- 1College of Environmental Science and Engineering, Tongji University, Shanghai, China
- 2Chinese Research Academy of Environmental Sciences, Beijing, China
Base-catalyzed transesterification of waste cooking oils (WCOs) into biodiesel is a widely used renewable fuel production technology. The traditional heating method for this process is electric heating (EH), while microwave-assisted heating (MW) has also received extensive attention in recent years. This study compares the two reaction processes in detail by one-way experiments and ANOVA. Catalyst content, reaction temperature (average temperature), and alcohol–oil molar ratio are key factors for these two transesterification processes. The maximum FAME yield of both EH and MW processes appeared at 1.0% catalyst concentration, with the reaction temperature around 60°C, while the MW process called for more methanol. It is speculated that the acid value of WCOs may be closely related to the time required for transesterification as well. The MW process can improve the transesterification efficiency, which is shown in kinetics as much larger than the reaction constant of the EH process and about one-tenth of the activation energy.
1 Introduction
Due to rapid population growth and economic growth in the last 2 decades, the consumption of edible oils has increased from 7,337,900 t (1999) to 50,660,000t (2018) in China (China, 2018). As waste cooking oils (WCOs) weigh approximately 25% of the total mass of edible oil production in China (Du et al., 2013), the output of WCOs can reach 12,665,000 t in 2018. WCOs are vegetable and animal oils used for food preparation and are not reusable. Pyrolysis, oxidation, and hydrolysis reaction would happen during cooking and frying (Cvengros and Cvengrosova, 2004; Maddikeri et al., 2012), in which fresh vegetable oils become WCOs, a mixture of triglycerides with saturation and serval harmful contents, such as phenols, ketones, short-chain free fatty acids, fatty acid polymers, and aflatoxins (Xingguo, 2013). WCOs could cause water and air pollution (Peiró et al., 2008). Additionally, there would be a risk of returning to the dining table to threaten human health because of the huge economic benefit [around 300% (Math et al., 2010; Bussness, 2012)].
WCOs are also renewable resources with multiple reuse pathways (Yinxia et al., 2009; fei and maiqian, 2011), and transesterification into biodiesel is becoming a key instrument in its management. In the past few years, fresh vegetable oils are commonly used raw materials for biodiesel production (Chuah et al., 2017; Putra et al., 2018). However, these materials account for about 80% cost of biodiesel production, which makes biodiesel cost a lot higher than that of fossil fuel (Ahmad Farid et al., 2017; Naylor and Higgins, 2017). This fact indicates that WCOs are an anticipated material for biodiesel production. As one of the most widely used technologies, homogeneous base catalysts—potassium, like hydroxide (KOH) and sodium hydroxide (NaOH), can produce biodiesel at a mild reaction temperature and pressure in a short time (Fadhil and Ali, 2013; Mardhiah et al., 2017; Akram, 2019; Harabi, 2019; Rajagopalachar et al., 2019). For homogeneous base-catalyzed transesterification, traditional electric heating (EH) is already sufficient for yield requirements; however, in order to further improve the reaction efficiency, a variety of strengthening methods have also been extensively studied, and microwave heating (MW) transesterification is one of them. Previous studies have demonstrated that MW can provide better thermal conductivity and convection generated in the mixture; thus, preheating of the reactants is dispensable (Milano et al., 2018a; Silitonga, 2020). Some previous practices of using KOH as a catalyst to produce biodiesel are summarized in Table 1. These data demonstrate the high efficiency of using KOH as a catalyst and that the use of MW technology can further improve the reaction efficiency.
However, due to the differences in the reaction materials, reaction conditions, and the operating level of the experimenters, the results of different studies lack contrast, and it is difficult to scientifically reflect the difference in the transesterification yields between the two processes. This study used WCOs obtained from canteens and restaurants around college as raw materials, performed single-factor experiments to examine details in the influencing factors and reaction kinetics of the two technologies, and thoroughly analyzed the advantages and disadvantages of the two comparisons.
2 Materials and Methods
2.1 Materials
The waste cooking oils used in the experiment came from a student canteen of Tongji University. To ensure the uniformity of the samples, three samples were taken from lunch, while others were taken from dinner. The collection process was continued for 7 days, from Monday to Sunday. A total of 42 samples were gathered and mixed into one WCO sample. Before starting the transesterification, the sample was filtered to remove the contaminants and water. The main processes included sieving, demulsification and extraction, liquid separation, and rotary evaporation (as demonstrated in Figure 1).
The characterization techniques were used to indicate the quality parameters of the WCOs after pretreatment. QP2010SE gas chromatography-mass spectrometer was employed to determine WCOs’ fatty acid profile. The Nicolet5700 Fourier infrared spectrometer was used to determine WCOs’ molecular structure. The physical and chemical properties were determined by titration.
Potassium hydroxide (AR) was bought from Sinopharm Chemical Reagent Co., Ltd. (China). Methanol (Sigma Aldrich-270504) and hexane (Sigma Aldrich-270504) were bought commercially from Sigma Aldrich (United States), and heptadecanoic methyl ester (GR) was purchased from Fluka (United States). High-purity nitrogen was provided by Chunyu Special Gases Co., Ltd. (Shanghai).
2.2 Transesterification Reaction
A three-necked flat-bottomed borax flask (250 ml) equipped with condensers and temperature sensors was used in both reaction vessels. A magnetic bar was put into the reactor for stirring, and the stirrer was set at 700 rpm as well. Transesterification reaction for the EH process was carried in a water-bath heating function. Oil was preheated to the specified temperature to keep the reaction temperature stable while pre-mixing methanol and KOH. Transesterification reaction for the MW process was carried under 2,450 MHz microwave radiation. Due to the high heating rate, oil and KOH-dissolved methanol were mixed into the reactor at the beginning of the reaction.
Transesterification was carried out at the fixed mixing intensity (700 rpm), varying the catalyst amount (0.5–2 wt.%), methanol/oils’ molar ratio (3:1–15:1), reaction time (5–60 min for EH and 0.5–30 min for MW), reaction temperature (50–70°C) for EH, or reaction power (50–500 W) for MW. The reacted biodiesel was immediately cooled by flowing water, then transferred to a separatory funnel and kept overnight to separate the phases by gravity.
2.4 Analytical of Biodiesel Yield
The FAME of biodiesel was determined by gas chromatography mass spectrometry (GC-MS). The detecting conditions would be as follows: HP5-MS column; injection volume 1 μl; inlet temperature 260°C; carrier gas was high-purity nitrogen, flow rated 50 ml/min, split ratio 19.9: 1; solvent was hexane. The column thermostat used a column heating program: initial temperature 70°C, held for 2 min, 10°C/min to 180°C, then 5 °C/min to 230°C, held for 10 min; detector was FID, temperature 260°C; hydrogen flow rate 25 ml/min, and air flow rate 300 ml/min. The FAME content was calculated using the internal standard method, and the analytical internal standard for quantitative determination was heptadecanoic methyl ester.
The methyl ester content in biodiesel samples was determined using the internal standard method. The results were calculated according to Eq. 1.
where C is the methyl content (%), ∑A is the total peak area, AEI is the peak area of heptadecanoic methyl ester, CEI is the concentration of heptadecanoic methyl ester in hexane (mg/L), VEI is the injection volume of heptadecanoic methyl ester solution (μl), and m is the mass of the biodiesel sample (mg).
2.5 Kinetics Study
The transesterification reaction equation can be written as Eq. 2.
The reaction rate of transesterification can be calculated according to Eqs 3, 4:
where t is the reaction time and kr represents the rate content.
In the EH process, homogeneous base-catalyzed reaction, KOH is dissolved in methanol in advance, and the effect of stirring makes the entire reaction system to be regarded as a homogeneous reaction. Since the molar concentration of methanol is much higher than the stoichiometric requirement throughout the reaction, the concentration of methanol can be regarded as a constant. Thus, the EH process can be regarded as a pseudo-first-order reaction (Ramezani et al., 2010; Zhang et al., 2010).
The rate equation for the EH process can be written as Eq. 5:
As for the MW process, it has been reported that under certain microwave power conditions, the reaction follows pseudo-second-order reaction kinetics (Yeong et al., 2019). The integrated rate equation can be written as Eq. 6.
After dividing left and right by [TG]0 at the same time, the rate equation can be expressed as Eq. 6:
The activation energy was calculated by the Arrhenius equation (Eq. 7).
Taking logarithm on both sides,
3 Results and Discussion
3.1 Characterization of the Waste Cooking Oils
The fatty acid composition and physicochemical properties of the prepared WCOs are listed in Table 2. From Table 2 https://www.sciencedirect.com/science/article/pii/S0016236120307201?via%3Dihub-t0010, it was clear that palmitic acid (C16:0), octadecanoic acid (C18:0), 9-octadecenoic acid (Z) (C18:1), linoleic acid (C18:2), and arachidic acid (C20:0) were the major fatty acids present in WCOs. The saturated fatty acid content in the WCOs was 39.64%. Compared with fresh refined vegetable oil, higher saturation of WCOs had a positive effect on the cetane number and oxidation stability of the prepared biodiesel (F. Ma et al., 1998). The acid value of WCOs was lower than the standard 1 mg KOH/g oil value required for the transesterification reaction, so the transesterification process could be directly carried out with a homogeneous base catalyst (Saka and Kusdiana, 2001).
3.2 Biodiesel Yield of the EH Process
3.2.1 Optimization of Transesterification Factors
In case of EH, the optimization of the factors included reaction temperature, reaction time, catalyst amount, and methanol/oil molar ratio. The maximum biodiesel yield obtained from the EH process was 93.45%, and the reaction conditions were 60°C, 30 min, 1 wt.% KOH, and the methanol/oil molar ratio of 6:1.
Experimental yield data were given as an input of the analysis of variance (ANOVA) in Table 3. The significant terms influencing the biodiesel yield in a decreasing order were catalyst amount, methanol/oil molar ratio, and reaction temperature. Catalyst content was the most significant influencing parameter. Anvita Sharma et al. (2021) reported that for a kind of WCOs, the catalyst weight % was the most significant process parameter for biodiesel production using catalyst loading from 0.3 to 0.7 (w/w).
Figure 2A indicated that FAME yield increased with the increase of temperature from 50 to 60°C, and further increase of temperature would reduce the biodiesel yield. Higher temperature could accelerate the reaction and shorten the reaction time by favoring the number of collisions (Ma and Hanna, 1999; Leung and Guo, 2006). In addition, the increase in the temperature decreased the viscosity of the reaction mixture, increasing alcohol–oil two-phase contact as well (Gupta and Rathod, 2018). Further increase of reaction temperature would accelerate methanol volatilization, which brought the decline of the FAME content. High temperature would promote the occurrence of saponification, which should be another important reason (Phan and Phan, 2008). For the process of preparing biodiesel by KOH-catalyzed transesterification, the common optimal reaction temperature was 60°C (Mercy Nisha Pauline et al., 2021; Yellapu et al., 2021), while the optimal catalytic temperature of another commonly used homogeneous base catalyst (NaOH) was slightly higher (Yesilyurt et al., 2019; Wongjaikham et al., 2021). Rocha J. G. (2019) reported that higher K+ adsorption in methanol–oil interface could make K-containing catalysts more active than their Na analogs. Thus, KOH is the base catalyst with the highest catalytic efficiency. When the WCOs met the process requirements, using KOH as the transesterification catalyst could maximize the production efficiency.
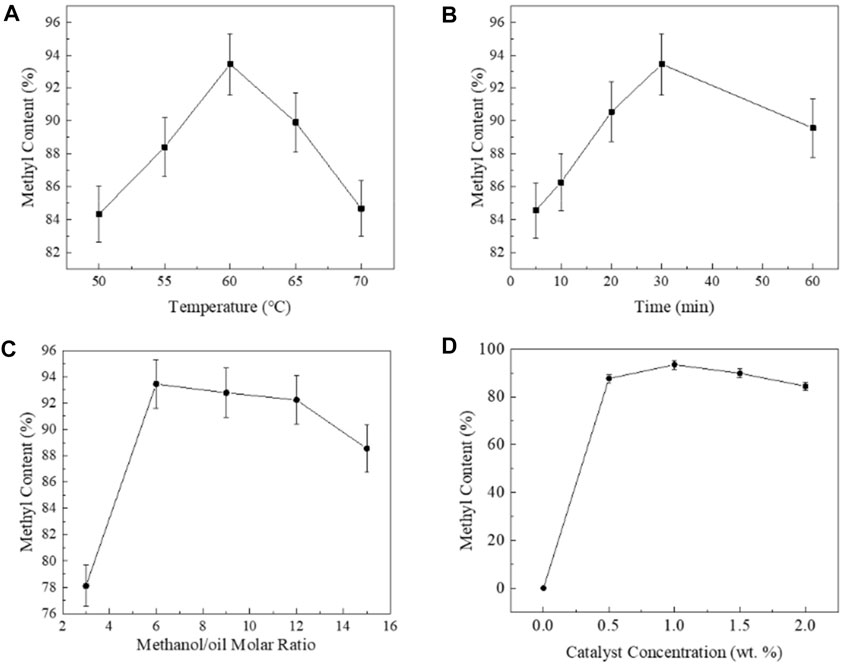
FIGURE 2. Effects of the process parameters (temperature, time, methanol/oils molar ratio, and KOH concentration). (A) Effect of temperature; (B) effect of time; (C) effect of methanol/oil molar ratio; and (D) effect of catalyst concentration.
Although reaction time had no significant effect on biodiesel yield in the time frame of 5–60 min, according to Figure 2B, the FAME yield still had a clear change rule with time. In the first 5 min, due to the large difference in the concentration of substances between the two ends of the equilibrium, the concentration of substance on the left end of the balance was much greater than that on the right end, which means the balance moved forward rapidly. However, after five minutes, the FAME yield exceeded 84%, and the process slowed down and tilled the maximum methyl content at 30 min (Figure 2B). Further increasing the reaction time from 30 to 60 min, the FAME yield would slightly decrease from 93.45% to 89.56%. Ahmad T. et al. (2019) reported a best reaction time as 33 min using flaxseed oil as feedstock. However, some optimal reaction time obtained by predecessors who used WCOs to produce biodiesel was about 60 min (Agarwal et al., 2012; Pugazhendhi, 2020). However, the optimal reaction time in the study of Uzun, B. B., et al. to produce waste frying oil biodiesel was 30 min s, as well as Abdelrahman B. Fadhil (Fadhil and Ali, 2013) used inedible oil—Silurus triostegus Heckel fish oil (STFO)—in biodiesel production, and the best reaction time of that study was 60 min. Comparing the properties of the feedstock oil used in this study and the previous studies (Table 4), it can be speculated that the increase of oleic acid ester would prolong the time required in transesterification.
When the methanol content increased from 3:1 to 15:1, the FAME yield could remain above 75% (Figure 2C). The improvement of methanol/oil molar ratio could drive the reaction process in the forward direction. In addition, with methanol content becoming higher in the system, more methanol could stay in the system with temperature increase. However, extra methanol would dissolve more glycerin (Milano et al., 2018b), while the specific surface area of methanol–oils turns less as well with more methanol (Motasemi and Ani, 2012). The maximum FAME yield of 93.45% was achieved for 6:1 methanol/oil molar ratio.
As shown in Figure 2D, the reaction would not occur without a catalyst, and lower concentration (0–0.5% w/w of oils) of KOH led to lower methyl content. The increase in the amount of catalyst brought more methoxy free radicals, increased the contact opportunities between free radicals and oils, and promoted the transesterification reaction. The maximum content of methyl ester was obtained with 1.0% KOH. An excess amount of KOH would reduce the biodiesel yield, as high KOH concentrations could cause more triglycerides being involved in the saponification reaction and bring about the formation of soap (Chhetri et al., 2008).
3.2.2 Kinetics Analysis
For the EH process, the rate constants for the transesterification reaction at different temperatures were determined by curve fitting the reaction rate equation to the biodiesel yield. Performing kinetic calculations according to 2.5, the reaction rate constant of the EH process was found to increase from 0.3479 to 0.4048 min−1. The reaction rate constant at 60°C was 0.3737. Activation energy values derived from Arrhenius plots using Eq. 8 for the EH process is shown in Figure 3. The activation energy for the EH process is found to be 6,768 J mol−1.
3.3 Biodiesel Yield of the MW Process
When the experiment was initially designed, we tried to control the reaction temperature of the microwave-assisted transesterification process by pulse switching, but we could only control the reaction temperature within the range of ±5°C. In this study, the temperature gradient of single-factor experiments was also ±5°C. Thus, the optimization factors of MW process were microwave power (instead of reaction temperature), reaction time, catalyst amount, and methanol/oil molar ratio. To illustrate the relationship between reaction temperature and methyl ester yield in the MW process, time–temperature curves (Figure 4) for the MW process were plotted, the average temperature was studied as the fifth indicator.
Experimental yield data were given as an input of the analysis of variance (ANOVA) in Table 5. According to the results, in the MW process, the significant terms influencing the biodiesel yield in the decreasing order are catalyst amount and methanol/oil molar ratio. The probability value of catalyst amount was almost the same in the EH process and MW process. This may indicate that the contact between the reactants and the catalyst is the limiting reaction for the efficiency of the transesterification reaction. Average temperature had a significant effect on FAME yield, second only to CA. Compared with the EH process, it can be speculated that for the MW process, the effect of temperature was more significant than that for the EH process.
3.3.1 Optimization of Transesterification Factors
Figure 5 showed the variation into FAME yield. The maximum biodiesel yield obtained from the MW technique is 80.66%, under the condition of 200 W, 5 min, the dosage of 1 wt.% KOH, and the methanol/oil molar ratio of 9:1. The detailed results are shown in Supplementary Table S2.
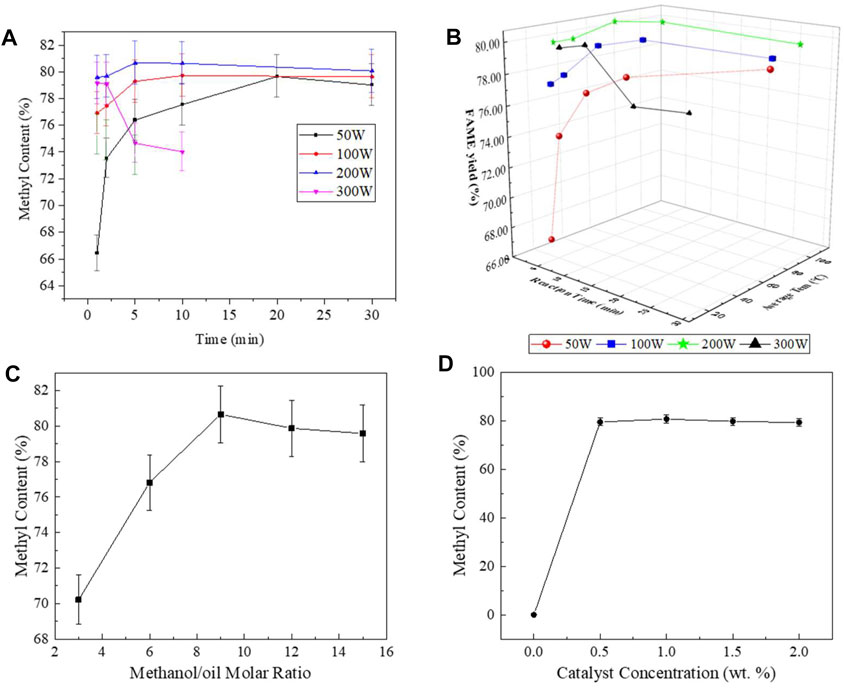
FIGURE 5. Effects of the process parameters (microwave power, time, methanol/oil molar ratio, and KOH concentration). (A) Effect of microwave power/time; (B) effect of average temperature; (C) effect of methanol/oils molar ratio; and (D) effect of catalyst concentration.
The curves of the MW process were very similar to those of the EH process, but there was difference in the value. In the microwave power range of 50–300 W, the closer the average reaction temperature is to 60°C, the higher the final FAME yield. It shows that the optimum temperature of microwave-assisted transesterification is similar to that of the EH process, about 60°C. In this study, the highest methyl ester yield was obtained when the microwave power was 200 W and the reaction time was 5 min, where the average temperature of the reaction system was 61.8°C. This was because microwave would affect dipole rotation and ion migration, and improve the thermal conductivity and convection current of the mixture (Manco et al., 2012; Sharma et al., 2021). This effect accelerated molecular level heating, which would sustainably reduce the reaction time. At the same time, the amount of methanol required in the MW process was higher. When molecular level heating accelerated, methanol in the system heated up rapidly, becoming a “hot spot” in the reaction system, and rapidly evaporated above its boiling point, causing the methanol concentration of the reaction system to drop, resulting in an increased methanol content requirement for methanol. As well, continuous microwave heating may make the methanol volatilization efficiency in the reaction system much greater than the reflux efficiency. This results in a decrease in the maximum methyl ester yield of the MW process; in this study, it was significantly smaller than that of the EH process. The actual optimal microwave conditions may need to further prolong the reaction time and increase the methanol required.
The optimal KOH content for both reactions was 1% by mass. With the increase of KOH dosage to 2%, the yield of FAME decreased slightly, and finally stabilized at about 80%. For the MW process, the biodiesel yield did not change significantly when the catalyst content increased from 0.5% to 2%. This microwave-assisted heating can increase the mass transfer efficiency of the oil–KOH–methanol two-phase interface, which can reduce the need for catalysts in applications.
3.3.2 Kinetics Analysis
The reaction rate constant at 200 W was 9.247 min−1. It is worth noting that the reaction rate constant of the MW process reached the maximum when the microwave power was 300 W, and decreased at 500 W. The k value was approximately 10–20 times higher in the MW process than that of EH. Activation energy values derived from Arrhenius plots using Eq. 8 are shown in Figure 6. The activation energy of the MW process was found to be 503.4 J mol−1. Microwave heating greatly reduced the activation energy of the reaction.
4 Conclusion
In this study, the influencing factors and effects of base-catalyzed transesterification of WCOs under EH and MW processes were systematically compared, and the specific conclusions are listed as follows.
For the EH process, within the range of experiment performed, temperature, methanol/oil molar ratio, and catalyst weight %, all have effect on the FAME yield, while the latter two have greater impact. The maximum FAME yield of the EH process appeared at the reaction temperature of 60°C, the molar ratio of alcohol to oil is 6:1, and the catalyst concentration is 1.0%, and then reaches 93.4%. The optimal reaction conditions obtained in this study are similar to those of previous studies. By comparing the oil properties of the optimal reaction time of 30 and 60 min, it is known that the increase in the acid value of WCOs may prolong the transesterification reaction time and reduce the production efficiency of biodiesel. The acid value of WCOs used in this study was only 0.4, and the optimal time required was 30 min.
One-way analysis of variance results showed that the biodiesel yield was witnessed to be very sensitive to the methanol/oil molar ratio, average temperature, and catalyst weight % for the MW process. Moreover, the effect of temperature on the transesterification process is more significant than that in the EH process. The maximum biodiesel yield obtained from the MW technique is 80.66%, under the condition of 200 W, 5 min, 1 wt. % KOH, and the methanol/oil molar ratio of 9:1. Its average temperature is 61.8°C. Compared with the EH process, microwave heating would not lower the required reaction temperature. But it can greatly shorten the time required for the reaction and improve the transesterification efficiency. Continuous microwave heating will aggravate methanol evaporation and may reduce the yield of methyl ester.
The activation energy of EH and MW were, respectively, determined by the pseudo-first-order kinetic modeling and pseudo-second-order kinetic modeling. The activation energy for EH and MW processes are found to be 6,768 and 503.4 J mol−1, respectively. Microwave heating greatly reduced the activation energy of the reaction.
On 21 May 2021, the State Administration for Market Supervision and Administration of China and the National Standardization Management Committee issued GB/T 40133-2021 Technical Requirements for Recycling and Further Processing of Waste Cooking Oil from restaurants. This standard makes corresponding provisions on the separation and recovery technology of WCOs, and takes the acid value of WCOs not greater than 2 mg (KOH)*g-1 as the property requirement for the production of biodiesel using strong base catalysis, which provides the necessary conditions for subsequent research and application. In the follow-up research, it is necessary to rely on industry standards to further clarify the influencing factors of the biodiesel production process, the cost consumption, and environmental impact on the process, and to improve the application value of the research.
Data Availability Statement
The original contributions presented in the study are included in the article/Supplementary Material, further inquiries can be directed to the corresponding author.
Author Contributions
WJL, GML, FW, HCZ, WZH, and JWH, contributed to the study conception and design. Material preparation, data collection, and analysis were performed by WJL, GML, FW. The first draft of the manuscript was written by WJL, and all authors commented on previous versions of the manuscript. All authors have read and approved the final manuscript.
Funding
The works were financially supported by the Key Project in the National Science and Technology Pillar Program in China (grant number: 2010BAK69B24).
Conflict of Interest
The authors declare that the research was conducted in the absence of any commercial or financial relationships that could be construed as a potential conflict of interest.
Publisher’s Note
All claims expressed in this article are solely those of the authors and do not necessarily represent those of their affiliated organizations, or those of the publisher, the editors and the reviewers. Any product that may be evaluated in this article, or claim that may be made by its manufacturer, is not guaranteed or endorsed by the publisher.
Supplementary Material
The Supplementary Material for this article can be found online at: https://www.frontiersin.org/articles/10.3389/fenvs.2022.885453/full#supplementary-material
References
Agarwal, M., Chauhan, G., Chaurasia, S. P., and Singh, K. (2012). Study of Catalytic Behavior of KOH as Homogeneous and Heterogeneous Catalyst for Biodiesel Production. J. Taiwan Inst. Chem. Eng. 43 (1), 89–94. doi:10.1016/j.jtice.2011.06.003
Ahmad Farid, M. A., Hassan, M. A., Taufiq-Yap, Y. H., Ibrahim, M. L., Othman, M. R., Ali, A. A. M., et al. (2017). Production of Methyl Esters from Waste Cooking Oil Using a Heterogeneous Biomass-Based Catalyst. Renew. Energ. 114, 638–643. doi:10.1016/j.renene.2017.07.064
Ahmad, T., Danish, M., Kale, P., Geremew, B., Adeloju, S. B., Nizami, M., et al. (2019). Optimization of Process Variables for Biodiesel Production by Transesterification of Flaxseed Oil and Produced Biodiesel Characterizations. Renew. Energ. 139, 1272–1280. doi:10.1016/j.renene.2019.03.036
Akram, W. (2019). Experimental Studies on Performance and Exhaust Emission Characteristics of a Diesel Engine Fuelled with Diesel-Linseed Oil Methyl Ester (LOME) Blends. Energy Sources Part a-Recovery Utilization and Environmental Effects.
Bussness, S. (2012). Gutter Oil Profit Chain Revealed: Up to 300%. Available at: http://business.sohu.com/20120905/n352362645.shtml.
Chhetri, A., Watts, K., and Islam, M. (2008). Waste Cooking Oil as an Alternate Feedstock for Biodiesel Production. Energies 1 (1), 3–18. doi:10.3390/en1010003
Chuah, L. F., Klemeš, J. J., Yusup, S., Bokhari, A., and Akbar, M. M. (2017). A Review of Cleaner Intensification Technologies in Biodiesel Production. J. Clean. Prod. 146, 181–193. doi:10.1016/j.jclepro.2016.05.017
Cvengros, J., and Cvengrosova, Z. (2004). Used Frying Oils and Fats and Their Utilization in the Production of Methyl Esters of Higher Fatty Acids. Biomass & Bioenergy 27 (2), 173–181.
Du, Z., Tang, Z., Wang, H., Zeng, J., Chen, Y., and Min, E. (2013). Research and Development of a Sub-critical Methanol Alcoholysis Process for Producing Biodiesel Using Waste Oils and Fats. Chin. J. Catal. 34 (1), 101–115. doi:10.1016/s1872-2067(11)60490-7
Fadhil, A. B., and Ali, L. H. (2013). Alkaline-catalyzed Transesterification of Silurus Triostegus Heckel Fish Oil: Optimization of Transesterification Parameters. Renew. Energ. 60, 481–488. doi:10.1016/j.renene.2013.04.018
fei, z., and maiqian, n. (2011). Study on the Production of Single Cell Protein by Discarded Edible Oils and Fats. Ecotechnology 17 (3), 1–4.
F. Ma, F., L. D. Clements, L. D., and M. A. Hanna, M. A. (1998). The Effects of Catalyst, Free Fatty Acids, and Water on Transesterification of Beef Tallow. Trans. Asae 41 (5), 1261–1264. doi:10.13031/2013.17292
Gupta, A. R., and Rathod, V. K. (2018). Waste Cooking Oil and Waste Chicken Eggshells Derived Solid Base Catalyst for the Biodiesel Production: Optimization and Kinetics. Waste Manage. 79, 169–178. doi:10.1016/j.wasman.2018.07.022
Harabi, M. (2019). Biodiesel and Crude Glycerol from Waste Frying Oil: Production, Characterization and Evaluation of Biodiesel Oxidative Stability with Diesel Blends. Sustainability 11 (7). doi:10.3390/su11071937
Leung, D. Y. C., and Guo, Y. (2006). Transesterification of Neat and Used Frying Oil: Optimization for Biodiesel Production. Fuel Process. Techn. 87 (10), 883–890. doi:10.1016/j.fuproc.2006.06.003
Ma, F., and Hanna, M. A. (1999). Biodiesel Production: a review1Journal Series #12109, Agricultural Research Division, Institute of Agriculture and Natural Resources, University of Nebraska-Lincoln.1. Bioresour. Techn. 70 (1), 1–15. doi:10.1016/s0960-8524(99)00025-5
Maddikeri, G. L., Pandit, A. B., and Gogate, P. R. (2012). Intensification Approaches for Biodiesel Synthesis from Waste Cooking Oil: A Review. Ind. Eng. Chem. Res. 51 (45), 14610–14628. doi:10.1021/ie301675j
Manco, I., Giordani, L., Vaccari, V., and Oddone, M. (2012). Microwave Technology for the Biodiesel Production: Analytical Assessments. Fuel 95 (1), 108–112. doi:10.1016/j.fuel.2011.09.047
Mardhiah, H. H., Ong, H. C., Masjuki, H. H., Lim, S., and Lee, H. V. (2017). A Review on Latest Developments and Future Prospects of Heterogeneous Catalyst in Biodiesel Production from Non-edible Oils. Renew. Sustain. Energ. Rev. 67, 1225–1236. doi:10.1016/j.rser.2016.09.036
Math, M. C., Kumar, S. P., and Chetty, S. V. (2010). Technologies for Biodiesel Production from Used Cooking Oil - A Review. Energ. Sustain. Dev. 14 (4), 339–345. doi:10.1016/j.esd.2010.08.001
Mercy Nisha Pauline, J., Sivaramakrishnan, R., Pugazhendhi, A., Anbarasan, T., and Achary, A. (2021). Transesterification Kinetics of Waste Cooking Oil and its Diesel Engine Performance. Fuel 285, 119108. doi:10.1016/j.fuel.2020.119108
Milano, J., Ong, H. C., Masjuki, H. H., Silitonga, A. S., Chen, W.-H., Kusumo, F., et al. (2018). Optimization of Biodiesel Production by Microwave Irradiation-Assisted Transesterification for Waste Cooking Oil-Calophyllum Inophyllum Oil via Response Surface Methodology. Energ. Convers. Manage. 158 (FEB), 400–415. doi:10.1016/j.enconman.2017.12.027
Milano, J., Ong, H. C., Masjuki, H. H., Silitonga, A. S., Kusumo, F., Dharma, S., et al. (2018). Physicochemical Property Enhancement of Biodiesel Synthesis from Hybrid Feedstocks of Waste Cooking Vegetable Oil and Beauty Leaf Oil through Optimized Alkaline-Catalysed Transesterification. Waste Manage. 80, 435–449. doi:10.1016/j.wasman.2018.09.005
Motasemi, F., and Ani, F. N. (2012). A Review on Microwave-Assisted Production of Biodiesel. Renew. Sustain. Energ. Rev. 16 (7), 4719–4733. doi:10.1016/j.rser.2012.03.069
Naylor, R. L., and Higgins, M. M. (2017). The Political Economy of Biodiesel in an Era of Low Oil Prices. Renew. Sustain. Energ. Rev. 77, 695–705. doi:10.1016/j.rser.2017.04.026
Peiró, L. T., Méndez, G. V., and Durany, X. G. i. (2008). Exergy Analysis of Integrated Waste Management in the Recovery and Recycling of Used Cooking Oils. Environ. Sci. Technol. 42 (13), 4977–4981. doi:10.1021/es071972a
Phan, A. N., and Phan, T. M. (2008). Biodiesel Production from Waste Cooking Oils. Fuel 87 (17-18), 3490–3496. doi:10.1016/j.fuel.2008.07.008
Pugazhendhi, A. (2020). Optimization, Kinetic and Thermodynamic Studies on Sustainable Biodiesel Production from Waste Cooking Oil: An Indian Perspective. Fuel, 273.
Putra, M. D., Irawan, C., Udiantoro, , Ristianingsih, Y., and Nata, I. F. (2018). A Cleaner Process for Biodiesel Production from Waste Cooking Oil Using Waste Materials as a Heterogeneous Catalyst and its Kinetic Study. J. Clean. Prod. 195, 1249–1258. doi:10.1016/j.jclepro.2018.06.010
Rajagopalachar, S., Joshi, S. S., and Reddy, R. P. (2019). Biodiesel Synthesis from Garcinia Gummi-Gutta (L. Robson) Seed Oil: Fuel Feasibility Evaluation of a Novel Feedstock by Homogeneous and Heterogeneous Transesterification. Biofuels 10 (3), 403–410. doi:10.1080/17597269.2017.1306681
Ramezani, K., Rowshanzamir, S., and Eikani, M. H. (2010). Castor Oil Transesterification Reaction: A Kinetic Study and Optimization of Parameters. Energy 35 (10), 4142–4148. doi:10.1016/j.energy.2010.06.034
Rocha, J. G. (2019). Biodiesel Synthesis: Influence of Alkaline Catalysts in Methanol-Oil Dispersion. J. Braz. Chem. Soc. 30 (2), 342–349.
Saka, S., and Kusdiana, D. (2001). Biodiesel Fuel from Rapeseed Oil as Prepared in Supercritical Methanol. Fuel 80 (2), 225–231. doi:10.1016/s0016-2361(00)00083-1
Sharma, A., Kodgire, P., and Singh Kachhwaha, S. (2021). An Experimental Investigation of the Performance of Biodiesel Production Techniques: Optimization, Kinetics, and Energy Analysis. Therm. Sci. Eng. Prog. 22, 100842. doi:10.1016/j.tsep.2021.100842
Silitonga, A. S. (2020). Biodiesel Synthesis from Ceiba Pentandra Oil by Microwave Irradiation-Assisted Transesterification: ELM Modeling and Optimization. Renewable Energy, 146.
Uzun, B. B., Kılıç, M., Özbay, N., Pütün, A. E., and Pütün, E. (2012). Biodiesel Production from Waste Frying Oils: Optimization of Reaction Parameters and Determination of Fuel Properties. Energy 44 (1), 347–351. doi:10.1016/j.energy.2012.06.024
Wongjaikham, W., Wongsawaeng, D., Ratnitsai, V., Kamjam, M., Ngaosuwan, K., Kiatkittipong, W., et al. (2021). Low-cost Alternative Biodiesel Production Apparatus Based on Household Food Blender for Continuous Biodiesel Production for Small Communities. Sci. Rep. 11 (1), 13827. doi:10.1038/s41598-021-93225-5
Yellapu, S. K., Kaur, R., and Tyagi, R. D. (2021). Oil Extraction from Scum and Ex Situ Transesterification to Biodiesel. Biofuels 12 (6), 715–722. doi:10.1080/17597269.2018.1532753
Yeong, S. P., Law, M. C., You, K. Y., Chan, Y. S., and Lee, V. C.-C. (2019). A Coupled electromagnetic-thermal-fluid-kinetic Model for Microwave-Assisted Production of Palm Fatty Acid Distillate Biodiesel. Appl. Energ. 237, 457–475. doi:10.1016/j.apenergy.2019.01.052
Yesilyurt, M. K., Arslan, M., and Eryilmaz, T. (2019). Application of Response Surface Methodology for the Optimization of Biodiesel Production from Yellow Mustard (Sinapis alba L.) Seed Oil. Int. J. Green Energ. 16 (1), 60–71. doi:10.1080/15435075.2018.1532431
Yinxia, Q., Jian, C., and Changhai, L. (2009). Advances in the Production of Single Cell Proteins by Fermentation Using Waste Resources. Food industry Technol. 5, 366–369.
Keywords: electric heating, microwave heating, kinetic analysis, significant analysis, WCOs, biodiesel
Citation: Li W, Li G, Wang F, Zhu H, He W and Huang J (2022) Optimization and Comparison of Biodiesel Production Process by Electric Heating and Microwave-Assisted Heating Transesterification for Waste Cooking Oil via One-Way Experiments and ANOVA. Front. Environ. Sci. 10:885453. doi: 10.3389/fenvs.2022.885453
Received: 28 February 2022; Accepted: 21 March 2022;
Published: 26 April 2022.
Edited by:
Gagan Deep Sharma, Guru Gobind Singh Indraprastha University, IndiaReviewed by:
Amar Rao, Shoolini University of Biotechnology and Management Sciences, IndiaSanjeet Singh, Chandigarh University, India
Copyright © 2022 Li, Li, Wang, Zhu, He and Huang. This is an open-access article distributed under the terms of the Creative Commons Attribution License (CC BY). The use, distribution or reproduction in other forums is permitted, provided the original author(s) and the copyright owner(s) are credited and that the original publication in this journal is cited, in accordance with accepted academic practice. No use, distribution or reproduction is permitted which does not comply with these terms.
*Correspondence: Guangming Li, bGlnbUB0b25namkuZWR1LmNu