- Centre National de la Recherche Scientifique, Institut de Recherches sur la Catalyse et l'Environnement de Lyon, UMR 5256, Université de Lyon, Université Claude Bernard Lyon 1, Villeurbanne, France
A new kind of electrochemical catalyst based on a Pt porous catalyst film deposited on a β″-Al2O3 ceramic Ag+ conductor was developed and evaluated during propane oxidation. It was observed that, upon anodic polarization, the rate of propane combustion was significantly electropromoted up to 400%. Moreover, for the first time, exponential increase of the catalytic rate was evidenced during galvanostatic transient experiment in excellent agreement with EPOC equation.
Introduction
Ionic conductors (i.e., materials that can selectively transport ions, also called electrolytes) are widely used in batteries, fuel cells, sensors and in gas separation technologies. Solid electrolytes with conducting ions of O2−, H+, Li+, K+, Na+, Ag+, F−, Cu+, or Cl− have been reported in the last decades (Hamann et al., 1998; Vayenas et al., 2001; Vielstich et al., 2003; Vernoux et al., 2013). The importance of these materials as catalytic carriers in heterogeneous catalysis has been obvious since the demonstration by Vayenas and coworkers (Vayenas et al., 2001; Vayenas, 2011; Vernoux et al., 2013) that the conducting ionic species can significantly promote the catalytic activity of metal or metal oxide nanoparticles, via the non-Faradaic Electrochemical Modification of Catalytic Activity (NEMCA) effect, also called Electrochemical Promotion of Catalysis (EPOC).
In EPOC studies, the catalyst active phase (conductive catalyst-electrode) is in contact with an ionic conductor-support (in an electrochemical cell configuration). Application of electrical currents or imposition of potentials between the catalyst film and a counter electrode (catalytically inactive) can cause significant alterations in catalytic properties (Vayenas et al., 2001; Vayenas, 2011; Vernoux et al., 2013).
A key parameter in EPOC studies is the catalyst potential UWR. The subscript “WR” denotes the potential of the working (“W”) electrode (which also serves as the catalyst) with respect to a reference “R” electrode. Experimental (i.e., in situ work function measurements) (Vayenas et al., 1990, 2001; Tsiplakides and Vayenas, 2001) and theoretical studies (Tsiplakides and Vayenas, 2001; Riess and Vayenas, 2003) have shown that there exists (over wide temperature ranges) an one-to-one correlation between the change in UWR and the concomitant change in the work function, Φ, of the gas exposed, i.e., catalytically active, catalyst surface:
Thus, in electrochemical promotion studies, upon varying the catalyst potential, UWR, the catalyst work function, Φ, is also modified. Increasing coverage of electron acceptor (electronegative) promoting species increases the catalyst potential and work function while increasing coverage of electron donor (electropositive) promoting species decreases both the catalyst potential and the work function (Stoukides and Vayenas, 1981; Vayenas et al., 2001).
Since the discovery of EPOC in the early 80 s (Stoukides and Vayenas, 1981), more than 100 different catalytic systems (oxidations, hydrogenations, dehydrogenations, isomerizations, decompositions) have been electrochemically promoted on Pt, Pd, Rh, Ag, Au, Ni, IrO2, RuO2 catalysts deposited on O2− (YSZ), Na+ (β″-Al2O3, NaSiCon), K+ (β″-Al2O3), H+ (CaZr0.9In0.1O3−α, Nafion), F− (CaF2), aqueous, molten salt and mixed ionic-electronic (TiO2, CeO2, La0.6Sr0.4Co0.2Fe0.8O3−δ/Ce0.9Gd0.1O1.95 composite) conductors (Vayenas et al., 2001; Katsaounis, 2010; Kambolis et al., 2012; Vernoux et al., 2013). EPOC does not seem to be limited to any specific type of catalytic reaction, metal catalyst or solid electrolyte, therefore, the investigation of new materials regarding the electrolyte, the promoting agent and the active catalyst phase, is very challenging. Moreover, the knowledge obtained from EPOC studies can be transferred in dispersed catalysts in terms of choosing the support for a specific reaction by choosing the appropriate ionic agent (Vernoux et al., 2009, 2013).
Silver catalysts have found excellent application to ethylene epoxidation (Dadyburjor et al., 1979; Ayame et al., 2003) and hold great promise for the SCR of NOx with hydrocarbons (Burch et al., 2002; Shimizu and Satsuma, 2006). However, sintering is a serious issue for silver catalysts (Presland et al., 1972; Plummer et al., 1987; Ruckenstein and Lee, 1988), and a complex array of factors have been linked to sintering, including the reaction gas environment (Ruckenstein and Lee, 1988), support effects (Bird et al., 2000), and surface binding and mobility (Meyer et al., 2007).
This work presents, for the first time, attempts to develop an electrochemical catalyst which allows transportation of Ag+ between the solid electrolyte and the Pt film. This provides a controlled, reversible, and reproducible way of altering the surface composition. The idea of this study is to utilize the phenomenon of EPOC to electrochemically control the transportation of Ag+ cations between the solid electrolyte and the catalyst film. Propane combustion was used as model reaction. This reaction is well-studied in the field of EPOC on Pt electrochemical catalysts deposited on O2− and Na+ conductors. Therefore, a Pt catalyst film was deposited on β″-Al2O3 (Ag+). Moreover, the use of Pt film instead of Ag allows the discrimination of species coming from the support.
Experimental
The electrochemical catalyst (Figure 1) consisted of a β″-Al2O3 pellet (Ionotec Ltd) Ag+ conductor, covered on both sides by three electrodes; the working-catalyst, the counter and the reference electrode. The Pt working electrode (0.8 cm2 geometric surface area and 1.9 mg loading) was deposited by application of metalorganic platinum paste (Engelhard-Clal 6926) and catalytically inactive gold counter (symmetrical to working). Reference and counter electrodes were deposited on the other side of the pellet by application of metalorganic paste, followed by calcination in air for 2 h at 450°C. The reference electrode was deposited close enough (about 3 mm) to the counter-electrode avoiding any electrical perturbation. A galvanostat/potentiostat Voltalab PGP 201 (Radiometer) was used in order to apply and measure both potential and current in the electrochemical catalyst. Voltage and current were applied and measured according to the procedure generally used in conventional three-electrode electrochemical cells. The catalyst potential, UWR, was measured between the working electrode and the reference electrode (Au) which may be considered as a pseudoreference since its potential does not vary significantly with the composition of the gaseous mixture, as experimentally checked.
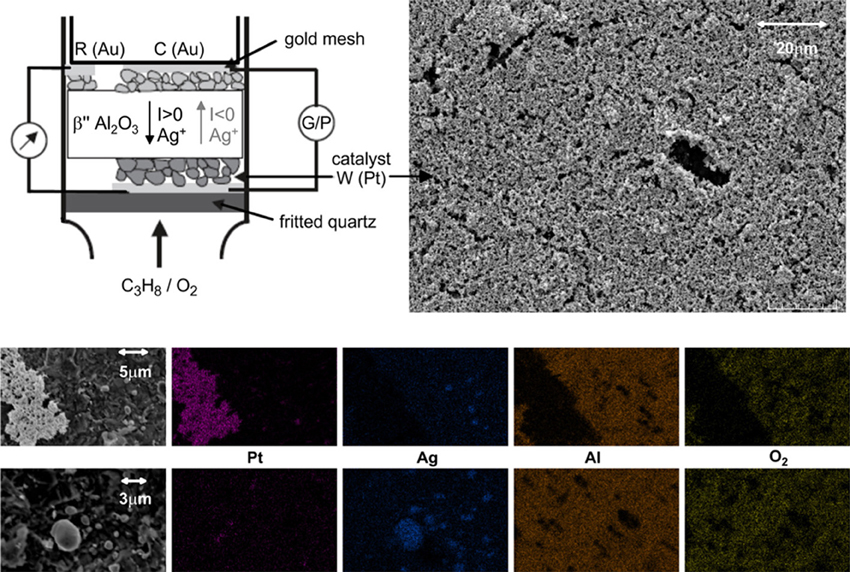
Figure 1. Schematic drawing of the electrochemical catalyst Pt/β″-Al2O3 (Ag+) placed in the quartz reactor (the galvanostat/potentiostat is denoted as G/P) and SEM micrograph of the catalyst porous Pt film, and X-ray mapping of Pt, Ag, Al, and oxygen at two different areas of the electrode-catalyst surface.
The presence of silver in the interface of the Pt porous catalytic film and the β″-Al2O3 support was confirmed by SEM-EDX analysis carried out over the sample after catalyst performances measurements. Before the SEM-EDX analysis, the sample was cooled down under the reaction conditions from 400°C to room temperature. During this period, the sample was under positive polarization of UWR = +2V. Figure 1 shows a SEM micrograph of the Pt film and a zoom in areas where the Pt film is open to the support. Figure 1 also includes a mapping of two regions for Pt, Ag, Al, and O2. From the mapping of elements, one can conclude that silver particles cover the area between the Pt and the β″-Al2O3. The presence of silver species in this interface can be attributed to surface diffusion during annealing the catalyst which is enhanced by the presence of oxygen (Presland et al., 1972; Baker and Skiba, 1977).
The catalytic performances of the electrochemical catalyst was evaluated in a quartz reactor, which was designed to facilitate the connection between the electrodes and the galvanostat/potentiostat, allowing the reactive mixture to reach the electrocatalyst surface. The temperature was measured with a K-type thermocouple placed in proximity to the working electrode surface. The reaction gases were mixtures of C3H8 (Air Liquide, 8000 ± 80 ppm), O2 (Air Liquide, 99.95%) and He (Air Liquide, 99.999%) as the vector gas. The gas composition was controlled by mass flow controllers (Brooks), with accuracy of 1%. The reaction products were analyzed by an on-line micro gas-chromatograph (R3000 SRA Instruments) and a CO2 IR analyzer (Horiba VA 3000). The C3H8 partial pressure in the feed was held constant during all the experiments at 0.24 kPa. The O2 partial pressure in the feed was kept at 1.2 kPa with total gas flow rate of 12 L/h. Carbon monoxide was never detected, according to our 10 ppm lower detection limit.
In order to quantify the magnitude of EPOC, three parameters are commonly used. First, the rate enhancement ratio, ρ:
second the apparent Faradaic efficiency, Λ:
and third the promotional index, PIAg:
where r is the electropromoted catalytic rate, ro the open-circuit catalytic rate, I the applied current, and n the number of exchanged electrons during the electrode reaction, F is the Faraday's constant and θAg the coverage of the Ag coverage onto the catalyst surface induced by the backspillover of Ag+ ions from the electrolyte.
When the promoting species can take part in the reaction (e.g., O2− in an oxidation reaction or H+ in a hydrogenation reaction), the Faradaic efficiency reveals if the process is (sub)Faradaic (i.e., Λ ≤ 1) or if the catalytic reaction exhibits NEMCA behavior (i.e., |Λ| > 1). However, in the case of promoting species that cannot participate in the reaction (e.g., K+, Na+, or Ag+), the Faradaic efficiency has no significant meaning and the promotional index is used. Upon applying a positive (negative) current, the Ag+ cations are removed (supplied) from (to) the Pt catalyst surface and, in this way, the θAg is decreased (increased).
Results and Discussion
Electrochemical Catalyst Characterization
The dispersion of the Pt film after catalysis was determined by measuring its reactive oxygen uptake at 400°C via the isothermal titration technique (Vayenas et al., 2001). The electrochemical catalyst was first exposed to O2 for 1 h, then purged with pure He for several times, tHe, longer (>10 times) than the reactor residence time (~0.5 min) to remove gaseous O2. Subsequently, the reactor was exposed to C3H6, and the amount of oxygen remaining on the Pt surface (NO) was obtained by integrating the area of the CO2 peak in the reactor effluent (Figure 2). The same procedure was repeated several times by varying the value of tHe. In this way, one can study the kinetics of oxygen desorption and obtains the reactive oxygen catalyst uptake, NG, by extrapolating NO at tHe = 0. Figure 2 shows the results of the surface titration measurements at 400°C. The reactive oxygen uptake was NG = 5.2 μ mol O. If we attributed this oxygen adsorption only to Pt, this led to a metal dispersion of 50%. This value of dispersion is around two orders of magnitude higher than the values usually observed in electrochemical catalysts (dispersion <0.5%) prepared with similar way (i.e., organometallic paste application annealed at high temperature) (Vayenas et al., 2001). This may indicate that a part of the adsorbed oxygen must be attributed to the presence of silver species in the catalyst/electrolyte interface, and that O-Ag-Pt complexes probably exist. Moreover the dissolution of oxygen on Ag, because of the finite solubility of oxygen in Ag, maybe plays a key role in this system.
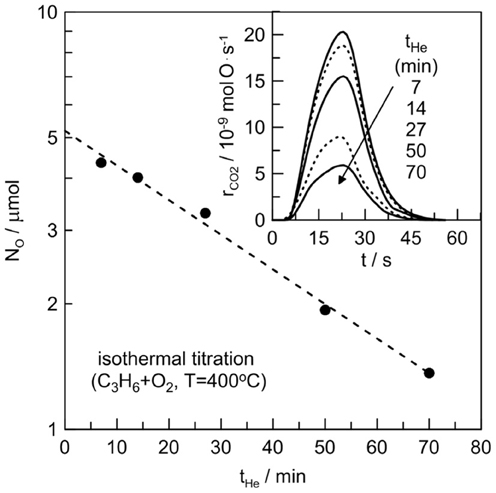
Figure 2. Isothermal surface titration of oxygen by C3H6 at 400°C. Effect of oxygen desorption time, tHe, on the mass of reactive oxygen adsorbed on the Pt/β″-Al2O3 (Ag+) electrochemical catalyst. CO2 peaks for each tHe are also depicted in the index.
The slope in the isothermal titration experiment is also peculiar if we consider that oxygen is only adsorbed on a Pt free of Ag catalyst surface. Indeed, even after 70 min purging with Helium (i.e. tHe = 70 min) significant amount of oxygen remains onto the catalyst surface (index of Figure 2). For instance, the titration of a Pt/Al2O3(K+) electrochemical catalyst, (sintered at the same temperature than the electrochemical catalyst of this work) performed at 350°C using C3H6 (de Lucas-Consuegra et al., 2007) gives a the desorption constant, kd, of 5.7·10−8 molO/s. In the electrochemical catalyst of the present study, at 400°C, the desorption constant is 50 times smaller (i.e., kd = 0.11·10−8 molO/s). This provides another insight that silver species play an important role in this electrochemical catalyst.
Catalytic Activity Measurements
Galvanostatic transient experiment
Figure 3 shows the catalytic rate and potential responses to step changes of a small (+175 nA) current application as well as a negative (−2V) potential imposition during C3H8 oxidation on Pt/β″-Al2O3 (Ag+) at 375°C. Initially (t < 0), the electrical circuit is open and the open-circuit (unpromoted) catalytic rate is 4.0 · 10−8 molO/s. At t = 0, a small positive current (I = +175 nA) is applied between the working and counter electrodes and thus Ag+ are removed from the catalyst surface, at the rate I/F = 1.8 · 10−12 mol/s. This causes (after 1 h) a nearly 70% enhancement in the catalytic rate (ρ = 1.7). The rate increase, Δr, is 31,200 times larger than the rate of Ag+ removal from the catalyst surface, thus the apparent Faradaic efficiency Λ equals 31,200, while the promotional index is equal to 1160, however, this value is calculated with the NG value extracted by the surface titration. Upon current interruption (t = 60 min), the catalytic rate decays to a slightly higher value (4.2 · 10−8 molO/s) than its initial value over a relaxation time period of several minutes (90 min).

Figure 3. Catalytic rate and potential responses to step changes of a small (+175 nA) current application and a negative (−2V) potential imposition during C3H8 oxidation on Pt/β″-Al2O3 (Ag+) at 375°C. Reactive mixture: C3H8/O2: 2400 ppm/1.2%. Overall flow: 12 L/h.
The catalyst potential, UWR, rapidly decays to a value of −145 mV, which is higher than the initial (before polarization) one of −215 mV. When the current application is interrupted, the Ag+ ions cannot totally return to the catalyst surface and this causes this difference in the open-circuit values of the catalytic rate and potential between before and after polarization. This behavior has been also observed in EPOC studies with Na+ and K+ conductors (de Lucas-Consuegra et al., 2007; Kotsionopoulos and Bebelis, 2007), where it was observed that potentiostatic imposition for several minutes can force alkali ions to move and this finally can restore the catalytic rate to its initial value.
Imposition of −2V between the working and the counter electrodes for 30 min was enough for restoring the initial state catalytic rate and after potential interruption the catalyst potential also returned to its initial value. In general the initial state depends on the initial Ag+ coverage and thus in the previous catalyst history, however, in this case the system after negative polarization returns to the same state.
Propane oxidation on Pt/β″-Al2O3 (Ag+) exhibits electrophobic behavior (i.e., the catalytic rate increase upon positive overpotential) as reported with Pt/β″-Al2O3 (Na+) and Pt/YSZ(O2−) electrochemical catalysts at stoichiometric conditions (Vernoux et al., 2002; Bultel et al., 2004; Kokkofitis et al., 2005, 2007; Kotsionopoulos and Bebelis, 2007; Kambolis et al., 2012). As reported in the literature (Vernoux et al., 2002; Bultel et al., 2004; Kokkofitis et al., 2005, 2007; Kotsionopoulos and Bebelis, 2007) propane and oxygen adsorb competitively on Pt catalyst surface and, as a result, a Langmuir–Hinshelwood type kinetic behavior is observed. Competitive adsorption of oxygen and propane strongly favors oxygen (Vernoux et al., 2002; Bultel et al., 2004; Kotsionopoulos and Bebelis, 2007). This explains positive reaction orders with respect to propane and zero or negative reaction orders with respect to oxygen, reported in the literature (Vernoux et al., 2002; Bultel et al., 2004; Kokkofitis et al., 2005, 2007; Kotsionopoulos and Bebelis, 2007). Therefore, propane deep oxidation on Pt is limited by the propane adsorption. Anodic polarization weakens the Pt-O bonds and therefore increases the propane coverage on the catalyst surface, which simultaneously improves the reaction kinetics.
EPOC equation for rate dependence on catalyst potential
A noteworthy aspect of the galvanostatic rate transient, depicted in Figure 3, is that, during the current application (t = 0–60 min), the catalyst potential increases almost linearly with the time (except from the initial abrupt increase of 150 mV due to the ohmic losses). This trend is due to extremely low current (near to equilibrium) and absence of parasitic effects of electrode reactions. The catalytic rate starts to increase when the catalyst potential exceeds 1 V (t = 15 min) and above 2 V (t = 45 min) this increase is exponential with time (the rCO2 scale is logarithmic).
This behavior (rate exponential increase with time) is, for the first time, observed in galvanostatic EPOC experiments although this in excellent agreement with EPOC theory. EPOC literature (Ladas et al., 1991; Vayenas et al., 2001; Tsampas et al., 2009) has shown that, quite often, over relatively wide (e.g., 0.3–0.5 V) ranges of potential, the catalytic rates depend on catalyst-electrode potential in an exponential manner, similar to the high field approximation of the Butler-Volmer equation, i.e., (Bockris et al., 2000):
where ro is the unpromoted (i.e., open-circuit) catalytic rate, kb is the Boltzmann's constant, ΔUWR is the applied overpotential, ΔΦ is the overpotential-induced change in the catalyst electrode work function and αN (typically |αN| ≈ 0.2–1) is a parameter which is positive for electrophobic reactions (∂r/∂Φ > 0). The second equality (5) holds because as shown both theoretically and experimentally [by means of Kelvin probe and UPS work function measurements (Vayenas et al., 1990; Tsiplakides and Vayenas, 2001)], the equality:
is valid over wide (e.g., 0.5–1 V) catalyst-electrode potential ranges in solid state electrochemistry.
The catalyst potential of the system examined in the present work, linearly increases with time. Therefore, if one considers that the Equation (1) is valid over a potential range, then the work function will also linearly increase with the time and according to Equation (5) the catalytic rate will increase exponentially with the time (as it is experimentally observed).
The slopes of the catalyst potential and rate (in logarithmic scale) of Figure 3 are ΔUWR/Δt = 1 mV/s and Δ1nr/Δt = 3.7 · 10−4 s−1. They are constant for a wide range of time. Therefore, the slope Δ1nr/ΔUWR is equal to 3.7 · 10−4 mV−1. Combining Equation (5) and this value, one can find that αN = 0.82.
The dipole moment of Ag on Pt can be extracted from the data depicted in Figure 3 according to the following procedure. From Faraday's law, it is known that during a galvanostatic experiment the rate of Ag coverage on the catalyst surface is given by Equation (6).
In general the variation in the work function, Φ, with the coverage, θj, of an adsorbate is described by the Helmholtz equation:
where e = 1.6·10−19 C, εo = 8.85·10−12 C2/J·m, NM is the surface atom density (e.g., for Pt is 1.53 · 1019 atom/m2) of the surface under consideration and Pj (C·m) is the dipole moment of adsorbate j in the adsorbed state. In a differential form Equation (7) can be written as following:
By combining Equations (6) and (8), one can find the following expression for the dipole moment (assuming that it is constant):
As it is already mentioned, the NG value measured with isothermal titration is overestimated by a factor of 100. Therefore, using this value in Equation (10) gives an overestimated value for the dipole moment of Ag on Pt, closed to 490 D. But, if we assume dispersion of the order of 0.5%, in relative agreement with literature data (Vayenas et al., 2001), the previous value becomes 4.9 D and also the promotional index is equal to 11.6.
Potentiostatic transient experiments
The catalytic rate response to a step change of a 2.5V is presented in Figure 4A for the temperature range of 325–400°C. Electropromotion becomes more pronounced as the temperature increases. The rate enhancement ratio is equal to 1, 1.3, 1.5, and 4 at 325, 350, 3720, and 400°C, respectively. The above exponential catalytic rate dependence on potential (Equation 5) is usually accompanied by linear variations of the catalytic activation energy, E, with potential, ΔUWR (Vayenas et al., 2001; Kotsionopoulos and Bebelis, 2007). Figure 4B presents the Arrhenius plots under open circuit and anodic polarization conditions. The apparent activation energy of the reaction was found to be 49 and 110 kJ/mol during initial state and anodic polarization, respectively.
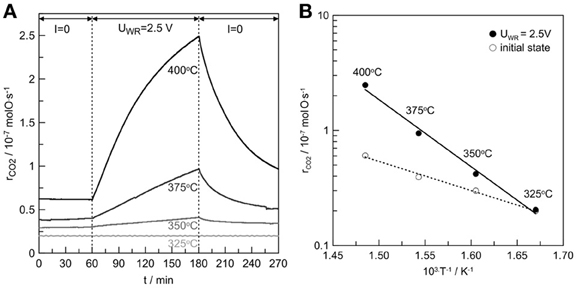
Figure 4. (A) Catalytic rate response to a step change of 2.5V during C3H8 oxidation on Pt/β″-Al2O3 (Ag+) at 325, 350, 375, and 400°C. (B) Arrhenius plots at the initial state and upon anodic polarization (UWR = 2.5 V) conditions. Reactive mixture: C3H8/O2: 2400 ppm/1.2%. Overall flow: 12 L/h.
This increase in the apparent activation energy seems to be in contrast with the EPOC concept which should lower the activation energy (Vayenas et al., 2001; Kotsionopoulos and Bebelis, 2007). This strong enhancement of the activation upon positive polarizations coupled with a drastic increase of the catalytic rate could be linked to a change of the nature of the active sites. By increasing the temperature, the positive polarization could reduce silver oxide into active metallic silver sites with a concomitant generation of oxygen ionic species that can migrate onto the catalyst surface. Therefore, significant rate enhancement can be observed. Clearly further investigations should be performed for obtaining better understanding of the processes related with silver oxide decomposition which could generate promoting ionic oxygen species. However, this study is just the first step of the development of a new generation of electrochemical catalysts.
Conclusions
The development of a new kind of electrochemical catalyst, which permits in situ control of Ag+ species during propane combustion, was investigated. Encouraging results have shown that significant electropromotion of the catalytic performance can be achieved (rate increase up to a factor of 4). During galvanostatic transient, response of catalytic rate is in excellent agreement with NEMCA theory. Indeed, exponential increase of the rate is observed when the potential linearly increases with time for extremely low currents. The origin of the electrochemical activation upon positive polarizations was tentatively attributed to the electrochemical decomposition of silver oxide which could generate promoting ionic oxygen species.
Conflict of Interest Statement
The authors declare that the research was conducted in the absence of any commercial or financial relationships that could be construed as a potential conflict of interest.
Acknowledgments
The authors would like to thank the IRCELYON department of microscopy.
References
Ayame, A., Uchida, Y., Ono, H., Miyamoto, M., Sato, T., and Hayasaka, H. (2003). Epoxidation of ethylene over silver catalysts supported on α-alumina crystal carriers. Appl. Catal. A 244, 59–70. doi: 10.1016/S0926-860X(02)00595-1
Baker, R. T. K., and Skiba, P. (1977). The behavior of silver particles supported on graphite in various gaseous environments. Carbon 15, 233–237. doi: 10.1016/0008-6223(77)90006-9
Bird, D. P. C., de Castilho, C. M. C., and Lambert, R. M. (2000). Catalysts genesis studied by atomic force microscopy. Surf. Sci. 449, L221–L227. doi: 10.1016/S0039-6028(99)01220-0
Bockris, J. O. M., Reddy, A. K. N., and Gamboa-Aldeco, M. (eds.). (2000). “Modern electrochemistry: no. 2A fundamentals of electrodics, no. 2B electrodics,” in Chemistry, Engineering, Biology, and Environmental Science, (New York, NY: Kluwer Academic/Plenum Publishers), 1083–1084.
Bultel, L., Roux, C., Siebert, E., Vernoux, P., and Gaillard, F. (2004). Electrochemical characterization of the Pt/YSZ interface exposed to a reactive gas phase. Solid State Ionics 166, 183–189. doi: 10.1016/j.ssi.2003.09.017
Burch, R., Breen, J. P., and Meunier, F. C. (2002). A review of the selective reduction of NOx with hydrocarbons under lean-burn conditions with non-zeolitic oxide and platinum-group metal catalysts. Appl. Catal. B 39, 283–303. doi: 10.1016/S0926-3373(02)00118-2
Dadyburjor, D. B., Jewur, S. S., and Ruckenstein, E. (1979). Selective oxidation of hydrocarbons on composite oxides. Catal. Rev. 19, 293–350. doi: 10.1080/03602457908068057
de Lucas-Consuegra, A., Dorado, F., Valverde, J. L., Karoum, R., and Vernoux, P. (2007). Low-temperature propene combustion over Pt/K-β Al2O3 electrochemical catalyst: characterization, catalytic activity measurements and investigation of the NEMCA effect. J. Catal. 251, 474–484. doi: 10.1016/j.jcat.2007.06.031
Kambolis, A., Lizarraga, L., Tsampas, M. N., Burel, L., Rieu, M., Viricelle, J. P., et al. (2012). Electrochemical promotion of catalysis with highly dispersed Pt nanoparticles. Electrochem. Commun. 19, 5–8. doi: 10.1016/j.elecom.2012.02.041
Katsaounis, A. (2010). Recent developments and trends in the electrochemical promotion of catalysis (EPOC). J. Appl. Electrochem. 40, 885–902. doi: 10.1007/s10800-009-9938-7
Kokkofitis, C., Karagiannakis, G., and Stoukides, M. (2007). Electrochemical promotion in O2- cells during propane oxidation. Top. Catal. 44, 361–368. doi: 10.1007/s11244-006-0128-0
Kokkofitis, C., Karagiannakis, G., Zisekas, S., and Stoukides, M. (2005). Catalytic study and electrochemical promotion of propane oxidation on Pt/YSZ. J. Catal. 234, 476–487. doi: 10.1016/j.jcat.2005.07.017
Kotsionopoulos, N., and Bebelis, S. (2007). In-situ electrochemical modification of catalytic activity for propane combustion on Pt/β-Al2O3 catalyst-electrodes. Top. Catal. 44, 379–389. doi: 10.1007/s11244-006-0130-6
Ladas, S., Bebelis, S., and Vayenas, C. G. (1991). Work function measurements on catalyst films subject to in situ electrochemical promotion. Surf. Sci. 251–252, 1062–1068. doi: 10.1016/0039-6028(91)91151-M
Meyer, R., Ge, Q., Lockemeyer, J., Yeates, R., Lemanski, M., Reinalda, D., et al. (2007). An ab-initio analysis of adsorption and diffusion of silver atoms on partially hydroxylated α-Al2O3 (001) surfaces. Surf. Sci. 601, 134–145. doi: 10.1016/j.susc.2006.09.028
Plummer, H. K. Jr., Watkins, W. L. H., and Gandhi, H. S. (1987). Characterization of silver catalysts for the oxidation of methanol. Appl. Catal. 29, 261–281. doi: 10.1016/S0166-9834(00)82897-3
Presland, A. E. B., Price, G. L., and Trimm, D. L. (1972). Hillock formation by surface diffusion on thin films. Surf. Sci. 29, 424–434. doi: 10.1016/0039-6028(72)90229-4
Riess, I., and Vayenas, C. G. (2003). Fermi level and potential distribution in solid electrolyte cells with and without ion spillover. Solid State Ionics 159, 313–329. doi: 10.1016/S0167-2738(03)00080-8
Ruckenstein, E., and Lee, S. H. (1988). The behavior of model Ag Al2O3 catalysts in various chemical environments. J. Catal. 109, 100–119. doi: 10.1016/0021-9517(88)90188-1
Shimizu, K., and Satsuma, A. (2006). Selective catalytic reduction of NO over supported silver catalysts-practical and mechanistic studies. Phys. Chem. Chem. Phys. 8, 2677–2695. doi: 10.1039/b601794k
Stoukides, M., and Vayenas, C. G. (1981). The effect of electrochemical oxygen pumping on the rate and selectivity of ethylene oxidation on polycrystalline silver. J. Catal. 70, 137–146. doi: 10.1016/0021-9517(81)90323-7
Tsampas, M. N., Sapountzi, F. M., and Vayenas, C. G. (2009). Electrochemical promotion of CO oxidation on Pt/YSZ: the effect of catalyst potential on the induction of highly active stationary and oscillatory states. Catal. Today 146, 351–358. doi: 10.1016/j.cattod.2009.06.007
Tsiplakides, D., and Vayenas, C. G. (2001). Electrode work function and absolute potential scale in solid-state electrochemistry. J. Electrochem. Soc. 148, E189–E202.
Vayenas, C. G. (2011). Bridging electrochemistry and heterogeneous catalysis. J. Solid State Electrochem. 15, 1425–1435. doi: 10.1007/s10008-011-1336-5
Vayenas, C. G., Bebelis, S., and Ladas, S. (1990). Dependence of catalytic rates on catalyst work function. Nature 343, 625–627. doi: 10.1038/343625a0
Vayenas, C. G., Bebelis, S., Pliangos, C., Brosda, S., and Tsiplakides, D. (2001). Electrochemical Activation of Catalysis: Promotion, Electrochemical Promotion Metal-Support Interactions. New York, NY: KluwerAcademic Publishers/Plenum Press.
Vernoux, P., Gaillard, F., Bultel, L., Siebert, E., and Primet, M. (2002). Electrochemical promotion of propane and propene oxidation on Pt/YSZ. J. Catal. 208, 412–421. doi: 10.1006/jcat.2002.3573
Vernoux, P., Guth, M., and Li, X. (2009). Ionically conducting ceramics as alternative catalyst supports. Electrochem. Solid State Lett. 12, E9–E11. doi: 10.1149/1.3122746
Keywords: EPOC, NEMCA effect, propane combustion, β″-Al2O3 (Ag+) electrochemical catalysts, Ag+ cations
Citation: Tsampas MN, Kambolis A, Obeid E, Lizarraga L, Sapountzi FM and Vernoux P (2013) Electrochemical promotion of propane oxidation on Pt deposited on a dense β″-Al2O3 ceramic Ag+ conductor. Front. Chem. 1:13. doi: 10.3389/fchem.2013.00013
Received: 21 May 2013; Accepted: 06 August 2013;
Published online: 30 August 2013.
Edited by:
Vasile I. Parvulescu, University of Bucharest, RomaniaReviewed by:
Antonio De Lucas Consuegra, University of Castilla La Mancha, SpainConstantinos G. Vayenas, University of Patras, Greece
Dimitrios Tsiplakides, Aristotle University of Thessaloniki, Greece
Copyright © 2013 Tsampas, Kambolis, Obeid, Lizarraga, Sapountzi and Vernoux. This is an open-access article distributed under the terms of the Creative Commons Attribution License (CC BY). The use, distribution or reproduction in other forums is permitted, provided the original author(s) or licensor are credited and that the original publication in this journal is cited, in accordance with accepted academic practice. No use, distribution or reproduction is permitted which does not comply with these terms.
*Correspondence: Philippe Vernoux, Institut de Recherches sur la Catalyse et l'Environnement de Lyon, 2 Avenue Albert Einstein, F-69626 Villeurbanne Cedex, France e-mail:cGhpbGlwcGUudmVybm91eEBpcmNlbHlvbi51bml2LWx5b24xLmZy