- 1School of Civil Engineering, Lanzhou University of Technology, Lanzhou, China
- 2Gansu Lanzhou Geophysics National Observation and Research Station, China Earthquake Administration, Lanzhou, China
- 3Lanzhou Institute of Seismology, China Earthquake Administration, Lanzhou, China
This study systematically examines the influence of joints on the mechanical properties of loess, highlighting the impact of joint dip angles on soil deformation and failure mechanisms. By employing an innovative layered compaction method to prepare jointed specimens, and conducting comparative experiments with different simulation materials (wax paper, rice paper, and plastic film), a series of controlled indoor triaxial compression tests were performed. The key findings are as follows: (1) The joint dip angle plays a decisive role in the evolution of failure mode, with five typical failure mechanisms identified based on fracture characteristics: shear failure, sliding failure, conjugate shear failure, sliding-shear failure, and sliding-conjugate shear failure. (2) The weakening effect of joints exhibits confining pressure dependency: Under low confining pressure (50 kPa), jointed specimens demonstrate increased axial displacement and a reduced shear strength attenuation ratio. (3) Mechanical parameters are significantly influenced by the dip angle: When the joint dip angle falls within the critical dip range of 60°–75°, both cohesion and internal friction angle reach their minimum values, forming zones of weakened mechanical properties. (4) A comparative analysis of simulation materials indicates that single-layer rice paper, due to its optimal thickness and tensile strength, effectively replicates the contact behavior of natural joint surfaces. This study establishes the quantitative relationship between joint geometric parameters and mechanical responses, providing an experimental basis for the engineering geological assessment of loess.
1 Introduction
The study of loess strength has a long-standing academic tradition; however, research on the influence of joint systems on the mechanical properties of loess remains fragmented, lacking a systematic research framework. Notably, existing studies predominantly focus on vertical joints formed by soil swelling and shrinkage, while the controlling role of tectonic joints—developed under tectonic stress fields—on soil strength characteristics has been largely overlooked. This cognitive gap has contributed to structural damage in numerous engineering applications. In 1958, Sun Guangzhong and his team Sun (1988) first identified the presence of tectonic joint networks within the ancient loess layers of Northwest China through systematic field observations, pioneering the recognition of tectonic joints as integral components of loess structural systems. Building on this foundation, Zhong (1983) experimentally validated the formation mechanisms of tectonic joints, demonstrating that X-shaped conjugate shear joint systems with dip angles of 60°–70° readily develop in loess under low moisture content conditions. This finding was further corroborated by Kang Chenyun′s research group through multidisciplinary approaches, including field surveys, statistical analyses, and topological modeling (Kang et al., 2019). Additionally, Wang Jingming and his colleagues systematically established the critical role of tectonic joints in geohazard development, landform evolution, and soil erosion processes through large-scale geological investigations and statistical analyses (Wang et al., 1994; Wang and Wang, 1994; Wang and Zhang, 1985). Extensive empirical studies have demonstrated that tectonic joints exhibit distinct spatial development patterns within loess strata. Investigating their correlation with engineering soil strength parameters has become a critical scientific challenge in geotechnical engineering. A comprehensive understanding of the influence of joints on the strength characteristics of loess is essential, offering both significant theoretical insights and practical engineering applications.
This article systematically reviews the research progress on the strength characteristics of loess containing structural joints. Current studies primarily utilize artificially pre-fabricated joint specimens for indoor direct shear testing. In terms of experimental method innovation, statistical investigations and theoretical analyses have confirmed that the loess joint network serves as the structural foundation for the formation of ground fissures. Through artificial simulation techniques, researchers have successfully reproduced the evolution of structural rupture surfaces, with crack dip angles predominantly ranging between 50° and 60° (Peng et al., 2007; Peng et al., 2008; Peng et al., 2020). Regarding specimen preparation, Wang Zhen et al. pioneered a comparative testing approach that contrasts artificially pre-fabricated joints with intact loess specimens, revealing the influence of vertical joints on the mechanical properties of loess through direct shear tests (Wang, 2017; Liu et al., 2017a; Liu et al., 2017b; Liu et al., 2020; Fang, 2010; Cheng et al., 2017). The Luo Yang research group further advanced a dual-mode preparation process: employing precision cutting with serrated saw blades combined with fine sandpaper to produce smooth joint surfaces, while utilizing irregular wire saw cutting on intact soil to create rough joint surfaces (Luo, 2014; Wang et al., 2013; Bai and Han, 2011; Zhu et al., 2021). Their study systematically demonstrated the coupling effects of dry density, moisture content, and joint surface morphology on cohesion and internal friction angle. Their research notably highlighted that when the joint dip angle approaches the inherent shear rupture angle of loess (approximately 60°), the sample exhibits the lowest strength indicators and the highest susceptibility to failure. In the field of innovative simulation materials, researchers have developed a joint surface simulation technique based on single-layer tissue paper, establishing a quantitative relationship model between joint dip angle, moisture content, and failure mode through a combination of unconfined compression and direct shear tests (Yu, 2020; Wang et al., 2021; Wang et al., 2021). Experimental results indicated that under a joint dip angle of 60°, the sample not only exhibited typical tensile crack failure characteristics but also corresponded to the critical state of maximum failure extent at the back edge of the slope. In the application of numerical simulation techniques, Liu Li et al. constructed a discrete element model of jointed loess, revealing the controlling effect of joint dip angle on mechanical responses through parametric analysis. Their findings demonstrated that when the joint orientation aligns with the potential shear plane, the sample’s bearing capacity sharply declines, and rupture surface development becomes most pronounced, reaching the extreme state of mechanical performance degradation (Liu, 2007; Jia et al., 2011). This research particularly emphasized that the influence of oblique joints on slope stability is significantly greater than that of vertical joints, providing a theoretical foundation for engineering protection and stability assessment.
In summary, this study aims to advance research on the mechanical properties of loess samples containing structural joints by addressing two key aspects. First, the optimization of the testing method. While the traditional direct shear test offers operational simplicity, it has inherent limitations: (1) the instrument imposes constraints on shear plane positioning, preventing failure along the sample’s natural weak plane; (2) uneven stress distribution during shearing leads to significant stress concentration; and (3) systematic deviations occur in the calculation of shear strength parameters. Although the unconfined compressive test improves shear plane positioning, its principal stress state (σ2 = σ3 = 0) deviates significantly from the actual stress conditions of natural soil. To overcome these limitations, this study employs the triaxial compression test, which offers several advantages: (1) precise control of the three-dimensional stress state, ensuring conditions closer to engineering reality; (2) the ability to allow failure surfaces to develop naturally along the true weak plane; and (3) the provision of a more reliable stress-strain relationship curve. Second, innovation in joint simulation techniques. Existing sample preparation methods often rely on manual cutting, which presents two major technical challenges: (1) the process is complex and inefficient, limiting the feasibility of large-scale testing; and (2) the geometric parameters of the joint surfaces exhibit high variability, reducing test reproducibility. To address these challenges, this study builds upon the loess joint simulation technology developed by Yu Yifan et al. and introduces the following key innovations: (1) optimizing the joint simulation medium through material mechanical parameter matching tests to enhance accuracy and reliability; and (2) developing standardized sample preparation molds to achieve precise control over critical parameters, including joint dip angle and surface roughness. Furthermore, by referencing strength theories and stress-strain relationship research on rock mass joints (Barton and Bandis, 1985; Gerrardc, 1986; Goodman, 1980; Barton and Choubey, 1977; Liu et al., 2016), this study proposes the most suitable methods and materials for simulating loess joints. The research also systematically examines the influence of structural joint dip angles on the mechanical behavior of loess, providing a refined theoretical framework for geotechnical engineering applications.
2 Field investigation
Extensive research has been conducted on the impact of tectonic joints on the stability of loess slopes under seismic action (Trifunac and Hudson, 1971; Shakal et al., 1988; Shakal et al., 2015), revealing that the correlation between a site’s seismic response patterns and its intrinsic properties diminishes under strong earthquake action (Borcherdt, 1970; Borcherdt and Glassmoyer, 1992; Robert et al., 1991; Hartzell et al., 1996). Moreover, loess exhibits pronounced nonlinear behavior (Arango and Seed, 1974; David and Keefer, 1984), which further complicates its mechanical response to seismic loading. This study conducts a systematic field investigation of loess tectonic joints induced by seismic activity, with the details outlined below.
Weixin Township and Yongguang Village in Min County, Dingxi City, Gansu Province, are located approximately 47 km apart, situated within the transitional zone between the northeastern edge of the Qinghai-Tibet Plateau and the Loess Plateau. The geological setting of this region is highly complex, shaped by multiple phases of tectonic activity. The basement strata primarily consist of slate, schist, and metamorphic sandstone, interspersed with localized limestone lens bodies. The central section comprises sandstone, shale, and minor conglomerate deposits, distributed along the wings of regional fold belts, indicative of a continental fluvial-lacustrine sedimentary environment. The uppermost strata are dominated by aeolian loess, including Malan loess and Lishi loess, with thicknesses ranging from several meters to several tens of meters, characterized by well-developed vertical joints (Gansu Provincial Bureau of Geology and Mineral Resources, 1989). On 22 July 2013, a magnitude 6.6 earthquake in Min County triggered extensive landslides in Baozi Village and Yongguang Village, exposing a typical X-type conjugate shear joint system (See Figures 1a,b). The first-phase joints exhibit an inclination of approximately 81°, forming near-vertical joint sets that develop in parallel at regular intervals, extending stably with distinct planar features. The second-phase joints, inclined at approximately 30° and 130°, inherit the structural framework of earlier formations, displaying smooth, unfilled joint surfaces with stable occurrences. Due to weathering and the overlying soil layers, the extension distance of the joints cannot be observed; however, the extension direction remains relatively stable, without any noticeable bends or curves.
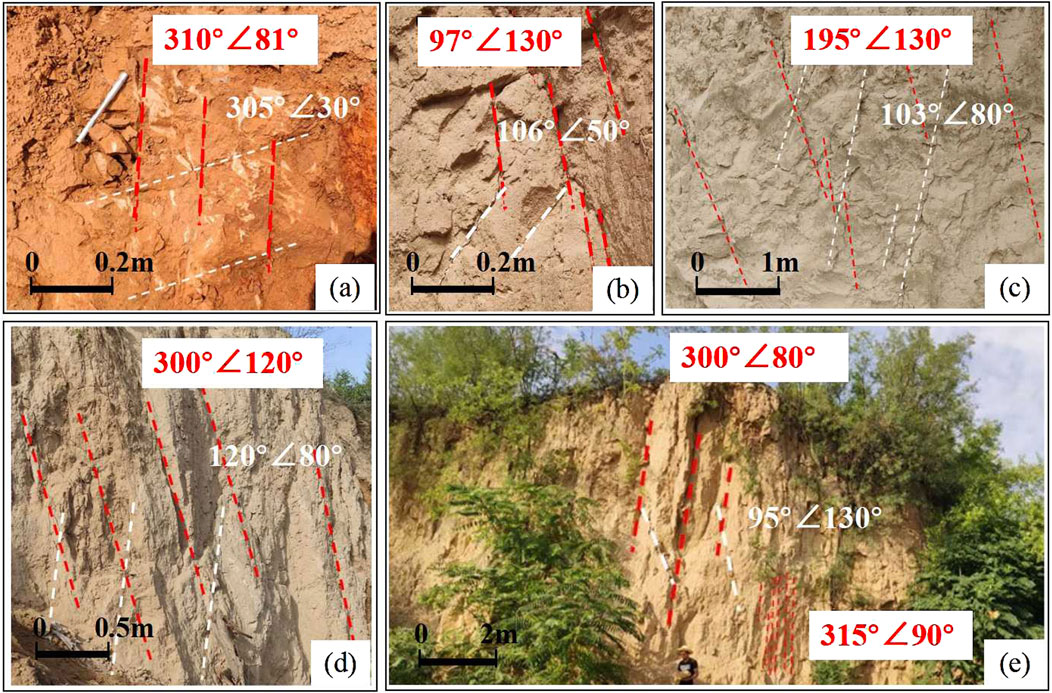
Figure 1. Field characterization of tectonic joints in Quaternary loess strata (Photo taken by Yu Yifan). (a) Baozi village; (b) Yongguang village; (c) Bijia mountain; (d) Zaoling township; (e) Xunbao village.
The Gangu County landslide (Tianshui City, Gansu Province) is situated at the tectonic transition zone between the northwestern Loess Plateau and the West Qinling orogenic belt. The region features a complex geological background, primarily composed of Quaternary loess deposits overlying Cenozoic and Mesozoic bedrock. On 19 June 1718, a magnitude 7.5 earthquake in Tongwei triggered a landslide at Bijiashan, where typical earthquake-induced X-type joints developed at the rear of the landslide. These joints exhibit parallel alignment, with an inclination of approximately 80°, an average spacing of 1 m, and no fillings on the joint surfaces. The joints remain in a closed state, displaying strong extension and continuity. A secondary joint set, inclined at approximately 130°, also develops parallel to the first, with an average spacing of about 1.5 m. The joint surfaces are closed, with no fillings, demonstrating strong extension and continuity, without interruptions between the joints. Some joints are constrained by earlier formations, terminating at previous joints, while others cut through earlier joints and extend forward (See Figure 1c).
Xiangning County in Linfen City, Shanxi Province, is situated in the middle reaches of the Yellow River and the southern section of the Lüliang Mountains, at the eastern edge of the Ordos Basin. The region’s geological background exhibits typical composite features of the Loess Plateau and tectonic activity zones. On 15 March 2019, a landslide in Zaoling Township was triggered by the combined effects of gravity and groundwater. X-type joints developed on the landslide sidewall, with the first set of joints inclined at approximately 80°, arranged in parallel at equal intervals with a spacing of about 50 cm. The joint surfaces are smooth and exhibit strong continuity. The second set of joints, inclined at approximately 120°, also developed in parallel, with a spacing of about 45 cm. These joints lack material fillings and have relatively smooth surfaces, remaining in a closed state and displaying a linear overall appearance, with misalignment observed in the middle of the joints (See Figure 1d).
Hongtong County in Linfen City, Shanxi Province, is located at the northern end of the Linfen Basin, in the western part of the North China platform and the southern section of the Shanxi graben system. The region′s geological background displays typical characteristics of a Shanxi fault basin, with well-developed strata and significant tectonic activity. On 17 September 1303, a magnitude 8.0 earthquake in Hongtong triggered a landslide in Xunbao Village, exposing three distinct groups of characteristic joints. The conjugate shear joint system consists of two contemporaneously developed X-type joints that cut through each other. The first group of joints has an inclination of approximately 80° with a spacing of about 120 cm. The joint surfaces are smooth and exhibit good extensibility, with no interruptions during their extension. The second group of joints, inclined at approximately 130°, is less densely developed (with only two visible joints), limited by vegetation cover, and has a shorter extension direction. The third group consists of a dense joint zone where, under the combined influences of earthquakes, regional tectonic stress fields, and geological structural actions, rock and soil layers are mutually compressed and fractured, resulting in localized fragmentation. Under tectonic stress, this leads to the extension and development of numerous densely formed joints, creating a joint-dense zone with an inclination near vertical (90°). This zone features a fracture cluster (more than 30 joints within an area of 2 × 3 m2), minimal spacing, and generally straight development, although some joints exhibit a wavy appearance (See Figure 1e).
3 Experimental program: research methods and data sources
3.1 Experimental equipment
This experiment was primarily conducted using a triaxial shear apparatus at the Key Laboratory of Loess Earthquake Engineering, China Earthquake Administration (as shown in Figure 2). The apparatus is designed to determine both the total shear strength and effective shear strength parameters of soil, with a maximum output capacity of 2,500 kg and a strain rate range from 0.0024 mm/min to 6 mm/min. It offers 25 mechanical speed settings and supports three sample sizes: Φ39.1 × 80 mm, Φ61.8 × 150 mm, and Φ101 × 200 mm. In this experiment, a strain-controlled loading method was applied with a loading rate of 0.6 mm/min, and the test was terminated once the strain reached 15%. The confining pressures for the triaxial tests were set at 50 kPa, 100 kPa, and 150 kPa.
At present, the necessary toolset for creating X-shaped shear joints has not yet been developed. Therefore, the sample preparation equipment used in this study was primarily an improved version of the original triaxial sample preparation device (Figure 3), designed to simulate a single joint. By replacing the base with different angles during the sample preparation process, we successfully fabricated samples with various joint inclinations, thereby enhancing the efficiency of sample preparation. Due to existing limitations, this experiment designed and manufactured a total of 10 bases with specific angles of 0°, 25°, 30°, 35°, 45°, 55°, 60°, 65°, 75°, and 90°.
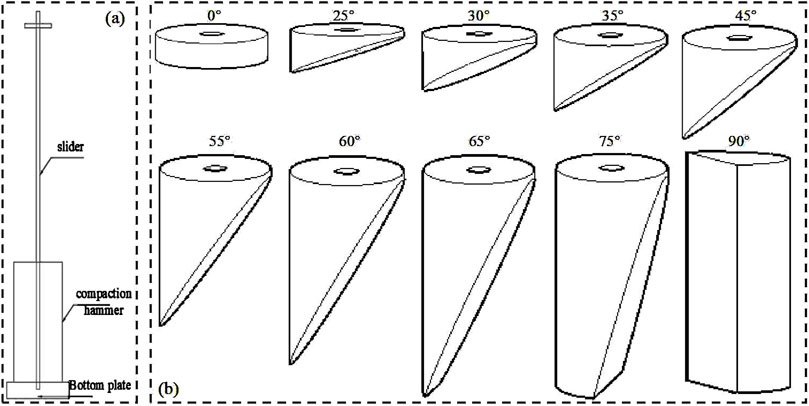
Figure 3. Sample preparation equipment. (a) Compaction device. (b) Bottom plate with different angles.
3.2 Material properties
The loess samples used in this experiment were collected from the landslide scarp in Yongguang Village, Minxian County, Dingxi City, Gansu Province. The soil exhibits a yellowish-brown color with a densely structured texture, containing insect burrows and root channels. The natural moisture content is 6%, the natural density is 1.48 g/cm3, and the maximum dry density is 1.68 g/cm3. The fundamental physical parameters of the loess samples are summarized in Table 1.
Based on the characteristics of joints—such as good continuity, well-defined planar surfaces, extended length, and moderate strength—as well as insights from our preliminary research and previous studies, this study selected three materials for simulating loess joints: single-layer paper, single-layer paper with a mesh pattern (created by cutting evenly spaced strips into the central part), and single-layer rice paper (see Figure 4). Two distinct sample preparation methods were employed to achieve joint simulation.
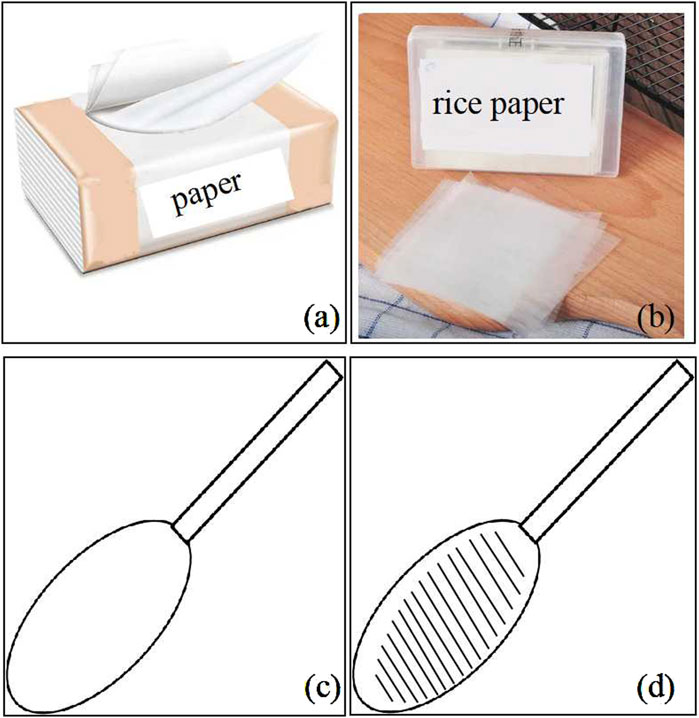
Figure 4. Different simulation materials and cutting styles. (a) Paper. (b) Rice paper. (c) Single layer joint material cutting. (d) Mesh joint material cutting.
3.3 Sample preparation
The loess material was sourced from the sidewall of the Yongguang Village landslide, then crushed, oven-dried, and sieved through a 0.75 mm mesh to eliminate impurities. The soil was subsequently mixed to a moisture content of 6% and compacted into cylindrical samples with an outer diameter of 39.1 mm, a height of 80 mm, and a density of 1.48 g/cm3. Samples with varying joint inclinations were prepared for subsequent testing.
During sample preparation, adjustments were made to the compaction mold base, simulated joint materials, and preparation methods to produce loess samples with varying joint inclinations. (1) Simulation of Joints Using Different Materials (see Figure 5):
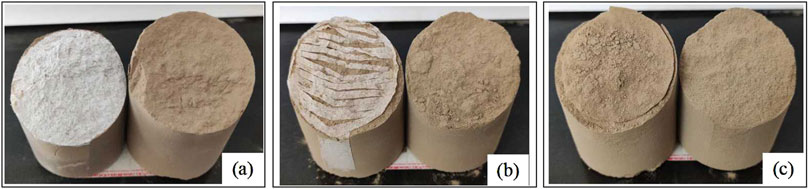
Figure 5. The joint surfaces of different materials. (a) Single-layer paper. (b) Single-layer paper with a mesh pattern. (c) Single-layer rice paper.
Step 1: Determine the joint surface dimensions based on the target inclination, then cut the simulated material accordingly, ensuring an extended section at one end for precise positioning during sample assembly.
Step 2: Prepare the loess sample using a specialized compaction device, constructing it in two equal-volume layers to maintain joint alignment at the designated position and minimize sample heterogeneity. The joint preparation process is illustrated in Figure 6.
(2) Simulation of Joints Using Different Preparation Methods (see Figure 7):
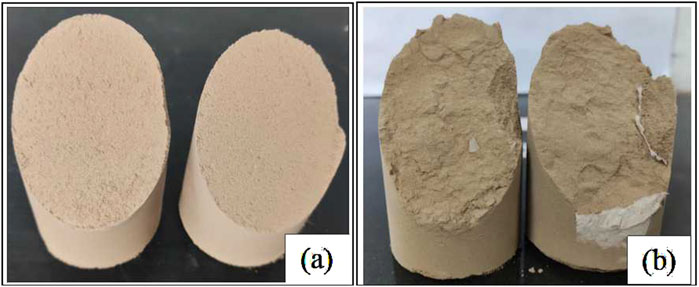
Figure 7. The joint surfaces of different sample making methods. (a) Smooth contact surfaces. (b) Rough contact surface.
Smooth Contact Surface Method: The joint interface is left unmodified, without surface roughening or the application of simulated material.
Rough Contact Surface Method: The loess sample prepared using method (1) is split along the joint surface, the tissue paper at the joint is removed, and the two-halves are realigned without displacement to replicate natural joint roughness. This approach is comparable to simulating joints through mechanical cutting.
4 Result analysis
4.1 Shear failure mode
The development of joint and fracture systems within rock and soil masses plays a crucial role in regulating gas storage and gas-transport coupling mechanisms (Li et al., 2022; Li, 2022). As early as the 1950s (Clough and Pirtz, 1956), a group of scholars summarized the fundamental relationships between the failure modes of loess slopes under seismic action, slope morphology, and geological structure (Wartman J et al., 2005; Arango and Seed, 1974). Loess, being a special structured soil, exhibits failure modes that can be classified into four categories based on mechanical response characteristics and energy dissipation patterns: (1) shear-through type (Shi, 2025): This mode involves strain localization along the joint surface, forming a single shear band accompanied by a sharp decrease in the porosity ratio. (2) tensile-shear composite type (Qiu et al., 2019): Vertical tensile cracks appear first, followed by the penetration of oblique shear bands, resulting in a “Y”-shaped bifurcation of the failure surface. (3) disintegration-collapse type (Zhang et al., 2013): This type involves the instantaneous disintegration of the cemented structure, leading to a “mudflow-like” failure and (4) progressive spalling type (Baoping et al., 2021; Li et al., 2022): Surface layers peel off successively, with the spalling thickness showing an exponential relationship with the number of cycles. Research on the failure modes of jointed loess primarily focuses on the effects of joint dip angle under multi-field coupling conditions, joint propagation under dynamic loading, and the joint weakening mechanism under freeze-thaw cycles. Based on the macroscopic failure observations in this study, the failure modes of loess specimens containing structural joints can generally be classified into shear failure, sliding failure, conjugate shear failure, sliding-shear failure, and sliding-conjugate shear failure. Taking 100 kPa as an example, the failure modes of loess specimens with structural joints are analyzed (as shown in Figure 8).
(1) Shear Failure Mode: Specimens exhibiting this mode demonstrated an oblique intersection between the joint surface and the shear plane, resulting in pronounced shear dilation and compression dilation failure. The soil layers above and below the joint surface maintained structural integrity, with no discernible relative displacement. Under a given confining pressure, as the axial stress progressively increased, the downward sliding force along the joint surface was insufficient to overcome the frictional resistance due to the low joint dip angle. Consequently, relative sliding was inhibited, and the soil mass underwent either single-inclined-plane shear or developed a relatively parallel double-inclined-plane shear mechanism. This failure mode was observed in specimens containing single-layer paper simulated joints (0°, 30°), single-layer paper mesh simulated joints (0°, 30°, 45°, 90°), single-layer rice paper simulated joints (0°, 90°), and smooth/rough contact surface simulated joints (0°, 30°; 30°, 90°).
(2) Sliding Failure Mode: The spatial alignment between the joint surface and the shear plane exceeded 85%, leading to significant shear sliding between the upper and lower soil layers, accompanied by interface shear dilation and compression dilation effects. However, the structural integrity of the soil matrix remained largely preserved. Under a given confining pressure, as the axial stress increased, the downward sliding force along the joint surface significantly surpassed the frictional resistance due to the high joint dip angle (60°–75°). This resulted in pronounced relative sliding or even separation at the joint surface, while the soil layers above and below maintained substantial integrity. This mode was observed in specimens with single-layer paper mesh simulated joints (60°, 75°) and smooth/rough contact surface simulated joints (75°).
(3) Conjugate Shear Failure Mode: This mode was characterized by the development of X-shaped conjugate shear planes that penetrated the original joint surface, forming a spatially intersecting failure system with localized crushing zones. In the case of horizontal joints, under a given confining pressure, progressive axial stress resulted in the crushing of soil proximal to the joint surface. Subsequently, fine cracks propagated around the joint surface, coalescing to form intersecting shear planes. This failure mechanism was observed in specimens with single-layer paper simulated joints (90°), rough contact surface simulated joints (0°), and smooth contact surface simulated joints (90°).
(4) Sliding-Shear Failure Mode: This composite failure mode combined the interfacial sliding characteristic of sliding failure with the oblique fracture surfaces characteristic of shear failure, forming a hybrid structure of a “main sliding zone” and a “secondary shear zone.” This mode was evident in specimens with single-layer paper simulated joints (75°), single-layer rice paper simulated joints (60°, 75°), and smooth contact surface simulated joints (45°, 60°).
(5) Sliding-Conjugate Shear Failure Mode: This mode was characterized by the concurrent development of interfacial sliding and X-shaped shear planes, resulting in a three-dimensional spatial failure system. This phenomenon primarily manifested under conditions of high joint dip angles. This failure mode was observed in specimens containing single-layer paper simulated joints (60°) and rough contact surface simulated joints (45°, 60°).
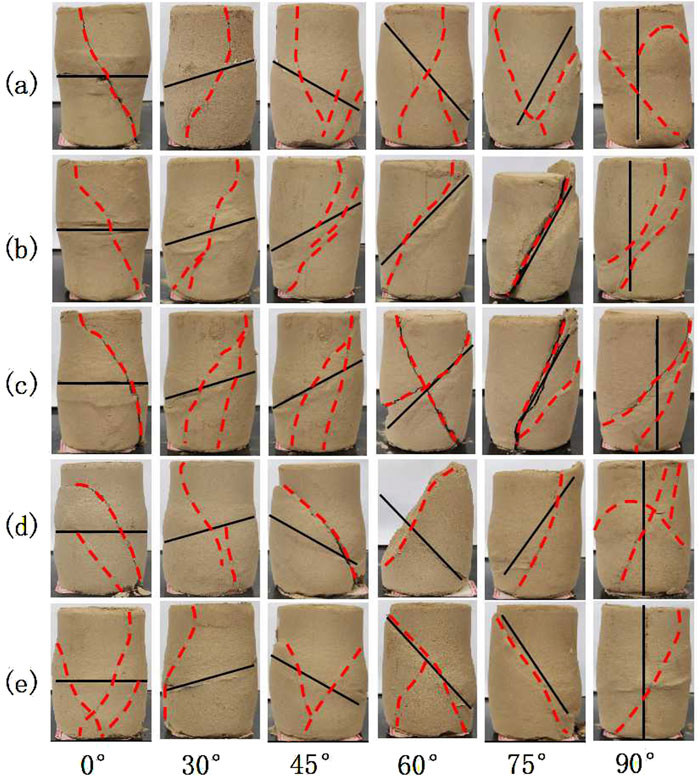
Figure 8. Shear failure mode of jointed loess specimens (100 kPa). (a) Single-layer paper. (b) Single-layer paper with a mesh pattern. (c) Single-layer rice paper. (d) Smooth contact. (e) Rough contact.
Validation studies revealed a consistency rate of 82%–89% between the failure modes observed in specimens with varying simulated materials (paper/rice paper/contact surface) and in-situ field observations reported by Zhong (1983). This concordance affirms the engineering reliability of the laboratory simulation methodologies employed. These findings furnish crucial criteria for identifying dominant joint surfaces in the stability analysis of loess slopes.
4.2 Axial maximum displacement
Triaxial compression tests demonstrated that at confining pressures of 100 kPa and 150 kPa, the loess specimens predominantly exhibited strain-hardening behavior, characterized by the absence of a discernible stress peak within an axial strain range of 15%. Consequently, a stable displacement state at 15% axial strain was adopted as the failure criterion for these specimens. To elucidate the influence of joint dip angles on the deformation characteristics of loess, experimental data obtained under a confining pressure of 50 kPa were selected as a representative case (Figure 9). The analysis revealed a significant nonlinear relationship between axial maximum displacement and increasing joint dip angle. Specifically, specimens with simulated joints constructed from single-layer tracing paper, single-layer rice paper, and rough contact surfaces exhibited peak axial displacements near a dip angle of 60°. Conversely, specimens with simulated joints composed of single-layer tracing paper mesh and smooth contact surfaces displayed peak displacements within the 75° dip angle range.
This divergent trend underscores the pivotal role of the spatial coupling effect between joint planes and shear planes in dictating failure modes. When the joint dip angle coincided with the potential shear plane orientation (i.e., under a sliding-shear composite failure mode), the specimens exhibited the maximum axial displacement response, concomitant with a diminished load-bearing capacity and the development of distinct rupture surfaces. Comparative analysis of various simulation methodologies revealed that single-layer paper, rice paper, and rough contact surfaces more faithfully reproduced the mechanical behavior of naturally jointed loess. The resultant failure modes and displacement patterns demonstrated enhanced practical applicability for engineering endeavors.
4.3 Stress–strain relationship
Based on the triaxial compression test results, this study employed a confining pressure of 100 kPa and a joint inclination of 60° as a representative condition to conduct a comparative analysis of the mechanical response characteristics between jointed loess and intact remolded loess. As illustrated in Figure 10, the stress-strain curves of the two specimen types exhibited marked disparities. For intact remolded loess, the deviatoric stress increased approximately linearly with strain up to an axial strain of 3%. Subsequently, a peak strength of 400 kPa was attained at approximately 10% strain, followed by a slight stress decrement, indicative of typical strain-softening behavior. In contrast, the stress-strain curve for jointed loess closely mirrored that of the intact specimen at strains below 1.5%, suggesting that the mechanical influence of the joint surface remained negligible during the elastic deformation and pore compaction phases. However, beyond 1.5% strain, the curve slope diminished substantially, with the absence of a distinct peak strength or stress drop, demonstrating continuous strain-hardening characteristics. This phenomenon can be attributed to the pre-existing joint disrupting the structural continuity of the soil, thereby impeding particle rearrangement. Notably, at 12% strain, the deviatoric stress values of the two specimen types converged, indicating that the strength properties were no longer influenced by the joint surface after complete soil failure.
Comparative analysis of the curve evolution revealed that the influence of the joint surface on the mechanical properties of loess was significantly strain-dependent: its effect was negligible during the elastic deformation stage (ε < 1.5%) and the complete failure stage (ε > 12%); however, during the plastic development stage (1.5% < ε < 12%), the presence of the joint surface reduced the specimen strength. This finding validates the efficacy of utilizing a combined methodology involving single-layer rice paper and rough contact surfaces for the preparation of joint specimens. This approach not only faithfully simulates the weakening effect of the joint surface but also mitigates excessive strength attenuation associated with traditional methods such as grooving, thereby providing a novel technical approach for the preparation of jointed loess specimens.
4.4 Shear strength damping ratio
For the purpose of comparative analysis, under identical confining pressures, the shear strength reduction ratio (Rs) of loess specimens containing tectonic joints relative to intact loess specimens is defined as follows:
In this formulation,
Through a series of triaxial shear tests, the influence of confining pressure conditions on the shear strength attenuation ratio (Rs) of jointed loess was systematically investigated (Figure 11). Under low confining pressure (σ3 = 50 kPa), the joint inclination angle exerted a significant influence on the Rs value. Despite variations in specimen preparation materials and methodologies, the shear strength attenuation ratio curves of specimens prepared using different joint simulation techniques exhibited similar trends: as the joint inclination angle increased from 0° to 75°, the Rs value initially decreased and subsequently increased, reaching its minimum within the 60°–75° range. All experimental data satisfied Rs < 1, indicating that the joint structure significantly diminished soil strength under low confining pressure, with this regularity being particularly pronounced for specimens simulated using single-layer paper mesh, single-layer rice paper, and rough contact surfaces. The experimental results confirmed that the Rs value was inversely correlated with the degree of joint influence, where a lower Rs value signified a more substantial joint weakening effect. Under medium confining pressure (σ3 = 100 kPa), the presence of joints still resulted in noticeable strength attenuation, but the significance of the inclination angle’s influence decreased. Notably, the single-layer paper specimen exhibited the minimum Rs value at a 0° inclination angle, whereas for single-layer paper mesh specimens, it occurred at a 60° inclination angle. Within the 25°–55° inclination range, the Rs value of single-layer paper mesh specimens was anomalously higher than that of 0° inclination specimens. It is noteworthy that the experimental data for single-layer paper and its mesh specimens under this confining pressure displayed considerable dispersion, potentially attributable to interface contact effects. Under high confining pressure (σ3 = 150 kPa), the Rs values of specimens prepared using different methods stabilized within the 0.95–1.00 range, with minimal influence from the joint inclination angle. This indicated that high confining pressure effectively suppressed the propagation and evolution of joint surfaces, and the soil failure mode gradually transitioned to the overall shear failure of the matrix.
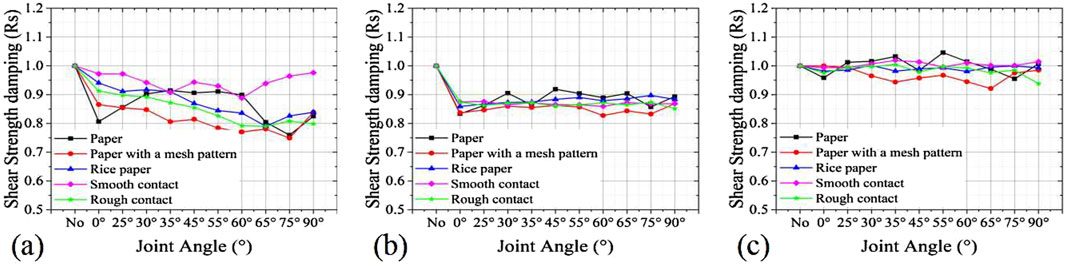
Figure 11. The shear strength damping ration of jointed loess sample. (a) Confining pressure = 50 kPa. (b) Confining pressure = 100 kPa. (c) Confining pressure = 150 kPa.
In summary, the experimental results highlight the significant regulatory role of confining pressure on joint effects. As the confining pressure increases, its normal constraint effect on the joint surface strengthens, significantly inhibiting the propagation and evolution of the joint structures. Consequently, the soil strength gradually approaches those of intact specimens. These findings provide valuable insights for the stability assessment of loess slopes. In practical engineering applications, particular attention should be given to the strength-weakening effects of joint surfaces in low confining pressure zones, especially near the surface.
4.5 Strength performance
4.5.1 Friction strength
The variation characteristics of the frictional strength of jointed loess specimens are illustrated in Figure 12. Research findings indicate that the internal friction angle of jointed loess specimens is generally higher than that of intact specimens. Simulation tests using different materials (Figure 12a) reveal a significant decrease in the internal friction angle when the joint inclination angles are between 60° and 65°, whereas for other inclination angles, the values remain largely consistent with those of intact specimens. Notably, the sample preparation method exerts considerable influences on the variation pattern of frictional strength (Figure 12b): in rough contact surface simulations, the internal friction angle peaks at a 60° inclination, while in smooth contact surface simulations, it reaches its lowest value within the 45°–60° inclination range. From the perspective of failure mode evolution, when the joint inclination angle is ≤45°, the specimens primarily exhibit shear failure, with frictional strength governed by the combined effects of sliding friction and interlocking friction. As the inclination angle increases to 60° and 75°, the failure mode shifts to a sliding-dominated mechanism, where sliding friction accounts for over 90% of the total frictional strength. This transition results in an overall reduction in frictional strength compared to shear failure modes.
Comprehensive analysis indicates that the internal friction angle of specimens reaches its minimum at a joint inclination angle of 60°, aligning with the research findings of Zhu Yanbo and Cheng Longhu et al. Furthermore, axial displacement monitoring data reveal that the displacement response patterns of jointed specimens simulated using single-layer rice paper and single-layer paper most closely resemble those of natural joints, making them the recommended preferred sample preparation methods.
4.5.2 Cohesive strength
The strength parameters of loess are composed of both frictional strength and cohesion, with the variation of cohesion in relation to joint characteristics presented in Figure 13. The experimental results indicate the following: (1) For specimens with joints simulated using single-layer paper and smooth contact surfaces, cohesion values are significantly lower than those of intact specimens, exhibiting an unimodal variation trend with increasing joint inclination and reaching a minimum at approximately 75°; (2) The cohesion of specimens with joints simulated by single-layer paper mesh, single-layer rice paper, and rough contact surfaces follows a typical V-shaped evolution pattern, with the minimum cohesion values for the latter two types of specimens occurring within the 60°–65° inclination range.
A comparative analysis of different specimen preparation methods and joint simulation materials reveals significant differences in the variation patterns of cohesion. Zhu Yanbo et al. systematically confirmed that the cohesion of jointed loess indeed follows a V-shaped evolution pattern with changing inclination angles; Cheng Longhu et al. further highlighted that loess strength parameters reach their lowest values at a joint inclination of 65°. Based on these research findings, using single-layer rice paper or rough contact surfaces to simulate jointed specimens in laboratory mechanical property studies more accurately reflects the strength degradation characteristics of jointed loess, demonstrating high rationality in the experimental methodology.
4.6 Mechanical mechanism
According to the single structural plane theory proposed by Jaeger (1960), a mechanical analysis of jointed loess was conducted, as illustrated in Figure 14. Assuming that the angle between the joint plane and the maximum principal stress plane (i.e., the inclination angle) is β, the principal stress σ and shear stress τ acting on the joint plane were calculated based on the Mohr’s stress circle theory. The shear strength of the joint plane was then determined according to the Coulomb-Navier criterion, as expressed by the following formula:
Based on the aforementioned calculation formulas, the failure of a jointed loess specimen along the joint surface must satisfy the following conditions:
In the equation,
According to the failure condition of soil along the joint surface, the soil strength is primarily governed by the joint inclination angle. When the joint inclination angle is 0° or 90°, the soil strength theoretically approaches infinity, preventing failure along the joint surface, and leading instead to shear failure within the soil matrix. However, when the joint inclination angle satisfies (
Experimental results indicate that the internal friction angle of intact loess is 21.6°, suggesting that when the joint inclination angle reaches 55.8°, sliding failure occurs along the joint surface, corresponding to the minimum soil strength.
4.7 Discussion
Building upon the findings of this study, the parameters obtained from different materials and sample preparation methods for simulating loess joints were systematically summarized and statistically analyzed. This analysis facilitated the identification of the most appropriate material or method for accurately replicating the mechanical behavior of jointed loess. Table 2 illustrates the rationality assessment of different simulation materials and methods, where a value of “1” indicates a relatively reasonable simulation, while “0” indicates otherwise. A higher total score suggests greater suitability for preparing jointed loess specimens and conducting laboratory-based mechanical property investigations. As shown in Table 2, the single-layer rice paper method emerges as the most suitable approach for simulating jointed loess specimens, followed by the rough contact surface method. Notably, the mechanical response patterns reveal that when the joint inclination approaches the critical value of 60°, the specimens exhibit significant strength weakening. This phenomenon is particularly evident in the single-layer rice paper simulation group, as its stress-strain curves and failure patterns closely replicate the mechanical behavior of natural jointed loess. These findings validate the scientific robustness and engineering applicability of the proposed simulation method, providing mechanistic insights into the strength evolution of jointed loess.
As presented in Table 2, the thin-layer structure of single-layer rice paper mirrors the weak interlayer characteristics of natural loess joints, where shear strength is primarily controlled by interfacial friction and cohesion. When the joint inclination approaches the critical angle (60°), the specimens exhibit significant strength degradation. Additionally, the joint surfaces simulated by rice paper demonstrate pronounced anisotropic characteristics, aligning with the strain localization phenomenon observed in natural loess joints. At the critical inclination, shear bands preferentially develop along the joint surface, leading to a sharp decline in the overall strength of the specimen. Therefore, single-layer rice paper proves effective in simulating the mechanical behavior of natural loess joints. In contrast, the rough contact surface method simulates joint surface undulations through physical etching, with its mechanical response being influenced by the coupling effect of surface roughness and normal stress. Although this method partially captures the frictional characteristics of the joint surface, the protrusions formed by etching are prone to shearing during the process, resulting in an overestimation of the friction angle and a deviation from the progressive failure mechanism typical of natural loess joints. Thus, the rough contact surface method exhibits suboptimal performance in simulating loess joints.
However, the single-layer rice paper method also presents certain limitations in accurately simulating natural loess joints. First, the mechanical properties of rice paper are highly susceptible to variations in humidity, which significantly compromises its long-term stability. This contrasts with the water resistance and time-dependent behaviors (e.g., cementation) exhibited by natural loess joints, which are not fully captured in the simulation. Second, the cohesion (c) parameter of rice paper differs considerably from that of natural joints, which may result in an overestimation of short-term strength and an underestimating long-term rheological effects that are typically observed in natural loess joints. Finally, the small-sized specimens used in the experimental setup (e.g., 50 mm × 50 mm) fail to adequately represent the scale effects of joint distribution as encountered in real-world engineering applications (e.g., joint spacing and persistence). Additionally, the plane strain conditions in laboratory tests differ from the three-dimensional stress state of slopes.
Therefore, in practical engineering applications, particular attention should be directed toward the dynamic evolution of joints exhibiting critical inclinations, especially those within the 50°–70° range in loess slopes. To mitigate potential risks, it is essential to identify potential slip surfaces using advanced technologies such as drone-based oblique photography or 3D laser scanning. Moreover, an integrated “identification-reinforcement-monitoring” strategy should be developed to effectively reduce the risk of instability in loess slopes, thereby enhancing the safety and reliability of engineering projects.
5 Conclusion
This study systematically investigates the mechanical properties of loess specimens containing structural joints through five key dimensions: failure modes, axial displacement response, stress-strain evolution, shear strength attenuation effects, and strength parameter variations. The research provides a comprehensive understanding of the reconstruction mechanism of joint mechanical properties by different simulation materials and methods, elucidating the controlling effect of joint inclination on the mechanical behavior of loess specimens. The principal conclusions are as follows:
(1) The maximum axial displacement in jointed loess specimens typically occurs when the joint surface aligns with the shear surface, making the specimen most susceptible to failure. Notably, when the joint inclination is 90°, the maximum axial displacement is smaller than that observed at a joint inclination of 60°.
(2) During the initial strain stage and after soil failure, the influence of joints on the deviatoric stress of loess is minimal. Consequently, the stress-strain curves of jointed loess specimens exhibit characteristics similar to those of intact loess.
(3) Under low confining pressure, the shear strength attenuation ratio initially decreases and then increases with increasing joint inclination, reaching a minimum value at joint inclinations between 60° and 75°. As confining pressure increases, the influence of joints on the strength of loess becomes negligible.
(4) The cohesion follows a V-shaped trend with increasing joint inclination, reaching its lowest value at joint inclinations between 60° and 65°, where the strength indicators of loess are minimized.
(5) Based on indoor triaxial test results, the single-layer rice paper method is identified as the most reasonable for simulating jointed loess specimens, followed by the rough contact surface method. A mechanical analysis further supports the single-layer rice paper method as the most appropriate technique for preparing jointed loess specimens.
Data availability statement
The original contributions presented in the study are included in the article/supplementary material, further inquiries can be directed to the corresponding author.
Author contributions
HW: Formal Analysis, Writing – original draft, Writing – review and editing. JZ: Supervision, Writing – review and editing. PW: Investigation, Project administration, Writing – review and editing. YW: Writing – original draft, Writing – review and editing.
Funding
The author(s) declare that financial support was received for the research and/or publication of this article. This research was funded by Gansu Lanzhou Geophysics National Observation and Research Station (2021Y14); Basic Scientific Research Fund, Science and Technology Innovation Base of Lanzhou, Institute of Earthquake Forecasting, China Earthquake Administration (2022IESLZ02); The Earthquake science and technology spark plan project (XH23041C); The Natural Science Foundation of Gansu Province (22JR11RA090, 23JRRA1398); the Earthquake joint fund (U1939209).
Acknowledgments
We are grateful to the students in our group (YW) for their help during field tests. We acknowledge JZ and PW for reviewing our manuscript, and to the subject group for their joint help. We sincerely acknowledge the constructive comments of the reviewers.
Conflict of interest
The authors declare that the research was conducted in the absence of any commercial or financial relationships that could be construed as a potential conflict of interest.
Generative AI statement
The author(s) declare that no Generative AI was used in the creation of this manuscript.
Publisher’s note
All claims expressed in this article are solely those of the authors and do not necessarily represent those of their affiliated organizations, or those of the publisher, the editors and the reviewers. Any product that may be evaluated in this article, or claim that may be made by its manufacturer, is not guaranteed or endorsed by the publisher.
References
Arango, I., and Seed, H. B. (1974). Seismic stability and deformation of clay slopes. J. Geotechnical Eng. Div. 100 (2), 139–156. doi:10.1061/ajgeb6.0000013
Bai, B., and Han, X. (2011). Experimental study on shear strength characteristics of artificial joints in intact loess. Low. Temp. Archit. Technol. 33 (07), 91–93. doi:10.3969/j.issn.1001-6864.2011.07.042
Baoping, L., Gaoquan, P., Yu, Z., and Qian, Y. (2021). Influence of freeze-thaw cycles on the mechanical properties of loess under plane strain conditions. J. Civ. Environ. Eng. Chin. Engl. doi:10.11835/j.issn.2096-6717.2020.043
Barton, N. R., Bandis, S., and Bakhtar, K. (1985). Strength, deformation and conductivity coupling of rock joints. Int. J. Rock Mech. and Min. Sci. and Geomechanics Abstr. 22, 121–140. doi:10.1016/0148-9062(85)93227-9
Barton, N. R., and Choubey, V. (1977). The shear strength of rock joints in theory and practice. Rock Mech. 10 (1), 1–54. doi:10.1007/BF01261801
Borcherdt, R. D. (1970). Effects of local geology on ground motion near San Francisco Bay. Bull. Seismol. Soc. Am. 60 (1), 29–61. doi:10.1029/EO050i010p00552
Borcherdt, R. D., and Glassmoyer, G. (1992). On the characteristics of local geology and their influence on ground motions generated by the Loma Prieta earthquake in the San Francisco Bay region, California. Bull. Seismol. Soc. Am. 82 (2), 603–641. doi:10.1785/BSSA0820020603
Cheng, L., Nie, R., and Liu, F. (2017). Experimental study on uniaxial compression of fissured loess. Hydrogeol. Eng. Geol. 44 (05), 80–85+91. doi:10.16030/j.cnki.issn.1000-3665.2017.05.13
Clough, R. W., and Pirtz, D. (1956). Earthquake resistance of rock-fill dams. Trans. Am. Soc. Civ. Eng. 123 (1), 792–810. doi:10.1061/TACEAT.0007548
David, K., and KEEFER, (1984). Landslides caused by earthquakes. GSA Bull. 95 (4), 406–421. doi:10.1130/0016-7606(1984)95<406:LCBE>2.0.CO;2
Fang, J. (2010). Experimental study on shear strength and permeability of loess joints and their engineering applications. Xi'an, China: Xi'an University of Architecture and Technology. doi:10.7666/d.d192642
Gansu Provincial Bureau of Geology and Mineral Resources (1989). Regional Geology of Gansu Province. Beijing: Geological Publishing House.
GERRARDC (1986). Shear failure of rock joints: appropriate constraint for empirical relation. Int. J. Rock Mech. Min. Sci. Geomechanics Abstr. 23, 421–429. doi:10.1016/0148-9062(86)92307-7
Hartzell, S., Leeds, A., Frankel, A., and Michael, J. (1996). Site response for urban Los Angeles using aftershocks of the northridge earthquake. Bull. Seismol. Soc. Am. 86, S168–S192. doi:10.1785/bssa08601bs168
Jia, H., He, Y., and Yang, S. (2011). Study on the influence of joints on the failure patterns and mechanical properties of loess. China Rural Water Hydropower (11), 77–81.
Kang, C., Shaokai, W., and He, M. (2019). Analysis of geometric characteristics of structural joints in Longxi loess. Chin. J. Geol. Hazard Control 30 (05), 131–138.
Li, H. (2022b). Research progress on evaluation methods and factors influencing shale brittleness: a review. Energy Rep. 8, 4344–4358. doi:10.1016/j.egyr.2022.03.120
Li, J., Li, H., Xu, J., Wu, Y., and Gao, Z. (2022). Effects of fracture formation stage on shale gas preservation conditions and enrichment in complex structural areas in the southern Sichuan basin, China. Front. Earth Sci. 10, 921988. doi:10.3389/feart.2022.921988
Lili, W., Ning, Li, He, M., and Liu, Q. (2020). Experimental study on the mechanical properties of jointed loess based on a remolded sample preparation method. J. Disaster Prev. Mitig. Eng. 40 (01), 35–42.
Liu, H. Y., Han, H., An, H. M., and Shi, J. J. (2016). Hybrid finite-discrete element modelling of asperity degradation and gouge grinding during direct shearing of rough rock joints. Int. J. Coal Sci. Technol. 3 (3), 295–310. doi:10.1007/s40789-016-0142-1
Liu, L. (2007). Study on loess strength characteristics and the influence of joints on the stability of loess high slopes. Tianjin, China: Tianjin University. doi:10.7666/d.y1358177
Liu, X., Fan, J., Cui, H., and Kong, Q. (2020). Experimental and numerical simulation of water infiltration in natural loess joints. J. Yangtze River Sci. Res. Inst. 37 (10), 110–116+124. doi:10.11988/ckyyb.20190669
Liu, X., Kong, Q., Sun, X., and Wang, Z. (2017a). Large-scale direct shear test study on natural loess joints. J. Xi'an Univ. Archit. Technol. Nat. Sci. Ed. 49 (05), 680–684+707. doi:10.15986/j.1006-7930.2017.05.010
Liu, X., Wang, Z., Wang, T., and Lu, J. (2017b). Experimental study on shear strength of intact loess joints. J. China Coal Soc. 42 (08), 2003–2010. doi:10.13225/j.cnki.jccs.2017.0379
Luo, Y. (2014). Study on the strength and seepage of loess joints. Xi'an, China: Xi'an University of Architecture and Technology. doi:10.7666/d.D560261
Peng, J., Chen, L., Huang, Q., Yuming, M., Wen, F., Yan, J., et al. (2008). Large-scale physical simulation experimental study on the fracture propagation of ground fissures. Chin. J. Geophys. 51 (6), 1826–1834. doi:10.3321/j.issn:0001-5733.2008.06.024
Peng, J., Wang, Q., Zhuang, J., Leng, Y., Fan, Z., and Wang, S. (2020). Dynamic mechanisms of landslide disasters on the Loess Plateau. J. Geomechanics 26 (05), 714–730. doi:10.12090/j.issn.1006-6616.2020.26.05.059
Peng, J., Wen, F., Xi'an, Li, Qingliang, W., Xijie, F., Jun, Z., et al. (2007). Key issues in the study of ground fissure genesis in the Fenwei Basin. J. Eng. Geol. (04), 433–440.
Qiu, N., Nan, M., and Lei, R. (2019). A review of the effects of freeze-thaw cycles on loess strength. China Hous. Facil. 2.
Robert, B., Darragh, , Anthony, F., and Shakal, (1991). The site response of two rock and soil station pairs to strong and weak ground motion. Bull. Seismol. Soc. Am. 81 (5), 1885–1899. doi:10.1785/BSSA0810051885
Shakal, A., Huang, M. J., and Cao, T. Q. (1988). The Whittier narrows, California earthquake of October 1, 1987—CSMIP strong motion data. Earthq. Spectra 4 (1), 75–100. doi:10.1193/1.1585466
Shakal, A. F., Ragsdale, J. T., and Sherburne, R. W. (2015). CSMIP strong-motion instrumentation and records from transportation structures—bridges[C]//Lifeline earthquake engineering. ASCE.
Shi, C. (2025). Experimental study on the influence of freeze-thaw cycles on the mechanical properties of loess. Xijing University.
Sun, G. Z. (1988). Structural joints in loess of Northwest China and their significance in geological engineering. Proc. Third Natl. Conf. Eng. Geol. 1, 17–23.
Trifunac, M. D., and Hudson, D. E. (1971). Analysis of the Pacoima dam accelerogram—San Fernando, California, earthquake of 1971. Bull. Seismol. Soc. Am. 61 (5), 1393–1411.
Wang, J., Ni, Y., and Sun, J. (1994). Study on loess structural joints and their applications. J. Eng. Geol. (04), 31–42.
Wang, J., and Wang, J. (1994). Loess subsurface erosion landforms and structural joints in central and southern Hebei. Geogr. Res. (01), 90–93. doi:10.11821/yj1994010012
Wang, P., Wang, H., Wang, L., Qian, Z., and Shao, S. (2021). Study on the strength characteristics of loess with structural joints. J. Nat. Disasters 30 (03), 133–141. doi:10.13577/j.jnd.2021.0315
Wang, T., Luo, Y., and Wang, J. (2013). Experimental study on shear strength characteristics of loess joints. Chin. J. Undergr. Space Eng. 9 (03), 497–501+551.
Wang, Z. (2017). Study on shear strength and constitutive relationship of intact loess joint surfaces. Xi'an, China: Xi'an University of Architecture and Technology.
Wartman, J., Seed, R. B., and Bray, J. D. (2005). Shaking table modeling of seismically induced deformations in slopes. J. Geotechnical Geoenvironmental Eng. 131 (5), 610–622. doi:10.1061/(asce)1090-0241(2005)131:5(610)
Yu, Y. (2020). Strength characteristics and seismic failure modes of loess slopes with structural joints. Lanzhou Inst. Seismol. China Earthq. Adm.
Zhang, Ze, Ma, W., and Qi, J. (2013). Evolution of soil structure and mechanism of engineering property changes under freeze-thaw cycles. J. Jilin Univ. (Earth Sci. Ed.) 43 (6). Available online at: http://ir.casnw.net/handle/362004/23408.
Zhong, S. (1983). Structural inclined joints in loess and their influence on the stability of loess tunnels. Chin. J. Geotechnical Eng. (04), 68–77.
Keywords: loess joint, failure mode, strength characteristics, test materials, manufacturing process
Citation: Wang H, Zhang J, Wang P and Wang Y (2025) Experimental study on the mechanical properties of loess containing tectonic joints. Front. Earth Sci. 13:1512722. doi: 10.3389/feart.2025.1512722
Received: 17 October 2024; Accepted: 18 April 2025;
Published: 12 May 2025.
Edited by:
Derek Keir, University of Southampton, United KingdomReviewed by:
Hu Li, Sichuan University of Science and Engineering, ChinaHuafeng Deng, China Three Gorges University, China
Copyright © 2025 Wang, Zhang, Wang and Wang. This is an open-access article distributed under the terms of the Creative Commons Attribution License (CC BY). The use, distribution or reproduction in other forums is permitted, provided the original author(s) and the copyright owner(s) are credited and that the original publication in this journal is cited, in accordance with accepted academic practice. No use, distribution or reproduction is permitted which does not comply with these terms.
*Correspondence: Ping Wang, d2FuZ3BpbmdAZ3NkemouZ292LmNu