- 1Department of Microbiology, Quaid-i-Azam University, Islamabad, Pakistan
- 2State Key Laboratory of Cryospheric Science, Northwest Institute of Eco- Environment, and Resources, Chinese Academy of Sciences, Lanzhou, China
- 3Department of Microbiology, University of Swat, Mingora, Pakistan
- 4Departmento de Fisiologia e Bioficisica, Instituto de Ciências Biológicas, Universidade Federal de Minas Gerais, Belo Horizonte, Minas Gerais, Brazil
- 5College of Agriculture Engineering and Food Sciences, Shandong University of Technology, Zibo, China
- 6Department of Botany and Microbiology, College of Science, King Saud University, Riyadh, Saudi Arabia
- 7Laboratory of Chemistry and Biochemistry, Faculty of Medicine and Pharmacy, Ibn Zohr University, Laayoune, Morocco
With the growing demand for vegetable oils, alternative non-edible feedstocks like Jatropha curcas seed oil have gained interest for biodiesel production. The study aimed to comprehensively evaluate the physicochemical properties and biodiesel production potential of locally produced J. curcas seeds in Pakistan. Two different approaches were applied: a chemical synthesis approach involving acidic pretreatment and alkaline transesterification, and a biosynthetic approach using a lipase-producing strain of the Bacillus subtilis Q5 strain. The microbial biosynthesized biodiesel was further optimized using the Plackett–Burman design. The physicochemical properties of the J. curcas methyl esters were analyzed to assess their suitability as biodiesel fuel. Initially, the raw oil had a high free fatty acid content of 13.11%, which was significantly reduced to 1.2% using sulfuric acid pretreatment, keeping the oil to methanol molar ratio to be 1:12. Afterward, alkaline transesterification of purified acid-pretreated seed oil resulted in 96% biodiesel yield at an oil to methanol molar ratio of 1:6, agitation of 600 revolutions per minute (RPM), temperature 60°C, and time 2 h. Moreover, alkaline transesterification yielded ∼98% biodiesel at the following optimized conditions: oil to methanol molar ratio 1:6, KOH 1%, time 90 min, and temperature 60°C. Similarly, the Bacillus subtilis Q5 strain yielded ∼98% biodiesel at the following optimized conditions: oil: methanol ratio of 1:9, agitation 150 RPM, inoculum size 10%, temperature 37°C, and n-hexane 10%. The fuel properties of J. curcas seed biodiesel are closely related to standard values specified by the American Society for Testing and Materials (ASTM D6751–20a), indicating its potential as a viable biodiesel fuel source.
1 Introduction
The consecutive decline in fossil fuel reserves and increase in global warming caused by the extensive combustion of petro-diesel have turned the focus of related industries and the scientific community to the utilization of renewable bioenergy resources such as biodiesel. Biodiesels are mono-alkyl esters that are biodegradable, non-toxic, and environmentally friendly green energy resources (Soudagar et al., 2018). It is acquired from vegetable or microalgae oils and animal fats. It can be effectively used as a substitute to petro-diesel alone and in the blended form with petro-diesel. The biodiesel blend possesses characteristics similar to those of petro-diesel but with comparatively less hazardous emissions of particulate matter such as hydrocarbons and oxides of nitrogen, sulfur, and carbon, like nitric oxide (NO), nitrogen dioxide (NO2), nitrous oxide (N2O), sulfur dioxide (SO2), and carbon monoxide (CO), respectively. The blend is evidenced to have lower toxicity, higher safety, and reduced CO2 emissions (Koh and Ghazi, 2011; Mofijur et al., 2019; Khan et al., 2020; Soudagar et al., 2020; Soudagar et al., 2020).
Both edible and non-edible oils are used for biodiesel. The use of edibles for biodiesel production is controversial due to the risk of diverting farmland for biofuel production and the detriment of food supply, while non-edible oils have no food versus fuel competition, and therefore, their use for biodiesel production is increasing worldwide (Liu et al., 2019). To date, several non-edible oil feedstocks have been used for biodiesel production, but Jatropha curcas is a non-edible feedstock and is considered an ideal option for biodiesel production due to its ability to thrive both in tropical and subtropical climates in marginal and non-agricultural wastelands. It originated from North America and Central America, and now also inhabits South Africa, Southeast Asia, India, and China. J. curcas belongs to the Euphorbiaceae family, has a life span of 50 years, and contains 27%–40% oil in its seeds (Nahar and Ozores-Hampton, 2011; Reddy et al., 2015). However, J. curcas seeds are also toxic to humans and animals due to toxic components such as phorbol esters and curcumin (Leung et al., 2010; Mofijur et al., 2012).
Biodiesel can be produced using different methods, but transesterification using methanol has remained the most widely used method compared to the direct use of oil or biodiesel blending, pyrolysis, and micro-emulsion (Meher et al., 2013). In transesterification, the triglycerides react with an alcohol to form fatty acid alkyl esters. However, it has been found that alkaline transesterification efficiency relies on the free fatty acid (FFA) composition of feedstocks. It has been reported that alkaline transesterification is not recommended for feedstocks having 3%–40% FFAs. So the alternate option is to use both acidic and alkaline catalysts for higher FFAs. Acid pretreatment can esterify FFAs, and after decreasing FFAs to an acceptable range, i.e., 1%–2%, its product can further be used for alkaline transesterification to obtain a higher biodiesel yield (Chung et al., 2008). The homogenous alkaline catalyst produces soap on reacting with FFAs, and hence, the quantity of catalyst required for transesterification is reduced, resulting in an incomplete reaction and complicated downstream processing (Marchetti et al., 2007; Bohlouli and Mahdavian, 2019).
Several studies have been conducted to increase the yield of biodiesel and improve its fuel properties. Various factors have been considered during biodiesel optimization, such as the oil-to-methanol molar ratio, agitation, temperature, and time. Optimization of these factors is necessary to decrease the process cost and increase the biodiesel yield (Micic et al., 2015). To the best of our knowledge, it is the first comprehensive assessment of locally produced J. curcas seed oil in Pakistan for its physicochemical properties, and biodiesel production via chemical and lipase-mediated transesterification. This study gives a detailed assessment of locally produced J. curcas seed oil for biodiesel production and its optimization. In the present study, Jatropha oil (JO) was characterized and used for biodiesel production. The optimization of various factors, including the oil-to-methanol molar ratio, time, amount of the catalyst, and temperature, was investigated for the chemical synthesis of biodiesel.
2 Materials and methods
In the current study, various physicochemical properties of raw oils and their methyl esters have been analyzed to investigate their suitability as biodiesel fuel. The initial free fatty acid (FFA) contents of raw oil were 13.11%, which were reduced by acid pretreatment. Afterward, alkaline transesterification of purified acid-pretreated seed oil was carried out. Moreover, the oil-to-methanol molar ratio, amount of KOH, temperature, and time were optimized for alkaline transesterification to achieve a high biodiesel yield.
2.1 Sample collection
J. curcas seeds, which were primarily produced in District Swabi, were supplied by a local supplier from Lahore, Pakistan. An amount of 10 kg of seeds were supplied for oil extraction, and 3.2 L of oil was obtained using a mechanical oil expeller unit in Rawalpindi, Pakistan. Seeds were sun-dried and subjected to mechanical oil extraction using an oil expeller. Oil was filtered to remove solid impurities. The crude oil was then heated at 105°C for 2–3 h to remove moisture and stored in the dark for further use. The oil yield was calculated using the following formula. Figure 1 shows the expeller unit used for the mechanical extraction of jatropha oil.
2.2 Microbial biosynthesis of biodiesel
As the lipase enzyme, in the presence of alcohol as a reaction medium, carries out transesterification of fatty oils, the previously isolated lipase-producing Bacillus subtilis Q5 strain, which was shown to be tolerant to a high methanol concentration and toxic J. curcas oil (Rana et al., 2019), was used for the production of biodiesel from seed oil using the whole-cell method described by Rana et al. (2019). Microbial cell mass was generated by the growing strain Q5 in Luria broth (LB) for 24 h. Cells were then pelleted by centrifugation. Approximately 1 ml of pelleted cells were then added into the reactor containing J. curcas oil and mobilized within the oil layer to avoid direct methanol exposure. Methanol was then added dropwise along with 300 μl of n-hexane as an emulsifier. The mouths of the flasks were closed tightly with rubber corks in order to restrict any evaporation of methanol from the reaction mixture. After 48 h, the flask’s mixture was poured into a separating funnel and kept overnight to separate different layers. The upper yellowish methyl ester layer (biodiesel layers) was collected in screw cap glass vials and stored. The produced biodiesel was then confirmed by both Fourier transform infrared spectroscopy (FTIR) and gas chromatography coupled with mass spectrometry (GCMS) analysis.
2.3 Optimization of parameters for microbial biosynthesis of biodiesel
Biodiesel production via the Q5 strain was statistically optimized for Jatropha oil using five factors, namely, temperature, agitation (rpm), inoculum size, oil: methanol ratio, and n-hexane percentage with respect to oil, which were optimized using the Plackett–Burman design in Stat-Ease Design-Expert software version 7.0. Experiments were performed according to conditions given in Table 1, and a total of 15 runs by the Plackett–Burman design and response (percentage volumetric yield of biodiesel) were recorded.
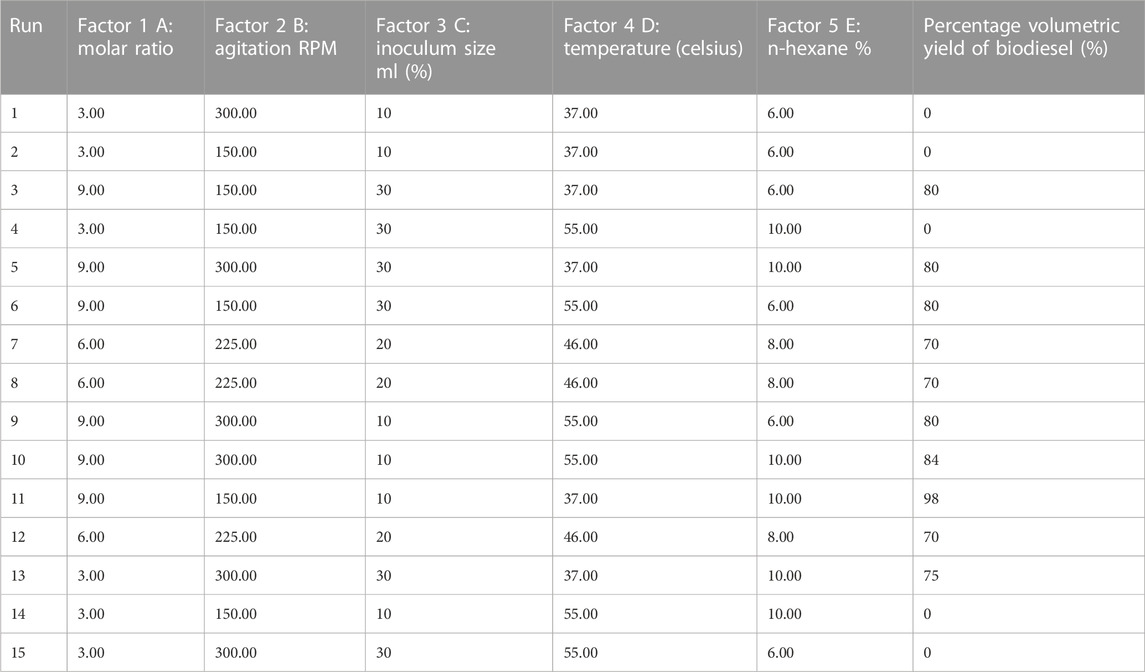
TABLE 1. Percentage volumetric yield of biodiesel in response to conditions specified by the Plackett–Burman design for each run.
2.4 Two-step transesterification of J. curcas seed oil
The crude jatropha oil was brown. The amount of FFA in JO (Table 3) was determined, as previously described (Ghadge and Raheman, 2006). J. curcas seed oil had an initial acid number of 26 ± 0.02 mg KOH/gram seed oil corresponding to the 13.11% FFA level, which is exceedingly above the acceptable limit (1%–2%) for the alkaline transesterification reaction. The main goal was to complete the conversion of FFA and triacylglycerides (TAG) into biodiesel using a two-step process. Therefore, FFA was converted to esters by esterification, as discussed in the following paragraphs.
2.5 Acid-catalyzed esterification of J. curcas seed oil
Esterification was used to convert seed oil FFA to esters using sulfuric acid with methanol, according to Veljković et al. (2006), with little modifications. In the esterification step, JO and methanol were used in a 1:12 molar ratio. Initially, 100 mL JO was added to three-necked round bottom flasks (250 mL) equipped with a reflux condenser, thermometer, and rubber corks, and heated up to 60°C. Absolute methanol and sulfuric acid (2% in accordance with the final volume of seed oil) were premixed together, heated, and then added to the seed oil in the flasks and continuously mixed at 600 revolutions per minute (rpm) to homogenize the mixture. The acid-catalyzed esterification (ACE) batch reaction was maintained at 60°C for 2 h on a heating mantle. After the completion of the ACE process, the mixture was completely separated into different layers using a separating funnel. After the separation of the oil layer, the sulfuric acid catalyst was washed out and removed by neutralization with calcium oxide (CaO). Approximately 20 mL of the hot 1% CaO solution was added to the pretreated oil mixture. The mixture was centrifuged at 1,744 g for 10 min, resulting in CaSO4 formation that was precipitated out and settled down. This washing was repeated twice to properly remove the acid catalyst. The supernatant containing catalyst-free pretreated oil was decanted and centrifuged again at the aforementioned conditions to separate water. The product obtained after ACE was again dried in an oven for 2–3 h and cooled down at 25°C. Finally, the pretreated JO was treated with anhydrous sodium sulfate to absorb any remaining moisture completely. The acid number of acid pretreated oil was determined and found to be 2.4 ± 0.01 mg KOH per gram of pretreated oil that was corresponding to an FFA level of 1.2%, which is within the acceptable limits for alkaline transesterification. This product was further used in an alkaline transesterification reaction.
2.6 Alkaline transesterification of J. curcas seed oil
Alkaline transesterification of acid-pretreated JO was carried out, as described by Berchmans and Hirata (2008) and Veljković et al. (2006), with slight modifications. KOH, 2% w/w (2% in accordance with a final volume of seed oil), was dissolved in methanol (1:6 oil-to-methanol molar ratio) and added to the same reactor, as described previously. The mixture was heated to 60°C and stirred at 600 rpm for 2 h; afterward, it was completely separated into different layers using a separating funnel.
After the completion of the reaction, the product (biodiesel) was poured into the round bottom flask of the distillation apparatus, and its temperature was adjusted to 65°C. The distillation apparatus was stopped when methanol collection in the flask on the other side of the distillation tube was stopped. KOH was removed through neutralization and washing with acidified distilled water. For this purpose, 100 mL of the 1% dilute sulfuric acid hot solution was then added to the transesterified mixture and centrifuged at the aforementioned conditions; the resultant product (potassium sulfate) was precipitated out, settled down, and removed from the mixture. This step was performed twice to remove any remaining catalyst. The catalyst-free product was again centrifuged at the aforementioned conditions to separate water from the final product. The water-free product was passed through anhydrous Na2SO4 on a Whatman filter paper to remove any remaining moisture. The volume of fatty acid methyl esters (FAMEs) was noted. The FAME yield was calculated using the following equation:
2.7 Optimization of alkaline transesterification
Parameters affecting the alkali-catalyzed transesterification reaction were optimized using the method of Patil and Deng (2009) with few modifications. An alkali-catalyzed transesterification reaction setup was used to determine the optimum oil-to-methanol molar ratio, amount of catalyst, and time at 600 rpm and 60°C. For batch setup, 25 mL of preheated JO was used in each batch reaction. The catalyst, along with methanol, was preheated at a desired temperature, added to the oil in a batch setup, and stirred at 600 rpm for 2 h. The reactions were conducted at different molar ratios of oil to methanol (1:6, 1:9, and 1:12), amount of the catalyst (1%, 1.5%, and 2%), and reaction times (30, 60, 90, and 120 min). After confirming the optimum parameters, the effect of different temperatures (50°C, 55°C, and 60°C) on biodiesel yield was evaluated at the optimized molar ratio, amount of KOH, and reaction time.
2.8 Physicochemical analyses of oil and biodiesel
Fuel properties of oil and biodiesel samples, obtained from chemical transesterification reactions, were carried out using standard procedures according to Mehta et al. (2015) and Onukwuli et al. (2017), with some modifications, as discussed in the following paragraphs.
2.8.1 Acid number and free fatty acid content
The acid number (AN) of JO, acid pretreated oil, and biodiesel was determined by adding 5 g of a sample in a flask and mixing it with 25 mL of absolute ethanol and 2–3 drops of phenolphthalein. They were heated at 65°C in a water bath for 10 min under continuous shaking, allowed to cool, and titrated against 0.1 normal KOH solution until a permanent pink color appeared. The amount of KOH solution needed for the reaction was calculated. The acid number (AN) was determined using the following formula.
where 56.1 represents the molecular weight of KOH (g/mol).
The FFA contents of JO and acid-pretreated oil were determined by the following formula. The percentage of FFA in a sample is always approximately half of the acid number.
2.8.2 Saponification number
The saponification number was determined by adding 2 g of JO in a 100-mL Erlenmeyer flask, followed by the addition of 25 mL of 0.5 normal alcoholic KOH solution. The same procedure was carried out for B (blank) without the addition of an oil sample. The flask was connected to the reflux condenser and placed in a water bath, and saponification was completed by gently and steadily boiling for an hour with periodic shaking. After 1 h, a few drops of phenolphthalein were added to it, and the solution was titrated against 0.5 normal hydrochloric acid until the disappearance of the pink color (endpoint). The saponification number of JO was determined using the following formula:
where “H°” is the number of hydrochloric acid concentrations used for the blank in mL, “S°” is the amount of hydrochloric acid used for the sample in mL, and N represents the normality.
2.8.3 Ester value and percentage of glycerin
Ester value is the number of milligrams of KOH needed to saponify the esters present in 1 g of substance and is determined by subtracting an acid number from the saponification number.
During the saponification reaction, the triacylglycerol is hydrolyzed in the presence of KOH to produce potassium salts of soap and glycerin. The percentage of glycerin can be obtained using the following formula.
2.8.4 Peroxide value
It was determined as described by the Association of Official Analytical Chemists’ (AOAC) method (Society, 1988). J. curcas seed oil/biodiesel (5 g) was added to the flask, and 30 mL of the acetic acid and chloroform mixture (at a molar ratio of 3:2) was added to it with swirling to dissolve oil in it. A measure of 0.5 mL of the potassium iodide solution (saturated) was added to the mixture and swirled for 1 min in the dark until its color turned into a light brown color. Afterward, 30 mL of distilled water was added to it and titrated against 0.1 normal Na2S2O3 until the solution turned pale yellow. Then, 1 mL of the 1% starch indicator was added and further titrated against 0.1 N Na2S2O3 until the disappearance of the blue color. For the blank, the same procedure was used without adding a sample. The peroxide value is expressed as the milli equivalent of peroxide oxygen per kg of the sample, as given as follows:
where S° represents the test sample titrated, B° represents the blank sample titrated, and N represents the normality of Na2S2O3.
2.8.5 Specific gravity and density
A 25-mL dried, clean bottle was weighed either empty or with water. The oil and biodiesel samples were added separately in it and weighed. All the steps were carried out at a similar temperature (30°C). Specific gravity (kg/m3) was calculated using the following equation:
where A° represents the weight (in grams) of the bottle along with oil, B° represents the weight (in grams) of the empty bottle, and C° represents the weight (in grams) of the bottle with water. The density was measured using a pycnometer.
2.8.6 Boiling point determination
A measure of 10 mL of the biodiesel sample was taken in a test tube, and a thermometer was inserted into it. After that, the temperature of the magnetic plate gradually increased. The point at which biodiesel started to bubble was recorded as the boiling point.
2.8.7 Cloud point and pour point
Approximately 30 mL of oil and biodiesel samples were poured into separate jars and placed in the cooling jacket in a water bath. A thermometer was fixed in each jar, and the jars were observed at different intervals without disturbing the liquids. The temperature at which clouds of crystals appeared was recorded as the cloud point. For the pour point, approximately 20 mL of each sample was placed in a beaker, sealed with corks, and incubated in the refrigerator to solidify. After solidification, the samples were kept in the open, and the temperature at which each sample melted and started flowing was recorded as the pour point.
2.9 Chemical characterization of J. curcas seed oil and biodiesel
J. curcas seed oil and biodiesel produced by the chemical transesterification method were analyzed using both FTIR and GCMS.
2.10 Chemical analysis
FTIR spectroscopy (Bruker, model Tensor 27, with software version Opus 65, and equipped with Zn-Se ATR) was performed. A measure of 5 µL of seed oil or its FAMEs was loaded at the sample injector, and FTIR spectra for all samples ranged between 4,000 and 400 cm−1.
Gas chromatography and mass spectrophotometry (GC-MS; model GCMS-QP5050A; Shimadzu Europe) were performed with a thermal conductivity detector (TCD) for the analysis of both oil and biodiesel samples with the following conditions: a measure of 2 µL of the sample was injected into the GC column using the split mode. Separation was performed on a capillary column DB-5 (column length: 30 m, internal diameter 0.25 mm, and thickness 0.25 μm). The initial temperature was 50°C, ramped at 5°C/min to 80°C, 10°C–300°C, and kept at 300°C for 18 min. The injector was set at 250°C with a column flow rate of 1.8 mL/min for seed oil and 1 mL/min for biodiesel. Helium gas was used as a mobile phase with a flow rate of 1 mL/min, and a split ratio for oil was 1/25 and for biodiesel was 1/48, while TCD was set at 300°C. The m/z scanning of MS was in the range of 50–650, with electron impact (EI) at 70 eV.
2.11 Statistical analyses
Each batch was conducted in triplicate, and the FAMEs obtained from each setup were analyzed individually in triplicates to calculate the average values of experimental data. One-way ANOVA and multiple comparisons were carried out by Tukey’s post-test (significance: p < 0.05).
3 Results and discussions
The mechanical extraction resulted in 32.5% crude oil, which is near the previously reported extraction yields (de Oliveira et al., 2009).
3.1 Microbial biosynthesis of biodiesel
FAMEs produced using the Bacillus subtilis strain Q5 were analyzed by FTIR and GCMS. Biodiesel is a mono-alkyl ester of long-chain fatty acids; thus, its IR spectrum should contain peaks of ester groups, which are observed at the frequency (cm−1) range of 1,735–1,750. The infrared spectra of the biodiesel produced showed peaks at 1,742.07, 1,198.16, and 1,034.90 cm−1 that were only present in the biodiesel, while crude Jatropha oil has no such bands in this region, which showed the presence of esters in the sample, thus confirming the production of biodiesel (Figure 2). GCMS chromatogram data (Table 2; Supplementary Figure S2) revealed that the total fatty acid methyl ester content of the produced biodiesel was >98%, which is in accordance with the biodiesel quality standards specified by ASTM D6751–20a (Table 3).
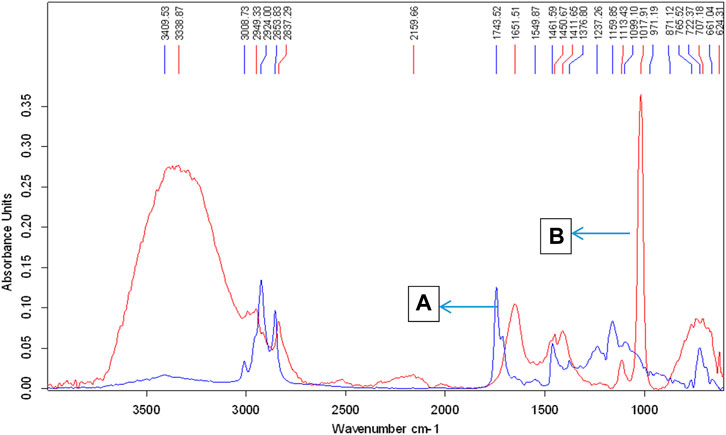
FIGURE 2. ATR-FTIR spectra of crude jatropha oil and FAMEs of jatropha oil produced by microbial biological synthesis. Peaks denoted by letters (A,B) represent jatropha oil and biodiesel, respectively.
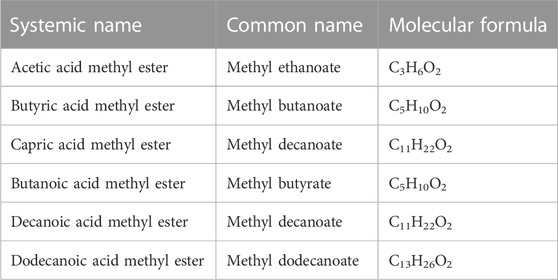
TABLE 2. FAMEs composition of biodiesel biosynthesized by Bacillus subtilis Q5 from J. curcas seed oil identified by GC-MS.
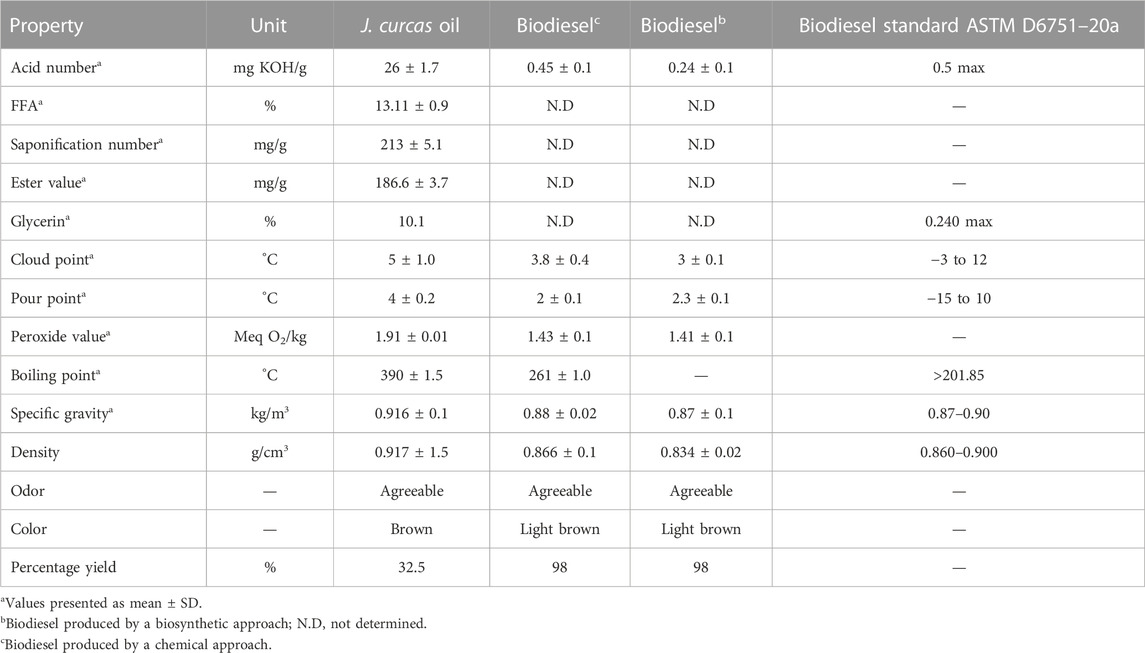
TABLE 3. Fuel properties of J. curcas seed oil and biodiesel (ASTM D6751–20a 2020; ASTM D975–20c 2020; Ong et al., 2011; Patil and Deng, 2009).
3.2 Optimization of parameters for microbial biosynthesis of biodiesel using the Plackett–Burman design
The Plackett–Burman design was used for statistical optimization of biodiesel production using the strain Q5 and selecting five factors, namely, temperature, agitation (rpm), inoculum size, oil: methanol ratio, and n-hexane percentage with respect to oil, which were optimized. The highest volumetric yield of biodiesel 98% was obtained with run 11 with an oil: methanol ratio of 1:9, agitation speed of 150 RPM, inoculum size 10%, temperature 37°C, and n-hexane 10%. ANOVA analysis of the design gave an F-value of 20.34, which depicted that the experimental model generated by the design was significant. The F-test on each factor was also applied by the software application to identify the significant factors. Values of Prob > F less than 0.0500 indicated that factors are significant. In this case, the molar ratio was a significant factor with a Prob > F value of 0.0001. The molar ratio affected the response, i.e., the percentage volumetric yield of biodiesel, positively, which means increasing the molar ratio increases the yield (Figure 3). The results are in alignment with those reported by Rana et al. (2019) and Rana et al. (2022).
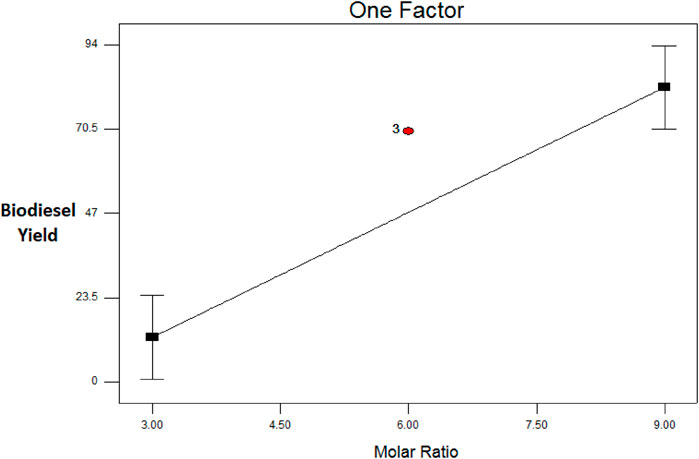
FIGURE 3. Plot of volumetric biodiesel yield (response) as a function of molar ratio (significant factor).
3.3 Acid pretreatment and alkaline transesterification of J. curcas seed oil
The JO had a high FFA content of 13.11% (Table 3), which is higher than the acceptable value for alkaline transesterification. The alkaline transesterification of high FFA-containing JO is considered complicated due to higher soap formation, loss of catalyst, and loss in product yield. The higher FFA content causes saponification of oil and requires the extra addition of an alkali catalyst for transesterification (Canakci and Van Gerpen, 2001). So in order to decrease the FFA before alkaline transesterification, acid pretreatment was used to reduce the FFA acids present in JO. The FFA was significantly reduced (p < 0.05) from 13.11% to 1.2% after 120 min of pretreatment (Figure 4).
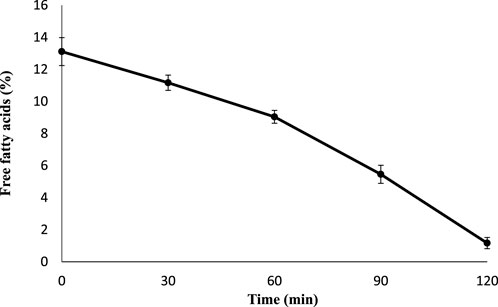
FIGURE 4. Acid-catalyzed pretreatment of J. curcas seed oil FFA with concentrated sulfuric acid. The data are presented as mean ± SD. The acid pretreatment was carried out in triplicate independently, and the conditions were 2% sulfuric acid, 1:12 oil-to-methanol molar ratio, 60°C of temperature, time of 120 min, and agitation at 600 rpm. The FFA percentage was investigated after each 30 mins. The free fatty acid reduction was statistically analyzed using one-way ANOVA, and multiple comparisons were carried out by Tukey’s post-test (significance: p < 0.05).
After acid pretreatment, the purified product was subjected to alkaline transesterification and processed at 2% KOH (w/v), an oil-to-methanol molar ratio of 1:6, time of 2 h, 60°C temperature, and agitation at 600 rpm. The resultant amount of methyl esters of JO was determined at different reaction times, but the highest biodiesel yield (96%) was obtained after 2 h of reaction with no significant increase compared to the methyl esters obtained at 30, 60, and 90 min (Figure 5). Meher et al. (2006) also reported similar findings, in which the karanja produced the highest biodiesel yield of 97% at an oil-to-methanol molar ratio of 1:6 using the KOH catalyst in alkaline transesterification.
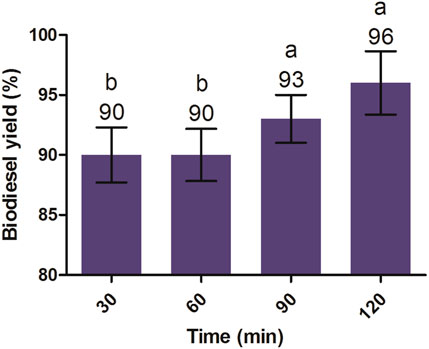
FIGURE 5. Alkaline transesterification of J. curcas seed oil was carried out at a 1:6 oil-to-methanol molar ratio, 2% KOH (alkaline catalyst), 600 rpm, and 60°C temperature. All of the setups were carried out as independent experiments in triplicates. The data are presented as mean ± SD. One-way ANOVA and multiple comparisons were carried out by Tukey’s post-test. The lowercase alphabets on adjacent bars show significant and non-significant differences. Similar alphabets on adjacent bars show non-significant differences, whereas different alphabets show a significant difference (significance: p < 0.05).
3.4 Optimization of alkaline transesterification of J. curcas seed oil
The alkaline transesterification process depends upon certain factors such as the oil-to-methanol molar ratio, amount of the catalyst, temperature, and time. Therefore, in order to enhance the biodiesel yield, different oil-to-methanol molar ratios, amount of KOH, and duration of time were investigated at 60°C, as mentioned previously. Stoichiometrically, 1 mol of oil requires 3 mol of alcohol for transesterification reaction completion. However, the 1:3 ratio of oil to methanol results in the formation of a unique and opaque layer due to the presence of unreacted triglycerides. Second, as transesterification is a reversible reaction, an excess of alcohol is required to proceed with the reaction in a forward direction (Leung and Guo, 2006). In practice, a higher amount of methanol is needed for higher conversion efficiency of oil (to ensure that the reaction completes). The conversion efficiency is defined as the increased yield of biodiesel in terms of percentages. Therefore, the biodiesel optimization setup was started at a molar ratio of 1:6 (oil: methanol) (Freedman et al., 1984; Fukuda et al., 2001). The optimum catalyst concentration and oil-to-methanol molar ratio are highly necessary for a complete and efficient transesterification process, and a slight variation in these parameters can result either in an incomplete reaction or may produce unnecessary products, leading to a lower biodiesel yield. Moreover, increasing the oil-to-methanol molar ratio may further complicate the purification due to more dissolution of glycerol in biodiesel, which ultimately decreases its yield (Ali et al., 2015). The highest biodiesel yield was obtained at 1% KOH, a molar ratio of 1:6 of oil to methanol, at 90 as well as 120 min reaction time, and incubated at 60°C (Figure 4). The catalyst is the most important factor in biodiesel production. It provides the available active site for the biodiesel reaction to occur. No further increase in biodiesel yield occurred when the catalyst amount was increased beyond 1%. This may be due to the possibility of some of the products’ solubility or absorption onto the excess amount of the catalyst surface (Kamel et al., 2018). Initially, there was no significant difference in biodiesel yields obtained at 30 and 60 min. However, at 90 and 120 min, the 1:6 molar (oil-to-methanol) ratio produced significantly higher (p < 0.05) yields than those obtained at 30 and 60 min. The biodiesel yield recorded for a 1:6 molar ratio was significantly higher (p < 0.05) than 1:9 at 90 min and 60°C (Figure 6).
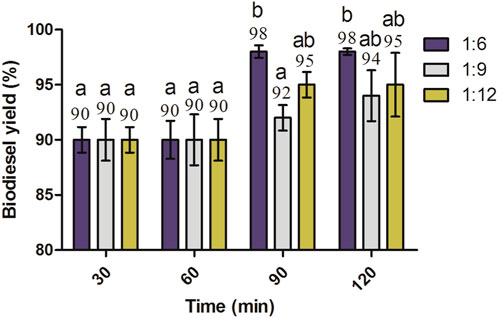
FIGURE 6. Effect of molar ratios and reaction time on the biodiesel yield of J. curcas seed oil maintained at 1% KOH, 600 rpm, and 60°C. All the setups were carried out as independent experiments in triplicate. The data are presented as mean ± SD. One-way ANOVA and multiple comparisons were carried out by Tukey’s post-test. The alphabets on the bars show significant and non-significant differences. Similar alphabets on different bars show non-significant differences, whereas different alphabets show a significant difference. The alphabets “ab” on bars represent a non-significant difference between bars annotated by “a” and “b” (significance: p < 0.05).
A similar pattern was also observed for alkaline transesterification at 1.5% KOH, and the biodiesel yield of a ratio of 1:6 was higher than that of 1:9 and 1:12 at 90 min and 120 min reaction times incubated at 60°C (Figure 7). Here, at 1.5% KOH, the biodiesel yield of a 1:6 molar ratio was significantly higher (p < 0.05) than that of 1:12 at 90 min and 120 min reaction times.
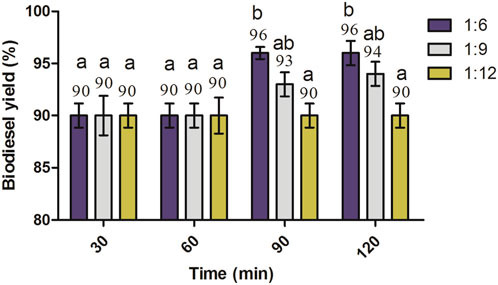
FIGURE 7. Effect of molar ratios and reaction time on the biodiesel yield of J. curcas seed oil maintained at 1.5% KOH, 600 rpm, and 60°C. All of the setups were carried out as independent experiments in triplicate. The data are presented as mean ± SD. One-way ANOVA and multiple comparisons were carried out by Tukey’s post-test. The alphabets on the bars show significant and non-significant differences. Similar lowercase alphabets on different bars show non-significant differences, while different alphabets show a significant difference between them. The alphabets “ab” on bars represent a non-significant difference between bars annotated by “a” and “b” (significance: p < 0.05).
Moreover, at 2% KOH, the same biodiesel yield was obtained at 1:6 and 1:12 molar ratios of oil to methanol (Figure 8), and the yield was found to be slightly higher compared to the 1:9 molar ratio, with no significant increase. The methyl ester yield for all molar ratios incubated at 60°C and 2% KOH was found higher at 120 min compared to other reaction times, with no significant increase (p > 0.05).
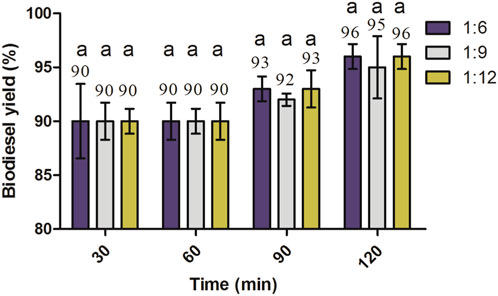
FIGURE 8. Effects of oil-to-methanol molar ratios and reaction time on the biodiesel yield of J. curcas seed oil maintained at 2% KOH, 600 rpm, and 60°C. All of the setups were carried out as independent experiments in triplicate. The data are presented as mean ± SD. One-way ANOVA and multiple comparisons were carried out by Tukey’s post-test. The alphabets on bars show significant and non-significant differences. Similar alphabets on different bars show non-significant differences, whereas different alphabets show a significant difference (significance: p < 0.05).
It is evident from the aforementioned results that the highest biodiesel yield was achieved at 1% KOH, an oil-to-methanol molar ratio of 1:6, and reaction time 90 min. Furthermore, it was also noted that an increase or decrease in the amount of KOH from 1% resulted in a lower biodiesel yield (Figure 9). The lower concentration than the optimum limit causes an incomplete transesterification reaction, ultimately producing lower methyl esters. Therefore, the catalyst concentration must be enough to complete the reaction. The excess amount of catalyst beyond its optimum limit reacts with triglycerides and free fatty acid-producing emulsion, which leads to the formation of a viscous gel or emulsion. It also makes the glycerol layer separation difficult, ultimately resulting in the loss of ester yields (Dorado et al., 2004). Similar findings were reported by Berchmans et al. (2010) and Rashid et al. (2008), achieving a biodiesel yield of 97% and 96% from the transesterification of JO and rapeseed oil, respectively, with 1% KOH catalyst.
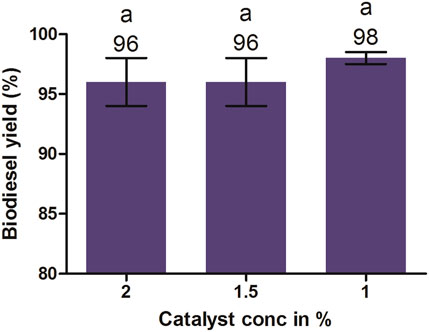
FIGURE 9. Effects of catalyst concentrations on biodiesel yield maintained at 1:6 molar ratios, 600 rpm, 60°C, and 90 min. All of the setups were carried out as independent experiments in triplicate. The data are presented as mean ± SD. One-way ANOVA and multiple comparisons were carried out by Tukey’s post-test. The alphabets on the bars show significant and non-significant differences. Similar alphabets on different bars show non-significant differences, whereas different alphabets show a significant difference (significance: p < 0.05).
From the cost and processing time perspectives, the ideal and the highest biodiesel yield was obtained at a molar ratio of 1:6 at 1% KOH catalyst, temperature 60°C, and 90 min of reaction time, with an optimum biodiesel yield of 98%. For standard biodiesel, the permissible level of glycerol is 0.24% in the final product, and to achieve this standard, the biodiesel yield must be ≥97.7% (Van Gerpen et al., 2004). The current study assumed the optimal molar ratio of oil to methanol as 1:6 in order to obtain a higher ester yield (Figure 7). No significant change in the biodiesel yield was observed when the oil-to-methanol molar ratio higher than 1:6 was used. The results showed similarities with the reports of Meher et al. (2013) and Usta (2005), where the highest yield of ester from methanolysis of P. pinnata and tobacco seed oil at the 6:1 alcohol-to-oil molar ratio, respectively, was reported. Similarly, 96% yield was obtained from the transesterification of rapeseed oil using a molar ratio of methanol to oil of 6:1 and 1% KOH as a catalyst (Rashid et al., 2008).
Similarly, the effect of different temperatures (50°C, 55°C, and 60°C) on biodiesel yield was evaluated at the aforementioned optimized conditions (1:6 molar ratio, reaction time 90 min, and 1% KOH). The reaction temperature above the boiling point of methanol was ignored because at higher temperatures, the saponification rate for glycerides of oil remains faster than that of transesterification. In addition, temperatures above the boiling point of methanol cause excessive evaporation and loss of methanol from the reaction mixture, which leads to an incomplete reaction and loss of ester formation. As shown in Figure 10, the highest yield for biodiesel was achieved at 60°C, followed by 55°C and 50°C, with no significant difference. The increase in temperature until the optimum limit (60°C) increased the conversion efficiency of oil into its methyl esters and any decrease from the optimum temperature caused a decrease in the methyl ester yield. A similar effect was observed by Chitra et al. (2005) and Rashid et al. (2008) during the transesterification of JO and rapeseed oil, respectively.
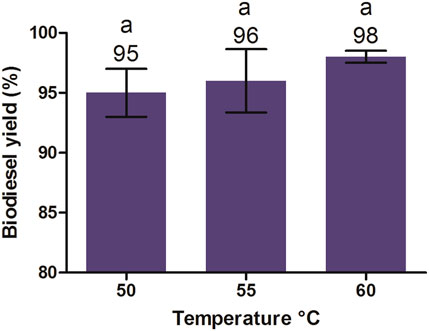
FIGURE 10. Effect of different temperatures on the biodiesel yield of J. curcas seed oil maintained at the 1:6 oil-to-methanol ratio, 1% KOH, 600 rpm, and a reaction time of 90 min. All of the setups were carried out as independent experiments in triplicate. The data are presented as mean ± SD. One-way ANOVA and multiple comparisons were carried out by Tukey’s post-test. The alphabets on the bars show significant and non-significant differences. Similar alphabets on different bars show non-significant differences, whereas different alphabets show a significant difference (significance: p < 0.05).
3.5 Physicochemical properties of oil- and chemical-mediated and biosynthesized biodiesel
The quality of seed oil and its methyl esters is expressed in terms of physicochemical properties such as the acid number, saponification number, peroxide value, specific gravity, pour point, and cloud point that were analyzed in the present study (Table 3). The least temperature at which biofuels can flow is called the pour point whereas the temperature at which the wax first appears when fuels are cooled is called the cloud point (Coutinho et al., 2002). The determined values of the pour point and cloud point of J. curcas biodiesels are closely in line with ASTM D6757 (Table 3). The acid number shows the amount of FFAs present in fuel oil. If the acid number for biodiesel is higher than 0.5 mg KOH g−1 FAME, it causes corrosion of the fuel engine. In the present study, the acid pretreatment of the oil reduced the acid number of oil from 26 ± 1.7 mg KOH per g of oil to 2.4 ± 0.01 mg KOH per gram of pretreated oil. The acid number of biodiesel was 0.45 mg KOH g−1 FAME, which is below the critical value and is considered safe for fuel engine operation (Table 3). Similarly, the acid number of biosynthesized biodiesel was 0.24 ± 0.1 mg KOH/g. The saponification number is an index of the mean molecular mass of fatty acids present in seed oil. The FFA, saponification number, ester value, specific gravity, density, and acid number of jatropha oil were 13.11%, 213 ± 5.1 mg/g, 186.6 mg/g, 0.916 ± 0.1 kg/m3, 0.917 ± 1.5 g/cm3, and 26 mg/KOH g, respectively. Similarly, the peroxide value, specific gravity, density, cloud point, and pour point of chemically transesterified FAMEs were 1.43 Meq O2/kg, 0.88 ± 0.02 kg/m3, 0.866 ± 0.1 g/cm3, 3.8°C, and 2°C, respectively. On the contrary, the peroxide value, specific gravity, density, cloud point, and pour point of lipase-mediated FAMEs were 1.41 ± 0.1 Meq O2/kg, 0.87 ± 0.01 kg/m3, 0.834 ± 0.02 g/cm3, 3°C ± 0.1°C, and 2.3°C ± 0.1°C, respectively. The present study showed that transesterification improved the fuel quality of oil with respect to the aforementioned properties. All of the physicochemical characteristics determined in the present study may slightly vary from other studies due to differences in habitats of feedstock, geography, and soil conditions but are in close coherence with the standards for biodiesel specified by ASTM D6751–20a and EN 14214 (ASTM D6751–20a 2020; ASTM D975–20c 2020; Demirbas, 2009).
3.6 Chemical composition of J. curcas seed oil and produced biodiesel
The FTIR spectra for JO and its FAMEs obtained at conditions of 1% KOH, 1:6 molar ratio of methanol to oil, reaction time 90 min, and temperature 60°C are presented in Figure 8. The FAMEs were confirmed, as described previously (Rana et al., 2019). One major and two minor stretches of ester bands observed at 1742.07, 1198.16, and 1034.90 were only present in the biodiesel, confirming FAMEs (Figure 11). The peaks at 1163.55 and 1198.16 correspond to C-O stretches for esters and are only present in FAMEs, confirming the biodiesel produced from JO.
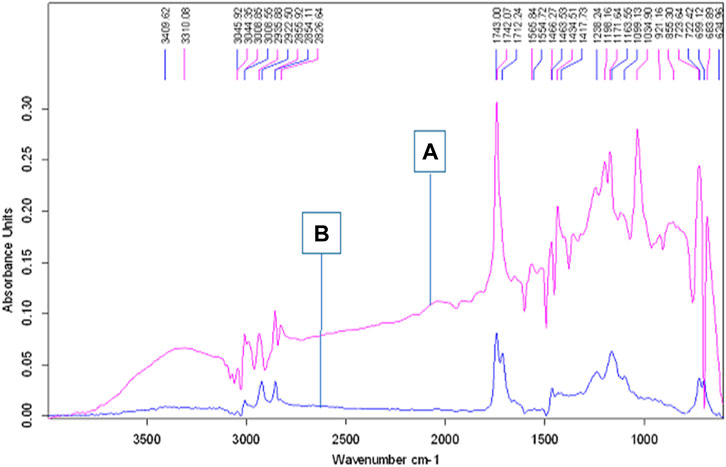
FIGURE 11. FTIR spectra of crude J. curcas oil and its alkaline catalyzed FAMEs; the upper peaks denoted by the letter “(A)” show biodiesel, and the lower peaks labeled with the letter “(B)” represent JO spectra.
The chemical composition of JO and its FAMEs was further analyzed by GC-MS. The GC-MS analysis showed 13 different saturated and unsaturated fatty acids in JO (Table 4; Supplementary Figure S1). Additionally, approximately eight different kinds of saturated and unsaturated FAMEs were observed in the total ion chromatogram (Table 5; Supplementary Figure S3). All of these fatty acids and FAMEs were confirmed using library match software provided by the National Institute of Standards and Technology (NIST). The GC-MS analysis also confirmed the presence of five saturated, two monounsaturated, and four poly-unsaturated FAMEs in the alkali-catalyzed biodiesel of JO (Table 5; Supplementary Figure S3). Usually, saturated and mono-unsaturated fatty acids or their esters are considered ideal for increasing energy yield and oxidative stability. However, oil or biodiesel containing mono-unsaturated fatty acids or their esters are prone to solidification at low temperatures. The fuels or oils containing polyunsaturated fatty acids or their esters have very good cold flow properties but are vulnerable to oxidation. This tendency of fuel oil or biodiesel harms fuel storage and combustion (Imahara et al., 2006). The determined components were in accordance with the reported composition of JO (Akbar et al., 2009). Here, in this case, the composition of fatty acids and their FAMEs may vary from other reports due to different geological variations, soil conditions, and seed varieties. De Oliveira et al. (2009) also support the same statement.
4 Conclusion
The study conducted concludes that the seeds of J. curcas contain a high content of oil that can be used for the production of high-quality biodiesel. However, J. curcas seed oil contains a high free fatty acid content of approximately 13.11%, which hinders the process of biodiesel production using alkali catalysts. This study depicts a successful implementation of a two-step transesterification process, in which, at the first step, the acid pretreatment with sulfuric acid reduced the FFA amount in oil to 1.2%. In the second step, the low FFA-containing pretreated oil was subjected to alkali-based transesterification to yield biodiesel. The study conducted was successful in optimizing the alkali transesterification process to achieve 98% biodiesel yield. Moreover, biosynthesis of biodiesel through a bacterial whole-cell approach is also a feasible option to supersede the chemical-mediated method and overcome the issue of free fatty acids in Jatropha oil. The maximum biodiesel yield obtained via lipase-mediated transesterification was 98%. The properties of the produced biodiesels satisfied the standards required for good-quality biodiesel. All the results obtained confirmed that J. curcas seed oil can be a viable option for both biosynthetic and two-step transesterification processes and can find successful applications in the field of biofuel production.
Data availability statement
The raw data supporting the conclusion of this article will be made available by the authors, without undue reservation.
Author contributions
Conceptualization, writing the original draft, formal analysis, methods: AH, ML, and QR. Investigation, resources, reviewing and editing, data validation, and data curation: AK, WS, HK, SK, AS, FH, SA, AI, and MaB. Reviewing and editing, data validation, and data curation: TS, TD, and MoB. All authors contributed to the article and approved the submitted version.
Funding
This study is a part of the Higher Education Commission of Pakistan NRPU project (6195/Federal/NRPU/R&D/HEC/2016). AH was supported by a scholarship granted by the Higher Education Commission of Pakistan.
Acknowledgments
The authors extend their appreciation to the Researchers Supporting Project number (RSP2023R197), King Saud University, Riyadh, Saudi Arabia. In addition, the financial support to accomplish this research by the Higher Education Commission of Pakistan and Quaid-i-Azam University, Islamabad, is gratefully acknowledged.
Conflict of interest
The authors declare that the research was conducted in the absence of any commercial or financial relationships that could be construed as a potential conflict of interest.
Publisher’s note
All claims expressed in this article are solely those of the authors and do not necessarily represent those of their affiliated organizations, or those of the publisher, the editors, and the reviewers. Any product that may be evaluated in this article, or claim that may be made by its manufacturer, is not guaranteed or endorsed by the publisher.
Supplementary material
The Supplementary Material for this article can be found online at: https://www.frontiersin.org/articles/10.3389/fenrg.2023.1225988/full#supplementary-material
References
Akbar, E., Yaakob, Z., Kamarudin, S. K., Ismail, M., and Salimon, J. (2009). Characteristic and composition of Jatropha curcas oil seed from Malaysia and its potential as biodiesel feedstock feedstock. Eur. J. Sci. Res. 29, 396–403.
Ali, R. M., Abd El Latif, M. M., and Farag, H. A. (2015). Preparation and characterization of CaSO4–SiO2–CaO/SO4 2-composite for biodiesel production. Am. J. Appl. Chem. 3 (3-1), 38–45. doi:10.11648/j.ajac.s.2015030301.16
Astm D6751–20a, (2020). Standard specification for biodiesel fuel blend stock (B100) for middle distillate fuels. West Conshohocken, PA, USA: ASTM International. doi:10.1520/D6751-20A
Astm D975–20c, (2020). Standard specification for diesel fuel. West Conshohocken, PA, USA: ASTM International. doi:10.1520/D0975-20C
Berchmans, H. J., and Hirata, S. (2008). Biodiesel production from crude Jatropha curcas L. seed oil a high content free Fat. acids Bioresour. Technol. 99, 1716–1721. doi:10.1016/j.biortech.2007.03.051
Bohlouli, A., and Mahdavian, L. (2019). Catalysts used in biodiesel production: a review Biofuels, 12 1–14. doi:10.1080/17597269.2018.1558836
Canakci, M., and Van Gerpen, J. (2001). Biodiesel production from oils and fats with high free fatty acids. Trans. ASAE 44, 1429. doi:10.13031/2013.7010
Chitra, P., Venkatachalam, P., and Sampathrajan, A. (2005). Optimisation of experimental conditions for biodiesel production from alkali-catalysed transesterification of Jatropha curcus oil. Energy Sustain. Dev. 9, 13–18. doi:10.1016/s0973-0826(08)60518-9
Chung, K-H., Chang, D-R., and Park, B-G. (2008). Removal of free fatty acid in waste frying oil by esterification with methanol on zeolite catalysts. Bioresour. Technol. 99, 7438–7443. doi:10.1016/j.biortech.2008.02.031
de Oliveira, J. S., Leite, P. M., de Souza, L. B., Mello, V. M., Silva, E. C., Rubim, J. C., et al. (2009). Characteristics and composition of Jatropha gossypiifolia and Jatropha curcas L. oils Appl. biodiesel Prod. Biomass Bioenergy 33, 449–453. doi:10.1016/j.biombioe.2008.08.006
Demirbas, A. (2009). Progress and recent trends in biodiesel fuels. Energy Convers. Manag. 50, 14–34. doi:10.1016/j.enconman.2008.09.001
Dorado, M. P., Ballesteros, E., López, F. J., and Mittelbach, M. (2004). Optimization of alkali-catalyzed transesterification of Brassica Carinata oil for biodiesel production. Energy & Fuels 18, 77–83. doi:10.1021/ef0340110
Freedman, B., Pryde, E., and Mounts, T. (1984). Variables affecting the yields of fatty esters from transesterified vegetable oils. J. Am. Oil Chem. Soc. 61, 1638–1643. doi:10.1007/bf02541649
Fukuda, H., Kondo, A., and Noda, H. (2001). Biodiesel fuel production by transesterification of oils. J. Biosci. Bioeng. 92, 405–416. doi:10.1016/s1389-1723(01)80288-7
Ghadge, S. V., and Raheman, H. (2006). Process optimization for biodiesel production from mahua (Madhuca indica) oil using response surface methodology. Bioresour. Technol. 97, 379–384. doi:10.1016/j.biortech.2005.03.014
Imahara, H., Minami, E., and Saka, S. (2006). Thermodynamic study on cloud point of biodiesel with its fatty acid composition. Fuel 85, 1666–1670. doi:10.1016/j.fuel.2006.03.003
Kamel, D. A., Farag, H. A., Amin, N. K., Zatout, A. A., and Ali, R. M. (2018). Smart utilization of jatropha (Jatropha curcas Linnaeus) seeds for biodiesel production: optimization and mechanism. Industrial Crops Prod. 111, 407–413. doi:10.1016/j.indcrop.2017.10.029
Khan, H., Soudagar, M. E. M., Kumar, R. H., Safaei, M. R., Farooq, M., Khidmatgar, A., et al. (2020). Effect of nano-graphene oxide and n-butanol fuel additives blended with diesel—Nigella sativa biodiesel fuel emulsion on diesel engine characteristics. Symmetry 12 (6), 961. doi:10.3390/sym12060961
Koh, M. Y., and Ghazi, T. I. M. (2011). A review of biodiesel production from Jatropha curcas L. oil Renew. Sustain. Energy Rev. 15, 2240–2251. doi:10.1016/j.rser.2011.02.013
Leung, D. Y., Wu, X., and Leung, M. (2010). A review on biodiesel production using catalyzed transesterification. Appl. Energy 87, 1083–1095. doi:10.1016/j.apenergy.2009.10.006
Leung, D. Y. C., and Guo, Y. (2006). Transesterification of neat and used frying oil: optimization for biodiesel production. Fuel Process. Technol. 87 (10), 883–890. doi:10.1016/j.fuproc.2006.06.003
Liu, J-Z., Cui, Q., Kang, Y-F., Meng, Y., Gao, M-Z., Efferth, T., et al. (2019). Euonymus maackii Rupr. Seed oil as a new potential non-edible feedstock for biodiesel. Renew. Energy 133, 261–267. doi:10.1016/j.renene.2018.10.035
Marchetti, J. M., Miguel, V., and Errazu, A. (2007). Possible methods for biodiesel production. Possible methods biodiesel Prod. Renew. Sustain. Energy Rev. 11, 1300–1311. doi:10.1016/j.rser.2005.08.006
Meher, L., Churamani, C., Arif, M., Ahmed, Z., and Naik, S. (2013). Jatropha curcas as a renewable source for bio-fuels—a review. Renew. Sustain. Energy Rev. 26, 397–407. doi:10.1016/j.rser.2013.05.065
Meher, L., Dharmagadda, V. S., and Naik, S. (2006). Optimization of alkali-catalyzed transesterification of Pongamia pinnata oil for production of biodiesel. Bioresour. Technol. 97, 1392–1397. doi:10.1016/j.biortech.2005.07.003
Mehta, B. M., Darji, V., and Aparnathi, K. (2015). Comparison of five analytical methods for the determination of peroxide value in oxidized ghee. Food Chem. 185, 449–453. doi:10.1016/j.foodchem.2015.04.023
Micic, R. D., Tomić, M. D., Kiss, F. E., Nikolić-Djorić, E. B., and Simikić, M. Ð. (2015). Optimization of hydrolysis in subcritical water as a pretreatment step for biodiesel production by esterification in supercritical methanol. J. Supercrit. Fluids 103, 90–100. doi:10.1016/j.supflu.2015.04.026
Mofijur, M., Masjuki, H., Kalam, M., Hazrat, M., Liaquat, A., Shahabuddin, M., et al. (2012). Prospects of biodiesel from jatropha in Malaysia. Renew. Sustain. Energy Rev. 16, 5007–5020. doi:10.1016/j.rser.2012.05.010
Mofijur, M., Rasul, M., Hassan, N., and Uddin, M. (2019). Investigation of exhaust emissions from a stationary diesel engine fuelled with biodiesel. Procedia 160, 791–797. doi:10.1016/j.egypro.2019.02.159
Nahar, K., and Ozores-Hampton, M. (2011). Jatropha: an alternative substitute to fossil fuel horticultural sciences departments Florida. Institute of Food and Agriculture Science, Immokalee, FL University of Florida, 1–9.
Ong, H., Mahlia, T., Masjuki, H., and Norhasyima, R. (2011). Comparison of palm oil, Jatropha curcas and Calophyllum inophyllum for biodiesel: a review. Renew. Sustain. Energy Rev. 15, 3501–3515. doi:10.1016/j.rser.2011.05.005
Onukwuli, D. O., Emembolu, L. N., Ude, C. N., Aliozo, S. O., and Menkiti, M. C. (2017). Optimization of biodiesel production from refined cotton seed oil and its characterization. J. Petroleum 26, 103–110. doi:10.1016/j.ejpe.2016.02.001
Patil, P. D., and Deng, S. (2009). Optimization of biodiesel production from edible and non-edible vegetable oils. Fuel 88, 1302–1306. doi:10.1016/j.fuel.2009.01.016
Rana, Q. U. A., Irfan, M., Ahmed, S., Hasan, F., Shah, A. A., Khan, S., et al. (2022). Bio-catalytic transesterification of mustard oil for biodiesel production. Biofuels 13 (1), 69–76. doi:10.1080/17597269.2019.1655907
Rana, Q. U. A., Rehman, M. L. U., Irfan, M., Ahmed, S., Hasan, F., Shah, A. A., et al. (2019). Lipolytic bacterial strains mediated transesterification of non-edible plant oils for generation of high quality biodiesel. J. Biosci. Bioeng. 127 (5), 609–617. doi:10.1016/j.jbiosc.2018.11.001
Rashid, U., Anwar, F., Moser, B. R., and Knothe, G. (2008). Moringa oleifera oil: a possible source of biodiesel. Moringa oleifera oil a possible source biodiesel Bioresour. Technol. 99, 8175–8179. doi:10.1016/j.biortech.2008.03.066
Reddy, A., Ahmed, A., Islam, M., and Hamdan, S. (2015). Methanolysis of Crude Jatropha oil using heterogeneous catalyst from the seashells and eggshells as green biodiesel. ASEAN J. Sci. Technol. Dev. 32, 16–30. doi:10.29037/ajstd.9
Society, A. O. C. (1988). Official and tentative methods. Association of Official Analytical Chemists.
Soudagar, M. E. M., Afzal, A., Safaei, M. R., Manokar, A. M., El-Seesy, A. I., Mujtaba, M. A., et al. (2020). Investigation on the effect of cottonseed oil blended with different percentages of octanol and suspended MWCNT nanoparticles on diesel engine characteristics. J. Therm. Analysis Calorim. 147, 525–542. doi:10.1007/s10973-020-10293-x
Soudagar, M. E. M., Nik-Ghazali, N. N., Kalam, M. A., Badruddin, I. A., Banapurmath, N. R., and Akram, N. (2018). The effect of nano-additives in diesel-biodiesel fuel blends: a comprehensive review on stability, engine performance and emission characteristics. Energy Convers. Manag. 178, 146–177. doi:10.1016/j.enconman.2018.10.019
Soudagar, M. E. M., Nik-Ghazali, N. N., Kalam, M. A., Badruddin, I. A., Banapurmath, N. R., Ali, M. A. B., et al. (2020). An investigation on the influence of aluminium oxide nano-additive and honge oil methyl ester on engine performance, combustion and emission characteristics. Renew. Energy 146, 2291–2307. doi:10.1016/j.renene.2019.08.025
Usta, N. (2005). An experimental study on performance and exhaust emissions of a diesel engine fuelled with tobacco seed oil methyl ester. Energy Convers. Manag. 46, 2373–2386. doi:10.1016/j.enconman.2004.12.002
Keywords: acid pretreatment, alkaline transesterification, biodiesel, Jatropha curcas, two-step biodiesel production
Citation: Haq A, Laiq Ur Rehman M, Rana QuA, Khan A, Sajjad W, Khan H, Khan S, Shah AA, Hasan F, Ahmed S, Islam A, Badshah M, Shah TA, Dawoud TM and Bourhia M (2023) Production, optimization, and physicochemical characterization of biodiesel from seed oil of indigenously grown Jatropha curcas. Front. Energy Res. 11:1225988. doi: 10.3389/fenrg.2023.1225988
Received: 20 May 2023; Accepted: 26 July 2023;
Published: 15 August 2023.
Edited by:
Mohammad Rehan, King Abdulaziz University, Saudi ArabiaReviewed by:
Cherng-Yuan Lin, National Taiwan Ocean University, TaiwanManzoore Elahi M. Soudagar, Universiti Tenaga Nasional, Malaysia
Copyright © 2023 Haq, Laiq Ur Rehman, Rana, Khan, Sajjad, Khan, Khan, Shah, Hasan, Ahmed, Islam, Badshah, Shah, Dawoud and Bourhia. This is an open-access article distributed under the terms of the Creative Commons Attribution License (CC BY). The use, distribution or reproduction in other forums is permitted, provided the original author(s) and the copyright owner(s) are credited and that the original publication in this journal is cited, in accordance with accepted academic practice. No use, distribution or reproduction is permitted which does not comply with these terms.
*Correspondence: Malik Badshah, bWFsaWtiYWRzaGFoQHFhdS5lZHUucGs=; Mohammed Bourhia, bW9oYWJvdXJoaUBnbWFpbC5jb20=
†Present addresses: Abdul Haq, Peshawar, Laboratories Complex, Pakistan Council of Scientific & Industrial Research, Peshawar, PakistanMian Laiq Ur Rehman, College of Environmental Science and Engineering, Nankai University, Tianjin, ChinaQurrat ul Ain Rana, Joint Genome Institute, Lawrence Berkeley National Laboratory, Berkeley, CA, United States Arshad Islam, Department of Pathology, Lady Reading Hospital Medical Teaching Institution, Peshawar, Pakistan
‡These authors have contributed equally to this work