Archanjo, B. S., Choi, K. M., Yaghi, O. M., et al. (2016). Copper nanocrystals encapsulated in Zr-based metal–organic frameworks for highly selective CO2 hydrogenation to methanol. Nano Lett. 16, 7645–7649. doi:10.1021/acs.nanolett.6b03637
Sahibzada, M., Metcalfe, I. S., and Chadwick, D. (1998). Methanol synthesis from CO/CO2/H2 over Cu/ZnO/Al2O3 at differential and finite conversions. J. Catal. 174, 111–118. doi:10.1006/jcat.1998.1964
Saito, M., Fujitani, T., Takeuchi, M., and Watanabe, T. (1996). Development of copper/zinc oxide-based multicomponent catalysts for methanol synthesis from carbon dioxide and hydrogen. Appl. Catal. Gen. 138, 311–318. doi:10.1016/0926-860x(95)00305-3
Sanches, S. G., Flores, J. H., De Avillez, R. R., and Pais da Silva, M. I. (2012). Influence of preparation methods and Zr and Y promoters on Cu/ZnO catalysts used for methanol steam reforming. Int. J. Hydrogen Energy 37, 6572–6579. doi:10.1016/j.ijhydene.2012.01.033
Schumann, J., Lunkenbein, T., Tarasov, A., Thomas, N., Schlögl, R., and Behrens, M. (2014). Synthesis and characterisation of a highly active Cu/ZnO: Al catalyst. ChemCatChem. 6, 2889–2897. doi:10.1002/cctc.201402278
Schumann, J., Tarasov, A., Thomas, N., Schlögl, R., and Behrens, M. (2016). Cu,Zn-based catalysts for methanol synthesis: on the effect of calcination conditions and the part of residual carbonates. Appl. Catal. Gen. 516, 117–126. doi:10.1016/j.apcata.2016.01.037
Sehested, J. (2019). Industrial and scientific directions of methanol catalyst development. J. Catal. 371, 368–375. doi:10.1016/j.jcat.2019.02.002
Semelsberger, T. A., Borup, R. L., and Greene, H. L. (2006). Dimethyl ether (DME) as an alternative fuel. J. Power Sources 156, 497–511. doi:10.1016/j.jpowsour.2005.05.082
Senanayake, S. D., Ramírez, P. J., Waluyo, I., Kundu, S., Mudiyanselage, K., Liu, Z., et al. (2016). Hydrogenation of CO2 to methanol on CeOx/Cu(111) and ZnO/Cu(111) catalysts: role of the metal–oxide interface and importance of Ce3+ sites. J. Phys. Chem. C 120, 1778–1784. doi:10.1021/acs.jpcc.5b12012
Shi, Z., Tan, Q., and Wu, D. (2019). Enhanced CO2 hydrogenation to methanol over TiO2 nanotubes-supported CuO-ZnO-CeO2 catalyst. Appl. Catal. Gen. 581, 58–66. doi:10.1016/j.apcata.2019.05.019
Słoczyński, J., Grabowski, R., Kozłowska, A., Olszewski, P., Lachowska, M., Skrzypek, J., et al. (2003). Effect of Mg and Mn oxide additions on structural and adsorptive properties of Cu/ZnO/ZrO2 catalysts for the methanol synthesis from CO2. Appl. Catal. Gen. 249, 129–138. doi:10.1016/S0926-860X(03)00191-1
Słoczyński, J., Grabowski, R., Kozłowska, A., Olszewski, P., Stoch, J., Skrzypek, J., et al. (2004). Catalytic activity of the M/(3ZnO·ZrO2) system (M = Cu, Ag, Au) in the hydrogenation of CO2 to methanol. Appl. Catal. Gen. 278, 11–23. doi:10.1016/j.apcata.2004.09.014
Słoczyński, J., Grabowski, R., Olszewski, P., Kozłowska, A., Stoch, J., Lachowska, M., et al. (2006). Effect of metal oxide additives on the activity and stability of Cu/ZnO/ZrO2 catalysts in the synthesis of methanol from CO2 and H2. Appl. Catal. Gen. 310, 127–137. doi:10.1016/j.apcata.2006.05.035
Smith, D. F., and Hirst, L. L. (1930). Reactions that occur on a methanol catalyst. Ind. Eng. Chem. 22, 1037–1040. doi:10.1021/ie50250a009
Smith, W. A., Burdyny, T., Vermaas, D. A., and Geerlings, H. (2019). Pathways to industrial-scale fuel out of thin air from CO2 electrolysis. Joule 3, 1822–1834. doi:10.1016/j.joule.2019.07.009
Spencer, M. (1999). The role of zinc oxide in Cu/ZnO catalysts for methanol synthesis and the water–gas shift reaction. Top. Catal. 8, 259–266. doi:10.1023/A:1019181715731
Stangeland, K., Li, H., and Yu, Z. (2018). Thermodynamic analysis of chemical and phase equilibria in CO2 hydrogenation to methanol, dimethyl ether, and higher alcohols. Ind. Eng. Chem. Res. 57, 4081–4094. doi:10.1021/acs.iecr.7b04866
Studt, F., Behrens, M., Kunkes, E. L., Thomas, N., Zander, S., Tarasov, A., et al. (2015). The mechanism of CO and CO2 hydrogenation to methanol over Cu-based catalysts. ChemCatChem. 7, 1105–1111. doi:10.1002/cctc.201500123
Studt, F., Sharafutdinov, I., Abild-Pedersen, F., Elkjær, C. F., Hummelshøj, J. S., Dahl, S., et al. (2014). Discovery of a Ni-Ga catalyst for carbon dioxide reduction to methanol. Nat. Chem. 6, 320. doi:10.1038/nchem.1873
Sugawa, S., Sayama, K., Okabe, K., and Arakawa, H. (1995). Methanol synthesis from CO2 and H2 over silver catalyst. Energy Convers. Manag. 36, 665–668. doi:10.1016/0196-8904(95)00093-s
Sun, K., Lu, W., Qiu, F., Liu, S., and Xu, X. (2003). Direct synthesis of DME over bifunctional catalyst: surface properties and catalytic performance. Appl. Catal. Gen. 252, 243–249. doi:10.1016/s0926-860x(03)00466-6
Sun, Y., Chen, L., Bao, Y., Wang, G., Zhang, Y., Fu, M., et al. (2018). Roles of nitrogen species on nitrogen-doped CNTs supported Cu-ZrO2 system for carbon dioxide hydrogenation to methanol. Catal. Today 307, 212–223. doi:10.1016/j.cattod.2017.04.017
Supp, E. (1973). Technology of Lurgi’s low pressure methanol process. http://pascal-francis.inist.fr/vibad/index.php?action=getRecordDetail&idt=PASCAL7388012182
Tada, S., Kayamori, S., Honma, T., Kamei, H., Nariyuki, A., Kon, K., et al. (2018). Design of interfacial sites between Cu and amorphous ZrO2 dedicated to CO2-to-Methanol hydrogenation. ACS Catal. 8, 7809–7819. doi:10.1021/acscatal.8b01396
Tang, Q.-L., Hong, Q.-J., and Liu, Z.-P. (2009). CO2 fixation into methanol at Cu/ZrO2 interface from first principles kinetic Monte Carlo. J. Catal. 263, 114–122. doi:10.1016/j.jcat.2009.01.017
Toyir, J., de la Piscina, P. R., Fierro, J. L. G., and Homs, N. (2001). Highly effective conversion of CO2 to methanol over supported and promoted copper-based catalysts: influence of support and promoter. Appl. Catal. B Environ. 29, 207–215. doi:10.1016/s0926-3373(00)00205-8
Toyir, J., Miloua, R., Elkadri, N. E., Nawdali, M., Toufik, H., Miloua, F., et al. (2009). Sustainable process for the production of methanol from CO2 and H2 using Cu/ZnO-based multicomponent catalyst. Phys. Procedia. 2, 1075–1079. doi:10.1016/j.phpro.2009.11.065
Twigg, M. V., and Spencer, M. S. (2001). Deactivation of supported copper metal catalysts for hydrogenation reactions. Appl. Catal. Gen. 212, 161–174. doi:10.1016/s0926-860x(00)00854-1
Ushikoshi, K., Moria, K., Watanabe, T., Takeuchi, M., and Saito, M. (1998). “A 50 kg/day class test plant for methanol synthesis from CO2 and H2,” in Studies in surface science and catalysis. Editors T. Inui, M. Anpo, K. Izui, S. Yanagida, and T. Yamaguchi (New York, NY: Elsevier), Vol. 114, 357–362.
Waller, D., Stirling, D., Stone, F. S., and Spencer, M. S. (1989). Copper–zinc oxide catalysts. Activity in relation to precursor structure and morphology. Faraday Discuss. Chem. Soc. 87, 107–120. doi:10.1039/dc9898700107
Wang, F., Wei, M., Evans, D. G., and Duan, X. (2016). CeO2-based heterogeneous catalysts toward catalytic conversion of CO2. J. Mater. Chem. 4, 5773–5783. doi:10.1039/c5ta10737g
Wang, G., Chen, L., Sun, Y., Wu, J., Fu, M., and Ye, D. (2015). Carbon dioxide hydrogenation to methanol over Cu/ZrO2/CNTs: effect of carbon surface chemistry. RSC Adv. 5, 45320–45330. doi:10.1039/c5ra04774a
Wang, G., Mao, D., Guo, X., and Yu, J. (2018). Enhanced performance of the CuO–ZnO–ZrO2 catalyst for CO2 hydrogenation to methanol by WO3 modification. Appl. Surf. Sci. 456, 403–409. doi:10.1016/j.apsusc.2018.06.0903
Wang, G., Mao, D., Guo, X., and Yu, J. (2019). Methanol synthesis from CO2 hydrogenation over CuO-ZnO-ZrO2-MxOy catalysts (M=Cr, Mo and W). Int. J. Hydrogen Energy 44, 4197–4207. doi:10.1016/j.ijhydene.2018.12.131
Wang, J., Huang, L., Yang, R., Zhang, Z., Wu, J., Gao, Y., et al. (2014). Recent advances in solid sorbents for CO2 capture and new development trends. Energy Environ. Sci. 7, 3478–3518. doi:10.1039/c4ee01647e
Wang, Y., Kattel, S., Gao, W., Li, K., Liu, P., Chen, J. G., et al. (2019). Exploring the ternary interactions in Cu–ZnO–ZrO2 catalysts for efficient CO2 hydrogenation to methanol. Nat. Commun. 10, 1166. doi:10.1038/s41467-019-09072-6
Weigel, J., Koeppel, R. A., Baiker, A., and Wokaun, A. (1996). Surface species in CO and CO2 hydrogenation over copper/zirconia: on the methanol synthesis mechanism. Langmuir 12, 5319–5329. doi:10.1021/la9506990
Whang, H. S., Lim, J., Choi, M. S., Lee, J., and Lee, H. (2019). Heterogeneous catalysts for catalytic CO2 conversion into value-added chemicals. BMC Chem. Eng. 1, 9. doi:10.1186/s42480-019-0007-7
Whittle, D. M., Mirzaei, A. A., Hargreaves, J. S. J., Joyner, R. W., Kiely, C. J., Taylor, S. H., et al. (2002). Co-precipitated copper zinc oxide catalysts for ambient temperature carbon monoxide oxidation: effect of precipitate ageing on catalyst activity. Phys. Chem. Chem. Phys. 4, 5915–5920. doi:10.1039/b207691h
Witoon, T., Chalorngtham, J., Dumrongbunditkul, P., Chareonpanich, M., and Limtrakul, J. (2016). CO2 hydrogenation to methanol over Cu/ZrO2 catalysts: effects of zirconia phases. Chem. Eng. J 293, 327–336. doi:10.1016/j.cej.2016.02.069
Witoon, T., Numpilai, T., Phongamwong, T., Donphai, W., Boonyuen, C., Warakulwit, C., et al. (2018). Enhanced activity, selectivity and stability of a CuO-ZnO-ZrO2 catalyst by adding graphene oxide for CO2 hydrogenation to methanol. Chem. Eng. J 334, 1781–1791. doi:10.1016/j.cej.2017.11.117
Wu, J., Saito, M., Takeuchi, M., and Watanabe, T. (2001). The stability of Cu/ZnO-based catalysts in methanol synthesis from a CO2-rich feed and from a CO-rich feed. Appl. Catal. Gen. 218, 235–240. doi:10.1016/s0926-860x(01)00650-0
Xiao, J., Mao, D., Guo, X., and Yu, J. (2015). Effect of TiO2, ZrO2, and TiO2–ZrO2 on the performance of CuO–ZnO catalyst for CO2 hydrogenation to methanol. Appl. Surf. Sci. 338, 146–153. doi:10.1016/j.apsusc.2015.02.122
Xiao, K., Wang, Q., Qi, X., and Zhong, L. (2017). For better industrial Cu/ZnO/Al2O3 methanol synthesis catalyst: a compositional study. Catal. Lett. 147, 1581–1591. doi:10.1007/s10562-017-2022-8
Xiao, S., Zhang, Y., Gao, P., Zhong, L., Li, X., Zhang, Z., et al. (2017). Highly efficient Cu-based catalysts via hydrotalcite-like precursors for CO2 hydrogenation to methanol. Catal. Today 281, 327–336. doi:10.1016/j.cattod.2016.02.004
Yang, B., Liu, C., Halder, A., Tyo, E. C., Martinson, A. B. F., Seifert, S., et al. (2017). Copper cluster size effect in methanol synthesis from CO2. J. Phys. Chem. C 121, 10406–10412. doi:10.1021/acs.jpcc.7b01835
Yang, B., Yu, X., Halder, A., Zhang, X., Zhou, X., Mannie, G. J. A., et al. (2019). Dynamic interplay between copper tetramers and iron oxide boosting CO2 conversion to methanol and hydrocarbons under mild conditions. ACS Sustain. Chem. Eng. 7, 14435–14442. doi:10.1021/acssuschemeng.9b01561
Yang, C., Ma, Z., Zhao, N., Wei, W., Hu, T., and Sun, Y. (2006). Methanol synthesis from CO2-rich syngas over a ZrO2 doped CuZnO catalyst. Catal. Today 115, 222–227. doi:10.1016/j.cattod.2006.02.077
Yang, D., Zhu, Q., Chen, C., Liu, H., Liu, Z., Zhao, Z., et al. (2019). Selective electroreduction of carbon dioxide to methanol on copper selenide nanocatalysts. Nat. Commun. 10, 1–9. doi:10.1038/s41467-019-08653-9
Yang, H., Zhang, C., Gao, P., Wang, H., Li, X., Zhong, L., et al. (2017). A review of the catalytic hydrogenation of carbon dioxide into value-added hydrocarbons. Catal. Sci. Technol. 7, 4580–4598. doi:10.1039/c7cy01403a
Yang, Y., Mei, D., Peden, C. H. F., Campbell, C. T., Mims, C. A., and Catal, A. (2015). Surface-bound intermediates in low-temperature methanol synthesis on copper: participants and spectators, ACS Catal. 5, 7328–7337. doi:10.1021/acscatal.5b02060
Yang, Y., Mims, C. A., Mei, D. H., Peden, C. H. F., and Campbell, C. T. (2013). Mechanistic studies of methanol synthesis over Cu from CO/CO2/H2/H2O mixtures: the source of C in methanol and the role of water. J. Catal. 298, 10–17. doi:10.1016/j.jcat.2012. doi:10.028
Yao, L., Shen, X., Pan, Y., and Peng, Z. (2019). Synergy between active sites of Cu-In-Zr-O catalyst in CO2 hydrogenation to methanol. J. Catal. 372, 74–85. doi:10.1016/j.jcat.2019.02.021
Zander, S., Kunkes, E. L., Schuster, M. E., Schumann, J., Weinberg, G., Teschner, D., et al. (2013). The role of the oxide component in the development of copper composite catalysts for methanol synthesis. Angew. Chem. Int. Ed. 52, 6536–6540. doi:10.1002/anie.201301419
Zhan, H., Li, F., Gao, P., Zhao, N., Xiao, F., Wei, W., et al. (2014). Methanol synthesis from CO2 hydrogenation over La–M–Cu–Zn–O (M = Y, Ce, Mg, Zr) catalysts derived from perovskite-type precursors. J. Power Sources 251, 113–121. doi:10.1016/j.jpowsour.2013.11.037
Zhang, F., Zhang, Y., Yuan, L., Gasem, K. A. M., Chen, J., Chiang, F., et al. (2017). Synthesis of Cu/Zn/Al/Mg catalysts on methanol production by different precipitation methods. Mol. Catal. 441, 190–198. doi:10.1016/j.mcat.2017.08.015
Zhang, L., Zhang, Y., and Chen, S. (2012). Effect of promoter SiO2, TiO2 or SiO2-TiO2 on the performance of CuO-ZnO-Al2O3 catalyst for methanol synthesis from CO2 hydrogenation. Appl. Catal. Gen. 415-416, 118–123. doi:10.1016/j.apcata.2011.12.013
Zhang, X., Zhong, L., Guo, Q., Fan, H., Zheng, H., and Xie, K. (2010). Influence of the calcination on the activity and stability of the Cu/ZnO/Al2O3 catalyst in liquid phase methanol synthesis. Fuel 89, 1348–1352. doi:10.1016/j.fuel.2009.06.011
Zhao, Y.-F., Yang, Y., Mims, C., Peden, C. H. F., Li, J., and Mei, D. (2011). Insight into methanol synthesis from CO2 hydrogenation on Cu(111): complex reaction network and the effects of H2O. J. Catal. 281, 199–211. doi:10.1016/j.jcat.2011.04.012
Zheng, H., Narkhede, N., Han, L., Zhang, H., and Li, Z. (2020). Methanol synthesis from CO2: a DFT investigation on Zn-promoted Cu catalyst. Res. Chem. Intermed 46, 1749–1769. doi:10.1007/s11164-019-04061-2
Zhou, W., Cheng, K., Kang, J., Zhou, C., Subramanian, V., Zhang, Q., et al. (2019). New horizon in C1 chemistry: breaking the selectivity limitation in transformation of syngas and hydrogenation of CO2 into hydrocarbon chemicals and fuels. Chem. Soc. Rev. 48, 3193–3228. doi:10.1039/c8cs00502h
Keywords: carbon dioxide, hydrogenation, methanol, Cu/ZnO catalyst, microstructure
Citation: Etim UJ, Song Y and Zhong Z (2020) Improving the Cu/ZnO-Based Catalysts for Carbon Dioxide Hydrogenation to Methanol, and the Use of Methanol As a Renewable Energy Storage Media. 8:545431. doi: 10.3389/fenrg.2020.545431
Received: 25 March 2020; Accepted: 25 August 2020;
Published: 29 September 2020.
Edited by:
James George Highfield, Independent Researcher, SingaporeReviewed by:
Andreas Borgschulte, Swiss Federal Laboratories for Materials Science and Technology, SwitzerlandBlaž Likozar, National Institute of Chemistry, Slovenia
Copyright © 2020 Etim, Song and Zhong. This is an open-access article distributed under the terms of the Creative Commons Attribution License (CC BY). The use, distribution or reproduction in other forums is permitted, provided the original author(s) and the copyright owner(s) are credited and that the original publication in this journal is cited, in accordance with accepted academic practice. No use, distribution or reproduction is permitted which does not comply with these terms.
*Correspondence: Ziyi Zhong, eml5aS56eW9uZ0BndGlpdC5lZHUuY24=