- College of Mechanical Engineering, Jiamusi University, Jiamusi, Heilongjiang, China
Biomass combustion serves as a carbon-neutral energy solution but faces persistent challenges due to ash-related operational inefficiencies. This review systematically examines the thermochemical interactions among alkali metals (K, Na), chlorine (Cl), and sulfur (S) in biomass ash systems, elucidating their synergistic contributions to deposition mechanisms while evaluating mitigation approaches. KCl volatilization-condensation dominates in high-chlorine feedstocks (agricultural residues), whereas sulfates control ash deposition in lignocellulosic biomass. Bed agglomeration mechanisms stem from alkali silicate eutectics with depressed melting points (K2O·nSiO2), while chloride-induced degradation of protective oxide layers initiates metallic corrosion. Comprehensive assessment of mitigation techniques reveals aluminosilicate additives (kaolin) outperform conventional pretreatment methods (aqueous and acid leaching), achieving ash fusion temperature elevation beyond 1,300°C through interfacial reactions generating refractory kalsilite (KAlSiO4). The synthesis demonstrates that hybrid strategies combining fuel-specific preprocessing with optimized additive formulations produce synergistic mitigation effects. These insights provide mechanistic understanding essential for optimizing combustion system durability, while highlighting unresolved challenges in fuel-additive compatibility, additive stability under thermal cycling, and advanced corrosion-resistant material development.
1 Introduction
The imperative to achieve carbon neutrality under intensifying climate change has positioned biomass combustion as a critical transitional technology, with potential to displace 8.2 GtO2-equivalent annual emissions from fossil fuels. However, its sustainable implementation faces dual environmental constraints: combustion-generated particulate emissions (PM2.5: 2.1–5.3 g/kg, PM10: 3.8–7.6 g/kg) and carbon monoxide (18–47 g/kg) exacerbate atmospheric pollution, while intrinsic ash behavior-particularly alkali-induced slagging-compromises 12%–18% of combustion efficiency in industrial systems (Huang et al., 2024; Kim et al., 2024). This operational paradox underscores the necessity to resolve ash transformation mechanisms, where potassium-silicate interactions dominate slag formation in agricultural residues (slagging indices >0.8), contrasting with sulfate-controlled deposition in woody biomass. Such fundamental limitations not only challenge emission reduction commitments but also hinder the technology’s scalability under Net-Zero scenarios. As a major agricultural country, China possesses abundant agricultural straw resources, particularly from corn, wheat, and rice-the three predominant contributors to national straw supply (Antar et al., 2021). These resources are predominantly utilized through three principal pathways: domestic fuel provision, agricultural fertilization, and industrial feedstock applications. Direct combustion has emerged as an effective strategy for large-scale biomass utilization, yet the characteristic high chlorine and alkali metal content inherent in Chinese crop straw induces significant technical challenges, including heat exchange surface deposition and high-temperature slagging during combustion processes. Current research efforts primarily concentrate on three technological pathways: biomass gasification, combustion, and pyrolysis (Figure 1).
Biomass resources are formally defined as heterogeneous organic substrates originating from photosynthetic conversion of atmospheric CO2, serving as renewable feedstocks for energy production and biorefinery applications (Sukatis, Wee, and Aris 2022). Based on provenance and physicochemical characteristics, they are systematically categorized into four classes: (1) Woody biomass comprising forestry residues (e.g., bark, branches), silvicultural byproducts (e.g., sawdust, wood chips), and post-consumer timber; (2) Agricultural biomass including lignocellulosic crop residues (e.g., cereal straws, rice husks), dedicated energy crops (e.g., Miscanthus, switchgrass), and agro-industrial processing wastes (e.g., sugarcane bagasse); (3) Waste-derived biomass encompassing municipal solid organic fractions, wastewater treatment biosolids, and construction/demolition cellulose-rich debris; (4) Animal-derived biomass consisting of livestock manures, anaerobic digestion effluents, and slaughterhouse residues (Guo et al., 2024; Alami et al., 2021). These carbonaceous materials exhibit near-carbon-neutral characteristics when utilized in energy systems, as photosynthetic carbon sequestration during growth phases counterbalances subsequent thermochemical conversion emissions. Strategic advantages stem from their global distribution scalability, biomass can play two roles, namely, bio-carbon capture and storage/bio-carbon capture and storage, and compatibility with circular bioeconomy frameworks through cascaded utilization pathways (Ilmiawati et al., 2025).
Biomass is composed of 38%–50% cellulose, 23%–32% hemicellulose, 15%–25% lignin, and 5%–13% other components (e.g., inorganic species and extracts) (Table 1) (Li et al., 2025). Its elemental composition is dominated by carbon (C), hydrogen (H), and oxygen (O), with carbon (approximately 50%) and oxygen (around 40%) together accounting for over 90% of its dry material. Slagging, ash accumulation, and slagging in biomass combustion systems can be attributed to intricate interactions between design parameters (e.g., thermal gradients and gas flow dynamics) and the unique physicochemical characteristics of the fuel (Su et al., 2024). In addition, biomass contains trace quantities of minerals, either in ionic form or as chemical compounds, such as aluminum (Al), calcium (Ca), iron (Fe), magnesium (Mg), sodium (Na), potassium (K), phosphorus (P), sulfur (S), and silicon (Si). At a structural level, hemicellulose and lignin form a chemically bonded matrix that encapsulates cellulose. Most of the ash-forming constituents are chiefly concentrated within the three-dimensional network of lignin. In comparison, the existence of major mineral elements results in ash fouling and slagging towards process equipment. In the combustion process, basic metal oxides participate in complex combustion reactions and eventually form silicates, chlorides and sulfates. These compounds can be mixed with other metal oxides to form low-temperature stable blends. Then alkali earth metals may also react with or dissolve into the melt K-silicates (Bostrom et al., 2012).
Biomass feedstock ash composition and its physicochemical attributes—especially the levels of alkali/alkaline earth metals (AAEMs), chlorine (Cl), and silicon-sulfur compounds—serve as critical determinants of combustion efficiency and operational reliability. The rapid release of volatiles from biomass, coupled with the intermittent feeding of biomass fuels and uneven spatial distribution of fuel particles, leads to inconsistency between the timescales of chemical reactions and diffusion. This results in inadequate mixing of fuel and oxygen, thereby reducing combustion efficiency (Ma et al., 2025). In particular, AAEMs (e.g., potassium, sodium, and calcium) combined with chlorine lower ash fusion temperatures through eutectic interactions, whereas silicon-sulfur compounds (such as SiO2-SO3 complexes) intensify ash agglomeration. Collectively, these constituents are recognized as key drivers of the interconnected processes leading to slagging, fouling, and high-temperature slagging, thereby prompting the development of novel material and process solutions (Yao et al., 2020). Operational challenges related to ash manifest via four primary mechanisms: slagging induced by alkali metals, agglomeration from silicate melts, particulate deposition dynamics, and slagging mediated by chlorine. Furthermore, elevated concentrations of chlorine and alkali metals (notably K and Na) in combustion environments intensify ash deposition, while the low melting points of alkali metal compounds facilitate particle adhesion and bonding (Tiainen, Daavitsainen, and Laitinen 2002). Under elevated thermal conditions, alkali metals and their derivatives follow two distinct migration routes: one involving direct deposition onto furnace surfaces via inertial impaction, and another characterized by vapor-phase transport with subsequent heterogeneous condensation onto downstream heat-exchanger surfaces, forming submicron fly ash particles. Addressing the complex multiphase evolution of biomass ash remains a significant obstacle to expanding clean energy systems. Figure 2 illustrates the trend in publications over the past 5 years focusing on biomass for diverse applications, thereby highlighting its emerging potential and growing scholarly attention. Biomass combustion technology-an essential pillar of decarbonization strategies-has garnered significant interest owing to its sustainable feedstock foundation and carbon-neutral life cycle. However, large-scale industrial deployment is impeded by persistent operational challenges, including slagging, fouling, and high-temperature corrosion. These issues stem from the migration, transformation, and interactions of alkali metals, chlorine, and sulfur, which collectively govern the dynamics of ash fusion and deposition. Although previous studies have partially unraveled ash evolution pathways, high ash containing biomass demonstrates several challenges when applying it as a biofuel owing to the increase in the capital and operating costs (Hess et al., 2019). Biological co-combustion, leaching, and adding additives have been identified as the most effective deashing treatment methods.
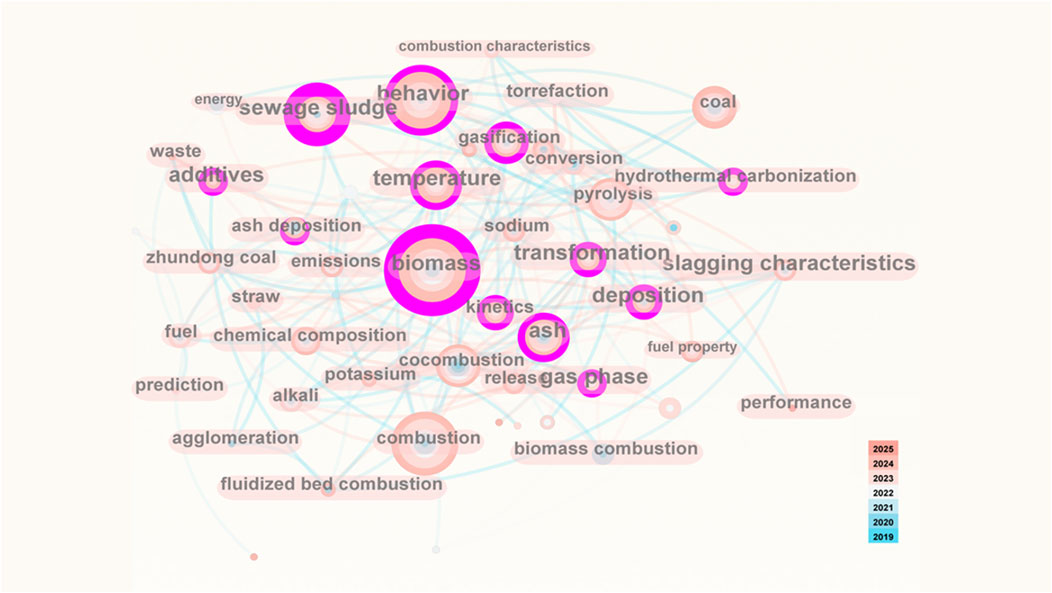
Figure 2. Representation of bibliometric analyses of words in relation to research on the use of biomass as a substrate in various applications, based on data obtained from the Scopus database between 2019 and 2025 using the Citespace program.
This review is to systematically elucidate the thermochemical interactions of alkali metals, chlorine, and sulfur in biomass ash systems and their roles in slagging mechanisms. Additionally, it evaluates mitigation strategies, including leaching pretreatments and aluminosilicate additives, to address ash-related operational challenges. By clarifying the slagging mechanisms and quantify alkali metal migration pathways, this advances the optimization of biomass combustion systems for enhanced durability and efficiency. The review provides a foundation for developing scalable solutions to mitigate ash deposition and corrosion, thereby supporting sustainable biomass energy integration into decarbonization frameworks.
2 Biomass ash and mechanism of slagging
In the process of biomass energy utilization, biomass ash is an important factor affecting the utilization process. Due to the high content of alkali metals, alkaline earth metals and chlorine in biomass fuel, After the alkali metal sulfate, chloride, carbonate and silicate enter the gas phase successively, they condense on the surface of fly ash particles, which reduces the melting point of fly ash and increases the viscosity of fly ash. Under the action of the air flow in the furnace, they bond on the heating surface and form the slag (Werkelin et al., 2010).
Figure 3 illustrates the processes of ash generation and modification during biomass combustion. Biomass combustion (Jia and Lighty 2012; Dai et al., 2025), volatile organometallic species (e.g., chromium [Cr] and vanadium [V]) are initially released during the ignition of biomass particles and the subsequent formation of char. Thereafter, alkali and alkaline earth metals-specifically potassium (K), sodium (Na), and calcium (Ca)-along with trace volatile elements such as mercury (Hg), arsenic (As), and selenium (Se), are liberated through surface diffusion from the char matrix. When the gas-phase temperature declines, these compounds undergo nucleation, resulting in the production of submicron aerosol particles via gas-to-particle conversion. Additionally, a portion of these volatiles condenses onto the surfaces of the residual fly ash. Elevated levels of alkali metals, particularly potassium (K), precipitate ash-related operational challenges, including high-temperature corrosion and slagging phenomena, owing to the synergistic interplay between nucleation-condensation processes and secondary chemical reactions.
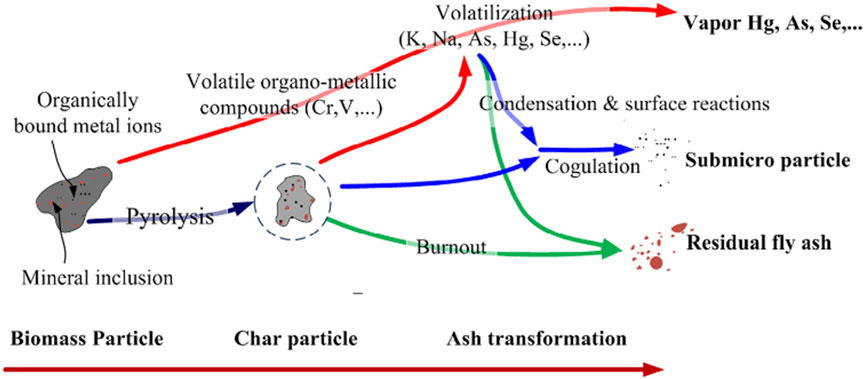
Figure 3. Formation and transformation mechanism of ash in biomass combustion process (Jia and Lighty 2012) Copyright © 2012 American Chemical Society.
2.1 Potassium (K) and sodium (Na)
Alkali metals (lithium (Li), sodium (Na), potassium (K), rubidium (Rb), cesium (Cs), and francium (Fr)) are defined by an ns1 configuration in their s orbital and are classified as Group 1 elements on the periodic table. These metals exhibit distinct properties, including high chemical reactivity, notable luster, and relatively low mechanical strength at ambient temperature, a behavior attributed to their minimal ionization energies. In biomass ash, sodium and potassium are particularly prevalent due to their superior mobility, serving as principal agents in adverse processes such as aerosol generation and slag accumulation. During the thermal decomposition of biomass, alkali metals volatilize, producing gas-phase precursors that nucleate into particulate compounds-such as KOH, KCl, K2SO4, NaCl, and Na2SO4 through gas-solid transformation mechanisms. These formed aerosol particles promote ash agglomeration by means of surface condensation and chemical bonding, ultimately facilitating slag formation via eutectic interactions in high-temperature regions (Mlonka-Medrala et al., 2020).
The thermochemical processing of biomass fuels initiates intricate alkali metal (K/Na) speciation dynamics and migration routes, driven by pyrolytic degradation of lignocellulosic polymers (lignin, cellulose, hemicellulose). Release behavior varies markedly with feedstock characteristics: (1) Low-chlorine biomass (e.g., woody types): Alkali metals primarily volatilize into stable sulfates (K2SO4, Na2SO4) and aluminosilicates (KAlSi3O8), facilitated by sulfur-silicate interactions; (2) High-chlorine biomass (e.g., herbaceous/straw feedstocks): Alkali species form volatile chlorides (KCl, NaCl) via chlorine-mediated coordination, with straw-derived fuels releasing substantial gaseous KCl/NaCl at elevated temperature (Wei, Schnell, and Hein 2005). Within the intermediate temperature, chloride-sulfate conversion occurs through gas-phase interactions between alkali chlorides and sulfur oxides (SO2/SO3) present in combustion effluents. Resulting sulfates undergo homogeneous nucleation to generate submicron aerosols (<1 µm), which subsequently condense on heat exchanger surfaces via thermophoretic forces.
Despite high alkali concentrations, chlorine-deficient woody biomass generates gaseous hydroxides (KOH, NaOH) during thermal degradation. During effluent cooling, these hydroxides participate in heterogeneous reactions with sulfur oxides to yield sulfates, while inherent silicates (e.g., SiO2) catalyze nucleation, amplifying aerosol production. Alkali species adsorb onto fly ash particulates during gas-to-particle transitions, markedly reducing ash fusion temperatures (AFT) and elevating surface viscosity by two to three logarithmic units (Wang et al., 2008; Chen et al., 2024). Turbulent flow conditions promote collisions among viscous particles, leading to stratified slag accumulation on heat exchanger surfaces. These processes are thermodynamically regulated by the equilibria outlined in Equations 1–5 (Blomberg 2011; Thy et al., 2006), where M represents alkali or alkaline earth metals.
Sulfation reaction:
Chlorination reaction:
2.2 Calcium (Ca) and magnesium (Mg)
Group IIA elements (Be, Mg, Ca, Sr, Ba, Ra), termed alkaline earth metals, display lower reducing capacity relative to alkali metals at ambient conditions (25°C, 1 atm), a property governed by their ns2 valence configuration. These elements exist as lustrous metallic solids characterized by elevated ionization energies. Analyses of biomass ash composition reveal that Ca and Mg constitute over 90% of alkaline earth metal mass fractions (Yu et al., 2021), a pattern stemming from their abundance in organic matrices (e.g., calcium pectate bonds in plant cell walls) and the superior thermal resilience of their mineralized forms. Under combustion conditions, these metals preferentially form thermally stable crystalline structures. Such refractory phases increase ash fusion temperatures while suppressing the generation of low-melting alkali silicates via competitive ion exchange mechanisms (Lindstrom et al., 2007).
As the predominant mineral constituent in woody biomass, calcium manifests in three primary configurations: organically chelated, acid-leachable, and acid-resistant. Acid-resistant calcium, primarily sequestered in aluminosilicate matrices, demonstrates thermal resilience surpassing common combustion range, thus minimally impacting gaseous pollutant evolution mechanisms. Conversely, organically chelated and acid-leachable calcium species decompose via decarboxylation under pyrolytic conditions, yielding nanoscale CaO particles that actively engage in heterogeneous interactions within combustion chambers and effluent streams. These CaO nanoparticles promote SO2 sulfation through chemisorptive pathways, as quantified in Equation 6 (Niu, Tan, and Hui 2016). CO2 and SO2 competitively adsorb onto CaO surfaces, producing passivating carbonate-sulfate surface films that suppress alkali chloride sulfation. This phenomenon amplifies the deposition likelihood of unreacted chlorides on thermal exchange interfaces, intensifying fouling and corrosion hazards.
2.3 Sulfur (S), chlorine (Cl) and phosphorus (P)
Non-metallic elements, such as sulfur (S), chlorine (Cl), and phosphorus (P), are characterized by properties including low atomic density, high electronegativity, and limited electrical conductivity. They play a crucial role in directing the formation routes of gaseous pollutants during biomass combustion. For example, Capablo et al. measured chlorine and sulfur contents across various biomass feedstocks, encompassing agricultural residues (e.g., brewery spent grains with 0.01 wt% Cl and 0.22 wt% S), forestry residues (e.g., empty fruit bunches with 0.35 wt% Cl and 0.13 wt% S), and municipal waste biomass (e.g., shea waste with 0.24 wt% Cl and 0.13 wt% S) (Capablo et al., 2009). Although present in trace amounts (<1 wt%), these elements exert a disproportionate influence on the kinetics of thermal decomposition and the emission profiles of pollutants. In biomass fuels, sulfur primarily occurs as inorganic sulfate species (SO42-) and heterocyclic organosulfur compounds; during combustion, these compounds decompose thermally to yield sulfur dioxide (SO2) in the gas phase. This transformation promotes the formation of acid rain precursors and particulate matter, underscoring the environmental significance of sulfur speciation in combustion systems (Niu et al., 2013). Conversely, chlorine mainly exists in water-soluble chloride forms (e.g., KCl, NaCl) in biomass feedstocks; these chlorides volatilize during combustion to generate gaseous alkali metal chlorides (KCl(g) and NaCl(g)) (Bostrom et al., 2012). The volatile chlorides then participate in both homogeneous and heterogeneous reaction pathways, as detailed in Equation 3, thereby contributing to corrosive deposit formation and the development of secondary aerosols. Moreover, Blasing et al. identified phosphorus as a critical non-metallic trace element in biomass, with measurable levels in lignocellulosic feedstocks such as willow, poplar, oak, and lignocellulose-rich residues (e.g., pine seed husks, hazelnut shells, and almond shells) (Blaesing, Zini, and Mueller 2013). Notably, even minor chlorine contents can intensify ash slagging, with slagging severity showing a strong positive correlation with chloride concentration due to the formation of low-melting-point eutectic mixtures. This observation underscores the essential role of chlorine speciation in feedstocks for mitigating combustion-related fouling and slagging.
3 Principle of slagging in biomass combustion
Although both slagging and fouling represent ash deposition processes in biomass boiler flue gas systems, they operate via fundamentally different mechanisms and are influenced by varying temperature regimes. Slagging manifests in high-temperature regions (above 1,000°C) via viscous flow sintering of molten ash, a process propelled by the phase transformation of alkali-rich silicates and aluminosilicates. Conversely, fouling prevails in lower-temperature areas (below 800°C) through the dry deposition of unmolten particulate ash (Shao et al., 2012). The unmolten ash is defined by a melting point that considerably exceeds the temperature of the deposition surface. Such deposits undermine the efficiency of slag removal, diminish thermal performance, and markedly curtail the operational lifespan of the boiler (Indrawan et al., 2020; Corona et al., 2020). Compared to coal-fired boilers, biomass systems exhibit a greater susceptibility to slagging and fouling, attributable to their elevated levels of alkali metals and chlorine (Rong et al., 2017). Chlorine promotes the volatilization of potassium as KCl vapors, which subsequently condense into submicron aerosols. These aerosols then deposit by means of thermophoresis-a migration driven by temperature gradients-and inertial impaction, ultimately forming tenacious layers on the surfaces of convective passes.
One study found that the K, S and Cl of biomass fuel gradually decreased with the temperature rising to 1,200°C, and their ash content also gradually decreased (Johansen et al., 2011). Then they remain either unchanged or decrease slightly between 1,200°C and 1,400°C. Cl concentration is essentially zero at 815°C. However, between 815°C and 1,200°C, K concentration decreases because of the volatility of KOH and K2SO4 aerosols. Meanwhile, inorganic S is released in the form of SO2 by the decomposition of K2SO4. All these conditions result in the continuing decrease of the ashing ratio as temperature increase until 1,200°C.
Deposits on the walls of tubes emerge from both solid-phase mineral conversions and vapor-phase condensation processes. The resulting layers, typically rich in alkali sulfates (such as K2SO4) and chlorides (such as KCl), possess adhesive qualities attributable to their low eutectic melting temperature, thereby fostering secondary agglomeration through capillary forces. Controlled drop-tube furnace experiments conducted by Wang et al. demonstrated that a synergistic interaction between sulfate and chloride compounds critically influences ash deposition kinetics in biomass combustion systems. At combustion temperatures exceeding 800°C–900°C, gaseous KCl participates in heterogeneous gas-solid reactions with SO2 (Wang L. et al., 2012).
When flue gas temperatures drop below 500°C, thermophoretic effects combined with turbulent diffusion drive the condensation of alkali-enriched aerosols, thereby initiating the formation of a sticky slag layer on heat exchange surfaces. This viscous film subsequently augments the adherence potential for additional particulate deposits. A portion of these alkali aerosols condenses onto fly ash particles, either creating tacky surfaces or reacting with refractory oxides to produce eutectic mixtures with melting points below 700°C. Upon further reduction of the gas temperature to below 300°C, alkali vapors traverse a sequence of phase changes: an initial phase (comprising condensation, nucleation, and coalescence) yields submicron aerosols (less than 1 μm), whereas a secondary phase, marked by oxidation, re-nucleation, and coalescence, produces coarser fly ash particles (greater than 10 μm) (Bostrom et al., 2012). Irrespective of their surface viscosity, coarse particles predominantly deposit onto the primary slag layer via inertial impaction. In contrast, fine particles enriched with potassium, sodium, chlorine, and sulfur (e.g., KCl, K3Na(SO4)2) tend to concentrate on surfaces due to their elevated surface-to-volume ratios, thereby enhancing the adsorption of silicon- and aluminum-rich coarse particles through electrostatic and van der Waals interactions (Nordgren et al., 2013). The lower adhesion efficiency between fine and coarse particles triggers secondary enrichment processes, ultimately producing self-organized, stratified slag formation via a hierarchical deposition mechanism. This process elucidates the heterogeneous microstructure characteristic of combustion deposits in industrial biomass boilers. In summary, the initial slag layer is composed of fine ash particles alongside coarse particles that display only partial adhesion. Owing to the surface’s low operational temperature and substantial thermal resistance, the layer remains non-adhesive even as its temperature approaches, but does not exceed, the ash fusion point. When ash-laden flue gas impinges upon the slag layer, inertial forces facilitate the primary deposition of particles that are softened or partially molten. As the slag layer accumulates, its surface temperature eventually exceeds the melting threshold, thereby transitioning into a molten state. Thereafter, fly ash particles coalesce to form a dense coke layer through secondary deposition. Gravitational shedding occurs when the deposit’s weight overcomes its structural cohesion or adhesion to the furnace wall (Zhou et al., 2013; Liu et al., 2011). Ultimately, the interplay between layer accumulation and gravitational shedding establishes a dynamic equilibrium that stabilizes the deposit thickness (Figure 4) (Niu et al., 2014).
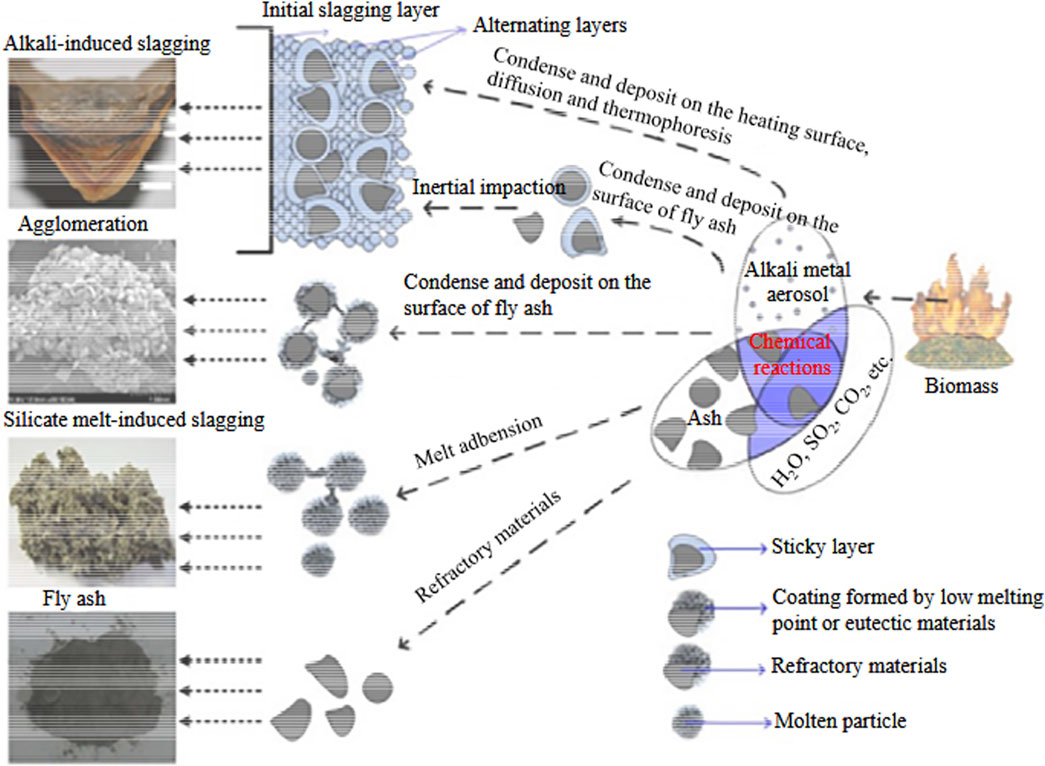
Figure 4. Slagging growth mechanism in boiler (Niu et al., 2014). Reprinted with permission from Reference 70. Copyright 2025, Elsevier and Copyright clearance, License number (6057670810864).
4 Biomass ash control methods
The application of high-ash biomass in thermochemical combustion systems poses significant technical and economic barriers, stemming from elevated capital expenditure and operational expense linked to ash management, accelerated equipment degradation, and unplanned maintenance interruptions (Hess et al., 2019). Three principal approaches-co-processing with low-ash feedstocks, leaching processes (e.g., water or acid pretreatment to diminish alkali concentrations), and additive integration (e.g., aluminosilicates to sequester mobile alkali species) have demonstrated efficacy in addressing ash-related inefficiencies. Selecting the optimal methodology necessitates a comprehensive evaluation of feedstock-specific ash composition (e.g., alkali metals, chlorine, silica ratios), ash production rates, regulatory limitations (e.g., particulate emission thresholds), and site-dependent variables, including reactor design and operational adaptability (Bostrom et al., 2012).
4.1 Blend combustion
Biomass fuels are characterized by elevated alkali metal content, which induces molten ash formation under high-temperature conditions. This phenomenon facilitates slag deposition on heat exchange surfaces and exacerbates corrosion at elevated temperatures. Co-combustion, the integrated utilization of biomass with complementary fuels for energy generation, has emerged as a viable approach for large-scale waste management and direct energy recovery (Aziz, Budianto, and Oda 2016; Khalid et al., 2024). This method not only diminishes waste stockpiles but also facilitates energy extraction. Relative to mono-fuel combustion, it substantially reduces the release of pollutants into the atmosphere (Rong et al., 2017). Han J (Han et al., 2023) found that have investigated blending biomass with municipal sludge and select coal varieties (e.g., high-calcium coal), revealing that such mixtures minimize ash agglomeration during thermal conversion. Table 2 summarizes documented applications of co-combustion systems addressing ash-related challenges. Suyatno, S (Suyatno et al., 2025) study found that biomass mixed fuel can reduce the risk of slagging, as well as improve the heating value. Research indicates that combining sewage sludge with biomass improves combustion performance while reducing ecological hazards, highlighting its technical viability (Wang et al., 2019). In light of operational limitations posed by ash-related issues in biomass-only systems, co-combustion represents a pragmatic strategy to avert equipment degradation. Analytical investigations highlight that synergistic effects arising from the interplay of biomass physicochemical characteristics improve combustion behavior, offering insights for refining co-combustion protocols (Ni et al., 2022).
4.2 Washing
Washing pretreatment effectively mitigates ash-related challenges by leaching water-soluble ions (e.g., K+, Cl−, SO42-) from biomass, thereby suppressing the formation of low-melting alkali salts and eutectics during combustion (Tonn et al., 2012). Inorganic species present in biomass can be divided into water soluble, acid soluble and residual compounds (Guo et al., 2020). Water soluble are salts which are easily soluble in water, e.g., alkali chlorides, alkali earth chlorides, sulfates and carbonates. Acid soluble are organically bound inorganic species and minerals that are indissoluble in water but soluble in acid, i.e., alkali earth carbonates, sulfates. Residual compounds are other acid indissoluble minerals. However, acid washing necessitates wastewater treatment to neutralize residual acidity and recover dissolved ions, adding operational complexity compared to water-only leaching.
4.2.1 Water washing
Water washing is commonly utilized in biomass pretreatment due to the high solubility of alkali metals (approximately 90%) and complete solubility of alkali chlorides in aqueous or acidic solutions (Wei et al., 2019). This process enhances fuel quality by preserving organic constituents, lowering ash content, and elevating calorific value. Such as, in the study (Singhal, Konttinen, and Joronen 2021) that the effect of water washing on fuel properties was evaluated, Washing was shown to have a high impact on the fuel properties and the fouling and slagging propensity. After washing, a significant increment in the content of VS (≤5.2%), C (≤1.8%), and O (≤2.3%), and a slight improvement in HHVs (≤0.5 MJ/kg).Simultaneously, the high removal of ash (≤39%), Cl (≤87%), S (≤74%), Mg (≤71%), K (≤68%), N (≤46%), P (≤45%), and Ca (≤29%) was also noted. Thereby optimizing combustion performance. Furthermore, it efficiently extracts volatile components such as alkali metals, chlorine, and sulfur, which elevates ash fusion temperatures. These modifications mitigate operational challenges linked to biomass combustion, including particulate emissions, ash agglomeration, and slagging of equipment.
Gudka et al. reported that hot water leaching (85°C–95°C) of wood pellets elevates the initial ash deformation temperature (IDT) from 820°C to 1,400°C, with potassium and sodium removal efficiencies ranging from 50%–90% and 10%–90%, respectively, contingent on feedstock porosity and treatment duration (Gudka et al., 2016). Carrillo et al. observed a 20% decrease in ash content and a 53% rise in lignin concentration post-washing (Carrillo, Staggenborg, and Pineda 2014). Investigations into water-washed biomass from varied sources, including corn straw and pepper residues, corroborate substantial reductions in ash slagging (clinker formation), underscoring the method’s efficacy across diverse feedstocks. Table 3 summarizes documented applications of water washing for ash-related issue mitigation.
4.2.2 Acid washing
Acid pretreatment improves ion elimination via proton (H+)-mediated exchange mechanisms, displacing alkali cations adsorbed on organic matrices. This process reduces boiler corrosion rates by limiting KCl/NaCl vapor deposition on superheater surfaces. Gao et al. reported barley straw treated with 7% nitric acid demonstrated >83% removal of K, Na, Ca, and Mg, alongside a 39.7% reduction in ash content (Gao et al., 2022). Subsequent thermal treatment at 230°C–290°C under nitrogen flow (200 mL/min, 30 min) elevated the C/O ratio and improved the higher heating value. Additionally, acid pretreatment enriched bio-oil sugar concentrations by suppressing amino acid and inorganic mineral retention. Feng et al. subjected lignocellulosic biomass (white pine, spruce, and birch bark) to 0.5 mol/L HNO3 for 8 h (solid-liquid ratio 1:20 g/mL, ambient temperature), achieving significant potassium removal across all samples, with notable calcium reduction in spruce and birch bark (Feng et al., 2014). Comparative analyses of acids such as HCl and CH3COOH reveal discrepancies in alkali metal extraction efficiency, ash agglomeration tendencies, and fusion temperature modulation. Representative applications of acid washing in mitigating ash-related challenges are summarized in Table 4.
While acid leaching represents a low-waste, practical approach for extracting alkali and alkaline earth metals (AAEMs) from biomass that improves ash removal efficacy and economic feasibility, its scalability is hindered by corrosive equipment degradation, residual acid accumulation risks, and environmental hazards (e.g., aquatic or terrestrial ecosystem contamination). Current research focuses on mitigating these limitations through innovations in pretreatment protocols and bio-oil refinement technologies, which are expected to enhance both sustainability and industrial applicability.
4.3 Additive
Additives are extensively employed to mitigate ash-related issues by modulating ash fusion characteristics—transforming low-melting components into thermally stable phases to increase ash fusion temperatures. These additives are classified into three primary categories: aluminosilicates, sulfur-containing compounds, and phosphorus derivatives (Wang et al., 2022). Through compositional modification of ash, additives regulate its melting behavior (Miguez et al., 2021). Li et al. demonstrated that blending sludge with biomass facilitates the formation of high-melting-point compounds such as potassium aluminosilicates (e.g., KAlSi2O6 and KAlSi2O8) and alkali phosphates [e.g., Ca9MgK(PO4)7], enabling both resource recovery from sludge and suppression of corrosive potassium chloride emissions (Li et al., 2013). Experimental evidence indicates that Ca3(PO4)2 not only dilutes ash constituents but also reacts with potassium salts to yield refractory phases like Ca10K(PO4)7 and Ca5(PO4)3Cl, thereby elevating ash melting temperatures. These findings illustrate Ca3(PO4)2’s efficacy in preventing ash sintering and fusion during biomass combustion.
Miccio et al. conducted systematic evaluations of fireclay and quartzite additives for olive pomace combustion, revealing fireclay’s sustained inhibition of bed agglomeration under prolonged thermal exposure (Miccio et al., 2019). Batir et al. elucidated the potassium immobilization mechanism of kaolin: interfacial reactions between kaolinite (Al2Si2O5(OH)4) and KCl/KOH generate kalsilite (KAlSiO4), a high-melting phase that mitigates slag formation induced by alkali migration during biomass thermochemical conversion (Batir, Selcuk, and Kulah 2019). Recent studies have validated kaolin’s efficacy in ash modification, particularly its unparalleled capacity for potassium chloride retention (Waqas et al., 2023). The mechanism involves thermal activation between 450°C and 600°C, where kaolinite undergoes dehydroxylation to produce reactive amorphous metakaolin (Al2O3·2SiO2) with concurrent release of structural water. Activated metakaolin subsequently engages in solid-state reactions with potassium species in ash, forming potassium aluminosilicate phases with melting points exceeding 1,300°C, as outlined in Equations 7–15 (Niu, Tan, and Hui 2016; Wang Xuebin et al., 2012):
5 Conclusion and prospect
5.1 Conclusion
This comprehensive review elucidates the intricate interplay between biomass ash chemistry and operational challenges in combustion systems, with a focus on slagging and corrosion mechanisms. Key findings reveal that alkali metals (K, Na), chlorine, and sulfur govern ash deposition dynamics through distinct pathways contingent on feedstock composition. High-chlorine agricultural residues exhibit KCl volatilization-condensation as the dominant slagging pathway, whereas lignocellulosic biomass is prone to sulfate-driven ash fusion. Thermodynamic analyses confirm that alkali silicate eutectics (e.g., K2O·nSiO2) and chloride-induced oxide layer degradation synergistically exacerbate bed agglomeration and metallic corrosion. Mitigation strategies demonstrate that aluminosilicate additives, particularly kaolin, outperform conventional leaching pretreatments by elevating ash fusion temperatures beyond 1,300°C through interfacial reactions forming refractory kalsilite (KAlSiO4) Hybrid approaches integrating fuel-specific preprocessing (e.g., acid washing) with optimized additive formulations achieve synergistic reductions in ash adhesion and alkali mobility, enhancing combustion efficiency. However, scalability remains constrained by unresolved challenges in fuel-additive compatibility, additive stability under thermal cycling, and residual acid contamination risks.
5.2 Prospects
Future research should prioritize three domains to advance biomass combustion technology. First, mechanistic studies on additive-ash interactions under transient thermal conditions are critical to optimize kaolin’s performance while addressing its long-term stability limitations. Second, the development of bio-compatible additives-such as phosphorus-enriched mineral composites-could mitigate corrosion risks without compromising ash fusion thresholds. Third, advanced computational models coupling ash chemistry with reactor hydrodynamics are essential to predict slagging propensity across diverse feedstocks.
The authors advocate for a paradigm shift toward circular bioeconomy frameworks, emphasizing co-combustion with phosphorus-rich waste streams (e.g., sewage sludge) to valorize underutilized resources while suppressing alkali volatilization. Conversely, overreliance on acid leaching-despite its efficacy in AAEM removal-should be cautiously evaluated due to its environmental footprint and operational complexity. Innovations inin situmonitoring systems (e.g., AI-driven deposit sensors) and corrosion-resistant alloys (e.g., Cr-Mo-Ni composites) are urgently needed to bridge the gap between laboratory-scale breakthroughs and industrial deployment. Ultimately, interdisciplinary collaboration among material scientists, combustion engineers, and policymakers will be indispensable to realize biomass energy’s full potential within global decarbonization agendas.
Author contributions
JL: Project administration, Supervision, Writing – original draft, Writing – review and editing. QW: Data curation, Visualization, Writing – original draft, Writing – review and editing. DS: Resources, Supervision, Writing – original draft, Writing – review and editing. BC: Visualization, Writing – original draft. PH: Conceptualization, Funding acquisition, Project administration, Resources, Supervision, Writing – original draft, Writing – review and editing. QH: Conceptualization, Funding acquisition, Project administration, Resources, Supervision, Writing – original draft, Writing – review and editing.
Funding
The author(s) declare that financial support was received for the research and/or publication of this article. This work was supported by the Basic scientific research Funds project of Heilongjiang Universities (grant numbers 2024-KYYWF-0558 and 2024-KYYWF-0554) and the New round of “Double first-class” collaborative innovation project of Heilongjiang Province (grant numbers LJGXCG 2023-080).
Acknowledgments
The authors would like to thank the College of Mechanical Engineering, Jiamusi University.
Conflict of interest
The authors declare that the research was conducted in the absence of any commercial or financial relationships that could be construed as a potential conflict of interest.
Generative AI statement
The author(s) declare that no Generative AI was used in the creation of this manuscript.
Publisher’s note
All claims expressed in this article are solely those of the authors and do not necessarily represent those of their affiliated organizations, or those of the publisher, the editors and the reviewers. Any product that may be evaluated in this article, or claim that may be made by its manufacturer, is not guaranteed or endorsed by the publisher.
References
Alami, A. H., Tawalbeh, M., Alasad, S., Ali, M., Alshamsi, M., and Aljaghoub, H. (2021). Cultivation of Nannochloropsis algae for simultaneous biomass applications and carbon dioxide capture. Energy Sources Part a-Recovery Util. Environ. Eff. 12, 8471–8482. doi:10.1080/15567036.2021.1933267
Antar, M., Lyu, D. M., Nazari, M., Shah, A. T., Zhou, X. M., and Smith, D. L. (2021). Biomass for a sustainable bioeconomy: an overview of world biomass production and utilization. Renew. & Sustain. Energy Rev. 139, 110691. doi:10.1016/j.rser.2020.110691
Aziz, M., Budianto, D., and Oda, T. (2016). Computational fluid dynamic analysis of Co-firing of palm kernel shell and coal. Energies 9 (3), 137. doi:10.3390/en9030137
Batir, O., Selcuk, N., and Kulah, G. (2019). Effect of kaolin addition on alkali capture capability during combustion of olive residue. Combust. Sci. Technol. 191 (1), 43–53. doi:10.1080/00102202.2018.1452376
Blaesing, M., Zini, M., and Mueller, M. (2013). Influence of feedstock on the release of potassium, sodium, chlorine, sulfur, and phosphorus species during gasification of wood and biomass shells. Energy & Fuels 27 (3), 1439–1445. doi:10.1021/ef302093r
Blomberg, T. (2011). A thermodynamic study of the gaseous potassium chemistry in the convection sections of biomass fired boilers. Mater. Corrosion-Werkstoffe Und Korrosion 62 (7), 635–641. doi:10.1002/maco.201005880
Bostrom, D., Skoglund, N., Grimm, A., Boman, C., Ohman, M., Brostrom, M., et al. (2012). Ash transformation chemistry during combustion of biomass. Energy & Fuels 26 (1), 85–93. doi:10.1021/ef201205b
Capablo, J., Jensen, P. A., Pedersen, K. H., Hjuler, K., Nikolaisen, L., Backman, R., et al. (2009). Ash properties of alternative biomass. Energy & Fuels 23 (3-4), 1965–1976. doi:10.1021/ef8008426
Carrillo, M. A., Staggenborg, S. A., and Pineda, J. A. (2014). Washing sorghum biomass with water to improve its quality for combustion. Fuel 116, 427–431. doi:10.1016/j.fuel.2013.08.028
Chen, X., Miao, Z., Chen, Y., Zhuang, J., Lv, J., Jiang, E., et al. (2024). Effect of alkali and alkaline earth metals on agglomeration in biomass chemical looping gasification. J. Energy Inst. 117, 101815. doi:10.1016/j.joei.2024.101815
Corona, B., Shen, Li, Sommersacher, P., and Junginger, M. (2020). Consequential Life Cycle Assessment of energy generation from waste wood and forest residues: the effect of resource-efficient additives. J. Clean. Prod. 259, 120948. doi:10.1016/j.jclepro.2020.120948
Dai, Y., Weng, W., Liu, S., He, Y., Wang, Z., and Li, Z. (2025). Research progress of laser photofragmentation-fragment detection techniques in combustion diagnostics. Appl. Spectrosc. Rev., 1–60. doi:10.1080/05704928.2025.2461317
Feng, S., Yuan, Z., Leitch, M., and Xu, C. C. (2014). Hydrothermal liquefaction of barks into bio-crude - effects of species and ash content/composition. Fuel 116, 214–220. doi:10.1016/j.fuel.2013.07.096
Gao, X., Zhou, Z., Coward, B., Wang, J. W., Tian, H., Yin, Y. S., et al. (2022). Improvement of wheat (T. aestivum) straw catalytic fast pyrolysis for valuable chemicals production by coupling pretreatment of acid washing and torrefaction. Industrial Crops Prod. 187, 115475. doi:10.1016/j.indcrop.2022.115475
Gudka, B., Jones, J. M., Lea-Langton, A. R., Williams, A., and Saddawi, A. (2016). A review of the mitigation of deposition and emission problems during biomass combustion through washing pre-treatment. J. Energy Inst. 89 (2), 159–171. doi:10.1016/j.joei.2015.02.007
Guo, J. H., Zhang, Y., Fang, J. J., Ma, Z. W., Li, C., Yan, M. Y., et al. (2024). Reduction and reuse of forestry and agricultural bio-waste through innovative green utilization approaches: a review. Forests 15 (8), 1372. doi:10.3390/f15081372
Guo, Q., Cheng, Z., Chen, G., Yan, B., Hou, L., and Ronsse, F. (2020). Optimal strategy for clean and efficient biomass combustion based on ash deposition tendency and kinetic analysis. J. Clean. Prod. 271, 122529. doi:10.1016/j.jclepro.2020.122529
Han, J., Yu, D., Wu, J., Yu, X., Liu, F., and Xu, M. (2023). Effects of torrefaction on ash-related issues during biomass combustion and co-combustion with coal. Part 3: ash slagging behavior. Fuel 339, 126925. doi:10.1016/j.fuel.2022.126925
Hess, D., Wendt, L. M., Wahlen, B. D., Aston, J. E., Hu, H., and Quinn, J. C. (2019). Techno-economic analysis of ash removal in biomass harvested from algal turf scrubbers. Biomass & Bioenergy 123, 149–158. doi:10.1016/j.biombioe.2019.02.010
Huang, H., Jin, Y., Sun, W., Gao, Y., Sun, P., and Ding, W. (2024). Biomass burning in northeast China over two decades: temporal trends and geographic patterns. Remote Sens. 16 (11), 1911. doi:10.3390/rs16111911
Ianez-Rodriguez, I., Martin-Lara, M. A., Perez, A., Gabriel, B., and Calero, M. (2020). Water washing for upgrading fuel properties of greenhouse crop residue from pepper. Renew. Energy 145, 2121–2129. doi:10.1016/j.renene.2019.07.143
Ilmiawati, A., Solikhin, A., Mangurai, S. U. N. M., Setiawan, Y., Istikorini, Y., Lowe, A. J., et al. (2025). Potential of carbon micro/nanofibers derived from lignocellulose biomass valorisation for CO2 adsorption: a review on decarbonization biotechnology for climate change solutions. Int. J. Biol. Macromol. 301, 140305. doi:10.1016/j.ijbiomac.2025.140305
Indrawan, N., Kumar, A., Moliere, M., Sallam, K. A., and Huhnke, R. L. (2020). Distributed power generation via gasification of biomass and municipal solid waste: a review. J. Energy Inst. 93 (6), 2293–2313. doi:10.1016/j.joei.2020.07.001
Jia, Y., and Lighty, J. A. S. (2012). Ash particulate formation from pulverized coal under oxy-fuel combustion conditions. Environ. Sci. & Technol. 46 (9), 5214–5221. doi:10.1021/es204196s
Johansen, J. M., Jakobsen, J. G., Frandsen, F. J., and Glarborg, P. (2011). Release of K, Cl, and S during pyrolysis and combustion of high-chlorine biomass. Energy & Fuels 25 (11), 4961–4971. doi:10.1021/ef201098n
Khalid, U., Khoja, A. H., Daood, S. S., Khan, W.Ul H., Din, I.Ud, Al-Anazi, A., et al. (2024). Experimental and numerical techniques to evaluate coal/biomass fly ash blend characteristics and potentials. Sci. Total Environ. 912, 169218. doi:10.1016/j.scitotenv.2023.169218
Kim, J.-H., Kim, M., Park, G., Kim, E., Song, H., Jung, S., et al. (2024). Chemicals and fuels from lipid-containing biomass: a comprehensive exploration. Biotechnol. Adv. 75, 108418. doi:10.1016/j.biotechadv.2024.108418
Li, J., Wen, Fu, Bai, X., Lin, X., Yang, H., Wang, M., et al. (2025). Oxidative pyrolysis characteristics and exothermic heat release effects of cellulose, hemicellulose, and lignin. Fuel 386, 134212. doi:10.1016/j.fuel.2024.134212
Li, L., Ren, Q., Li, S., and Lu, Q. (2013). Effect of phosphorus on the behavior of potassium during the Co-combustion of wheat straw with municipal sewage sludge. Energy & Fuels 27 (10), 5923–5930. doi:10.1021/ef401196y
Lindstrom, E., Sandstrom, M., Bostrom, D., and Marcus, O. (2007). Slagging characteristics during combustion of cereal grains rich in phosphorus. Energy & Fuels 21 (2), 710–717. doi:10.1021/ef060429x
Liu, H., Tan, H., Liu, Y., Liu, Z., Lin, Ma, Mohamed, P., et al. (2011). Study of the layered structure of deposit in a biomass-fired boiler (case study). Energy & Fuels 25 (6), 2593–2600. doi:10.1021/ef2003365
Ma, C., Tian, H., Ma, Y., Du, B., Zhang, Y., Lyu, J., et al. (2025). Experimental investigation on the effect of iron-rich coal ash on biomass-volatile combustion characteristics in the fluidized bed. Energy 321, 135391. doi:10.1016/j.energy.2025.135391
Matus, M., Krizan, P., Soos, L., and Beniak, J. (2018). The effect of papermaking sludge as an additive to biomass pellets on the final quality of the fuel. Fuel 219, 196–204. doi:10.1016/j.fuel.2018.01.089
Miccio, F., Natali Murri, A., Medri, V., and Landie, E. (2019). Utilization of fireclay for preventing fluidized-bed agglomeration during biomass thermochemical processing. Industrial & Eng. Chem. Res. 58 (51), 23498–23507. doi:10.1021/acs.iecr.9b06253
Miguez, L., Behrendt, F., Blanco, D., Patino, D., and Dieguez-Alonso, A. (2021). Review of the use of additives to mitigate operational problems associated with the combustion of biomass with high content in ash-forming species. Renew. & Sustain. Energy Rev. 141, 110502. doi:10.1016/j.rser.2020.110502
Mlonka-Medrala, A., Magdziarz, A., Gajek, M., Nowinska, K., and Nowak, W. (2020). Alkali metals association in biomass and their impact on ash melting behaviour. Fuel 261, 116421. doi:10.1016/j.fuel.2019.116421
Mu, L., Tong, Li, Zuo, S., Yin, H., and Dong, M. (2022). Effect of leaching pretreatment on the inhibition of slagging/sintering of aquatic biomass: ash transformation behavior based on experimental and equilibrium evaluation. Fuel 323, 124391. doi:10.1016/j.fuel.2022.124391
Ni, Z., Bi, H., Jiang, C., Sun, H., Zhou, W., Tian, J., et al. (2022). Investigation of co-combustion of sewage sludge and coffee industry residue by TG-FTIR and machine learning methods. Fuel 309, 122082. doi:10.1016/j.fuel.2021.122082
Niu, Y., Du, W., Tan, H., Xu, W., Liu, Y., Xiong, Y., et al. (2013). Further study on biomass ash characteristics at elevated ashing temperatures: the evolution of K, Cl, S and the ash fusion characteristics. Bioresour. Technol. 129, 642–645. doi:10.1016/j.biortech.2012.12.065
Niu, Y., and Tan, H.Shi'en Hui (2016). Ash-related issues during biomass combustion: alkali-induced slagging, silicate melt-induced slagging (ash fusion), agglomeration, corrosion, ash utilization, and related countermeasures. Prog. Energy Combust. Sci. 52, 1–61. doi:10.1016/j.pecs.2015.09.003
Niu, Y. Q., Zhu, Y. M., Tan, H. Z., Hui, S., Jing, Z., and Xu, W. G. (2014). Investigations on biomass slagging in utility boiler: criterion numbers and slagging growth mechanisms. Fuel Process. Technol. 128, 499–508. doi:10.1016/j.fuproc.2014.07.038
Nordgren, D., Henry, H., Padban, N., Bostrom, D., and Marcus, O. (2013). Ash transformations in pulverised fuel co-combustion of straw and woody biomass. Fuel Process. Technol. 105, 52–58. doi:10.1016/j.fuproc.2011.05.027
Novendianto, I. B., Tony Suryo Utomo, M. S. K., Muchammad, M., Milkiy Kuswa, F., Ghazidin, H., Karuana, F., et al. (2024). Investigation of the slagging and fouling aspects of co-firing coal and organic refuse-derived fuel. Therm. Sci. Eng. Prog. 49, 102447. doi:10.1016/j.tsep.2024.102447
Priyanto, D. E., Ueno, S., Sato, N., Kasai, H., Tanoue, T., and Fukushima, H. (2016). Ash transformation by co-firing of coal with high ratios of woody biomass and effect on slagging propensity. Fuel 174, 172–179. doi:10.1016/j.fuel.2016.01.072
Rong, H., Wang, T., Zhou, M., Wang, H., Hou, H., and Xue, Y. (2017). Combustion characteristics and slagging during Co-combustion of rice husk and sewage sludge blends. Energies 10 (4), 438. doi:10.3390/en10040438
Shao, Y., Wang, J., Preto, F., Zhu, J., and Xu, C. (2012). Ash deposition in biomass combustion or Co-firing for power/heat generation. Energies 5 (12), 5171–5189. doi:10.3390/en5125171
Shen, Y., Zhou, T., Luo, S., Ma, P., and Sun, S. (2025). Study on the characteristics of sludge and biomass co-combustion and heavy metal migration and transformation. Energy 316, 134632. doi:10.1016/j.energy.2025.134632
Singhal, A., Goel, A., Bhatnagar, A., Roslander, C., Wallberg, O., Konttinen, J., et al. (2023). Improving inorganic composition and ash fusion behavior of spruce bark by leaching with water, acetic acid, and steam pre-treatment condensate. Chem. Eng. J. 452, 139351. doi:10.1016/j.cej.2022.139351
Singhal, A., Konttinen, J., and Joronen, T. (2021). Effect of different washing parameters on the fuel properties and elemental composition of wheat straw in water-washing pre-treatment. Part 1: effect of washing duration and biomass size. Fuel 292, 120206. doi:10.1016/j.fuel.2021.120206
Su, X., Chen, X., Fang, Q., Ma, L., Tan, P., Zhang, C., et al. (2024). An integrated model for flexible simulation of biomass combustion in a travelling grate-fired boiler. Energy 307, 132605. doi:10.1016/j.energy.2024.132605
Sukatis, F. F., Wee, S. Y., and Ahmad, Z. A. (2022). Potential of biocompatible calcium-based metal-organic frameworks for the removal of endocrine-disrupting compounds in aqueous environments. Water Res. 218, 118406. doi:10.1016/j.watres.2022.118406
Suyatno, S., Ghazidin, H., Prismantoko, A., Karuana, F., Kuswa, F. M., Dwiratna, B., et al. (2025). Evaluation of combustion characteristics and ash-related issues during co-firing of acacia and mahogany wood biomass fuels with coal. Biomass & Bioenergy 196, 107763. doi:10.1016/j.biombioe.2025.107763
Thy, P., Jenkins, B. M., Grundvig, S., Shiraki, R., and Lesher, C. E. (2006). High temperature elemental losses and mineralogical changes in common biomass ashes. Fuel 85 (5-6), 783–795. doi:10.1016/j.fuel.2005.08.020
Tiainen, M., Daavitsainen, J., and Laitinen, R. S. (2002). The role of amorphous material in ash on the agglomeration problems in FB boilers. A powder XRD and SEM-EDS study. Energy & Fuels 16 (4), 871–877. doi:10.1021/ef010269j
Tonn, B., Ulrich, T., Lewandowski, I., and Claupein, W. (2012). Leaching of biomass from semi-natural grasslands - effects on chemical composition and ash high-temperature behaviour. Biomass & Bioenergy 36, 390–403. doi:10.1016/j.biombioe.2011.11.014
Wang, C., Wang, X., Jiang, X., Li, F., Lei, Y., and Lin, Q. (2019). The thermal behavior and kinetics of co-combustion between sewage sludge and wheat straw. Fuel Process. Technol. 189, 1–14. doi:10.1016/j.fuproc.2019.02.024
Wang, G., Poulsen, J. N. F., Poulsen, S. N. F., Jensen, P. A., and Frandsen, F. J. (2022). Influence of kaolin and coal fly ash addition on biomass ash deposition in an entrained flow reactor. Fuel 313, 123041. doi:10.1016/j.fuel.2021.123041
Wang, L., Becidan, M., and Skreiberg, O. (2012a). Sintering behavior of agricultural residues ashes and effects of additives. Energy & Fuels 26 (9), 5917–5929. doi:10.1021/ef3004366
Wang, S., Jiang, X. M., Han, X. X., and Wang, H. (2008). Fusion characteristic study on seaweed biomass ash. Energy & Fuels 22 (4), 2229–2235. doi:10.1021/ef800128k
Wang, X., Liu, Y., Tan, H., Lin, Ma, and Xu, T. (2012b). Mechanism research on the development of ash deposits on the heating surface of biomass furnaces. Industrial & Eng. Chem. Res. 51 (39), 12984–12992. doi:10.1021/ie302009m
Waqas, S., Harun, N. Y., Sambudi, N. S., Abioye, K. J., Zeeshan, M. H., Ali, A., et al. (2023). Effect of operating parameters on the performance of integrated fixed-film activated sludge for wastewater treatment. Membranes 13 (8), 704. doi:10.3390/membranes13080704
Wei, X. L., Schnell, U., and Hein, K. R. G. (2005). Behaviour of gaseous chlorine and alkali metals during biomass thermal utilisation. Fuel 84 (7-8), 841–848. doi:10.1016/j.fuel.2004.11.022
Wei, Yi, Tang, J., Xie, J., and Shen, C. (2019). Molten alkali carbonates pyrolysis of digestate for phenolic productions. J. Clean. Prod. 225, 143–151. doi:10.1016/j.jclepro.2019.03.234
Werkelin, J., Skrifvars, B.-J., Zevenhoven, M., Holmbom, B., and Hupa, M. (2010). Chemical forms of ash-forming elements in woody biomass fuels. Fuel 89 (2), 481–493. doi:10.1016/j.fuel.2009.09.005
Yao, X., Zhao, Z., Li, J., Zhang, B., Zhou, H., and Xu, K. (2020). Experimental investigation of physicochemical and slagging characteristics of inorganic constituents in ash residues from gasification of different herbaceous biomass. Energy 198, 117367. doi:10.1016/j.energy.2020.117367
Yu, J., Guo, Q., Gong, Y., Ding, Lu, Wang, J., and Yu, G. (2021). A review of the effects of alkali and alkaline earth metal species on biomass gasification. Fuel Process. Technol. 214, 106723. doi:10.1016/j.fuproc.2021.106723
Keywords: biomass combustion, biomass ash, slagging, alkali metals, ash behavior control
Citation: Luan J, Wang Q, Shao D, Cui B, Han P and He Q (2025) Research progress on influencing factors and control methods of slagging in biomass combustion. Front. Energy Res. 13:1634354. doi: 10.3389/fenrg.2025.1634354
Received: 24 May 2025; Accepted: 24 June 2025;
Published: 03 July 2025.
Edited by:
Zhi Wang, Tianjin University, ChinaCopyright © 2025 Luan, Wang, Shao, Cui, Han and He. This is an open-access article distributed under the terms of the Creative Commons Attribution License (CC BY). The use, distribution or reproduction in other forums is permitted, provided the original author(s) and the copyright owner(s) are credited and that the original publication in this journal is cited, in accordance with accepted academic practice. No use, distribution or reproduction is permitted which does not comply with these terms.
*Correspondence: Qiang He, aGVxaWFuZzQ1MzJAMTYzLmNvbQ==; Ping Han, aGFucGluZ19qdHlzQDE2My5jb20=