- VTT Technical Research Centre of Finland, Helsinki, Finland
Cellular agriculture can help to meet the growing global demand for proteins and other food products by producing, e.g., single-cell protein (SCP) through fermentation, simultaneously enhancing sustainability and resource efficiency. However, our path toward 2040 may involve crises related to energy, water and raw material availability, contaminated production processes, logistics or increased costs. In this study, we assessed the risks of a cell factory operating in 2040, which could face challenges such as freshwater shortages, power outages, and scarcity of chemicals and other materials. The envisioned cell factory utilises various side streams as raw materials and operates in an urban area. We employed the qualitative HAZSCAN (Hazardous Scenario Analysis) method to assess the occupational, product, and environmental safety of a fully operational hypothetical business to business (B2B) cell factory producing cellular agriculture ingredients. The analysis was conducted by a working group, including experts from VTT and industrial representatives, through five focused meetings to prepare activity and process model, systematically identify hazards, and estimate their severity and probability. Risk was then classified using a tailored risk matrix. Hazards causing production interruptions, impairment to occupational health and product safety, as well as environmental safety, were identified and their risks were assessed. Future risks may arise from resource scarcity, the quality of raw materials or logistical issues related to raw materials. Risks related to utilities stem from the availability of electricity, steam, or water. Operational risks can originate from maintenance challenges, process quality control, storage and handling of materials, insufficient instructions for operators, and potential leaks into the environment. Additionally, risks may be caused by disruptions in information transfer or vandalism. The analysis emphasised the need for comprehensive safety and risk management methods that consider both process safety and environmental impacts.
Introduction
Cellular agriculture is becoming a viable option to complement the increasing worldwide need for proteins, lipids, and other food and feed commodities. This innovative approach can, for example, produce single-cell protein (SCP) through fermentation, utilising various microorganisms such as algae, yeast, fungi, and bacteria in fermenters within a contained cell factory environment (Ritala et al., 2017; Nyyssölä et al., 2022; Li et al., 2024). One notable application is using grass silage as a feedstock, which is an effective way to produce SCP with high protein content (Pihlajaniemi et al., 2020; Rinne, 2024). Additionally, cellular agriculture can leverage other side streams and by-products from the agri-food sector, even single-carbon compounds like CO2 or methane as feedstock, enhancing sustainability and resource efficiency, thus advancing circular food systems as a whole (Fytsilis et al., 2024).
While cellular agriculture promises numerous benefits, it might pose potential risks related to, e.g., health, thus further studies are required (Hadi and Brightwell, 2021). Much attention has been paid to food security and the environmental and societal impacts of the current food system. It has been pointed out that challenges in toxicological risk assessment associated with cellular agricultural products and possible food security risks could necessitate new safety assessment methodologies (Fytsilis et al., 2024). Risks can result from, e.g., chemical or microbiological contamination, mycotoxin or unexpected toxic secondary metabolites production, mycoprotein allergens and high nucleic acid content (Jacobson and DePorter, 2018; Whittaker et al., 2020; Hadi and Brightwell, 2021; Nyyssölä et al., 2022; Fytsilis et al., 2024).
It is also possible to employ genetically engineered organisms in cellular agriculture, e.g., in precision fermentation microbial host can be altered to produce targeted proteins or lipids. The manufacturing of these GMOs is classified as contained use in Europe. This classification refers to the use of genetically modified micro-organisms under containment to prevent their contact with the environment. Such activities must be reported to the competent authorities. If the activity poses a moderate or high risk (i.e., Class 3 or 4), written consent from the authorities is required before commencing the contained use activity. The authorities ensure that the manufacturing processes are appropriate and do not pose a threat to human health or the environment. Then additionally, when the aim is to use GMOs for food and feed purposes, GMO authorisation must be performed in Europe by submitting a dossier with experimental data and a risk assessment. In their review focusing on New Genomic Techniques (NGT) applied to microorganisms, EFSA GMO Panel did not recognise any novel potential hazards to humans compared to established genomic techniques or conventional mutagenesis (Panel on Genetically Modified Organisms EFSA et al., 2024). Nevertheless, they also recommended updating the guidance on risk assessment of genetically modified microorganisms and their products (Panel on Genetically Modified Organisms EFSA et al., 2024).
Harnessing cellular agriculture could help decrease the amount of land needed for food production and lower greenhouse gas emissions when compared to conventional agriculture-based food production (El Wali et al., 2024). However, this new protein and other food commodities production method requires critical minerals and more energy when compared to conventional agriculture (Tuomisto, 2022; El Wali et al., 2024). The propagation of food and feed ingredients with large-scale industrial bioreactors requires the use of electricity, energy and chemicals. Therefore, the means to produce the energy for cellular agriculture are of critical importance, and it has already been emphasised that green energy demand is high for these new emerging food ingredient production technologies (Kobayashi et al., 2022; El Wali et al., 2024).
Currently, scaling up cellular agriculture technologies faces significant technical and financial hurdles (Ye et al., 2024). However, these barriers can likely be overcome with ongoing research efforts (Ye et al., 2024). One aspect of the future development of cellular agriculture is to increase the resilience of the production, for example, SCP production can be essential, particularly in sudden disruptions like pandemics, wars, droughts, floods and other disasters affecting traditional food supply chains (García Martínez et al., 2022). At the same time, the centralised production model in factories is vulnerable to disruptions and closures (Soice and Johnston, 2021). Despite the potential benefits, there is a notable gap in the literature regarding the risk analysis of a cell factory producing, e.g., SCP or operating in the field of precision fermentation of targeted food ingredients like milk proteins or lipids to replace animal-derived counterparts at least partially. While several risk assessment studies exist, a comprehensive conceptual-level risk analysis is crucial, especially to anticipate and mitigate the impacts of sudden incidents. This underscores the need for further research to ensure the safety and resilience of cellular agriculture systems.
In this study, we performed a risk assessment for a future cell factory in 2040 operating in a world where several crises might complicate the factory operations, such as fresh water shortages, uncertainty in electricity and shortages of chemicals and other materials. We envisioned that the factory would valorise various side streams as feedstock and operate in urban settings. Our focus within cellular agriculture technologies was exclusively on microbial single-cell protein manufacturing and precision fermentation.
Materials and methods
The commonalities and development issues of foresight, Technology Analysis (TA), and risk assessment methodologies give us a multi-dimensional and interdisciplinary assessment framework (Koivisto et al., 2009). Within this framework, we selected the risk assessment methodology, which considers occupational, product and environmental safety, namely a Hazardous Scenario Analysis (HAZSCAN) method. While cellular agriculture processes resemble other process industries, the HAZSCAN method was suitable for analysing process risks (Malmén et al., 1999). HAZSCAN is designed to identify hazards in the production plant arising from equipment, human factors, and organisational issues. The HAZSCAN method was selected because it is applicable even in the very early stages of the production process development, as specific process details are not required. This methodology is described in more detail in the following.
Hazardous scenario analysis (HAZSCAN) method
The HAZSCAN method was applied to identify and evaluate risks related to a cell factory in a general level, without focusing on any specific factory. An illustration of the HAZSCAN analysis process used in this study is presented in Figure 1.
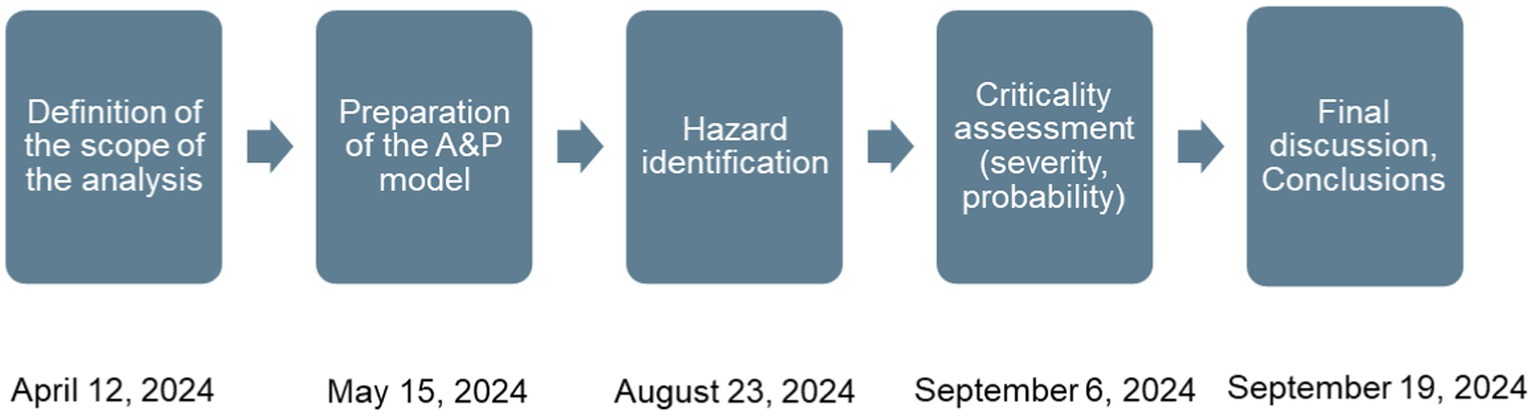
Figure 1. HAZSCAN analysis process and work group meeting dates. A&P refers to the activity and process model.
The HAZSCAN analysis is typically conducted by a working group, usually consisting of 3 to 6 members in addition to the analysis leader(s). In this study, the group included researchers from VTT with expertise in microbiology, fermentation, downstream processing, foresight, and risk analysis, as well as industrial representatives from two different cell factories. The analysis was conducted through five 2–3 h working group meetings, each with a specific focus (Figure 1).
In the first meeting, the scope of the risk analysis was defined. The risk assessment process generally requires a description of the system being evaluated. In this case, the system is a fictional B2B cell factory, which is detailed in the following sections. The second meeting focused on preparing the HAZSCAN activity and process model (A&P model), which was subsequently used in the later phases to systematically identify hazards. This was accomplished in the third meeting. During the fourth meeting, the severity and probability of the identified hazards were assessed, and each event was categorised in the criticality matrix. Finally, the conclusions of the risk analysis were formulated in the fifth and final meeting. Additionally, the authors worked with the materials between and after the sessions.
Description of a B2B cell factory producing cellular agriculture ingredients
The scope was defined to identify and evaluate the risks associated with a general cell factory that produces ingredients for industrial customers. To achieve this, a group of experts in the field described a fictional future B2B Cell Factory. This factory is designed to convert agri-food side streams into culture medium components, starting with microbe strains and culture medium preparation.
The factory was envisioned to be located in Europe, ensuring compliance with EU regulations. In this study, we assumed that the factory was fully operational, with all necessary authorisations (e.g., operations involving possible GMOs, environmental permits, food safety, and occupational safety) being valid and adhering to Good Manufacturing Practices (GMP).
The basic process flow of this imaginary factory is shown in Figure 2. A more detailed picture of the process is presented in Figure 3. It included the most common process steps. For risk analysis, the factory was divided into two parts. The first part was the side stream valorisation process, taking liquid or solid feedstock and processing those into culture medium components for the second part. The second part was the production process, starting from microbe strains and medium and ending with packed ingredients.

Figure 2. The basic process flow of an imaginary B2B cell factory producing cellular agriculture ingredients. A more detailed picture of the process is presented in Figure 3.
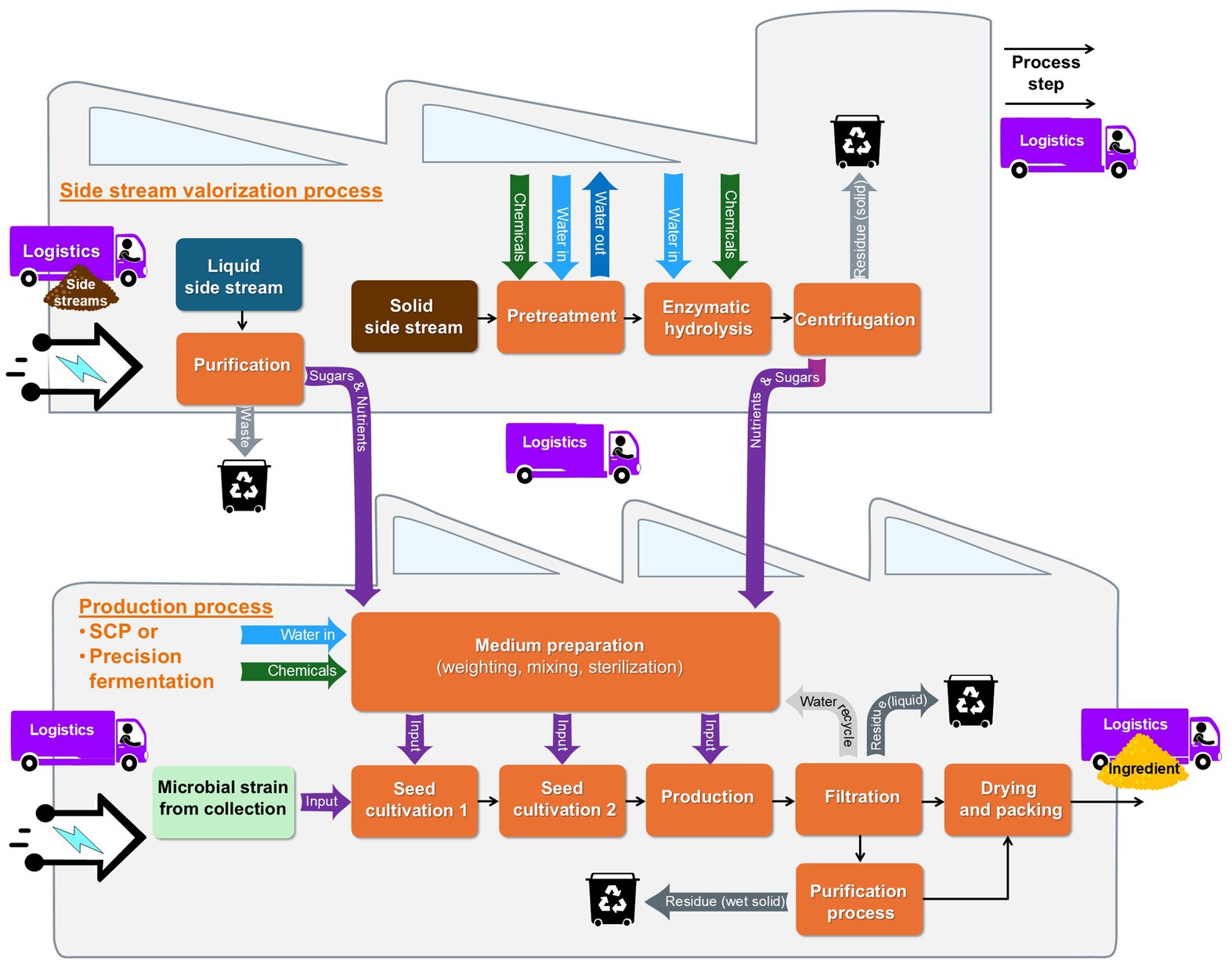
Figure 3. A process flow of a imaginary B2B cell factory producing cellular agriculture ingredients. The upper part illustrates how liquid and solid side streams are processed to provide sugars and nutrients for the actual cellular agriculture production process happening in the below parts of the figure. All process steps are marked with orange boxes and black arrows. Input and logistics are marked with violet arrows and trucks. Residual and waste streams including recyclable water streams are marked with grey arrows.
Preparation of the activity and process model
The HAZSCAN analysis employs an activity and process model (A&P model) to describe the system under study. This model includes details on equipment, functions and other phenomena, chemicals, substances and commodities, safety measures, product and waste streams, operational and maintenance issues, and process control aspects. A template for A&P model is presented in Figure 4.
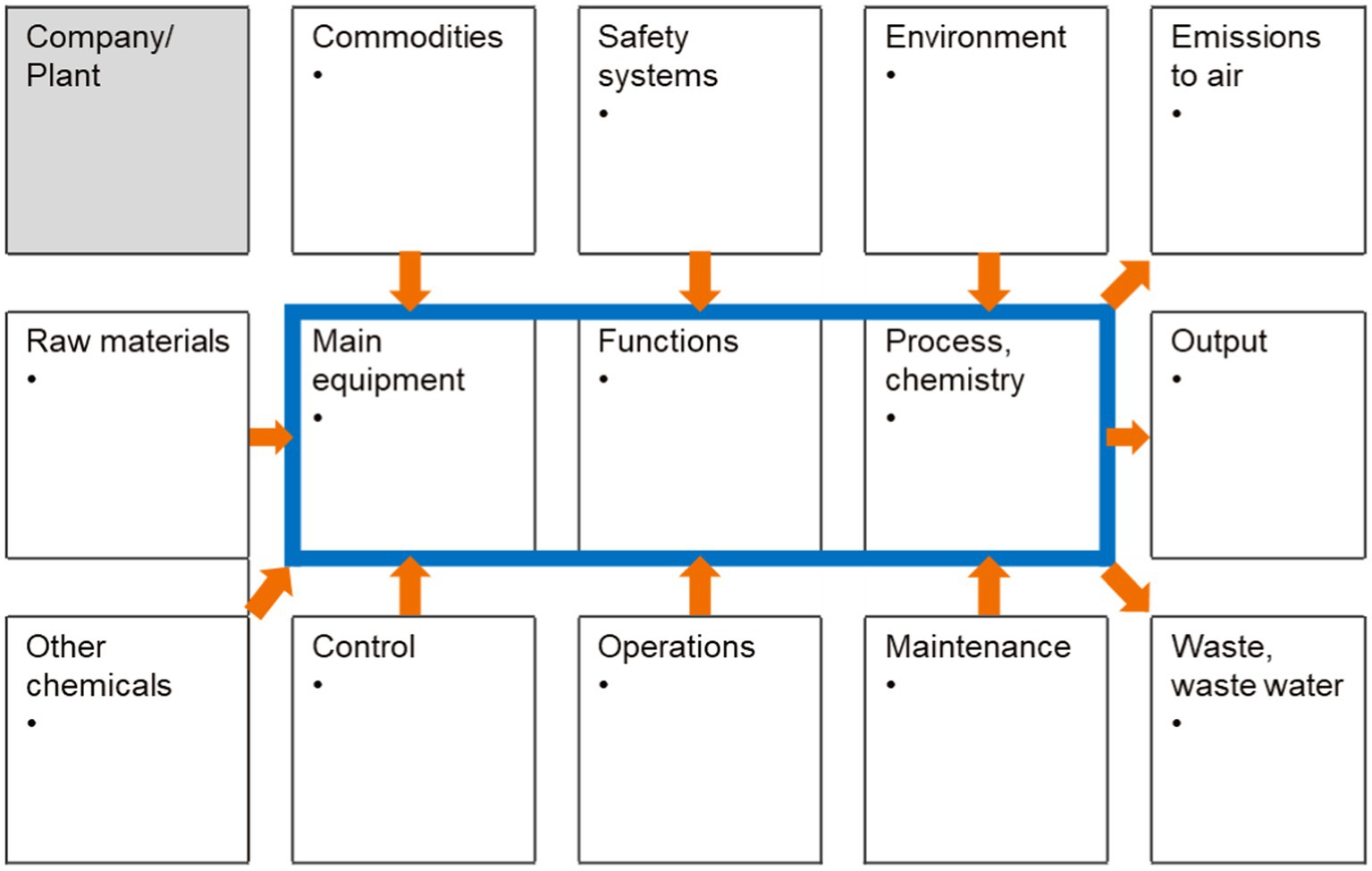
Figure 4. A blank template for the activity and process model. Blue box in the middle highlights the main process. The boxes around the main process illustrate inputs, corresponding factors and functions and outputs of the main process. Arrows depicture the main direction of material, information, actions etc. Grey box is for the identification information of the studied factory.
Typical commodities in the cell factory processes include tap water, cooling water, nitrogen, compressed air, and electricity. Maintenance lists should cover planned maintenance, unplanned repairs, and subcontractor use, reflecting factory-specific factors that have caused accidents or near misses. The control section lists systems used in the process control, with emphasis on operations if the facility is partly manually controlled.
Hazard identification
Based on the process and function description, guided by the experienced leader of the analysis, the identification and ideation of potential hazards were started systematically, point by point, proceeding from the A&P model. The focus was on identifying undesired events such as hazardous situations, accidents, and production interruptions. The analysis began with raw materials, proceeded through the main production process, and concluded with the output part of the A&P model. The main process was complemented by reviewing all other functions and operations mentioned in the A&P model (Figure 4). The actual list of keywords was not used in the analysis, but the leader chose the guiding questions according to the device or function to be investigated. Identified situations were recorded on analysis sheets (Figure 5), detailing the hazardous situation, its cause, possible consequences, and precautions (e.g., containment basins, training, protective equipment, backup systems).
Throughout the HAZSCAN analysis, improvement proposals were recorded to eliminate potential hazards or reduce their consequences. The main idea is that the A&P model describes what has been discussed in the analysis, and the hazardous situations and other results that are central to the analysis are recorded on the analysis sheet.
Criticality assessment
For the criticality assessment, a conventional criticality matrix approach with consequence and likelihood dimensions was applied (IEC, 2019). The likelihood, i.e., probability of occurrence was estimated on one scale (from A to D), but the severity of consequences was assessed from three different viewpoints for each identified case:
• Effect on production (P); how the identified problem affects the continuation of production of the cell factory.
• Occupational safety and health & product safety (S): how the identified problem directly affects personnel safety or indirectly affects the safety of people through product quality issues.
• Environmental safety (E): How seriously and widely the identified problem affects the environment around the factory.
The scales were tailored for this specific analysis and agreed upon within the expert group that conducted the analysis. The criticality matrix and the scales are presented in Figure 6.
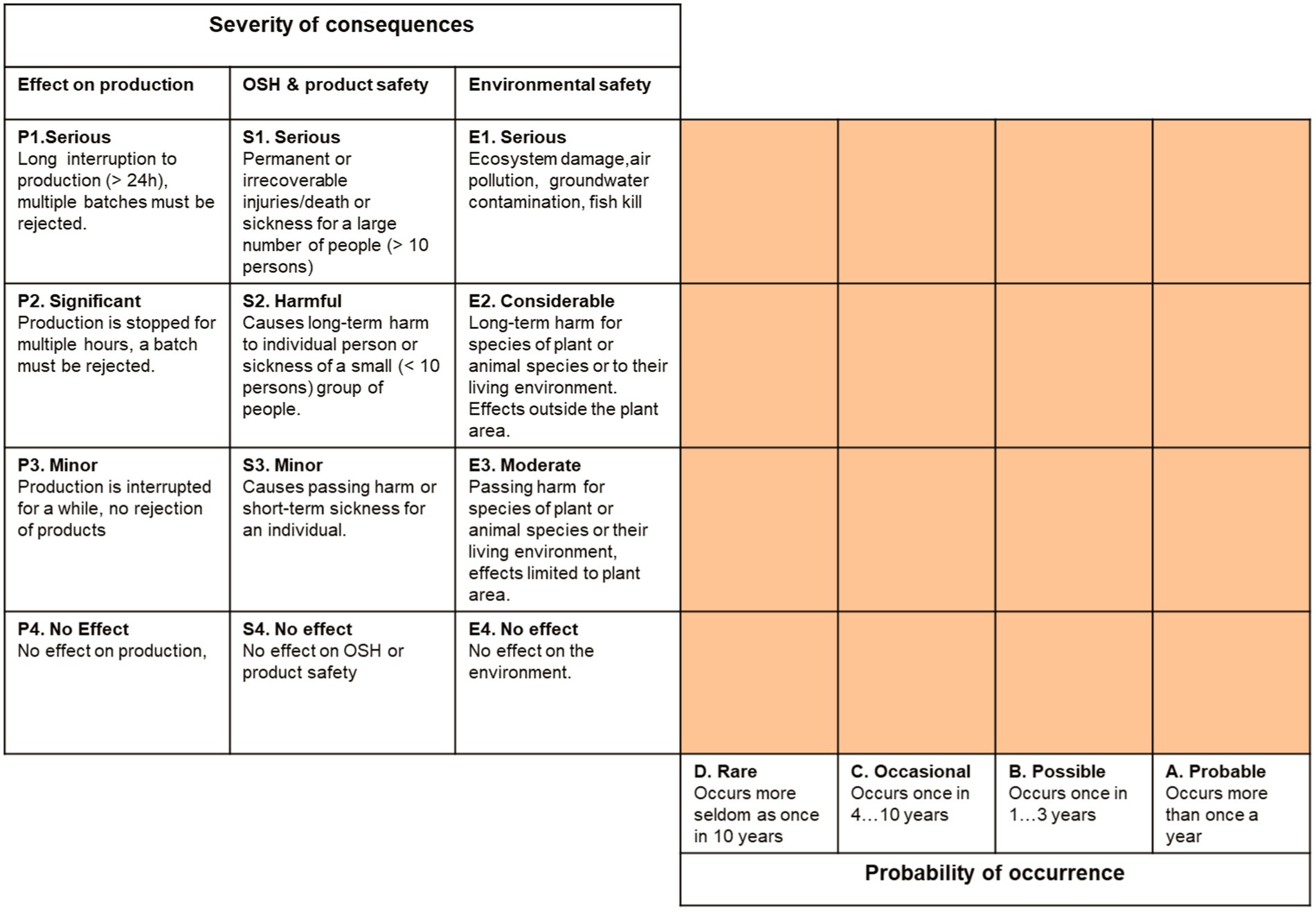
Figure 6. Criticality matrix: Single scale for probability of occurrence and three separate scales for severity. Probability categories are marked from A (Probable) to D (Rare). The severity of the consequences are classified as 1 (Serious) to 4 (No Effect). Consequences are assessed individually for production (P), Occupational Safety and Health (OSH) & product safety (S) and environmental safety (E).
The severity of different consequence viewpoints (production, OSH & product safety, environmental safety) was evaluated individually. We did not use, e.g., risk indexing for combining different types of risks. The following chapter presents the results separately for each consequence point of view.
Results
A&P models
Two A&P models were developed: one for the side stream valorisation process, and another for the actual production process (e.g., SCP, precision fermentation of proteins). The A&P model for the side stream valorisation process is presented in Figure 7 and for the production process in Figure 8.
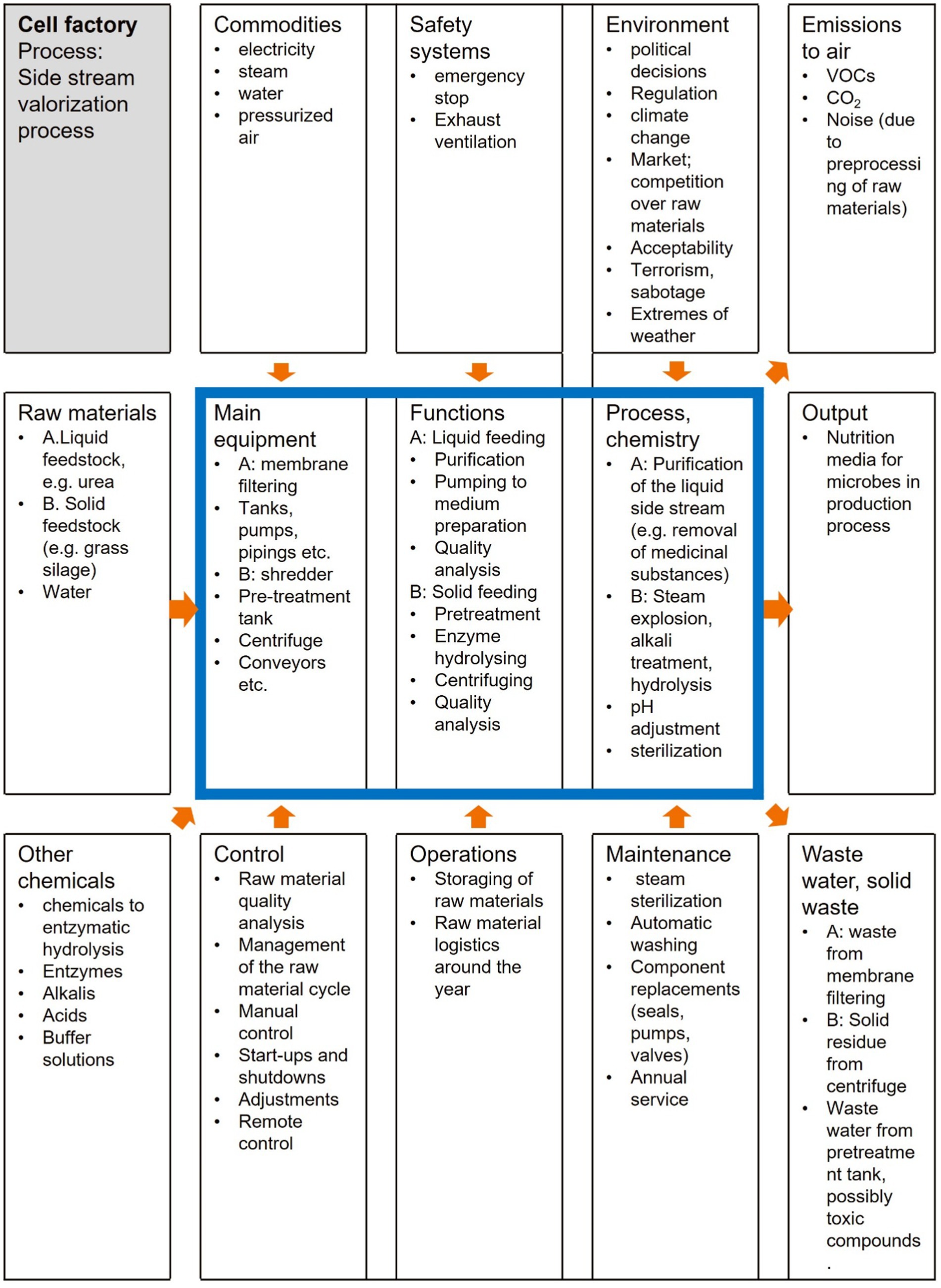
Figure 7. HAZSCAN activity and process (A&P) model for the side stream valorization process. The main valorization process is in the middle, highlighted with a blue line. The main process is complemented by surrounding functions and operations essential to the valorization process. In the main process letter A refers to liquid feedstock and B to solid feedstock. VOCs = volatile organic compounds.
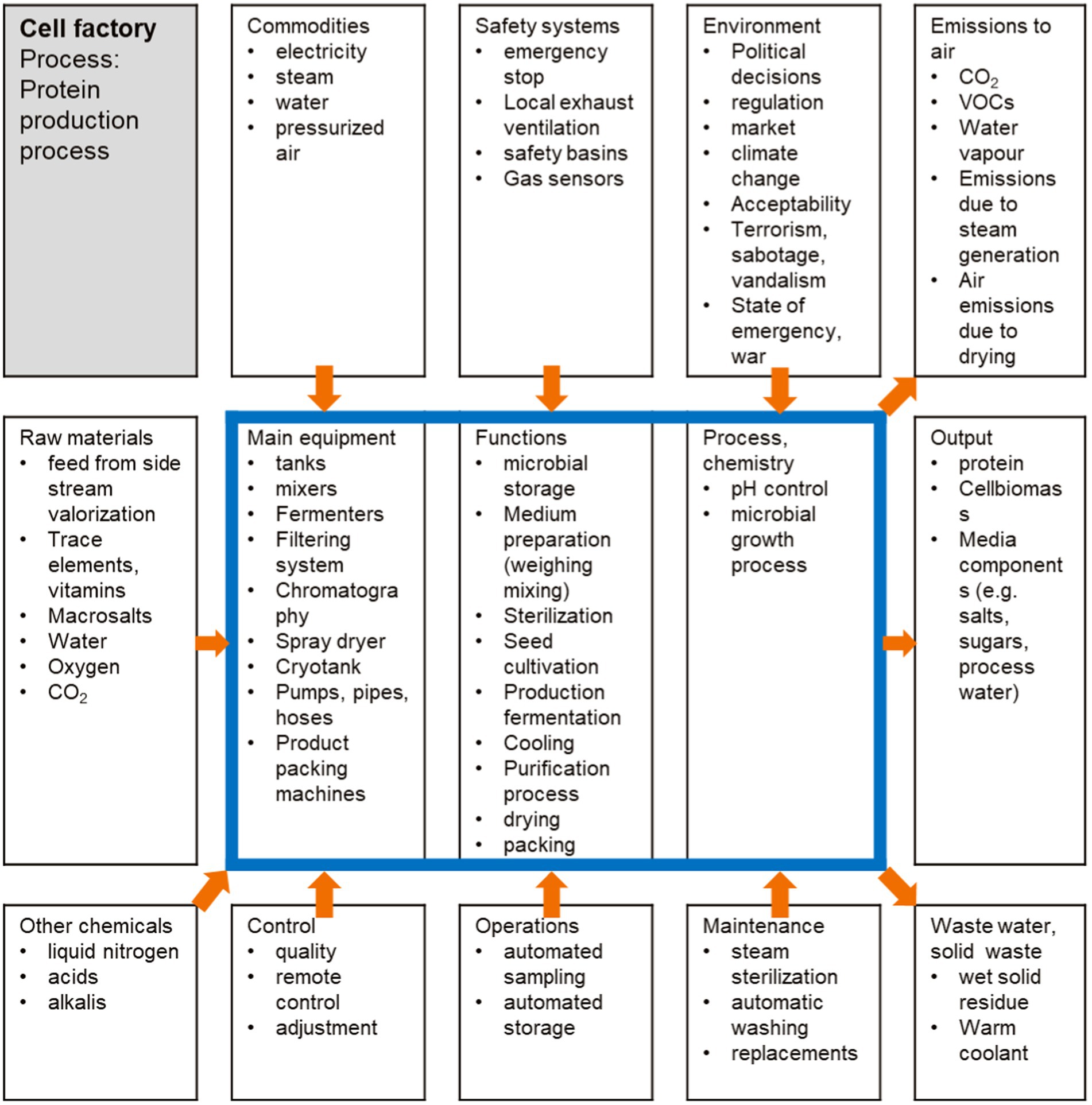
Figure 8. HAZSCAN activity and process (A&P) model for the actual production process (e.g., SCP production, precision fermentation of proteins). The main production process of the cell factory is in the middle, highlighted with a blue line. The main process is complemented by surrounding functions and operations essential to the production process.
Risks causing interruptions of the production process
The operation of the cell factory requires an uninterrupted supply of commodities and consistent quality of raw materials. The distribution of identified scenarios on the production-related criticality matrix is shown in Figure 9. The most critical scenarios, assessed in the red area of the criticality matrix, related to production interruption risks are associated with commodities, especially the availability of electricity. The number of these critical (intolerable) scenarios was 25 out of 110.
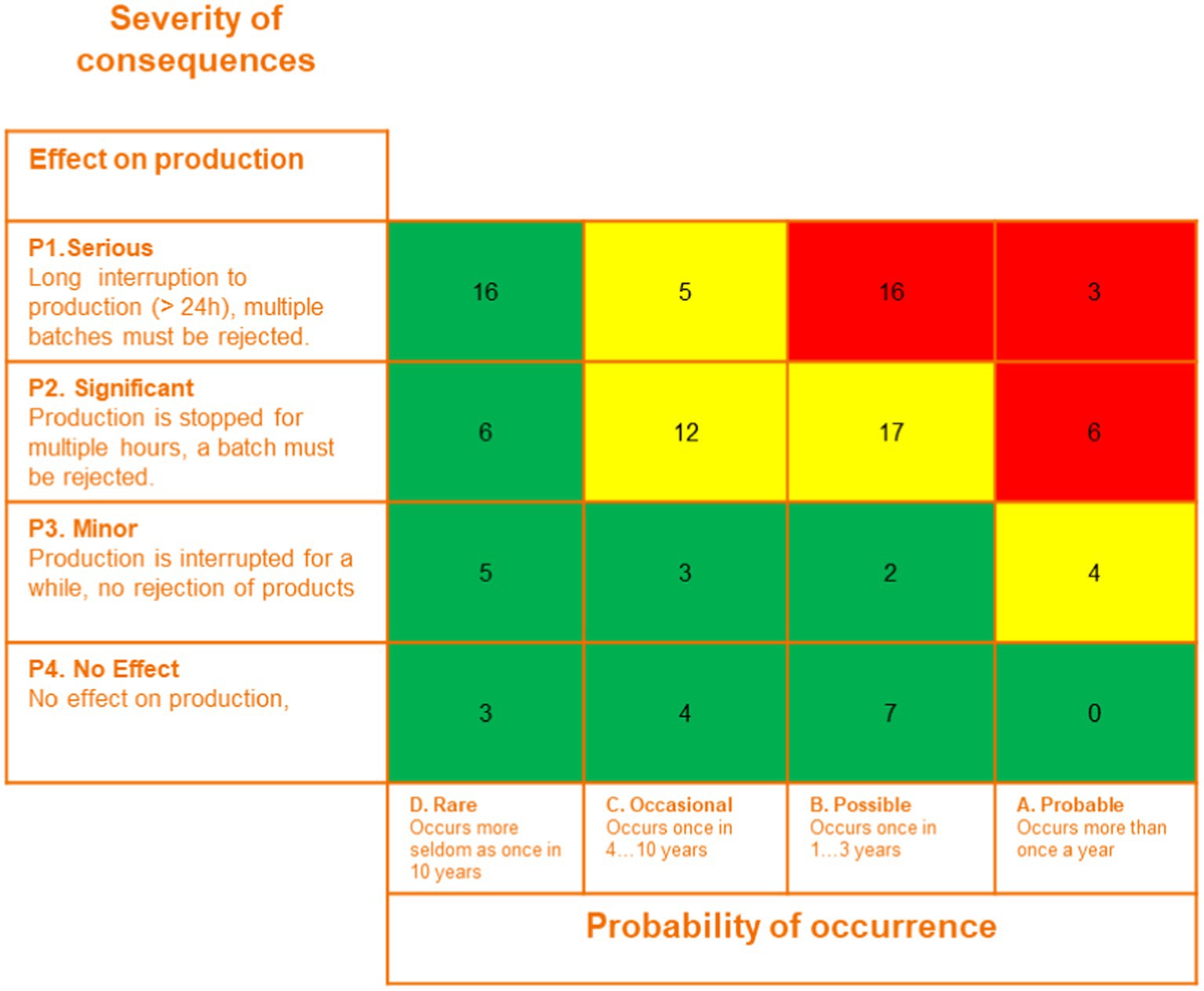
Figure 9. The distribution of identified scenarios on production-related criticality matrix of a cell factory. The number in each criticality matrix cell expresses the number of scenarios assessed to that risk category. The most critical categories are marked with red colour (intolerable risks), moderate categories with yellow colour and insignificant risks with green colour indicating the severity of consequences if the scenario in question would realise.
Interruptions in the supply of electricity cause problems in cooling, heating, and the availability of compressed air in the cell factory environment. Situations that were assessed as interrupting the production process include short power cuts and high energy prices. These can lead to product quality issues and production interruptions. The energy supply should be secured either with a sufficiently large backup power capacity or with an in-house power plant that produces both the necessary electricity and thermal energy for the plant.
Problems in raw material logistics, steam availability, and water quantity or quality issues can also lead to long production interruptions. In addition, problems with the availability and quality variations of raw materials can threaten the continuity of the process. To ensure the consistency of raw materials, the cell factory should have a sufficiently large storage capacity to prevent small disruptions in raw material logistics from causing problems in the process and to smooth out possible variations in raw material quality, e.g., by mixing different batches of raw materials before feeding them into the process.
Among the operational environment issues, disruptions in information and communication systems were considered problematic. Disruptions in information systems can be caused by either internal system-related problems or external cyber threats. The connection of control systems directly related to production to external networks should be avoided, and external control commands should be limited to only those absolutely necessary for the operation of the production system.
Unforeseen changes in the operating environment can affect production. One significant factor identified was consumer acceptance of cell factory ingredients, which is influenced by various aspects such as price, taste, texture, and the origin of raw materials. Normally, consumer acceptance is assessed before these ingredients are introduced to the market. However, acceptance issues can still arise after production has begun, particularly if there are changes in the raw materials used, such as those sourced from waste. Quality variations are typically monitored by testing samples taken during the production process to identify any foreign objects or quality issues in the raw materials.
Maintenance challenges were also considered critical, for example, unavailability of consumables or other spare parts can lead to long interruptions of production. Critical spare parts for maintenance should be identified and procured in sufficient, but not excessively large quantities, for local storage.
Occupational safety and health (OSH) and product safety
Many risks related to occupational safety were identified to be connected to production facilities and machinery, e.g., mechanical hazards of production equipment. The distribution of identified scenarios on OSH & product safety criticality matrix is shown in Figure 10. The number of the most critical scenarios, i.e., scenarios assessed to the red area of the matrix, was 19 out of 110.
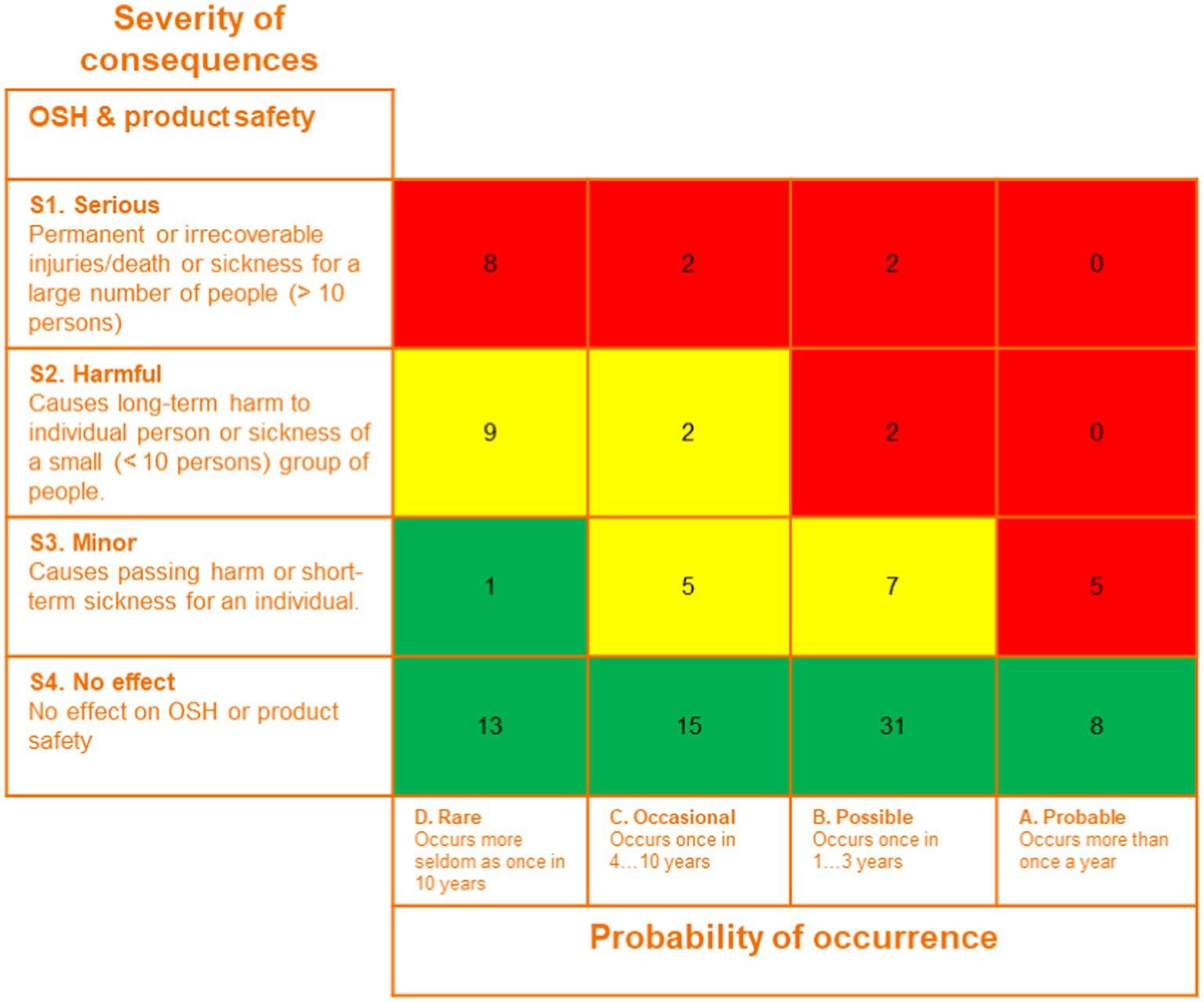
Figure 10. The distribution of identified scenarios on the OSH and product safety criticality matrix of a cell factory. The number in each criticality matrix cell expresses the number of scenarios assessed to that risk category. The most critical categories are marked with red colour (intolerable risks), moderate categories with yellow colour and insignificant risks with green colour indicating the severity of consequences if the scenario in question would realise.
The most critical scenarios were assessed to be hazards threatening occupational safety related to main equipment, especially packaging machines, and maintenance-related risks due to, for example, inadequate instructions. The packaging phase is also critical for product safety, as errors in packaging can compromise the product’s shelf life, potentially posing a risk to a large number of people.
The next most critical categories were assessed to be occupational safety risks related to shredders used in processing raw material mass and associated disturbance management. Occupational risks particularly typical for the cell factory are allergenic substances, such as enzymes and organic materials, which can cause irritation and even allergies and occupational diseases for workers even in small concentrations. Power outages can also pose a danger to people either through product quality deterioration or due to unsafe disturbance management measures. Inadequacies in sampling (coverage, representativeness) can pose risks to many people if poor-quality products reach the market.
Rare but serious risks to personal safety were assessed to arise from incompatibility issues of stored chemicals (reactions), pressure releases or explosions of pressure equipment. Some substances used, e.g., nitrogen, can also cause either oxygen displacement or suffocation hazards in the event of a leak. Ammonia leakage can cause fatalities, if people are present in the same location where the leakage occurs. Malfunctioning of safety systems was also assessed to cause serious personal injuries.
Compromising product safety can pose a risk to many people. Food safety and nutritional risks of the product can also pose a danger to consumers, although the existing novel food approval processes were considered to reduce this risk significantly. However, food safety needs to be guaranteed and controlled continuously from raw materials to final product at well planned control points. Since fermentation processes are supposed to provide optimal growth conditions to production microbes, it is important to prevent contamination of process and have strict threshold limits for harmful microbes, especially when side streams are used as raw materials. A proper HACCP (hazard analysis and critical control points) plan should be made separately from food safety point of view in order to ensure food grade quality, good manufacturing practices and efficient cleaning procedures (Lelieveld et al., 2003).
Impacts on environmental safety
The cell factory was assessed to pose a risk to environmental safety mainly through air emissions during normal operation. The distribution of identified scenarios on the environmental safety criticality matrix is shown in Figure 11. The number of the most critical scenarios from the environmental point of view was 7 out of 110.
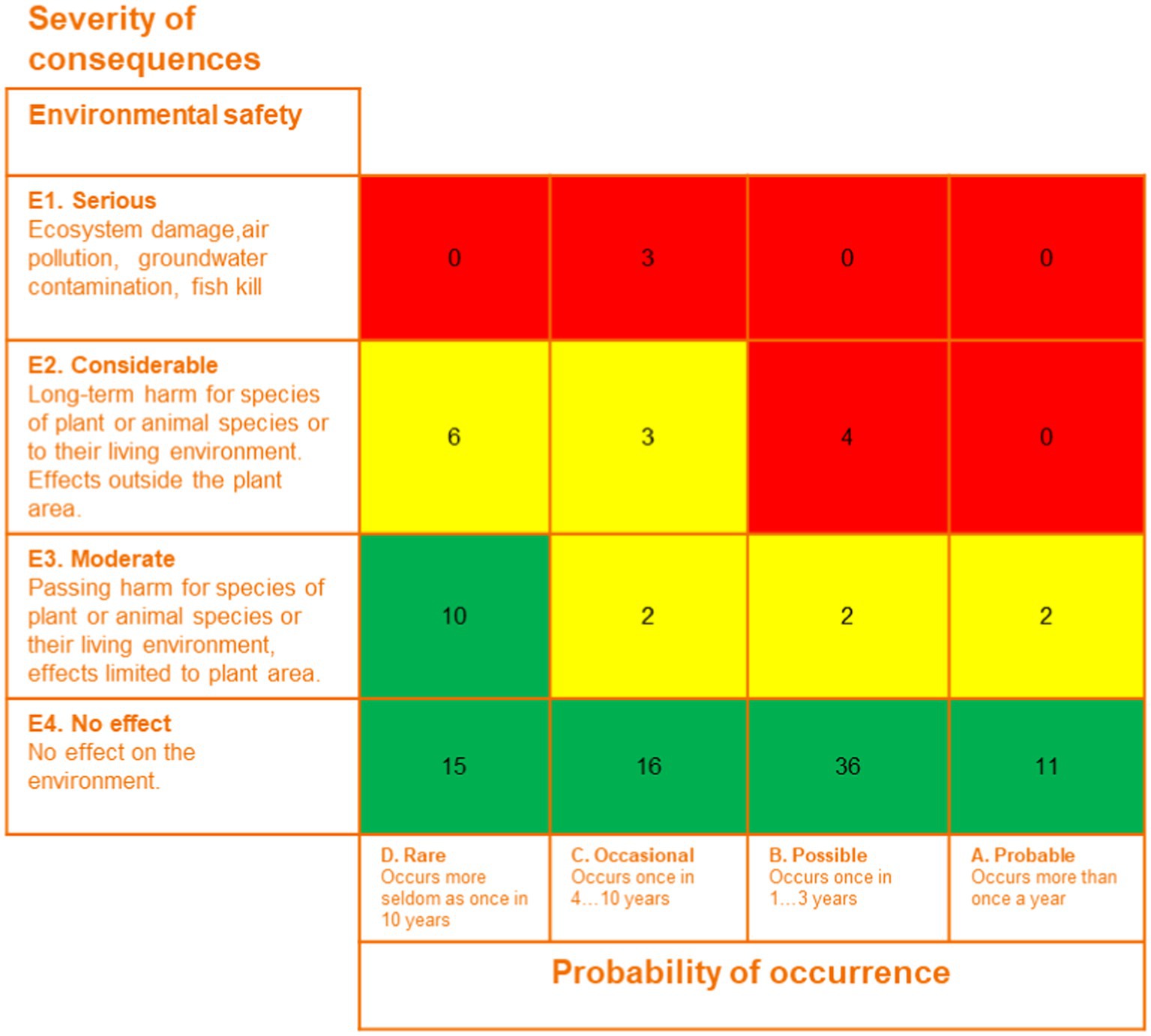
Figure 11. The distribution of identified scenarios on environmental safety criticality matrix of a cell factory. The number in each criticality matrix cell expresses the number of scenarios assessed to that risk category. The most critical categories are marked with red colour (intolerable risks), moderate categories with yellow colour and insignificant risks with green colour indicating the severity of consequences if the scenario in question would realise.
The most critical environmental risks were assessed to be occasional air emissions, odours, other impurities in the air (depending on the steam production method used), and noise. Such environmentally impactful disturbance situations were estimated to occur every few years.
If GM organisms are utilised in the process, their accidental release into the surrounding environment can lead to environmental damage, the extent and duration of which are challenging to predict without exact prior knowledge of the organism in question. Although the release of GMOs outside the facility due to failed inactivation, either directly or through wastewater, is considered infrequent, regulations mandate comprehensive risk assessments when applying for GM operation permits thus ensuring that adequate risk management practices are in place.
The facility may use hazardous substances, e.g., ammonia, which can pose a danger to the surrounding environment and nearby people. In the event of a fire, the water and possible extinguishing chemicals used must be collected in separate firewater basins to prevent surface and groundwater contamination. Intentional vandalism, such as sabotage or terrorism, can cause significant environmental damage. Emissions to the environment due to terrorism or intentional vandalism were classified as occasional. These incidents can have unpredictable consequences if, for example, pipelines carrying toxic substances or tanks containing them are damaged.
Even if no direct environmental damage occurs, intentional vandalism can cause very long production interruptions, at worst leading to the complete shutdown of the entire production facility. While accidental situations can be prepared for, it is more challenging to prepare for intentional vandalism. Special attention should be paid to preventing terrorist acts, for example, in the placement of critical pipelines (underground channels), the strength of above-ground structures (drone threat), and the arrangement of road connections (multiple route options, avoiding bridges and tunnels).
The most meaningful risks identified
Key risks according to our study in future cell factory include:
• Significant risks related to the availability of raw materials, water, and energy, which could disrupt the production process.
• The impact of megatrends like climate change and resource scarcity on cellular agriculture processes.
• The potential for cybersecurity threats to cause production cancellations, quality issues, and environmental impacts.
The results of the analysed production interruption, occupational health, product and environmental risks are summarised in Table 1. The risks are classified into related categories: raw materials, commodities, operations, and communication. Problems with raw material quality and logistics lead to production interruptions. Issues with commodities problems can also lead to production interruptions and pose health risks to people. Risks in process operations can result in maintenance challenges but also pose risks to people. Communication problems will jeopardize production, people and environmental safety.
Discussion
Cellular agriculture relies heavily on advanced technologies, biotechnology, industrial processes, automation, ICT, and energy. Also climate change and resource scarcity can significantly impact production. Various global phenomena and the evolving, interdependent operating environment affect the authorities, society and individual companies (Ministry of Interior, 2023; Hartley et al., 2024). Consumer acceptance and safety are also crucial for cellular agriculture-based ingredients (Ritala et al., 2017; Soice and Johnston, 2021; Powell et al., 2023).
The risks in cell and traditional food factories are partly similar but differ significantly due to their operations and specific hazards. Traditional food factories face significant microbiological risks from handling raw agricultural products and live animals, which can introduce pathogens. Effective hygienic design and sanitation practices are crucial to mitigate these risks (Lelieveld et al., 2003). While cell factories also face microbiological risks, their controlled environments can reduce contamination likelihood. However, breaches can lead to significant contamination issues. Single-cell protein products may still pose potential food safety challenges, such as the presence of toxins, contamination, and allergens, especially if alternative carbon sources are used (Hadi and Brightwell, 2021). Compromising ingredient safety poses significant risks, including potential contaminants and questions about nutritional benefits and long-term health impacts (Häkkinen et al., 2020; Soice and Johnston, 2021; Rao et al., 2023).
Chemical risks in cell factories stem from bioprocessing stages, whereas in traditional food factories, they often come from ingredients, packaging materials, and cleaning agents. Physical risks are generally lower in cell factories but can include contamination from equipment or materials used in bioprocessing. Traditional food factories face physical hazards like foreign objects entering the food during processing. Future cell factories may use side streams as raw material, which typically have variations in content, microbiological load, and may contain toxins, hazardous components, and foreign objects. Emerging threats include allergens, necessitating research and data on potential allergens in new products. New combinations of processing steps can lead to unknown risks.
Cellular agriculture can face numerous disruptions that could impede its progress and implementation, challenging its resilience (García Martínez et al., 2022; Kakaei et al., 2022). These challenges include energy and water shortages, logistical disruptions, cyber threats, infrastructure needs, communication network issues, and broader concerns such as conflict, terrorism, and climate change (Ministry of Interior, 2023). Disruptions in global value and supply chains test companies’ ability to adapt and maintain operational continuity.
In this study, we identified several incidence scenarios which might impact cellular agriculture processes, each with multiple impacts on society. Disruptions in energy supply (e.g., electricity, steam) and their occasional high price were found to be critical risks for production continuity. Interruptions in electricity supply can disrupt cooling, heating, and compressed air availability in cell factories, leading to production and quality problems. The most common threats are disruptions in the availability of energy and its price. This is consistent with previous findings (Ministry of Interior, 2023; Kuhmonen et al., 2023). Similarly, the dependence of cellular agriculture on a continuous energy supply is crucial for resilient production and sustainability, both vital for food production stability (Soice and Johnston, 2021; Li et al., 2024). Therefore, ensuring a stable energy supply through backup power or an in-house power plant is crucial.
This study emphasises the criticality of the water supply and quality. Disruptions in good quality water availability can cause process interruptions or even damage to the process equipment. Water quality hazards or disruptions can result from several reasons. According to UNESCO (2024), climate change is anticipated to modify the global water cycle affecting rainfall patterns and potentially leading to droughts or floods (UNESCO, 2024). Additionally, disruptions in water supply may arise from issues such as shortages of essential chemicals or components, power outages, and telecommunication failures (Ministry of Interior, 2023).
Ensuring product safety requires continuous monitoring and preventive measures are needed to protect against intentional vandalism and other disruptions. The high-tech food production processes are dependent on information and communication systems (ICT) (Kuhmonen et al., 2023). Disruptions in information and communication systems, whether due to internal issues or external cyber threats, were found to be problematic. ICT systems comprise multiple vulnerabilities related to data management, automation, and cyber risks, among other things (Ministry of Interior, 2023). In the future factories, also cell factories, will be governed by digital technologies, like advanced artificial intelligence (AI), digital twin modelling and internet of things (IoT) systems with on-line monitoring, data sharing and management, as are the future technological trends in process industry (Maia et al., 2022). Cybersecurity threats will increase in the future, and focus should be on managing them with cybersecurity measures.
The supply of raw materials is critical in all production processes. Disruption in transportation and logistics chains will impact through several pathways, for example, changes in transportation routes due to political situations or pandemics causing disruptions in the global container transport system (Ministry of Interior, 2023). Cyber-attacks, data breaches, sabotage, and malware can also affect the transportation network (Ministry of Interior, 2023). Disruptions in any part of the logistics chain can cause severe problems, especially in the supply of raw materials, in this case, decentralised production of agriculture side streams. Similarly, Kuhmonen et al. (2023) noticed that disruption in arranging sufficient raw material production may bring on vulnerabilities. The transportation disruptions may affect even the global value and supply chains, causing discontinuity in the availability of fuels, chemicals, components, and spare parts. In addition, difficulties in the supply of other commodities (pressurised air, cooling, heating) were discovered as significant risks as well.
Safety risks are similar in other alternative protein products (Banach et al., 2023). Strict regulatory frameworks and comprehensive safety assessments are in place, but improvements are needed in evaluating contaminants in raw materials/feedstock (Li et al., 2024). An effective product quality monitoring system should be built in the cell factory, operating continuously. Non-continuous monitoring based on sampling can allow poor-quality batches to reach the market. The HACCP (Hazard Analysis and Critical Control Points) approach should be applied while building the self-monitoring system for the cell factory. Recognised occupational risks were mechanical crushing and impact risks typical for moving machine actuators. Occupational safety concerns include mechanical hazards caused by machinery and exposures or chemical release incidents. Also, the handling of potentially allergenic substances was identified as a significant occupational risk. However, similar risks are common also in other sectors of the food-processing industry (Spök, 2006; Gaspar et al., 2019).
Since cellular agriculture requires much energy, the choice of the energy sources will impact the air emissions (Smetana et al., 2015; Järviö et al., 2021a; Järviö et al., 2021b). This was one of the identified environmental risks in our study as well. Current and future trends are moving toward fossil-free energy, which will ensure carbon-free energy production and mitigate air emissions. Green energy options include renewable energy options like wind and solar. Additionally, if clean energy is considered, nuclear energy could also be an option for cell factories in the future, especially with the advancement of small modular reactor technology.
Ab Rahim et al. (2024) advocate for comprehensive approaches incorporating process safety, security and threat management (Ab Rahim et al., 2024). In our exercise we structured the risks in production interruptions, which cause mainly economic impacts, occupational, health and product safety including consumer safety, and environmental safety representing the impacts to the surrounding society. Therefore, in our case, we tried to tackle all the sustainable development pillars in risk search, which are economical, societal and environmental impacts.
Study limitations
HAZSCAN method is often utilised to analyse an existing process plant. In this study it was applied to an imaginary production process, which does not exist at the moment. Consequently, the A&P model description might not be as comprehensive as it would be for an existing facility. However, the subprocesses are fairly well known, so the main parts of the A&P model are valid.
HAZSCAN is a comprehensive step-by-step risk assessment method. However, as it is qualitative in nature, the results depend entirely on the expertise of the analysis group. In this study, most participants had extensive experience with microbial processes, both in research and industrial applications. Despite this fact, it is probable that if the same analysis were conducted by the same group a second time, the results could differ slightly from the first round.
In the criticality assessment part of the study, estimating the probability of occurrence of scenarios was particularly challenging due to the lack of operational data from the exact process combination studied. The analysis group based their probability estimations on their own expertise, which was gathered from various microbiological applications and processes. Criticality assessment was accomplished in a single session to maintain consistency in the assessments.
Tixier et al. (2002) provide an overview of various risk analysis techniques for industrial plants, noting the challenges in addressing all potential risks and emphasising that no single method can universally manage industrial risks (Tixier et al., 2002). Therefore, other risk analysis methods could be utilised to complement the results gathered with HAZSCAN.
Conclusion
This study identifies several significant risks that may affect the operation of a cell factory in 2040. These include potential shortages of freshwater, power outages, and scarcity of chemicals and other materials. The findings highlight that the availability of raw materials, water, and energy are critical to maintaining production continuity. Moreover, the analysis underscores the necessity for comprehensive safety and risk management methods that account for process, occupational and environmental safety. We can also conclude that megatrends, such as climate change and resource scarcity (WEF, 2024), are significantly impacting cell agriculture processes jeopardising resource and raw material availability as well as increasing the electricity and water vulnerability. Climate change will cause extreme weather conditions (extreme temperatures, droughts, storms, floods, etc.) impacting ecosystems, industry, and supply chains. Operational risks will however remain consistent and the same as those currently faced by the process and food industry.
Increasing digitalisation and dependence on information and communication services expose operators to cybersecurity threats. Disruptions in electricity and information systems make highly automated systems particularly vulnerable. Our risk assessment highlighted these issues, noting that they can lead to production cancellations, quality problems, and environmental impacts. These challenges may intensify as automation, digitalisation, and terrorism become more prevalent. Wars and other societal disruptions could also increasingly threaten industrial systems. Climate change and biodiversity loss are expected to exacerbate these challenges. A growing concern is the information transfer within the process and the potential for hindering or disrupting these communications.
The risk analysis method was working well, although the challenge is to move the identification of risks to the far future. Cell factory is in general a normal process industry plant, and therefore the identified risks are quite much the same as in existing process and food industry plants. However, only a few products, e.g., Quorn and recombinant enzymes like chymosin widely applied in the food industry are in use and most of the cellular agriculture-based products are still in the development stages (Olempska-Beer et al., 2006). Thus, the existing examples are few and this makes the interpretation of the risk scenarios related to Cell Factories in connection to the future society very important.
Recommendations
Ensure stable supply of commodities. Secure a reliable electricity, water, and raw materials supply to prevent production interruptions. Consider backup power solutions or in-house power plants to mitigate risks from power outages.
Enhance cybersecurity measures. Protect information and communication systems from cyber threats to avoid production disruptions. Limit external network connections to essential control commands only.
Improve raw material logistics. Develop robust logistics plans to handle potential disruptions in raw material supply and maintain sufficient storage capacity to buffer against supply chain interruptions.
Implement comprehensive safety protocols. Establish rigorous occupational safety measures to protect workers and apply the HACCP (Hazard Analysis and Critical Control Points) approach for continuous product quality monitoring.
Address environmental risks. Ensure proper handling and containment of hazardous substances to prevent accidental releases. Monitor and control air emissions, odours, and noise to minimise environmental impact.
Foster consumer acceptance. Engage in proactive communication to address consumer concerns about the safety and quality of cellular agriculture ingredients. Conduct thorough testing and quality assurance to build trust in new products.
Data availability statement
The datasets presented in this article are not readily available because confidential information. Requests to access the datasets should be directed to dGVyby52YWxpc2Fsb0B2dHQuZmk=.
Author contributions
TV: Conceptualization, Formal analysis, Investigation, Methodology, Writing – original draft, Writing – review & editing. SS: Conceptualization, Formal analysis, Methodology, Writing – original draft, Writing – review & editing. NW: Conceptualization, Formal analysis, Methodology, Writing – original draft, Writing – review & editing. AR: Conceptualization, Formal analysis, Methodology, Writing – original draft, Writing – review & editing. AS: Conceptualization, Formal analysis, Methodology, Writing – original draft, Writing – review & editing.
Funding
The author(s) declare that financial support was received for the research and/or publication of this article. This work was funded by the VTT’s internal strategic innovation programme, VTT iBEX in 2024.
Acknowledgments
The authors thank Dr. Emilia Nordlund for supporting the study and encouraging its publication. The authors thank also experts participating in the group work session during the risk assessment: Drs. Anu Seisto, Marjoriikka Ylisiurua, Juha-Pekka Pitkänen, Joosu Kuivanen, Kaisu Riihinen, Eevi Haajanen, Juha Tähtiharju, and Hans Mattila.
Conflict of interest
The authors declare that the research was conducted in the absence of any commercial or financial relationships that could be construed as a potential conflict of interest.
Generative AI statement
The authors declare that Gen AI was used in the creation of this manuscript. The authors utilised Scopus AI for literature search and Microsoft Co-Pilot for proofreading.
Publisher’s note
All claims expressed in this article are solely those of the authors and do not necessarily represent those of their affiliated organizations, or those of the publisher, the editors and the reviewers. Any product that may be evaluated in this article, or claim that may be made by its manufacturer, is not guaranteed or endorsed by the publisher.
References
Ab Rahim, M. S., Reniers, G., Yang, M., and Bajpai, S. (2024). Risk assessment methods for process safety, process security and resilience in the chemical process industry: a thorough literature review. J. Loss Prev. Process Ind. 88:105274. doi: 10.1016/j.jlp.2024.105274
Banach, J. L., van der Berg, J. P., Kleter, G., van Bokhorst-van de Veen, H., Bastiaan-Net, S., Pouvreau, L., et al. (2023). Alternative proteins for meat and dairy replacers: food safety and future trends. Crit. Rev. Food Sci. Nutr. 63, 11063–11080. doi: 10.1080/10408398.2022.2089625
El Wali, M., Rahimpour Golroudbary, S., Kraslawski, A., and Tuomisto, H. L. (2024). Transition to cellular agriculture reduces agriculture land use and greenhouse gas emissions but increases demand for critical materials. Commun. Earth Environ. 5:61. doi: 10.1038/s43247-024-01227-8
Fytsilis, V. D., Urlings, M. J. E., van Schooten, F.-J., de Boer, A., and Vrolijk, M. F. (2024). Toxicological risks of dairy proteins produced through cellular agriculture: current state of knowledge, challenges and future perspectives. Future Foods 10:100412. doi: 10.1016/j.fufo.2024.100412
García Martínez, J. B., Pearce, J. M., Throup, J., Cates, J., Lackner, M., and Denkenberger, D. C. (2022). Methane single cell protein: potential to secure a global protein supply against catastrophic food shocks. Front. Bioeng. Biotechnol. 10:906704. doi: 10.3389/fbioe.2022.906704
Gaspar, P. D., Lima, T., and Lourenço, M. (2019). Relevant occupational health and safety risks in the portuguese food processing industry. Int. J. Occup. Environ. Safety 3, 23–33. doi: 10.24840/2184-0954_003.003_0003
Hadi, J., and Brightwell, G. (2021). Safety of alternative proteins: technological, environmental and regulatory aspects of cultured meat, plant-based meat, insect protein and single-cell protein. Food Secur. 10:1226. doi: 10.3390/foods10061226
Häkkinen, S. T., Nygren, H., Nohynek, L., Puupponen-Pimiä, R., Heiniö, R.-L., Maiorova, N., et al. (2020). Plant cell cultures as food—aspects of sustainability and safety. Plant Cell Rep. 39, 1655–1668. doi: 10.1007/s00299-020-02592-2
Hartley, K., Baldassarre, B., and Kirchherr, J. (2024). Circular economy as crisis response: a primer. J. Clean. Prod. 434:140140. doi: 10.1016/j.jclepro.2023.140140
IEC (2019). 31010:2019 Risk management - Risk assessment techniques. Geneva, Switzerland: International Electrotechnical Commission.
Jacobson, M. F., and DePorter, J. (2018). Self-reported adverse reactions associated with mycoprotein (Quorn-brand) containing foods. Ann. Allergy Asthma Immunol. 120, 626–630. doi: 10.1016/j.anai.2018.03.020
Järviö, N., Maljanen, N.-L., Kobayashi, Y., Ryynänen, T., and Tuomisto, H. L. (2021a). An attributional life cycle assessment of microbial protein production: a case study on using hydrogen-oxidizing bacteria. Sci. Total Environ. 776:145764. doi: 10.1016/j.scitotenv.2021.145764
Järviö, N., Parviainen, T., Maljanen, N.-L., Kobayashi, Y., Kujanpää, L., Ercili-Cura, D., et al. (2021b). Ovalbumin production using Trichoderma reesei culture and low-carbon energy could mitigate the environmental impacts of chicken-egg-derived ovalbumin. Nat. Food 2, 1005–1013. doi: 10.1038/s43016-021-00418-2
Kakaei, H., Nourmoradi, H., Bakhtiyari, S., Jalilian, M., and Mirzaei, A. (2022). “Effect of COVID-19 on food security, hunger, and food crisis” in COVID-19 and the sustainable development goals, eds. R. R. K. Mohammad Hadi Dehghani and Sharmili Roy. Kakei: Elsevier. 3–29.
Kobayashi, Y., Kärkkäinen, E., Häkkinen, S. T., Nohynek, L., Ritala, A., Rischer, H., et al. (2022). Life cycle assessment of plant cell cultures. Sci. Total Environ. 808:151990. doi: 10.1016/j.scitotenv.2021.151990
Koivisto, R., Wessberg, N., Eerola, A., Ahlqvist, T., Kivisaari, S., Myllyoja, J., et al. (2009). Integrating future-oriented technology analysis and risk assessment methodologies. Technol. Forecast. Soc. Chang. 76, 1163–1176. doi: 10.1016/j.techfore.2009.07.012
Kuhmonen, T., Penttilä, A., Kuhmonen, I., Selänniemi, M., Saarimaa, R., Savikurki, A., et al. (2023). ed. Kumonen, et al. “Suomen ruokajärjestelmän haavoittuvuus: keskinäisriippuvuuksien verkko toimintakyvyn haasteena” in Tutu e-julkaisuja : University of Turku.
Lelieveld, H. L., Mostert, M. A., Holah, J., and White, B. (2003). Hygiene in food processing. England: Woodhead Publishing Limited, Cambridge.
Li, Y. P., Ahmadi, F., Kariman, K., and Lackner, M. (2024). Recent advances and challenges in single cell protein (SCP) technologies for food and feed production. NPJ Sci. Food 8:66. doi: 10.1038/s41538-024-00299-2
Maia, E., Wannous, S., Dias, T., Praça, I., and Faria, A. (2022). Holistic security and safety for factories of the future. Sensors 22:9915. doi: 10.3390/s22249915
Malmén, Y., Tiihonen, J., and Wessberg, N. (1999). Management of accidental releases in the forest industry. Water Sci. Technol. 40, 313–317. doi: 10.1016/S0273-1223(99)00733-7
Ministry of Interior (2023). “National Risk Assessment 2023”, in: Internal security - publications of the Ministry of the Interior 2023:6. Helsinki, Finland: Ministry of Interior.
Nyyssölä, A., Suhonen, A., Ritala, A., and Oksman-Caldentey, K.-M. (2022). The role of single cell protein in cellular agriculture. Curr. Opin. Biotechnol. 75:102686. doi: 10.1016/j.copbio.2022.102686
Olempska-Beer, Z. S., Merker, R. I., Ditto, M. D., and DiNovi, M. J. (2006). Food-processing enzymes from recombinant microorganisms—a review. Regul. Toxicol. Pharmacol. 45, 144–158. doi: 10.1016/j.yrtph.2006.05.001
Panel on Genetically Modified Organisms EFSA Mullins, E., Bresson, J.-L., Dewhurst, I. C., Epstein, M. M., Firbank, L. G., et al. (2024). New developments in biotechnology applied to microorganisms. EFSA J. 22:e8895. doi: 10.2903/j.efsa.2024.8895
Pihlajaniemi, V., Ellilä, S., Poikkimäki, S., Nappa, M., Rinne, M., Lantto, R., et al. (2020). Comparison of pretreatments and cost-optimization of enzymatic hydrolysis for production of single cell protein from grass silage fibre. Biores. Technol. Rep. 9:100357. doi: 10.1016/j.biteb.2019.100357
Powell, L. J., Mendly-Zambo, Z., and Newman, L. L. (2023). Perceptions and acceptance of yeast-derived dairy in British Columbia, Canada. Front. Sustain. Food Syst. 7:1127652. doi: 10.3389/fsufs.2023.1127652
Rao, V. V., Datta, B., and Steinmetz, K. (2023). The role of natural scientists in navigating the social implications of cellular agriculture: insights from an interdisciplinary workshop. Front. Sustain. Food Syst. 7:1134100. doi: 10.3389/fsufs.2023.1134100
Rinne, M. (2024). Novel uses of ensiled biomasses as feedstocks for green biorefineries. J. Animal Sci. Biotechnol. 15:36. doi: 10.1186/s40104-024-00992-y
Ritala, A., Häkkinen, S. T., Toivari, M., and Wiebe, M. G. (2017). Single cell protein—state-of-the-art, industrial landscape and patents 2001–2016. Front. Microbiol. 8:2009. doi: 10.3389/fmicb.2017.02009
Smetana, S., Mathys, A., Knoch, A., and Heinz, V. (2015). Meat alternatives: life cycle assessment of most known meat substitutes. Int. J. Life Cycle Assess. 20, 1254–1267. doi: 10.1007/s11367-015-0931-6
Soice, E., and Johnston, J. (2021). How cellular agriculture systems can promote food security. Front. Sustain. Food Syst. 5:753996. doi: 10.3389/fsufs.2021.753996
Tixier, J., Dusserre, G., Salvi, O., and Gaston, D. (2002). Review of 62 risk analysis methodologies of industrial plants. J. Loss Prev. Process Ind. 15, 291–303. doi: 10.1016/S0950-4230(02)00008-6
Tuomisto, H. L. (2022). Challenges of assessing the environmental sustainability of cellular agriculture. Nat. Food 3, 801–803. doi: 10.1038/s43016-022-00616-6
UNESCO (2024). The United Nations world water development report 2024: Water for prosperity and peace. Paris: UNESCO.
Whittaker, J. A., Johnson, R. I., Finnigan, T. J. A., Avery, S. V., and Dyer, P. S. (2020). “The biotechnology of Quorn Mycoprotein: past, present and future challenges” in Grand challenges in fungal biotechnology. ed. H. Nevalainen (Cham: Springer International Publishing), 59–79.
Keywords: cellular agriculture, risk assessment, HAZSCAN, continuity, occupational safety, product safety, environmental safety, process safety
Citation: Välisalo T, Salo S, Wessberg N, Ritala A and Säämänen A (2025) Risk evaluation of a future B2B cell factory process producing cellular agriculture ingredients. Front. Sustain. Food Syst. 9:1562464. doi: 10.3389/fsufs.2025.1562464
Edited by:
Elena Velickova, Saints Cyril and Methodius University of Skopje, North MacedoniaReviewed by:
Abdullah Mohammad Shohael, Jahangirnagar University, BangladeshFatih Demirel, Iğdır University, Türkiye
Copyright © 2025 Välisalo, Salo, Wessberg, Ritala and Säämänen. This is an open-access article distributed under the terms of the Creative Commons Attribution License (CC BY). The use, distribution or reproduction in other forums is permitted, provided the original author(s) and the copyright owner(s) are credited and that the original publication in this journal is cited, in accordance with accepted academic practice. No use, distribution or reproduction is permitted which does not comply with these terms.
*Correspondence: Tero Välisalo, dGVyby52YWxpc2Fsb0B2dHQuZmk=
†These authors have contributed equally to this work
‡ORCID: Tero Välisalo, https://orcid.org/0009-0009-4717-7608