- 1College of Energy and Mining Engineering, Shandong University of Science and Technology, Qingdao, China
- 2College of Geodesy and Geomatics, Shandong University of Science and Technology, Qingdao, China
To facilitate coal mining under the industrial square in Western China, short-wall paste continuous mining and continuous backfilling (PCMCB) is proposed to release the overlaid resources and handle coal gangue. First, the concept of short-wall PCMCB is presented, and the principle of surface subsidence is analyzed. Second, the mechanical model of the branch roadway and strength of the backfill body are established via mechanical derivations. Third, the proportion of backfill materials is calculated. Finally, field applications are carried out in the Dingjiaqu coal mine. The results show the following: 1) Based on the simply supported beam model of the roof and strength design model of the backfill body, the reasonable width of the branch roadway was determined as 5 m and late strength of the backfill body should exceed 2.62 MPa in the Dingjiaqu coal mine. 2) According to the design strength of the backfill body and backfill material proportion, the reasonable ratio of cement: fly ash: gangue: water was determined as 1:1.82:4.17:1.78. 3) In accordance with the equivalent mining height theory, the critical filling rate of the goaf should be more than 90% to ensure that the deformation is within the first level of building damage. 4) The field application shows that subsidence could be effectively controlled by backfilling, the overall surface subsidence was very small, and the maximum subsidence value (77 mm) was far lower than the deformation extremes of the building protection requirements. This study provides practical guidance for the exploitation of overlaid resources under similar shallow burial conditions, which can help in the disposal of coal gangue with considerable social and economic benefits with popularization and application.
1 Introduction
China has abundant coal resources that are widely distributed across the country. The overall distribution of the coal resources is uneven, with more availability in the west and less in the east. Coal resources in western China account for more than 70% of total national coal resources; with the gradual depletion of the coal resources in eastern China, the west is expected to be the main production base for coal and is characterized by its large scale, high intensity, high efficiency, and high recovery rate (Han et al., 2018; Xiao et al., 2021). Given the arid or semi-arid climate and inadequate water resources, the ecological environment in the west is fragile and coal seams are generally shallow (Yang et al., 2018). Traditional fully mechanized caving mining causes greater damage to the surface and environment, and the low recovery rate of partial mining does not conform with the concept of sustainable development (Fan and Ma, 2018; Yang et al., 2019). In parts of the west, the amounts of “three under” coal resources (i.e., those under buildings, railroads, and waterways) are large, and the problem of coal overlaid under industrial squares is typical. The amount of coal overlaid under the industrial square is estimated to be of the order of millions to tens of millions of tons, but there are many buildings in the industrial square with complex structures and high protection levels (Feng et al., 2020). Therefore, solving the problem of coal overlaid under the industrial square is important for solving the problem of three under mining in western China; this will also entail milestone significance for achieving large-scale resource recovery (Yan et al., 2018). Backfill mining is a technology developed in the past decade and can be used to control surface subsidence as well as protect buildings and structures in the industrial square by reducing the equivalent mining height. At the same time, the backfill method with coal gangue as the main raw material can effectively solve the problem of gangue disposal while protecting the fragile ecological environment in west China (Zhang et al., 2021a; Li et al., 2021).
The mainstream backfill technologies used in China are solid, paste, high water, and slurry backfill technologies. The application conditions of each of these backfill technologies are different. The purpose of backfilling is fundamental to the choice of the backfill technology used. If backfilling is adopted for solving problems with the three under coal resources, the primary purpose is to control subsidence; if it is used to solve problems with gangue disposal, then the main purpose is to digest solid wastes. At the same time, particular mining conditions must be considered in the backfill process because the proportion of backfill materials required in each mine as well as the model used are different.
Zhang Q. et al. (2019) summarized the research progress on solid backfill technologies in China and introduced the mining-separating-backfilling technology based on the specific engineering case of the Pingmei no.12 coal mine. Zhu et al. (2016) proposed a model to accurately predict the surface dynamic subsidence process of solid backfill mining and assess the mining damage; the validity of this method was verified using in situ measured subsidence data from the roofs of two backfill working faces. Zhang and Wang (2007) studied the feasibility of cemented gangue backfill and noted that coal gangue was not an ideal aggregate for pipeline gravity flow backfill; however, the disadvantages of gangue, such as bad fluidity and severe pipe wear, could be overcome by the addition of fly ash to obtain reasonable proportions of the backfill materials. Belem and Benzaazoua (2007) presented the laboratory- and backfill-plant-scale designs for paste backfill mix design and optimization, and they built different models (analytical, semi-empirical, and empirical) to predict the rheological factors of paste backfill (shear yield stress and viscosity). Chang et al. (2021) created a mechanical model of a paste false roof to analyze its stability for lower slicing mining and obtained the law of the plastic zone in the lower slicing face. Based on the characteristics of strip mining and backfilling, Zhu et al. (2007) proposed the method of filling with grouting for mining-induced overburden separation, which was successfully used without village relocation in the Huaibei mining area. Based on the properties of ultrahigh water materials, Jia and Feng (2012) analyzed the basic features of high water materials and presented different high water backfill methods for a goaf as engineering cases. By employing aeolian sand as the backfill aggregate, Bai et al. (2018) studied the mechanical properties of paste backfill materials with different proportions to provide reference for backfilling of the shallow seam in western China.
Extensive studies have been carried out to study the feasibility of using solid wastes, such as coal gangue, to recycle the overlaid coal resources owing to the increasing need for energy and consciousness regarding environmental protection. Great contributions on the backfill models and materials have been made in the development of backfill mining technologies by the above scholars, and good application results have been achieved in the field with various backfill technologies, especially in longwall mining. However, the filling rate of solid backfill is generally less than 80%, and its control of surface subsidence is not as good as those of paste and high water backfill; solid backfill is mainly used for digesting quantities of gangue. Although high water backfill can fulfill the control requirements of surface deformation, it cannot be used to dispose large amounts of solid wastes; spaces for separated strata need to be formed in slurry backfill, but the current research on delaminated space development are insufficient (Zhang J. et al., 2019). In response to the above problems, paste backfill is proposed as a reasonable means to achieve both high filling rate and effective digestion of gangue. The application of backfill mining is limited by restrictions on various factors, such as filling cost and filling yield. According to statistics, backfill mines are mainly distributed in eastern China in the Shandong, Shanxi, and Hebei provinces. There are very few cases of coal recovery under the industrial squares in western China (Liu et al., 2020). This study is mainly concerned with the short-wall PCMCB technology for developing resources under the industrial square. The basic concept is first presented, and the principle of controlling surface subsidence is analyzed; the mechanical model of the branch roadway and strength of the backfill body are established next; based on the geological mining conditions of the Dingjiaqu coal mine, the parameters of the branch roadway and strength of the backfill body are determined, and the reasonable proportions of backfill materials are calculated; finally, the critical filling rate for controlling deformation of the building structure is obtained from the equivalent mining height theory, and the feasibility of this technology is proved through a site application.
2 Concept and principle
2.1 Concept of short-wall PCMCB
Short-wall PCMCB is a green mining technology that is being used and developed since 2012. The diagram of the short-wall PCMCB system is shown in Figure 1, and the system is mainly divided into the gangue crushing and storage, stirring, pipeline pumping, and coal mining and separating systems. Coal gangue is transported to the backfill workshop after crushing; then, it is placed in a blender with fly ash, cement, and water to form a paste according to the determined proportion. Finally, the paste is transported to the goaf through pipelines. Before the backfill process, a complete ventilation and transportation system should be implemented on the basis of the original development and mining roadway. Then, the mining area is divided into multiple branch roadways in a direction parallel to the open-off cut and numbered serially as 1, 2, 3, 4, 5, etc. The odd-numbered branch roadways are mined first; when the filled odd-numbered branch roadways are stable, the remaining even-numbered branch roadways are mined so as to complete the mining and backfilling process (Lin et al., 2021). Short-wall PCMCB technology effectively integrates the three machines matching of short-wall mining and paste backfill process; it realizes separation of mining and backfilling while avoiding technical problems, such as mutual interference, low efficiency, and poor roof control in longwall mining and backfilling (Zhang et al., 2021b).
2.2 Principle of controlling surface subsidence by short-wall PCMCB
According to the basic principle of mining subsidence, when the overburden lithology is certain, a smaller mining width
3 Design of technical parameters
3.1 Design of the width and length of the branch roadway
In the width design, the immediate roof can be regarded as a beam structure supported by coal pillars on both sides. Because the buried depth of the coal seam is low and the coal pillar is affected by mining, the stability calculation of the roof can be considered as a simply supported beam (Chi, 2012). The calculation of the roof load q is the premise of rock beam stability calculation; according to the principle of a composite beam (Figure 3), this can be expressed as (Qian et al., 1996)
In the above formula,
When
In accordance with the stress distribution of a simply supported beam under a uniform load, the normal and shear stresses at any point B (Figure 4A) can be expressed as (Gere and Goodno, 2012)
where
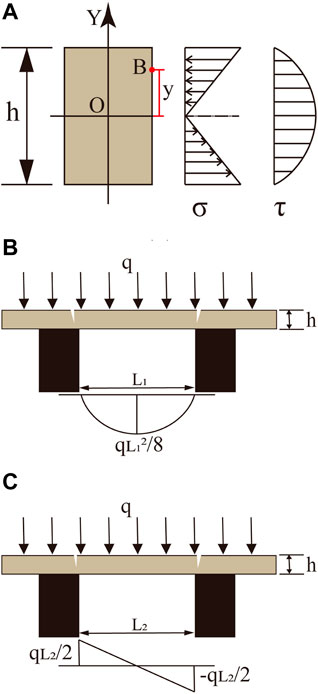
FIGURE 4. Failure model of a simply supported beam under a uniform load for (A) the stress state of any point on the section, (B) bending failure, and (C) shear failure.
Taking into account the nonhomogeneity of rock, a safety factor
where
When bending damage of a rock beam occurs, the maximum bending moment is at the center of the beam (Figure 4B), and the maximum normal stress can be expressed as (Gere and Goodno, 2012)
In this case, the ultimate span of the rock beam can be expressed as
When shear damage of a rock beam occurs, the maximum shear force appears at both ends of the beam (Figure 4C), and the maximum shear stress generated can be expressed as (Gere and Goodno, 2012)
Owing to shear damage, the ultimate span of the rock beam can be expressed as
Referring to Table 5,
The length of the branch roadway can be solved using the lowest cost per ton of coal, which can be expressed as (Liu et al., 2007)
where
From the formula, it is seen that the longer the branch roadway, the lower is the tunneling cost. Correspondingly, the costs of transportation and maintenance of the roadway will also increase. The length of the branch roadway also depends on the mining equipment; in the Dingjiaqu coal mine, two EBZ-160 fully mechanized driving machines with 40T scraper conveyors are employed, and the maximum daily excavation capacity is 40 m. To reduce the amount of continuous handling of the equipment, the final length of the branch roadway is 200 m.
3.2 Strength design of the backfill body
The strength of the backfill body generally comprises early and late strengths. There is no concept of early strength for the short-wall PCMCB as the backfill materials are fully solidified in the odd-numbered branch roadways when the even-numbered branch roadways are to be mined. The maximum strength of the backfill body is required to recover the coal pillar safely under its supporting condition. Therefore, the late strength design is the key to the backfill body. At present, the effective area theory is mainly used to analyze the load sustained by the backfill body; the backfill body bears the gravity of the rock layers directly above it and half of the branch roadway on each side. The load
where
The late strength is usually calculated by the Bieniawski formula (Bieniawski and Van Heerden, 1975), which is expressed as
where
Considering the influence of the specimen size (Shao et al., 2018),
where
Based on the limit strength theory, to maintain the stability of the backfill body, it is indispensable to consider the safety factor
According to the actual state,
3.3 Equivalent mining height prediction
To determine whether the surface deformation after backfilling meets the protection requirements of buildings, it is necessary to predict the surface deformation accurately. The probability integral method is the most widely used approach to subsidence prediction (Wang et al., 2018). Under the gravity of the overburden strata, a certain deformation is produced between the coal roof and floor, and the backfill body will dehydrate and shrink during the backfill process. Therefore, in actual calculations (Qu et al., 2010), the equivalent mining height theory is generally used to predict surface deformation, and the equivalent mining height is expressed as follows:
where
Based on the industrial square building protection grade and equivalent mining height theory, the surface movement and deformation parameters of the 42201 working face (Table 1) were selected, and the surface deformation characteristics under different filling rates (equivalent mining height divided by actual mining height) were obtained using the probability integral method (Table 2). The results show that when the filling rate is more than 90%, the damage may be within the first level of building damage.
4 Backfill materials
Paste backfill materials are mainly composed of gangue, cement, fly ash, and water. As the most abundant material, gangue plays the role of the skeleton in the backfill body; as the cementitious material, cement is the fundamental source of strength; fly ash can significantly reduce the amount of cement required and effectively improve the pumping performances of the backfill materials.
4.1 Reasonable gradation of gangue
Washed gangue from the Dingjiaqu coal washery was used in the field. After screening, the size distribution of the washed gangue is as shown in Figure 5A. Since the particle sizes of the washed gangue did not meet the requirements of long-distance pipeline transportation, the washed gangue had to be crushed until the maximum particle size was less than 25 mm. The particle size distribution after screening for the crushed gangue is as shown in Figure 5B. It can be seen that most of the crushed gangue particles are between 0.3 mm and 20 mm, and only a very small fraction of the particles are 20–25 mm in size. The gangue particles between 5 and 20 mm account for 50.1%, and those with sizes less than 5 mm account for 48%, which conforms to the ideal particle gradation curve (maximum particle size of the gangue is less than 25 mm, and the proportion of gangue with particle sizes less than 5 mm is about 40–50%) (Zheng et al., 2006; Sun et al., 2017).
4.2 Design of the proportion of backfill materials
Since there are many studies on the proportion of backfill materials (Koohestani et al., 2016; Jiang et al., 2020; Liu et al., 2022), the composition was adjusted according to the one in the neighboring Tianyu coal mine, and the laboratory and downhole proportioning experiments were conducted. As shown in Tables 3, 4, the final results obtained via the uniaxial compression test show that when the cement dosage is certain, excess gangue leads to lower strength of the backfill body, so the proportion of gangue should be in a reasonable range. The final choice of backfill material proportion for cement: fly ash: gangue: water is 1:1.82:4.17:1.78 for the Dingjiaqu coal mine.
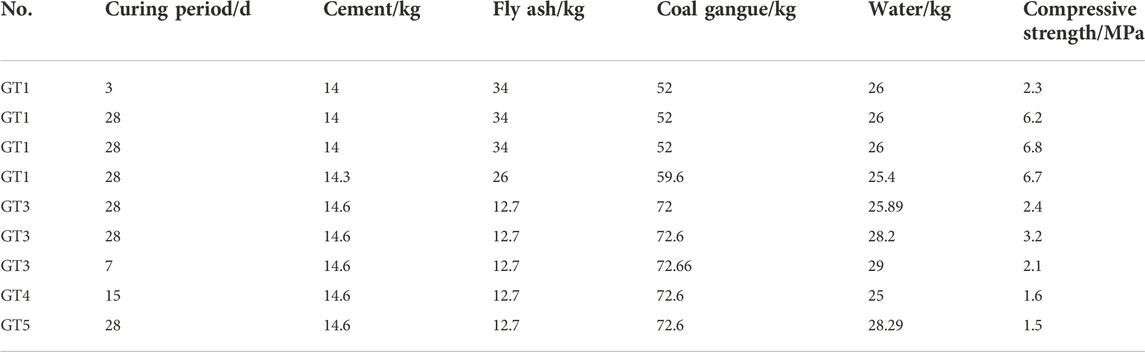
TABLE 3. Uniaxial compression test results for different ratios of the backfill body over the ground.
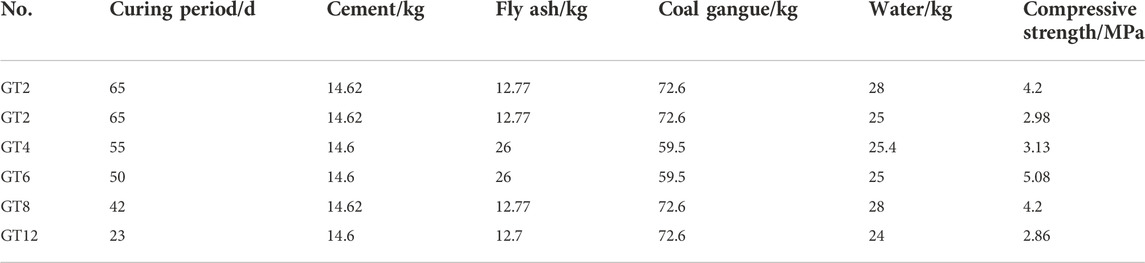
TABLE 4. Uniaxial compression test results for different ratios of the backfill body under the ground.
5 Case studies
5.1 Geological settings and mining conditions
The Dingjiaqu coal mine is located in Ordos, Inner Mongolia, China. The terrain of the mining area is gentle, with a dip angle of less than 10°. At present, the 3-2 coal in the main coal seam has been mined out, and only the 4-2 coal under the industrial square, Baofu highway, and boundary coal pillar remain; the 5-2 coal is a thin seam with an average recoverable thickness of 1.24 m. Thus, a large quantity of coal gangue will be produced once mining commences. To extend the service life of the coal mine, improve the resource recovery rate, and digest the abandoned coal gangue, the short-wall PCMCB was considered for adoption for the pressed coal under the industrial square. The buried depth of the 4-2 coal is about 60 m, with a natural thickness of 0.70–3.45 m (average value: 2.57 m). The specific information and mechanical parameters of the coal seam roof and floor are shown in Table 5.
5.2 Determination of key parameters
First, the roof load
5.3 Backfill process
The pattern of building the backfill plant on the ground was adopted in the Dingjiaqu coal mine, and the physical effect diagram is as shown in Figure 6. There are two stages in the backfill process. The first stage involves paste preparation, where the raw materials are weighed by proportion and then transported to the mixer through belt conveyors and pipelines for complete mixing. The second stage involves pipeline pumping, where the prepared paste is carried to the storage hopper and then transported to the underground working face through backfill pipelines.
The 42207 working face was mined as shown in Figure 1. After each of the branch roadways were mined, the upper and lower exits of the branch roadways were sealed with paste baffles first, and single hydraulic props were installed on the outside to strengthen the supports (Figure 7); finally, the paste was injected from the upper exit.
5.4 Measurement of surface subsidence
In line with the layout of the 42207 mining area and distribution of the surface features, third-class leveling was adopted for deformation monitoring as it has sufficient for subsidence monitoring. A strike observation line and a tendency observation line were arranged above the 42207 mining area, as shown in Figure 8. There were 25 observation points numbered 1 to 25 and set along the north–south observation line at distances of 20 m for a total length of 500 m; then, 29 observation points numbered 26 to 54 were set along the east–west observation line at distances of 20 m for a total length of 560 m.
The monitoring results (Figure 9) show that the subsidence could be reduced dramatically by backfilling and that the integral surface subsidence was small, with a maximum subsidence of 77 mm. The overall subsidence of the industrial square was uniform. Large inclination and horizontal deformations were observed at the edges of the subsidence basin as the coal seam is buried shallowly; accordingly, the inclination and horizontal deformation values changed rapidly. The maximum value of inclination was 1.99 mm/m; the maximum value of horizontal deformation was 0.56 mm/m; the maximum value of curvature deformation was 0.07×10–3 /m. Taking into account the errors between the forecast software and actual measurements, the observations basically show the law of surface deformation; a comprehensive analysis shows that the surface movement and deformations after backfilling meet the requirements of the building fortification level.
6 Discussion
To further reveal the advantages and disadvantages of the proposed short-wall PCMCB technology, a comparison between similar technologies is given in Table 7. Considering the characteristics of the western mining area, the solid backfill is less effective for controlling the surface deformations, and the high water backfill cannot handle a large amount of coal gangue (Hu et al., 2020). The surface control effect of the full mechanized and paste backfill is good, but its mining and backfilling interferences are serious, geological conditions of the working face are poorly adapted (Zhu, 2021), and the total investment in the full mechanized and paste backfill is generally more than twice that of the short-wall PCMCB, with the production capacity and tons of coal filling cost being similar (Zhu et al., 2017). Short-wall PCMCB also realizes full separation of the mining and backfilling, and the working face arrangement of this backfill method is flexible without being limited by the thickness of the coal seam; it also has strong applicability to the exploitation of overlaid and boundary coal resources (Lu et al., 2017; Li et al., 2022).
7 Conclusion
In the practice of three under mining, it is necessary to pay attention to improving the resource recovery rate and controlling the surface subsidence. Backfill mining not only achieves excellent recovery of the remaining coal resources but also reduces environmental damage effectively. To solve the problem of coal compressed under the industrial square in western China, the short-wall PCMCB scheme is proposed. The key to short-wall PCMCB is in the reasonable design of the width, length of the branch roadway, and strength of the backfill body. Based on the stress state of the branch roadway roof, it can be simplified as a simply supported beam, and the width of the branch roadway can be designed according to the bending and shear failure modes; the length of the branch roadway can be designed in accordance with the lowest cost per ton of coal; the late strength is calculated according to the strength design model of the backfill body. The filling rate is the standard for assessing whether the surface movement and deformation meet the requirements of building protection, which is obtained by the probability integral method. The selection and proportion of backfill materials are other important factors in the short-wall PCMCB; a reasonable proportion of the materials affords sufficient strength to the backfill body while maintaining backfill cost and digesting as much gangue as possible. The field application of the short-wall PCMCB in the Dingjiaqu coal mine shows that the subsidence could be reduced dramatically by backfilling. The integral subsidence of the industrial square was uniform, and the maximum subsidence values (77 mm) were far lower than the deformation extremes based on the requirements of the first level of building damage. This application proves that the short-wall PCMCB has good effects on the exploitation of the overlaid resources in western China.
Data availability statement
The original contributions presented in the study are included in the article/Supplementary Material, and further inquiries can be directed to the corresponding author.
Author contributions
Conceptualization, ZM and YD; methodology, YD; software, ZM and XZ; validation, XZ, FJ, YF, and CT; formal analysis, XZ; investigation, ZM; resources, XZ; data curation, ZM; writing—original draft preparation, ZM and YD; writing—review and editing, XZ; visualization, YD; supervision, XZ; project administration, XZ; funding acquisition, XZ. All authors have read and agreed to the published version of the manuscript.
Funding
This work was supported by the National Natural Science Foundation of China (no. 52104203), Shandong Province Natural Science Foundation Project (no. ZR2020QE128), National Key R&D Program of China (no. 2018YFC0604705), SDUST Research Fund (no. 2018TDJH102), and National Natural Science Foundation of China (nos. 51574159, 52074251, 51974172, 51974173, 92058211, and 51804179).
Acknowledgments
The authors would like to thank the Dingjiaqu coal mine for providing field measurement data.
Conflict of interest
The authors declare that the research was conducted in the absence of any commercial or financial relationships that could be construed as a potential conflict of interest.
Publisher’s note
All claims expressed in this article are solely those of the authors and do not necessarily represent those of their affiliated organizations, or those of the publisher, editors, and reviewers. Any product that may be evaluated in this article or claim that may be made by its manufacturer is not guaranteed or endorsed by the publisher.
References
Bai, E., Guo, W., Tan, Y., and Yang, D. (2018). The analysis and application of granular backfill material to reduce surface subsidence in China's northwest coal mining area. PLoS One 13 (7), e0201112. doi:10.1371/journal.pone.0201112
Belem, T., and Benzaazoua, M. (2007). Design and application of underground mine paste backfill technology. Geotech. Geol. Eng. 26 (2), 147–174. doi:10.1007/s10706-007-9154-3
Bieniawski, Z. T., and Van Heerden, W. (1975). The significance of in situ tests on large rock specimens. Int. J. Rock Mech. Min. Sci. Geomechanics Abstr. 12 (4), 101–113. doi:10.1016/0148-9062(75)90004-2
Chang, Q., Sun, Y., Leng, Q., Liu, Z., Zhou, H., and Sun, Y. (2021). Stability analysis of paste filling roof by cut and fill mining. Sustainability 13 (19), 10899. doi:10.3390/su131910899
Chi, X., and Liu, M. (2012). The stability analysis of stope roof based on beam model. China Min. Mag. 21 (08), 113–115.
Fan, L., and Ma, X. (2018). A review on investigation of water-preserved coal mining in Western China. Int. J. Coal Sci. Technol. 5 (4), 411–416. doi:10.1007/s40789-018-0223-4
Feng, G., Zhang, Y., Qi, T., and Kang, L. (2020). Status and research progress for residual coal mining in China. J. China Coal Soc. 45 (01), 151–159. doi:10.13225/j.cnki.jccs.YG19.1280
Han, S., Chen, H., Long, R., and Cui, X. (2018). Peak coal in China: A literature review. Resour. Conservation Recycl. 129, 293–306. doi:10.1016/j.resconrec.2016.08.012
Hu, B., Liu, P., Cui, F., and Wang, H. (2020). Review and development status of backfill coal mining technology in China. Coal Sci. Technol. 48 (09), 39–47. doi:10.13199/j.cnki.cst.2020.09.004
Jia, K., and Feng, G. (2012). Application and prospect of super-high-water packing material in mining engineering. Coal Sci. Technol. 40 (11), 6–9+23. doi:10.13199/j.cnki.cst.2015.01.002
Jiang, N., Wang, C., Pan, H., Yin, D., and Ma, J. (2020). Modeling study on the influence of the strip filling mining sequence on mining-induced failure. Energy Sci. Eng. 8 (6), 2239–2255. doi:10.1002/ese3.660
Kang, H., Xu, G., Wang, B., Wu, Y., Jiang, P., Pan, J., et al. (2019). Forty years development and prospects of underground coal mining and strata control technologies in China. J. Min. Strata Control Eng. 1 (02), 7–39. doi:10.13532/j.jmsce.cn10-1638/td.2019.02.002
Koohestani, B., Belem, T., Koubaa, A., and Bussière, B. (2016). Experimental investigation into the compressive strength development of cemented paste backfill containing Nano-silica. Cem. Concr. Compos. 72, 180–189. doi:10.1016/j.cemconcomp.2016.06.016
Li, S., Zhao, Z., Yu, H., and Wang, X. (2021). The recent progress China has made in the backfill mining method, Part II: The composition and typical examples of backfill systems. Minerals 11 (12), 1362. doi:10.3390/min11121362
Li, Y., Lu, B., Yang, S., Lin, H., Xu, B., and Liu, C. (2022). Cemented backfilling mining technology with continuous mining and continuous backfilling method for underground coal mine and typical engineering cases. J. China Coal Soc. 47 (03), 1055–1071. doi:10.13225/j.cnki.jccs.2021.1612
Lin, H., Yang, R., Lu, B., Li, Y., Fang, S., Fan, Z., et al. (2021). Overlying strata movement law of continuous mining and continuous backfilling cemented-fill mining. Environ. Earth Sci. 80 (20). doi:10.1007/s12665-021-09993-w
Liu, K., Xu, J., and Miao, X. (2007). Short-wall mining technology and its application. Beijing: Coal Industry Press.
Liu, J., Li, X., and He, T. (2020). Application status and prospect of backfill mining in Chinese coal mines. J. China Coal Soc. 45 (01), 141–150. doi:10.13225/j.cnki.jccs.YG19.1063
Liu, Y. F., Wu, X. H., Zhu, T., Wang, X. J., Zhang, G. Y., and Wang, Z. G. (2022). Influence of mechanical properties of filling paste on overlying strata movement and surface settlement. Shock Vib. 2022, 1–9. doi:10.1155/2022/4687200
Lu, B., Zhang, X., Li, F., Zhang, B., and Pang, Z. (2017). Study and application of short-wall gangue cemented backfilling technology. J. China Coal Soc. 42 (S1), 7–15. doi:10.13225/j.cnki.jccs.2016.1416
Qian, M., Miao, X., and Xu, J. (1996). The key strata theory study in rock strata control. J. China Coal Soc. (03), 2–7.
Qu, Q., Yao, Q., Li, X., and Rong, T. (2010). Key factors affecting control surface subsidence in backilling mining. J. Min. Saf. Eng. 27 (04), 458–462.
Shao, X., Liu, E., Cai, X., Wu, J., and Zhang, J. (2018). Experimental study on stability of pillar in upward mining in pillar mined out area. Coal Eng. 50 (04), 5–9.
Sun, X., Qiang, H., Shi, X., and Chang, Q. (2017). Mixture ratio optimization of mine gangue paste filling materials. Saf. Coal Mines 48 (10), 69–72+75. doi:10.13347/j.cnki.mkaq.2017.10.018
Wang, L., Wei, T., Li, N., Chi, S. S., Jiang, C., and Fang, S. Y. (2018). Research on probability integration parameter inversion of mining-induced surface subsidence based on quantum annealing. Environ. Earth Sci. 77 (21). doi:10.1007/s12665-018-7927-z
Xiao, W., Chen, W., and Deng, X. (2021). Coupling and coordination of coal mining intensity and social-ecological resilience in China. Ecol. Indic. 131, 108167. doi:10.1016/j.ecolind.2021.108167
Xie, H., Duan, F., Zhou, H., and Zhao, G. (1998). Recent development of theory and analysis methods of strip pillar stability. China Min. Mag. (05), 37–41.
Yan, H., Zhang, J., Zhang, S., and Zhou, N. (2018). Physical modeling of the controlled shaft deformation law during the solid backfill mining of ultra-close coal seams. Bull. Eng. Geol. Environ. 78 (5), 3741–3754. doi:10.1007/s10064-018-1335-1
Yang, Z., Li, W., Pei, Y., Qiao, W., and Wu, Y. (2018). Classification of the type of eco-geological environment of a coal mine district: A case study of an ecologically fragile region in western China. J. Clean. Prod. 174, 1513–1526. doi:10.1016/j.jclepro.2017.11.049
Yang, Z., Li, W., Li, X., and He, J. (2019). Quantitative analysis of the relationship between vegetation and groundwater buried depth: A case study of a coal mine district in western China. Ecol. Indic. 102, 770–782. doi:10.1016/j.ecolind.2019.03.027
Zhang, Q., and Wang, X. (2007). Performance of cemented coal gangue backfill. J. Cent. South Univ. Technol. doi:10.1007/s11771−007−0043−y
Zhang, J., Li, M., Taheri, A., Zhang, W., Wu, Z., and Song, W. (2019a). Properties and application of backfill materials in coal mines in China. Minerals 9 (1), 53. doi:10.3390/min9010053
Zhang, Q., Zhang, J. X., Wu, Z. Y., and Chen, Y. (2019b). Overview of solid backfilling technology based on coal-waste underground separation in China. Sustainability 11 (7), 2118. doi:10.3390/su11072118
Zhang, Y., Liu, Y., Lai, X., Gao, J., and Wu, Y. (2021a). Physical modeling of the controlled water-flowing fracture development during short-wall block backfill mining. Lithosphere 2021 (4). doi:10.2113/2021/2860087
Zhang, Y., Wang, B., Zhang, X., and Li, F. (2021b). Forty years' development and future prospect on mechanized short-wall mining technology with continuous miner in China. J. China Coal Soc. 46 (01), 86–99. doi:10.13225/j.cnki.jccs.2020.1632
Zheng, B., Zhou, H., and He, R. (2006). Experimental research on coal gangue paste filling material. J. Min. Saf. Eng. (04), 460–463.
Zhu, L. (2021). Application and practice of solid waste multi-state filling technology in ecological fragile area of Western China. Min. Saf. Environ. Prot. 48 (04), 81–86. doi:10.19835/j.issn.1008-4495.2021.04.015
Zhu, W., Xu, J., Lai, W., and Wang, Z. (2007). Research of isolated section-grouting technology for overburden bed separation space to reduce subsidence. J. China Coal Soc. (05), 458–462.
Zhu, X., Guo, G., Zha, J., Chen, T., Fang, Q., and Yang, X. (2016). Surface dynamic subsidence prediction model of solid backfill mining. Environ. Earth Sci. 75 (12). doi:10.1007/s12665-016-5817-9
Keywords: paste backfill, surface subsidence, solid waste utilization, shallow coal seam, continuous mining and continuous backfilling
Citation: Meng Z, Dong Y, Zhang X, Jiao F, Fan Y and Thammavongsa C (2023) Short-wall paste continuous mining and continuous backfilling for controlling industrial square surface subsidence. Front. Earth Sci. 10:1009617. doi: 10.3389/feart.2022.1009617
Received: 02 August 2022; Accepted: 22 September 2022;
Published: 09 January 2023.
Edited by:
Zefa Yang, Central South University, ChinaReviewed by:
Xiaojun Zhu, Anhui University, ChinaWang Lei, Anhui University of Science and Technology, China
Copyright © 2023 Meng, Dong, Zhang, Jiao, Fan and Thammavongsa. This is an open-access article distributed under the terms of the Creative Commons Attribution License (CC BY). The use, distribution or reproduction in other forums is permitted, provided the original author(s) and the copyright owner(s) are credited and that the original publication in this journal is cited, in accordance with accepted academic practice. No use, distribution or reproduction is permitted which does not comply with these terms.
*Correspondence: Xinguo Zhang, emhhbmd4ZzEyMjlAMTYzLmNvbQ==