- 1School of Information Engineering, Tianjin University of Commerce, Tianjin, China
- 2Engineering Maintenance Section, Highway Construction and Maintenance Center, Xiqing District Transportation Administration, Tianjin, China
High-power laser technology has become an important tool in the field of modern machining due to its high energy density, non-contact processing characteristics and high-precision control ability to make it show significant advantages in cutting and welding. With the continuous development of laser technology, the application of high power laser (such as fiber laser, CO2 laser) in the industrial field is also expanding. This paper combs through the technical advantages, application research, challenges and future trends of high power lasers in cutting, welding and drilling. In recent years, the increase of laser power and the optimization of processing have promoted the wide application of high-power lasers in aerospace, automotive manufacturing and electronic devices. In this paper, we will discuss laser cutting, welding and drilling, and discuss their future development directions in light of recent research progress.
1 Introduction
High-power laser technology has gone through an evolutionary process from basic theoretical research to wide application. With the continuous progress of science and technology, lasers have been widely used, such as fiber lasers and carbon dioxide lasers play an increasingly important role in industrial processing. Fiber lasers have the advantages of high electro-optical conversion efficiency, good beam quality, good heat dissipation, high stability, low cost, etc. [1, 2], and their power range is usually in the range of a few kilowatts to tens of thousands of kilowatts, which is suitable for the processing of metal or part of the non-metallic materials. Carbon dioxide lasers have the advantages of high output power, good beam quality, and narrow heat-affected zone, etc. Paper and non-metallic materials are suitable for cutting with carbon dioxide lasers [3, 4], and these materials have a high absorption rate of the wavelength of carbon dioxide lasers [5]. The advantages of high-power lasers lie in their high energy density, non-contact processing characteristics, and adaptability to complex shapes, making them an indispensable processing tool in modern manufacturing. Laser processing technologies such as laser welding and laser cutting have been widely used in aerospace, automotive, electronic equipment and many other fields, significantly improving productivity and product quality [6, 7].
2 High-power laser cutting technology
2.1 Cutting carbon fiber reinforced composites (CFRP)
High-power laser cutting is an advanced material processing technology that irradiates the material with a high energy density laser beam to melt or vaporize it to achieve separation. It has significant advantages over traditional cutting methods, capable of cutting with high precision and speed, with a small heat-affected zone and high cutting quality [5]. The performance of high-power laser cutting is also affected by the laser parameters, the higher the power, the smaller the focused spot, which can improve the laser absorption rate and energy density, so that the powder melting is better [8], while too high a laser power will reduce the quality of the cut. Laser wavelength, spot size and divergence angle also affect the cutting performance, and optimizing these parameters can improve the cutting quality and efficiency. In addition, laser cutting is one of the most widely used non-contact material cutting methods based on the process of generating thermal energy [9], and can be used to cut engineering materials such as titanium, stainless steel, aluminum and aluminum alloys, as well as non-metallic materials such as wood, glass, plastics, ceramics, and composites, which are widely used in various manufacturing industries [10]. Fiber lasers are mainly used for processing metals, but are emerging in some non-metallic areas, and CO2 lasers are particularly suitable for cutting non-metallic materials.
Carbon fiber reinforced composites (CFRP), which are made by embedding carbon fibers in a polymer matrix, are widely used in aerospace, automotive manufacturing, and renewable energy due to their high strength, light weight, durability [11, 12]. In recent years, significant progress has been made in fiber laser cutting of CFRP. When laser cutting CFRP, the laser power and cutting speed need to be precisely controlled to avoid excessive thermal damage and delamination of the material. Li M et al. conducted a feasibility study on high-power fiber laser cutting of thick CFRP sheets, and the results showed that 10.0 mm thick CFRP sheets could be successfully cut using a high-power fiber laser and a one-pass cutting strategy [13]. Figure 1a summarizes the cross-sectional morphology of the processed samples at different laser powers in the study. Based on their study, it can be concluded that high cutting efficiency, high cutting surface quality and high material removal rate can be achieved by using fiber laser for cutting CFRP. Fiber laser cutting of CFRP is prone to thermal damage and formation of heat affected zone (HAZ), which leads to degradation of material properties. The laser parameters need to be strictly controlled, too high energy will seriously damage the material, and insufficient power will not cut thoroughly. Due to its high energy density, it is suitable for cutting CFRP sheets with moderate thickness, high efficiency requirements and less stringent requirements on HAZ, or it can be prioritized in scenarios that are sensitive to cutting speed and cost.
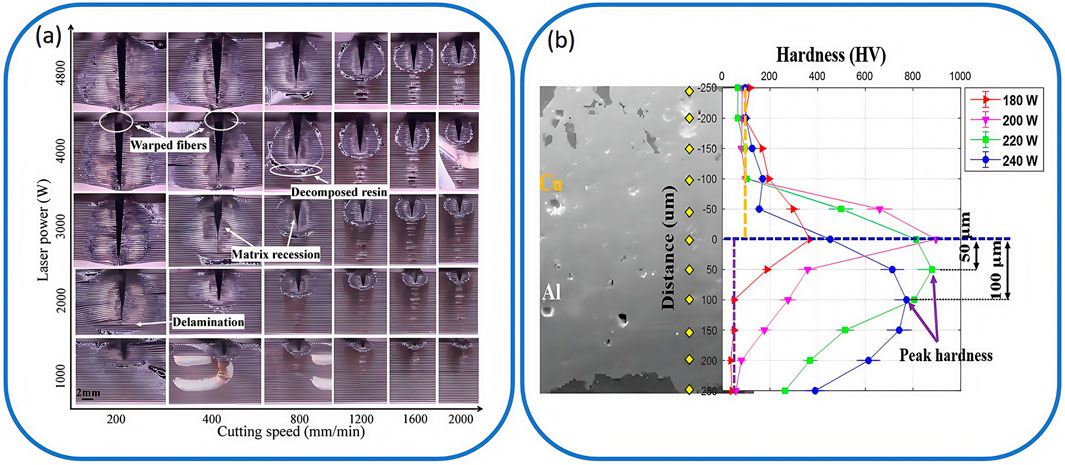
Figure 1. (a) Surface morphology observed on cross section of CFRP samples following fiber laser cutting with different processing parameters. Reprinted with permission from ref. [13]. Copyright (2021) Elsevier. (b) Hardness distribution in the weld of Cu/Al. Reprinted with permission from ref. [26]. Copyright (2024) Springer Nature.
2.2 CO2 laser cutting glass sheet
Thin glass sheets are widely used in electronics, microfluidic devices, optical applications and automotive components due to their light weight, high transparency and wear resistance. Due to its brittleness, amorphous nature and low mechanical strength, cutting thin glass sheets has become an important engineering problem. And the traditional mechanical cutting methods suffer from many defects, such as cracks, uncontrollable fracture and fragments at the cutting edge. With the rapid development of CO2 laser technology in recent years, it is widely used for cutting non-metallic materials, such as cutting thin glass plates, because of its advantages of good processing quality, high processing efficiency [14], cleanliness and environmental protection. However, cutting at open environment can produce a large heat affected zone, which leads to cracks and affects the quality of the cut. Prakash S and Nirala CK did a study of CO2 laser cutting of glass sheet in different environments [15], which showed that underwater CO2 laser cutting of glass sheet has significant advantages over open air processing, reducing heat related defects such as crack formation and large damage areas, and the cracks produced during the cutting process are more controllable or crack-free. CO2 laser cutting of thin glass can be used when high precision and efficiency are required and underwater processing equipment and devices are available.
3 High-power laser welding technology
3.1 Dissimilar metal welding
High-power laser welding is an advanced welding technology that utilizes a high-energy-density laser beam to locally heat the material to a molten state, thereby achieving a material connection. Laser welding is one of the useful techniques that provides high energy and fewer heat deformation and heat-affected zones (HAZs) [16]. Compared to traditional welding methods, laser beam welding enables high manufacturing precision and locally concentrated thermal input into the material at high processing speeds [17]. Traditional welding methods, such as arc welding and resistance welding, there are often slow welding speed, large heat-affected zone, welding deformation and other problems. In contrast, high-power laser welding is capable of realizing high speed and high quality welding with small heat-affected zone and small welding deformation [18, 19]. Moreover, laser welding can be adapted to different working environments [20]. Another advantage of laser welding is that the welding process can be automated by robots and no additional material is required to achieve the specified wall thickness [21]. By means of an advanced control system, the laser beam could be kept focused over a wide range of welding parameters and full penetration was realized [22]. In addition, laser welding is a non-contact process that improves precision and prevents distortion of the weld material [23].
Dissimilar metal welding is of great significance in industrial applications, but traditional welding methods often face many challenges when welding dissimilar metals, such as poor weldability, low joint strength,and the formation of brittle intermetallic compounds [24]. Laser welding of dissimilar materials is characterized by a thin heat affected zone (HAZ), high energy density, low distortion, high welding speed and high heat input control [19]. Fiber lasers, have the advantages of good beam quality, high conversion efficiency, excellent heat dissipation performance, and good maintainability [1], and are inherently suitable for intermetallic welding, and are considered to be a desirable choice for dissimilar metal welding [25]. Trinh L and Lee D used a pulsed fiber laser to weld aluminum-copper dissimilar metals, which demonstrated that the pulsed fiber laser welding technique can effectively join the two dissimilar metals, aluminum and copper, and the optimization of welding parameters can significantly improve the performance of welding joints [26]. The hardness of the Al/Cu welds in is shown in Figure 1b. At the same time, the optimization of welding parameters can significantly improve the mechanical properties of the joints and reduce defects. Tao TAO et al. used the sandwich-assisted laser welding technique to study the welding of magnesium alloy with steel, and the study showed that under the process conditions of 1,000 W laser power, 30 mm/s welding speed, 30° laser head deflection, 2 mm defocusing, and 15 L/min argon protection, the welding of magnesium and steel can be achieved by adding a sandwich can realize the metallurgical connection between magnesium and steel, and the weld surface is continuous and smooth, without spatter, and well formed [27]. In addition to fiber laser, CO2 laser also has unique advantages in welding of dissimilar metals, which has the advantages of precise heat input control, high speed welding, high quality weld seam, etc., which is suitable for high quality welding of thick materials, such as dissimilar metal welding in power equipment. Prabakaran M P and his team did CO2 laser welding of dissimilar metals of mild steel (AISI 1018) and austenitic stainless steel (AISI 316) dissimilar metals to influence dissimilar metal process optimization [28], which showed that the optimum process parameters for CO2 laser welding of mild steel (AISI 1018) and austenitic stainless steel (AISI 316) can be determined by Response Surface Methodology (RSM) and Centered Composite Design (CCD) to obtain the maximum weld strength. Therefore, fiber lasers and CO2 lasers have their own advantages in dissimilar metal welding. Fiber laser welding of dissimilar metals such as aluminum, copper, magnesium and steel is highly efficient and of high quality, while CO2 laser welding of dissimilar metals in thick materials such as mild steel and stainless steel can be optimized to achieve maximum welding strength.
3.2 Transparent material welding
Laser welding of transparent materials is one of the important research directions of laser technology in recent years. Ultrafast laser welding technology is able to weld a variety of transparent materials, including but not limited to glass, diamond, organic polymers, etc. These materials have important applications in many fields such as aerospace, sensors, microelectronics, optical communications, optical storage, and so on, due to their excellent optical properties, high mechanical strength, chemical stability, and excellent electro-thermal-mechanical properties [29, 30]. Nonlinear absorption and thermal accumulation effects are the core mechanisms of ultrafast laser welding of transparent materials, and efficient energy deposition and thermal accumulation can be realized by precisely controlling the laser parameters. It is found that the welding index will be significantly affected by controlling the number of pulses. Jia X et al. conducted a study on the burst ultrafast laser welding of quartz glass, and found through experiments that the Burst mode with different numbers of sub-pulses had a significant effect on the melting structure and welding strength of quartz glass, indicating that the length of the melting structure increases and the width decreases with the increase of the number of sub-pulses, but the welding strength gradually decreases [31]. Femtosecond laser welding of transparent materials has also made significant progress in recent years. Gao Z et al. proposed a method of using a double-pulse femtosecond laser to weld quartz glass under non-optical contact conditions by adjusting the optical paths of the two pulsed lasers to control the time difference between their arrivals at the sample to achieve double-pulse processing, and by optimizing the parameters of the average power, pulse delay, and scanning intervals, we have successfully realized the High-strength welding of quartz glass under non-optical contact conditions, the welding strength reached 57.15 MPa, and the temperature resistance test showed that the welded samples have excellent stability and thermal shock resistance under high temperature conditions [32]. Laser welding of transparent materials technology has shown great potential for application in many fields due to its wide material applicability, high precision, and excellent welding performance. With the continuous innovation and optimization of the technology, its prospect will be even broader.
4 High-power laser drilling technology
4.1 Alumina ceramic drilling
High-power laser drilling technology is a processing method that uses a high-energy density laser beam focused on the surface of the material to remove the material through local melting and vaporization caused by the high-energy laser beam, without the need for traditional drilling tools [33], and to achieve precise removal of the material and the formation of holes. Compared with traditional mechanical drilling, laser drilling laser drilling can produce a large number of holes in a non-contact manner, with non-contact machining, fast speed, high machining accuracy, wide range of applications and other significant advantages, laser beam drilling is widely used in a variety of aerospace fields that require high dimensional accuracy and hole quality [34]. Alumina ceramics are widely used in electronics, machinery, healthcare and other fields due to their excellent hardness and high temperature stability [35]. However, the traditional processing methods have problems such as low efficiency, large heat affected zone, and poor hole wall quality. Compound pulsed laser (CPL), by combining two or more lasers (e.g., millisecond and nanosecond lasers), can significantly improve the drilling performance. Li Z et al. investigated the dynamic process of compound pulsed laser (CPL) drilling in alumina ceramics through theoretical modeling and experimental validation, and demonstrated that the CPL can achieve high efficiency and high quality microporous machining without the aid of high-pressure gases or absorbing coatings, and high-quality microvia processing without the assistance of high-pressure gas or absorption coating [36], which provides important technical support for the miniaturization of ceramic substrates.
4.2 Composite material drilling
Composite materials are widely used due to their excellent properties, CFRP is widely used in aerospace field due to its light weight and high strength, but its laser drilling process is prone to problems such as accuracy, surface quality and thermal damage, while SiCf/SiC is widely used in many fields due to its excellent high temperature mechanical properties and oxidation resistance, so it is necessary to study its drilling strategy in depth in order to improve the processing quality. Liu X et al. conducted a study on optimizing the laser drilling strategy for CFRP, and used a one-way experimental strategy to investigate the effects of the laser beam moving order (Scheme I and Scheme II), scanning spacing, and the direction of pumping (Pump-Front and Pump-Rear) on the hole quality under the helical scanning path, showing that the laser beam moving order (Scheme I) and the direction of pumping (Scheme III) are the same as those of Scheme I and Scheme IV, respectively, but the laser beam moving order (Scheme I) and Scheme II are the same as those of Scheme III. It is shown that the best micro-hole accuracy, surface morphology, and the smallest thermal damage defects can be achieved when Scheme I moving order, 20 μm scanning spacing, and Pump-Rear pumping direction are adopted, which can effectively improve the quality of CFRP laser drilling, and provide new insights and optimization references for the research in this field, Figure 2a shows the schematic diagram of the laser drilling system [37]. SiCf/SiC composites are difficult to process with the characteristics of high hardness, high brittleness, and low electrical conductivity. SiCf/SiC composites, with high hardness, high brittleness, low electrical conductivity and other characteristics, are difficult to process, and there are many challenges in the processing of their small holes. The femtosecond laser has the advantages of short pulse and small heat-affected zone, and the femtosecond laser rotary drilling technology can realize small-hole machining with high precision and short drilling time, and the femtosecond laser rotary drilling (FLRD) technology also shows great potential for the application of the femtosecond laser rotary drilling technology to the machining of small holes in the difficult-to-machine materials, such as the silicon carbide fiber-reinforced silicone carbide-ceramic matrix composites (SiCf/SiC), Feng Y et al. The application of femtosecond laser rotary drilling (FLRD) technology in the small hole processing of silicon carbide fiber reinforced silicon carbide ceramic matrix composites (SiCf/SiC) was investigated by experimental research, which showed that FLRD technology can effectively improve the quality and efficiency of small hole processing of SiCf/SiC composites, and realize the processing of small holes with no obvious thermal damage, high precision, and short drilling time, which can provide a solution for the precision processing of small holes in difficult-to-machine materials. The FLRD technique can effectively improve the quality and efficiency of small-hole machining of SiCf/SiC composites without obvious thermal damage, realize high-precision and short drilling time, and provide a new method for precision machining of small holes in difficult-to-machine materials,Figure 2b shows the FLRD system including a femtosecond laser, a rotation optical system, a focusing module, and so on [38]. These studies provide valuable theoretical support and practical guidance for the application of high-power laser drilling technology in different difficult-to-machine materials, and promote the further development and application of this technology in aerospace, electronics, machinery and other fields.
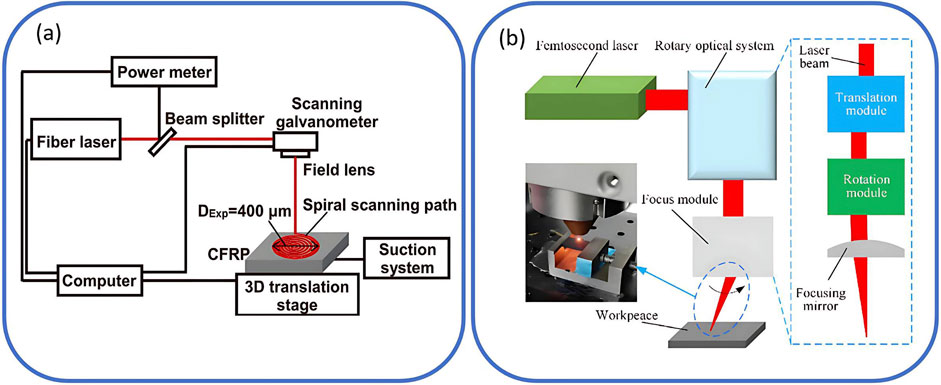
Figure 2. (a) Laser drilling experimental system. Reprinted with permission from Ref. [37]. Copyright (2024) Elsevier. (b) Schematic diagram and actual processing of FLRD system. Reprinted with permission from Ref. [38]. Copyright (2025) Elsevier.
5 Conclusion and outlook
In summary, high-power laser cutting and welding technology has many advantages, but still faces some challenges in practical applications, such as when processing highly reflective materials, the reflection of the laser beam may lead to damage of guards or melting of specific areas of other sensitive components [39]; when cutting thick plates, the cutting speed and quality are difficult to be guaranteed; and the laser welding process produces a serious thermal conversion effect, which has high demands on the welding process parameters and the Workpiece fixation precision requirements are very high [40]. When welding thick plates, in addition to ordinary defects, special defects such as root defects, intermediate cracks (longitudinal and transverse), humps, and air holes can occur during the formation of lock holes [41]. Laser drilling faces challenges such as the control of thermal effects in high-precision micro-hole processing and the need for higher energy density and longer processing time when processing thick or hard materials, where processing efficiency has to be optimized. In addition, the high cost and stringent maintenance requirements of high-power laser equipment limit its wide application in certain fields. The continuous progress of ultrafast laser technology will provide new ways for high-precision and low-damage material processing. The integration of laser processing and artificial intelligence will realize real-time monitoring and parameter optimization of the processing process, improving production efficiency and processing quality. At the same time, laser-assisted processing technology innovation, such as laser-assisted additive manufacturing, laser micro-nano-processing, etc., will expand the application areas of laser technology, providing stronger technical support for intelligent manufacturing. In short, the application of high-power laser technology in the field of machining has a broad prospect. By constantly overcoming the limitations of the existing technology and promoting the development of technological innovation, high-power laser technology will realize breakthroughs in more fields, and provide strong support for the upgrading and innovation of the manufacturing industry.
Author contributions
Y-GW: Investigation, Writing – original draft, Resources. S-PH: Writing – review and editing, Supervision. Q-CL: Writing – review and editing.
Funding
The author(s) declare that financial support was received for the research and/or publication of this article. This work was supported by Tianjin Science and Technology Plan Project (Grant No. 24YDTPJC00780), Open Project of Hebei Province Key Laboratory of Advanced Laser Technology and Equipment (Grant No. HBKL-ALTE2024009).
Conflict of interest
The authors declare that the research was conducted in the absence of any commercial or financial relationships that could be construed as a potential conflict of interest.
Generative AI statement
The author(s) declare that no Generative AI was used in the creation of this manuscript.
Publisher’s note
All claims expressed in this article are solely those of the authors and do not necessarily represent those of their affiliated organizations, or those of the publisher, the editors and the reviewers. Any product that may be evaluated in this article, or claim that may be made by its manufacturer, is not guaranteed or endorsed by the publisher.
References
1. Zhang L, Zhu K, Yao Y, Tian X, Xu H, Nie Z. Research progress in tunable fiber lasers based on multimode interference filters. Micromachines (2023) 14(11):2026. doi:10.3390/mi14112026
2. Zhao X, Sun J, Wang Y, Wang X, Fu B. Ag/MXene as saturable absorber for Tm:Ho Co-doped Q-switched fiber laser. Nanomaterials (2024) 14(11):951. doi:10.3390/nano14110951
3. Pincjer I, Miketic N, Gvoic V, Maricic K, Vukelic D, Prica M. Optimization of tensile strength in the paper material cutting process based on CO2 laser process parameters. Materials (2023) 16(7):2719. doi:10.3390/ma16072719
4. Bratu AM, Petrus M, Popa C. Identification of absorption spectrum for IED precursors using laser photoacoustic spectroscopy. Molecules (2023) 28(19):6908. doi:10.3390/molecules28196908
5. Zhan Z, Wang C, Yap JBH, Loi MS. Retrofitting ancient timber glulam mortise and tenon construction joints through computer-aided laser cutting. Heliyon (2020) 6(4):e03671. doi:10.1016/j.heliyon.2020.e03671
6. Feng J, Wang J, Zhao X, Liu Z, Ding Y. Laser weld spot detection based on YOLO-weld. Scientific Rep (2024) 14(1):29403. doi:10.1038/s41598-024-80957-3
7. Niu J, Liu W, Li JX, Pang X, Liu Y, Zhang C, et al. Machining water through laser cutting of nanoparticle-encased water pancakes. Nat Commun (2023) 14(1):3853–0. doi:10.1038/s41467-023-39574-3
8. Zhao X, Zheng H, Ma X, Sheng Y, Zeng D, Yuan J. Microstructure,Mechanical properties, and corrosion resistance of Ag–Cu alloys with La2O3 fabricated by selective laser melting. Materials (2023) 16(24):7670. doi:10.3390/ma16247670
9. Liu F, Yu A, Wu C, Liang S. Process analysis and topography evaluation for monocrystalline silicon laser cutting-off. Micromachines (2023) 14(8):1542. doi:10.3390/mi14081542
10. Olender-Skóra M, Banaś W, Turek M, Skóra P, Gwiazda A, Foit K, et al. Effects of using laser technology for cutting polymer films. Materials (2024) 17(15):3678. doi:10.3390/ma17153678
11. Huang W, Cheng F, Zuo S, Ji Y, Yang G, He J, et al. The effects of combined treatments of laser engraving, plasma spraying and resin pre-coating on improving the bonding strength of titanium alloy and carbon fiber-reinforced polymer. Polymers (2024) 16(14):2041. doi:10.3390/polym16142041
12. Ivars J, Labanieh AR, Soulat D. Influence of the thermoplastic fiber ratio on the mechanical properties of recycled carbon fibers during the carding process. Materials (2025) 18(2):302. doi:10.3390/ma18020302
13. Li M, Chen L, Yang X. A feasibility study on high-power fiber laser cutting of thick CFRP laminates using single-pass strategy. Opt Laser Technology (2021) 138(0):106889. doi:10.1016/j.optlastec.2020.106889
14. Son S, Lee D. The effect of laser parameters on cutting metallic materials. Materials (2020) 13(20):4596. doi:10.3390/ma13204596
15. Prakash S, Nirala CK. CO2 laser cutting of thin glass sheet under different ambient conditions. Lasers Eng (Old City Publishing) (2021) 49(1-3):107–17. Available online at: https://research.ebsco.com/c/224ngr/search/details/3c67pt4raj?q=CO2+Laser+Cutting+of+Thin+Glass+Sheet+Under+Different+Ambient+Conditions (Accessed April 12, 2025).
16. Alhajhamoud M, Candan L, Ilgaz MA, Cinar I, Ozbey S, Čorović S, et al. Laser welding of 316L austenitic stainless steel in an air and a water environment. Materials (2022) 15(6):2248. doi:10.3390/ma15062248
17. Haddad E, Poggenburg F, Häusler A, Olowinsky A. Welding of thin stainless-steel sheets using a QCW green laser source. Scientific Rep (2024) 14(1):4105–0. doi:10.1038/s41598-024-54305-4
18. Lai ZH, Xu S, Clark SJ, Fezzaa K, Li J. Unveiling mechanisms and onset threshold of humping in high-speed laser welding. Res Square (Research Square) (2024) 0(0):0. doi:10.21203/rs.3.rs-4087583/v1
19. Ramaphoko NA, Skhosane S, Maledi N. Microstructural characterization and mechanical properties of laser beam-welded dissimilar joints between A6000 aluminum alloy and galvanized steel. Materials (2022) 15(2):543. doi:10.3390/ma15020543
20. Ma B, Gao X, Huang Y, Zhang Y. Effect of different pulse shapes on the laser welding of aluminum and copper. Opt Laser Technology (2024) 171(0):110312. doi:10.1016/j.optlastec.2023.110312
21. Capek J, Trojan K, Kec J, Černý I, Ganev N, Němeček S. On the weldability of thick P355NL1 pressure vessel steel plates using laser welding. Materials (2020) 14(1):131. doi:10.3390/ma14010131
22. Cao Y, Wang X, Yan X, Jia C, Gao J. Prediction of fusion hole perforation based on arc characteristics of front image in backing welding. Materials (2020) 13(21):4706. doi:10.3390/ma13214706
23. Wencel Z, Wiewiórowska S, Wieczorek P, Gontarz A. Electron beam welding process for Ti6Al-4V titanium alloy. Materials (2023) 16(14):5174. doi:10.3390/ma16145174
24. Su S, Duan W, Wu Y, Shao F, Sun T, Gu X, et al. Interfacial energy conversion mechanism between 3003 aluminum alloy and 321 stainless steel in vaporizing foil actuator welding process. Scientific Rep (2024) 14(1):23307–0. doi:10.1038/s41598-024-74077-1
25. Zhao Y, Qin X, Long Y, Zhou J, Jiao H. Study on the influence of weld spacing on the tensile strength of laser double-pass reciprocating welding of dp780/6061-T6 dissimilar metals. Materials (2023) 16(7):2560. doi:10.3390/ma16072560
26. Trinh L, Lee D. A study on laser welding for dissimilar metals of aluminum and copper using pulsed fiber laser. Int J Precision Eng Manufacturing (2024) 0(0):2467–77. doi:10.1007/s12541-024-01073-w
27. Tao TAO, Liu J, Zhou D, Li H, Wang X. Microstructure and properties of magnesium/steel dissimilar metals by interlayer assisted laser welding. Trans Nonferrous Met Soc China (2023) 33(3):765–76. doi:10.1016/s1003-6326(23)66144-8
28. Prabakaran MP, Kannan GR. Optimization of CO2 laser beam welding process parameters to attain maximum weld strength in dissimilar metals. Mater Today Proc (2018) 5(2):6607–16. doi:10.1016/j.matpr.2017.11.316
29. Jia X, Luo J, Li K, Wang C, Li Z, Wang M, et al. Ultrafast laser welding of transparent materials: from principles to applications. Int J Extreme Manufacturing (2025) 7:032001. doi:10.1088/2631-7990/ada7a7
30. Song D, Wang J, Wu X, Gao L, Yang J, Liu X, et al. Microscopic processing of transparent material with nanosecond and ultrafast lasers. Micromachines (2024) 15(9):1101. doi:10.3390/mi15091101
31. Jia X, Fu Y, Li K, Wang C, Li Z, Wang C, et al. Burst ultrafast laser welding of quartz glass. Materials (2025) 18(5):1169. doi:10.3390/ma18051169
32. Gao Z, He J, Jia X, Yi Z, Zhang S, Li C, et al. High-strength welding of silica glass using double-pulse femtosecond laser under non-optical contact conditions. Photonics (2024) 11(10):945. doi:10.3390/photonics11100945
33. Yang T, Xiao Y, Hang Y, Wu X, Kong W. Research on helical electrode electrochemical drilling assisted by anode vibration for jet micro-hole arrays on tube walls. Micromachines (2025) 16(1):86. doi:10.3390/mi16010086
34. Petrů J, Pagáč M, Grepl M. Laser beam drilling of inconel 718 and its effect on mechanical properties determined by static uniaxial tensile testing at room and elevated temperatures. Materials (2021) 14(11):3052. doi:10.3390/ma14113052
35. Liu C, Wu H, Guo A, Kong D, Zhao Z, Wang L, et al. Vat photopolymerization of sepiolite fiber and 316L stainless steel-reinforced alumina with functionally graded structures. Materials (2024) 17(12):2973. doi:10.3390/ma17122973
36. Jia X, Li Z, Wang C, Li K, Zhang L, ji'an D. Study of the dynamics of material removal processes in combined pulse laser drilling of alumina ceramic. Opt Laser Technology (2023) 160(0):109053. doi:10.1016/j.optlastec.2022.109053
37. Liu X, Li L, Yang S, Xu M, Zhong M, Wang B, et al. Optimization of nanosecond laser drilling strategy on CFRP hole quality. J Mater Process Technology (2024) 332(0):118559. doi:10.1016/j.jmatprotec.2024.118559
38. Feng Y, Zhigang D, Renke K, Hongbin M, Guangyi M, Yan B. Femtosecond laser rotary drilling for SiCf/SiC composites. Chin J Aeronautics (2024) 0(0):0. doi:10.1016/j.cja.2024.05.012
39. Cortina M, Arrizubieta JI, Ruiz JE, Ukar E, Lamikiz A. Latest developments in industrial hybrid machine tools that combine additive and subtractive operations. Materials (2018) 11(12):2583. doi:10.3390/ma11122583
40. Fan K, Peng P, Zhou H, Wang L, Guo Z. Real-time high-performance laser welding defect detection by combining ACGAN-based data enhancement and multi-model fusion. Sensors (2021) 21(21):7304. doi:10.3390/s21217304
Keywords: high power laser technology, machining applications, laser cutting and welding, laser drilling, future development trends
Citation: Wang Y-G, Hou S-P and Lv Q-C (2025) Research progress on the application of high-power laser cutting, welding, and drilling. Front. Phys. 13:1595077. doi: 10.3389/fphy.2025.1595077
Received: 17 March 2025; Accepted: 28 April 2025;
Published: 13 May 2025.
Edited by:
Rajib Biswas, Tezpur University, IndiaCopyright © 2025 Wang, Hou and Lv. This is an open-access article distributed under the terms of the Creative Commons Attribution License (CC BY). The use, distribution or reproduction in other forums is permitted, provided the original author(s) and the copyright owner(s) are credited and that the original publication in this journal is cited, in accordance with accepted academic practice. No use, distribution or reproduction is permitted which does not comply with these terms.
*Correspondence: Shu-Ping Hou, aG91c2h1cGluZ0B0amN1LmVkdS5jbg==