- 1Department of Physics, University of North Bengal, Darjeeling, West Bengal, India
- 2Department of Chemistry, University of North Bengal, Darjeeling, West Bengal, India
- 3Université Paris-Saclay, CentraleSupélec, Laboratoire de Mécanique Paris-Saclay, Gif-sur-Yvette, France
Fabricating a piezoelectric generator for harvesting mechanical energy is a recent development that has exhibited great potential to enhance the piezoelectric coefficient, stretchability, flexibility, and integrability in small-scale (i.e., micro or nano) power supply and sensor systems for diverse applications. In this study, we report on the preparation of a copolymer composite P(VDF-HFP)/(Fe2O3–PANI) film, i.e., (‘hfp-fe-pn’), fabricated by incorporating ferric oxide (Fe2O3) and polyaniline (PANI) fillers with the host poly(vinylidene fluoride-co-hexafluoropropylene) [P(VDF-HFP)] copolymer that yields more than 99% electroactive β- and γ-phase formation, where a traditional electrical poling treatment was avoided. The nucleation and enhancement in the piezoelectric phase (i.e., β-phase) and the conversion of the degree of crystallinity (
1 Introduction
With the development of scientific technology and energy limitations, renewable energy sources have become one of the most rapidly growing research areas. Traditionally, batteries are used as the primary energy source to power vast number of small electronic devices such as actuators, sensors, wireless transmitters, and other embedded systems in medical, remote-control, and environmental protection applications. However, with a limited lifetime, managing, monitoring, and recycling large quantities of batteries is a challenge. The waste of hazardous chemicals left in the exhausted batteries has become another crucial environmental threat. Each device requires only small-scale power, with an average of microwatt (μW) to milliwatt (mW) levels. As a result, developing self-powered system becomes an ideal approach to relieve energy crises and environmental threats (Chu and Majumdar, 2012; Fan et al., 2016). Therefore, a different energy harvesting method called ‘nanogenerator’ (NG) was introduced by Wang and Song in 2006 to symbolize the energy harvesting devices that generate electricity based on the piezoelectric effect from nanoscale piezoelectric materials by employing them in low-frequency mechanical vibrations accessible under ambient atmospheres and human body motions (Wang, 2006; Wang, 2017). In the last 10 years, different types of NGs, including piezoelectric nanogenerators (PENGs), triboelectric nanogenerators (TENGs), pyroelectric nanogenerators (PyNGs), and thermoelectric devices, have exhibited excellent performance in harvesting and converting energy from natural resources (Fan et al., 2012; Zi and Wang, 2017; Garain et al., 2015; Adhikary and Mandal, 2017). Among the various energy harvesting systems, converting mechanical energy into electric power is a recent emerging technology in self-powered electronic devices. Mechanical energy is one of the most abundant forms of energy in the environment; energy from walking, running, talking, using transportation, the motion of eyes, muscle stimulation, and even the movement of bodily fluids, heartbeats, and respiration is often wasted (Chu and Majumdar, 2012; Adhikary and Mandal, 2017). For self-powering Internet of Things (IoT) systems, this energy can be collected and used as an essential source of renewable energy. Therefore, unlike other energy converting systems, converting wasted mechanical energy into electricity has become one of the crucial technologies compared to TENGs and PyNGs in embedded electronic systems, biomedical sensor fabrication, and self-powering IoTs where the external power sources may be ignored (Garain et al., 2015; Zi and Wang, 2017). Several research groups have attempted to fabricate high-performance piezoelectric generators (PEGs) with well-grown nanostructures of inorganic piezoelectric materials, i.e., BaTiO3, PZT, ZnSnO3, ZnO, and GaN, and their composite forms with polymers (Chen et al., 2010; Lin et al., 2012; Anand et al., 2020). Piezoelectric polymers, particularly poly(vinylidene fluoride) (PVDF) and its copolymers such as poly(vinylidene fluoride-co-hexafluoropropylene) (P(VDF-HFP)) and poly(vinylidene fluoride-co-trifluoroethylene) (P(VDF-TrFE)), in their all-trans pseudohexagonal phase, offer recognizable advantages over ceramics in specific applications. These advantages include ease of processing at low temperatures, low density, low stiffness, flexibility, and mechanical robustness, such as toughness and the ability to withstand high strains before failure (Wu et al., 2022; Hoque et al., 2017; Singh et al., 2017; Saxena and Shukla, 2021; Nalwa and Dekker, 1995). Recently, several investigations have revealed that the piezoelectric coefficient (d31) and the electromechanical coupling factor (k31) of P(VDF-HFP) (4.5 mol%) are significantly higher than those of PVDF and P(VDF-TrFE) copolymers. Moreover, the copolymer P(VDF-HFP) exhibits an unusual piezoelectric response, i.e., |d31/d33| > 1, which is uncommon compared to other piezopolymers (Neese et al., 2007; Adhikary and Mandal, 2017). Owing to this property, P(VDF-HFP) might be responsible for longitudinal and transverse directions, making it more effective under ubiquitous environmental vibrations. P(VDF-HFP) has been reported as a ferroelectric copolymer having at least three regular conformations with similar energies; it occurs in several conformations: the α-phase (TGTG conformation) with alternating trans (T) and gauge (G) linkages; the β-phase (all trans, TTTT conformation); the semi-polar γ-phase (TTTG conformation); and the δ-phase (polarized α-phase), but only the β-, γ-, and δ-phases show favorable electroactivity specifically, piezoelectricity manifested through spontaneous polarization which is the focus of interest here. In contrast, among all of these phases, the α-phase is electrically inactive (Hoque et al., 2018; Shin et al., 2014; Chen et al., 2010; Chipara et al., 2020). It has been observed that the piezo-response and energy harvesting capability from the films arise due to molecular dipoles (i.e., –CH2−/−CF2–) present in the P(VDF-HFP) copolymer matrix existing in the β-, γ-, and δ-phases and are directly related to and essentially proportional to effective polarization (Singh et al., 2017). So, enhancing the β-, γ-, and δ-phases will affect the piezoelectric response and the energy harvesting performances by increasing the number of external free electrons that accumulate on both sides of the composite films to balance the potential produced by the –CH2−/−CF2 dipoles (Hoque et al., 2018). Several techniques can be used to achieve the β- and γ-phases in P(VDF-HFP), including electrical poling, mechanical stretching, electrospinning, spin coating, and doping with different salt fillers and nanoparticles (Adhikary and Mandal, 2017; Sk et al., 2022). Particularly, it is widely accepted that mechanical stretching is required to achieve a polar electroactive β-phase that exhibits piezoelectricity after external electrical poling treatment (Mao et al., 2014). However, the stretched film suffers from surface and thickness inhomogeneity, which is unfavorable for device fabrication. In addition, electrical poling steps must be performed carefully as the film is susceptible to failure due to electrical breakdown. In addition, the great interest in wearable electronics increases the interest in self-powered technologies and continues to gain researchers’ attention. Recently, piezoelectric composites with different fillers in a polymer matrix have emerged as promising candidates for PEGs and PENGs. These composites combine the high piezoelectric performance of the fillers with the flexibility of the polymer matrix. Examples include organic/inorganic piezoelectric composites such as BTO/PVDF, solid solution (BCZT)/PVDF, PZT/PVDF, and PZT/polydimethylsiloxane (PDMS) (Zhao et al., 2015). Sumanta et al. developed a flexible, sensitive, cost-effective hybrid piezoelectric nanogenerator (HPNG) by integrating flexible steel-woven fabric electrodes into a poly(vinylidene fluoride) (PVDF)/aluminum oxide-decorated reduced graphene oxide (AlO-rGO) nanocomposite film, where AlO-rGO acts as a nucleating agent for electroactive β-phase formation. The fabricated nanogenerator (HPNG) shows an unprecedented shifting of open-circuit output voltage to a high value of ∼36 V and short-circuit current of ∼0.8 μA, corresponding to a power density of ∼27.97 μW/cm3 under repeating human finger imparting conditions, which are reported with PVDF-based PNGs (Karan et al., 2016). Yu et al. reported a high-performance β-PVDF-based piezoelectric and triboelectric hybrid nanogenerator (PTNG) employing large-scale PVDF films or bulks by using liquid nitrogen to induce the phase transition and in situ doped conductive polyaniline (PANI). Adding PANI as a conductive material opens the channel for carriers to move the charge in the bulk material. Subsequently, the polymer chains become entangled with each other through strong hydrogen bonding and dipole–dipole interactions. The PTNG exhibits excellent piezoelectric properties, and the optimal output of the PTNG, with a β-phase content of up to 71%, reaches 246 V and 122 μA at a frequency of 30 Hz and a pressure of 0.31 MPa, and the power density is calculated to be 6.69 W/m2 (Yu et al., 2021). Ongun et al. demonstrated electrospinning PVDF-based nanogenerators with various concentrations of iron oxide (Fe2O3) nanoparticles (0.2, 0.4, 0.6, and 0.8 wt%). In a nanogenerator with piezoelectric properties, the output voltage of β-PVDF in the presence of 0.4 wt% of Fe2O3 NPs reaches up to 1.39 V (Ongun et al., 2020). Chen et al. reported a flexible hybrid NG based on an array of P(VDF-TrFE) nanowires with improved piezoelectric output voltage/current of approximately 4.0 V/65 nA. Likewise, another hybrid NG was designed, consisting of micro-patterned P(VDF-TrFE) with a thickness of approximately 7 μm, acting as both pyroelectric and piezoelectric layers; graphene nanosheets and a PDMS-CNT composite served as the two electrodes of the nanogenerator. The structure diagram of the hybrid piezoelectric–PyNG and SEM images of PDMS-CNT composite and P(VDF-TrFE) were provided. The highly stretchable PyNGs generated output voltages ranging from 8 mV to 2.48 V (Chen et al., 2016). Yang et al. demonstrated a flexible hybrid energy harvesting cell consisting of piezoelectric and pyroelectric NGs and solar cells, which can be employed to individually or simultaneously harvest thermal, mechanical, and solar energies. The presented cell was fabricated using PVDF with a film thickness of approximately 110 μm and a flexible array of ZnO nanowires of diameters of approximately 100 nm and poly(3-hexylthiophene) (P3HT) film heterojunctions for scavenging solar energy. The PVDF film-based piezoelectric NG showed an output voltage and a current of (0.5 V/20 nA) when a compressive strain was applied to the NG (Yang et al., 2012). It is realized that incorporating different external fillers in a polymer matrix is one of the most cost-effective and industrially friendly approaches in large-scale PEG fabrication (Davis et al., 1978; Chen et al., 2007; Lei et al., 2024; Parangusan et al., 2021).
In this study, we selected P(VDF-HFP) as a host material and incorporated Fe2O3 and PANI fillers to investigate the cooperative effect of the surface charges from Fe2O3 and the presence of the (=N–H)+ group in PANI within the ‘hfp-fe-pn’ composite film. The goal was to efficiently reduce the heterogeneity between two different dielectric phases, induce the electro-active β- and γ-phases, and enhance the piezoelectric response. In contrast, electrical poling steps can be avoided if self-poled techniques are implemented, and thus, a cost-effective piezoelectric-based device becomes easier to fabricate. A concentration of 0.6 wt% of Fe2O3 and PANI fillers in the P(VDF-HFP)/Fe2O3–PANI composite film resulted in the formation of more than 99% electroactive phase (FEA). A decrease in the piezoelectric β-phase content in the composite indicates the formation of the δ-phase (αp-phase). This δ-phase may have contributed to dipole moment in aligned molecular dipoles along with the β- and γ-phases, which shows higher piezo voltage for the ‘hfp-fe-pn’ composite containing a lower β-phase. The addition of PANI to this as a conductive material opens the channel for carriers to move charge in the bulk material, and subsequently, the polymer chains become entangled with each other through strong hydrogen bonding and dipole–dipole interactions. Freely mobile electrons in the conductive PANI can promote the movement of charge in the material through the conductive network formed between PANI and P(VDF-HFP), thus improving energy transfer efficiency. It can be observed from the morphology analysis of the ‘hfp-fe-pn’ composite that the dispersion of PANI in the P(VDF-HFP) copolymer matrix causes more agglomerations of particles in the composite. This particular composite’s morphology helps reduce the loss of the material’s unique properties needed for energy harvesting applications. Metal oxides, such as iron oxide (Fe2O3), can be suitable reinforcement candidates in P(VDF-HFP) to improve the energy harvesting properties of polymer composites. Fe2O3 can create defects and alter the materials’ electronic structure, making it more responsive to mechanical stress. It is also observed that ferric oxide (Fe2O3), when doped at concentrations above the critical threshold of 0.4 wt% of Fe2O3 NPs in PVDF, shows unusual behavior within the composite. Yempally et al. reported a simple and fast non-solvent-induced phase separation (NIPS) process to develop PVDF-based polymer composites containing Zn–Fe2O3 nanomaterials. At 3 wt%, Zn–Fe2O3 induced an open-circuit voltage of 0.41 V, which is approximately 12 times greater than that of the neat PVDF film (Yempally et al., 2023). We have mainly focused our study on the synergistic effects of Fe2O3 and PANI fillers in the P(VDF-HFP) copolymer matrix. The fabricated ‘hfp-fe-pn’-based flexible PEG’s output voltage response of ∼8 V demonstrated the different electroactive phase formations in the copolymer matrix and the contributions of Fe2O3 and PANI fillers. The PANI filler effectively reduces the internal resistance of the PEG and easily forms a conduction pathway through its network structure, and Fe2O3 acts as a reinforcing agent in the P(VDF-HFP) copolymer matrix.
2 Experimental sections
2.1 Materials
Poly(vinylidene fluoride-co-hexafluoropropylene) (P(VDF-HFP)) pellets (Mw ∼ 275,000, Sigma-Aldrich, United States), N, N-dimethylformamide (DMF) (Merck Chemical, India), ferric oxide (Fe2O3) (Alfa Aesar), and polyaniline (PANI) (SRL, India) were used in the experiment.
2.2 Preparation of the composite film
We used a simple solution-casting method to prepare these films without mechanical, thermal, or electrical treatment. First, 6 wt% of P(VDF-HFP) was dissolved in 10 mL of DMF by continuous stirring for 12 h at 60°C. The solution was designated as the ‘hfp’ solution. Then, we divided the solution into five equal parts and kept them in vials; one of the vials was used as the reference sample, referred to as the ‘neat’ sample. Then, the same amounts, i.e., concentrations (0.2, 0.4, 0.6, and 0.8, 1 wt%), of Fe2O3 and PANI were added into the remaining vails containing the ‘hfp’ solution. The mixtures were vigorously stirred under constant magnetic stirring for 6 h to ensure proper dissolution of the external additives and homogeneous dispersion in the composite films. Afterward, the ‘neat’ and composite solutions were drop-cast onto the clean glass slides and dried at 60°C for 5 h. Finally, the resulting free-standing dried films were peeled off the glass substrates for further characterization and device fabrication. The films were designated as “hfp” for the neat, where the external additives were not added, and ‘hfp-fe’, ‘hfp-pn’ and ‘hfp-fe-pn’ for the composites. A thick film (thickness ∼0.2 mm) of the ‘hfp-fe-pn’ sample was also prepared at 60°C for energy harvesting applications. For simplicity, we used the short notations of these external additives, i.e>., ‘fe’ for ferric oxide (Fe2O3) ‘pn’ for polyaniline (PANI).
2.3 Film characterization
The crystalline phases of the ‘hfp’ and ‘hfp-fe-pn’ films that are relevant to the characteristic vibrational modes of the molecular chain of copolymer P(VDF-HFP) were identified via attenuated total reflectance (ATR) spectroscopy. The ATR spectra were recorded on a Bruker Tensor II Spectrometer with a spectral resolution 4 cm–1. An X-ray diffractometer (Empyrean, D8 ADVANCE) in the range 2θ = 0°–100° with CuKα radiation of 1.54 Å wavelength was used to analyze the crystallographic information of the P(VDF-HFP) polymorph and its degree of crystallinity (
3 Results and discussion
3.1 Characterizations of the composite film
3.1.1 Spectroscopic analysis
ATR spectroscopy of the films was performed to understand the crystalline phase identifications of the polymorphs regarding local phonon bands of P(VDF-HFP) and analyze the piezoelectric β-phase and electroactive γ-phase formation. Now, a piezoelectric material should have non-centro symmetry. In copolymer P(VDF-HFP), α-, β-, γ-, δ-, and ε- are the five well-known phases of molecular chain conformation, and among them, the β-phase is polar-electroactive and ferroelectric and is responsible for the piezo- and pyroelectric properties of the material. In the ATR spectra (Figure 1a), the characteristic phonon modes of the well-known phases provide clear insights into the development of the different phases of the films, and the spectra confirm the presence of a predominantly non-electroactive α-phase in the ‘hfp’ and ‘hfp-fe’ film, which is evidenced by characteristic vibrational bands at 616 and 764 (CF2 bending and skeletal bending), 797 (CH2 rocking), 978, and 1,211 cm–1, along with a trace amount of β/γ-phases revealed by the presence of a weak band at 840 cm–1 (CH2 rocking) (Martins et al., 2014; Maity et al., 2018). After the two fillers, Fe2O3 and PANI, were introduced into the ‘hfp’ solution, prominent characteristic peaks at 1,233 cm–1
where AEA is the intensity of absorbance at 840 cm–1, ANEA is the intensity of absorbance at 764 cm–1, K840 is the coefficient of absorption at wave number 840 cm–1, and K764 is the coefficient of absorption at wave number 764 cm–1. K840 = 7.7 × 104 cm2mol–1, and K764 = 6.1 × 104 cm2mol–1. The normalization of ATR absorption was carried out with respect to the 1,070 cm–1 band (related to the thickness of composite films) before quantitative estimation of the relative amount of polar and nonpolar phase fractions. To separate β- and γ-phases at 840 cm–1 and to quantify them individually, we have deconvoluted the ATR spectra of the ‘hfp’ and ‘hfp-fe-pn’ films in the range from 720 to 930 cm–1, as shown in Figure 1d, where the ATR pattern of the 840 cm–1 band was isolated by the Gaussian function for calculating the relative proportion of individual electroactive β-, i.e., F(β), and γ-, i.e., F(γ), phases, separately. The relative proportion of individual β- and γ-phases is calculated using Equations 2a, b as follows:
and
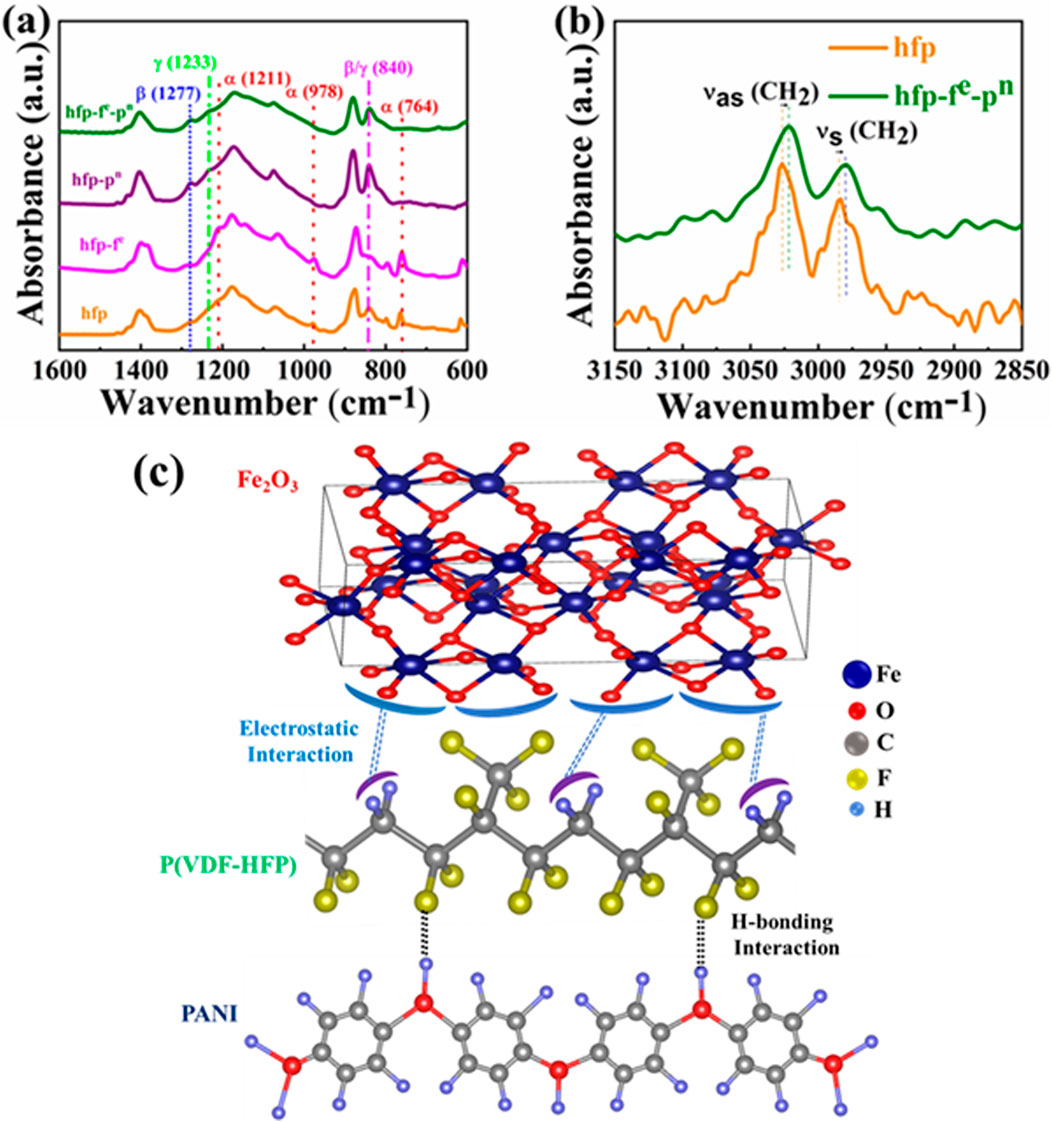
Figure 1. (a) ATR spectra of ‘hfp’ film and ‘hfp-fe’, ‘hfp-pn’ and ‘hfp-fe-pn’ composite films in the range from 1,600 to 600 cm–1. (b) An enlarged view from 3,150 to 2,850 cm–1 of the ATR spectra demonstrates the frequency shifting of the (–CH2–) stretching vibrations. (c) Plausible interaction mechanism between Fe2O3/PANI and P(VDF-HFP) molecular chains, inducing the formation of the TTTT conformation.
where Aβ and Aγ represent areas of the band under the deconvoluted curves of the β- and γ-phases, respectively, which are centered at 840 cm–1.
The deconvoluted curve centered at 840 cm–1 of the ‘hfp’ and composite ‘hfp-fe’, ‘hfp-pn’ and ‘hfp-fe-pn’ films are represented in Figure 2. Using Equations 2a, b, the proportions of β-, i.e., F(β), and γ-, i.e., F(γ), fractions are found to be 75% and 23%, respectively, for the ‘hfp-fe-pn’ composite. It should be noted that there is a decrease in the β-phase content ratio in the composite. This is due to the growth of a polarized α-phase that exhibits properties analogous to electroactive phases, such as the β-phase; in other words., the formation of δ-phase may occur in the composite during film preparation. For the other composites, the calculated values of F(β) and F(γ) are tabulated in Table 1. So, using 0.6 wt% of both Fe2O3 and PANI fillers in the copolymer P(VDF-HFP) results in a higher yield of electroactive phases, which might be more suitable for designing piezo-, pyro-, and ferroelectric-based sensors, actuators, and vibration-based energy harvesters.
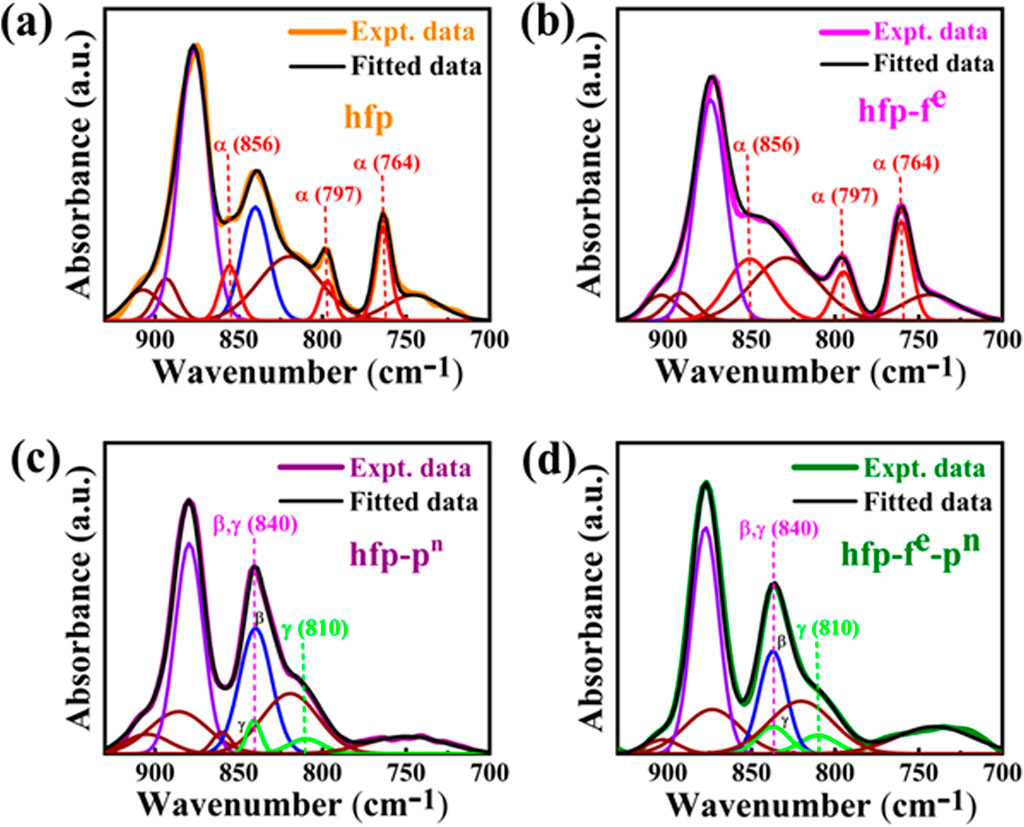
Figure 2. ATR spectra for (a) ‘hfp’ film and (b) ‘hfp-fe’, (c) ‘hfp-pn’ and (d) ‘hfp-fe-pn’ composite films that are deconvoluted in the region from 720 to 930 cm–1 to identify β- and γ-phases present at 840 cm–1.

Table 1. The degree of crystallinity in percentage (%) and the sizes of the films’ α-, β-, and γ-crystallites determined by ATR and XRD spectra.
The ATR spectra in the frequency region 3,150–2,850 cm–1 of the ‘hfp’ and ‘hfp-fe-pn’ films of the –CH2– asymmetric (
3.1.2 X-ray diffraction studies
P(VDF-HFP) is semi-crystalline and approximately 50% amorphous with several stable crystalline forms. The piezoelectric performance of P(VDF-HFP) depends on the electroactive crystalline phases’ content, where the β-phase is the most piezoelectrically responsive one. The XRD pattern, as shown in Figures 3a, b, of the ‘neat hfp’ and ‘hfp-fe’ films shows peaks at 17.6° (100), 18.3° (202), 19.8° (110), and 19.9° (110) of the diffracting planes that are attributed to the presence of the characteristic non-electroactive α-phase (Benz and Euler, 2003; Jin et al., 2013; Chen et al., 2007). On the other hand, Figures 3c, d show that the fillers Fe2O3 and PANI used in the ‘neat hfp’ sample, i.e., ‘hfp-pn’ and ‘hfp-fe-pn’ films, possess an intense diffraction 2θ peak as a doublet at 20.6° of two overlapping lattice reflections of the diffracting planes (110)/(200) due to the presence of the piezoelectric polar β-phase along with a trace amount of moderately polar γ-phase, which is confirmed by the presence of three additional peaks (202), (110), and (110) at 18.5°, 20.4°, and 20.2°, respectively (Adhikary et al., 2016; Martins et al., 2014; Gregorio, 2006; Chen et al., 2021). So, the XRD results reveal that electroactive β- and γ-phases are formed in these composite films, and α-characteristic peaks still exist in the ‘hfp-fe’ film. It may be due to the growth of polarized α-phase, i.e., the formation of δ-phase (αp-phase) in the composite ‘hfp-fe’ film during film preparation, which is also clear from the ATR spectrum with a dominant peak at 764 cm−1, the characteristic peak of the α-phase. Among the different phases of the polymer PVDF, the δ-phase is analogous to the polarized form of the α-phase, also known as the αp-phase, which is electroactive, and few recent studies also showed that the δ-phase has almost analogous electroactive properties like the piezoelectric β-phase (Mishra et al., 2022; Gupta et al., 2021; Martín et al., 2017; Chipara et al., 2020). The peak intensity with the addition of external fillers at these doublet 2θ values is enhanced due to the interaction between the –CH2−/−CF2– dipoles of P(VDF-HFP) and the fillers at the interfaces, inducing the formation of a greater amount of crystalline β-phase in the composite ‘hfp-pn’ and ‘hfp-fe-pn’ films than in the pure ‘hfp’ and ‘hfp-fe’ films. Thus, all α-phase characteristic peaks are transformed (i.e., α → γ/β phase) in the ‘hfp-fe-pn’ film as fillers Fe2O3 and PANI play important roles in inducing a crystallographic α → γ/β phase transformation in the P(VDF-HFP) matrix, which is confirmed further with the ATR spectroscopic data analysis. It is noteworthy that the broad peak at 20.5° arises from the overlapping of β-phase peak [at 20.6° (110)/(200)] and γ-phase peak [at 20.4° (110)]. So, curve deconvolution of the peak at 20.5° can provide information on the crystallites of β- and γ-phases. The broad halo around these intense doublet 2θ peaks arises from the amorphous components of the P(VDF-HFP) copolymer. So, the crystalline and amorphous regions shown in the XRD patterns were isolated first by the Gaussian function to calculate the average degree of total crystallinity (
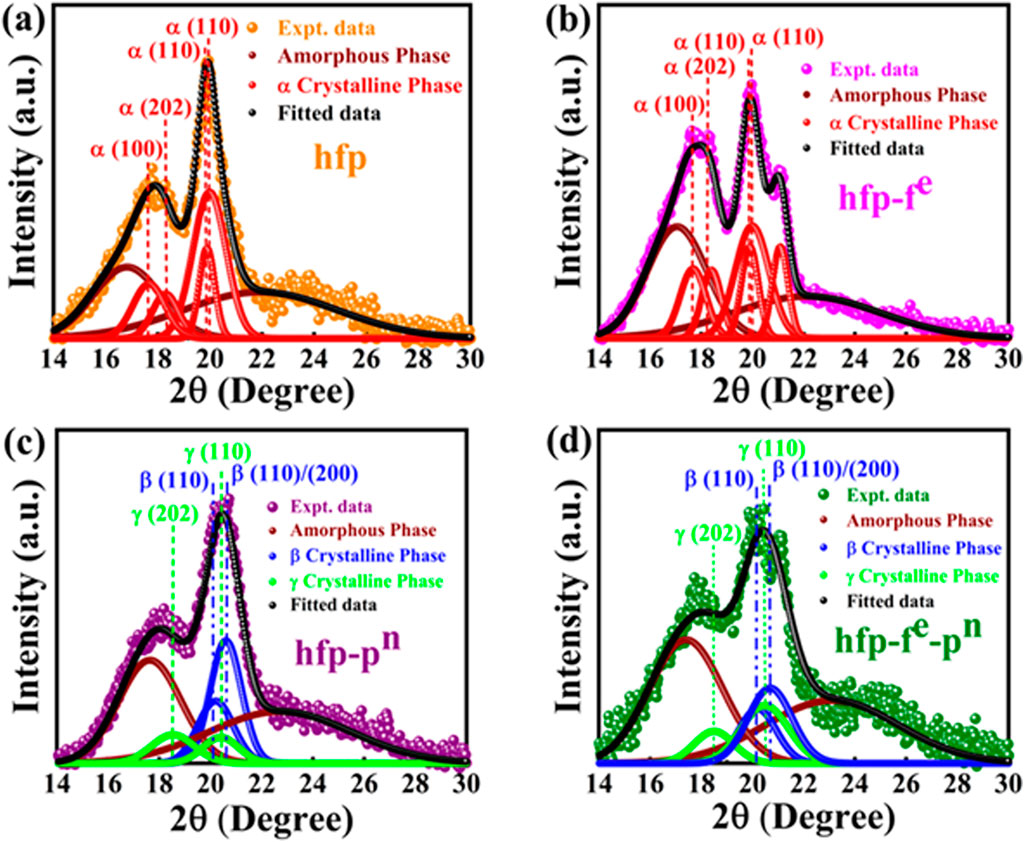
Figure 3. XRD patterns for (a) ‘hfp’ film and (b) ‘hfp-fe’, (c) ‘hfp-pn’ and (d) ‘hfp-fe-pn’ composite films deconvoluted in the 14°–30° range.
where
where ‘t’ is the crystallite size, ‘B’ is the full width at half maximum (FWHM) of the diffraction peak in radians, ‘λ’ is the X-ray wavelength (i.e., 1.54 Å), and k = 0.89 is a constant. The individual degree of crystallinity of the respective crystalline, i.e., β- and γ-phases, can be calculated using Equations 5a, b, which are tabulated in Table 1.
and
It should be noted that in the ‘hfp-fe-pn’ film with added fillers Fe2O3 and PANI, the initial value of the ‘hfp’ film (
3.1.3 Morphological study
For crystalline phase identification, surface morphology is one of the important parameters for the P(VDF-HFP) copolymer as most of the characteristics of the materials depend on their surface morphology (Garain et al., 2015; Adhikary and Mandal, 2017). The FE-SEM image shown in Figure 4a of the film shows the presence of a predominant α-phase, evidenced by the spherulitic texture of the micrometer scale, one of the characteristic features of α-phase presence that are consistent with the ATR and XRD data. Fe2O3 and PANI fillers utilized in P(VDF-HFP) give rise to polymer microstructures, as observed by the surface morphology (Figure 4b) of the composite ‘hfp-fe-pn’ film. The presence of Fe2O3 and PANI on the surface of the ‘hfp-fe-pn’ composite film sample was confirmed by EDS spectra at each of the locations investigated, as shown in Supplementary Figure S4. As observed in the FE-SEM images, incorporating fillers into the P(VDF-HFP) matrix leads to some morphological alterations. A large number of aggregated particles likely consisting of indistinguishable Fe2O3 and agglomerate PANI fillers are observed on the surface of the modified copolymer matrix, i.e., in the ‘hfp-fe-pn’ film. This agglomeration is likely due to the formation of the polymer-filler complexes through interactions with the charges of different fillers, resulting in their non-uniform distribution within the modified co-polymer matrix (Thakur et al., 2015; Jisha et al., 2020; Yempally et al., 2023). It should also be noted that in the modified ‘hfp-fe-pn’ film, the stability of the copolymer and its miscibility can be promoted by dipole or van der Waals interactions. The composite is miscible due to the dipole/dipole interactions between the –CF2 groups of P(VDF-HFP) and the (=N–H)+ groups of PANI and the interfacial interactions by the negative surface charges of Fe2O3 and –CH2 dipoles present in the P(VDF-HFP) matrix. These types of interactions have the potential to create novel morphologies and alter the spherulitic morphologies of P(VDF-HFP), respectively. The clustering of PANI and Fe2O3 results from enhanced interfacial interaction among the constituent fillers, which can be attributed to the compatibility between the fillers and the P(VDF-HFP) copolymer matrix. The morphology of this particular composite will help in reducing the dielectric loss of the material. So, in the ‘hfp-fe-pn’ film, where external fillers are incorporated into the ‘neat hfp’ sample, the characteristic spherulitic texture of the α-phase is significantly reduced. This signifies that fillers can hinder the growth of the non-electroactive α-phase and promote the formation of the electroactive phases, i.e., β- and γ-phases (Adhikary and Mandal, 2017; Sk et al., 2022; Adhikary et al., 2015). Thus, it is expected that the refined microstructure of the host P(VDF-HFP) copolymer created by introducing the Fe2O3 and PANI fillers might play an obvious role in promoting the piezoelectric response and the energy harvesting performances in a synthesized ‘hfp-fe-pn’ composite film.
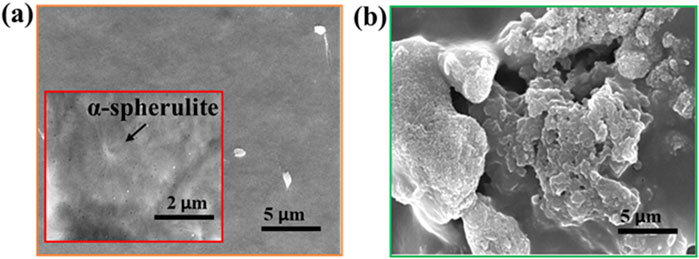
Figure 4. Surface morphology of the (a) ‘hfp’ and (b) ‘hfp-fe-pn’ films. The inset of (a) shows a high-magnification FE-SEM image of the ‘hfp’ film to show the characteristic spherulitic texture of the α-phase.
3.1.4 Energy harvesting performances
To fabricate the flexible PEG, the different films of thickness 0.2 mm ± 9 µm with an area of 3 × 1 cm2 were placed between two aluminum foil electrodes. The entire multilayer structure was then carefully encapsulated using polydimethylsiloxane (PDMS) (SYLGARD 184 Silicone Elastomer) adhesive, prepared with a 10:1 ratio of base to curing agent, and cured in an oven at 60°C for 30 min; this encapsulation ensured structural compactness and provided protection against physical damage. The final cured thickness of the PDMS layer is approximately 42 μm on either side of the electrode–polymer–electrode (EPE) stack, and the corresponding schematic is presented in Figure 6a. The piezo-potential was measured using a DSO using repetitive stress by constant finger tapping applied on the surface of the PEGs of the films, which causes the creation of net dipole moment of –CH2−/−CF2– dipoles present in the P(VDF-HFP) matrix. The piezo-response was measured without applying any electrical poling treatment, which is essential for dipole alignment. Here, it can be assumed that the behavior of the dipoles in copolymer P(VDF-HFP) is self-polarized in a specific direction that helps induce polarization, i.e., resulting in the piezoelectric β-phase formation. Theoretically, it is also observed that piezoelectricity is directly related to and essentially proportional to effective polarization (Mahapatra et al., 2021). So, contributing to microstructural studies of the films can play a significant role in understanding the mechanism better. At the initial state, i.e., before any finger impact on these PEGs’ surface, no electric output is observed because no charge transfer occurs through the external circuit. This is due to the absence of a change in the dipole moment of the aligned molecular dipoles, i.e., –CH2−/−CF2– present in the P(VDF-HFP) matrix existing in the β-phase. When a compressive force is applied by the finger, the surface of the PEG experiences vertical strain, leading to deformation of the β-crystalline structure in the composite films, which causes a piezo-response; in other words, electric output is observed because of charge transfer through the external circuit (Singh et al., 2017; Maity et al., 2018). Figure 5 shows the piezoelectric output voltage responses of the ‘hfp’ film and ‘hfp-fe,’ ‘hfp-pn,’ and ‘hfp-fe-pn’ composite films by applying external mechanical pressure from constant finger tapping on the PEG’s surface (impact pressure amplitude of ∼14 kPa, directly measured using a Flexi Force sensor (A201)). It shows a higher open-circuit voltage of ∼8 V in the ‘hfp-fe-pn’ composite film (PEG) than that in other PEGs, as shown in Table 2. To ensure that the output voltage mainly originated from the piezoelectric effect, we have checked the finger touch response of the ‘hfp-fe-pn’ PEG in both forward and reverse connections, as shown in ESI† (Supplementary Figure S5). When the finger was in contact with the upper surface of the PEG, a piezoelectric potential difference occurred through the electrodes via compressive force, and it gave rise to a positive output voltage, i.e., the ‘touch’ response. After the pressure was released from the upper surface of the PEG, the composite film tried to return to its unstressed state, resulting in a voltage impulse with reversed polarity, which was assigned as the ‘release’ response.

Figure 5. Non-rectified finger touch response from the PEGs prepared with (a) ‘hfp,’ (b) ‘hfp-fe,’ (c) ‘hfp-pn,’ and (d) ‘hfp-fe-pn’ films.

Table 2. Performance comparison of P(VDF-HFP)-based PEGs of ‘hfp’ film and ‘hfp-fe’, ‘hfp-pn’, and ‘hfp-fe-pn’ composite films.
So, it should be noted that the piezo-response in the ‘hfp-fe-pn’ composite film arises solely from the reversible transformation of the overall deformed β-crystalline structures of –CH2−/−CF2– dipole present in the P(VDF-HFP) copolymer matrix into more stable configurations and vice versa under the application of external pressure. The charges generated by the external additives Fe2O3 and PANI utilized in the ‘hfp’ solution actively interact with the –CH2−/−CF2– dipoles of P(VDF-HFP) for the nucleation of the piezoelectric β-phase by filler-induced polarization, resulting in self-polarized films under local stress development and propagation over the joint structures (Sk et al., 2022; Adhikary et al., 2015). To gain better understanding with the applied pressure, a spontaneously induced distortion, i.e., a change in the object’s shape, size, or position, in the fillers Fe2O3 and PANI causes marked improvement in the piezoelectric response by the interplay of the sample between its initial and final states (Lei et al., 2024; Parangusan et al., 2021). On the other hand, the electrical potential generated by the applied external pressure further facilitates the alignment of –CH2−/−CF2– electric dipoles in a unidirectional manner via stress-induced polarization. The piezoelectricity arising in the PEG fabricated with an electro-active phase that dominated the ‘hfp-fe-pn’ film is mainly due to the combined effect of the change in the dipole moment by the applied external mechanical pressure and the presence of two types of interfacial interactions, i.e., electrostatic interactions for Fe2O3 and dipole–dipole interactions by the PANI fillers with the P(VDF-HFP) copolymer matrix. As mentioned above, in the case of the PANI filler, the presence of the (=N–H)+ group and the –CF2 group of P(VDF-HFP) stimulate the interfacial dipole–dipole interaction, which favors the highly polar trans-conformation for the higher yield of piezoelectric β-phase formation (Thakur et al., 2015; Khalifa and Anandhan, 2019; Saïdi et al., 2013). This type of interaction can affect the spherulitic and granular morphology of P(VDF-HFP) and PANI, respectively, leading to the emergence of a new morphology, as observed in the FE-SEM images (Saïdi et al., 2013). It was also reported that the experimental introduction of ferrite particles such as Fe2O3 could nucleate the electroactive β-phase and exhibit both piezoelectric and magnetic properties for the fabricated composites (Andrew and Clarke, 2008). In the case of Fe2O3, negative charges electrostatically interact with the –CH2 dipoles of P(VDF-HFP) responsible for the nucleation of the β-phase, which is also supported by the shifting of –CH2– asymmetric (
where ‘V’ is the output voltage across the load resistance and ‘RL’ reaches up to 10.3 nW at a typical value of ∼10 MΩ of resistance. In addition to instantaneous output voltage, to demonstrate the application of the PEG as a DC power source, it was connected to the capacitors (e.g., 1, 2.2, and 4.7 μF) of different capacitances separately through a full-wave bridge circuit for successfully charging up via a repetitive touch and release motion by the finger on the surface of the PEG made with the ‘hfp-fe-pn’ film, as shown in Figure 6b. Based on the capacitor charging performance curves, the power stored in the capacitors was calculated using Equation 7 as follows:
where ‘C’ is the capacitance of the capacitor, ‘V’ is the saturation voltage, and ‘t’ is the time the capacitor takes to reach a steady state, as shown in Figure 6d. So, the performance of capacitor charging of the PEG indicates its suitability in effectively harvesting the mechanical energies from finger impact, thus making it a potential alternative in the area of self-powered energy harvesting devices. We are also able to lighten white and red LEDs by the ‘hfp-fe-pn’ PEG instantly connected in series through a typical bridge circuit, as shown in ESI† (Supplementary Figure S6) and illustrated in video file 1 (ESI†) by the repetitive finger press and release cycle, where no storage device is used. For a better understanding, we have included some previously reported publications and their results that use various filler materials to highlight advantages or differences in performance and compare their results, as shown in Tables 2, 3. We have also checked the piezoelectric response performances of different PEGs prepared with 0.2, 0.4, 0.8, and 1 wt% of both Fe2O3 and PANI using finger impact and included the performance comparisons, as shown in ESI† (Supplementary Figure S7). It should be noted that piezo-voltage arising in the copolymer P(VDF-HFP) composite films is due to the change in dipole moment in aligned molecular dipoles (i.e., –CH2−/−CF2–) existing in the molecular chain conformation. As previously mentioned, Fe2O3 and PANI used in the ‘hfp-fe-pn’ composite result in the formation of more than 99% electroactive phases (FEA) at a 0.6 wt% concentration, and the decrease in the β-phase content in the composite is due to the formation of the δ-phase (αp-phase). This δ-phase may contribute to dipole moment in aligned molecular dipoles along with the β- and γ-phases, which shows higher piezo voltage for the ‘hfp-fe-pn’ composite containing a lower β-phase (a comparative table was presented in supporting electronic information data file, Supplementary Table S1) (Mishra et al., 2022; Gupta et al., 2021). We have also checked the cycling stability and durability of “hfp-fe-pn” (PEG). For the cycling test, the output performance of the PEG was monitored for at least up to 500 cycles, and the durability test was performed at monthly intervals of 4 months under applied forces using finger impact, and the corresponding results are shown in Figures 7a, b. Interestingly, the piezoelectric output voltage of the PDMS-encapsulated ‘hfp-fe-pn’ PEG was more or less repeatable and had a loss of ∼2% in the second month, ∼4% in the third month, and ∼8% in the fourth month.
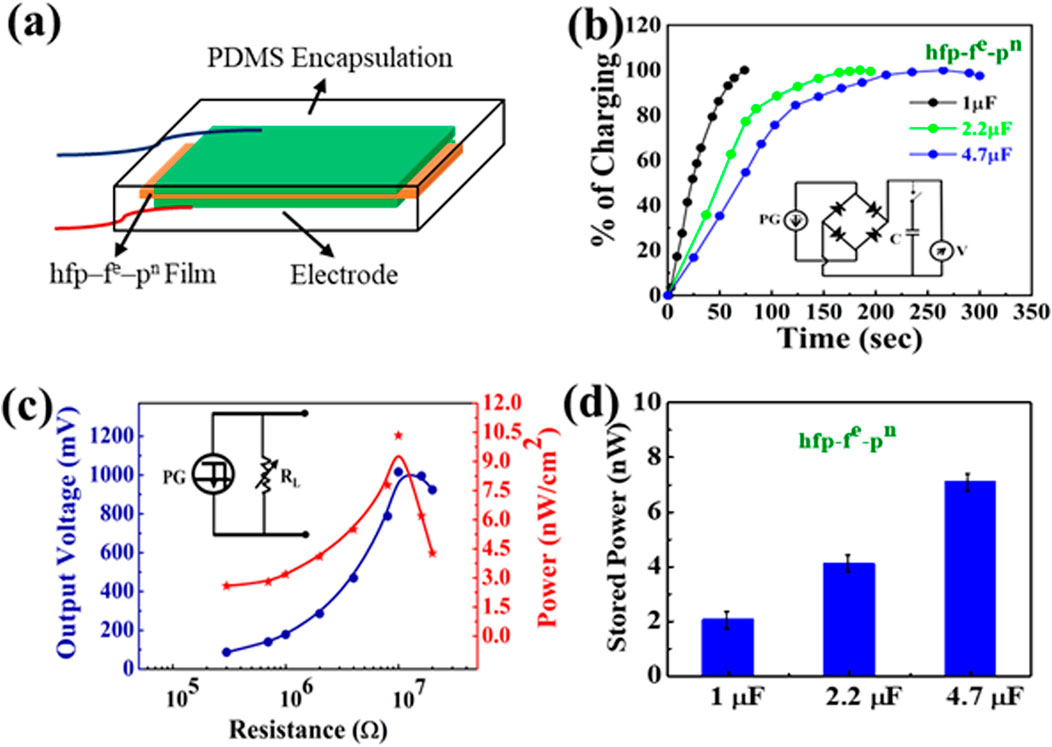
Figure 6. (a) Schematic of PDMS-encapsulated ‘hfp-fe-pn’ composite film. (b) Capacitor (e.g., 1, 2.2, and 4.7 μF) charging performance by finger tapping of ‘hfp-fe-pn’ PEG, and the corresponding circuit diagram is represented in the inset. (c) Dependence of the output voltage and output power on the outer variable resistance of the ‘hfp-fe-pn’ composite PEG. (d) Power stored in the capacitors of 1, 2.2, and 4.7 μF from the PEG.
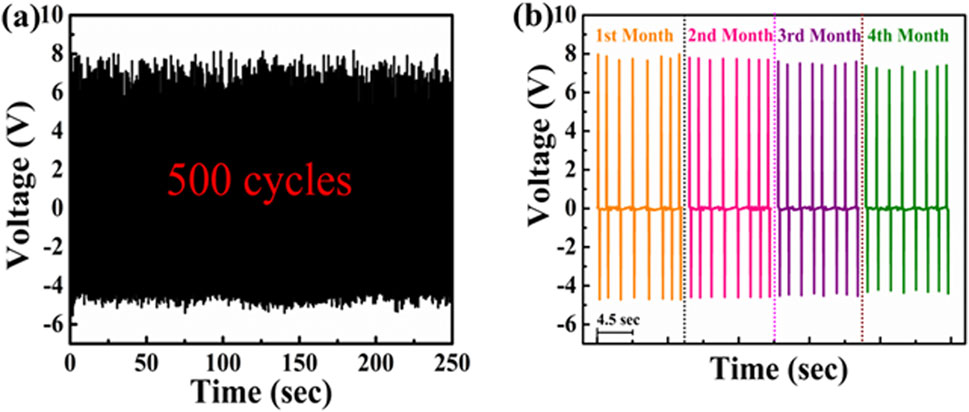
Figure 7. (a) Cycling stability test up to 500 cycles and (b) durability test for 4 months of the PDMS-encapsulated ‘hfp-fe-pn’ PEG.
4 Conclusions
This work emphasized inducing a large proportion (∼99%) of the electroactive β- and γ-phases in copolymer P(VDF-HFP) using fillers (i.e., Fe2O3 and PANI), and the films have been prepared by a simple solution-casting method without any mechanical, electrical, or thermal treatment. It is observed that electroactive phases can be enhanced, which is essential for fabricating the piezoelectric-based generator, by optimizing the incorporated external additives, as revealed by ATR and XRD investigations. The surface morphological study showed distinct differences between the ‘hfp’ film and the ‘hfp-fe-pn’ composite film, and it can be signified as a different phase formation in the composites. The PEG composed of ‘hfp-fe-pn’ composite film can generate an open-circuit voltage of ∼8 V and an output power of 10.3 nW just by finger tapping. The charging capability of the capacitors (e.g., 1, 2.2, and 4.7 μF) of the composite film within a very short time reflects its potential applicability for piezoelectric-based energy harvesting applications in self-powered technologies to utilize the environmental vibrations available around us. Thus, it is very promising for several possible implementations, such as wearable technology, biomedical sensing, health monitoring, environmental protection, and even security.
Data availability statement
The original contributions presented in the study are included in the article/Supplementary Material further inquiries can be directed to the corresponding authors.
Author contributions
PB: conceptualization, data curation, formal analysis, methodology, resources, software, visualization, writing – original draft, and writing – review and editing. AB: formal analysis, validation, resources, writing – review and editing. SA: formal analysis, resources, validation, and writing – review and editing. DR: formal analysis, resources, and writing – review and editing. MR: investigation, methodology, and writing – review and editing. SG: data curation, software, supervision, validation, and writing – review and editing. PA: funding acquisition, investigation, supervision, and writing – review and editing.
Funding
The author(s) declare that no financial support was received for the research and/or publication of this article.
Acknowledgments
The authors thank the Department of Physics, North Bengal University, for providing financial support. Priti Sundar Barman thankfully acknowledges the Govt. of West Bengal for providing a Swami Vivekananda Merit-cum-Means Scholarship (WB-SVMCM; Applicant ID: WBP211629445105). The authors are thankful to the Department of Pharmaceutical Technology and University Science Instrumentation Center (USIC), University of North Bengal, SAIF of Gauhati University, and CIF of Lovely Professional University for the instrumental facility.
Conflict of interest
The authors declare that the research was conducted in the absence of any commercial or financial relationships that could be construed as a potential conflict of interest.
Generative AI statement
The author(s) declare that no Generative AI was used in the creation of this manuscript.
Publisher’s note
All claims expressed in this article are solely those of the authors and do not necessarily represent those of their affiliated organizations, or those of the publisher, the editors and the reviewers. Any product that may be evaluated in this article, or claim that may be made by its manufacturer, is not guaranteed or endorsed by the publisher.
Supplementary material
The Supplementary Material for this article can be found online at: https://www.frontiersin.org/articles/10.3389/fenrg.2025.1570397/full#supplementary-material
References
Adhikary, P., Garain, S., and Mandal, D. (2015). The co-operative performance of a hydrated salt assisted sponge like P(VDF-HFP) piezoelectric generator: an effective piezoelectric based energy harvester. Phys. Chem. Chem. Phys. 17, 7275–7281. doi:10.1039/c4cp05513f
Adhikary, P., Garain, S., Ram, S., and Mandal, D. (2016). Flexible hybrid eu3+doped P(VDF-HFP) nanocomposite film possess hypersensitive electronic transitions and piezoelectric throughput. J. Polym. Sci. Part B Polym. Phys. 54, 2335–2345. doi:10.1002/polb.24144
Adhikary, P., and Mandal, D. (2017). Enhanced electro-active phase in a luminescent P(VDF–HFP)/Zn2+ flexible composite film for piezoelectric based energy harvesting applications and self-powered UV light detection. Phys. Chem. Chem. Phys. 19, 17789–17798. doi:10.1039/c7cp01714f
Anand, A., Meena, D., and Bhatnagar, M. C. (2020). Synthesis and characterization of flexible PVDF/Bi2Al4O9/RGO based piezoelectric materials for nanogenerator application. J. Alloys Compd. 843, 156019. doi:10.1016/j.jallcom.2020.156019
Andrew, J. S., and Clarke, D. R. (2008). Enhanced ferroelectric phase content of polyvinylidene difluoride fibers with the addition of magnetic nanoparticles. Langmuir 24, 8435–8438. doi:10.1021/la801617q
Benz, M., and Euler, W. B. (2003). Determination of the crystalline phases of poly(vinylidene fluoride) under different preparation conditions using differential scanning calorimetry and infrared spectroscopy. J. Appl. Polym. Sci. 89, 1093–1100. doi:10.1002/app.12267
Chamankar, N., Khajavi, R., Yousefi, A. A., Rashidi, A., and Golestanifard, F. (2020). A flexible piezoelectric pressure sensor based on PVDF nanocomposite fibers doped with PZT particles for energy harvesting applications. Ceram. Int. 46, 19669–19681. doi:10.1016/j.ceramint.2020.03.210
Chen, S., Chen, S., Qiao, R., Xu, H., Liu, Z., Luo, H., et al. (2021). Enhanced dielectric constant of PVDF-based nanocomposites with one-dimensional core-shell polypyrrole/sepiolite nanofibers. Compos. Part A Appl. Sci. Manuf. 145, 106384. doi:10.1016/j.compositesa.2021.106384
Chen, S., Yao, K., Tay, F. E. H., and Liow, C. L. (2007). Ferroelectric poly(vinylidene fluoride) thin films on Si substrate with the β phase promoted by hydrated magnesium nitrate. J. Appl. Phys. 102, 104108. doi:10.1063/1.2812702
Chen, X., Shao, J., Li, X., and Tian, H. (2016). A flexible piezoelectric-pyroelectric hybrid nanogenerator based on P(VDF-TrFE) nanowire array. IEEE Trans. Nanotechnol. 15, 295–302. doi:10.1109/tnano.2016.2522187
Chen, X., Xu, S., Yao, N., and Shi, Y. (2010). 1.6 V nanogenerator for mechanical energy harvesting using PZT nanofibers. Nano Lett. 10, 2133–2137. doi:10.1021/nl100812k
Chipara, D., Kuncser, V., Lozano, K., Alcoutlabi, M., Ibrahim, E., and Chipara, M. (2020). Spectroscopic investigations on PVDF-Fe2O3 nanocomposites. J. Appl. Polym. Sci. 137, 48907. doi:10.1002/app.48907
Chu, S., and Majumdar, A. (2012). Opportunities and challenges for a sustainable energy future. Nature 488, 294–303. doi:10.1038/nature11475
Davis, G. T., McKinney, J. E., Broadhurst, M. G., and Roth, S. C. (1978). Electric-field-induced phase changes in poly(vinylidene fluoride). J. Appl. Phys. 49, 4998–5002. doi:10.1063/1.324446
Fan, F. R., Tang, W., and Wang, Z. L. (2016). Flexible nanogenerators for energy harvesting and self powered electronics. Adv. Mater. 28, 4283–4305. doi:10.1002/adma.201504299
Fan, F.-R., Tian, Z.-Q., and Lin Wang, Z. (2012). Flexible triboelectric generator. Nano Energy 1, 328–334. doi:10.1016/j.nanoen.2012.01.004
Garain, S., Sinha, T. K., Adhikary, P., Henkel, K., Sen, S., Ram, S., et al. (2015). Self-poled transparent and flexible UV light-emitting cerium complex–PVDF composite: a high-performance nanogenerator. ACS Appl. Mater. and Interfaces 7, 1298–1307. doi:10.1021/am507522r
Gregorio, R. (2006). Determination of the α, β, and γ crystalline phases of poly(vinylidene fluoride) films prepared at different conditions. J. Appl. Polym. Sci. 100, 3272–3279. doi:10.1002/app.23137
Greijer, H., Mirotta, N., Treossi, E., Valorosi, F., Schütt, F., Siebert, L., et al. (2022). Tuneable conductivity at extreme electric fields in ZnO tetrapod-silicone composites for high-voltage power cable insulation. Sci. Rep. 12, 6035. doi:10.1038/s41598-022-09966-4
Gupta, V., Babu, A., Ghosh, S. K., Mallick, Z., Mishra, H. K., and Mandal, D. (2021). δ-PVDF based flexible nanogenerator. arXiv 2108.09581, 1–15. doi:10.48550/arXiv.2108.09581
Hoque, N. A., Thakur, P., Biswas, P., Saikh, M. M., Roy, S., Bagchi, B., et al. (2018). Biowaste crab shell-extracted chitin nanofiber-based superior piezoelectric nanogenerator. J. Mater. Chem. A 6, 13848–13858. doi:10.1039/c8ta04074e
Hoque, N. A., Thakur, P., Roy, S., Kool, A., Bagchi, B., Biswas, P., et al. (2017). Er3+/Fe3+ stimulated electroactive, visible light emitting, and high dielectric flexible PVDF film based piezoelectric nanogenerators: a simple and superior self-powered energy harvester with remarkable power density. ACS Appl. Mater. and Interfaces 9, 23048–23059. doi:10.1021/acsami.7b08008
Jiawei Chen, J., Fan, J., Livojevic, M., Gupta, M., Tang, T., and Ayranci, C. (2024). Enhancing piezoelectric properties of PVDF-HFP composite nanofibers with cellulose nanocrystals. Mater. Today Commun. 39, 108872. doi:10.1016/j.mtcomm.2024.108872
Jin, J., Zhao, F., Han, K., Haque, M. A., Dong, L., and Wang, Q. (2013). Multiferroic polymer laminate composites exhibiting high magnetoelectric response induced by hydrogen-bonding interactions. Adv. Funct. Mater. 24, 1067–1073. doi:10.1002/adfm.201301675
Jisha, P., Suma, M. S., Murugendrappa, M. V., and Raj, K. (2020). A study on the effect of PVDF on the structural and transport properties of polyaniline. Int. J. Polym. Analysis Charact. 25, 176–187. doi:10.1080/1023666x.2020.1779431
Karan, S. K., Bera, R., Paria, S., Das, A. K., Maiti, S., Maitra, A., et al. (2016). An approach to design highly durable piezoelectric nanogenerator based on self-poled PVDF/AlO-rGO flexible nanocomposite with high power density and energy conversion efficiency. Adv. Energy Mater. 6, 1601016. doi:10.1002/aenm.201601016
Khalifa, M., and Anandhan, S. (2019). PVDF nanofibers with embedded polyaniline-graphitic carbon nitride nanosheet composites for piezoelectric energy conversion. ACS Appl. Nano Mater. 2, 7328–7339. doi:10.1021/acsanm.9b01812
Koc, M., Donmez, C. E. D., Paralı, L., Ali Sarı, A., and Akturk, S. (2022). Piezoelectric and magnetoelectric evaluations on PVDF/CoFe2O4 based flexible nanogenerators for energy harvesting applications. J. Mater Sci. Mater Electron 33, 8048–8064. doi:10.1007/s10854-022-07956-w
Lei, D., Hu, N., Wu, L., Ning, H., Wang, Y., Jin, Z., et al. (2024). Improvement of the piezoelectricity of PVDF-HFP by CoFe2O4 nanoparticles. Nano Mater. Sci. 6, 201–210. doi:10.1016/j.nanoms.2023.03.002
Lin, Z.-H., Yang, Y., Wu, J. M., Liu, Y., Zhang, F., and Wang, Z. L. (2012). BaTiO3 nanotubes-based flexible and transparent nanogenerators. J. Phys. Chem. Lett. 3, 3599–3604. doi:10.1021/jz301805f
Mahapatra, S. D., Mohapatra, P. C., Aria, A. I., Christie, G., Mishra, Y. K., Hofmann, S., et al. (2021). Piezoelectric materials for energy harvesting and sensing applications: roadmap for future smart materials. Adv. Sci. 8, 2100864. doi:10.1002/advs.202100864
Maity, K., Garain, S., Henkel, K., Schmeißer, D., and Mandal, D. (2018). Natural sugar assisted chemically reinforced highly durable piezo-organic nanogenerator with superior power density for self-powered wearable electronics. ACS Appl. Mater. and Interfaces 50, 44018–44032. doi:10.1021/acsami.8b15320
Mao, Y., Zhao, P., McConohy, G., Yang, H., Tong, Y., and Wang, X. (2014). Sponge-like piezoelectric polymer films for scalable and integratable nanogenerators and self-powered electronic systems. Adv. Energy Mater. 4, 1301624. doi:10.1002/aenm.201301624
Martín, J., Zhao, D., Lenz, T., Katsouras, I., de Leeuw, D. M., and Stingelin, N. (2017). Solid-state-processing of δ-PVDF. Mater. Horizons 4, 408–414. doi:10.1039/c7mh00007c
Martins, P., Lopes, A. C., and Lanceros-Mendez, S. (2014). Electroactive phases of poly(vinylidene fluoride): determination, processing and applications. Prog. Polym. Sci. 39, 683–706. doi:10.1016/j.progpolymsci.2013.07.006
Mishra, H. K., Gupta, V., Roy, K., Babu, A., Kumar, A., and Mandal, D. (2022). Revisiting of δ−PVDF nanoparticles via phase separation with giant piezoelectric response for the realization of self-powered biomedical sensors. Nano Energy 95, 107052. doi:10.1016/j.nanoen.2022.107052
Mokhtari, F., Shamshirsaz, M., Latifi, M., and Foroughi, J. (2020). Nanofibers-based piezoelectric energy harvester for self-powered wearable technologies. Polymers 12, 2697. doi:10.3390/polym12112697
Nalwa, H. S., and Dekker, M. (1995). Ferroelectric polymers. New York, 183–232. doi:10.1201/9781482295450
Neese, B., Wang, Y., Chu, B., Ren, K., Liu, S., Zhang, Q. M., et al. (2007). Piezoelectric responses in poly(vinylidene fluoride/hexafluoropropylene) copolymers. Appl. Phys. Lett. 90, 242917. doi:10.1063/1.2748076
Ongun, M. Z., Paralı, L., Oğuzlar, S., and Pechousek, J. (2020). Characterization of β-PVDF-based nanogenerators along with Fe2O3 NPs for piezoelectric energy harvesting. J. Mater. Sci. Mater. Electron. 31, 9146–19158. doi:10.1007/s10854-020-04451-y
Parangusan, H., Bhadra, J., and Al-Thani, N. (2021). Flexible piezoelectric nanogenerator based on [P(VDF-HFP)]/PANI-ZnS electrospun nanofibers for electrical energy harvesting. Mater. Electron. 32, 6358–6368. doi:10.1007/s10854-021-05352-4
Saïdi, S., Bouzitoun, M., Mannaî, A., Gmati, F., Derouiche, H., and Mohamed, A. B. (2013). Effect of PANI rate percentage on morphology, structure and charge transport mechanism in PANI–PVDF composites above percolation threshold. J. Phys. D Appl. Phys. 46, 355101. doi:10.1088/0022-3727/46/35/355101
Saxena, P., and Shukla, P. (2021). A comprehensive review on fundamental properties and applications of poly(vinylidene fluoride) (PVDF). Adv. Compos. Hybrid Mater. 4, 8–26. doi:10.1007/s42114-021-00217-0
Shin, S.-H., Kim, Y.-H., Lee, M. H., Jung, J.-Y., Seol, J. H., and Nah, J. (2014). Lithium-doped zinc oxide nanowires–polymer composite for high performance flexible piezoelectric nanogenerator. ACS Nano 8, 10844–10850. doi:10.1021/nn5046568
Singh, H. H., Singh, S., and Khare, N. (2017). Enhanced β -phase in PVDF polymer nanocomposite and its application for nanogenerator. Polym. Adv. Technol. 29, 143–150. doi:10.1002/pat.4096
Sk, A., Adhikary, P., and Haldar, P. K. (2022). Nucleation of electro-active β and γ -phases in P(VDF−HFP) for manufacturing energy harvesting device and self powered weight measuring device. Polym. Eng. Sci. 62, 3858–3867. doi:10.1002/pen.26152
Thakur, P., Kool, A., Bagchi, B., Das, S., and Nandy, P. (2015). Effect of in situ synthesized Fe2O3 and Co3O4 nanoparticles on electroactive β phase crystallization and dielectric properties of poly(vinylidene fluoride) thin films. Phys. Chem. Chem. Phys. 17, 1368–1378. doi:10.1039/c4cp04006f
Tohluebaji, N., Thainiramit, P., Putson, C., and Muensit, N. (2021). Phase and structure behavior vs. Electromechanical performance of electrostrictive P(VDF-HFP)/ZnO composite nanofibers. Polymers 13, 2565. doi:10.3390/polym13152565
Wang, Z. L. (2017). On Maxwell’s displacement current for energy and sensors: the origin of nanogenerators. Mater. Today 20, 74–82. doi:10.1016/j.mattod.2016.12.001
Wang, Z. L., and Song, J. (2006). Piezoelectric nanogenerators based on zinc oxide nanowire arrays. Science 312, 242–246. doi:10.1126/science.1124005
Wu, L., Huang, G., Hu, N., Fu, S., Qiu, J., Wang, Z., et al. (2014a). Improvement of the piezoelectric properties of PVDF-HFP using AgNWs. RSC Adv. 4, 35896–35903. doi:10.1039/c4ra03382e
Wu, L., Jin, Z., Liu, Y., Ning, H., Liu, X., Alamusi and Hu, N., et al. (2022). Recent advances in the preparation of PVDF-based piezoelectric materials. Nanotechnol. Rev. 11, 1386–1407. doi:10.1515/ntrev-2022-0082
Wu, L., Yuan, W., Hu, N., Wang, Z., Chen, C., Qiu, J., et al. (2014b). Improved piezoelectricity of PVDF-HFP/carbon black composite films. J. Phys. D Appl. Phys. 47, 135302. doi:10.1088/0022-3727/47/13/135302
Yang, Y., Zhang, H., Zhu, G., Lee, S., Lin, Z.-H., and Wang, Z. L. (2012). Flexible hybrid energy cell for simultaneously harvesting thermal, mechanical, and solar energies. ACS Nano 7, 785–790. doi:10.1021/nn305247x
Yempally, S., Patricia Magadia, P., and Ponnamma, D. (2023). Effect of Zn–Fe2O3 nanomaterials on the phase separated morphologies of polyvinylidene fluoride piezoelectric nanogenerators. RSC Adv. 13, 33863–33874. doi:10.1039/D3RA03745B
Yu, H., Huang, T., Lu, M., Mao, M., Zhang, Q., and Wang, H. (2013). Enhanced power output of an electrospun PVDF/MWCNTs-based nanogenerator by tuning its conductivity. Nanotechnology 24, 405401. doi:10.1088/0957-4484/24/40/405401
Yu, S., Zhang, Y., Yu, Z., Zheng, J., Wang, Y., and Zhou, H. (2021). PANI/PVDF-TrFE porous aerogel bulk piezoelectric and triboelectric hybrid nanogenerator based on in-situ doping and liquid nitrogen quenching. Nano Energy 80, 105519. doi:10.1016/j.nanoen.2020.105519
Zhao, Y., Liao, Q., Zhang, G., Zhang, Z., Liang, Q., Liao, X., et al. (2015). High output piezoelectric nanocomposite generators composed of oriented BaTiO3 NPs@PVDF. Nano Energy 11, 719–727. doi:10.1016/j.nanoen.2014.11.061
Keywords: β-phase, piezoelectricity, P(VDF-HFP), Fe2O3, PANI
Citation: Barman PS, Biswas A, Ali S, Roy D, Roy MN, Garain S and Adhikary P (2025) Flexible piezoelectric energy harvester based on self-poled electroactive P(VDF-HFP)/(Fe2O3–PANI) composite film. Front. Energy Res. 13:1570397. doi: 10.3389/fenrg.2025.1570397
Received: 03 February 2025; Accepted: 27 May 2025;
Published: 02 July 2025.
Edited by:
Hulin Zhang, Taiyuan University of Technology, ChinaReviewed by:
Lei Sun, Taiyuan University of Technology, ChinaSaeed Ahmed Khan, Sukkur IBA University, Pakistan
Copyright © 2025 Barman, Biswas, Ali, Roy, Roy, Garain and Adhikary. This is an open-access article distributed under the terms of the Creative Commons Attribution License (CC BY). The use, distribution or reproduction in other forums is permitted, provided the original author(s) and the copyright owner(s) are credited and that the original publication in this journal is cited, in accordance with accepted academic practice. No use, distribution or reproduction is permitted which does not comply with these terms.
*Correspondence: Prakriti Adhikary, cHJha3JpdGlAbmJ1LmFjLmlu; Samiran Garain, c2FtaXJhbmdhcmFpbkBnbWFpbC5jb20=