- 1Aix Marseille University, CNRS, ISM, Marseille, France
- 2UMR7039 Centre de recherche en automatique de Nancy (CRAN), Vandoeuvre LesNancy, Lorraine, France
Tendon-driven continuum robots usually consists of several actuators and cables pulling a flexible backbone. The tendon path alongside the backbone allows to perform complex movements with high dexterity. Yet, the integration of multiple tendons adds complexity and the lack of rigidity makes continuum robots susceptible to torsion whenever an external force or load is applied. This paper proposes a reduced complexity, hybrid tendon-driven continuum robot (HTDCR) that avoids undesired torsion under external load. Bending of the HTDCR is achieved from a single tendon with lateral joints alongside the backbone acting as mechanical constraint on the bending plane. A rotary base then provides an additional degree of freedom by allowing full rotation of the arm. We developed a robot prototype with control law based on a constant curvature model and validated it experimentally with various loads on the tip. Body deviation outside the bending plane is negligible (mm range), thereby demonstrating no torsional deformation. Tip deflection within the bending plane is smaller than the one obtained with a 4-tendon driven continuum robot. Moreover, tip deflection can be accurately estimated from the load and motor input which paves the way to possible compensation. All together, the experiments demonstrate the efficiency of the HTDCR with 450 g payload which makes it suitable in agricultural tasks such as fruit and vegetable harvesting.
1 Introduction
Tendon-driven continuum robots (TDCRs) are characterized by their continuous, flexible structure actuated by tendons or cables that run along the body, enabling smooth and multi-directional movements that depend on factors such as the number of cables, cable routing, number of sections, among others. There has been a growing interest in such highly adaptive mechanical systems capable of operating in unpredictable or constrained spaces with soft interaction with the enviroment, such as encountered in medical or agricultural applications (Russo et al., 2023; Bai et al., 2024). Medicine is currently a key focus of interest and research for TDCRs as their continuum structure can adapt to the human body made up of soft and deformable organs. Additionally, they can be miniaturized to millimeter-scale diameters and centimeter-scale lengths, providing a significant advantage over conventional robots with rigid links in minimally invasive procedures (Veiga et al., 2020). TDCRs have been deployed as steerable cardiac catheter with 3.8 mm diameter and a NiTi rod backbone (Camarillo et al., 2008), for cardiovascular intervensions composed of rolling contact joints with 4.65 mm diameter (Kim et al., 2018), in orthopedic surgery (Alambeigi et al., 2019), intracerebral hemorrhage evacuation (Yan et al., 2022), among others.
Agriculture is an emerging field for TDCRs, holding great potential for navigating through crop fields without causing damage to the plants (Armanini et al., 2024). However, TDCRs flexibility, also implies lower stiffness materials, which can pose challenges in achieving precise positioning under load or in responding to external forces without deformations. This limitation can be particularly problematic for harvesting where, despite the relatively low weight of common fruits (on average, 150 g for peaches, 120 g for pears, and 200 g for apples), external forces can still induce undesired bending or twisting that disrupts the robot’s accuracy. As a result, achieving consistent and controlled interaction with the environment may require compensatory mechanisms, such as advanced feedback systems or structural reinforcements, to mitigate these unintended movements and improve handling precision.
There have been efforts to counteract or compensate the effects of external loads on TDCRs, such as deflection, torsional deformation, buckling and slack cable, to enable their use at larger scales making them more suitable for applications in fields such as agriculture. In (Yeshmukhametov et al., 2020; Yuan and Li, 2018), a pre-tensioning mechanism was used to avoid cable slack in a TDCR with universal joints that aims to harvest cherry tomatoes. There have also been proposals to incorporate mechanisms that restrict the robot’s movements, aiming to enhance stability and control under external loads such as a sliding mechamism as in (Tokunaga et al., 2017), also adding an extra cable attached directly to the tip, without routing it through the tendon paths as a means to provide a compensation (Childs and Rucker, 2021). Efforts have also been made to implement different materials and joints that increase resistance, as demonstrated in (Xiao et al., 2024), where a TDCR with two segments (each 80 mm in length and 70 mm in diameter) utilizes a shape memory alloy (SMA) spring and a gooseneck structure achieving a resistance capacity of 5 N.
Similarly, a novel joint design have been proposed as in (Dong et al., 2015) and (Yang et al., 2021), where the implementation of twin-pivot structures using NiTi rods as elastic joints, enhanced resistance under external loading has been observed. However, such mechanisms have been typically fabricated with a small diameter/length ratio, 15/280 (mm) and 17/150 (mm) respectively, limiting their application to small-scale robotic systems or structures that do not require extensive reach or high load capacity. In Dong et al. (2017), Wang et al. (2021), Yang et al. (2024), tests were conducted on multi-segment TDCRs for inspection/repair of engines by implementing twin-pivot structure and contact-aided compliant mechanisms design concepts with diameter/length ratio of 13–40/1,270 (mm) and 14–16/384 (mm) respectively with load capacity of up to 200g and 300 g with body deformations, showing that implementing longer structures with wider diameters does not necessarily lead to an increase in load capacity.
This paper focuses on a TDCR that could be used in agricultural tasks like fruit or vegetable harvesting, pest or disease detection, pesticide or fertilizer spray, among others. In these tasks, size and precision requirements for the robot are less critical than in medical applications. Most important is that the TDCR should have the ability to carry loads with some flexibility to navigate through crop fields. To prevent torsional deformation under load while maintaining bending flexibility, we propose a hybrid tendon-driven continuum robot (HTDCR) with a rotary base and rigid links alongside a flexible backbone. A unique tendon path allows bending in a plane whose direction is given by the rotary base. Because rigid-link structures offer relatively high precision and load capacity as compared to compliant joints, the HTDCR does not experience any torsion or deviation outside the bending plane.
2 Materials and methods
2.1 HTDCR principle and mechanical design
In tendon-driven continuum robotics, typically flexible materials are used as joints and/or the backbone giving them the capacity of enabling complex movements actuated by cables. Depending on factors such as number of cables and cable routing, the robot can bend in one or several directions. Standard TDCRs require at least two tendons for planar bending and three tendons for spatial bending (Rao et al., 2021). TDCRS are, however, susceptible to deformation under external loads or forces affecting their precision. In classical robotics, revolute joints are commonly used where controlled and precise rotational movements are required. Revolute joints allow relative rotation between two parts joined around a fixed axis, restricting motion to a single degree of freedom, meaning that the body can rotate but cannot translate in other directions.
By combining these two concepts, a hybrid tendon-driven continuum robot (HTDCR) is proposed with revolute joints placed laterally along a flexible backbone. A unique tendon path allows bending the backbone in a plane whose direction is given by the rotary base (Figure 1).
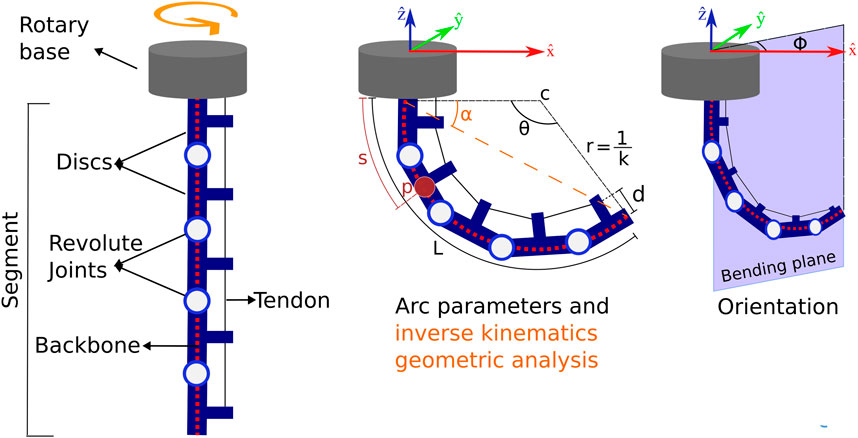
Figure 1. Schematics of the proposed hybrid cable-driven continuum robot (HTDCR) implementing revolute joints and a rotary base. In the constant curvature model, the shape of the backbone is defined by the direction of bending
A prototype of the HTDCR was built from a backbone with 6 sections (Figure 2), each one having a steel spring (inner diameter of 25.6 mm, length of 42 mm, wire diameter of 1.8 mm and spring constant of 2.119 N/mm) encapsulated between two 3D printed discs with ToughPLA. The springs provide stiffness to the robot body (Xing et al., 2021; Santiago et al., 2015; Yoon and Yi, 2009; Gao et al., 2015; Visentin et al., 2019; Qi et al., 2024) and its hollow center allows the integration of cables, tubes, and sensors within their internal structure. Aluminium pins are placed laterally and maintained with snap rings so that the backbone can resist to torsional stress, ensuring more stability during operation when an external force or load is added on the tip. Additionally, the revolute joints create a mechanical constraint that maintains the length of the springs at any time. Thus, there is no elongation or compression of the springs when the tendon is actuated, which results in bending motion only with a stiffness at each joint.
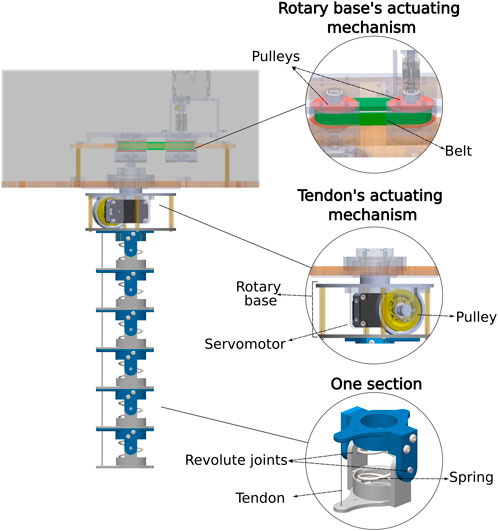
Figure 2. Mechanical design of the proposed HTDCR which implements a belt and pulley system for rotation and a pulley and motor system to actuate the tendon.
To enable bending in one direction, one tendon path is added to the discs and incorporates a steel cable with a diameter of 0.8 mm parallel to the backbone. The tendon is fixed to the tip and wraps around a pulley attached to a DYNAMIXEL XL-430-W250-T servomotor. An adjustment is made to the initial position of the motor to ensure that the cable is taut from the start. Then, the cable remains taut in any bending position because of the revolute joints that prevent elongation or compression of the backbone. This tendon servomotor is fixed to a rotating plate, which allows the body to rotate 360°, providing an additional degree of freedom to the robot. To enable rotation, another DYNAMIXEL XL-430-W250-T servomotor is coupled to a pulley (30T and 48 T) and GT2 belt system is mainly used for impact absorption and motion transmission. The current design does not support multiple rotations of the rotary base. This is to prevent twisting of the power and data cables that supply the servo motor in the rotary base. Moreover, a 360° rotation covers the entire workspace and there is no requirement for having multiple turns. Yet, if needed in future implementations, the use of a rotating connector can accommodate continuous rotation without causing entanglement.
2.2 Constant-curvature kinematic model
A constant curvature model was implemented for the HTDCR due to its simplicity. It assumes that the body has a constant curvature and neglects gravitational and torsional effects, in addition to the effects that may also be caused by external forces and the weight of the robot. Despite its simplicity, this geometric model has been shown to be effective and is widely used in continuum robotics (Webster and Jones, 2010; Li et al., 2018; Wang et al., 2013). It is worth noting that the model complexity for the HTDCR is even reduced as compared to (Webster and Jones, 2010; Li et al., 2018; Wang et al., 2013) because bending the body is performed with a single tendon and the bending orientation is directly obtained from the rotary base (
The forward kinematics determines the position and orientation of any point of the backbone based on the change in tendon length
with
The entries in
The inverse kinematics determines the change in tendon length and bending direction for a given tip position
The tendon length can then be determined from the above arc parameters and the forward kinematics (Equation 2). Finally, the direction of the bending plane is given by Equation 6
2.3 4-Tendon driven continuum robot (4TDCR) for comparison with HTDCR
A standard prototype was built based on the design principles for TDCRs outlined in Section 2.1. The aim of this 4TDCR prototype is to allow comparison with the HTDCR. The 4TDCR consists of a spring backbone connected by spaced discs achieving its actuation through four tendons parallel to the backbone, and attached to the tip of the robot arm (see Figure 3). Each tendon is spaced at 90° intervals and controlled independently by a servomotor, thus allowing bending in any direction. Despite design differences between 4TDCR and HTDCR, both prototypes share the same dimensional parameters (i.e.,
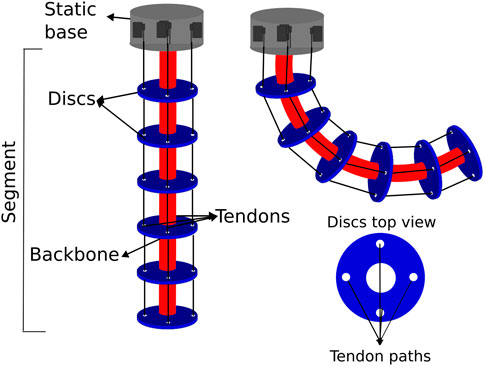
Figure 3. Schematics of the 4TDCR. The backbone is shown in red. as for the HTDCR, it is made of 6 sections, each one having the same steel spring. The sections are separated by discs with 4 holes for the tendon paths.
Additionally, a constant-curvature kinematic model was implemented for controlling the 4TDCR. The 4TDCR model has been developed and validated in previous works (Rao et al., 2021; Webster and Jones, 2010; Li et al., 2018; Neppalli and Jones, 2007). Specifically, the arc parameters depend on the length of each tendon, as the differential actuation of the tendons generates bending. Although related, the constant-curvature model for the HTDCR is simpler as it depends on a single tendon (Section 2.2).
3 Results
3.1 Validation of the constant curvature model for the HTDCR
To validate the constant curvature model, measurements were obtained on the real HTDCR with a motion capture system (Qualisys 6 Miqus cameras and 14 reflective markers placed along the body). We compared the measurements to simulations of the forward kinematic model (last column of
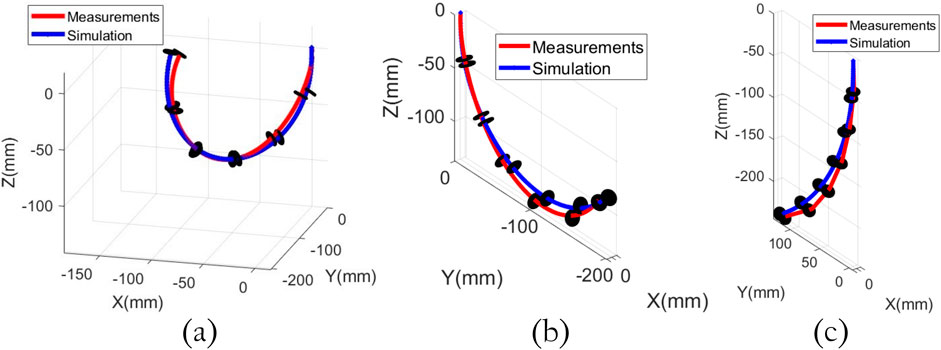
Figure 4. HTDCR measurements vs. simulations of the constant curvature model for three different bendings. (a) Maximum bending (b,c) intermediate bendings.
3.2 HTDCR maximum payload estimation
A prerequisite to experiments under load is to characterize the maximum load the HTDCR can support. The force required to induce maximum bending of the body without load is estimated to
The bending of individual sections was then replicated for the whole arm and validated experimentally by measuring the force for maximum bending of the arm with a dynamometer (KERN HDB 5K5N). Then, maximum force capacity
This maximum force equals to 4,379 g-force, and, dividing by 9.81
3.3 Body deviation analysis
Figure 6 shows an example of the behavior of the HTDCR vs. 4TDCR when a load is applied to the tip. We note that, unlike the HTDCR, the 4TDCR undergoes torsional deformation under load. To characterize the deformation, the shape of the body was measured at multiple points with reflective markers along the backbone, including the tip. Measurements were obtained with and without load for 18 random bendings, with 3 trials each, leading to a total of 108 measurements for each prototype. The experimental data was analyzed by comparing the measured positions with predictions from the constant curvature model and with measurements obtained with the 4TDCR.
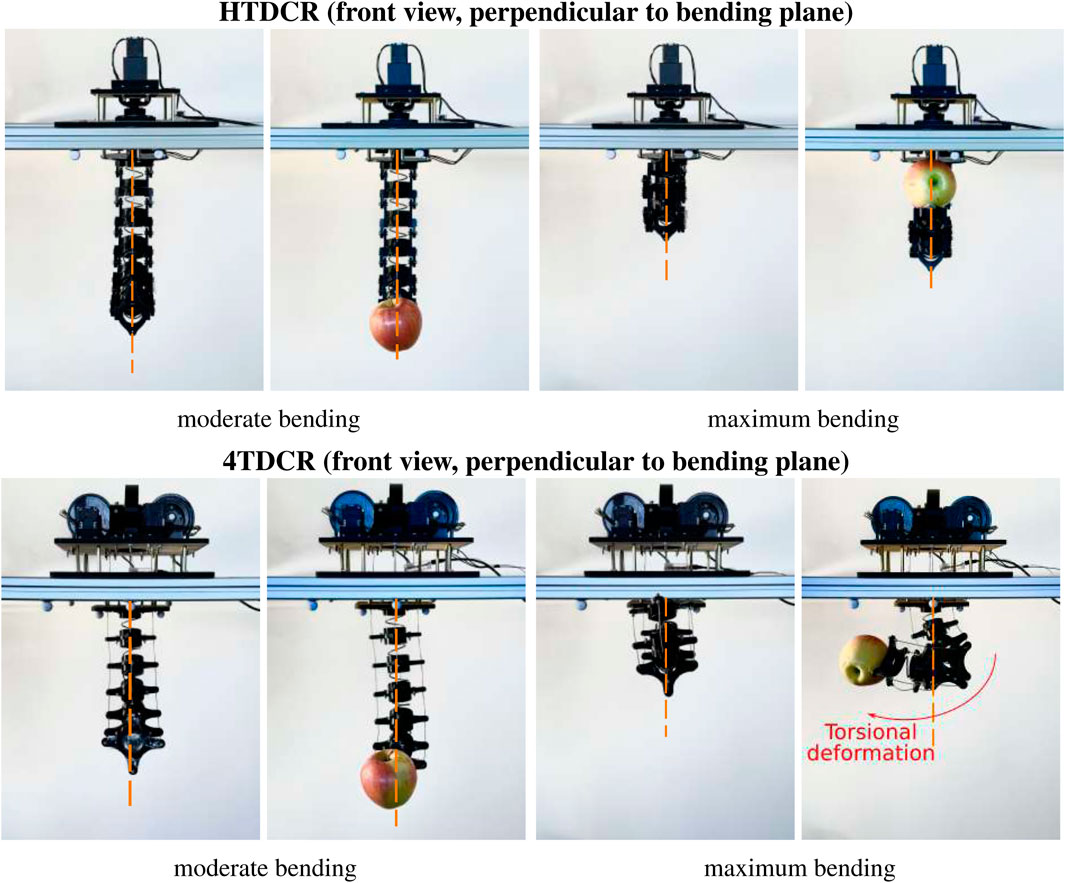
Figure 6. Illustrative example of torsional deformation Frontview comparison of the HTDCR and 4TDCR prototypes with and without a 186 g apple at the tip. Two bendings were considered (moderate and maximum).
Body deviation error is defined as the perpendicular distance between the center line of the backbone and the bending plane so that it is zero when the center line of the backbone belongs to the bending plane. In other words, it represents the displacement of the backbone out of the bending plane as a result of torsional deformation. Top view (
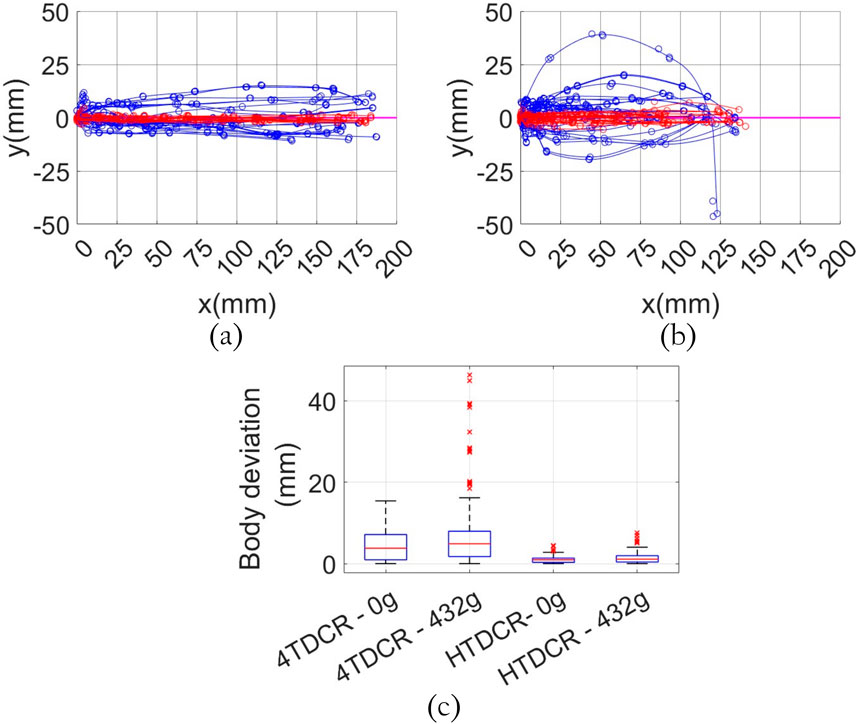
Figure 7. Body deviation out of the bending plane for 4TDCR (plots in blue) vs. HTDCR (plots in red) with and without tip load. The superimposed plots in panel a and b were obtained by rotating the measured positions so that the resulting bending plane corresponds to
3.4 Tip deflection analysis
Tip deflection under load is simply defined as the difference in Z-coordinate obtained with and without load. Specifically, it refers to the change in the tip position within the bending plane due to the applied external load (see Figure 8). The first series of tests involved adding weight progressively to the tip, starting from no load, up to the maximum load of 432 g. The effects of the load was tested in different positions for the tendon servomotor starting from 0° to 300° in 75° increments. The motor position is directly correlated to the bending angle, with 0° corresponding to a fully extended position (no bending) and 300° to the maximum bending position. The same tests were conducted with the 4TDCR. As expected, tip deflection depends on the bending angle for both HTDCR and 4TDCR and increases as the arm bends further. Also, in Figure 9, it is observed that tip deflection increases with load due to the body flexibility retained within the bending plane of both prototypes. In the 4TDCR, the deflection increases proportionally with the load. In the HTDCR, the deflection rate is nonlinear and tip deflection stabilizes for higher loads. This is noticeable between the loads 194g, 289g and 432 g in Figure 9A. Actually, the tip deflection can be predicted accurately from the tip load and the tendon motor angle (Root Mean Squared Error (RMSE) in the mm range, Figure 9C).
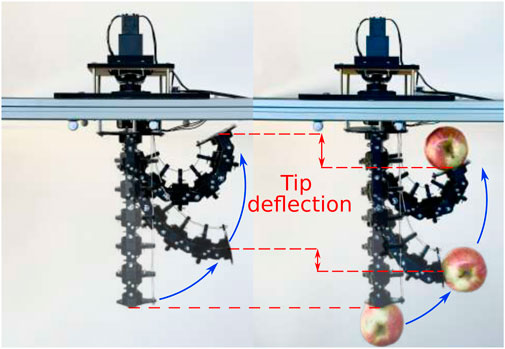
Figure 8. Illustrative example of tip deflection for HTDCR. Lateral view, facing the bending plane, for HTDCR with and without load.
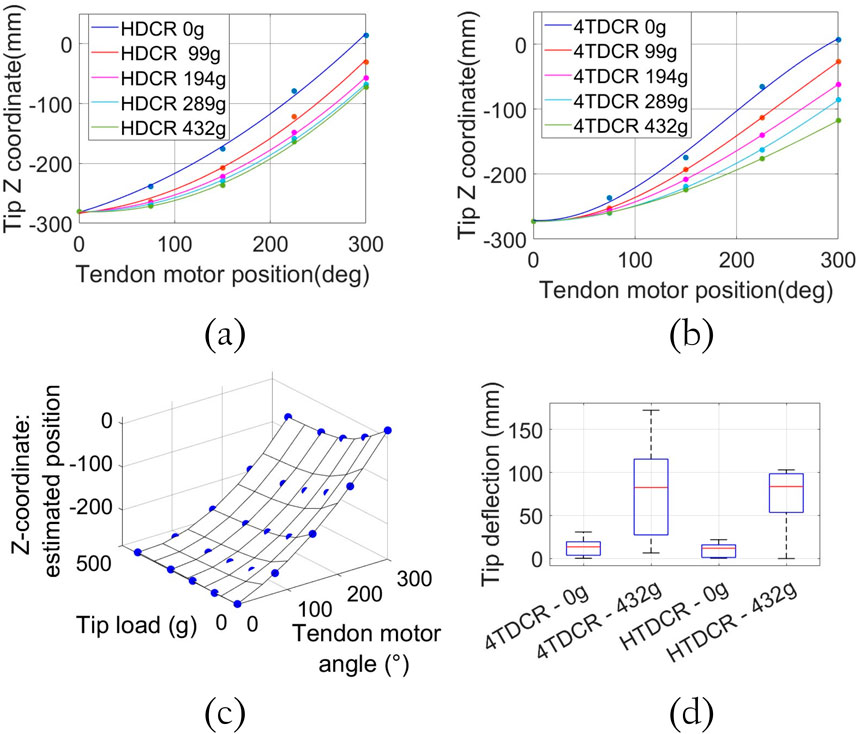
Figure 9. Tip deflection analysis with diffent loads and bending positions. Tip deflection for HTDCR (a) vs. 4TDCR (b) Tip deflection is measured from initial to maximum tendon motor position as the
3.5 Tip error analysis
In previous analysis, body deviation and tip deflection were measured with respect to the bending plane. Here we analyze how deviation and deflection errors translate into global tip position
Where
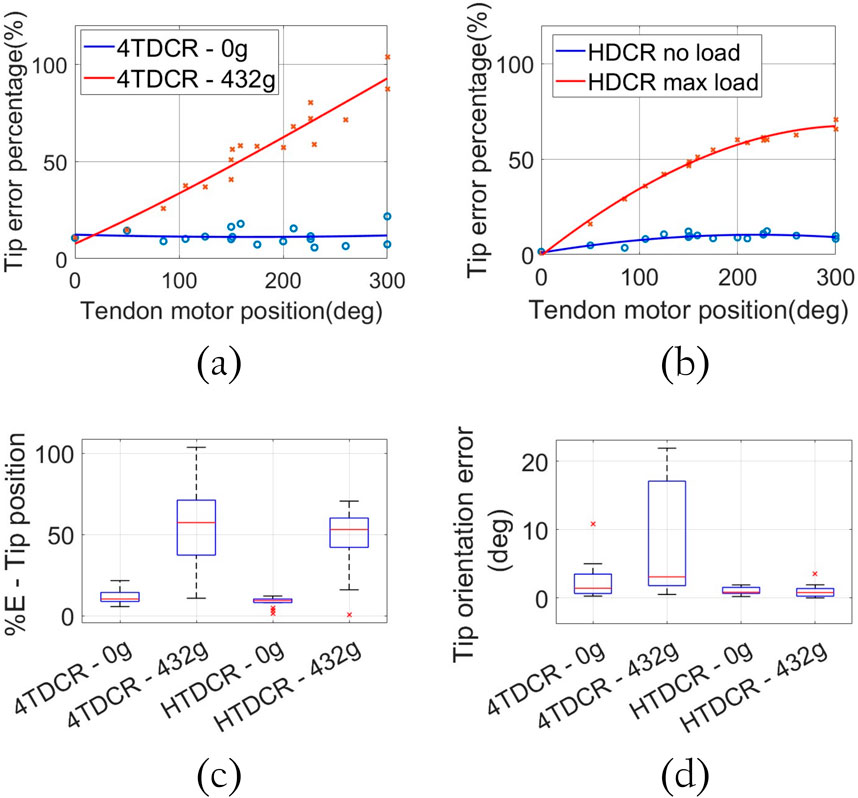
Figure 10. Comparison of the tip position
4 Discussion
This study presents the design and validation of a Hybrid 1-Tendon Driven Continuum Robot (HTDCR), incorporating revolute joints to the structure for avoiding the effects of torsion under external loads, which remains a persistent challenge in continuum robotics. Two series of experiments were conducted on the HTDCR with varying loads. The data obtained were compared with those from a conventional 4-Tendon Driven Continuum Robot (4TDCR). The first test involved a progressive loading on the tip, while the second tested random configurations with and without maximum load.
The results of the experiments demonstrate that the mechanical constraint introduced by the revolute joints effectively reduces torsional effects, allowing for significantly improved control of the robot’s orientation when subjected to various loads. This design feature enhances the HTDCR’s stability and orientation control, especially under increasing load conditions (Figure 10D) having a maximum orientation error of 3.6°. While the integration of revolute joints significantly reduces torsional effects, deflection within the bending plane persists under external load due to the robot flexible backbone. This highlights an important issue to address for future research in order to explore ways to further balance flexibility with rigidity in continuum robots. One line of research would be to implement a tip deflection compensation system based on the established relationship between the tendon motor position and the applied load to obtain an estimation of the deflection, providing a better understanding of the position when the body deforms.
The HTDCR is particularly advantageous for applications requiring relatively high loads in continuum robotics, e.g., harvesting small-to medium-sized fruits and vegetables, such as apples with an average weight of 200g. Future work will concentrate on integrating the HTDCR with a cable-driven robot (Pott, 2018; Pannequin et al., 2020) or a quadrirotor for performing pest detection, crop surveillance, and harvesting as depicted in Figure 11.
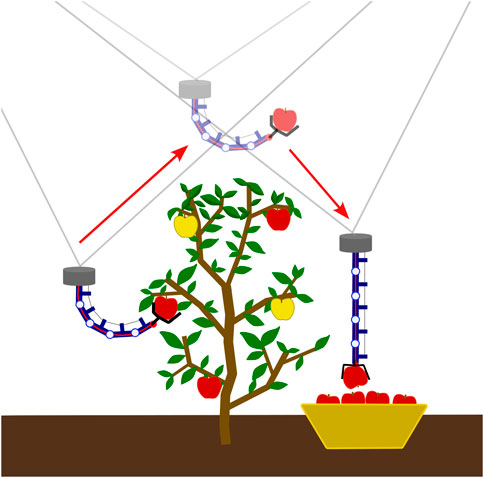
Figure 11. Harvesting scenario with the HTDCR used as the end-effector of a cable-driven parallel robot.
Data availability statement
The raw data supporting the conclusions of this article will be made available by the authors, without undue reservation.
Author contributions
DM: Supervision, Writing - original draft, Writing - review & editing. MH: Methodology, Software, Validation, Writing – original draft, Writing – review and editing. MB: Writing – review and editing.
Funding
The author(s) declare that financial support was received for the research and/or publication of this article. The authors acknowledge financial support from the SATT Sud-est and the consortium ASTRAGAL.
Conflict of interest
The authors declare that the research was conducted in the absence of any commercial or financial relationships that could be construed as a potential conflict of interest.
The author(s) declared that they were an editorial board member of Frontiers, at the time of submission. This had no impact on the peer review process and the final decision.
Generative AI statement
The author(s) declare that no Generative AI was used in the creation of this manuscript.
Publisher’s note
All claims expressed in this article are solely those of the authors and do not necessarily represent those of their affiliated organizations, or those of the publisher, the editors and the reviewers. Any product that may be evaluated in this article, or claim that may be made by its manufacturer, is not guaranteed or endorsed by the publisher.
References
Alambeigi, F., Bakhtiarinejad, M., Sefati, S., Hegeman, R., Iordachita, I., Khanuja, H., et al. (2019). On the use of a continuum manipulator and a bendable medical screw for minimally invasive interventions in orthopedic surgery. IEEE Trans. Med. Robotics Bionics 1 (1), 14–21. doi:10.1109/tmrb.2019.2895780
Amanov, E., Nguyen, T.-D., and Burgner-Kahrs, J. (2021). Tendon-driven continuum robots with extensible sections—a model-based evaluation of path-following motions. Int. J. Robotics Res. 40 (1), 7–23. doi:10.1177/0278364919886047
Armanini, C., Junge, K., Johnson, P., Whitfield, C., Renda, F., Calisti, M., et al. (2024). Soft robotics for farm to fork: applications in agriculture and farming. Bioinspiration Biomimetics 19 (2), 021002. doi:10.1088/1748-3190/ad2084
Bai, H., Lee, B. G., Yang, G., Shen, W., Qian, S., Zhang, H., et al. (2024). Unlocking the potential of cable-driven continuum robots: a comprehensive review and future directions. Actuators 13, 52. doi:10.3390/act13020052
Camarillo, D. B., Milne, C. F., Carlson, C. R., Zinn, M. R., and Salisbury, J. K. (2008). Mechanics modeling of tendon-driven continuum manipulators. IEEE Trans. Robotics 24 (6), 1262–1273. doi:10.1109/tro.2008.2002311
Childs, J., and Rucker, D. (2021). Leveraging geometry to enable high-strength continuum robots. Front. Robotics AI 8, 629871. doi:10.3389/frobt.2021.629871
Dong, X., Axinte, D., Palmer, D., Cobos, S., Raffles, M., Rabani, A., et al. (2017). Development of a slender continuum robotic system for on-wing inspection/repair of gas turbine engines. Robotics Computer-Integrated Manuf. 44, 218–229. doi:10.1016/j.rcim.2016.09.004
Dong, X., Raffles, M., Cobos-Guzman, S., Axinte, D., and Kell, J. (2015). A novel continuum robot using twin-pivot compliant joints: design, modeling, and validation. J. Mech. Robotics 8 (2), 021010. doi:10.1115/1.4031340
Gao, A., Liu, H., Zhou, Y., Yang, Z., Wang, Z., and Li, H. (2015). A cross-helical tendons actuated dexterous continuum manipulator. IEEE/RSJ International Conference on Intelligent Robots and Systems IROS, 2012–2017.
He, B., Wang, Z., Li, Q., Xie, H., and Shen, R. (2013). An analytic method for the kinematics and dynamics of a multiple-backbone continuum robot. Int. J. Adv. Robotic Syst. 10. doi:10.5772/54051
Kim, K., Woo, H., and Suh, J. (2018). “Design and evaluation of a continuum robot with discreted link joints for cardiovascular interventions,” in 2018 7th IEEE International Conference on Biomedical Robotics and Biomechatronics (Biorob), USA, 26-29 Aug. 2018, 627–633. doi:10.1109/biorob.2018.8487633
Li, M., Kang, R., Geng, S., and Guglielmino, E. (2018). Design and control of a tendon-driven continuum robot. Trans. Inst. Meas. Control 40 (11), 3263–3272. doi:10.1177/0142331216685607
Neppalli, S., and Jones, B. A. (2007). “Design, construction, and analysis of a continuum robot,” IEEE/RSJ international conference on intelligent robots and systems in, pp. 1503–1507.
Pannequin, R., Jouaiti, M., Boutayeb, M., Lucas, P., and Martinez, D. (2020). Automatic tracking of free-flying insects using a cable-driven robot. Sci. Robotics 5 (43), eabb2890. doi:10.1126/scirobotics.abb2890
Qi, Q., Qin, G., Yang, Z., Chen, G., Xu, J., Lv, Z., et al. (2024). Design and motion control of a tendon-driven continuum robot for aerospace applications. Proc. Institution Mech. Eng. Part G 238 (13), 1296–1310. doi:10.1177/09544100241263004
Rao, P., Peyron, Q., Lilge, S., and Burgner-Kahrs, J. (2021). How to model tendon-driven continuum robots and benchmark modelling performance. Front. Robotics AI 7 (02), 630245. doi:10.3389/frobt.2020.630245
Rucker, D. C., and Webster, R. J. (2011). Statics and dynamics of continuum robots with general tendon routing and external loading. IEEE Trans. Robotics 27 (6), 1033–1044. doi:10.1109/tro.2011.2160469
Russo, M., Sadati, S., Dong, X., Mohammad, A., Walker, I., Bergeles, C., et al. (2023). Continuum robots: an overview. Adv. Intell. Syst. 5, 2200367. doi:10.1002/aisy.202200367
Santiago, J. L. C., Walker, I. D., and Godage, I. S. (2015). “Continuum robots for space applications based on layer-jamming scales with stiffening capability,” in 2015 IEEE aerospace conference, 1–13.
Tokunaga, T., Oka, K., and Harada, A. (2017). “1segment continuum manipulator for automatic harvesting robot - prototype and modeling,” in 2017 IEEE International Conference on Mechatronics and Automation, China, August 6 to 9, 2017 (ICMA), 1655–1659.
Veiga, T., Chandler, J., Lloyd, P., Pittiglio, G., Wilkinson, N., kafash hoshiar, A., et al. (2020). Challenges of continuum robots in clinical context: a review. Prog. Biomed. Eng. 2, 032003. doi:10.1088/2516-1091/ab9f41
Visentin, F., Mishra, A. K., Naselli, G. A., and Mazzolai, B. (2019). “Simplified sensing and control of a plant-inspired cable driven manipulator,” in 2019 2nd IEEE International Conference on Soft Robotics (RoboSoft), USA, 14-18 April 2019, 422–427. doi:10.1109/robosoft.2019.8722729
Wang, H., Chen, W., Yu, X., Deng, T., Wang, X., and Pfeifer, R. (2013). “Visual servo control of cable-driven soft robotic manipulator,” in 2013 IEEE/RSJ International Conference on Intelligent Robots and Systems, China, 3-7 Nov. 2013, 57–62. doi:10.1109/iros.2013.6696332
Wang, M., Dong, X., Ba, W., Mohammad, A., Axinte, D., and Norton, A. (2021). Design, modelling and validation of a novel extra slender continuum robot for in-situ inspection and repair in aeroengine. Robotics Computer-Integrated Manuf. 67, 102054. doi:10.1016/j.rcim.2020.102054
Webster, I. R. J., and Jones, B. A. (2010). Design and kinematic modeling of constant curvature continuum robots: a review. Int. J. Robotics Res. 29 (13), 1661–1683. doi:10.1177/0278364910368147
Xiao, J., Wang, M., and Chen, C. (2024). A novel shape memory alloy modular robot with spatially stable structure. Adv. Intell. Syst. 6. doi:10.1002/aisy.202400091
Xing, Z., Wang, P., Cao, G., Liu, Y., He, Z., and Zhao, J. (2021). “A novel design of a contractible, tubular continuum manipulator,” in 2021 6th IEEE International Conference on Advanced Robotics and Mechatronics (ICARM), China, 3-5 July 2021, 335–339. doi:10.1109/icarm52023.2021.9536109
Yan, J., Chen, J., Chen, J., Yan, W., Ding, Q., and Yan, K. (2022). A continuum robotic cannula with tip following capability and distal dexterity for intracerebral hemorrhage evacuation. IEEE Trans. Biomed. Eng. 69 (9), 2958–2969. doi:10.1109/tbme.2022.3158539
Yang, Z., Yang, L., Sun, Y., and Chen, X. (2024). A novel contact-aided continuum robotic system: design, modeling, and validation. IEEE Trans. Robotics 40, 3024–3043. doi:10.1109/tro.2024.3400944
Yang, Z., Yang, L., Xu, L., Chen, X., Guo, Y., Liu, J., et al. (2021). “A continuum robot with twin-pivot structure: the kinematics and shape estimation,” in Intelligent robotics and applications Editors X.-J. Liu, Z. Nie, J. Yu, F. Xie, and R. Song (Cham: Springer International Publishing), 466–475.
Yeshmukhametov, A., Koganezawa, K., Buribayev, Z., Amirgaliyev, Y., and Yamamoto, Y. (2020). Study on multi-section continuum robot wire-tension feedback control and load manipulability. Industrial Robot Int. J. robotics Res. Appl. 47, 837–845. ahead-of-print, 05 2020. doi:10.1108/ir-03-2020-0054
Yoon, H.-S., and Yi, B.-J. (2009). “A 4-dof flexible continuum robot using a spring backbone,” in 2009 international conference on mechatronics and automation, 1249–1254.
Keywords: tendon-driven continuum robot, revolute joints, torsional deformation, constant curvature model, agricultural robotics, harvesting
Citation: Huertas Niño MP, Boutayeb M and Martinez D (2025) A hybrid tendon-driven continuum robot that avoids torsion under external load. Front. Robot. AI 12:1576209. doi: 10.3389/frobt.2025.1576209
Received: 13 February 2025; Accepted: 28 April 2025;
Published: 14 May 2025.
Edited by:
Pietro Bilancia, University of Modena and Reggio Emilia, ItalyReviewed by:
Giacomo Moretti, University of Trento, ItalyMario Baggetta, Università degli Studi di Genova, Italy
Copyright © 2025 Huertas Niño, Boutayeb and Martinez. This is an open-access article distributed under the terms of the Creative Commons Attribution License (CC BY). The use, distribution or reproduction in other forums is permitted, provided the original author(s) and the copyright owner(s) are credited and that the original publication in this journal is cited, in accordance with accepted academic practice. No use, distribution or reproduction is permitted which does not comply with these terms.
*Correspondence: Dominique Martinez, ZG9taW5pcXVlLm1hcnRpbmV6QHVuaXYtYW11LmZy