- 1China Communications Third Shipping Engineering Bureau Co., Ltd., Shanghai, China
- 2Ninth Engineering Company, CCCC Third Harbor Engineering Co., Ltd., Shanghai, China
- 3Ccid Urban Construction (Chongqing) Co. Ltd., Chongqing, China
- 4School of Civil Engineering, Wuhan University, Wuhan, Hubei, China
Foundation pit engineering usually encounters the problems of foundation reinforcement and mud soil (MS) disposal. This study proposes a solidification technology utilizing blast furnace slag (BFS)-MS based geopolymer, enhanced by renewable plant fibers, to achieve resource utilization of MS. The key parameters including activator modulus, alkali content, water-to-solid ratio, and MS replacement rate were systematically optimized through orthogonal experimental design. Based on considering the mechanical properties and economy, the pretreated wood (WF), jute (JF) and bamboo (BF) fibers were incorporated respectively to study the influence of plant fiber type and content on the mechanical properties of geopolymer. The results demonstrated that the optimal parameters for BFS-MS precursors were activator modulus 1.7 and alkali content 0.2. The BFS-MS geopolymer under the optimal ratio of 28 days can reach 43.56 MPa, maintaining excellent potential for engineering application even at 30% MS replacement. At 1.0% dosage, WF, JF and BF enhanced the 28-day compressive strength by 27.80%, 12.35% and 29.05% respectively. The microstructural analysis revealed that geopolymer gels derived from BFS hydration dominated early strength development, while potentially active minerals in MS contributed to later stage strength enhancement. This study provides theoretical and technical foundations for MS utilization and fiber-reinforced geopolymer design in sustainable construction practices.
1 Introduction
The disposal and resource utilization of MS remain persistent challenges in deep foundation pit engineering, dredging projects, and related fields. The conventional approaches are mainly landfill or dewatering and drying, which have bottlenecks such as land resource occupation, secondary pollution risk and high carbon emission (Jia et al., 2024; Zhao et al., 2024; Wang and Hao, 2024). In current stabilization practices, MS is predominantly used as an inert filler blended with cement or lime, functioning as a physical additive rather than a chemically active component (Cao et al., 2024). This results in suboptimal material utilization and compromised long-term stability of solidified matrices (Wang Q. et al., 2024). Although emerging techniques like chemical modification and bio-cementation have partially improved the mechanical properties of MS-based materials, they still face issues such as low stabilization efficiency, high costs, and poor environmental compatibility (Wei et al., 2023; Cui et al., 2022; James, 2020). Notably, MS contains abundant silicates and aluminates, demonstrating potential as a geopolymer precursor. By activating its inherent reactivity, MS can transform into the primary cementitious phase rather than merely serving as a passive reinforcement. This enables its conversion from waste material to active cementitious component (Zhang et al., 2024; Nematollahi et al., 2017; Davidovits, 1991).
Geopolymer technology has long attracted attention for its low-carbon characteristics and resource recovery potential for silica-alumina-rich wastes. Its fundamental mechanism involves alkaline activation of Si and Al-rich precursors to develop substantial strength (Davidovits, 1989; Wang et al., 2005). Under optimal alkaline conditions, Si and Al minerals in MS undergo depolymerization to form siloxane and aluminate units, which subsequently polymerize into cementitious materials with good mechanical properties (Van-Jaarsveld et al., 1997; Gluk and hovsky, 1965; Almutairi et al., 2021). Zhang et al. (Zhang et al., 2023a) achieved a maximum UCS of 1.88 MPa for MS-based geopolymers using straw ash and sodium silicate as composite activators. Similarly, Kong et al. (Kong et al., 2023) reported a 28 days strength of 4.29 MPa through co-stabilization of MS with MgO and industrial slag. Conventional alkaline activation methods are difficult to significantly enhance MS’s mechanical performance due to its “calcium-deficient” nature and high content of inert components formed by precipitation (Mikhailova et al., 2019). Lu et al. (2022) demonstrated synergistic alkali-thermal activation of MS, achieving 7 days and 28 days strengths of 8.93 MPa and 16.37 MPa, respectively. While effective, this method incurs substantial costs, highlighting the need to introduce calcium-rich precursors like blast furnace slag to supplement early -stage strength development in MS based geopolymers (Zhang et al., 2022). Lv et al. (2022) developed loess-slag geopolymer composites (LSGC) using loess and slag as precursors. Their results showed that at the optimal 1:1 ratio, the LSGC exhibited satisfactory workability and setting time, achieving a 28-day UCS of approximately 14.61 MPa with a dense and stable microstructure.
In the study of multifactor effects on geopolymer properties, orthogonal experimental design (OED) can identify key influencing factors and their optimal combinations effectively through partial implementation strategies, significantly improving experimental efficiency (Wang Y. et al., 2024; Cai et al., 2023). Chen et al. (2025) conducted a three-factor, four-level L16 (43) OED study and found that a drainage sludge replacement rate of 30%, sodium silicate modulus of 1, and liquid-solid ratio of 0.3 yielded the highest 28-day compressive strength (6.78 MPa) for geopolymer containing drainage sludge, fly ash, and coal gangue. Similarly, Li et al. (2024a) conducted a three-factor L9 (33) orthogonal experiment examining alkali equivalent, Si/Al ratio, and hot-pressed curing time. Their results demonstrated that alkali equivalent had the greatest impact on the compressive strength of hot-pressed metakaolin-fly ash based geopolymers. Within the 4-8 wt% alkali equivalent range, the maximum difference in 28-day compressive strength reached 190.72 MPa. Concurrently, fiber-modified construction mateials have seen considerable advancement. Zhong et al. (2024) enhanced the 28 days compressive strength of lithium slag-based geopolymer by 14.9% through 0.1% incorporation of carboxylated multi-walled carbon nanotubes. Chen et al. (2018) reported 39.4% and 32.3% improvements in flexural strength for metakaolin-based geopolymers using 5 wt% polyacrylic emulsion or 0.2 v/v% polypropylene fiber, respectively. As renewable reinforcements, plant fibers have gained traction in green construction materials due to their low density, high specific strength, and carbon neutrality. Their cellulose microfibril structures effectively enhance composite toughness and suppress crack propagation (Withana et al., 2024; Di Sarno et al., 2024; Zainal et al., 2024). However, research on plant fibers in geopolymer systems remains nascent, necessitating systematic studies to elucidate their impact on mechanical performance and underlying mechanisms (Kuqo et al., 2023a; Yang et al., 2023).
This study proposes an in-situ MS stabilization technology based on a BFS-MS geopolymer system. The key parameters such as activator modulus, alkali content, water-to-solid ratio and MS replacement rate were optimized by orthogonal experiments. On the basis of considering the mechanical properties and economy, different types of plant fibers were added to the slag-mud soil based geopolymer to study the influence of plant fiber type and content on its mechanical properties, and to study the internal mechanism of its mechanical properties evolution. The findings aim to advance the resource utilization of MS and plant fibers in sustainable construction materials.
2 Experimental
2.1 Materials
2.1.1 Mud soil (MS)
The mud soil used in this study was taken from the bottom soil of a deep foundation pit project in Hangzhou, Zhejiang Province, China, as shown in Figure 1. The organic matter pollution of the MS was light, and there was no obvious odor after air drying. A series of tests determined the basic properties of MS: specific gravity of approximately 2.68, initial moisture content ranging from 25% to 65%, plastic limit of 25.3%, and liquid limit of 45.6%. The MS of the foundation pit engineering project is naturally dried and condensed, and the block is large. Firstly, it is preliminarily crushed, then it is ground by vibrating mill, and finally screened by 200 mesh (0.074 mm) sieve. The MS treated by the above process can be used for raw material property test and sample preparation.
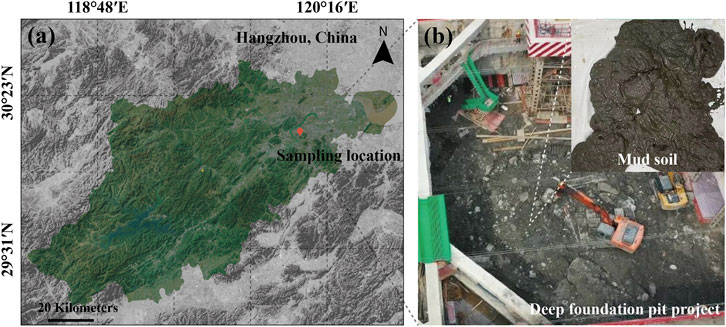
Figure 1. Sampling location and morphology of mud soil. (a) Engineering location; (b) Sampling and morphology of mud soil.
The XRF test results of MS are shown in Table 1, indicating the weight percentage of each element. It is showed that both BFS and MS contain many potential active components, such as SiO2 and Al2O3. The LOI refers to the loss of ignition, which means that the MS that loses free water after drying continues to burn for a long enough time under certain high temperature conditions, and the mass lost in this process accounts for the percentage of the original sample mass. The micro-morphology of MS is shown in Figure 2A, which is rod-like or granular.
2.1.2 Blast furnace slag (BFS)
Blast furnace slag (BFS) is a molten material with silicate and aluminosilicate as the main components after quenching and granulation when smelting pig iron in the blast furnace. The BFS was provided by a mineral product processing plant in Hebei Province, China. It is an S105 grade mineral powder. This gray powder has a specific surface area of 480 m2/kg, a density of 3.1 g/cm3, and a loss on ignition of 0.84%. The chemical composition (in the form of oxides of each element) of the BFS was analyzed using an X-ray fluorescence (XRF) analyzer (ZETIUM, PANalytica B.V., Netherlands), and the results are shown in Table 2. Figure 2B is the apparent and micro-morphology of BFS, which can be seen as irregular flake or granular, and most of the particle size range is below 10 μm.
2.1.3 Sodium silicate-sodium hydroxide type activator (SS)
The activator used in this study was a mixture of sodium silicate and sodium hydroxide. Sodium silicate and sodium hydroxide are provided by Myrel Chemical Technology Co., Ltd, Shanghai, China. Sodium silicate is a white powder solid with a modulus of two and a purity of 99.7%. Sodium hydroxide is a white granular solid with a purity of 99.7%.
Modulus is one of the important parameters of the SS, which refers to the value of n in the general formula of sodium silicate Na2O·nSiO2. The smaller the value of n, the stronger the alkalinity of the SS, and the higher the solubility in water. In order to configure the SS with specified modulus, the mass of sodium hydroxide added to sodium silicate with a modulus of two can be calculated according to Formula 1:
Where, m(NaOH) is the amount of sodium hydroxide, g; c is the modulus of the SS; x is the modulus of the sodium silicate; Ar(A) is the relative molecular mass of substance A.
2.1.4 Plant fibers (PF)
Wood fiber (WF), as shown in Figure 3a, 40–80 mesh, 1–3 mm in length, 2.1–2.3% in elongation at break, self-processed, produced from a wood market in Hangzhou, China.
Jute fiber (JF), as shown in Figure 3b, 30–50 mesh, length of 1–3 mm, elongation at break of 2.7–3.1%, self-processed, produced from a hemp product Co., Ltd. in Wuhan, China.
Bamboo fiber (BF), as shown in Figure 3c, 30–50 mesh, length of 1–3 mm, elongation at break of 3.5–3.8%, self-processed, produced from a wood market in Hangzhou, China.
Each plant fiber was dried to absolute dryness and sealed at 103°C ± 2°C.
2.2 Experimental design and sample preparation
The mechanical properties of slag-mud soil (BFS-MS) geopolymers are critically influenced by four compositional parameters: the modulus of SS, the SS alkali content (expressed as m (Na2O)/m (H2O) ratio), the water-solid ratio (the mass ratio of water to total solid precursors), and mud soil replacement rate (expressed as m (MS)/m (BFS + MS) ratio). Specifically, the first two factors are related to the composition and dosage of SS. They directly determine the alkalinity of the reaction system and the amount of reactive silica introduced. Since SS is a high-energy-consumption and high-cost raw material, its parameter selection significantly affects the economic feasibility of BFS-MS based geopolymers. The water-solid ratio is closely linked to the workability during preparation and the final material performance. Different application scenarios may require different values for this parameter. The mud soil replacement rate is the key focus of this study. It directly influences both the utilization efficiency of MS waste and the balance of material properties. In this study, these variables were systematically optimized using an orthogonal experimental design (OED) to establish performance-composition relationships. On the basis of considering the mechanical properties and economy, different types of plant fibers (wood, jute, bamboo) were added to the slag-mud soil based geopolymer to study the influence of plant fiber type and content on its mechanical properties, and to study the underlying mechanism of its mechanical properties evolution.
2.2.1 Composition design and preparation of slag-mud soil based geopolymers
The characteristic of the OED method is to use the orthogonal table to scientifically arrange the experiment, select the representative points with the characteristics of “uniform dispersion, neat and comparable” for the experiment (Yuan et al., 2022). Its advantage is that it can systematically consider multiple factors and their interactions to ensure the comprehensiveness and reliability of the test results. At the same time, it has economic efficiency by greatly reducing the number of tests, improving test efficiency, and reducing time and cost (Luo et al., 2022).
In this study, the modulus of the SS, the alkali content of SS, the water-solid ratio, the mud soil replacement rate were selected as four factors of orthogonal design. The range and step length of each factor are selected on the basis of reference to relevant literature (Lu et al., 2022; Lin et al., 2025; Kina et al., 2025). Specifically, the modulus of the SS (factor A) ranges from 1.3 to 1.9, and the step length is increased by 0.2. The alkali content of SS (factor B) ranges from 0.15 to 0.30, and the step length is increased by 0.05. The water-solid ratio (factor C) ranges from 0.3 to 0.6, and the step length is increased by 0.1. Additionally, the range of the mud soil replacement rate in this study was determined based on the activity index of the solid waste raw materials. According to the Ground granulated blast furnace slag used for cement, mortar, and concrete standard (GB18046-2017) (National Cement Standardization Technical Committee 2017), the 7-day activity index of BFS was measured as 88%, while that of MS was 45%. This indicates that the activity of MS is significantly lower than that of BFS. In the precursor composed of MS and BFS, an excessive proportion of MS would lead to insufficient material performance. Therefore, the mud soil replacement rate was selected within the range of 0–0.45, with an increment step of 0.15. The experimental design of four factors and four levels is shown in Table 3. The quantities of all other materials were calculated and recorded in the table, using 1,000 g of solid waste precursor as the baseline reference.
The preparation process of the slag-mud soil based geopolymer is illustrated in Figure 4, consisting of three key steps. First, precisely weighed MS powder was uniformly blended with BFS to form the solid precursor (SP). The SS solution was then prepared by mixing sodium silicate-sodium hydroxide type activator with the required amount of water. Finally, the SP was combined with the SS solution and thoroughly mixed to form a relatively homogeneous slurry. This slurry was cast into 20 × 20 × 20 mm molds, vibrated for compaction, and cured at 20°C ± 2°C with 65%–70% relative humidity. As described in Section 2.1, all precursor materials particle sizes including MS and BFS were below 75 μm. It ensured sample homogeneity, minimizing potential size effects on mechanical property measurements - a well-established approach frequently reported in literature (Brustolin et al., 2024; Li et al., 2024b). After 24 h of room temperature curing, the demolded samples were aged to target test periods for subsequent macro- and micro-scale characterization.
2.2.2 Preparation of plant fiber modified geopolymers
On the basis of comprehensive consideration of the mechanical properties and economy of slag-mud soil based geopolymer, different types of plant fibers were added to study the influence of fiber type and content on its mechanical properties. The fiber modification protocol comprised two stages: 1) Fiber pretreatment: Raw fibers were immersed in 5 wt% NaOH solution at 60°C for 2 h to remove hemicellulose, followed by rinsing to neutrality, oven-drying at 80°C for 24 h, and mechanical cutting into 1–3 mm segments, which were then stored in sealed containers; 2) Composite fabrication: Pretreated fibers were homogenously blended with the SP (BFS-MS mixture), followed by alkali activation and molding as detailed in Section 2.2.1. Furthermore, existing studies indicate that excessive fiber content can lead to fiber clustering, void formation, and poor dispersion within the matrix (Yang et al., 2021). This results in reduced workability of the slurry, as well as decreased compressive strength and impact resistance. In contrast, a low fiber dosage (below 2%) demonstrates better reinforcement and toughening effects (Li et al., 2023; Yang et al., 2025; Hua et al., 2025). Therefore, this study prepared plant fibers modified geopolymer samples with fiber contents of 0.5 wt%, 1.0 wt%, and 1.5 wt%. It should be noted that unlike the 20 mm cubic samples used for MS-BFS geopolymers in Section 2.2.1, the plant fiber modified BFS-MS geopolymers required larger dimensions due to the 1–3 mm fiber length. To ensure sample homogeneity, cylindrical samples measuring 50 mm in diameter and 100 mm in height were adopted for all PF-modified geopolymer samples. Triplicate samples for each formulation were cured under standardized conditions to ensure reproducibility. The preparation workflow is schematically illustrated in Figure 4.
2.3 Testing method
2.3.1 Uniaxial compressive strength (UCS)
The uniaxial compression tests were conducted on solidified samples at 3, 7, and 28 curing days using a DW1210 universal testing machine (50 kN capacity) under strain-controlled loading (0.5 mm/min), following Common Portland Cement (GB 175–2023) standards (National Cement Standardization Technical Committee, 2023). The UCS was defined as the peak stress at sample failure (Hai-feng et al., 2022).
2.3.2 X-ray diffraction (XRD)
The phase composition analysis was performed using a PANalytical Xpert-Pro diffractometer (Cu-Kα radiation, λ = 1.5406 Å) with 2θ ranging 20°–60° at 5°/min (step size 0.02°). Powdered samples (<75 μm, 200-mesh) were prepared to ensure diffraction signal accuracy.
2.3.3 Scanning electron microscopy (SEM)
The microstructural characterization was carried out on a JEOL JSM-6501 SEM at 5 kV. The samples were gold-coated to enhance conductivity. Secondary electron imaging revealed surface morphology and fiber-matrix interactions (Zhang et al., 2023b).
3 Results and discussions
3.1 The UCS of the slag-mud soil based geopolymer
The uniaxial compressive strength results of slag-mud soil geopolymer samples are summarized in Table 3, with the temporal evolution of average UCS across groups illustrated in Figure 5.
The BFS-MS based geopolymer samples exhibited considerable early-age strength development. All sample groups achieved 3-day UCS values above 20 MPa, representing over 50% of their respective 28-day strengths. Notably, certain groups (SM1, SM6, SM8) demonstrated particularly rapid strength gain, attaining more than 80% of their 28-day UCS within 3 days, highlighting the material’s early-strength characteristics. These groups with faster early strength development consistently featured lower levels of Factor D, primarily attributable to the abundant reactive calcium sources in the BFS precursor that significantly accelerated geopolymerization. At 28 days, SM9 showed the highest UCS (42.02 MPa), while SM2 displayed the lowest (31.34 MPa). However, these samples did not consistently maintain maximum or minimum strength values across all curing ages, indicating that the influence of factor levels on UCS varies with curing time. This age-dependent behavior necessitates further examination through orthogonal analysis (Wang Y. et al., 2024; Alameri et al., 2025).
3.2 Range analysis
Range analysis was performed on the unconfined compressive strength results of slag-mud soil based geopolymers using orthogonal design methodology. The calculation procedure involved two key parameters: ki and R. The complete statistical results are presented in Table 4. In which, Ki represents the summation of UCS values when the factor is set at level i, where the average value ki reflects the systematic variation induced by adjusting the factor level. The range parameter R, defined as the difference between maximum and minimum ki values, quantitatively indicates the sensitivity of UCS to each individual factor.
Through this analytical approach, the relative importance of different factors affecting geopolymer strength could be systematically evaluated. Larger R values correspond to greater influence on the mechanical properties, allowing clear identification of dominant and secondary controlling factors (Zhang et al., 2024). Taking the UCS of 3 days as an example, the R-value analysis revealed the following significance ranking of influencing factors: D (mud soil replacement rate) > A (SS modulus) > C (water-solid ratio) > B(SS alkali content). This demonstrates that factor D exerted the most important influence on the early strength development of slag-mud soil based geopolymers, while factor B showed the least impact. Furthermore, the results in Table 4 reveal non-monotonic relationships between factors and performance metrics. Taking the SS modulus (Factor A) as an example: within the tested range, the UCS of 3 days initially increased with rising SS modulus up to 1.5, beyond which further modulus increases resulted in gradual strength reduction. To better illustrate the influence of each factor level on the target value, Figures 6a–d graphically shows the variation trends of average UCS with respect to different level settings for each experimental factor. The theoretically optimal combination was obtained by selecting the peak performance level for each factor. For the UCS of 3 days, this corresponded to the A2(SS modulus)-B2(SS alkali content)-C4(water-solid ratio)-D1 (mud soil replacement rate) parameter set. The significance ranking of each factor’s influence on the experimental objectives and their optimal combinations were determined through ki and R analysis, with all results presented in Table 4.
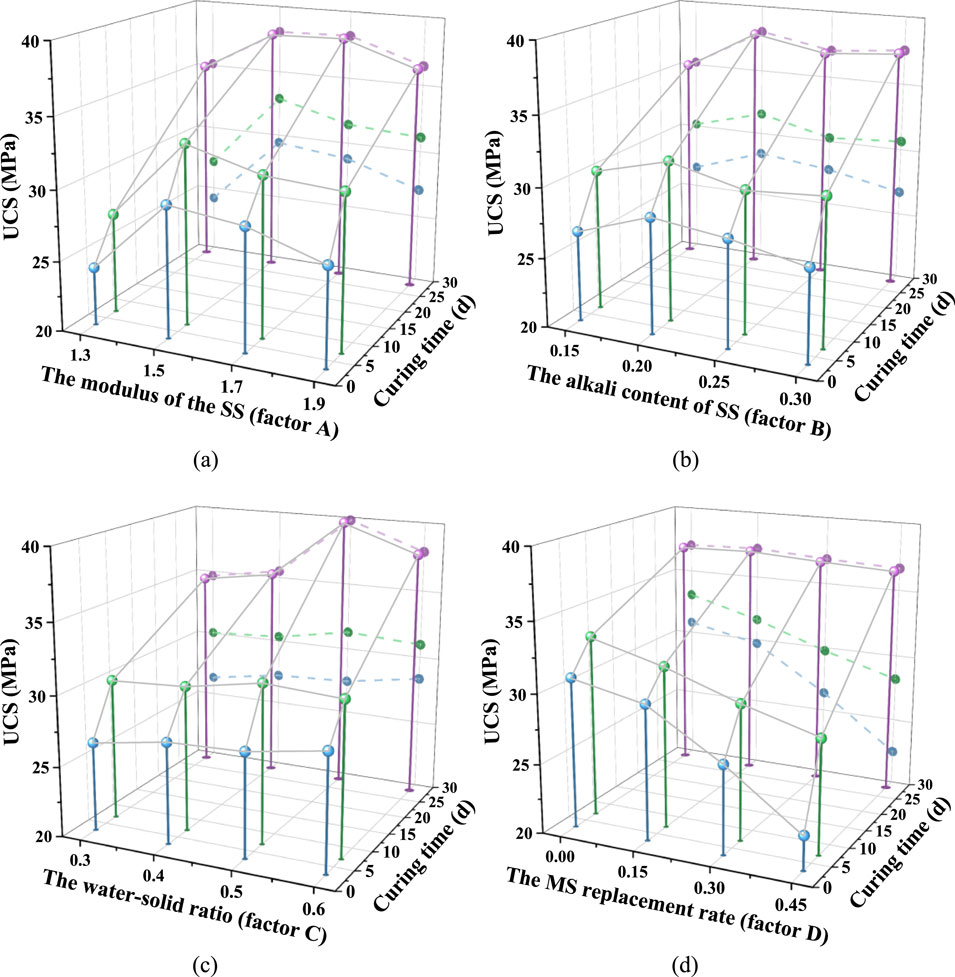
Figure 6. The effect trend of each factor on the UCS of the slag-mud soil based geopolymer samples. (a) Effect trend of factor A on UCS; (b) Effect trend of factor B on UCS; (c) Effect trend of factor C on UCS; (d) Effect trend of factor D on UCS.
For Factor A (SS modulus), the UCS of samples at different curing ages exhibited a consistent trend of initial increase followed by decrease as the modulus increased. The optimal SS modulus was 1.5 for maximum 3-day and 7-day strength, while 1.7 produced the highest 28-day strength. When the SS modulus was below the optimal value, the alkali activator provided insufficient reactive silicate oxide monomers, potentially leading to incomplete polycondensation reactions (Cui et al., 2017). This resulted in reduced mechanical properties of the samples. As shown in Figure 6b, the lower SS modulus significantly decreased sample strength, and this weakening effect persisted throughout the curing period. Conversely, when the SS modulus increased beyond the optimal value, the alkalinity of the solution system decreased significantly. This reduction in alkalinity slowed both the precursor dissolution and geopolymerization reaction rates (Zhao et al., 2022). As illustrated in Figure 6a, elevated SS modulus values exhibited a more pronounced effect on the early-age UCS of the samples. However, the negative impact of excessively high SS modulus gradually diminished with prolonged curing duration.
For Factor B (SS alkali content), the optimal value for maximum strength at all curing ages was consistently 0.20 within the studied range. When the alkali content fell below this value, both alkalinity and silicate oxide monomer concentration in the reaction system decreased significantly, leading to reduced UCS across all curing ages (Zhang et al., 2022). However, increasing the alkali content beyond 0.20 resulted in strength reduction. This may be attributed to excessive alkali causing detrimental effects such as efflorescence, which was observed during testing.
For Factor C (water-solid ratio), the optimal values varied with curing age within the studied range. The 3-day strength peaked at a water-solid ratio of 0.6, while the highest 7-day and 28-day strengths occurred at 0.5. During early reactions, higher water-solid ratios reduced solution viscosity, facilitating ion exchange and enhancing strength development (Davidovits, 1991). However, in later curing stages, excess water caused detrimental effects including significant drying shrinkage stress, ultimately reducing the final strength (Mikhailova et al., 2019).
For Factor D (mud soil replacement rate), the range analysis showed that sample strength approximately decreased as the MS replacement rate increased across all curing ages. Within the studied range, the optimal replacement rate was 0 for maximum 3-day and 7-day strength, while 0.15 yielded the highest 28-day strength. Figure 6d revealed that the MS replacement rate significantly affected early-age strength. A 0.45 replacement rate reduced 3-day strength to 72.9% of the reference value, though this recovered to 98.9% by 28 days. This improvement suggests that mud soil actively participated in geopolymerization during later curing stages, contributing to strength development. Moreover, when the MS replacement rate was 0.3, the sample achieved 85.7%, 90.0%, and 99.5% of the original strength at 3, 7, and 28 days respectively. This formulation maintains satisfactory mechanical performance across all curing ages while significantly reducing material costs, demonstrating excellent potential for engineering applications.
The UCS variation is presented in Figure 7. Based on the R-value analysis, the significance ranking of each factor’s influence on the target property was determined as shown in Table 4. The range analysis revealed that the optimal composition for achieving maximum 28-day UCS consists of: SS modulus of 1.7, SS alkali content of 0.2, water-solid ratio of 0.5, and MS replacement rate of 0.15. A verification test confirmed this optimized formulation yielded a UCS of 43.56 MPa, demonstrating good agreement with the predicted results. This optimal combination balances multiple competing factors: sufficient alkalinity for activation, appropriate viscosity for workability, and adequate reactive components for geopolymer formation. The experimental validation confirms the reliability of the orthogonal design approach for slag-MS based geopolymer optimization.
3.3 Variance analysis
In orthogonal experimental design, the observed variations in UCS may result from either controlled factor-level changes or uncontrolled experimental errors. While range analysis effectively identifies influential factors, it cannot statistically separate these effects from random experimental variations. Analysis of variance provides a more rigorous approach, enabling quantitative evaluation of each factor’s significance through F-tests. This method distinguishes systematic factor effects from random noise, offering greater reliability for optimization decisions (Nguyễ et al., 2023). The variance analysis results contain key parameters of the orthogonal experimental system: the sum of squares Sk, mean square value Vk, degrees of freedom f, and F-value Fk. A higher Fk value indicates greater significance of the corresponding factor. The complete variance analysis results are provided in Table 5.
It is found that the mud soil replacement rate has the most significant effect on the UCS of slag-mud soil based geopolymer samples, especially during the early stage of curing (≤7 days). Moreover, the effects of the mud soil replacement rate and the modulus of the SS on the UCS of the samples decreased with the age of curing. The effect of the water-solid ratio increases with the age of curing.
3.4 Effect of plant fiber on UCS of geopolymer
According to the results of orthogonal test, the slag-mud soil based geopolymer was selected for plant fiber modification under the following parameters: the modulus of the SS is 1.7, the alkali content of SS is 0.2, the water-solid ratio is 0.5 and the MS replacement rate is 0.30. The purpose of this choice is to use SS as little as possible to obtain the most significant economic benefits, while maintaining a high UCS to consume and utilize MS as much as possible. As a control group, the slag-mud soil based geopolymer without any plant fiber was prepared under this parameter. The UCS results are shown in Table 6. The UCS of fiber-modified geopolymer samples and their increments as shown in Figure 8.
The optimal reinforcement effect was observed for WF and BF at fiber contents of 1.0%–1.5%, with particularly significant early strength enhancement. The maximum UCS increase reached 48.23% at 3 days for WF modified geopolymers and 48.36% for BF modified counterparts. This enhancement mechanism can be attributed to two primary factors: 1) The smooth surface morphology of WF and BF facilitated uniform dispersion within the matrix, enabling effective crack bridging and load transfer; 2) Alkali treatment exposed cellulose hydroxyl groups, which formed strong hydrogen bonds with the geopolymer’s Si-Al network, promoting pore filling and significantly improving early strength (Fioroni et al., 2025). In contrast, the rough surface of JF fibers tended to induce agglomeration, creating stress concentration points under loading (Kuqo et al., 2023b). JF modified samples exhibited a distinct threshold effect: at 0.5% content, 28 days UCS decreased by 7.88%, while at 1.0% content, UCS increased by 12.35%, followed by a sharp decline to 4.73% at 1.5% content. Furthermore, existing studies confirm that JF provides limited enhancement or even negatively affects performance (Yang et al., 2021). Korniejenko et al. (Korniejenko et al., 2018) observed that 1% coconut fiber content yielded a 26.55% improvement in 28-day compressive strength for geopolymers, which is slightly lower than the enhancements achieved by both WF and BF in our study, with cotton fibers showing even more modest gains.
In addition, the reinforcement efficiency of all fiber types diminished with prolonged curing, with 28 days UCS increases generally falling below 30%. This phenomenon stems from two mechanisms. On the one hand, with the increase of age, the strength of geopolymer matrix tends to be stable. At this time, the relative enhancement efficiency of plant fiber decreases. On the other hand, Prolonged exposure to the alkaline environment induces cellulose depolymerization in plant fibers, accompanied by interfacial debonding and cracking, leading to reduced late-age strength enhancement (Glaus and Van Loon, 2008). Therefore, when selecting plant fibers for geopolymer modification, easily dispersible fibers such as WF and BF are recommended. An optimal fiber content of approximately 1.0% can provide effective reinforcement, particularly during the early stages of strength development.
3.5 XRD analysis
To investigate the strength origins of slag-mud soil-based geopolymer, XRD analysis was conducted on raw materials and SM 9 with the highest strength at 28 days in the orthogonal tests. Their XRD patterns are shown in Figure 9.
In MS, quartz and illite dominate as primary mineral components. The sharp and narrow peaks in the XRD pattern indicate well crystallized mineral phases, which is the result of long-term geological stabilization. Although exhibiting low reactivity, these minerals provide essential Si and Al components to the reaction system, contributing to the late-stage strength development of samples. For BFS, quartz, calcite, and mullite constitute the main mineral phases. The broad and low-intensity diffraction peaks in pattern suggest lower crystallinity and higher pozzolanic activity, which account for the early strength enhancement of samples. In SM 9, the XRD pattern demonstrates attenuated characteristic peaks of raw materials and the emergence of new phases. At about 29.06°, an amorphous dispersion peak appears, which is generally considered to be a mixed phase of geopolymer products C-S-H and C-(N)-A-S-H, and also a cementitious phase product that maintains the strength of the samples (Wang et al., 2023; Pan et al., 2018). The diffraction peaks of calcium carbonate were also observed in the samples, which may originate from the calcite in the raw materials and secondary hydration products. In addition, the Al2O3 peaks in SM-9 may originate from the decomposition products of clay minerals in MS (Zhang et al., 2024). These products also act as weak impurities filling the geopolymer samples, negatively affecting the sample’s integrity and load-bearing capacity.
3.6 SEM analysis
Figure 10 displays the micro-morphology of plant fiber-modified geopolymer with a 1.5% fiber dosage. While direct observation of the microscopic fiber pull-out process within the matrix remains challenging under SEM, the bonding characteristics between fibers and geopolymer matrix can be preliminarily assessed through morphological examination. Figure 10a clearly shows WF fibers pulled out from the geopolymer matrix, with matrix fragments adhering to their surfaces. In Figure 10b, fractured JF fibers are visible - their smooth surfaces remain partially embedded in the geopolymer matrix. Figure 10c displays the geopolymer matrix after BF fiber extraction, showing a flat interface with localized flaking phenomena. Based on the correlation between micro-features and macro-mechanical performance, the modification mechanisms of different plant fibers in geopolymers can be attributed to synergistic interactions between interfacial bonding characteristics and fiber structural properties. For WF (diameter <10 μm), the fine diameter and high specific surface area significantly enhance fiber-matrix contact. The surface-adhered C-(N)-A-S-H gel particles indicate chemical bonding or mechanical interlocking with the geopolymer matrix, enabling effective stress transfer and crack suppression. This mechanism explains its superior compressive strength improvement (36.74% increase at 1.5% dosage in 28 days). In contrast, JF (diameter >50 μm) exhibits performance deterioration due to dual factors. On the one hand, the large fibers act as stress concentrators (Zhao et al., 2025), inducing interfacial debonding (crack width >5 μm). On the other hand, the high cellulose content promotes self-degradation and interfacial weakening in alkaline environments (Suyam et al., 2024), resulting in attenuated strength gain or even negative growth (−7.88% increase at 0.5% dosage in 28 days). BF, with intermediate diameter between WF and JF, shows limited reinforcement efficiency due to its smooth surface restricting mechanical anchoring. When exceeding 1.0% dosage, BF accumulation increases localized porosity, leading to reduced strength enhancement.
This analysis elucidates the mechanisms of plant fiber-modified geopolymers and provides optimized dosage recommendations. However, two critical technical challenges require further investigation: 1) improving alkali resistance of plant fibers through surface modification or hybrid treatments, and 2) developing graded-size dosage processes to enhance reinforcement efficiency while mitigating pore formation. Addressing these aspects will advance the practical application of plant fibers in sustainable geopolymer reinforcement technologies.
4 Conclusion
The resource utilization of MS is a topic that has been neglected for a long time. This study proposes an in situ MS stabilization technology based on a BFS-MS geopolymer system, with key parameters—activator modulus, alkali content, water-to-solid ratio, and MS replacement rate—optimized through orthogonal experiments. Additionally, the effects of plant fiber type and dosage on the mechanical properties of geopolymers were investigated. The main conclusions are as follows.
(1) The significance ranking of factors affecting the early-age (3-day) strength of BFS-MS geopolymer was: D (mud soil replacement rate) > A (SS modulus) > C (water-solid ratio) > B (SS alkali content). In contrast, the influence on long-term (28-day) strength followed a different order: C > A > B > D. While higher level of Factor D significantly inhibited early strength development, it showed negligible negative effects on the ultimate 28-day strength.
(2) For the BFS-MS precursor system, the optimal SS modulus is 1.7, and the alkali content is 0.2. These parameters ensure high ion exchange efficiency and alkaline depolymerization of Si, Al, and Ca precursors, supporting both high early stage strength and sustained strength development during later curing phases. The BFS-MS geopolymer under the optimal ratio of 28 days can reach 43.56 MPa.
(3) A moderate water supply facilitates ion exchange and reactions without inducing significant drying shrinkage. The optimal water-to-solid ratio in this study is 0.5. Within a specific range, the MS replacement rate does not markedly affect long-term strength. When the MS replacement rate was 0.3, the materials achieved 85.7%, 90.0%, and 99.5% of the original strength at 3, 7, and 28 days respectively, demonstrating excellent potential for engineering applications.
(4) At 1.0% dosage, WF, JF and BF enhanced the 28-day compressive strength by 27.80%, 12.35% and 29.05% respectively. Furthermore, JF induces stress concentration due to agglomeration, resulting in a 7.88% strength reduction at 0.5% dosage and 4.73% improvement even at 1.5% dosage.
(5) Microscopically, WF’s small diameter and high specific surface area maximize fiber-matrix contact. In contrast, JF’s large size and poor dispersion trigger interfacial debonding and stress concentration, degrading strength. BF’s intermediate diameter and smooth surface limit mechanical anchoring, yielding lower reinforcement efficiency than WF. While this study provides preliminary investigation into the mechanical properties of PF-modified geopolymers, further research on hybrid fiber reinforcement and long-term durability, along with field application studies, remains essential for material optimization and practical implementation.
Data availability statement
The original contributions presented in the study are included in the article/supplementary material, further inquiries can be directed to the corresponding authors.
Author contributions
ZZ: Writing – review and editing, Writing – original draft. DC: Writing – original draft. YZ: Writing – original draft. JL: Writing – original draft. KZ: Writing – original draft, Writing – review and editing. HL: Writing – review and editing.
Funding
The author(s) declare that no financial support was received for the research and/or publication of this article.
Conflict of interest
Authors ZZ and DC were employed by China Communications Third Shipping Engineering Bureau Co., Ltd. and Ninth Engineering Company, CCCC Third Harbor Engineering Co., Ltd. Authors YZ and JL were employed by Ccid Urban Construction (Chongqing) Co. Ltd.
The remaining authors declare that the research was conducted in the absence of any commercial or financial relationships that could be construed as a potential conflict of interest.
Generative AI statement
The author(s) declare that no Generative AI was used in the creation of this manuscript.
Publisher’s note
All claims expressed in this article are solely those of the authors and do not necessarily represent those of their affiliated organizations, or those of the publisher, the editors and the reviewers. Any product that may be evaluated in this article, or claim that may be made by its manufacturer, is not guaranteed or endorsed by the publisher.
References
Alameri, M., Ali, M. M., Elchalakani, M., and Sheikh, A. (2025). Optimizing slag-based geopolymer mix design for enhanced strength and durability. J. Build. Eng. 100, 111770. doi:10.1016/j.jobe.2025.111770
Almutairi, A. L., Tayeh, B. A., Adesina, A., Isleem, H. F., and Zeyad, A. M. (2021). Potential applications of geopolymer concrete in construction: a review. Case Stud. Constr. Mater. 15, e00733. doi:10.1016/j.cscm.2021.e00733
Brustolin, A., da Luz, C. A., Silvestro, L., and Pereira Filho, J. I. (2024). Assessing natural carbonation and service life prediction of supersulfated cement. Case Stud. Constr. Mater. 21, e04022. doi:10.1016/j.cscm.2024.e04022
Cai, C., Li, F., Fan, S., Yan, D., Sun, Q., Jin, H., et al. (2023). Investigation on deterioration mechanism of geopolymer cemented coal Gangue-Fly ash backfill under combined action of high temperature and salt corrosion environment. Constr. Build. Mater. 398, 132518. doi:10.1016/j.conbuildmat.2023.132518
Cao, X., Jiang, T., Shimada, H., Sasaoka, T., and Hamanaka, A. (2024). Influence of CO2 nano-bubble water concentration and curing time on the macroscopic and microscopic mechanical properties of cemented backfill materials. J. Build. Eng. 98, 111099. doi:10.1016/j.jobe.2024.111099
Chen, W., Zhu, H., Liu, F., Zeng, X., Mao, Y., and Yang, A. (2025). Green transformation of mining waste: synergistic effects of coal mine drainage sludge and industrial by-products in high-performance geopolymer production and environmental benefits. Constr. Build. Mater. 471, 140595. doi:10.1016/j.conbuildmat.2025.140595
Chen, X., Zhou, M., Shen, W., Zhu, G., and Ge, X. (2018). Mechanical properties and microstructure of metakaolin-based geopolymer compound-modified by polyacrylic emulsion and polypropylene fibers. Constr. Build. Mater. 190, 680–690. doi:10.1016/j.conbuildmat.2018.09.116
Cui, C., Peng, H., Liu, Y., Zhang, J., Cai, C., and Peng, A. (2017). Influence of GGBFS content and activator modulus on curing of metakaolin based geopolymer at ambient temperature. J. Build. Mater. 20 (04), 535–542. doi:10.3969/j.issn.1007-9629.2017.03.010
Cui, Y. L., Pan, F. R., Zhang, B. B., Wang, X. Q., and Diao, H. G. (2022). Laboratory test of waste mud treated by the flocculation-vacuum-curing integrated method. Constr. Build. Mater. 328, 127086. doi:10.1016/j.conbuildmat.2022.127086
Davidovits, J. (1989). Geopolymers and geopolymeric materials. J. Therm. Analysis 35, 429–441. doi:10.1007/bf01904446
Davidovits, J. (1991). Geopolymers-Inorganic polymeric new materials. J. Therm. Analysis 37 (8), 1633–1656. doi:10.1007/bf01912193
Di Sarno, L., Albuhairi, D., and Medeiros, J. M. P. (2024). Exploring innovative resilient and sustainable bio-materials for structural applications: hemp-fibre concrete. Structures 68, 107096. doi:10.1016/j.istruc.2024.107096
Fioroni, C. A., Kadivar, M., do Amaral, L. M., Ezugwu, E. K., Calabria-Holley, J., and Júnior, H. S. (2025). Sol-gel treated pulp and accelerated carbonation curing: a novel approach for high-performance bamboo fibre cement composites. Constr. Build. Mater. 458, 139487. doi:10.1016/j.conbuildmat.2024.139487
Glaus, M. A., and Van Loon, L. R. (2008). Degradation of cellulose under alkaline conditions: new insights from a 12 years degradation study. Environ. Sci. and Technol. 42 (8), 2906–2911. doi:10.1021/es7025517
Glukhovsky, V. D. (1965). “Soil silicates,” in Their properties, technology and manufacturing and fields of application[D]. Kiev: Civil Engineering Institute.
Hai-feng, L., Kai, Z., Jin-long, Y., and Ai-chao, W. (2022). A study on the optimal selection of similar materials for the physical simulation experiment based on rock mineral components. Eng. Fail. Anal. 140, 106607. doi:10.1016/j.engfailanal.2022.106607
Hua, J. M., Yi, H. L., Xue, X. Z., Zhan, J. H., and Xiao, Z. (2025). Mechanical properties of lunar regolith simulant geopolymer with basalt fiber reinforcement. J. Civ. Environ. Eng., 1–13. doi:10.11835/j.issn.2096-6717.2025.026
James, J. (2020). Sugarcane press mud modification of expansive soil stabilized at optimum lime content: strength, mineralogy and microstructural investigation. J. Rock Mech. Geotechnical Eng. 12 (2), 395–402. doi:10.1016/j.jrmge.2019.10.005
Jia, K., Zhou, Z., Singh, S. V., and Wang, C. (2024). A review of the engineered treatment of red mud: construction materials, metal recovery, and soilization revegetation. Results Eng. 24, 102927. doi:10.1016/j.rineng.2024.102927
Kina, C., Tanyildizi, H., and Acik, V. (2025). Hybrid portland cement-slag-based geopolymer mortar: strength, microstructural and environmental assessment. Process Saf. Environ. Prot. 195, 106771. doi:10.1016/j.psep.2025.106771
Kong, X., Zhang, Z., Liang, Y., Wang, X., and Liu, M. (2023). Experimental study on solidified dredged sediment with MgO and industrial waste residue. Constr. Build. Mater. 366, 130105. doi:10.1016/j.conbuildmat.2022.130105
Korniejenko, K., Łach, M., Hebdowska-Krupa, M., and Mikuła, E. J. (2018). The mechanical properties of flax and hemp fibres reinforced geopolymer composites. IOP Conf. Ser. Mater. Sci. Eng. 379, 012023. doi:10.1088/1757-899x/379/1/012023
Kuqo, A., Koddenberg, T., and Mai, C. (2023b). Use of dry mixing-spraying process for the production of geopolymer-bonded wood and seagrass fibreboards. Compos. Part B Eng. 248, 110387. doi:10.1016/j.compositesb.2022.110387
Kuqo, A., Mayer, A. K., Amiandamhen, S. O., Adamopoulos, S., and Mai, C. (2023a). Enhancement of physico-mechanical properties of geopolymer particleboards through the use of seagrass fibers. Constr. Build. Mater. 374, 130889. doi:10.1016/j.conbuildmat.2023.130889
Li, Y., Wei, M. L., Liu, L., Wei, W., and Chen, Y. J. (2023). Strength characteristics and mechanism analysis of fiber reinforced highly cohesive tailings solidified using high-calcium geopolymer. Rock Soil Mech. 44 (01), 43–53. doi:10.16285/j.rsm.2022.0252
Li, Z., Du, P., Zhou, Y., Wang, J., and Cheng, X. (2024a). Synchronous hot-pressed metakaolin-fly ash based geopolymer: compressive strength and hydration products. J. Build. Eng. 97, 110997. doi:10.1016/j.jobe.2024.110997
Li, Z., Lu, H., Zhang, K., and Wu, Y. (2024b). Mechanism of developing early strength of Portland cement-desert sand system under radiation in desert conditions. Case Stud. Constr. Mater. 21, e03693. doi:10.1016/j.cscm.2024.e03693
Lin, M., Chen, G., Chen, Y., Han, D., Su, R., and Wu, J. (2025). Mechanical properties and microstructure of fly ash and slag-based geopolymer prepared by silica fume-based activator. J. Clean. Prod. 498, 145214. doi:10.1016/j.jclepro.2025.145214
Lu, H. F., Yi, J. L., He, D., Xu, J. B., Kong, X. X., and Zhang, K. (2022). Experimental study on preparation of geological polymer grouting material based on dredged sediment. Chin. J. Rock Mech. Eng. 41 (12), 2567–2578. doi:10.13722/j.cnki.jrme.2022.0501
Luo, Y., Meng, J., Wang, D., Jiao, L., and Xue, G. (2022). Experimental study on mechanical properties and microstructure of metakaolin based geopolymer stabilized silty clay. Constr. Build. Mater. 316, 125662. doi:10.1016/j.conbuildmat.2021.125662
Lv, H., Chen, Y., Xie, Q., Wu, P., Chen, Y., Gu, J., et al. (2022). Performance optimization and characterization of loess-slag-based geopolymer composite: a new sustainable green material for backfill. Constr. Build. Mater. 354, 129103. doi:10.1016/j.conbuildmat.2022.129103
Mikhailova, O., Del Campo, A., Rovnanik, P., Fernández, J. F., and Torres-Carrasco, M. (2019). In situ characterization of main reaction products in alkali-activated slag materials by confocal Raman microscopy. Cem. Concr. Compos. 99, 32–39. doi:10.1016/j.cemconcomp.2019.02.004
National Cement Standardization Technical Committee (2023). 175–2023: Common Portland cement, GB. China: China Natl. Stand. Manag. Comm.
National Cement Standardization Technical Committee (2017). GB/T 18046-2017: Ground granulated blast furnace slag used for cement, mortar, and concrete. China: China Natl. Stand. Manag. Comm.
Nematollahi, B., Sanjayan, J., Qiu, J., and Yang, E. H. (2017). High ductile behavior of a polyethylene fiber-reinforced one-part geopolymer composite: a micromechanics-based investigation. Archives Civ. Mech. Eng. 17 (3), 555–563. doi:10.1016/j.acme.2016.12.005
Nguyễn, P. H., Nguyễn, H. H., Lương, Q. H., Bolander, J. E., and Lee, B. Y. (2023). Optimization of fly ash-based polyethylene fiber-reinforced engineered cement-free composites with low-density and ultra-ductility using Taguchi robust design method. J. Build. Eng. 66, 105946. doi:10.1016/j.jobe.2023.105946
Pan, Z., Tao, Z., Cao, Y. F., Wuhrer, R., and Murphy, T. (2018). Compressive strength and microstructure of alkali-activated fly ash/slag binders at high temperature. Cem. Concr. Compos. 86, 9–18. doi:10.1016/j.cemconcomp.2017.09.011
Suyambulingam, I., Sudherson, D. P. S., Perumal, S. N., and Perumal, S. N. (2024). Comprehensive characterization of microcrystalline cellulose from lemon grass (Cymbopogan citratus) oil extraction agro-industrial waste for cementitious composites applications. Int. J. Biol. Macromol. 271, 132644. doi:10.1016/j.ijbiomac.2024.132644
Van-Jaarsveld, J. G. S., Van-Deventer, J. S. J., and Lorenzen, L. (1997). The potential use of geopolymeric materials to immobilise toxic metals: Part I. Theory and applications. Miner. Eng. 10 (7), 659–669. doi:10.1016/s0892-6875(97)00046-0
Wang, J., Luan, Y., Ma, T., Zhang, W., and Xu, G. (2023). Experimental investigation on the mechanical performance and microscopic characterization of desulfurization gypsum-reinforced ternary geopolymer. Constr. Build. Mater. 392, 131855. doi:10.1016/j.conbuildmat.2023.131855
Wang, P. Z., Trettin, R., and Rudert, V. (2005). Effect of fineness and particle size distribution of granulated blast-furnace slag on the hydraulic reactivity in cement systems. Adv. Cem. Res. 17 (4), 161–167. doi:10.1680/adcr.2005.17.4.161
Wang, Q., Zhang, R., Guo, J., Cai, G., and Li, Y. (2024a). Study on mechanical properties and microstructure of metakaolin-slag-calcium carbide residue synergistic solidifying waste engineering mud. Constr. Build. Mater. 438, 137135. doi:10.1016/j.conbuildmat.2024.137135
Wang, S., and Hao, M. (2024). Plant communities and potential phytoremediation species for resource utilization of abandoned drilling mud. Front. Environ. Sci. 11, 1302278. doi:10.3389/fenvs.2023.1302278
Wang, Y., Weng, Y., and Chen, B. (2024b). Enhancing compressive strength of phosphogypsum-based geopolymer cement with five alkaline activator combinations. J. Build. Eng. 95, 110352. doi:10.1016/j.jobe.2024.110352
Wei, M., Yang, Y., Xiong, L., Wu, W., Feng, T., and Zhong, K. (2023). Cement-SG curing agent for solidification of mucky soils. Bull. Eng. Geol. Environ. 82 (6), 236. doi:10.1007/s10064-023-03241-0
Withana, H., Rawat, S., Fanna, D. J., and Zhang, Y. X. (2024). Engineered cementitious composite with nanocellulose and high-volume fly ash. Constr. Build. Mater. 451, 138849. doi:10.1016/j.conbuildmat.2024.138849
Yang, H., Dai, F., Chen, H., He, Y., Wang, Z., and Wang, R. (2023). Fabrication of stalk fiber/geopolymers-based slow-release fertilizer with agricultural waste and loess for promoting plant growth. J. Environ. Chem. Eng. 11 (2), 109481. doi:10.1016/j.jece.2023.109481
Yang, S. Y., Zhao, R. D., Zeng, X. S., Jia, W. T., Jin, H. S., and Li, F. H. (2021). Reinforced geopolymer materials with natural fibers: a review. Mater. Rep. 35 (07), 7107–7113. doi:10.11896/cldb.19100048
Yang, Z. H., Zhu, T., Zhang, D. S., Yang, Q. N., and Mao, M. J. (2025). Study on the properties of Nano-Al2O3and steel fiber composite reinforced geopolymer grouting materials. Mater. Rep., 1–20. doi:10.11896/cldb.24050076
Yuan, L., Ma, Y., Zhang, J., Men, J., Sun, T., Zhao, H., et al. (2022). Orthogonal analysis and mechanism of compressive strength and microstructure of the metakaolin-fly ash geopolymer. Case Stud. Constr. Mater. 17, e01154. doi:10.1016/j.cscm.2022.e01154
Zainal, S. I. S., Abel, M., Durai, D., Rizalman, A. N., and Sulaiman, M. F. (2024). Experimental investigation on the mechanical properties of cement mortar containing recycled tire crumbs reinforced with polypropylene, oil palm and banana fibers. J. Build. Eng. 92, 109728. doi:10.1016/j.jobe.2024.109728
Zhang, K., Lu, H., Li, J., and Bai, H. (2022). Orthogonal experimental study on the factors affecting the mechanical properties of alkali-activated slag materials. Materials 15 (24), 8795. doi:10.3390/ma15248795
Zhang, K., Lu, H., and Li, Z. (2024). Effect of precursor element composition on compressive strength of alkali-activated dredged sediment. Case Stud. Constr. Mater. 20, e03404. doi:10.1016/j.cscm.2024.e03404
Zhang, K., Xu, H., Kong, X. X., Zhang, C. Y., Lu, H. F., and He, D. (2023b). Study on the influence mechanism of micro-mechanical properties of heterogeneous geopolymer gels. J. Build. Eng. 76, 107164. doi:10.1016/j.jobe.2023.107164
Zhang, K., Yi, J. L., Kong, X. X., Li, Z. Y., Lu, H. F., Zhang, Q. Z., et al. (2023a). Preparations of lake sediment geopolymers using the alkaline activation and their mechanical properties. J. Test. Eval. 51, 3451–3463. doi:10.1520/jte20220619
Zhao, G., Xie, S., Zhang, Z., Ren, G., Ding, Y., Wu, T., et al. (2024). Engineering properties optimization of dispersive soil by calcium silicate waste—the role of steel-making slag. J. Environ. Manag. 365, 121563. doi:10.1016/j.jenvman.2024.121563
Zhao, Y., Yang, C., Li, K., Qu, F., Yan, C., and Wu, Z. (2022). Toward understanding the activation and hydration mechanisms of composite activated coal gangue geopolymer. Constr. Build. Mater. 318, 125999. doi:10.1016/j.conbuildmat.2021.125999
Zhao, Z., Zhang, A., Sheng, G., Jiang, S., Zhou, W., and Li, J. (2025). Biomineralized aminated cellulose toughened and reinforced magnesium oxychloride cement for the construction and wood industry. Mater. Today Commun. 42, 111235. doi:10.1016/j.mtcomm.2024.111235
Keywords: mud soil, blast furnace slag, plant fibers, orthogonal experimental design, uniaxial compressive strength, geopolymer
Citation: Zhu Z, Chang D, Zhu Y, Li J, Zhang K and Lu H (2025) Mechanical properties and microstructure of plant fiber reinforced BFS-MS geopolymer: an orthogonal design approach. Front. Earth Sci. 13:1605929. doi: 10.3389/feart.2025.1605929
Received: 04 April 2025; Accepted: 05 June 2025;
Published: 23 June 2025.
Edited by:
Muhammad Junaid Munir, Jinan University, ChinaReviewed by:
Xiaoyun Yang, Yuncheng Vocational and Technical University, ChinaHaoyan Lyu, Kyushu University, Japan
Sanjoli Gupta, Indian Institute of Technology (BHU), India
Gabo Cyprien Bailly, École Spéciale des Travaux Publics, France
Zhongchen Ao, China University of Mining and Technology, China
Copyright © 2025 Zhu, Chang, Zhu, Li, Zhang and Lu. This is an open-access article distributed under the terms of the Creative Commons Attribution License (CC BY). The use, distribution or reproduction in other forums is permitted, provided the original author(s) and the copyright owner(s) are credited and that the original publication in this journal is cited, in accordance with accepted academic practice. No use, distribution or reproduction is permitted which does not comply with these terms.
*Correspondence: Kai Zhang, MjY4NTM3MDQ4NEBxcS5jb20= Haifeng Lu, bHVoYWlmZW5nQHdodS5lZHUuY24=