- 1Guangxi Key Laboratory of Manufacturing System and Advanced Manufacturing Technology, School of Mechanical Engineering, Guangxi University, Nanning, China
- 2Guangxi Key Laboratory of Petrochemical Resource Processing and Process Intensification Technology, Guangxi University, Nanning, China
- 3Advanced Technology Center, Research and Engineering Institute, Guangxi Yuchai Machinery Co., Ltd., Yulin, China
- 4College of Electrical Engineering Guangxi University, Nanning, China
The research on the recovery of low-grade thermal energy carried away by boiler flue gas is significant for sugar mills. This paper designs a waste heat recovery system based on sugar plant flue gas, integrating absorption refrigeration cycle and the organic Rankine cycle, and the effects of nine working fluids on the system are investigated. The aim is to realize the multi-form conversion of energy. The performance of the system is evaluated in terms of energy, exergy, and economic metrics. Multi-objective optimization is performed with the method of the NSGA-II genetic algorithm. The results show that Butane is the most suitable working fluid for ORC. The exergy efficiency of the system is 32.125% before optimisation, with an increased space cooling capacity of 15820.56 MW per year for the sugar mill. The exergy destruction analysis of the system reveals that the generator accounts for the highest proportion of exergy destruction (50.8%). The entire system shows the LCOE is as low as 0.0406$/kWh under the optimized condition. The optimized system can obtain an estimated annual electricity sales revenue of $136,300, and the sugar mill can save $308,600 in cooling costs. In addition, the payback period can be shortened to 5.79 years.
1 Introduction
1.1 Background
Bioenergy is a large-scale renewable energy source, accounting for 10%–14% of the world’s primary energy and potentially reaching 30%–40% by 2050 (Rosillo-Calle, 2016). Currently, over 120 million tons of sugar are produced worldwide each year, with approximately 70% derived from sugarcane (USDA, 2018). The biomass potential of this crop can replace fossil fuels, leading to energy savings (de Matos et al., 2020) and transforming the sugar industry into a more versatile and competitive sector. The untapped waste heat resources in the global sugar industry show great potential. In the production process of sugar mills, a large amount of sugarcane residue, such as bagasse are produced while a substantial amount of recoverable low-temperature waste heat are generated (Birru et al., 2016), making the recovery of waste heat emissions from sugar mills becomes very essential. Mohammadi et al. (2020) investigated the potential of using bagasse as a substitute for natural gas in a sugar factory for the generation of thermal energy and electricity. Singh (2019) analyzed the thermodynamic performance of a 16-megawatt cogeneration system in a sugar mill and found that 6.342% of the fuel energy was lost in the boiler flue gas. The substantial amount of low-temperature flue gas emitted by sugar mill boilers represents the main portion of heat loss and contains a significant amount of unused low-temperature waste heat. This not only affects the thermal efficiency of the boilers but also imposes significant pressure on the environment, causing ecological damage and contributing to intensified greenhouse effects. Fujii et al. (2019) demonstrated that the high-temperature flue gases produced from sugarcane boilers at approximately 200°C during the combustion process has been wasted, which could reduce fuel consumption by 29.6% if this portion of energy was effectively utilized. The aforementioned studies indicate that the boiler flue gases from sugar mills have not only high economic benefits, but also considerable thermodynamic potential.
1.2 Waste heat recovery technology of sugar factories
Organic Rankine cycle (ORC) system is more prominent in recovering low-temperature waste heat (Mana et al., 2023). ORC system not only converts waste heat into high-grade energy (electricity), but also are widely used due to their simplicity of construction, lower material and sealing costs, and adaptability to heat sources of different temperature levels (Nemati et al., 2017). Zhang et al. (2016) investigated the system properties of organic Rankine cycle (ORC), steam-organic Rankine cycle (S-ORC) as well as steam Rankine cycle (SRC) within the range of 150°C–350 °C by comparing their performances. The results indicated that more prominent thermodynamic performance and power generation are obtained when ORC is employed in the heat source temperature range of 150°C–210°C. Waste heat can be used for refrigeration in addition to electricity generation. Uphade (2021) studied the heat recovery potential of flue gas in the sugar industry and used a vapor absorption cycle instead of the conventional vapor compression cycle, allowing a sugar mill with 2,500 Tons of cane crushed per day capacity to produce 293 Tons of refrigeration cooling, which is sufficient to meet the internal demand of the sugar mill. Singh (2020) recovered waste heat from the boiler flue gases of the sugar mill, resulting in an increase of 375.2135 kW in the net power generation and an increase in the energy efficiency of the sugar mill’s cogeneration by 0.3819%. Sugar mills need to consume huge financial and material resources in refrigeration every year (Du et al., 2014; Kapanji et al., 2021). In many heat-driven refrigeration systems, the absorption refrigeration technology is gradually becoming an effective alternative to the conventional vapor compression refrigeration system (Kumar et al., 2018) and is widely used in an increasing number of plants. This is due to its ability in fully utilizing low temperature heat sources to provide cooling capacity and the use of more eco-friendly refrigerants than chlorofluorocarbon refrigerants (CFCs) (Li et al., 2016). Bandgar al (Bandgar et al., 2018). utilized a vapor absorption system for waste heat recovery of excess water removed from the sugar mill for using as cooling in the factory office area. It saved 64,314 kWh per crushing season for the plant, which is equivalent to at least Rs. 529,304.22 per season. Chouhan and Chandrakar (2014) suggested the use of the absorption refrigeration system to recover heat sources, including flue gas and boiler emissions, which could save 1,870 tons of bagasse per year in terms of additional cooling capacity for sugar mills.
The separate utilization of ORC and absorption refrigeration has achieved excellent comprehensive benefits in various fields, but the energy generated by individual systems is relatively homogeneous in form and may not be as efficient as an integrated system. Therefore, some researchers have proposed cogeneration systems that integrate waste heat recovery technologies to upgrade the economic efficiency as well as the thermodynamic performance of the system and enrich forms of energy utilization. Dogbe et al. (2019) used absorption heat pump (AHP) technologies as well as organic Rankine cycle (ORC) to improve the energy efficiency in a sugar mill, resulting in a 1.7% improvement in exergy performance and a total bagasse value saving of 0.83%. Zhang et al. (2020) proposed a novel cogeneration system for coal-fired power plants based on ORC as well as AHP and evaluated the thermodynamic as well as economic efficiency of the system. The findings demonstrated that the power generation and heat production were increased by a factor of one, while the general exergy efficiency as well as thermal efficiency were increased by 9.38% and 1.71%, respectively, compared with the conventional CHP system. Wang et al. (2020) designed a new triple generation system consisting of an organic Rankine cycle, an absorption refrigeration cycle as well as a supercritical CO2 Brayton cycle for waste heat recovery from gas turbines in addition. The results showed that the new system could produce 6.02 MW of cooling capacity, 9.93 MW of heat load, as well as 40.65 MW of net power generation. Tian et al. (2018) used an integrated system to increase system efficiency with a newly proposed triple system of CO2 capture system, ammonia absorption cooler as well as organic Rankine cycle (ORC) integrated with SOFC. The calculation indicated that the exergy efficiency as well as net electrical efficiency of the comprehensive system can reach 59.96% and 52.83%, respectively.
1.3 Motivation and contribution
Currently, there is relatively little research on the construction and optimization of waste heat recovery systems in sugar factories, with most studies focused on cogeneration and single systems. In order to provide both electric and cooling power, and achieve efficient energy utilization, this study adopts the cascade Organic Rankine Cycle (ORC) and Absorption Refrigeration Cycle (ARC) waste heat recovery system. Sugar factories require a certain cooling system during sugar processing to control process temperatures, ensuring product quality and normal equipment operation, such as crystalline sugar particles and sugar storage. Therefore, using ORC-ARC to achieve combined cooling and power has significant significance. First, the ORC system is suitable for medium and low temperature waste heat recovery, with lower cost and simpler operation compared to other systems, such as reheating, reheat, and bypass. The ARC uses an absorbent to absorb and desorb the solute for cooling, and steam refrigeration cycles require compressors to compress steam, consuming more energy. At the same time, the absorbent used by ARC is more environmentally friendly than traditional refrigerants such as fluorine. Furthermore, both the ORC and ARC systems possess high flexibility, allowing for efficient energy conversion by adjusting system parameters according to the requirements of the heat source and environment. Finally, by cascading ORC and ARC systems, not only can a large amount of “green” electricity be generated, but also sufficient cooling capacity provided for sugar factories, achieving efficient energy utilization and comprehensive recycling. Therefore, adopting the ORC-ARC system provides a feasible solution for waste heat recovery in sugar factories with higher economic and environmental performance.
This study compares the performance and environmental friendliness of nine working fluids in the ORC system, and determines the best organic working fluid in the integrated system based on comprehensive performance comparison, which helps optimize the operation of the entire integrated system. The performance of the ORC and absorption refrigeration cycle after integration is evaluated through thermodynamics and economic analysis, and the influence of key operating parameters such as evaporator temperature and generator temperature on the entire waste heat recovery system is studied. The economic efficiency of the system is evaluated using LCOE. Finally, NSGA-II is used to determine the system’s optimal operating environment.
2 System description and assumptions
In this study, a new waste heat recovery system based on the flue gas of boilers in sugar mills is proposed. A specific analysis of the exergy in sugar mills has been carried out in the literature (Dogbe et al., 2018), and it was found that only 23.4% of the exergy in sugar mills leaves through the product during the whole production process, in which 3.5% of exergy is lost through waste and 73.1% is wasted during the production process due to various irreversible factors. The production process of a sugar mill is shown in Figure 1.
The significant energy loss caused by the waste heat from boiler flue gas during the production process can be effectively reduced by recovering this waste heat, thereby improving the economic performance and energy efficiency of the sugar factory. Considering that the recovered waste heat is around 190°C, an Organic Rankine Cycle (ORC) is used as the base cycle. Conventional steam refrigeration cycles require higher temperatures and pressures, making them less suitable for handling low-temperature waste heat (Li et al., 2014). ORC utilizes organic working fluids that can evaporate and condense at relatively low temperatures, making it particularly suitable for recovering low-temperature waste heat. Additionally, the Absorption Refrigeration Cycle (ARC) replaces traditional refrigerants with organic working fluids, which usually have minimal negative impact on the atmosphere. When the flue gas passes through the first round of energy recovery in the ORC, its temperature drops to a range suitable for capturing and utilizing by ARC, providing the sugar factory with additional refrigeration capacity. There are various areas in the sugar factory that require significant cooling, such as syrup cooling and crystallization cooling. By combining ORC with ARC, the waste heat from the boiler flue gas can be fully utilized. This not only converts waste heat into electrical energy but also provides additional refrigeration capacity, thereby improving the overall system performance and efficiency. The sugar factory can achieve efficient energy utilization, reduce energy consumption and emissions, and lower production costs. This is not only economically beneficial for the sugar factory itself but also aligns with environmental protection and sustainable development requirements. This research has achieved gradient utilization of boiler flue gas from sugar mills by integrating ORC and ARC, enabling multiform conversion of energy to cooling and electricity.
Figure 2 illustrates a schematic diagram of the complete waste heat recovery system. The principal components of the proposed system are the evaporator, condenser, turbine, absorber, pump, solution heat exchanger, and generator. The work process is: In the ORC system, the working fluid is pressurized by pump 1 to the heat exchanger (02–03) and absorbs heat from the energy source fed to the heat exchanger, which is heated to high-temperature high-pressure vapor, which enters the Turbine to expand and generate electricity (03–04). Afterwards, it flows into the condenser 1 (04-01) and is condensed into a liquid by the refrigeration water, which then circulates through the ORC system again by pump 1 (01–02). In the absorption refrigeration cycle, water is the absorbent and ammonia is the refrigerant. We utilize waste heat from the heat exchanger to drive the heat source for the ARC system into the generator, where a concentrated solution of ammonia-water mixture is heated to evaporation, leaving a high temperature dilute solution. The high-pressure vapor is then condensed into a low temperature saturated liquid as it passes through condenser 2 (10–11), which is depressurized by the throttle valve and proceeds to the evaporator, which provides cooling through evaporation (11–13). The low-pressure ammonia steam is fed to the absorber (13-07) where it is diluted and absorbed into a concentrated solution into a concentrated solution of ammonia saturated water, which is sent under pressure to SHE via pump 2 to reclaim the waste heat of the concentrated solution in the generator (07–08). The dilute ammonia-water mixture remaining in the generator after the ammonia evaporation passes through SHE and returns to the absorber through a reduced pressure throttle valve (15–16).
3 Mathematical model
3.1 Thermodynamic model
The simulations of the waste heat recovery system in this study were implemented in MATLAB and all reactions were in thermodynamic equilibrium. The thermodynamic properties of the flue gas were calculated by REFPROP9.1 based on its basic composition: 58.14% N2, 10.42% H2O, 26.27% CO2 and 5.17% O2. The added system is composed of ORC and absorption refrigeration cycles, respectively, and the two subsystems are thermodynamically balanced for the new system by mass flow equilibrium on the generator and heat exchanger. Table 1 summarizes all the key input data of the system. In order to improve the effect of the system in practical application, the system parameters are rationalized. In order to ensure that the turbine can reach the target state in practical applications, the turbine efficiency is set to 70%, while the actual value is around 80% (Cai et al., 2016; Pethurajan et al., 2018). Men et al. (2021) compared the performance of different heat exchangers in practical applications, and the results showed the EW heat exchange efficiency was higher than 85%. In the theoretical design of this paper, the efficiency of the heat exchanger is set at 70%, lower than the actual value.
In the sub-section, a mathematical model based on thermodynamics as well as economics is established for the system. In order to streamline the model, some essential assumptions are defined:
(1) The subsystems operate at a steady state.
(2) The pumps and turbines operate at a specific isentropic efficiency.
(3) The pressure drop of piping is negligible.
(4) The low-temperature waste heat comes from the sugar mill exhaust gas at a temperature of about 190°C (Dogbe et al., 2018).
(5) The generator outlet refrigerant in ARC is superheated.
3.2 Energy analysis
On the basis of the mass balance equation (Eq. 1) and energy balance equation (Eq. 2) (Nami et al., 2019), the thermodynamic model of all parts of the subsystem was studied and the corresponding mass and energy equations were listed to easily analyze the system later, as shown in Table 2.
Where out and in represent the outlet and inlet of the component, respectively.
3.3 Exergy analysis
Exergy analysis has been widely used in the economic analysis of thermal systems that reveals the location, as well as the extent of process inefficiencies to optimize their capabilities and complements traditional mass flow analysis (Ghannadzadeh and Sadeqzadeh, 2017). The thermodynamic model of each component can be identified from the energy balance equation.
The exergy balance equation for the individual component is represented as Eq. 3 (Pan et al., 2021b):
The exergy value for each point is determined as Eq. 4 (Ebrahimi-Moghadam et al., 2021):
The detailed exergy equations for each component are concluded in Table 3.
3.4 Economic analysis
Integrated sugar mill flue gas waste heat recovery system should consider not only thermodynamic aspects but also matters such as economic costs. The Levelized Cost Of Energy (LCOE) is one of the more extensively employed criteria in the feasibility analysis of evaluating new generation systems and power plants (Boukelia et al., 2016). The relationship between LCOE and annual system power generation and input costs is calculated using Eq. 5:
Where
CRF indicates the capital recovery factor calculated by Eq. 6:
Where i and n are the interest rate (i = 0.1) as well as the lifetime of the system (n = 20 years) (Zhang et al., 2018), respectively.
Considering the Chemical Engineering Plant Cost Index (CEPCI) of 699.97 in 2021 (The Chemical Engineering Plant Cost Index, n.d.), the cost function in Table 4 was updated to the year 2021 according to Eq. 7.
Based on the total investment cost and annual net income, the system’s investment payback cycle PP can be estimated as Eq. 8 (Wang et al., 2015):
Where
Ztot is composed of equipment investment cost (ZB) and maintenance cost (ZOM), which is calculated using Eq. 9:
The annual net income (NE) is determined by the net output power, electricity price, refrigeration capacity, and cooling water price, which is calculated using Eq. 10:
Where
For the heat transfer area of each component, the calculation is performed by Eq. 11 (Li et al., 2019):
Where
3.5 Performance evaluation
To evaluate the capacity of the waste heat recovery system, some concepts is calcluated using Eqs 13–15:
The cooling exergy of the system is defined as Eq. 16:
The equation for the thermal efficiency of the systemis defined as Eq. 17:
The exergy efficiency formula for the system is defined as Eq. 18:
3.6 Multi-objective optimization
To resolve the conflict between economic factors and the thermodynamic performance of the cycle, a non-dominated ranking genetic algorithm II (NSGA-II) is adopted for the multi-objective optimization of the cascaded system (Tan et al., 2023). As in Figure 3, the objective function, decision variables and constraints are the three elements of the optimization problem, and
3.7 Validation
To confirm the accuracy of the system model, the key subsystems of the built system were verified. The key subsystems include the ORC and the absorption refrigeration cycle, and the modeling of each subsystem were validated individually using experimental data from the literature. To validate the ORC model, results from the literature (Vaja and Gambarotta, 2010) were used for comparison. The ARC model was also validated using the literature (Zare, 2020). As shown in Tables 8, 9, there is excellent concordance between the findings of the current study and the data presented in the literature (Vaja and Gambarotta, 2010; Zare, 2020). Therefore, the accuracy of the current study results was verified. As can be seen from Figure 5, the simulation results of this study are in excellent consistency with references.
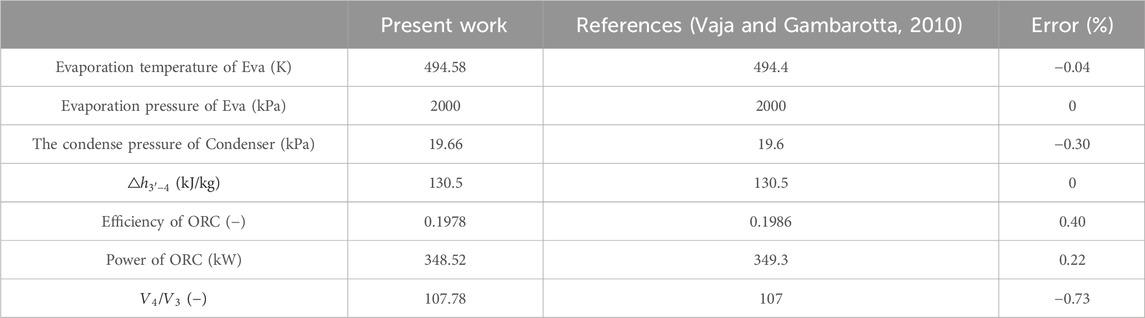
TABLE 8. The results of comparison between present work and Ref. (Vaja and Gambarotta, 2010).
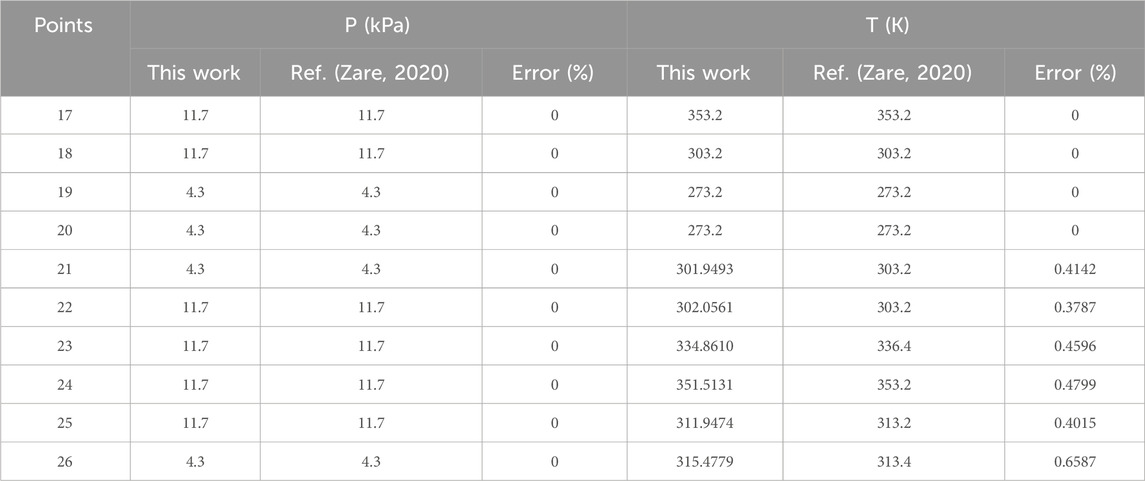
TABLE 9. The results of comparison between present work and Ref. (Zare, 2020).
4 Results and discussion
This section discusses and analyzes a new system developed based on waste flue gas from sugar mills after bagasse combustion with ORC and absorption refrigeration system composition. The analysis is carried out for parameters such as evaporation temperature and generator temperature to summarize the conclusions. Bagasse is composed of 0.8% wax, 2.3% ash, 18.1% lignin, 33.8% hemicellulose, as well as 43.6% cellulose (Nemomsa et al., 2022). Bagasse is burned in the sugar mill to provide steam for the sugar mill process, however a significant quantity of low-temperature heat is still emitted to the atmosphere with the flue gas. The heat source in the ORC system is the flue gas from the sugar mill (190°C) (Dogbe et al., 2018), and has a high exergy content of 11.95 MW. This paper presents the system’s exergy, mass flow rate, distribution of fire loss of each component, and multi-objective optimization results.
4.1 The analysis of ORC working fluid
The operational performance of waste heat recovery systems is affected by the properties of the organic working fluid. Examples of ideal working fluid properties include suitable boiling point temperature, lower latent heat, higher critical temperature and pressure, appropriate specific volume, higher thermal conductivity, lower density and surface tension, non-corrosive, higher thermal stability, non-toxic, zero ODP, as well as low GWP (Hung et al., 1997; Luo et al., 2015). In addition, the closer the critical temperature of the working fluid is to the temperature of the heat source, the higher the performance of the system will be (Lu et al., 2020). Based on the aforementioned conditions, nine organic working fluids were screened, as shown in Table 10. By comparing the operation results under the same working conditions, the ORC working fluids with more ideal conditions were obtained.
The net power output of ORC is reflective of the performance of the waste heat recovery system. Therefore, in the present research, the net power output was determined as the target value, and the net power output (
4.2 Parametric study
4.2.1 High pressure in ORC analysis
The outlet pressure of Pump1, as the highest pressure in the ORC system, affects many factors in the system, for example, the heat load of the heat exchanger. Therefore, it is an important object of study in this research. As shown in Figures 7A–F, this study analyzes the effect of Pump1 outlet pressure on
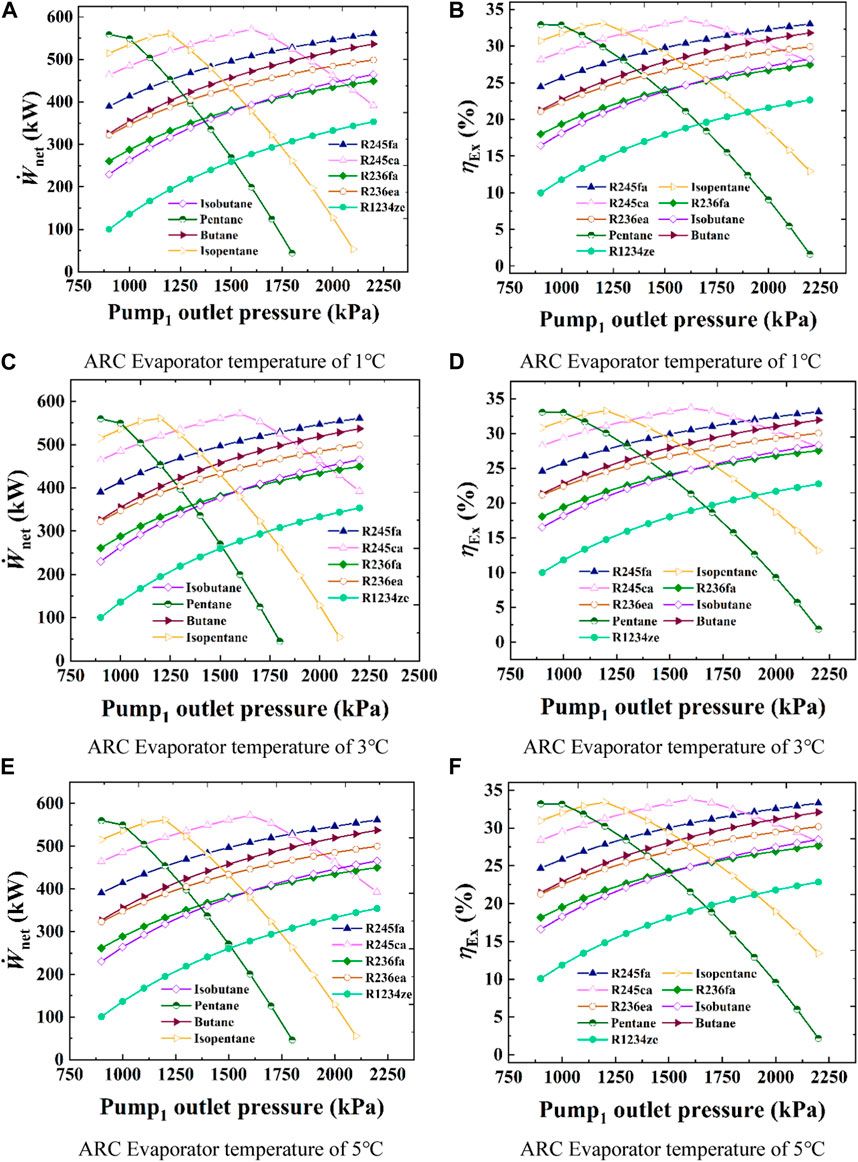
FIGURE 7. Effect of high pressure in ORC on
As shown in Figure 7F, when Pump1 outlet pressure = 2,100 kPa and other working conditions are the same, the total exergy system efficiency
4.2.2 The effect of evaporator temperature
Based on the comprehensive research on the performance impact of various organic working fluids on the ORC system, it was found that Butane provides superior benefits compared to other fluids. Therefore, in the subsequent analysis, we have chosen Butane as the working fluid for the ORC system. The evaporator temperature in the absorption refrigeration cycle is a key design parameter, and Figure 8 presents the impact of evaporator temperature on the exergy efficiency (
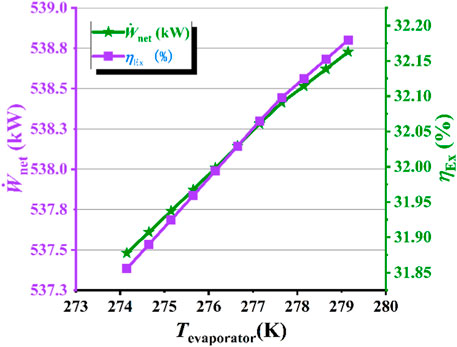
FIGURE 8. Effect of ARC evaporator temperature on the net system output power
4.2.3 The effect of generator temperature
The temperature of the generator is also an important parameter to study when designing the ARC system, heat transfer rate of condenser2 (
4.2.4 The effect of ORC evaporator pressure and condenser temperature
In an organic Rankine cycle (ORC) system, the maximum working pressure (
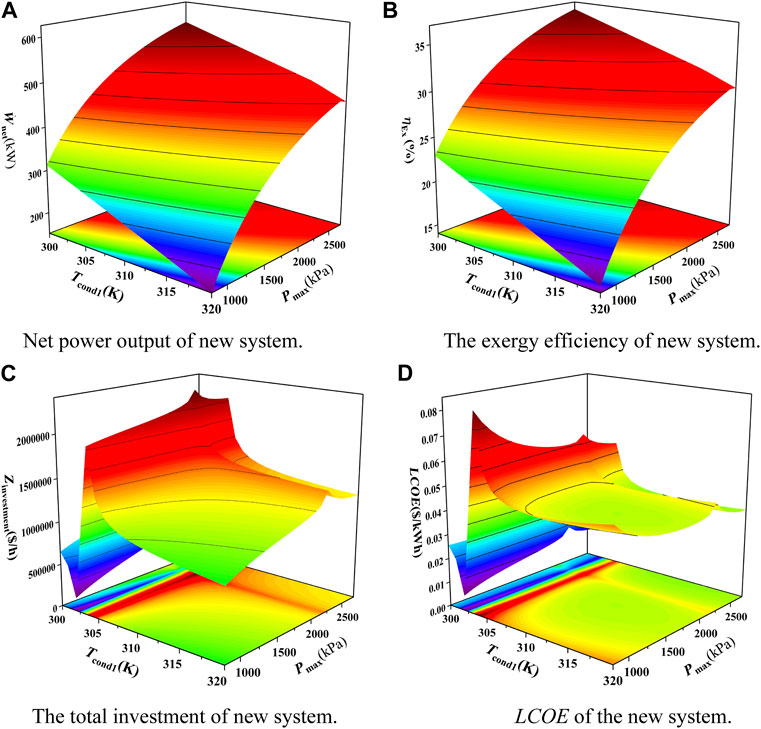
FIGURE 10. Effects of ORC evaporator pressure and condenser temperature on the system. (A) Net power output of new system. (B) The exergy efficiency of new system. (C) The total investment of new system. (D) LCOE of the new system.
4.2.5 The effect of ARC evaporator temperature and condenser temperature
The effects of ARC evaporator temperature and condenser temperature on the net output power, exergy efficiency, total investment, and LCOE of the system are shown in Figures 11A–D. The results indicate that decreasing the condenser temperature (
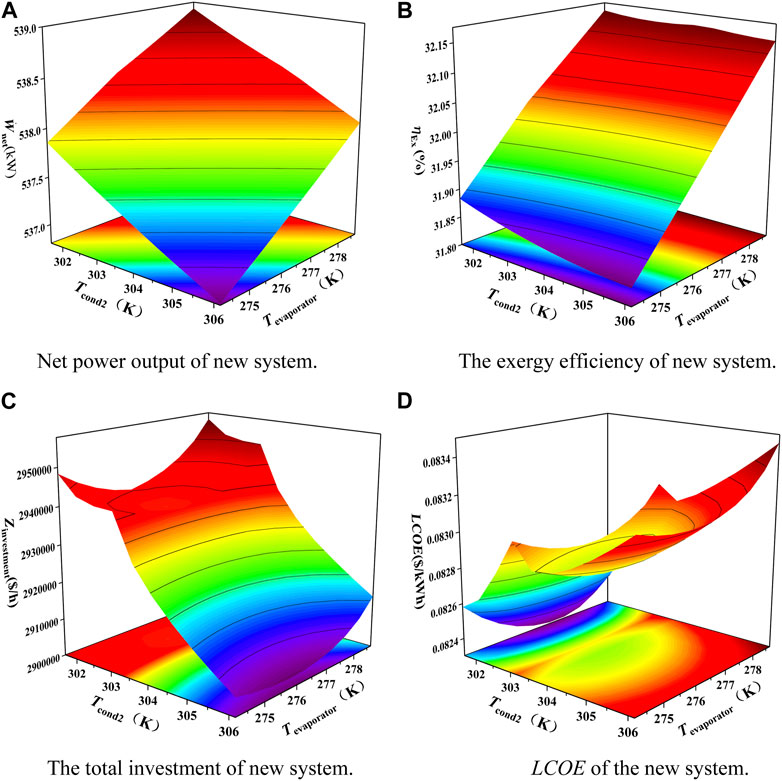
FIGURE 11. Effects of ARC evaporator pressure and condenser temperature on the system. (A) Net power output of new system. (B) The exergy efficiency of new system. (C) The total investment of new system. (D) LCOE of the new system.
4.2.6 The effect of generator temperature and condenser temperature
Figures 12A–D illustrates the impact of ARC generator temperature and condenser temperature on the net output power, exergy efficiency, total investment, and LCOE of the overall system. While keeping
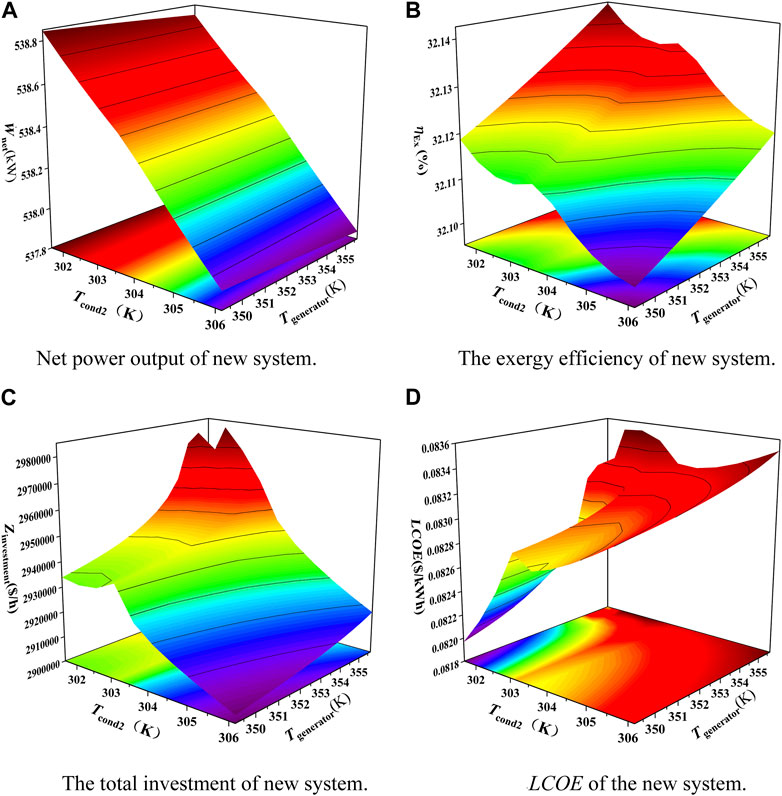
FIGURE 12. Effects of ARC Generator pressure and condenser temperature on the system. (A) Net power output of new system. (B) The exergy efficiency of new system. (C) The total investment of new system. (D) LCOE of the new system.
4.3 The analysis of exergy destruction in the component
Figure 13 presents the findings of the exergy analysis based on the design conditions for the waste heat recovery system. The primary function of Pump2 is to enhance heat transfer efficiency, rather than being the primary workload in the circulation system, hence the negligible impact of Pump2 can be neglected. 50.8% of exergy destruction in the system occurs in the generator, followed by the evaporator and absorber. This is because of the high-temperature ammonia mixture solution under isobaric conditions, which causes the generator to operate at elevated temperatures. As a result, it concentrated most exergy destruction in the generator and absorber. These irreversibilities are mainly due to mixing destruction in the generator and absorber as well as to concentration gradients, temperature gradients and external forces (Nami et al., 2017). The exergy destruction in the ORC system occurs mainly in the HE (6.79%), and the high value of energy destruction is primarily caused by the large temperature discrepancy that exists between the cold and hot flows in the component (Aman et al., 2014). This figure shows the need to consider the design of the generator, absorber and Heat Exchanger to reduce exergy destruction by them. The thermodynamic properties of the system are shown in Table 11.
4.4 The results of economic analysis
The economic efficiency is an effective factor to judge the sustainability of the system, which depends not only on the exergy efficiency of the system but also on the net output efficiency and the LCOE, as shown in Table 12 for the new sugar plant. The investment cost of the new system is 2.94 million dollars (M$). It can be concluded from Figure 14 that the overall cost of the ORC cycle is based higher than the cost of the ARC cycle. In addition, the ORC system has the highest heat exchanger cost. However, by recycling the system, the net power output is increased by 0.5385 MW, providing 4717.26 MW of renewable electricity and 15,820.56 MW of space cooling capacity for the sugar plant per year. The payback period of the system is 5.79 years. The economic performance of the system is highly dependent on the price of renewable electricity, and the higher the price, the more investment potential the project has. The results of the economic analysis of the system illustrate that the waste heat recovery system of the sugar mill has a great economic potential, and the project is economically feasible.
4.5 Multi-objective optimization results
In this study, we employ NSGA-II to identify optimal system operation parameters in order to address the trade-off between LCOE and exergy efficiency
4.6 Comparison of multiple systems and single system
Malwe et al. (2021) proposed a VCRS-ORC system aiming to achieve waste heat recovery, cooling, and electricity generation. The final exergy efficiency of this system was determined to be 17.95%, with a net output power of 0.296 kW. In this study, an ORC-ARC system was introduced to achieve higher energy utilization efficiency. Compared to the former, the exergy efficiency of this system increased by 14.175%, reaching a net output power of 5,385 kW. Significantly improved system efficiency and power output were achieved by studying the optimal working fluid in the ORC and analyzing key factors within the system.
4.7 Possible differences in real exploitation conditions
First, in the actual operation process, the heat exchanger may not reach the ideal pinch point designed, resulting in a large temperature difference and failure to achieve the desired performance. Second, the efficiency of pumps and turbines depends on variable operating conditions. The optimal working conditions of the pump and the turbine may be difficult to achieve, resulting in reduced system performance. The characteristics of the heat source affect the performance of ORC. In the actual operation process, heat source fluctuations will reduce the efficiency of the steam turbine and the effectiveness of the heat exchanger, so the performance may be reduced.
5 Conclusion
This research presents a novel waste heat recovery system composed of an absorption refrigeration cycle and an organic Rankine cycle, which is applied for the recovery of boiler flue gas in a sugar factory. By taking the utilization of flue gas, considerable power generation and refrigeration output are obtained, resulting in improvements in system irreversibility and exhaust emissions. An economic and thermodynamic analysis of the entire system are conducted. The main conclusions are summarized as:
(1) In this research, nine working fluids were adopted and among which Butane was identified as the most appropriate working fluid for ORC.
(2) With an investment of 2.94 million dollars (M$), the system has a high exergy efficiency of 32.125%, with an increased power output of 4717.26 MW h and an increased space cooling capacity of 15,820.56 MW per year for the sugar mill. Additionally, the payback period of the system can be shortened to 5.79 years.
(3) Through multi-objective optimization, the optimal operating parameters of the system are obtained. The LCOE at the optimum working condition is as low as 0.0406$/kWh, and the exergy efficiency is 31.57%. The annual revenue from electricity sales and the saving cost for cooling are $136,300 and $308,600, respectively.
(4) ORC and ARC were used for waste heat gradient utilization from boiler exhaust gas. The system has achieved multi-forms conversion of energy to cooling and generating electricity through cascade utilization of waste heat.
(5) The highest exergy destruction occurs in the generator, accounting for 50.8% of the overall system.
To expand this research in the future, it is necessary to evaluate the system by combining environmental factors. Second, it is crucial to consider the optimization of the heat exchanger model. There are various working fluids that can be used in absorption refrigeration cycles, and it is possible to conduct thermodynamic analysis by switching between them to optimize the system. In addition, it is essential to study different refrigeration systems and thus achieving a more efficient energy conversion system.
Data availability statement
The original contributions presented in the study are included in the article/Supplementary Material, further inquiries can be directed to the corresponding author.
Author contributions
ZW: Writing–original draft, Writing–review and editing. WG: Writing–review and editing. SZ: Methodology, Writing–review and editing. HS: Methodology, Writing–review and editing. WQ: Supervision, Writing–review and editing. LL: Project administration, Writing–review and editing.
Funding
The author(s) declare financial support was received for the research, authorship, and/or publication of this article. This research was supported by Natural Science Foundation of China, (No. 22302044), Science and Technology Major Project of Guangxi under Grant, (AA23062041) and Supported by the Dean/Open Project of Guangxi Key Laboratory of Petrochemical Resource Processing and Process Intensification Technology, (No. 2022K010).
Conflict of interest
Authors SZ and HS were employed by Guangxi Yuchai Machinery Co., Ltd.
The remaining authors declare that the research was conducted in the absence of any commercial or financial relationships that could be construed as a potential conflict of interest.
Publisher’s note
All claims expressed in this article are solely those of the authors and do not necessarily represent those of their affiliated organizations, or those of the publisher, the editors and the reviewers. Any product that may be evaluated in this article, or claim that may be made by its manufacturer, is not guaranteed or endorsed by the publisher.
References
Aman, J., Ting, D. S.-K., and Henshaw, P. (2014). Residential solar air conditioning: energy and exergy analyses of an ammonia–water absorption cooling system. Appl. Therm. Eng. 62, 424–432. doi:10.1016/j.applthermaleng.2013.10.006
Bandgar, R. S., Jagtap, K. M., Kokare, S. S., and Kshirsagar, A. S. (2018). Waste heat from sugar indusrty to drive vapour absorption acs. JournalNX 29 (7), 1039–1051.
Bhattacharyya, S. C., and Quoc Thang, D. N. (2004). Economic buy-back rates for electricity from cogeneration: case of sugar industry in Vietnam. Energy 29, 1039–1051. doi:10.1016/j.energy.2003.04.001
Birru, E., Erlich, C., Beyene, G. B., and Martin, A. (2016). Upgrading of a traditional sugar cane mill to a modern mill and assessing the potential of energy saving during steady state and transient conditions—part II: models for a modified cogeneration unit. Biomass Conv. bioref. 6, 233–245. doi:10.1007/s13399-015-0180-8
Boukelia, T. E., Arslan, O., and Mecibah, M. S. (2016). ANN-based optimization of a parabolic trough solar thermal power plant. Appl. Therm. Eng. 107, 1210–1218. doi:10.1016/j.applthermaleng.2016.07.084
Cai, D., Jiang, J., He, G., Li, K., Niu, L., and Xiao, R. (2016). Experimental evaluation on thermal performance of an air-cooled absorption refrigeration cycle with NH3–LiNO3 and NH3–NaSCN refrigerant solutions. Energy Convers. Manag. 120, 32–43. doi:10.1016/j.enconman.2016.04.089
Chouhan, P., and Chandrakar, A. (2014). Performance enhancement of sugar mill by alternate cooling system for condenser. IOSR J. Mech. Civ. Eng. 11, 18–25. doi:10.9790/1684-11511825
de Matos, M., Santos, F., and Eichler, P. (2020). “Chapter 1 - sugarcane world scenario,” in Sugarcane biorefinery, technology and perspectives. Editors F. Santos, S. C. Rabelo, M. De Matos, and P. Eichler (Academic Press), Cambridge, MA, USA, 1–19. doi:10.1016/B978-0-12-814236-3.00001-9
Dogbe, E. S., Mandegari, M., and Görgens, J. F. (2019). Assessment of the thermodynamic performance improvement of a typical sugar mill through the integration of waste-heat recovery technologies. Appl. Therm. Eng. 158, 113768. doi:10.1016/j.applthermaleng.2019.113768
Dogbe, E. S., Mandegari, M. A., and Görgens, J. F. (2018). Exergetic diagnosis and performance analysis of a typical sugar mill based on Aspen Plus® simulation of the process. Energy 145, 614–625. doi:10.1016/j.energy.2017.12.134
Du, S., Wang, R. Z., and Xia, Z. Z. (2014). Optimal ammonia water absorption refrigeration cycle with maximum internal heat recovery derived from pinch technology. Energy 68, 862–869. doi:10.1016/j.energy.2014.02.065
Ebrahimi-Moghadam, A., Farzaneh-Gord, M., Jabari Moghadam, A., Abu-Hamdeh, N. H., Lasemi, M. A., Arabkoohsar, A., et al. (2021). Design and multi-criteria optimisation of a trigeneration district energy system based on gas turbine, Kalina, and ejector cycles: exergoeconomic and exergoenvironmental evaluation. Energy Convers. Manag. 227, 113581. doi:10.1016/j.enconman.2020.113581
Fujii, S., Horie, N., Nakaibayashi, K., Kanematsu, Y., Kikuchi, Y., and Nakagaki, T. (2019). Design of zeolite boiler in thermochemical energy storage and transport system utilizing unused heat from sugar mill. Appl. Energy 238, 561–571. doi:10.1016/j.apenergy.2019.01.104
Ghannadzadeh, A., and Sadeqzadeh, M. (2017). Exergy aided pinch analysis to enhance energy integration towards environmental sustainability in a chlorine-caustic soda production process. Appl. Therm. Eng. 125, 1518–1529. doi:10.1016/j.applthermaleng.2017.07.052
Hung, T. C., Shai, T. Y., and Wang, S. K. (1997). A review of organic rankine cycles (ORCs) for the recovery of low-grade waste heat. Energy 22, 661–667. doi:10.1016/S0360-5442(96)00165-X
Kapanji, K. K., Haigh, K. F., and Görgens, J. F. (2021). Techno-economics of lignocellulose biorefineries at South African sugar mills using the biofine process to co-produce levulinic acid, furfural and electricity along with gamma valeractone. Biomass Bioenergy 146, 106008. doi:10.1016/j.biombioe.2021.106008
Khaljani, M., Khoshbakhti Saray, R., and Bahlouli, K. (2015). Comprehensive analysis of energy, exergy and exergo-economic of cogeneration of heat and power in a combined gas turbine and organic Rankine cycle. Energy Convers. Manag. 97, 154–165. doi:10.1016/j.enconman.2015.02.067
Kumar, B., Selvarasan, I., Annadurai, G., and Ramalingam, S. (2018). Thermodynamic analysis of a single effect lithium bromide water absorption system using waste heat in sugar industry. Therm. Sci. 22, 507–517. doi:10.2298/tsci151013285b
Li, T. X., Wang, R. Z., Kiplagat, J. K., Wang, L. W., and Oliveira, R. G. (2009). Thermodynamic study of a combined double-way solid–gas thermochemical sorption refrigeration cycle. Int. J. Refrig. 32, 1570–1578. doi:10.1016/j.ijrefrig.2009.05.004
Li, T. X., Wang, R. Z., and Li, H. (2014). Progress in the development of solid–gas sorption refrigeration thermodynamic cycle driven by low-grade thermal energy. Prog. Energy Combust. Sci. 40, 1–58. doi:10.1016/j.pecs.2013.09.002
Li, T. X., Xu, J. X., Yan, T., and Wang, R. Z. (2016). Development of sorption thermal battery for low-grade waste heat recovery and combined cold and heat energy storage. Energy 107, 347–359. doi:10.1016/j.energy.2016.03.126
Li, X., Song, J., Yu, G., Liang, Y., Tian, H., Shu, G., et al. (2019). Organic Rankine cycle systems for engine waste-heat recovery: heat exchanger design in space-constrained applications. Energy Convers. Manag. 199, 111968. doi:10.1016/j.enconman.2019.111968
Liu, X., Yang, X., Yu, M., Zhang, W., Wang, Y., Cui, P., et al. (2020). Energy, exergy, economic and environmental (4E) analysis of an integrated process combining CO2 capture and storage, an organic Rankine cycle and an absorption refrigeration cycle. Energy Convers. Manag. 210, 112738. doi:10.1016/j.enconman.2020.112738
Lu, F., Zhu, Y., Pan, M., Li, C., Yin, J., and Huang, F. (2020). Thermodynamic, economic, and environmental analysis of new combined power and space cooling system for waste heat recovery in waste-to-energy plant. Energy Convers. Manag. 226, 113511. doi:10.1016/j.enconman.2020.113511
Luo, D., Mahmoud, A., and Cogswell, F. (2015). Evaluation of low-GWP fluids for power generation with organic rankine cycle. Energy 85, 481–488. doi:10.1016/j.energy.2015.03.109
Malwe, P. D., Gawali, B. S., Choudhari, M. S., Dhalait, R. S., and Deshmukh, N. S. (2021). Energy and exergy analysis of an organic rankine cycle integrated with vapour compression refrigeration system. Adv. Appl. Math. Sci. 20.
Mana, A. A., Kaitouni, S. I., Kousksou, T., and Jamil, A. (2023). Enhancing sustainable energy conversion: comparative study of superheated and recuperative ORC systems for waste heat recovery and geothermal applications, with focus on 4E performance. Energy 284, 128654. doi:10.1016/j.energy.2023.128654
Men, Y., Liu, X., and Zhang, T. (2021). Performance comparison of different total heat exchangers applied for waste heat recovery. Appl. Therm. Eng. 182, 115715. doi:10.1016/j.applthermaleng.2020.115715
Mohammadi, F., Roedl, A., Abdoli, M. A., Amidpour, M., and Vahidi, H. (2020). Life cycle assessment (LCA) of the energetic use of bagasse in Iranian sugar industry. Renew. Energy 145, 1870–1882. doi:10.1016/j.renene.2019.06.023
Nami, H., and Anvari-Moghaddam, A. (2020). Small-scale CCHP systems for waste heat recovery from cement plants: thermodynamic, sustainability and economic implications. Energy 192, 116634. doi:10.1016/j.energy.2019.116634
Nami, H., Arabkoohsar, A., and Anvari-Moghaddam, A. (2019). Thermodynamic and sustainability analysis of a municipal waste-driven combined cooling, heating and power (CCHP) plant. Energy Convers. Manag. 201, 112158. doi:10.1016/j.enconman.2019.112158
Nami, H., Nemati, A., and Jabbari Fard, F. (2017). Conventional and advanced exergy analyses of a geothermal driven dual fluid organic Rankine cycle (ORC). Appl. Therm. Eng. 122, 59–70. doi:10.1016/j.applthermaleng.2017.05.011
Nemati, A., Nami, H., Ranjbar, F., and Yari, M. (2017). A comparative thermodynamic analysis of ORC and Kalina cycles for waste heat recovery: a case study for CGAM cogeneration system. Case Stud. Therm. Eng. 9, 1–13. doi:10.1016/j.csite.2016.11.003
Nemomsa, S., Tibba, G., Dejene, N., and Negeri, D. (2022). Design and simulation of combined flue gas and steam bagasse dryer to increase boiler efficiency of sugar factory. Rochester, NY, USA: Social Science Research Network. doi:10.2139/ssrn.4064539
Pan, M., Lu, F., Zhu, Y., Li, H., Yin, J., Liao, Y., et al. (2021). 4E analysis and multiple objective optimizations of a cascade waste heat recovery system for waste-to-energy plant. Energy Convers. Manag. 230, 113765. doi:10.1016/j.enconman.2020.113765
Pan, M., Zhu, Y., Liang, Y., Lu, F., Zhi, R., and Xiao, G. (2021). Performance assessment of a waste-heat driven CO2-based combined power and refrigeration cycle for dual-temperature refrigerated truck application. Energy Convers. Manag. 249, 114863. doi:10.1016/j.enconman.2021.114863
Pethurajan, V., Sivan, S., and Joy, G. C. (2018). Issues, comparisons, turbine selections and applications – an overview in organic Rankine cycle. Energy Convers. Manag. 166, 474–488. doi:10.1016/j.enconman.2018.04.058
Rosillo-Calle, F. (2016). A review of biomass energy – shortcomings and concerns. J. Chem. Technol. Biotechnol. 91, 1933–1945. doi:10.1002/jctb.4918
Singh, O. K. (2019). Exergy analysis of a grid-connected bagasse-based cogeneration plant of sugar factory and exhaust heat utilization for running a cold storage. Renew. Energy 143, 149–163. doi:10.1016/j.renene.2019.05.012
Singh, O. K. (2020). Application of Kalina cycle for augmenting performance of bagasse-fired cogeneration plant of sugar industry. Fuel 267, 117176. doi:10.1016/j.fuel.2020.117176
Srikhirin, P., Aphornratana, S., and Chungpaibulpatana, S. (2001). A review of absorption refrigeration technologies. Renew. Sustain. Energy Rev. 5, 343–372. doi:10.1016/S1364-0321(01)00003-X
Tan, D., Wu, Y., Lv, J., Li, J., Ou, X., Meng, Y., et al. (2023). Performance optimization of a diesel engine fueled with hydrogen/biodiesel with water addition based on the response surface methodology. Energy 263, 125869. doi:10.1016/j.energy.2022.125869
The Chemical Engineering Plant Cost Index (n.d.), (2022). Chemical Engineering. Available at: https://www.chemengonline.com/pci-home/ (Accessed September 21, 2022).
Tian, M., Yu, Z., Zhao, H., and Yin, J. (2018). Thermodynamic analysis of an integrated solid oxide fuel cell, Organic Rankine Cycle and absorption chiller trigeneration system with CO2 capture. Energy Convers. Manag. 171, 350–360. doi:10.1016/j.enconman.2018.05.108
Uphade, D. B. (2021). The potential of heat recovery for air-conditioning in sugar industry. J. Inst. Eng. India Ser. C 102, 1299–1309. doi:10.1007/s40032-021-00741-4
Vaja, I., and Gambarotta, A. (2010). Internal combustion engine (ICE) bottoming with organic rankine cycles (ORCs). Energy 35, 1084–1093. doi:10.1016/j.energy.2009.06.001
Wang, S., Liu, C., Li, J., Sun, Z., Chen, X., and Wang, X. (2020). Exergoeconomic analysis of a novel trigeneration system containing supercritical CO2 Brayton cycle, organic Rankine cycle and absorption refrigeration cycle for gas turbine waste heat recovery. Energy Convers. Manag. 221, 113064. doi:10.1016/j.enconman.2020.113064
Wang, X.-Q., Li, X.-P., Li, Y.-R., and Wu, C.-M. (2015). Payback period estimation and parameter optimization of subcritical organic Rankine cycle system for waste heat recovery. Energy 88, 734–745. doi:10.1016/j.energy.2015.05.095
Zare, V. (2020). Performance improvement of biomass-fueled closed cycle gas turbine via compressor inlet cooling using absorption refrigeration; thermoeconomic analysis and multi-objective optimization. Energy Convers. Manag. 215, 112946. doi:10.1016/j.enconman.2020.112946
Zhang, H., Liu, Y., Liu, X., and Duan, C. (2020). Energy and exergy analysis of a new cogeneration system based on an organic Rankine cycle and absorption heat pump in the coal-fired power plant. Energy Convers. Manag. 223, 113293. doi:10.1016/j.enconman.2020.113293
Zhang, X., Liu, X., Sun, X., Jiang, C., Li, H., Song, Q., et al. (2018). Thermodynamic and economic assessment of a novel CCHP integrated system taking biomass, natural gas and geothermal energy as co-feeds. Energy Convers. Manag. 172, 105–118. doi:10.1016/j.enconman.2018.07.002
Zhang, X., Wu, L., Wang, X., and Ju, G. (2016). Comparative study of waste heat steam SRC, ORC and S-ORC power generation systems in medium-low temperature. Appl. Therm. Eng. 106, 1427–1439. doi:10.1016/j.applthermaleng.2016.06.108
Nomenclature
Keywords: sugar mill, waste heat recovery, thermodynamic analysis, economic analysis, multi-objective optimization
Citation: Wang Z, Guan W, Zhang S, Sang H, Que W and Liang L (2024) Multi-objective optimization of the organic Rankine cycle cascade refrigeration cycle driven by sugar mills waste heat. Front. Energy Res. 12:1308519. doi: 10.3389/fenrg.2024.1308519
Received: 06 October 2023; Accepted: 01 February 2024;
Published: 07 March 2024.
Edited by:
Ellen B. Stechel, Arizona State University, United StatesReviewed by:
Vedran Mrzljak, University of Rijeka, CroatiaZhiqing Zhang, Guangxi University of Technology, China
Copyright © 2024 Wang, Guan, Zhang, Sang, Que and Liang. This is an open-access article distributed under the terms of the Creative Commons Attribution License (CC BY). The use, distribution or reproduction in other forums is permitted, provided the original author(s) and the copyright owner(s) are credited and that the original publication in this journal is cited, in accordance with accepted academic practice. No use, distribution or reproduction is permitted which does not comply with these terms.
*Correspondence: Lu Liang, bGlhbmdsdUBzdC5neHUuZWR1LmNu