- 1Institute of Mineral Resources, Chinese Academy of Geological Sciences, Beijing, China
- 2Institute of Materials Industry, China Center for Information Industry Development, Beijing, China
- 3China University of Geosciences, Beijing, China
- 4Development and Research Center, China Geological Survey, Beijing, China
Gallium is deemed to be a critical mineral given its irreplaceable use in consumer electronics and clean energy technologies. China has become a significant consumer of gallium while also playing a leading role in global gallium production, accounting for more than 90% of the world’s primary output in recent years. However, the quantification and evolution of China’s gallium cycle is limited until now. This study aims to uncover the dynamic flows and stocks of gallium in China during the period of 2005–2020. The results reveal that: 1) From 2005 to 2020, China’s gallium demand increased more than 20-fold, as a result of the booming semiconductor industry and the surging use of gallium in some low-carbon technologies; 2) despite the inefficient recovery issues existed in the production stage, the supply of gallium extracted as a byproduct grew in tandem with the capacity of alumina production, resulting in a significant supply surplus of 948 t by 2020; 3) China exported nearly half of its gallium mainly as raw materials and final products, but still experienced a high reliance on imported gallium-containing intermediate products from abroad, such as integrated circuits; 4) the generations of in-use stocks and end-of-life flows of gallium have accelerated since 2005 and reached about 278 t and 169 t in 2020, respectively. These indicate a large amount of available secondary gallium resource, with nonexistent recycling. The results provide a basis for identifying gallium extraction, use, loss and recycling within its anthropogenic cycle in China, as well as guidance for stakeholders to make future decisions concerning ways to improve resource efficiency and promote sustainable gallium practices from a dynamic material cycle perspective.
1 Introduction
Today, the global energy system is undergoing a dramatic transition from fossil fuels to clean energy in response to the sustainable development goal of combating climate change in line with the Paris Agreement (UNFCCC, 2015). To realize a low-carbon future, many countries have committed to reduce their greenhouse gas emissions to net zero by the middle of this century, which necessitate massive deployment of a wide range of renewable energy technologies such as electric vehicles and battery storage, wind, and solar photovoltaics. Critical minerals have thus played a vital role in the emergence of such clean energy technologies in a decarbonizing world (World Bank, 2020; IEA, 2021). Gallium is an essential scarce metal that has many irreplaceable applications in a variety of industries including aerospace, chemical, medical, military, optoelectronics, telecommunications, and nuclear due to its unique physical and chemical properties (Moskalyk, 2003; Gray et al., 2005). With the accelerating pace of economic development and technological innovation, gallium is becoming one of the most important ingredients for developing key emerging technologies that modern society relies on, such as high-speed wireless communication, energy-efficient lighting, electric vehicles, solar photovoltaics, and wind power (Buchert et al., 2012; Elshkaki and Graedel, 2013; Redlinger et al., 2015). Consequently, gallium consumption has increased rapidly in recent years due to its widening and increasing use in high-tech fields and criticality for the low-carbon transition (Roskill, 2014; U.S. Geological Survey, 2018). Driven by global demand, primary gallium production has grown at a rate of 7% per year on average over the past decades, much faster than most industrial metals (Frenzel et al., 2016). It will almost certainly need to maintain this rate of expansion in order to fulfil the fast-increasing demand for the expanding population and economic growth (Peiró et al., 2013; Frenzel et al., 2017). There are, however, a few countries that possess large reserves of gallium, including China, the United States, Japan, Korea, Germany, and Russia. In particular, China is the world’s top producer of gallium, accounting for 96% of the worldwide supply in 2019 (U.S. Geological Survey, 2021). In the view of the high economic importance and concerns about its supply security, gallium is listed as a critical mineral in the European Union (European Commission, 2011, 2014, 2017, 2020), the United States (U.S. Department of Commerce, 2017), Japan (Hatayama and Tahara, 2015), China (CMLR, 2016), and other economies. In this regard, increasing research have been conducted to determine whether future availability of gallium will hinder the sustainable development of its related industries. Academically, recent assessments of metal supply risk and criticality have indicated that gallium is among those critical materials that are vital to domestic economy, susceptible to supply constraints, and facing a problematic substitutability (Nassar et al., 2015; Hayes and McCullough, 2018; Graedel and Reck, 2016; Fu et al., 2018; Yan et al., 2021). However, among the criticality-related indicators adopted, most studies focus on the geopolitically concentrated production and by-product nature as major determinants (Graedel et al., 2015; Ioannidou et al., 2019; European Commission, 2020). While these previous criticality assessments can provide an intuitive comparison among elements, they are limited in reflecting the true level of criticality. This point was proved by Wang et al. (2020) who quantified the flows and stocks of China’s europium and found the critically of europium is not as severe as previously assessed due to its decreasing demand. As such, their research suggested that the identification of supply risks should not only be based on indicators such as supply concentration and by-product dependence, but also examine the actual mineral supply situations by tracing the changes through supply chain analysis of critical minerals. A recent study by Løvik et al. (2016) explored the linkage between by-product and host metals and pointed out that future availability of gallium is not limited by geological reserves, but by the production of aluminum. According to their findings, there may be a trade-off between supporting ambitious closed-loop recycling, material efficiency methods, and a potential gallium supply crisis in the future. As a result, more rigorous and thorough information for a holistic and dynamic perspective on the critical mineral’s whole supply chain (from production, consumption, loss, stock to end-of-life recycling) is clearly required to address concerns about potential supply shortages, supply security, resource efficiency, and future recycling potential. In order to provide valuable insights on these aspects, it is crucial to quantify the anthropogenic flow of a mineral through each stage of its life cycle, as underlined by many studies (Song et al., 2019; Watari et al., 2020; Zeng et al., 2020; Zhou et al., 2021).
Material flow analysis (MFA) is demonstrated to be an effective tool to provide insights for sustainable resource management by tracking the stocks and flows of minerals in a given temporal-spatial boundary (Chen and Graedel, 2012; Graedel, 2019; Islam and Huda, 2019). This method has been used extensively to explore the supply and demand relation for a number of bulk metals including iron (Li et al., 2018), copper (Zhang et al., 2017), aluminum (Liu and Müller, 2013), nickel (Zeng et al., 2018), lead (Liu et al., 2016), zinc (Meylan and Reck, 2017), and tungsten (Tang et al., 2020). Though there have been numerous studies describing the flows and stocks of critical by-product minerals, such as Lithium (Ziemann et al., 2012; Sun et al., 2018), cobalt (Chen et al., 2019; Sun et al., 2019), chromium (Gao et al., 2022), indium (Werner et al., 2018; Zhou et al., 2021), REEs (Du and Graedel, 2011; Ciacci et al., 2019; Geng et al., 2020), platinum (Rasmussen et al., 2019), and tantalum (Nassar, 2017), existing literature on the life cycle of gallium is limited. A survey of the literature revealed only five MFA studies on gallium. The earliest one was conducted by Yaramadi Dehnavi who developed the first quantification model of gallium flow at global level in the year 2010 from production, consumption to potential recycling (Yaramadi Dehnavi, 2013). Subsequently, a global assessment mainly focused on gallium’s extraction, use, and loss as part of its anthropogenic cycle in the year 2011 was provided (Licht et al., 2015). Løvik et al. (2015) performed a comprehensive analysis of the global gallium cycle in 2011, providing detailed statistical data and technical parameters. They further pointed out that to meet the growing gallium demand in the future, there is a need to increase primary production and improve material efficiency across the system. Based on the global framework, Meylan et al. (2017) traced gallium flows in the United States in 2012, but the purpose of their research was to assess the reliability of MFA results by exemplifying flows of three minor metals that are often considered critical. Finally, the latest study by Eheliyagoda et al. (2019) focused solely on predicting the possible end-of-life gallium waste generation in China until 2050 using linear regression and scenario analysis methods. In addition, there have also been a few attempts to track the current availability and potential future supply constraints of gallium (Frenzel et al., 2016; Song et al., 2022). These studies lay the groundwork for a better understanding of the gallium cycle. However, the existing MFAs on gallium provided only static results at the global level and the national scale of the United States, leaving the shifts and dynamics of gallium flows unclear. As the world’s largest producer and consumer of primary gallium, no comprehensive assessment of China’s gallium flows and stocks has been published yet. Therefore, the objective of this study is to use a dynamic MFA method to model the time-varying evolution of gallium flows and stocks through its main life cycle stages over a period of 2005–2020 in China. Our findings may provide valuable insight into China’s gallium flow structure and recycling possibilities, assisting decision-making.
As for the remainder of this paper: the MFA framework, accounting method, and data sources are described in Section 2. In Section 3, we provide results of an overview of the gallium cycle, as well as details on production, consumption and trade trends. Then comes a detailed examination of dynamic shifts in the in-use stock and end-of-life flows, a discussion of the prospective recycling capacity and an evaluation of uncertainty. Finally, Section 4 draws conclusions and raises policy recommendations.
2 Methods and Data
2.1 System Boundary
Figure 1 depicts the system boundary of this study. The spatial boundary is defined as mainland China excluding Hong Kong, Macau and Taiwan. Due to data availability, the period from 2005 to 2020 is set to be the temporal boundary, which is enough to capture the development and evolution of gallium utilization in modern industry. The entire life cycle of gallium in the anthroposphere can be divided into six principal stages: mining, smelting, refining, manufacturing, use and waste management, as shown in Figure 1. Gallium flowing through these stages in commodities include ores, metals, gallium-contained intermediate products, final products, wastes, and scraps.
Gallium is commonly recovered as a by-product from alumina or zinc processing (Schulte and Foley, 2014), but probably the purpose of processing gallium-contained minerals is not to get gallium. More than 95% of China’s primary gallium was sourced from bauxite for alumina production via the Bayer process, with the remaining produced from the hydrometallurgical process during the extraction of zinc (U.S. Geological Survey, 2018). Therefore, we mainly concentrate on the gallium extraction in the Bayer process as it represents the major source of gallium in this study. Fly ash from coal combustion in power plants, phosphate ores, and aluminous clay stone and mudstone are also plausible sources (Lu et al., 2017), but this study does not address any of these due to their lack of commercial relevance.
2.1.1 Mining
The model begins with the amount of bauxite exploited from the mine. Since there is no existing information on the exact gallium quantities extracted from the lithosphere, it is possible to estimate the total amount of gallium extracted in the mining stage with gallium concentration in bauxite. However, not all mined bauxite that for alumina production are bound to be used in gallium cycle. Therefore, the gallium input in the bauxite production is calculated bottom-up by using the production of primary gallium, gallium content in bauxite and the recovery rate during the mining process. The amount of gallium recovered from the underground and open-pit mines of bauxite is estimated with an average recovery rate of 90% Ministry of Industry and Information Technology of the People’s Republic of China (MIIT), 2013).
2.1.2 Smelting
Bauxite is delivered to the alumina smelter to get by-product gallium via the Bayer process. In the Bayer process, bauxite is dissolved under high temperature in a caustic soda solution, which is the so-called Bayer liquor (Zhao et al., 2012). A portion of gallium clumps in the Bayer liquor, with the rest ending up in a poisonous residue known as “red mud” or in the form of impurities entering the aluminum cycle. Within the Bayer process, the mother liquor containing gallium is recycled in a closed loop. The commonly used method to extract gallium from the Bayer liquor at industrial scale is the ion-exchange resin technology with an average recovery efficiency of 46.5% (Lu et al., 2017).
2.1.3 Refining
The production of 99.99% (4N) pure gallium in the refining stage refers to the primary production, excluding production from scraps. Crude gallium is obtained by smelting and refining of the metal to higher purities (i.e., 6N, 7N) for the electronics industry and communication field is achieved through a combination of methods. At present, high purity gallium is mainly prepared by fractional crystallization and directional crystallization. Considering that the discarded material would be reintroduced in the process chain, the overall yield of purification by crystallization is close to 100% (Yamamura et al., 2007). In the refining stage, there is a stock that fits the characteristics of the Chinese market. The differences between inflows and outflows reflect net changes in stockpiles of refined gallium.
2.1.4 Manufacturing
In the form of metals or gallium-containing compounds, refined gallium is processed to manufacture intermediate products. Common gallium compounds include gallium arsenide (GaAs), gallium nitride (GaN), gallium phosphide (GaP), and copper indium gallium diselenide (CIGS). These are necessary ingredients either for growth of single crystal ingots that would be cut into wafers or for preparing monocrystal film during semiconductor devices production process (Kramer, 1988). As an alloying element, gallium is often added less than 1% of the mass in rare earth magnetic materials for minor improvements of magnetic properties and corrosion resistance (Butcher and Brown, 2014). Low melting point alloys, catalysts, optical glasses, tooth filling materials, and piezoelectric materials are some of the other uses for gallium. The four major gallium-containing industrial uses, which account for more than 90% of gallium usage worldwide and in China, are light emitting diodes (LEDs), integrated circuits (ICs), neodymium iron boron (NdFeB) permanent magnets, and CIGS thin-film photovoltaics (PVs) (Roskill, 2014; U.S. Geological Survey, 2018). The fabrication of GaAs/GaN compound semiconductors, so called wafers, consists of a few microns’ thick epitaxial deposition layer on top of the much thicker substrate. GaAs/GaP-based LEDs and ICs are mainly processed on GaAs substrates, while GaN-based LEDs are produced on the substrates of sapphire, silicon carbide (SiC) or silicon. The whole process of semiconductor manufacturing produces a lot of waste due to backgrinding of the substrates, deposition of epitaxial layers, and trimming, etching, and polishing of wafers, a portion of which is recycled as new scrap in closed loop (Izumi et al., 2001; Ho et al., 2006). As for the manufacturing of NdFeB magnets, gallium is often added in a small amount to improve the performance and corrosion stability of magnets, with final material losses of 20–40% (Binnemans et al., 2013). Recycled gallium in the manufacturing stage may be further refined entering the processing chain.
2.1.5 Use
In the use stage, gallium-containing final products are grouped into eight end-use sectors: general lighting, consumer electronics, home appliances, vehicles, general machineries, wind turbines, equipment, CIGS and others. For consumer electronics, they include mobile phones, computers (desktop PCs, laptops and tablets), and other CEs (digital cameras, camcorders, CD/DVD players, car liquid crystal display (LCD) screens and navigation systems); and for home appliances, LCD televisions, washing machines, refrigerators, and air conditioners are included. Ordinary car and new energy automobile are classified into vehicles; equipment include industrial robots and energy-saving elevators.
For this stage estimations, the inflow can be defined as supply of gallium assigned to distinct end products applying a bottom-up method, as shown in Section 2.2.1. When finished products approach the end of their useful lives, the gallium incorporated in them is either collected for further treatment or formed into in-use stocks.
2.1.6 Waste Management
The end-of-life products can be theoretically recycled for secondary gallium resources in the waste management stage. Typical recycling techniques, on the other hand, promote the recovery of bulk metals and some precious metals, whereas gallium would wind up in the waste stream and end up in the environment. These gallium-containing wastes will be treated with general waste management such as landfill and incineration. Since there is minimal data on the recycling of gallium-bearing end products, the end-of-life flows are classified as non-recoverable wastes entering the environment.
2.2 Accounting Method
Methods are presented here for calculating the flow and stock of the gallium cycle. Gallium flows of the entire cycle are balanced according to the law of conservation of mass (Brunner and Rechberger, 2017). Accordingly, the total gallium inputs into each stage equals the total gallium outputs, plus any stock changes in this stage. Data for all flows and stocks in this study are expressed in gallium metallic equivalent unless otherwise noted.
2.2.1 Quantification of Domestic Gallium Transformation and Loss
Gallium embedded in mined bauxite from the lithosphere is transformed into metal (refined gallium) and subsequently changed into compounds, processed into intermediate products. These products are further assembled into final products that are used in human society, and are eventually discarded when reaching their service life. The incoming and outgoing flows through each stage of gallium cycle can be calculated using the following equations:
where
The gallium inflows into final products are determined by combining production statistics, market share of Ga-containing products, and gallium content per unit, which is shown in Eq. 3:
where U refers to the use stage;
Using the output data and corresponding material yield rates, losses at different stages of the gallium cycle are directly calculated with Eq. 4:
where
2.2.2 Calculation of Gallium-Containing Commodities International Trade
According to the life cycle framework of gallium (Figure 1), a list of traded commodities is identified, which is shown in Supplementary Table S1. Trade flows were estimated by combining the number (or mass) of commodities containing gallium with corresponding content coefficient per commodity (or mass fraction), and market penetration rate, as shown in the following equations:
where m is the different categories of gallium-containing commodities traded;
2.2.3 Determination of Recycling Flows
For LEDs and ICs, new scraps are generated in two ways: one from the GaAs substrate processing waste, and the other from the semiconductor device manufacturing process, both of which can be recycled internally. On the other hand, the PV processing scrap is also served as possible source of gallium recycling, while gallium is not recycled from the magnets processing scrap. The recycling flows of gallium embedded in new scraps from the manufacturing stage are given by the following equation:
where
Considering a lack of statistics for end-of-life gallium in China, the recycling flows of gallium-containing old scraps recycled from the waste management stage cannot be quantitatively obtained.
2.2.4 Estimation of Gallium Stocks
By quantifying the inflow and outflow of the refining stage, we identified a gap in which the outflow is less than the inflow from primary resource and recycled new scrap of gallium. Therefore, we inferred this gap as the stockpile of refined gallium in the light of the mass conservation principle. Stocks in the manufacturing stage are ignored since they are considered stationary over a year (Gao et al., 2022).
In the use stage, the stock is defined as in-use stock referring to the accumulation of materials in the anthroposphere as end-use products (Gerst and Graedel, 2008; Müller et al., 2014). A top-down method is used to determine the in-use stock by quantifying the distinction between input and output flows with Eqs. 8–10:
where Sm,t0 and
2.3 Data Sources
Gallium contents are obtained from research reports, research papers, and expert interviews, as shown in Supplementary Table S1. Yield rate, loss rate and recycling rate in the mining, smelting, refining and manufacturing stages are derived from the literature and relevant domestic metallurgical standards (see Supplementary Table S3). The data for domestic yearly output of 99.99% (4N) pure gallium in the refining stage are obtained from China Nonferrous Metals Industry Association and Antaike’s research report. The annual production data of end-use products are primarily obtained from official and industrial sources, including National Bureau of Statistics of China, Department of Consumer Goods Industry, Ministry of Industry and Information Technology, China Automotive Industry Association, and Yearbook of China Electronic Information Industry. The domestic gallium consumption distribution in “Photovoltaics” and “Others” refers to Antaike’s report (Li, 2021). Data on international trade comes from the U.N. Commodity Trade Database (UN Comtrade, 2021), which uses 6-digit HS codes, and the General Administration of Customs of the People’s Republic of China (GAC) (2005-2016) (2021), which uses 8-digit HS codes. Supplementary Table S1 shows the relevant HS code for each commodity.
2.4 Uncertainty Analysis
There is an element of uncertainty in the calculation results of this study because of different parameters incorporated into the model. Therefore, the Monte Carlo simulation was conducted to quantify the impacts of uncertainties from different input data on the gallium flows and stocks. There are three levels of uncertainty in the ranges: low, medium, and high. We assumed that the data collected directly from official statistics (e.g., domestic output and international trade) would have low uncertainties with a standard deviation of 2%. For data collected from literatures or through expert interview (e.g., coefficient of gallium-containing products), or mine production of gallium, medium uncertainties were assumed. Based on the actual situation, the standard deviation range is set at 5–10%. Those data of technical parameters during production and processing, and lifetime distribution estimated based on other data were assumed to have high uncertainties with the standard deviation varying from 10 to 15%. The impact of uncertainty on eight major results, including domestic gallium consumption, trade, refined gallium surplus, in-use stock, end-of-life flows, manufacturing loss and new scrap recycling flows are shown in Figure 10.
3 Results and Discussion
3.1 Gallium Cycle
Figure 2A depicts the accumulated gallium stocks and flows along its life cycle in China during 2005–2020. Results show that the total bauxite mined in China was around 745.3 Mt (In physical quantity), with 36,519 t gallium available to be extracted theoretically between 2005 and 2020. As few alumina producers have gallium extraction facilities, exact numbers for the amount of bauxite required to extract gallium are unavailable. Therefore, a bottom-up calculation shows that only 12,660 t of the potential gallium contained in mined bauxite was actually utilized for further gallium recovery, a percentage of 35%. Around 6,583 t gallium flowed into the Bayer liquor, with nearly half of the total extraction ending up in red mud (4,811 t) and entering the aluminum cycle (1,266 t) as an impurity. Over the last 16 years, the total primary production of gallium was 3,061 t, with 3,522 t gallium lost to the environment during refining. Among the refined gallium, about 36% was exported to other countries, while almost 54% was consumed domestically in the form of finished products for diverse end purposes. From a dynamic point of view, the scale of gallium cycles in China grew significantly from 2005 to 2020, as indicated by the flow widths in Figures 2B–E. Specifically, from 2005 to 2020, the total mining production, export volume, domestic consumption of gallium increased by more than 20, 8, and 73 times, respectively. These are primarily driven by the large increases in gallium flows to LEDs (from 1 t to 203 t), integrated circuits (from 3 t to 25 t), NdFeB magnets (from 0 t to 88 t), and photovoltaics (from 0 t to 25 t).
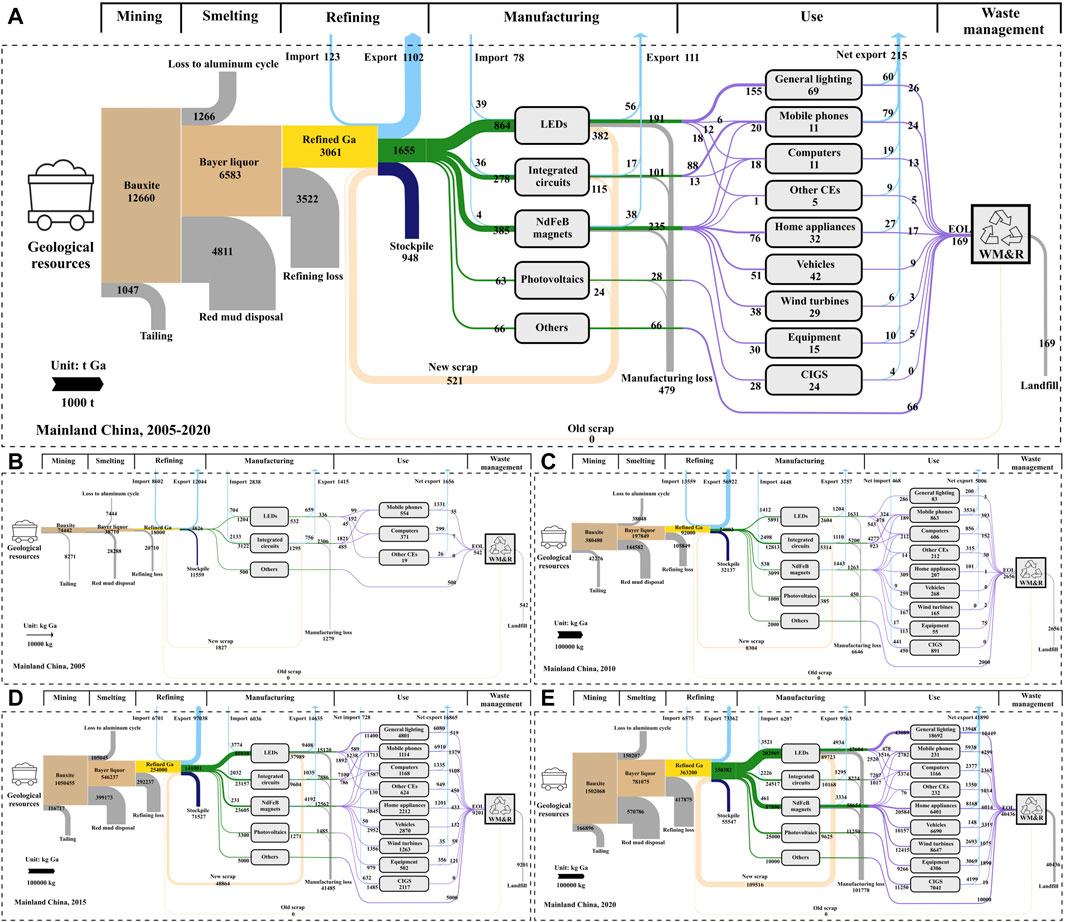
FIGURE 2. Sankey diagram of (A) the accumulated gallium cycle in China during 2005–2020, and four representative 1-year cycles in year (B) 2005 (C) 2010 (D) 2015 (E) 2020 (LED: light-emitting diode; CE: consumer electronic; CIGS: copper indium gallium selenide).
It is estimated that there was roughly 948 t gallium surplus stockpiled by the Fanya Metal Exchange or the government, accounting for approximately 31% of the total gallium output. Large material losses occurred in the manufacturing process following primary production, of which LEDs (273 t) dominated, followed by NdFeB magnets (116 t), integrated circuits (80 t), and thin-film PVs (10 t). However, 521 t gallium was recycled as new scraps during the fabrication of semiconductor devices, resulting in an overall recycling rate of about 17%. Despite the fact that considerable amounts of gallium were used to make various intermediate products, only 622 t of gallium entered the use phase, representing a 38% share of the inflow. In addition, 169 t of the cumulative gallium from nine categories of abandoned end-of-life products was estimated to dissipate in landfills or disperse in other material cycles (Figure 2).
3.2 Gallium Supply and Demand Pattern
Figure 3 illustrates the supply and demand of gallium in China during 2005–2020, reflecting remarkable changes in the supply chain structure of gallium. China had a small primary production of only 18 t in 2005, most of which was exported, with roughly 27% used to meet domestic demand. From 2010 onward, the production capacity of gallium in China increased rapidly, driven by the continual expansion of domestic alumina production (Li et al., 2021) and the gradual maturation of gallium extraction technologies of some producers. As a result, the mineral supply of gallium also rose dramatically and reached a peak at 282 t in 2012, much exceeding the domestic demand. Because of the growing supply expansions but a modest demand market in the early 2010s (Liu et al., 2014), the gallium supply surplus increased to 509 t by 2012 (Figure 4A), which in turn triggered a sharp drop in the market prices of gallium since then. It should be noted that China’s gallium production experienced a significant fluctuation between 2012 and 2016 and reached its bottom at 171 t in 2016 (Figure 3). Such a fluctuation is primarily caused by the production suspension or reduction of many local enterprises due to the ongoing decline of gallium prices from an average of 4100 CNY/kg in 2011 to 875 CNY/kg in 2017 (Figure 4B), which reached a low point in 2016 (790 CNY/kg), lower than the production costs of several enterprises. Overall, the supply of gallium in China has maintained a stable growth and mounted to 363 t in 2020.
On the other hand, owing to the late start of domestic gallium industry, China’s gallium consumption has grown much slower than production prior to 2015 (Figure 3), which is heavily constrained by downstream industries. In recent years, LEDs rapidly infiltrated the Chinese lighting market (CSSLA, 2016) as they have increasingly become the preferred technology for general lighting due to their energy-saving, cost-effective and environmentally friendly properties (Baumgartner et al., 2011; Nair and Dhoble, 2015). This technology transition from traditional lighting sources (i.e., fluorescent lamps) to LEDs stimulated gallium demand by 29 times from 2011 to 2020. Meanwhile, the rising popularity of smartphones and wireless technologies is propelling the market for wider adoption of gallium arsenide technology (Roskill, 2014), which has fueled gallium demand. Moreover, the broadening deployment low-carbon technologies in China, ranging from electric vehicles to wind turbines and solar panels, has also contributed to the soaring demand for gallium in permanent magnets and solar PVs (Guo et al., 2019) by 21 and 25 times from 2011 to 2020, respectively. As shown in Figure 2, gallium consumption in China climbed to 350 t in 2020, roughly 73 times that of 2005. During the past 16 years, approximately 70% of China’s gallium has been consumed in the semiconductor field (52% in LEDs, and 17% in integrated circuits), with a rising share in NdFeB magnets (23%) and solar PVs (4%). The remaining 4% is attributed to other uses that are not further detailed owing to a lack of data. Driven by the progressive implementation of policies and national strategies, such as “Made in China 2025”, “Outline of the 14th Five-Year Plan for National Economic and Social Development”, and “Goal for Carbon Peak by 2030 and Carbon Neutrality by 2060” (CASA, 2016; Zhao et al., 2017), gallium demand in China may further rise in tandem with the fast increasing semiconductor industry and clean energy technologies. The growing momentum for gallium demand indicates the significant implications of gallium in global low-carbon transition for the foreseeable future.
3.3 Trades of Gallium-Containing Commodities
Figure 5 depicts the trajectory of China’s international trade in gallium-contained commodities between 2005 and 2020. China is a net exporter of gallium products throughout its life cycle and has exported about 49% of gallium to the world. The annual net export of gallium kept growing, peaking at 193 t in 2018, and then showed a downward trend after 2019, with the total net export volume of gallium increasing more than eight-fold during 2005–2020. There was a net export of 33 t gallium embodied in the intermediate products, with gross imports and exports calculated to be 78 t and 111 t, respectively. However, China served as a net importer of gallium-containing intermediate products until 2012 and gradually shifted to a net exporter following its changing role in the global semiconductor manufacturing market (Li, 2016; Grimes and Du, 2022). China mainly exported raw materials (refined gallium) and end-use products. The average annual growth rate of export raw materials and end-use products reached 17 and 26% during 2005–2020, respectively.
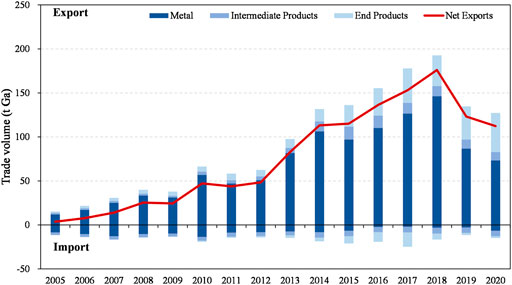
FIGURE 5. Historical evolution of the trade volume of gallium in China between 2005 and 2020 (Data source: China Customs, UN Comtrade. Supplementary Table S4 contains the underlying data).
As shown in Figure 6, China had tight ties with more than fifty countries and regions in terms of exporting gallium-contained products, the majority of which were developed and developing economies. During the study period, Japan is the largest importer of refined gallium (349 t), followed by Germany (175 t), the United States (166 t), the United Kingdom (155 t), and Korea (124 t), while the majority of gallium in intermediate products flowed to China Taiwan, China Hongkong, Korea, India, and Japan. Furthermore, regarding the specific gallium-containing end-use commodities exported, general lighting accounted for the largest proportion (33%), followed by mobile phones (30%), home appliances (10%), computers (7%), and CIGS (7%). It is estimated that China’s cumulative net exports of gallium in final products were around 215 t during 2005–2020.
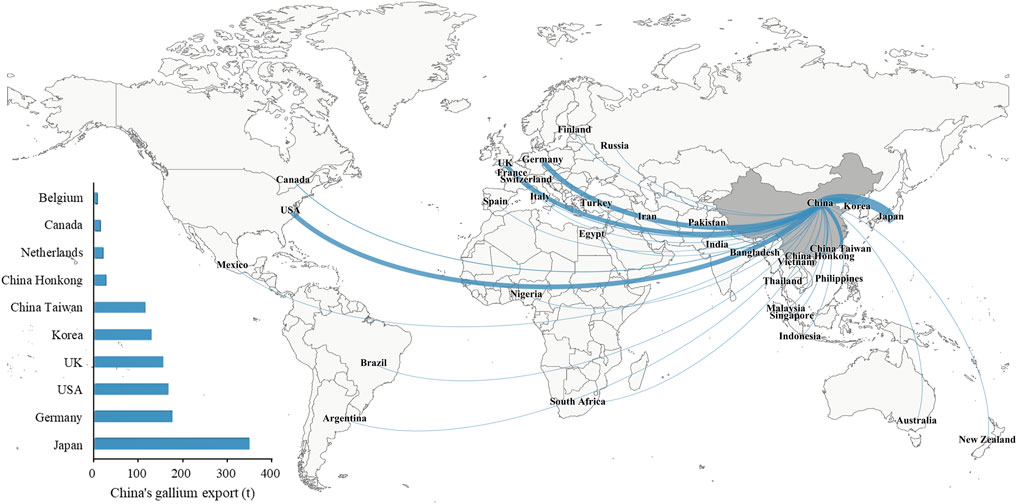
FIGURE 6. China’s accumulated export gallium flows to its key trading partners from 2005 to 2020 (Each flow is proportionate to the volume of gallium exported, and the trade flows under 1 t are not depicted in the graph. Horizontal bars indicate the top ten biggest importers of China’s gallium products).
Generally, the upstream mining and refining stages are highly resource-intensive and characterized by high environmental effects and low technological barriers. In contrast, the downstream fabrication and manufacturing stage is characterized by tech-intensive product design, manufacturing and packing with high value-added (Tang et al., 2020). It is shown that China accounted for more than 90% of the global primary production of gallium in recent years (U.S. Geological Survey, 2021), which means China produces a high percentage of upstream gallium products that have low value added and are resource-intensive. However, as a net exporter of gallium commodities, China is highly dependent on imports of processed products because of its relatively low share in downstream high value-added and tech-intensive gallium-containing manufactured goods produced domestically. For example, Chinese companies accounted for only 5% of the global market for integrated circuits in 2020 (IC insights, 2021). Even the most advanced Chinese semiconductor companies are much smaller in size and technologically lagging compared to international leaders (Li, 2021). In recent years, the increasing demand for integrated circuits in memory, communication chips, sensors and other high-end fields has promoted the import of integrated circuits in China (Fang et al., 2018). According to customs statistics, during 2005–2020, China’s trade deficit of integrated circuits increased year by year and reached a historical peak in 2018 (Figure 7A), reflecting China’s high dependence on the import of integrated circuits. Moreover, China has been the world’s largest consumer of integrated circuits since 2005, but its self-sufficiency rate was only 15.9% by 2020, with the self-sufficiency rate of some cutting-edge integrated circuits (i.e., <10 nm) almost zero (IC insights, 2021). It means that more than 80% of China’s high-end integrated circuits rely on imports from other countries and regions, including China Taiwan, Korea, Japan and the United States (Figure 7B). It is worth noting that the raw materials used to produce high value-added gallium-containing commodities in these countries and regions are mostly sourced from China as shown in Figure 6. Thus, it can be argued that China provides the global economy with high value-added products indirectly through the provision of virgin materials.
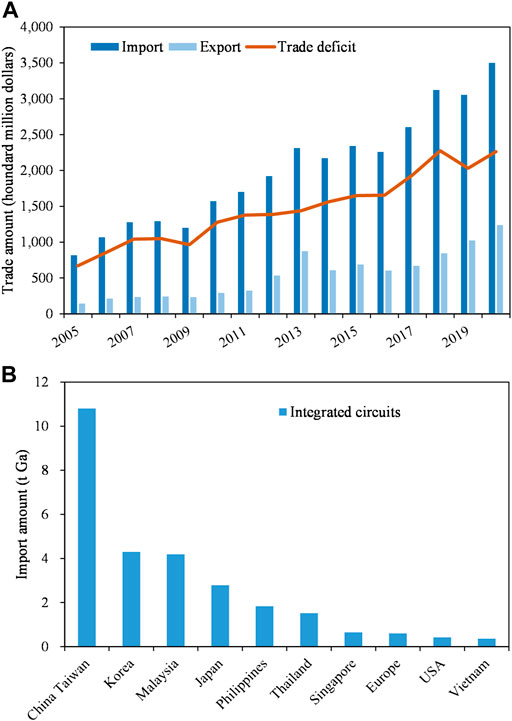
FIGURE 7. (A) Trade volumes of China’s integrated circuits during 2005–2020 (B) Key exporters of gallium-containing intermediate products to China during 2005–2020.
3.4 In-Use Stock and End-Of-Life Flows
Gallium in-use stock accumulation is attributed to the discrepancy between the inflows and outflows in the use phase in each year investigated. As illustrated in Figure 2, consumer electronics (including mobiles, computers and other CEs) accounted for more than 45% of gallium consumption before 2010 and has always been one of the crucial end-use sectors for gallium. As a result of the continuous growth in demand for energy efficient and low carbon applications, inflows into the general lighting, home appliances, vehicles, and CIGS sectors kept increasing. The accumulated gallium consumption has risen sharply since 2015, reaching around 556 t by 2020 (Figure 8A). Meanwhile, the in-use gallium stock expanded 56 times over the research period, with general lighting accounting for the largest share, 35% in 2020, followed by wind turbines (16%), CIGS (13%), vehicles (13%), home appliances (12%), equipment (8%), and consumer electronics (3%). Notably, the net stock accumulation of certain gallium-containing finished products was negative in a given year (Figure 8B). For example, the in-use stock of mobile phones declined in 2008, as mobile phones export remained high and the outflow of spent mobile phones was still increasing after reaching their lifespans.
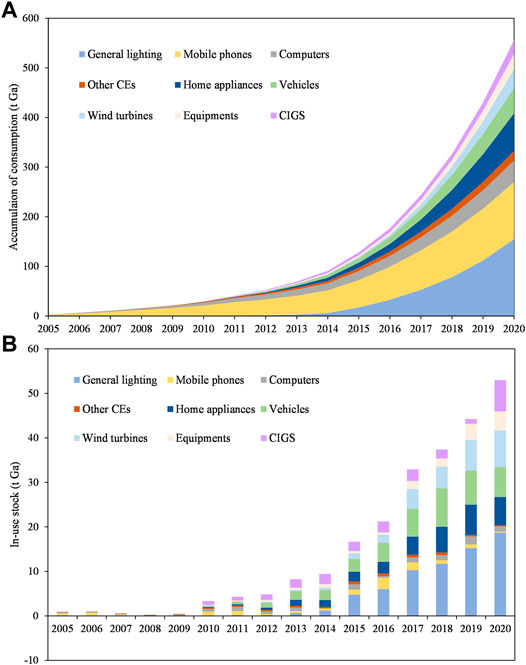
FIGURE 8. Dynamics of (A) accumulation of gallium consumption in China during 2005–2020 (B) yearly net increased gallium in-use stock in China during 2005–2020.
Gallium end-of-life flows from various end-use sectors also increased in lockstep with domestic consumption of gallium. Figure 9 illustrates that total output of gallium scrap increased by 81% from 0.05 t in 2005 to 169 t in 2020. As the “others” sector are all expected to enter the end-of-life stream for a lack of data, consumer electronics made up the largest share of total old scrap generation (25%), as it has a larger market share and a shorter lifespan (∼4 years). The general lighting (15%) was the second largest source of old scarp because of its relatively larger inflow and shorter average lifespan (∼6,000 h), followed by home appliances (10%). Although the total amount of gallium end-of life flow grew rapidly in recent years, there is still a long way to go for China’s gallium waste management system to achieve efficient recovery of end-of-life gallium considering the current recycling situation (Eheliyagoda et al., 2019).
3.5 Recycling Potential
An overall extraction potential of 24% for gallium was estimated in the mining, smelting and refining stages during 2005–2020, showing a low recovery efficiency of raw gallium. The total losses in these stages amount to 10,646 t, more than three times that of the primary production of refined gallium. During the Bayer process, a substantial quantity of gallium can be found in red mud (45%) or refining loss (33%). These indicate that there is still room for improving recovery in the mining, smelting and refining stages. Improving material output in the production process can significantly boost the total resource efficiency (Zhou et al., 2021; Liang et al., 2022). Notably, a considerable portion of loss occurs in the manufacturing process, including substrate production, wafer fabrication, and manufacturing of semiconductor devices (Licht et al., 2015; Løvik et al., 2015). For example, the utilization of substrate material in gallium arsenide device manufacture is inefficient, with a considerable portion of the initial generated material being wasted during processing (i.e., GaAs wafer grinding, cutting, lapping and polishing). Additionally, the waste streams contain a high concentration of dissolved arsenic, which should be handled as hazardous waste (Izumi et al., 2001; Uryu et al., 2003; Torrance et al., 2010). Therefore, more sustainable manufacturing processes are needed to be developed and adopted to improve material yield in the production processes, as well as reduce the environmental impact of gallium arsenide device manufacture.
It is widely recognized that gallium can be recycled from new scraps generated during the manufacturing of GaAs-based semiconductor devices (Eichler, 2012; Løvik et al., 2015). When it comes to recovering gallium from end-of-life products, however, the current recycling rate is less than 1% (Graedel et al., 2011; UNEP–International Resource Panel, 2011; Ueberschaar et al., 2017). The primary reason for this could be that gallium is frequently present in minute amounts in relevant fragments (e.g., printed circuit board, and LED chip) embedded and glued within the end products, posing technical challenges for recycling as well as the lack of a collecting system to recover metals of interest such as gallium (Eheliyagoda et al., 2019). As gallium has been widely used in electronics, electronic waste is becoming an excellent secondary source of gallium metal. According to previous research, China has become the world’s top producer of waste electrical and electronic equipment (Baldé et al., 2017). As a result, numerous studies have focused on recovering gallium from waste electronic devices such as LED lamps, mobile phones, tablets and liquid crystal displays in recent years (Buchert et al., 2012; Cucchiella et al., 2015; Avarmaa et al., 2018; Charles et al., 2020). Many recycling technologies are available for gallium metal in e-waste, including pyrometallurgical processing, hydrometallurgical processing and biohydrometallurgy (De Oliveria et al., 2021). Though these metallurgical extraction techniques for gallium in e-waste can reach recovery efficiencies of more than 90%, they are still in the lab and have a long way to go before commercialization (Swain et al., 2015a, 2015b; Lu et al., 2015; Zhan et al., 2015). Under current industrial waste management practices, when end-of-life gallium-containing products (e.g., waste electronics) are collected, they often wind up in the base metal waste stream (e.g., ferrous metal, copper and aluminum) or for precious metals recovery, without gallium recycled (Fang et al., 2018). In this regard, it is crucial to enhance technologies not only for extracting gallium from primary production and processing wastes, but also for recovery from manufacturing scraps and obsolete products, so as to achieve a circular economy.
Aside from technical impediments to gallium recovery that are very ineffective, a lack of inadequate economic incentives for gallium recycling is also a key challenge. Capturing gallium through improved recycling could be much more expensive than primary resources (Redlinger et al., 2015). Not only that, but the worth of other metals in the same waste end-products might make gallium recovery difficult. To be specific, because neodymium in magnets is currently more valuable than gallium, neodymium recovery from manufacturing wastes is limited, and even from these end-of-life materials is unfeasible (Schulze and Buchert., 2016; Geng et al., 2020; Yao et al., 2021). With the widespread usage of gallium in the magnet industry (Figure 2), it is unclear whether recovering gallium from NdFeB manufacturing scraps and end-of-life products would be economically viable in the future. Meanwhile, as solar PVs penetrate more deeply into the market (Grandell et al., 2016), end-of-life recycling of CIGS will also be a significant source of gallium in the future.
3.6 Uncertainty Evaluation
In Figure 10, a box plot illustrates the maximum, minimum, median values and quartiles of the uncertainty evaluations results for China’s gallium cycle in 2020. For each flow, these data provide a good representation of the uncertainty. Domestic gallium consumption, recycled new scrap and manufacturing loss had higher uncertainty ranges (box heights) than the rest, indicating that these flows were more unpredictable. The reason for this is because the estimation of these flows involves several technical parameters with wider standard deviation range. Relatively flat boxes indicated lower uncertainties in other flows or stocks, indicating that they had higher concentrations of simulation values. Overall, a high degree of reliability was observed in the uncertainty assessment results.
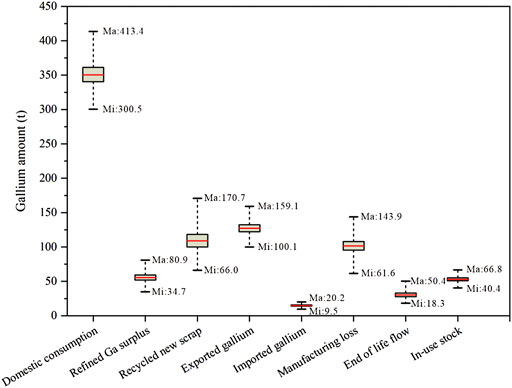
FIGURE 10. Results of uncertainty evaluation for China’s gallium cycle in 2020. (Top line is the maximum value (Ma); bottom line is the minimum value (Mi); box top is the third quartile; box bottom is the first quartile; thick red line in center of the box is the data median).
4 Conclusion and Policy Implications
This study presents a comprehensive description and analysis of China’s gallium flows and stocks between 2005 and 2020, based on a detailed dynamic MFA model. Not only does this research provide information on gallium utilization and recycling possibilities, but also supports policies targeted at increasing resource efficiency. Main conclusions can be drawn as follows:
First, due to domestic capacity expansion, China’s primary gallium production is expected to grow 20-fold from 2005 to 2020, making it the world’s largest producer. Meanwhile, the gallium consumption grew rapidly to approximately 350 t by 2020. Despite the rapid growth of gallium consumption in recent years, with more than 70% used for making semiconductors, there is still an oversupply of 948 t of refined gallium stockpiled. This indicates a disequilibrium between supply and demand, which is not conducive to the sustained gallium development in the long run. It is therefore imperative to not only steer the upstream production of gallium in a reasonable manner, but also enhance gallium industry by encouraging the downstream use of gallium.
Second, although China has become the world’s biggest supplier of raw gallium and exported 1,102 t of unwrought or wrought gallium, it still relies on importing high-end gallium products (i.e., integrated circuits) from abroad, whose raw materials are originally sourced from China. It is possible that the heavy reliance on imports of high-end gallium products will result in an unhealthy development of the domestic gallium industry. Thus, it is urgently needed to improve the advanced integrated circuit processing technology to promote the development of semiconductor industry, which is helpful for enhancing China’s position in the downstream gallium industry chain.
Third, results show that the losses amounted to 11,125 t during the study period, among which 10,646 t was attributed to the inefficient mining, beneficiation and refining, while 479 t existed in the manufacturing process, with an overall recycling rate of 17% for the new scraps. Although more efficient recycling can be achieved to some extent, they are still in the experimental stage due to technical and economic limitations. The cumulative in-use gallium stock experienced a boom period during the last decade, reaching about 238 t in 2020. Besides, the total gallium end-of-life flows increased from 0.05 t in 2005 to 169 t in 2020, which suggests a great potential for recycling. However, there is no end-of-life recycling of gallium commercially, reflecting an extremely low utilization efficiency of secondary gallium resources. Therefore, more policies and investment should be given in encouraging cultivation of advanced technologies to improve the system-wide yield efficiency and recovery rate of gallium throughout its whole life cycle. Attention should be paid particularly to semiconductor manufacturing scraps, since they accounted for more than half of gallium processing waste streams, while recycling LED scraps such as obsolete LED lamps and electronics is of equal importance from a long-term perspective.
Data Availability Statement
The original contributions presented in the study are included in the article/Supplementary Material, further inquiries can be directed to the corresponding authors.
Author Contributions
HJ: Conceptualization, Methodology, Software, Writing-original draft, review and editing; YZ: Data curation, Methodology; AW: Writing-review and editing, Supervision, Funding acquisition; GW: Conceptualization, Formal analysis; TL: Writing-review and editing; CW: Software, Visualization; WX: Formal analysis; ZM: Formal analysis; PL: Formal analysis.
Funding
This study is supported by the National Natural Science Foundation of China (Grant No. 71991485, and No. 71991480), Basic Science Center Project for National Natural Science Foundation of China (Grant No. 72088101), and geological survey projects of China Geological Survey (Grant No. DD20221795).
Conflict of Interest
The authors declare that the research was conducted in the absence of any commercial or financial relationships that could be construed as a potential conflict of interest.
Publisher’s Note
All claims expressed in this article are solely those of the authors and do not necessarily represent those of their affiliated organizations, or those of the publisher, the editors and the reviewers. Any product that may be evaluated in this article, or claim that may be made by its manufacturer, is not guaranteed or endorsed by the publisher.
Acknowledgments
The authors would like to thank Jianwu Li and Yilan Li for their helpful recommendations while authoring this work. The editor and two reviewers are appreciated for their insightful and constructive remarks, which substantially improved this manuscript.
Supplementary Material
The Supplementary Material for this article can be found online at: https://www.frontiersin.org/articles/10.3389/fenrg.2022.944617/full#supplementary-material
References
Avarmaa, K., Yliaho, S., and Taskinen, P. (2018). Recoveries of Rare Elements Ga, Ge, in and Sn from Waste Electric and Electronic Equipment through Secondary Copper Smelting. Waste Manag. 71, 400–410. doi:10.1016/j.wasman.2017.09.037
Baldé, C. P., Forti, V., Gray, V., Kuehr, R., and Stegmann, P. (2017). The Global E-Waste Monitor 2017. Bonn/Geneva/Vienna: United Nations University UNU, International Telecommunication Union ITU & International Solid Waste Association ISWA.
Baumgartner, T., Wunderlich, F., Wee, D., Jaunlich, A., Sato, T., Erxleben, U., et al. (2011). Lighting the Way: Perspectives on the Global Lighting Market. McKinsey & Company, Inc.\
Binnemans, K., Jones, P. T., Blanpain, B., Van Gerven, T., Yang, Y., Walton, A., et al. (2013). Recycling of Rare Earths: a Critical Review. J. Clean. Prod. 51, 1–22. doi:10.1016/j.jclepro.2012.12.037
Brunner, P. H., and Rechberger, H. (2017). Handbook of Material Flow Analysis: For Environmental, Resource, and Waste Engineers. Boca Raton, FL: CRC Press.
Buchert, M., Manhart, A., Bleher, D., and Pingel, D. (2012). Recycling Critical Raw Materials from Waste Electronic Equipment. FreiburgGermany: Ӧko-Institut e.V.
Butcher, T., and Brown, T. (2014). “Gallium,” in Critical Metals Handbook. Editor G. Gunn (Hoboken: John Wiley & Sons), 150
CASA (2016). The Third Generation Semiconductor Materials and Applications Industry Development Report in 2016. China advanced semiconductor industry innovation alliance. (in Chinese).
Charles, R. G., Douglas, P., Dowling, M., Liversage, G., and Davies, M. L. (2020). Towards Increased Recovery of Critical Raw Materials from WEEE- Evaluation of CRMs at a Component Level and Pre-processing Methods for Interface Optimisation with Recovery Processes. Resour. Conservation Recycl. 161, 104923. doi:10.1016/j.resconrec.2020.104923
Chen, W., and Graedel, T. E. (2012). Anthropogenic Cycles of the Elements: A Critical Review. Environ. Sci. Technol. 46, 8574–8586. doi:10.1021/es3010333
Chen, Z., Zhang, L., and Xu, Z. (2019). Tracking and Quantifying the Cobalt Flows in Mainland China during 1994-2016: Insights into Use, Trade and Prospective Demand. Sci. Total Environ. 672, 752–762. doi:10.1016/j.scitotenv.2019.02.411
China Solid State Lighting Alliance (Cssla) (2016). China Semiconductor Lighting Industry Development White Book 2016. Available at: https://www.iea.org/reports/the-role-of-critical-minerals-in-clean-energy-transitionshttp://www.casa-china.cn/uploads/soft/170322/6-1F322160S7.pdf December 11, 2021).
Chinese Ministry of Land and Resources (CMLR) (2016). National Mineral Resources Planning (2016-2020). Beijing: Ministry of Natural Resources of the People’s Republic of China. (in Chinese).
Ciacci, L., Vassura, I., Cao, Z., Liu, G., and Passarini, F. (2019). Recovering the “New Twin”: Analysis of Secondary Neodymium Sources and Recycling Potentials in Europe. Resour. Conservation Recycl. 142, 143–152. doi:10.1016/j.resconrec.2018.11.024
Cucchiella, F., D’Adamo, I., Lenny Koh, S. C., and Rosa, P. (2015). Recycling of WEEEs: An Economic Assessment of Present and Future E-Waste Streams. Renew. Sustain. Energy Rev. 51, 263–272. doi:10.1016/j.rser.2015.06.010
De Oliveira, R. P., Benvenuti, J., and Espinosa, D. C. R. (2021). A Review of the Current Progress in Recycling Technologies for Gallium and Rare Earth Elements from Light-Emitting Diodes. Renew. Sustain. Energy Rev. 145, 111090. doi:10.1016/j.rser.2021.111090
Du, X., and Graedel, T. E. (2011). Global In-Use Stocks of the Rare Earth Elements: a First Estimate. Environ. Sci. Technol. 45, 4096–4101. doi:10.1021/es102836s
Eheliyagoda, D., Zeng, X., Wang, Z., Albalghiti, E., and Li, J. (2019). Forecasting the Temporal Stock Generation and Recycling Potential of Metals towards a Sustainable Future: The Case of Gallium in China. Sci. Total Environ. 689, 332–340. doi:10.1016/j.scitotenv.2019.06.413
Eichler, S. (2012). “Green Gallium Arsenide (GaAs) Substrate Manufacturing,” in 2012 International Conference on Compound Semiconductor Manufacturing Technology (Boston, Massachusettes: CS ManTech).
Elshkaki, A., and Graedel, T. E. (2013). Dynamic Analysis of the Global Metals Flows and Stocks in Electricity Generation Technologies. J. Clean. Prod. 59, 260–273. doi:10.1016/j.jclepro.2013.07.003
European Commission (2017). “On the 2017 List of Critical Raw Materials for the EU,” in Ad-hoc Working Group on Defining Critical Raw Minerals of the Raw Materials Supply Group. Luxembourg: Publications Office of the European Union.
European Commission (2014). Ad-hoc Working Group on Defining Critical Raw Minerals of the Raw Materials Supply Group.On the Review of the List of Critical Raw Materials for the EU and the Implementation of the Raw Materials Initiative. Luxembourg: Publications Office of the European Union.
European Commission (2020). Study on the EU’s List of Critical Raw Materials–Final Report. Luxembourg: Publications Office of the European Union.
European Commission (2011). “Tackling the Challenges in Commodity Markets and on Raw Materials,” in Ad-hoc Working Group on Defining Critical Raw Minerals of the Raw Materials Supply Group. Luxembourg: Publications Office of the European Union.
Fang, S., Yan, W., Cao, H., Song, Q., Zhang, Y., and Sun, Z. (2018). Evaluation on End-Of-Life LEDs by Understanding the Criticality and Recyclability for Metals Recycling. J. Clean. Prod. 182, 624–633. doi:10.1016/j.jclepro.2018.01.260
Frenzel, M., Ketris, M. P., Seifert, T., and Gutzmer, J. (2016). On the Current and Future Availability of Gallium. Resour. Policy 47, 38–50. doi:10.1016/j.resourpol.2015.11.005
Frenzel, M., Mikolajczak, C., Reuter, M. A., and Gutzmer, J. (2017). Quantifying the Relative Availability of High-Tech By-Product Metals - the Cases of Gallium, Germanium and Indium. Resour. Policy 52, 327–335. doi:10.1016/j.resourpol.2017.04.008
Fu, X., Polli, A., and Olivetti, E. (2018). High‐Resolution Insight into Materials Criticality: Quantifying Risk for By‐Product Metals from Primary Production. J. Industrial Ecol. 23, 452–465. doi:10.1111/jiec.12757
Gao, Z., Geng, Y., Zeng, X., Tian, X., Yao, T., Song, X., et al. (2022). Evolution of the Anthropogenic Chromium Cycle in China. J Industrial Ecol. 26, 592–608. doi:10.1111/jiec.13207
General Administration of Customs of the People’s Republic of China GAC 2005-2016 (2021). China Customs Statistical Yearbook. Beijing, China: China Customs Press.
General Administration of Customs of the People’s Republic of China (GAC) (2021). China Customs Statistics Database. Available at: http://www.customs.gov.cn/December 20, 2021).
Geng, J., Hao, H., Sun, X., Xun, D., Liu, Z., and Zhao, F. (2020). Static Material Flow Analysis of Neodymium in China. J. Industrial Ecol. 25, 114–124. doi:10.1111/jiec.13058
Gerst, M. D., and Graedel, T. E. (2008). In-use Stocks of Metals: Status and Implications. Environ. Sci. Technol. 42, 7038–7045. doi:10.1021/es800420p
Graedel, T. E., Allwood, J., Birat, J. P., Reck, B. K., Sibley, S. F., Sonnemann, G., et al. (2011). “Recycling Rates of Metals: A Status Report,” in A Report of the Working Group on the Global Metal Flows to the International Resource Panel (United Nations Environment Programme).
Graedel, T. E., Harper, E. M., Nassar, N. T., Nuss, P., and Reck, B. K. (2015). Criticality of Metals and Metalloids. Proc. Natl. Acad. Sci. U.S.A. 112, 4257–4262. doi:10.1073/pnas.1500415112
Graedel, T. E. (2019). Material Flow Analysis from Origin to Evolution. Environ. Sci. Technol. 53, 12188–12196. doi:10.1021/acs.est.9b03413
Graedel, T. E., and Reck, B. K. (2016). Six Years of Criticality Assessments: what Have We Learned So Far? J. Industrial Ecol. 20, 692–699. doi:10.1111/jiec.12305
Grandell, L., Lehtilä, A., Kivinen, M., Koljonen, T., Kihlman, S., and Lauri, L. S. (2016). Role of Critical Metals in the Future Markets of Clean Energy Technologies. Renew. Energy 95, 53–62. doi:10.1016/j.renene.2016.03.102
Gray, F., Kramer, D. A., and Bliss, J. D. (2005). Gallium and Gallium Compounds. Kirk-Othmer Encycl. Chem. Technol. 12, 337–364. doi:10.1002/0471238961.0701121219010215.a01.pub2
Grimes, S., and Du, D. (2022). China's Emerging Role in the Global Semiconductor Value Chain. Telecommun. Policy 46, 101959. doi:10.1016/j.telpol.2020.101959
Hatayama, H., and Tahara, K. (2015). Criticality Assessment of Metals for Japan’s Resource Strategy. Mat. Trans. 56, 229–235. doi:10.2320/matertrans.m2014380
Hayes, S. M., and McCullough, E. A. (2018). Critical Minerals: A Review of Elemental Trends in Comprehensive Criticality Studies. Resour. Policy 59, 192–199. doi:10.1016/j.resourpol.2018.06.015
Ho, W. J., Liu, J., Chou, H. C., Wu, C. S., Tsai, T. C., Chang, W. D., et al. (2006). Manufacturing of GaAs MMICs for Wireless Communications Applications. J. Semicond. Tech. Sci. 6, 136
IC Insights (2021). McClean Report – a Complete Analysis and Forecast of the Integrated Circuit Industry. IC Insights. Available at: https://www.iea.org/reports/the-role-of-critical-minerals-in-clean-energy-transitionshttp://www.icinsights.com/services/mcclean-report/(Accessed April 20, 2022).
IEA (2021). The Role of Critical Minerals in Clean Energy Transitions. Available at: https://www.iea.org/reports/the-role-of-critical-minerals-in-clean-energy-transitions (Accessed May 25, 2022).
Ioannidou, D., Heeren, N., Sonnemann, G., and Habert, G. (2019). The Future in and of Criticality Assessments. J. Industrial Ecol. 23, 751–766. doi:10.1111/jiec.12834
Islam, M. T., and Huda, N. (2019). Material Flow Analysis (MFA) as a Strategic Tool in E-Waste Management: Applications, Trends and Future Directions. J. Environ. Manag. 244, 344–361. doi:10.1016/j.jenvman.2019.05.062
Izumi, S., Shirahama, H., and Kouji, Y. (2001). Environmental Safety Issues for Molecular Beam Epitaxy Platform Growth Technology. J. Cryst. Growth 227-228, 150–154. doi:10.1016/s0022-0248(01)00654-6
Kramer, D. A. (1988). Gallium and Gallium Arsenide: Supply, Technology, and Uses. United States: U.S. Department of the Interior, Bureau of Mines.
Li, Q., Dai, T., Gao, T., Zhong, W., Wen, B., Li, T., et al. (2021). Aluminum Material Flow Analysis for Production, Consumption, and Trade in China from 2008 to 2017. J. Clean. Prod. 296, 126444. doi:10.1016/j.jclepro.2021.126444
Li, Q., Dai, T., Wang, G., Cheng, J., Zhong, W., Wen, B., et al. (2018). Iron Material Flow Analysis for Production, Consumption, and Trade in China from 2010 to 2015. J. Clean. Prod. 172, 1807–1813. doi:10.1016/j.jclepro.2017.12.006
Li, Y. L. (2021). Antaike Non-ferrous Metals Market Development Report in 2021: Gallium. Beijing, China, 1–27. (in Chinese).
Li, Y. (2016). “State, Market, and Business Enterprise: Development of the Chinese Integrated Circuit Foundries,” in China as an Innovation Nation. Editors Y. Zhou, W. Lazonick, and Y. Sun (Oxford, UK: Oxford University Press), 306
Li, Y. (2021). “The Semiconductor Industry: A Strategic Look at China's Supply Chain,” in The New Chinese Dream, Palgrave Studies of Internationalization in Emerging Markets. Editors F. Spigarelli, and J. R. McIntyre (UKCham: Palgrave Macmillan), 121–136. doi:10.1007/978-3-030-69812-6_8
Liang, J., Geng, Y., Zeng, X., Gao, Z., and Tian, X. (2022). Toward Sustainable Utilization of Tungsten: Evidence from Dynamic Substance Flow Analysis from 2001 to 2019 in China. Resour. Conservation Recycl. 182, 106307. doi:10.1016/j.resconrec.2022.106307
Licht, C., Peiró, L. T., and Villalba, G. (2015). Global Substance Flow Analysis of Gallium, Germanium, and Indium: Quantification of Extraction, Uses, and Dissipative Losses within Their Anthropogenic Cycles. J. Industrial Ecol. 19, 890–903. doi:10.1111/jiec.12287
Liu, G., and Müller, D. B. (2013). Mapping the Global Journey of Anthropogenic Aluminum: A Trade-Linked Multilevel Material Flow Analysis. Environ. Sci. Technol. 47, 11873–11881. doi:10.1021/es4024404
Liu, M., Huo, Y. B., and Pei, L. S. (2014). Antaike Non-ferrous Metals Market Development Report in 2014: Gallium. Beijing, China, 1–31. (in Chinese).
Liu, W., Chen, L., and Tian, J. (2016). Uncovering the Evolution of Lead In-Use Stocks in Lead-Acid Batteries and the Impact on Future Lead Metabolism in China. Environ. Sci. Technol. 50, 5412–5419. doi:10.1021/acs.est.6b00775
Løvik, A. N., Restrepo, E., and Müller, D. B. (2016). Byproduct Metal Availability Constrained by Dynamics of Carrier Metal Cycle: the Gallium-Aluminum Example. Environ. Sci. Technol. 50, 8453. doi:10.1021/acs.est.6b02396
Løvik, A. N., Restreppo, E., and Müller, D. B. (2015). The Global Anthropogenic Gallium System: Determinants of Demand, Supply and Efficiency Improvements. Environ. Sci. Technol. 49, 5704. doi:10.1021/acs.est.5b00320
Lu, F., Xiao, T., Lin, J., Ning, Z., Long, Q., Xiao, L., et al. (2017). Resources and Extraction of Gallium: A Review. Hydrometallurgy 174, 105–115. doi:10.1016/j.hydromet.2017.10.010
Melo, M. T. (1999). Statistical Analysis of Metal Scrap Generation: the Case of Aluminium in Germany. Resour. Conservation Recycl. 26, 91–113. doi:10.1016/s0921-3449(98)00077-9
Meylan, G., Reck, B. K., Rechberger, H., Graedel, T. E., and Schwab, O. (2017). Assessing the Reliability of Material Flow Analysis Results: The Cases of Rhenium, Gallium, and Germanium in the United States Economy. Environ. Sci. Technol. 51, 11839–11847. doi:10.1021/acs.est.7b03086
Meylan, G., and Reck, B. K. (2017). The Anthropogenic Cycle of Zinc: Status Quo and Perspectives. Resour. Conservation Recycl. 123, 1–10. doi:10.1016/j.resconrec.2016.01.006
Ministry of Industry and Information Technology of the People's Republic of China (MIIT) (2013). Aluminium Industry Specification Conditions. Available at: https://www.miit.gov.cn/zwgk/zcwj/wjfb/yclgy/art/2020/art_0f0125404e2749399d30e080da850203.html (Accessed April 10, 2022).
Moskalyk, R. R. (2003). Gallium: the Backbone of the Electronics Industry. Miner. Eng. 16, 921–929. doi:10.1016/j.mineng.2003.08.003
Müller, E., Hilty, L. M., Widmer, R., Schluep, M., and Faulstich, M. (2014). Modeling Metal Stocks and Flows: A Review of Dynamic Material Flow Analysis Methods. Environ. Sci. Technol. 48, 2102–2113. doi:10.1021/es403506a
Nair, G. B., and Dhoble, S. J. (2015). A Perspective Perception on the Applications of Light-Emitting Diodes. Luminescence 30, 1167–1175. doi:10.1002/bio.2919
Nassar, N. T., Graedel, T. E., and Harper, E. M. (2015). By-product Metals Are Technologically Essential but Have Problematic Supply. Sci. Adv. 1, e1400180. doi:10.1126/sciadv.1400180
Nassar, N. T. (2017). Shifts and Trends in the Global Anthropogenic Stocks and Flows of Tantalum. Resour. Conservation Recycl. 125, 233–250. doi:10.1016/j.resconrec.2017.06.002
Peiró, L. T., Méndez, G. V., and Ayres, R. U. (2013). Material Flow Analysis of Scarce Metals: Sources, Functions, End-Uses and Aspects for Future Supply. Environ. Sci. Technol. 47, 2939. doi:10.1021/es301519c
Rasmussen, K. D., Wenzel, H., Bangs, C., Petavratzi, E., and Liu, G. (2019). Platinum Demand and Potential Bottlenecks in the Global Green Transition: A Dynamic Material Flow Analysis. Environ. Sci. Technol. 53, 11541–11551. doi:10.1021/acs.est.9b01912
Redlinger, M., Eggert, R., and Woodhouse, M. (2015). Evaluating the Availability of Gallium, Indium, and Tellurium from Recycled Photovoltaic Modules. Sol. Energy Mater. Sol. Cells 138, 58–71. doi:10.1016/j.solmat.2015.02.027
Roskill (2014). Gallium: Global Industry Markets and Outlook. London: Roskill Information Services Ltd. (in Chinese).
Schulte, R. F., and Foley, N. K. (2014). Compilation of Gallium Resource Data for Bauxite Deposits: U.S. Geological Survey Open-File Report 2013-1272. Reston, VA: Mineral Resources Program. doi:10.3133/ofr20131272
Schulze, R., and Buchert, M. (2016). Estimates of Global REE Recycling Potentials from NdFeB Magnet Material. Resour. Conserv. Recycl. 113, 12. doi:10.1016/j.resconrec.2016.05.004
Song, H., Wang, C., Sen, B., and Liu, G. (2022). China Factor: Exploring the Byproduct and Host Metal Dynamics for Gallium-Aluminum in a Global Green Transition. Environ. Sci. Technol. 56, 2699–2708. doi:10.1021/acs.est.1c04784
Song, J., Yan, W., Cao, H., Song, Q., Ding, H., Lv, Z., et al. (2019). Material Flow Analysis on Critical Raw Materials of Lithium-Ion Batteries in China. J. Clean. Prod. 215, 570–581. doi:10.1016/j.jclepro.2019.01.081
Sun, X., Hao, H., Liu, Z., Zhao, F., and Song, J. (2019). Tracing Global Cobalt Flow: 1995-2015. Resour. Conservation Recycl. 149, 45–55. doi:10.1016/j.resconrec.2019.05.009
Sun, X., Hao, H., Zhao, F., and Liu, Z. (2018). Global Lithium Flow 1994-2015: Implications for Improving Resource Efficiency and Security. Environ. Sci. Technol. 52, 2827–2834. doi:10.1021/acs.est.7b06092
Swain, B., Mishra, C., Kang, L., Park, K.-S., Lee, C. G., and Hong, H. S. (2015b). Recycling Process for Recovery of Gallium from GaN an E-Waste of LED Industry through Ball Milling, Annealing and Leaching. Environ. Res. 138, 401–408. doi:10.1016/j.envres.2015.02.027
Swain, B., Mishra, C., Lee, C. G., Park, K.-S., and Lee, K.-J. (2015a). Valorization of GaN Based Metal-Organic Chemical Vapor Deposition Dust a Semiconductor Power Device Industry Waste through Mechanochemical Oxidation and Leaching: A Sustainable Green Process. Environ. Res. 140, 704–713. doi:10.1016/j.envres.2015.06.003
Tang, L., Wang, P., Graedel, T. E., Pauliuk, S., Xiang, K., Ren, Y., et al. (2020). Refining the Understanding of China's Tungsten Dominance with Dynamic Material Cycle Analysis. Resour. Conservation Recycl. 158, 104829. doi:10.1016/j.resconrec.2020.104829
Torrance, K. W., Keenan, H. E., Hursthouse, A. S., and Stirling, D. (2010). Measurement of Arsenic and Gallium Content of Gallium Arsenide Semiconductor Waste Streams by ICP-MS. J. Environ. Sci. Health, Part A 45, 471–475. doi:10.1080/10934520903540133
Ueberschaar, M., Otto, S. J., and Rotter, V. S. (2017). Challenges for Critical Raw Material Recovery from WEEE - the Case Study of Gallium. Waste Manag. 60, 534–545. doi:10.1016/j.wasman.2016.12.035
UN Comtrade (2021). UN Comtrade International Trade Statistics Database. Available at: https://comtrade.un.org (Accessed December 1, 2021).
UNEP–International Resource Panel (2011). Recycling Rates of Metals – A Status Report. Available at: https://wedocs.unep.org/bitstream/handle/20.500.11822/8702/Recycling_Metals.pdf?sequence=1&isAllowed=y (Accessed May 31, 2022).
Uryu, T., Yoshinaga, J., and Yanagisawa, Y. (2003). Environmental Fate of Gallium Arsenide Semiconductor Disposal. J. Industrial Ecol. 7, 103–112. doi:10.1162/108819803322564370
U.S. Department of Commerce (2017). A Federal Strategy to Ensure Secure and Reliable Supplies of Critical Minerals. Available at: https://www.commerce.gov/sites/default/files/2020-01/Critical_Minerals_Strategy_Final.pdf (Accessed November 20, 2021).
U.S. Geological Survey (2021). Gallium Mineral Commodity Summaries 2021. Available at: https://www.usgs.gov/centers/national-minerals-information-center/gallium-statistics-and-information (Accessed April 30, 2022).
U.S. Geological Survey (2018). Minerals Yearbook of Gallium 2018. Available at: https://www.usgs.gov/centers/national-minerals-information-center/gallium-statistics-and-information (Accessed November 20, 2021).
Wang, Q., Wang, P., Qiu, Y., Dai, T., and Chen, W. (2020). Byproduct Surplus: Lighting the Depreciative Europium in China's Rare Earth Boom. Environ. Sci. Technol. 54, 14686–14693. doi:10.1021/acs.est.0c02870
Watari, T., Nansai, K., and Nakajima, K. (2020). Review of Critical Metal Dynamics to 2050 for 48 Elements. Resour. Conservation Recycl. 155, 104669. doi:10.1016/j.resconrec.2019.104669
Werner, T. T., Ciacci, L., Mudd, G. M., Reck, B. K., and Northey, S. A. (2018). Looking Down under for a Circular Economy of Indium. Environ. Sci. Technol. 52, 2055–2062. doi:10.1021/acs.est.7b05022
World Bank (2020). Minerals for Climate Action: The Mineral Intensity of the Clean Energy Transition. Washington, DC: World Bank. Available at: https://pubdocs.worldbank.org/en/961711588875536384/Minerals-for-Climate-Action-The-Mineral-Intensity-of-the-Clean-Energy-Transition (Accessed May 25, 2022).
Yamamura, T., Kato, H., Ohgami, T., Tayama, K., and Okuda, K. (2007). Refining Process for High Purity Gallium for Producing Compound Semiconductor and Apparatus for the Same. European: EU Patent No 1099770European Patent Office.
Yan, W., Wang, Z., Cao, H., Zhang, Y., and Sun, Z. (2021). Criticality Assessment of Metal Resources in China. iScience 24, 102524. doi:10.1016/j.isci.2021.102524
Yao, T., Geng, Y., Sarkis, J., Xiao, S., and Gao, Z. (2021). Dynamic Neodymium Stocks and Flows Analysis in China. Resour. Conservation Recycl. 174, 105752. doi:10.1016/j.resconrec.2021.105752
Yaramadi Dehnavi, P. (2013). Global Cycle of Gallium Production, Use and Potential Recycling. Stockholm: Royal Institute of Technology. [dissertation/master’s thesis].
Zeng, X., Ali, S. H., Tian, J., and Li, J. (2020). Mapping Anthropogenic Mineral Generation in China and its Implications for a Circular Economy. Nat. Commun. 11, 1544. doi:10.1038/s41467-020-15246-4
Zeng, X., Zheng, H., Gong, R., Eheliyagoda, D., and Zeng, X. (2018). Uncovering the Evolution of Substance Flow Analysis of Nickel in China. Resour. Conservation Recycl. 135, 210–215. doi:10.1016/j.resconrec.2017.10.014
Zhan, L., Xia, F., Ye, Q., Xiang, X., and Xie, B. (2015). Novel Recycle Technology for Recovering Rare Metals (ga, in) from Waste Light-Emitting Diodes. J. Hazard. Mat. 299, 388–394. doi:10.1016/j.jhazmat.2015.06.029
Zhan, L., Xia, F., Ye, Q., Xiang, X., and Xie, B. (2015). Novel Recycle Technology for Recovering Rare Metals (Ga, in) from Waste Light-Emitting Diodes. J. Hazard. Mater. 299, 388–394. doi:10.1016/j.jhazmat.2015.06.029
Zhang, L., Chen, T., Yang, J., Cai, Z., Sheng, H., Yuan, Z., et al. (2017). Characterizing Copper Flows in International Trade of China, 1975-2015. Sci. Total Environ. 601-602, 1238–1246. doi:10.1016/j.scitotenv.2017.05.216
Zhao, T., Qin, P. Z., Wang, A. J., Wang, G. S., Li, J. W., Liu, C., et al. (2017). An Analysis of Gallium Ore Resources Demand Trend and the Thinking Concerning China’s Gallium Industry Development. Acta Geosci. Sin. 38, 77 (in Chinese). Available at: https://kns.cnki.net/kcms/detail/detail.aspx?FileName=DQXB201701012&DbName=CJFQ2017
Zhao, Z., Yang, Y., Xiao, Y., and Fan, Y. (2012). Recovery of Gallium from Bayer Liquor: a Review. Hydrometallurgy 125-126, 115–124. doi:10.1016/j.hydromet.2012.06.002
Zhou, Y., Rechberger, H., Li, J., Li, Q., Wang, G., and Chen, S. (2021). Dynamic Analysis of Indium Flows and Stocks in China: 2000-2018. Resour. Conservation Recycl. 167, 105394. doi:10.1016/j.resconrec.2021.105394
Keywords: gallium, material flow analysis, dynamic material cycle, in-use stocks and flows, China
Citation: Jia H, Zhou Y, Wang A, Wang G, Li T, Wang C, Xing W, Ma Z and Li P (2022) Evolution of the Anthropogenic Gallium Cycle in China From 2005 to 2020. Front. Energy Res. 10:944617. doi: 10.3389/fenrg.2022.944617
Received: 15 May 2022; Accepted: 17 June 2022;
Published: 11 July 2022.
Edited by:
Zhi Cao, University of Antwerp, BelgiumReviewed by:
Peng Wang, Institute of Urban Environment (CAS), ChinaQindong Yang, Institute of Geographic Sciences and Natural Resources Research (CAS), China
Copyright © 2022 Jia, Zhou, Wang, Wang, Li, Wang, Xing, Ma and Li. This is an open-access article distributed under the terms of the Creative Commons Attribution License (CC BY). The use, distribution or reproduction in other forums is permitted, provided the original author(s) and the copyright owner(s) are credited and that the original publication in this journal is cited, in accordance with accepted academic practice. No use, distribution or reproduction is permitted which does not comply with these terms.
*Correspondence: Anjian Wang, YWp3YW5nQGNhZ3MuYWMuY24=; Gaoshang Wang, cGFjaWZpY3dAc2luYS5jb20=