- 1Openly Published Environmental Sensing Lab, Department of Biological and Ecological Engineering, College of Agricultural Sciences, Oregon State University, Corvallis, OR, United States
- 2School of Electrical Engineering and Computer Science, College of Engineering, Oregon State University, Corvallis, OR, United States
- 3Department of Biological and Ecological Engineering, College of Agricultural Sciences, Oregon State University, Corvallis, OR, United States
Our objective was to develop and validate a freely downloadable, open-source, 3D printed rain gauge calibrator that can be adjusted for a wide range of gauges. The calibrator applies constant low, medium, and high-intensity water delivery rate, and allows the user to modify the design to conform to their system based on parametric design. The design may be modified and printed using freely available computer-aided design (CAD) software. Currently available devices for calibration tend to be designed for specific rain gauges, are expensive, employ low-precision water reservoirs, are not field portable, and do not offer the flexibility needed to test the ever more popular small-aperture rain gauges (smaller surface area to catch precipitation than the classical 200 mm standard). To overcome the fact that different 3D printers yield different print qualities, we devised a simple post-printing step that controls critical dimensions to assure robust performance. Specifically, orifices of the calibrator are drilled to reach the target flow rates. Laboratory tests showed that flow rates of 25, 50, and 83 ml/min were consistent between prints (coefficient of variation of 3.9, 2.2, and 1.8%, respectively), and between trials of each part, while the total applied water was precisely controlled (0.1%) by the use of a volumetric flask as the reservoir. The entire system costs under US$10.
Introduction
Rain gauges are essential tools for high-quality and reliable observation of precipitation. They are the most direct method for surface rainfall quantification, as utilized for hydrological, climatological, and agricultural studies (Habib et al., 2012). The following question arises concerning the validity of rain gauges: How do we know that the sampler is correctly reporting the rainfall amount. To validate the integrity of the rain gauge requires the application of a known volume of water at a known constant flow rate. It is essential to do dynamic calibration, calibration that requires a constant flow rate, because it allows for compensation of error cause by spillage (Ciach, 2003; Texas Electronics, 2019). Spillage occurs when a tipping bucket is not able to capture the rainfall due to the transition between the tipping, the rain is then spilled and not measured. Such devices already exist but have important limitations. Some employ simple gravity fed inverted bottles wherein the rate of flow decreases with the depletion of the water supply, and thus do not provide a constant rate of application. Others are tuned to specific size rain gauges, applying rates of flow and requiring a mechanical attachment that is not adaptable to alternative sizes and shapes of rain collectors. An example of this ATMOS 41 rain gauge’s (Meter group, Pullman, WA, United States) collection area smaller than those for which calibration tools had been developed, requiring that we develop a design capable of delivering lower rates of application. Custom calibrators may include a setup of programmable pumps, loggers, digital scales, and computers to be able to perform the calibration of the rain gauge (Humphrey et al., 1997). With numerous external instruments, it is time consuming to organize and reprogram all the devices required to calibrate different rain gauges.
We sought to provide a robust system with a repeatability within less than 1% in total amount and 5% of the target rate that can be modified to match a variety of rain gauge specifications and geometries. The repeatability of 5% was chosen because it is an achievable target given the technologies used to make the calibrator: 3D printing and drilling. We chose 740 mm/h (high), 450 mm/h (medium), and 220 mm/h (low); these will be referred to as 6-, 10-, and 20-min stoppers, respectively, which represent the time to drain for our setup. Three options were chosen so that the user had a range of rates to calibrate their device. These rates were selected with the objective to be able to capture data in the events of high intensity rainfall. We believe that it is in these events during which the data collection must be performed more carefully. In addition to this, it is not quite possible to design a calibrator with extremely fine resolution due to the elevated cost of the finding the equipment to manufacture it. We sought to remove the constraints of the high cost of many calibration solutions and the requirement to return a rain gauge to the lab to conduct calibration (Bergmann et al., 2001; Vasvári, 2005). Thus, we present a low-cost rain gauge calibration system which is easily customized in geometry to fit a wide range of gauges, provides for a user-definable range of constant flow rates, and most importantly is easily employed in the field. It is imperative that rain gauges are not used out-of-the box as they need proper calibration so that the collected data is correct. Our proposed solution removes the need to perform the calibration in the lab and allows the user to perform these calibrations while in the field; this reduces the time to setup and speeds up the data collection process.
A robust passive approach that delivers a constant flow rate is the Mariotte bottle (Mariotte, 1679). A typical Mariotte bottle setup has a container with a tube coming in from the top for air and another orifice for the liquid output usually on the side or through the top (Supplementary Figure 1). The flow rate is dictated by the following equation: hair − houtput = h. hair is the level from the bottom of the container to the air inlet inside the container and houtput is the level from bottom of the container to the water outlet. The difference between these two is net head which can be seen depicted in Supplementary Figure 1. The bottle is designed to deliver a constant flow of liquid, which is a function of the distance between the bottom of the air inlet and liquid outlet, orifice sizes, and the hydraulic resistance.
Our design employs the Mariotte bottle principle (Figure 1A) with the bottle inverted and both tubes formed into an O-ring sealed element we refer to as “Mariotte stoppers” that seal into the top of a volumetric flask. The materials list for seals and bottles can be found in Supplementary Table 4. Multiple flow rates were achieved in the same device by placing three Mariotte stoppers on a single plate that rests in the rain gauge (Figures 1A,B). Each Marriot stopper is cylindrical with two orifices on the top, a short-path air inlet and a long-path liquid outlet, with half of the cone suppressed toward the core; the suppressed section goes from the core to the outside in the direction of the air inlet (Figure 1C). The suppression is to facilitate the flow of air into the bottle and limit the path it must travel to enter. The side that is not suppressed gives the calibrator the change in height, from the air inlet to liquid outlet, required to dictate the flow rate (Figure 1C). The rate of outflow is dictated by the combination of the constant head, hydraulic resistance, and the outlet aperture. Except for the first few seconds of operation, the delivered water is in the form of discrete drips, and so the device could be used with disdrometers as well as other mechanical rain gauges.
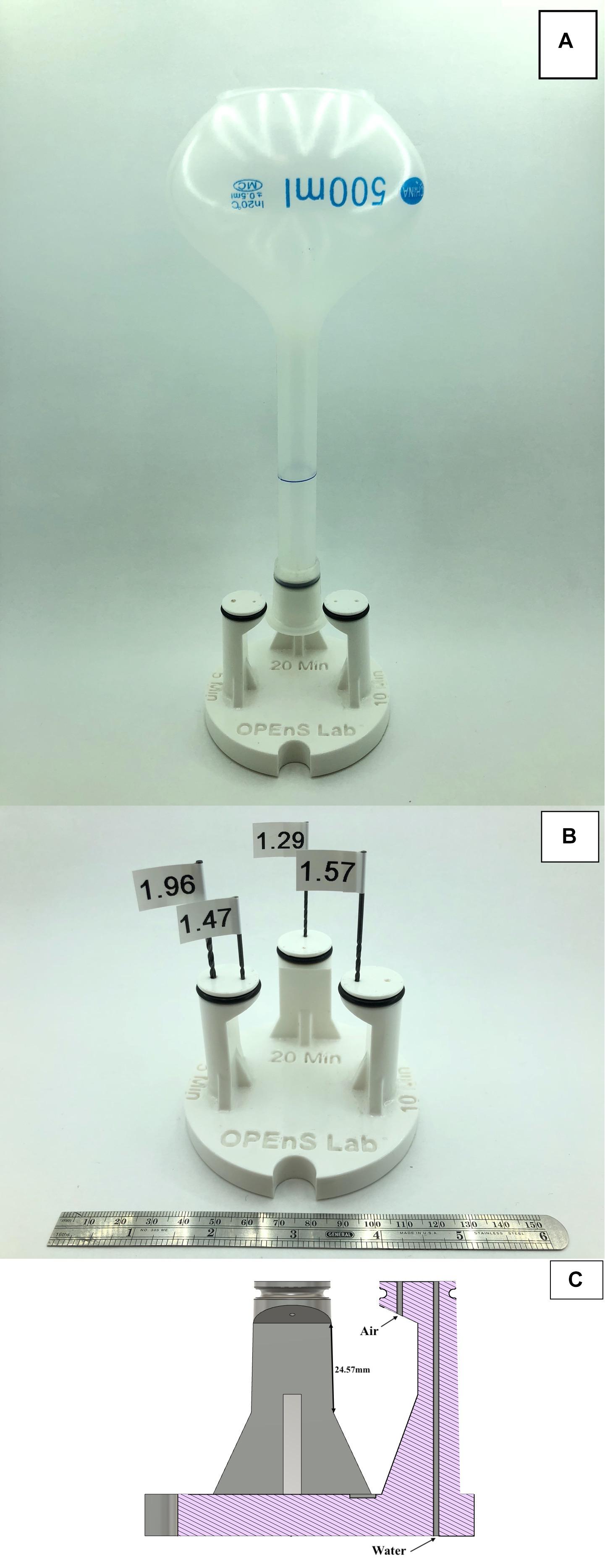
Figure 1. (A) Assembled three-rate assembly system; the circular cutout in this version accommodates the solar radiation sensor located within the rain gauge for which this was designed. (B) A particular print of the design illustrates the limitations of many printers to achieve a smooth surface and presents the drill-bits sizes, in mm, employed to obtain reproducible performance. (C) CAD rendering of the design illustrates that each stopper has an air inlet port and water outlet port.
Materials and Methods
The three-rate calibrator was designed in Fusion 360 (Fusion360, 2018) which provides a freely available, user-friendly interface which allows the design to be edited per the requirements of a particular rain gauge. The design is parametric allowing the user to change defined variables that will change the design to be adapted to a classic round rain gauge. The design also includes the individual calibrator, without the base attachment, that can be used to create a custom shape base for a different geometry rain gauge. The reservoir of water employed in the test was a 500 ml (±0.5 ml, or ±0.1%) volumetric flask made from polypropylene, as purchased online for under US$5. Volumetric flasks of 100, 250, and 1000 ml are available with the same size openings, allowing a variety of total volumes of water delivery. This specific bottle does not need to be used but it will require customization if another bottle is used.
At the OPEnS lab1, we employed two 3D printers to confirm multi-platform production capability: a Lulzbot TAZ5 and Fusion3 F400. The Fusion3 F400 uses a 0.4 mm nozzle and used a 1.75 mm diameter filament. The slicer used was Simplify3D and used their F400_0.4_HatchABS printing profile with the auto-configure option “Standard.” The Lulzbot TAZ5 uses a 0.5 mm nozzle and used a 3.0 mm diameter filament. The slicer software used was Cura Lulzbot edition and used their ABS (Village Plastics) printing profile with the auto-configure option “Standard.” Important printer settings are listed in Supplementary Tables 1, 2 for the Fusion3 and TAZ5, respectively. The layer height set by the profiles is adequate for a working calibrator. A smaller layer height will produce a smoother part, whereas a thicker layer height will have a coarse finish. Generally, having a smaller layer height will result in a better part, but ultimately the accuracy and precision of the calibrator is controlled by the post-processing steps. All parts were printed from Acrylonitrile Butadiene Styrene (ABS) plastic filament. ABS plastic is considered a good engineering plastic and it was chosen for its structural stability, impact resistance, and price. It is worth noting that there are other filaments that could be used for this application but ABS offers a good balance between price and material properties. After cooling, the precise diameter of the water outlet and air inlet apertures were established by drilling out the excess plastic using a drill press and drill bits of the sizes in Supplementary Table 3. It is recommended to use a drill press and not a hand drill for the post-processing.
Once the drill bit has been locked in on the drill press the calibrator’s corresponding hole must be aligned to the drill. For example, if the 6-min setting is being drilled out, a 1.47 mm drill bit would correspond to the air hole and a 1.96 mm drill bit would correspond to the water hole. Two methods for the post-processing with the drill were tested on the 20-min stoppers. For the first method, used on stoppers 1 and 2, the drill was inserted one time and it penetrated as far as it could go. In the more careful method, for stoppers 3 and 4, the drill was allowed only to enter a small bit and then taken out for cleaning: this way the drill was only cutting into new material and not heating excessive residue inside the orifice. All of the drilling should be done at the same speed and at the recommend speed for the specific machine used. Figure 1B shows the drill bits’ diameters, in millimeters, used to drill out the holes. The 6-min setting was drilled with a 1.47 mm drill bit for the air inlet and a 1.96 mm for the water outlet. The 10-min setting employed a 1.57 mm (1/16-in) drill bit for both orifices. The 20-min setting had the air inlet drilled with a 1.29 mm and a 1.57 mm (1/16-in) for the water outlet. These hole sizes and configurations were experimentally determined to approximate the target times and are summarized in Supplementary Table 3. Supplementary Figures 2–7 illustrate the iterative design steps used to prototype the final result.
Results
Figure 2 present the results of the flow rates of the 6-, 10-, and 20-min setting. Tests of the 6-min stoppers resulted with an average time of 6.28 min, 0.11 min standard deviation, and 0.018 coefficient of variation. The small standard deviation and coefficient of variation indicate that the post-processing is eliminating most of the variation is produced by the 3D printer’s inability to reproduce the same piece. Tests of the 10-min stopper resulted in with an average of time of 10.29 min, with a standard deviation of 0.23 min and a coefficient of variation of 0.022. Tests of the 20-min stoppers resulted with an average time of 19.76 min, standard deviation of 0.78 min, and coefficient of variation of 0.04. The last two stoppers also demonstrate the same response to the post-processing. It reduces the variation between each print and gives the stoppers consistent performance. This data was created using stoppers from both printers, the Fusion3 F400 and Lulzbot 5. It is apparent that regardless of where the part came from, the performance is consistent after the post-processing. To test the importance of post-printing adjustment of the hole sizes, we tested an “as-printed” 30-min design finding variation both between prints and tests. The results we obtained were an average time of 29.8 min, standard deviation of 7.59, and standard error of 2.53. The finishing step of drilling the apertures for the 6-, 10-, and 20-min stoppers resulted in consistent behavior, while the undrilled 30-min stopper gave flow rates which varied greatly between prints.

Figure 2. Table that holds the results of 30, 20, 10, and 6 min stoppers showing the performance of each.
Discussion
There was still variability in the rates even with careful drilling of all of the orifices, but it is significantly reduced compared to the stoppers that are not drilled after printing. The stoppers demonstrate average times that fall within 5% of the target time, but individual tests had a variability up to approximately 8%. It can be concluded that post-processing is needed to achieve the desired rates and that different post-processing methods such as the ones described above yield different accuracy. The results demonstrate that our targets can be approximated if the post-processing is done carefully. For this reason, the 30-min stoppers were not further developed as they require very specialized equipment to approximate the rate and it would have created a barrier to create such a device. The quality of a stopper can be attributed to the post-processing methods. If the drill is cleaned every time it is inserted, then the drilling will be cleaner as it will not be drilling excessive material as well as overheating the plastic. The results indicate that the variability of the physical object produced by the 3D printing process due to the 3D printer model, environmental conditions, slicer program, and print settings can be compensated for by careful post-processing. To obtain lower flow rates, and potentially more consistency, one could establish the water delivery tube diameter using sealed-in glass capillary tubes, which are available in a wide range of sizes.
Conclusion
Even with high performance Fused Filament Fabrication (FFF) printers, such as the Fusion3 F400, the orifice sizes do not come out to the design specification in the CAD: the resolution is not accurate enough. Drilling is the most exact way to get the results that are needed across all 3D printers. An alternate approach to the drilling process is to use reamers; they offer better consistency across the whole length of the hole because of the structure of the tool. This offers more accuracy to the hole and creates a more precise calibrator.
When the small apertures in the device were drilled post-printing, the multi-rate rain gauge calibrator performs on average within 5% of target time and can be readily modified, printed and employed in the field. The post-processing will not always yield a stopper that is within 5%; this can be attributed to the variability of the post-processing and human error. We demonstrate that without post-printing drilling, small orifices will have enough variability between prints and between printers to yield unacceptable performance. We also note that the most critical aspect of calibration of the rain gauge, that a known total volume of water is applied, is guaranteed to less than 0.1% deviation through use of a calibrated volumetric flask, purchased for this effort for under US$5 and made from high-impact polypropylene. Use and transport of this flask over 9 months in five countries has confirmed that it is amply sturdy for field use.
Author Contributions
JS contributed to the concept and design of the project. JL prototyped and validated the designs and wrote the first draft of the manuscript. JL, JS, and CU performed design revisions and contributed to the manuscript revision and read and approved the submitted version.
Funding
This work was supported by the USDA National Institute of Food and Agriculture, Hatch project NI18HFPXXXXXG055.
Conflict of Interest
The authors declare that the research was conducted in the absence of any commercial or financial relationships that could be construed as a potential conflict of interest.
Acknowledgments
The authors would like to thank the OPEnS Lab for providing the space and tools necessary to develop this project and to all members of the OPEnS Lab for all their support.
Supplementary Material
The Supplementary Material for this article can be found online at: https://www.frontiersin.org/articles/10.3389/feart.2019.00338/full#supplementary-material
Footnotes
References
Bergmann, H., Breinhalter, H., Hable, O., and Krainer, R. (2001). Calibration of tipping bucket hyetographs. Phys. Chem. Earth, Part C Solar, Terr. Planet. Sci. 26, 731–736. doi: 10.1016/S1464-1917(01)95017-2
Ciach, G. J. (2003). Local random errors in tipping-bucket rain gauge measurements. J. Atmos. Oceanic Technol. 20, 752–759. doi: 10.1175/1520-0426(2003
Fusion360 (2018). Autodesk. Available at: https://www.autodesk.in/products/fusion-360/overview#generative-design (accessed October 21, 2018).
Habib, E., Haile, A. T., Tian, Y., and Joyce, R. J. (2012). Evaluation of the high-resolution CMORPH satellite rainfall product using dense rain gauge observations and radar-based estimates. J. Hydrometeorol. 13, 1784–1798. doi: 10.1175/JHM-D-12-017.1
Humphrey, M. D., Istok, J. D., Lee, J. Y., Hevesi, J. A., and Flint, A. L. (1997). A new method for automated dynamic calibration of tipping-bucket rain gauges.” J. Atmosph. Ocean. Technol. 14:1513. doi: 10.1175/1520-0426(1997)014<1513:anmfad>2.0.co;2
Mariotte, E. (1679). Essais de Physique: ou Mémoires Pour Servir á la Science des Choses Naturelles. Paris: Chez Estienne Michallet.
Texas Electronics (2019). Field_Calibration_Device_Spec. [PDF] Dallas: Texas Electronics, p.1. Available at: https://texaselectronics.com/media/mconnect_uploadfiles/f/i/field_calibration_device_spec.pdf (accessed Oct 2, 2019).
Keywords: calibration, rain gauge, 3D printing, OPEnS lab, Mariotte bottle, computer-aided design, ABS plastic
Citation: Lopez Alcala JM, Udell CJ and Selker JS (2019) A User-Printable Three-Rate Rain Gauge Calibration System. Front. Earth Sci. 7:338. doi: 10.3389/feart.2019.00338
Received: 01 November 2018; Accepted: 02 December 2019;
Published: 17 December 2019.
Edited by:
Rolf Hut, Delft University of Technology, NetherlandsReviewed by:
Benjamin Michael Clemens Fischer, Stockholm University, SwedenWitold F. Krajewski, The University of Iowa, United States
Jan Friesen, Helmholtz Centre for Environmental Research (UFZ), Germany
Copyright © 2019 Lopez Alcala, Udell and Selker. This is an open-access article distributed under the terms of the Creative Commons Attribution License (CC BY). The use, distribution or reproduction in other forums is permitted, provided the original author(s) and the copyright owner(s) are credited and that the original publication in this journal is cited, in accordance with accepted academic practice. No use, distribution or reproduction is permitted which does not comply with these terms.
*Correspondence: John S. Selker, am9obi5zZWxrZXJAb3JlZ29uc3RhdGUuZWR1