- 1Shanghai Power Equipment Research Institute Co. Ltd, Shanghai, China
- 2Ningbo Water Meter(Group) Co. Ltd., Ningbo, China
- 3College of Electrical, Energy and Power Engineering, Yangzhou University, Yangzhou, China
Monodisperse encapsulated phase change materials (PCMs) are fabricated via microfluidic technology. To evaluate the thermoregulation ability of PCM capsules applied in building thermal energy storage, a gypsum model house with PCM capsules embedded is prepared. The temperature revolutions outside and inside the gypsum model house with different PCM capsules filling ratios are investigated. The effect of the filling ratio of the PCM on the thermoregulation performance is discussed. The potential application of monodisperse encapsulated PCMs in building thermal energy storage is verified. Attributing to the PCM capsules, the thermal response of the gypsum model house to the varying environmental temperature is retarded. As the filling ratios increase, the thermoregulation performance of the gypsum model house is better.
Introduction
Phase change materials (PCMs), which can absorb or release heat during the melting or solidification process, can be applied to indoor thermal comfort (Deng et al., 2021; Lamrani et al., 2021), personal thermal management (Shi et al., 2021; Li et al., 2021), electronic cooling (Wang et al., 2021; Kothari et al., 2021), photothermal functional surface (Wang et al., 2018; Wang et al., 2017), and solar energy storage (Zhang et al., 2020; Javadi et al., 2020; Kumar et al., 2020), as shown in Figure 1. However, the leakage of PCMs may lead to corrosion or fire risk (Hu, 2020). Hence, it is important to encapsulate the PCMs with a shell or supporting matrix (Su et al., 2015).
There are several approaches for the encapsulation of PCMs (Milián et al., 2017), which are usually categorized into physical methods and chemical methods, including spray drying (Borreguero et al., 2011), interfacial polycondensation (Zhang and Rochefort, 2012), suspension polymerization (Sánchez-Silva et al., 2010), and emulsion polymerization (Zhang et al., 2019). However, traditional encapsulation approaches suffer from low encapsulation efficiency and poor monodispersity, which makes it hard to obtain encapsulated PCMs with stable thermal properties (Cárdenas-Ramírez et al., 2020). Recently, droplet microfluidics technology shed light on the encapsulation of PCMs, for the precise control of a single droplet (Chen et al., 2015) and high encapsulation efficiency (Liang et al., 2014; Chen and Deng, 2017; Zhang et al., 2018; Akamatsu et al., 2019). Wen et al. prepared the phase change microfibers with core–shell structure by a facile and controllable microfluidic strategy (Wen et al., 2015). Shi et al. prepared polyurea microcapsules containing paraffin via a microfluidic device, with an encapsulation efficiency of 96.5% (Shi et al., 2020). Han et al. achieved the precisely microfluidic encapsulation of PCMs with high monodispersity (Han et al., 2020). Hao et al. introduced multilayer graphene to the preparation of encapsulated PCMs via microfluidic technology (Hao et al., 2022). The thermoregulation ability of the PCM capsules is enhanced while the degeneration of energy storage capacity is negligible. However, there are few studies on the thermoregulation capacity of monodisperse encapsulated PCMs via microfluidic technology for building thermal energy storage.
In this study, PCM capsules are generated via microfluidic technology. A thermoregulation experiment system is built to test the thermal performance of the gypsum model house embedded with the PCM capsules. The temperature distributions inside the gypsum model house and outside the gypsum model house are investigated. The effect of the filling ratio of the PCM on the thermoregulation performance is discussed. The potential application of monodisperse encapsulated PCMs in building thermal energy storage is verified.
Experimental Setup and Methods
Preparation of PCM Capsules
In this study, the PCM capsule emulsion template is obtained by a microfluidic chip made of two capillaries in this paper (Chen et al., 2013). The details about the fabrication and structure of the microfluidic chip can be found in our previous study (Hao et al., 2022). The inner phase fluid is paraffin RT25 with a phase change temperature of 22–27°C, and the outer phase fluid is low viscosity sodium alginate (C6H7O6Na) aqueous solution with a mass fraction of 3 wt%. The emulsion template is introduced into the collection unit, and then the shell is solidified by chemical reaction to prepare the wet PCM capsules. The calcium chloride (CaCl2) aqueous solution with a mass fraction of 5 wt% is filled in the collection unit. Subsequently, the dry PCM capsules are obtained after putting the wet PCM capsules into an oven at 30°C. The coefficient of variation of the PCM capsules prepared in this study is less than 2%, indicating that the PCM capsules have good monodispersity. The dimensional parameter M is defined as the mass ratio between the core material RT25 of the PCM capsules and the shell calcium alginate to characterize the core–shell structure of PCM capsules. The PCM capsules with M = 11.2 are used in this study. The melting enthalpy and solidification enthalpy of PCM capsules are △Hm = 165.9 (J/g) and △Hc = 166.1 J/g.
Experimental System for Characterization of Thermoregulation
In order to systematically characterize the thermal regulation ability, a gypsum model house filled with PCM capsules (radius of 1.5-mm) is designed and built, and then the temperature changes on the surface and inside the model house with different filling ratios (FRs) of PCM capsules under the condition of infrared radiation heating are observed experimentally. The dimension of the gypsum model house is 50 mm in length, 25 mm in width, and 30 mm in height. The experimental system diagram of thermal regulation characterization of PCM capsules is shown in Figure 2. The gypsum model house is heated by radiant heat, and the surface and internal temperatures of the model house are measured and recorded using an infrared thermal imager (TH9260, Japan Electric Co., Ltd., Japan) and a thermocouple thermometer (K type, Omega Co., Ltd., United States), The temperature measuring points inside the gypsum model house are arranged as TI1, TI2, and TI3 successively from the heat source side (as shown in Figure 1).
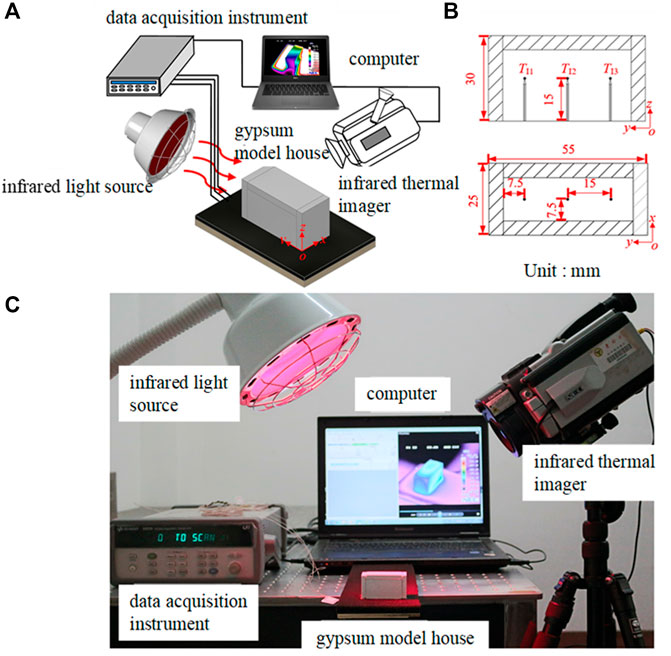
FIGURE 2. Thermal regulation characterization experiment of PCM capsules: (A) schematic diagram; (B) structure of the model house; (C) photograph of the experimental system.
In this experiment, the FR of PCM capsules in the gypsum board is adjusted by changing the number of filled PCM capsules of the same size. The number of PCM capsules filled in a single gypsum board is 0, 20, 35, and 60, respectively, and the FR of PCM capsules is 0%, 11.91%, 20.85%, and 35.74%, respectively, according to Eq. 1.
Here, Vcapsule and Vgb represent the volume of PCM capsules and gypsum board, respectively, and Ncapsule indicates the number of PCM capsules inside the gypsum board.
Results and Discussion
During the heating process, the initial temperature of the model house with filling rates of 0%, 11.91%, 20.85%, and 35.74% is the same as the ambient temperature (15.5°C). Figure 3 presents the comparison of infrared thermal images of the model house surface during the heating and cooling stages under infrared light source thermal radiation with different FRs of PCM capsules. As expected, the surface temperature of the gypsum model house increases significantly after the infrared light source is turned on. At the initial stage of the heating process (before 4.5 min), there is no clear difference between the infrared thermal images on the gypsum model house surface with different FRs. It can be explained that the change of the surface temperature mainly depends on the radiation heat of the infrared light source. As time goes on, the surface temperature of the gypsum model house further rises and reaches the melting point of RT25. At this time, the surface temperature of the gypsum model house begins to be affected by the PCM capsules filled inside. Since the PCM contained in the capsules absorb part of the energy from the external environment in the melting process, the rising surface temperature of the gypsum model house can be effectively reduced. Therefore, it can be seen that the surface temperature of the gypsum model house filled with PCM capsules is significantly lower than that without PCM capsules at the same time. In addition, with the increase in heating time, the continuous endothermic melting process of the internal PCM further slows down the rise of the surface temperature. Therefore, it can be seen that as heating time goes on, the difference in the surface temperature between the gypsum model house with FR > 0% and that with FR = 0% becomes more obvious. In addition, for the gypsum model house with higher FR, the volume of PCM inside the model house is higher, so more heat can be absorbed from the surrounding environment. Thus, the thermal response of the gypsum model house to the rising environmental temperature is retarded.
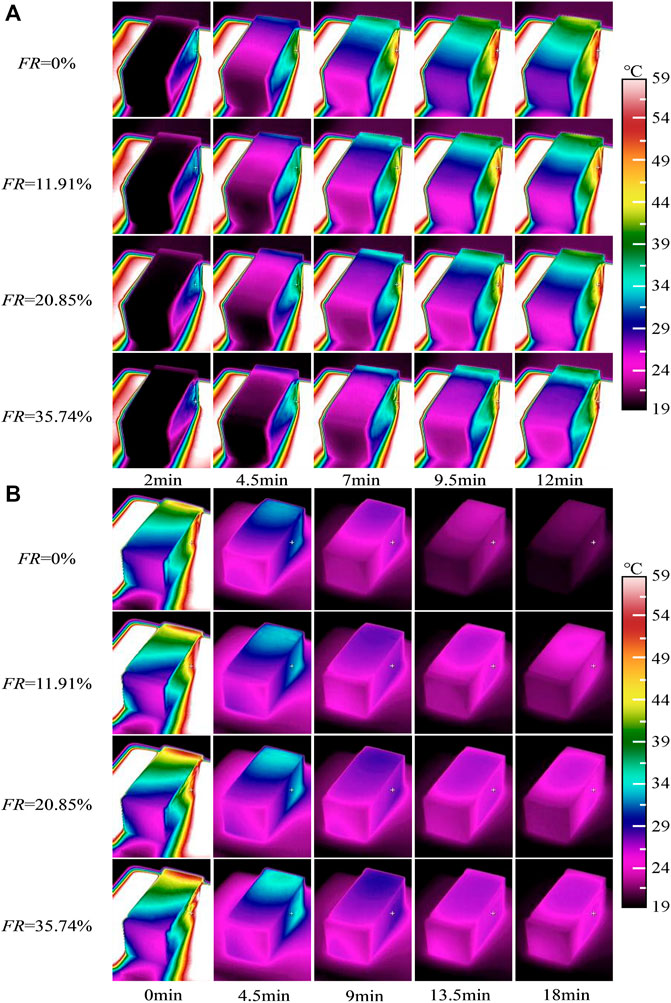
FIGURE 3. Surface temperature distribution of model house with different FRs: (A) heating stage; (B) cooling stage.
Under the thermal radiation of an infrared light source, three thermocouples (TI1, TI2, and TI3) are used to measure the inside temperature of the gypsum model house with different FRs, and Tavg is the arithmetical average of the temperature measured by the three thermocouples. As seen in Figure 4A, at the initial heating stage, there is little difference in the internal temperature of the gypsum model house with different FRs, because the melting point of most PCMs has not been reached at this time, and the rising temperature mainly depends on sensible heat of gypsum board and PCM capsules. In addition, when the environment temperature rises to the melting point of PCM, the PCM begins to melt and absorbs heat from the environment, thus reducing the rising rate of the temperature inside the model house. Compared with the gypsum model house filled with PCM capsules, the overall temperature variations of the gypsum model house filled with PCM capsules are significantly less. As FR increases, there are more PCMs in the gypsum model house, so more heat can be absorbed by PCM during the melting process. The retarded thermal response of the gypsum model house to the rising environmental temperature is more obvious. Therefore, the curve of the inside temperature of the gypsum model house is gentler with the increasing FR.
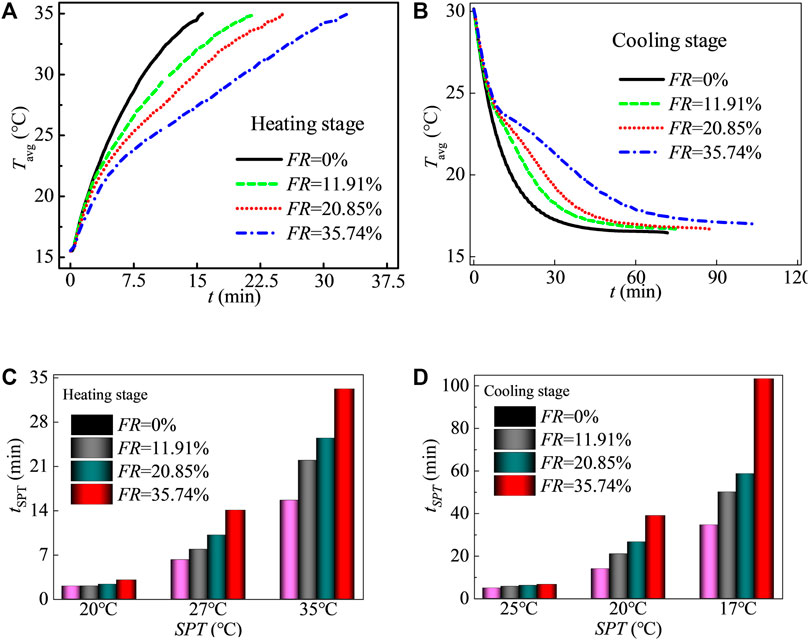
FIGURE 4. Thermal performance of the model house with different FRs: (A) temperature distributions inside the model house during the heating stage; (B) temperature distributions inside the model house during the cooling stage; (C) time required for the model house to reach SPTs during the heating stage; (D) heating stage; (B) time required for the model house to reach SPTs during the cooling stage.
As seen in Figure 3, during the heating stage, before the melting of the PCMs, the surface temperature of the gypsum model house is not affected by FR. So, the initial temperature of the cooling stage is set at 30°C. First, the gypsum model house is heated by infrared thermal radiation till its internal temperature reaches 30°C. The gypsum model house with different FRs is cooled by natural convection at ambient temperature (18°C). It can be seen from the variations of the infrared thermal image of the gypsum model house (shown in Figure 3B) that the gypsum model house surface temperature drops rapidly when the infrared light source is turned off. As it reaches the solidification range of RT25 (22–27°C), PCM solidifies and releases heat which can offset part of the heat in the environment released by the gypsum model house and slow down the drop in surface temperature of the house. As a result, it can be seen that the gypsum model house surface temperature filled with PCM capsules is significantly higher than that without PCM capsules. In addition, when FR increases, the heat released during solidification also increases, and the gypsum model house surface temperature is higher at the same time. Combined with what is presented in Figure 3B, at the initial cooling stage, there is basically no difference in the internal temperature of the gypsum model house with different filling rates. This is because the temperature of PCM has not reached the solidification point, and the drop in the temperature is mainly caused by the sensible heat decrease of the gypsum board and PCM under natural convection. When the ambient temperature drops to the solidification temperature of PCM, the PCM releases heat to the surrounding environment under the action of latent heat, thus slowing down the decrease of the internal temperature of the gypsum model house. It can also be seen that when the FR increases, the declining trend of the internal temperature of the gypsum model house filled with more PCM capsules will be slower.
In order to more intuitively characterize the thermoregulation ability of PCM capsules, the time required for the temperature of the gypsum model house to reach the three set point temperatures (SPTs) of 20°C, 27°C, and 35°C in the heating stage are calculated, respectively. In addition, the time required for the temperature of the gypsum model house to reach 25°C, 20°C, and 17°C in the cooling stage are also calculated. As seen in Figures 4C,D, both during the heating and cooling stage, the time required to reach the three SPTs increases with the increasing FR, and the difference in the required time is most obvious at 30°C and 17°C. At this temperature, the PCM filled inside the capsules has completely absorbed or released all its latent heat through the melting or solidification process. For the filling ratio of 11.91%, 20.85%, and 35.74%, the time required to reach the SPT of 17°C during the cooling stage increases by 44.8%, 69.9%, and 198.8%, respectively. So, the thermoregulation effect of the PCM on the gypsum model house is strongest at this temperature.
Conclusion
In this study, the PCM capsules with good monodispersity are generated via microfluidic technology. The potential application of monodisperse encapsulated PCMs in building thermal energy storage is tested by the thermoregulation experiment of the gypsum model house embedded by the PCM capsules. The results indicate that the variation of the inside and outside surface temperatures of the model house decreases due to the heat capacity of the PCM capsules. Attributing to the PCM capsules, the thermal response of the gypsum model house to the varying environmental temperature is retarded. As the filling ratios increase, the thermoregulation performance of the gypsum model house is better. For the filling ratio of 11.91%, 20.85%, and 35.74%, the time required to reach the SPT of 17°C during the cooling stage increases by 44.8%, 69.9%, and 198.8%, respectively. Hence, the application of the monodisperse encapsulated PCMs in building thermal energy storage is verified.
Data Availability Statement
The raw data supporting the conclusions of this article will be made available by the authors, without undue reservation.
Author Contributions
CL and YC contributed to the conception and design of the study. ZL performed the statistical analysis and wrote the first draft of the manuscript. NH, LJ, and WB wrote sections of the manuscript. All authors contributed to manuscript revision, read, and approved the submitted version.
Conflict of Interest
Authors ZL, CL, NH, LJ and WB were employed by Shanghai Power Equipment Research Institute Co. Ltd. Author YC was employed by Ningbo Water Meter (Group) Co. Ltd.
Publisher’s Note
All claims expressed in this article are solely those of the authors and do not necessarily represent those of their affiliated organizations, or those of the publisher, the editors, and the reviewers. Any product that may be evaluated in this article, or claim that may be made by its manufacturer, is not guaranteed or endorsed by the publisher.
References
Akamatsu, K., Ogawa, M., Katayama, R., Yonemura, K., and Nakao, S.-I. (2019). A Facile Microencapsulation of Phase Change Materials within Silicone-Based Shells by Using Glass Capillary Devices. Colloids Surfaces A Physicochem. Eng. Aspects 567, 297–303. doi:10.1016/j.colsurfa.2019.01.076
Borreguero, A. M., Valverde, J. L., Rodríguez, J. F., Barber, A. H., Cubillo, J. J., and Carmona, M. (2011). Synthesis and Characterization of Microcapsules Containing RubithermRT27 Obtained by Spray Drying. Chem. Eng. J. 166, 384–390. doi:10.1016/j.cej.2010.10.055
Cardenas-Ram, C., Jaramillo, F., and G Mez, M. (2020). Systematic Review of Encapsulation and Shape-Stabilization of Phase Change Materials. J. Energy Storage 30, 101495. doi:10.1016/j.est.2020.101495
Chen, Y., and Deng, Z. (2017). Hydrodynamics of a Droplet Passing through a Microfluidic T-Junction. J. Fluid Mech. 819, 401–434. doi:10.1017/jfm.2017.181
Chen, Y., Liu, X., and Shi, M. (2013). Hydrodynamics of Double Emulsion Droplet in Shear Flow. Appl. Phys. Lett. 102, 051609. doi:10.1063/1.4789865
Chen, Y., Wu, L., and Zhang, L. (2015). Dynamic Behaviors of Double Emulsion Formation in a Flow-Focusing Device. Int. J. Heat Mass Transf. 82, 42–50. doi:10.1016/j.ijheatmasstransfer.2014.11.027
Deng, Z., Zhang, X., Zhang, Y., Jiang, S., and Yu, C. (2021). Thermal Energy Charging Improvement of a Latent Thermal Energy Storage System Via Fractal-Branched Fins. Fractals 29, 2150007. doi:10.1142/s0218348x21500079
Han, X., Kong, T., Zhu, P., and Wang, L. (2020). Microfluidic Encapsulation of Phase-Change Materials for High Thermal Performance. Langmuir 36, 8165–8173. doi:10.1021/acs.langmuir.0c01171
Hao, G., Yu, C., Chen, Y., Liu, X., and Chen, Y. (2022). Controlled Microfluidic Encapsulation of Phase Change Material for Thermo-Regulation. Int. J. Heat Mass Transf. 190, 122738. doi:10.1016/j.ijheatmasstransfer.2022.122738
Hu, H. (2020). Recent Advances of Polymeric Phase Change Composites for Flexible Electronics and Thermal Energy Storage System. Compos. Part B Eng. 195, 108094. doi:10.1016/j.compositesb.2020.108094
Javadi, F. S., Metselaar, H. S. C., and Ganesan, P. (2020). Performance Improvement of Solar Thermal Systems Integrated with Phase Change Materials (PCM), a Review. Sol. Energy 206, 330–352. doi:10.1016/j.solener.2020.05.106
Kothari, R., Sahu, S. K., Kundalwal, S. I., and Mahalkar, P. (2021). Thermal Performance of Phase Change Material-Based Heat Sink for Passive Cooling of Electronic Components: An Experimental Study. Int. J. Energy Res. 45, 5939–5963. doi:10.1002/er.6215
Kumar, A., Singh, A. P., and Singh, O. (2020). Effect of Novel PCM Encapsulation Designs on Electrical and Thermal Performance of a Hybrid Photovoltaic Solar Panel. Sol. Energy 205, 320. doi:10.1016/j.solener.2020.05.062
Lamrani, B., Johannes, K., and Kuznik, F. (2021). Phase Change Materials Integrated into Building Walls: An Updated Review. Renew. Sustain. Energy Rev. 140, 110751. doi:10.1016/j.rser.2021.110751
Li, J., Zhu, X., Wang, H., Lin, P., Jia, L., Li, L., et al. (2021). Synthesis and Properties of Multifunctional Microencapsulated Phase Change Material for Intelligent Textiles. J. Mater Sci. 56, 2176–2191. doi:10.1007/s10853-020-05399-4
Liang, W.-G., Yang, C., Wen, G.-Q., Wang, W., Ju, X.-J., Xie, R., et al. (2014). A Facile and Controllable Method to Encapsulate Phase Change Materials with Non-toxic and Biocompatible Chemicals. Appl. Therm. Eng. 70, 817–826. doi:10.1016/j.applthermaleng.2014.06.006
Milian, Y. E., Gutierrez, A., Grageda, M., and Ushak, S. (2017). A Review on Encapsulation Techniques for Inorganic Phase Change Materials and the Influence on Their Thermophysical Properties. Renew. Sustain. Energy Rev. 73, 983. doi:10.1016/j.rser.2017.01.159
Sanchez-Silva, L., Rodr Guez, J. F., Romero, A., Borreguero, A. M., Carmona, M., and S Nchez, P. (2010). Microencapsulation of PCMs with a Styrene-Methyl Methacrylate Copolymer Shell by Suspension-like Polymerisation. Chem. Eng. J. 157, 216. doi:10.1016/j.cej.2009.12.013
Shi, J., Qin, M., Aftab, W., and Zou, R. (2021). Flexible Phase Change Materials for Thermal Energy Storage. Energy Storage Mater. 41, 321–342. doi:10.1016/j.ensm.2021.05.048
Shi, T., Hu, P., and Wang, J. (2020). Preparation of Polyurea Microcapsules Containing Phase Change Materials Using Microfluidics. ChemistrySelect 5, 2342–2347. doi:10.1002/slct.201904570
Su, W., Darkwa, J., and Kokogiannakis, G. (2015). Review of Solid-Liquid Phase Change Materials and Their Encapsulation Technologies. Renew. Sustain. Energy Rev. 48, 373–391. doi:10.1016/j.rser.2015.04.044
Wang, J., Gao, W., Zhang, H., Zou, M., Chen, Y., and Zhao, Y. (2018). Programmable Wettability on Photocontrolled Graphene Film. Sci. Adv. 4, eaat7392. doi:10.1126/sciadv.aat7392
Wang, J., Sun, L., Zou, M., Gao, W., Liu, C., Shang, L., et al. (2017). Bioinspired Shape-Memory Graphene Film with Tunable Wettability. Sci. Adv. 3, e1700004. doi:10.1126/sciadv.1700004
Wang, J., Yu, K., Duan, R., Xie, G., and Sund N, B. (2021). Enhanced Thermal Management by Introducing Nanoparticle Composite Phase Change Materials for Cooling Multiple Heat Sources Systems. Energy 227, 120495.
Wen, G.-Q., Xie, R., Liang, W.-G., He, X.-H., Wang, W., Ju, X.-J., et al. (2015). Microfluidic Fabrication and Thermal Characteristics of Core-Shell Phase Change Microfibers with High Paraffin Content. Appl. Therm. Eng. 87, 471–480. doi:10.1016/j.applthermaleng.2015.05.036
Zhang, B., Zhang, Z., Kapar, S., Ataeian, P., Da Silva Bernardes, J., Berry, R., et al. (2019). Microencapsulation of Phase Change Materials with Polystyrene/cellulose Nanocrystal Hybrid Shell via Pickering Emulsion Polymerization. ACS Sustain. Chem. Eng. 7, 17756–17767. doi:10.1021/acssuschemeng.9b04134
Zhang, C., Li, J., and Chen, Y. (2020). Improving the Energy Discharging Performance of a Latent Heat Storage (LHS) Unit Using Fractal-Tree-Shaped Fins. Appl. Energy 259, 114102. doi:10.1016/j.apenergy.2019.114102
Zhang, X., Xie, R., Hu, W.-X., Faraj, Y., Zhao, Q., Fan, X.-X., et al. (2018). Microfluidic Fabrication of Core-Sheath Composite Phase Change Microfibers with Enhanced Thermal Conductive Property. J. Mater Sci. 53, 15769–15783. doi:10.1007/s10853-018-2677-6
Keywords: phase change materials, thermal energy storage, encapsulation, droplet microfluidics, thermoregulation
Citation: Li Z, Liu C, Chen Y, Hao N, Jiang L and Bian W (2022) Application of Monodisperse Encapsulated Phase Change Materials in Building Thermal Energy Storage. Front. Energy Res. 10:918161. doi: 10.3389/fenrg.2022.918161
Received: 12 April 2022; Accepted: 26 April 2022;
Published: 30 May 2022.
Edited by:
Chengbin Zhang, Southeast University, ChinaReviewed by:
Feng Yao, Suzhou University of Science and Technology, ChinaJiayi Zheng, Nanjing University of Science and Technology, China
Copyright © 2022 Li, Liu, Chen, Hao, Jiang and Bian. This is an open-access article distributed under the terms of the Creative Commons Attribution License (CC BY). The use, distribution or reproduction in other forums is permitted, provided the original author(s) and the copyright owner(s) are credited and that the original publication in this journal is cited, in accordance with accepted academic practice. No use, distribution or reproduction is permitted which does not comply with these terms.
*Correspondence: Chuanliang Liu, bGl1Y2h1YW5saWFuZ0BzcGVyaS5jb20uY24=; Yingying Chen, MTgzNjI4MjU5MzJAMTYzLmNvbQ==