- 1School of Mechanical and Electrical Engineering, Quzhou College of Technology, Quzhou, China
- 2Key Laboratory of Advanced Materials and Applications for Batteries of Zhejiang Province, Zhejiang University, Hangzhou, China
- 3School of Mechanical Engineering, Quzhou University, Quzhou, China
- 4Quzhou Special Equipment Inspection Center, Quzhou, China
Hydrogen has become a promising energy source due to its efficient and renewable properties. Although promising, hydrogen energy has not been in widespread use due to the lack of high-performance materials for hydrogen storage. Previous studies have shown that the addition of Al-based compounds to LiBH4 can create composites that have good properties for hydrogen storage. In this work, the dehydrogenation performances of different composite systems of 2LiBH4+ M (M = Al, LiAlH4, Li3AlH6) were investigated. The results show that, under a ball to powder ratio of 25:1 and a rotation speed of 300 rpm, the optimum ball milling time is 50 h for synthesizing Li3AlH6 from LiH and LiAlH4. The three studied systems destabilized LiBH4 at relatively low temperatures, and the 2LiBH4-Li3AlH6 composite demonstrated excellent behavior. Based on the differential scanning calorimetry results, pure LiBH4 released hydrogen at 469°C. The dehydrogenation temperature of LiBH4 is 416°C for 2LiBH4-Li3AlH6 versus 435°C for 2LiBH4-LiAlH4 and 445°C for 2LiBH4-Al. The 2LiBH4-Li3AlH6, 2LiBH4-LiAlH4, and 2LiBH4-Al samples released 9.1, 8, and 5.7 wt.% of H2, respectively. Additionally, the 2LiBH4-Li3AlH6 composite released the 9.1 wt.% H2 within 150 min. An increase in the kinetics was achieved. From the results, it was concluded that 2LiBH4-Li3AlH6 exhibits the best dehydrogenation performance. Therefore, the 2LiBH4-Li3AlH6 composite is considered a promising hydrogen storage material.
Introduction
Hydrogen energy has become an ideal new energy resource due to its clean, efficient, and renewable properties (Schlapbach and Zuttel, 2001). Although the use of hydrogen energy is promising, widespread use has been hindered by issues in the advancement of high-performance materials for hydrogen storage (Liu et al., 2010). The complex hydride (Ley et al., 2014) LiBH4, which has a hydrogen capacity storage of 18.5 wt.%, has drawn extensive attention. LiBH4 decomposes into an intermediate compound Li2B12H12, which generates B and releases H2 as described in Equation (1) (Orimo et al., 2006).
However, many factors impede the commercial application of pure LiBH4, such as high dehydrogenation temperature, slow dehydrogenation rate, and poor cycle reversibility (Lodziana and Vegge, 2004). To solve these issues, researchers have concentrated on modifying LiBH4 (Vajo and Olson, 2007) through anion/cation substitution (Fang et al., 2011; Lombardo et al., 2019), catalytic modification (Kou et al., 2012; Huang et al., 2016; Zhai et al., 2016), the combined effect of composites (Vajo et al., 2010; Kou et al., 2012), and the application of the confinement effect of nano-materials (Vajo, 2011; Zhang et al., 2017).
Al and Al-based composites with LiBH4 are of interest. Founded on first-principles calculation, Siegel et al. (2007) predicted that LiBH4 would react with Al to generate AlB2, LiH, and H2 at 280°C under a hydrogen pressure of 1 bar. For the LiAlH4-LiBH4 system, Mao et al. (2009) found that the addition of TiF3 decreased the onset temperatures of H2 release by 64 and 150°C compared with the undoped system. The decomposition enthalpy values of LiBH4 also reduced to 60.4 kJ/mol. He et al. (2019) studied the dehydrogenation performance of LiBH4/LiAlH4 composite, found that 8.7 wt.% of hydrogen was released at 500°C, and defined a “Li-Al-B-H” compound. Soru et al. (2014) focused on the phase structural transformation of the LiAlH4 + LiBH4 system, which can produce 6.8 wt.% of hydrogen. According to a study by Carrillo-Bucio et al. (2017), a surface-oxidized 2LiBH4 + Al composite did not release hydrogen until heated to 400°C under a 3 bar initial backpressure. With the catalytic effect of TiF3, the mixture obtained 9.3 wt.% of hydrogen release as compared to the 5.8 wt.% of the undoped mixture. In research by Zhang et al. (2018), a combined mixture of MgH2, LiBH4, and LiAlH4 showed superior performance, starting to release hydrogen at 280°C and maintaining reversibility. In our previous studies (Li et al., 2012), the dehydrogenation temperatures of 2LiBH4 + Li3AlH6 doped with titanium were decreased by 80 and 50°C, respectively, vs. the undoped system. From the previous studies, it can be summarized that Al can enhance the hydrogen storage performance of LiBH4 to some extent. However, the dehydrogenation behaviors of different Al source composite systems have not been systematically studied. In this work, three Al-based LiBH4 composite systems, 2LiBH4-Al, 2LiBH4-LiAlH4, and 2LiBH4-Li3AlH6 were prepared, and the hydrogen storage performance was investigated.
Materials and Methods
Table 1 shows the raw materials used in this study. All powders were carefully stored in a glove box (MIKROUNA), in which noble gas was loaded and the oxygen content and water vapor content were kept below 1 ppm. A planetary mill (QM-3SP2) was utilized to prepare the composites.
The dehydrogenation properties of the materials were tested with a Sievert-type device. The changes in temperature and pressure over time were recorded. The ideal gas state equation was utilized to calculate the dehydrogenation capacity. Thermal analysis was performed using differential scanning calorimetry (DSC, Netzsch 449C Jupiter) combined with thermogravimetric analysis (TG, QMS 403C). To protect the samples from oxidation, high purity argon gas was added at a flow rate of 50 mL/min. An empty aluminum crucible was used as a reference during analysis. The phase compositions of the samples were determined by X-ray powder diffraction (X'Pert-PRO, PANalytical); its scanning range (2θ) was 15°-80°. A specific sealed device was used to protect samples from being oxidized or damped during analysis. Fourier transform infrared spectroscopy (FTIR, Tensor 27) was employed to detect some amorphous substances with a scanning rate of 30 cm−1/min and a resolution ratio of 0.5 cm−1.
Results and Discussion
Preparation of Li3AlH6 Powder
In this work, Li3AlH6 powder was synthesized in-situ by ball milling LiH and LiAlH4. Approximately 15 g mixed powder of LiH and LiAlH4 was milled each time with a molar ratio of 2:1, a ball to powder ratio of 25:1, and a milling speed of 300 rpm. To suppress temperature rise in the ball milling, every 30 min was set as an operation cycle, which contained a stop time of 6 min, periodically. After ball milling for 20 h, XRD patterns were obtained and examined to characterize the mixed powder. Figure 1 shows the XRD results of pure LiH powder, LiAlH4 powder, and the LiH and LiAlH4 powder after ball milling for 20 h. No impurity phases were observed in any of the samples, which indicates that the samples were highly pure and did not oxidize. As shown in Figure 1C, a few Li3AlH6 diffraction peaks are present, while the rest are of LiAlH4 and LiH. This shows that the synthesis reaction was not completed. Due to long milling time, LiH peaks were much lower than before. The LiH content was lower, and an amorphous structure was formed.
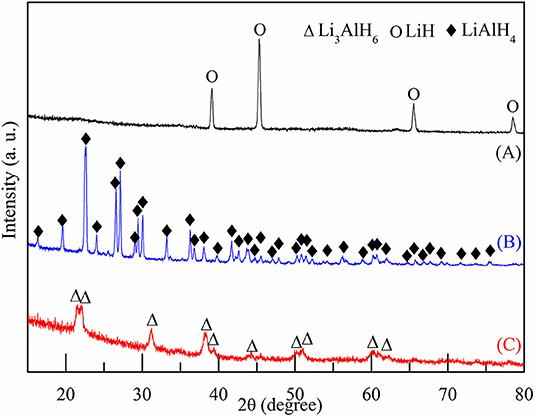
Figure 1. XRD patterns of (A) pure LiH, (B) pure LiAlH4, and (C) mixed powder of LiH and LiAlH4 after ball milling for 20 h.
Further ball milling was carried out since the synthesis reaction to Li3AlH6 was not completed. The milling samples were taken for XRD analysis after every 10 h. Figure 2 shows the XRD results of the milled powders after 20, 30, 40, and 50 h. Strong double peaks at 22° and 23° are detected, which are the characteristic peaks of Li3AlH6. After ball milling for 30 h, most of the diffraction peaks are Li3AlH6; however, some LiAlH4 and LiH peaks can still be found at 27°, 43°, and 46°. As the ball milling time increased, the LiH and LiAlH4 content decreased, which shows that the synthesis reaction proceeds as the milling time increases. Nevertheless, the diffraction intensity of Li3AlH6 decreased, which shows that the longer milling time, the more likely the production of an amorphous phase becomes.
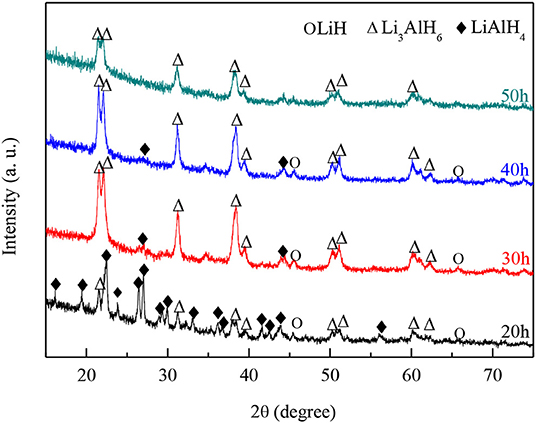
Figure 2. XRD patterns of mixed powder of LiH and LiAlH4 after ball-milling for different numbers of hours.
FTIR analysis was used to investigate the synthesized powder. In pure LiAlH4 (Figure 3A), the bending modes around 1,780 and 1,610 cm−1 correspond to the A-H stretching band, as was previously shown by Chen et al. (2001). After 50 h ball milling, this A-H stretching band disappeared in the 2LilH-LiAlH4 mixtures (Figure 3B). A new A-H stretching band was generated around 1,380 cm−1, which belongs to Li3AlH6. This indicates the completion of the synthesis reaction.
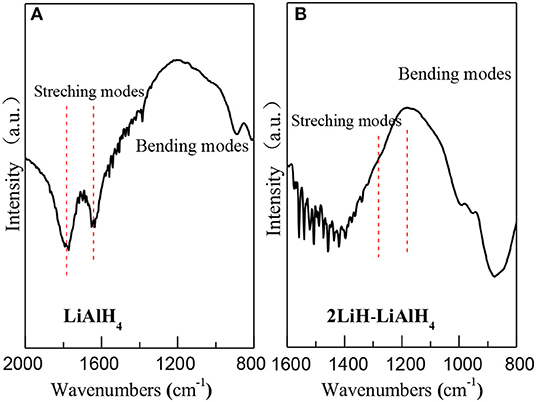
Figure 3. FT-IR spectrums of (A) pure LiAlH4 and (B) 2LiH-LiAlH4 mixed powder after 50-h ball milling.
Characterization of the Composite Samples
The 2LiBH4 + M (M = Al, LiAlH4, Li3AlH6) composite systems were prepared by ball milling, respectively. The ball-milling time was 1 h, with a mole ratio of 2:1. The as-milled mixtures are presented in Figure 4. In the 2LiBH4-Al composite, the narrow and sharp diffraction peaks are of Al, while the other diffraction peaks are of LiBH4. The intensity of the LiAlH4 peaks in the 2LiBH4-LiAlH4 composite are also strong, but both LiBH4 and Li3AlH6 have attenuated diffraction peaks in 2LiBH4-Li3AlH6. The absence of other peaks indicated that there were no side reactions that could generate impurities or by-products during ball milling.
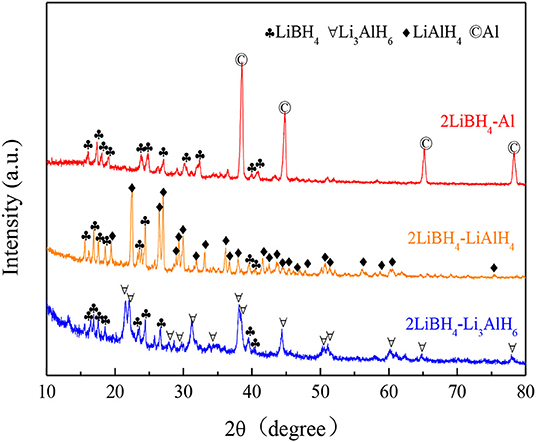
Figure 4. XRD patterns of 2LiBH4-Al, 2LiBH4-LiAlH4, and 2LiBH4-Li3AlH6 mixtures after ball milling for 1 h.
Dehydrogenation Performances
The dehydrogenation performances of the samples were investigated. The four samples were heated to 550°C at a heating rate of 5°C/min in an argon atmosphere. The DSC/TG results are shown in Figure 5. In the pure LiBH4 sample (Figure 5A), the endothermic peak at 120°C denotes that LiBH4 transformed from an orthorhombic to a hexagonal crystal system. The endothermic peak at 286°C is attributed to the melting of LiBH4. According to the TG curve, LiBH4 began to release hydrogen and lose weight at 400°C. There is a dehydrogenation peak at around 469°C, and the rate of dehydrogenation slowed down after that. Both the transformation and the melting peak of LiBH4 for each composite sample are shown in Figures 5B–D. All samples have lower transformation and melting temperatures than pure LiBH4 (transformation temperature: Td < Tc < Tb < Ta; melting temperature: Tc < Td < Tb < Ta). In the as-milled 2LiBH4-Al sample (Figure 5B), the wide endothermic range around 445°C represents the decomposition of LiBH4. The last peak at 529°C is the decomposition of LiH. As shown in Figure 5C, peaks at 190 and 198°C indicated the dehydrogenation of LiAlH4, which were verified in our previous study (Li et al., 2012). LiAlH4 decomposed into Li3AlH6 at 190°C, and Li3AlH6 started to generate LiH, Al, and release H2 at 198°C. LiBH4 and LiH started to decompose at 435 and 472°C, respectively. Figure 5D shows that the decomposition peak of Li3AlH6 is at 198°C, which is consistent with the 2LiBH4-LiAlH4 sample. The decomposition peak of LiBH4 (416°C) is lower than that of the 2LiBH4-LiAlH4 (435°C) or 2LiBH4-Al samples (445°C). In addition, the decomposition peak of LiH, which is around 452°C, is also lower than that of the other composite systems. These results showed that the LiBH4 became more unstable due to the addition of Li3AlH6 and that hydrogen was released at a lower temperature. The main reason for this is that the Al present in Li3AlH6 was active enough to stimulate the dehydrogenation reaction.
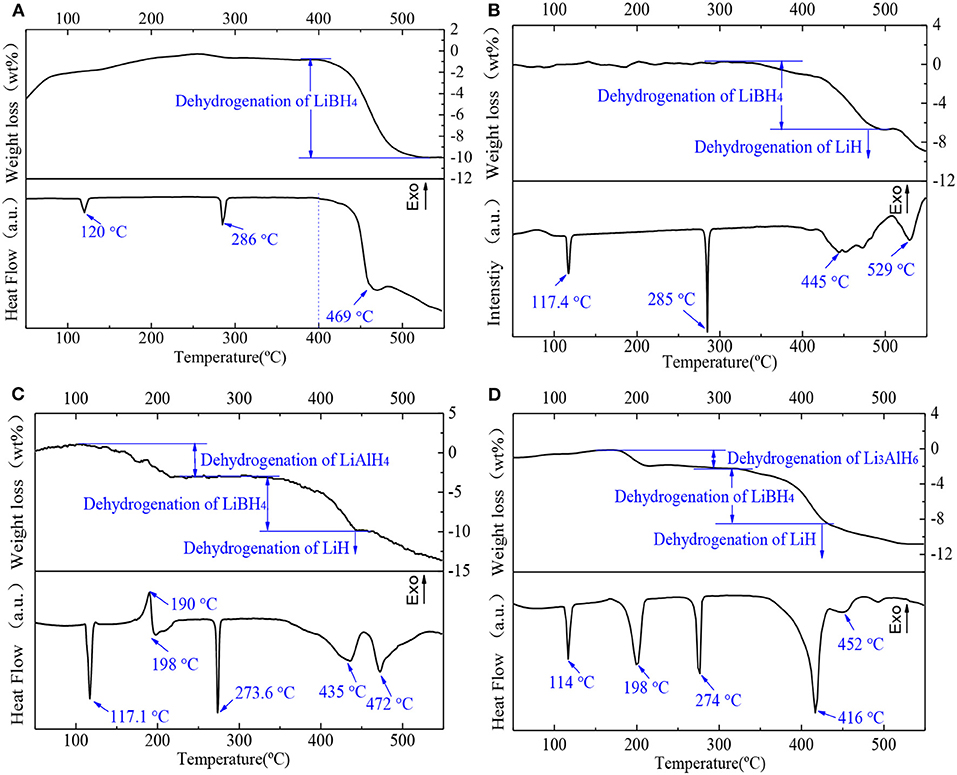
Figure 5. DSC/TG curves of (A) pure LiBH4, (B) 2LiBH4-Al, (C) 2LiBH4-LiAlH4, and (D) 2LiBH4-Li3AlH6 samples after ball milling for 1 h.
The temperature-programmed desorption (TPD) method was implemented to study the dehydrogenation performance of pure LiBH4, 2LiBH4-Al, 2LiBH4-LiAlH4, and 2LiBH4-Li3AlH6; the results are shown in Figure 6. The samples were heated to 400°C and held for 5 h. The pure LiBH4 began to release H2 at around 400°C. Its desorption rate slowed down when 5 wt.% of H2 had been released. The 2LiBH4-Li3AlH6 sample released 9.1 wt.% H2 within 150 min, which is the fastest reaction kinetics in this work. Its decomposition process includes two main steps, with the release of 3 and 6.1 wt.% H2 as the first and second steps, respectively. In the 2LiBH4-LiAlH4 sample, LiAlH4 began to decompose at ~130°C and released 3.9 wt.% H2. Subsequently, its desorption rate was retarded. This composite released a total of 8 wt.% H2. The 2LiBH4-Al composite had a slower desorption rate. Only 5.7 wt.% H2 was released after 6 h, which is much lower than the 8.6 wt.% predicted by theoretical capacity. Previous research (Friedrichs et al., 2009) has reported that Al is an effective catalyst to activate LiBH4, and this phenomenon can also be observed in this study. However, the Al element generated from 2LiBH4-Li3AlH6 is much more effective than for the other samples. Since aluminum can be easily oxidized, an oxide film can easily form on the surface of the Al powder, which can slow down the dehydrogenation kinetics. In contrast, the Al in 2LiBH4-Li3AlH6, decomposed from Li3AlH6 exhibits high purity and is non-oxidized, resulting in the superior reaction kinetics of LiBH4.
Characterization of the Dehydrogenation Materials
The XRD patterns of the dehydrogenated samples are shown in Figure 7. In Figure 7A, prominent diffraction peaks of LiH and Al are present. However, the LiBH4 phase was not observed, as its diffraction intensity is relatively weaker. In Figure 7B, residual peaks of LiBH4 are observed, which demonstrates incomplete dehydrogenation. In Figure 7C, besides LiH and Al, the dehydrogenation products contain AlB2, which was reported as the reversible phase (Friedrichs et al., 2009). AlB2 can accelerate the formation of LiBH4 in the reverse reaction. The AlB2 content was higher in 2LiBH4-Li3AlH6 than in the other samples, which signifies higher reversibility of 2LiBH4-Li3AlH6. There is an unexpected peak near 50° both in the 2LiBH4-LiAlH4 and 2LiBH4-Li3AlH6 samples, which was not identified but was also detected in previous reports (Yang et al., 2007).
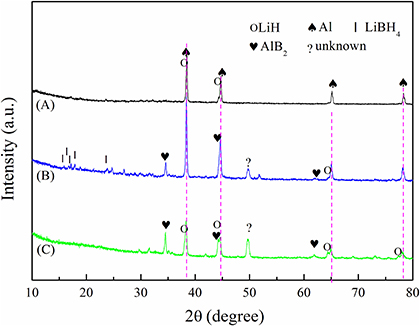
Figure 7. XRD results of dehydrogenated samples at 400°C: (A) 2LiBH4-Al, (B) 2LiBH4-LiAlH4, and (C) 2LiBH4-Li3AlH6.
Conclusions
In this work, the dehydrogenation performance of three different Al source composite systems, 2LiBH4-Al, 2LiBH4-LiAlH4, and 2LiBH4-Li3AlH6, was analyzed. Elemental Al was the raw material and was used without further purification in the 2LiBH4-Al composite, in contrast to the other two samples, where it was decomposed from LiAlH4 or Li3AlH6. Li3AlH6 powder was prepared from LiH and LiAlH4. It can be concluded that the optimum synthetic conditions for ball milling are 50 h with a 25:1 ball to powder ratio at 300 rpm. The results demonstrate that Al, LiAlH4, and Li3AlH6 had a stimulative effect on LiBH4, allowing dehydrogenation at a relatively lower temperature. Additionally, 2LiBH4-Li3AlH6 was shown to have the best performance, with the endothermic peak of LiBH4 at 416°C, 53°C lower than that of the pure LiBH4 sample (469°C). The TPD results also verified the superior results of 2LiBH4-Li3AlH6, which showed the best kinetics performance among the composite samples. 2LiBH4-Li3AlH6 released 9.1 wt.% H2 in only 150 min, which is over 95% of its theoretical hydrogen storage capacity. Its dehydrogenation product, AlB2, was reported as a reversible phase by researchers (Friedrichs et al., 2009), which could promote the reverse reaction of producing LiBH4. Further studies are needed to research the reversibility of the 2LiBH4-Li3AlH6 composite.
Data Availability Statement
All datasets generated for this study are included in the article/supplementary material.
Author Contributions
LC and YL: conception and design of study. YL and JH: acquisition of data. YL and XX: analysis and/or interpretation of data. YL: drafting the manuscript. DZ and SW: revising the manuscript critically for important intellectual content. YL, SW, DZ, JH, XX, and LC: approval of the version of the manuscript to be published.
Funding
This work was supported by the National Natural Science Foundation of China (51671173) and the Curriculum Reform Project (KCSZ 201809 and JGXM201912).
Conflict of Interest
The authors declare that the research was conducted in the absence of any commercial or financial relationships that could be construed as a potential conflict of interest.
References
Carrillo-Bucio, J., Tena-García, J., and Suárez-Alcántara, K. (2017). Dehydrogenation of surface-oxidized mixtures of 2LiBH4 + Al/additives (TiF3 or CeO2). Inorganics 5:82. doi: 10.3390/inorganics5040082
Chen, J., Kuriyama, N., Xu, Q., Takeshita, H. T., and Sakai, T. (2001). Reversible hydrogen storage via titanium-catalyzed LiAlH4 and Li3AlH6. J. Phys. Chem. B 105, 11214–11220. doi: 10.1021/jp012127w
Fang, F., Li, Y., Song, Y., Sun, D., Zhang, Q., Ouyang, L., et al. (2011). Superior destabilization effects of MnF2 over MnCl2 in the decomposition of LiBH4. J. Phys. Chem. C 115, 13528–13533. doi: 10.1021/jp203527c
Friedrichs, O., Kim, J. W., Remhof, A., Buchter, F., Borgschulte, A., Wallacher, D., et al. (2009). The effect of Al on the hydrogen sorption mechanism of LiBH4. Phys. Chem. Chem. Phys. 11, 1515–1520. doi: 10.1039/b814282c
He, Q., Zhu, D., Wu, X., Dong, D., Xu, M., and Tong, Z. (2019). Hydrogen desorption properties of LiBH4/xLiAlH4 (x = 0.5, 1, 2) composites. Molecules 24:1861. doi: 10.3390/molecules24101861
Huang, X., Xiao, X. Z., Shao, J., Zhai, B., Fan, X. L., Cheng, C. J., et al. (2016). Building robust architectures of carbon-wrapped transition metal nanoparticles for high catalytic enhancement of the 2LiBH4-MgH2 system for hydrogen storage cycling performance. Nanoscale 8, 14898–14908. doi: 10.1039/C6NR04100K
Kou, H. Q., Xiao, X. Z., Li, J. X., Li, S. Q., Ge, H. W., Wang, Q. D., et al. (2012). Effects of fluoride additives on dehydrogenation behaviors of 2LiBH4 + MgH2 system. Int. J. Hydrogen Energy 37, 1021–1026. doi: 10.1016/j.ijhydene.2011.03.027
Ley, M. B., Jepsen, L. H., Lee, Y. S., Cho, Y. W., von Colbe, J. M. B., Dornheim, M., et al. (2014). Complex hydrides for hydrogen storage - new perspectives. Mater. Today 17, 122–128. doi: 10.1016/j.mattod.2014.02.013
Li, Y., Xiao, X., Chen, L., Han, L., Shao, J., Fan, X., et al. (2012). Effects of fluoride additives on the hydrogen storage performance of 2LiBH4-Li3AlH6 destabilized system. J. Phys. Chem. C 116, 22226–22230. doi: 10.1021/jp307572x
Liu, C., Li, F., Ma, L. P., and Cheng, H. M. (2010). Advanced materials for energy storage. Adv. Mater. 22, E28–E62. doi: 10.1002/adma.200903328
Lodziana, Z., and Vegge, T. (2004). Structural stability of complex hydrides: LiBH4 revisited. Phys. Rev. Lett. 93:145501. doi: 10.1103/PhysRevLett.93.145501
Lombardo, L., Yang, H., and Züttel, A. (2019). Study of borohydride ionic liquids as hydrogen storage materials. J. Energy Chem. 33, 17–21. doi: 10.1016/j.jechem.2018.08.011
Mao, J. F., Guo, Z. P., Liu, H. K., and Yu, X. B. (2009). Reversible hydrogen storage in titanium-catalyzed LiAlH4-LiBH4 system. J. Alloys Comp. 487, 434–438. doi: 10.1016/j.jallcom.2009.07.158
Orimo, S. I., Nakamori, Y., Ohba, N., Miwa, K., Aoki, M., Towata, S–I., et al. (2006). Experimental studies on intermediate compound of LiBH4. Appl. Phys. Lett. 89:021920. doi: 10.1063/1.2221880
Schlapbach, L., and Zuttel, A. (2001). Hydrogen-storage materials for mobile applications. Nature 414, 353–358. doi: 10.1038/35104634
Siegel, D. J., Wolverton, C., and Ozolins, V. (2007). Thermodynamic guidelines for the prediction of hydrogen storage reactions and their application to destabilized hydride mixtures. Phys. Rev. B 76:134102. doi: 10.1103/PhysRevB.76.134102
Soru, S., Taras, A., Pistidda, C., Milanese, C., Bonatto Minella, C., Masolo, E., et al. (2014). Structural evolution upon decomposition of the LiAlH4 + LiBH4 system. J. Alloys Comp. 615, S693–S697. doi: 10.1016/j.jallcom.2013.12.027
Vajo, J. J. (2011). Influence of nano-confinement on the thermodynamics and dehydrogenation kinetics of metal hydrides. Curr. Opin. Solid State Mater. Sci. 15, 52–61. doi: 10.1016/j.cossms.2010.11.001
Vajo, J. J., Li, W., and Liu, P. (2010). Thermodynamic and kinetic destabilization in LiBH4/Mg2NiH4: promise for borohydride-based hydrogen storage. Chem. Commun. 46, 6687–6689. doi: 10.1039/c0cc01026j
Vajo, J. J., and Olson, G. L. (2007). Hydrogen storage in destabilized chemical systems. Scripta Mater. 56, 829–834. doi: 10.1016/j.scriptamat.2007.01.002
Yang, J., Sudik, A., and Wolverton, C. (2007). Destabilizing LiBH4 with a metal (M) Mg, Al, Ti, V, Cr, or Sc) or metal hydride (MH2 = MgH2, TiH2, or CaH2). J. Phys. Chem. C 111, 19134–19140. doi: 10.1021/jp076434z
Zhai, B., Xiao, X., Lin, W., Huang, X., Fan, X., Li, S., et al. (2016). Enhanced hydrogen desorption properties of LiBH4–Ca(BH4)2 by a synergetic effect of nanoconfinement and catalysis. Int. J. Hydrogen Energy 41, 17462–17470. doi: 10.1016/j.ijhydene.2016.06.170
Zhang, L. T., Zheng, J. G., Xiao, X. Z., Wang, X. C., Huang, X., Liu, M. J., et al. (2017). A new strategy to remarkably improve the low-temperature reversible hydrogen desorption performances of LiBH4 by compositing with fluorographene. Int. J. Hydrogen Energy 42, 20046–20055. doi: 10.1016/j.ijhydene.2017.05.060
Keywords: hydrogen storage materials, LiBH4, composite system, 2LiBH4-Li3AlH6, dehydrogenation performance
Citation: Li Y, Wu S, Zhu D, He J, Xiao X and Chen L (2020) Dehydrogenation Performances of Different Al Source Composite Systems of 2LiBH4 + M (M = Al, LiAlH4, Li3AlH6). Front. Chem. 8:227. doi: 10.3389/fchem.2020.00227
Received: 19 February 2020; Accepted: 10 March 2020;
Published: 15 April 2020.
Edited by:
Guanglin Xia, Fudan University, ChinaReviewed by:
Jian Zhang, Changsha University of Science and Technology, ChinaHujun Cao, Chinese Academy of Sciences, China
Copyright © 2020 Li, Wu, Zhu, He, Xiao and Chen. This is an open-access article distributed under the terms of the Creative Commons Attribution License (CC BY). The use, distribution or reproduction in other forums is permitted, provided the original author(s) and the copyright owner(s) are credited and that the original publication in this journal is cited, in accordance with accepted academic practice. No use, distribution or reproduction is permitted which does not comply with these terms.
*Correspondence: Shaolong Wu, c2hhbnhpbGl5dW4yMDA2QDE2My5jb20=; Dongdong Zhu, emh1ZGQ4QDE2My5jb20=