- Energy Storage Group, Energy Storage and Distributed Resources Division, Lawrence Berkeley National Laboratory, Berkeley, CA, United States
This procedure describes the setup and testing protocol for metal-supported solid oxide electrolysis cell (MS-SOEC) button cell performance evaluation. It defines a standard testing protocol, describes materials selection, and identifies common pitfalls for testing MS-SOEC button cells.
Introduction
This procedure describes the setup and testing of metal-supported solid oxide electrolysis cell (MS-SOEC) button cells. Many features are quite similar to the procedure for testing electrode-supported or electrolyte-supported SOECs. There are several key differences for MS-SOECs, however. The operating and sealing temperature limits are lower, as MS-SOECs with stainless steel supports should not be exposed to oxidizing conditions at temperatures that promote rapid chromia scale growth. The operating temperature is typically lower than 750°C for long term stability, and the maximum sealing temperature is around 850°C. For symmetric-architecture MS-SOECs with porous metal supports on both sides, the sealing surface is the thin face of the dense electrolyte on the edge of the cell. This makes compression seals difficult to implement, so glass paste or ceramic adhesive seals are preferred. Electrical leads can be directly spot-welded to the metal support, eliminating the challenges associated with applying paste-and-mesh current collectors.
Several groups globally have reported MS-SOEC steam electrolysis testing efforts, and the results were reviewed recently (Tucker, 2020). For oxide-conducting MS-SOECs, cells were operated in the temperature range 600–800°C with steam content ranging from 30 to 90%. Proton-conducting MS-SOECs were typically operated around 600°C, with some as low as 400°C. A range of test rig designs, materials, and sealing strategies were implemented. For example, a ceramic rig with Pt mesh current collectors and gold/glass sealing was used to test an oxide-conducting cell prepared by plasma spraying the electrolyte onto a stainless steel substrate (Schiller et al., 2009). A stainless steel rig with Pt mesh current collectors welded to the cell and glass sealing was used to test an oxide-conducting cell prepared by co-sintering and catalyst infiltration (Wang et al., 2019; Shen et al., 2020). A commercial Probostat test rig with Pt mesh and Pt paste current collector and compressed mica seal was used to test a proton-conducting cell prepared by pulsed laser deposition (Stange et al., 2017). In many cases the details of the test rig, sealing material, and test protocol were not reported.
The objectives of this procedure are to define a standard testing protocol, describe materials selection, and identify common pitfalls for testing MS-SOEC button cells. This procedure contains preparation and operation details specific to MS-SOECs, a discussion of seal and test rig materials, alternative sealing and start-up protocols for a metal test rig with glass seal or alumina test rig with ceramic adhesive seal, and a discussion of the consequences of off-normal operation.
Protocol Scope
Scope and Applicability
This procedure applies to sealing and operation of MS-SOEC button cells. Procedures for larger cells mounted with flowfields, manifolds, or interconnects can be adapted from this procedure but are not explicitly described. The procedure does not cover cell fabrication, rig design details, steam generator or humidifier designs, detailed electrochemical diagnostic, and operational techniques, or post-mortem analysis, many of which are covered in detail elsewhere in this issue. The step-by-step procedure was developed during the authors’ research on symmetric cells with oxide-conducting electrolyte and porous stainless steel supports on both sides. Variations in the procedure for other electrolyte and support materials or cell architectures may be necessary.
Summary of Method
The protocol provides for reproducible operation of MS-SOEC button cells at a variety of operating conditions. A pre-fabricated metal-supported solid oxide electrolysis cell is connected to a platinum or nickel mesh with conductive wire leads on the steam electrode side. Then the cell is sealed on a test rig (typically with glass paste or ceramic adhesive). Hydrogen is humidified to a specific steam content and delivered to the test rig via a heated tube. The MS-SOEC is then operated. A schematic setup with heated bubbler for controlling the steam:hydrogen ratio is shown in Figure 1.
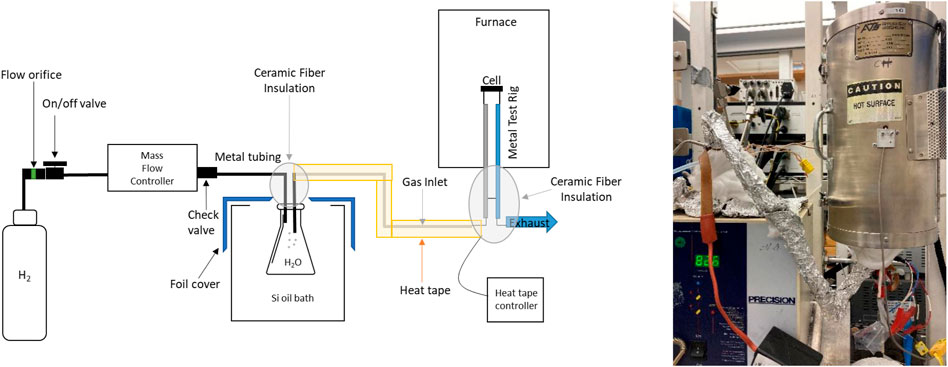
FIGURE 1. Schematic and photograph of a MS-SOEC test setup with a heated bubbler as the humidification system.
Personnel Qualifications/Responsibilities
Users must be trained on the safe handling and use of hydrogen, high-temperature furnaces, pressurized gas systems, and electrical systems. Users also need basic knowledge of electrochemistry and understanding of electrochemical characterization methods prior to implementing the procedure. Additional training or certification is required before modifying the setup or equipment, for example the Qualified Electrical Worker training.
Health and Safety Warning
H2 is flammable and explosive, with flammability occurring between the limits of 4.0 and 75.0% based on the volume of hydrogen in air at 1 atm. H2 cylinders should be secured away from the testing furnace or any other heat source. Metal tubing (not plastic) should be used for H2 and all tubing and connections should be leak-checked before normal operation. The testing furnace should be located in a fume hood or other ventilated area for increased safety in the case of a hydrogen leak. It is preferred to have a hydrogen gas sensor mounted in the lab area. Other hazards include: glassware which may become pressurized, electrical energy, hot steam, and hot surfaces. Follow guidelines of the research institute, fire marshal, and other regulatory bodies.
Equipment and Supplies
Examples of useful equipment and supplies are listed in Table 1. Many alternatives exist, but these items have been used successfully by the authors. Required equipment includes a furnace, electrochemical potentiostat, mass flow controller, humidification system, and gas delivery system for hydrogen. Optional equipment includes a gas delivery system for air, humidity meter (for example EE23, E + E Elektronik Ges.m.b.H, Germany) suitable for high absolute humidity, hydrogen sensor, and fume hood.
Options for the hydrogen humidification system include a heated bubbler, reaction of mixed oxygen, and excess hydrogen streams inside the test rig, a controlled evaporation mixer, vaporization chamber with low-flow liquid pump for water delivery, a pressurized vaporization chamber with restricted flow orifice, and a steam generator. Due to the low flowrates associated with button cell operation, the first two options are the most suitable, whereas the other options are preferred for large cells or stacks. Downstream of the hydrogen/steam mixing unit (for example a heated bubbler), all tubing and connections must be heated to above the dewpoint of mixture to eliminate condensation of liquid water. A temperature of ∼120°C is recommended. This can be accomplished with heat-traced lines or heating tapes wrapped around the lines. Junctions between lines and other fittings are common cold spots, and special attention must be paid to insulating or actively heating them.
Required materials include hydrogen, DI water, and a seal material. Optional materials include compressed air and an ink vehicle for glass powder such as terpineol.
The ubiquitous alumina tube test rig design used in research laboratories worldwide for SOFC/SOEC button cell testing can also be used for MS-SOEC testing, Figure 2A (Pomfret et al., 2008; Wu et al., 2017; Shen and Lu, 2018; Cui et al., 2021). A ceramic adhesive or sealing glass that wets and bonds to both the button cell and the test rig is required. Alumina paste (Ceramabond 552, Aremco) or glass powder (GL-1709, Mo-Sci) are acceptable (Tucker, 2017; Wu et al., 2017). The alumina tube and MS-SOEC have significantly different coefficients of thermal expansion (CTE), and the resulting stress typically cracks the seal during cooling down from operating temperature to room temperature. This precludes repeated or rapid thermal cycling, which is an important feature to demonstrate for MS-SOECs. A metal test rig with well-matched CTE enables thermal cycling. Stainless steel alloy 410 is a suitable material for the test rig. Various glasses will wet and bond with the metal test rig and MS-SOEC, including GM31107 (Schott) and V1515 (3M) (Tucker, 2017; Deka et al., 2019). Both have CTE that is well matched with the metal components, enabling rapid thermal cycling. Seal materials that contain K or Na can accelerate Cr poisoning of the SOEC anode by enhancing Cr evaporation from nearby stainless steel components (Cruse et al., 2007; Tucker et al., 2017). This is especially a concern for MS-SOEC architectures that have a porous Cr-containing alloy support, such as stainless steel, in the anode (oxygen) side, Figure 2B. Cermabond 552 contains Na, so is best used for short-term performance studies only. Alkali-free glasses, such as GM31107 are preferred for long-term durability studies.
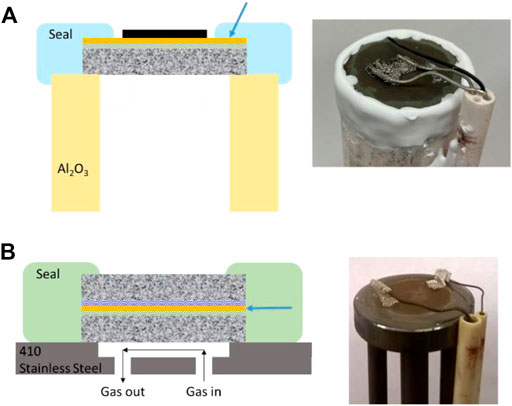
FIGURE 2. Schematic and photographs of MS-SOECs sealed onto test rigs. Electrical lead wires and gas tubing are omitted from the schematic for clarity. The arrows point to the critical sealing surface where the seal material (light blue or light green) contacts the dense electrolyte layer (orange). (A) MS-SOEC with a metal support on one side only, and exposed electrolyte on the perimeter of the top surface, sealed to an alumina tube test rig using ceramic adhesive. (B) Symmetric-architecture MS-SOEC mounted with glass seal on a test rig machined from 410 stainless steel. Note that the sealing surface is much smaller for (B).
Procedure
Step-by-Step Procedure
Step by Step Procedure—metal rig and glass seal
1) Check the test rig for any damage. Polish the surface which will be in contact with the cell with sandpaper.
2) Prepare glass seal slurry: A typical example is 12 g Schott GM31107 glass powder and 3 g terpineol ink vehicle mixed by a centrifugal mixer (Thinky, Japan). A typical amount of slurry used is 60 mg per cm of cell perimeter length.
3) Connect the steam electrode to a Pt or nickel mesh by spot welding. The mesh is spot welded to metal wire leads for electrical connection to the potentiostat.
4) Center the cell on the test rig and load glass paste on the edge of the cell with a syringe. It is critical to ensure the seal material contacts the thin electrolyte edge, as this is the sealing surface, see Figure 2B. Typical thermal treatment: 90°C/0.2 h (10°C/min), 200°C/0 h (2°C/min), 700°C/1 h (10°C/min), cool down to room temperature (10°C/min).
5) Connect the air electrode to a Pt or Au mesh by spot welding. Similar to the steam electrode side, the mesh is spot welded to metal wire leads for electrical connection.
6) Apply a second layer of glass slurry if needed to cover defects in the first layer and fire it with the same procedure.
7) Connect the conductive metal wires to the potentiostat and monitor the OCV change. The OCV should be close to 0 V.
8) Check the water bubbler and H2 tubing. Make sure all connections are tight and there is no leakage.
9) Flush the water bubbler with H2 to remove the oxygen inside.
10) Flush the test rig with nitrogen before connecting it to the H2 tube. The OCV is around 0.1 V with nitrogen.
11) Connect H2 tube to the test rig. The OCV should increase to >1.1 V. Typical H2 flow is 150 SCCM for 3% H2O/97% H2 and 75 SCCM for 50% H2O/50% H2. Keep an eye on the water level in the bubbler during testing and refill it if the water is depleted.
12) Set the temperature (81.7°C for 50% H2O/50% H2) of the silicone oil bath with the DI water bubbler inside. Wrap the metal tube connecting the bubbler to the test rig with a heating belt. Set the temperature of the heating belt to be 40 °C higher than the oil bath (around 120°C). It should be noted to avoid wrapping the heat tape on itself or it could be burned.
13) Wait for equilibrium of the bubbler temperature; it could take up to 2 h.
14) Conduct electrochemical tests, such as LSV, EIS at OCV, durability with constant voltage or current. For LSV, scan the voltage from 0 V (vs. Eoc) to 1.5 V (vs. Ref) with the speed of 10 mV/s. For EIS at OCV, scan the frequency from 200 kHz to 100 mHz with amplitude of 5 mV. For the durability test, apply a constant voltage (like 1.3 V vs. Ref) or a constant current (like 2.5 A, which is equal to 0.5 A/cm2 for a 5 cm2 cell).
Step by Step Procedure—alumina rig and ceramic adhesive seal
1) Secure fuel electrode electrical leads by spot welding with Pt or Ni mesh.
2) Mix the alumina paste (Ceramabond 552, Aremco) well and apply a thin layer of paste to the top surface of the alumina test rig tube.
3) Working quickly (to avoid dry paste), center the SOEC button cell on the test rig with the steam electrode and wires facing down and press down gently to secure to the alumina paste. Allow to dry for ∼1 h.
4) Apply another layer of the alumina paste to the perimeter of the SOEC taking care to thoroughly seal the dense electrolyte on the edge of the cell. A typical amount of paste is 100 mg per cm of cell perimeter length. Allow to dry for ∼1 h.
5) Apply a third layer of paste to drape over the edge of the cell. Allow to dry for ∼1 h and repeat.
6) Spot weld the electrical leads to the oxygen electrode (facing up) using Pt or Au mesh.
7) Curing the alumina paste can be done in the same furnace used for testing. Typical thermal treatment includes: 93°C/2 h (10°C/min), 260°C/2 h (2°C/min), and 700°C/hold (10°C/min). Thermal treatment can be done under flowing H2 starting at room temperature. This is in contrast to the glass seal, where the cell and seal is heated in air then hydrogen is introduced at the operating temperature.
8) Check tubing and connections for leaks, and flush the system with nitrogen prior to the flow of H2.
9) When the cell is at desired operating temperature, connect metal wires to the potentiostat and monitor OCV. The OCV should be > 1.1 V.
10) For operation with 50%H2O/50%H2 conditions see steps 12–13 above.
11) Wait for the temperature of the water bubbler to reach equilibrium and conduct the electrochemical test (see step14 above).
When the test is done and the furnace has cooled down to room temperature, disassemble the cell from the rig. For glass seal, one way to detach the cell from the test rig is using a diamond saw to cut off a small seam on the interface of the cell edge and the glass seal, and then peel off the cell with a tweezer. Ceramic adhesive seals often are cracked after cooling down, and can be removed by grinding with an abrasive wheel or by impacting with a small hammer. Measure the active area of the cell for use in calculating the current density, hydrogen production rate, or other area-based metrics. For a cell with metal support on one side only, the active area is generally defined by the smaller electrode (top electrode in Figure 2A). For a symmetric-architecture cell with metal supports on both sides, the active area is defined by the portion of the cell that is not covered by seal material.
The procedure for metal-supported proton-conducting electrolysis cells is similar to that described above except for the gas compositions. Generally, dry hydrogen or nitrogen is used as the sweep gas on the cathode and steam/air or steam/oxygen on the anode side.
Possible improvements include adding flowing air to sweep oxygen produced at the anode. It is recommended to intermittently monitor OCV when undertaking long-term tests, to assess electrolyte or seal damage that could result in gas leakage. When performing electrolysis operation, a drop in OCV due to leakage or increased steam content appears as a false improvement in performance (increased current at fixed voltage, or decreased voltage at fixed current). While 50% H2O/50% H2 and 700°C is the standard operating point, it is useful to characterize the cell performance over a wide range of steam:hydrogen ratio and operating temperature. In addition, limiting the voltage to <1.8 V is important for the constant current mode, as the voltage could spike due to off-normal operation, such as heating tape failure, water depletion in the bubbler, and so on. The high voltage would delaminate the cell, leading to test failure.
Sample Preparation and Analysis
It is desirable to monitor and analyze the composition of the inlet and outlet gases, especially the hydrogen content, to enable a mass balance on the cell operation. Suitable methods include humidity meter, gas chromatography, flame detection, and others. Implementation is outside the scope of this procedure.
Data Collection, Analysis, and Results
After acquiring raw data, the current, power, hydrogen production rate, ohmic and polarization impedances, and other area-dependent metrics must be normalized by the active area of the cell. All figures should have the initial OCV, steam:hydrogen ratio, temperature, and constant current density or constant voltage clearly stated in the figure or in the figure caption. The polarization curve should be reported with voltage on the y-axis and current density on the x-axis with negative current density for electrolysis mode. The electrochemical impedance spectrum should be reported with square axes using the same number spacing on both axes to preserve the shape of the spectrum. Durability should be reported as voltage or current density vs. time, with calculated ASR optionally shown on a second y-axis. Degradation rates should be reported as %/1000 h (or % kh−1). An example of the data reporting is shown in Figure 3.
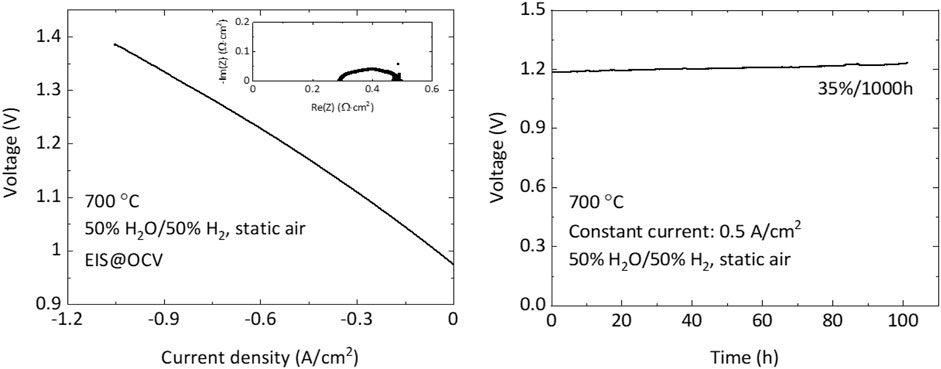
FIGURE 3. An example of graphical data reporting. (A) I-V plot with EIS at OCV (∼0.97 V); (B) Durability.
Quality Control and Quality Assurance
Instrument or Method Calibration and Standardization
Calibrate the electrochemical work station, thermocouple readouts, and flow meters periodically using the manufacturer recommended procedure. Repeat experiments with multiple cells to confirm the quality of the data. Maintaining the steam:hydrogen ratio at the intended level is critically important, as it impacts the OCV and polarization behavior of the cell. Using a thermocouple, calibrate the temperature controller for the heated bubbler by measuring the difference between the set point value and the temperatures in the water and at the outlet of the bubbler. Do the same for the heating tape or heat tracing on the gas delivery tubing and fittings, for which the temperature should be at least 20°C higher than the dew point of the flowing gas to avoid cold spots and condensation. Confirm the steam:hydrogen ratio at the junction between the test rig and gas delivery tubing, using a humidity meter with the sensor heated to above the dew point. Sealant loading on the cell edge changes the active area of the cell in contact with the supplied gases, and the small area of the cell covered by sealant do not participate in the electrochemical reactions. It is recommended to keep the same loading area to enhance cell performance repeatability.
Durability tests are prone to be interrupted by water bubbler refilling. When the water is colder immediately after refilling, the partial pressure of steam supplied to the cell is lower. For fixed current, this causes an increase in operating voltage and possibly mass transport limitation. If the cell voltage spikes too high, the cell could be damaged permanently. To avoid this, pause the cell operation when refilling the bubbler and restart after the water warms up and the OCV stabilizes, which could take around 1 h.
Cautions, Common Issues, and Interferences
To avoid an explosive mixture entering the hot zone, flush the bubbler with H2 and flush the test rig with nitrogen to remove oxygen inside before connecting the gas delivery system to the test rig. To avoid shattering the glass humidification bubbler jar in the event of over-pressure, install a pressure release valve (<10 psi) upstream of the bubbler.
Use a four-probe test system to compensate for resistance in the conductive wires, by attaching one voltage lead and one current lead to each electrode. The current lead must be thick enough to pass the total cell current without overheating. Pt wire of at least 0.75 mm diameter is recommended. Thin wire can become hot at high current, posing a safety risk, and also limiting the lifetime of the wire.
The metal test rig must not be in contact with electrical ground or electrified components of the system. A common issue is that the metal test rig comes into contact with a metal tube, metal clamp, etc. Because the metal test rig is also in contact with the cell, the potential of the cell will not be “floating”, and the potentiostat will pass current to the contacted metal as well as the cell. This often appears as unstable OCV, noisy data, or a large drop in voltage between OCV and the first data point when doing a current-voltage polarization scan. This issue can be avoided by insulating nearby metal components, and installing a short PTFE or alumina tube between the test rig and the metal gas delivery tubing to electrically isolate the test rig from the gas delivery system.
Maintaining the intended steam:hydrogen ratio throughout the system can be challenging. If the OCV is higher than 0.97 V with 50% H2O/50% H2, the moisture concentration could be lower than the intended 50%. This may be due to the bubbler or tubing temperature being lower than 81.7°C, and the user must search for cold spots in the gas delivery system. If the exhaust gas line coming from the test rig out of the furnace is colder than the dew point at that location, liquid water will condense. The droplets of water can block the exhaust flow, or be pushed out as liquid slugs by the exhaust gas. This causes small changes in pressure and flowrate which can appear as noise in the current or voltage data. Refilling the humidification bubbler with water generally changes the temperature of the bubbler, and therefore the steam:hydrogen ratio. One way to minimize the impact is to add the fresh cold water slowly through a tube inserted to the bottom of the bubbler. This minimizes the change in temperature of the top of the water column, which is in direct contact with the flowing gas and therefore controls the dewpoint of the gas. Pre-heating the water before adding it to the bubbler is also useful. If addition of cold water to the bubbler causes a drop in steam content, and the cell is held at constant current, then the cell voltage can briefly rise until the water warms up. If the voltage is above a certain threshold, it can permanently damage the cell. We observe that the cell voltage must be below ∼1.85 V to avoid permanent damage.
Stainless steel supports are sensitive to oxidation, which is highly temperature-dependent (Karczewski et al., 2019; Reisert et al., 2020). If there is a pinhole in the electrolyte or seal, it may cause local heating due to hydrogen burning. This heating can cause rapid breakaway oxidation of the support and the resulting local volume change can cause cracking of the electrolyte or delamination (Dogdibegovic et al., 2019). The crack promotes further burning and heating, quickly leading to cell failure. A telltale sign of this phenomenon is rapid decay of OCV, and brown/red iron oxide visible on the failed cell. Cells should be leak-tested before long-term operation begins. If the OCV is much lower than 1.1 V with 3% H2O/97% H2, the cell or seal could be leaking.
Data Availability Statement
The original contributions presented in the study are included in the article/Supplementary Material, further inquiries can be directed to the corresponding author.
Author Contributions
FS, MW, and MT contributed to protocol development, writing, and editing. MT contributed to funding acquisition.
Funding
This material is based upon work supported by the United States Department of Energy’s Office of Energy Efficiency and Renewable Energy (EERE) under the Hydrogen and Fuel Cell Technologies Office (HFTO) HydroGEN program. This work was funded in part by the United States Department of Energy under contract no. DE-AC02-05CH11231.
Conflict of Interest
The authors declare that the research was conducted in the absence of any commercial or financial relationships that could be construed as a potential conflict of interest.
Publisher’s Note
All claims expressed in this article are solely those of the authors and do not necessarily represent those of their affiliated organizations, or those of the publisher, the editors and the reviewers. Any product that may be evaluated in this article, or claim that may be made by its manufacturer, is not guaranteed or endorsed by the publisher.
Acknowledgments
The authors thank Ruofan Wang for establishing the initial MS-SOEC test setup on which this work is based. The views and opinions of the authors expressed herein do not necessarily state or reflect those of the United States Government or any agency thereof. Neither the United States Government nor any agency thereof, nor any of their employees, makes any warranty, expressed or implied, or assumes any legal liability or responsibility for the accuracy, completeness, or usefulness of any information, apparatus, product, or process disclosed, or represents that its use would not infringe privately owned rights.
Supplementary Material
The Supplementary Material for this article can be found online at: https://www.frontiersin.org/articles/10.3389/fenrg.2022.817981/full#supplementary-material
Abbreviations
Acronyms
ASC/ESC, anode-supported cell or electrolyte-supported cell; ASR, area-specific resistance; CTE, coefficient of thermal expansion; DI, deionized (water); MS-SOEC, metal-supported solid oxide electrolysis cell; OCV, open-circuit voltage; SOEC, solid oxide electrolysis cell; SOFC, solid oxide fuel cell; SCCM, standard cubic centimeters per minute.
References
Cruse, T. A., Ingram, B. J., Liu, D.-J., and Krumpelt, M. (2007). Chromium Reactions and Transport in Solid Oxide Fuel Cells. ECS Trans. 5, 335–346. doi:10.1149/1.2729015
Cui, C., Wang, Y., Tong, Y., Wang, S., Chen, C., and Zhan, Z. (2021). Syngas Production through CH4-Assisted Co-electrolysis of H2O and CO2 in La0.8Sr0.2Cr0.5Fe0.5O3-δ-Zr0.84Y0.16O2-δ Electrode-Supported Solid Oxide Electrolysis Cells. Int. J. Hydrogen Energ. 46, 20305–20312. doi:10.1016/j.ijhydene.2021.03.177
Deka, D. J., Gunduz, S., Kim, J., Fitzgerald, T., Shi, Y., Co, A. C., et al. (2019). Hydrogen Production from Water in a Solid Oxide Electrolysis Cell: Effect of Ni Doping on Lanthanum Strontium Ferrite Perovskite Cathodes. Ind. Eng. Chem. Res. 58, 22497–22505. doi:10.1021/acs.iecr.9b03731
Dogdibegovic, E., Wang, R., Lau, G. Y., Karimaghaloo, A., Lee, M. H., and Tucker, M. C. (2019). Progress in Durability of Metal-Supported Solid Oxide Fuel Cells with Infiltrated Electrodes. J. Power Sourc. 437, 226935. doi:10.1016/j.jpowsour.2019.226935
Karczewski, J., Brylewski, T., Miruszewski, T., Andersen, K. B., Jasinski, P. Z., and Molin, S. (2019). High-temperature Kinetics Study of 430L Steel Powder Oxidized in Air at 600-850 °C. Corrosion Sci. 149, 100–107. doi:10.1016/j.corsci.2019.01.005
Pomfret, M. B., Marda, J., Jackson, G. S., Eichhorn, B. W., Dean, A. M., and Walker, R. A. (2008). Hydrocarbon Fuels in Solid Oxide Fuel Cells: In Situ Raman Studies of Graphite Formation and Oxidation. J. Phys. Chem. C 112, 5232–5240. doi:10.1021/jp711312p
Reisert, M., Berova, V., Aphale, A., Singh, P., and Tucker, M. C. (2020). Oxidation of Porous Stainless Steel Supports for Metal-Supported Solid Oxide Fuel Cells. Int. J. Hydrogen Energ. 45 (55), 30882–30897. Submitted. doi:10.1016/j.ijhydene.2020.08.015
Schiller, G., Ansar, A., Lang, M., and Patz, O. (2009). High Temperature Water Electrolysis Using Metal Supported Solid Oxide Electrolyser Cells (SOEC). J. Appl. Electrochem. 39, 293–301. doi:10.1007/s10800-008-9672-6
Shen, F., and Lu, K. (2018). Comparison of Different Perovskite Cathodes in Solid Oxide Fuel Cells. Fuel Cells 18, 457–465. doi:10.1002/fuce.201800044
Shen, F., Wang, R., and Tucker, M. C. (2020). Long Term Durability Test and post Mortem for Metal-Supported Solid Oxide Electrolysis Cells. J. Power Sourc. 474, 228618. doi:10.1016/j.jpowsour.2020.228618
Stange, M., Stefan, E., Denonville, C., Larring, Y., Rørvik, P. M., and Haugsrud, R. (2017). Development of Novel Metal-Supported Proton Ceramic Electrolyser Cell with Thin Film BZY15-Ni Electrode and BZY15 Electrolyte. Int. J. Hydrogen Energ. 42, 13454–13462. doi:10.1016/j.ijhydene.2017.03.028
Tucker, M. C., Carreon, B., Charyasatit, J., Langston, K., Taylor, C., Manjarrez, J., et al. (2017). Playing with Fire: Commercialization of a Metal-Supported SOFC Product for Use in Charcoal Cookstoves for the Developing World. ECS Trans. 78, 229–236. doi:10.1149/07801.0229ecst
Tucker, M. C. (2017). Durability of Symmetric-Structured Metal-Supported Solid Oxide Fuel Cells. J. Power Sourc. 369, 6–12. doi:10.1016/j.jpowsour.2017.09.075
Tucker, M. C. (2020). Progress in Metal-Supported Solid Oxide Electrolysis Cells: A Review. Int. J. Hydrogen Energ. 45, 24203–24218. doi:10.1016/j.ijhydene.2020.06.300
Wang, R., Dogdibegovic, E., Lau, G. Y., and Tucker, M. C. (2019). Metal‐Supported Solid Oxide Electrolysis Cell with Significantly Enhanced Catalysis. Energy Technol. 7, 1801154. doi:10.1002/ente.201801154
Keywords: Soec, metal-supported, standard operating procedure, glass seal, ceramic paste
Citation: Shen F, Welander MM and Tucker MC (2022) Metal-Supported Solid Oxide Electrolysis Cell Test Standard Operating Procedure. Front. Energy Res. 10:817981. doi: 10.3389/fenrg.2022.817981
Received: 18 November 2021; Accepted: 05 April 2022;
Published: 25 April 2022.
Edited by:
Marcelo Carmo, Nel, NorwayReviewed by:
Aniruddha Pramod Kulkarni, Commonwealth Scientific and Industrial Research Organisation (CSIRO), AustraliaDong Ding, Idaho National Laboratory (DOE), United States
Copyright © 2022 Shen, Welander and Tucker. This is an open-access article distributed under the terms of the Creative Commons Attribution License (CC BY). The use, distribution or reproduction in other forums is permitted, provided the original author(s) and the copyright owner(s) are credited and that the original publication in this journal is cited, in accordance with accepted academic practice. No use, distribution or reproduction is permitted which does not comply with these terms.
*Correspondence: Michael C. Tucker, bWN0dWNrZXJAbGJsLmdvdg==