- 1Hunan Urban and Rural Environmental Construction Co., Ltd., Changsha, Hunan, China
- 2School of Civil Engineering, Central South University of Forestry and Technology, Changsha, Hunan, China
- 3Intelligent Construction Department, Changsha Building Engineering School, Changsha, Hunan, China
- 4Hunan Construction Investment Group Infrastructure Investment Company, Changsha, Hunan, China
The fundamental cause of leakage in grouting curtains of dams in karst areas lies in the localized damage induced by performance degradation of the curtain under seepage-induced erosion. This work investigated the degradation mechanisms of grouting curtains exposed to karst water erosion by analyzing the mechanical and microstructural evolution of cement-grouted stone (CGS) and cement-clay-grouted stone (CCGS). The results indicate that both materials experience progressive deterioration in mechanical properties, with CCGS demonstrating significantly higher vulnerability. After 120 days, the compressive strength of CGS decreased from 32.89 MPa to 20.03 MPa, while the strength of CCGS declined sharply from 3.89 MPa to 2.03 MPa. Porosity increased from 26.06% to 33.91% for CGS and from 58.04% to 77.01% for CCGS. Microstructural analysis revealed that karst water induced chemical erosion and structural damage in both materials, with CCGS exhibiting accelerated degradation due to weaker cementitious bonding and higher initial porosity, which facilitated ion penetration and reaction-induced damage. The findings highlight the inferior durability of cement-clay composites under karst water conditions and provide critical insights for optimizing grouting materials in karst-prone environments.
1 Introduction
Grout curtain grouting is the preferred construction method for anti-seepage reinforcement of dams in karst regions. However, the karst stratum contains interconnected fissures and conduits with mineral-rich groundwater, where the synergistic effects of hydrostatic pressure, chemical interactions, and geostress can readily induce deterioration and structural damage to the grouting curtain (Liu, 2004; Yu et al., 2020). Extensive engineering projects have demonstrated that the cause of seepage incidents in dam grouting curtains within karst areas lies in the performance degradation of curtain structures under seepage-induced erosion, ultimately leading to localized failures, as evidenced by the Tangab Dam (Mozafari et al., 2021), Logan Martin Dam (Bruce et al., 2017), and Teton Dam (Verma et al., 2023).
Currently, scholars primarily characterize the performance degradation of grouting curtains by investigating changes in the physical-mechanical properties of grouted stones under karst water erosion (Ahmad et al., 2019; Wei et al., 2025), a method whose feasibility has been validated. For instance, Liu (2019) conducted accelerated dissolution tests to obtain the compressive strength, cohesion, internal friction angle, permeability coefficient, and microstructural characteristics of grouted samples at different curing ages. Recent work also emphasizes the temperature field evolution in backfill materials, which could correlate with chemical and mechanical degradation pathways in similar subsurface environments (Ahmad et al., 2021). Feng (2015) compared the soft-water erosion resistance of cement-clay grouts with varying mix ratios through orthogonal experiments, analyzing the degradation patterns of cement-clay reinforcements under different erosion media and durations using strength and mass loss as performance indicators. Sha and Fan (2021) investigated the early impermeability, flexural strength, unconfined compressive strength, corrosion resistance coefficient, volume/mass variations, fracture surface characteristics, corrosion minerals, microstructure, and pore size distribution of a novel high-efficiency micro-cement grouting material in corrosive environments. Tu (2012) evaluated the durability of cement-based grouting materials in seawater using fuzzy analytic hierarchy analysis based on seawater erosion resistance tests. Wang et al. (2021) and Wang et al. (2020). addressed grouting design challenges in sand layers under seawater erosion by conducting accelerated degradation tests, establishing quantitative relationships between seawater exposure time and grouted reinforcement strength, and proposing a constitutive model for degradation damage, providing theoretical guidance for sand-layer grouting in marine environments. Fu et al. (2013) enriched durability prediction frameworks by comparing erosion rates of cement grouting curtains under low-alkalinity soft water at varying permeation pressures.
However, the initial performance of grouted stones is closely tied to grouting environments of karst dams, construction parameters, and material properties-factors often overlooked in existing studies. This oversight leads to significant discrepancies between the performance of laboratory-tested grouted stones and the behavior of real-world karst dam grouting curtains, limiting the practical applicability of experimental findings. Thus, this work simulated the erosion environment of karst dam grouting curtains by preparing high-concentration karst water curing solutions and controlling curing temperatures based on accelerated erosion principles. Specimens cured for varying durations undergo tests for compressive strength, porosity, mass loss, and microstructural morphology to elucidate the performance degradation mechanisms of karst dam grouting curtains under aggressive environmental conditions. Modeling approaches have also been applied to understand cemented geomaterial behavior under similar erosive and structural loading conditions (Rizvi et al., 2020a).
2 Methods
2.1 Raw materials and preparation
The experiment used pure cement grout and cement-clay grout to create grouted stone samples, with mix proportions corresponding to standard practices for grouting curtains in karst areas. The cement utilized was again 42.5R Ordinary Portland Cement, adhering to the national standard of normal Portland cement in China. The clay component consisted of specialized calcium-based clay from Lingshou County, Hebei Province, China. The water-cement ratio for the pure cement slurry was 1:2, while the mixing ratio for the cement-clay slurry was 2:1, with the clay content making up 50% of the cement weight. The grouting process parameters, such as pressure and duration, play a critical role in ensuring uniform penetration and minimizing head losses during injection, as highlighted in prior fluid dynamics studies (Haroon et al., 2017). During the preparation process of grouting stone bodies, a grouting pressure of 1 MPa was applied for a duration of 6 s. The samples were cured under standard conditions of 20°C ± 1°C and ≥95% humidity. Figures 1–3 illustrate the test preparation process, test equipment and grout stone samples.
2.2 Design of accelerated degradation test
The critical challenge in conducting laboratory accelerated degradation tests lies in constructing an accelerated erosion environment that effectively replicates the long-term service conditions of grout curtains. In this work, the degradation process of grouted specimens was accelerated by controlling the concentrations of aggressive ions in simulated karst groundwater and adjusting the curing temperature. The transport mechanisms governing the ingress of aggressive ions into grouted matrices typically include adsorption, diffusion, pressure-driven permeation, and dispersion. Among these, the diffusion of aggressive ions is generally considered to be the most important migration mechanism (Yu and Sun, 2006). When neglecting the binding capacity of aggressive ions within grouted matrices and the influence of time-dependent structural defects on diffusion coefficients, the theoretical model for ion diffusion can be derived from Fick’s Second Law (Yu and Sun, 2006; Wang, 2016), as shown in Equation 1 and Equation 2.
where c0 and cs are the initial erosive ion concentration in the grouted stone and the erosive ion concentration on the exposed surface, respectively. And erf is the error function.
According to the test design, it can be considered that c0 = 0, then Equation 1 can be simplified to Equation 3:
Therefore, the diffusion of aggressive ions in the experiment exhibits direct proportionality to the surface concentration cs. When the erosive ion concentration at the exposed surface of grouted matrices increases by a factor of 20, the corresponding acceleration factor s1 for the test duration also increases by 20 times.
The fundamental mechanism of aggressive ion diffusion in grouted matrices involves random thermal motion of ions through the pore solution within the matrix. The diffusion coefficient of aggressive ions demonstrates a positive temperature dependence (Lindvall, 2007). As described by the Arrhenius equation (Zuo, 2021), the influence of ambient temperature on the diffusion of aggressive ions within grouted matrices is quantified by Equation 4:
where: D0 is the diffusion coefficient of aggressive ions at temperature T0, m2/s; DT is the diffusion coefficient of aggressive ions at temperature T, m2/s; T1 is the reference temperature, generally 293 K; E/R is the activation energy, which is taken as 14,242 in reference (Wang, 2019).
According to literature (Jiang et al., 2014; Pan et al., 2023), the annual average water temperature of rivers in Changsha area is about 18°C (290.9 K), and constant temperature 30°C (303 K) was used in this experiment to maintain the grouted stone test. The acceleration coefficient s2 is calculated in Equation 5.
Therefore, the total acceleration coefficient S of this degradation test is equal to the product of external erosive ion concentration and temperature acceleration coefficient, that is, S = 138.94.
Based on the pre-determined 20 times accelerated erosion factor, the karst water curing solution was prepared at 20 times the concentration of natural karst water. According to investigations, chloride (Cl−), bicarbonate (HCO3−), and sulfate (SO42−) are the primary aggressive ions in karst water affecting grouted matrices. Referencing groundwater monitoring data from a karst-area dam in Hunan Province, Table 1 lists the normal and accelerated concentrations of these three ions.
The curing solution was prepared using sodium chloride, sodium bicarbonate, and potassium sulfate, with an analytical purity of ≥ 99%. Based on calculations of ion concentration, each liter of the prepared karst water curing solution contained 1.52 g of sodium chloride, 8.91 g of sodium bicarbonate, and 21.61 g of potassium sulfate. A self-made accelerated curing box was utilized to accelerate the erosion and deterioration of the stone test block. A small heater was placed at the bottom of the curing box to control the temperature of the karst water, which was set to 30°C within a control range of 20°C–35°C. The accelerated karst water erosion test is shown in Figure 4.
2.3 Testing methods
To investigate the degradation of physical and mechanical performance in CGS (Group A) and CCGS (Group B) specimens under karst water erosion, we conducted analyses of compressive strength, porosity, mass loss, and scanning electron microscopy (SEM) on pre-prepared specimens. The tests adhered to the technical code for testing in China (Ministry of Transport of the People’s Republic of China, 2019; Ministry of Construction of the People’s Republic of China, 2019). A summary of the experimental design, including test conditions, is presented in Table 2. The procedures were as follows.
(1) Specimen preparation and curing. CGS and CCGS specimens were cast, then placed in water-filled tanks for standard curing under controlled conditions (temperature: 20°C ± 1°C, humidity: ≥95%) for 28 days.
(2) Testing. After 28 days of curing, initial properties, including compressive strength, porosity, mass, and microstructural morphology, were evaluated.
(3) Accelerated erosion exposure. Specimens were transferred to a temperature-controlled accelerated erosion chamber (30°C ± 0.5°C) for grouped curing periods of 30, 60, 90, and 120 days.
(4) Post-erosion evaluation. Post-curing tests replicated baseline measurements to quantify degradation metrics: compressive strength loss (%), porosity increase (%), mass loss (%), and microcrack evolution (SEM).
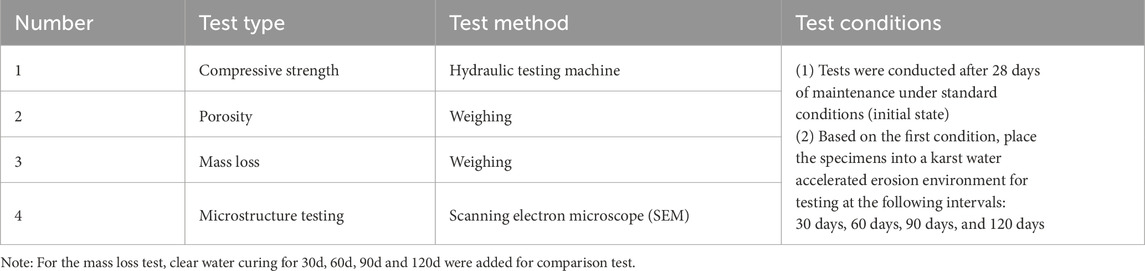
Table 2. Design of physical-mechanical tests for grouted stone under accelerated erosion by karst water.
3 Results
3.1 Analysis of compressive strength test results
The compressive strength test results for grouted stones under accelerated karst water erosion are summarized in Figure 5. With prolonged curing time, the compressive strength of CGS (Group A) decreased from 32.89 MPa to 20.03 MPa, while CCGS (Group B) declined from 3.89 MPa to 2.03 MPa. Notably, Group A exhibited significantly higher strength than Group B. This difference stems from the charge interaction in cement-clay grout: positively charged cement hydration particles partially exchange charges with clay particles, inducing clay agglomeration to form a gel-structured skeleton. However, this skeleton demonstrates inferior mechanical performance compared to the robust particle skeleton created by cement hydration (Feng, 2015). Furthermore, both groups experienced progressive strength reduction over time due to chemical erosion from karst water. The dissolution of calcium hydroxide and degradation of hydration products (e.g., calcium silicate hydrate and calcium aluminate hydrate) into less cohesive compounds gradually compromised the structural integrity of the grouted stones, diminishing their load-bearing capacity (Zhou et al., 2022).
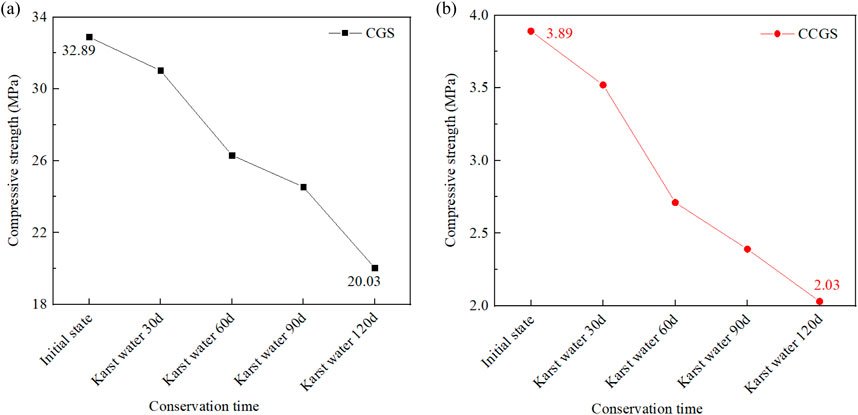
Figure 5. Compressive strength results of grouted stones under karst water erosion: (a) CGSs (Group A); (b) CCGSs (Group B).
Figure 6 illustrates the reduction rates of compressive strength for Groups A and B grouted stones. After 120 days of curing in a karst water environment, Group A exhibited a strength reduction rate of 39.10%, while Group B showed a higher reduction rate of 47.67%, indicating that Group A experienced less strength degradation compared to Group B. This disparity arises because cement particles, with their coarser size and superior cementation properties, form a more stable granular skeleton structure in cement grout (Xie et al.,2025). This enhanced stability mitigates strength deterioration in cement grout stones relative to cement-clay grout, where the weaker clay-cement matrix is more susceptible to karst water erosion. These results further confirm that cement-clay materials exhibit inferior resistance to karst water erosion compared to pure cement materials (Bai, 2001).
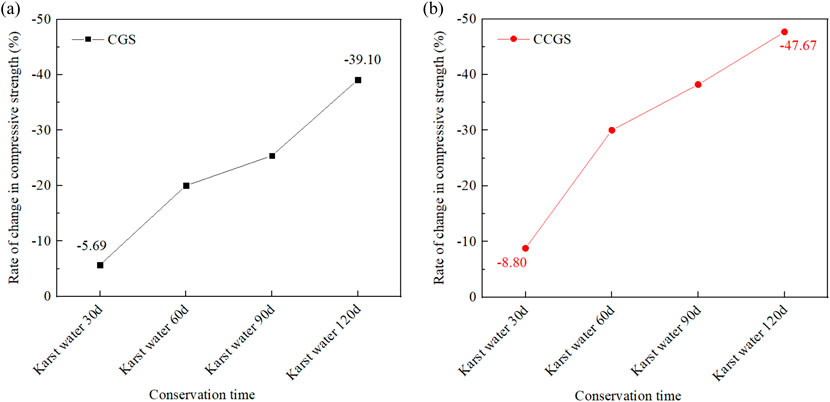
Figure 6. Degradation trends of compressive strength in grouted stones under karst water erosion: (a) CGSs (Group A); (b) CCGSs (Group B).
Additionally, Figure 7 depicts the compressive failure morphology of grouted stone specimens cured in karst water for varying durations. Unconfined compressive strength tests revealed that failure occurred through a progressive crack propagation process: cracks initiated at the base and outer surfaces, extended upward and inward, and ultimately coalesced to cause specimen failure. The crack orientation aligned predominantly with the axial loading direction. Notably, no significant shear failure was observed during the entire unconfined compression process, demonstrating that structural disintegration was driven primarily by tensile splitting rather than shear mechanisms.
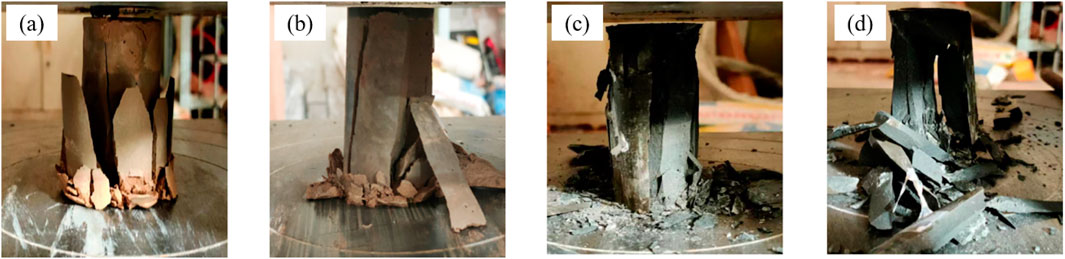
Figure 7. Failure mode of grouted stones under compression: (a) CGS cured for 28d under standard conditions; (b) CCGS cured for 28d under standard conditions; (c) CGS after 60 days of karst water erosion; (d) CCGS after 60 days of karst water erosion.
3.2 Analysis of porosity test results
Figure 8 shows the porosity test results of grouted stone specimens under different accelerated karst water erosion conditions. With the increase in curing time, the porosity of Group A increased from 26.06% to 33.91%, while that of Group B increased from 58.04% to 77.01%. The porosity of Group B was significantly higher than that of Group A. This is because the cement-based grouting material used in Group A exhibited better fluidity and higher density compared to the clay-cement grouting material in Group B. The porosity of both Groups A and B increased with curing time. The primary reason is that in the karst water environment, calcium hydroxide (Ca(OH)2) within the grouted stones dissolves and reacts with erosive ions, reducing its concentration in the surrounding water. This process accelerates the decomposition and dissolution of other hydration products, resulting in continuous loss of chemical substances and gradual enlargement of pores within the grouted stones (Tang, 2019).
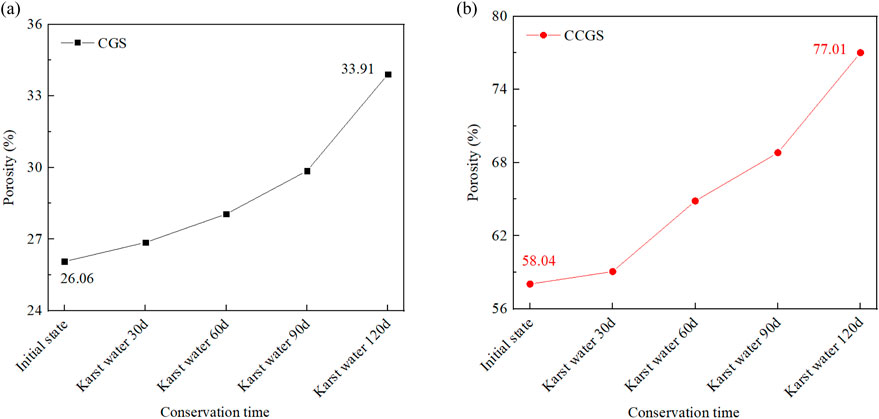
Figure 8. Porosity results of grouted stones under karst water erosion: (a) CGSs (Group A); (b) CCGSs (Group B).
As shown in Figure 9, after 120 days of curing in the karst water environment, the porosity increase magnitude of Group A reached 30.12%, while that of Group B was 32.68%. The smaller variation in Group A’s porosity aligns with its lower strength reduction compared to Group B, and the underlying mechanisms are similar. Additionally, it was observed that the porosity growth rates of both groups were relatively slow during the first 90 days of curing. However, after 90 days, the rates accelerated. This phenomenon can be attributed to calcium hydroxide being the primary dissolved component in the early stage. As pores enlarged and increased, the contact area between various hydration products and karst water increased, accelerating the dissolution and erosion rates of calcium hydroxide and other hydration products, thereby hastening porosity growth (He, 2019). Pore structure and thermal behavior of subsurface materials have been extensively modeled to assess effective thermal conductivity and degradation behavior (Rizvi et al., 2020b).
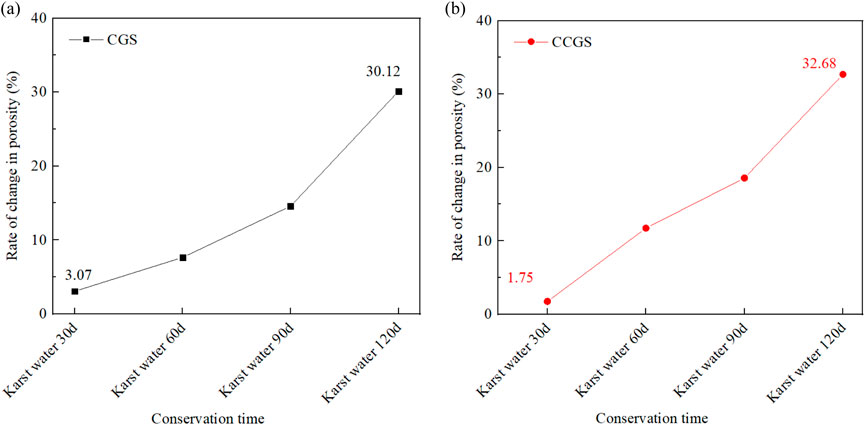
Figure 9. Porosity variation of grouted stones under karst water erosion: (a) CGSs (Group A); (b) CCGSs (Group B).
3.3 Analysis of the results of the grouted stone mass test
The experimental study on grouted stone body specimens cured in clear water and karst water environments revealed distinct mass variation trends over different periods (as shown in Figure 10). Prior to 60 days of curing, the mass change rates of Groups A and B showed minimal differences between the two environments. However, beyond 60 days, specimens in karst water exhibited significantly greater mass variations compared to those in clear water, with the divergence amplifying over time, indicating accelerated deterioration effects from karst water. At 150 days, Group A specimens demonstrated mass change rates of 3.00% (clear water) and 4.50% (karst water), while Group B reached 4.63% and 6.44%, respectively. Notably, Group B consistently displayed higher mass variation rates than Group A. Early-stage chemical reactions between erosive ions in karst water and hydration products (e.g., calcium hydroxide dissolution) initially reduced specimen mass. However, subsequent formation of expansive minerals like gypsum and ettringite partially filled pore structures, temporarily offsetting mass loss through physical expansion while retarding further dissolution. For Group A specimens, this expansive filling initially outweighed dissolution effects, causing a slight mass gain. Prolonged exposure ultimately weakened cementitious bonding, inducing surface softening and edge spalling in both groups, thereby gradually reversing the mass trends. Underground structural performance also varies with geometric and geomechanical parameters, as seen in tunnel stability studies (Alsabhan et al., 2021).
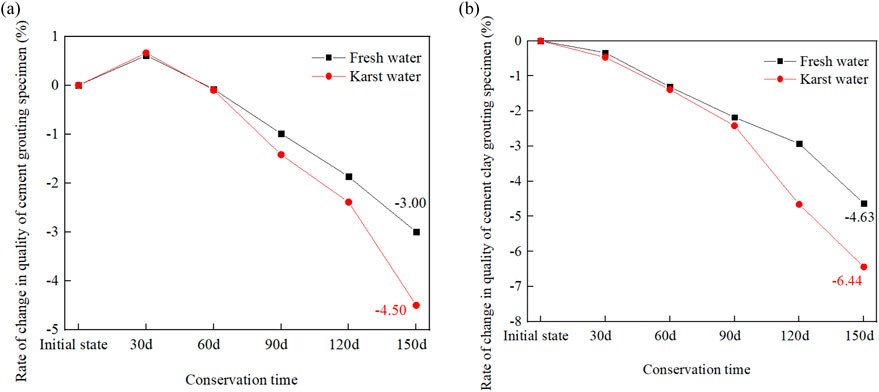
Figure 10. Mass loss rate of grouted stones under fresh and karst water erosion: (a) CGSs (Group A); (b) CCGSs (Group B).
4 Discussion
Microstructural morphology serves as a critical indicator for reflecting changes in the internal composition and pore structure of grouted stones. SEM analysis was conducted on specimens cured for varying durations under karst water erosion. As shown in Figures 11, 12, the cement-grouted stone specimens (Group A) exhibited a dense structure with sufficient hydration, abundant C-S-H gels, and layered calcium hydroxide (irregular hexagonal flakes), along with minor calcium carbonate (blocky formations). In contrast, the CCGS (Group B) showed reduced cement content due to clay incorporation. Their microstructure revealed cement hydration products enveloped by clay particles, limited exposed cementitious materials, and sparse calcium hydroxide crystals and ettringite (needle-shaped). Notably, Group B specimens displayed distinct pores and microcracks, resulting in higher porosity and lower strength compared to Group A, macroscopic analysis revealed that Group A exhibited a compact microstructure, whereas Group B demonstrated pronounced porosity, consistent with macroscopic test results. Lattice element methods further enable accurate simulation of thermal transport and its relationship to geomaterial integrity (Rizvi et al., 2018).
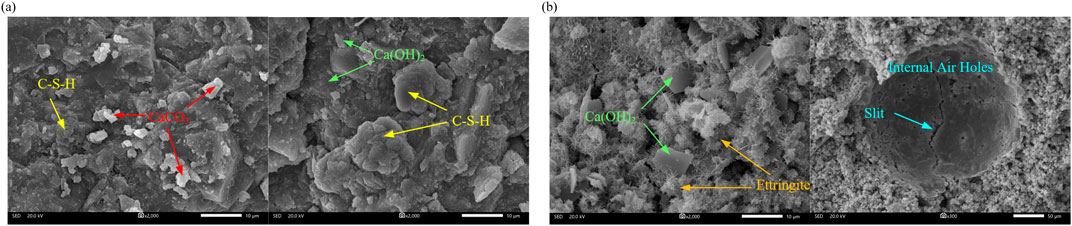
Figure 11. Micro-morphology of grouted stones for 28d under standard conditions (initial state): (a) CGSs (Group A); (b) CCGSs (Group B).
Figures 12, 13 illustrate that after 60 days of karst water erosion, chemical reactions within the grouted stones generated secondary products such as calcium carbonate, gypsum, and ettringite. Compared to the initial state after 28 days of standard curing, the 60-day eroded specimens developed pores and cracks. This deterioration arises from erosive ions reacting with calcium hydroxide to form gypsum, which subsequently interacts with aluminum phases to produce expansive ettringite. The growth of ettringite generates swelling stress at pore interfaces, fracturing the cementitious matrix. As erosion products dissolve or detach, the grouted stones become increasingly porous and fragile, leading to altered physical-mechanical properties (e.g., compressive strength, porosity) (Yu, 2017). Environmental fluctuations such as heat and moisture changes significantly influence the microstructural evolution of underground materials (Ahmad et al., 2025).
Figures 14, 15 demonstrate that after 120 days of karst water erosion, the grouted stones exhibited significantly increased crack density and width, indicating severe structural degradation. While calcium carbonate and gypsum continued to form, no chloride-containing compounds (e.g., calcium chloride) were detected. This absence is attributed to the low chloride ion concentration in the simulated karst water and the competitive reaction between sulfate ions (prioritized due to their higher affinity with C3A phases) and chloride ions. Consequently, chloride-related erosion products were negligible and undetectable in the sampled specimens (Wang et al., 2022).
5 Conclusion
Compressive strength and porosity tests were conducted on cement and CCGS specimens under varying curing durations to investigate the evolution of their mechanical and structural properties. Results demonstrated that under karst water curing, both groups exhibited progressive compressive strength reduction and porosity increase. Within 120 days, CGS specimens showed a strength decline from 32.89 MPa to 20.03 MPa, while CCGS specimens experienced a more pronounced deterioration, decreasing from 3.89 MPa to 2.03 MPa. Similarly, porosity values for CGSs rose from 26.06% to 33.91%, whereas CCGSs displayed a significantly higher porosity increase from 58.04% to 77.01% over the same period, confirming that CCGS suffered greater degradation in both strength and porosity.
Mass variation and microstructural morphology analyses were performed on cement and CCGS specimens under different curing durations and environments. Experimental findings revealed that karst water induced chemical and structural alterations in both groups through erosive effects. However, CCGSs exhibited more severe deterioration, characterized by higher mass variation rates and more drastic internal structural changes. The cement-clay matrix in CCGSs proved more vulnerable to karst water erosion, likely due to its inherently weaker cementitious bonding and higher initial porosity, which accelerated ion penetration and reaction-induced damage. The findings highlight the inferior durability of cement-clay composites under karst water conditions and provide critical insights for optimizing grouting materials in karst-prone environments.
Data availability statement
The original contributions presented in the study are included in the article/supplementary material, further inquiries can be directed to the corresponding author.
Author contributions
WT: Writing – original draft, Validation, Writing – review and editing, Data curation. MX: Writing – review and editing, Methodology, Conceptualization. XF: Writing – review and editing. CH: Writing – review and editing, Investigation. CM: Visualization, Writing – review and editing. YC: Writing – review and editing.
Funding
The author(s) declare that financial support was received for the research and/or publication of this article. This work was supported by the National Natural Science Foundation of China (No.52378426), Natural Science Foundation of Hunan Province (No. 2025JJ60272), Distinguished Young Scholars of Changsha city Bureau (kq2209017), Science and technology innovation Program of Hunan Province (No. 2023RC3160), and the projects of water conservancy science and technology in Hunan Province (XSKJ2024064-48, XSKJ2023059-02). The corresponding author gratefully acknowledges this financial support.
Conflict of interest
Author WT was employed by Hunan Urban and Rural Environmental Construction Co., Ltd. Author CH was employed by Hunan Construction Investment Group Infrastructure Investment Company.
The remaining authors declare that the research was conducted in the absence of any commercial or financial relationships that could be construed as a potential conflict of interest.
Generative AI statement
The author(s) declare that no Generative AI was used in the creation of this manuscript.
Publisher’s note
All claims expressed in this article are solely those of the authors and do not necessarily represent those of their affiliated organizations, or those of the publisher, the editors and the reviewers. Any product that may be evaluated in this article, or claim that may be made by its manufacturer, is not guaranteed or endorsed by the publisher.
References
Ahmad, S., Rizvi, Z., Khan, M. A., Ahmad, J., and Wuttke, F. (2019). Experimental study of thermal performance of the backfill material around underground power cable under steady and cyclic thermal loading. Mater. today Proc. 17, 85–95. doi:10.1016/j.matpr.2019.06.404
Ahmad, S., Rizvi, Z. H., Arp, J. C. C., Wuttke, F., Tirth, V., and Islam, S. (2021). Evolution of temperature field around underground power cable for static and cyclic heating. Energies 14 (23), 8191. doi:10.3390/en14238191
Ahmad, S., Rizvi, Z. H., and Wuttke, F. (2025). Unveiling soil thermal behavior under ultra-high voltage power cable operations. Sci. Rep. 15 (1), 7315. doi:10.1038/s41598-025-91831-1
Alsabhan, A. H., Sadique, M. R., Ahmad, S., Alam, S., and Binyahya, A. S. (2021). The effect of opening shapes on the stability of underground tunnels: a finite element analysis. GEOMATE J. 21 (87), 19–27. doi:10.21660/2021.87.j2267
Bai, Y. (2001). “New technologies for seepage prevention and reinforcement of Chinese dams,” in Beijing, China: water resources and electric power. Press 404. 200109. (in Chinese).
Bruce, D. A., Greene, B. H., Craig, F. R., Williams, B. E., Williams, J. H., and Mickwee, R. L. (2017). Long-term grouting of a karst foundation at logan Martin dam, Alabama. Grouting, 47–57. doi:10.1061/9780784480786.005
Feng, S. (2015). Experimental study on deterioration of clay-cement grout under erosion conditions. Changsha, China: Changsha University of Science and Technology. (in Chinese).
Fu, P., Xing, Z., and Yang, X. (2013). “Experimental research on durability of dam foundation curtains under low-alkalinity soft water conditions,” in Foundation engineering technology for water resources and hydropower projects 2013-proceedings of the 12th national conference of Chinese hydraulic engineering society. Editor K. F. Xia (Beijing: China Water and Power Press), 41–47. (in Chinese).
Haroon, A., Ahmad, S., and Hussain, A. (2017). CFD prediction of loss coefficient in straight pipes development of water resources in India. Springer International Publishing, 477–485.
He, S. (2019). Experimental study on dissolution properties of mineral admixture concrete under soft water conditions. Nanjing, China: Nanjing University of Science and Technology. (in Chinese).
Jiang, X., Yang, C., Wen, J., and Shi, Z. (2014). Water temperature variation and influencing factors in lakes/reservoirs of Changsha region. J. Hunan Univ. Nat. Sci. 41 (9), 93–99. (in Chinese). doi:10.3969/j.issn.1674-2974.2014.09.015
Lindvall, A. (2007). Chloride ingress data from field and laboratory exposure-Influence of salinity and temperature. Cem. Concr. Compos. 29 (2), 88–93. doi:10.1016/j.cemconcomp.2006.08.004
Liu, S. (2004). Study on curtain grouting in karst areas. Changchun, China: Jilin University. (in Chinese).
Liu, Y. (2019). Mechanical performance degradation and durability of grouted soils under seawater erosion conditions. Jinan, China: Shandong University. (in Chinese).
Ministry of Construction of the People's Republic of China (2019). GB/T 50081-2019 Standard for test methods of concrete physical and mechanical properties. Beijing: China Architecture and Building Press. (in Chinese).
Ministry of Transport of the People's Republic of China (2019). TS/T 236-2019 Technical specification for concrete testing in water transport engineering. Beijing: China Communications Press. (in Chinese).
Mozafari, M., Milanović, P., and Jamei, J. (2021). Water leakage problems at the Tangab Dam Reservoir (SW Iran), case study of the complexities of dams on karst. Bull. Eng. Geol. Environ. 80 (10), 7989–8007. doi:10.1007/s10064-021-02387-z
Pan, H., Cai, H., Wang, B., Zhang, P., and Yao, Y. (2023). Evolution characteristics of water temperature in Dongting Lake from 1973 to 2020. J. Lake Sci. 35 (1), 326–337. doi:10.18307/2023.0125 (in Chinese)
Rizvi, Z. H., Mustafa, S. H., Sattari, A. S., Ahmad, S., Furtner, P., and Wuttke, F. (2020a). “Dynamic lattice element modelling of cemented geomaterials,” in Advances in computer methods and geomechanics: IACMAG symposium 2019 volume 1 (Singapore: Springer), 655–665.
Rizvi, Z. H., Shrestha, D., Sattari, A. S., and Wuttke, F. (2018). Numerical modelling of effective thermal conductivity for modified geomaterial using lattice element method. Heat Mass Transf. 54, 483–499. doi:10.1007/s00231-017-2140-2
Rizvi, Z. H., Zaidi, H. H., Akhtar, S. J., Sattari, A. S., and Wuttke, F. (2020b). Soft and hard computation methods for estimation of the effective thermal conductivity of sands. Heat Mass Transf. 56, 1947–1959. doi:10.1007/s00231-020-02833-w
Sha, F., and Fan, G. X. (2021). Durability of a novel effective microfine cementitious grouting material in corrosion environments. Constr. Build. Mater. 306, 124842. doi:10.1016/j.conbuildmat.2021.124842
Tang, Y. (2019). Failure mechanisms and performance evaluation of cement-based materials under dissolution and chloride erosion. Nanjing, China: Nanjing University of Science and Technology. (in Chinese).
Tu, P. (2012). Experimental study and theoretical evaluation on durability of grouted soils. Central South University. (in Chinese).
Verma, D., Berwal, P., Khan, M. A., Alharbi, R. S., Alfaisal, F. M., and Rathnayake, U. (2023). Design for the prediction of peak outflow of embankment breaching due to overtopping by regression technique and modelling. Water 15 (6), 1224. doi:10.3390/w15061224
Wang, H. (2019). Grouting diffusion reinforcement and degradation mechanisms in sand layers under seawater erosion-seepage interactions. Shandong, China: Shandong University. (in Chinese).
Wang, H., Li, Z., Wang, X., Zhang, Q., and Zhang, L. (2021). Study on grouted body deterioration mechanism of sand layer in seawater environment. Adv. Mater. Sci. Eng. 2021, 1–8. doi:10.1155/2021/6329257
Wang, H. B., Liu, Q. W., Sun, S. Q., Zhang, Q., Li, Z., and Zhang, P. (2020). Damage model and experimental study of a sand grouting-reinforced body in a seawater environment. Water 12 (9), 2495. doi:10.3390/w12092495
Wang, P., Mo, R., Sui, X., Tian, L., Xu, J., and Jin, Z. (2022). Research progress on chemo-damage-transport models for coupled chloride-sulfate attack in concrete. J. Chin. Ceram. Soc. 50 (2), 512–521. (in Chinese).
Wang, T. (2016). Numerical simulation and analysis of chloride ion diffusion in marine environment concrete. Ganzhou, China: Jiangxi University of Science and Technology. (in Chinese).
Wei, G., Feng, F. F., Huang, S. Y., Xu, T. B., Zhu, J. X., Wang, X., et al. (2025). Full-scale loading test for shield tunnel segments:Load-bearing performance and failure patterns of lining structures. Underground Space 20, 197–217. doi:10.1016/j.undsp.2024.05.003
Xie, Y., Qu, T., Yang, J., Wang, S., Zhao, J., et al. (2025). Multiscale insights into tunneling-induced ground responses in coarse-grained soils. Computers and Geotechnics 185, 107319. doi:10.1016/j.compgeo.2025.107319
Yu, H. (2017). Macro-micro damage mechanisms of concrete under different salt erosion types. Changchun, China: Jilin University. (in Chinese).
Yu, H., and Sun, W. (2006). Theoretical model of chloride ion diffusion in concrete. J. Southeast Univ. Nat. Sci. Ed. (S2), 68–76. (in Chinese).
Yu, R., Tong, X., Ding, M., Qian, D., and Zhou, F. (2020). Degradation mechanisms and countermeasure analysis of concrete materials in underground environments. Prot. Eng. 42 (1), 70–78. (in Chinese).
Zhou, D., Shen, Z., Ma, B., and Zhang, K. (2022). Distribution law of mass loss in concrete dams under permeation and dissolution effects. Adv. Sci. Technol. Water Resour. 42 (2), 72–78. doi:10.3880/j.issn.1006-7647.2022.02.011 (in Chinese)
Keywords: karst, grouting curtain, erosion effect, performance degradation, grouted stone
Citation: Tang W, Xie M, Fang X, Huang C, Mo C and Chen Y (2025) Experimental investigation on the performance degradation of grouting materials in karst erosion environment. Front. Earth Sci. 13:1603845. doi: 10.3389/feart.2025.1603845
Received: 01 April 2025; Accepted: 05 May 2025;
Published: 20 May 2025.
Edited by:
Tongming Qu, Hong Kong University of Science and Technology, Hong Kong SAR, ChinaReviewed by:
Jiawei Xie, The University of Newcastle, AustraliaZarghaam Rizvi, GeoAnalysis Engineering GmbH, Germany
Sun Rui, Anhui University of Science and Technology, China
Jie Li, East China Jiaotong University, China
Copyright © 2025 Tang, Xie, Fang, Huang, Mo and Chen. This is an open-access article distributed under the terms of the Creative Commons Attribution License (CC BY). The use, distribution or reproduction in other forums is permitted, provided the original author(s) and the copyright owner(s) are credited and that the original publication in this journal is cited, in accordance with accepted academic practice. No use, distribution or reproduction is permitted which does not comply with these terms.
*Correspondence: Xinghua Fang, eGhmYW5nOTVAMTYzLmNvbQ==