- 1Thermodynamics-Materials-Separations Research Group (TMSRG), Department of Chemical Engineering, Mangosuthu University of Technology, Umlazi, South Africa
- 2Faculty of Engineering, Mangosuthu University of Technology, Umlazi, South Africa
Optimization studies for the esterification and transesterification of oil extracted from Croton gratissimus grains were carried out using the response surface methodology (RMS) that utilizes the central composite design (CCD) and the analysis of variance (ANOVA). A 23 full-factorial rotatable CCD for three independent variables at five levels was developed in each case, giving a total of 20 experiments needed per study. The three design factors chosen for study were the catalyst concentration, methanol-to-oil ratio, and the reaction temperature. The values of the acid value of oil (in esterification) and the percentage FAME yield and FAME purity (in transesterification) were taken as the responses of the designed experiments. In the optimization of the esterification and transesterification processes, the ANOVA showed that both quadratic regression models developed were significant. The optimum operating conditions for the esterification process that could give an optimum acid value of 2.693 mg KOH/g of oil were found to be 10.96 mass% SO42–/ZrO2 catalyst concentration, 27.60 methanol-to-oil ratio, and 64°C reaction temperature. In the optimization of the transesterification process, the model revealed that the catalyst concentration and the methanol-to-oil ratio were the terms that had the most influence on the % FAME yield and the % FAME purity of the final biodiesel product. From the combined regression model, it was established that optimum responses of the 84.51% FAME yield and 90.66% FAME purity could be achieved when operating the transesterification process at 1.439 mass% KOH catalyst concentration, 7.472 methanol-to-oil ratio, and at a temperature of 63.50°C. Furthermore, in the two-step biodiesel synthesis, a predominantly monoclinic-phased sulfated zirconia (SO42–/ZrO2) catalyst exhibited high activity in the esterification of high free fatty acid oil extracted from Croton gratissimus grains. A 91% reduction in the acid value of the Croton gratissimus oil from 21.46 mg KOH/g of oil to 2.006 mg KOH/g of oil, well below the 4 mg KOH/g of oil maximum limit, was achieved. This resulted in the high FAME yield and purity of the biodiesel produced in the subsequent catalytic transesterification of oil using KOH.
Introduction
Concerns of dwindling crude oil reserves and global environmental degradation arising from the extensive use of petroleum-based fuels have made the biofuels-focused research more relevant than ever. Emphasis of earlier study, that saw the birth of the biodiesel industry, was on the use of edible vegetable crops, animal fat, and a selection of tropical plant species as biodiesel feedstock. But the unresolved food security issues raised against the use of edible crops in biodiesel production and low cold flow properties due to high freezing points (0°C−5°C) associated with biodiesel derived from animal fats (Berrios and Skelton, 2008) have shifted the attention of investigative study towards the high free fatty acid (FFA) non-edible vegetable crops.
For the continued sustainability of the biodiesel industry, economic challenges facing the industry must be addressed. The success and future survival of the biodiesel industry, therefore, depends entirely on its economic viability. An economically viable biodiesel production process must be capable of providing an ultimate gain in energy over all the energy sources used in the process. For this to happen, a biodiesel process must be energy efficient, allowing sufficient throughput volumes to be achieved whilst keeping the energy demand to a bare minimum. It is for this reason that the wholesale of non-edible vegetable crops (Croton gratissimus being one of them) is being investigated as potential feedstock in biodiesel processes (Atabani et al., 2012) to produce high quality biodiesel whilst operating at moderate conditions, of temperature and pressure, and over shorter reaction times.
Croton gratissimus grains, under investigation in this study, are classified as high FFA non-edible vegetable crops. They are a product of a terrestrial plant of a semi-deciduous tree species that belongs to the family of Euphorbiaceae. For productive cultivation, Croton gratissimus tree does not require frequent soil tillage nor demand constant irrigation for growth. The plant grows naturally in uninhabitable places, as it is often found in stony terrains of the warmer and drier regions of the African continent (Mulholland et al., 2010). It promises, therefore, to be a future second generation crop for biodiesel production on the African continent. Non-edible oil extracted from Croton gratissimus grains has proven to have a potential of producing high quality biodiesel (Bahadur et al., 2014).
Generally, in biodiesel production processes, oil extraction from the grains is achieved by the solvent oil extraction (SOE) technique that offers reasonably high oil yields (Atabani et al., 2013; Jiyane et al., 2018) when compared to other techniques, viz., supercritical fluid extraction (SFE), ultrasonic-assisted extraction (UAE), and enzymatic oil extraction (EOE) techniques. The SFE and UAE techniques, despite their high oil recovery yields, have drawbacks of being highly energy intensive and difficult to scale-up for commercial biodiesel production (Kumar and Sharma, 2015). In the case of the enzymatic oil extraction technique, long oil processing times are a major drawback (Atabani et al., 2013). n-Hexane, the most commonly used solvent in the SOE technique, is an industrial favorite for its relatively low purchase cost and the fact that it can be recycled after use (Li et al., 2004); an economic factor. Soxhlet extractions performed by Sánchez-Arreola et al. (2015) on Jatropha curcas grains using n-hexane and ethyl ether gave oil yields of 47.7 and 45.9%, respectively. Bahadur et al. (2014), on the other hand, reported a 23.5% oil yield when n-hexane was used as an extraction solvent in Croton gratissimus grains. Evidently, better extraction oil yields could be obtained from Jatropha curcas than Croton gratissimus grains for the same solvent selection in extraction. These differences can be attributed to the differences in lipid profiles of the oils extracted from these two crop species. Croton gratissimus oil has 24.71% unsaturated fatty acids (Bahadur et al., 2014) compared to 75.46% found in Jatropha curcas (Sánchez-Arreola et al., 2015). High number of double bonds (unsaturation) in fatty acids leads to greater oil solubility (Kostić et al., 2013). This increased solubility of oil leads to increased mass transfer between the oil and the surface of the ground seed particles resulting in higher extraction yields.
The production of biodiesel from high FFA crops, unlike from oils extracted from edible vegetable crops, requires a conventional two-step process approach. This begins by reducing the acid value of oil to below 4 mg KOH/g in the esterification reaction step over a homogeneous or heterogeneous acid catalyst before the main base-catalyzed transesterification reaction step. When a one-step approach is used in these crops, a catalyst capable of simultaneously catalyzing both the esterification and transesterification reaction steps must be employed. Heterogeneous solid acid catalysts, offering shorter reaction times (Chouhan and Sarma, 2011) and suitable for both low and high temperature operations (Aransiola et al., 2014), have proven to be the ideal choice in this regard. These catalysts have drawn much of the attention from industry and academia because of their high activity at low temperature that make them operational where thermodynamic equilibrium compositions contain a fraction of the desired products possible (Srinivasan et al., 1995). One such catalyst is the heterogeneous sulfated zirconia (ZrO2SO4). Depending on the method of preparation, ZrO2SO4 as a catalyst is either effective in its monoclinic-phased or tetragonal-phased form. When used to simultaneously catalyze both reactions, monoclinic and tetragonal phases must be present with the tetragonal phase being the dominant phase.
This article intends to report on the response surface methodology (RSM) optimization study, based on the central composite design (CCD) technique, performed on the Croton gratissimus biodiesel production process. The study was aimed at finding the optimum operating conditions of catalyst concentration, methanol-to-oil ratio and reaction temperature, under which biodiesel can be produced from Croton gratissimus oil to give the highest biodiesel yield and high FAME purity. High free fatty acid oil extracted from the grains was subjected to an esterification reaction process carried out over a synthesized monoclinic ZrO2SO4 catalyst followed by a transesterification reaction process over a homogeneous KOH catalyst.
Materials and Methods
Materials
Croton gratissimus oil was produced in the laboratories at Mangosuthu University of Technology (MUT) in an extraction process of Croton gratissimus grains (Figure 1) carried out using n-hexane as an extraction solvent (Jiyane et al., 2018). The oil produced had an acid value of 21.46 mg KOH/g oil and a specific gravity of 0.928 (Table 1). Sulfated zirconia catalyst, SO42–/ZrO2, was synthesized in the laboratories at MUT following the method proposed by Chen et al. (1993) and modified by Reddy et al. (2005). Potassium hydroxide (KOH ≥ 85%) and zirconyl chloride octahydrate (ZrOCl2·8H2O), a precursor for the sulfated zirconia catalyst SO42–/ZrO2, were purchased from Sigma-Aldrich, South Africa. Methanol AR of 99% purity was purchased from Merck Laboratories in South Africa.

TABLE 1. Comparison of properties of extracted oil with literature data for non-edible vegetable oils.
An analytical balance, RADWAG® AS 220/C/2, was used for accurate weight measurement of catalyst samples used in FAME production. A HERMLE centrifuge was used for final separation of the esterification and transesterification products. The laboratory-assembled equipment, shown in Figure 2, was used in the esterification and transesterification reactions. A PerkinElmer Clarus® 580 Gas Chromatograph equipped with a Clarus® SQ 8S Mass Spectrometer (GC-MS) was used in the characterization of finished biodiesel product.
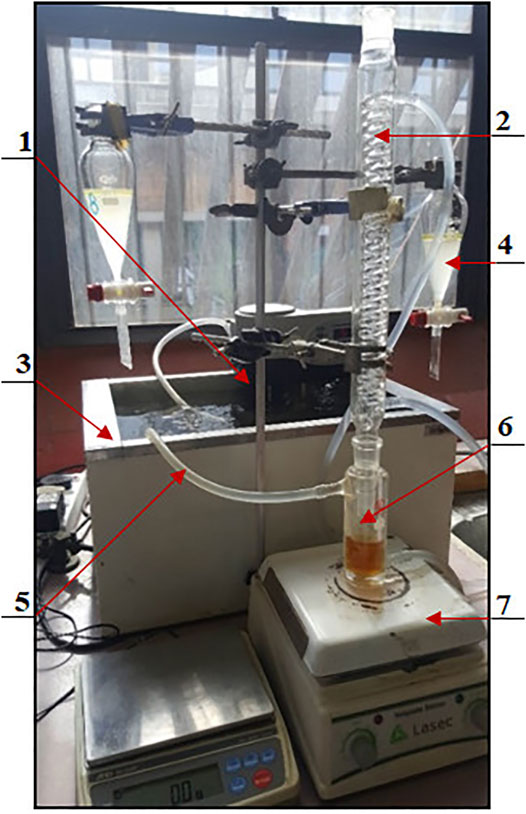
FIGURE 2. Experimental set-up. 1. Temperature regulator-circulator; 2. Graham condenser; 3. rectangular hot water bath; 4. separation flask; 5. circulatory hot water plastic tubing; 6. jacketed reaction beaker; 7. magnetic stirrer and heater.
Experimental Methods
Biodiesel is mainly produced in a transesterification reaction, a chemical reaction where alcohol from an ester is displaced by another alcohol in a process similar to hydrolysis, except that transesterification uses an alcohol instead of water. During this reaction, triglycerides from oils and fats react with an alcohol in the presence of a catalyst to produce fatty acid esters (biodiesel) and the by-product glycerol. It is important to note that with recent advances in research in this field, other methods have been developed that do not require the use of a catalyst, that is, catalyst-free. In this regard, supercritical methods that employ supercritical methanol have been successfully used in biodiesel processing (Madras et al., 2004) albeit being energy intensive and inherently unsafe. In a catalytic environment, a basic or acidic catalyst is used to convert the glycerol-based esters (triglycerides), which make up fats or oils, to alcohol-based esters (methyl esters) giving off free glycerol as a by-product. Glycerol, after separation from the reaction mixture, may be purified and sold for use to the pharmaceutical, cosmetics, foods, and the plastics industries (Vicente et al., 1998). The mass balance of croton gratissimus production can be written as follows:
1,000 kg + 110.50 kg → 1,004.64 kg + 105.86 kg
Fat oil + 3 Methanol → 3 Methyl Ester + Glycerol
This mass balance is based on the fatty acid composition of Croton gratissimus oil shown in Table 2 and assumes complete conversion of triglycerides to fatty acid methyl esters. It therefore gives the theoretically attainable FAME yield from this virgin oil.
Esterification of Oil
A weighed sample (±10 g) of oil was placed in a 50 ml jacketed reaction beaker fitted with a Graham condenser. Hot water was allowed to flow through the jacket to keep the oil inside the beaker at the reaction temperature. A proportional amount of catalyst (SO42–/ZrO2) and methanol (MeOH) was added to the heated oil, and the reaction mixture was stirred at 650 rpm. Reaction temperature was maintained at a predetermined level by water circulating from a rectangular hot water bath equipped with an immersion temperature regulator-circulator as shown in Figure 2.
After 1½ hours of reaction time, the mixture was poured into a separation flask and allowed to settle. Three distinct layers were observed, that is, the bottom layer consisting mainly of the used catalyst, next the product layer in the middle, and the top layer consisting mainly of water and the unused methanol from the reaction. The two bottom layers were taken for further separation in a centrifuge. The centrifuge was set at 4,000 rpm for 5 min with an acceleration/deceleration speed set at 5 cycles per second. The SO42–/ZrO2 catalyst was recovered, and the intermediate product of esterification was stored for further processing. The same procedure was followed in all 20 experimental runs conducted.
Transesterification of Oil
A known mass of esterified oil was placed in a 50 ml jacketed beaker and brought to the reaction temperature by circulating water from a hot water bath fitted with an immersion temperature regulator-circulator. About 5 ml of n-hexane was added into the oil to improve the miscibility of MeOH in oil. Potassium methoxide (KOCH3) solution was then prepared in a 50 ml beaker by dissolving weighed mass of KOH catalyst in a known volume of MeOH. The KOCH3 solution was poured into the beaker and agitated using a magnetic stirrer. A Graham condenser, connected to the jacketed beaker was used to capture MeOH escaping from the reaction vessel.
After 1½ hours of reaction time, the mixture was poured into a 50 ml beaker to remove the bottom dark brown glycerol layer. The top biodiesel layer was transferred into a 50 ml separating flask. Water (±25 ml) was added and the mixture was vigorously shaken for 6 min, taking 30 s breaks after every 2 min of continuous shaking. The mixture was then left to settle in the separating flask for a few hours. After 5 washes, the final washed product was separated in a HERMLE centrifuge. n-Hexane solvent used to enhance miscibility of reactants and excess MeOH remaining after reaction were removed by flash evaporation.
The final biodiesel product was transferred into sampling bottles and weighed. The biodiesel yield was calculated as the ratio of mass of biodiesel (m) produced to the mass of Croton gratissimus oil, (M) used in the transesterification reaction.
A total of 20 experimental runs were conducted, and the results from these experiments were used in the optimization study. Biodiesel (FAME) samples were characterized using the gas chromatography mass spectroscopy (GC-MS).
Optimization of Biodiesel Processes
The response surface methodology (RSM), adopted in this study, is a collection of mathematical and statistical techniques that are used for modeling and analysis in applications where a response of interest is influenced by a number of variables and the objective is to optimize (minimize or maximize) this response. Its main objective is “to determine the optimum operating conditions for the system or to determine a region of the factor space in which operating specifications are satisfied” (Montgomery and Runger, 2010). This method uses multiple regression and correlation analyses as tools to assess the effects of the chosen independent factors on the dependent variables. It is known to generate sufficient data for statistically acceptable results from a few experimental runs (Jeong et al., 2009). The RSM uses the central composite design (CCD) or the Box–Behnken design (BBD) to fit a model by the least squares technique and verify the adequacy of the model using a diagnostic tool, the analysis of variance (ANOVA) (Ahmadi et al., 2005).
CCDs are based on 2-level factorial designs and augmented with center points,
where Y is the predicted response,
The BBD, an alternative to CCD, are a class of second-order rotatable or almost rotatable designs that are based on 3-level partial factorial designs (Ferreira et al., 2007a). These designs do not have runs at the extreme combinations (higher or lower levels) of all the factors, but compensate by possessing better prediction precision in the center of the factor space. Compared to the CCD, the BBD always gives fewer experimental runs. For the development of the Box–Behnken design, a total of
With these two design techniques (central composite and Box–Behnken designs) available, one has to select the specific one to use in a particular situation. The most important factors to consider are the number of experimental runs and the effects of interactions. Either way, these techniques are both used with ANOVA, a statistical tool that is able to give a rigorous analysis of the developed model.
A Doehlert design (DD) is yet another optimization tool that has been extensively exploited by many researchers in a variety of fields. Unlike the CCD and the BBD, these designs are characterized by being asymmetrical, affording the researcher the freedom to study different factors at different numbers of levels (Doehlert, 1970). DDs are incapable of rotation, despite being spherical, but have the ability to fill the entire design space; hence, the claim that they are “uniform space fillers”. These designs make it possible to cover an experimental range with a uniform grid of points, even when the range being studied is irregular (Ferreira et al., 2007a); (Doehlert, 1970).
An optimization study carried out using RSM involves three stages. First, the determination of independent variables and their levels followed by the selection of the experimental design prediction and verification of the model equation, and finally the graphical presentation of the model equation and the determination of the optimum operating conditions (Baş and Boyacı, 2007). The determination of independent variables and their levels is a critical stage because choosing wrong levels may result in an unsuccessful optimization. The classical one-factor-at-a-time (OFAT) optimization approach is usually used at this stage to develop screening experiments to help identify important independent parameters that are most likely to affect the chosen responses. This gives the experimenter direction in which the improvements lie and, hence, facilitate the identification of the levels of parameters (Baş and Boyacı, 2007).
Vicente et al. (2007) successfully developed a model for FAME synthesis from sunflower oil using a potassium hydroxide (KOH) as catalyst. They applied a full CCD for 3 independent variables at two levels. Independent variables investigated for the responses of biodiesel yield and purity were initial catalyst concentration, the methanol-to-oil molar ratio, and temperature. The second-order models they developed to predict these responses were significant. Their results revealed that the operating conditions of a temperature of 25°C, a catalyst concentration of 1.3% wt, and a 6:1 methanol-to-oil molar ratio could give maximum purity and yield of 100 and 98.4%, respectively.
Dwivedi and Sharma (2015) conducted an optimization study to maximize the biodiesel yield from Pongamia oil. They used a Box–Behnken design with 4 factors, viz., the methanol-to-oil ratio, reaction time, reaction temperature, and the amount of KOH catalyst, to study the response pattern and to determine the optimum combination of these factors. The model developed was significant, validating its reliability in establishing a correlation between the process variables and the Pongamia biodiesel yield. They found that a biodiesel yield of 98.4% was achievable with a methanol-to-oil ratio of 11.06 using 1.43% w/w KOH catalyst in 81.4 min at a temperature of 56.6°C.
Two optimization tools were used by Betiku et al. (2014) in their study on biodiesel produced from non-edible Neem (Azadirachta indica) seed oil. They used the response surface methodology (RSM) to optimize the esterification process followed by the transesterification process where artificial neural netstudys (ANN) was used. The esterification reaction was catalyzed by H2SO4, which reduced the acid value of Neem oil from 10.18 mg KOH/g oil to less than 2 mg KOH/g oil. A potassium hydroxide (KOH) catalyst was then used in the transesterification reaction giving a biodiesel yield of 98.7% at a catalyst concentration of 1.01%, temperature of 48.15°C, and the methanol-to-oil ratio of 0.200 in a time interval of 42.9 min.
The model developed by Mendonça et al. (2011) using the Doehlert matrix had a good predictive performance for both the chosen responses of biodiesel purity and yield. They first applied the 2-level full factorial design to establish the factors with greater influence on the beef tallow biodiesel purity and yield. Thereafter a full optimization study was carried out using the Doehlert matrix method. To find the critical point of the second-order equation developed, they use the Lagrange criterion. From the factorial design they found the methanol-to-oil ratio and KOH catalyst to have had greater influence on tallow biodiesel purity and yield and selected these factors for the Doehlert optimization. Reaction time and temperature were less significant in factorial design optimization hence were fixed at their minimum, 20 min and 50°C, respectively, in the Doehlert matrix. The Lagrange criterion revealed that, according to the quadratic model obtained, the point of highest purity was at a methanol-to-oil ratio of 9.3 and KOH catalyst concentration of 3.49 wt%. The optimized models developed from the Doehlert matrix showed that 99.4% purity and 88.4% yield could be obtained when the reaction conditions are: Methanol-to-oil ratio = 7.5, KOH catalyst concentration = 1.5 wt%, reaction time = 20 min, and temperature = 50°C.
Results and Discussion
Catalyst Characterization
The calcined catalyst was characterized using the X-ray diffraction (XRD) analyses to establish the phases and measure the crystalline sizes; the scanning electron microscopy (SEM) to evaluate the catalyst’s surface topography and composition, and the transmission electron microscopy (TEM) that provided morphological, compositional, and crystallographic information on the catalyst.
Supplementary Figure 1 provided in supplemental materials shows the X-ray diffraction profile obtained from the measurements carried on the SO42–/ZrO2 catalyst. The main phase was found to be ZrO2, which matched the tetragonal lattice pattern (red lines). The tetragonal phase was predominant at 2θ of 30.5°, and Baddeleyite, a monoclinic ZrO2 phase (powder blue lines), was mostly found at 2θ of 28.2°. The presence of both phases (with a dominant monoclinic phase) in the crystal lattice indicated that the doped sulfate ions did not successfully influence the phase modification of zirconia from the thermodynamically more stable monoclinic phase to the metastable tetragonal phase. For this reason, the synthesized SO42–/ZrO2 catalyst was observed to be highly active in catalyzing only the esterification reaction and not the transesterification reaction.
Morphological studies on the catalyst were performed using the TEM and its composition was analyzed using the SEM. Supplementary Figure 2 (Supplemental materials) shows the morphology of SO42–/ZrO2 catalyst calcined at 620°C for 4 h. Highly packed crystal morphology with irregularly arranged ZrO2 aggregation was observed. There was a high loading amount of Zr in the catalyst structure as proven by a 61.78 mass% Zr from the elemental analysis of the catalyst (Table 3). The presence of all the constituent atoms (Zr, O, and S) that make sulfated zirconium catalyst was confirmed by spectrum 1 in Supplementary Figure 3 (Supplemental materials). The spectrum was developed from a randomly picked area on the face of the sample (Supplementary Figure 3). Because of its rather low mass and abundance in the catalyst, the concentration of sulfur was low and in some spot spectra (spectra 2 and 5 on Table 3) of Supplementary Figure 3 remain undetected (Figure 6). To determine the concentration of sulfates and, hence, the acidity and activity of sulfated zirconium catalyst, other methods are usually employed. The mean diameter of the monoclinic zirconia crystals is ± 30 nm while that of the tetragonal crystals is ± 200 nm (Miranda M et al., 2015). In Supplementary Figure 4, the TEM micrographs show the sizes of most of the crystals in the SO42–/ZrO2 sample to range between 10 and 100 nm, indicating an overwhelming presence of the monoclinic phase.
Biodiesel (FAME) Characterization
A PerkinElmer Clarus® 580 Gas Chromatograph equipped with a Clarus® SQ 8S Mass Spectrometer (GC-MS) was used to measure the percentage purity (% P) of FAME samples. The gas chromatograph (GC) used has a 30 m length PerkinElmer Elite-5MS II capillary column of 0.5 µm film thickness and 0.25 mm inner diameter. The stationary phase in the column selected is a low polarity 5% diphenyl/95% dimethyl polysiloxane, and the mobile phase is pure helium (He), flowing at 1 ml/min, used as carrier gas.
The FAME sample of ±100 µL was dissolved in 10 ml of ethanol and a 1 µL volume of the diluted sample was injected into the GC. Methyl heptadecanoate was used as an internal FAME standard. The oven temperature was initially kept at 140°C for 5 min and ramped up at 4 °C/min to a maximum of 240°C for a total run time of 31 min. The sampling rate was maintained at 1.5625 pts/s enabling the detector to capture enough data points across very narrow peaks. The purity of FAME was then determined from the chromatographic peak areas using the following formula (Jeong et al., 2009):
where,
The FAME analysis method described above, that employs Eq. 3, was adopted in this study as it is the most preferred when the quantity (purity) rather than the quality (composition) of FAME is being investigated in biodiesel synthesis. But, when the composition of FAME in the biodiesel test sample is of an essence, FAME standards of known concentration are used to plot calibration curves which are then used in the determination of individual methyl esters.
The concentration and volume of the internal standard (methyl heptadecanoate) were 33 mg/ml and 100 μL, respectively. The peak area (
Optimization Procedure
At the end of the experiments, the data collected was subjected to an optimization study to find the optimum operating conditions for both the esterification and the transesterification processes. Henceforth, the optimization studies of these processes will be referred to as OPTIMA1 and OPTIMA2, respectively. An optimization study further carried out to find a set of optimum independent variables that could simultaneously satisfy both optimum values of FAME yield and FAME purity obtained in OPTIMA2 will be referred to as OPTIMA3. Thereafter, the response surface methodology (RSM), that employs the central composite design (CCD) and analysis of variance (ANOVA) techniques, was employed in these studies.
The CCD was applied with three design factors, viz., catalyst concentration
For both processes (OPTIMA1 and OPTIMA2), 23 full-factorial rotatable CCD designs for three independent variables at five levels were employed and the total number of experiments conducted was 2 × 20, including axial and replicate experimental runs. Experiments were performed in a randomized order to balance out the effect of any nuisance variable that may influence the observed response (Montgomery and Runger, 2010). The Design-Expert® version 10 software was used to design the experiments for regression and graphical analyses of the data obtained. Acid values obtained in OPTIMA1 and the FAME yield and purity obtained in OPTIMA2 and OPTIMA3 were all taken as responses of the designed experiments.
Statistical analysis of the model was performed to evaluate the analysis of variance (ANOVA). The Fisher’s F-test was performed to test the significance of adding quadratic terms to the two-factor interaction (2FI) model. Ideally a small p-value (Prob>F less than 0.05) is desirable as it indicates that the addition of these (quadratic) terms has contributed to an improvement in the model. The goodness of fit of the model was evaluated by the determination coefficient (R2), adjusted determination coefficient (Adj. R2), and the coefficient of variation (C.V.).
The coefficient of variation (C.V.) or most commonly known as the relative standard deviation is the standard deviation expressed as a percentage of the mean and is crucial in measuring the reproducibility of the model. Predicted R2 is a measure of how well the model predicts a response value and adjusted R2, on the other hand, measures the amount of variation around the mean that is explained by the model. For the model to fit the collected data, the predicted R2 (Pred. R2) value must be in reasonable agreement with the adjusted R2 (Adj. R2) value by not more than 0.2 point difference. The adequate precision (Adeq. Precision) measures the signal-to-noise ratio and should ideally be greater than 4. A value greater than 4 is desirable as it indicates that the developed model has a high degree of precision and can thus be used to navigate the entire design space.
From the developed quadratic regression model, a combination of independent variables
In OPTIMA1, an acid value of 2.963 and a reaction temperature of 64°C were used as constraints to reduce the number of plausible optimum set. FAME yield of 84.51% and FAME purity of 90.66% obtained in OPTIMA2 and reaction temperature of 63.5°C were selected as constraints for use in OPTIMA3. The choice of the final optimum set of independent variables was based on process economics, that is, reduced temperatures and low levels of catalyst usage.
Overlay plots were drawn, in graphical optimization, to display the areas of feasible response values within the factor space, and with “flag inserts” to show the optimum solution set. In the overlay plots shown in Figure 3, the region colored in green (1) represents a region where graphical optimization solutions that meet the specific criteria can be found. The gray region (2) represents the graph area with solutions outside of model prediction. The region colored in red (3) represents the graph area outside the interval bound for at least one response.
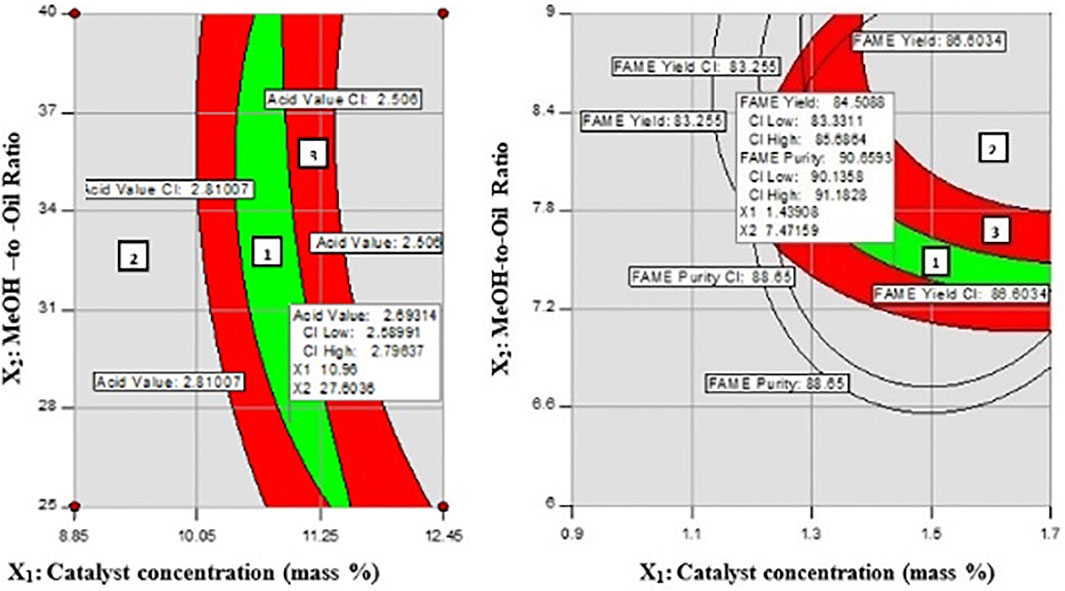
FIGURE 3. Overlay plots of independent variables satisfying targeted optimum response of: (A) acid value =2.693 mg KOH/g bound by 64°C reaction temperature constraint; (B) FAME yield and FAME purity bound by 63.50°C reaction temperature constraint.
Optimization of the Esterification Process (OPTIMA1)
High acid value of Croton gratissimus oil (21.455 mg KOH/g) necessitated that an esterification reaction be conducted prior to the main transesterification reaction. This was done in order to reduce the acid value of the extracted oil to below 4 mg KOH/g of oil. The effects of catalyst concentration

TABLE 5. Independent variables and levels used for the CCRD in the esterification and transesterification processes.
Table 6 gives the results of acid value reduction for the 20 experimental runs carried out to find the optimum conditions for the esterification process. To evaluate the accuracy of the model in predicting the response values that match the actual experimental values, various statistical parameters are provided in Table 7.
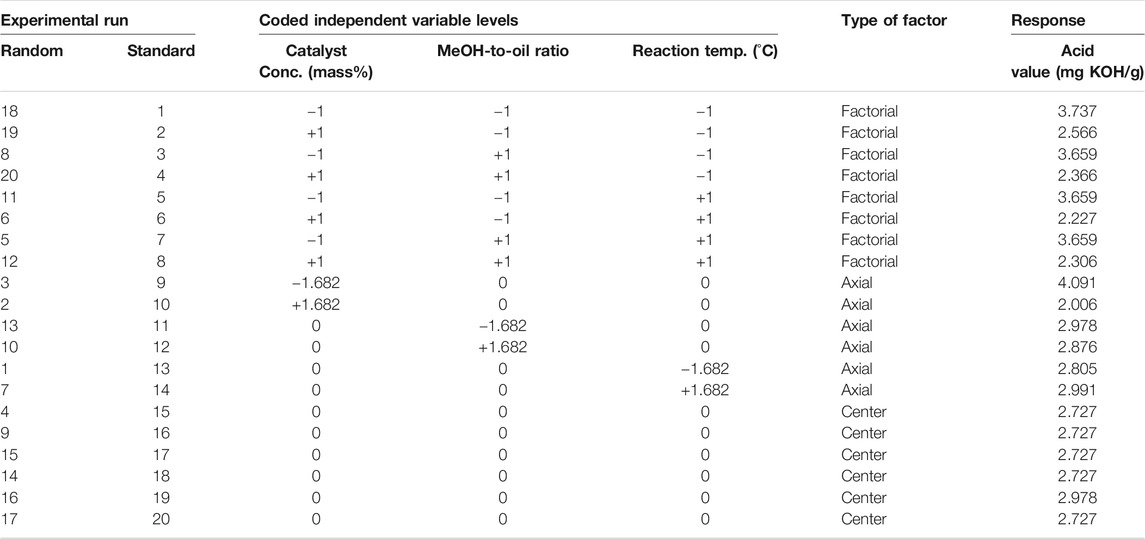
TABLE 6. Central composite rotatable design (CCRD) arrangement and responses for the acid value reduction.
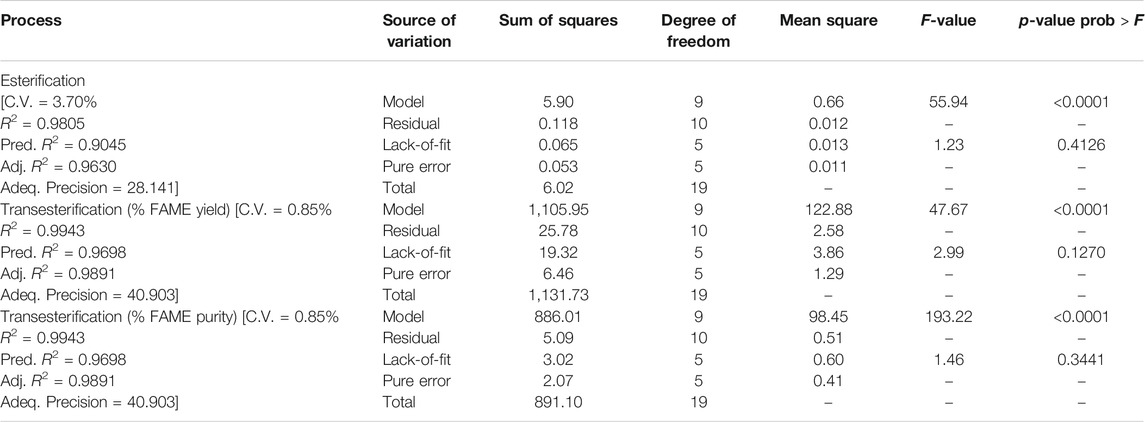
TABLE 7. ANOVA results for the models related to the esterification and transesterification processes.
The developed model was able to predict most of the response values as the points on the plot lie in close proximity to the 45° diagonal line (Figure 4).
The experimental data obtained in the esterification process was analyzed by the ANOVA and is best described by the following quadratic regression model:
where
The ANOVA results in Table 7 showed the significant nature of the developed quadratic regression model with a reasonably low probability value, Prob > F: (p-value) < 0.0001. The Fisher’s F-test gave an F value for the model of 55.94, indicating a less than 0.01% chance that an F value this large could be due to noise. The lack-of-fit with an F-value of 1.23 implied that the lack-of-fit was not significant and was proof that the model developed adequately represented the collected data. The value of the coefficient of determination (R2) was found to be 0.9805, indicating that only 0.20% of the total variations was not explained by the developed regression model. The predicted R2 of 0.9045 was in reasonable agreement with the adjusted R2 of 0.9630 with only an acceptable difference of less than 0.20. The developed model had a high degree of precision as the adequate precision found was high enough at 28.141. The coefficient of variation (C.V.) of 3.70% indicated that the model was reproducible.
From the developed model, an acid value of 2.693 mg KOH/g could be obtained when operating the process under optimum conditions of 10.96 mass% catalyst concentration, 27.60 methanol-to-oil ratio, and a reaction temperature of 64°C. The 91% reduction in the acid value of Croton gratissimus oil (based on the lowest experimental value obtained) achieved in this esterification step could positively influence the reaction extent in the next transesterification process step. Figure 4 also shows surface plots of the effects of catalyst concentration, the methanol-to-oil ratio, and the reaction temperature on the acid value of Croton gratissimus oil during the esterification process. The amount of catalyst used had the most significant effect on the acid value of oil. This is shown by the almost flat-shaped response surfaces obtained for the methanol- to-oil ratio and reaction temperature on the acid value when the catalyst concentration was kept constant at 10.96 mass% (Figure 4). The focus of the esterification reaction was on the use of the sulfated zirconia, SO42–/ZrO2 in its current form as a predominantly monoclinic phase and evaluating its effectiveness in converting free fatty acids to di and monoglycerides. For this reason, a much wider range of catalyst concentration, between 6 and 14 mass%, was selected for the study whilst feeding methanol in excess (more than the stoichiometric amount). Arora et al. (2015) in their study on the esterification of high free fatty acid rice bran oil found out that there was no significant increase in the FFA conversion when the methanol-to-oil ratio was increased beyond 20. In the current study, methanol was fed in a range of between 20 and 40:1 to rule it out as the contributing factor, should there be low or no conversion of FFA at the end of the reaction.
The amount of the SO42–/ZrO2 catalyst used in the esterification reaction was found to have the most significant effect in the reduction of the acid value of Croton gratissimus oil from 21.455 mgKOH/g to an average of 2.927 mg KOH/g oil. The highest and lowest acid values were obtained when the same operating conditions of temperature (70°C) and the methanol-to-oil ratio (32.50) whilst more than doubling the catalyst concentration from 6 to 14 mass% (Table 6 standard experimental run 9 and 10). This dependency of the esterification reaction on the catalyst concentration was consistent with the observations by Kumar Tiwari et al. (2007). Their optimized RSM model for biodiesel produced from high FFA Jatropha curcas oil showed that catalyst concentration was the most significant factor (followed by the methanol-to-oil ratio) in the conversion efficiency of free fatty acids (FFA) in oil.
Within the lower limit of the 95% confidence interval, the developed quadratic model predicted an optimum acid value of 2.693 mg KOH/g of oil when the esterification process was operated at 10.96 mass% catalyst concentration, 27.60 methanol-to-oil ratio, and 64°C reaction temperature. In a two-step biodiesel production process, Muthu et al. (2010) converted Azadirachta indica A. Juss oil to biodiesel using SO42–/ZrO2 and KOH as catalysts in the esterification and transesterification reactions, respectively. From an unoptimized process operating at the methanol-to-oil ratio of 9:1, catalyst concentration of 1%, reaction time of 2 h, and reaction temperature of 65°C, they obtained a 94% FFA conversion efficiency in the esterification step with a predominantly tetragonal-phased SO42–/ZrO2 catalyst.
Optimization of the Transesterification Process (OPTIMA2)
Independent variables selected for an investigation in the optimization of the transesterification process were catalyst concentration
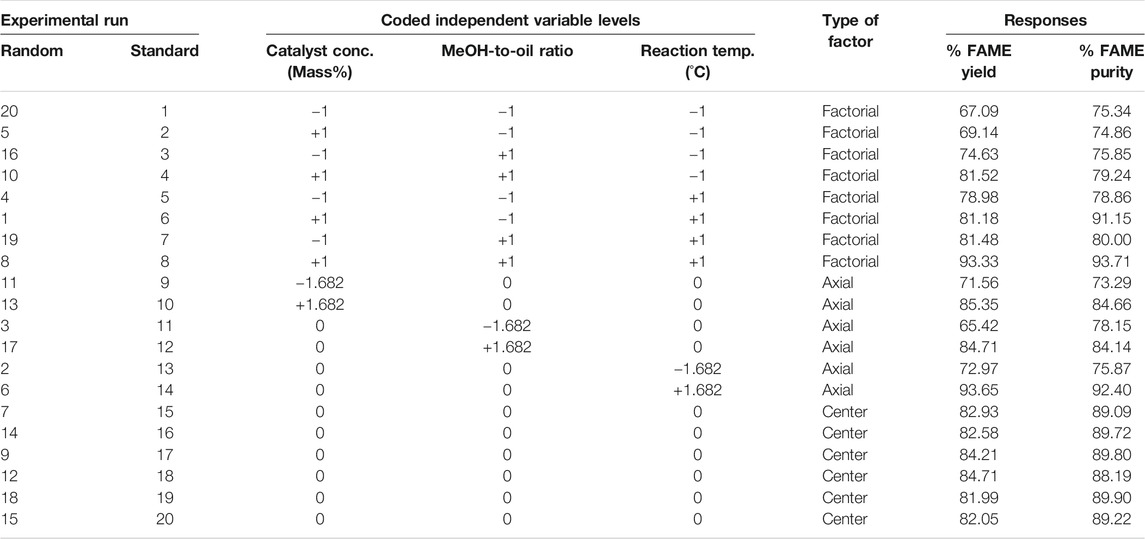
TABLE 8. Central composite rotatable design (CCRD) arrangement and responses for the transesterification Process.
Response 1: Percentage FAME Yield
The transesterification experiments conducted revealed that the highest FAME yield of 93.65% was achievable when the reactor was operated at 1.30 mass% catalyst concentration, 7.5 methanol-to-oil ratio, and 80°C reaction temperature. The lowest FAME yield was found to be 65.42% at 1.30 mass% catalyst concentration, 5 methanol-to-oil ratio, and 62.50°C reaction temperature. It is important to note that these values of % FAME yield were obtained from the experimental data collected before carrying out a full optimization study. The experimental data obtained for % FAME yield in the transesterification process was analyzed by the ANOVA and can be described by the following quadratic regression model:
where
Equation 5 shows all 3 linear terms as positive, meaning that they all had a positive effect on the percentage FAME yield. An increase in the catalyst concentration, the methanol-to-oil ratio, or reaction temperature resulted in an increase in the percentage FAME yield. But larger magnitudes of the coefficient of the methanol-to-oil ratio (p-value < 0.0001) when compared to the magnitudes of the coefficients of the other two independent variables indicated that the methanol-to-oil ratio was the most significant independent variable in controlling the transesterification process for an optimum FAME yield.
Table 7 also shows the results of the ANOVA for the developed quadratic model. The ANOVA showed that the quadratic regression model (Eq. 5) was significant. This was evident from the Fisher’s F-test which gave an F value for the model of 47.67 with a very low probability value (p-value < 0.0001). The value of R2 was found to be 0.9772, indicating that only 0.23% of the total variations was not explained by the developed regression model. The predicted R2 of 0.8571 was in reasonable agreement with the adjusted R2 of 0.9567. The lack-of-fit F-value of 2.99 implied that the lack-of-fit was not significant and that there was a 12.70% chance that a lack-of-fit that large could occur due to noise. The adequate precision was also evaluated and found to be high enough at 24.79. This meant that the developed model had a high degree of precision. The C.V. of 2.01% indicated that the model was reproducible. It was found from the developed quadratic model (Eq. 5) that an optimum % FAME yield of 84.51% could be obtained under the following operating conditions: 1.22 mass%, catalyst concentration, 7.3 methanol-to-oil ratio, and 68°C reaction temperature. Surface plots shown in Figure 5 explain the behavior of the developed process when the optimum values of the catalyst concentration, the methanol-to-oil ratio, and the reaction temperature are individually fixed.
The significant factors in the transesterification reaction for the optimum FAME yield were the methanol-to-oil ratio and KOH catalyst concentration, the former having the most effect. At higher methanol-to-oil ratios (greater than stoichiometric values), reactions proceed faster, giving higher FAME yields. But excessive amounts of methanol in the reaction mixture result in the formation of water and soaps, inevitably leading to substantial loss of esters. In this study, this sudden decline in FAME yield was observed at a methanol-to-oil ratio of 8.47 that gave 86.97% FAME yield (shown on the Flag insert in Figure 5). Beyond this point, an increase in the methanol-to-oil ratio caused a decrease in the % FAME yield. Similar surface response plots are shown in Figure 5.
The catalyst concentration also seemed to have a positive influence on the FAME yield, but up to a catalyst concentration of 1.74 mass% that gave 85.07% FAME yield. A decline in the FAME yield was observed beyond this point (Figure 5). These observations are in agreement with the study by Dwivedi and Sharma (2015). In their study on the optimization of FAME yield from the KOH-catalyzed synthesis of biodiesel from Pongamia oil, they discovered a strong relationship between catalyst concentration and the molar ratio of the methanol-to-oil. Biodiesel yield increased with increasing amounts of catalyst and methanol in the reaction mixture. They also noted a reverse in the trend when the amounts of these independent variables reached certain values.
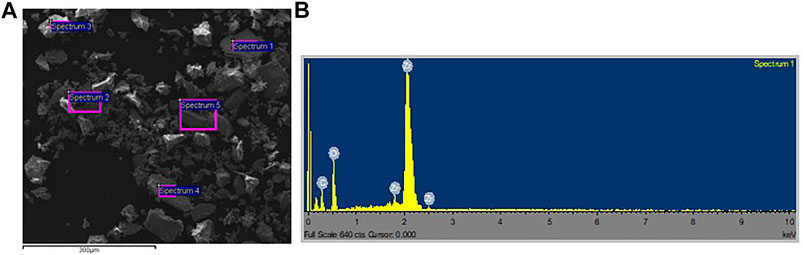
FIGURE 6. (A) SEM micrograph of SO42−/ZrO2 catalyst calcined at 620°C. (B) SEM – EDS Spectra for the Elemental Composition of the SO42−/ZrO2 catalyst.
The results of the transesterification experiments performed, with the exception of standard experimental runs 8 and 14 (Table 8), gave an average FAME yield of 78.47% (based on triglycerides fed only) evaluated over a range of set factor limits. This is lower than the theoretically attainable maximum FAME yield of 90.47% (based on the reactor feed); a value derived from the mass balance of Croton gratissimus biodiesel process. Certainly, there still is a potential of improving FAME yield beyond what was achieved in this optimization study, and since KOH catalyst and methanol, both fed in excess, had significant effects in controlling the transesterification reaction, a reduction in the amounts of these two reactants could eliminate the problems associated with their excessive usage.
In the transesterification of Croton gratissimus oil, the amount of KOH catalyst added into the reaction mixture had a significant influence on both the extent of reaction and the ease of separation of the final products. In this study, caution was, therefore, exercised in the amount of catalyst used in this reaction as the addition of high quantities of KOH catalyst in an effort to compensate for possible low reaction rates could result in the formation of emulsions that could inadvertently increase the viscosity of the reaction mixture (Crabbe et al., 2001). Moreover, high concentrations of KOH catalyst in the reaction mixture promote the formation of water as the hydroxides combine with methanol. This leads to the hydrolysis of the methyl esters already formed, resulting in soap formation in an undesired saponification reaction (Hameed et al., 2009). The presence of soap in the final products has a tendency of reducing the FAME yield to below the theoretical maximum and making the separation of glycerol from biodiesel product difficult to manage.
Response 2: Percentage FAME Purity
Experimental conditions that gave the highest and lowest percentage FAME purity were noted, before carrying out a full optimization study. From the experiments carried out in the transesterification of Croton gratissimus oil, the highest FAME purity of 93.71% was obtained when the reactor was operated at 1.7 mass% catalyst concentration, 9 methanol-to-oil ratio, and 73°C reaction temperature, and the lowest FAME purity was found to be 73.29% when operating the reactor at 0.65 mass% catalyst concentration, 7.5 methanol-to-oil ratio, and 62.50°C reaction temperature. The experimental data obtained for percentage FAME purity in the transesterification process was analyzed by the ANOVA and can be described by the following quadratic regression model:
where
The ANOVA showed that the quadratic regression model (Eq. 6) was significant. This was evident from the Fisher’s F-test which gave an F value for the model of 193.22 with a very low probability value (p-value < 0.0001). The value of the coefficient of determination (R2) was found to be 0.9943, indicating that only 0.06% of the total variations was not explained by the developed regression model. The predicted R2 of 0.9698 was in reasonable agreement with the adjusted R2 of 0.9891. The lack-of-fit F-value of 1.46 implied that the lack-of-fit was not significant and that there was a 34.41% chance that a lack-of-fit that large could occur due to noise. The adequate precision was also evaluated and found to be high enough at 40.90. This meant that the developed model had a high degree of precision. The coefficient of variation (C.V.) of 0.85% indicated that the model was reproducible.
From the developed quadratic model (Eq. 6), it was found that an optimum % FAME purity of 90.66% could be obtained under the following operating conditions: 1.2 mass% catalyst concentration, 7.8 methanol-to-oil ratio, and 66°C reaction temperature. Surface plots (not shown in this article) explain the behavior of the developed process when the optimum values of the catalyst concentration, the methanol-to-oil ratio, and the reaction temperature are individually fixed. In the transesterification of the pretreated Croton gratissimus oil, the purity of FAME depended mostly on the catalyst concentration and the amount of methanol fed into the reaction mixture. An increase in both these independent variables resulted in an increase in the purity of FAME produced. But at an optimum FAME purity of 92.49%, the catalyst concentration and the methanol-to-oil ratio reached their peak values of 1.57 mass% and 7.96, respectively. Beyond these maximum values, a sharp decline in the percentage FAME purity was observed. Vincente et al. (2007) made the same observations in their study on the optimization of biodiesel production from sunflower oil using KOH as a transesterification catalyst. Their statistical analysis identified the initial catalyst concentration and the methanol-to-oil ratio as the most important factors in FAME purity response. According to their results, FAME purity reached its maximum value (virtual 100%) at the maximum catalyst concentration of 1.5 mass%, thereafter reaching a stability region (Vicente et al., 2007).
Combined Model Optimization (OPTIMA3)
The two quadratic models developed for the transesterification process predicted two sets of factor values for catalyst concentration, the methanol-to-oil ratio, and reaction temperature corresponding to the optimum values of the 2 responses, FAME yield and FAME purity. Because the transesterification process is but one process, it must be described by one set of variable values for the attainment of these optimum responses. A combined model was, therefore, developed for the optimum set of independent variables that gave responses of FAME yield and FAME purity within the region of 95% confidence interval (95% CI). This set of independent variables had to simultaneously satisfy the optimum responses obtained in OPTIMA2.
Numerical optimization techniques, that use the response targeting approach bound by constraints and the graphical optimization technique that utilizes overlay plots to display regions of feasible responses that fit the optimization criteria, were employed. This task was achieved by overlaying critical response contours on a contour plot (overlay plot) after targeting optimum responses from OPTIMA2 and using constraints to narrow down the search for the optimum set. Reaction temperatures ranging between 63.50 and 64°C (below 64.50°C, the boiling point temperature of methanol) and low catalyst concentration between 10.50 and 10.98 mass% for OPTIMA1 and 1.40 and 1.60 mass% for OPTIMA3, were used as constraints. The choice of these constraints was based on process economics. From the combined model optimization, it was found that when the transesterification process is operated at 1.439 mass% catalyst concentration, 7.472 methanol-to-oil ratio, and 63.50°C reaction temperature, 84.51% FAME yield and 90.66% FAME purity could be achieved. These independent variables were, therefore, taken as the optimum set that satisfies optimum responses predicted by the developed models.
Conclusion
The monoclinic sulfated zirconia, SO42–/ZrO2 catalyst has high acid strength and exhibits high catalytic activity; both qualities found in the tetragonal-phased type catalyst. But the monoclinic type, with low levels of anion repulsion, is more susceptible to sulfate doping than its counterpart. This makes the monoclinic-phased catalyst the most preferred form to catalyze the esterification reaction that require high acid activity. In the esterification of Croton gratissimus oil, the monoclinic SO42–/ZrO2 catalyst offered a 91% reduction in the acid value of oil, contributing immensely to the high yield and purity of FAME produced in the transesterification process. The RSM model developed for the esterification process showed that the acid value of Croton gratissimus oil could be reduced from 21.455 mg KOH/g to an optimum 2.693 mg KOH/g when the process is operated at 10.96 mass% catalyst concentration, 27.60 methanol-to-oil ratio, and 64°C reaction temperature.
The optimization models developed for the transesterification process in this study have demonstrated sufficient degree of accuracy in predicting the Croton gratissimus biodiesel yield and the purity of its FAME. These two regression models were combined to give one set of optimum operating conditions for the attainment of the two responses. Operating conditions selected were from a wide range of process parameters found within the experimental domain in the optimum region. The selection was based on process constraints of energy consumption and resource utilization, considered as important factors in the economic viability of biodiesel processes. For this reason, the final process chosen for development was the one that gave the desired optimum responses from minimal use of catalyst and methanol whilst operating at moderate conditions of temperature. The combined model predicted, therefore, that when this transesterification process is operated at 1.439 mass% catalyst concentration, 7.472 methanol-to-oil ratio, and at a reaction temperature of 63.50°C, an optimum FAME yield of 84.51% and a FAME purity of 90.66% is achievable.
On the basis of the data collected and the results obtained in this study, Croton gratissimus crop has proven to be a good feedstock for biodiesel production processes in the Republic of South Africa and beyond.
Data Availability Statement
The original contributions presented in the study are included in the article/Supplementary Material; further inquiries can be directed to the corresponding author.
Author Contributions
PJ: conceptualization, methodology, experimental investigation, software, and original draft preparation. KT: conceptualization, validation, data curation, supervision, and project administration. PM: supervision, project administration, and reviewing and editing.
Conflict of Interest
The authors declare that the research was conducted in the absence of any commercial or financial relationships that could be construed as a potential conflict of interest.
Publisher’s Note
All claims expressed in this article are solely those of the authors and do not necessarily represent those of their affiliated organizations, or those of the publisher, the editors and the reviewers. Any product that may be evaluated in this article, or claim that may be made by its manufacturer, is not guaranteed or endorsed by the publisher.
Supplementary Material
The Supplementary Material for this article can be found online at: https://www.frontiersin.org/articles/10.3389/fenrg.2021.646229/full#supplementary-material
References
Ahmadi, M., Vahabzadeh, F., Bonakdarpour, B., Mofarrah, E., and Mehranian, M. (2005). Application of the central Composite Design and Response Surface Methodology to the Advanced Treatment of Olive Oil Processing Wastewater Using Fenton's Peroxidation. J. Hazard. Mater. 123, 187–195. doi:10.1016/j.jhazmat.2005.03.042
Aransiola, E. F., Ojumu, T. V., Oyekola, O. O., Madzimbamuto, T. F., and Ikhu-Omoregbe, D. I. O. (2014). A Review of Current Technology for Biodiesel Production: State of the Art. Biomass and Bioenergy 61, 276–297. doi:10.1016/j.biombioe.2013.11.014
Arora, R., Toor, A. P., and Wanchoo, R. K. (2015). Esterification of High Free Fatty Acid Rice Bran Oil: Parametric and Kinetic Study. Chem. Biochem. Eng. Q. 29, 617–623.
Atabani, A. E., Silitonga, A. S., Badruddin, I. A., Mahlia, T. M. I., Masjuki, H. H., and Mekhilef, S. (2012). A Comprehensive Review on Biodiesel as an Alternative Energy Resource and its Characteristics. Renew. Sustain. Energ. Rev. 16, 2070–2093. doi:10.1016/j.rser.2012.01.003
Atabani, A. E., Silitonga, A. S., Ong, H. C., Mahlia, T. M. I., Masjuki, H. H., Badruddin, I. A., et al. (2013). Non-edible Vegetable Oils: A Critical Evaluation of Oil Extraction, Fatty Acid Compositions, Biodiesel Production, Characteristics, Engine Performance and Emissions Production. Renew. Sustain. Energ. Rev. 18, 211–245. doi:10.1016/j.rser.2012.10.013
Bahadur, I., Bux, F., Guldhe, A., Tumba, K., Singh, B., Ramjugernath, D., et al. (2014). Assessment of Potential of Croton Gratissimus Oil for Macroscale Production of Biodiesel Based on Thermophysical Properties. Energy Fuels 28, 7576–7581. doi:10.1021/ef502270v
Baş, D., and Boyacı, İ. H. (2007). Modeling and Optimization I: Usability of Response Surface Methodology. J. Food Eng. 78, 836–845.
Berrios, M., and Skelton, R. L. (2008). Comparison of Purification Methods for Biodiesel. Chem. Eng. J. 144, 459–465. doi:10.1016/j.cej.2008.07.019
Betiku, E., Omilakin, O. R., Ajala, S. O., Okeleye, A. A., Taiwo, A. E., and Solomon, B. O. (2014). Mathematical Modeling and Process Parameters Optimization Studies by Artificial Neural Network and Response Surface Methodology: A Case of Non-edible Neem (Azadirachta indica) Seed Oil Biodiesel Synthesis. Energy 72, 266–273. doi:10.1016/j.energy.2014.05.033
Chen, F. R., Coudurier, G., Joly, J. F., and Vedrine, J. C. (1993). Superacid and Catalytic Properties of Sulfated Zirconia. J. Catal. 143, 616–626. doi:10.1006/jcat.1993.1304
Chouhan, A. P. S., and Sarma, A. K. (2011). Modern Heterogeneous Catalysts for Biodiesel Production: A Comprehensive Review. Renew. Sustain. Energ. Rev. 15, 4378–4399. doi:10.1016/j.rser.2011.07.112
Crabbe, E., Nolasco-Hipolito, C., Kobayashi, G., Sonomoto, K., and Ishizaki, A. (2001). Biodiesel Production from Crude palm Oil and Evaluation of Butanol Extraction and Fuel Properties. Process Biochem. 37, 65–71. doi:10.1016/s0032-9592(01)00178-9
Dwivedi, G., and Sharma, M. P. (2015). Application of Box-Behnken Design in Optimization of Biodiesel Yield from Pongamia Oil and its Stability Analysis. Fuel 145, 256–262. doi:10.1016/j.fuel.2014.12.063
Ferreira, S. L. C., Bruns, R. E., Da Silva, E. G. P., Dos Santos, W. N. L., Quintella, C. M., David, J. M., et al. (2007a). Statistical Designs and Response Surface Techniques for the Optimization of Chromatographic Systems. J. Chromatogr. A 1158, 2–14. doi:10.1016/j.chroma.2007.03.051
Ferreira, S. L. C., Bruns, R. E., Ferreira, H. S., Matos, G. D., David, J. M., Brandão, G. C., et al. (2007b). Box-Behnken Design: An Alternative for the Optimization of Analytical Methods. Analytica Chim. Acta 597, 179–186. doi:10.1016/j.aca.2007.07.011
Hameed, B. H., Lai, L. F., and Chin, L. H. (2009). Production of Biodiesel from palm Oil (Elaeis Guineensis) Using Heterogeneous Catalyst: An Optimized Process. Fuel Process. Technol. 90, 606–610. doi:10.1016/j.fuproc.2008.12.014
Jeong, G.-T., Yang, H.-S., and Park, D.-H. (2009). Optimization of Transesterification of Animal Fat Ester Using Response Surface Methodology. Bioresour. Technol. 100, 25–30. doi:10.1016/j.biortech.2008.05.011
Jiyane, P. C., Tumba, K., and Musonge, P. (2018). Optimisation of Croton Gratissimus Oil Extraction by N-Hexane and Ethyl Acetate Using Response Surface Methodology. J. Oleo Sci. 67, 369–377. doi:10.5650/jos.ess17197
Kostić, M. D., Joković, N. M., Stamenković, O. S., Rajković, K. M., Milić, P. S., and Veljković, V. B. (2013). Optimization of Hempseed Oil Extraction by N-Hexane. Ind. Crops Prod. 48, 133–143.
Kumar, M., and Sharma, M. P. (2015). Assessment of Potential of Oils for Biodiesel Production. Renew. Sustain. Energ. Rev. 44, 814–823. doi:10.1016/j.rser.2015.01.013
Kumar Tiwari, A., Kumar, A., and Raheman, H. (2007). Biodiesel Production from Jatropha Oil (Jatropha Curcas) with High Free Fatty Acids: An Optimized Process. Biomass and Bioenergy 31, 569–575. doi:10.1016/j.biombioe.2007.03.003
Li, H., Pordesimo, L., and Weiss, J. (2004). High Intensity Ultrasound-Assisted Extraction of Oil from Soybeans. Food Res. Int. 37, 731–738. doi:10.1016/j.foodres.2004.02.016
Madras, G., Kolluru, C., and Kumar, R. (2004). Synthesis of Biodiesel in Supercritical Fluids. Fuel 83, 2029–2033. doi:10.1016/j.fuel.2004.03.014
Mendonça, D. R., Andrade, H. M. C., Guimarães, P. R. B., Vianna, R. F., Meneghetti, S. M. P., Pontes, L. A. M., et al. (2011). Application of Full Factorial Design and Doehlert Matrix for the Optimisation of Beef Tallow Methanolysis via Homogeneous Catalysis. Fuel Process. Technol. 92, 342–348. doi:10.1016/j.fuproc.2010.09.026
Miranda, M. C. D., Ramírez S., A. E., Jurado, S. G., and Vera, C. R. (2015). Superficial Effects and Catalytic Activity of ZrO2-So42− as a Function of the crystal Structure. J. Mol. Catal. A: Chem. 398, 325–335. doi:10.1016/j.molcata.2014.12.015
Montgomery, D. C., and Runger, G. C. (2010). Applied Statistics and Probability for Engineers. 5th Edition. Wiley.
Mulholland, D. A., Langat, M. K., Crouch, N. R., Coley, H. M., Mutambi, E. M., and Nuzillard, J.-M. (2010). Cembranolides from the Stem Bark of the Southern African Medicinal Plant, Croton Gratissimus (Euphorbiaceae). Phytochemistry 71, 1381–1386. doi:10.1016/j.phytochem.2010.05.014
Muthu, H., Sathyaselvabala, V., Varathachary, T. K., Kirupha Selvaraj, D., Nandagopal, J., and Subramanian, S. (2010). Synthesis of Biodiesel from Neem Oil Using Sulfated Zirconia via Tranesterification. Braz. J. Chem. Eng. 27, 601–608. doi:10.1590/s0104-66322010000400012
Reddy, B. M., Sreekanth, P. M., and Lakshmanan, P. (2005). Sulfated Zirconia as an Efficient Catalyst for Organic Synthesis and Transformation Reactions. J. Mol. Catal. A: Chem. 237, 93–100. doi:10.1016/j.molcata.2005.04.039
Sánchez-Arreola, E., Martin-Torres, G., Lozada-Ramírez, J. D., Hernández, L. R., Bandala-González, E. R., and Bach, H. (2015). Biodiesel Production and De-oiled Seed Cake Nutritional Values of a Mexican Edible Jatropha Curcas. Renew. Energ. 76, 143–147. doi:10.1016/j.renene.2014.11.017
Srinivasan, R., Keogh, R. A., Milburn, D. R., and Davis, B. H. (1995). Sulfated Zirconia Catalysts: Characterization by TGA/DTA Mass Spectrometry. J. Catal. 153, 123–130. doi:10.1006/jcat.1995.1114
Tan, I., Ahmad, A., and Hameed, B. (2008). Optimization of Preparation Conditions for Activated Carbons from Coconut Husk Using Response Surface Methodology. Chem. Eng. J. 137, 462–470. doi:10.1016/j.cej.2007.04.031
Vicente, G., Coteron, A., Martinez, M., and Aracil, J. (1998). Application of the Factorial Design of Experiments and Response Surface Methodology to Optimize Biodiesel Production. Ind. Crops Prod. 8, 29–35. doi:10.1016/s0926-6690(97)10003-6
Keywords: sulfated zirconia, RMS, optimization, Croton gratissimus, biodiesel production
Citation: Jiyane PC, Tumba K and Musonge P (2021) Production of Biodiesel From Croton gratissimus Oil Using Sulfated Zirconia and KOH as Catalysts. Front. Energy Res. 9:646229. doi: 10.3389/fenrg.2021.646229
Received: 25 December 2020; Accepted: 02 July 2021;
Published: 17 August 2021.
Edited by:
Amit Kumar, Massachusetts Institute of Technology, United StatesReviewed by:
Perumal Varalakshmi, Madurai Kamaraj University, IndiaJaime Puna, Lisbon Higher Institute of Engineering (ISEL), Portugal
Copyright © 2021 Jiyane, Tumba and Musonge. This is an open-access article distributed under the terms of the Creative Commons Attribution License (CC BY). The use, distribution or reproduction in other forums is permitted, provided the original author(s) and the copyright owner(s) are credited and that the original publication in this journal is cited, in accordance with accepted academic practice. No use, distribution or reproduction is permitted which does not comply with these terms.
*Correspondence: Kaniki Tumba, dHVtYmFAbXV0LmFjLnph