- 1Department of Chemical Engineering, Pennsylvania State University, University Park, PA, United States
- 2Department of Energy, Environmental and Chemical Engineering, Washington University in St. Louis, St. Louis, MO, United States
- 3Pritzker School of Molecular Engineering, University of Chicago, Chicago, IL, United States
- 4Nel Hydrogen, Wallingford, CT, United States
While anion exchange membrane water electrolyzers show promise as a source of green hydrogen using low-temperatures and non-platinum group metal catalysts, many concerns must be addressed. A primary challenge for the development of high-performance anion exchange membrane water electrolyzers is the fabrication of a stable membrane that will be able to survive long-term stability test while maintaining high anion conductivity, which is a necessity for a durable water electrolyzer. This method will present a standardized protocol that can be used by researchers to assess the quality of their AEM materials and be able to provide insight into how materials may be degrading and how to improve the quality of AEMs. Using Mohr or Volhard titration to measure ion-exchange capacity, EIS to determine the ionic conductivity, NMR and FTIR to understand the extent of membrane degradation over time, and mechanical analyzers to determine the strength of their AEMs, this standardized protocol will guide researchers to determining and improving upon the long-term durability and performance of their AEM materials.
Introduction
Anion exchange membrane water electrolyzers (AEMWEs) have many advantages when compared to other green hydrogen production methods. When compared to liquid alkaline electrolysis, the use of a membrane electrolyte allows for a significant reduction in ohmic overpotential and allows for AEMWEs to operate at high current densities (Ayers et al., 2019). In addition, AEMWEs can use the cost-effective non-platinum group metal catalysts that can lead to a significant reduction in catalyst costs while also utilizing low-cost cell hardware components when using a water feed. Based on these advantages, it is potentially feasible to reduce the cost of clean hydrogen production with AEMWEs.
Despite the advantages of AEMWEs, many challenges remain before they can become widely commercialized. A significant concern for AEMWE development is the chemical and mechanical stability of anion exchange membrane (AEM) materials (Varcoe et al., 2014). Since the hydroxide ion has lower mobility than protons, many AEM materials attempt to increase the ion exchange capacity and improve the ionic conductivity (Ayers et al., 2019). However, this can increase the water uptake of the membrane and lead to worsened mechanical stability. Additionally, when used in alkaline environments, the OH− ions have been seen to severely degrade AEMs through direct nucleophilic reaction (SN2) as nucleophiles (Varcoe et al., 2014). When AEM are exposed to oxygen molecules, OH− ions participate the generation of highly reactive superoxide anion radical and hydroxyl free radicals, which will accelerate the degradation of AEMs. The detailed reaction mechanism can be found in our previous reports. (Parrondo et al., 2016; Zhang et al., 2017). This poor oxidative stability significantly limits the durability of the AEMs and prevents long-term operation of AEMWEs.
While many researchers have begun to develop and characterize new AEM materials with the intent of improving the oxidative stability and ionic conductivity, it is important to follow a standard protocol for an accurate comparison of these new AEMs. This method article will present researchers with a standardized procedure for testing the oxidative stability of AEMs by placing AEM materials into oxygen saturated aqueous alkaline solutions and examining the ion exchange capacity over time using Mohr or Vohlard titration compared to a control sample. AEM samples can also be examined over time using NMR and FTIR techniques which can allow researchers the ability to understand the extent of AEM degradation over time and can provide insight into the possible degradation mechanisms that are occurring. This method also uses electrochemical impedance spectroscopy (EIS) to assist in the measurement of ionic conductivity. Lastly, this report describes a protocol of determining the mechanical stability of AEM materials using tensile test analyzers. It provides information for the mechanical properties of the AEM material, such as ultimate tensile strength and elongation of the AEM at the break point.
Protocol Scope
Scope and Applicability
This procedure describes experimental methods for characterizing the chemical and mechanical stability of anion exchange membranes (AEMs) exposed to oxygen saturated aqueous alkaline solutions. The stability testing condition is aggressive, akin to an accelerated stress test (AST), and is used to assess the viability of a given AEM material to be stable in the presence of alkaline solutions containing dissolved oxygen at near saturation level. The testing procedure is based on previous publications by Arges, Ramani, and others (Arges et al., 2013; Arges et al., 2015; Parrondo et al., 2016). Their work showed accelerated degradation of quaternary ammonium based AEM materials in oxygen saturated aqueous alkaline solutions when compared to nitrogen saturated alkaline solutions. Since water electrolyzers using AEMs generate oxygen at the anode and operate under an alkaline environment, this procedure allows stability assessment of AEM materials under AEMWE conditions without having to test an AEM in a water electrolyzer cell.
Summary of Method
This method carries out chemical stability experiments of AEMs by immersing AEM samples in oxygen saturated alkaline solutions at elevated temperatures (e.g., 1 M KOH or 1 M NaOH at 80°C). Control experiments are performed by immersing AEM samples in nitrogen saturated alkaline solutions at elevated temperatures (i.e., identical conditions). After exposing the samples for a period time to the oxygen saturated and nitrogen saturated alkaline solutions, post-mortem analysis is performed on the AEMs to assess the extent of membrane degradation. This includes measuring ionic conductivity, ion-exchange capacity via titration, collecting NMR spectra (and/or FTIR spectra), and assessing mechanical properties (e.g., tensile test). The properties and spectra of the AEM samples before exposure to the alkaline solutions are compared against the AEM samples exposed to oxygen and nitrogen saturated alkaline solutions. The change in AEM properties when compared to the pristine AEM are quantified over exposure time to the alkaline solutions to determine degradation modes and rate of degradation.
Personnel Qualifications/Responsibilities
The person performing this procedure should have basic training in chemistry at the college level and should have taken a general chemistry class and lab along with an organic chemistry class and lab. All users are responsible for their safety and should be familiar with the safety data sheets (SDS) of the chemicals used during this method. All users should have training on the equipment that is being used and should understand the basics of titration, NMR, FTIR, and mechanical stress testing.
Health and Safety Warning
Be cautious when working with solutions that contain NaOH, KOH, and HCl as they are corrosive and can cause skin burns and damage metals and other equipment. d6-DMSO is flammable, and it can be adsorbed by skin and should not be inhaled. Other chemicals dissolved in d6-DMSO can penetrate the skin and body if direct contact with DMSO is made. Read through all relevant safety data sheets (SDS) before performing the experiments stated in this protocol.
Equipment and Supplies
• Personal protective equipment (PPE)—lab jacket, safety glasses, and safety gloves that protect against d6-DMSO and other caustic solutions
• 150 ml empty high-density polyethylene, polypropylene, or polytetrafluoroethylene jars with lids. You need one jar for each sample to be tested with oxygen saturated alkaline solutions and with nitrogen saturated alkaline solutions.
• KOH or NaOH pellets. The water content of the pellets should be noted so accurate 1 M solutions can be prepared.
• Polytetrafluoroethylene or polypropylene tweezers for handling AEM samples in and out of the jar.
• Deionized (DI) water (18.2 MΩ, < 10 ppb TOC). Water should be withdrawn the day the alkaline solutions are prepared.
The following items are needed for NMR characterization:
• NMR tubes
• Deuterated dimethyl sulfoxide (d6-DMSO)
• NMR spectrometer
The following items are needed for conductivity measurements:
• 500 ml beaker
• Potentiostat/galvanostat for conductivity measurements
The following items are needed for IEC titrations:
• 1 M sodium nitrate in deionized water
• 0.1 M silver nitrate in deionized water
• 14 wt% iron (III) nitrate in deionized water
• 0.1 M potassium thiocyanate in deionized water
Other required equipment for this protocol includes an FTIR spectrometer with a transmission sample holder as well as an Instron® (or other) dynamic mechanical analyzer for AEM mechanical property testing.
Nomenclature and Definitions
• AEM: anion exchange membranes
• AEMWE: anion exchange membrane water electrolyzer
• AgNO3: silver nitrate
• AST: accelerated stress test
• d6-DMSO: deuterated dimethyl sulfoxide
• DI: deionized
• Fe(NO3)3: iron (III) nitrate
• FTIR: Fourier transform infrared spectroscopy
• HFR: high frequency resistance
• IEC: ion-exchange capacity
• KOH: potassium hydroxide
• KSCN: potassium thiocyanate
• M: molar
• MΩ: megaohm
• NaNO3: sodium nitrate
• NaOH: sodium hydroxide
• NMR: nuclear magnetic resonance
• ppb: parts per billion
• PP: polypropylene
• PPE: personal protective equipment
• PTFE: polytetrafluoroethylene
• SOP: standard operating procedure
• TOC: total organic carbon
Recommended Reading
Other literature sources which may help understand the concepts listed in this protocol include:
Arges, Christopher G., and Vijay Ramani. 2012. “Two-dimensional NMR spectroscopy reveals cation-triggered backbone degradation in polysulfone-based anion exchange membranes.” Proceedings of the National Academy of Sciences 2,490–2,495.
Arges, Christopher G., Javier Parrondo, Graham Johnson, Athrey Nadhan, and Vijay Ramani. 2012. “Assessing the influence of different cation chemistries on ionic conductivity and alkaline stability of anion exchange membranes.” Journal of Materials Chemistry 3,733–3,744.
Becerra-Arciniegas, R.-A., R. Narducci, G. Ercolani, S. Antonaroli, E. Sgreccia, L. Pasquini, P. Knauth, and M.L. Di Vona. 2019. “Alkaline stability of model anion exchange membranes based on poly (phenyene oxide) (PPO) with grafted quaternary ammonium groups: Infulence of the functionalization route.” Polymer 121,931.
Cho, Min Kyung, Ahyoun Lim, So Young Lee, Hyoung-Juhn Kim, Sung Jong Yoo, Yung-Eun Sung, Hyun S. Park, and Jong Hyun Jang. 2017. “A Review on Membranes and Catalysts for Anion Exchange Membrane Water Electrolysis Single Cells.” Journal of Electrochemical Science and Technology 183–196.
Procedure
Step-by-Step Procedure
1. Place 150–200 mg of AEM sample in a 150 ml empty high-density polyethylene, polypropylene, or polytetrafluoroethylene jar. The jar should be sealable using a screw lid. Replicate samples should be prepared for assessing sample stability at different time points, stability repeatability, and to benchmark against a control (i.e., alkaline solution saturated with nitrogen as opposed to oxygen).
2. For each sample being assessed, 100 ml of 1 M sodium hydroxide (NaOH) in deionized water (18.2 MΩ and <100 ppb TOC) should be prepared. KOH can be substituted for NaOH. Split the 1 M NaOH (or 1 M KOH) solution in half. For one of the 1 M NaOH (or 1 M KOH) solutions, bubble pure oxygen gas through it continuously for over 30 min. The liquid volume should not exceed over 500 ml. If more than 500 ml needs to be saturated with oxygen, then have two separate containers for bubbling oxygen gas through it. The orifice for bubbling the oxygen gas should be near the bottom of the container holding the 1 M NaOH (or 1 M KOH) solution to ensure the gas bubbles make adequate contact with the entire volume of the liquid solution. For the other 1 M NaOH (or 1 M KOH) solution not saturated with oxygen, bubble pure nitrogen through it continuously for over 30 min. The liquid volume should not exceed over 500 ml. If more than 500 ml needs to be saturated with nitrogen, then have two separate containers for bubbling nitrogen gas through it. The orifice for bubbling the nitrogen gas should be near the bottom of the container holding the 1 M NaOH (or 1 M KOH) solution to ensure the gas bubbles make adequate contact with the entire volume of the liquid solution.
3. For each jar containing a sample, 50 ml of the 1 M NaOH (or 1 M KOH) saturated with oxygen should be added to the jar. The addition of liquid solution to the jar should occur within 5 min after bubbling the gas. After adding the liquid solution, the jar needs to be sealed shut with the screw cap. The immersed AEM sample in the liquid solution stored in the jar should be stored in a 60°C oven. If an AEM candidate has demonstrated acceptable stability at 60°C, additional testing can be performed at 80°C or higher to further analyze that material.
4. Repeat this procedure for replicate samples that can be used to assess the AEM stability at various time points and with nitrogen saturated 1 M NaOH (or 1 M KOH) solution.
5. After storing the AEM samples in gas saturated alkaline solutions for a given period at 60°C or 80°C, remove the jar sample from the oven. Let it cool for 30 min. Unscrew the lid and remove the AEM sample from the jar with a pair of PTFE (or PP) tweezers/forceps. Immerse the sample in 0.1 M HCl for 30 min followed by 1 M NaCl for 12–18 h. Then, rinse the AEM sample with deionized water and store in deionized water for 2 h. Remove the deionized water from the sample and add fresh deionized water for another 2 h. Then, store the AEM sample in an empty, clean jar with the lid open and let it dry in a fume hood for a day. The sample will be ready for IEC, NMR, ionic conductivity, and mechanical testing.
6. The AEM samples should be stored at 60°C or 80°C over a 4 week period. A sample should be withdrawn from the oven at 7, 14, and 28 days, etc.
7. All AEM samples (both virgin samples and samples which have been exposed to gas saturated alkaline solutions at elevated temperatures) should be characterized via the following methods:
i. Ion-exchange capacity via Mohr or Vohlard titration. The AEMs in chloride form (dry weight of approximately 0.1 g) should be immersed in 20 ml of 1 M NaNO3 for 48 h. The amount of chloride ions exchanged can be determined by back titration using 0.1 M KSCN, after addition of 5 ml of 0.1 M AgNO3. A control sample containing only 20 ml of 1M NaNO3 should be also titrated as described above. Fe(NO3)3 is used as endpoint indicator (Arges et al., 2013).
ii. NMR and/or FTIR spectroscopy to characterize the change in the chemical structure of the samples (Arges et al., 2013; Varcoe et al., 2014; Arges et al., 2015). For NMR measurements, 3–5 mg of AEM samples with different immersion time should be dissolved in 1 ml d6-DMSO. Note that d6-DMSO is not a universal solvent that used to run NMR experiments. Operator should choose an appropriate deuterated solvent to dissolve the polymer. 1H-NMR and 13C-NMR spectrum can be coupled to analyze the degradation mechanisms both from the polymer backbone and the cationic groups. An example of using 2D NMR spectra to detect the degradation process of AEM can be found in Supplementary Material. The presence of functional groups can be qualitatively confirmed by using FTIR spectroscopy. An example of using FTIR spectroscopy to monitor the alkaline stability of AEM can be found in Supplementary Material.
iii. Ionic conductivity in deionized water at 25 °C with a 4-pt conductivity probe. In-plane ionic conductivity measurements can be carried out in a 4-point conductivity cell using electrochemical impedance spectroscopy (EIS) to measure the resistance. A 1 cm × 3 cm membrane is placed in the PTFE conductivity cell in contact with the four platinum electrodes and immersed in a temperature-controlled DI water bath. Figure 1 shows 4-electrode measurements with membrane samples assembled in conductivity cells. A potentiostat is used to measure the impedance in the frequency range 100 kHz to 0.1 Hz. The high frequency resistance that is associated with ion transport is estimated from the Bode plots (corresponding to a phase angle close to zero) (Arges et al., 2013). Bode plots consist plots of the magnitude of the impedance and phase as a function of frequency. Figure 2 shows an exemplary of Bode plots with ionic conduction characteristics (Vadhva et al., 2021)). An example of measuring ionic conductivity in an alkaline environment is shown in Supplementary Material.
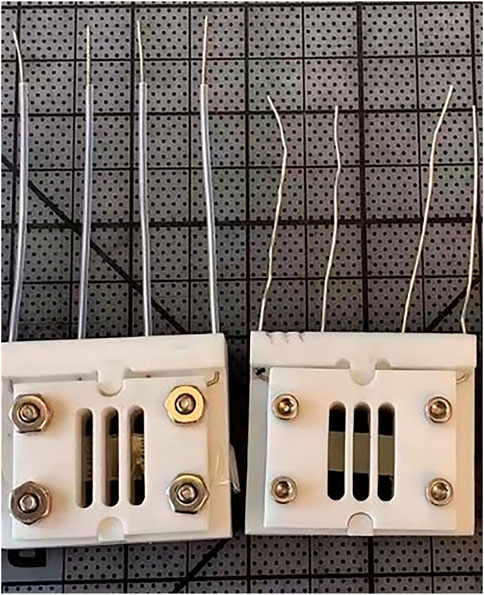
FIGURE 1. Conductivity cells for in-plane ionic conductivity measurements using stand-alone membrane samples.
iv. Stress-strain curve of the AEM by performing a tensile test or using a dynamic mechanical analyzer (DMA). The tensile tests for the AEM can be performed using a differential mechanical analyzer. The membrane sample (approximate dimensions: 50 mm × 5 mm × 0.05 mm) is fixed in a film tension clamp using a certain torque. The experiments can be performed at 25 °C with different relative humidity values. The membrane can be stretched at 0.5 MPa/min until the sample fractures (Arges et al., 2013). Figure 3 shows an example of a membrane sample in the clamps of a DMA (Bashir, 2021). Exemplary tensile test curves can be found in Figure 4 in our previous report (Wang et al., 2020).
Sample Preparation and Analysis
AEM samples should be cut so that the sample weight is approximately 150–200 mg. Enough samples should be cut so that samples can be placed in oxygen saturated alkaline solution, nitrogen saturated alkaline solution, and so that there are replicate samples that can be tested at various time intervals. During the IEC titration measurements, the samples should have an estimated dry weight of approximately 100 mg. For NMR measurements, the sample weight should be 3–5 mg. Samples that are to be used for measuring the ionic conductivity in water should be 10 mm × 30 mm so that they can fit within the PTFE conductivity cell. Samples to be used for the stress-strain measurement should have an approximate dimension of 50 mm × 5 mm x 0.05 mm. When preparing samples, ensure that there is enough virgin AEM material remaining for characterization.
Results
From the data collected from step 4.1.7. i., the anion exchange capacity for the chloride counter ion can be calculated using the following equation:
In this equation, IEC is the anion exchange capacity (mmol/g), VC is the volume (ml) of 0.1 M KSCN necessary to reach the equivalence point with the control sample, V is the volume (ml) of 0.1 M KSCN necessary to reach the equivalence point with the AEM sample, and W is the dry weight (g) of the AEM sample.
To determine the ionic conductivity of the AEM sample, the ionic resistance of the sample should first be determined using the collected EIS data. Since the high frequency resistance (HFR) measured with EIS is associated with the ionic resistance of the sample, the ionic resistance is measured by reading the resistance of the sample on a Bode plot when the phase angle is equal to zero. Once the ionic resistance is known, the ionic conductivity of the membrane can be determined using the following equation:
In this equation,
When performing the tensile tests with the AEM samples, a stress-strain curve should be recorded and presented. This plot will detail the stress applied to the AEM sample and the strain felt by the sample. This plot will allow the user to record the ultimate tensile strength and elongation at the break point.
Quality Control and Quality Assurance
Instrument or Method Calibration and Standardization
Ionic conductivity measurements can be calibrated by measuring a well-studied ion conducting membrane such as Nafion® 212. For IEC measurements, Vohlard titration can be calibrated by titrating 0.1 M AgNO3 solutions with no AEM samples and then titrating with 0.1 M KSCN. The volume of KSCN needed to reach the endpoint should be the same volume of added AgNO3. Titration method can also be calibrated by measuring the IEC of a commercially available AEM such as Fumasep®. The same principle applies to the tensile test. When performing the spectroscopy methods, background corrections should be performed to account for environmental conditions.
Cautions
AEM samples that are too brittle to handle after removing from the jar with alkaline solutions should be discarded appropriately. Note that the sample did not mechanically survive the alkaline stability test at the specified temperature and time point.
Interferences
Do not use glass containers for storing or hold NaOH and KOH solutions as the caustic media can etch the glass leading to precipitates that interfere with the degradation analysis.
Discussion
Plot ionic conductivity, IEC, and mechanical properties (stress or elongation at break) versus time. Create separate traces for samples exposed to oxygen saturated alkaline solutions versus nitrogen saturated alkaline solutions. Please refer to the results (Figure 3 in page 4) published in our previous report (Parrondo et al., 2016). At t = 0 h, the initial point refers to IEC of the virgin AEM sample. If NMR characterization is possible, the 1H NMR for the AEM sample at different time points should be compared. Peaks associated with backbone and cation integrity in the virgin AEM sample should be assigned and monitored in the 1H NMR. An internal standard should be added to the AEM sample dissolved in a deuterated solvent such as d6-DMSO to quantify cation and backbone degradation products. Similarly, FTIR spectra can be compared versus the samples exposed to alkaline solutions and the virgin AEM sample.
Note that the membrane sample might suffer from mechanical failure during the stability test. For instance, membrane sample might break into pieces due to the degradation process from nucleophiles, which would result in the difficulty of continued ionic and mechanical measurements. It is still necessary to extract degradation information from the NMR characterization.
Data Availability Statement
The original contributions presented in the study are included in the article/Supplementary Material, further inquiries can be directed to the corresponding author.
Author Contributions
CA and ZW were responsible for draft writing and editing. VR and RO were responsible for reviewing and editing.
Conflict of Interest
RO was employed by Nel Hydrogen
The remaining authors declare that the research was conducted in the absence of any commercial or financial relationships that could be construed as a potential conflict of interest.
Publisher’s Note
All claims expressed in this article are solely those of the authors and do not necessarily represent those of their affiliated organizations, or those of the publisher, the editors and the reviewers. Any product that may be evaluated in this article, or claim that may be made by its manufacturer, is not guaranteed or endorsed by the publisher.
Acknowledgments
The author VR would like to acknowledge with gratitude the Office of Naval Research (ONR grant no. N00014-16-1-2833) for funding this work. The author VR also acknowledges with gratitude generous support from the Roma B. and Raymond H. Wittcoff Distinguished University Professorship at Washington University in St. Louis. The author RO would like to acknowledge the U.S. Department of Energy and the funding support from project DOE-DE-EE0008092, Benchmarking Advanced Water Splitting Technologies: Best Practices in Materials Characterization.
Supplementary Material
The Supplementary Material for this article can be found online at: https://www.frontiersin.org/articles/10.3389/fenrg.2022.871851/full#supplementary-material
References
Arges, C. G., Wang, L., Parrondo, J., and Ramani, V. (2013). Best Practices for Investigating Anion Exchange Membrane Suitability for Alkaline Electrochemical Devices: Case Study Using Quaternary Ammonium Poly(2,6-Dimethyl 1,4-phenylene)oxide Anion Exchange Membranes. J. Electrochem. Soc. 160, F1258–F1274. doi:10.1149/2.049311jes
Arges, C. G., Wang, L., Jung, M.-S., and Ramani, V. (2015). Mechanically Stable Poly(arylene Ether) Anion Exchange Membranes Prepared from Commercially Available Polymers for Alkaline Electrochemical Devices. J. Electrochem. Soc. 162, F686–F693. doi:10.1149/2.0361507jes
Ayers, K., Danilovic, N., Ouimet, R., Carmo, M., Pivovar, B., and Bornstein, M. (2019). Perspectives on Low-Temperature Electrolysis and Potential for Renewable Hydrogen at Scale. Annu. Rev. Chem. Biomol. Eng. 10, 219–239. doi:10.1146/annurev-chembioeng-060718-030241
Bashir, M. A. (2021). Use of Dynamic Mechanical Analysis (DMA) for Characterizing Interfacial Interactions in Filled Polymers. Solids 2, 108–120. doi:10.3390/solids2010006
Parrondo, J., Wang, Z., Jung, M.-S. J., and Ramani, V. (2016). Reactive Oxygen Species Accelerate Degradation of Anion Exchange Membranes Based on Polyphenylene Oxide in Alkaline Environments. Phys. Chem. Chem. Phys. 18, 19705–19712. doi:10.1039/c6cp01978a
Vadhva, P., Hu, J., Johnson, M. J., Stocker, R., Braglia, M., Brett, D. J. L., et al. (2021). Electrochemical Impedance Spectroscopy for All‐Solid‐State Batteries: Theory, Methods and Future Outlook. ChemElectroChem 8, 1930–1947. doi:10.1002/celc.202100108
Varcoe, J. R., Atanassov, P., Dekel, D. R., Herring, A. M., Hickner, M. A., Kohl, P. A., et al. (2014). Anion-exchange Membranes in Electrochemical Energy Systems. Energy Environ. Sci. 7, 3135–3191. doi:10.1039/c4ee01303d
Wang, Z., Parrondo, J., Sankarasubramanian, S., Bhattacharyya, K., Ghosh, M., and Ramani, V. (2020). Alkaline Stability of Pure Aliphatic-Based Anion Exchange Membranes Containing Cycloaliphatic Quaternary Ammonium Cations. J. Electrochem. Soc. 167, 124504. doi:10.1149/1945-7111/abac29
Keywords: anion exchange membrane, conductivity, electrolysis, stability, protocol and guidelines
Citation: Arges CG, Ramani V, Wang Z and Ouimet RJ (2022) Assessing the Oxidative Stability of Anion Exchange Membranes in Oxygen Saturated Aqueous Alkaline Solutions. Front. Energy Res. 10:871851. doi: 10.3389/fenrg.2022.871851
Received: 08 February 2022; Accepted: 11 March 2022;
Published: 28 March 2022.
Edited by:
Roel Van de Krol, Helmholtz Association of German Research Centers (HZ), GermanyReviewed by:
Ryszard Wycisk, Vanderbilt University, United StatesViatcheslav Freger, Technion Israel Institute of Technology, Israel
Copyright © 2022 Arges, Ramani, Wang and Ouimet. This is an open-access article distributed under the terms of the Creative Commons Attribution License (CC BY). The use, distribution or reproduction in other forums is permitted, provided the original author(s) and the copyright owner(s) are credited and that the original publication in this journal is cited, in accordance with accepted academic practice. No use, distribution or reproduction is permitted which does not comply with these terms.
*Correspondence: Vijay Ramani, cmFtYW5pQHd1c3RsLmVkdQ==