- 1School of Materials Science and Engineering, University of Shanghai for Science and Technology, Shanghai, China
- 2Institute for New Energy Materials & Low-Carbon Technologies, School of Materials Science and Engineering, Tianjin University of Technology, Tianjin, China
- 3Research Institute for Structure Technology of Advanced Equipment, School of Mechanical Engineering, Hebei University of Technology, Tianjin, China
- 4Key Laboratory of Advanced Energy Materials Chemistry (Ministry of Education), College of Chemistry, Nankai University, Tianjin, China
Magnesium hydride (MgH2) is regarded as a promising solid-state hydrogen storage material, on account of its moderate price and high gravimetric capacity. However, MgH2's inferior kinetic of hydrogen release impedes its widespread application. In this work, we use core-shell Co@N-rich carbon (CoNC) additive as catalysts to ameliorate the performances of MgH2. The surface morphologic structures and hydrogen desorption kinetics of different MgH2-CoNC composites are systematically studied. We find that MgH2-5 wt% CoNC with carbon contents of 17% (CoNC0) composites exhibit better hydrogen desorption performance. At 325°C, the MgH2-5 wt% CoNC0 composites can release up to 6.58 wt% of H2 in 5 min, which is much higher than 0.3 wt% for pure MgH2. Our results demonstrate that importing the core-shell structured catalysts can effectively enhance the hydrogen release kinetics.
Introduction
Low-cost manufacturing, safe storage, and transportation, as well as the effective conversion of hydrogen are the basic requirements for the realization of the large-scale application of hydrogen energy (Baykara, 2018; Abe et al., 2019; Li A. et al., 2019; Staffell et al., 2019; Wei et al., 2019; Xu et al., 2019). Therefore, it is essential to explore a novel and high-capacity hydrogen storage material. Magnesium hydride (MgH2) has been considered as a promising hydrogen storage material due to its high hydrogen storage amount of 7.6 wt% and high volumetric hydrogen storage density of 110 kg m−3 (Aguey-Zinsou and Ares-Fernandez, 2010; Jeon et al., 2011; Shao et al., 2018; Yartys et al., 2019). However, the high hydrogen desorption temperature, sluggish kinetics, and thermodynamics performances of MgH2 have impeded its further applications.
To enhance the hydrogen adsorption kinetics properties of Mg/MgH2 materials, three different strategies have been investigated to decrease the dehydrogenation temperature: nano-crystallization (Zhu et al., 2011; Lin et al., 2016; Li et al., 2018), alloying with transition metal (Rusman and Dahari, 2016; Wang et al., 2016; Zhong and Xu, 2019), and catalyst additives (De et al., 2016; Zhang et al., 2018; Liu et al., 2019b; Wang et al., 2019; Wang K. et al., 2019; Zhou et al., 2019a,b). Several papers have demonstrated that using proper catalysts is more convenient for practical applications (Zhang et al., 2017, 2019; Huang et al., 2018; Valentoni et al., 2018; Chen et al., 2019; Li B. et al., 2019; Hu et al., 2020). Among the catalyst additives, the prominent catalytic influences of Co metal on enhancing the hydrogen desorption properties of MgH2 have been reported in previous literature (Mao et al., 2010; Novakovic et al., 2010; Verón et al., 2013; Liu et al., 2018, 2019a). Novakovic et al. have reported that the higher number of d-electrons in Co metal has made it superior to Ti in destabilizing MgH2 (Novakovic et al., 2010). Mao et al. proved that the dehydrogenation temperature was lower and the adsorption/desorption kinetics could be enhanced by adding CoCl2 catalyst (Mao et al., 2010). MgH2-Co mixture was reported showing better hydrogen storage properties and high-rate hydrogen adsorption/desorption (Verón et al., 2013). Liu et al. have demonstrated that Co@CNTs nano-catalyst doped into MgH2 played an essential role in improving its hydrogen storage properties (Liu et al., 2018). A novel bi-metallic Co/Pd@B-CNTs catalyst was also reported recently showing excellent catalytic effects of MgH2 at low temperatures (Liu et al., 2019a). Based on literature, the mixture of Co metal and carbon material exhibits effectively catalytic function. It is well-known that the morphology and micro-structure of materials is one of the significant factors to further improve its physical or chemical performance. In comparison with the bulk structure, the core-shell structure exhibits much higher specific surface area for exposed active sites and the more electronic interaction of core and shell material. Different constituent of core and shell can be modulated as a parameter to exhibit the optimal synergistic effect. Herein, we introduced the core-shell Co@N-rich carbon hybrids as catalyst additives into MgH2 system to effectively improve the hydrogen desorption performances of MgH2. The carbon shell can protect Co core from oxidation and aggregation. The core-shell structure could further significantly enhance the intimate interface between Co@C and MgH2, providing more active “catalytic sites” and hydrogen “diffusion channels” to reduce the dehydrogenation temperature. Such benefits of additives with core-shell structure then improve the dehydrogenation kinetics of MgH2. Our study also compared the effect of different carbon contents and found that the MgH2-5 wt% CoNC with the carbon contents of 17% (CoNC0) composites had the lowest dehydrogenation temperature and best dehydrogenation kinetic properties.
Materials and Methods
The chemical agents used in this work were purchased from Adamas. Core-shell Co@N-rich carbon hybrids were synthesized according to our previous work (An et al., 2017). The obtained sample with the carbon contents of 17% was designated as CoNC0, and the sample with the carbon amount of 25% was designated as CoNC1. The purchased MgH2 was mixed with 3 or 5 wt% of CoNC0 and CoNC1 hybrids through ball-milling at room temperature for 5 h at 450 rpm under 2 MPa H2 pressure. The mass ratio of big or small balls and powder was about 40:1.
The surface morphological structures of CoNC and various MgH2-CoNC composites were determined by transmission electron microscopy (TEM). The thermal decomposition of various MgH2-CoNC composites was studied on differential scanning calorimetry (DSC) and temperature programmed desorption (TPD). The test conditions of DSC measurement were as follows: heating rate of 2, 5, 10, and 15°C min−1, shielding and sweeping gas of high-purity Ar with 30 ml min−1 flow rate, respectively. As for TPD, the Ar flow rate was 35.1 ml min−1 and the measured temperature was 50–500°C. The isothermal hydrogen desorption properties were characterized by a self-made Sieverts-type instrument under an initial pressure of 0.05 MPa hydrogen at 275, 300, and 325°C, respectively. After complete dehydrogenation, the pressure increased to 0.08 MPa.
Results and Discussion
Figure 1 displays the DSC curves of pure MgH2 and various MgH2-CoNC composites to investigate the thermal decomposition properties at a heating rate of 5°C min−1. Obviously, the onset and hydrogen desorption temperatures of MgH2-CoNC composites are lower than that of pure MgH2, demonstrating that the addition of CoNC hybrids can improve the hydrogen desorption kinetics of MgH2. The value of the onset and hydrogen desorption temperatures for these MgH2-CoNC composites are listed in Table 1. The onset temperature suggests the dehydrogenation starting. As displayed in Figure 1, there is a broad hydrogen desorption peak during the heating process in MgH2, MgH2-3 wt% CoNC1, MgH2-3 wt% CoNC0, and MgH2-5 wt% CoNC1 composites, suggesting the sluggish hydrogen desorption kinetics. As for the remaining MgH2-5 wt% CoNC0 composites, there is only one sharp peak, located at 307°C, further implying the enhanced hydrogen desorption kinetics. Moreover, there are two endothermic peaks observed in the case of MgH2-3 wt% CoNC1 and MgH2-5 wt% CoNC1 samples. The identification of two peaks may be due to bimodal particle size distribution formed during ball-milling. This issue can be reduced when increasing the ball-milling time.
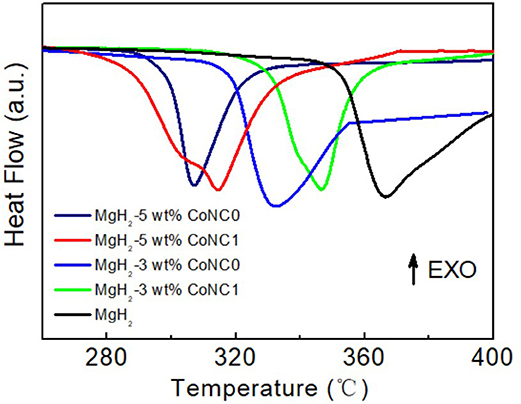
Figure 1. DSC curves of the pure MgH2, MgH2-3 wt% CoNC0, MgH2-5 wt% CoNC0, MgH2-3 wt% CoNC1, and MgH2-5 wt% CoNC1 composites at a heating rate of 5°C min−1.
In order to further illustrate the impacts of the CoNC additives on the hydrogen desorption properties of MgH2, TPD measurements have been conducted (Figure 2). There are two hydrogen desorption peaks of the MgH2-5 wt% CoNC1 composites in the pyrolysis procedure, which can be ascribed to the uneven distribution of the particles after the addition of CoNC1 hybrids (Figure 2A). The peak temperatures of MgH2-5 wt% CoNC0, MgH2-5 wt% CoNC1, MgH2-3 wt% CoNC0, MgH2-3 wt% CoNC1, and pure MgH2 are 293, 304, 324, 336, and 348°C, respectively. Obviously, the peak temperatures of the MgH2-CoNC composites are lower than that of pure MgH2. Similarly, the onset temperatures for the above four composites are lower than that of pure MgH2, illustrating the improved dehydrogenation kinetics. This observation from TPD results is consistent with the DSC results. Compared with the pure MgH2, the dehydrogenation amount of the four MgH2-CoNC composites was almost the same (Figure 2B), due to the fact that the CoNC hybrids are non-active materials for hydrogen adsorption. Among all the samples, the MgH2 with 5 wt% CoNC0 additives exhibits the decreased hydrogen desorption temperature. Therefore, after comprehensive analysis, MgH2-5 wt% CoNC0 composites have been regarded as the optimal material for hydrogen storage in this study.
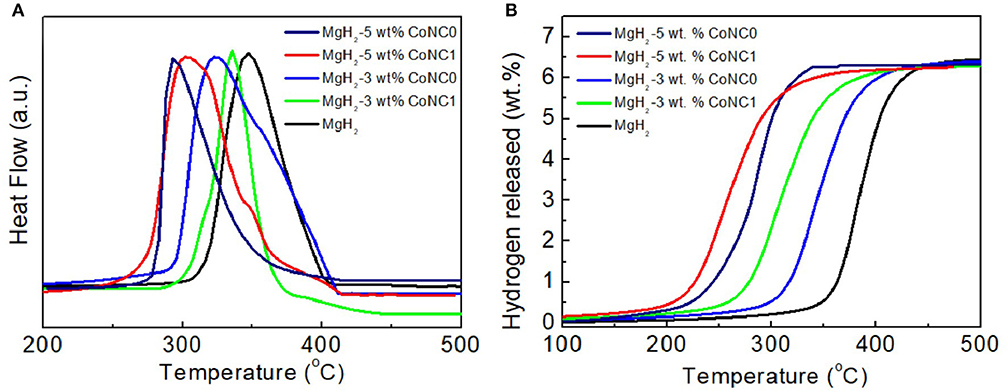
Figure 2. The TPD plots (A) and the corresponding H2 desorption amount curves (B) of the pure MgH2 and MgH2-CoNC composites.
The surface morphological structures of CoNC0 additives and MgH2-5 wt% CoNC0 composites are characterized and the corresponding TEM images are shown in Figure 3. CoNC0 hybrids display a core-shell structure with a Co core (18 nm) coated with N-rich carbon shell. More details on core-shell structure of hybrids are available in our previous report (An et al., 2017). The TEM images of MgH2-5 wt% CoNC0 composites after first dehydrogenation and five cycles are also presented in Figure 3. The MgH2-5 wt% CoNC0 composites after first dehydrogenation (Figure 3b) showed irregular morphologies of accumulated nanoparticles (~30 nm in diameter). Likewise, after five cycles, the anomalous morphology and structure of the MgH2-5 wt% CoNC0 composites have been retained while the size of the nanoparticles have increased apparently (Figure 3c). The morphological changes after dehydrogenation can be explained by the disaggregation, spreading, nucleation, development, and re-separation procedures of the nanoparticles during hydrogen adsorption-desorption process. The interface migration, disintegration, and incorporation of various phases have been referred to this process, in which the formation of metal hydride would lead to the rapid increase of nanoparticle size after several hydrogen adsorption–desorption cycles.
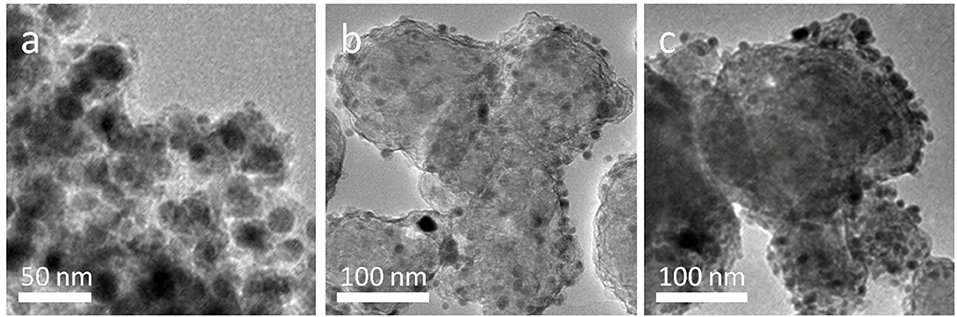
Figure 3. TEM images of CoNC0 (a), MgH2-5 wt% CoNC0 composites after first dehydrogenation (b), and MgH2-5 wt% CoNC0 composites after five dehydrogenation cycles (c).
To gain a deeper understanding on the enhanced dehydrogenation kinetics of MgH2-5 wt% CoNC0 composites, the hydrogen desorption kinetics plots at different temperatures (275, 300, and 325°C) are obtained (Figure 4). At the same temperature (300°C), the dehydrogenation amount of MgH2-5 wt% CoNC0 composites can reach up to 3.49 wt% in 5 min while the amount is only 0.05 wt% for pure MgH2. Even though the reaction time is extended to 50 min, the dehydrogenation amount of pure MgH2 reaches a value of 1.51 wt%, which is still lower than that of MgH2-5 wt% CoNC0 composites in 5 min. The slope for MgH2-5 wt% CoNC0 composites is much larger than that of pure MgH2, further demonstrating that the addition of CoNC0 hybrids has a prominent influence on the dehydrogenation kinetics of pure MgH2. As for MgH2-5 wt% CoNC0 composites, the dehydrogenation temperature has a significant impact on the hydrogen desorption amount. Specifically, the hydrogen desorption amount of MgH2-5 wt% CoNC0 composites at 325 and 275°C are 6.58 wt% and 0.26 wt% in 5 min, respectively, which increases nearly 25 times.
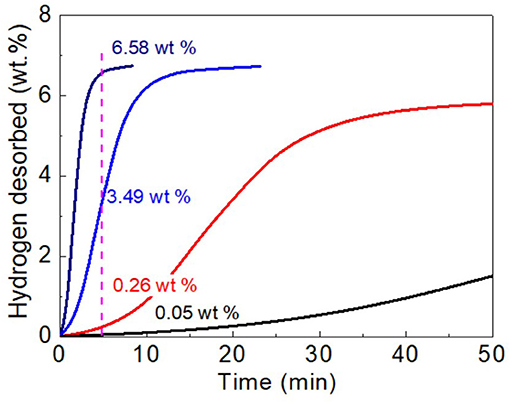
Figure 4. Hydrogen desorption kinetics curves of pure MgH2 at 300°C (black line), MgH2-5 wt% CoNC0 at 275°C (red line), MgH2-5 wt% CoNC0 at 300°C (blue line), and MgH2-5 wt% CoNC0 at 325°C (navy line).
The above results have further demonstrated that the CoNC0 additives could enhance the dehydrogenation kinetic performances of MgH2. Next, the activation energy of hydrogen desorption for MgH2-5 wt% CoNC0 composites is investigated by DSC measurements at various heating rate. There is only one endothermic peak of the MgH2-5 wt% CoNC0 composites at various heating rate (Figure 5A). The temperatures of hydrogen desorption process of MgH2-5 wt% CoNC0 composites are 298, 307, 330, and 354°C at a heating rate of 2, 5, 10, and 15°C min−1, respectively. The activation energy of MgH2-5 wt% CoNC0 composites is then calculated according to the following equation:
According to the fitting result, ln(β/) depends linearly on 1/TP, which is consistent with the Kissinger plot (Figure 5B). Based on the fitted slope of the Kissinger plot and the constant R, the activation energy Ea is determined to be 116 ± 1.4 kJ mol−1. The Ea value of MgH2-5 wt% CoNC0 composites is comparable to the values for the materials reported previously, such as MgH2-10 wt% CoB/CNTs (119 kJ mol−1) (Gao et al., 2017), MgNCG (137 kJ mol−1) (Liu et al., 2016), MgH2-TiN (144 kJ mol−1) (Wang et al., 2015), and MgH2-FeCl3 (130 kJ mol−1) (Ismail et al., 2014). These results further manifest the prominent effects of the Co@C additives on enhancing the dehydrogenation kinetics of pure MgH2. However, the Ea value of MgH2-5 wt% CoNC0 is higher than 53.4 kJ mol−1 of FeCo nanosheets, 67.64 kJ mol−1 of TiO2 nanosheets, 82.2 kJ mol−1 of ZrMn2 nanoparticle, and 99 kJ mol−1 of VNbO5 in the current literature (Valentoni et al., 2018; Yang et al., 2019; Zhang et al., 2019; Zhang M. et al., 2019). Lower activation energies could be due to the intrinsic catalytic activities of different additives with high surface energy. Comparing with many reported dopants, the simple preparation of CoNC composite and relatively inexpensive raw materials in our study may be advantageous to decrease the cost of product for practical application. The properties reported in this work could naturally be enhanced via optimizing the constituent structure, for example, the amount of the Co and the diameter of the core-shell nanoparticles, which will be the future research direction. It is also interesting to fabricate the core-shell structured catalyst additives with high catalytic activity in a simple preparation procedure for the hydrogen energy storage in a future study.
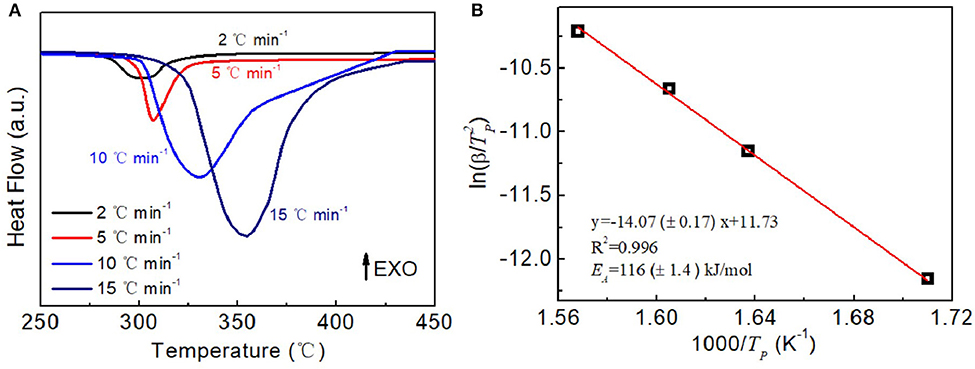
Figure 5. DSC (A) and the fitting Kissinger plots (B) of the MgH2-5 wt% CoNC0 at 2°C min−1, 5°C min−1, 10°C min−1, and 15°C min−1 heating rate.
Conclusion
To summarize, MgH2-x wt% Co@NC (Co@NC0 and Co@NC1) (x = 3, 5) composites were synthesized via ball-milling method. The microstructure, dehydrogenation kinetics of the MgH2-x wt% Co@NC composites and the influences of Co@NC additives on the hydrogen desorption kinetics of MgH2 materials are discussed. Based on the experimental results, the addition of Co@NC additives has promoted the hydrogen desorption kinetics of MgH2. In addition, the MgH2-5 wt% CoNC0 composite exhibits the lowest hydrogenation temperature and maintains a moderate dehydrogenation amount. The MgH2-5 wt% Co@NC0 composites generate 6.58 wt% hydrogen in 5 min at 325°C and 3.49 wt% hydrogen in 5 min at 300°C. Moreover, according to the Kissinger plot, the calculated Ea of the MgH2-5 wt% Co@NC0 composites is about 116 kJ mol−1, indicating that the Co@NC hybrids have effectively promoted the hydrogen adsorption kinetics of MgH2. Our work imports the core-shell microstructure to play a positive role on the hydrogen storage performance of magnesium hydride and then provides useful guidance for the future development of advanced materials for hydrogen storage.
Data Availability Statement
All datasets generated for this study are included in the article/supplementary material.
Author Contributions
KW performed the experiments, analyzed the data, and wrote the original draft. QD designed the experiments and reviewed manuscript. KW and QD revised manuscript. All authors discussed the results and commented on the manuscript.
Conflict of Interest
The authors declare that the research was conducted in the absence of any commercial or financial relationships that could be construed as a potential conflict of interest.
Acknowledgments
All authors thank Prof. Cuihua An for the helpful discussions and the assistance on experiments. KW thanks the support from the Program of Shanghai Pujiang Program (No. 18PJ1409100), the Natural Science Foundation of University of Shanghai for Science and Technology (No. ZR18PY05), and the program for Professor of Special Appointment (Eastern Scholar) at Shanghai Institutions of Higher Learning. QD thanks the support from the Hundred Talents Program of Tianjin University of Technology.
References
Abe, J. O., Popoola, A. P. I., Ajenifuja, E., and Popoola, O. M. (2019). Hydrogen energy, economy and storage: review and recommendation. Int. J. Hydrogen Energy 44, 15072–15086. doi: 10.1016/j.ijhydene.2019.04.068
Aguey-Zinsou, K. F., and Ares-Fernandez, J. R. (2010). Hydrogen in magnesium: new perspectives toward functional stores. Energy Environ. Sci. 3, 526–543. doi: 10.1039/b921645f
An, C. H., Wang, M. Y., Li, W. Q., Deng, Q. B., Wang, Y. J., Jiao, L. F., et al. (2017). Mesoporous Co@N-rich carbon hybrids for a high rate aqueous alkaline battery. Electrochim. Acta 250, 135–142. doi: 10.1016/j.electacta.2017.08.060
Baykara, S. Z. (2018). Hydrogen: a brief overview on its sources, production and environmental impact. Int. J. Hydrogen Energy 43, 10605–10614. doi: 10.1016/j.ijhydene.2018.02.022
Chen, M., Hu, M. M., Xie, X. B., and Liu, T. (2019). High loading nanoconfinement of V-decorated Mg with 1 nm carbon shells: hydrogen storage properties and catalytic mechanism. Nanoscale 11, 10045–10055. doi: 10.1039/C8NR09909J
De, S., Zhang, J. G., Luque, R., and Yan, N. (2016). Ni-based bimetallic heterogeneous catalysts for energy and environmental applications. Energy Environ. Sci. 9, 3314–3347. doi: 10.1039/C6EE02002J
Gao, S. C., Liu, H. Z., Xu, L., Li, S. Q., Wang, X. H., and Yan, M. (2017). Hydrogen storage properties of nano-CoB/CNTs catalyzed MgH2. J. Alloys Compd. 735, 635–642. doi: 10.1016/j.jallcom.2017.11.047
Hu, M. H., Xie, X. B., Chen, M., Zhu, C. X., and Liu, T. (2020). TiCX-decorated Mg nanoparticles confined in carbon shell: preparation and catalytic mechanism for hydrogen storage. J. Alloys Compd. 817:152813. doi: 10.1016/j.jallcom.2019.152813
Huang, X., Xiao, X. Z., Wang, X. C., Wang, C. T., Fan, X. L., Tang, Z. C., et al. (2018). Synergistic catalytic activity of porous rod-like TMTiO3 (TM= Ni and Co) for reversible hydrogen storage of magnesium hydride. J. Phys. Chem. C 122, 27973–27982. doi: 10.1021/acs.jpcc.8b10387
Ismail, M., Juahir, N., and Mustafa, N. S. (2014). Improved hydrogen storage properties of MgH2 Co-doped with FeCl3 and carbon nanotubes. J. Phys. Chem. C 118, 18878–18883. doi: 10.1021/jp5046436
Jeon, K. J., Moon, H. R., Ruminski, A. M., Jiang, B., Kisielowski, C., Bardhan, R., et al. (2011). Air-stable magnesium nanocomposites provide rapid and high-capacity hydrogen storage without using heavy-metal catalysts. Nat. Mater. 10, 286–290. doi: 10.1038/nmat2978
Li, A., Zhu, W. J., Li, C. C., Wang, T., and Gong, J. L. (2019). Rational design of yolk-shell nanostructures for photocatalysis. Chem. Soc. Rev. 48, 1874–1907. doi: 10.1039/C8CS00711J
Li, B., Li, J. D., Zhao, H. J., Yu, X. Q., and Shao, H. Y. (2019). Mg-based metastable nano alloys for hydrogen storage. Int. J. Hydrogen Energy 44, 6007–6018. doi: 10.1016/j.ijhydene.2019.01.127
Li, J. D., Li, B., Shao, H. Y., Li, W., and Lin, H. J. (2018). Catalysis and downsizing in Mg-based hydrogen storage materials. Catalysts 8:89. doi: 10.3390/catal8020089
Lin, H. J., Zhang, C., Wang, H., Ouyang, L. Z., Zhu, Y. F., Li, L. Q., et al. (2016). Controlling nanocrystallization and hydrogen storage property of Mg-based amorphous alloy via a gas-solid reaction. J. Alloys Compd. 658, 272–277. doi: 10.1016/j.jallcom.2016.05.286
Liu, G., Wang, K. F., Li, J. P., Wang, Y. J., and Yuan, H. T. (2016). Enhancement of hydrogen desorption in magnesium hydride catalyzed by graphene nanosheets supported Ni-CeOx hybrid nanocatalyst. Int. J. Hydrogen Energy 41, 10786–10794. doi: 10.1016/j.ijhydene.2016.03.205
Liu, M. J., Xiao, X. Z., Zhao, S. C., Chen, M., Mao, J. F., Luo, B. S., et al. (2019a). Facile synthesis of Co/Pd supporeted by few-walled carbon nanotubes as an efficient bidirectional catalyst for improving the low temperature hydrogen storage properties of magnesium hydride. J. Mater. Chem. A 7, 5277–5287. doi: 10.1039/C8TA12431K
Liu, M. J., Xiao, X. Z., Zhao, S. C., Saremi-Yarahmadi, S., CHen, M., Zheng, J. G., et al. (2018). ZIF-67 derived Co@CNTs nanoparticels: remarkably improved hydrogen storage properties of MgH2 and synergetic catalysis mechanism. Int. J. Hydrogen Energy 44, 1059–1069. doi: 10.1016/j.ijhydene.2018.11.078
Liu, M. J., Zhao, S. C., Xiao, X. Z., Chen, M., Sun, C. H., Yao, Z. D., et al. (2019b). Novel 1D carbon nanotubes uniformly wrapped nanoscale MgH2 for efficient hydrogen storage cycling performances with extreme high gravimetric and volumetric capacities. Nano Energy 61, 540–549. doi: 10.1016/j.nanoen.2019.04.094
Mao, J., Guo, Z., Yu, X., Liu, H., Wu, Z., and Ni, J. (2010). Enhanced hydrogen sorption properties of Ni and Co-catalyzed MgH2. Int. J. Hydrogen Energy 35, 4569–4575. doi: 10.1016/j.ijhydene.2010.02.107
Novakovic, N., Novakovic, J. G., Matovic, L., Manasjevic, M., Radisavljevic, I., Mamula, B. P., et al. (2010). Ab initio calculations of MgH2, MgH2:Ti and MgH2:Co compounds. Int. J. Hydrogen Energy 35, 598–608. doi: 10.1016/j.ijhydene.2009.11.003
Rusman, N. A. A., and Dahari, M. (2016). A review on the current progress of metal hydrides material for solid-state hydrogen storage. Int. J. Hydrogen Energy 41, 12108–12126. doi: 10.1016/j.ijhydene.2016.05.244
Shao, H. Y., He, L. Q., Lin, H. J., and Li, H. W. (2018). Progress and trends in magnesium-based materials for energy-storage research: a review. Energy Technol. 6, 445–458. doi: 10.1002/ente.201700401
Staffell, I., Scamman, D., Abad, A. V., Balcombe, P., Dodds, P. E., Ekins, P., et al. (2019). The role of hydrogen and fuel cells in the global energy system. Energy Environ. Sci. 12, 463–491. doi: 10.1039/C8EE01157E
Valentoni, A., Mulas, G., Enzo, S., and Garroni, S. (2018). Remarkable hydrogen storage properties of MgH2 doped with VNbO5. Phys. Chem. Chem. Phys. 20, 4100–4108. doi: 10.1039/C7CP07157D
Verón, M. G., Condó, A. M., and Gennari, F. C. (2013). Effective synthesis of Mg2CoH5 by reactive mechanical milling and its hydrogen sorption behavior after cycling. Int. J. Hydrogen Energy 38, 973–981. doi: 10.1016/j.ijhydene.2012.10.086
Wang, H., Lin, H. J., Cai, W. T., Ouyang, L. Z., and Zhu, M. (2016). Tuning kinetics and the thermodynamics of hydrogen storage in light metal element based systems- a review of recent process. J. Alloys Compd. 658, 280–300. doi: 10.1016/j.jallcom.2015.10.090
Wang, K., Zhang, X., Ren, Z. H., Zhang, X. L., Hu, J. J., Gao, M. X., et al. (2019). Nitrogen-stimulated superior catalytic activity of niobium oxide for fast full hydrogenation of magnesium at ambient temperature. Energy Storage Mater. 23, 79–87. doi: 10.1016/j.ensm.2019.05.029
Wang, Y., Zhang, Q. Y., Wang, Y. J., Jiao, L. F., and Yuan, H. T. (2015). Catalytic effects of different Ti-based materials on dehydrogenation performances of MgH2. J. Alloys Compd. 645, S509–S512. doi: 10.1016/j.jallcom.2014.12.071
Wang, Z. Y., Zhang, X. L., Ren, Z. H., Liu, Y., Hu, J. J., Li, H. W., et al. (2019). In situ formed ultrafine NbTi nanocrystals from a NbTiC solid-solution MXene for hydrogen storage in MgH2. J. Mater. Chem. A 7, 14244–14252. doi: 10.1039/C9TA03665B
Wei, C., Rao, R. R., Peng, J. Y., Huang, B. T., Stephens, I. E. L., Risch, M., et al. (2019). Recommended practices and benchmark activity for hydrogen and oxygen electrocatalysis in water splitting and fuel cells. Adv. Mater. 31:1806296. doi: 10.1002/adma.201806296
Xu, H. M., Ci, S. Q., Ding, Y. C., Wang, G. X., and Wen, Z. H. (2019). Recent advances in precious metal-free bifunctional catalysts for electrochemical conversion systems. J. Mater. Chem. A 7, 8006–8029. doi: 10.1039/C9TA00833K
Yang, X. L., Ji, L., Yan, N. H., Sun, Z., Lu, X., Zhang, L. T., et al. (2019). Superior catalytic effects of FeCo nanosheets on MgH2 for hydrogen storage. Dalton Trans. 48, 12699–12706. doi: 10.1039/C9DT02084E
Yartys, V. A., Lototskyy, M. V., Akiba, E., Albert, R., Antonov, V. E., Ares, J. R., et al. (2019). Magnesium based materials for hydrogen based energy storage: past, present and future. Int. J. Hydrogen Energy 44, 7809–7859. doi: 10.1016/j.ijhydene.2018.12.212
Zhang, J. G., Shi, R., Zhu, Y. F., Liu, Y. N., Zhang, Y., Li, S. S., et al. (2018). Remarkable synergistic catalysis of Ni-doped ultrafine TiO2 on hydrogen sorption kinetics of MgH2. ACS Appl. Mater. Interfaces 10, 24975–24980. doi: 10.1021/acsami.8b06865
Zhang, L. T., Cai, Z. L., Yao, Z. D., Ji, L., Sun, Z., Yan, N. H., et al. (2019). A striking catalytic effect of facile synthesized ZrMn2 nanoparticles on the de/rehydrogenation properties of MgH2. J. Mater. Chem. A 7, 5626–5634. doi: 10.1039/C9TA00120D
Zhang, L. T., Chen, L. X., Fan, X. L., Xiao, X. Z., Zheng, J. G., and Huang, X. (2017). Enhanced hydrogen storage properties of MgH2 with numberous hydrogen diffusion channels provided by Na2Ti3O7 nanotubes. J. Mater. Chem. A 5, 6178–6185. doi: 10.1039/C7TA00566K
Zhang, M., Xiao, X. Z., Wang, X. W., Chen, M., Lu, Y. H., Liu, M. J., et al. (2019). Excellent catalysis of TiO2 nanosheets with high-surface-energy {001} facets on the hydrogen storage properties of MgH2. Nanoscale 11, 7465–7473. doi: 10.1039/C8NR10275A
Zhong, H. C., and Xu, J. B. (2019). Tuning the de/hydriding thermodynamics and kinetics of Mg by mechanical alloying with Sn and Zn. Int. J. Hydrogen Energy 44, 2926–2933. doi: 10.1016/j.ijhydene.2018.11.173
Zhou, C. S., Bowman, R. C., Fang, Z. Z., Lu, J., Xu, L., Sun, P., et al. (2019a). Amorphous TiCu-based additives for improving hydrogen storage properties of magnesium hydride. ACS Appl. Mater. Interfaces 11, 38868–38879. doi: 10.1021/acsami.9b16076
Zhou, C. S., Fang, Z. G. Z., Sun, P., Xu, L., and Liu, Y. (2019b). Capturing low-pressure hydrogen using V-Ti-Cr catalyzed magnesium hydride. J. Power Sources 413, 139–147. doi: 10.1016/j.jpowsour.2018.12.048
Keywords: magnesium hydride, hydrogen storage performance, core-shell (C-S)nanostructures, carbon additives, dehydrogenation kinetics
Citation: Wang K and Deng Q (2020) Constructing Core-Shell Co@N-Rich Carbon Additives Toward Enhanced Hydrogen Storage Performance of Magnesium Hydride. Front. Chem. 8:223. doi: 10.3389/fchem.2020.00223
Received: 07 January 2020; Accepted: 09 March 2020;
Published: 07 April 2020.
Edited by:
Hai-Wen Li, Kyushu University, JapanReviewed by:
Claudio Pistidda, Helmholtz Centre for Materials and Coastal Research (HZG), GermanyJacques Huot, Université du Québec à Trois-Rivières, Canada
Hiroki Miyaoka, Hiroshima University, Japan
Copyright © 2020 Wang and Deng. This is an open-access article distributed under the terms of the Creative Commons Attribution License (CC BY). The use, distribution or reproduction in other forums is permitted, provided the original author(s) and the copyright owner(s) are credited and that the original publication in this journal is cited, in accordance with accepted academic practice. No use, distribution or reproduction is permitted which does not comply with these terms.
*Correspondence: Qibo Deng, cWlib2RlbmdAdGp1dC5lZHUuY24=