- Mechatronic Systems Laboratory, Institute of Machine Design and Systems Technology, Technische Universität Berlin, Berlin, Germany
This paper presents the development and experimental validation of a hybrid modeling framework for a bistable soft robotic system driven by dielectric elastomer (DE) actuators. The proposed approach combines physics-based analytical modeling with data-driven radial basis function (RBF) networks to capture the nonlinear and dynamic behavior of the soft robots. The bistable DE system consists of a buckled beam structure and symmetric DE membranes to achieve rapid switching between two stable states. A physics-based model is first derived to describe the electromechanical coupling, energy functions, and dynamic behavior of the actuator. To address discrepancies between the analytical model and experimental data caused by geometric asymmetries and unmodeled effects, the model is augmented with RBF networks. The model is refined using experimental data and validated through analytical, numerical, and experimental investigation.
1 Introduction
The emerging field of soft robotics offers the potential to replace traditional articulated robots made of rigid joints and materials, such as electric motors and piezoceramic actuators, with soft actuators functioning as artificial muscles in robotic systems. Dielectric elastomer transducers (DETs) are a prominent class of soft actuators capable of deforming under applied voltage. These actuators mimic biological muscles, excelling in attributes such as large deformation (Li et al., 2013), high energy density (Duduta et al., 2019), and fast response times (Chen et al., 2019). DETs consist of a soft dielectric material sandwiched between two flexible electrodes, with layer thicknesses in the micrometer range. Functionally, DETs act as deformable capacitors, relying on electrostatic stress to achieve significant deformation upon sufficient voltage application (Pelrine et al., 2000).
DE-based actuators have been widely adopted in the development of soft robotic systems (Guo et al., 2021), including grasping mechanisms (Kofod et al., 2007; Wang et al., 2019), walking robots (Eckerle et al., 2001; Pelrine et al., 2002), flying robots (Lau et al., 2014), and humanoid robots (Kovacs et al., 2007).
Bistable soft robotic systems have attracted significant research attention due to their energy-efficient and versatile design potential, particularly in applications requiring rapid and reliable switching between two stable states. These actuators are well-suited for a variety of applications, including robotic systems, valve controls, and gripper mechanisms, where precise and consistent actuation is essential (Cao Y. et al., 2021; Chi et al., 2022; Harne and Wang, 2013). A range of bistable DE transducer designs have been proposed, highlighting their adaptability for diverse use cases. Examples include digital mechatronic systems with multiple degrees of freedom (Wingert et al., 2006), compact configurations combining cross-shaped bistable elements with conical DE actuators (Follador et al., 2015a), and bio-inspired soft grippers based on DE minimum energy structures Wang et al. (2019). Another design involves a bistable DE actuator comprising a buckled beam and two vertically arranged DE roll actuators to drive a rigid plate (Baltes et al., 2022). These designs are often supported by analytical and finite element models to study their static and dynamic behaviors. A common feature in many bistable DE designs is the use of buckled beams, valued for their mechanical bistability and reliability. Additionally, membrane geometries such as diamond, conical, roll, or strip shapes allow for tailored actuator performance to meet specific application requirements (Follador et al., 2015a; Follador et al., 2015b).
Beside, advancements in modeling and simulation of DETs have addressed their complex nonlinear behaviors. Physics-based approaches have been extensively utilized to describe the static behavior of DEs, considering hyperelastic material properties and electrostatic coupling (Suo, 2010; Zhang et al., 2006) as well as static hysteresis effects (Mertens et al., 2024). Finite element methods (FEM) have been used to capture the influence of mechanical boundary conditions, geometric inhomogeneities, and complex DE configurations (Wissler and Mazza, 2005; Kuhring et al., 2015). Furthermore, advanced dynamic continuum models have been introduced, accounting for nonlinear electromechanical coupling (Hansy-Staudigl et al., 2019). In addition to FEM-based methods, control-oriented modeling approaches have emerged, treating DEs as systems with lumped parameters. These models incorporate viscoelastic behaviors, represented by Kelvin-Voigt, Maxwell elements and address electrical losses from resistances (Sarban and Jones, 2012; Jones and Sarban, 2012; Hackl et al., 2005). Specific dynamic models have been proposed for various DE configurations, including stack actuators (Hoffstadt and Maas, 2015; Masoud et al., 2021), membrane actuators with spring preloading (Rizzello et al., 2016), and bistable robot modules featuring roll DE actuators (Soleti et al., 2023). For bistable DE systems, dynamic vibration and bifurcation analyses of circular membranes with springs were further investigated (Wang Z. et al., 2024; Cao C. et al., 2021).
Despite the widespread success of physics-based methods, there is a notable shift toward data-driven approaches for modeling soft robot systems, using advancements in machine learning techniques (Kim et al., 2021). Purely data-driven methods, such as radial basis function networks, recurrent neural networks (RNNs), and multilayer perceptrons, have been employed to model complex nonlinear behaviors without requiring explicit knowledge of underlying physical principles (Chen et al., 2024; Melingui et al., 2014). These approaches rely on empirical training, achieving high accuracy in capturing system dynamics.
Hybrid methods, combining data-driven machine learning with physics-based models, have also gained attention. These include frameworks that integrate machine learning components with existing first-principles models (Johnson et al., 2021) and physics-informed neural networks (PINNs), designed to embed physical laws directly into the learning process (Liu et al., 2024; Wang X. et al., 2024; Sun et al., 2022). Such approaches offer a balance between empirical accuracy and interpretability, enhancing the robustness of nonlinear system modeling. In the context of dielectric elastomer actuators (DEAs), neural network architectures such as long short-term memory (LSTM) networks (Xiao et al., 2020), radial basis function networks (Xiao et al., 2023), and gated recurrent units (GRUs) (Zhang et al., 2023) have been employed to model dynamic and nonlinear behaviors, including hysteresis and creep effects. Additionally, self-sensing models for DEAs have been developed using nonlinear autoregressive networks with exogenous inputs, enabling predictive modeling of displacement without requiring external sensors (Huang et al., 2023). While these data-driven approaches exhibit excellent alignment with experimental data, they often lack explicit incorporation of physical principles, underscoring the trade-off between predictive accuracy and interpretability.
This paper focuses on the development of a physics-based and data driven dynamic model for a bistable soft robot based on DE actuators. In this work, a similar structure to that in (Follador et al., 2015b) is investigated, but with a different constructive and kinematic design. While (Follador et al., 2015b) incorporated two lateral beams and two parallel DEs (consisting of VHB) in the center, our design features a single central beam with two laterally arranged DE membranes made of silicone. Similar structures and ideas have been previously introduced in (Masoud and Maas, 2023), where a variant is implemented in this paper for model validation and analyzed in detail. While previous studies employed a static model for designing the bistable DE actuator, this paper presents a systematic design approach that not only considers the static behavior but also incorporates dynamic effects, external forces, and a comprehensive description of the kinematics. The model is developed to be directly applicable to further system and control engineering applications. Moreover, the models investigated in this paper are directly compared with experimental data, with a particular focus on analyzing the transient response and accounting for inaccuracies in the entire actuator design. The derivation of the governing equations follows the framework presented in (Masoud and Maas, 2023), providing a foundation for analyzing the DE system’s dynamic behavior.
To enhance the accuracy and generalizability of the model, a hybrid approach is introduced that integrates physics-informed structures with data-driven methodologies. Specifically, the model is refined and augmented using artificial neural networks trained with experimental data, with a focus on radial basis function (RBF) networks. The RBF network is chosen for its ability to handle nonlinearities in a straightforward and interpretable manner, offering an effective means of capturing the complex behaviors of the bistable DE actuator.
The further contribution of this paper is structured as follows. Section 2 introduces the operating principles and design details of the bistable DE actuated system. Section 3 presents the physics-based modeling approach, analyzing the essential characteristics of the soft system and offers a reduced-order model under analytical considerations. In Section 4, a hybrid modeling approach is outlined, where the physics-based model is enhanced with a RBF neural network to effectively capture nonlinearities and uncertainties of the bistable DE systems. Section 5 provides a comprehensive validation of the proposed model through numerical simulations and experimental data. Finally, Section 6 summarizes the findings.
2 Concept and design of the bistable dielectric elastomer
Figure 1 illustrates the concept and behavior of the proposed bistable DE-actuator, highlighting both its mechanical configuration and its bistable characteristics through potential energy and force curves. Figure 1a shows the actuator system in its three possible states. The system consists of a buckled beam, two symmetric DE membrane, and a moving mass (blue) that connects the elastic structure to the DEs. The DE membranes are pre-stretched such that the beam assumes one of two stable, buckled positions, either to the left or to the right. The application of a voltage (
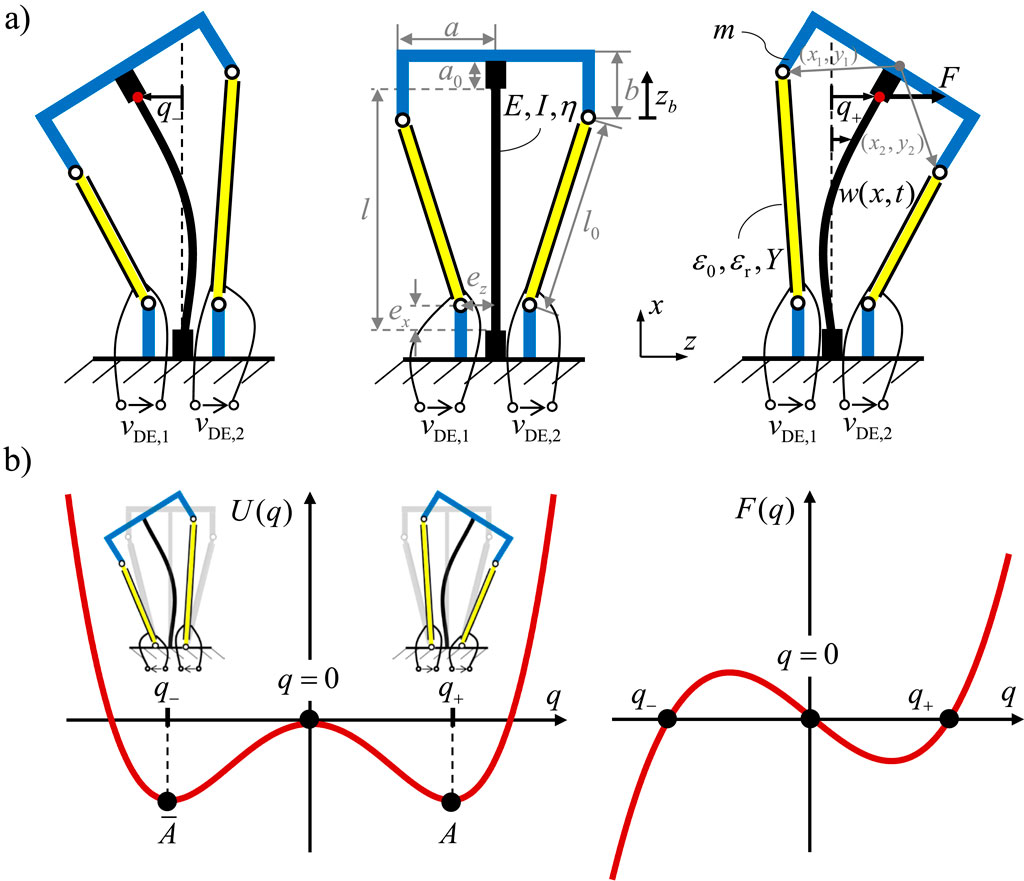
Figure 1. Concept of the bistable DE actuated system: (a) Schematic Representation with geometric dimensions and material parameters, (b) potential energy and force curves.
Figure 1b visualizes the bistable nature of the system through potential energy
The CAD design of the bistable DE system is illustrated in Figure 2. The exploded view shows the arrangement of the system’s parts. The U-shaped lower fixed frame serves as a platform for mounting two black suspensions on its right and left sides, which are used to attach the two DE membranes at their lower ends. The DE actuators are designed in a strip-like configuration and arranged and arranged symmetrically. Centrally positioned within this frame is a slender beam made of PETG, which forms the buckled axis capable of toggling between two stable positions.
The actuator’s active elements are two symmetrical DE membranes and produced as multilayer laminates using the manufacturing process (Krüger et al., 2023). For the experimental investigations presented in this paper, we used the dielectric elastomer material ELASTOSIL® 2030 (EL 2030) (Wacker, 2016), which has a layer thickness of
The two membranes, held in dedicated mounts, deform in response to applied voltage, thereby actuating the buckled beam. The two upper black mounts connect the two DE actuators at their upper ends, which are linked to a freely movable U-shaped frame. At this upper section of the actuator, two adjustment screws enable precise control of the pre-strains in the DE membranes and allow for fine-tuning of the membrane tension. The pre-stretched DEs are a critical feature, as it enables precise calibration of the actuator’s initial state and facilitates smooth transitions between its two stable states. Various connecting components, including screws and fasteners, ensure the precise alignment and structural integrity of the system.
The fully assembled soft DE system in Figure 2b presents a compact design tailored for precise functionality. The central buckled structure is symmetrically clamped by the DE membranes, which are configured to tilt the axis to either side based on the activated voltage. The design is particularly well-suited for demanding soft material applications that require consistent, adaptable joint performance and the flexibility to integrate with various structural configurations.
3 Modeling and analysis of bistable dielectric elastomer
In the following, the bistable DE actuator shown in Figure 1 is analyzed, and a dynamic model is derived. The figure visualizes the geometric dimensions and material parameters of the system. The modeling approach presented in (Masoud and Maas, 2023) is applied here. In the first step, the kinematic deformation of the DEs are introduced. Subsequently, the energy and virtual work terms for the DE actuators and the beam element are formulated, taking into account the mechanical and electrical behavior of the model. The dynamics of the electrical behavior are neglected in this paper. The Rayleigh-Ritz approximation is employed to describe the deformation of the beam, incorporating various boundary conditions and defining the generalized coordinates. Finally, the Hamiltonian principle is applied to the electromechanical system, resulting in a nonlinear system of differential equations. This system can be conveniently transformed into a state-space model for further analysis. Geometric nonlinearities are considered to accurately describe the unstable buckling behavior of the beam element, which leads to multiple equilibrium solutions. These solutions are a characteristic feature of the actuator concept and play a crucial role in its bistable performance.
3.1 Deformation of the DEs
To describe the deformation of the DE system in the deformed state, the geometric quantities depicted in Figure 1 are introduced. These quantities are used to calculate the kinematics of the actuators and the forces acting on them as a result of the deformation. The deformation of the DE actuator is described by the pitch angle
where
The displacement
represents the deflection at the position
where
where
where
3.2 Energy function and virtual work of the bistable DE system
To investigate the dynamic behavior of the bistable DE system, the Lagrangian function is derived:
It includes the kinetic energy
3.2.1 Kinetic energy
The kinetic energy
Here,
3.2.2 Strain energy of the beam and potential energy of the mass
The strain energy of the beam represents the elastic energy stored in the material due to deformations. It is formulated as a function of the displacement
Here, the first term represents the energy due to bending stress, while the second term corresponds to the contribution from axial strain.
where
3.2.3 Free energy of the DE actuators
The free energy of the two DE actuators
Here,
3.2.4 Mechanical virtual work
The mechanical virtual work
where
The introduced energy and work terms form the basis for modeling the bistable DE system. This framework enables the analysis of the system’s static and dynamic behavior as well as its electromechanical coupling. To describe the system, the displacement
However, since
3.3 Analysis of the bistable DE system
The geometric and material parameters used for this investigation are provided in Table 1.
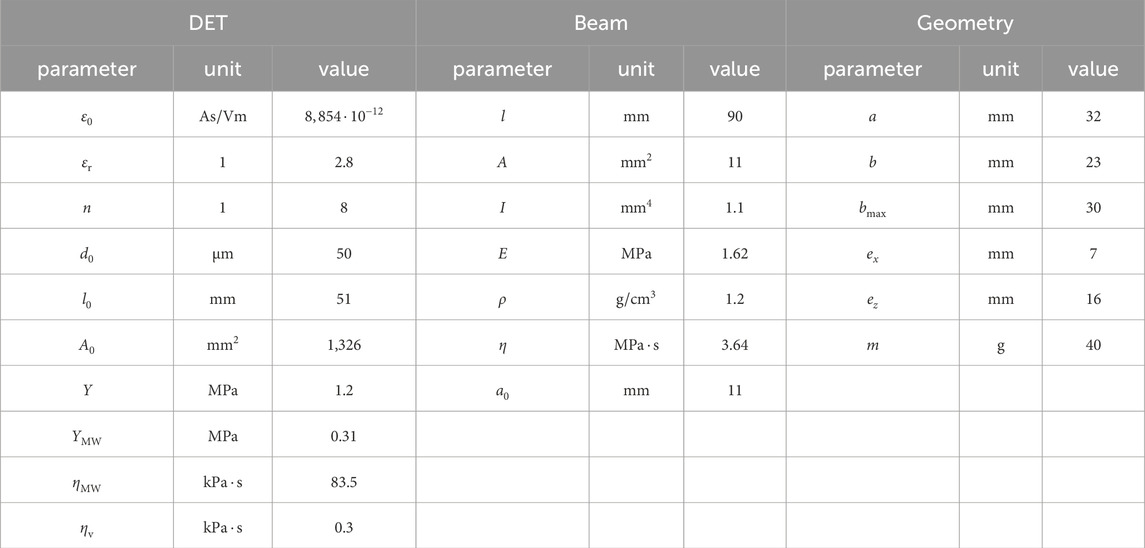
Table 1. Geometry and material parameters of the bistable DE soft robot joint under investigation for model-based analyses.
The material parameters of the DE actuators (Neo-Hookean model with
Regarding the beam material, the elastic modulus
Therefore, the parameters
The static behavior of the bistable DE system is analyzed by focusing on the total potential energy of the DE system, dependent on deformation
3.3.1 Polynomial ritz approximation
To calculate the static deformation of the DE beam actuator, a fourth-order polynomial Ritz approximation is employed:
This approximation satisfies the boundary conditions and is chosen based on a balance between accuracy and model simplicity. Lower-order polynomials
3.3.2 Energy formulation using the Hamilton principle
The Hamilton principle is applied to the static electromechanical DE beam structure. The total potential energy of the system is expressed as:
considering Equations 9–11. substituting the Ritz approximation (Equation 13) into the total energy (Equation 14) and applying the principle of stationary energy, the equilibrium equations with respect to the generalized coordinates
3.3.3 Influence of pre-strain on actuation behavior
The influence of pre-strain on the actuation behavior is analyzed by adjusting the geometric parameter
The results are presented in Figure 3, where the x-axis represents the maximum displacement:
and the y-axis denotes the displacement parameter
For
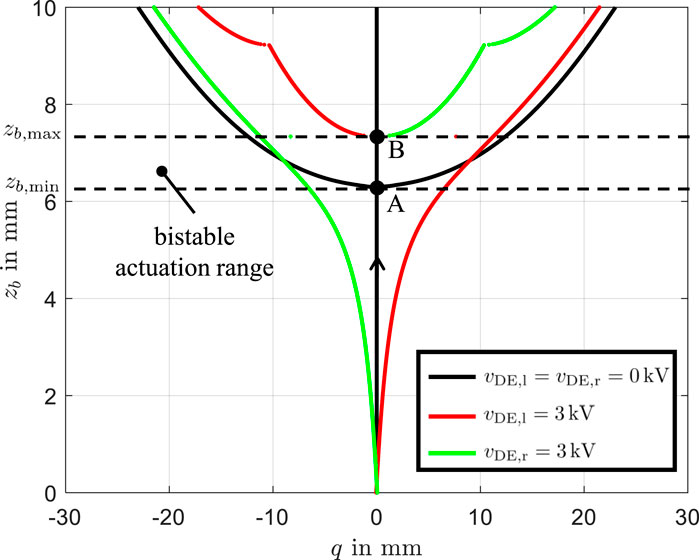
Figure 3. Equilibrium states of the DE-actuator system as a function of the position
When a voltage of
3.3.4 Force-displacement characteristic
The force-displacement relationship of the bistable beam actuator in the direction of
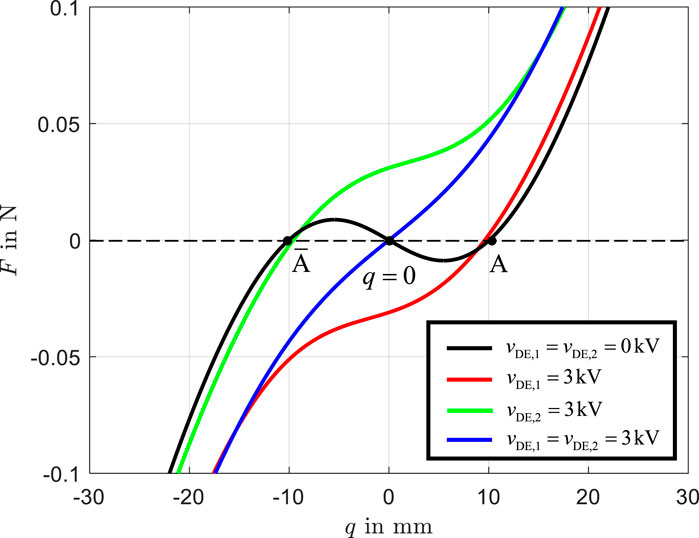
Figure 4. Force-displacement characteristic
Using Equation 15, the system is solved for
The black curve illustrates the unactuated state, where the actuator exhibits two stable equilibrium positions at
3.3.5 Evaluation of the capacitance-displacement relationship
The capacitance-displacement characteristics,
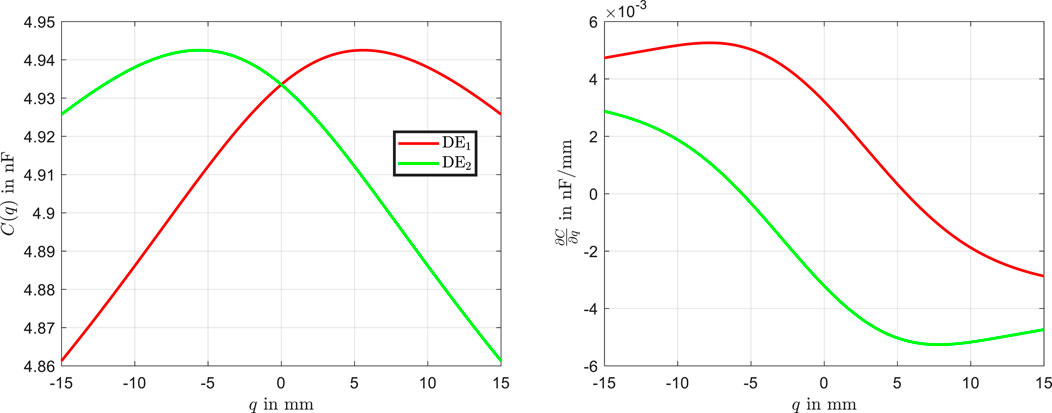
Figure 5. Capacitance-displacement characteristics of the left and right DE actuators, along with their derivatives with respect to
The electromechanical force
where
From Figure 5, it is evident that the derivative of the capacitance for the left actuator is predominantly positive. This results in a net force in the positive
The characteristic curves offer an intuitive way to understand the physical behavior of the bistable DE actuator. They serve as a basis for explaining the system’s force generation and equilibrium transitions. Additionally, these insights are critical for comprehending the actuator’s dynamic behavior, which will be explored in the following section. By analyzing these characteristics, simplifications can be introduced to model the dynamic behavior more effectively, ensuring a better understanding of the actuator’s performance under varying operating conditions.
3.4 Data-based reduced order state space model
The dynamic behavior of the bistable DE actuator can be described analogously to the approach in (Masoud and Maas, 2023) neglecting the electrical equations. The governing equation is expressed as:
considering Equations 7–12. Using the state variables:
the system can be transformed into the state-space form:
where
and
When the focus is on motion in a measurable direction
To analyze the system’s eigenmodes, simulation data from the model defined in Equation 21 were evaluated using singular value decomposition (SVD). The system was excited using the input signals shown in Figure 7, where the left actuator was activated first, followed by the right. The resulting beam dynamics were simulated accordingly. Figure 6a presents the identified mode shapes. The model response (black dashed line) closely matches the first mode shape (red line), while the second and third modes are nearly negligible. The right figure illustrates the mode shapes during transient oscillation. Here, the second and third modes exhibit significantly lower amplitudes compared to the dominant first mode, indicating that the transient dynamics are primarily governed by the first eigenmode. A slight deviation between the model and the first mode is observed under dynamic conditions. Overall, the analysis demonstrates that the bistable DE actuator’s behavior can be accurately captured by the first eigenmode alone, which supports the validity of reducing the model to a single generalized coordinate
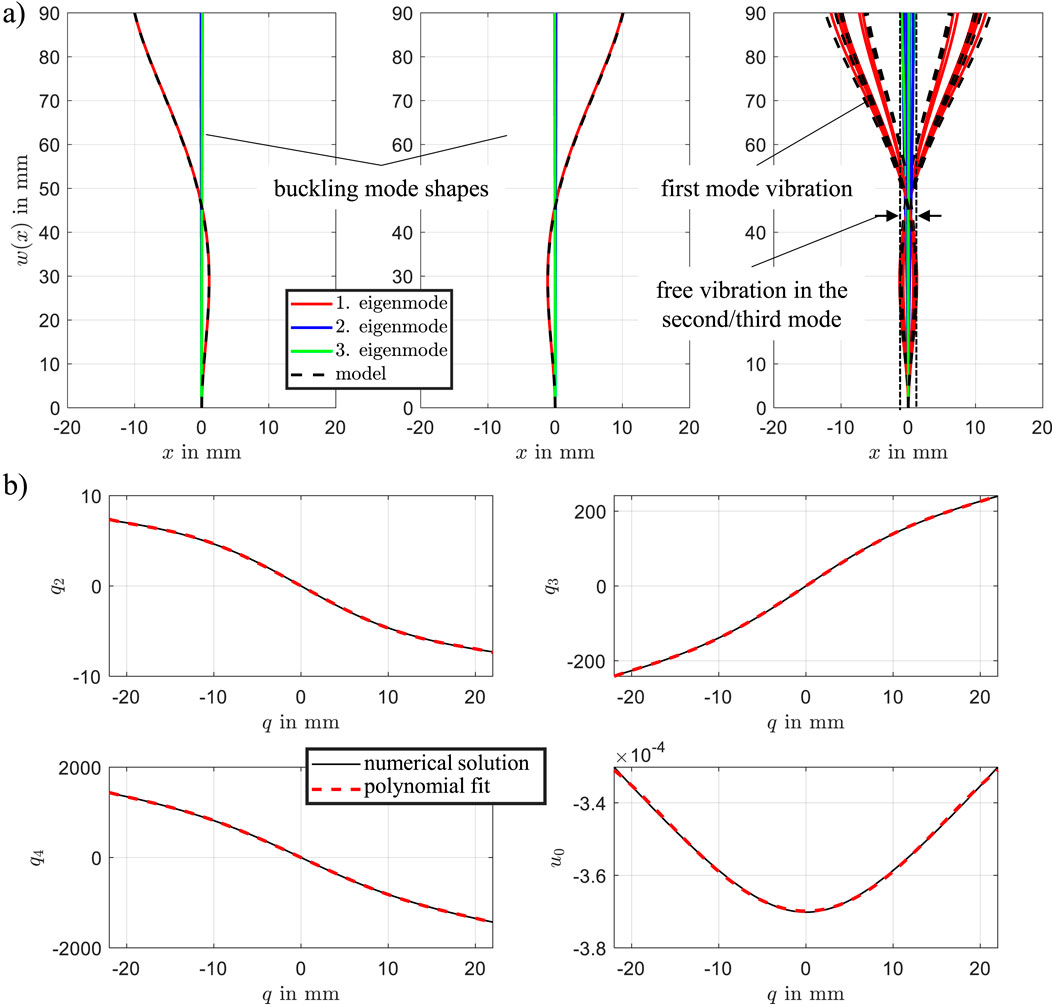
Figure 6. (a) Identified mode shapes of the beam during vibration. (b) State vector
The reduction of the system model is achieved by using the equilibrium solutions of the static model. The state vector
The static solutions depicted in Figure 6b are approximated using polynomial functions. This fitting enables the derivation of an analytical expression for
By substituting Equation 24 into the approximation
the Hamilton principle is then applied based on the measurable generalized coordinate
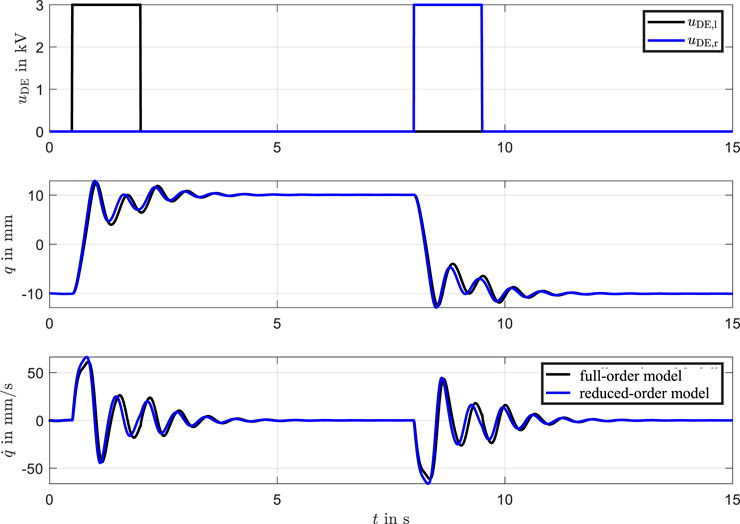
Figure 7. Comparison of simulations between the full-order and reduced-order models. The alignment confirms the reduced model’s accuracy in capturing key dynamics.
4 Data-driven modeling using RBF-Networks
Once the bistable DE has been designed and is available for further control, the mathematical model can alternatively be identified through experimental data aimed at accurately representing real-world behavior. The model presented in the previous section was used to design the actuator and perform analytical investigations and simulations to gain a better understanding of its behavior. However, in real-world implementations, deviations from the model can arise due to several factors. These include undetermined geometric asymmetries in the setup, such as imperfectly symmetric bearings, and unmodeled friction effects, such as hysteresis and dynamic friction, which are difficult to predict. These discrepancies necessitate significant post-experimental effort to adjust the model parameters, such as accounting for asymmetries in the geometry and fine-tuning the viscous parameters, in order to match the actual measurement data as closely as possible.
To address these challenges with comparably little effort, the model will be refined using experimental data and enhanced with RBF neural networks. This will allow for a more accurate representation of the actuator’s real-world performance. A generalized dynamic friction model will be incorporated to better account for the nonlinear and time-dependent frictional forces. Specifically, the viscous losses composed of the beam and DE previously described in the equations will be replaced with a generalized Maxwell-slip model (Al-Bender et al., 2005). This simple adjustment will improve the model’s ability to capture the complex friction dynamics and enhance its predictive accuracy.
The Hamiltonian principle is applied to the measurable coordinates
where the kinetic energy
The elastic energy of the beam and the hyperelastic behavior of the DEs are collectively represented by the potential energy of a nonlinear spring element
This potential energy function encompasses both the mechanical strain energy of the beam and the nonlinear hyperelastic properties characteristic of DE materials, effectively unifying them within a single expression. The electrical energy stored in the left and right DE actuator can be represented using the energy expression for a deformable capacitor. In this approach, each DE actuator is modeled as a capacitor whose capacitance changes with deformation. This variable capacitance effectively captures the energy dynamics as the actuator undergoes shape changes. The electrical co-energy for each DE actuator
For the derivation of the dynamic equations, co-energy is utilized since the voltages are directly measurable. To account for additional hysteresis effects and dynamic friction forces, observed in experimental laboratory tests, the model is expanded in accordance with (Al-Bender et al., 2005). Thus a generalized dynamic friction model is introduced, and an internal state equation is considered:
Following the principles of the Lagrange formalism, the differential equations can be derived:
This leads to the following equation:
Using the model in Equation 33, the nonlinear system can be experimentally identified by utilizing the measured quantities
4.1 Radial basis function network
One approach to identify the nonlinearities in Equation 33 is to use radial basis functions, as illustrated in Figure 8a.
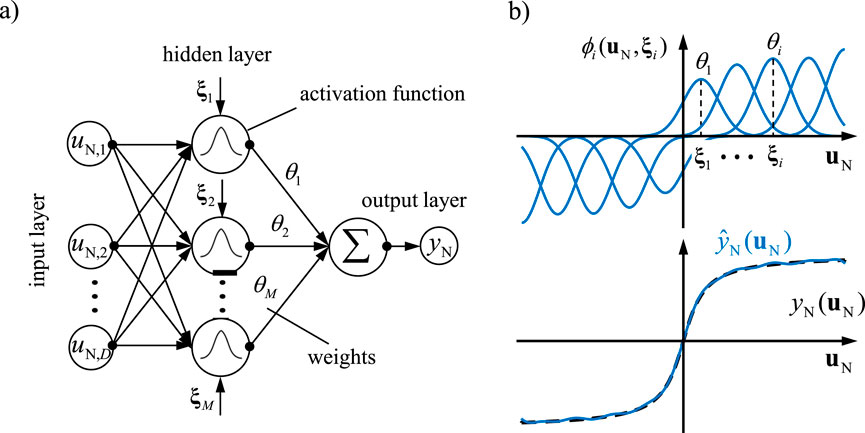
Figure 8. Radial basis function (RBF) network: (a) structure of the RBF network, (b) example of function approximation.
The RBF network consists of a hidden layer that contains neurons. The activation function of each neuron (radial basis functions
where
The variance
The basis functions transforms the
An important feature of the RBF network is that it is nonlinear with respect to the input variables but linear with respect to the parameters. This property is especially advantageous for online parameter identification, as the linear dependency on the parameters allows for efficient real-time computation and adjustment. This means that the weights, which represent the network’s variable parameters, can be optimized in real-time using techniques such as the least squares method or gradient methods without requiring an extensive, computationally intensive optimization of the entire model structure.
This separation of nonlinearity in the input variables from linearity in the parameters also facilitates the stability and convergence of model adaptation. In practice, this property leads to improved adaptability of the RBF network, making it especially suitable for applications that demand dynamic and rapid adjustment to changing input data, such as in nonlinear dynamical models and nonlinear system control.
The radial basis function (RBF) network was selected due to its simple and interpretable structure, as well as the advantageous property that its parameters enter the model linearly. This linearity allows the identification problem to be formulated as a convex optimization task with a unique solution. In the presented approach, the RBF network is embedded within a physics-based model framework and serves to approximate nonlinearities arising from uncertainties or simplifications in the physical description. Since the dominant system dynamics are already represented by the physics-based component, the RBF network acts purely as a corrective term and does not need to reconstruct the full dynamics from data.
Alternative neural network architectures such as Long Short-Term Memory (LSTM) or Gated Recurrent Units (GRU) are more suitable for black-box modeling scenarios, where system dynamics are learned implicitly through internal memory mechanisms and time-delayed inputs. These models are inherently more complex, demand significantly more training data, and involve nonlinear optimization processes that are sensitive to initialization and may result in multiple local minima. Moreover, the integration of such recurrent structures into a physics-informed framework would necessitate a discrete-time formulation of the governing equations, which complicates both model development and training. In contrast, the use of RBF networks provides a transparent and efficient means of enhancing model accuracy while maintaining a strong connection to the underlying physical principles.
4.2 Dynamic identification of bistable DE system using physics-informed RBF network
The physical model should be as grounded in fundamental physical laws as possible while still utilizing neural networks to generalize any unknown functions effectively. This approach reduces the demand for extensive training data, striking a balance between the incorporation of physics-based structure and the amount of data required for neural network training. Achieving this compromise allows for accurate model identification with limited data, optimizing both computational efficiency and model accuracy.
Two approaches can be employed for identifying the nonlinear model in Equation 33. The first approach involves measuring characteristic curves with external integrated sensors and using neural networks to identify the unknown dynamic friction. Thus, a force sensor can be used to determine the force component
The second proposed approach involves predefining the structure of dynamic friction and representing all unknown functions using simple neural networks that are linear in the unknown parameters. To simplify the structure of dynamic friction, it is suggested in (De Wit et al., 1995; Dankowicz, 1999) to represent the state equation
The nonlinear functions
where
where
The incorporation of fundamental physical principles allows the model to accurately represent key system characteristics, reducing the need for large data sets to train the neural network while enhancing generalizability. The RBF functions provide a flexible approach for modeling unknown nonlinear relationships within the system without extensive data requirements. This results in an efficient model structure that combines physics-based insights with data-driven optimization to enable reliable predictions of the DE dynamic responses.
Additionally, the figure illustrates the parameterization of individual components, including the weighting parameters
The identification problem of the nonlinear system can be transformed into a linear regression problem using the RBF network, as the unknown parameters to be identified enter linearly, with the nonlinearities contained within the measurement vector. Here, the inertial force
The model parameters
5 Experimental validation
5.1 Experimental setup for identification and validation
The experimental setup for the characterization and validation of the bistable DE system is illustrated in Figure 10. The setup comprises the physical assembly of the bistable DE actuator, the electronic drive circuitry, a laser sensor, and the dSPACE real-time platform.
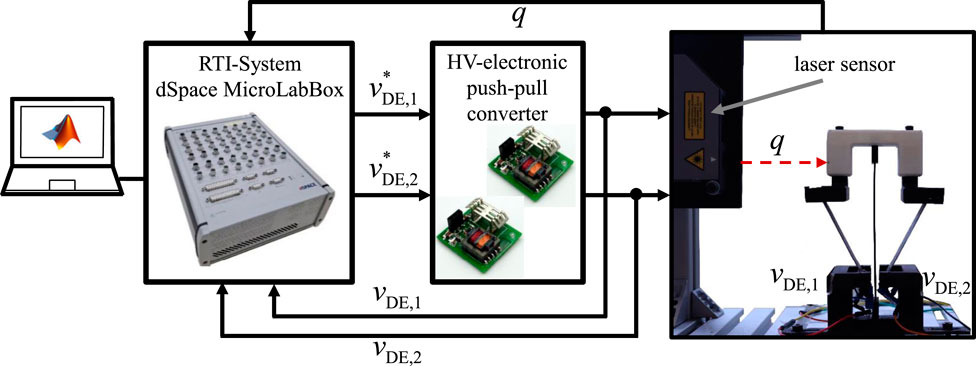
Figure 10. Experimental setup and hardware-in-the-loop system for the identification and validation of the bistable DE system.
The pre-tension applied via screws serves a dual purpose: it must exceed the critical buckling load of the beam to maintain structural stability, yet it should not surpass a threshold beyond which the DE actuators cannot move the system between its two stable states. For the experiments, an operating point of
The horizontal displacement
The electrical actuation system employs two high-voltage (HV) drive circuits configured as push-pull converters, as described in (Junglas et al., 2022). These converters are HV DC-DC systems specifically designed for capacitive loads in the range of tens of nanofarads. Each converter can deliver a maximum voltage of
The programs are implemented in MATLAB and Simulink and compiled for execution on a MicroLabBox from dSPACE. This platform interfaces with both the drive electronics and sensors while providing a real-time data acquisition interface. It also allows on-the-fly modification of parameters such as setpoints and filter constants.
Figure 11a displays the position, velocity, and acceleration profiles, along with the measured excitation voltages
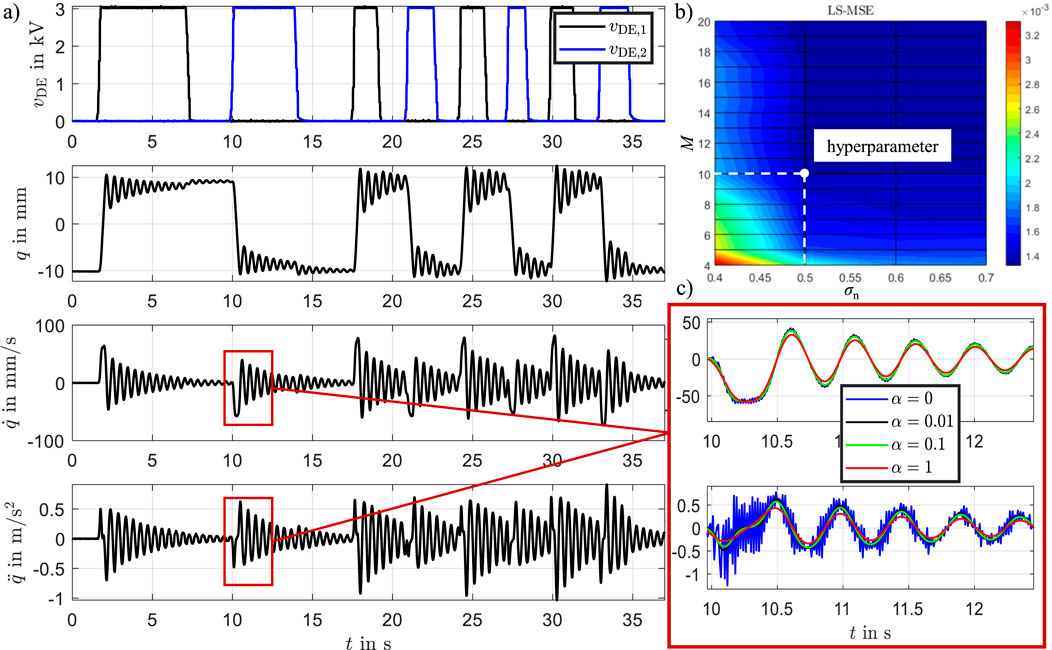
Figure 11. (a) Measurement data: position, velocity, and acceleration profiles, along with the measured excitation voltages applied to the bistable DE system, (b) sensitivity study of the mean squared error (MSE) with respect to the hyperparameters
To calculate the time derivatives of the measured signals in a robust manner, we applied the total variation regularized differentiation algorithm (TVRegDiff). The regularization parameter was set to
The bistable behavior of the DE system is evident in the measurements. Starting from an initial position near
5.2 Results
The generated measurement data from Figure 11 were used to determine the parameters
The results are presented in Figure 12, comparing the measured position with the analytical model and the RBF-based model. The comparison includes position, velocity, and acceleration as well as the pitch angel
For the following evaluation of the overall modeling, the statistical error measure normalized root mean squared error (NRMSE) was selected:
Here,
The RBF-based model achieves a significantly lower NRMSE across all tested scenarios, particularly in the transient regime and during oscillatory behavior. This confirms that augmenting the analytical model with a data-driven RBF correction improves the model’s capability to capture nonlinearities and dynamic effects that are not fully represented in the analytical formulation.
A zoomed-in view of the data for the time interval between 24 and 30 s is shown in Figure 13, highlighting the dynamic differences between the models. Overall, the trained RBF network demonstrates excellent agreement with the experimental results.
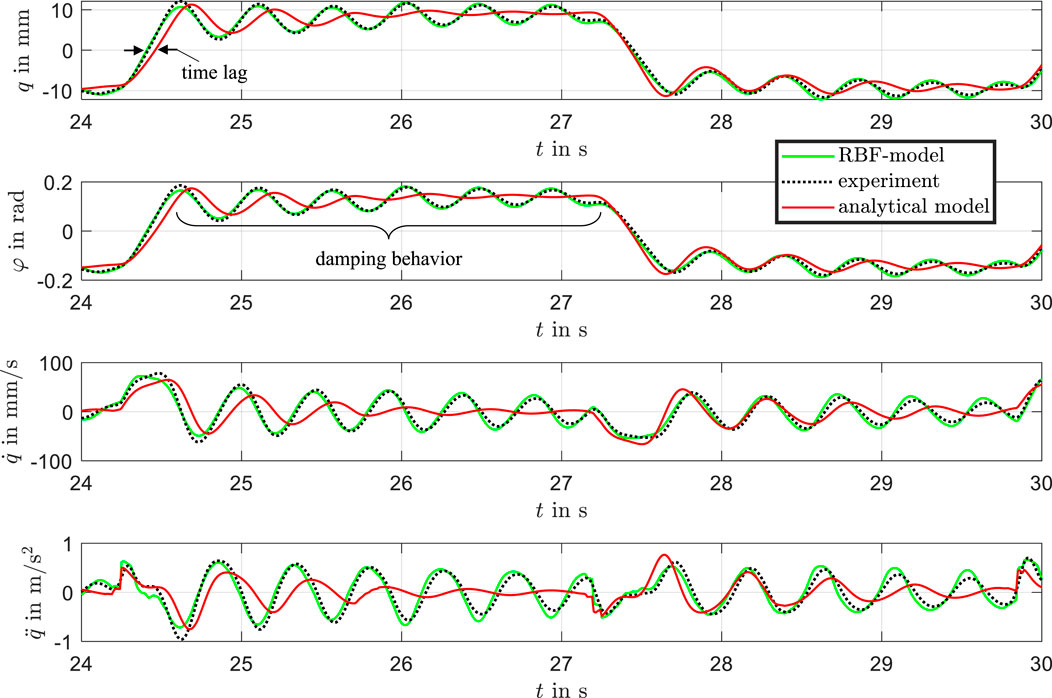
Figure 13. Zoomed-in comparison of measured data, analytical model, and RBF model in the time window from 24 to 30 s, highlighting differences in transient behavior.
While the analytical model captures the experimental data reasonably well and reproduces the static behavior effectively, it struggles to accurately represent the transient behavior during the settling process. This limitation stems from imprecise parameterization of the viscous effects and the presence of plastic effects in the beam material. For the analytical model, new parameters would need to be defined and optimized through a labor-intensive process for each actuator to improve accuracy. The analytical model exhibits a noticeable time lag and a stronger damping effect, which leads to an underestimation of overshoot and a failure to reproduce the oscillatory characteristics observed in the experimental data during fast input transitions. In contrast, the physics-informed RBF model closely matches the measured response, accurately capturing overshoot, phase delay, and the amplitude of oscillations. This improved performance demonstrates the capability of the RBF-model to represent complex nonlinear and transient dynamics that are not sufficiently captured by the analytical model. These findings support the hybrid modeling approach as an effective method for improving predictive accuracy in highly dynamic regimes.
Interestingly, the identification process using the RBF network allows for the direct derivation of the physical characteristic curves, as shown in Figure 14. The analytical characteristic curves (black lines) are compared with the RBF-based curves (red and green lines).
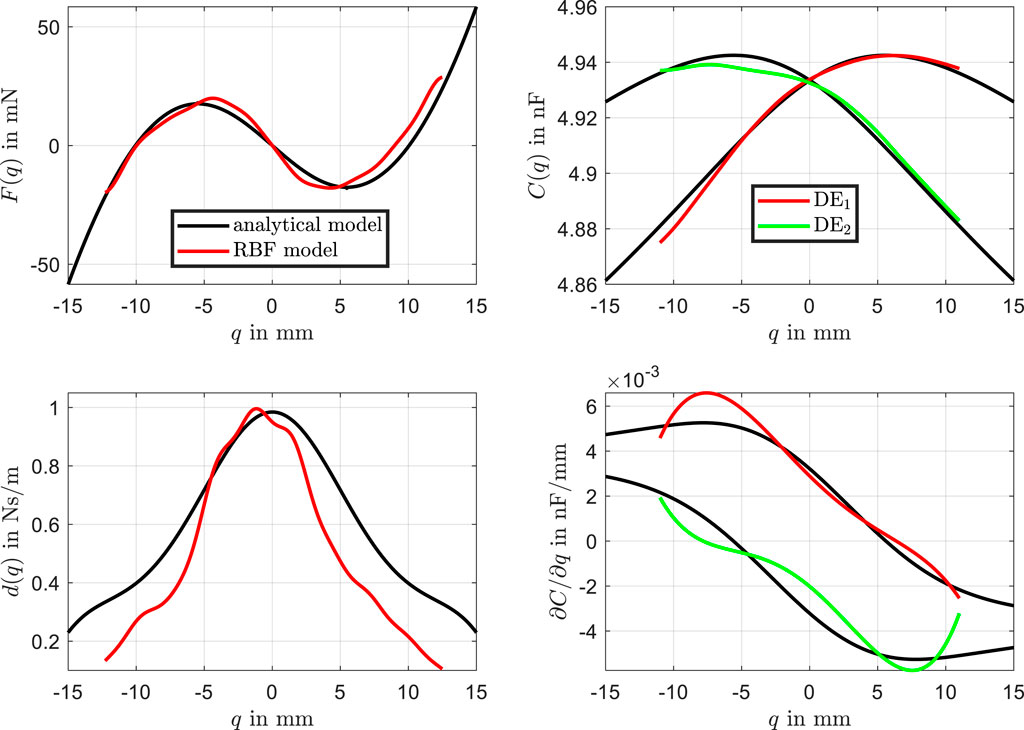
Figure 14. Physical characteristic curves. Comparison between the analytical curves (black lines) and the RBF-based curves (red and green lines for
The RBF network captures the force characteristic curve with high accuracy, showing minimal deviation from the analytical model. The RBF-based curves for the two dielectric elastomer layers also align closely with the analytical model, demonstrating good agreement across the entire range. The most significant discrepancy is observed in the damping characteristic curve. This is where the model uncertainties, particularly related to dynamic and viscous effects of the beam, are most pronounced. This is due to the fact that the beam was modeled using a linear damping behavior, which is insufficient to improve modeling quality. One potential approach to enhance accuracy would be to explore alternative dynamic friction models for the beam and integrate them into the analytical model, which would likely yield more accurate results. However, this would involve a substantial modeling effort and would still not address other sources of inaccuracies and uncertainties.
Small asymmetries in the force and capacitance curves are evident, which are effectively captured by the RBF model but are absent in the analytical model. The comparison of the derived characteristic curves also includes the derivative of the capacitance
The obtained results highlights the ability of the RBF network to follow the experimental data precisely, including dynamic transitions. These underscore the flexibility and accuracy of the RBF network, particularly in capturing nonlinearities and asymmetries that are not accounted for in the analytical model.
The cross-validation results, as shown in Figure 15, demonstrate how the models respond to new measurement data not used in the identification process. This validation is critical for assessing the generalizability and robustness of both the analytical model and the RBF-based model.
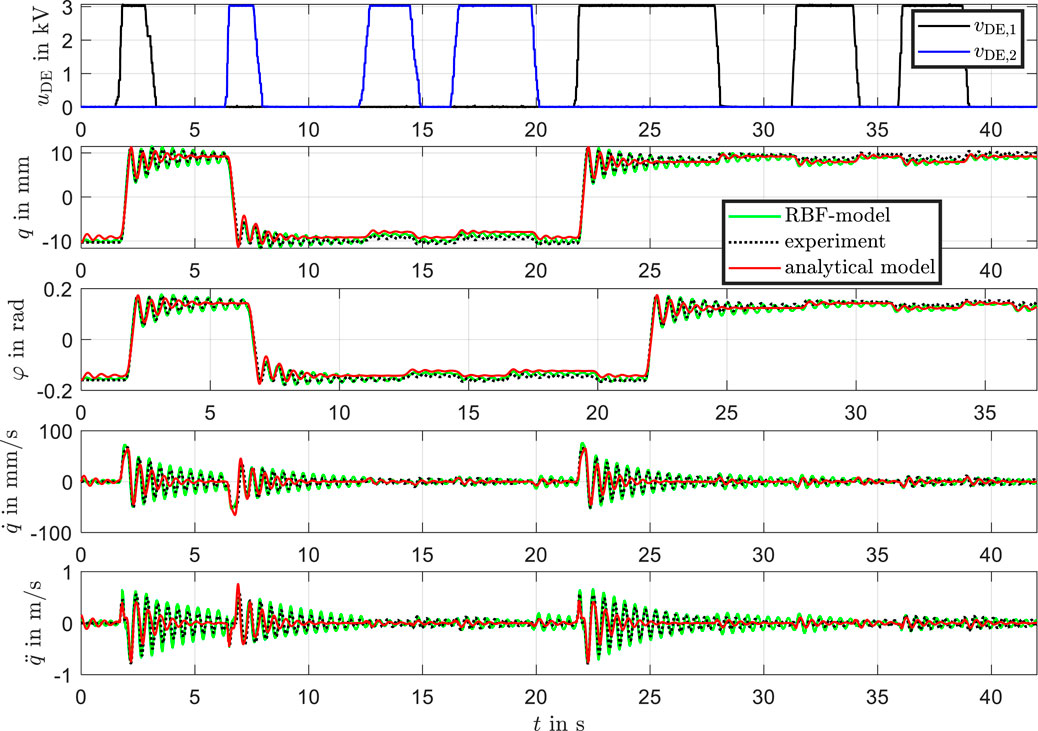
Figure 15. Cross-validation of measurement data, analytical model, and RBF model. Comparison of model predictions with new measurement data not used in the identification process.
The results from the cross-validation, as depicted in the figure, closely resemble the trends observed in Figure 12. The RBF model exhibits excellent agreement with the experimental data across all tested variables, including position, velocity, and acceleration. The analytical model continues to capture the general trends well, particularly in steady-state behavior, but shows limitations in transient dynamics.
The RBF network model demonstrates excellent generalizability by accurately predicting system behavior for previously unseen data. This robustness validates the model’s applicability to new conditions without requiring extensive reparameterization.
The main intention of our work was not to compare the RBF model with the best possible analytical model but rather to demonstrate a systematic approach for deriving a dynamic model for complex DE systems by combining physics-based approaches with the useful extension of data-driven models in order to better capture inaccuracies and uncertainties with comparatively little effort. In the analytical model a perfectly symmetrical configuration was assumed with identical parameters for the DE actuators. Of course, the model could be modified and refined to match the experimental results more closely. To achieve this, it would be necessary to not only adjust the parameters describing the material behavior of the DE material and the beam but also to account for geometric asymmetries.
The entirety of all parameters could then be adjusted using an optimizer by minimizing the sum of squared errors. Since this problem represents a nonlinear optimization problem with multiple parameters, it is well known that multiple local minima may exist, and there is no guarantee that a global minimum can be reached. Overall, these steps lead to a highly complex and time-consuming process of model improvement and optimization.
To simplify the parameterization of the model for new actuator prototypes in systems and control engineering applications, the RBF model was introduced. The complex analytical modeling process could be replaced by a simple model based on RBF networks, which are easier to parameterize since the unknown parameters enter linearly. Consequently, the resulting optimization problem is a simple convex problem for which a unique global minimum always exists.
While the proposed RBF model offers notable advantages in terms of accuracy and interpretability, it also faces inherent limitations. A central challenge is its limited scalability in high-dimensional or strongly nonlinear input spaces. As the input dimensionality increases or the system exhibits complex nonlinear behavior such as sharp gradients, discontinuities, or abrupt transitions in behavior, the number of required basis functions can grow rapidly, resulting in a significantly enlarged parameter space and substantial computational effort. This phenomenon, often referred to as the curse of dimensionality, may hinder the model’s efficiency and generalizability in more complex scenarios.
Another important aspect is the need for sufficient excitation of all relevant dynamic modes during the identification phase. The model is only capable of capturing physical behaviors that are adequately stimulated in the training data. Consequently, its predictive performance is restricted to the domain spanned by the experimental input signals. Extrapolation beyond this range may lead to significant inaccuracies due to the inherently local approximation properties of RBF networks. However, by carefully designing the excitation signals during experiments, it is possible to ensure that the system operates within the trained domain during subsequent use, thereby avoiding the need for extrapolation.
The risk of overfitting must also be taken into account. A large number of basis functions or excessive overlap (e.g.,
The performance of the RBF-enhanced model depends on the careful selection of hyperparameters such as the number and width of basis functions. These must be chosen to balance model accuracy with generalization capability.
6 Conclusion
This work successfully demonstrates the development and implementation of a hybrid modeling framework for a bistable dielectric elastomer (DE) actuator system, combining physics-based analytical methods with radial basis function (RBF) neural networks. The proposed bistable DE actuator is analyzed in terms of its mechanical configuration and bistable characteristics. A physics-based modeling approach is employed to capture the key features of the actuator, leading to the derivation of a reduced-order model based on analytical considerations. To improve the accuracy and to achieve generalizability of the model, a hybrid approach is introduced, integrating physics-informed structures with data-driven methodologies. The model is enhanced by incorporating experimental data and RBF neural networks.
While the analytical model performs well for design purposes and captures general characteristics, it requires significant parameter tuning for each physical actuator prototype. In contrast, the RBF-based model can easily adapt to uncertainties in assembly, making it more flexible and efficient. The proposed approach effectively addresses challenges posed by nonlinearities and unmodeled dynamics, ensuring a highly accurate representation of the system’s performance. Experimental results confirm the model’s capability to capture both static and dynamic behaviors, including transient responses and bistable switching, with high fidelity. By combining physical principles with data-driven methods, the model achieves improved accuracy and generalizability, while reducing the necessity on extensive datasets. Future research will aim to use the proposed model for the development of a model-based controller specifically tailored to the bistable dielectric elastomer actuator, enhancing its performance and control accuracy.
Data availability statement
The raw data supporting the conclusions of this article will be made available by the authors, without undue reservation.
Author contributions
AM: Formal Analysis, Methodology, Validation, Visualization, Writing – original draft. JM: Formal Analysis, Methodology, Validation, Visualization, Writing – original draft.
Funding
The author(s) declare that financial support was received for the research and/or publication of this article. We acknowledge support by the Open Access Publication Fund of TU Berlin.
Conflict of interest
The authors declare that the research was conducted in the absence of any commercial or financial relationships that could be construed as a potential conflict of interest.
Generative AI statement
The author(s) declare that no Generative AI was used in the creation of this manuscript.
Publisher’s note
All claims expressed in this article are solely those of the authors and do not necessarily represent those of their affiliated organizations, or those of the publisher, the editors and the reviewers. Any product that may be evaluated in this article, or claim that may be made by its manufacturer, is not guaranteed or endorsed by the publisher.
References
Al-Bender, F., Lampaert, V., and Swevers, J. (2005). The generalized maxwell-slip model: a novel model for friction simulation and compensation. IEEE Trans. automatic control 50, 1883–1887. doi:10.1109/tac.2005.858676
Baltes, M., Kunze, J., Prechtl, J., Seelecke, S., and Rizzello, G. (2022). A bi-stable soft robotic bendable module driven by silicone dielectric elastomer actuators: design, characterization, and parameter study. Smart Mater. Struct. 31, 114002. doi:10.1088/1361-665x/ac96df
Cabuk, O., and Maas, J. (2021). Investigation of a deposition method for the application of electrode layers for dielectric elastomer transducers. Electroact. Polym. Actuators Devices (EAPAD) XXIII (SPIE) 11587, 265–274.
Cao, C., Hill, T. L., Li, B., Wang, L., and Gao, X. (2021). Nonlinear dynamics of a conical dielectric elastomer oscillator with switchable mono to bi-stability. Int. J. Solids Struct. 221, 18–30. doi:10.1016/j.ijsolstr.2020.02.012
Cao, Y., Derakhshani, M., Fang, Y., Huang, G., and Cao, C. (2021). Bistable structures for advanced functional systems. Adv. Funct. Mater. 31, 2106231. doi:10.1002/adfm.202106231
Carpi, F., Anderson, I., Bauer, S., Frediani, G., Gallone, G., Gei, M., et al. (2015). Standards for dielectric elastomer transducers. Smart Mater. Struct. 24, 105025. doi:10.1088/0964-1726/24/10/105025
Chartrand, R. (2011). Numerical differentiation of noisy, nonsmooth data. Int. Sch. Res. Notices 2011, 1–11. doi:10.5402/2011/164564
Chen, Y., Zhao, H., Mao, J., Chirarattananon, P., Helbling, E. F., Hyun, N.-S. P., et al. (2019). Controlled flight of a microrobot powered by soft artificial muscles. Nature 575, 324–329. doi:10.1038/s41586-019-1737-7
Chen, Z., Renda, F., Le Gall, A., Mocellin, L., Bernabei, M., Dangel, T., et al. (2024). Data-driven methods applied to soft robot modeling and control: a review. IEEE Trans. Automation Sci. Eng. 22, 2241–2256. doi:10.1109/tase.2024.3377291
Chi, Y., Li, Y., Zhao, Y., Hong, Y., Tang, Y., and Yin, J. (2022). Bistable and multistable actuators for soft robots: structures, materials, and functionalities. Adv. Mater. 34, 2110384. doi:10.1002/adma.202110384
Dankowicz, H. (1999). On the modeling of dynamic friction phenomena. ZAMM-Journal Appl. Math. Mechanics/Zeitschrift für Angewandte Math. und Mech. Appl. Math. Mech. 79, 399–409. doi:10.1002/(sici)1521-4001(199906)79:6<399::aid-zamm399>3.0.co;2-k
Demuth, H. B., Beale, M. H., De Jess, O., and Hagan, M. T. (2014). Neural network design (martin hagan).
De Wit, C. C., Olsson, H., Astrom, K. J., and Lischinsky, P. (1995). A new model for control of systems with friction. IEEE Trans. automatic control 40, 419–425. doi:10.1109/9.376053
Duduta, M., Hajiesmaili, E., Zhao, H., Wood, R. J., and Clarke, D. R. (2019). Realizing the potential of dielectric elastomer artificial muscles. Proc. Natl. Acad. Sci. 116, 2476–2481. doi:10.1073/pnas.1815053116
Eckerle, J., Stanford, S., Marlow, J., Schmidt, R., Oh, S., Low, T., et al. (2001). Biologically inspired hexapedal robot using field-effect electroactive elastomer artificial muscles. Smart Struct. Mater. 2001 Industrial Commer. Appl. smart Struct. Technol. (SPIE) 4332, 269–280. doi:10.1117/12.429666
Follador, M., Cianchetti, M., and Mazzolai, B. (2015a). Design of a compact bistable mechanism based on dielectric elastomer actuators. Meccanica 50, 2741–2749. doi:10.1007/s11012-015-0212-2
Follador, M., Conn, A., and Rossiter, J. (2015b). Bistable minimum energy structures (bimes) for binary robotics. Smart Mater. Struct. 24, 065037. doi:10.1088/0964-1726/24/6/065037
Guo, Y., Liu, L., Liu, Y., and Leng, J. (2021). Review of dielectric elastomer actuators and their applications in soft robots. Adv. Intell. Syst. 3, 2000282. doi:10.1002/aisy.202000282
Hackl, C. M., Tang, H.-Y., Lorenz, R. D., Turng, L.-S., and Schroder, D. (2005). A multidomain model of planar electro-active polymer actuators. IEEE Trans. industry Appl. 41, 1142–1148. doi:10.1109/tia.2005.853384
Hansy-Staudigl, E., Krommer, M., and Humer, A. (2019). A complete direct approach to nonlinear modeling of dielectric elastomer plates. Acta Mech. 230, 3923–3943. doi:10.1007/s00707-019-02529-1
Harne, R. L., and Wang, K. (2013). A review of the recent research on vibration energy harvesting via bistable systems. Smart Mater. Struct. 22, 023001. doi:10.1088/0964-1726/22/2/023001
Hoffstadt, T., Koellnberger, A., and Maas, J. (2018). “Characterization of enhanced silicone materials for dielectric elastomer transducers,” in ACTUATOR 2018; 16th International Conference on New Actuators, Bremen, Germany, 25-27 June 2018 VDE, 1–4. Available online at: https://ieeexplore.ieee.org/document/8470795.
Hoffstadt, T., and Maas, J. (2015). Analytical modeling and optimization of deap-based multilayer stack-transducers. Smart Mater. Struct. 24, 094001. doi:10.1088/0964-1726/24/9/094001
Huang, P., Wu, J., Meng, Q., Wang, Y., and Su, C.-Y. (2023). Self-sensing motion control of dielectric elastomer actuator based on narx neural network and iterative learning control architecture. IEEE/ASME Trans. Mechatronics 29, 1374–1384. doi:10.1109/tmech.2023.3300364
Johnson, C. C., Quackenbush, T., Sorensen, T., Wingate, D., and Killpack, M. D. (2021). Using first principles for deep learning and model-based control of soft robots. Front. Robotics AI 8, 654398. doi:10.3389/frobt.2021.654398
Jones, R. W., and Sarban, R. (2012). Inverse grey-box model-based control of a dielectric elastomer actuator. Smart Mater. Struct. 21, 075019. doi:10.1088/0964-1726/21/7/075019
Junglas, S., Hubracht, A., and Maas, J. (2022). “Small and scalable high voltage push-pull converter for feeding dielectric elastomer transducers (det),” in ACTUATOR 2022; International Conference and Exhibition on New Actuator Systems and Applications, Mannheim, Germany, 29-30 June 2022 VDE, 1–4. Available online at: https://ieeexplore.ieee.org/document/9899195.
Kim, D., Kim, S.-H., Kim, T., Kang, B. B., Lee, M., Park, W., et al. (2021). Review of machine learning methods in soft robotics. Plos one 16, e0246102. doi:10.1371/journal.pone.0246102
Kofod, G., Wirges, W., Paajanen, M., and Bauer, S. (2007). Energy minimization for self-organized structure formation and actuation. Appl. Phys. Lett. 90. doi:10.1063/1.2695785
Kovacs, G., Lochmatter, P., and Wissler, M. (2007). An arm wrestling robot driven by dielectric elastomer actuators. Smart Mater. Struct. 16, S306–S317. doi:10.1088/0964-1726/16/2/s16
Krüger, T. S., Çabuk, O., and Maas, J. (2023). Manufacturing process for multilayer dielectric elastomer transducers based on sheet-to-sheet lamination and contactless electrode application. Actuators (MDPI) 12, 95. doi:10.3390/act12030095
Kuhring, S., Uhlenbusch, D., Hoffstadt, T., and Maas, J. (2015). Finite element analysis of multilayer deap stack-actuators. Electroact. Polym. Actuators Devices (EAPAD) 2015 (SPIE) 9430, 395–407.
Lau, G.-K., Lim, H.-T., Teo, J.-Y., and Chin, Y.-W. (2014). Lightweight mechanical amplifiers for rolled dielectric elastomer actuators and their integration with bio-inspired wing flappers. Smart Mater. Struct. 23, 025021. doi:10.1088/0964-1726/23/2/025021
Li, T., Keplinger, C., Baumgartner, R., Bauer, S., Yang, W., and Suo, Z. (2013). Giant voltage-induced deformation in dielectric elastomers near the verge of snap-through instability. J. Mech. Phys. Solids 61, 611–628. doi:10.1016/j.jmps.2012.09.006
Liu, J., Borja, P., and Della Santina, C. (2024). Physics-informed neural networks to model and control robots: a theoretical and experimental investigation. Adv. Intell. Syst. 6, 2300385. doi:10.1002/aisy.202300385
Masoud, A. E., Hubracht, A., Junglas, S., and Maas, J. (2021). “Flatness-based control for dielectric elastomer transducers,” in ACTUATOR; International Conference and Exhibition on New Actuator Systems and Applications 2021, 17-19 February 2021 VDE, 1–5. Available online at: https://ieeexplore.ieee.org/document/9400603.
Masoud, A. E., and Maas, J. (2023). Energy-based nonlinear dynamical modeling of dielectric elastomer transducer systems suspended by elastic structures. Acta Mech. 234, 239–260. doi:10.1007/s00707-022-03151-4
Melingui, A., Escande, C., Benoudjit, N., Merzouki, R., and Mbede, J. B. (2014). Qualitative approach for forward kinematic modeling of a compact bionic handling assistant trunk. IFAC Proc. Vol. 47, 9353–9358. doi:10.3182/20140824-6-za-1003.01758
Mertens, J., Masoud, A. E., Hubracht, A., Çabuk, O., Krüger, T. S., Maas, J., et al. (2024). Modeling and experimental investigation of multilayer de transducers considering the influence of the electrode layers. Smart Mater. Struct. 33, 095041. doi:10.1088/1361-665x/ad6798
Pelrine, R., Kornbluh, R., Pei, Q., and Joseph, J. (2000). High-Speed electrically actuated elastomers with strain greater than 100%. Science 287, 836–839. doi:10.1126/science.287.5454.836
Pelrine, R., Kornbluh, R. D., Pei, Q., Stanford, S., Oh, S., Eckerle, J., et al. (2002). Dielectric elastomer artificial muscle actuators: toward biomimetic motion. Smart Struct. Mater. 2002 Electroact. Polym. actuators devices (EAPAD) (SPIE) 4695, 126–137. doi:10.1117/12.475157
PETG (2023). Fillamentum addictive polymers. Available online at: https://fillamentum.com/collections/petg-filament/?utm_source.Fillamentumaddi(c)tivepolymers.
Popescu, M.-C., Balas, V. E., Perescu-Popescu, L., and Mastorakis, N. (2009). Multilayer perceptron and neural networks. WSEAS Trans. Circuits Syst. 8, 579–588. Available online at: https://www.wseas.us/e-library/transactions/circuits/2009/29-485.pdf.
Rizzello, G., Naso, D., Turchiano, B., and Seelecke, S. (2016). Robust position control of dielectric elastomer actuators based on lmi optimization. IEEE Trans. Control Syst. Technol. 24, 1909–1921. doi:10.1109/tcst.2016.2519839
Sarban, R., and Jones, R. W. (2012). Physical model-based active vibration control using a dielectric elastomer actuator. J. Intelligent Material Syst. Struct. 23, 473–483. doi:10.1177/1045389x11435430
Soleti, G., Prechtl, J., Massenio, P. R., Baltes, M., and Rizzello, G. (2023). Energy based control of a bi-stable and underactuated soft robotic system based on dielectric elastomer actuators. IFAC-PapersOnLine 56, 7796–7801. doi:10.1016/j.ifacol.2023.10.1153
Sun, W., Akashi, N., Kuniyoshi, Y., and Nakajima, K. (2022). Physics-informed recurrent neural networks for soft pneumatic actuators. IEEE Robotics Automation Lett. 7, 6862–6869. doi:10.1109/lra.2022.3178496
Suo, Z. (2010). Theory of dielectric elastomers. Acta Mech. Solida Sin. 23, 549–578. doi:10.1016/s0894-9166(11)60004-9
Wang, X., Dabrowski, J. J., Pinskier, J., Liow, L., Viswanathan, V., Scalzo, R., et al. (2024). Pinn-ray: a physics-informed neural network to model soft robotic fin ray fingers. arXiv preprint arXiv:2407.08222.
Wang, Y., Gupta, U., Parulekar, N., and Zhu, J. (2019). A soft gripper of fast speed and low energy consumption. Sci. China Technol. Sci. 62, 31–38. doi:10.1007/s11431-018-9358-2
Wang, Z., Fang, S., Feng, A., Wu, M., Lin, B., Shi, R., et al. (2024). Dynamic analysis of a dielectric elastomer–based bistable system. J. Sound Vib. 572, 118183. doi:10.1016/j.jsv.2023.118183
Wingert, A., Lichter, M. D., and Dubowsky, S. (2006). On the design of large degree-of-freedom digital mechatronic devices based on bistable dielectric elastomer actuators. IEEE/ASME Trans. mechatronics 11, 448–456. doi:10.1109/tmech.2006.878542
Wissler, M., and Mazza, E. (2005). Modeling and simulation of dielectric elastomer actuators. Smart Mater. Struct. 14, 1396–1402. doi:10.1088/0964-1726/14/6/032
Xiao, H., Guo, F., Li, Z., Liu, D., Liu, Y., Wang, Y., et al. (2023). “Adaptive inverse compensation output feedback control for dielectric elastomer actuator motion control system,” in 2023 6th International Conference on Intelligent Robotics and Control Engineering (IRCE), Jilin, China, 04-06 August 2023 IEEE, 1–6.
Xiao, H., Wu, J., Ye, W., and Wang, Y. (2020). “Dynamic modeling for dielectric elastomer actuators based on lstm deep neural network,” in 2020 5th international conference on advanced robotics and mechatronics (ICARM), Shenzhen, China, 18-21 December 2020 IEEE, 119–124.
Zhang, R., Lochmatter, P., Kunz, A., and Kovacs, G. M. (2006). Spring roll dielectric elastomer actuators for a portable force feedback glove. Smart Struct. Mater. 2006 Electroact. Polym. Actuators Devices (EAPAD) (SPIE) 6168, 505–516.
Keywords: bistable dielectric elastomer actuator, RBF network, dynamical and hybrid modeling, soft robot, smart structure
Citation: Masoud AE and Maas J (2025) Data-driven modeling and identification of a bistable soft-robot element based on dielectric elastomer. Front. Robot. AI 12:1546945. doi: 10.3389/frobt.2025.1546945
Received: 17 December 2024; Accepted: 26 June 2025;
Published: 17 July 2025.
Edited by:
Holger Voos, University of Luxembourg, LuxembourgReviewed by:
César M. A. Vasques, University of Aveiro, PortugalRaj Kumar Sahu, National Institute of Technology Raipur, India
Copyright © 2025 Masoud and Maas. This is an open-access article distributed under the terms of the Creative Commons Attribution License (CC BY). The use, distribution or reproduction in other forums is permitted, provided the original author(s) and the copyright owner(s) are credited and that the original publication in this journal is cited, in accordance with accepted academic practice. No use, distribution or reproduction is permitted which does not comply with these terms.
*Correspondence: Abd Elkarim Masoud, YWJkZWxrYXJpbS5tYXNvdWRAZW1rLnR1LWJlcmxpbi5kZQ==