- Center of Excellence in Robotics and Control, Advanced Robotics and Automated Systems (ARAS), Department of Mechanical Engineering, K. N. Toosi University of Technology, Tehran, Iran
Tendon-Driven Continuum Robots are widely recognized for their flexibility and adaptability in constrained environments, making them invaluable for most applications, such as medical surgery, industrial tasks, and so on. However, the inherent uncertainties and highly nonlinear dynamics of these manipulators pose significant challenges for classical model-based controllers. Addressing these challenges necessitates the development of advanced control strategies capable of adapting to diverse operational scenarios. This paper presents a centralized position control strategy using Deep Reinforcement Learning, with a particular focus on the Sim-to-Real transfer of control policies. The proposed method employs a customized Modified Transpose Jacobian control strategy for continuum arms, where its parameters are optimally tuned using the Deep Deterministic Policy Gradient algorithm. By integrating an optimal adaptive gain-tuning regulation, the research aims to develop a model-free controller that achieves superior performance compared to ideal model-based strategies. Both simulations and real-world experiments demonstrate that the proposed controller significantly enhances the trajectory-tracking performance of continuum manipulators. The proposed controller achieves robustness across various initial conditions and trajectories, making it a promising candidate for general-purpose applications.
1 Introduction
The advancement of Tendon-Driven Continuum Robots (TDCRs) presents a significant opportunity to enhance precision and adaptability in applications such as medical devices, flexible manufacturing systems, and exploratory robotics (Burgner-Kahrs et al., 2015). These robots, characterized by their continuous and flexible structures, offer superior dexterity compared to traditional rigid robots, making them ideal for navigating complex and constrained environments. However, their control remains a significant challenge due to their high degrees of freedom (DOF) and nonlinear dynamics (Chikhaoui and Burgner-Kahrs, 2018). Addressing these challenges requires innovative control strategies capable of handling the inherent complexities of TDCRs (George Thuruthel et al., 2018; Wang X. et al., 2021).
Traditional control methods often struggle with the high-dimensional and nonlinear nature of TDCRs, necessitating the exploration of advanced techniques such as Reinforcement Learning (RL). RL has emerged as a promising approach due to its capacity to handle complex, high-DOF systems without requiring precise analytical models. For example, the application of Deep Deterministic Policy Gradient (DDPG) in controlling a spatial three-section continuum robot demonstrated superior trajectory-tracking performance, with a maximum error of only 1 mm compared to traditional methods (Djeffal et al., 2024). Similarly, Fuzzy Reinforcement Learning (FRL) has shown effectiveness in trajectory tracking under varying conditions, leveraging robust Cosserat rod-based modeling (Goharimanesh et al., 2020). These studies underscore the potential of RL in overcoming the limitations of conventional controllers, particularly in tasks demanding high precision.
Beyond TDCRs, RL has been successfully applied in soft robotics to address similar challenges. Visual learning-based controllers, for instance, have been utilized for soft robotic fish, enabling flexible and cost-effective designs by reducing reliance on complex curvature-sensing electronics (Rajendran and Zhang, 2022). Similarly, model-free RL methods have been shown to enhance task performance in soft continuum robots across tasks like reaching, crank rotation, and peg-in-hole operations (Morimoto et al., 2022). These advancements highlight the adaptability and scalability of RL methods for various robotic systems.
One of the critical challenges in deploying RL-based controllers for continuum robots is the transition from simulation to real-world applications, known as Sim-to-Real transfer. This process is essential for validating RL algorithms in dynamic environments. Robust Sim-to-Real strategies have been developed to address this challenge. For instance, ELFNet demonstrated that policies trained in simulation could be directly applied to real-world scenarios with minimal performance degradation (Morimoto et al., 2021). Similarly, integrated tracking control approaches combining rolling optimization with RL have proven effective in real-time tasks, such as managing space debris (Jiang et al., 2022). These efforts emphasize the importance of incorporating model dynamics and reward design to enhance the stability and efficiency of RL algorithms in real-world applications.
Despite the progress, challenges such as noise processes, state representation, and training stability persist. Comparative studies have shed light on these aspects, providing insights for fine-tuning RL frameworks to improve their robustness and adaptability (Kołota and Kargin, 2023). By addressing these challenges, RL-based controllers can bridge the gap between theoretical advancements and practical utility, paving the way for broader deployment in TDCRs and other high-DOF robotic systems.
Based on previous studies, three general strategies have been considered for employing Deep Reinforcement Learning (DRL) in control systems (Wang S. et al., 2021). The first strategy involves utilizing the DRL agent as a model-free intelligent controller and force distributor, where the agent directly learns the control policy and parameters without relying on any analytical models of the system’s kinetics or kinematics. Although this approach allows for the full utilization of DRL’s capacity, it requires extensive training time and computational resources. The second strategy also employs the DRL agent as a model-free intelligent controller; however, it incorporates the system’s kinematics (e.g., Jacobian matrix) for force distribution. While this strategy reduces complexity compared to the first one, it still imposes a significant computational burden. In contrast, the third strategy, adopted in this study, leverages the DRL agent as an optimal adaptive gain-tuning system for a model-free controller. Instead of directly acting as the primary controller, the DRL agent optimizes the controller’s parameters under various operating conditions, effectively combining the strengths of analytical models (e.g., kinematics) with DRL’s optimization capabilities.
Previous works in this domain have primarily focused on the first and second strategies, where DRL-based controllers were designed to fully or partially replace analytical models. However, the approach in this study follows the third strategy, which takes advantage of both analytical modeling and DRL to achieve efficient and adaptive parameter tuning. Given that extracting forward kinematics equations and calculating the Jacobian matrix for a TDCR is straightforward and can be achieved with reasonable accuracy, completely bypassing this information in favor of a fully model-free DRL approach is unnecessary. Furthermore, utilizing DRL as the main controller is computationally expensive and time-intensive, making it less suitable for real-time applications. Therefore, the selected strategy prioritizes the integration of available analytical models with DRL to achieve a more efficient and practical control solution.
The main contribution of this paper is the proposed Sim-to-Real transfer of control policies, enabling the Modified Transpose Jacobian (MTJ) controller to achieve precise trajectory tracking starting from any arbitrary initial condition and following any desired trajectory in the workspace. Consequently, in this research, DRL is employed as an optimal adaptive gain-tuner system, providing the following advantages.
• Reduced Training Time through Predefined Structure: The time required for training the DRL agent is reduced because the agent benefits from a pre-fixed control structure. Therefore, the algorithm’s effort is only focused on finding the optimal parameters.
• Locally Robust Control with Adaptive Gains: The proposed approach leverages DRL as a gain-tuning mechanism for locally robust PID-based controller (MTJ). This ensures that the control strategy remains robust in local operating conditions while adapting the controller gains optimally for dynamic system requirements.
• Lightweight Neural Network for Real-Time Application: The algorithm results in a simplified and efficient neural network policy, which is lightweight enough to facilitate real-time implementation on hardware systems without compromising performance.
• Improved Stability during Learning: Prior knowledge of the robot and controller allows for the selection of appropriate ranges for the controller parameters, which not only reduces training time but also prevents instability during and after the learning process.
The paper is organized as follows: The Introduction highlights the motivation, background, and relevance of learning-based control for TDCRs. The Basic Discussions section details the simulation model, TDCR redundancy resolution, and the DRL application in control system design. The Proposed Learning-based Controller section integrates the MTJ control strategy with the DDPG algorithm, explaining the strategy and implementation. The Obtained Results section demonstrates the learning process and simulation outcomes, while the Experimental Implementation section validates the approach through real-world tests. The Discussion analyses results, comparing them with similar methods (e.g., FIS-MTJ), and explores potential improvements. Finally, the Conclusions summarize key findings and suggest future research directions. Table 1 provides descriptions of the symbols used in the article.
2 Basic discussions
In this section, the kinematics and kinetics models of the robot are presented, which are used to derive the Jacobian matrix and simulate the system’s behavior in the simulation environment. Subsequently, the redundancy resolution of TDCR is analyzed, forming the basis for enhancing the MTJ algorithm for controlling continuum robots. Finally, the application of DRL in control system design is examined using the DDPG algorithm.
2.1 Kinematics and kinetics modeling
Given the primary focus of this study on the position control of the end-effector within the task-space, forward kinematics refers to the direct mapping from the joint-space to the task-space of the TDCR (passing through the configuration-space). The kinetics model for continuum robots can be categorized as either a dynamics model or a statics model. The dynamics model is a memory-based model and is used for accelerating movements. In contrast, the statics model is memory-less, making it suitable for quasi-static movements (Grassmann et al., 2022; Rucker and Webster, 2011).
This study employs a statics model with the assumption of constant curvature for each subsegment, known as the Piecewise Constant Curvature (PCC) model, selected for its effectiveness in representing continuum robots (Yuan et al., 2019; Rao et al., 2021). The PCC model was used for training the DRL agent and simulating the proposed controller. Compared to the Variable Curvature (VC) model, the PCC model requires significantly less computational cost while maintaining adequate accuracy. The VC model considers the dependence on time (
2.2 TDCR redundancy resolution
One of the most critical issues in tendon-driven and cable-driven robotic systems is preventing tendon slack, or more precisely, maintaining tension in the tendons. This research utilizes the Null-Space Projection Operator (NSPO) of the Jacobian matrix to address this problem. The Jacobian matrix is a crucial tool for analyzing the structural characteristics of robotic systems. By calculating this matrix, the structural properties of TDCRs can be examined. Various methods have been proposed for computing the Jacobian, and in this section, the linear part of this matrix is derived from the forward kinematics equations (Jones and Walker, 2006). The continuum robot studied in this research is a two-segment system, with each segment actuated by three tendons. If the position vector of the end-effector is defined as
For the continuum robot under consideration, this results in a 3 × 6 rectangular matrix. The partial derivatives corresponding to the elements of this matrix are analytically derived using the forward kinematics equations. The null-space of matrix
In TDCRs, the mapping of generalized forces from the joint-space (
In the above equation,
2.3 DRL application in control system design
The goal of solving a problem using DRL is to find an optimal mapping from the state-space to the action-space, known as the policy. The policy dictates the action to be taken by the DRL agent in each state, and the optimal policy aligns perfectly with the rewards received from the environment (Kober et al., 2013; François-Lavet et al., 2018). Initial efforts in development of DRL algorithms assumed a continuous state-space and a discrete action-space, such as the Deep Q-Network (DQN). The basis of this method is to assign a value to the state-action value function (
3 Proposed learning-based controller
This section starts with developing a customized Modified Transpose Jacobian algorithm for continuum robots. Subsequently, the process of designing an optimal adaptive gain-tuning system via DRL is presented.
3.1 Customized MTJ control algorithm for TDCRs
The MTJ control strategy aims to estimate the system dynamics using the previous time step control input in the task-space, achieving a performance similar to feedback linearization in model-based controllers within the model-free Transpose Jacobian (TJ) control algorithm (Moosavian and Papadopoulos, 2007; Craig, 2018). In this research, a customised MTJ control algorithm for TDCRs is proposed by incorporating the NSPO. The modification in the TJ structure involves adding a modification term, represented by the vector
The control gains (
The modification term (
where
The diagonal elements of matrix K are computed using Equation 7:
where
According to Equation 2, this formulation ensures that the tendons of the robot remain under tension (do not slack) while maintaining the control objective. The null-space adjustment vector (
3.2 Optimal adaptive gain-tuner system design via deep reinforcement learning
Given the explanations provided, this study uses DRL for online tuning of the gains of the model-free MTJ controller. Consequently, the DRL agent is responsible for determining the appropriate values for these gains in real-time. Figure 1 shows the block diagram related to the use of DRL in the MTJ control strategy. Here, the DRL agent’s task is to determine the suitable values for the control gains in the
In the application of DRL to engineering problems, the reward function, state-space (observations), and action-space must first be defined. The following sections describe these elements for the problem of optimally tuning the MTJ controller gains for the position control of the end-effector in the TDCRs.
1) State Space: After trial and error and consideration of various variables, the position of the end-effector, position error, and the joint-space forces (tendon tensions) are defined as the system states in Equation 9:
2) Action Space: Given the objective for the DRL agent (to optimally tune the controller gains), the actions, or outputs of the DRL policy, are defined in Equation 10:
3) Reward Function: Based on the information obtainable from the environment (plant), the reward function is defined as a combination of the sum of squared errors (SSE) and a penalty function related to the controller gains, as defined in Equation 11:
In the above equation,
4) Actor and Critic Network Structures: The study employed Multi-Layer Perceptron (MLP) neural network architectures for both the actor (policy approximator) and critic (value function approximator) components. The actor network, responsible for determining the optimal actions, processes the input state through several layers. Specifically, it starts with an input layer (observation), followed by three fully-connected layers each with 36 neurons and ReLU activation functions. The final layer is a fully-connected layer with nine neurons, followed by a Tanh activation function and a scaling layer to produce the action output. Conversely, the critic network evaluates the value of state-action pairs. It takes the state and action as inputs, which are processed through a series of fully-connected layers with ReLU activations. The state input goes through two fully-connected layers each with 36 neurons and ReLU activations, while the action input is processed by one fully-connected layer with 36 neurons and a ReLU activation. These streams are then concatenated and passed through two more fully-connected layers, each with 36 neurons and ReLU activations, before reaching the output layer. The final output layer is a single neuron that represents the Q-value, indicating the value of the state-action pair.
To enhance the robustness of the neural network resulting from the execution of the DDPG algorithm, which maps the state-space to the action-space (policy), the reference point in the control loop and the initial conditions of the system (tendon tensions at the start of the simulation) are randomized in each episode.
4 Obtained results
The obtained results from the learning process are presented in this section. The trained agent is ultimately employed as an optimal adaptive gain-tuning system in the simulation environment, and its performance in trajectory tracking is evaluated.
4.1 Learning process results
Figure 2A shows the changes in discounted rewards per episode and their averages, as obtained by the DRL agent. Since all rewards in the defined reward function are negative, the ideal outcome would be to find a policy that results in a reward of zero throughout the episode. As depicted, after approximately 700 episodes, the DRL agent has nearly succeeded in estimating the optimal policy.
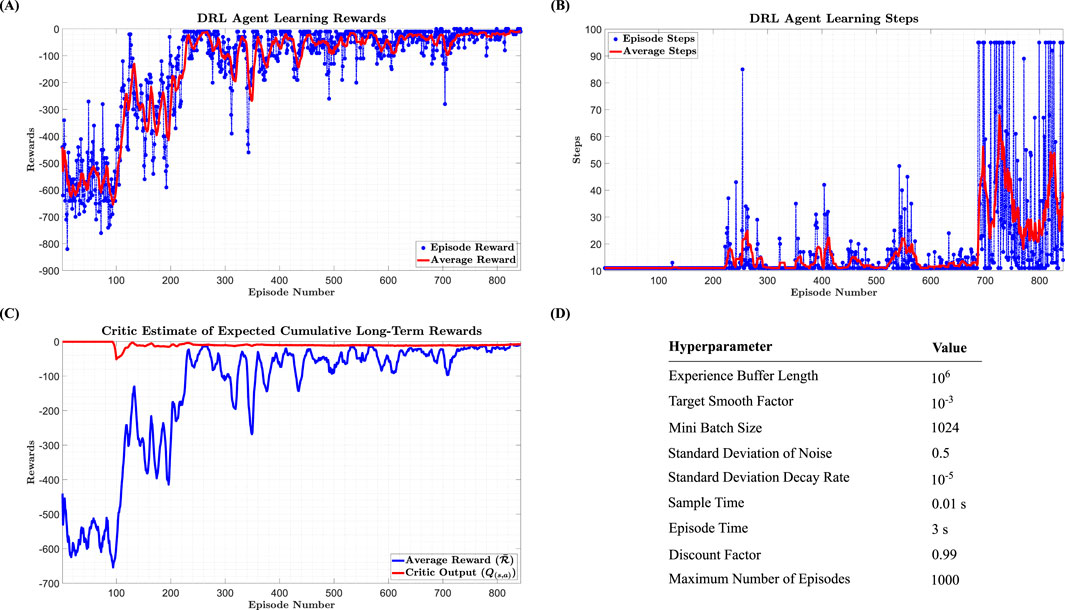
Figure 2. (A) Changes in discounted rewards received in each episode and their average (B). Changes in the number of steps taken in each episode by the DRL agent and their average (C). Comparison of the average sum of discounted rewards with the value function estimated by the critic network (D). Values considered for the hyperparameters of the DDPG algorithm.
The graph in Figure 2B presents the number of steps taken in each episode by the DRL agent and their averages. The results of this graph provide additional evidence for the success of the DRL agent in estimating the optimal policy. After about 700 episodes, the number of steps taken in each episode increases. This indicates that the episode termination condition (defined based on unfavorable conditions for the DRL agent) has not been activated.
Figure 2C compares the average sum of discounted rewards with the value function estimated by the critic network. This graph provides key evidence of the DRL agent’s success in estimating the optimal policy. According to the figure, the value function estimated by the critic network reaches a steady state after about 400 episodes, suggesting that the expected return of rewards received during each episode has stabilized. Referring to the graph of the average rewards, after about 700 episodes, the actor network has succeeded in finding the optimal policy, as the average sum of discounted rewards has nearly equaled the output of the critic network (which represents the value function or the expected return of rewards received during each episode). The hyperparameters considered for the algorithm are presented in the table of Figure 2D.
4.2 Simulation results
To evaluate the performance quality of the DRL agent in tuning the controller gains, the trajectory designed by (Maghooli et al., 2023) to assess the FIS-MTJ strategy is considered, as expressed in Equation 12:
where
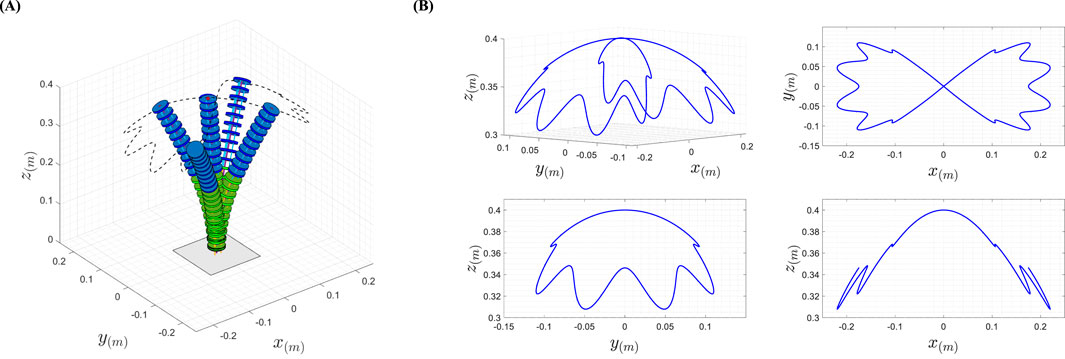
Figure 3. (A) A visualization of the robot movement in the MATLAB environment (B). Reference path obtained from the designed trajectory for the TDCR in 3D Space.
By simulating the performance of the designed control systems to follow this path using the PCC model, the following results were obtained. In Figure 4, the trajectory-tracking quality of the MTJ controller with gains tuned by the DRL agent and the FIS is shown. Figure 4A presents the graphs of the controller gains, adjusted in real-time by the DRL agent during trajectory tracking, compared to those provided by the FIS. The results for the x-direction are displayed, with similar results obtained for the other coordinates. A notable observation in the results is the variation in control gains by the DRL agent compared to the FIS over the simulation period. Specifically, the FIS provides nearly constant gains for a specific path throughout the simulation, while the DRL agent updates the gains at each time step, striving to provide the most suitable gains for the current state of the robot. To better understand the performance of the controllers, the root mean square error (RMSE) is calculated throughout the simulation.
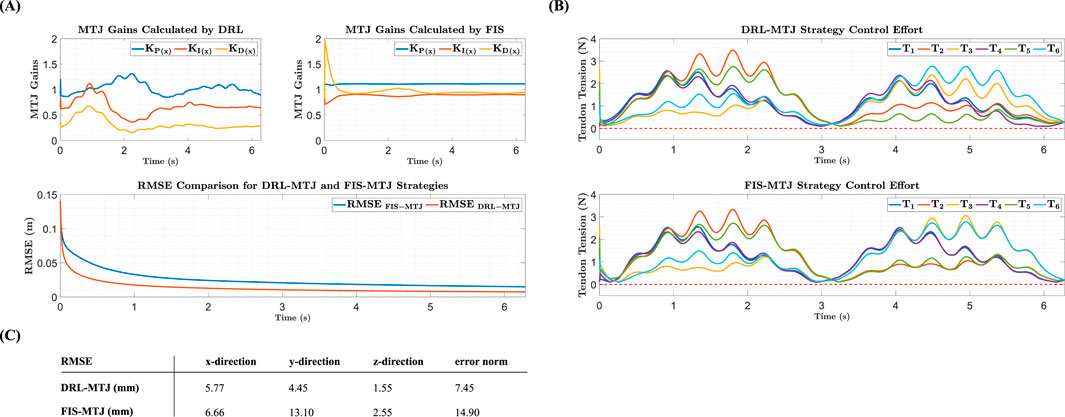
Figure 4. (A) Comparison of controller gains and trajectory-tracking quality between FIS-MTJ and DRL-MTJ strategies (B). Comparison of tendon tension for both strategies (C). Comparison of the RMSE for both strategies.
The tendon tension graphs for both strategies are shown in Figure 4B. As observed, the tendon tensions are almost within the same range in terms of magnitude, indicating better management by the DRL agent compared to the FIS in optimally tuning the control gains and minimizing the error. According to the obtained values presented in Figure 4C, using DRL compared to the FIS halves the RMSE in trajectory tracking, with values of 14.90 mm for FIS and 7.45 mm for DRL.
5 Experimental implementation
This section begins by introducing the mechanical structure, electronic hardware, actuators, and sensors of the continuum robot developed in the ARAS laboratory. Subsequently, the challenges of transferring learning results from the simulation environment to the real world are discussed, and the validation of the Jacobian matrix for force distribution in the control loop is examined. Finally, the outcomes of transferring learning from the simulation to the real-world environment are evaluated.
5.1 Introduction to continuum robotic arm
The continuum robotic arm developed at the ARAS robotics laboratory (Robo-Arm) is a tendon-driven system with external actuation, as shown in Figure 5. The main components of the system are described below.
• Backbone: The backbone forms the main structure of the arm and is made of a nickel-titanium alloy (Nitinol). Nitinol is a shape-memory alloy, and its super-elasticity is the primary reason for its use as the central backbone of the system.
• Robot Main Board: The robot board serves as an interface between the computer and the system’s actuators and sensors. All control commands to the servomotors and data received from the load cells are transmitted via the board through serial communication between the robot and the computer. The only exception is the cameras, whose data is directly transferred to the computer via USB ports.
• Spacer Disks: Spacer disks made of plexiglass are placed along the backbone to guide the tendons parallel to the central backbone. These disks also convert the tendon tension into a concentrated moment at the end of each segment, where the tendons attach to the backbone.
• Tendons: The tendons, with a maximum allowable tension of 394 Newtons, transfer force and ultimately convert it into concentrated moment at the end of each segment. When selecting the tendon material, inextensibility and flexibility are important characteristics, in addition to high maximum tension, as these significantly affect the system’s power transmission performance.
• Servomotors: The actuators for the continuum robotic arm are Dynamixel servomotors (model AX-12A), which offer two modes: joint and wheel. These modes allow for position (
• Load Cells: Real-time information on tendon tension is essential for the kinetic control of the continuum robotic arm. By using load cells and implementing an inner loop to regulate tendon tension, the system can be kinetically controlled. The selected load cells have a maximum force capacity of 30 kg-force, which is approximately 294 Newtons.
• Cameras: To determine the real-time position of the continuum robotic arm’s end-effector, two cameras are used to observe the robot’s movement in the
5.2 Sim-to-real gap considerations
One key difference between simulation and real-time implementation of this robotic system is the nature (dimension) of the input signals to the plant. In the simulation environment, the input to the system is the tendon tensions, and kinetic control is performed by determining these inputs. Conversely, in the hardware of the Robo-Arm, kinematic actuators (Dynamixel servomotors) are employed. If the input to the system is directly the motor position or velocity, a kinematic control strategy is implemented, which is not ideal for a continuum robot (Centurelli et al., 2022). This claim is supported by three reasons:
Firstly, kinematic control does not account for tendon tension. If the robot body or end-effector collides with the task-space or becomes stuck in the null-space, the controller cannot issue the correct commands to resolve these issues. Secondly, without information on tendon tension, the kinematic controller will not be aware if the tension increases beyond the tendon tolerance thresholds. This can lead to tendon rupture, damage to the spacer disks, or even damage to the robot backbone. Thirdly, the use of the Jacobian transpose as the force distributor is only possible with kinetic control. According to the equation
Based on these reasons, it is evident that the appropriate strategy for position control of the TDCR is kinetic control. Implementing kinetic control, despite having kinematic actuators, involves using a cascaded control structure and creating an inner loop to adjust tendon tensions. In this structure, feedback from load cells is used to calculate the tendon tensions, which are then compared to the desired tension (Equation 8). The tension error is fed into the inner-loop controller (a PID controller), and finally, the command to adjust the motor velocity is sent to the servomotor. The block diagram of the proposed strategy for kinetic control of the TDCR is shown in Figure 6.
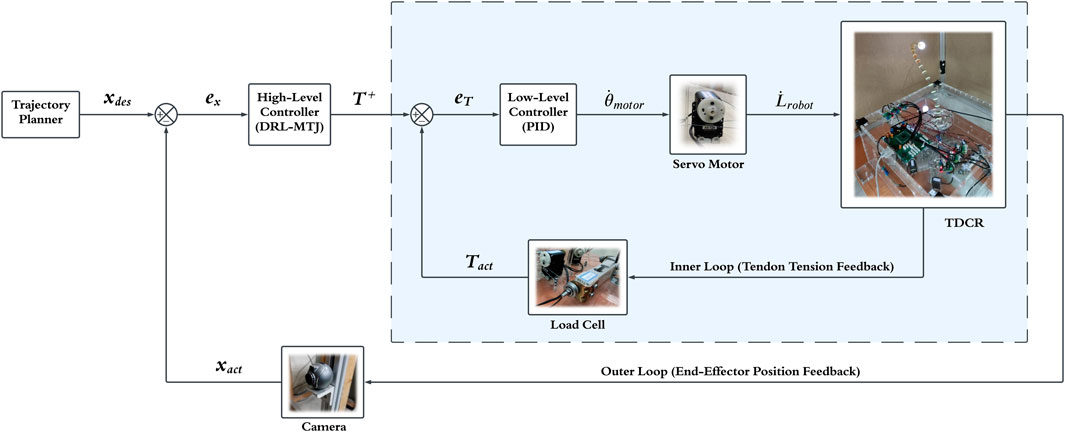
Figure 6. Proposed cascade control structure for kinetic control of the TDCRs in the task-space. Using a PID as the low-level controller (inner loop) and a DRL-MTJ as the high-level controller (outer loop).
5.3 Jacobian validation for force distribution
As previously explained, having the Jacobian matrix for force mapping from the task-space to the joint-space is essential for control in the task-space. This research relies on using the closed form of the Jacobian matrix, which has shown satisfactory results in simulations. Before using these equations, it is necessary to ensure their accuracy and consistency with Robo-Arm for force distribution during real-time implementation.
Before addressing the Jacobian matrix, the validation of the forward kinematics equations (mapping tendon lengths to the end-effector position coordinates) is examined. Harmonic inputs with phase differences are applied to the servomotor angles, and the instantaneous position of the end-effector is recorded by cameras. The tendon lengths (calculated as the product of harmonic inputs and the servomotor pulley radius) are then input into the forward kinematics equations, and the output is compared with the camera measurements. Figure 7A shows the comparison between the camera output and the forward kinematics output for each coordinate of the end-effector in the task-space. Based on the computed RMSEs, the forward kinematics equations, considering the structural and parametric uncertainties of the system, are accurate enough for calculating the Jacobian matrix for force distribution and implementation on hardware.
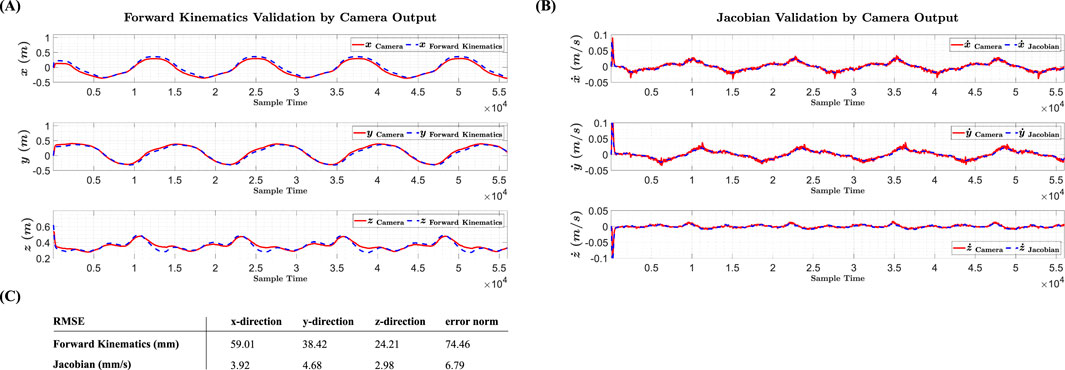
Figure 7. (A, B) Validation results of Forward Kinematics equations and Jacobian matrix using camera data (C). Obtained RMSE from validation process.
After validating the forward kinematics, the Jacobian matrix (which maps the rate of change in tendon lengths to the end-effector velocity) is examined. The derivative of the tendon lengths with respect to time is calculated and multiplied as a vector by the Jacobian matrix, and the output is compared with the derivative of the camera measurements (representing the instantaneous velocity of the end-effector). Figure 7B shows the comparison between the derivative of the camera output and the velocity obtained from the Jacobian for each coordinate of the end-effector in the task-space. According to the results, the Jacobian matrix is accurate enough for implementation on hardware, and its transpose can be used as the force distributor in the MTJ controller structure. The comparison of the RMSEs of the forward kinematics and Jacobian with camera data is presented in Figure 7C.
5.4 DRL policy sim-to-real transfer results
To successfully implement the MLP neural network obtained as the policy on the continuum robotic arm hardware (Robo-Arm), derived from executing the DDPG algorithm in the simulation environment on a PCC model, the simulation model must closely approximate the physical system. This requirement is partially met by ensuring the accuracy of the mass and geometric parameters of the system in the model. However, due to the presence of uncertainties such as friction, hysteresis, and other factors that are challenging to model precisely, it is expected that the results of implementing the policy on the robot will differ somewhat from the simulation. The more effort that is put into accurately modeling these terms, the smaller this discrepancy will be.
To evaluate and compare the performance of the DRL agent in tuning the controller gains, a circular trajectory in the horizontal plane is considered for a fair comparison between DRL and the FIS strategies. The trajectory is defined by Equation 13:
By implementing the designed control systems on the Robo-Arm, the following results are obtained. In Figure 8, the trajectory-tracking quality of the MTJ controller with gains tuned by the DRL agent and the FIS is shown. Figure 8A presents the controller gains graph (x-direction), adjusted in real-time by the DRL agent during trajectory tracking, compared to those provided by the FIS. Similar to the simulation results, the changes in control gains obtained by the DRL agent are more significant than those by the FIS throughout the implementation period. In other words, the DRL agent makes greater efforts to provide more suitable control gains at each time step according to the robot’s state, resulting in a lower RMSE in trajectory tracking.
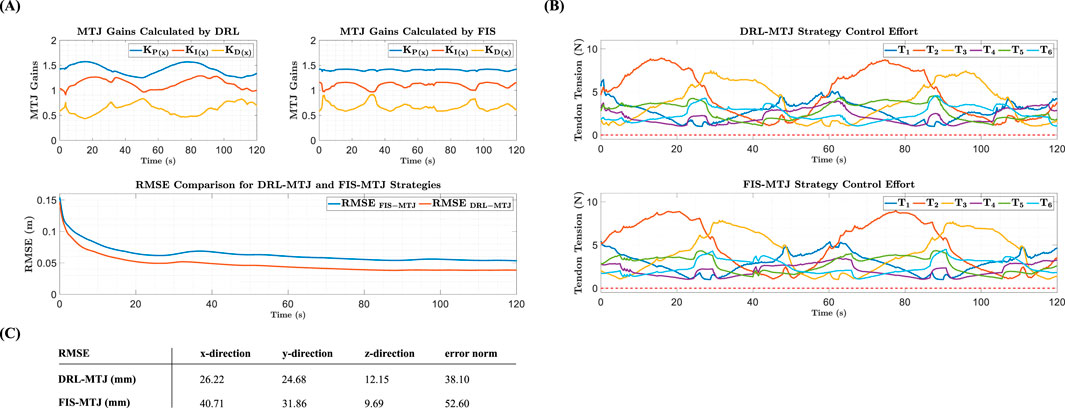
Figure 8. (A) Comparison of controller gains and trajectory-tracking quality between FIS-MTJ and DRL-MTJ strategies (B). Comparison of tendon tension for both strategies (C). Comparison of the RMSE for both strategies.
Figure 8B shows the tendon tension graphs for both strategies. The results indicate that the tendon tensions are almost within the same range, demonstrating better management by the DRL agent compared to the FIS in tuning the control gains and minimizing the error. To better illustrate the performance of the controllers, the obtained RMSE for each coordinate for both strategies are presented in Figure 8C. According to the obtained values, using DRL compared to the FIS significantly reduces the RMSE in trajectory-tracking (38.10 mm for DRL and 52.60 mm for FIS).
6 Discussion
In this study, the primary objective was to design an optimal adaptive gain-tuning system to enhance the performance of a customized MTJ controller for TDCRs. The results achieved in the trajectory-tracking problem, when compared to the application of a FIS for the same problem, demonstrate improvements in both simulation and real-world implementation. When comparing supervised learning methods (e.g., FIS) with semi-supervised methods (e.g., DRL), it can be stated that both approaches show satisfactory performance and require minimal prior knowledge of the system’s behavior. Specifically, defining membership functions and the rule-base in a FIS necessitates knowledge of appropriate ranges for controller gains. On the other hand, defining states, actions, and rewards in DRL requires an understanding of how these variables affect system performance and their optimal selection within the problem’s context. Notably, the FIS operates online from the outset and does not require prior training. However, the DRL agent can achieve appropriate online performance after a sufficient number of episodes and adequate training of the neural networks within its structure. Ultimately, based on the obtained results and the comparison of RMSE values, the DRL method demonstrates superior performance in tuning the proposed controller gains. Its application in the control of TDCRs results in more accurate following of the reference trajectory with reduced error. The simultaneous control of both position and orientation of a TDCR, leveraging the results of this paper to address shape constraints, has been independently explored in (Maghooli et al., 2024).
7 Conclusion
In this study, a learning-based control strategy was developed and validated by integrating a customized MTJ controller for TDCRs with the DDPG algorithm. The main contribution of this work lies in the effective Sim-to-Real transfer of control policies, enabling the model-free MTJ controller to achieve high-precision trajectory-tracking. The obtained results from both simulation and real-time implementation indicate that the optimal adaptive gain-tuning system significantly enhances controller performance, reducing the RMSE and improving the robustness of the control system. The success of this approach in both simulated and real-world environments underscores its potential for broader applications in medical devices, flexible manufacturing, and exploratory robotics. This work paves the way for more reliable and efficient deployment of TDCRs in real-world scenarios. Future work will focus on further optimizing the learning algorithms and exploring their application to shape estimation and control in continuum robotic arms.
Data availability statement
The original contributions presented in the study are included in the article/Supplementary Material, further inquiries can be directed to the corresponding author.
Author contributions
NM: conceptualization, investigation, methodology, software, validation, visualization, writing – original draft. OM: software, validation, writing – review and editing. MB: software, methodology, writing – review and editing. SAM: supervision, project administration, funding acquisition, resources, writing – review and editing.
Funding
The author(s) declare that no financial support was received for the research and/or publication of this article.
Conflict of interest
The authors declare that the research was conducted in the absence of any commercial or financial relationships that could be construed as a potential conflict of interest.
Publisher’s note
All claims expressed in this article are solely those of the authors and do not necessarily represent those of their affiliated organizations, or those of the publisher, the editors and the reviewers. Any product that may be evaluated in this article, or claim that may be made by its manufacturer, is not guaranteed or endorsed by the publisher.
Supplementary material
The Supplementary Material for this article can be found online at: https://www.frontiersin.org/articles/10.3389/frobt.2025.1488869/full#supplementary-material
References
Burgner-Kahrs, J., Rucker, D. C., and Choset, H. (2015). Continuum robots for medical applications: a survey. IEEE Trans. Rob. 31, 1261–1280. doi:10.1109/TRO.2015.2489500
Centurelli, A., Arleo, L., Rizzo, A., Tolu, S., Laschi, C., and Falotico, E. (2022). Closed-loop dynamic control of a soft manipulator using deep reinforcement learning. IEEE Rob. Autom. Lett. 7, 4741–4748. doi:10.1109/LRA.2022.3146903
Chiaverini, S., Oriolo, G., and Walker, I. D. (2008). Kinematically redundant manipulators. Heidelberg: Springer Handbook of Robotics, 245–268. doi:10.1007/978-3-540-30301-5_12
Chikhaoui, M. T., and Burgner-Kahrs, J. (2018). “Control of continuum robots for medical applications: state of the art,” in ACTUATOR 2018; 16th international conference on new actuators, 1–11.
Dehghani, M., and Moosavian, S. A. A. (2013). Compact modeling of spatial continuum robotic arms towards real-time control. Adv. Rob. 28, 15–26. doi:10.1080/01691864.2013.854452
Djeffal, S., Morakchi, M. R., Ghoul, A., and Kargin, T. C. (2024). DDPG-based reinforcement learning for controlling a spatial three-section continuum robot. Franklin Open 6, 100077. doi:10.1016/J.FRAOPE.2024.100077
François-Lavet, V., Henderson, P., Islam, R., Bellemare, M. G., and Pineau, J. (2018). An introduction to deep reinforcement learning. Found. Trends Mach. Learn. 11, 219–354. doi:10.1561/2200000071
George Thuruthel, T., Ansari, Y., Falotico, E., and Laschi, C. (2018). Control strategies for soft robotic manipulators: a survey. Soft Rob. 5, 149–163. doi:10.1089/soro.2017.0007
Godage, I. S., Branson, D. T., Guglielmino, E., and Caldwell, D. G. (2012). “Path planning for multisection continuum arms,” in 2012 IEEE international conference on mechatronics and automation (ICMA), (IEEE). 1208–1213. doi:10.1109/ICMA.2012.6283423
Goharimanesh, M., Mehrkish, A., and Janabi-Sharifi, F. (2020). A fuzzy reinforcement learning approach for continuum robot control. J. Intell. Rob. Syst. Theory Appl. 100, 809–826. doi:10.1007/s10846-020-01237-6
Grassmann, R. M., Rao, P., Peyron, Q., and Burgner-Kahrs, J. (2022). FAS—a fully actuated segment for tendon-driven continuum robots. Front. Rob. AI 9, 873446. doi:10.3389/frobt.2022.873446
Jiang, D., Cai, Z., Liu, Z., Peng, H., and Wu, Z. (2022). An integrated tracking control approach based on reinforcement learning for a continuum robot in space capture missions. J. Aerosp. Eng. 35, 04022065. doi:10.1061/(ASCE)AS.1943-5525.0001426
Jones, B. A., and Walker, I. D. (2006). Kinematics for multisection continuum robots. IEEE Trans. Rob. 22, 43–55. doi:10.1109/TRO.2005.861458
Kober, J., Bagnell, J. A., and Peters, J. (2013). Reinforcement learning in robotics: a survey. Int. J. Rob. Res. 32, 1238–1274. doi:10.1177/0278364913495721
Kołota, J., and Kargin, T. C. (2023). Comparison of various reinforcement learning environments in the context of continuum robot control. Appl. Sci. 13, 9153. doi:10.3390/APP13169153
Lillicrap, T. P., Hunt, J. J., Pritzel, A., Heess, N., Erez, T., Tassa, Y., et al. (2015). “Continuous control with deep reinforcement learning,” in 4th international conference on learning representations, ICLR 2016 - conference track proceedings. Available online at: https://arxiv.org/abs/1509.02971v6 (Accessed August 19, 2023).
Maghooli, N., Mahdizadeh, O., Bajelani, M., and Moosavian, S. A. A. (2024). “Control of continuum manipulators with shape constraints via deep reinforcement learning,” in 2024 12th RSI international conference on robotics and mechatronics (ICRoM), 631–636. doi:10.1109/ICROM64545.2024.10903601
Maghooli, N., Mahdizadeh, O., and Moosavian, S. A. A. (2023). “Intelligent model-free control for tendon-driven continuum robotic arms,” in 11th RSI international conference on robotics and mechatronics, ICRoM 2023, 606–613. doi:10.1109/ICROM60803.2023.10412410
Moosavian, S. A. A., and Papadopoulos, E. (1997). Control of space free-flyers using the modified transpose Jacobian algorithm. IEEE Int. Conf. Intell. Rob. Syst. 3, 1500–1505. doi:10.1109/IROS.1997.656557
Moosavian, S. A. A., and Papadopoulos, E. (2007). Modified transpose Jacobian control of robotic systems. Automatica 43, 1226–1233. doi:10.1016/J.AUTOMATICA.2006.12.029
Morimoto, R., Ikeda, M., Niiyama, R., and Kuniyoshi, Y. (2022). Characterization of continuum robot arms under reinforcement learning and derived improvements. Front. Rob. AI 9, 895388. doi:10.3389/frobt.2022.895388
Morimoto, R., Nishikawa, S., Niiyama, R., and Kuniyoshi, Y. (2021). “Model-free reinforcement learning with ensemble for a soft continuum robot arm,” in 2021 IEEE 4th international conference on soft robotics, roboSoft 2021, 141–148. doi:10.1109/ROBOSOFT51838.2021.9479340
Rajendran, S. K., and Zhang, F. (2022). Design, modeling, and visual learning-based control of soft robotic fish driven by super-coiled polymers. Front. Rob. AI 8, 809427. doi:10.3389/frobt.2021.809427
Rao, P., Peyron, Q., Lilge, S., and Burgner-Kahrs, J. (2021). How to model tendon-driven continuum robots and benchmark modelling performance. Front. Rob. AI 7, 630245. doi:10.3389/frobt.2020.630245
Rucker, D. C., and Webster, R. J. (2011). Statics and dynamics of continuum robots with general tendon routing and external loading. IEEE Trans. Rob. 27, 1033–1044. doi:10.1109/TRO.2011.2160469
Satheeshbabu, S., Uppalapati, N. K., Fu, T., and Krishnan, G. (2020). “Continuous control of a soft continuum arm using deep reinforcement learning,” in 2020 3rd IEEE international conference on soft robotics, roboSoft 2020, 497–503. doi:10.1109/ROBOSOFT48309.2020.9116003
Wang, S., Wang, R., Liu, M., Zhang, Y., and Hao, L. (2021a). “Review on reinforcement learning controller in soft manipulator,” in 2021 IEEE international conference on robotics and biomimetics, ROBIO, 558–563. doi:10.1109/ROBIO54168.2021.9739342
Wang, X., Li, Y., and Kwok, K. W. (2021b). A survey for machine learning-based control of continuum robots. Front. Rob. AI 8, 730330. doi:10.3389/frobt.2021.730330
Wu, Q., Gu, Y., Li, Y., Zhang, B., Chepinskiy, S. A., Wang, J., et al. (2020). Position control of cable-driven robotic soft arm based on deep reinforcement learning. Information 2020 11, 310. doi:10.3390/INFO11060310
Keywords: tendon-driven continuum robots, modified transpose Jacobian, deep reinforcement learning, deep deterministic policy gradient algorithm, optimal adaptive gain-tuning system, sim-to-real transfer, learning-based control, data-driven control
Citation: Maghooli N, Mahdizadeh O, Bajelani M and Moosavian SAA (2025) Learning-based control for tendon-driven continuum robotic arms. Front. Robot. AI 12:1488869. doi: 10.3389/frobt.2025.1488869
Received: 30 August 2024; Accepted: 21 March 2025;
Published: 14 July 2025.
Edited by:
Hamid Marvi, Arizona State University, United StatesReviewed by:
Ivan Virgala, Technical University of Košice, SlovakiaReza Ahmed, Raytheon Technologies, United States
Copyright © 2025 Maghooli, Mahdizadeh, Bajelani and Moosavian. This is an open-access article distributed under the terms of the Creative Commons Attribution License (CC BY). The use, distribution or reproduction in other forums is permitted, provided the original author(s) and the copyright owner(s) are credited and that the original publication in this journal is cited, in accordance with accepted academic practice. No use, distribution or reproduction is permitted which does not comply with these terms.
*Correspondence: Nima Maghooli, bmltYS5tYWdob29saUB1dC5hYy5pcg==