- 1CHN Energy Shendong Coal Group Co., Ltd., Yulin, China
- 2CCTEG Xi’an Research Institute (Group) Co., Ltd., Xi’an, China
Aiming at the technical problem of low efficiency of gas drainage in high-gas and low-permeability coal seams in China, this paper takes the No. 8 coal seam in Baode Coal Mine as the engineering background and conducts a study on the technology of enhancing gas permeability and gas drainage through staged hydraulic fracturing of directional long boreholes. By adopting the drag-type staged fracturing process with double-packers and a single-slip, and combining it with methods such as the analysis of pump injection stress curve stages, gas extraction concentration analysis, and in-hole transient electromagnetic detection, the laws of fracture propagation and the mechanism of permeability modification are revealed. The research shows that during the rock formation fracturing stage, the stress drop reaches 8.2–9.6 MPa, and the drop rate of the fracturing stress from the bottom to the opening of the borehole is approximately 14.6%. The influence radius of the fracturing extends to 30 m, forming a strip-shaped low-resistance abnormal area. The gas extraction data indicates that after fracturing, the gas extraction concentration increases to 54.37% (with a peak value of 68%), the comprehensive flow rate increases by 200%–300% (stabilizing at 0.6–0.8 m3/min), which is 5.6 times higher than that of the unfractured boreholes. Through reconstructing the fracture network of the coal seam, this technology can break through the limitations of the original gas permeability, shorten the pre-extraction cycle, and reduce the borehole density. The research results provide theoretical support and engineering demonstration for the efficient gas extraction from coal seams with similar geological conditions.
1 Introduction
As an associated mineral resource of coal, gas is a clean and efficient energy source. However, it is also a major factor affecting the safety of coal mines in China (Li et al., 2025a; Zhang et al., 2024a; Su et al., 2020). In China, more than 70% of coal seams have a permeability of less than 1.0 × 10−3 μm2, and in high-gas and outburst coal mines, 95% of the mined coal seams are of low permeability (Li et al., 2024a; Yao et al., 2025). Pre-drainage of coalbed methane is not only beneficial for the full utilization of gas resources but also for the prevention and control of gas disasters (Wei et al., 2021; Liu et al., 2021a; Zhang et al., 2024b; Yang et al., 2024; Wang et al., 2023a). However, with the increase in mining depth and the decrease in coal seam permeability, the difficulty of gas drainage increases and the efficiency is significantly reduced (Liu et al., 2021a; Chen et al., 2025). Therefore, certain technical measures need to be taken during gas drainage to increase the permeability of the coal seam and improve the gas drainage efficiency as much as possible (Manjunath et al., 2023; Liu et al., 2019; Yang et al., 2020; Liu et al., 2021b; Zeng et al., 2023; Wang et al., 2025).
At present, the common coal seam permeability enhancement technologies mainly include hydraulic fracturing, hydraulic slotting, high-stress water jet punching, supercritical CO2 fracturing, etc. (Fu et al., 2018; Li et al., 2024a; Gao et al., 2024; Liu et al., 2025; Wang, 2024; Ma et al., 2019; Kong et al., 2024). Hydraulic fracturing has been widely applied in coal mine production due to its large permeability enhancement range and relatively low cost (Li et al., 2025b; Luo et al., 2024; Atkinson et al., 2020; Dai et al., 2024; Wei et al., 2020; Sun et al., 2024). Due to the complex destructive effect of hydraulic fracturing on coal seams, the changes in coal seams and the laws of gas migration after fracturing are also quite complex (Ma et al., 2017; Liu et al., 2023; Xue et al., 2018; Li et al., 2023; Jiang, 2024; Ghanbari and Dehghanpour, 2016; Ismail and Azadbakht, 2024). Many scholars at home and abroad have achieved a large number of research results regarding this issue. Kang et al. (2024) employed the finite element method to study the characteristics of fracture propagation during the hydraulic fracturing process in steeply dipping reservoirs. The research findings revealed that the fracture propagation can be divided into three stages: upward-dipping fracture propagation, fracture arrest, and downward-dipping fracture propagation. Zhai et al. (2020) established a storage model with randomly distributed weak surfaces using the cohesion zone method in their research. Then put forward the concept of “reservoir reconstruction efficiency” as an indicator to evaluate the effect of hydraulic fracturing. By using the proposed model and orthogonal experiments, they found that the flow rate had the most significant impact on RRE, followed by the perforation direction and perforation length. Zhang et al. (2021) developed a multi-stage hydraulic fracturing technology based on the goaf, established a mathematical model for determining the location of hydraulic fracturing, and established a collaborative support system composed of caved filling bodies, coal pillars, and bearing layers. He et al. (2021) adopted the roof weakening technology of staged hydraulic fracturing with double-packer, single-sealing, multi-point dragging for directional long boreholes in underground coal mines. By pre-weakening the structure of the coal seam roof in advance, they enhanced the degree of fracture development in the hard roof and reduced the overall strength of the roof. Niu (2022) analyzed the simplified mechanical model of the overburden structure of the hard roof through theoretical analysis and on-site industrial tests. He revealed the mechanism by which hydraulic fracturing weakens the hard roof and reduces the manifestation of mine stress during the coal mining period. Tan et al. (2025) proposed a method for determining the target horizons for hydraulic fracturing. This method combines the bending strain energy accumulated in the critical state of the first fracture of the hard roof during the coal seam extraction process, as well as the distribution and response characteristics of microseismic events. Wen et al. (Wen et al., 2022) studied the influence of water sensitivity damage on the permeability of coal seams, focusing on the similar simulation experiment method of hydraulic fracturing of cross-seam boreholes in underground coal seams. Wang et al. (2023b) explored the initiation mechanism of hydraulic fracturing in steeply inclined coal seams and the influence of triaxial stress on the fracturing effect through indoor physical experiments.
Based on the previous research, this study takes the construction of the No. 8 coal seam in Shenhua Baode Coal Mine as the engineering background and solve the challenge of difficult precise interval control in traditional hydraulic fracturing of long boreholes, a staged hydraulic fracturing technology for directional long boreholes in moderate-hard and low-permeability coal seams was developed. This technology uses a stage-by-stage isolation method to perform directional fracturing with segmented time intervals and stress gradients, guided by the permeability and in-situ stress characteristics of the coal seam. It has significantly improved the permeability of the coal seam and the gas drainage effect, reduced the number of pre-drainage boreholes in the area and the pre-drainage time of gas, and achieved good results in gas control. It provides certain references for the application of hydraulic fracturing permeability enhancement technology in this mining area and mines under similar engineering conditions.
2 Overview of the coal mine
Baode Coal Mine is located in Baode County, Shanxi Province (as shown in Figure 1). The mining area is in the monoclinic structural region on the eastern edge of the Ordos Basin. The degree of development of folds and faults is low and their scales are small. The coal-bearing strata are of the Carboniferous-Permian system. The dip angle of the coal seams is between 3° and 9°, with an average of 5°. The area of the mine field is 55.9077 km2, and the mining depth ranges from 420 m to 540 m. The hydrogeological conditions belong to a medium to complex type of deposit, and the exploration type is Class III(2), Type II. The No. 8 coal seam in the experimental area is located above the S3 sandstone at the bottom of the Shanxi Formation (P1S), and it is the uppermost minable coal seam in the area. The thickness of the coal seam ranges from 1.85 m to 9.01 m, and the average thickness of pure coal is 6.02 m. The minable coal seam coefficient is 17.05%. It is a thick to extremely thick coal seam, mainly composed of thick coal seams, with an average density of 1.51 t/m3. This coal seam is gas coal and belongs to Class II spontaneous combustion coal seam.
The working face of this experiment is the 81313 working face in the No. 3 (Lower) Panel of the southwest wing of the mine field. The strike length of the working face is approximately 3,117 m, and the dip length is 242 m. The coal thickness in the entire No. 3 (Lower) Panel ranges from 2.15 m to 10.5 m, with an average of 7.36 m. It is a stable coal seam for mining in the whole area. The average original gas stress of the working face is 1.05 MPa, and the gas content is 5–6 m3/t. During the driving project of the coal roadways in the upper and lower gate roads of the adjacent 81311 working face, the maximum measured raw coal gas content is 6.57 m3/t. The gas content that cannot be desorbed under normal stress is 0.72 m3/t. The gas permeability coefficient of the coal seam is 0.17–0.8 m2/(MPa2·d). The absolute gas emission quantity is 78.48 m3/min, and the relative gas emission quantity is 11.08 m3/t. It belongs to a typical high-gas and low-permeability coal seam that is difficult to drain. The ventilation system adopts the mechanical extraction type with two-wing diagonal ventilation. The total intake air volume is 30178 m3/min, the total return air volume is 30767 m3/min, the effective air volume rate is 90.41%, and the ventilation conditions are excellent.
3 Theory and design of sectional hydraulic fracturing for directional long boreholes
3.1 Construction technical process of sectional hydraulic fracturing for permeability enhancement
This experiment intends to adopt the multi-modal sectional hydraulic fracturing technology with double packers, single packer clamping, and multi-point dragging, to conduct a study on the sectional hydraulic fracturing reconstruction technology for long boreholes along the coal seam. The principle of this technology is that after the directional drilling construction is completed and the fracturing tool string is sent to the designated position, the target interval of the formation is fractured by clamping it with a single packer among the double packers. By utilizing the designed balanced stress relief channel in the packer, the balanced transfer of stress between the fracturing fluid in the high-stress tubing string and the packer is achieved. When the high-stress fracturing fluid reaches the set stress, the packer is fully set. After the stress is continuously increased to the set stress, the flow restrictor opens, enabling the fracturing operation of the fracturing interval. During the fracturing operation, the high-stress fracturing fluid is continuously injected into the coal seam, causing the water stress acting on the target coal seam to gradually increase. When the stress exceeds the fracture stress of the coal seam, the elastic residual energy of the coal seam is released in the form of kinetic energy, leading to the generation of a new fracture system in the coal seam. The fracture propagation mainly occurs through the communication, development, extension, and penetration of the self-generated matrix pores and fractures, bedding fractures in the coal seam, and the new fractures formed by the fracturing. After the first-stage fracturing operation is completed, the fracturing pumping equipment at the borehole mouth is shut down, and water is drained at the borehole mouth to relieve the stress. The directional drilling rig is used to drag the high-stress tubing string at the borehole mouth, and the packer is dragged to the designed position for the second-stage fracturing operation. The fracturing operations of the designed construction intervals are completed in sequence. Three-dimensional continuous fractures are formed in the adjacent fracturing intervals, which improves the coal structure and reduces the overall strength of the coal seam. The construction process of the dragging-type sectional hydraulic fracturing for permeability enhancement is shown in Figure 2.
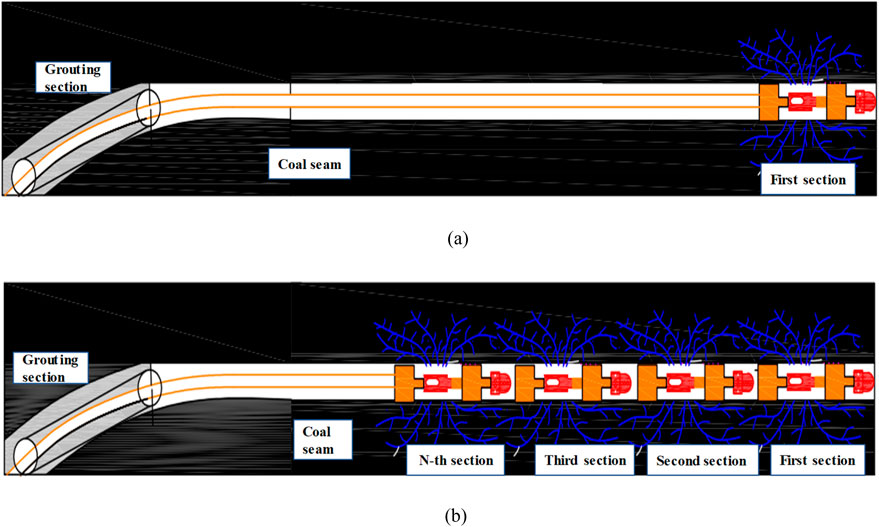
Figure 2. Schematic diagram of the drag-type staged fracturing process. (a) The first section of the fracturing operation. (b) The N-th section of the fracturing operation.
3.2 Hydraulic fracturing equipment
The hydraulic fracturing equipment used in this experiment mainly includes a directional drilling rig, a fracturing pump unit, a rapid hole-sealing device, etc. The directional drilling rig selected is the ZDY6000LD (B) crawler-type full-hydraulic directional drilling rig (as shown in Figure 3). This drilling rig is convenient to relocate, has a wide range of speed adjustment, a large torque, and advanced technical performance. It is mainly used for the construction of various high-precision directional boreholes such as geological exploration holes, gas drainage holes, and water injection holes in coal mines.
The BYW65/400 type emulsion pump (as shown in Figure 4) is selected as the hydraulic fracturing water injection pump. It uses a YB2-400M-4 flameproof motor as the power source and is equipped with a BY610Z hydraulic transmission. It features a compact structure and a relatively small size, and is mainly used for operations such as coal seam fracturing and water injection. The overall external dimensions of the pump unit (length × width × height) are 8,700 × 1,450 × 1770 mm, and the total weight is 13 tons. To prevent fracturing fluid from contaminating the coal seam, clear water is selected as the hydraulic fracturing fluid.
In order to ensure the hole-sealing effect of hydraulic fracturing, this experiment adopts a rapid hole-sealing device for sectional hydraulic fracturing in coal mines, which is composed of a guide shoe, a check valve, a differential stress sliding sleeve, a flow restrictor, a safety joint, oil pipes, a backwashing wellhead, etc., as shown in Figure 5. Among them, the guide shoe is a device that guides the tubing string to smoothly enter the borehole during the process of pushing the sectional fracturing hole-sealing equipment, and it is an important component to prevent the tubing string from inserting into or scraping the borehole wall. The check valve is a component that ensures the action direction of the water flow during hydraulic fracturing. This device can achieve a rapid and stable hole-sealing effect, improve the construction efficiency, and has the characteristics of being able to be smoothly recovered and reused after fracturing.
3.3 Design of hydraulic fracturing scheme
3.3.1 Design of borehole layout
Based on the current status of hydraulic fracturing technology, processes, and equipment in coal mines, and combined with the effects of hydraulic fracturing of directional long boreholes in coal and rock formations that have been implemented in previous mining areas. In this experiment, the dragging-type sectional hydraulic fracturing process is planned to be adopted in the 81313 working face of Baode Coal Mine. The engineering experiment designs two drilling sites, and one main fracturing borehole is constructed at each drilling site. The lengths of the boreholes are 500 m, 300 m, and 1,000 m respectively, and the diameter of each borehole is 96 mm. The two main boreholes are respectively subjected to sectional fracturing in 7 sections, 5 sections, and 8 sections. The gas drainage boreholes are designed according to a unilateral influence range of 30 m. Three gas drainage boreholes are arranged on both sides of the main fracturing borehole, and the spacing between the boreholes is 6–10 m. One gas drainage comparison borehole is arranged in the unfractured area, which is 100 m away from the main fracturing borehole. The diameter of each borehole is the same as that of the main fracturing borehole. The borehole layout is shown in Figure 6.
3.3.2 Construction design of sectional hydraulic fracturing for permeability enhancement
The sectional hydraulic fracturing process of the double-packer and single-packer clamping dragging tubing string mainly consists of the optimization of fracturing equipment, the combination of fracturing tools, the selection of tools, the pumping process, etc. The sectional fracturing method is to carry out the fracturing operation sequentially from the inside outwards. The technological process is shown in Figure 7.
During the fracturing design stage, appropriate fracturing equipment is selected and debugged to adapt to specific geological conditions and engineering requirements. Meanwhile, the sectional tool string is selected and assembled, the pumping stress, displacement, and water injection volume are determined, and monitoring and safety technical measures are formulated to ensure the safety and effectiveness of the fracturing process.
When entering the stage of sectional hydraulic fracturing construction, first, the sectional tool string is sent to the predetermined position. Then, the double packers are used for setting and checking for leaks to ensure the tightness during the fracturing process. After that, water injection fracturing is carried out. During the fracturing process, it is necessary to determine whether the fracturing is completed. If not, the process is repeated; if completed, the section count is updated, and preparations are made for the next section of fracturing. The tubing string is moved to the next fracturing point. After all the fracturing sections are completed, the borehole mouth is treated with stress maintenance to ensure the stability of the fracturing effect.
Finally, in the stage of withdrawing the tool string for maintenance, after all the fracturing work is completed, the tool string is withdrawn and necessary maintenance and repairs are carried out. The above systematic process can ensure the efficiency and safety of the fracturing operation, provide guidance for practical operations, and lay a foundation for subsequent research.
4 Results and discussion
4.1 Analysis of the pumping injection stress curve
4.1.1 Classification of the fracture propagation stages
Based on the characteristics of the hydraulic fracturing pumping injection stress curve, the curve can be divided into three stages: the stress rising stage, the fracturing stage, and the stable fracture propagation stage.
The stress rising stage includes the process of setting the packer. The packer is inflated by artificially controlling the stress to ensure it makes full contact with the borehole wall. After the packer is fully inflated and set, the constant-stress shut-off valve opens, and the fracturing fluid flows into the borehole. This process will lead to a stress drop, and the magnitude of the stress drop varies for each fracturing section.
Subsequently, the stress continues to rise and enters the fracturing stage. When the stress rises to reach the fracturing stress of the roof rock formation or coal seam, the destruction of the rock formation or coal seam creates new liquid storage spaces, resulting in a stress drop. The magnitude of the stress drop reflects the size of the generated fracture volume or the richness of the fracture network. The greater the stress drop, the larger the formed liquid storage space, that is, the larger the fracture volume. It is particularly important to emphasize that during the fracturing stage, there will be multiple stress drop phenomena with different magnitudes, and the magnitude of the first stress drop is the largest. It is certain that the first stress drop is caused by the generation or connection of fractures in the rock formation section. There are three possible reasons for this phenomenon: 1) After fractures are generated in the rock formation, the fractures expand to different strata, causing the destruction of strata with different lithologies. The resulting different fracture volumes lead to different stress drops; 2) The first stress drop represents the destruction of the rock formation, and the generated fractures expand into the coal seam. Subsequent stress drops occur in the coal seam, indicating the initiation, expansion, and extension of fractures in the coal seam; 3) Destruction occurs not only in the rock formation but also in the coal seam, and the dual fracture effect results in stress drops with different magnitudes.
After the coal and rock mass are fractured, the fractures expand into the coal seam. Under the action of high-stress water, the fractures continuously expand within the coal seam and exhibit a sawtooth-like fluctuation around a certain stable value. At this point, the fractures enter the stable propagation stage.
4.1.2 Analysis of the characteristics of fracture stress
The sectional hydraulic fracturing stress curves of the main fracturing boreholes are shown in Figure 8 respectively. During the stable fracture propagation stage, the stable stresss of each fracturing section are different. The stress of the first section of the fracturing borehole fluctuates in a sawtooth pattern at around 9 MPa. The stresss of the second, third, and fourth sections fluctuate in a sawtooth pattern at around 8.3 MPa. The stresss of the fifth and sixth sections fluctuate in a sawtooth pattern at around 9.5 MPa, and the stress of the seventh section fluctuates in a sawtooth pattern at around 8 MPa. The different magnitudes of the sawtooth-shaped stress fluctuations during the stable fracture propagation stage indicate different degrees of difficulty in the extension and propagation of fractures and different levels of fracture richness. On the one hand, the more obvious the sawtooth-shaped change is, the more frequently the coal seam fractures, the slower the fracture extension and propagation are, and the richer the generated fractures are. If the sawtooth-shaped change is not obvious, it is likely that a single fracture is formed or the fracture extends forward along the structural plane within the coal seam.
The fracture stress of the main fracturing boreholes are 8.3 MPa, 8.5 MPa, 8.4 MPa, 9.1 MPa, 8.9 MPa, 9.6 MPa, and 8.2 MPa in sequence. From this, it can be seen that there is a gradually decreasing trend from the bottom of the fracturing borehole to the borehole opening. The main reasons for the above situation are as follows: 1) The bottom of the borehole is relatively farther from the hydraulic pump unit system than the borehole opening, and the friction resistance in the pipeline is large, resulting in a higher fracture stress of the rock formation. As the fracturing position gets closer to the borehole opening, the fracture stress shows a decreasing trend. 2) The stratum position or lithology of the fracturing position is a key factor affecting the hydraulic fracturing fracture stress. Generally, the fine sand has a small fluid loss, while the coarse sandstone has a large fluid loss. The fracture stress of the fine sandstone section during fracturing is greater than that of the coarse sandstone section. 3) The fracturing is related to factors such as the operation of the injection holes, the branch holes, and the vertical distance from the fracturing position to the coal seam. 4) The influence of variations in the coal seam’s physicomechanical properties on fracture stress shows a positive correlation between coal hardness and fracture stress. Hard coal (e.g., with gangue interlayers) has stronger resistance to failure, requiring higher stress for fracturing. Conversely, pore structure exhibits a negative correlation with fracture stress: coal seams with high porosity and dense cleats facilitate fracturing fluid penetration, thereby reducing the initiation stress. The combined effect of the above three factors results in the fracture stress of the bottom section of the borehole being greater than that of the opening section of the borehole.
4.2 Analysis of the gas drainage effect
4.2.1 Analysis of gas concentration
To further explore the permeability enhancement effect of the coal seam hydraulic fracturing technology, during the gas drainage process, the gas concentrations of the No. 1 main fracturing borehole and the No. 8 natural gas drainage comparison borehole in the gas drainage chamber of the 18th crossheading in the auxiliary haulage roadway of 81313 were monitored for a month. Three sets of data were collected every day, and their average values were calculated. Then, a trend chart showing the changes over time was drawn, as shown in Figure 9.
By observing Figure 9, it can be seen that from the 1st day to the 10th day, the gas drainage concentration of the main fracturing borehole remained above 55%, with a maximum of 68% and an average drainage concentration of 63%. From the 11th day to the 20th day, the gas drainage concentration decreased slightly, ranging from 40% to 62%, with an average gas drainage concentration of 55.12%. From the 21st day to the 30th day, the gas drainage concentration was below 60%, with an average gas drainage concentration of 43.17%. Throughout the entire gas drainage process, the highest gas drainage concentration was 68%, the lowest was 35%, and the average gas drainage concentration was 54.37%. The highest gas drainage flow rate was 0.81 m3/min, the lowest was 0.41 m3/min, and the average gas drainage flow rate was 0.58 m3/min. The gas drainage concentration of the comparison borehole always remained below 20%, with a maximum of 18% and an average drainage concentration of 9.7%. The gas drainage concentration curves of both the main fracturing borehole and the comparison borehole showed a trend of first increasing and then stabilizing.
As time goes by, although the gas concentration in the fracturing borehole fluctuates, it remains at a relatively high level overall. In the early stage, the gas concentration occasionally decreased, yet it still stayed within a relatively high range. For example, around the 5th day, the gas concentration was above 60%. Subsequently, the gas concentration in the fracturing borehole rebounded to approximately 62% during the period from the 7th to the 10th day. This is due to the gas replenishment within the coal seam and the dynamic equilibrium changes during the gas drainage process. Later, within the 20th to 30th days, although there were fluctuations, the gas concentration was relatively high for most of the time. The lowest concentration was still above 40%, and it rebounded to above 55% several times, generally presenting a high-concentration situation. Thanks to the effect of hydraulic fracturing on the fracturing borehole, the permeability of the coal seam has been enhanced, allowing the gas to be released and drained more quickly. As a result, the gas drainage concentration has always remained at a relatively high level.
The gas concentration curve of the non-fractured comparison borehole is relatively stable with a small fluctuation range. During the one-month monitoring period, the gas concentration of this borehole basically fluctuated between 5% and 15%. This indicates that for the comparison borehole without hydraulic fracturing, the gas release and drainage process is relatively slow and stable. The permeability of the coal seam has not been effectively improved, making it difficult for a large amount of gas to flow out rapidly, which results in a relatively gentle change in the gas concentration.
In conclusion, through the comparative analysis of the gas concentration change curves of the fracturing borehole and the comparison borehole, it can be seen that the sectional hydraulic fracturing technology of directional long boreholes along the coal seam has a significant impact on the gas concentration in the coal seam. The large fluctuations in the gas concentration of the fracturing borehole reflect that this technology has enhanced the fluidity and drainability of the gas in the coal seam. On the other hand, the relatively slow and stable gas concentration of the natural gas drainage borehole further demonstrates the important role of the directional long borehole hydraulic fracturing technology in changing the occurrence state of the gas in the coal seam and improving the gas drainage effect.
4.2.2 Flow decay law
The comprehensive flow rate during gas extraction refers to the total amount of gas extracted from the coal seam or gas storage space per unit time during the gas extraction process. It takes into account the impacts of various factors on gas flow comprehensively and is one of the important indicators for measuring the efficiency and effectiveness of gas extraction. Due to the above reasons, during the gas extraction process, in addition to monitoring the gas extraction concentration of the main fracturing holes and natural extraction holes in the gas drainage chamber of the 18th connecting roadway of the auxiliary haulage in 81313, the collection of comprehensive flow rate data is also carried out. Figure 10 is a comparative chart of the comprehensive gas extraction flow rates, which is drawn by sorting out the data.
By observing Figure 10, it can be seen that the curve of the fracturing hole exhibits the characteristic of flow rate fluctuation in the early stage. The possible reason is that the gas stress and flow state are unstable during the initial mining period. When it is approximately the third day, the comprehensive flow rate has climbed to around 0.85 cubic meters per minute. Subsequently, this upward trend continued, and a relatively high value was reached within the time period of 5–10 days, approaching the level of 0.85 cubic meters per minute. After that, during the subsequent monitoring period, the comprehensive flow rate basically fluctuated within a relatively high range between 0.6 and 0.8 cubic meters per minute. This phenomenon fully demonstrates that after the implementation of the hydraulic fracturing measure, the gas permeability of the coal seam around the fracturing hole has been significantly enhanced. Under the action of the stress difference, the gas in the coal seam can flow into the borehole more smoothly and be effectively extracted. As a result, the comprehensive gas extraction flow rate can continuously remain at a relatively high level, which strongly reflects the good gas extraction effect brought about by the staged hydraulic fracturing technology of the long boreholes along the coal seam.
In contrast, the flow rate curve of the natural gas extraction borehole shows a relatively slow upward process. Throughout the entire monitoring period, the comprehensive flow rate of this borehole remained at a relatively low level. The highest value never exceeded 0.7 m3/min, and it fluctuated mostly between 0.2 and 0.4 m3/min. This phenomenon indicates that there is a significant gap in the gas extraction efficiency between the boreholes that have not undergone hydraulic fracturing treatment and the fractured boreholes. Due to the poor original gas permeability of the coal seam, it is difficult for the gas to desorb effectively and migrate into the borehole, resulting in low gas extraction efficiency.
4.3 Analysis of the influence range of hydraulic fracturing
4.3.1 Detection principle
The principle of the transient electromagnetic detection technology in the borehole lies in the fact that the fracturing fluid formula contains highly conductive electrolyte substances. When fracturing occurs, the fracturing fluid penetrates into the coal and rock strata, altering the resistivity of these strata. By processing and comparing the changes in the resistivity or potential of the strata before and after fracturing, the direction and length of the fracturing fractures can be inferred. For the transient electromagnetic profile detection in the borehole, the transmitting coil and the receiving probe are sent into the borehole together. Three-component measurements are carried out point by point. The secondary field of the vertical component Z in the direction of the borehole is used to analyze the possible low-resistance abnormal areas around the borehole. The secondary fields of the two sets of horizontal components X and Y (the X component is perpendicular to the borehole and points to the right, and the Y component is perpendicular to the borehole and points downward), which are perpendicular to the borehole and orthogonal to each other, are used to analyze the spatial orientation of the abnormal area relative to the borehole. Finally, a cylindrical detection area is formed, centered on the borehole and within a certain radial distance range. The schematic diagram of the detection is shown in Figure 11.
4.3.2 Analysis of detection data
Due to the instability of the borehole wall after the hydraulic fracturing of the open-hole borehole, the detection instrument encountered resistance during the pushing process, and the detection depth was shallower than that before the fracturing. In this experiment, there were only 192 valid data points available for analysis, ranging from 50 to 239 m, which covered the fracturing areas of the sixth and fifth sections. Through comparative analysis, the boundaries and grade standards for abnormal division were determined, and appropriate colors and their transitions were corresponding to them. It is agreed that the normal value of the apparent resistivity is set to zero. When the abnormal value of the apparent resistivity is less than or equal to zero, it is the low-resistance boundary. Green indicates a low-resistance anomaly (or water-rich area), orange or colorless indicates a high-resistance anomaly (weakly water-bearing or water-free area), and other intermediate colors indicate the transition area from low-resistance to high-resistance anomalies. Figure 12 shows the processing results of the borehole transient electromagnetic method for extracting the pure abnormal field before and after the fracturing. In the result graph, the abscissa represents the detection distance (the starting point corresponds to a borehole depth of 0 m), and the ordinate represents the radial distance of the borehole. The blue and green parts in the graph are the low-resistance abnormal areas. The darker the color, the greater the change of the resistivity towards the lower value.
According to the strength and continuity of the anomalies, it can be divided into three abnormal areas. The No. 1 abnormal area is located in the interval of 10–20 m in borehole depth, and the center of the anomaly is mainly concentrated around 15 m in borehole depth. Its abnormal range is relatively large, and the anomaly intensity is strong. Considering all factors, it is believed that this area is caused by the water content in the rock formation due to fracturing. The No. 2 abnormal area is located in the interval of 20–50 m in borehole depth, and the center of the anomaly is mainly concentrated around 35 m in borehole depth. Its abnormal range is small, and the local banding is obvious. Considering all factors, it is believed that this area is caused by the water content in the rock formation due to the fracturing of the sixth section. The No. 3 abnormal area is located in the interval of 80–100 m in borehole depth, and the center of the anomaly is mainly concentrated around 90 m in borehole depth. Its abnormal range is large, and the banding is relatively obvious. Considering all factors, it is believed that this area is caused by the water content in the rock formation due to the fracturing of the fifth section.
Judging from the extracted pure abnormal areas, the abnormal areas take the fracturing section as the radiation source point and show obvious banded shapes. Moreover, the farthest development distance of the bands along the radial direction of the borehole is 30 m. In terms of the orientation of the abnormal areas relative to the borehole, the No. 1 and No. 2 abnormal areas are located below the borehole, while the No. 3 abnormal area is located above the borehole. By conducting detections before and after the hydraulic fracturing project respectively, the delineated low-resistance abnormal areas basically correspond to the positions of the hydraulic fracturing sections. The borehole transient electromagnetic method can be used to determine the influence range of hydraulic fracturing.
5 Conclusion
(1) The analysis of the pumping stress curve of the main fracturing borehole shows that its fracture stress ranges from 8.2 to 9.6 MPa, and it shows a gradually decreasing trend from the bottom to the orifice of the borehole. During the fracture stage, there are multiple stress drops with different amplitudes, and the amplitude of the first stress drop is the largest, which reflects the generation, expansion, and communication of the fractures in the rock formation and coal seam.
(2) There is a significant difference in the gas extraction effect between the fractured boreholes and the natural gas extraction boreholes. The average gas extraction concentration of the fractured boreholes reaches 54.37%, with the highest being 68%. The average extraction concentration of the comparison boreholes is only 9.7%, with the highest being 18%. Although the comprehensive flow rate of the fractured boreholes fluctuated in the early stage, it quickly climbed to around 0.85 m3/min and stabilized within the relatively high range of 0.6–0.8 m3/min. The comprehensive flow rate of the unfractured comparison boreholes increased slowly, and the highest value did not exceed 0.7 m3/min, lingering mostly between 0.2 and 0.4 m3/min. Compared with the natural gas extraction boreholes, the comprehensive gas flow rate of the fractured boreholes has been significantly increased, with a year-on-year growth of approximately 200%–300%.
(3) The influence range of hydraulic fracturing is determined through the transient electromagnetic detection technology in the borehole. The abnormal areas are distributed in a banded pattern with the fracturing section as the radiation source. The farthest development distance of the bands along the radial direction of the borehole reaches 30 m. The low-resistance abnormal areas basically correspond to the positions of the hydraulic fracturing sections, indicating that this technology can effectively form a fracture area with a considerable influence range.
Data availability statement
The original contributions presented in the study are included in the article/Supplementary Material, further inquiries can be directed to the corresponding author.
Author contributions
ZZ: Conceptualization, Methodology, Writing – original draft. JQ: Funding acquisition, Writing – original draft. SY: Conceptualization, Funding acquisition, Writing – original draft. KZ: Project administration, Supervision, Writing – original draft. DZ: Methodology, Writing – review and editing. JZ: Supervision, Writing – review and editing.
Funding
The author(s) declare that financial support was received for the research and/or publication of this article. This study was financially supported by the Natural Science Foundation of Shandong Province (7R2022QE243, 2R202AME097).
Acknowledgments
The authors also thank the editor and reviewers for useful advice.
Conflict of interest
Authors ZZ, JQ, and DZ were employed by CHN Energy Shendong Coal Group Co., Ltd. Authors SY, KZ, and JZ were employed by CCTEG Xi’an Research Institute (Group) Co., Ltd.
Generative AI statement
The author(s) declare that no Generative AI was used in the creation of this manuscript.
Publisher’s note
All claims expressed in this article are solely those of the authors and do not necessarily represent those of their affiliated organizations, or those of the publisher, the editors and the reviewers. Any product that may be evaluated in this article, or claim that may be made by its manufacturer, is not guaranteed or endorsed by the publisher.
Supplementary material
The Supplementary Material for this article can be found online at: https://www.frontiersin.org/articles/10.3389/feart.2025.1610921/full#supplementary-material
References
Atkinson, G., Eaton, D., and lgonin, N. (2020). Developments inunderstanding seismicity triggered by hydraulic fracturing. Nat. Rev. Earth Environ., 1(5), 264–277.
Chen, B., Li, S., and Tang, D. Z. (2025). Numerical simulation study on hydraulic fracture propagation of multi-cluster fracturing of horizontal well in deep fractured coal seams. Eng. Fract. Mech. 318, 110983. doi:10.1016/j.engfracmech.2025.110983
Dai, H., Yin, T. B., Wu, Y., Chen, Y., Ma, J., and Li, X. (2024). A study of geothermal hydraulic fracture surface morphology and heat transfer characteristics. Energy 312, 133527. doi:10.1016/j.energy.2024.133527
Fu, J. W., Fu, X. H., Liu, Q., et al. (2018). Study on key technologies of systematic gas control in low-permeability and highly outburst-prone coal seams. China Saf. Sci. J. 28 (7), 109–115.
Gao, S. J., Yang, Y., Chen, M., Zheng, J., Qin, L., Liu, X., et al. (2024). Hydraulic fracture parameter inversion method for shale gas wells based on transient pressure-drop analysis during hydraulic fracturing shut-in period. Energy Eng. 121 (11), 3305–3329. doi:10.32604/ee.2024.053622
Ghanbari, E., and Dehghanpour, H. (2016). The fate of fracturingwater: a field and simulation study. Fuel 163 (1), 282–294. doi:10.1016/j.fuel.2015.09.040
He, B., Lei, P. X., and Gong, Z. B. (2021). Application of hydraulic fracturing technology in working face 52502 of daliuta coal mine. Coal Sci. Technol. 49 (S2), 78–84.
Ismail, A., and Azadbakht, S. (2024). A comprehensive review of numerical simulation methods for hydraulic fracturing. Int. J. Numer. Anal. Methods Geomechanics 48 (5), 1433–1459. doi:10.1002/nag.3689
Jiang, B. C. (2024). Using borehole radar detecting hydraulic fracturing crack in near horizontal holes in coal mine. Front. Earth Sci. 12, 1253315. doi:10.3389/feart.2024.1253315
Kang, J. Q., Kuo, J., Fu, X. H., et al. (2024). Study on the propagation of hydraulic fractures in steeply dipping coal reservoirs. Saf. Coal Mines 55 (11), 49–60.
Kong, X. G., Zhan, M. Z., Lin, H. F., Cai, Y., Ji, P., He, D., et al. (2024). Time-varying characteristics of acoustic emission and fractals based on information dimension during structural failure of coal subjected to uniaxial compression. Measurement 236, 115088. doi:10.1016/j.measurement.2024.115088
Li, H. T., Li, X. L., Fu, J. H., Zhu, N., Chen, D., Wang, Y., et al. (2023). Experimental study on compressive behavior and failure characteristics of imitation steel fiber concrete under uniaxial load. Constr. Build. Mater. 399 (8), 132599. doi:10.1016/j.conbuildmat.2023.132599
Li, J. L., Zhong, Y., Yan, Y. H., Huang, T., Mou, Q., and Yang, B. (2025a). Mechanism of hydraulic fracture propagation and the uneven propagation behavior of multiple clusters in shale oil reservoirs. Fuel 395 (4), 135241. doi:10.1016/j.fuel.2025.135241
Li, S. G., He, D., Kong, X. G., Lin, H., Ma, Y., Li, X., et al. (2024a). Relationship between micro-pores fractal characteristics about NMR T2 spectra and macro cracks fractal laws based on box dimension method of coal under impact load from energy dissipation theory. Chaos, Solit. & Fractals 189, 115685. doi:10.1016/j.chaos.2024.115685
Li, X. L., Cao, Z. Y., and Xu, Y. L. (2025b). Characteristics and trends of coal mine safety development. Energy Sources, Part A Recovery, Util. Environ. Eff. 47 (1), 2316–2334. doi:10.1080/15567036.2020.1852339
Li, X. L., Chen, D. Y., Li, Z., Liu, S., Zhai, M., et al. (2024b). Roadway portal and self-moving hydraulic support for rockburst prevention in coal mine and its application. Phys. Fluids 36 (12), 124136. doi:10.1063/5.0243798
Liu, S. M., Li, X. L., Li, Z. H., Chen, P., Yang, X., and Liu, Y. (2019). Energy distribution and fractal characterization of acoustic emission (AE) during coal deformation and fracturing. Measurement 136 (3), 122–131. doi:10.1016/j.measurement.2018.12.049
Liu, S. M., Li, X. L., Wang, D. K., and Zhang, D. (2025). Investigations on the mechanism of the microstructural evolution of different coal ranks under liquid nitrogen cold soaking. Energy Sources, Part A Recovery, Util. Environ. Eff. 47 (1), 2596–2612. doi:10.1080/15567036.2020.1841856
Liu, S. M., Sun, H. T., Zhang, D. M., Yang, K., Li, X., Wang, D., et al. (2023). Experimental study of effect of liquid nitrogen cold soaking on coal pore structure and fractal characteristics. Energy 275 (7), 127470. doi:10.1016/j.energy.2023.127470
Liu, T., Lin, B. Q., Fu, X. H., Zhao, Y., Gao, Y., and Yang, W. (2021a). Modeling coupled gas flow and geomechanics process in stimulated coal seam by hydraulic flushing. Int. J. Rock Mech. Min. Sci. 142 (6), 104769. doi:10.1016/j.ijrmms.2021.104769
Liu, Y. J., Li, X. L., Li, J. G., Chen, P., and Yang, T. (2021b). Experimental study on variation laws of coal surface potential during gas adsorption. Energy Sources Part A-Recovery Util. Environ. Eff. 43 (5), 634–643. doi:10.1080/15567036.2019.1630518
Luo, M. K., Cui, S. J., Zhou, X. H., Li, S., and Fan, C. (2024). Experimental study on permeability enhancement of coal seam with high mineral content by acid fracturing. Energy Sources Part A-Recovery Util. Environ. Eff. 46 (1), 7770–7783. doi:10.1080/15567036.2020.1758854
Ma, D., Rezania, M., Yu, H. S., and Bai, H. B. (2017). Variations of hydraulic properties of granular sandstones during water inrush: effect of small particle migration. Eng. Geol. 217 (1), 61–70. doi:10.1016/j.enggeo.2016.12.006
Ma, W. W., Li, J. T., and Liang, W. X. (2019). Experimental study on application of directional staged hydraulic fracturing permeability enhancement device in coal seam. Coal Sci. Technol. 47 (5), 132–138.
Manjunath, G. L., Liu, X. Q., and Jha, B. (2023). Multi-stage hydraulic fracture monitoring at the lab scale. Eng. Fract. Mech. 289 (9), 109448. doi:10.1016/j.engfracmech.2023.109448
Niu, T. H. (2022). Study on surrounding rock control technology of weakening hard roof in mining stope by staged hydraulic fracturing. Coal Sci. Technol. 50 (8), 50–59.
Su, X. B., Song, J. X., Guo, H. Y., et al. (2020). Production-increasing mechanism and key technologies of coal mine gas extraction. Coal Sci. Technol. 48 (12), 1–30.
Sun, H., He, N., and Gurkalo, F. (2024). Application and researchof microseismic monitoring system and hydraulic fracturing technology in coal mines. Water 16 (7), 1062. doi:10.3390/w16071062
Tan, Y., Wang, Y., He, M. C., et al. (2025). Technology of multi-dimensional staged hydraulic fracturing for controlling rock bursts and reducing damages of hard roofs in deeply buried and extra-thick coal seams. J. China Coal Soc. 50 (2), 794–809.
Wang, F. C., Wang, E. M., Chang, B., et al. (2023b). Study on the fracture creation law and mechanism of hydraulic fracturing in steeply inclined coal seams. Min. Saf. Environ. Prot. 50 (3), 18–22.
Wang, K., Zhang, G. D., Du, F., Wang, Y., Yi, L., and Zhang, J. (2023a). Simulation of directional propagation of hydraulic fractures induced by slotting based on discrete element method. Petroleum 9 (4), 592–606. doi:10.1016/j.petlm.2022.04.007
Wang, Y. F. (2024). Application of hydraulic fracturing for permeability enhancement in mine gas control. Energy Energy Conservation 11 (3), 294–296.
Wang, X., Jiang, T., Zhu, C., Wei, Y., and Jiang, Y. (2025). Mechanical manifestation characteristics and damage evolution law of unloading perturbation damage in surrounding rock of deep roadways. Geomech. Geophys. Geo-energ. Geo-resour. 11, 35. doi:10.1007/s40948-025-00956-0
Wei, G. M., Hu, W., Jun, D., Li, Z., Fan, S., Lei, C., et al. (2021). Enhanced coalbed permeability and methane recovery via hydraulic slotting combined with liquid CO2 injection. Process Saf. Environ. Prot. 147 (3), 234–244. doi:10.1016/j.psep.2020.08.033
Wei, J. G., Huang, S. P., Hao, G. W., Li, J., Zhou, X., and Gong, T. (2020). A multi-perforation staged fracturing experimental study onhydraulic fracture initiation and propagation. Energy Explor. Exploitation 38 (6), 2466–2484. doi:10.1177/0144598720914991
Wen, G. C., Yang, S., and Cao, J. (2022). Experimental study on the influence of water sensitivity damage on the permeability enhancement effect of hydraulic fracturing in coal seams. Min. Saf. Environ. Prot. 49 (4), 65–71.
Xue, Y., Dang, F. N., Li, R. J., et al. (2018). Seepagestress-damage coupled model of coal under geo-stress influence. Tunn. Undergr. Space Technol. 54 (1), 43–59.
Yang, F., Li, B., Wang, K. J., Wen, H., Yang, R., and Huang, Z. (2024). Extreme massive hydraulic fracturing in deep coalbed methane horizontal wells: a case study of the Linxing Block, eastern Ordos Basin, NW China. Petroleum Explor. Dev. 51 (2), 440–452. doi:10.1016/s1876-3804(24)60035-2
Yang, X. L., Wen, G. C., Lu, T. K., Wang, B., Li, X., Cao, J., et al. (2020). Optimization and field application of CO2 gas fracturing technique for enhancing CBM extraction. Nat. Resour. Res. 29 (3), 1875–1896. doi:10.1007/s11053-019-09563-9
Yao, M. Y., Yang, H., Xia, Y. J., Chen, J., and Tang, C. (2025). Optimization of multiple hydraulic fracture initiation and propagation in deep tight reservoirs considering fracture macro/micro characteristics. Int. J. Rock Mech. Min. Sci. 191, 106126. doi:10.1016/j.ijrmms.2025.106126
Zeng, Q. D., Bo, L., Liu, L. J., Li, X., Sun, J., Huang, Z., et al. (2023). Analysis of fracture propagation and shale gas production by intensive volume fracturing. Appl. Math. Mechanics-English Ed. 44 (8), 1385–1408. doi:10.1007/s10483-023-3021-6
Zhai, H. L., Zhang, H., Pan, D. B., Zhu, Y., Zhu, J., Zhang, Y., et al. (2020). Optimisation of hydraulic fracturing parameters based on cohesive zone method in oil shale reservoir with random distribution of weak planes. J. Nat. Gas Seience Eng. 75 (3), 103130–103213. doi:10.1016/j.jngse.2019.103130
Zhang, C. L., Liu, M. L., Wang, E. Y., et al. (2024a). Study on influence law and control mechanism of coal seam permeability on coal and gas outburst. J. China Coal Soc. 49 (12), 4842–4854.
Zhang, D. X., Wu, C. X., Shi, Z. J., Li, Y., and Zhao, Y. (2024b). A fluid-solid coupling model for hydraulic fracture of deep coal seam based on finite element method. Phys. Fluids 36 (6), 66609. doi:10.1063/5.0213223
Keywords: hydraulic fracturing, gas drainage, coal seam permeability enhancement, effective radius, segmental hydraulic fracturing
Citation: Zhang Z, Qiao J, Yang S, Zheng K, Zhang D and Zhang J (2025) A study on the technology of enhancing gas permeability and gas drainage by sectional hydraulic fracturing in directional long boreholes: a case study of the no. 8 coal seam in baode coal mine. Front. Earth Sci. 13:1610921. doi: 10.3389/feart.2025.1610921
Received: 13 April 2025; Accepted: 05 May 2025;
Published: 23 May 2025.
Edited by:
Krzysztof Skrzypkowski, AGH University of Krakow, PolandReviewed by:
Zechao Chang, China University of Mining and Technology, ChinaXinfeng Wang, Xiangtan University, China
Copyright © 2025 Zhang, Qiao, Yang, Zheng, Zhang and Zhang. This is an open-access article distributed under the terms of the Creative Commons Attribution License (CC BY). The use, distribution or reproduction in other forums is permitted, provided the original author(s) and the copyright owner(s) are credited and that the original publication in this journal is cited, in accordance with accepted academic practice. No use, distribution or reproduction is permitted which does not comply with these terms.
*Correspondence: Sen Yang, eWFuZ3NlbkBjY3RlZ3hpYW4uY29t