- 1Birmingham Centre for Energy Storage (BCES), School of Chemical Engineering, University of Birmingham, Birmingham, United Kingdom
- 2Department of Materials, University of Barcelona, Barcelona, Spain
A comprehensive and updated review is provided in this article, with a focus on water sorption-based thermochemical storage (WSTCS) materials, covering materials and their manufacturing routes. The state of the art of 22 most relevant salt hydrates is classified into seven groups (bromides, sulphates, carbonates, chlorides, nitrates, hydroxides, and sulphides) and studied as candidates. This is followed by a discussion on TCS material manufacturing, covering both conventional (shaping, pelletizing, etc.) and more advanced routes (e.g., extrusion, 3D printing, encapsulation, etc.). Finally, concluding remarks are presented, including limitations and future potentials for TCS research.
Highlights
- This study provides a comprehensive and updated review of water sorption-based thermochemical storage
- The 22 most relevant salt hydrate (bromides, sulphates, carbonates, chlorides, nitrates, hydroxides, and sulphides) candidates are reviewed
- Conventional manufacturing routes (shaping, pelletizing, etc.) and more advanced routes (e.g., extrusion, 3D printing, encapsulation, etc.) are discussed
1 Introduction
Nowadays, renewable energy (wind, solar, tidal, geothermal, etc.) is a hot topic as it offers energy resources with the potential of eventually reaching a zero-carbon energy future. One of the biggest challenges to achieve this is the mismatch between most renewable energy supply and end-user demand (Aydin et al., 2015). Energy storage has a key role to play in this regard, as it can store surplus energy to bridge generation and demand. Thermal energy storage (TES) is one of the storage technologies that have attracted increasing attention in recent years (N’Tsoukpoe et al., 2009). TES can be divided into sensible, latent, and thermochemical categories. This study concerns thermochemical heat storage (TCS), which has a very high energy density and virtually zero loss during storage and is particularly suitable for large-scale, medium- to-long-term energy storage, although it can also be used for meeting short-term needs. The TCS, however, is currently still in its early stage of development with the bulk of the activities still embedded in academic research (Delta Energy & Environment Ltd, 2016).
TCS refers to the use of reversible chemical reactions to store large quantities of thermal energy in a compact volume. The material is charged when heat is applied by using different chemical reactants, and one or more products of the reaction are stored separately. Three different mechanisms can be used to store thermochemical heat (Aydin et al., 2015).
(1) Physical sorption is caused by surface forces with storage temperatures starting at 30°C
(2) Chemical sorption is caused by covalent attraction at temperatures above 100°C
(3) Reversible chemical reactions are caused by ionic forces at temperatures above 200°C
Among the TCS technologies, sorption offers a high storage capacity in a low-to-medium temperature range. Researchers have extensively worked on developing the systems up to the prototype level; however, the full understanding and complexity of these reactions’ mechanisms, given the poor scalability of the systems and the scattered information among the published studies, suppose a barrier to the TCS technology deployment. Although some systems have been tested at the reactor level in the literature (Zondag et al., 2013; de Boer et al., 2014; Michel et al., 2014; Michel et al., 2016), the levels have not yet been interconnected from the conceptualization–laboratory scale to prototype level.
Most of the reviews published in the area reported the materials used, systems implemented, and development status at the time being. A brief state of the art of the most relevant (most-cited) reviews published is provided in the following lines. N’Tsoukpoe et al. (2009) published a landmark review in 2009 that set the pathways to thermochemical energy storage. The authors presented the materials used in long-term sorption solar energy storage and the ongoing projects at that time. They highlighted closed absorption systems as the future direction for TCS systems, concluding that this system could lead to satisfying results with proper system optimization tasks. Cabeza et al. (2017) published an article in 2017 mainly oriented to absorption systems, discussing the operation principle of the technology, and the materials used or in search are listed and compared. The authors concluded that sorption had advanced very much due to the immense amount of research carried out around heat pumping and solar refrigeration. The same year, Donkers et al. (2017) provided a review on salt hydrates aimed to screen and select potential candidates for seasonal storage. Therefore, the authors performed a literature review followed by a framework of boundary conditions to narrow down to different candidates, according to certain operational conditions. As a result, potassium carbonate (K2CO3) showed the best performance, although requiring a change in the design of seasonal heat storage systems, which according to the authors is needed to overcome energy density and price issues. In 2019, Jarimi et al. (2019) published a review on the recent progress of TCS systems. The authors provided a comprehensive overview of three directions, namely, sorption materials, sorption reactor design, and sorption process design. In 2020, Clark et al. (2020) published an article reviewing the state of the art of hydrates in building applications. The authors outlined that to further develop this technology and bring it closer to commercialization, a merging of research from both material and system design viewpoints is needed. They also highlighted the main research lines to tackle at the material, reactor, and modeling level.
The reviews published are of outstanding importance for the scientific community as they drew the pathways for TCS during the last decades. However, the authors identified a gap in the literature when it comes to linking the technology progress from basic material research to material manufacturing at commercial levels. There is a need of understanding, for which have been the most studied materials by replying to the following burning questions: why have they been studied? What are the challenges that have been addressed? Which are the unresolved matters? How to move forward in the following years? With this review article, we aim to provide a guideline for energy researchers in the energy field to lay out the concepts and key challenges to researching the implementation of storage candidates. More importantly, we aim to give an overview of the current status to understand the blueprint of sorption thermochemical storage that can eventually help draw the progress and roadmap of the technology in the following years. The eventual goal is to assess the current state of the art and bring up the importance of water sorption-based materials in the energy scenario and propose a catalog of material candidates and their implementation challenges. The state of the art of an extensive list of water sorption candidates is reviewed, and their specific challenges are identified. Moreover, we dive into the commercialization challenges of thermochemical materials that are directly linked to the water sorption material formulation approaches to address the storage media challenges, by a review of conventional (shaping, impregnation, etc.) and emerging manufacturing routes (extrusion, encapsulation, etc.) and the possible manufacturing pathways.
2 Scope and guidance
This study aims for both newcomers and experienced researchers working on thermochemical energy storage and more specifically for researchers interested in developing and processing water sorption storage media. The main body of the article is divided into three main blocks. The first one provides an assessment of water sorption chemical storage with analyses on publication rates and the importance of water sorption in the energy scenario, and the second block includes a comprehensive literature review on water sorption screening candidates from low to medium application, namely, sulphates, nitrates, carbonates, chlorides, and bromides. The third block presents the current conventional and emerging manufacturing routes applied to TCS pure materials and composites. Finally, an outlook and conclusions are presented to tie up the concepts presented in the three previous blocks.
3 Importance of water sorption chemical storage
Sorption storage technologies store heat by breaking the binding forces, such as van der Waals forces or covalent forces, between a sorbent and a sorbate (Clark et al., 2020). The heat required to break the binding forces can be higher than that associated with the evaporation heat of a pure sorbate (e.g., water). As a result, the energy density of sorption-based TCS materials can be significantly higher than that of PCMs. Sorption-based systems are classified into sub-groups (Table 1): (1) solid adsorption, (2) liquid absorption, (3) chemical reactions, and (4) composites (Yan and Zhang, 2022). Sorption chemical reactions are divided into coordination reaction of ammoniate with ammonia and hydration reaction of salt hydrate with water (Soda and Beyene, 2016). In contrast to liquid absorption and solid adsorption, the chemical reaction is mono-variant, and the equilibrium uptake is defined by only one independent property (pressure or temperature) and the working temperature is easily controlled and adjusted by changing the pressure (Zhang et al., 2016). The sorption chemical reaction hysteresis may exist (Soda and Beyene, 2016). Sorption reaction systems provide high ESD and cover different ranges of heat source temperatures depending on the salt type (Posern and Osburg, 2017). WTES takes place by the absorption and desorption of water in salt hydrates. Salt hydration is viewed as two steps: water adsorption and hydrate formation. Salt hydrates form new crystal structures by dissociating or absorbing water molecules, and this process realizes the storage (Yan and Zhang, 2022).
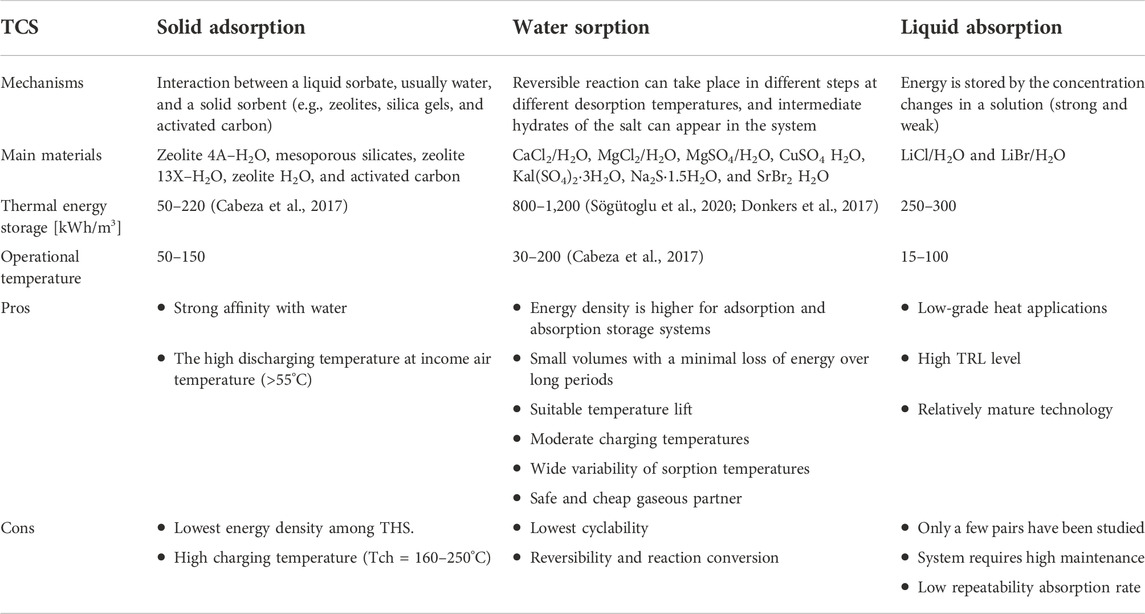
Table 1. Technology overview of sorption thermochemical storage (Donkers et al., 2017;Scapino et al., 2017a;Pathak et al., 2017).
Water sorption thermal energy storage (WSTES) technology is a promising thermal energy storage method that provides the inherent advantages of thermochemical storage systems of high energy storage density and negligible heat loss during storage periods. In addition to allowing the storage of heat in a strategic temperature range (25–200°C), which tackles a need for thermal energy storage in the current energy scenario for space heating and domestic hot water. A total of 66% of the current energy demand for heating in the industry and building sector in Europe accounts for space heating and hot water (<150°C), which falls in the working temperature range of sorption technologies (see Figure 1). Moreover, 28% of energy demand is for process heating at a temperature lower than 200°C. Process heating is most relevant and most challenging to decarbonize. In this framework, WSTES provides higher storage capacity than commercial phase change materials or water tanks for an added feature that they can operate as heat transformers.
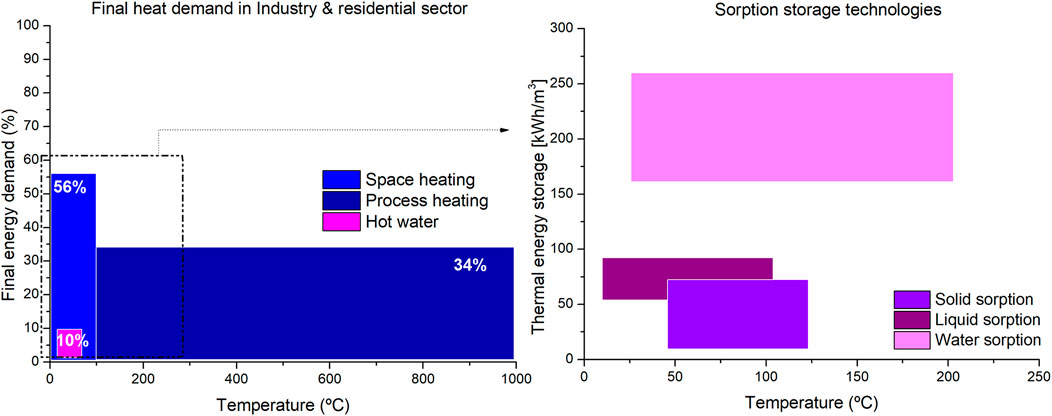
Figure 1. On the left; final heating demand in the industry and residential sector EU-28 2018 per temperature levels. On the right; sorption storage technologies per temperature levels.
In addition, WSTES has a key role in the seasonal and interseasonal thermal energy storage (STES) fields, which can be used to cover a portion or meet the whole space and water heat (SWH) demands in residential and commercial buildings (Alkhalidi et al., 2021; Donkers et al., 2017). Solar thermal energy can be stored in summer to be used in winter for SWH demand. Solar thermal systems use heat collectors to capture solar energy to be used according to the demand load. Energy can be stored for short-term and extended periods (seasonal) according to the storage system’s size. Water-based sorption is the preferred option for seasonal and interseasonal storages among thermochemical storage as it provides a higher energy density in the temperature range.
4 Assessment of the current status and challenges
Thermochemical research is currently successful in the thermal energy storage sector, see Figure 2. Sorption storage accounts for 80% of the thermochemical storage research, given the advanced material research undergone and the wide interest in seasonal storage and the strategic operational temperature range. WTES has been investigated for the application of short-duration, long-duration, or seasonal thermal energy storage by harvesting solar energy or industrial waste heat (Yan and Zhang, 2022). Although WTES has been highly praised in recent years (see Figure 2), its practical application reflects many technical shortcomings. Currently, the research on salt hydrate-based sorption heat storage is driven by material property studies focused on thermogravimetric analysis and energy density evaluation in the single hydration/dehydration process while not targeting the reaction kinetics (ref), which is one of the main challenges for their implementation.
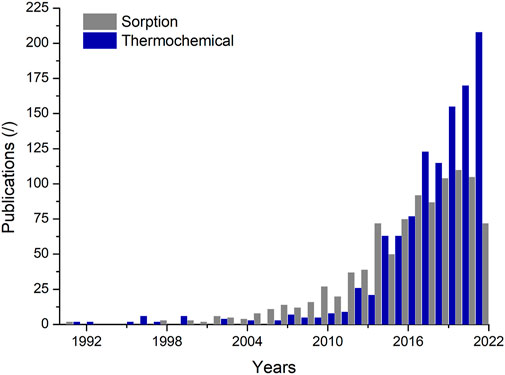
Figure 2. Publications of the thermochemical and sorption technologies. Accessed Web of Science 07/07/2022. Keywords: “thermal energy storage and sorption” and “thermal energy storage and thermochemical.”
4.1 Implementation challenges
WSTES is currently blocked at low TRLs (3–4), given their outstanding implementation challenges that particularly involve the structure stability on how to control the structure at the material and device levels to achieve optimal heat and mass transfer and reaction conversion rate. Researchers have highlighted the storage media stability as the main scalability-limiting factor. Water sorption materials are very dependent on any change in the system (particle size, density, temperature gradient, and kinetics) that can eventually translate into undesired side effects such as agglomeration, volume expansion, deliquescence (formation of a saturated solution), and chemical and physical degradation, see listed challenges in Table 2. The performance of a thermochemical material is defined by the temperature and reaction rate (Sögütoglu et al., 2020). At the same time, the temperature at which heat can be retrieved is limited by the reaction equilibrium. Therefore, to optimize the performance, the energy must be stored as close as possible to the equilibrium conditions (with workable reaction rates). Hence, ensuring a good knowledge and understanding of reaction kinetics is a key. Moreover, during charging/discharging cycles, the material suffers from volume expansion and pore reduction that leads to agglomeration, volume expansion, deliquescence (formation of a saturated solution), and chemical and physical degradation. All these factors are crucial for the technology implementation.
Over the years, authors have come up with different approaches to modify and adapt to those changes, while ensuring homogeneous particle distribution by the prevention of agglomeration effects (Afflerbach et al., 2017). Among the most popular strategies, there is an introduction of salt into a porous (from nano to micro size) solid matrix, which contains the water-based sorption TCM ensuring a stable structure over cycles (Korhammer et al., 2016a; Courbon et al., 2017a; Casey et al., 2017). The composite materials mainly consist of the active storage material (e.g., MgSO4/CaCl2/LiBr) in ranges from 20 to 40 %wt. and the supporting matrix, which can either provide sorption heat (e.g., silica gel/zeolites) or can retain larger amounts of salt but do not participate in the sorption process (e.g., graphite and magnesium oxide) (Scapino et al., 2017a). These composites have been reported to improve thermal stability and heat and mass transfer, allowing them to withstand larger thermal cycles. However, the use of a matrix also brings in new challenges such as the compromise between the large pore size and the improved thermal stability at the expense of the decrease in energy density and the increase in the production cost (Scapino et al., 2017b). These modifications should ideally minimize the cost production process and the low complexity of scalability. In addition, the step processes should not affect the conversion rate of the thermochemical material. Hence, given the high level of uncertainty in this paradigm, this has become the main challenge for the scientific community. This will be discussed in more detail in the manufacturing section of this article.
More efforts should be put into materials R&D, as this is currently the stagnation point for this technology, materials stay mainly in the laboratory research scale and only a few of them have been upgraded to the prototype scale. This is especially triggered by the level of understanding, which is scattered among the TCM materials, and the numerous challenges for the practical application of TCS. The former, level of understanding, is mainly a consequence of the long list of possible candidates and the fact that the material’s research outcomes are periodical; researchers focus on certain materials for years as they seem potential candidates disregarding the others, and this imbalances, even more, the level of knowledge (see Table 2). The latter, the main challenges for practical application, is common for all TCMs such as agglomeration, stability, and cyclability. The main general needs to tackle them are thermal conductivity enhancement, minimizing the cost of storage and the additional unit cost, and maximizing the conversion efficiency. However, there are specific challenges for each TCM that should be individually looked at and every single TCM that can be applicable for a certain application (waste heat, domestic hot water, industrial processes, etc). Thus, diversifying research and efforts can drive future material development and reveal novel candidates that have been overlooked because of applying a general systematic screening method. The main research focus and the related innovation needs of the candidates considered in this review are listed in Table 2, and it is to be noted that those are particularly materially oriented. These are extracted from the comprehensive state of the art presented in Section 5 (Table 3).
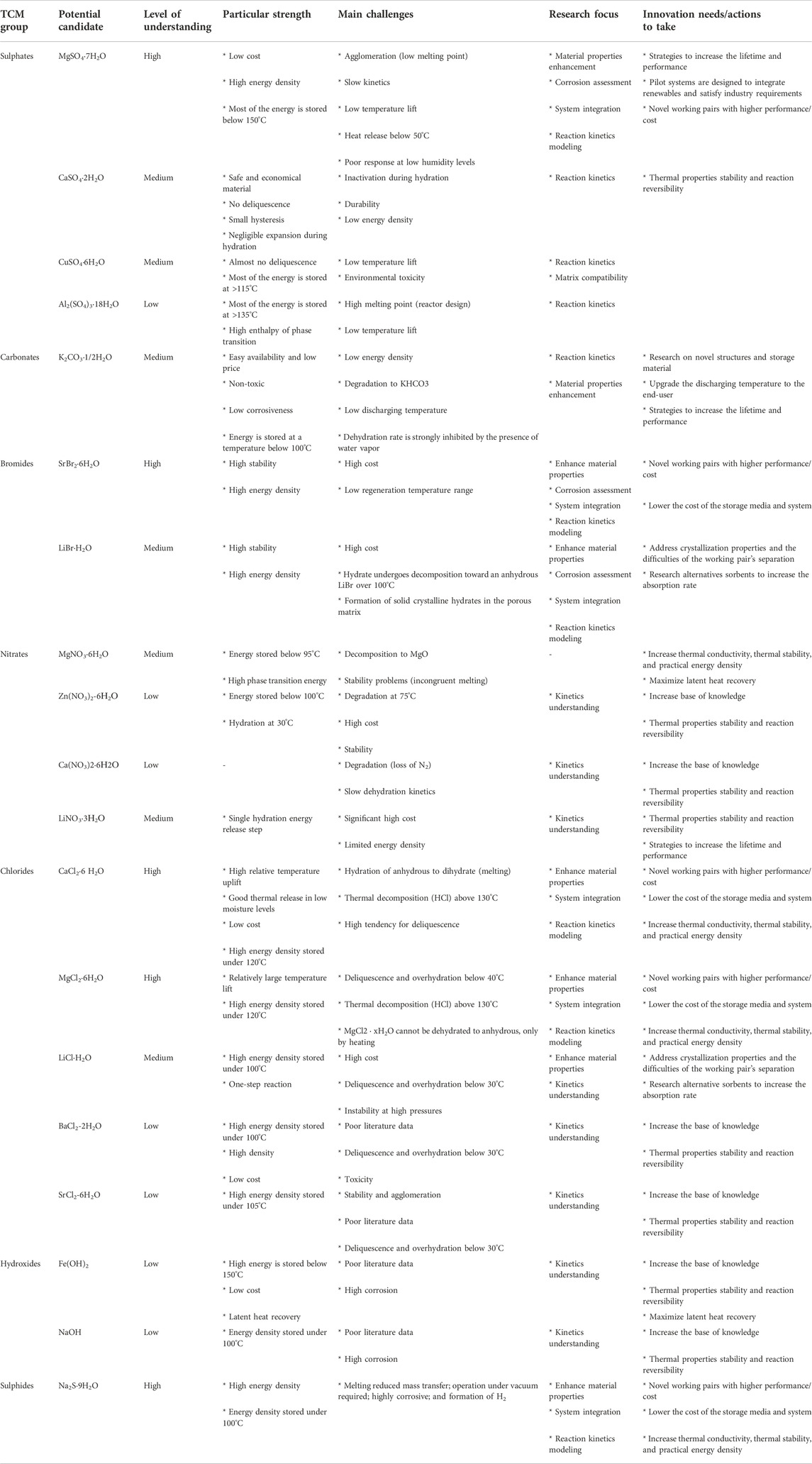
Table 3. Strengths, main challenges, and projections of the potential candidates included in this review article. Insights are extracted from the literature review in Section 5.
4.2 Candidates
The available candidates for WSTES salt hydrates, low to medium, have been reported and listed by researchers in the last few years (Donkers et al., 2017; Clark et al., 2020; Glasser, 2014; Hawwash et al., 2017). The outstanding candidates are listed in Figure 3, according to their deployment level. The preferred candidates by researchers and the ones that have reached higher development levels are magnesium chloride (Kim et al., 2014; Whiting et al., 2014; Nedea et al., 2016; Soda and Beyene, 2016; Pathak et al., 2017; Posern and Osburg, 2017; Sutton et al., 2018a), strontium bromide (Courbon et al., 2017a), (Zhang et al., 2016; Zhao et al., 2016; Fopah-Lele and Tamba, 2017; Fopah-Lele and Gaston, 2017; Gilles et al., 2018), magnesium sulfate (Posern and Kaps, 2008; Whiting et al., 2013; Ferchaud et al., 2014; Calabrese et al., 2018), sodium sulfate (Scapino et al., 2017b;Sharma et al., 1990; De Jong et al., 2014; Roelands et al., 2015; Solé et al., 2016), and calcium chloride (Molenda et al., 2012; Bouché et al., 2016; Jabbari-Hichri et al., 2017; van der Pal and Critoph, 2017; Sutton et al., 2018b). In the past 3 years, potassium carbonate has appeared as a new promising candidate for building applications, although this material has not reached a deployed level yet (Linnow et al., 2014; Sögütoglu et al., 2018; Gaeini et al., 2019; Shkatulov et al., 2020a).
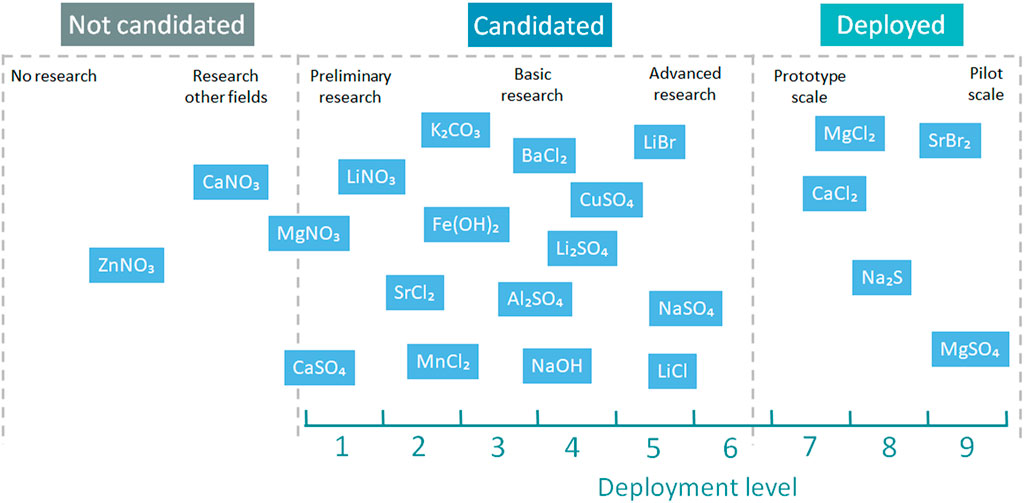
Figure 3. TCS screening candidates for building applications (Donkers et al., 2017;Clark et al., 2020;Glasser, 2014;Hawwash et al., 2017). No research is defined as materials not studied in any field but that is capable of storing thermochemical heat. Research in other fields has been conducted on those materials that have been studied but not in TCS. Preliminary research is materials that have been briefly studied. Basic research is the stage where the materials have been studied in TCS but there is no profound understating. Advanced research is those materials that have been thoroughly researched but are not yet in prototype or pilot scale. Prototype scale is those materials that have been implemented in prototype scale projects. Pilot scale is those materials that have been implemented in pilot scale projects.
An assessment of sorption-based thermochemical materials reviewed in the reported literature is included in this section. This assessment is aimed to identify the strengths, main challenges, and projections of the potential candidates included. In order to achieve that goal, we have gathered the number of publications over the last 25 years, see Figure 4. Looking at the publication trends, calcium chloride and magnesium chloride are the most studied TCM followed by magnesium sulfate, sodium sulfide, and strontium bromide. Calcium chloride was first studied in 1986 by Chaudhari et al. (1986) but increasingly attracted attention from 2005 onward, whereas magnesium sulfate was first published in 1981 (Steinmetz et al., 1981) and has been consistently studied since the early 2000s. Magnesium chloride was first published in 1976 for thermochemical water splitting (Yu Sung and Ulrichson, 1976) but increasingly attracted attention in 2004s. As a general trend, TCS technology is booming and it has following years of research and development to come as some materials have recently been added, possibly to stay, to the list of researched TCM; for example, potassium carbonate, sodium sulfide, strontium chloride, lithium chloride, sodium sulfite, etc.
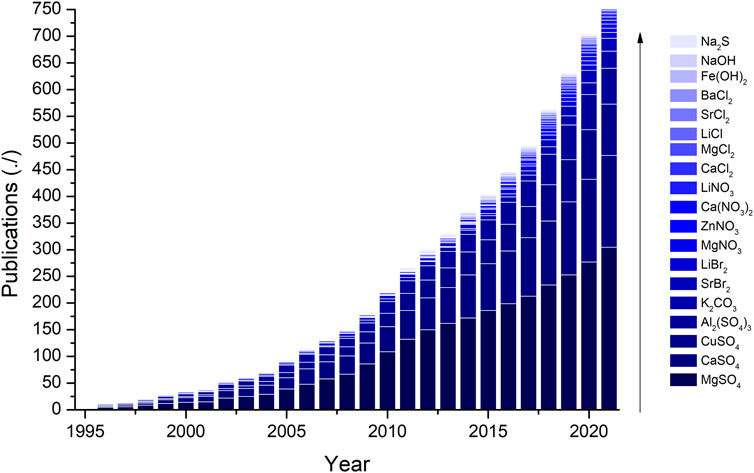
Figure 4. Publications of the water sorption-based materials studied in this review article. Accessed Scopus 06/05/2022.
5 Sorption material candidates
In this section, an extensive literature review is presented including all the WSTES candidates from low to medium temperature in Figure 3. The materials are gathered by their chemical groups, namely, sulphates, carbonates, bromides, nitrates, chlorides, hydroxides, and sulfides. Given that commonly, the reaction steps, reaction temperature, and key physical properties (melting point, density, and crystalline structure) of the different dehydrated states of the salt are not always easy to find and scattered in the literature, the authors provide a list of subsequence reactions and all related to them, see Table 4.
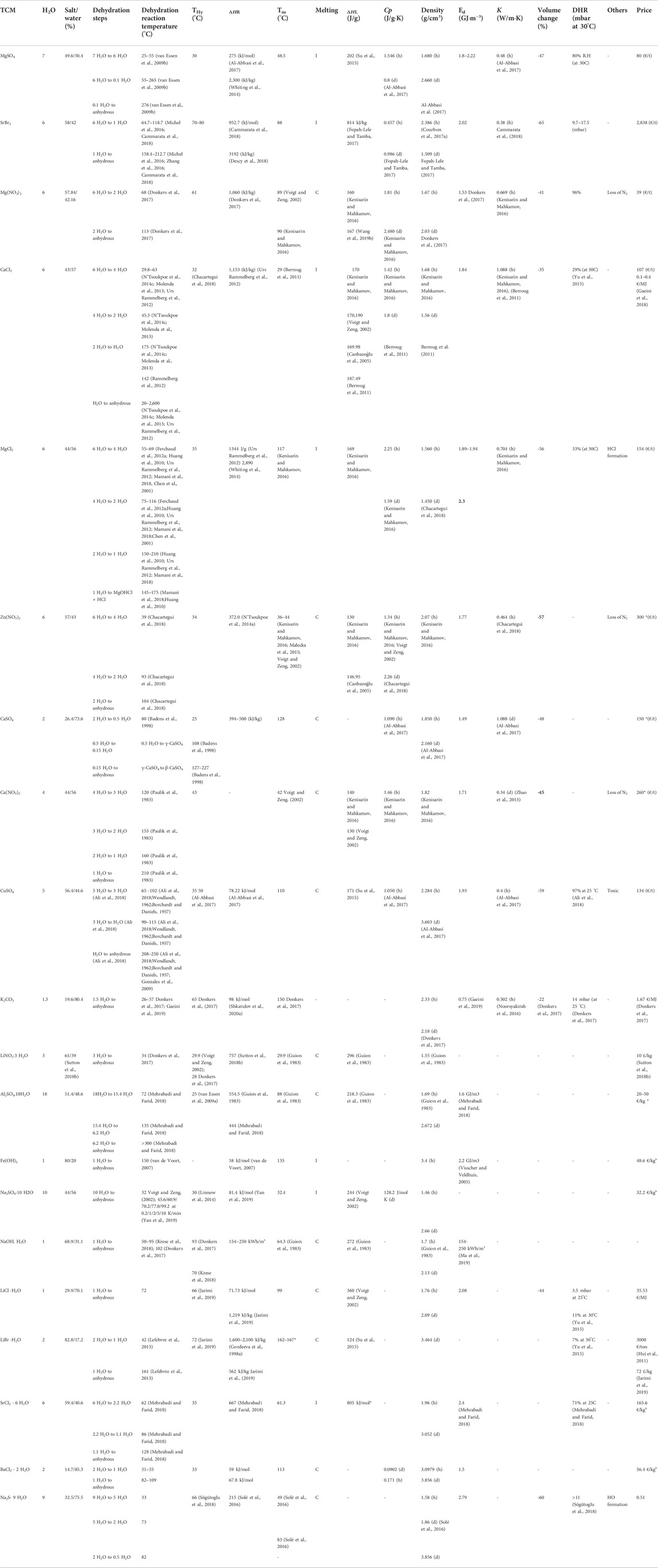
Table 4. Literature review of relevant properties for the preliminary screened materials. It is to be noted that the energy density (Ed) is for an open system, and specific heat (Cp) and thermal conductivity (K) are provided for the hydrated (h) and dehydrated (d) form, respectively, when possible. The melting behavior is defined as congruent (C) and incongruent (I) (Scapino et al., 2017a;N’Tsoukpoe et al., 2014a;Donkers et al., 2017;Xie et al., 2017;Donkers et al., 2016; Fopah-Lele and Tamba, 2017; Riffat et al., 2018). It is to be noted that the samples with * mean the data are collected from the NIST database.
5.1 Sulphates
5.1.1 Magnesium sulfate
Magnesium sulfate is one of the TCMs that accounts for higher energy density (Abedin and Rosen, 2011), and it has been widely studied for seasonal storage (van Essen et al., 2009a; van Essen et al., 2009b; Hongois et al., 2011). Even though the melting point lies in the first dehydration step, this material meets other high-priority requirements such as hydration/dehydration temperature, energy density, deliquescence, and volume variation. Magnesium sulfate allows storing theoretical energy of up to 2.8 GJ m−3 (Okhrimenko et al., 2017). However, the use of magnesium sulfate powder is difficult in a storage reactor because the particles rapidly form agglomerates during dehydration/hydration cycles, thus liming gas transfer and causing reversibility issues and low temperature lift, resulting in poor system performance (Okhrimenko et al., 2017). The thermochemical storage pair works following reaction 1, the heat is released/stored by the hydration and dehydration of magnesium sulfate. The charging/discharging process of magnesium sulfate takes place at a temperature range of 30°C–275°C (van Essen et al., 2009b) and involves three stages.
Regarding its implementation challenges, the authors put their efforts into understanding the underlying mechanisms. Donkers et al. (2015) analyzed magnesium sulfate by NRM under dynamic conditions in a dry nitrogen atmosphere. It was observed that liquid water is formed in the pore of the crystal during dehydration (at 48°C) due to the local increase of the water vapor pressure. van Essen et al. (2009b) studied the influence of different particle sizes since that can also lead to the partial formation of liquid water inside the crystal, especially when working with large particle size distribution (200–500 μm). Previous experimental studies performed at the Energy research Centre of the Netherlands (ECN) showed that this material presents a storage energy density of 1 GJ m−3 when the material is used in a TC storage system with a 50% porosity-packed bed reactor (Ferchaud et al., 2012a). However, slow reaction kinetics under seasonal storage conditions (Ferchaud et al., 2014) might be related to the amorphization of the material (Ferchaud et al., 2012a). This phenomenon occurs when the system works under 13 mbar p (H2O) (corresponding to the average value in northern Europe) (Ferchaud et al., 2014). Ferchaud et al. (2012a) studied the effect of vapor pressure in the dehydration reaction to find the optimal conditions that should be set in a TC storage system. The two consecutive reactions taking place during the dehydration of MgSO4·7H2O show an increase in the reaction rate with increasing p (H2O) until 50 mbar. The reaction rate decreases again for p (H2O) above 50 mbar. This phenomenon is known as the Topley–Smith effect, which is found in many salt hydrates (L’vov, 2007). This effect is often explained by assuming that the increasing water vapor pressure promotes the formation of additional structural defects (additional channels, cracks, and pores), which increases the water vapor removal out of the material and thereby facilitate the formation of a new lower hydrated phase. The authors concluded that the dehydration process is directly influenced by the water vapor pressure applied in a seasonal heat storage system. The kinetics of the reaction increases when the water pressure is below 50 mbar and decreases when pressure is above 50 mbar. When working at lower pressures (less than 50 mbar), the water pressure seems to promote the formation of structural defects, which facilitate the water removal of the material. However, above 50 mbar the water vapor saturation of the material surface reduces the removal of the water vapor in the material. Posern et al. (2015) explained the deliquescence phenomena that take place above the hydration reaction or the deliquescence humidity (DRH) at a certain temperature. Scapino et al. (2017a) also reviewed its potential use in open systems. As demonstrated by van Essen et al. (2009b), the authors also experienced that magnesium sulfate is unable to uptake water above 50°C unless very high relative humidity is applied
5.1.2 Calcium sulfate
Calcium sulfate is a case of a less studied TCM material that presents significant potential for thermal energy storage. Calcium sulfate occurs in nature in three different forms, namely, CaSO4∙2H2O (gypsum), CaSO4∙1.5H2O (hemihydrate), and CaSO4∙0.5H2O (anhydrite) (Freyer and Voigt, 2003). The hydration reaction of calcium sulfate (2 H2O to ½ H2O) has been studied for gas–solid chemical pump applications (Xu et al., 2017). However, this material is mostly used in industrial processes (limestone–gypsum flue gas desulfurization (FGD), production of phosphoric acid or phosphate fertilizers) and has not been boarded to thermochemical storage. Some industrial processes are accompanied by the crystallization of calcium sulfate phases such as the wet limestone–gypsum flue gas desulfurization (FGD), the hydrometallurgical production of zinc and copper, and the recovery of natural gas and oil. Given its application as a binder and building material, attention has also been paid to the hydration–dehydration processes of calcium sulfate for chemical heat pumps. CaSO4 hydration CHPs offer certain advantages, such as high heat density, using only safe and economical materials, no deliquescence, very small hysteresis, negligible expansion in hydration, long-term storage of the absorbent and products, and low heat loss (Shiren et al., 2020). As the main disadvantages, previous studies have reported the problem of inactivation of CaSO4 due to hydration under high water vapor pressure (Lee et al., 2014; Richter et al., 2018); however, CaSO4 has the potential to improve durability by material development as shown by Shiren et al. (2020). Strydom et al. (1995) investigated the thermal dehydration of synthetic calcium sulfate at different heating rates. They concluded that dehydration takes place in three steps, which are highly influenced by the number of impurities present in the salt. The first dehydration stage is driven by nucleation, and the second and third stages are diffusion controlled.
The second dehydration (loss of 1.5 mol of water) overlaps with the first dehydration, and the reaction from dihydrate to hemihydrate is observed to be very slow under 95°C. While the last stage is uncertain to determine where it starts and ends, at 450°C the authors still observe some traces of CaSO4·0.15 H2O together with anhydrous. Hudson-Lamb et al. (1996) studied the dehydration of natural gypsum and pure calcium sulfate dihydrate. Although the authors stated that the dehydration takes place in two different steps, from dihydrate to hemihydrate and from hemihydrate to anhydrous, they also found traces of CaSO4·0.15H2O at 240 °C. Unlike Strydom et al. (1995), at 450 °C only anhydrite was present in the calcium sulfate. Badens et al. (1998) also studied the dehydration of gypsum powder, reporting the presence of two anhydride species γ-CaSO4 and β-CaSO4. The first one is called soluble anhydride because of its spontaneous hydration into hemihydrate under normal atmospheric conditions, and the beta form is called the insoluble anhydride. The transformation from alpha to beta takes place at approximately 127–227°C. The thermal path highly varies on the vapor pressure, and the authors found that at 500 Pa or below there is only one dehydration product from gypsum to γ-CaSO4. At 900 Pa, the hemihydrate is an intermediate product between gypsum and γ-CaSO4. Ogura et al. (2007) proposed a reversible chemical heat pump based on calcium sulfate and water reaction. They particularly studied the reaction from the hemihydrate to anhydrous state in the open and closed systems. The main outcomes were related to the reaction rate in the open system, which was not different from the semi-open system data and quite close to that in the closed system. Lee et al. (2014) studied the same reaction also for a CHP system, storing heat at around 100°C. The authors calculated the hydration and dehydration conversions after 450 cycles; they observed a reaction degradation given the irreversible transformation of III- CaSO4 to II- CaSO4, which are different forms of the crystal structure. From these results, they concluded that this phenomenon is dependent on proper pressure control (423 K at 30 kPa, 413 K at 151 kPa, and 403 K at 453 kPa) for ensuring the durability of the material. Richter et al. (2018), in their material screening study, also included calcium sulfate, which showed appropriate temperature levels for the reversible hydration reaction and a small reaction hysteresis. Recently, Shiren et al. (2020) studied calcium sulfate for waste heat recovery at a temperature of 423 K or less.
5.1.3 Copper sulfate
Copper sulfate (CuSO4) is a salt hydrate material that has the advantage of having a high DRH at ambient temperature (25°C), and the dehydration of the first four water molecules can be driven by a low-temperature heat source of 60–85°C. Such attributes have attracted the researcher’s attention as a new working pair for thermally driven adsorption desalination–cooling systems (ADCSs). Ali et al. (2018) explored the use of copper sulfate in ADCS by studying the effect of changing relative pressure in the sorption reaction. The authors concluded that the copper sulfate system could be driven by solar energy or other low temperature renewable energy heat source (55–85°C), allowing the activation energy of 25.053 kJ/mol. The salt dehydration studies were mostly in the ‘60s and ‘80s (Borchardt and Daniels, 1957; Reisman and Karlak, 1958; Wendlandt, 1962; Mu and Perlmutter, 1981; Sørensen, 1981), and some comparative studies with other thermochemical materials have been published in the last years (Glasser, 2014), (Savchenko et al., 2006), (Al-Abbasi et al., 2017). Wendlandt (1962) studied the dehydration of copper sulfate, concluding that the dehydration from hepta to the trihydrate occurs in two steps and an intermediate phase CuSO4∙4 H2O at high pressures. Borchardt and Daniels (1957) studied the X-ray diffraction and dehydration stages. They found that no peaks appear between 275 and 725°C, and above 725 °C the two-stage decomposition from CuSO4 to CuO with CuSO4 and CuO as an intermediate was observed. However, they did not find any traces of the tetrahydrate, concluding that Borchardt and Daniels must have had a sample consisting of a mixture (CuSO4∙3 H2O and adhering solution). A number of up-to-date studies have studied hybrid composites, Savchenko et al. (2006) prepared a silica gel/copper sulfate “salt in a porous host matrix” composite, concluding that copper sulfate allowed the lowest salt content among the salts studied (17.3 wt% of salt content), although the ratio between the linked metal and the free metal was the highest, with an increasing salt content, and the free metal fraction increased as well. Al-Abbasi et al. (2017) overviewed the performance characteristics of copper sulfate, revealing that the salt shows a high thermal efficiency, slow reaction kinetics, and the melting during dehydration significantly affects the lifetime over consecutive cycles. The copper sulfate can be also used to produce hydrogen by water splitting using the decomposition reaction after full dehydration of the salt, as reported by Gonzales et al. (2009). Although the dehydration reaction is considered in the cycles, this is not the driving force for the hydrogen production (Bhosale et al., 2016).
5.1.4 Aluminum sulfate
Aluminum sulfate hydrated salt presents a reasonable dehydration temperature and high enthalpy of hydration/dehydration, which made it to be considered one of the most promising TCS materials. Aluminum sulfate hydrates, Al2(SO4)3·nH2O, range from 0 to 18 n and have been reported by several authors (Bassett and Goodwin, 1949; KŐmives et al., 1984; Mehrabadi and Farid, 2018; Guide for Authors, 2022). Further decomposition, as can be seen in reactions from 1 to 4,
and
occurs between 770 and 890°C in oxygen (Johnson and Gallagher, 1971).
The dehydration process of Al2(SO4)3·18H2O involves several phase transformations from high to low hydration phases until fully dehydrated Al2(SO4)3. Jabbari-Hichri et al. (2016) expressed the disagreement on which is the more stable hydrated form, reviewing several authors’ studies where 14 or 17 (KŐmives et al., 1984) was claimed the most stable. Sixteen hydrated forms have also been found but are unstable. In addition, hydrates containing 12, 9 (Guide for Authors, 2022), and 6 mol of water have been studied by the decomposition of higher hydrated forms. The clear advantage of aluminum sulfate compared with other hydrate salts is the higher enthalpy of phase transition, which may significantly increase the heat storage capacity (Meisingset and Grønvold, 1986; Kruk et al., 1997). Çılgı and Cetişli (2009) studied the thermal decomposition of Al2SO4· 18H2O by the TG method and four decomposition stages were found. Three of them were dehydration processes, Eqs 3–5, all endothermic reactions, where 2, 10, and 6 mol of water was lost, respectively. The last stage is sulfate decomposition.
Zondag et al. (2011a) considered the aluminum sulfate hydrated form as a candidate for working temperatures between 50 and 150 °C. The results of the study selected calcium and magnesium chlorides; chlorides showed a higher temperature lift of 11–19, whereas aluminium sulfate showed a lift of 1–2 °C (van Essen et al., 2009a). However, Al2SO4· 18H2O, like others, present a melting temperature above the discharging temperature leading to systems without melting in the reactor during the discharging process, which complicates the design of the system. Therefore, it has also been studied in composites with supporting porous matrices such as mesoporous amorphous silica. The presence of the hydrated salt dispersed on the pores facilitated the hydration of both salt and supported adsorbing higher amounts of water, hence a consequently higher heat capacity (KŐmives et al., 1984). Mehrabadi and Farid (2018) also studied Al2SO4· 18H2O along with other TCM in different composite/host matrices. Overall, Al2SO4· 18H2O exhibits a very small temperature lift (DT = 10°C) during hydration of Al2SO4· 5H2O at 25°C under 32 mbar; only 1–2°C of lift at 50°C under 13 mbar (N’Tsoukpoe et al., 2014a).
5.1.5. Other sulphates
Other sulfate hydrated salts have been studied and considered potential candidates for TCS. However, several undesired findings have been relegated to potential candidates. Li2SO4 and Na2SO4. have not shown significant reversibility under 100 °C when subjected to a heating rate of 10 K min (N’Tsoukpoe et al., 2014a). In addition, Li2SO4 presents acute toxicity and, like all lithium materials, limited lithium resources (N’Tsoukpoe et al., 2014a).
Yan et al. (2019) studied the melting and dehydrating processes of different hydrated salts. They determined that a high heating rate during the dehydrating process leads to the formation of molten hydrate, showing a lower dehydrating rate and higher activation energy when it is further dehydrated. In the case of Na2SO4, a dehydrating–dissolving process is suggested, and a mutual effect of melt and dehydration influences the equilibrium state. Moreover, Na2SO4 ·10H2O high content and weakly linked water molecules can be considered a concentrated salt aqueous solution, presenting incongruent melting, which leads to the formation of lower hydrate salt, which is irreversible and leads to the loss of storage capacity. Zinc sulfate hexahydrate has also been studied recently by Rehman et al. (2021). The authors concluded that six water molecules were released with associated energy of 1747 J⋅g−1, from 25°C to 150°C. Moreover, the water sorption study ensured that at 75% RH the material absorbs maximum water under ambient air temperature.
5.2 Carbonates
5.2.1 Potassium carbonate
Potassium carbonate was proposed by Donkers et al. (2017) for open and closed systems for domestic applications, although they also stated the inconvenience of its low energy density. Due to this, we decided to include this study, aiming to provide more experimental data and evidence of the physical and chemical properties of potassium carbonate. In Donkers’s work, they applied four criteria to select a TCM according to energy density on a material level above 1.3 GJ m−3, hydration temperature above 50°C, dehydration temperature below 120 °C, and a melting point above the dehydration temperature. Among 25 candidates, the reaction of K2CO3 (0–1.5) was the one that accounted for the lowest volume change while is not strongly corrosive, no higher hydrates are known, and it has no known unsafe side reactions. The interest in potassium carbonate lies in its easy availability, reasonable capacity for water uptake, and energy density at low temperatures (below 100 °C), while better stability than other salts that show higher energy density attributes. Since this work was published, some other authors have studied potassium carbonate for building applications. Gaeini et al. (2019) studied the reaction kinetics and mechanisms of de/re-hydration of K2CO3. According to their outputs, the dehydration takes place on a single step from sesquihydrate to anhydrous with an enthalpy of reaction of 60.88 kJ/mol and a bulk material energy density of 0.75 GJ m−3. The performance of the material improves upon cycling since its kinetics become faster after each cycle (Gaeini et al., 2019). Despite the advantages, the application of K2CO3 is challenged by the slow hydration rate, swelling/shrinking, and particle agglomeration (Shkatulov et al., 2020a).
5.3 Bromides
5.3.1 Strontium bromide hexahydrate
Strontium bromide has been detected as one of the most promising salts along with magnesium sulfate (N’Tsoukpoe et al., 2014a). SrBr2·6H2O has been already well-investigated at the laboratory and prototype level for various applications either for solar cooling and heat storage in a closed process (Lahmidi et al., 2006), or seasonal storage of solar energy in an open process (Michel et al., 2014;Marias et al., 2014). For short storage applications, it can be considered as storage and thermal comfort material (also as phase change material). The high enthalpy (
5.3.2 Lithium bromide monohydrate
Given that the DRH values for LiBr (7% at 30°C) are quite low, meaning that it is more likely for them to form liquid salt solutions directly in most cases, this salt is often applied in liquid/gas absorption cycles (Yu et al., 2015). If the desorption temperature is high enough to generate the solution to its crystallized state or even anhydrous state, the sorption process can be seen as a three-phase process, during which the solid crystal could be completely turned into a liquid solution (Yu et al., 2014). Thus, most of the studies are targeted at those used as an adsorption system for solar heating (N’Tsoukpoe et al., 2013; N’Tsoukpoe et al., 2014b; Myagmarjav et al., 2014; Manole and Lage, 1995). However, lithium bromide can be also considered for ‘open’ TES interseasonal systems, the reaction by water sorption without bringing the salt to the solution. Lefebvre et al. (2013) studied the hydration characteristics of lithium bromide concluding that two different transitions were observed corresponding to the transitions LiBr.2H2O/LiBr.H2O and LiBr.H2O/anhydrous LiBr. LiBr crystallizes in the dihydrated form at the temperature of the storage tank surrounding (5–10°C) with a water content of 29 wt% of water (N’Tsoukpoe et al., 2014b; Lefebvre et al., 2013). Gordeeva et al. (1998a) studied in the ‘90s the confinement of the system “lithium bromide–silica gel” that was prepared by filling pores of silica gel. The authors also estimated the sorption capacity to be 1,600–2,100 kJ/kg. Myagmarjav et al. (2014) developed a novel composite by mixing pure magnesium hydroxide with lithium bromide, the addition of LiBr was found to decrease the estimated activation energy in the dehydration. Casey et al. (2014) studied the insertion of lithium chloride, among other hygroscopic salts, in different matrices (silica gel, zeolite, activated carbon, and vermiculite). The main outputs are that lithium bromide with vermiculite appeared to have significantly higher TES potential compared to the other candidates. Gordeeva et al. (2002) studied the water sorption equilibrium of LiBr confined to pores of a mesoporous synthetic carbon Sibunit and macroporous expanded graphite. They estimated the energy storage to be 1.1 and 2.8 kJ/g in the temperature range from 30 to 140°C. The authors also studied the water uptake over temperature and pressures, concluding that the hydrate is rather stable and possesses no transformation over 25–35 °C. At high temperatures, this hydrate undergoes decomposition toward an anhydrous LiBr (over 100°C). They also remarked on the formation of solid crystalline hydrates in the porous matrix.
5.4 Nitrates
5.4.1 Magnesium nitrate hexahydrate
Magnesium nitrate has been used as a phase change material (PCM), given its relatively high latent heat of fusion (Meisingset and Grønvold, 1986; Kruk et al., 1997; Jabbari-Hichri et al., 2016). However, it also allows for storing heat in the thermochemical reaction (Donkers et al., 2017). These dual materials are called reactive phase change materials. Although it shows a decent energy density, volume change, and a melting point above the hydration/dehydration process, it is usually not considered a strong candidate as it displays a tendency for significant supercooling and decomposes to magnesium oxide under strong heating conditions (Kenisarin and Mahkamov, 2016;Paulik et al., 1988). MgNO3 hexahydrate turns into a dehydrated form if heated above 95°C, the equilibrium diagram of magnesium nitrate and water was reported by Kenisarin and Mahkamov (2016). The dehydration occurs in three steps; from the hexahydrate to the dihydrate showing that the slow dehydration is stable at lower hydrate states before decomposing at 400 °C. Two decomposition steps were observed by Paulik et al. (1988) and Drake et al. (2018), one from 300 to 400 °C with 56% mass loss of the initial hexahydrate and 450–500 °C with 17%. Drake et al. (2018) combined two energy storage methods aiming to harness the advantages of both (latent heat and thermochemical) by studying the eutectic composition of magnesium nitrate and water. For that purpose, they studied the melting and dehydration of magnesium nitrate. They found that from the dihydrate to the complete anhydride (at 270°C), no endothermic peaks can be observed, which they attributed to an obscured peak due to an experiment drift. It has been concluded that the use of quasi-isothermal and quasi-isobaric conditions is needed for an adequate resolution. Since the study was latent heat targeted, they also studied the melting, which they found to be incongruent (a common effect in salt hydrate PCMs). When the magnesium nitrate melts, the water is evenly dispersed, but on freezing, the original crystalline structure may not be perfectly reformed, and these different states may have an energy disparity (supercooling) (Drake et al., 2018). Likewise, higher dehydration temperatures are associated with increased supercooling and incongruent melting. The formation of a lower hydrate from incongruent melting is irreversible. The two stable hydrates of dehydrating are formed by incongruent melting of hexahydrate (Soda and Beyene, 2016).
5.4.2 Zinc nitrate hexahydrate
Similarly, magnesium nitrate, zinc nitrate, and calcium nitrate were proposed for latent heat storage (Xie et al., 2017) but have not yet been explored for thermochemical storage. The solid–liquid equilibrium was studied by Voigt and Zeng, (2002), and they were also screened by Donkers et al. (2017) for domestic applications. Both have an energy density of around 1.5–1.7 GJ m−3 and a dehydration–hydration temperature range that meets the system requirements. The thermal decomposition of zinc nitrate has been recently studied by Małecka et al. (2015), and they found that the dehydration starts at 30 °C, which is accompanied by the melting at 35°C. According to them, dehydration occurs in three consecutive steps that finish at 120 °C. The decomposition of nitrate groups starts at 75 °C and ends at 265 °C, forming ZnO as the final product. The literature shows that it is difficult to get high-purity zinc nitrate from zinc nitrate hexahydrate and compute the stoichiometric content of water (Kumar et al., 2018). Kumar et al. (2018) added nucleation additives to zinc nitrate hexahydrate, and, therefore, they also studied its thermal decomposition.
N’Tsoukpoe et al. (2014a) considered zinc nitrate hexahydrate in their systematic multi-step screening, and they remarked that the partial dehydration of this salt is preceded by the melting. The salt melts during the tests but remains reversible. However, the authors remarked that the reaction needs to be checked deeply because of the lack of coherence in the literature. Meanwhile, Kozak et al. (2003) suggest that the salt does not dehydrate but decomposes in other compounds involving Zn(OH)NO3⋅H2O and HNO3 by following the reactions given below.
Zn(NO3)2·6H2O (solid phase) → pseudo-melting → HNO3–H2O (solution 1:6)→ evaporation (H2O, HNO3), hydrolysis, crystallization→Zn(OH)NO3·H2O (solid phase)→polycondensation, evaporation (H2O, HNO3)→Zn3(OH)4(NO3)2 → →dehydroxylation, thermal decomposition→ZnO (solid phase).
5.4.3 Calcium nitrate tetrahydrate
Calcium nitrate tetrahydrate is one of the most commonly used inorganic salts given its high latent heat and low melting point (Vranes et al., 2010). However, it has not been thoroughly studied for thermochemical storage purposes. Liu and Zhu (2015) used a double-layer coating technology to add an epoxy resin and cement layer to calcium nitrate tetrahydrate, which significantly enhanced the heat resistance of the crystals and reduced the deliquescence problems at room temperature. Guo et al. (2019) proposed a solid–liquid calcium-based composite by adding calcium nitrate tetrahydrate to calcium nitrate hexahydrate as a modifier for latent heat applications purposes. As for magnesium nitrate, Paulik et al. (1983) examined the dehydration of calcium nitrate under quasi-isothermal and quasi-isobaric conditions. They reported, as shown by other authors before, that calcium nitrate dehydrates in four steps. The salt melts at 42.7°C forming a saturated solution that with increasing temperature becomes unsaturated. Until the boiling point, the salt does not lose water, above 135 °C, the solution starts losing water. Therefore, the authors concluded that the dehydration process was not based on consecutive reactions but on the course and overlapping of physical processes such as evaporation, boiling, drying, and solid crust formation.
5.4.4 Lithium nitrate trihydrate
Lithium nitrate trihydrate has also been studied as a potential candidate for thermochemical energy storage (Sutton et al., 2018a; Sutton et al., 2018b). One of the main problems and reasons for not being extensively studied, as with all lithium materials, is their use limitation due to lithium resources (N’Tsoukpoe et al., 2014a).
Sutton et al. (2018b) impregnated LiNO3 into porous vermiculite to form a salt matrix. They concluded that the single step of energy liberation of hydration for LiNO3 allows a mechanism for the rapid hydration of LiNO3 (liberating the energy) on the surface of the SIM and continues to liberate energy at a far slower rate as the salt within the core of the vermiculite particle is hydrated. The same authors in another publication (Sutton et al., 2018a) studied the experimental performance of mixed ‘salt in matrix’ materials. Layering and blending techniques established that the performance could be increased by up to 24% by the correct choice of mixing technique. Layering CaCl2 on LiNO3 provided the most efficient thermal release strategy and yielded a thermal storage density of 0.2 GJ/m3. N’Tsoukpoe et al. (2014a) considered lithium nitrate in their systematic screening concluding that the price might be a limitation due to ongoing pressure on lithium resources. Moreover, the authors could not identify a LiNO3 hydrate with a melting temperature above 60°C. Casey et al. (2017) studied LiNO3 with silica gel, vermiculite, activated carbon, and zeolite 13X, concluding that an energy density of 364 kJ/kg can be reached, with a promising working range of 30°C < T < 140°C, good isotherms, and longtime interval to reach the equilibrium moisture content across all relative humidity.
5.5 Chlorides
LiCl, MgCl2, and CaCl2 are of strong hygroscopicity, which could adsorb water vapor and form a solution in a closed system. This phenomenon is called deliquescence (see Section 4.2), which can bring salt segregation, corrosion in sorption reactors, and deterioration of heat and mass transfer of sorbents (Zhao et al., 2016). Calcium chloride and magnesium chloride are the other two TCMs targeted with significant potential for thermochemical heat storage (van Essen et al., 2009a). They exhibit high energy density at the desired operational temperatures. However, magnesium chloride suffers from thermal decomposition and HCl formation and deliquescence below 40 °C.
5.5.1 Calcium chloride
N’Tsoukpoe et al. (2014c) reviewed the use of calcium hydrate in applied thermal engineering, concluding that calcium chloride is a promising material for drying and heat storage applications. This material is already used for air dehumidification in buildings. Calcium chloride also has the potential to be used as a phase change material, given its melting point of around 30°C. Its use for thermochemical storage is promising although it presents challenges such as low melting point and a high tendency for agglomeration. Tang et al. (2017) studied the working pair zeolite/calcium chloride, by impregnating zeolite 13X with different concentrations of CaCl2 aqueous solutions. They found out that the samples containing 5 wt% and 10 wt% have a better performance than the pure zeolite, the water uptakes equilibrium of formulation with 15 wt% and 20 wt% were lower than the pure zeolite. Richter et al. (2016) studied the CaCl2·4H2O dehydration for industrial waste heat upgrade by using an open system in the range of 100–200°C at 150 C, 130 C, and 100 °C at around 40 kPa, concluding that the system enables the use of waste heat at 100 °C with a thermal upgrade of 65 K. D’Ans et al. (2018) and Courbon et al. (2017b) proposed a working pair based on silica and calcium chloride, with a salt content of 43 wt% and 40–43 wt%, respectively. Meanwhile D’Ans et al. (2018) opted to encapsulate the salt in mesoporous silica, and Courbon et al. (2017b) proposed to successively impregnate the salt solution into silica gel, producing high content and stability composites. Both studies lead to a cycle loading lift of 0.4 g/g. Courbon et al. (2017b) found out that the mechanism of water sorption goes beyond hydration from anhydrous to 4 H2O, the CaCl2∙4 H2O dissolves to form a CaCl2 solution, leading to water trapped in the silica gel pores. Gough et al. (2016) studied the deliquescence of calcium chloride for exploring its potential on Mars. The authors used a Raman microscope to determine the occurrence of deliquescence of the salt for the three phases of calcium chloride (hexahydrate, dihydrate, and anhydrous). They observed that often CaCl2∙2 H2O deliquesced directly into liquid brine without forming CaCl2∙6 H2O phase, jumping the hydration step before deliquescence. Deliquescence was observed to lower with increasing temperature for the hexahydrate, while the dihydrate showed weaker temperature dependence. Savchenko et al. (2006) used the impregnation method to prepare silica gel/calcium chloride composites, concluding that the sorption equilibrium of the composites can be managed by varying conditions of the composite preparation. Jabbari-Hichri et al. (2017) prepared calcium chloride composites with silica gel, alumina, and bentonite (15 wt% of TCM), among all the matrices, silica gel showed the best performance given the low pore blocking and the high heat and water storage values. Jiang et al. (2017) explored the development of bi- and tri-salt graphite composite sorbents by combining magnesium chloride, calcium chloride, and ammonium chloride. The multilevel sorption alleviated the sorption hysteresis and led to a higher energy density. Karunadasa et al. (2018) investigated the correlation between the stability of hydrated/anhydrous products and microstructural changes of calcium chloride, finding that there are two different phases of anhydrous calcium after dehydration (large and small unit cell). The stability of the phases is dominated by the lattice strain, larger crystallite size, and small unit cell volume. Kim et al. (2013) studied a composite comprising a mixture of expanded graphite, magnesium oxide, and calcium chloride for a chemical heat pump application. From the study, the authors proposed a multiplied factor consisting of dehydration rate and mixing weight ratio, which suggested that 0.8 was the optimized value when the mixing molar ratio between CaCl2 and Mg(OH)2 was 0.10. Korhammer et al. (2016b) studied the reaction of the mixture between calcium chloride and magnesium chloride with alcohol, which revealed that the sorption behavior can be controlled by the variation of ethanol pressure and, as confirmed by other authors, that the mixtures of salts from the same family led to a superior thermal behavior with higher heat storage capacities. Gaeini et al. (2018) published a comprehensive study on the stability of calcium chloride-based materials and different manufacturing approaches: impregnated expanded graphite composite, impregnated vermiculite composite, and encapsulated calcium chloride powder. Of all the methods used, encapsulation is the one that shows the best cycling stability, although it allows for the lowest energy density, whereas the impregnated samples lead to an agglomerated structure similar to the dehydrated pure salt, which reduces the conversion rate over cycles. Molenda et al. (2013) studied the reversible reaction of calcium chloride at high H2O partial pressures, which demonstrated that the reaction of calcium chloride is applicable for thermochemical energy storage up to 180 °C. They found intermediate hydration, a metastable step with 0.3 mol H2O/mol CaCl2, although they did not observe the formation of the monohydrate as Gaeini et al. (2018). Interestingly, they noticed the dehydration occurs in two processes depending on the pressure; at high pressures, the 0.3 H2O intermediate step appears to be determinant, while at low pressures the monohydrate appears to be the intermediate step. This revealed a correlation between the formation temperatures, the intermediate species, and the partial vapor pressure. Richter et al. (2016) studied the endothermic dehydration of calcium chloride dihydrate at the laboratory scale exhibiting complete reversibility, thermal and cycling stability, and reasonable kinetics at temperatures up to 200 °C. They reported a thermal upgrade of 35 °C, discharging at 165°C and charging at 130 °C with a full conversion from the anhydrous to the dihydrate. By using the intermediate step (CaCl2∙0.3 H2O) reported by Molenda et al. (2013), the discharging could be conducted at 180 °C, which increases the thermal upgrade to 50 °C but reduces the storage density. Therefore, to increase the thermal upgrade hydration needs to take place at higher temperatures or dehydration at lower ones.
5.5.2 Magnesium chloride
Several studies revealed the promising potential of magnesium chloride for seasonal heat storage in terms of energy density and charging/discharging temperature. Apart from the common issues of instability and decomposition over cycles of other TCMs, this material is particularly disadvantaged by the fact that at ambient temperature it tends to overhydrate into a solution, which causes inhomogeneous dehydration. In addition, above 150 °C (some authors reported even lower temperatures) the chlorides decompose into magnesium hydroxy chloride involving a release of hydrochloric acid. Such a reaction causes obvious damage and reduces the quantity of active sorption material over time. The hydrolysis reaction occurs at the same time as the last dehydration reaction stage (from dihydrate to monohydrate) (Kirsh et al., 1987). Ferchaud et al. (2012a) studied the XRD patterns of hydration/dehydration intending to determine the temperature range over which magnesium chloride remains in a stable hydrated state during its dehydration/hydration reactions (13 mbar). The main outputs of this study are that the minimum hydration temperature should be set at 40 °C to avoid the overhydration of the material; the dehydrate/hydrates to tetra at 100 °C, and hexahydrate at 60 °C; the material remains in a solid state until 30 °C; no characteristic peaks of magnesium hydroxy chloride were observed at 150 °C after 3 h. Gutierrez et al. (2018) recently studied the reversible reaction of a ternary equilibrium solution KCl-MgCl2-H2O. The authors brought more evidence that at temperatures close to 180 °C, small amounts of HCl were observed from the decomposition of magnesium chloride. Also, decomposition and/or melting were confirmed, which had a strong effect on the cycling stability of the active material. According to Zondag et al. (2011b), the formation of HCl was found to occur at temperatures above 150 °C, before 180 °C. They also found out that the material closer to the evaporator was overhydrated, transforming to a gel-like structure after being remained long-term hydrated. Mamani et al. (2018) studied the viability of using bischofite (a material containing 97.4% of MgCl2 ∙ 6 H2O), bringing more shreds of evidence of the hydration/dehydration behavior of the active thermochemical material, following the previously published work. Huang et al. (2010) described the thermal decomposition of magnesium chloride in six steps (under air), from hexa to tetra, from tetra to di, from di to 0.3 H2O/MgOHCl, from 0.3 H2O/MgOHCl to MgOHCl, and from MgOHCl to MgO. Urs Rammelberg et al. (2012) studied the dehydration from hexahydrate to dihydrate in terms of water vapor pressure and conversion independence on the heating rate. The dehydration is completed after 2 h below 140 °C (heating rate 1 °C/min), and they found that the irreversible decomposition side reaction was running side-by-side with the dehydration MgCl2∙H2O at lower temperatures than other authors. According to Rammelberg et al., dehydration occurred in three overlapping stages, which are not highly dependent on the heating rate. Ferchaud et al. (2012b) studied magnesium chloride at a prototype level, they concluded that the thermochemical material could be dehydrated at temperatures below 130 °C, and the hydration was sufficient to provide tap water heating at 60 °C.
5.5.3 Lithium chloride
LiCl is a hygroscopic salt with high moisture capacity, easy renewability, and high chemical stability. It is the most widely used desiccant in commercial rotary dehumidifiers. LiCl/H2O shows significant potential for sorption thermal energy storage with its large water sorption capacity. However, the fact that is a highly hygroscopic salt is likely to turn into a liquid solution when in contact with water vapor. In the temperature range of 19.1–93.5°C, there is anhydrous LiCl and monohydrate system, i.e., solid LiCl, a saturated solution containing monohydrate or dilute solution (Rau et al., 1991). Above 93.5°C, the solution contains anhydrous salt. Therefore, lithium chloride monohydrate dehydration takes place in one step from mono to anhydrous starting at 72°C until dehydration is finalized at 94.1°C. Below 19 °C, the solid phase consists of dehydrated LiCl. The one-step reaction allows for storing 2.08 GJ/m3 in an open system and 1.36 GJ/m3 in a closed system (Donkers et al., 2017).
5.5.4 Strontium chloride
The high energy storage density of SrCl2⋅6H2O (2.6 GJ/m3) further ensures its potential as a promising thermochemical energy storage material, especially at low temperatures as 80% of the energy storage capacity can be driven off at 90°C. The kinetics of this thermochemical material was first studied by Iyimen-Schwarz and Lechner (1983), the authors remarked that strontium chloride dehydrates in three steps in the temperature range from 50°C to 135°C; from hexa to dihydrate (
5.5.5. Barium chloride
Barium chloride was widely studied in the early ’90s, and di- and monohydrate are the most commonly reported hydrates. The BaCl2-H2O system is one of the few hydrates that has been demonstrated to undergo fully reversible dehydration–hydration reactions (Lumpkin and Perlmutter, 1995). Dihydrate to monohydrate and monohydrate to anhydrous salt reactions are commonly observed to proceed in a stepwise manner; however, under moderate vacuum conditions the reactions overlap, and dihydrate reacts directly to form the anhydrous salt. Fenstad and Fray (2006) studied the H2O-BaCl2 equilibrium of the monohydrate and dihydrate proposing an updated diagram. No recent studies have been found for the system BaCl2-H2O; however, many studies have looked at the working pair BaCl2-NH3 (Jiang et al., 2013; Jenkins and Glasser, 2018; Martínez-Tejeda et al., 2018; Ma et al., 2019).
5.6 Hydroxides
Hydroxides, such as Fe(OH)2, have been considered as potential TCM for solar seasonal storage. One of the studies carried out by Visscher and Veldhuis (2005) looked for materials to work under temperatures between 60 °C and 250 °C, an energy storage density higher than 1 GJ/m3 and abundant and easy to mine, simulated the use of Fe(OH)2 according to the following reaction.
The energy storage density of the material, 2.2 GJ/m3 occurred at 150°C. It was observed that when the water vapor was released during the dissociation reaction into the atmosphere, a higher cycle storage density was reached. Also, when latent heat recovery was used, the cycle storage density increased by more than 60%, and the collector area needed was reduced by more than 40%. However, other practical applications were not considered such as corrosiveness or health and safety aspects. Hydroxides, like NaOH, and other corrosive alkalis cause chemical burns, permanent injury or scarring on human or animal tissue, and can cause blindness if contacts with the eye (Hui et al., 2011). Moreover, hydroxides are corrosive in contact with common system materials components such as stainless steel 304, which increases with mass fraction and temperature. Weber et al. (Fumey et al., 2014) reported a NaOH storage for long-term heat storage with high specific heat density designing a system with nearly three times the storage capacity of water ones.
5.7 Sulphides
Sodium sulphide is a widely studied TCM that has reached the prototype level and has been chosen as a candidate in several thermal storage projects like TEPIDIUS, SWEAT, and MERITS. One of the reasons behind that is its large energy density (2.66 GJ/m3 from penta to hemihydrate (Roelands et al., 2015)). Although it attracted significant interest in the past, Na2S.nH2O has some remarkable drawbacks, it is highly corrosive and reactive with the risk of outgassing H2S (Donkers et al., 2017). In addition, physical instability involves phase transitions of sodium sulphide hydrate salts, as shown in the phase diagram of sodium sulphide (De Boer et al., 2002); (1) at a temperature of 49°C, a phase transition of the nonahydrate salt to the pentahydrate salt occurs while simultaneously a solution of sodium sulphide forms, (2) at a temperature of 83°C the pentahydrate structure partially dissolves while it forms a solution of sodium sulphide (Roelands et al., 2015). However, when researchers started to work with Na2S, they were driven by the promising energy density but there was a lack of prototype studies results that later revealed its chemical, physical, and mechanical limitations.
Indeed, all the projects suffered initially from corrosion and faced variable results by overcoming such issues. Until now, there are still concerns raised regarding how the coatings perform in years, and how the last 1.5 water molecules, whereby the loading power is limited given the melting temperature and dehydration temperature are equal at the current vapor pressure. Moreover, the environmental issues due to the toxicity of the salt hydrate and its by-products such as hydrogen sulphide should not be overlooked. This salt has been studied thoroughly to the prototype level, and the main constraints have already been brought up.
6. Sorption storage material manufacturing routes
The challenges at the material level significantly influence the manufacturing strategies, which at the same time limit the technology readiness level of WSTES. In this section, we provide an overview of the manufacturing routes drawn by researchers in the past decade, and we also try to provide a pathway for future research. Currently, the TCM manufacturing routes are divided between conventional manufacturing procedures (shaping and insertion in a binder) and emerging manufacturing procedures (nano-alternatives, encapsulation, and extrusion), and all these procedures are described in this section. The manufacturing paths that have been considered by researchers and the emerging manufacturing routes are summarized in Figure 5.
Little has been carried out on large-scale manufacturing of thermochemical materials, and most work is still at a laboratory scale (from grams to kilos). Until now, only a few approaches for particle stabilization of thermochemical storage materials are reported in the literature 111. The fact is that there is still no agreed approach in the manufacturing process at the laboratory scale, not to mention large scale manufacturing. The publications registered in the last 10 years for conventional and non-conventional manufacturing methods are presented in Figure 6. The binder matrix has been the most widely studied, while encapsulation and nanomaterial composite are attracting researchers’ attention since 2016 while increasing their publication rate yearly.
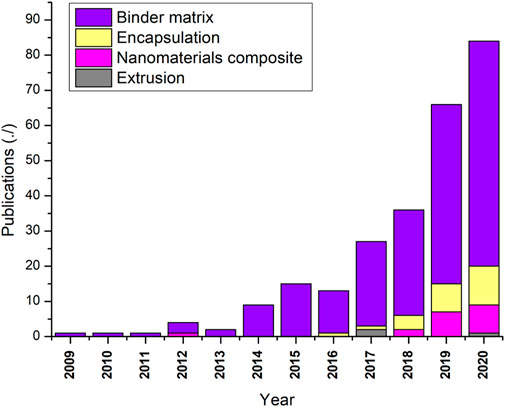
Figure 6. Publications of conventional and non-conventional manufacturing routes. Accessed Scopus 01/12/21 (Scopus data based, 2020).
6.1 Conventional manufacturing routes
Conventional manufacturing routes can be classified into shaping or insertion in a binder matrix. Although these routes are not yet at a commercial scale, they are the most commonly used when TCMs are formulated in laboratories.
6.1.1 Shaping
Shaping or pelletizing pure thermochemical powder is the most convenient way to maximize energy density, as suggested by researchers. Despite shaping might appear as the cheapest and less complex solution, it does not tackle the TCM problems at once as after one cycle of hydration/dehydration a significant change in molar density and molar volume takes place, which leads to a breakage of the pellets or granules decomposing quickly upon repeated cycles (Afflerbach et al., 2017; Fujii et al., 1994).
6.1.2 Insertion in a binder matrix
Potential host matrices (binders) are selected primarily on their ability to disperse the salt, prevent deliquescence during hydration, possess a high internal surface area on which to disperse the salt, be highly porous (to both gas and liquid phases), lightweight, durable, inert, and be of relatively low cost (Sutton et al., 2018a). However, binders can influence TCM performance in terms of permeability, pressure drop, and mechanical integrity, among others (Sarkar and Bhattacharyya, 2012; Gordeeva and Aristov, 2012). The first publications on the composites ‘salt inside porous matrix’ (CSPM) appeared at the end of the 20th century. Since then, the number of studies has increased exponentially (see Figure 4). Different methods can be used for the insertion of TCM in a matrix.
(1) Simple/direct mixture method: This method relies on the matrix-TCM mixing, which optimizes material’s ratios (to obtain a high energy density) and porosity (good heat and mass transfer) (Mauran et al., 1993; Sánchez et al., 2003; Klein and Groll, 2004).
(2) Another method used is melting–solidifying, which consists of melting the TCM together with the matrix (cellulose is the polymer normally used). The mixture is then dispersed in a hot solution (Roelands et al., 2015) and cooled to room temperature to finally form pellets by compression.
(3) Impregnation is defined as the procedure whereby a certain volume of solution containing a precursor of an active phase is placed in contact with a solid phase (support or another active solid phase), which, in a subsequent step, is dried to remove the imbibed solvent (Casey et al., 2017), (Van Dillen et al., 2003). Impregnation has been the most studied insertion method so far given that they are relatively inexpensive, and allow TCM final properties and configuration to be controllable by tailoring the pore size, a load of salt and topology. Impregnation methods can be categorized depending on the volume of solution and the driving forces to hold the salt inside the matrix: wet impregnation and dry impregnation. A schematic of the impregnation methods procedure is shown in Figure 7 (Jarimi et al., 2019, Gordeeva et al., 2008) (1) drying the matrix to remove absorbed water; (2) impregnating the grains with salt solution; (3) filtration, and (4) drying the composite matrix to remove the adsorbed water (Zhao et al., 2015). In the dry impregnation method, capillary action draws the salt solution into the pores while in the wet impregnation method, the solution transport changes from a capillary action process to a diffusion process, which is much faster. Regarding the volume of the salt solution vs the pore volume, in wet impregnation, the volume of the salt solution exceeds the volume of the pores, which leads to an excess of solution that has to be removed either by filtration or vacuum desiccator. While in the dry impregnation the salt solution is equal or slightly lower than the pore volume.
(4) The sol–gel method consists of TCM impregnation into silica gel. Sol–gel offers an alternative to conventional impregnation methods for silica gel matrices that allows synthesizing composites with an aero-gel structure that possesses an extremely large pore volume and sorption capacity (Gordeeva and Aristov, 2012). The sol–gel impregnation consists of the preparation of a colloidal solution by mixing in an aqueous solution of the TCM, silica glass, and the precursors by magnetic stirring until the solution is converted into a gel-like shape (Yeromin et al., 2018).
The choice of the matrix can lead to different ways of preparing CSPMs, regarding the type of matrix used, the pore size, and microstructure, among others. A review of the state of the art is listed in Figure 8, the thermochemical material used, matrix, additive, and the preparation method used are thereof gathered as a schematic picture. Dry impregnation has been the method preferably chosen by researchers, given that the filtration step is omitted and the method is easier to follow (Gordeeva and Aristov, 2012). Nevertheless, when manufacturing large amounts of salt, the main defect is that special procedures and equipment are required to ensure a uniform distribution of the salt into the solution. Thus, even though at the laboratory scale, dry impregnation might stand as a feasible solution, many challenges must be faced before bringing it to the next level.
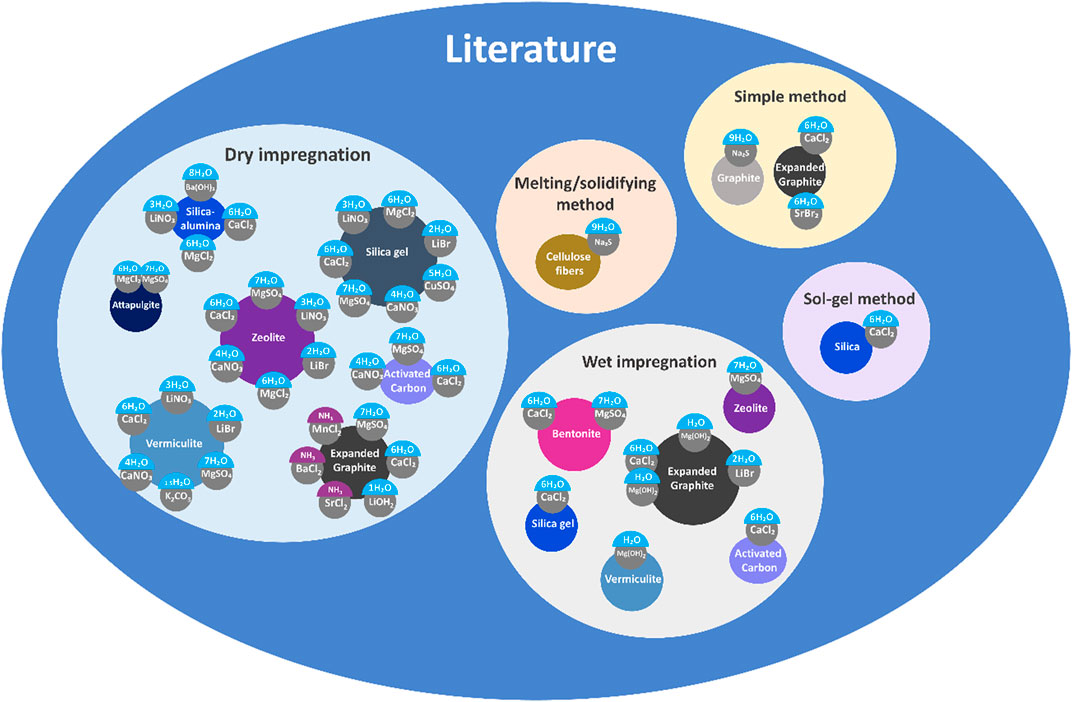
Figure 8. Summary of TCM/matrix pair studies found in the literature (Whiting et al., 2014;Whiting et al., 2013;Roelands et al., 2015;Shkatulov et al., 2020a;Hongois et al., 2011;Casey et al., 2014;Miao et al., 2021;Mauran et al., 2008;Myagmarjav et al., 2014;Gordeeva et al., 2002;Kim et al., 2013;Jiang et al., 2013;Aristov et al., 1996; Mrowiec-Białoń et al., 1997; Gordeeva et al., 1998b; Iammak et al., 2004; Zhu et al., 2006; Freni et al., 2007; Wu et al., 2007; Fujioka et al., 2008; Li et al., 2009a; Li et al., 2009b; Simonova et al., 2009; Posern and Kaps, 2010; Shkatulov et al., 2012; Tian et al., 2012; Tso and Chao, 2012; Tanashev et al., 2013; Druske et al., 2014; Duan et al., 2014; Ristić and Henninger, 2014; Zamengo et al., 2014; Jabbari-Hichri et al., 2015; Kerskes, 2016; Wang et al., 2016; Shere et al., 2018; Ousaleh et al., 2019; Li et al., 2021)
Carbon-based matrices are normally the ones used for solely matrix purposes, see Table 5. Among them, activated carbon has been used as a matrix, given it can increase the surface area, enhance the capillary force of the materials, and ensure it becomes a good carrier to conduct and hold water (Wang et al., 2016). Another alternative is expanded graphite (EG), which has been used as a binding material to enhance the heat transfer properties of the thermochemical reactants (Zamengo et al., 2014; Fopah Lele et al., 2015b;Cammarata et al., 2018). Similarly to activated carbon, EG is characterized by a high thermal conductivity, chemical stability, and large surface area and does not react with adsorbents reactants (Mauran et al., 1993), (Fujioka et al., 2008). In addition, EG has a worm-like particle shape that can host the TCM particles, which is required to remain unaltered after the binding method. Thus, some authors have experienced some issues when preparing the EG/TCM composites such as breakage or exfoliation (Zamengo et al., 2013). Non-carbon-based matrices are silica gel, zeolite, and vermiculite see Table 5. Mesoporous disordered silicas (silica gels) are widely studied as hydrophilic compounds due to their high affinity to water vapor (Ristić and Henninger, 2014). Silica gel composite shows a carryover problem at high humidity and temperatures, which depends on the ratio between the concentrations of salt/pores (Wang et al., 2016). Zeolite is a class of highly porous crystalline aluminosilicate materials that are most used in granular, cylindrical, or beaded forms. Zeolite provides a high specific surface area and accessible reaction sites to ensure good mass transfer, given the high absorbance capacity the salt can be absorbed into the pores (Shere et al., 2018). Vermiculite allows a single layer impregnation of the salt while absorbing large content of TCM than any other matrix used in the literature. As stated by Aydin et al. (2015), vermiculite stands as an excellent host matrix due to its low regeneration temperature (50–80 °C) and low cost.
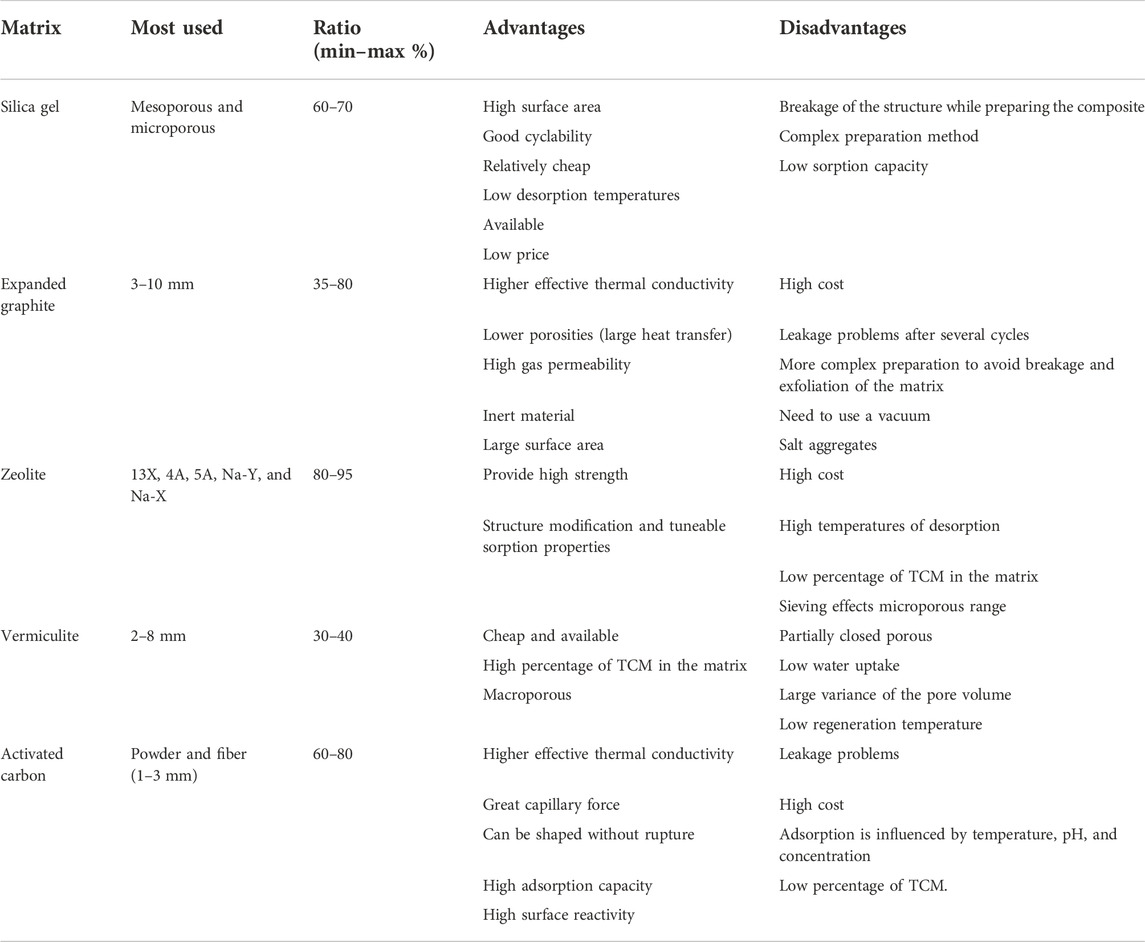
Table 5. Summary of binders used in TCM composites, adapted from the work of Navarro et al. (2021).
6.2 Emerging manufacturing routes
In the previous manufacturing routes, we considered the option of artificially increasing the size of particles (by pelletizing) or re-structuring the material to prevent further agglomeration problems (impregnation). However, due to volume changes these structures can break, which leads to smaller particle size and (again) tend to agglomerate. In this framework, novel and emerging manufacturing routes to TCM manufacturing have proliferated in the last 5 years. In this section, we divide them into nano-alternatives, encapsulation, and extrusion.
6.2.2 Nano-alternatives
Nanocomposites are a new class of chemical heat storage materials for moderate-temperature storage owing to their comparatively lower decomposition temperatures (Cot-Gores et al., 2012). Such nanocomposites are generally co-precipitated metallic hydroxides, following a similar manufacturing method as the one reported in the “insertion in a binder” section. Researchers have used the co-precipitated method of two metallic hydroxides (Ryu et al., 2007; Kato et al., 2009; Ishitobi et al., 2013; Zheng et al., 2015), the advantage of this method is that a homogeneous nanocomposite can be obtained by the chemical reaction in the solution directly (Zheng et al., 2015). By using such a method, the decomposition temperature can be substantially decreased (300 °C lower) while increasing cyclability and achieving an optimal storage capacity.
Another nano-alternative is the one used in bulk industries; several flow agents are known to improvethe powder flowability by increasing the surface roughness (nanocoating) or minimize the contact area between particles to improve flow behavior, nanoparticles addition (flowing agents), especially for better handling properties. When applying this method to thermochemical applications, the main challenge is that the additives must maintain their benefits after several hydration/dehydration cycles. Silicon dioxide (SiO2) nanoparticles (Pontiga et al., 2013) is a good candidate to be used as a doping agent, they either improve fluidization behavior or as a host matrix by using its agglomerates. Some researchers have already studied this strategy for thermochemical materials. Pontiga et al. (2013) (Roßkopf et al., 2014) used nanosilica to contain calcium hydroxide reaction, intending to improve fluidization, and the authors used the dry mixing technique to prepare the composite. Indeed, the use of nanosilica additive was useful to increase the flowability and enhance mass transfer. Interestingly, a commercialized nano-alternative is the nanocoating of the TCM with hydrophobic nanoparticles that improves material compatibility and provides a long-term service (Bolin and Glebov, 2016). The nanocoating (CaO, lithium bromide, lithium chloride, calcium chloride, calcium bromide, and sodium sulfate with silica nanoparticles) is prepared in a blender with the nanoparticles added to the salt solution and mixed at different intervals. The company (SaltX©) owns the patent and manufactures and delivers the product at a commercial scale. In another study, Roßkopf et al. (2015) used a dry mixing process to coat calcium hydroxide with silicon dioxide nanoparticle agglomerates. They found some difficulties in the manufacturing process: the mixing intensity strongly influences the conversion of the reaction; higher intensity leads to higher conversion.
6.2.3 Encapsulation
The newest and one of the most promising methods to shape TCMs is encapsulation, showing the most efficient way to reduce low temperature lift and the interaction between the TCMs sorption process and their matrices. Encapsulation not only works as a TCM enclosure but also compensates energy losses as the salt hydrate particles are enveloped with a second inherently stable material to prevent coalescence and agglomeration. However, there is a key point to consider when working with encapsulated TCMs, the shell needs to ensure water penetration into the capsule during the heat absorption and release during desorption and a permeable capsule after thermal cycles is required. Apart from the challenge of having a semipermeable capsule to allow the steam to diffuse inside the shell, the shell must enable mechanical stability over several cycles. The capsule should be able to bear forces resulting from the volume expansion of the core material during charging–discharging. The material must be inert and not react or interact with the reversible reaction in any way, which can be challenging under hydrothermal conditions and temperatures up to 550 °C. Some researchers have published interesting studies on this matter as reviewed in the following. The Büchi spray dryer technique was used by Cuypers et al. (2013) to encapsulate CaCl2·6H2O. The authors conclude that the encapsulated TCM can store energy at lower temperatures, and the material shows a large thermal response to dehydration upon temperature increase. Gaeini et al. (2018) studied CaCl2·6H2O microencapsulation and their results show high multicycles stability and fastest kinetics in comparison with impregnation of graphite and vermiculite composite, although energy density was lower. A ceramic capsule was used by Afflerbach et al. (2017) to encapsulate CaCl2·6H2O following a four-step encapsulation method. The ceramic encapsulation not only increased the mechanical stability of the capsules but also the heterogeneities in the ceramic shell. A MgSO4/polymer composite was synthesized by Kallenberger et al. (2016), which claimed some problems during the dehydration process with the monohydrate form. van Ravensteijn et al. (2021) performed a systematic evaluation of various commercially available polymers as stabilizing shell materials. The authors explored different preparation methods from polymer solutions, preparation of freestanding polymer films, cross-linked films, and coating of zeolite and potassium carbonate with polymer by fluidized bed coating. The authors identified ethylhydroxypropyl cellulose as a promising candidate combining ductility with sufficient water vapor permeabilities. The authors also concluded that the coating thickness has a distinct influence on permeability. Regarding the granular material study, coating of zeolite and potassium carbonate showed that the polymer layer remained intact and significantly improved the mechanical resilience, although the price must be assessed in this case. Shkatulov et al. (2020b) investigated the composites of three salt hydrates (CaCl2, SrBr2, and LiCl) encapsulated in mesoporous silica shells. The authors considered the silica shell capsules as promising for hot tap water and space heating, with emphasis on the LiCl encapsulation that confirmed significant stability after 50 hydration/dehydration cycles.
In summary, the encapsulation technique has a high potential to manufacture TCMs but involves additional steps that increase complexity and manufacturing costs. Also, the materials needed to encapsulate the TCM are expensive and not highly available, which will hinder the production of large quantities of encapsulated storage media.
6.3 Extrusion
Extrusion is one of the most common methods to manufacture polymers on a large scale and it has recently started to be used to shape TCMs through zeolites honeycombs. The extrusion of materials needs the addition of additives or binders to thermal process them. Many types of binders are available in the market depending on their origin (natural or synthetic), their nature (organic or inorganic), colloidal particle type or molecular type, and water-soluble or non-polar liquid soluble. The most common binders are the following (Bingre et al., 2018): kaolin, attapulgite, boehmite, aluminas, and/or silica or a combination of them. The paste extrusion technique was used by Li et al. (2001) to extrude 5A zeolite monolith using different bentonite percentages as a binder to improve the internal particle friction. The suggested amount recommended was 10–35% wt., less than the recommended amount will cause extrusion failure due to particle friction, and more than the recommended amount will cause difficulties in handling. To the best of the author’s knowledge, the scalability of this method has not been proven. As extrusion is widely used in other conventional manufacturing industries, adapting the manufacturing process with these materials should not be highly difficult due to the know-how and expertise in this process.
6.4 Summary of manufacturing techniques
Since thermochemical materials are still under material development, researchers have invested most of their efforts in searching for a proper way of stabilizing the salt particles to enable an efficient sorption process. This has limited the manufacturing routes studied in the field to a laboratory scale level, following a bottom-up approach. It is noted that most of the manufacturing routes that present better scalability (extrusion and shaping) are the ones that have been studied the least, whereas others such as impregnation and encapsulation are proven to increase the stability of the material but decrease in storage capacity and non-industrialized complex routes. To wrap up the manufacturing sections, we have elaborated a summary table that includes all the relevant parameters for the manufacturing routes included in the previous sections, see Table 6.
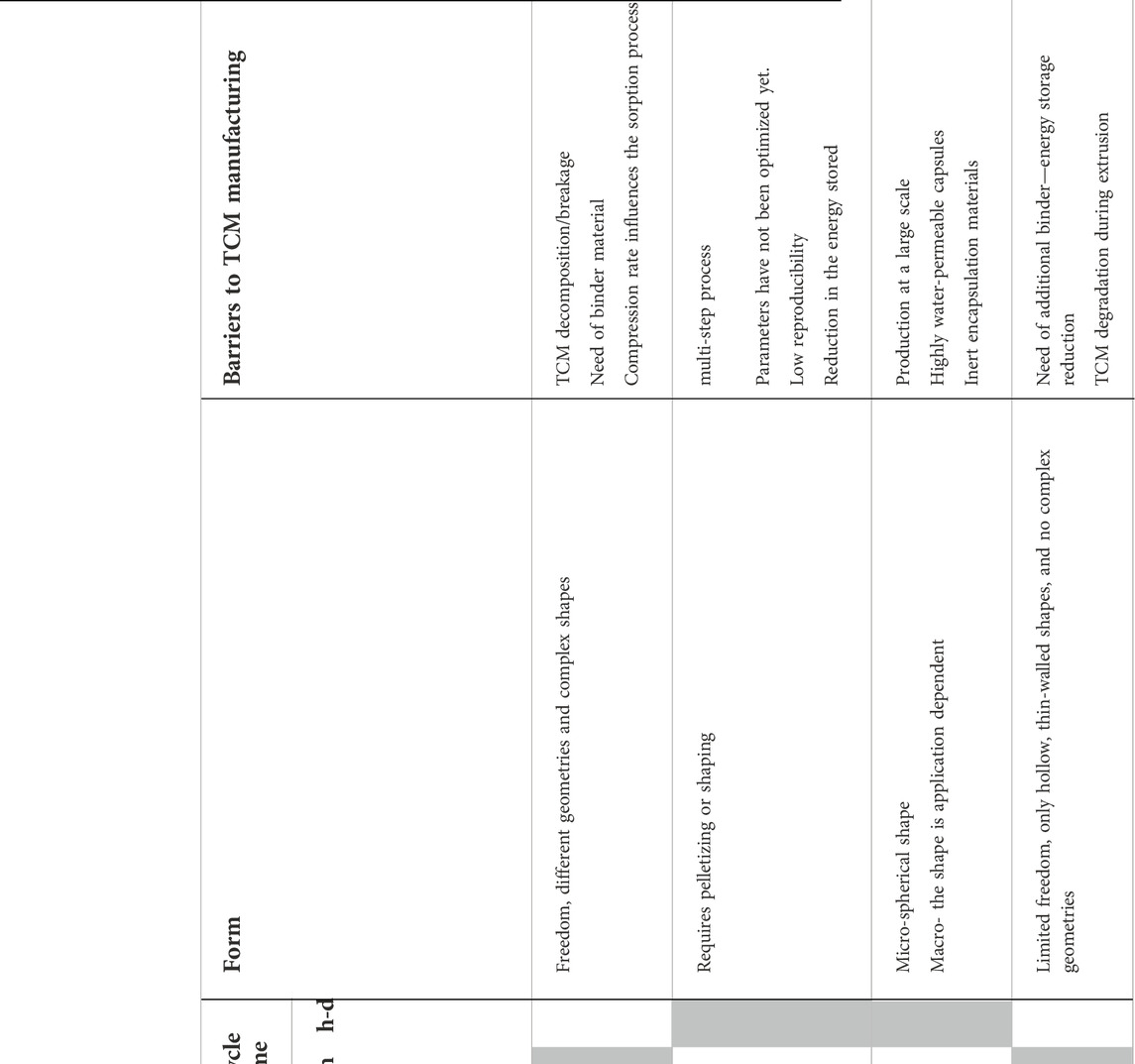
Table 6. Comparison of manufacturing routes’ inherent parameters and barriers for TCM manufacturing.
7. Outlook and concluding remarks
A comprehensive thermochemical technology material perspectives overview from conceptualization to manufacturing level has been described in this article. The authors have tackled the different hot areas of interest in the field; (1) key attributes to consider; (2) characterization techniques and boundary conditions; (3) state of the art and property collection of relevant TCM candidates; and (4) emerging and conventional manufacturing routes. The main outputs and concluding remarks from the aforementioned points are listed as follows:
(1) Sorption water-based storage provides a compact storage solution in a strategic temperature range; in the residential and commercial sectors for hot water and district heating and in the industrial sector for process heating decarbonization (100–200°C). Sorption-based thermochemical storage accounts for the most research thermochemical storage technology; however, the innovation is blocked at TRL 3–4 given the magnitude of the challenges to face (material stability and large scale manufacturing).
(2) TCS research has been particularly focused on a few numbers of candidates, while from the literature many potential candidates can be found to be feasible for low to medium temperature applications. Extended literature is available for the most commonly used TCMs; however, there are a group of materials that have not yet been addressed. A thorough understanding of the working mechanism of such materials is needed to enrich the knowledge at the working pair’s material level.
(3) TCS materials are still at a low development level, and while problems at the material level are still to be faced, novel manufacturing routes must be found to deploy the technology and bring it to commercialization. The development at the manufacturing level is highly linked to the progress in material formulation and characterization, as the components dictate the synthesis method, conditions, and final performance. Hence, researchers should focus more on emerging techniques as the conventional manufacturing routes (e.g., impregnation) have shown to be feasible just at low material production batches. When increasing the material amount needed, the complexity and multiple-step processes hinder their scalability.
Author contributions
AP: investigation, conceptualization, writing—original draft, and visualization. MN: conceptualization, investigation, and writing—original draft. CB: writing—review and editing and conceptualization. YD: funding acquisition and project administration.
Funding
Funding was received from the University of Birmingham library as gold open access with a Creative Commons Attribution licence (CC-BY) to be compliant with the funder.
Acknowledgments
The authors would like to acknowledge the ABC programme—UK EPSRC under EP/V012053/1 (the Active Building Centre Research Programme).
Conflict of interest
The authors declare that the research was conducted in the absence of any commercial or financial relationships that could be construed as a potential conflict of interest.
Publisher’s note
All claims expressed in this article are solely those of the authors and do not necessarily represent those of their affiliated organizations, or those of the publisher, the editors, and the reviewers. Any product that may be evaluated in this article, or claim that may be made by its manufacturer, is not guaranteed or endorsed by the publisher.
References
Abedin, A. H., and Rosen, M. A. (2011). A critical review of thermochemical energy storage systems. Open Renew. Energy J. 4 (1), 42–46. doi:10.2174/1876387101004010042
Afflerbach, S., Kappes, M., Gipperich, A., Trettin, R., and Krumm, W. (2017). Semipermeable encapsulation of calcium hydroxide for thermochemical heat storage solutions. Sol. Energy 148, 1–11. doi:10.1016/j.solener.2017.03.074
Al-Abbasi, O., Abdelkefi, A., and Ghommem, M. (2017). Modeling and assessment of a thermochemical energy storage using salt hydrates. Int. J. Energy Res. 41 (14), 2149–2161. doi:10.1002/er.3776
Ali, E. S., Askalany, A. A., Harby, K., Diab, M. R., and Alsaman, A. S. (2018). Adsorption desalination-cooling system employing copper sulfate driven by low grade heat sources. Appl. Therm. Eng. 136, 169–176. doi:10.1016/j.applthermaleng.2018.03.014
Alkhalidi, A., Al Khatba, H., and Khawaja, M. K. (2021). Utilization of buildings’ foundations for a seasonal thermal energy storage medium to meet space and water heat demands. Int. J. Photoenergy 2021, 2021. doi:10.1155/2021/6668079
Aristov, Y., Tokarev, M., Cacciola, G., and Restuccia, G. (1996). Selective water sorbents for multiple applications, 1. CaCl2 confined in mesopores of silica gel: Sorption properties. React. Kinet. Catal. Lett. 59 (2), 325–333. doi:10.1007/bf02068130
Aydin, D., Casey, S. P., and Riffat, S. (2015). The latest advancements on thermochemical heat storage systems. Renew. Sustain. Energy Rev. 41, 356–367. doi:10.1016/j.rser.2014.08.054
Badens, E., Llewellyn, P., Fulconis, J., Jourdan, C., Veesler, S., Boistelle, R., et al. (1998). Study of gypsum dehydration by controlled transformation rate thermal analysis (CRTA). J. Solid State Chem. 139 (1), 37–44. doi:10.1006/jssc.1998.7797
Bassett, H., and Goodwin, T. H. (1949). 480. The basic aluminium sulphates. J. Chem. Soc. 1949, 2239–2276. doi:10.1039/jr9490002239
Berroug, F., Lakhal, E. K., El Omari, M., Faraji, M., and El Qarnia, H. (2011). Thermal performance of a greenhouse with a phase change material north wall. Energy Build. 43 (11), 3027–3035. doi:10.1016/j.enbuild.2011.07.020
Bhosale, R., Dardor, D., Kumar, A., Al Momani, F., and Ghosh, U. (2016). Thermochemical copper Oxide - copper sulfate water splitting cycle for solar hydrogen production. Adv. Mat. 2, 2–6.
Bingre, R., Louis, B., and Nguyen, P. (2018). An overview on zeolite shaping technology and solutions to overcome diffusion limitations. Catalysts 8 (4), 163. doi:10.3390/catal8040163
Borchardt, H. J., and Daniels, F. (1957). Differential thermal analysis of inorganic hydrates. J. Phys. Chem. 61 (7), 917–921. doi:10.1021/j150553a016
Bouché, M., Richter, M., and Linder, M. (2016). Heat transformation based on CaCl2/H2O - Part B: Open operation principle. Appl. Therm. Eng. 102, 641–647. doi:10.1016/j.applthermaleng.2016.03.102
Cabeza, L. F., Solé, A., and Barreneche, C. (2017). Review on sorption materials and technologies for heat pumps and thermal energy storage. Renew. Energy 110, 3–39. doi:10.1016/j.renene.2016.09.059
Calabrese, L., Brancato, V., Palomba, V., Frazzica, A., and Cabeza, L. F. (2018). Assessment of the hydration/dehydration behaviour of MgSO4∙7H2O filled cellular foams for sorption storage applications through morphological and thermo-gravimetric analyses. Sustain. Mater. Technol. 17, e00073. doi:10.1016/j.susmat.2018.e00073
Calabrese, L., Brancato, V., Palomba, V., Frazzica, A., and Cabeza, L. F. (2019). Magnesium sulphate-silicone foam composites for thermochemical energy storage: Assessment of dehydration behaviour and mechanical stability. Sol. Energy Mat. Sol. Cells 200, 109992. doi:10.1016/j.solmat.2019.109992
Cammarata, A., Verda, V., Sciacovelli, A., and Ding, Y. (2018). Hybrid strontium bromide-natural graphite composites for low to medium temperature thermochemical energy storage: Formulation, fabrication and performance investigation. Energy Convers. Manag. 166, 233–240. doi:10.1016/j.enconman.2018.04.031
Canbazoǧlu, S., Şahinaslan, A., Ekmekyapar, A., Aksoy, Y. G., and Akarsu, F. (2005). Enhancement of solar thermal energy storage performance using sodium thiosulfate pentahydrate of a conventional solar water-heating system. Energy Build. 37 (3), 235–242. doi:10.1016/j.enbuild.2004.06.016
Casey, S. P., Aydin, D., Elvins, J., and Riffat, S. (2017). Salt impregnated desiccant matrices for ‘open’ thermochemical energy conversion and storage – improving energy density utilisation through hygrodynamic & thermodynamic reactor design. Energy Convers. Manag. 142, 426–440. doi:10.1016/j.enconman.2017.03.066
Casey, S. P., Elvins, J., Riffat, S., and Robinson, A. (2014). Salt impregnated desiccant matrices for ‘open’ thermochemical energy storage - selection, synthesis and characterisation of candidate materials. Energy Build. 84, 412–425. doi:10.1016/j.enbuild.2014.08.028
Chacartegui, R., Valverde, J. M., Barrios-Padura, A., Lizana, J., and Ortiz, C. (2018). Identification of best available thermal energy storage compounds for low-to-moderate temperature storage applications in buildings. Mater. Construcción 68, 331. doi:10.3989/mc.2018.10517
Chaudhari, S. K., V Paranjape, D., Eisa, M. A. R., Holland, F. A., and Engineering, G. (1986). A comparative study of the operating characteristics of water-lithium chloride and water-calcium chloride absorption heat pumps. J. Heat Recovery Syst. 6 (1), 39–46. doi:10.1016/0198-7593(86)90170-0
Chen, J., Ma, P., Chen, G., and Chen, F. (2001). The measurement of hydration heats for magnesium chloride with low water by means of DSC. J. Therm. Anal. Calorim. 65 (3), 777–786. doi:10.1023/A:1011963712794
Çılgı, G. K., and Cetişli, H. (2009). Thermal decomposition kinetics of aluminum sulfate hydrate. J. Therm. Anal. Calorim. 98 (3), 855–861. doi:10.1007/s10973-009-0389-5
Clark, R. J., Mehrabadi, A., and Farid, M. (2020). State of the art on salt hydrate thermochemical energy storage systems for use in building applications. J. Energy Storage 27, 101145. doi:10.1016/j.est.2019.101145
Cot-Gores, J., Castell, A., and Cabeza, L. F. (2012). Thermochemical energy storage and conversion: A-state-of-the-art review of the experimental research under practical conditions. Renew. Sustain. Energy Rev. 16 (7), 5207–5224. doi:10.1016/j.rser.2012.04.007
Courbon, E., D'Ans, P., Permyakova, A., Skrylnyk, O., Steunou, N., Degrez, M., et al. (2017). A new composite sorbent based on SrBr2and silica gel for solar energy storage application with high energy storage density and stability. Appl. Energy 190, 1184–1194. doi:10.1016/j.apenergy.2017.01.041
Courbon, E., D'Ans, P., Permyakova, A., Skrylnyk, O., Steunou, N., Degrez, M., et al. (2017). Further improvement of the synthesis of silica gel and CaCl2 composites: Enhancement of energy storage density and stability over cycles for solar heat storage coupled with space heating applications. Sol. Energy 157, 532–541. doi:10.1016/j.solener.2017.08.034
Cuypers, R., de Jong, A. J., Eversdijk, J., van 't Spijker, J. C., Oversloot, H. P., Ingenhut, B. L. J., et al. (2013). “Microencapsulation of salts for enhanced thermochemical storage materials.” in 40th Annual Meeting and Exposition of the Controlled Release Society, 21-24 July 2013, Honolulu, Hawaii, USA. 2–3.
D’Ans, P., Skrylnyk, O., Hohenauer, W., Courbon, E., Malet, L., Degrez, M., et al. (2018). Humidity dependence of transport properties of composite materials used for thermochemical heat storage and thermal transformer appliances. J. Energy Storage 18, 160–170. doi:10.1016/j.est.2018.04.027
De Boer, R., Haije, W. G., and Veldhuis, J. B. J. (2002). Determination of structural, thermodynamic and phase properties in the Na2S-H2O system for application in a chemical heat pump. Thermochim. Acta 395, 3–19. doi:10.1016/S0040-6031(02)00158-2
de Boer, R., Smeding, S., Zondag, H., and Krol, G. (2014). Development of a prototype system for seasonal solar heat storage using an open sorption process. Eurotherm Semin. 2014, 1–9. [Online]. Available at: https://www.ecn.nl/publications/PdfFetch.aspx?nr=ECN-M--14-009.
De Jong, A. J., Trausel, F., Finck, C., Van Vliet, L., and Cuypers, R. (2014). Thermochemical heat storage - system design issues. Energy Procedia 48, 309–319. doi:10.1016/j.egypro.2014.02.036
Delta Energy & Environment Ltd (2016). Evidence gathering: Thermal energy storage (TES) technologies. Edinburgh: Delta Energy & Environment Ltd.
Descy, G., Frère, M., Bougard, J., Heymans, N., Skrylnyk, O., and Courbon, E. (2018). Performance characterization of salt-in-silica composite materials for seasonal energy storage design. J. Energy Storage 19, 320–336. doi:10.1016/j.est.2018.08.015
Ding, Q., Luo, X., Lin, X., and Zhang, H. (2012). Study of magnesium nitrate hexahydrate and magnesium chloride hexahydrate mixture as phase change material. Asia-Pacific Power Energy Eng. Conf. APPEEC 2012, 2–5. doi:10.1109/APPEEC.2012.6306921
Donkers, P. A. J., Beckert, S., Pel, L., Stallmach, F., Steiger, M., and Adan, O. C. G. (2015). Water transport in MgSO4·7H2O during dehydration in view of thermal storage. J. Phys. Chem. C 119 (52), 28711–28720. doi:10.1021/acs.jpcc.5b08730
Donkers, P. A. J., Pel, L., and Adan, O. C. G. (2016). Experimental studies for the cyclability of salt hydrates for thermochemical heat storage. J. Energy Storage 5, 25–32. doi:10.1016/j.est.2015.11.005
Donkers, P. A. J., Sögütoglu, L. C., Huinink, H. P., Fischer, H. R., and Adan, O. C. G. (2017). A review of salt hydrates for seasonal heat storage in domestic applications. Appl. Energy 199, 45–68. doi:10.1016/j.apenergy.2017.04.080
Drake, G., Freiberg, L., and AuYeung, N. (2018). Reactive phase-change materials for enhanced thermal energy storage. Energy Technol. 6 (2), 351–356. doi:10.1002/ente.201700495
Druske, M.-M., Fopah-Lele, A., Korhammer, K., Rammelberg, H. U., Wegscheider, N., Ruck, W., et al. (2014). Developed materials for thermal energy storage: Synthesis and characterization. Energy Procedia 61, 96–99. doi:10.1016/j.egypro.2014.11.915
Duan, Z., Zhang, H. z., Sun, L. x., Cao, Z., Xu, F., Zou, Y. j., et al. (2014). CaCl2·6H2O/Expanded graphite composite as form-stable phase change materials for thermal energy storage. J. Therm. Anal. Calorim. 115 (1), 111–117. doi:10.1007/s10973-013-3311-0
Fenstad, J., and Fray, D. J. (2006). The binary diagram water + barium chloride. C. R. Chim. 9 (10), 1235–1242. doi:10.1016/j.crci.2006.02.004
Ferchaud, C. J., Scherpenborg, R. A. A., Zondag, H. A., and De Boer, R. (2014). Thermochemical seasonal solar heat storage in salt hydrates for residential applications - influence of the water vapor pressure on the desorption kinetics of MgSO4·7H2O. Energy Procedia 57, 2436–2440. doi:10.1016/j.egypro.2014.10.252
Ferchaud, C. J., Zondag, H. A., Rubino, A., and de Boer, R. (2012). Seasonal sorption heat storage – research on thermochemical materials and storage performance. Proc. Heat. Power Cycle 2012, 1–7. [Online]. Available at: https://pure.tue.nl/ws/files/3821108/572851890456641.pdf.
Ferchaud, C. J., Zondag, H. A., Veldhuis, J. B. J., and De Boer, R. (2012). Study of the reversible water vapour sorption process of MgSO4.7H2O and MgCl2.6H2O under the conditions of seasonal solar heat storage. J. Phys. Conf. Ser. 395 (1), 012069. doi:10.1088/1742-6596/395/1/012069
Fopah Lele, A., Kuznik, F., Opel, O., and Ruck, W. K. L. (2015). Performance analysis of a thermochemical based heat storage as an addition to cogeneration systems. Energy Convers. Manag. 106, 1327. doi:10.1016/j.enconman.2015.10.068
Fopah Lele, A., N’Tsoukpoe, K. E., Osterland, T., Kuznik, F., and Ruck, W. K. L. (2015). Thermal conductivity measurement of thermochemical storage materials. Appl. Therm. Eng. 89, 916–926. doi:10.1016/j.applthermaleng.2015.06.077
Fopah-lele, A., and Gaston, J. (2017). Solar Energy Materials & Solar Cells A review on the use of SrBr 2 · 6H 2 O as a potential material for low temperature energy storage systems and building applications. Sol. Energy Mat. Sol. Cells 164, 175–187. doi:10.1016/j.solmat.2017.02.018
Fopah-Lele, A., and Tamba, J. G. (2017). A review on the use of SrBr2·6H2O as a potential material for low temperature energy storage systems and building applications. Sol. Energy Mat. Sol. Cells 164, 175–187. doi:10.1016/j.solmat.2017.02.018
Freni, A., Gordeeva, L. G., Vasta, S., and Restuccia, G. (2007). Composite sorbent of methanol ‘ lithium chloride in mesoporous silica gel ’ for adsorptive cooling machines : Performance evaluation. Combustion 5, 28–32.
Freyer, D., and Voigt, W. (2003). Crystallization and phase stability of CaSO4 and CaSO 4 - based salts. Monatsh. F-r. Chem./Chem. Mon. 134 (5), 693–719. doi:10.1007/s00706-003-0590-3
Fujii, I., Ishino, M., Akiyama, S., Murthy, M. S., and Rajanandam, K. S. (1994). Behavior of Ca(OH)2/CaO pellet under dehydration and hydration. Sol. Energy 53 (4), 329–341. doi:10.1016/0038-092X(94)90036-1
Fujioka, K., Hatanaka, K., and Hirata, Y. (2008). Composite reactants of calcium chloride combined with functional carbon materials for chemical heat pumps. Appl. Therm. Eng. 28 (4), 304–310. doi:10.1016/j.applthermaleng.2006.02.032
Fumey, B., Weber, R., Gantenbein, P., Daguenet-Frick, X., Williamson, T., and Dorer, V. (2014). Closed sorption heat storage based on aqueous sodium hydroxide. Energy Procedia 48, 337–346. doi:10.1016/j.egypro.2014.02.039
Gaeini, M., Rouws, A. L., Salari, J. W. O., Zondag, H. A., and Rindt, C. C. M. (2018). Characterization of microencapsulated and impregnated porous host materials based on calcium chloride for thermochemical energy storage. Appl. Energy 212, 1165–1177. doi:10.1016/j.apenergy.2017.12.131
Gaeini, M., Shaik, S. A., and Rindt, C. C. M. (2019). Characterization of potassium carbonate salt hydrate for thermochemical energy storage in buildings. Energy Build. 196, 178. doi:10.1016/j.enbuild.2019.05.029
Gilles, D., Segato, T., Courbon, E., Degrez, M., and D’Ans, P. (2018). Affordable process for the production of strontium bromide used in low grade heat recovery applications. Procedia CIRP 69, 383–388. doi:10.1016/j.procir.2017.11.056
Glasser, L. (2014). Thermodynamics of inorganic hydration and of humidity control, with an extensive database of salt hydrate pairs. J. Chem. Eng. Data 59 (2), 526–530. doi:10.1021/je401077x
Gonzales, R. B., Law, V. J., and Prindle, J. C. (2009). Analysis of the hybrid copper oxide-copper sulfate cycle for the thermochemical splitting of water for hydrogen production. Int. J. Hydrogen Energy 34 (9), 4179–4188. doi:10.1016/j.ijhydene.2008.12.026
Gordeeva, L. G., and Aristov, Y. I. (2012). Composites ‘salt inside porous matrix’ for adsorption heat transformation: A current state-of-the-art and new trends. Int. J. Low-Carbon Tech. 7 (4), 288–302. doi:10.1093/ijlct/cts050
Gordeeva, L. G., Freni, A., Krieger, T. A., Restuccia, G., and Aristov, Y. I. (2008). Composites ‘lithium halides in silica gel pores’: Methanol sorption equilibrium. Microporous Mesoporous Mat. 112 (1–3), 254–261. doi:10.1016/j.micromeso.2007.09.040
Gordeeva, L. G., Restuccia, G., Cacciola, G., and Aristov, Y. I. (1998). Selective water sorbents for multiple applications, 5. LiBr confined in mesopores of silica gel: Sorption properties. React. Kinet. Catal. Lett. 63 (1), 81–88. doi:10.1007/BF02475434
Gordeeva, L. G., Restuccia, G., Freni, A., and Aristov, Y. I. (2002). Water sorption on composites ‘LiBr in a porous carbon. Fuel Process. Technol. 79 (3), 225–231. doi:10.1016/S0378-3820(02)00186-8
Gordeeva, L. G., Tokarev, M. M., Parmon, V. N., and Aristov, Y. I. (1998). Selective water sorbents for multiple application, 6. Freshwater production from the atmosphere. React. Kinet. Catal. Lett. 65 (1), 153–159. doi:10.1007/BF02475329
Gough, R. V., Chevrier, V. F., and Tolbert, M. A. (2016). Formation of liquid water at low temperatures via the deliquescence of calcium chloride: Implications for Antarctica and Mars. Planet. Space Sci. 131, 79–87. doi:10.1016/j.pss.2016.07.006
Guillaume, R. (2007). Modélisation de transfert de vapeur d ’ eau à faible pression à travers un milieu poreux réactif, 4–10.
Guion, J., Sauzade, J. D., and Laügt, M. (1983). Critical examination and experimental determination of melting enthalpies and entropies of salt hydrates. Thermochim. Acta 67 (2–3), 167–179. doi:10.1016/0040-6031(83)80096-3
Guo, L., Yu, X., Gao, D., Guo, Y., Ma, C., and Deng, T. (2019). Synthesis and thermal energy storage properties of a calcium-based room temperature phase change material for energy storage. J. Therm. Anal. Calorim. 135 (6), 3215–3221. doi:10.1007/s10973-018-7610-3
Gutierrez, A., Ushak, S., and Linder, M. (2018). High carnallite-bearing material for thermochemical energy storage: Thermophysical characterization. ACS Sustain. Chem. Eng. 6 (5), 6135–6145. doi:10.1021/acssuschemeng.7b04803
Hawwash, A. A., Hassan, H., Ahmed, M., Ookawara, S., and El Feky, K. (2017). Long-term thermal energy storage using thermochemical materials. Energy Procedia 141, 310–314. doi:10.1016/j.egypro.2017.11.111
Hongois, S., Kuznik, F., Stevens, P., and Roux, J. J. (2014). Developement and characterisation of a new MgSO4-zeolite composite for long-term thermal energy storage to cite this version : HAL id : hal-00683965.
Hongois, S., Kuznik, F., Stevens, P., and Roux, J. J. (2011). Development and characterisation of a new MgSO4-zeolite composite for long-term thermal energy storage. Sol. Energy Mat. Sol. Cells 95 (7), 1831–1837. doi:10.1016/j.solmat.2011.01.050
Huang, Q. Z., Lu, G. M., Wang, J., and Yu, J. G. (2010). Mechanism and kinetics of thermal decomposition of MgCl 2 × 6H 2O. Metall. Materi. Trans. B 41 (5), 1059–1066. doi:10.1007/s11663-010-9390-4
Hudson-Lamb, D. L., Strydom, C. A., and Potgieter, J. H. (1996). The thermal dehydration of natural gypsum and pure calcium sulphate dihydrate (gypsum). Thermochim. Acta 282–283, 483–492. doi:10.1016/0040-6031(95)02819-6
Hui, L., Edem, N. K., Nolwenn, L. P., and Luo, L. (2011). Evaluation of a seasonal storage system of solar energy for house heating using different absorption couples. Energy Convers. Manag. 52 (6), 2427–2436. doi:10.1016/j.enconman.2010.12.049
Iammak, K., Wongsuwan, W., and Kiatsiriroj, T. (2004)., 022. December, 504–507.Investigation of modular chemical energy storage performanceProc. Jt. Int. Conf. ‘‘sustainable energy Environ.
Ishitobi, H., Uruma, K., Takeuchi, M., Ryu, J., and Kato, Y. (2013). Dehydration and hydration behavior of metal-salt-modified materials for chemical heat pumps. Appl. Therm. Eng. 50 (2), 1639–1644. doi:10.1016/j.applthermaleng.2011.07.020
Iyimen-Schwarz, Z., and Lechner, M. D. (1983). Energiespeicherung durch chemische reaktionen. I. DSC-messungen zur quantitativen verfolgung der enthalpieänderungen von speicherstoffen für die hin- und rückreaktion. Thermochim. Acta 68 (2–3), 349–361. doi:10.1016/0040-6031(83)80237-8
Jabbari-Hichri, A., Bennici, S., and Auroux, A. (2017). CaCl2-containing composites as thermochemical heat storage materials. Sol. Energy Mat. Sol. Cells 172, 177–185. doi:10.1016/j.solmat.2017.07.037
Jabbari-Hichri, A., Bennici, S., and Auroux, A. (2016). Effect of aluminum sulfate addition on the thermal storage performance of mesoporous SBA-15 and MCM-41 materials. Sol. Energy Mat. Sol. Cells 149, 232–241. doi:10.1016/j.solmat.2016.01.033
Jabbari-Hichri, A., Bennici, S., and Auroux, A. (2015). Enhancing the heat storage density of silica–alumina by addition of hygroscopic salts (CaCl2, Ba(OH)2, and LiNO3). Sol. Energy Mat. Sol. Cells 140, 351–360. doi:10.1016/j.solmat.2015.04.032
Jarimi, H., Aydin, D., Yanan, Z., Ozankaya, G., Chen, X., and Riffat, S. (2019). Review on the recent progress of thermochemical materials and processes for solar thermal energy storage and industrial waste heat recovery. Int. J. Low-Carbon Technol. 14 (1), 44–69. doi:10.1093/ijlct/cty052
Jenkins, H. D. B., and Glasser, L. (2018). Ionic hydrates, MpXq·nH2O: Lattice energy and standard enthalpy of formation estimation. Inorg. Chem. 53, 240–255. doi:10.4067/s0717-97072008000200018
Jiang, L., Gao, J., Wang, L., Wang, R., Lu, Y., and Roskilly, A. P. (2017). Investigation on performance of multi-salt composite sorbents for multilevel sorption thermal energy storage. Appl. Energy 190, 1029–1038. doi:10.1016/j.apenergy.2017.01.019
Jiang, L., Wang, L. W., Jin, Z. Q., Wang, R. Z., and Dai, Y. J. (2013). Effective thermal conductivity and permeability of compact compound ammoniated salts in the adsorption/desorption process. Int. J. Therm. Sci. 71, 103–110. doi:10.1016/j.ijthermalsci.2013.03.017
Johnson, D. W., and Gallagher, P. K. (1971). Kinetics of the decomposition of freeze-dried aluminum sulfate and ammonium aluminum sulfate. J. Am. Ceram. Soc. 54 (9), 461–465. doi:10.1111/j.1151-2916.1971.tb12386.x
Kallenberger, P. A., Brieler, F. J., Posern, K., and Fröba, M. (2016). Magnesium sulfate/polymer composites for seasonal, thermochemical energy storage. Chem. Ing. Tech. 88 (3), 379–384. doi:10.1002/cite.201500095
Karunadasa, K. S. P., Manoratne, C. H., Pitawala, H. M. T. G. A., and Rajapakse, R. M. G. (2018). Relative stability of hydrated/anhydrous products of calcium chloride during complete dehydration as examined by high-temperature X-ray powder diffraction. J. Phys. Chem. Solids 120, 167–172. doi:10.1016/j.jpcs.2018.04.034
Kato, Y., Takahashi, R., Sekiguchi, T., and Ryu, J. (2009). Study on medium-temperature chemical heat storage using mixed hydroxides. Int. J. Refrig. 32 (4), 661–666. doi:10.1016/j.ijrefrig.2009.01.032
Kenisarin, M., and Mahkamov, K. (2016). Salt hydrates as latent heat storage materials:Thermophysical properties and costs. Sol. Energy Mat. Sol. Cells 145, 255–286. doi:10.1016/j.solmat.2015.10.029
Kerskes, H. (2016). Experimental and numerical investigations on thermo chemical heat storage. Eng. Environ. Sci. 2016, 1–10. doi:10.18086/eurosun.2010.16.14
Kim, S. T., Ryu, J., and Kato, Y. (2013). Optimization of magnesium hydroxide composite material mixed with expanded graphite and calcium chloride for chemical heat pumps. Appl. Therm. Eng. 50 (1), 485–490. doi:10.1016/j.applthermaleng.2012.07.005
Kim, S. T., Zamengo, M., Ryu, J., and Kato, Y. (2014). Kinetic characterization of expanded graphite, calcium chloride, and magnesium hydroxide composite for the chemical heat pump. Heat. Transf. Res. 46 (2), 91–107. doi:10.1615/heattransres.2014006874
Kirsh, Y., Yariv, S., and Shoval, S. (1987). Kinetic analysis of thermal dehydration and hydrolysis of MgCl2·6H2O by DTA and TG. J. Therm. Analysis 32 (2), 393–408. doi:10.1007/BF01912692
Klein, H. P., and Groll, M. (2004). Heat transfer characteristics of expanded graphite matrices in metal hydride beds. Int. J. Hydrogen Energy 29 (14), 1503–1511. doi:10.1016/j.ijhydene.2004.01.017
Kőmives, J., Tomor, K., Sztatisz, J., Lassu, L., and Gál, S. (1984). Thermoanalytical studies on the preparation of industrial crystalline aluminium sulphate. J. Therm. Analysis 29 (5), 1083–1093. doi:10.1007/BF02188861
Korhammer, K., Apel, C., Osterland, T., and Ruck, W. K. L. (2016). Reaction of calcium chloride and magnesium chloride and their mixed salts with ethanol for thermal energy storage. Energy Procedia 91, 161–171. doi:10.1016/j.egypro.2016.06.194
Korhammer, K., Druske, M. M., Fopah-Lele, A., Rammelberg, H. U., Wegscheider, N., Opel, O., et al. (2016). Sorption and thermal characterization of composite materials based on chlorides for thermal energy storage. Appl. Energy 162, 1462–1472. doi:10.1016/j.apenergy.2015.08.037
Kozak, A. J., Wieczorek-ciurowa, K., and Kozak, A. (2003). The thermal transformations in Zn(NO3)2 – H2O(1:6) system. J. Therm. Analysis Calorim. 74 (3), 497–502. doi:10.1023/B:JTAN.0000005186.15474.be
Krese, G., Koželj, R., Butala, V., and Stritih, U. (2018). Thermochemical seasonal solar energy storage for heating and cooling of buildings. Energy Build. 164, 239–253. doi:10.1016/j.enbuild.2017.12.057
Kruk, M., Jaroniec, M., and Sayari, A. (1997). Adsorption study of surface and structural properties of MCM-41 materials of different pore sizes. J. Phys. Chem. B 101 (4), 583–589. doi:10.1021/jp962000k
Kumar, N., Banerjee, D., and Chavez, R. (2018). Exploring additives for improving the reliability of zinc nitrate hexahydrate as a phase change material (PCM). J. Energy Storage 20, 153–162. doi:10.1016/j.est.2018.09.005
Lahmidi, H., Mauran, S., and Goetz, V. (2006). Definition, test and simulation of a thermochemical storage process adapted to solar thermal systems. Sol. Energy 80 (7), 883–893. doi:10.1016/j.solener.2005.01.014
Lee, J. H., Ogura, H., and Sato, S. (2014). Reaction control of CaSO4 during hydration/dehydration repetition for chemical heat pump system. Appl. Therm. Eng. 63 (1), 192–199. doi:10.1016/j.applthermaleng.2013.10.043
Lefebvre, E., Bennici, S., Gagnière, E., Mangin, D., and Auroux, A. (2013). Hydration characteristics of lithium, zinc, potassium and sodium salts. MATEC Web Conf. 3, 01003–01005. doi:10.1051/matecconf/20130301003
Li, T. X., Wang, R. Z., Kiplagat, J. K., and Wang, L. W. (2009). Performance study of a consolidated manganese chloride-expanded graphite compound for sorption deep-freezing processes. Appl. Energy 86 (7–8), 1201–1209. doi:10.1016/j.apenergy.2008.06.004
Li, T. X., Wang, R. Z., Wang, L. W., and Kiplagat, J. K. (2009). Study on the heat transfer and sorption characteristics of a consolidated composite sorbent for solar-powered thermochemical cooling systems. Sol. Energy 83 (9), 1742–1755. doi:10.1016/j.solener.2009.06.013
Li, W., Klemeš, J. J., Wang, Q., and Zeng, M. (2021). Energy storage of low potential heat using lithium hydroxide based sorbent for domestic heat supply. J. Clean. Prod. 285, 124907. doi:10.1016/j.jclepro.2020.124907
Li, Y., Perera, S., Crittenden, B., and Bridgwater, J. (2001). The effect of the binder on the manufacture of a 5A zeolite monolith. Powder Technol. 116 (1), 85–96. doi:10.1016/S0032-5910(00)00366-1
Linnow, K., Niermann, M., Bonatz, D., Posern, K., and Steiger, M. (2014). Experimental studies of the mechanism and kinetics of hydration reactions. Energy Procedia 48, 394–404. doi:10.1016/j.egypro.2014.02.046
Liu, D., and Zhu, J. (2015). Investigation of anti-deliquesce properties of Ca(NO3)2·4H2O crystal particles in double-layer coated materials with epoxy resins and portland cement. Asian J. Chem. 27 (10), 3097–3100. doi:10.14233/ajchem.2015.18923
Lumpkin, J. A., and Perlmutter, D. D. (1995). Thermal and water vapor effects on the rate of the dehydration reactions of barium chloride. Thermochim. Acta 249, 335–349. doi:10.1016/0040-6031(95)90720-3
L’vov, B. V. (2007). “Thermal decomposition of solids and melts,” in New thermochemical approach to the mechanism, kinetics and methodology (Berlin, Germany: Springer Dordrecht), Vol. 7. doi:10.1007/978-1-4020-5672-7
Ma, Z., Bao, H., and Roskilly, A. P. (2019). Seasonal solar thermal energy storage using thermochemical sorption in domestic dwellings in the UK. Energy 166, 213–222. doi:10.1016/j.energy.2018.10.066
Mahon, D., Claudio, G., and Eames, P. (2019). A study of novel high performance and energy dense zeolite composite materials for domestic interseasonal thermochemical energy storage. Energy Procedia 158, 4489–4494. doi:10.1016/j.egypro.2019.01.763
Małecka, B., Łącz, A., Drozdz, E., and Małecki, A. (2015). Thermal decomposition of d-metal nitrates supported on alumina. J. Therm. Anal. Calorim. 119 (2), 1053–1061. doi:10.1007/s10973-014-4262-9
Mamani, V., Gutiérrez, A., and Ushak, S. (2018). Development of low-cost inorganic salt hydrate as a thermochemical energy storage material. Sol. Energy Mat. Sol. Cells 176, 346–356. doi:10.1016/j.solmat.2017.10.021
Manole, D. M., and Lage, J. L. (1995). Thermodynamic optimization method of a triple effect absorption system with wasted heat recovery. Int. J. Heat. Mass Transf. 38 (4), 655–663. doi:10.1016/0017-9310(94)00190-7
Marias, F., Neveu, P., Tanguy, G., and Papillon, P. (2014). Thermodynamic analysis and experimental study of solid/gas reactor operating in open mode. Energy 66, 757. doi:10.1016/j.energy.2014.01.101
Martínez-Tejeda, F., Pilatowsky, I., Best, R., Meza-Cruz, O., Gomez, V., Cadenas, E., et al. (2018). Experimental barium chloride-ammonia cooling cycle study at low generation temperatures. Appl. Therm. Eng. 141, 751–761. doi:10.1016/j.applthermaleng.2018.06.020
Mauran, S., Lahmidi, H., and Goetz, V. (2008). Solar heating and cooling by a thermochemical process First experiments of a prototype storing 60 kW h by a solid/gas reaction. Sol. Energy 82 (7), 623–636. doi:10.1016/J.SOLENER.2008.01.002
Mauran, S., Prades, P., and L’Haridon, F. (1993). Heat and mass transfer in consolidated reacting beds for thermochemical systems. Heat Recovery Syst. CHP 13 (4), 315–319. doi:10.1016/0890-4332(93)90055-Z
Mehrabadi, A., and Farid, M. (2018). New salt hydrate composite for low-grade thermal energy storage. Energy 164, 194–203. doi:10.1016/j.energy.2018.08.192
Meisingset, K. K., and Grønvold, F. (1986). Thermodynamic properties and phase transitions of salt hydrates between 270 and 400 K IV. CaCl2·6H2O, CaCl2·4H2O, CaCl2·2H2O, and FeCl3·6H2O. J. Chem. Thermodyn. 18 (2), 159–173. doi:10.1016/0021-9614(86)90130-8
Miao, Q., Zhang, Y., Jia, X., Tan, L., and Ding, Y. (2021). MgSO4-expanded graphite composites for mass and heat transfer enhancement of thermochemical energy storage. Sol. Energy 220, 432–439. doi:10.1016/j.solener.2021.03.008
Michel, B., Mazet, N., Mauran, S., Stitou, D., and Xu, J. (2012). Thermochemical process for seasonal storage of solar energy: Characterization and modeling of a high density reactive bed. Energy 47 (1), 553–563. doi:10.1016/j.energy.2012.09.029
Michel, B., Mazet, N., and Neveu, P. (2014). Experimental investigation of an innovative thermochemical process operating with a hydrate salt and moist air for thermal storage of solar energy: Global performance. Appl. Energy 129, 177–186. doi:10.1016/j.apenergy.2014.04.073
Michel, B., Mazet, N., and Neveu, P. (2016). Experimental investigation of an open thermochemical process operating with a hydrate salt for thermal storage of solar energy: Local reactive bed evolution. Appl. Energy 180, 234–244. doi:10.1016/j.apenergy.2016.07.108
Molenda, M., Bouché, M., Linder, M., Blug, M., Busse, J., and Wörner, A. (2012). Thermochemical energy storage for low temperature applications : Materials and first studies in a gas-solid reactor. Int. Conf. Energy Storage 2, 1–10.
Molenda, M., Stengler, J., Linder, M., and Wörner, A. (2013). Reversible hydration behavior of CaCl2 at high H2O partial pressures for thermochemical energy storage. Thermochim. Acta 560, 76–81. doi:10.1016/j.tca.2013.03.020
Mrowiec-Białoń, J., Jarzȩbski, A. B., Lachowski, A. I., Malinowski, J. J., and Aristov, Y. I. (1997). Effective inorganic hybrid adsorbents of water vapor by the sol-gel method. Chem. Mat. 9 (11), 2486–2490. doi:10.1021/cm9703280
Mu, J., and Perlmutter, D. D. (1981). Thermal decomposition of inorganic sulfates and their hydrates. Ind. Eng. Chem. Proc. Des. Dev. 20 (4), 640–646. doi:10.1021/i200015a010
Myagmarjav, O., Ryu, J., and Kato, Y. (2014). Lithium bromide-mediated reaction performance enhancement of a chemical heat-storage material for magnesium oxide/water chemical heat pumps. Appl. Therm. Eng. 63 (1), 170–176. doi:10.1016/j.applthermaleng.2013.10.045
Navarro, M. E., Palacios Trujillo, A., Jiang, Z., Jin, Y., Zhang, Y., and Ding, Y. (2021). “Chapter 7. Manufacture of thermal energy storage materials,” in Thermal energy storage: Materials, devices, systems and applications, first. Editor Y. Ding (London, UK: Royal Society of Chemistry), 500. doi:10.1039/9781788019842-00121
Nedea, S., Zondag, H., Rindt, C., Pathak, A. D., Smeulders, D., and van Duin, A. C. T. (2016). Reactive force field development for magnesium chloride hydrates and its application for seasonal heat storage. Phys. Chem. Chem. Phys. 18 (23), 15838–15847. doi:10.1039/c6cp02762h
Noorsyakirah, A., Mazlan, M., Afian, O. M., Aswad, M. A., Jabir, S. M., Nurazilah, M., et al. (2016). Application of potassium carbonate as space holder for metal injection molding process of open pore copper foam. Procedia Chem. 19, 552–557. doi:10.1016/j.proche.2016.03.052
N’Tsoukpoe, K. E., Le Pierrès, N., and Luo, L. (2013). Experimentation of a LiBr-H2O absorption process for long-term solar thermal storage: Prototype design and first results. Energy 53, 179–198. doi:10.1016/j.energy.2013.02.023
N’Tsoukpoe, K. E., Le Pierres, N., and Luo, L. (2014). Experimentation of a LiBr-H2O absorption process for long-term solar thermal storage: Prototype design and first results. Energy 37 (1), 179–198. doi:10.1016/j.energy.2013.02.023
N’Tsoukpoe, K. E., Liu, H., Le Pierrès, N., and Luo, L. (2009). A review on long-term sorption solar energy storage. Renew. Sustain. Energy Rev. 13 (9), 2385–2396. doi:10.1016/j.rser.2009.05.008
N’Tsoukpoe, K. E., Rammelberg, H. U., Lele, A. F., Korhammer, K., Watts, B. A., Schmidt, T., et al. (2014). A review on the use of calcium chloride in applied thermal engineering. Appl. Therm. Eng. 75, 513–531. doi:10.1016/j.applthermaleng.2014.09.047
N’Tsoukpoe, K. E., Schmidt, T., Rammelberg, H. U., Watts, B. A., and Ruck, W. K. L. (2014). A systematic multi-step screening of numerous salt hydrates for low temperature thermochemical energy storage. Appl. Energy 124, 1–16. doi:10.1016/j.apenergy.2014.02.053
Ogura, H., Haguro, M., Shibata, Y., and Otsubo, Y. (2007). Reaction characteristics of CaSO4/CaSO4·1/2H2O reversible reaction for chemical heat pump. J. Chem. Eng. Jpn. 40 (13), 1252–1256. doi:10.1252/jcej.07WE223
Okhrimenko, L., Favergeon, L., Johannes, K., Kuznik, F., and Pijolat, M. (2017). Thermodynamic study of MgSO4– H2O system dehydration at low pressure in view of heat storage. Thermochim. Acta 656, 135–143. doi:10.1016/j.tca.2017.08.015
Ousaleh, H. A., Said, S., Zaki, A., Faik, A., and El Bouari, A. (2019). Silica gel/inorganic salts composites for thermochemical heat storage: Improvement of energy storage density and assessment of cycling stability. Mater. Today Proc. 30, 937–941. doi:10.1016/j.matpr.2020.04.354
Pathak, A. D., Nedea, S., Zondag, H., Rindt, C., and Smeulders, D. (2017). Diffusive transport of water in magnesium chloride dihydrate under various external conditions for long term heat storage: A ReaxFF-MD study. Eur. J. Mech. - B/Fluids 64, 93–101. doi:10.1016/j.euromechflu.2016.12.011
Paulik, F., Paulik, J., Arnold, M., and Naumann, R. (1988). Investigation on the thermal behaviour of Mg(NO3)2·6H2O I. The decomposition behaviour. J. Therm. Analysis 34 (3), 627–635. doi:10.1007/BF02331764
Paulik, J., Paulik, F., and Arnold, M. (1983). Thermogravimetric examination of the dehydration of calcium nitrate tetrahydrate under quasiisothermal and quasi-isobaric conditions. J. Therm. Analysis 27 (2), 409–418. doi:10.1007/BF01914678
Pistorius, C. E. F. (1962). Polymorphism and incongruent melting of SrCl2 6H2O to 50 kilobars. Z. für Phys. Chem. 40, 1918. doi:10.1524/zpch.1962.31.3_4.155
Pontiga, F., Valverde, J. M., Moreno, H., and Duran-Olivencia, F. J. (2013). Dry gas-solid carbonation in fluidized beds of Ca(OH)2 and nanosilica/Ca(OH)2 at ambient temperature and low CO2 pressure. Chem. Eng. J. 222, 546–552. doi:10.1016/j.cej.2013.02.067
Posern, K., and Kaps, C. (2010). Calorimetric studies of thermochemical heat storage materials based on mixtures of MgSO4 and MgCl2. Thermochim. Acta 502 (1–2), 73–76. doi:10.1016/j.tca.2010.02.009
Posern, K., and Kaps, C. (2008). Humidity controlled calorimetric investigation of the hydration of MgSO4 hydrates. J. Therm. Anal. Calorim. 92 (3), 905–909. doi:10.1007/s10973-007-8640-4
Posern, K., Linnow, K., Niermann, M., Kaps, C., and Steiger, M. (2015). Thermochemical investigation of the water uptake behavior of MgSO4 hydrates in host materials with different pore size. Thermochim. Acta 611, 1–9. doi:10.1016/j.tca.2015.04.031
Posern, K., and Osburg, A. (2017). Determination of the heat storage performance of thermochemical heat storage materials based on SrCl2 and MgSO4. J. Therm. Anal. Calorim. 131 (3), 2769–2773. doi:10.1007/s10973-017-6861-8
Rammelberg, H. U., Schmidt, T., and Ruck, W. (2012). Hydration and dehydration of salt hydrates and hydroxides for thermal energy storage - kinetics and energy release. Energy Procedia 30, 362–369. doi:10.1016/j.egypro.2012.11.043
Rau, J. J., Klein, S. A., and Mitchell, J. W. (1991). Characteristics of lithium chloride in rotary heat and mass exchangers. Int. J. Heat. Mass Transf. 34 (11), 2703–2713. doi:10.1016/0017-9310(91)90229-8
Rehman, A. U., Shah, M. Z., Ali, A., Zhao, T., Shah, R., Ullah, I., et al. (2021). Thermochemical heat storage ability of ZnSO4 · 7H2O as potential long-term heat storage material. Int. J. Energy Res. 45 (3), 4746–4754. doi:10.1002/er.6077
Reisman, A., and Karlak, J. (1958). Observations on the differential thermal analysis of copper sulfate pentahydrate. J. Am. Chem. Soc. 80 (24), 6500–6503. doi:10.1021/ja01557a009
Richter, M., Bouché, M., and Linder, M. (2016). Heat transformation based on CaCl2/H2O - Part A: Closed operation principle. Appl. Therm. Eng. 102, 615–621. doi:10.1016/j.applthermaleng.2016.03.076
Richter, M., Habermann, E. M., Siebecke, E., and Linder, M. (2018). A systematic screening of salt hydrates as materials for a thermochemical heat transformer. Thermochim. Acta 659, 136–150. doi:10.1016/j.tca.2017.06.011
Riffat, S., Ozankaya, G., Yanan, Z., Jarimi, H., Aydin, D., and Chen, X. (2018). Review on the recent progress of thermochemical materials and processes for solar thermal energy storage and industrial waste heat recovery. Int. J. Low-Carbon Technol. 2018, 44–69. doi:10.1093/ijlct/cty052
Ristić, A., and Henninger, S. K. (2014). Sorption composite materials for solar thermal energy storage. Energy Procedia 48, 977–981. doi:10.1016/j.egypro.2014.02.111
Roelands, M., Cuypers, R., Kruit, K. D., Oversloot, H., de Jong, A. J., Duvalois, W., et al. (2015). Preparation & characterization of sodium sulfide hydrates for application in thermochemical storage systems. Energy Procedia 70 (0), 257–266. doi:10.1016/j.egypro.2015.02.122
Roßkopf, C., Afflerbach, S., Schmidt, M., Gortz, B., Kowald, T., Linder, M., et al. (2015). Investigations of nano coated calcium hydroxide cycled in a thermochemical heat storage. Energy Convers. Manag. 97, 94–102. doi:10.1016/j.enconman.2015.03.034
Roßkopf, C., Haas, M., Faik, A., Linder, M., and Wörner, A. (2014). Improving powder bed properties for thermochemical storage by adding nanoparticles. Energy Convers. Manag. 86, 93–98. doi:10.1016/j.enconman.2014.05.017
Ryu, J., Takahashi, R., Hirao, N., and Kato, Y. (2007). Effect of transition metal mixing on reactivities of magnesium oxide for chemical heat pump. J. Chem. Eng. Jpn. 40 (13), 1281–1286. doi:10.1252/jcej.07WE171
Sánchez, A. R., Klein, H. P., and Groll, M. (2003). Expanded graphite as heat transfer matrix in metal hydride beds. Int. J. Hydrogen Energy 28 (5), 515–527. doi:10.1016/S0360-3199(02)00057-5
Sarkar, J., and Bhattacharyya, S. (2012). Application of graphene and graphene-based materials in clean energy-related devices Minghui. Arch. Thermodyn. 33 (4), 23–40. doi:10.1002/er
Savchenko, E. V., Gordeeva, L. G., Glaznev, I. S., Aristov, Y. I., and Malakhov, V. V. (2006). Impact of phase composition on water adsorption on inorganic hybrids ‘salt/silica. J. Colloid Interface Sci. 301 (2), 685–691. doi:10.1016/j.jcis.2006.05.009
Scapino, L., Zondag, H. A., Van Bael, J., Diriken, J., and Rindt, C. C. M. (2017). Energy density and storage capacity cost comparison of conceptual solid and liquid sorption seasonal heat storage systems for low-temperature space heating. Renew. Sustain. Energy Rev. 76, 1314–1331. doi:10.1016/j.rser.2017.03.101
Scapino, L., Zondag, H. A., Van Bael, J., Diriken, J., and Rindt, C. C. M. (2017). Sorption heat storage for long-term low-temperature applications: A review on the advancements at material and prototype scale. Appl. Energy 190, 920–948. doi:10.1016/j.apenergy.2016.12.148
Scopus data based (2020). Scopus data based. Available at: https://www.scopus.com/term/analyzer.uri?sid=481cd47e95109f8ff702d116971b405d&origin=resultslist&src=s&s=TITLE-ABS-KEY%28%22electric+batteries%22%29&sort=plf-f&sdt=b&sot=b&sl=35&count=60654&analyzeResults=Analyze+results&txGid=950fcd83cc0c9d84bd58735e62fb (Accessed Feb. 14, 2020).
Sharma, S. K., Jotshi, C. K., and Kumar, S. (1990). Thermal stability of sodium salt hydrates for solar energy storage applications. Sol. Energy 45 (3), 177–181. doi:10.1016/0038-092X(90)90051-D
Shere, L., Trivedi, S., Roberts, S., Sciacovelli, A., and Ding, Y. (2018). Synthesis and characterization of thermochemical storage material combining porous zeolite and inorganic salts. Heat. Transf. Eng. 40, 1176–1181. doi:10.1080/01457632.2018.1457266
Shiren, Y., Masuzawa, M., Takahashi, T., Yamada, S., Hayakawa, K., Motohashi, Y., et al. (2020). Thermal input/output and operation characteristics of a chemical heat pump using the hydration reaction of calcium sulphate. Sustain. Energy Fuels 4 (8), 4046–4056. doi:10.1039/d0se00500b
Shkatulov, A. I., Houben, J., Fischer, H., and Huinink, H. P. (2020). Stabilization of K2CO3 in vermiculite for thermochemical energy storage. Renew. Energy 150, 990–1000. doi:10.1016/j.renene.2019.11.119
Shkatulov, A., Joosten, R., Fischer, H., and Huinink, H. (2020). Core-shell encapsulation of salt hydrates into mesoporous silica shells for thermochemical energy storage. ACS Appl. Energy Mat. 3 (7), 6860–6869. doi:10.1021/acsaem.0c00971
Shkatulov, A., Ryu, J., Kato, Y., and Aristov, Y. (2012). Composite material ‘ Mg(OH)2/vermiculite’: A promising new candidate for storage of middle temperature heat. Energy 44 (1), 1028–1034. doi:10.1016/j.energy.2012.04.045
Simonova, I. A., Freni, A., Restuccia, G., and Aristov, Y. I. (2009). Water sorption on composite ‘silica modified by calcium nitrate. Microporous Mesoporous Mat. 122 (1–3), 223–228. doi:10.1016/j.micromeso.2009.02.034
Soda, M., and Beyene, A. (2016). Multiphase ultra-low grade thermal energy storage for organic Rankine cycle. Int. J. Energy Res. 40 (1), 51–60. doi:10.1002/er.3300
Sögütoglu, L. C., Birkelbach, F., Werner, A., Fischer, H., Huinink, H., and Adan, O. (2020). Hydration of salts as a two-step process: Water adsorption and hydrate formation. Thermochim. Acta 695, 178819. doi:10.1016/j.tca.2020.178819
Sögütoglu, L. C., Donkers, P. A. J., Fischer, H. R., Huinink, H. P., and Adan, O. C. G. (2018). In-depth investigation of thermochemical performance in a heat battery: Cyclic analysis of K2CO3, MgCl2 and Na2S. Appl. Energy 215, 159–173. doi:10.1016/j.apenergy.2018.01.083
Solé, A., Barreneche, C., Martorell, I., and Cabeza, L. F. (2016). Corrosion evaluation and prevention of reactor materials to contain thermochemical material for thermal energy storage. Appl. Therm. Eng. 94, 355–363. doi:10.1016/j.applthermaleng.2015.10.156
Sørensen, O. T. (1981). Quasi-isothermal methods in thermal analysis. Thermochim. Acta 50 (1–3), 163–175. doi:10.1016/0040-6031(81)85052-6
Steinmetz, D., Ducarroir, M., Paredes Romero, H., and Rivot, M. (1981). Decomposition kinetics of magnesium sulfate in considering solar energy storage. Entrople Paris 17 (102), 18–17.
Strydom, C. A., Hudson-Lamb, D. L., Potgieter, J. H., and Dagg, E. (1995). The thermal dehydration of synthetic gypsum. Thermochim. Acta 269-270, 631–638. doi:10.1016/0040-6031(95)02521-9
Su, W., Darkwa, J., and Kokogiannakis, G. (2015). Review of solid-liquid phase change materials and their encapsulation technologies. Renew. Sustain. Energy Rev. 48, 373–391. doi:10.1016/j.rser.2015.04.044
Sutton, R., Jewell, E., Searle, J., and Elvins, J. (2018a). Discharge performance of blended salt in matrix materials for low enthalpy thermochemical storage. Appl. Therm. Eng. 145, 483–493. doi:10.1016/j.applthermaleng.2018.09.052
Sutton, R. J., Jewell, E., Elvins, J., Searle, J. R., and Jones, P. (2018b). Characterising the discharge cycle of CaCl2and LiNO3hydrated salts within a vermiculite composite scaffold for thermochemical storage. Energy Build. 162, 109–120. doi:10.1016/j.enbuild.2017.11.068
Tanashev, Y. Y., Krainov, A. V., and Aristov, Y. I. (2013). Thermal conductivity of composite sorbents ‘salt in porous matrix’ for heat storage and transformation. Appl. Therm. Eng. 61 (2), 401–407. doi:10.1016/j.applthermaleng.2013.08.022
Tang, X., Jia, S., Cheng, J., Zhang, M., Yan, H., Zhao, H., et al. (2017). Experimental investigations of composite adsorbent 13X/CaCl2 on an adsorption cooling system. Appl. Sci. (Basel). 7 (6), 620. doi:10.3390/app7060620
Tian, B., Jin, Z. Q., Wang, L. W., and Wang, R. Z. (2012). Permeability and thermal conductivity of compact chemical and physical adsorbents with expanded natural graphite as host matrix. Int. J. Heat. Mass Transf. 55 (15–16), 4453–4459. doi:10.1016/j.ijheatmasstransfer.2012.04.016
Tso, C. Y., and Chao, C. Y. H. (2012). Activated carbon, silica-gel and calcium chloride composite adsorbents for energy efficient solar adsorption cooling and dehumidification systems. Int. J. Refrig. 35 (6), 1626–1638. doi:10.1016/j.ijrefrig.2012.05.007
Urs Rammelberg, H., Schmidt, T., and Ruck, W. (2012). Hydration and dehydration of salt hydrates and hydroxides for thermal energy storage - kinetics and energy release. Energy Procedia 30, 362–369. doi:10.1016/j.egypro.2012.11.043
van der Pal, M., and Critoph, R. E. (2017). Performance of CaCl2-reactor for application in ammonia-salt based thermal transformers. Appl. Therm. Eng. 126, 518–524. doi:10.1016/j.applthermaleng.2017.07.086
Van Dillen, A. J., Terörde, R. J. A. M., Lensveld, D. J., Geus, J. W., and De Jong, K. P. (2003). Synthesis of supported catalysts by impregnation and drying using aqueous chelated metal complexes. J. Catal. 216 (1–2), 257–264. doi:10.1016/S0021-9517(02)00130-6
van Essen, V. M., Cot Gores, J., Bleijendaal, L. P. J., Zondag, H. A., Schuitema, R., Bakker, M., et al. (2009). Characterization of salt hydrates for compact seasonal thermochemical storage. Int. Conf. Energy Sustain. 2 (2), 825–830. doi:10.1115/ES2009-90289
van Essen, V. M., Zondag, H. A., Gores, J. C., Bleijendaal, L. P. J., Bakker, M., Schuitema, R., et al. (2009). Characterization of MgSO4 hydrate for thermochemical seasonal heat storage. J. Sol. Energy Eng. 131 (4), 041014. doi:10.1115/1.4000275
van Ravensteijn, B. G. P., Donkers, P. A. J., Ruliaman, R. C., Eversdijk, J., Fischer, H. R., Huinink, H. P., et al. (2021). Encapsulation of salt hydrates by polymer coatings for low-temperature heat storage applications. ACS Appl. Polym. Mat. 3, 1712–1726. doi:10.1021/acsapm.0c01186
Visscher, K., and Veldhuis, J. B. J. (2005). “Comparison of candidate materials for seasonal storage of solar heat through dynamic simulation of building and renewable energy system,” in IBPSA 2005 - International Building Performance Simulation Association 2005, September, 2005, 1285–1292.
Voigt, W., and Zeng, D. (2002). Solid–liquid equilibria in mixtures of molten salt hydrates for the design of heat storage materials. Pure Appl. Chem. 74 (10), 1909–1920. doi:10.1351/pac200274101909
Vranes, M., Gadzuric, S., Dozic, S., and Zsigrai, I. (2010). Stability and thermodynamics of thermochromic cobalt(II) chloride complexes in low-melting phase change materials. J. Chem. Eng. Data 55 (5), 2000–2003. doi:10.1021/je9009267
Wang, J. Y., Wang, R. Z., and Wang, L. W. (2016). Water vapor sorption performance of ACF-CaCl2 and silica gel-CaCl2 composite adsorbents. Appl. Therm. Eng. 100, 893–901. doi:10.1016/j.applthermaleng.2016.02.100
Wang, Q., Xie, Y., Ding, B., Yu, G., Ye, F., and Xu, C. (2019). Structure and hydration state characterizations of MgSO4-zeolite 13x composite materials for long-term thermochemical heat storage. Sol. Energy Mat. Sol. Cells 200, 110047. doi:10.1016/j.solmat.2019.110047
Wendlandt, W. W. (1962). A new apparatus for simultaneous differential thermal analysis and gas evolution analysis. Anal. Chim. Acta X. 27, 309–314. doi:10.1016/s0003-2670(00)88506-2
Whiting, G., Grondin, D., Bennici, S., and Auroux, A. (2013). Heats of water sorption studies on zeolite-MgSO 4 composites as potential thermochemical heat storage materials. Sol. Energy Mat. Sol. Cells 112, 112–119. doi:10.1016/j.solmat.2013.01.020
Whiting, G. T., Grondin, D., Stosic, D., Bennici, S., and Auroux, A. (2014). Zeolite-MgCl2 composites as potential long-term heat storage materials: Influence of zeolite properties on heats of water sorption. Sol. Energy Mat. Sol. Cells 128, 289–295. doi:10.1016/j.solmat.2014.05.016
Wu, H., Wang, S., and Zhu, D. (2007). Effects of impregnating variables on dynamic sorption characteristics and storage properties of composite sorbent for solar heat storage. Sol. Energy 81 (7), 864–871. doi:10.1016/j.solener.2006.11.013
Xie, N., Huang, Z., Luo, Z., Gao, X., Fang, Y., and Zhang, Z. (2017). Inorganic salt hydrate for thermal energy storage. Appl. Sci. 2017, 1–17. doi:10.3390/app7121317
Xu, C., Yu, Z., Xie, Y., Ren, Y., Ye, F., and Ju, X. (2017). Study of the hydration behavior of zeolite-MgSO4 composites for long-term heat storage. Appl. Therm. Eng. 129, 250–259. doi:10.1016/j.applthermaleng.2017.10.031
Xu, S. Z., Wang, L., Wang, R. Z., Wang, L. W., and Zhu, J. (2018). A zeolite 13X/magnesium sulfate–water sorption thermal energy storage device for domestic heating. Energy Convers. Manag. 171, 98–109. doi:10.1016/j.enconman.2018.05.077
Yan, T. S., Li, T. X., Xu, J. X., and Chao, J. W. (2019). Understanding the transition process of phase change and dehydration reaction of salt hydrate for thermal energy storage. Appl. Therm. Eng.November 166, 114655. doi:10.1016/j.applthermaleng.2019.114655
Yan, T., and Zhang, H. (2022). A critical review of salt hydrates as thermochemical sorption heat storage materials: Thermophysical properties and reaction kinetics. Sol. Energy 242, 157–183. doi:10.1016/j.solener.2022.07.002
Yeromin, O., Belyanovskaya, E., Kovalenko, V., Kotok, V., Sukhyy, M., Kolomiyets, O., et al. (2018). The study of properties of composite adsorptive materials ‘silica gel – crystalline hydrate’ for heat storage devices. Eastern-European J. Enterp. Technol. 1 (691), 52–58. doi:10.15587/1729-4061.2018.123896
Yu, N., Wang, R. Z., Lu, Z. S., Wang, L. W., and Ishugah, T. F. (2014). Evaluation of a three-phase sorption cycle for thermal energy storage. Energy 67, 468–478. doi:10.1016/j.energy.2013.12.044
Yu, N., Wang, R. Z., Lu, Z. S., and Wang, L. W. (2015). Study on consolidated composite sorbents impregnated with LiCl for thermal energy storage. Int. J. Heat. Mass Transf. 84, 660–670. doi:10.1016/j.ijheatmasstransfer.2015.01.065
Yu Sung, Y., and Ulrichson, D. L. (1976). Thermochemical water splitting: The reverse deacon reaction and alternatives. Proc. Symp. Thermochem Gener. Hydrog. 21 (3), 55–64.
Zamengo, M., Ryu, J., and Kato, Y. (2013). Magnesium hydroxide - expanded graphite composite pellets for a packed bed reactor chemical heat pump. Appl. Therm. Eng. 61 (2), 853–858. doi:10.1016/j.applthermaleng.2013.04.045
Zamengo, M., Ryu, J., and Kato, Y. (2014). Thermochemical performance of magnesium hydroxide-expanded graphite pellets for chemical heat pump. Appl. Therm. Eng. 64 (1–2), 339–347. doi:10.1016/j.applthermaleng.2013.12.036
Zhang, Y. N., Wang, R. Z., Zhao, Y. J., Li, T. X., Riffat, S. B., and Wajid, N. M. (2016). Development and thermochemical characterizations of vermiculite/SrBr2 composite sorbents for low-temperature heat storage. Energy 115, 120–128. doi:10.1016/j.energy.2016.08.108
Zhao, C. Y., Ji, Y., and Xu, Z. (2015). Investigation of the Ca(NO3)2–NaNO3 mixture for latent heat storage. Sol. Energy Mat. Sol. Cells 140, 281–288. doi:10.1016/j.solmat.2015.04.005
Zhao, Y. J., Wang, R. Z., Zhang, Y. N., and Yu, N. (2016). Development of SrBr2composite sorbents for a sorption thermal energy storage system to store low-temperature heat. Energy 115, 129–139. doi:10.1016/j.energy.2016.09.013
Zhang, Y., Sun, J., Ma, G., Wang, Z., Xie, S., Jing, Y., et al. (2019). Hydrophilic expanded graphite-magnesium nitrate hexahydrate composite phase change materials: Understanding the effect of hydrophilic modification on thermophysical properties. Int. J. Energy Res. 43 (3), 1121–1132. doi:10.1002/er.4336
Zheng, M., Sun, S., Hu, J., Zhao, Y., and Yu, L. J. (2015). Preparation of nano-composite Ca2-αZnα(OH)4 with high thermal storage capacity and improved recovery of stored heat energy. Open Eng. 5 (1), 42–47. doi:10.1515/eng-2015-0002
Zhu, D., Wu, H., and Wang, S. (2006). Experimental study on composite silica gel supported CaCl2 sorbent for low grade heat storage. Int. J. Therm. Sci. 45 (8), 804–813. doi:10.1016/j.ijthermalsci.2005.10.009
Zondag, H. A., Kikkert, B. W. J., Smeding, S., and Bakker, M. (2011). Thermochemical seasonal solar heat storage with mgcl2 . 6h2o : First upscaling of the reactor. Int. Conf. Sustain. Energy Storage, Belf. Irel. 2011, 1–9.
Zondag, H. A., van Essen, V. M., Bleijendaal, L. P. J., Kikkert, B. W. J., and Bakker, M. (2011). “Application of MgCl2· 6H2O for thermochemical seasonal solar heat storage,” in Presented at the the 5th International Renewable Energy Storage Conference IRES 2010, Berlin, Germany, 22-24 November 2010. [Online]. Available at: ftp://www.nrg-nl.com/pub/www/library/report/2010/m10086.pdf%5Cnfiles/316/Zondag-et-al2.pdf.
Keywords: thermochemical energy storage, sorption, manufacturing, candidates, review
Citation: Palacios A, Navarro ME, Barreneche C and Ding Y (2022) Water sorption-based thermochemical storage materials: A review from material candidates to manufacturing routes. Front. Therm. Eng. 2:1003863. doi: 10.3389/fther.2022.1003863
Received: 26 July 2022; Accepted: 27 October 2022;
Published: 01 December 2022.
Edited by:
Zhiwei Ma, Durham University, United KingdomReviewed by:
Andrea Frazzica, National Research Council (CNR), ItalyShanshan Cai, Huazhong University of Science and Technology, China
Copyright © 2022 Palacios, Navarro, Barreneche and Ding. This is an open-access article distributed under the terms of the Creative Commons Attribution License (CC BY). The use, distribution or reproduction in other forums is permitted, provided the original author(s) and the copyright owner(s) are credited and that the original publication in this journal is cited, in accordance with accepted academic practice. No use, distribution or reproduction is permitted which does not comply with these terms.
*Correspondence: Anabel Palacios, YW5hYmVsLnBhbGFjaW9zQGhzbHUuY2g=