- 1Laboratory of Laser Technology and Application, Weifang University, Weifang, China
- 2Shandong Haomai Machinery Technology Corporation, Weifang, China
- 3Optoelectronic Research Institute of China Electronics Technology Group Corporation, Tianjin, China
The high beam fill factor of the flat-top laser can effectively increase the output power of the laser without damaging the components. A fiber-solid hybrid high-energy picosecond pulsed laser system was studied, which realized the gain bandwidth matching between the fiber laser and the solid-state regeneration amplifier. In order to achieve the effective amplification of laser energy, the laser beam expander system and the serrated aperture were used to realize the conversion of Gaussian beam to flat-top beam, and a single-pass amplifier was used to generate a picosecond pulse laser output with a single pulse energy of 2.94 mJ. The front-end of the laser system is a Gaussian picosecond all-polarization-maintaining-fiber laser with an average output power of 400 mW, which is injected into the concave-convex cavity regeneration amplifier for power amplification, and the picosecond pulse laser output with a single pulse energy of 1.73 mJ and a repetition rate of 1 kHz is obtained when the pump current is 50 A. Then, using the laser beam expander system and the serrated aperture, a laser pulse with a flat-top beam energy distribution of 0.9 mJ was obtained, which can maintain a high fill factor within a transmission distance of 200 mm. Finally, a 4 mm diameter Nd:YAG gain module was used for single-pass power amplification to achieve a high-energy picosecond pulse laser output of 2.94 mJ, which has a broad application prospect in the field of laser manufacturing.
1 Introduction
In recent years, high-power fiber solid-state coupled picosecond lasers have shown significant advantages in fields such as strong field physics, laser ranging, biomedical, high-precision material processing, and nonlinear optics due to the superior performance [1–5]. Lu et al. developed a fiber solid-state picosecond laser of 1.5 MW high peak power using a high repetition rate fiber seed source and a four-stage end pumped Nd:YVO4 amplifier, providing an ideal laser source for the field of material processing and handling [6]. Zhao et al. reported a continuously adjustable fiber solid picosecond laser source, which could obtain 2.34 mJ laser output at 1 kHz repetition rate, giving a stable front-end solution for subsequent high-energy disk amplifier [7]. However, the output energy of lasers usually had a Gaussian distribution, which not only suppressed further increase in laser power, but also easily caused damage to laser components due to the high power at the center of the laser spot [8, 9]. On the contrary, flat-top laser beams possessed high fill factor and relatively low power density, which were beneficial for laser power amplification efficiently [10, 11]. With the increasing requirements for the output power, energy and other performance of lasers in the field of laser manufacturing, it was of great significance to carry out high-energy picosecond laser flat-top beams conversion to achieve high-efficiency amplification of laser energy [12, 13]. At present, the main methods for generating flat-top laser beams included aperture shaping [14], spatial beam shaping [15, 16], non-spherical lens shaping [17], and programmable beam control system shaping [18]. Researchers also applied flat-top beams generation technology to high-energy picosecond lasers, further improving the performance of ultra-fast lasers. Daniel et al. used a 5.5 mm circular aperture to shape a 1.2 mJ laser pulse into a flat-top beam, and then obtained a laser output with a single pulse energy of 130 mJ and a pulse width of 64 ps through a two-stage side pumped Nd:YAG module [19]. Bahk et al. significantly improved the performance of liquid crystal spatial laser modulators by utilizing a programmable beam shaping system. After passing through rod-shaped crystals and disk amplifiers, they achieved laser output with a single pulse energy of 39 J, a repetition rate of 5 Hz, and a square-shaped flat-top beam profile [18]. Meijer et al. used a 4f system with a spatial filter to achieve flat-top laser output, and then realized laser output with a single pulse energy greater than 440 mJ, a pulse width of 430 ps, and a repetition rate of 100 Hz through a grazing incidence slatted amplifier and a dual-pass module amplifier [9]. Recently, Li et al. used a laser beam expander to control the beam size and adjust the fundamental laser intensity, transforming the initial Gaussian beam into an intensity distribution with a flat-top center or even a saddle-shaped concave center. Ultimately, they achieved a pulsed laser output with a single pulse energy of 172 mJ at 355 nm [20]. Compared to the above methods, serrated aperture beam shaping was undoubtedly a simple and cost-effective approach [21, 22]. Especially, the serrated design of the soft edge aperture could significantly reduce the energy loss by the beam passing through a finite aperture, which improved the efficiency of the laser. By employing a mode-locked fiber oscillator as a laser seed source and Nd:YLF crystal as a regenerative amplifier gain medium, Peng et al. acquired a flat-top beam laser output with a diameter of 3 mm using a laser beam expander combined with a serrated aperture. After shaping, the laser was injected into a four-pass amplifier, resulting in a pulsed laser output with a repetition rate of 1 Hz, a pulse width of 8.6 ps, and a single pulse energy of 6.2 mJ [8]. Su et al. obtained a single pulse energy of 316.5 mJ, a repetition rate of 100 Hz, a pulse width of 50 ps, and a center wavelength of 1,064 nm through two-stage dual pass amplification by using a serrated aperture with a diameter of 6 mm to shape a 6.5 mm Gaussian beam into a flat-top beam, with a shaping efficiency of about 72% [23].
In this paper, a fiber solid-state hybrid high-energy picosecond pulse laser system based on serrated aperture beam shaping was designed, which used fiber laser source as the front-end of solid-state regenerative amplifier. The matching of gain bandwidth between fiber laser and solid-state laser was realized by broadening the spectrum through the self-phase modulation effect of single-mode fiber. In order to effectively suppress the strong point at the center of the laser spot and amplify laser energy, a serrated aperture was used to shape the Gaussian laser into a flat-top beam energy distribution, and finally the output energy of the laser system was further improved by using the Nd:YAG gain module. In the experiment, a MOPA laser amplifier with an all-polarization-maintaining-fiber structure was used as the front-end of the laser system, which could fully leverage the advantages of fiber lasers, such as small size and stable mode locking. The output spectral center wavelength of the fiber laser source was 1,064.1 nm with a 3 dB spectral width of approximately 1.48 nm. The output power was 400 mW, with beam quality of Mx2 = 1.359 and My2 = 1.259. Subsequently, a Z-shaped folded concave convex cavity Nd:YAG regenerative amplifier was employed to further increase the output energy to 1.73 mJ. The Galileo beam expander system was adopted in conjunction with a serrated aperture to achieve the transformation of Gaussian beams into flat-top beams, and high-frequency components in the laser spot were filtered out using an adjustable aperture circular aperture. Although the pulse energy of the laser in this process is reduced to 0.9 mJ, the generated flat-top laser beam could maintain a high fill factor within a transmission distance of 200 mm. Finally, a single pulse energy of 2.94 mJ ps pulse laser output was achieved using a side pumped Nd:YAG main amplifier with a diameter of 4 mm.
2 Experimental setup
The laser system mainly consisted of fiber laser source, regenerative amplifier, and main amplifier. The fiber laser source adopted an ytterbium doped all-polarization-maintaining-fiber structure, as shown in Figure 1, which was divided into four parts: fiber oscillator, fiber preamplifier, single-mode fiber stretcher and fiber master amplifier. The fiber oscillator used semiconductor saturable absorber mirrors (SESAM) passively mode-locking to generate a picosecond pulsed laser with a center wavelength of 1,064.1 nm, a spectral width of approximately 0.1 nm, and an average output power of 12 mW. The laser output could be increased to 400 mW with conversion efficiency of 43.8% by using 6/125 μm single-mode gain fiber (SM-YDF) and 10/130 μm double clad fiber (10/130-YDF). In order to match the output spectrum of the fiber laser source with the gain bandwidth of the Nd:YAG crystal, the self-phase modulation effect of single-mode fiber stretcher was utilized to broaden the spectrum, resulting in a laser output with a spectral width of 1.48 nm at 3 dB. The pulse width of the laser was displayed as 456 ps measured by a high-speed photodetector with a bandwidth of 10 GHz and a LyCroy high-speed oscilloscope with a bandwidth of 13 GHz. The M2 factors of the fiber laser source measured after the fiber collimator were Mx2 = 1.359, My2 = 1.259.
The experimental setup of the entire laser system is shown in Figure 2. The laser generated by the fiber laser output through a self-made fiber collimator, and then was led into a regenerative amplifier for power amplification. After beam shaping by a beam expander system and a serrated aperture, it was finally amplified using a 4 mm side pumped Nd:YAG gain module for single-pass power amplification. The Gaussian type fiber seed laser (as shown in Figure 2) was first optimized for laser polarization state through a half wave plate (HWP1), and then injected into a regenerative amplifier through a thin film polarizer (TFP1) and a two-stage Faraday isolator. The gain medium used in the amplification process of the laser was an Nd:YAG crystal with a diameter of 3 mm. The folded Z-shaped cavity structure was designed with a total length of 1.39 m. The laser system mainly consisted of two convex mirrors (M3 and M6) with a focal length of +1,000 mm, two concave mirrors (M4 and M5) with a focal length of −900 mm, a BBO (CASTECH Inc., Fuzhou, China) Pockels cell (PC), a quarter wave plate (QWP), two thin film polarizers (TFP3 and TFP4), a side pumped gain module (Nd:YAG, 808 nm, 25°C), and two 0°total reflection mirrors (HR1 and HR2). The PC and QWP formed an electro-optic Q-switch, which served as a polarization switch to control the amplification and output of the laser pulses. The PC used the BBO electro-optic crystal with an aperture size of 4 mm and a transmittance of 99.3% at 1,064 nm, which had a high damage threshold of 1 GW/cm2 and was suitable for high repetition rate and high-energy picosecond laser systems. After regenerative amplification, the pulsed laser output through the thin film polarizer (TFP3) and then reversed through a second stage isolation system before outputs from a 34 total mirror (M7). After above procedure, the Gaussian spot diameter output by the regenerative amplifier was about 2.1 mm. Then, a 2x Galilean beam expander was used to shape the laser using a flat concave lens with f = −100 mm and a flat convex lens with f = 200 mm. Due to the complementary relationship between the spherical aberration generated by the positive and negative lenses used in this process, the aberration in the laser system could be well corrected. Furthermore, after beam expander, the laser spot was shaped into a flat-top laser energy distribution using a serrated aperture (SA), and high-frequency components in the spot were filtered out with the aid of an adjustable aperture circular aperture. The serrated aperture, engineered by the Shanghai Institute of Optics and Fine Mechanics (SIOM), features precisely controlled geometric parameters with an inner diameter of 3.2 mm and outer diameter of 4 mm. This specialized component incorporates 128 uniformly distributed serrations, achieving micron-scale manufacturing precision as demonstrated by its 50 μm machining tolerance. The serrated aperture under the optical microscope is shown in Figure 3. Finally, the output energy of the laser system was further enhanced by an Nd:YAG gain module with a diameter of 4 mm, a length of 67 mm, and a doping concentration of 0.5%.
3 Results and discussions
In the experiment, the matching of gain spectra between ytterbium-doped fiber laser source and Nd:YAG regenerative amplifier is one of the key factors for obtaining high-efficiency laser output. The spectral width generated by SESAM mode-locked ytterbium-doped fiber oscillator is about 0.1 nm, which is slightly narrower compared to the gain bandwidth of Nd:YAG crystal at 0.45 nm. Accordingly, in order to prevent the mismatch of gain spectral lines from affecting the amplification efficiency, a 450 m single-mode broadened fiber is used to broaden the 3 dB spectral width of the laser to 1.48 nm owing to the self-phase modulation effect, as shown in Figure 4a. Meanwhile, the pulse broadening can be accelerated by the combined effect of group velocity dispersion and self-phase modulation in single-mode fibers. The repetition rate of the fiber laser source is measured to be 20.89 MHz with the stable locking sequence, as shown in Figure 4b. The broadened pulse laser is then amplified using a polarization-maintaining 10/130 gain fiber. During the amplification process, no significant nonlinear effects are found to affect the spectrum and pulse width of the output laser. The output spectrum of the fiber laser source is measured to be consistent with that of the fiber stretcher, as shown in Figure 4a. Therefore, by employing this self-phase modulation effect to broaden the spectrum, the matching of gain spectral lines between fiber laser sources and solid-state regenerative amplifiers has been basically achieved. The advantages of compact size and stable mode locking of fiber laser sources can be fully utilized. Finally, the center wavelength of the pulsed laser generated by the fiber laser source is 1,064.1 nm with the output power of 400 mW. The single pulse energy is 19.14 nJ and the 3 dB spectral width is 1.48 nm, which is injected into a regenerative amplifier through a fiber collimator for power amplification.
In the regenerative amplifier, the process of establishing cavity emptying is stable and has good reproducibility as shown in Figure 5a. The output pulse of the regenerative amplifier is measured by a 2 GHz oscilloscope, which is clean and no pre-pulses observed in the temporal profile as shown in Figure 5b. The regenerative amplifier employs a three-sided side-pumping configuration, where 12 diode arrays are uniformly distributed at 120° intervals to ensure symmetric energy deposition. The pump radiation exhibits a triangular intensity profile within the Nd:YAG crystal, characterized by elevated power densities at both the central and peripheral regions, with an effective pump spot diameter of ∼1.2 mm. Thermal management is implemented via a copper water-cooled heat sink, maintaining the crystal temperature at 25.0 ± 0.5°C to minimize thermal lensing effects. Under optimized pumping conditions (50 A drive current, 120 W pump power, 1 kHz repetition rate), the system delivers a stable output pulse energy of 1.73 mJ, corresponding to a slope efficiency of 16.5% relative to the absorbed pump power. Long-term energy stability testing in 2 h reveals a root-mean-square (RMS) fluctuation of 1.22%, as quantified in Figure 5c. Spatial beam characterization, shown in the inset of Figure 2, confirms that the amplified output retains a near-Gaussian intensity profile, with minimal distortion induced by the amplification process. Recently, it was reported in the referenced literature demonstrates significant advantages in key parameters including single-pulse energy (316.5 mJ), pulse width (50 ps), and repetition rate (100 Hz) [23]. While the energy output of our fiber-solid hybrid architecture is comparatively lower, the integrated approach offers enhanced flexibility and greater potential for long-term operational stability. Furthermore, the spectral broadening effect induced by self-phase modulation (SPM) effectively addresses the matching issue between gain media, providing a viable methodology for advancing research on high-energy laser systems.
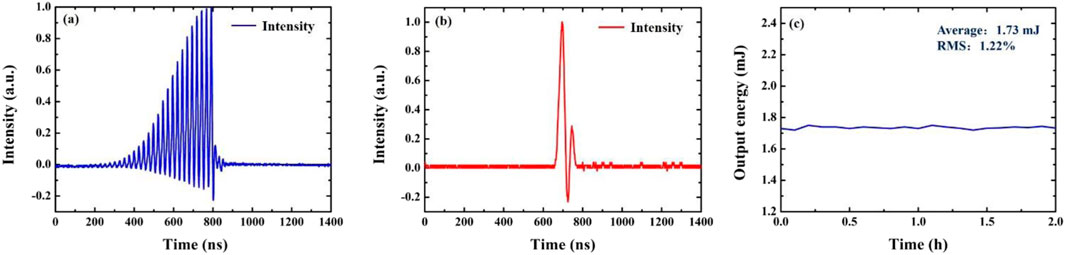
Figure 5. (a) The process of emptying the cavity of the regenerative amplifier; (b) the output pulse waveform; (c) The energy stability of regenerative amplifier in 2 h.
In order to further improve the amplification efficiency and prevent damage to the laser device caused by the nonlinear self-focusing effect of the laser, the serrated aperture is used to shape the spot into a flat-top intensity energy distribution. Firstly, the Galileo type beam expander system is used to adjust the spot size, to approximately 4.1 mm. Then, the Gaussian pulse laser is shaped into a flat-top beam energy distribution by a serrated aperture. The laser output with a spot size of approximately 3.4 mm is obtained after using an adjustable aperture circular aperture to filter out high-frequency components in the laser spot. The experiments were conducted in a strictly controlled ultra-clean laboratory environment, with temperature stabilized at 23°C via a thermostatic system and humidity maintained below 40%. The optical system was constructed on a vibration-isolated optical platform, utilizing low thermal expansion coefficient mounts to secure optical components. The power loss induced by the serrated aperture was measured using a laser spot detector (Ophir-SP920S CCD), revealing an approximate 25% energy attenuation through the beam shaping system, with the residual pulse energy stabilized at 0.9 mJ. This energy loss arises from three interconnected mechanisms. First, the geometric blocking effect of the serrated aperture’s non-transmissive regions physically obstructs 10%–15% of the incident beam energy, which dependents on serration parameters such as the number of teeth and tip length. Second, the phase modulation imposed by the serrated structure, governed by the transmission function in Formula 1:
where r and a are the radius of the serrated aperture and the flat-top region, respectively. n is the order of the super-Gaussian and ω0 is the beam waist radius. M is the number of serrations. This modulation distributes the Gaussian wavefront into a super-Gaussian profile while generating high-spatial-frequency sidelobe diffraction. These unwanted frequency components are subsequently filtered by a spatial aperture, introducing an additional 5%–10% energy loss. Third, numerical simulations attribute 3%–5% of the attenuation to transverse energy diffusion and edge scattering during the homogenization process as the beam transitions to a flat-top distribution. As shown in Figure 6, the reshaped flat-top beam maintains a high fill factor over a 200 mm propagation distance, a performance enabled by synergistic effects of diffraction suppression and beam quality optimization. The serrated aperture disrupts the phase coherence of Sommerfeld diffraction wavepackets, effectively mitigating near-field modulation, while the 2x Galilean beam expander reduces divergence angle to extend the effective Rayleigh length. Beyond 200 mm, the cumulative diffraction effect plays a dominant role, which transforms the beam from near-field to intermediate-field regime and degrades the fill factor. These findings highlight the critical balance between energy loss mechanisms and propagation stability. The future work will focus on serration parameter optimization and 4f spatial filtering enhancements to further improve system efficiency.
The last part of the article is the main amplifier of the laser system. The pulsed laser is directly injected into a single-pass power amplifier of Nd:YAG gain module with a diameter of 4 mm, a center wavelength of 808 nm, and an operating condition of 25°C. The repetition rate and pulse width of the pump module are set to 1 kHz and 250 μs, respectively. An acousto-optic Q-conversion driver (EO Q-SWITCH DRIVER) is used to control the timing synchronization. When the pump current in the single-pass Nd:YAG gain module is set to 76 A with pump power of 493 W, a flat-top laser beam with a single pulse energy of 0.9 mJ is amplified to 2.94 mJ, with an amplification factor of about 3.2 times. The variation curve of output energy with pump current measured is shown in Figure 7. The current water-cooling system exhibits inherent limitations due to the 4-mm Nd:YAG gain module operating at a coolant temperature of 25 ± 0.5°C with a fixed flow rate of 10 L min−1, without real-time crystal temperature monitoring. Experimental data indicate that when pump currents exceeds 70 A, thermal lensing-induced focal spot drift becames the dominant factor constraining output power scaling efficiency. To mitigate these effects, an optimized thermal management system will be implemented, incorporating real-time crystal temperature diagnostics (resolution: ±0.1°C) with PID-controlled adaptive cooling. Concurrently, an Nd:YAG module with a diameter of 6 mm will be used to increase laser efficiency and power scalability.
4 Conclusion
In this work, we demonstrate a fiber-solid hybrid picosecond laser system capable of generating a flat-top laser with a pulse energy of 2.94 mJ and maintaining a high fill factor at a distance of 200 mm, achieved by serrated aperture beam shaping and efficient spectral matching. The front-end of the laser system adopts an all-polarization-maintaining-fiber laser source with a center wavelength of 1,064.1 nm. The matching of gain bandwidth between fiber laser source and solid-state regenerative amplifier is achieved by utilizing the self-phase modulation effect of broadened fiber to widen the spectrum. Then the generated pulsed laser is injected into a Z-folded concave convex cavity Nd:YAG regenerative amplifier to further increase the output energy to 1.73 mJ. In order to effectively suppress the strong point at the center of the laser spot and amplify the laser energy, a Galilean beam expander system combined with a serrated aperture is used to achieve the conversion of Gaussian beams to flat-top beams. Although the single pulse energy of the pulsed laser is reduced to 0.9 mJ, the laser beam can maintain a high fill factor within a transmission distance of 200 mm. Finally, after single-pass power amplification of the picosecond laser with a repetition rate of 1 kHz by an Nd:YAG gain module with a diameter of 4 mm, the single pulse energy can reach 2.94 mJ. Future work will focus on developing an optimized serrated aperture to mitigate energy loss and extend transmission distance, coupled with a 4f spatial filter system to further enhance laser output energy.
Data availability statement
The original contributions presented in the study are included in the article/supplementary material, further inquiries can be directed to the corresponding authors.
Author contributions
SL: Conceptualization, Data curation, Formal Analysis, Investigation, Methodology, Project administration, Resources, Validation, Writing–original draft, Writing–review and editing. YY: Data curation, Investigation, Validation, Writing–original draft. HW: Data curation, Writing–original draft. ZY: Writing–review and editing. MW: Investigation, Writing–review and editing. CM: Data curation, Methodology, Writing–review and editing. XF: Conceptualization, Data curation, Formal Analysis, Funding acquisition, Writing–original draft. YZ: Funding acquisition, Supervision, Writing–original draft. HJ: Funding acquisition, Writing–review and editing. DL: Funding acquisition, Resources, Writing–review and editing.
Funding
The author(s) declare that financial support was received for the research and/or publication of this article. The author(s) declare financial support was received for the research, authorship, and/or publication of this article. This work was funded the Weifang Science and Technology Development Plan (2023GX014, 2021GX010), Shandong Provincial Key R&D Program (Innovation Ability Improvement Project for Small and Medium-sized Science and Technology Enterprises) (2024TSGC0553) and Weifang Science and Technology Development Plan (Competitive Innovation Platform) Project (2024JZ0021).
Conflict of interest
Authors WH, ZY, JH, and LD were employed by Shandong Haomai Machinery Technology Corporation. Author ZY was employed by Optoelectronic Research Institute of China Electronics Technology Group Corporation.
The remaining authors declare that the research was conducted in the absence of any commercial or financial relationships that could be construed as a potential conflict of interest.
Generative AI statement
The author(s) declare that no Generative AI was used in the creation of this manuscript.
Publisher’s note
All claims expressed in this article are solely those of the authors and do not necessarily represent those of their affiliated organizations, or those of the publisher, the editors and the reviewers. Any product that may be evaluated in this article, or claim that may be made by its manufacturer, is not guaranteed or endorsed by the publisher.
References
1. Ji LL, Wang WT, Tian Y, Tian Y, Yao JP, Zheng YH, et al. Ultra-strong and ultrafast laser physics and cutting-edge applications. Chin J Lasers (2024) 51(11):1101003. doi:10.3788/CJL240635
2. Long ML, Deng RH, Zhang HF, Wu ZB, Zhang ZP, Chen M. Development of 1 kHz repetition rate multi-pulse picosecond laser and its application of space debris laser ranging. Acta Optica Sinica (2021). doi:10.3788/AOS202141.0614001
3. Shen Y, Zong N, Wen Y, Bao Y, Peng QJ. Review on Novel 6.45 μm Laser Scalpel, the Medical Applications and Laser Sources (Invited). Electro-Optic Technology Application (2022). p. 037.
4. Chen B, Bai Z, Ma T, Cheng Y, Cui C, Qi Y, et al. Characteristics of high-energy non-collinear Brillouin amplifier based on fused silica. Opt and Laser Technology (2025) 180:111547. doi:10.1016/j.optlastec.2024.111547
5. Chen H, Cui Y, Li X, Zhang B, Cai Y, Ding J, et al. High-power dual-wavelength intracavity diamond Raman laser. Funct Diamond (2023) 3(1):2282527. doi:10.1080/26941112.2023.2282527
6. Lu Y, Wang Y, Liu B, Zhang Xiang Z., Wang Chunhua W., Ye Zhibin Y., et al. 1.5 MW peak power, fiber-solid hybrid amplification MOPA lasers. Chin J Lasers (2015) 42(2):0202009. doi:10.3788/cjl201542.0202009
7. Zhao M, Hao Q, Guo ZR, Zeng HP. Compact kHz repetition rate fiber-solid picosecond laser light source. Chin J Lasers (2018) 45(4):7. doi:10.3788/CJL201845.0401010
8. Peng YJ, Pan X, Wang JF, Fan W, Li XC. Research on the pumping source of high-stability and high-performance picosecond optical parametric amplifier. Chin J Lasers (2014)(8) 6. doi:10.3788/CJL201441.0802009
9. Meijer RA, Stodolna AS, Eikema KSE, Witte S. High-energy Nd:YAG laser system with arbitrary sub-nanosecond pulse shaping capability. Opt Lett (2017) 42(14):2758–61. doi:10.1364/ol.42.002758
10. Lu S, Lv SQ, Chen M, Peng Hongpan P., Yang Ce Y. C., Zhang Xie Z. X. Realization of single-pulse energy 3 mJ, repetition frequency 1 kHz picosecond super-Gaussian beam. Infrared Laser Eng (2019) 48(10):1005012. doi:10.3788/irla201948.1005012
11. Paliesek T, Petr N, Jan P, Divoký M, Smrž M, Mocek T. Beam shaping in the high-energy kW-class laser system Bivoj at the HiLASE facility. High Power Laser Sci Eng (2023) 11(6):e79. doi:10.1017/hpl.2023.79
12. Lv X, Su H, Peng Y, Leng Y. High-energy, quasi-CW 355 nm UV pulses generation from a diode-pumped sub-nanosecond Nd:YAG system. In: Solid state lasers XXVIII: technology and devices (2019).
13. Zhai ZS, Tian G, Zhang Y, Lv Q, Wang X, Xie B. Flattop beam shaping using hybrid gratings. IEEE Photon J (2022) 14(4):1–5. doi:10.1109/jphot.2022.3186902
14. Gu M, Gan XS. Fresnel diffraction by circular and serrated apertures illuminated with an ultrashort pulsed-laser beam. J Opt Soc America A (1996) 13(4):771–8. doi:10.1364/josaa.13.000771
15. Li SS, Wang YL, Lu ZW, Ding L, Du P, Chen Y, et al. High-quality near-field beam achieved in a high-power laser based on SLM adaptive beam-shaping system. Opt Express (2015) 23(2):681–9. doi:10.1364/oe.23.000681
16. Michailovas A, Aleknavičius A, Michailovas K, Balickas S, Petrauskienė V, Gertus T, et al. Implementation of a SVWP-based laser beam shaping technique for generation of 100-mJ-level picosecond pulses. Appl Opt (2016) 55(28):8007–15. doi:10.1364/ao.55.008007
17. Ma HT, Liu ZJ, Jiang PZ, Xu X, Du S. Improvement of Galilean refractive beam shaping system for accurately generating near-diffraction-limited flattop beam with arbitrary beam size. Opt Express (2011) 19(14):13105. doi:10.1364/oe.19.013105
18. Bahk SW, Begishev IA, Zuegel JD. Precompensation of gain nonuniformity in a Nd:glass amplifier using a programmable beam-shaping system. Opt Commun (2014) 333:45–52. doi:10.1016/j.optcom.2014.07.054
19. Daniel WE, Stefan W, Jonas M, Altmann RK, Eikema KSE. High-energy, high-repetition-rate picosecond pulses from a quasi-CW diode-pumped Nd:YAG system. Opt Lett (2013) 38(16):3021. doi:10.1364/ol.38.003021
20. Li J, Zhang J, Ma T, Li Y, Wang P, Leng Y. A high-energy, 100 Hz, picosecond laser for OPCPA pumping. Appl Sci (2017) 7(10):997. doi:10.3390/app7100997
21. Long ML, Li G, Chen M. 1 kHz, 96 W pulse-burst picosecond laser system with six equal spacing and amplitude pulses. Appl Opt (2017) 56(15):4274. doi:10.1364/ao.56.004274
22. Chen H, Bai Z, Chen J, Li X, Zhu ZH, Wang Y, et al. Diamond Raman vortex lasers. ACS Photon (2025) 12(2):864–9. doi:10.1021/acsphotonics.4c01852
Keywords: beam shaping, serrated aperture, flat-top beams, regenerative amplifier, picosecond laser
Citation: Li S, Yang Y, Wang H, Zhu Y, Wang M, Ma C, Fan X, Zhao Y, Jing H and Liu D (2025) Research on fiber-solid hybrid picosecond laser technology based on serrated aperture beam shaping. Front. Phys. 13:1572448. doi: 10.3389/fphy.2025.1572448
Received: 07 February 2025; Accepted: 13 March 2025;
Published: 28 March 2025.
Edited by:
Shuo Liu, Hebei University of Technology, ChinaReviewed by:
Xinyang Su, Beijing Jiaotong University, ChinaZu Yuqian, Qilu University of Technology, China
Yan Xu, Chinese Academy of Sciences (CAS), China
Copyright © 2025 Li, Yang, Wang, Zhu, Wang, Ma, Fan, Zhao, Jing and Liu. This is an open-access article distributed under the terms of the Creative Commons Attribution License (CC BY). The use, distribution or reproduction in other forums is permitted, provided the original author(s) and the copyright owner(s) are credited and that the original publication in this journal is cited, in accordance with accepted academic practice. No use, distribution or reproduction is permitted which does not comply with these terms.
*Correspondence: Chao Ma, bWFjaGFvQHdmdS5lZHUuY24=; Xinmin Fan, eGlubWluZmFuQHdmdS5lZHUuY24=