- School of Electrical and Electronic Engineering, The University of Sheffield, Sheffield, United Kingdom
Soft growing robots (SGRs) navigate confined environments by everting material from the tip while keeping the rest of the body stationary, enabling frictionless navigation. This opens up huge potential for inspection, search, and rescue tasks. However, controlling the direction of tip growth is still a challenge because of the ever-changing tip of the robot during tip growth. This study presents a compact steering mechanism that integrates a tendon-driven pivot joint with a pressure-tunable internal bladder. By modulating friction between the pivot joint and the inner material, the mechanism switches between two states: decoupled (stationary for bending) and coupled (move forward together with robot’s inner material). This enables the robot to bend locally and then continue growing in the new direction, without using complex full-body actuation or external mechanisms. A robotic platform was developed to implement this mechanism, and its performance was characterized and validated through modeling and experiments. Experimental results confirm that the mechanism achieves reliable tip steering, closely matches kinematics models, and interacts gently with the environment. The proposed design offers a scalable and structurally simple solution for long-range navigation in soft growing robots.
1 Introduction
Tip-everting Soft Growing Robots (SGRs), which can lengthen their bodies by everting their inner material at the tip (Hawkes et al., 2017), have emerged in recent years. Tip growth is a common phenomenon in plant growth, from pollen tubes (Steer and Steer, 1989) and plant roots to creeping vines (Weigel and Jürgens, 2002). This particular attribute of mobile growth allows the tip to navigate frictionlessly in a narrow and tightly restricted environment and to build a conduit with the aid of the surrounding environment (Sanati Nezhad and Geitmann, 2013). Without relative sliding with the environment, there is no friction between the robot and the environment, reducing the impact of the robot to the environment and enabling the robot to travel further (Blumenschein et al., 2020). This leads to broad application of SGR for minimally invasive surgery (Taylor and Stoianovici, 2003), small-environment inspection (Liu and Kleiner, 2013), rescue (Siciliano and Khatib, 2016), and archaeology (Coad et al., 2020).
For tip-everting SGRs, achieving reversible, localized steering during continuous eversion remains a core challenge. A steering unit must (i) lock to the body long enough to generate curvature, then (ii) decouple so new material can emerge. After bending, the shape must be held while fresh membrane everts, yet practical locking or environment-bracing solutions remain scarce. Moreover, few robots can shift the steering site downstream as they elongate without external insertion tools. Many approaches have been proposed to actively steer the Tip Everting SGR, such as (1) integrated pneumatic latch mechanism (Hawkes et al., 2017), (2) SPAM (Series Pneumatic Artificial Muscles) (Coad et al., 2020), (3) helical tendon routing (Blumenschein et al., 2018), (4) variable stiffness (Do et al., 2023), (5) Distributed Pneumatic Segment (der Maur et al., 2021), (6) Internal-Skeleton-Based Steering (Haggerty et al., 2021; Takahashi et al., 2021; Li et al., 2021; Qin et al., 2025), (7) Non-actuator-based strategies Mendoza et al. (2024), Davy et al. (2024).
Many approaches have been proposed to actively steer the Tip Everting SGR. The integrated pneumatic latch mechanism in SGR features a pneumatic chamber on each side with prelocked wrinkles controlled by a series of latches (Hawkes et al., 2017). Actuating a chamber releases a latch at the tip of the robot, creating different lengths on the sides of the SGR and allowing directional steering. This design ensures that the shape of the SGR remains constant during navigation, thus reducing the environmental impact. However, steering occurs only during growth and is irreversible; that is, once a direction is set, it cannot be changed.
The more commonly used SPAM (Series Pneumatic Artificial Muscles) approach involves a pneumatic chamber in the SGR body that contracts when pressurised, causing reversible bending (Coad et al., 2020). Unlike pneumatic latching mechanisms, SPAM allows for steering without growth and is reversible. However, it bends the entire SGR body, which is not always desirable, particularly when only tip steering is preferred. In constrained environments, SPAM-steered SGR may produce unpredictable steering owing to their interactions with their surroundings. In addition, the large size of pneumatic pouches makes the robots bulky and difficult to miniaturise, limiting their use in medical applications.
The helical tendon routing approach uses a tendon routed along the helical path around an inflated beam through a series of short tendon-guiding segments (Blumenschein et al., 2018). When pulled, the tendon reconfigures the inflated beam into a helical shape. This can only generate a structure of the desired shape, but is limited in providing arbitrary steering during navigation.
The variable stiffness approach uses layer jamming to dynamically change the stiffness of sections along an inflated continuum beam to selectively “activate” discrete joints (Do et al., 2023). By changing the activated joints, the output of a single actuator can be reconfigured to actively control the bending angles of various joints. This approach can remarkably change the shape of the SGR in many different sections; however, it requires many valves and pneumatic lines to separately control the layer jamming of each section, leading to a complex and bulky robot body design.
Another commonly adopted method involves distributed pneumatic segment actuation, in which multiple internal pneumatic chambers are embedded along the robot body. der Maur et al. (2021) developed RoBoa, a steerable vine robot driven by such distributed actuators. While this design enables effective steering and navigation, especially in search-and-rescue scenarios, it introduces mechanical complexity due to the need for pneumatic routing and synchronized control.
Internal-skeleton steering typically fixes a mechanical linkage to the inner membrane at two points, the two-contact position draw together as the actuation mechanism driven, forming a wrinkle that creates a length mismatch between the robot’s flanks and thus a bend. For single steering structure, Haggerty et al. (2021) drive the linkage with on-board electric motors, increasing mass and restricting use in environments sensitive to electronics; moreover, their tip-mounted storage scheme limits the availability of a central tool channel. Takahashi et al. (2021) require manual repositioning of the linkage relative to the base, which precludes fully autonomous operation. Li et al. (2021), Qin et al. (2025) and Wang et al. (2020) employ distributed embedded actuation network for steering and shape retention. Although highly dexterous, these electro-magnetic or pneumatic lattices increase design complexity and confine the effective growth length to the region that contains actuators, leaving unactuated segments unable to steer. Wang et al. (2020) introduced a variable-length shape-locking backbone that allows segment-wise bending by mechanically constraining curvature from within. The approach demands intricate internal locking hardware distributed along the entire robot, these additional components also adding complexity to control.
Recent efforts exploring non actuator based steering mechanisms that rely on either material anisotropy or field-based control, rather than centralized tendon or pneumatic actuation. Mendoza et al. (2024) presented a vine robot capable of achieving high curvature and force through asymmetric elongation of its body, leveraging anisotropic elastic films and layer-jamming. However, the reliance on complex material fabrication restricts scalability and practical miniaturization. Davy et al. (2024) proposed magnetically-actuated steering by embedding magnetic particles within the robot’s skin, offering non-contact control suitable for surgical applications. Nevertheless, external magnetic field requirements restrict deployment scenarios and introduce challenges in environments sensitive to electromagnetic interference.
In this study, we propose an Integrated Bladder and Pivot Joint steering mechanism to control the growth direction through local bending. A tendon-driven pivot joint, attached to the inner inverted material, can bend the robot body at the location of the joint when actuated; inside the pivot joint, there is a pressure-tunable bladder that provides a friction-based connection between the pivot joint and the inner inverted material. Zero bladder pressure (no friction bonding) allows the pivot joint to remain stationary relative to the everting inner body, preserving the bending angle while the robot continues to grow forward. A high-friction bonding (high bladder pressure) would enable the pivot joint to move along with the inverted material during growth until the joint reaches a desired bending location inside the robot body. Our tendon-driven pivot joint, stabilized by a friction-based bladder, delivers reversible and localized steering without embedded motors or distributed actuators. As the two tendons and single bladder are actuated from the base, the steering unit remains lightweight, electronics-free, and leaves the central inverted membrane available as a tool channel. Furthermore, since the steering unit is not permanently affixed to the robot body, the overall growth length is not constrained by pre-distributed actuation, offering clear advantages in terms of scalability. The simplicity of the pneumatic–tendon architecture also makes it inherently amenable for miniaturization due to its simple topology, and for deployment in electromagnetically or spatially constrained environments.
The primary contributions of this study include.
• The design of the novel steering mechanism and its implementation on an SGR prototype. The mechanism is compact in design and can selectively vary the local steering location along the robot body without having to be attached all along the robot body like the SPAM and layer-jamming approaches.
•The tendon-actuated pivot joint is automatically carried by the everted body, enabling steer-lock-release cycles without external intervention.
•The modeling and testing on the inner friction, kinematics, and environment interaction forces of the robot.
•The demonstration of the robot inside a branched arena, demonstrating the effectiveness of the steering mechanism.
2 Materials and methods
The proposed mechanism utilizes an embedded, tendon-driven pivot joint and an pressure-tunable bladder to manipulate the orientation and growth direction of the SGR. Figure 1 illustrates the detailed structural components and operational sequences across several distinctive stages, showcasing the decoupling of axial pivot-joint position from the robot’s eversion and steering.
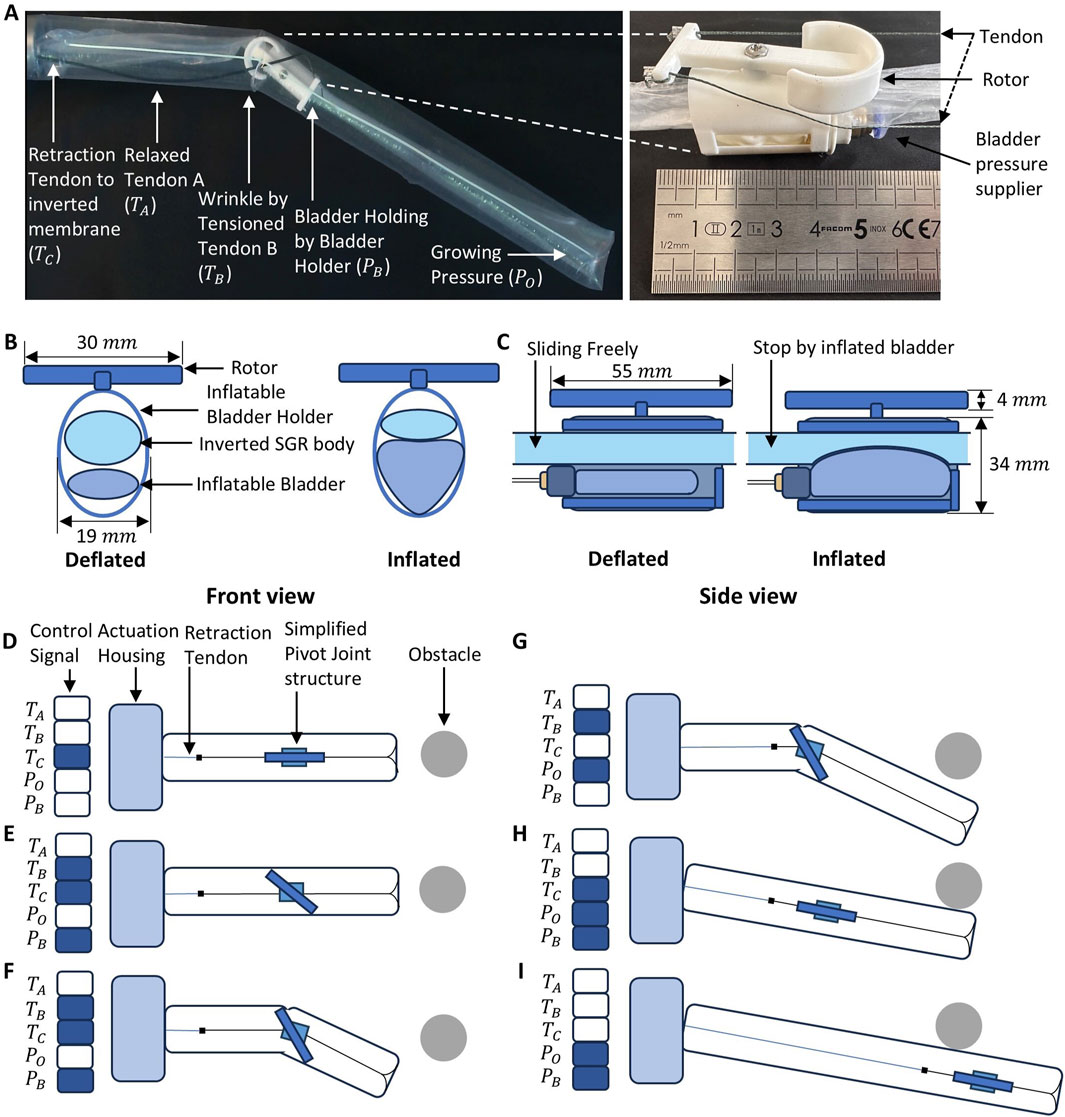
Figure 1. Detailed operational stages and structural components of the pivot-joint integrated soft growing robot: (A) Real image depicting pivot-joint and tendon-driven wrinkle; (B,C) Front and side views illustrating bladder inflation for friction-based pivot joint anchoring mechanism; (D) Initial linear eversion; (E,F) Initiation and execution of steering; (G) Obstacle negotiation through controlled deformation; (H) Post-steering linear growth along new trajectory; (I) Shape retention and locking by internal bladder inflation.
2.1 Mechanism design
The SGR body is essentially an inverted membrane tubing. Releasing the inner inverted membrane material via a central tendon (tendon C) and increasing the air pressure of the SGR would enable the robot to grow at the tip. Inside the SGR body, there is a pivot joint mechanism which has an embedded, pressure-tunable bladder. The pivot joint mechanism is composed of a bladder holder and a rotor driven by two actuating tendons tendon
2.2 Operational stages and steering principle
The detailed steering process depicted in Figures 1D–I is systematically described as follows:
Stage 1: Initial State (Figure 1D): The robot initiates linear eversion with pneumatic pressure
Stage 2: Steering (Figures 1E,F): When encountering an obstacle, to avoid and passing through, the bladder pressure
Stage 3: Decoupled Growth for Obstacle Avoidance (Figure 1G): The robot grows by increasing pneumatic pressure
Stage 4: Coupled Growth (Figures 1H,I): After successfully passing the obstacle, all tendon tensions are released. The bladder is re-inflated to restore frictional coupling between the pivot joint and the inner membrane. Pressure
2.3 Mechanics modelling
2.3.1 Tensioned tendon for steering
To evaluate the bending moment applied by the rotor to the robot body, we first isolate the rotor structure as a free body, as illustrated schematically in Figure 2A.
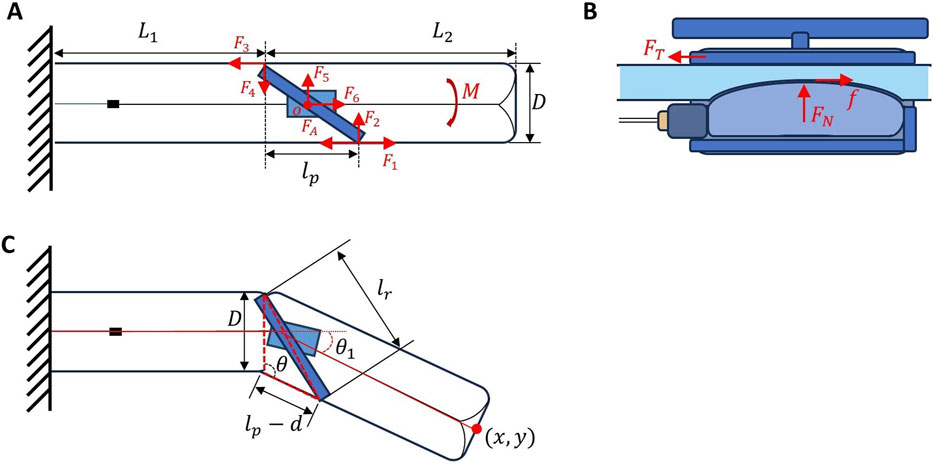
Figure 2. Mechanics analysis diagram illustrating wrinkling forces, frictional engagement, and resultant bending moments influencing robot steering: (A) Simplified free-body diagram of forces acting on the pivot joint; (B) Side-view of frictional locking mechanism via bladder inflation; (C) Geometric definitions interactions associated with steering.
In addition, the rotor is free to rotate around a rotation shaft connected to the bladder holder. The rotation shaft applies an orthogonal pair of forces to the rotor
The rotor has movement-equilibrium under these forces. Take point
Thus,
Note that
2.3.2 Wrinkling force for steering
The steering of the SGR with pivot joint fundamentally relies on forming localized wrinkles via tendon-driven actuation, combined with internal pneumatic pressure, the result also flows the equation proposed by Wang et al. (2020).
As depicted in Figures 2A–C, the robot’s body deformation arises from the interaction of internal pneumatic pressure
Where
The implication of Equation 3 is that, at a given internal pressure
2.3.3 Inner bladder friction analysis
Throughout the operational stages (Figures 1D–I), the robot’s main pneumatic pressure
During the above-mentioned Stage 2 (steering), the internal inflatable bladder is inflated with a high pressure
where
During Stage 3 (decoupled growth), the bladder is deflated (Figure 2B) so that the normal force
2.4 Kinematics modelling
To capture the characteristic of the soft growing robot equipped with a pivot joint mechanism, a kinematic model was theoretically derived. The model maps the actuation space (tendon displacement) to the configuration space (robot spinning angle and pivot joint position) and ultimately to the task space (tip poses). The model was then experimentally verified.
As shown in the robot schematic diagram (Figure 2), the robot can be treated as two sections connected by a pivot joint. The pivot joint is controlled by one tendon on each side, with its position coupled with the releasing of the central retraction tendon when the bladder is inflated during steering stage. The total length of the robot
To bend the robot body, the rotor must first contact with the body inner membrane (Figure 2A). Further pulling the tendon would bend the robot. Here, we built the relationship between the tendon input displacement and the robot bending angle based on the geometry of a triangle (see the dashed red lines in Figure 2C) formed by the width of the robot (SGR diameter)
We can get the angle of the pivot joint with the robot outer membrane (Equation 7):
As the rotor contact the membrane, the initial
The pivot joint can produce a controllable bend of up to
As the robot steering angle
2.5 Experiment setups
2.5.1 Kinematics verification and critical buckling force evaluation
As shown in Figure 3A, a 445
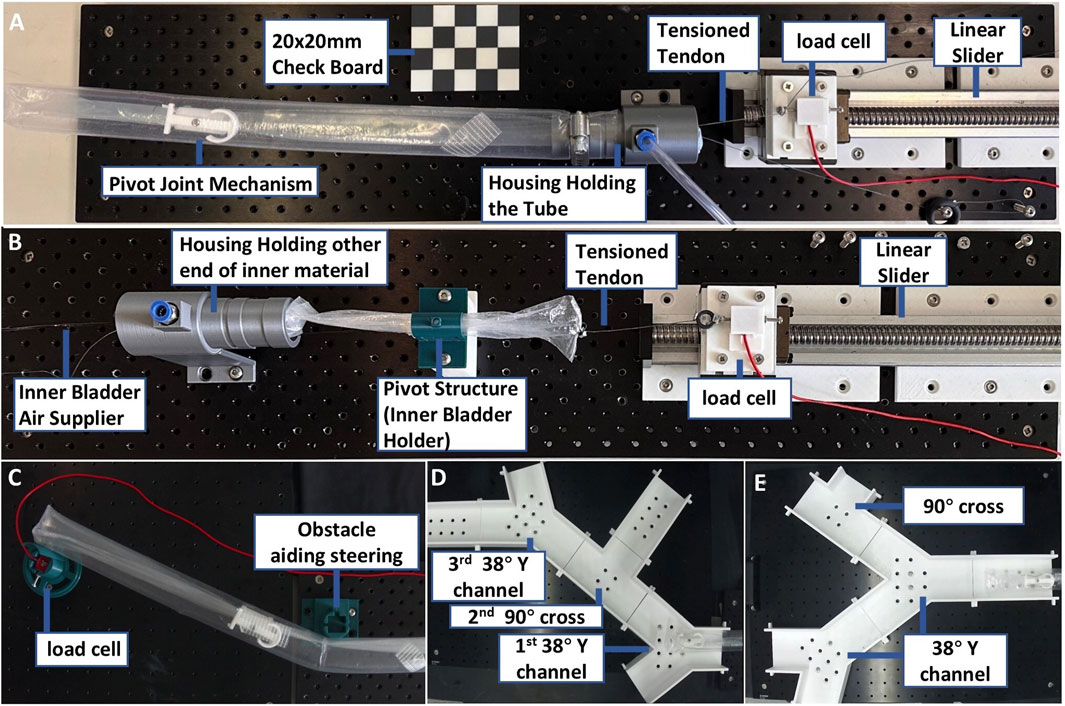
Figure 3. Experimental setups for evaluating robot performance. (A) Setup for kinematics and buckling tests using tendon actuation and visual tracking. (B) Frictional anchoring test to evaluate bladder-induced holding force on the pivot joint. (C) Setup for measuring contact forces during environmental interaction. (D,E) Different maze-like navigation arena settings for steering performance demonstration in unstructured environments.
2.5.2 Bladder friction test
To evaluate the friction force that can be generated by the bladder at different pressures (0–1
2.5.3 Evaluation of environmental contact forces for postural support
During the above-mentioned Stage 4, The robot body relies on the surrounding environment to preserve the bending configuration. It is important to evaluate the interaction forces between the environment and the robot. In this experiment, a loadcell was employed to measure the required external physical support of the obstacle to passively maintain the robot’s posture during growth (Figure 3C). The robot was tested under various internal pressures ranging from 0.4
2.5.4 Exploration and navigation in unstructured environments
To evaluate the robot’s ability to explore unfamiliar and dynamically arranged surroundings through real-time control and navigation, modular reconfigurable mazes (Figures 3D,E) were constructed using interlocking components to emulate an unstructured environment. Several 3D-printed modular components, including Y-shaped junctions (each providing a 38° bend angle), T-shaped junctions, and straight segments, were used to assemble the experimental mazes. These modular components were rearranged to create the two distinct mazes configurations presented in Figures 3D,E.
3 Results and discussion
3.1 Kinematics verification
The kinematic model was validated by comparing its simulations against experimental deformation profiles under both bending and unbending conditions. The predicted robot end effector position (Equation 9) were compared against experimentally recorded deformation profiles under both bending (Figure 4A) and unbending motions (Figure 4B). As shown in Figure 4, the simulated end effector position closely matched the experimental observations, with average relative errors of
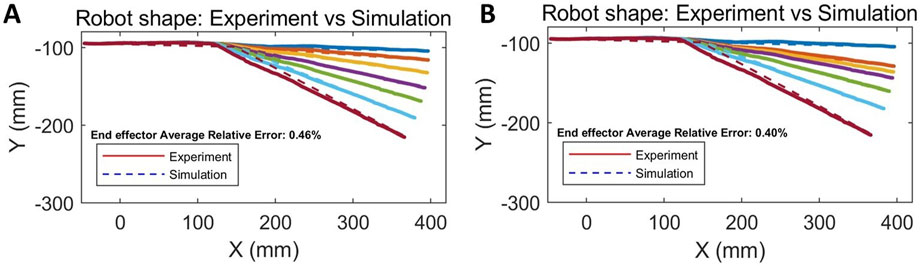
Figure 4. Kinematic verification through experiment and simulation. (A) Bending process. (B) Unbending process. Experimental results are compared with simulation to evaluate model accuracy.
3.2 Effects of air pressure to steering
The robot exhibited a clear buckling behavior in response to tendon actuation. In the initial stage from
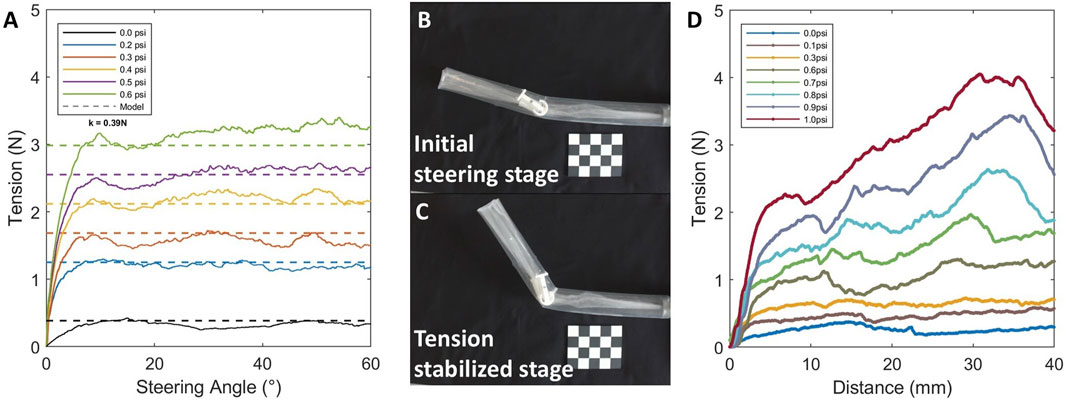
Figure 5. Evaluation of pressure effects on robot steering performance. (A) Effect of internal pressure on the critical tension required for buckling. (B) Tendon tension increasing stage with initial steering (C) Tendon tension stabilized stage with increasing steering angle (D) Effect of bladder pressure on the frictional force for pivot joint anchoring.
In addition to the internal pressure used for tip eversion and growth, the bladder pressure, which controls the anchoring of the pivot joint, also plays a critical role in the robot’s functionality. As previously described, higher inflation pressures generate larger frictional forces between the bladder and the inverted inner tube membrane, effectively securing the pivot joint to the robot body and enabling co-growth. Conversely, reducing the bladder pressure releases internal constraints, allowing the robot to extend independently of the joint.
The test measured the axial frictional resistance provided by the bladder–tube interface at different pressure levels (Figure 5D). Results showed that when the bladder pressure reached 1
3.3 Role of environmental constraints in steering and growth
The robot can actively steer and grow via tip eversion. However, after bending, it lacks dedicated mechanisms to hold its shape. Instead, posture is passively maintained through contact with the environment—a form of morphology stabilization enabled by external constraints.
To quantify the role of environmental contact in maintaining robot posture, we measured the interaction force between the robot body and external supports under different internal pressures and contact positions, corresponding to different steering angles. As shown in Figure 6A, the contact force exhibited a transient peak upon initial contact, with values not exceeding 0.15
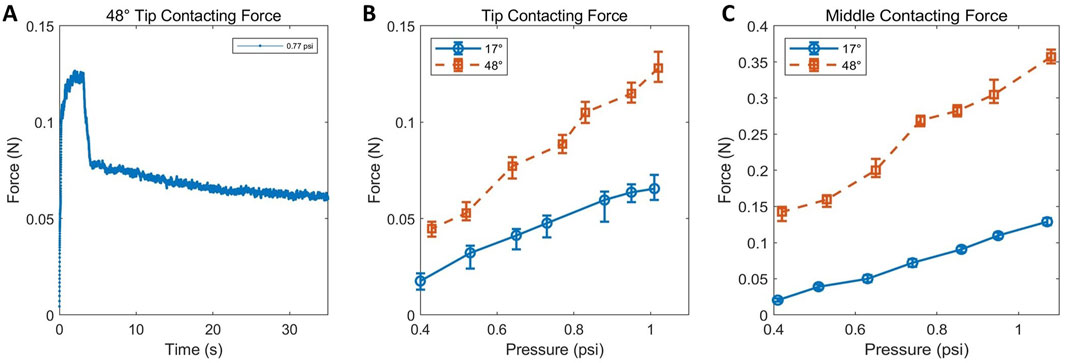
Figure 6. Contact force evaluation during robot-environment interaction. (A) Full force profile during contact. (B,C) Steady-state contact forces under different bending angles and contact positions.
Overall, while the robot relies on passive environmental constraints to maintain its postural configuration after deformation, the contact force involved remains low. This suggests that the stabilization mechanism does not significantly burden or damage the environment, nor does it require strong or specially structured external supports. The low-contact nature of this stabilization strategy enhances the system’s adaptability and ensures compatibility with a wide range of operating conditions without requiring structural modifications to the environment.
3.4 Demonstration of pivot joints navigation capabilities
The navigation capabilities of the soft growing robot equipped with pivot joints were evaluated in structured maze-like environments. As shown in Figures 7A,B, the robot performed an initial turning rotor to cross the first corner of a maze. Figure 7C demonstrates its ability to continue tip eversion and growth after steering. Subsequently, in Figures 7D–F, the robot executed a secondary bending motion, successfully navigating toward the end of a bifurcated path.
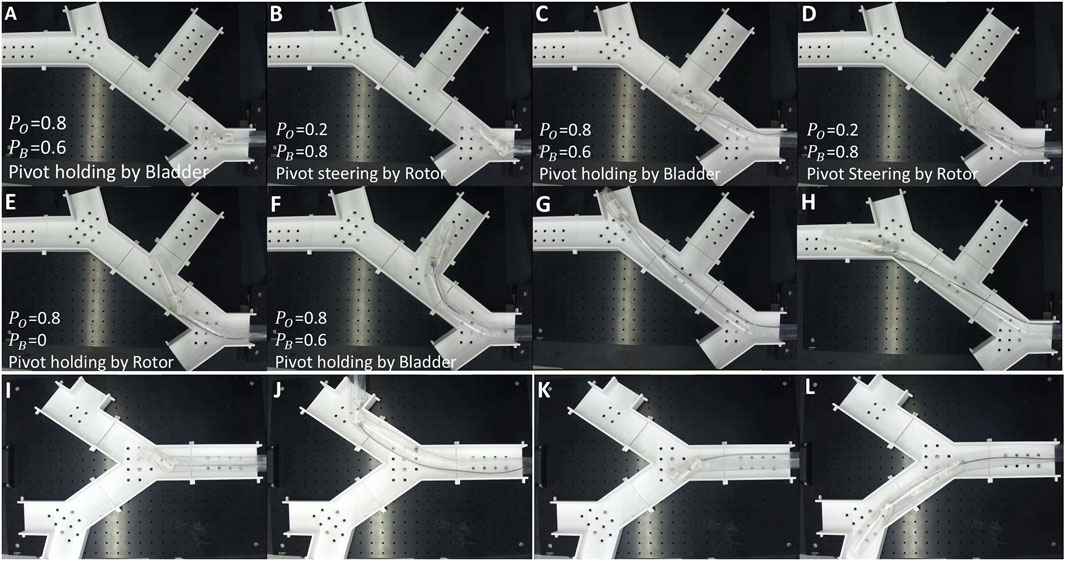
Figure 7. Demonstration of robot navigation using pivot joints in unstructured environments. (A,B) The robot successfully steers through the first corner of a maze. (C) Continued growth after initial steering. (D–F) Secondary bending enables navigation toward a bifurcated dead-end. (G,H) The robot explores the alternative paths in the same maze under manual steering. (I–L) Navigation in a different maze structure, demonstrating robustness across environments.
These sequential deformations highlight the robot’s capacity for complex navigation and repeated directional change. In Figures 7G,H, under manual control, the robot was steered to explore an alternative branch within the same maze, demonstrating its capability for operator-guided decision-making in unstructured settings. Finally, Figures 7I–L ppresents the robot operating within an altered maze configuration constructed from the same modular components. In this scenario, the robot continues to exhibit consistent exploratory behavior, with Figures 7I,J depicting the robot choosing the upper branch at the first Y-junction and subsequently executing another 90° turn in the same direction. Conversely, Figures 7K,L demonstrates the robot initially choosing the alternate path at the first Y-junction and performing a further bend along this route. The repositioning of panels was intentionally chosen to clearly illustrate the robot’s adaptability across different environmental layouts.
During steering, the pivot joint rotor must first establish firm contact with the robot’s inner wall before tendon displacement effectively induces bending of the leading segment. This required sequence inherently introduces some delay, which may slightly impact real-time manual control responsiveness.
After repeated testing, we observed that multiple bending and inflation cycles could potentially cause material degradation in the robot’s root membrane, increasing susceptibility to unintended bending. Additionally, repeated bladder inflation-deflation cycles occasionally caused partial extrusion of the bladder from its holder, potentially leading to punctures and subsequent air leakage. Such damage could impair the reliability of the locking mechanism.
These results confirm that the robot’s steering and growth are not limited to preprogrammed trajectories. Instead, the system can be manually controlled in real time to explore unfamiliar, unstructured environments, reflecting strong potential for use in navigation tasks where environmental layouts are unknown or dynamic.
4 Conclusion
In this study, we presented a novel steering mechanism for SGRs. The proposed design integrates a tendon-driven pivot joint with a pressure-tunable internal bladder, leveraging frictional engagement to selectively couple or decouple the joint from the everting body. This enables smooth transitions between local bending and forward growth with a compact unit, in contrast to body-long steering mechanisms that require distributed actuators along the entire body to achieve shape change.
Through analytical modelling and experimental validation, we demonstrated that the pivot joint can reliably generate controlled steering with low tendon tension and subsequently grow to the steer direction. The proposed kinematic model accurately predicted robot configuration with less than
For the SGR with pivot joint steering mechanism, it relies on environmental contact to passively retain its posture after bending. As the pressurized body generates a self-straightening moment that tends to restore the structure to its original configuration during continued growth. Additionally, the use of a bladder to compress the inverted inner membrane of the tip-everting SGR may interfere with the future integration of tool channels extending from the base, limiting internal payload deployment.
Future work will focus on expanding the system’s directional control into three dimensions using pivot actuation with torque coil attached on the end of the pivot joint structure. By imposing controlled axial rotation, the coil will realign the mechanism and allowing navigation in 3-D space. Moreover, tendon would also be enclosed to reduce direct contact with the robot’s outer membrane, thereby reducing friction accumulation.
Data availability statement
The original contributions presented in the study are included in the article/supplementary material, further inquiries can be directed to the corresponding author.
Author contributions
TJ: Conceptualization, Data curation, Formal Analysis, Investigation, Methodology, Project administration, Software, Validation, Visualization, Writing – original draft, Writing – review and editing. ZB: Data curation, Formal Analysis, Software, Validation, Visualization, Writing – original draft, Writing – review and editing. LC: Conceptualization, Data curation, Formal Analysis, Funding acquisition, Investigation, Methodology, Project administration, Resources, Software, Supervision, Validation, Visualization, Writing – original draft, Writing – review and editing.
Funding
The author(s) declare that financial support was received for the research and/or publication of this article. We acknowledge the support by United Kingdom Royal Society under Grant Nos RGS222365 and IE33657. We also acknowledge the support from University of Sheffield Institutional Open Access Fund.
Conflict of interest
The authors declare that the research was conducted in the absence of any commercial or financial relationships that could be construed as a potential conflict of interest.
Generative AI statement
The author(s) declare that no Generative AI was used in the creation of this manuscript.
Publisher’s note
All claims expressed in this article are solely those of the authors and do not necessarily represent those of their affiliated organizations, or those of the publisher, the editors and the reviewers. Any product that may be evaluated in this article, or claim that may be made by its manufacturer, is not guaranteed or endorsed by the publisher.
References
Blumenschein, L. H., Coad, M. M., Haggerty, D. A., Okamura, A. M., and Hawkes, E. W. (2020). Design, modeling, control, and application of everting vine robots. Front. Robotics AI 7, 548266. doi:10.3389/frobt.2020.548266
Blumenschein, L. H., Usevitch, N. S., Do, B. H., Hawkes, E. W., and Okamura, A. M. (2018). “Helical actuation on a soft inflated robot body,” in 2018 IEEE international conference on soft robotics (RoboSoft), 245–252. doi:10.1109/ROBOSOFT.2018.8404927
Coad, M. M., Hammond, F. L., Naclerio, N. D., Cutler, S., Yoder, L., Rone, W. S., et al. (2020). Vine robots: design, teleoperation, and deployment for navigation and exploration. IEEE Robotics and Automation Mag. 27, 120–132. doi:10.1109/MRA.2019.2947538
Davy, J., Greenidge, N., Kim, S., Tinsley, L. J., Lloyd, P., Chandler, J. H., et al. (2024). Vine robots with magnetic skin for surgical navigations. IEEE Robotics Automation Lett. 9, 6888–6895. doi:10.1109/lra.2024.3412637
der Maur, P. A., Djambazi, B., ur, Y. H., ormann, P. K., ubler, A., Lustenberger, M., et al. (2021). “Roboa: construction and evaluation of a steerable vine robot for search and rescue applications,” in 2021 IEEE 4th international conference on soft robotics (RoboSoft) IEEE, 15–20.
Do, B. H., Wu, S., Zhao, R. R., and Okamura, A. M. (2023). Stiffness change for reconfiguration of inflated beam robots. arXiv Prepr. arXiv:2307.03247. doi:10.48550/arxiv.2307.03247
Haggerty, D. A., Naclerio, N. D., and Hawkes, E. W. (2021). Hybrid vine robot with internal steering-reeling mechanism enhances system-level capabilities. IEEE Robotics Automation Lett. 6, 5437–5444. doi:10.1109/LRA.2021.3072858
Hawkes, E., Blumenschein, L., Greer, J., and Okamura, A. (2017). A soft robot that navigates its environment through growth. Sci. Robotics 2, eaan3028. doi:10.1126/scirobotics.aan3028
Li, P., Zhang, Y., Zhang, G., Zhou, D., and Li, L. (2021). A bioinspired soft robot combining the growth adaptability of vine plants with a coordinated control system. Research 2021, 9843859. doi:10.34133/2021/9843859
Liu, Z., and Kleiner, Y. (2013). State of the art review of inspection technologies for condition assessment of water pipes. Meas. J. Int. Meas. Confed. 46, 1–15. doi:10.1016/j.measurement.2012.05.032
Mendoza, M. J., Naclerio, N. D., and Hawkes, E. W. (2024). “High-curvature, high-force, vine robot for inspection,” in 2024 IEEE international conference on robotics and automation (ICRA) (IEEE), 3014–3021.
Qin, K., Tang, W., Zong, H., Guo, X., Xu, H., Liu, X., et al. (2025). Parthenocissus-inspired soft climbing robots. Sci. Adv. 11, eadt9284. doi:10.1126/sciadv.adt9284
Sanati Nezhad, A., and Geitmann, A. (2013). The cellular mechanics of an invasive lifestyle. J. Exp. Bot. 64, 4709–4728. doi:10.1093/jxb/ert254
Steer, M. W., and Steer, J. M. (1989). Pollen tube tip growth. New Phytol. 111, 323–358. doi:10.1111/j.1469-8137.1989.tb00697.x
Takahashi, T., Tadakuma, K., Watanabe, M., Takane, E., Hookabe, N., Kajiahara, H., et al. (2021). Eversion robotic mechanism with hydraulic skeletonto realize steering function. IEEE Robotics Automation Lett. 6, 5413–5420. doi:10.1109/LRA.2021.3073653
Taylor, R. H., and Stoianovici, D. (2003). Medical robotics in computer-integrated surgery. IEEE Trans. Robotics Automation 19, 765–781. doi:10.1109/TRA.2003.817058
Wang, S., Zhang, R., Haggerty, D. A., Naclerio, N. D., and Hawkes, E. W. (2020). “A dexterous tip-extending robot with variable-length shape-locking,” in 2020 IEEE international conference on robotics and automation (ICRA). doi:10.1109/ICRA40945.2020.9197311
Keywords: soft growing robot, actuation mechanism design, tendon actuated, confined space navigation, soft robot
Citation: Ji T, Bi Z and Cao L (2025) A pivot joint steering mechanism for tip-everting soft growing robots. Front. Robot. AI 12:1627116. doi: 10.3389/frobt.2025.1627116
Received: 12 May 2025; Accepted: 04 July 2025;
Published: 17 July 2025.
Edited by:
Hongjun Xing, Nanjing University of Aeronautics and Astronautics, ChinaReviewed by:
Mijaíl Jaén Mendoza Flores, University of California, Santa Barbara, United StatesJie Zhang, Dalian University of Technology, China
Rajashekhar V. S., Indian Institute of Technology Kanpur, India
Matthew Hausladen, Northeastern University, United States
Yunwei Zhao, Beihua University, China
Copyright © 2025 Ji, Bi and Cao. This is an open-access article distributed under the terms of the Creative Commons Attribution License (CC BY). The use, distribution or reproduction in other forums is permitted, provided the original author(s) and the copyright owner(s) are credited and that the original publication in this journal is cited, in accordance with accepted academic practice. No use, distribution or reproduction is permitted which does not comply with these terms.
*Correspondence: Lin Cao, bC5jYW9Ac2hlZmZpZWxkLmFjLnVr
†These authors have contributed equally to this work