- Guangdong Key Laboratory of Electric Power Equipment Reliability, Electric Power Research Institute of Guangdong Power Grid Co., Ltd., Guangzhou, China
This paper presents a comprehensive review of gas detection and early warning technologies for lithium-ion battery thermal runaway a critical safety concern in modern energy storage and electric vehicle applications. With the increasing push for higher battery energy densities, thermal runaway has emerged as a severe risk characterized by rapid self-heating, complex exothermic reactions, and the evolution of flammable gases that can lead to explosions and fires. The review begins by detailing the underlying physicochemical mechanisms of thermal runaway and the subsequent gas generation processes, emphasizing the early evolution of gas signals as a promising indicator for imminent failure. A wide range of detection techniques are critically evaluated, including gas chromatography, Fourier-transform infrared spectroscopy, Raman spectroscopy, differential electrochemical mass spectrometry, metal oxide semiconductor sensors, and non-dispersive infrared technology—each offering unique advantages and facing distinct challenges in practical applications. Special attention is given to the emerging role of optical fiber-based sensors (e.g., Fabry–Perot interferometers, fiber Bragg gratings, and fluorescence-based sensors), which provide notable benefits such as immunity to electromagnetic interference, flexible integration, and high sensitivity for key gases (CO2, H2, and CH4). The paper concludes by discussing the limitations of current approaches and proposes future directions to achieve integrated, cost-effective, and robust battery safety monitoring systems.
1 Introduction
As global consumption of fossil fuels increases, there is an urgent need to transition to green, renewable energy sources. Lithium-ion batteries, as a significant form of secondary new energy, are increasingly used in the fields of energy storage and new energy vehicles. In January 2022, China’s National Development and Reform Commission and the National Energy Administration issued the “14th Five-Year Plan for the Development of New Energy Storage,” emphasizing that new energy storage is an important technology and fundamental equipment for building a new type of power system, and plays a crucial supporting role in achieving the goals of carbon peak and carbon neutrality. On 2 June 2023, the National Energy Administration released the “New Power System Development Blue Paper,” proposing a comprehensive construction of a new energy system and strengthening the large-scale layout and application system of energy storage. However, as the demand for longer battery life increases, the improvement in the energy density of lithium-ion batteries also brings the risk of thermal runaway. The self-heating of batteries, thermal runaway, and the resulting risks of explosions and fires pose new challenges for fire protection and firefighting.
In large-scale battery energy storage systems, the risk of thermal runaway is even more severe. To reduce the footprint of battery packs, a high-density arrangement is often used. Once a single cell experiences thermal runaway, the fire can quickly spread throughout the entire system. Therefore, ensuring the safety and stable operation of the system while rapidly increasing the deployment of battery energy storage projects has become a major challenge for the industry. Researching the thermal runaway characteristics of lithium-ion batteries and analyzing the severity of the consequences they cause is crucial for thermal safety management of batteries. Many experts and scholars have conducted in-depth studies on the mechanisms of battery thermal runaway, preventive measures, and emergency responses, aiming to reduce this risk and enhance the safety of the entire system. Researching battery thermal runaway is not only about the performance and efficiency of the batteries but also a vital issue for ensuring human safety and environmental health. Developing new and effective safety monitoring technologies is key to ensuring the safe use of lithium-ion batteries, reducing the potential for fires and explosions, and protecting public safety and the environment.
2 Common lithium battery thermal runaway early warning methods
Battery thermal runaway is a complex physicochemical phenomenon that mainly occurs as a result of reactions within the battery materials when the temperature rises. These reactions typically happen in lithium-ion batteries composed of components such as copper foil current collectors, negative electrode active materials, separators, positive electrode active materials, and aluminum foil current collectors. As the temperature of the battery increases, these materials begin to undergo various exothermic reactions, including the decomposition of the SEI film, reactions between the anode and the electrolyte, shrinking and melting of the separator, decomposition of the cathode, decomposition of the electrolyte solution, reactions between the anode and the binder, and combustion of the electrolyte, among others. These reactions lead to a rapid increase in the internal temperature of the battery, further exacerbating the thermal runaway phenomenon [1]. In cases of high energy density, lithium-ion batteries are more prone to thermal runaway. When the internal temperature of the battery reaches a critical point due to overcharging, over-discharging, excessive external temperatures, or internal defects, it triggers a self-heating chain reaction. Once these reactions start, they are difficult to stop, and the internal temperature of the battery can rise sharply in a very short time, releasing a large amount of heat. This accumulation of heat can not only destroy the battery itself but also potentially cause a fire. During thermal runaway, the temperature of the battery may reach extremely high levels, increasing the risk of fires and explosions [2].
To ensure the safe use of lithium-ion batteries (LIBs), researchers have developed various methods for early warning of thermal runaway [3]. Resistance, current, voltage signals serve as fundamental methods for monitoring thermal runaway. By monitoring changes in the battery’s resistance, current, and voltage, lithium plating phenomena occurring inside the battery can be timely detected [4]. Negative electrode lithium plating can cause changes in voltage and impedance, monitoring of potential, dynamic capacitance, and internal resistance reduction, allowing for in situ monitoring of the battery. Temperature signals are direct methods for monitoring thermal runaway. Changes in the internal temperature of the battery are key indicators during the thermal runaway process. By using temperature sensors to monitor the battery’s temperature, an alarm can be triggered once the temperature exceeds a critical value. However, due to thermal conduction inside and outside the battery, temperature monitoring may have time delays and measurement errors [5]. In the early stages of battery thermal runaway, due to changes in internal structure and the occurrence of side reactions, gases are generated inside the battery, and the rapid increase in the concentrations of these gases can serve as early warning signals [6]. Compared to surface temperature sensing, gas sensors react more quickly. As gases accumulate, they lead to an increase in internal pressure within the battery. This change in pressure is also an important early warning signal for thermal runaway [7]. When the battery pressure reaches a certain threshold and the safety valve opens, the battery produces specific sound signals. Monitoring these sound signals can be used for early warning of thermal runaway [8]. More seriously, when the battery casing expands and ruptures, smoke and flames are released. Although flame signal monitoring typically occurs in the late stages of thermal runaway, it remains an important alarm signal [9]. Flames accompany smoke, which is a substance formed by the thermal decomposition or combustion of polymer materials within the battery at high temperatures. Smoke is an important characteristic before the outbreak of a safety incident in the later stages of thermal runaway [10].
The method of thermal runaway early warning based on gas type and concentration signals, compared to methods based on electrical signals, temperature signals, and pressure signals, has the advantage of early warning [3]. The electrical signal method is directly related to the inherent properties of the battery and is suitable for monitoring individual batteries, but its timeliness and reliability are limited in large-scale energy storage. The temperature signal method has nonlinear characteristics during the thermal runaway process, and there can be a significant difference between internal and surface temperatures of the battery. The pressure signal method faces issues of low sensitivity and high cost. Therefore, the gas signal method, with its ability to provide early warning in the initial stages of thermal runaway, is considered a more effective choice.
2.1 The mechanism of gas generation from thermal runaway in lithium batteries
Lithium-ion batteries are comprised of anodes, cathodes, electrolytes, and separators. Under abusive conditions, thermal decomposition of materials would occur, leading to a self-heating phenomenon. When the rate of heat generation inside the battery exceeds its dissipation rate, the temperature of the battery can increase dramatically, eventually leading to thermal runaway. During the thermal runaway process in lithium batteries, the temperature increases from low to high, and the internal reactions gradually escalate. The structure of a lithium battery is shown in Figure 1. Initially, in the temperature ranging from 70°C to 90°C, the solid electrolyte interface (SEI) membrane near the anode side of the lithium battery decomposes, releasing gases such as CO2, C2H4, etc [11]. The SEI membrane plays a role in enhancing electrolyte/electrode interface compatibility, suppressing electrolyte decomposition, and stabilizing the electrode to improve battery performance. Following the decomposition of the SEI membrane, the internal temperature of the battery continues to rise, and the lithiated battery anode reacts with the organic solvent in the electrolyte, producing short-chain hydrocarbon gases such as CH4, C3H6, and C2H6 [12]. These reactions further exacerbate the local temperature increase inside the battery, leading to the destruction of the battery’s separator. The separator, made from insulating materials, serves to keep the battery’s anode and cathode apart. The disintegration of the separator triggers an internal short circuit, releasing a significant amount of heat. When the battery temperature reaches about 170°C, the cathode and the electrolyte undergo disproportionation and decomposition reactions, continuing to release O2 and a large amount of heat. These two stages are considered to be the most intense reactions during the thermal runaway process of the battery [13]. Subsequently, the battery’s anode, cathode, and electrolyte begin to decompose, producing gases such as CO, CO2, PF5, HF, Alkyl fluorides, and Phosphorus fluoride compounds [14]. Finally, reactions occur between the electrodes and the binder, releasing a large amount of H2. These complex reaction processes are intertwined and have a chain-reaction characteristic, making them difficult to reverse once initiated [15].
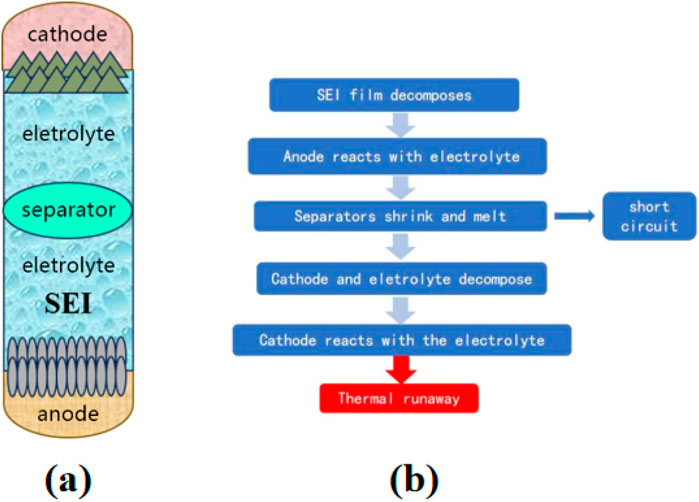
Figure 1. (a) Schematic diagram of a lithium-ion battery. (b) Thermal runaway process of a lithium-ion battery.
2.2 Types of gases produced by lithium battery thermal runaway
As mentioned in the previous section, a battery’s thermal runaway involves six critical stages, including dozens of chemical reactions. The types and quantities of gases produced during this process are quite complicated. Taking lithium-ion batteries as an example, the gas components and concentrations produced during thermal runaway can be influenced by various factors, including the anode and cathode materials of the battery itself, separator, electrolyte system, the battery’s operating environment, and the mechanisms triggering thermal runaway, such as mechanical, thermal, and electrical abuse [16–18]. According to a survey of 21 domestic and international literature on battery gas production during thermal runaway [19–39], the main components of the produced gases are shown in Figure 1. Nitrogen (N2) and oxygen (O2), which are abundant in the atmosphere, are not suitable as characteristic gases for battery thermal runaway and are not counted in this paper. In Figure 2, during the thermal runaway process, a total of 13 gases were detected, including carbon dioxide (CO2), carbon monoxide (CO), hydrogen (H2), ethylene (C2H4), methane (CH4), ethane (C2H6), other short-chain hydrocarbons (CxHy, x >3 years >3), hydrogen fluoride (HF), acetylene (C2H2), volatile organic compounds (Org), phosphorus pentafluoride (PF5), fluoroethane (C2H5F), and organics of the CxHyOz type. In the literature on battery thermal runaway, CO2 and CO are the most commonly mentioned gases, with mention rates of 90.5% and 85.7%, respectively. More than 50% of the scientific literature mentions the five gases CO2, CO, H2, C2H4, and CH4, C2H6. In addition, C2H2, other short-chain hydrocarbons (CxHy,x >3 years >3), and HF are also often mentioned during the battery thermal runaway process.
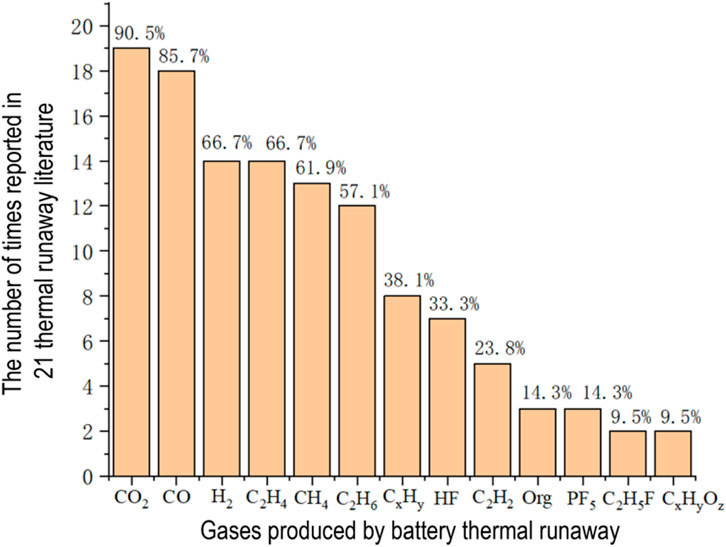
Figure 2. The main types of gases generated during thermal runaway in lithium-ion batteries based on major references from domestic and international literature.
Apart from nitrogen (N2) and oxygen (O2), gases produced by mainstream lithium batteries during thermal runaway are listed in Table 1. These lithium batteries include lithium cobalt oxide, nickel cobalt manganese (NCM) lithium, lithium iron phosphate, lithium titanate, and lithium manganate. The triggers for battery thermal runaway include thermal abuse, electrical abuse, and mechanical abuse. To provide a clear visualization of the types of gases generated during thermal runaway in mainstream lithium-ion batteries, the factors triggering thermal runaway are categorized in Table 1, and the battery types are systematically summarized.
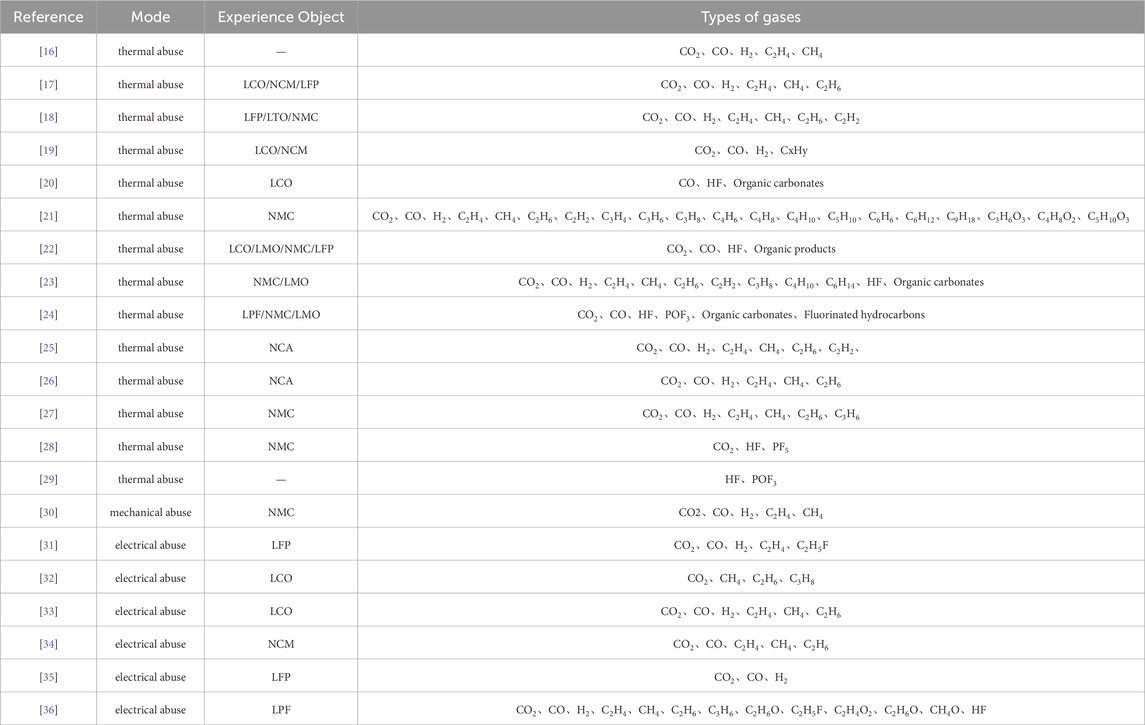
Table 1. Types of gases generated during thermal runaway in different types of lithium-ion batteries. NCA stands for lithium cobalt oxide, LCO for lithium cobalt oxide, NCM/NMC for lithium nickel cobalt manganese oxide, LFP for lithium iron phosphate, LTO for lithium titanate, and LMO for lithium manganese oxide.
2.3 The volume of gases produced by lithium battery thermal runaway
Due to the limited number of studies on gas production during lithium battery thermal runaway, there is a lack of systematic research on the volume of gases produced, particularly studies that meticulously control variables. According to references [19–40], factors affecting gas production during lithium battery thermal runaway include battery capacity, battery material system, operating environment, and the mode of initiation of thermal runaway. It is generally believed that lithium batteries with larger capacities may produce more gas during thermal runaway, as they contain more electrolyte and electrode materials. Here, the authors only compared the relationship between different battery capacities and the volume of gases produced. According to Figure 3, without controlling for other conditions, there is no evident positive correlation between the capacity of a battery and the volume of gases it produces during thermal runaway. Lithium cobalt oxide batteries with a capacity of 1 Ah and lithium iron phosphate batteries with a capacity of 1.1 Ah have a 100-fold difference in the volume of gases produced during thermal runaway [20, 22]. For thermal runaways induced by thermal abuse, a nickel cobalt manganese lithium battery with a capacity of 3.2 Ah produces approximately three times the volume of gases as a lithium iron phosphate battery with a capacity of 3.8 Ah. Overall, within the capacity range of up to 4 Ah for lithium battery thermal runaway, the total volume of gases produced generally ranges from 1 to 10 L From 1 to 10 L.
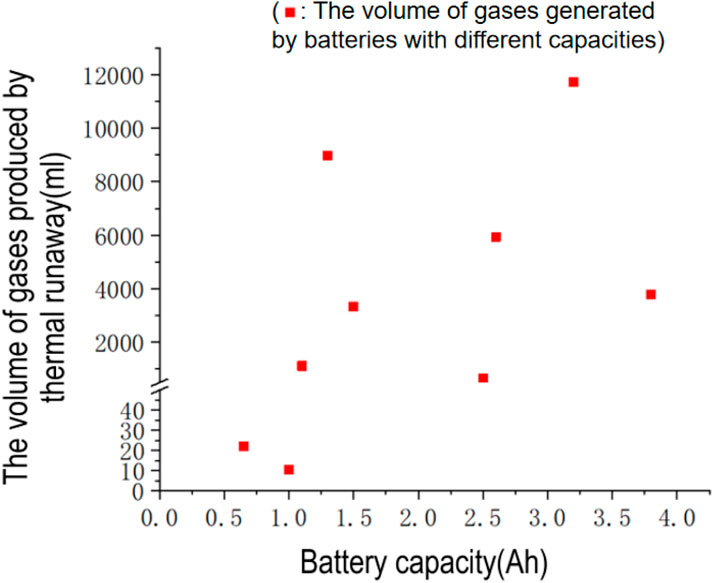
Figure 3. Shows the relationship between lithium battery capacity and the gas generation rate during thermal runaway.
2.4 Lithium battery thermal runaway gas detection technologies
In the general field, common gas detection technologies and sensors include semiconductor-based [40], electrochemical [41, 42], optical [43–45], thermal gas sensors [46–48], acoustic [50, 51], and gas chromatography-mass spectrometry [49, 52–54], among others. Currently, specific technologies applied to lithium battery thermal runaway gas monitoring mentioned in literature include gas chromatography [23, 55, 56], electrochemical mass spectrometry [57], Fourier transform infrared spectroscopy [58, 59], Raman spectroscopy [40, 60], non-dispersive infrared gas detection [61], and metal-oxide semiconductor gas sensor technologies [62].
Firstly, we explore the application of Gas Chromatography (GC) technology in studies related to lithium-ion battery thermal runaway. Golubkov and others conducted thermal runaway tests on three commercial 18,650 model lithium-ion batteries, intentionally introducing overheating under controlled conditions, measuring the temperature and gas release of the batteries at high temperatures [51]. This study utilized gas chromatography technology to quantitatively analyze the main gas components, emphasizing the close relationship between battery safety and its energy capacity, chemical composition, and design, among other factors. Gachot and colleagues analyzed gases emitted by lithium-ion batteries during thermal runaway using gas chromatography-mass spectrometry, investigated the impact of different cathode materials on battery safety, and identified CO2 as a potential target gas for detection, as shown in Figure 4 [56]. This research highlights the potential application prospects of gas chromatography technology in battery safety studies. Furthermore, Wang and others emphasized the significance of gas chromatography analysis in studies on fire and explosion hazards, proposing a series of optimization goals to improve the design of electrochemical energy storage systems. These goals include increasing the materials’ resistance to high temperatures and heat absorption capacity, reducing the propagation of heat conduction to combustible elements, and decreasing the probability of gas ignition, providing guidance for future battery safety assessments [55].
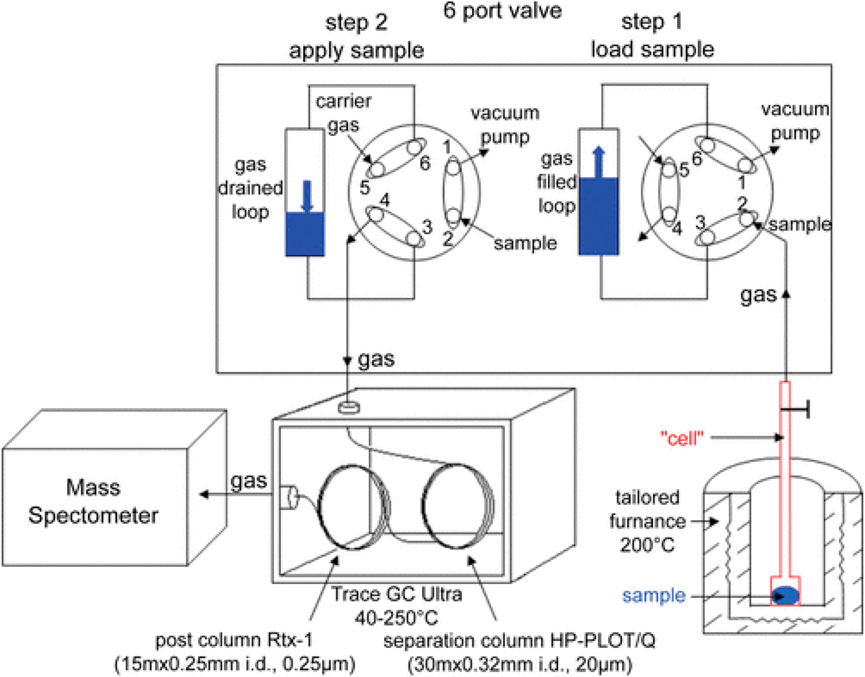
Figure 4. Illustration of gas chromatography-mass spectrometry experimental system for lithium battery thermal runaway gases [56].
Fourier Transform Infrared (FTIR) spectroscopy plays a crucial role in the study of lithium battery thermal runaway [63]. Chen and colleagues used FTIR to analyze the gas composition and combustion/explosion characteristics produced by electric vehicle lithium-ion battery systems under thermal runaway fire conditions. By employing an FTIR spectrometer, they conducted a detailed study on the characteristics of gas generation and explosion risks within the battery compartment, finding that the gases had a strong combustion/explosion performance during the jet fire stage, influenced by inert gases and hydrogen [58]. Srinivasan and colleagues utilized real-time in situ Fourier Transform Infrared spectroscopy to analyze the gas composition of ejecta during lithium-ion battery thermal runaway. They revealed that a large amount of carbonate esters were ejected before the battery entered thermal runaway, and these gases could ignite upon cooling, transmitting heat and causing adjacent batteries to also enter a state of thermal runaway. These studies emphasize the critical role of FTIR technology in understanding the mechanisms and propagation processes of lithium battery thermal runaway, providing important insights and methodologies for preventing and managing thermal runaway events [59].
Raman spectroscopy can also be used to measure the gas composition and explosion risk in real-time during the lithium-ion battery thermal runaway process. Chen Da and colleagues employed high temporal resolution laser Raman spectroscopy to successfully construct a quantitative Raman spectroscopy model of characteristic gases, including air components, that can analyze the changes in gas composition in actual scenarios of lithium-ion battery thermal runaway online and in situ. This technique, with its high correlation coefficient and low root mean square error, can efficiently analyze multi-component gases online, offering an effective means for studying gases released by lithium-ion battery thermal runaway, thus promising accurate assessment of explosion risks [60]. Wan Fu from Chongqing University proposed a novel method for the early, non-destructive, and simultaneous analysis of gas products from lithium-ion battery thermal runaway based on hollow-core anti-resonant fiber-enhanced Raman spectroscopy, as shown in Figure 5. By combining two filtering methods, the background noise level of the system was effectively reduced, optimizing the detection performance of the sensing device. Within a 60-s integration time, simultaneous high-sensitivity detection of seven main thermal runaway gas products was successfully achieved, demonstrating the device’s potential for early detection of thermal runaway faults. Moreover, it can be directly connected to batteries, pushing gas analysis towards online and integrated directions [64].
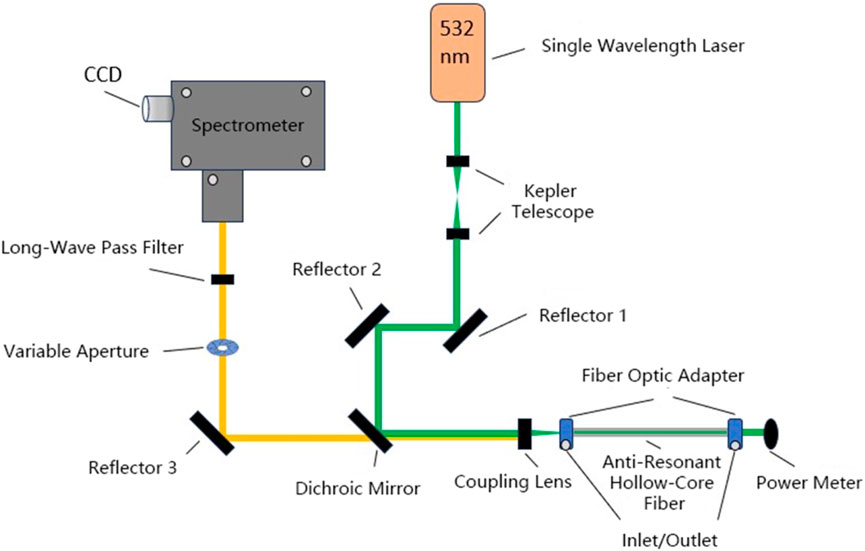
Figure 5. Schematic diagram of Raman spectroscopy gas analysis experimental apparatus [64].
Differential Electrochemical Mass Spectrometry (DEMS) is an advanced analytical technique that combines an electrochemical cell with a mass spectrometer. Hu and others used NMC as the model material and explored the gas generation mechanisms of single-crystal and polycrystalline NMC during electrochemical testing through the use of coin cells and pouch cells [57]. The study utilized in situ Differential Electrochemical Mass Spectrometry analysis to monitor gas generation, employing argon as the inert carrier gas, in conjunction with an HPR-40 mass spectrometer and ECC-DEMS battery for electrochemical testing. In the experiments, batteries utilized both original and cycled cathode materials, with charge/discharge rates at 0.2 C. This research provides valuable information for understanding the gas generation behavior of lithium battery materials, especially the safety of nickel-rich cathode materials, highlighting the importance of differential electrochemical mass spectrometry technology in foundational battery diagnostic studies.
Metal Oxide Semiconductor (MOS) gas sensors are gas sensors that have advantages in terms of cost or size. In Figure 6 Wenger and colleagues adopted MOS gas sensors as a key technology for monitoring gases in large lithium-ion battery systems to detect potential faults early and enhance safety [62]. These tiny silicon substrate and sensitive layer sensors are capable of sensing changes in the concentration of compounds in the surrounding atmosphere, especially volatile organic compounds (VOC) and combustible gases like hydrogen. By measuring changes in gas concentration, these sensors can quickly detect electrolyte leaks within the battery as well as gases released under abuse conditions, issuing early warnings to alert users and initiate emergency shutdown procedures to prevent further damage. The study results showed that these gas sensors could detect increases in VOC concentration even before the battery fails completely, providing earlier warnings for timely intervention.
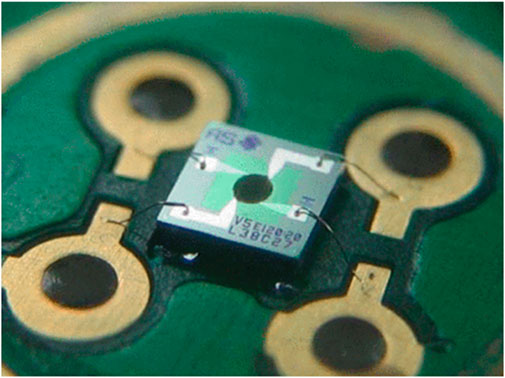
Figure 6. Metal oxide gas sensor based on MEMS process [62].
Non-dispersive Infrared Technology is a gas detection technology characterized by low cost, high sensitivity, and fast response. Cai and others conducted overcharge experiments that led to battery venting, successfully detecting CO2 concentrations over 30,000 ppm using a non-dispersive infrared gas sensor kit [61]. Moreover, they demonstrated how to use venting experiments on a single battery to determine the CO2 concentration threshold for triggering an alarm within a battery pack. This series of studies and experiments clearly highlight the importance and feasibility of non-dispersive infrared gas detection technology in the early detection and warning of lithium-ion battery thermal runaway events, emphasizing its potential in enhancing battery safety.
3 Limitations of the current gas monitoring technologies for battery
In the previous sections, we have discussed common thermal runaway gas detection technologies and their applications as reported in the literature, including Gas Chromatography (GC), Fourier Transform Infrared (FTIR) spectroscopy, Raman spectroscopy, Differential Electrochemical Mass Spectrometry (DEMS), Metal Oxide Semiconductor (MOS) gas sensor technology, and Non-Dispersive Infrared (NDIR) technology. However, these technologies, which have been developed primarily within a laboratory research context, still face numerous limitations and challenges when it comes to actual commercial battery monitoring.
3.1 Technology complexity, suitability, and interference
Current gas detection systems (e.g., GC, DEMS/Online Electrochemical Mass Spectrometry, OEMS) are often large-scale laboratory instruments with complex vacuum environments, high costs, and sophisticated operating requirements [65]. These characteristics make them challenging to integrate into real-world applications such as electric vehicles or large-scale energy storage systems. Continuous sampling can also disturb the internal environment of the battery, potentially causing electrolyte drying or pressure imbalance [66]. Furthermore, many of these methods rely on pouch or customized cells, whereas commercial cylindrical and prismatic cells are harder to modify due to rigid casings. These modifications or additional ports can compromise the structural integrity of the battery, leading to safety risks and discrepancies with actual working conditions.
3.2 Gas evolution, consumption, and monitoring scope
In situ monitoring of gas evolution is complicated by secondary reactions: gases generated after the first charge may gradually be reabsorbed or consumed [67–69]. Techniques like DEMS effectively extract produced gases but have difficulty tracking real-time consumption. Similarly, Online Electrochemical Mass Spectrometry (OEMS) seeks to mitigate pressure fluctuations but still faces non-constant internal gas dynamics and reaction rates [70, 71]. Additionally, many existing methods provide full-spectrum analysis, which is valuable in research but can be cost-prohibitive and overly complex for commercial-scale monitoring. In practical settings, focusing on one or two critical gases (e.g., CO2 for overcharge, H2 for water contamination) can be a viable strategy, albeit with the risk of missing other hazardous byproducts.
3.3 Cost, integration, and challenges with novel battery systems
DEMS, OEMS, and other mass spectrometry-based methods demand specialized equipment and technical expertise, making them expensive for large-scale deployments (e.g., battery packs with thousands of cells). Additional complexities arise with new battery chemistries—such as sodium-ion or all-solid-state systems—which may release different gases (e.g., SO2) that are not always captured by instruments focused on CO2 or H2 [72]. Aqueous-based energy storage systems further require monitoring of H2 and O2 to evaluate water splitting and corrosion [73, 74]. Hence, any long-term, broad-spectrum monitoring solution must be both adaptable to diverse electrode/electrolyte configurations and feasible in large-volume manufacturing.
4 Advantages of optical and fiber sensor for battery monitoring
Fiber optic sensors offer significant advantages over traditional electrical sensors, making them ideal for Battery Management System (BMS) integration to monitor critical cell parameters. As some reports said, silica-based fiber optic cables are immune to Electromagnetic Interference (EMI) and frequency interference while providing electrical insulation [75], and plastic fiber optic cables resist corrosive chemicals in Li-ion battery electrolytes. Furthermore, their lightweight nature, flexibility, and low cost facilitate seamless integration into individual battery cells, enabling internal temperature monitoring. And the high sensitivity, multiplexing and capability of fiber optic sensors allow for the detection of strain, temperature and chemical species to monitor battery status.
Fiber optic sensors are categorized into three types based on their spatial distribution: single-point, quasi-distributed, and fully distributed sensors. Quasi-distributed sensors consist of multiple fixed-point sensors, while fully distributed sensors measure continuously along the entire fiber length, with resolution depending on the interrogation scheme. Fiber optic sensors encode physical parameters through light modulation, including wavelength shifts, frequency changes, and polarization variations. In contrast, Fiber Bragg grating (FBG) sensors, suitable for single-point and quasi-distributed sensing, offer cost-effective multiplexing and self-referencing capabilities, making them attractive for battery management systems.
Fiber optic sensors have been widely studied for gas sensing, particularly for CO2 detection, which is crucial for assessing battery state of health and predicting early cell failure leading to thermal runaway. As previously discussed, lithium-ion batteries release gases, with CO2 comprising a substantial fraction, both prior to and during thermal runaway events. Since CO2 is among the earliest detectable gases before thermal runaway, it is a key indicator for battery health monitoring.
4.1 Principle and applications of fiber optic sensing technology
4.1.1 Optical fiber FP interferometer gas sensors
The Fabry-Perot Interferometer (FPI) sensor is an optical sensor that utilizes interference between two partially reflective surfaces to measure environmental changes. This sensor consists of an optical cavity in which the incident light is reflected several times to form an interference pattern that varies according to parameters such as temperature, pressure, strain or gas concentration. The interference condition is governed by the phase difference between successive reflected beams, The phase shift
where n is the refractive index of the cavity medium, L is the cavity length, and
Figure 7 shows two kinds of FPI sensors. Wu et al. propose a new fiber-optic CO2 sensor that is fabricated by optically printing a dye-free polymer Fabry-Perot Interferometer (FPI) in situ on the fiber end face [77]. This kind of fiber-optic CO2 sensor exhibited good performance in the simultaneous measurement of CO2 concentration and temperature with good sensitivity and selectivity as well as a very wide dynamic operation range.

Figure 7. Extrinsic FPI sensor made by forming an external air cavity, and intrinsic FPI sensor formed by two reflecting components along a fiber [76].
4.1.2 Fiber bragg grating gas sensors
Figure 8 shows the schematic of fiber Brag grating sensor. Fiber Bragg Grating (FBG) sensors operate based on periodic modulations of the refractive index along the optical fiber core. These modulations form a Bragg grating, which selectively reflects light at a specific wavelength, known as the Bragg wavelength, while allowing other wavelengths to pass through. The Bragg wavelength is given by:

Figure 8. Schematic of fiber Brag grating sensor [78].
Where
Zhou et al. design and fabricate cost-effective polymer-coated Fiber Bragg Grating (FBG) gas sensor for the detection of CO2 [79]. They found that the maximum shift of the Bragg wavelength is positively correlated with the coating thickness and negatively correlated with temperature. This FBG sensor exhibits good sensitivity, with a detection limit for CO2 of approximately 0.78%. Additionally, yielding minimum response and recovery times of 3.27 and 3.98 min. Furthermore, the sensor demonstrates excellent selectivity and specificity towards CO2. After prolonged intermittent testing, the sensor exhibited good durability.
4.1.3 Fluorescence-based gas sensors
Fluorescence is a form of luminescence emitted by fluorophores upon absorbing electromagnetic radiation. In fiber optic sensors, fluorescence spectroscopy offers inherent advantages over absorbance-based methods, including higher sensitivity and the flexibility and versatility of fluorophore interactions with various analytes. The detectable signal variations include intensity, lifetime, color, wavelength, and emission polarization. Currently, the two primary fluorescence-based techniques employed in sensing applications are anisotropy decay and quenching. The former is dependent on the time-dependent orientation of fluorophores, while the latter can be described using the Stern–Volmer equation [80], which characterizes the quenching mechanism. Dong et al. present a novel gas sensor integrating Metal-Organic Frameworks (MOF) with fluorescence sensing technology in Figure 9 [81].
The proposed sensor exhibits ultra-high sensitivity and rapid response time, demonstrating superior performance in the detection of various gases, including oxygen and nitrogen oxides (NOx).
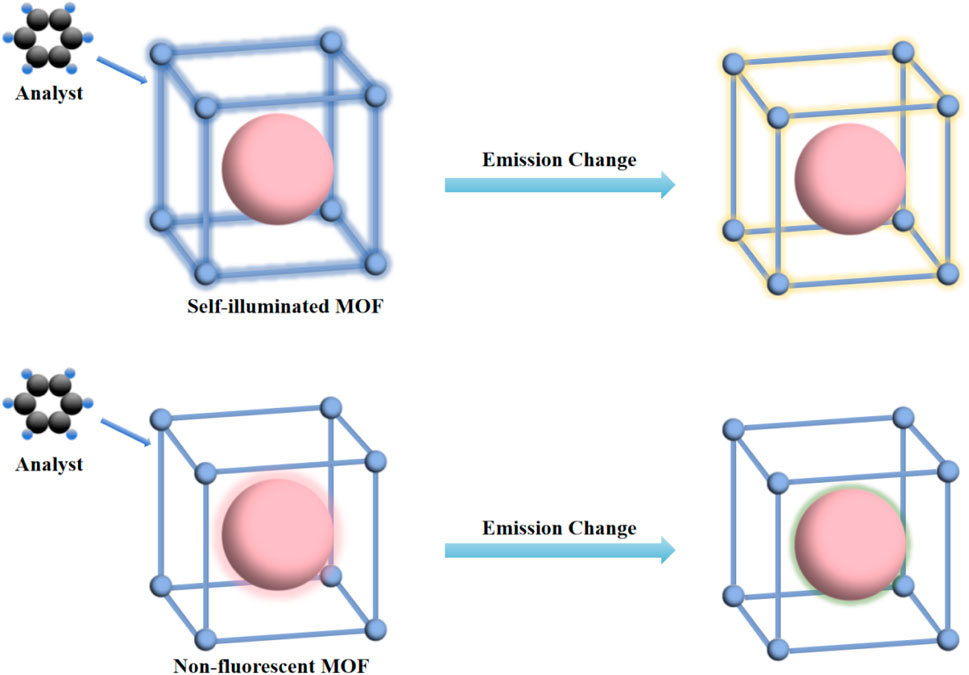
Figure 9. The mechanisms of MOF sensing gas analysts [81].
4.2 Principle and applications of fiber optic sensing technology
Optical fiber sensing technologies have significant potential for gas detection, particularly in providing early warnings for lithium-ion battery thermal runaway. In this section, we wil discusses the main fiber optic gas sensing methods, categorized into direct absorption and indirect interaction techniques. According to the thermal runaway process introduced in Section 2, the main components of the produced gases are CO2, methane, hydrogen, etc., . So therefore, we focus on these three kinds of gases and describe the sensing methods.
4.2.1 Carbon dioxide
The methods for detecting CO2 primarily include direct absorption and indirect interaction techniques. In the direct absorption method, a fully optical fiber CO2 sensor has been proposed [82], utilizing a 74 cm hollow-core photonic crystal fiber as the interaction cavity for light and gas. The main absorption peaks of CO2 are located in the near-infrared and mid-infrared regions, and this sensor detects CO2 based on its absorption in the 2 μm range. Its operational range spans from 2% to 100% CO2 concentration, functioning at three wavelengths, 2003.5 nm, 1997.0 nm, and 1954.5 nm, while maintaining high detection sensitivity across the entire concentration spectrum.
In indirect interaction techniques, the integration of MOF with optical fibers, as previously mentioned, has garnered significant attention. The study in Figure 10 [83] achieved an ultra-low detection limit of less than 20 ppm for CO2, at a wavelength of 1.57 μm by depositing a Cu-benzene-1,3,5-tricarboxylic acid (BTC) MOF thin film on a single-mode optical fiber with a length of only 5 cm.
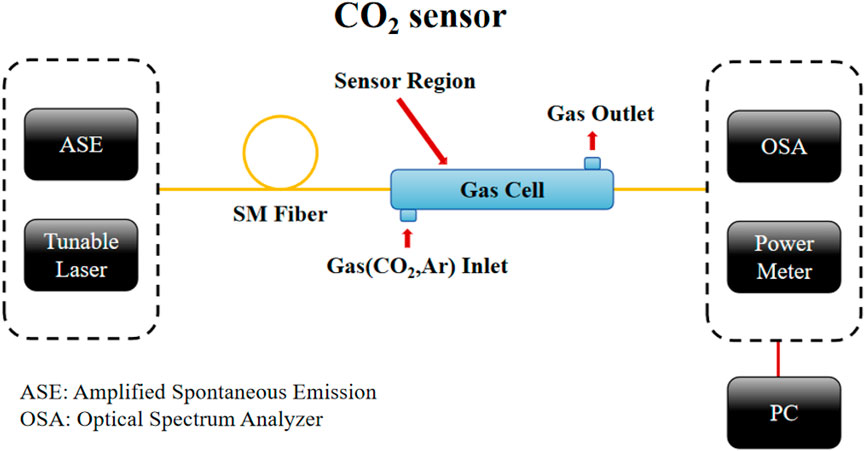
Figure 10. Schematic of the experimental setup for CO2 sensing [83].
Kim et al. demonstrated the use of a simple solution method to uniformly form a dense and stable MOF film on the surface of etched optical fibers [84]. The resulting sensor exhibited high sensitivity and selectivity for CO2 gas, showing a stronger response compared to other small molecular gases such as H2, N2, O2, and CO.
4.2.2 Hydrogen
The absorption peak intensity of hydrogen in the near-infrared region is weak, making it unsuitable for concentration measurement using direct absorption methods. Currently, the methods employed for measuring hydrogen concentration predominantly utilize indirect interaction techniques. Cao et al. presents a method for fabricating optical fiber chemical sensors using a Fabry-Perot interferometer, employing a hydrogen-sensitive palladium (Pd) alloy as the sensing material. This approach enables reproducible and reversible measurement of hydrogen concentrations, achieving a detection limit of 0.25% at room temperature. The utilization of palladium as an indirect interaction material proves highly effective for hydrogen concentration measurement [85]. And Perrotton et al. show a fiber optic Surface Plasmon Resonance (SPR) sensor design, optimizing the sensor structure [86]. By employing palladium as a sensitive layer for hydrogen detection and depositing a multilayer stack consisting of silver, silica, and palladium onto the exterior of a multimode fiber after removing the optical cladding, a detection limit of 30 nm/90 ppm was achieved. Furthermore, the initial resonance wavelength can be modulated by varying the thickness of the silica layer.
4.2.3 Methane
Analogous to the use of palladium as a gas-sensitive medium for hydrogen detection, graphene can be employed as an indirect interaction medium for methane measurements. Wei et al.present a graphene-based long-period fiber grating (LPFG) surface plasmon resonance (SPR) sensor [87]. A monolayer of graphene is coated onto the Ag film surface of the LPFG SPR sensor to enhance the interaction between the SPR wave and methane molecules, enabling a sensor sensitivity of 0.344 nm%−1.
However, owing to the presence of significant absorption peaks of methane in the near-infrared and mid-infrared regions [88], direct absorption methods are also applicable for methane measurement. Hu et al. introduces a free-space coupling structure [89]. This configuration facilitates the transfer of modes from a single-mode fiber (SMF) into the hollow-core photonic band-gap fibers (HC-PBF), and subsequently, from the HC-PBF to a photodetector. In methane measurements conducted at atmospheric pressure, the optimized sensor, employing an approximately 2 mW laser and a 0.45 m HC-PBF, achieved a detection limit of approximately 4.35 ppm with a 0.5 s averaging time, and a minimum detection limit of approximately 360 ppb with a 75 s averaging time.
4.3 Comparative of fiber-optic gas sensors and conventional detection technologies
Fiber-optic gas sensors are unparalleled in environments demanding EMI immunity, distributed sensing, or operation under extreme conditions. Their dominance in oil and gas, power generation, and aerospace applications underscores this niche. Conversely, electrochemical and NDIR sensors retain superiority in cost-sensitive, high-speed, or single-gas detection scenarios. Future advancements in nanomaterial functionalization and photonic integration may bridge these gaps, but for now, the choice hinges on aligning technological strengths with operational priorities.
4.3.1 Environmental robustness and harsh condition performance
Fiber-optic sensors excel in environments where traditional sensors falter, particularly under extreme temperatures, electromagnetic interference (EMI), and corrosive conditions. Unlike electrochemical sensors, which suffer from electrolyte degradation at high temperatures and humidity fluctuations, fiber-optic systems maintain functionality from cryogenic temperatures to 800°C due to their inorganic, dielectric construction. For instance, distributed fiber-optic networks enable real-time methane monitoring in oil and gas pipelines, where explosive atmospheres and EMI from high-voltage equipment render electrochemical or catalytic sensors unsafe.
4.3.2 Sensitivity and selectivity trade-offs
Electrochemical sensors dominate low-concentration detection (ppm-level) for gases like CO and H2S, leveraging tailored catalytic reactions for high specificity. In contrast, fiber-optic sensors face challenges in discriminating between gases with overlapping absorption spectra. For example, methane (CH4) and ethanol (C2H5OH) exhibit similar near-infrared absorption bands, necessitating advanced signal deconvolution algorithms or functionalized coatings (e.g., graphene oxide) to enhance selectivity. Recent advances in surface plasmon resonance (SPR)-based fiber sensors have improved limits of detection to ppb levels for volatile organic compounds (VOCs), rivaling electrochemical systems. Nevertheless, such enhancements often require costly nanomaterials or complex fabrication, limiting scalability compared to mass-produced electrochemical cells.
NDIR sensors are highly specific for gases with strong IR absorption (e.g., CO2, CH4) fail entirely for diatomic molecules like O2 and N2. Fiber-optic sensors circumvent this limitation through hybrid approaches, such as integrating fluorescent dyes for oxygen sensing. This versatility enables simultaneous multi-gas detection-a feat unattainable with single-purpose electrochemical or NDIR units.
4.3.3 Multiplexing and distributed sensing capabilities
A defining strength of fiber-optic systems lies in their ability to multiplex hundreds of sensors along a single optical fiber using wavelength- or time-division techniques. This capability is transformative for large-scale infrastructure monitoring, such as detecting hydrogen leaks across a fuel cell stack or mapping CO2 plumes in carbon capture facilities. In contrast, electrochemical and catalytic sensors require individual wiring and power supplies, escalating installation and maintenance costs in sprawling installations.
Distributed acoustic sensing (DAS) further extends this advantage by enabling spatially resolved gas detection over kilometers of fiber. For example, methane leaks in underground pipelines can be pinpointed within meters using Rayleigh scattering patterns, a feature absent in point-source technologies like NDIR. However, this scalability comes at the cost of data complexity, demanding advanced machine learning tools to interpret high-dimensional datasets.
4.3.4 Long-term stability and maintenance requirements
Electrochemical sensors suffer from short shelf lives (6–12 months) and progressive electrolyte depletion, necessitating frequent recalibration. Fiber-optic sensors, devoid of consumable components, offer decades-long operational stability-critical for remote or inaccessible deployments.
Optical systems are vulnerable to mechanical degradation (e.g., micro bending losses) and contamination (e.g., dust accumulation on fiber tips). While NDIR sensors use sealed optical chambers to mitigate fouling, fiber-optic variants exposed to particulate-laden environments (e.g., industrial exhaust streams) require periodic cleaning or protective membranes, complicating maintenance protocols.
4.3.5 Cost and scalability considerations
Fiber-optic sensors incur higher upfront costs than electrochemical or catalytic units, driven by specialized components like tunable lasers and high-resolution spectrometers. A single-channel fiber-optic CO2 sensor may cost 3–5× more than an equivalent NDIR unit. However, lifecycle costs favor optical systems in large-scale applications.
Miniaturization remains a hurdle. While Microstructured Optical Fibers (MOFs) and photonic crystal fibers have enabled sub-millimeter sensor diameters, they lag behind microelectromechanical systems-based NDIR sensors in consumer electronics integration.
5 Other types of early warning signals for thermal runaway
In addition to gases serving as early warning signals for lithium-ion battery thermal runaway, electrolyte-based indication methods also represent a viable approach for early-stage detection. Electrolyte-based indication relies on observing changes in the electrolyte composition or physical state, such as electrolyte decomposition products or color changes in indicator additives. These changes typically occur after the battery has reached elevated temperatures and progressed into mid-to-late thermal runaway stages, limiting their utility for early warning. Gas sensor-based detection techniques, particularly semiconductor gas sensors, exploit the early release of characteristic gases (hydrogen, carbon monoxide, carbon dioxide, volatile electrolytes like dimethyl carbonate) during initial thermal runaway stages. These sensors can detect trace gas concentrations rapidly, providing early warnings well before visible or structural damage occurs. Teng et al. highlight specific semiconductor sensors with rapid response times (seconds to minutes) and low detection thresholds (ppb to ppm), which outperform electrolyte-based indicators in early-stage detection capability [90].
Gas sensor-based detection technologies demonstrate superior performance over electrolyte-based indication methods in both response time and detection threshold for early-stage thermal runaway monitoring in lithium-ion batteries. Their ability to provide quantitative, rapid, and sensitive detection of signature gases makes them more suitable for integration into real-time battery management and safety systems.
6 Conclusion and outlook
This article comprehensively summarizes the current state of research and development trends in lithium-ion battery thermal runaway gas detection and early warning technologies. Thermal runaway, as a core issue in lithium-ion battery safety, is crucial for ensuring the safe operation of battery systems. The article provides an integrated analysis of the physicochemical changes in batteries during thermal runaway and the types of gases produced, noting significant differences in gas types produced by different types of lithium-ion batteries during thermal runaway. Moreover, the article deeply explores various thermal runaway gas detection technologies, including gas chromatography, Fourier-transform infrared spectroscopy, Raman spectroscopy, differential electrochemical mass spectrometry, metal oxide semiconductor gas sensors, and non-dispersive infrared technology, each with its unique advantages and applicable scenarios. To provide a clear and intuitive comparison of their respective advantages, a concise table is presented in this work. Table 2 clearly illustrates a comparative overview of the key parameters for various gas sensing methods.
Current detection and early warning technologies face the following issues: 1) Limitations in early warning capabilities. Although existing thermal runaway gas detection technologies can achieve early warning to some extent, they still suffer from delayed response times and insufficient accuracy. In the early stages of battery thermal runaway, the accumulation of gases and pressure changes are relatively slight, making it difficult for existing technologies to quickly and accurately capture these early signals. 2) Costs and practicality of the technology. High-precision gas detection technologies are often costly, which may not be economical for large-scale commercial applications. Additionally, the complexity and maintenance requirements of these technologies could limit their widespread application in actual battery systems. 3) Environmental adaptability and stability issues. Lithium-ion batteries exhibit different thermal runaway characteristics and gas emissions under various usage and environmental conditions. Current detection technologies need further improvement in their adaptability to different conditions and long-term stability.
Optical fiber sensor technologies have emerged as a promising alternative. Their inherent advantages—such as resistance to electromagnetic interference, lightweight and flexible form factors, and the capacity for high-sensitivity, in situ monitoring—make them well-suited for integration into battery management systems. Techniques like Fabry–Perot interferometry, fiber Bragg grating, and fluorescence-based sensing have demonstrated effective detection of critical gases (CO2, H2, and CH4) that serve as early warning signals during thermal runaway.
However, translating these laboratory-scale innovations into scalable, maintainable solutions for commercial battery packs presents a series of practical challenges that must be systematically addressed. Foremost among these challenges is scalability. Commercial battery systems, particularly those employed in electric vehicles and grid storage, consist of thousands of individual cells arranged in complex architectures. Deploying optical sensors across such extensive arrays requires cost-effective manufacturing techniques and standardized integration protocols. Current optical sensor fabrication often involves specialized materials and precision assembly, which limit mass production feasibility. Routing optical fibers or embedding photonic components within densely packed battery modules demands innovative packaging solutions that preserve sensor functionality without compromising cell safety or thermal management.
Optical sensors must endure harsh electrochemical environments characterized by temperature fluctuations, mechanical vibrations, and potential chemical exposure. Ensuring stable sensor performance over the battery’s operational lifespan necessitates robust encapsulation strategies and self-calibration capabilities to mitigate signal drift. Additionally, diagnosing and replacing faulty sensors in densely integrated systems without disrupting battery operation poses logistical complexities. Developing modular sensor architectures and leveraging wireless interrogation methods may alleviate maintenance burdens but require further technological maturation.
While advanced optical sensors offer transformative potential for commercial lithium-ion battery monitoring, overcoming scalability and maintenance challenges is essential for widespread adoption. Future research should focus on developing cost-effective fabrication methods, resilient sensor packaging, modular integration schemes, and intelligent data processing frameworks. Addressing these aspects will pave the way for reliable, scalable optical sensing solutions that enhance battery safety and longevity in real-world applications.
To enhance the efficacy and practicality of lithium-ion battery thermal runaway early warning technologies, the following three recommendations are worth exploring and implementing: 1) Develop multi-parameter integrated detection technologies. Research and develop detection systems that integrate multiple sensors, combining temperature, voltage, current, and gas detection for more comprehensive monitoring of battery operational states [66], thereby improving the accuracy and timeliness of the warning system. 2) Optimize the cost-effectiveness of detection technologies. Focus on reducing costs and simplifying maintenance of existing gas detection technologies to meet the needs of large-scale battery applications. Enhance their commercial potential and competitiveness by improving sensor technology and simplifying design structures. 3) Strengthen testing and optimization under actual application environments. Thoroughly test and optimize gas detection technologies under different usage conditions and environments to enhance their adaptability and long-term stability in various contexts. Additionally, strengthen collaboration with battery manufacturers and users to ensure that these detection technologies can be effectively integrated into battery management systems and function effectively in actual use.
With regard to the influence of regulations and standards on the application of advanced gas detection technologies in lithium-ion batteries, existing standards like UL 2580 and IEC 62619 primarily address traditional detection methods, lacking specific guidelines for novel optical sensors. This regulatory gap creates uncertainty for manufacturers regarding validation, compliance, and certification, thereby slowing technology adoption. Establishing consensus-based standards that define performance, calibration, and durability criteria for advanced sensors is crucial to facilitate regulatory acceptance. Collaborative efforts among sensor developers, battery producers, and regulators can expedite this process. Incorporating optical sensor requirements into current safety standards or developing dedicated protocols would provide clearer pathways for commercialization. Regulations promoting real-time monitoring and proactive safety management can incentivize the use of advanced gas sensors, recognizing their enhanced sensitivity and early-warning capabilities. Conversely, inflexible regulations may hinder innovation by imposing excessive certification burdens. In now situation, clear and adaptable regulatory and standardization frameworks are essential to accelerate the industrial adoption of advanced gas detection technologies, ultimately improving lithium-ion battery safety and reliability.
As new energy technologies continue to develop and be applied, the safety of lithium-ion batteries is receiving increasing attention. Through technological innovation and interdisciplinary collaboration, future gas detection technologies are expected to achieve higher accuracy, faster response times, and lower costs, providing stronger support for battery safety management. Furthermore, with the development of big data and artificial intelligence technologies, applying these technologies to battery safety monitoring and early warning systems can further improve the intelligence and automation level of early warnings, offering more effective means to ensure battery safety.
Author contributions
YQ: Writing – original draft, Writing – review and editing. YaZ: Writing – original draft, Writing – review and editing. ZL: Writing – review and editing, Writing – original draft. QW: Writing – original draft, Writing – review and editing. YiZ: Writing – original draft, Writing – review and editing.
Funding
The author(s) declare that financial support was received for the research and/or publication of this article.
Conflict of interest
Authors YQ, YaZ, ZL, QW, and YiZ were employed by Electric Power Research Institute of Guangdong Power Grid Co., Ltd.
The authors declare that this study received funding from the China Southern Power Grid Co., Ltd. Science and Technology Project Fund (No. GDKJXM20230996). The funder had the following involvement in the study: design, collection, analysis, interpretation of data, the writing of this article, and the decision to submit it for publication.
Generative AI statement
The author(s) declare that no Generative AI was used in the creation of this manuscript.
Publisher’s note
All claims expressed in this article are solely those of the authors and do not necessarily represent those of their affiliated organizations, or those of the publisher, the editors and the reviewers. Any product that may be evaluated in this article, or claim that may be made by its manufacturer, is not guaranteed or endorsed by the publisher.
References
1. Li Z, Chen C, Niu H, Li L. Characteristic parameter analysis of thermal runaway early warning of lithium-ion battery. Fire Sci Tech (2020). Available online at: https://www.xfkj.com.cn/EN/Y2020/V39/I2/146.
2. Wang L, Ding G, Li Z, Zhao Y, Yuan Z, et al. Development of energy storage safety monitoring technology for lithium-ion batteries. Energy and Energy Conservation (2023)(11) 149–52. doi:10.16643/j.cnki.14-1360/td.2023.11.050
3. Xu Z, Zhou X, Fu J, Li Q, Tan Z, Fan X, et al. Monitoring and diagnostic approaches for thermal runaway in lithium-ion batteries. Chin Sci Bull (2023) 68(33):4501–16. doi:10.1360/tb-2023-0273
4. Xu L, Xiao Y, Yang Y, Yang SJ, Chen XR, Xu R, et al. Operando quantified lithium plating determination enabled by dynamic capacitance measurement in working Li-ion batteries. Angew Chem Int Edition (2022) 61(39):e202210365. doi:10.1002/anie.202210365
5. Ping P, Wang Q, Huang P, Sun J, Chen C. Thermal behaviour analysis of lithium-ion battery at elevated temperature using deconvolution method. Appl Energ (2014) 129:261–73. doi:10.1016/j.apenergy.2014.04.092
6. Wang C, Gong L, Kang P, Tan Y, Li M. Research on early warning system of lithium ion battery energy storage power station. Energy Storage Sci Tech (2018) 7(6):1152. doi:10.12028/j.issn.2095-4239.2018.0174
7. Maleki H, Howard JN. Effects of overdischarge on performance and thermal stability of a Li-ion cell. J Power Sourc (2006) 160(2):1395–402. doi:10.1016/j.jpowsour.2006.03.043
8. Su T, Lyu N, Zhao Z, Wang H, Jin Y. Safety warning of lithium-ion battery energy storage station via venting acoustic signal detection for grid application. J Energ storage (2021) 38:102498. doi:10.1016/j.est.2021.102498
9. Wang L, Lu C, Ge J, Huang Z, Li B. Mechanism of adhesion failure of electric vehicle high voltage relays. Mod Ind Economy Informationization (2022) 12(03):47–8+65. doi:10.16525/j.cnki.14-1362/n.2022.03.014
10. Huangbu C. The early fire detection technology and equipment development of power lithium battery thermal runaway. Master's thesis. Huaqiao University (2018). Available online at: https://kns.cnki.net/kcms2/article/abstract?v=X0pQrW14MItNtyEDMrAwL4fbcgfwtP-Sa11TinjHx3mqyeMO_omg-fcvz02FR2xNttVTo9uIdcLeuWbXn5dBUm1R_zGdC35BKUxNzg1sFvvrlOWp1g2nkaWbmzyzuSCG8Dop8EtqSbY4TX9W2bUTgB2rMP8eg70Fd6xKQS2sTBxi8ZdZ6OIsI-sQOmlM8D2Qry5mRK_2yZA=&uniplatform=NZKPT&language=CHS.
11. Wang Q, Mao B, Stoliarov SI, Sun J. A review of lithium ion battery failure mechanisms and fire prevention strategies. Prog Energy Combustion Sci (2019) 73:95–131. doi:10.1016/j.pecs.2019.03.002
12. Spotnitz R, Franklin J. Abuse behavior of high-power, lithium-ion cells. J Power Sourc (2003) 113(1):81–100. doi:10.1016/s0378-7753(02)00488-3
13. Zou K, Lu S, Chen X, Gao E, Cao Y, Bi Y. Thermal and gas characteristics of large-format LiNi0. 8Co0. 1Mn0. 1O2 pouch power cell during thermal runaway. J Energy Storage (2021) 39:102609. doi:10.1016/j.est.2021.102609
14. Allen J. Review of polymers in the prevention of thermal runaway in lithium-ion batteries. Energy Rep (2020) 6:217–24. doi:10.1016/j.egyr.2020.03.027
15. Huang Z, Zhao C, Li H, Peng W, Zhang Z, Wang Q. Experimental study on thermal runaway and its propagation in the large format lithium ion battery module with two electrical connection modes. Energy (2020) 205:117906. doi:10.1016/j.energy.2020.117906
16. Tan Z, Zhou X, Xu Z, Fan X, Tian B, Wang Z, et al. Research progress of gas-sensing technologies for the monitoring and early warning of thermal runaway in lithium-ion batteries. Energy Storage Sci Tech (2023) 12(11):3456–70. doi:10.19799/j.cnki.2095-4239.2023.0386
17. Zhang Q, Liu T, Hao C, Qu Y, Niu J, Wang Q, et al. In situ Raman investigation on gas components and explosion risk of thermal runaway emission from lithium-ion battery. J Energy Storage (2022) 56:105905. doi:10.1016/j.est.2022.105905
18. Golubkov AW, Fuchs D, Wagner J, Wiltsche H, Stangl C, Fauler G, et al. Thermal-runaway experiments on consumer Li-ion batteries with metal-oxide and olivin-type cathodes. RSC Adv (2014) 4(7):3633–42. doi:10.1039/c3ra45748f
19. Yuan L, Dubaniewicz T, Zlochower I, Thomas R, Rayyan N. Experimental study on thermal runaway and vented gases of lithium-ion cells. Process Saf Environ Prot (2020) 144:186–92. doi:10.1016/j.psep.2020.07.028
20. Zhang Q, Liu T, Hao C, Qu Y, Zhang W, Chen D. Rapid detection analysis method of thermal runaway gas composition and risk of lithium ion battery. J Beijing Univ Aeronautics Astronautics (2023) 49(9):2227–33. doi:10.13700/j.bh.1001-5965.2021.0668
21. Jin Y, Zheng Z, Wei D, Jiang X, Lu H, Sun L, et al. Detection of micro-scale Li dendrite via H2 gas capture for early safety warning. Joule (2020) 4(8):1714–29. doi:10.1016/j.joule.2020.05.016
22. Larsson F, Bertilsson S, Furlani M, Albinsson I, Mellander BE. Gas explosions and thermal runaways during external heating abuse of commercial lithium-ion graphite-LiCoO2 cells at different levels of ageing. J Power Sourc (2018) 373:220–31. doi:10.1016/j.jpowsour.2017.10.085
23. Fernandes Y, Bry A, De Persis S. Identification and quantification of gases emitted during abuse tests by overcharge of a commercial Li-ion battery. J Power Sourc (2018) 389:106–19. doi:10.1016/j.jpowsour.2018.03.034
24. Hoelle S, Scharner S, Asanin S, Hinrichsen O. Analysis on thermal runaway behavior of prismatic lithium-ion batteries with autoclave calorimetry. J The Electrochem Soc (2021) 168(12):120515. doi:10.1149/1945-7111/ac3c27
25. Essl C, Golubkov AW, Gasser E, Nachtnebel M, Zankel A, Ewert E, et al. Comprehensive hazard analysis of failing automotive lithium-ion batteries in overtemperature experiments. Batteries (2020) 6(2):30. doi:10.3390/batteries6020030
26. Sturk D, Rosell L, Blomqvist P, Ahlberg Tidblad A. Analysis of li-ion battery gases vented in an inert atmosphere thermal test chamber. Batteries (2019) 5(3):61. doi:10.3390/batteries5030061
27. Lammer M, Königseder A, Hacker V. Holistic methodology for characterisation of the thermally induced failure of commercially available 18650 lithium ion cells. RSC Adv (2017) 7(39):24425–9. doi:10.1039/C7RA02635H
28. Abraham DP, Roth EP, Kostecki R, McCarthy K, MacLaren S, Doughty DH. Diagnostic examination of thermally abused high-power lithium-ion cells. J Power Sourc (2006) 161(1):648–57. doi:10.1016/j.jpowsour.2006.04.088
29. Koch S, Fill A, Birke KP. Comprehensive gas analysis on large scale automotive lithium-ion cells in thermal runaway. J Power Sourc (2018) 398:106–12. doi:10.1016/j.jpowsour.2018.07.051
30. Sun J, Li J, Zhou T, Yang K, Wei S, Tang N, et al. Toxicity, a serious concern of thermal runaway from commercial Li-ion battery. Nano Energy (2016) 27:313–9. doi:10.1016/j.nanoen.2016.06.031
31. Du G, Zheng L, Zhang Z, Wang D, Feng Y, Dai Z. Experimental study on high temperature thermal runaway of cylindrical high nickel ternary lithium-ion batteries. Energy Storage Sci Tech (2020) 9(1):249. doi:10.12028/j.issn.2095-4239.2019.0164
32. Zhuang C, Huang H, Hu M, Huang Y, Qiu D. Design and experimental study on thermal runaway data acquisition experiment system. Lab Sci (2022) 25(2):14–8. doi:10.3969/j.issn.1672-4305.2022.02.003
33. Ohsaki T, Kishi T, Kuboki T, Takami N, Shimura N, Sato Y, et al. Overcharge reaction of lithium-ion batteries. J Power Sourc (2005) 146(1-2):97–100. doi:10.1016/j.jpowsour.2005.03.105
34. Kumai K, Miyashiro H, Kobayashi Y, Takei K, Ishikawa R. Gas generation mechanism due to electrolyte decomposition in commercial lithium-ion cell. J Power Sourc (1999) 81:715–9. doi:10.1016/s0378-7753(98)00234-1
35. Yuan Q, Zhao F, Wang W, Zhao Y, Liang Z, Yan D. Overcharge failure investigation of lithium-ion batteries. Electrochimica Acta (2015) 178:682–8. doi:10.1016/j.electacta.2015.07.147
36. Zhang Y, Wang H, Li W, Li C. Quantitative identification of emissions from abused prismatic Ni-rich lithium-ion batteries. ETransportation (2019) 2:100031. doi:10.1016/j.etran.2019.100031
37. Kriston A, Adanouj I, Ruiz V, Pfrang A. Quantification and simulation of thermal decomposition reactions of Li-ion battery materials by simultaneous thermal analysis coupled with gas analysis. J Power Sourc (2019) 435:226774. doi:10.1016/j.jpowsour.2019.226774
38. Bertilsson S, Larsson F, Furlani M, Albinsson I, Mellander BE. Lithium-ion battery electrolyte emissions analyzed by coupled thermogravimetric/Fourier-transform infrared spectroscopy. J Power Sourc (2017) 365:446–55. doi:10.1016/j.jpowsour.2017.08.082
39. Wang Z, Zhu L, Liu J, Wang J, Yan W. Gas sensing technology for the detection and early warning of battery thermal runaway: a review. Energy and fuels (2022) 36(12):6038–57. doi:10.1021/acs.energyfuels.2c01121
40. Kanan SM, El-Kadri OM, Abu-Yousef IA, Kanan MC. Semiconducting metal oxide based sensors for selective gas pollutant detection. Sensors (2009) 9(10):8158–96. doi:10.3390/s91008158
41. Hatfield JV, Neaves P, Hicks PJ, Persaud K, Travers P. Towards an integrated electronic nose using conducting polymer sensors. Sensors Actuators B: Chem (1994) 18(1-3):221–8. doi:10.1016/0925-4005(94)87086-1
42. Siden J, Zeng X, Unander T, Koptyug A, Nilsson HE. Remote moisture sensing utilizing ordinary RFID tags. In: SENSORS, 2007 ieee. IEEE (2007). p. 308–11.
43. Wang C, Xie J, Zhuang R, Lin H, Lin L, Cui R, et al. Highly sensitive carbon dioxide gas sensor based on 2μm laser diode and herriott multi-pass absorption cell(invited). Acta Photonica Sinica (2023) 52(10):77–86. doi:10.3788/gzxb20235210.1052406
44. Bond TC, Cole GD, Goddard LL, Behymer EM. Photonic MEMS for NIR in-situ gas detection and identification. In: SENSORS, 2007 ieee. IEEE (2007). p. 1368–71.
45. Arunajatesan V, Subramaniam B, Hutchenson KW, Herkes FE. In situ FTIR investigations of reverse water gas shift reaction activity at supercritical conditions. Chem Eng Sci (2007) 62(18-20):5062–9. doi:10.1016/j.ces.2007.01.010
46. Kulinyi S, Brandszájsz D, Amine H, Ádám M, Fürjes P, Bársony I, et al. Olfactory detection of methane, propane, butane and hexane using conventional transmitter norms. Sensors Actuators B: Chem (2005) 111:286–92. doi:10.1016/j.snb.2005.06.068
47. Loui A, Elhadj S, Sirbuly DJ, McCall SK, Hart BR, Ratto TV. An analytic model of thermal drift in piezoresistive microcantilever sensors. J Appl Phys (2010) 107(5). doi:10.1063/1.3326972
48. Tardy P, Coulon JR, Lucat C, Menil F. Dynamic thermal conductivity sensor for gas detection. Sensors Actuators B: Chem (2004) 98(1):63–8. doi:10.1016/j.snb.2003.09.019
49. Kim KH. Performance characterization of the GC/PFPD for H2S, CH3SH, DMS, and DMDS in air. Atmos Environ (2005) 39(12):2235–42. doi:10.1016/j.atmosenv.2004.12.039
50. King WH. Piezoelectric sorption detector. Anal Chem (1964) 36(9):1735–9. doi:10.1021/ac60215a012
51. Minglei S, Xiang L, Changping Z, Jiahua Z. Gas concentration detection using ultrasonic based on wireless sensor networks. In: The 2nd international conference on information science and engineering. IEEE (2010). p. 2101–6.
52. Golubkov AW, Scheikl S, Planteu R, Voitic G, Wiltsche H, Stangl C, et al. Thermal runaway of commercial 18650 Li-ion batteries with LFP and NCA cathodes–impact of state of charge and overcharge. RSC Adv (2015) 5(70):57171–86. doi:10.1039/c5ra05897j
53. van Ruth SM. Evaluation of two gas chromatography–olfactometry methods: the detection frequency and perceived intensity method. J Chromatogr A (2004) 1054(1-2):33–7. doi:10.1016/j.chroma.2004.05.046
54. Liu X, Cheng S, Liu H, Hu S, Zhang D, Ning H. A survey on gas sensing technology. Sensors (2012) 12(7):9635–65. doi:10.3390/s120709635
55. Wang H, Xu H, Zhang Z, Wang Q, Jin C, Wu C, et al. Fire and explosion characteristics of vent gas from lithium-ion batteries after thermal runaway: a comparative study. ETransportation (2022) 13:100190. doi:10.1016/j.etran.2022.100190
56. Gachot G, Ribière P, Mathiron D, Grugeon S, Armand M, Leriche JB, et al. Gas chromatography/mass spectrometry as a suitable tool for the Li-ion battery electrolyte degradation mechanisms study. Anal Chem (2011) 83(2):478–85. doi:10.1021/ac101948u
57. Hu J, Li L, Bi Y, Tao J, Lochala J, Liu D, et al. Locking oxygen in lattice: a quantifiable comparison of gas generation in polycrystalline and single crystal Ni-rich cathodes. Energy Storage Mater (2022) 47:195–202. doi:10.1016/j.ensm.2022.02.025
58. Chen Q, Wang X, Mi W. Experiential study on the toxic and explosive characteristics of thermal runaway gas generated in electric-vehicle lithium-ion battery systems. Energy Storage Sci Tech (2023) 12(7):2256. doi:10.19799/j.cnki.2095-4239.2023.0294
59. Srinivasan R, Thomas ME, Airola MB, Carkhuff BG, Frizzell-Makowski LJ, Alkandry H, et al. Preventing cell-to-cell propagation of thermal runaway in lithium-ion batteries. J The Electrochem Soc (2020) 167(2):020559. doi:10.1149/1945-7111/ab6ff0
60. Chen D, Hao C, Liu T, Han Z, Zhang W. Raman spectrum analysis method of thermal runaway gas from lithium-ion batteries. Chin J Lasers (2022) 49(23):2311001. doi:10.3788/cjl202249.2311001
61. Cai T, Valecha P, Tran V, Engle B, Stefanopoulou A, Siegel J. Detection of Li-ion battery failure and venting with Carbon Dioxide sensors. ETransportation (2021) 7:100100. doi:10.1016/j.etran.2020.100100
62. Wenger M, Waller R, Lorentz VR, März M, Herold M. Investigation of gas sensing in large lithium-ion battery systems for early fault detection and safety improvement. In: IECON 2014-40th annual conference of the IEEE industrial electronics society. IEEE (2014). p. 5654–9.
63. Baraton MI, Merhari L. Investigation of the gas detection mechanism in semiconductor chemical sensors by FTIR spectroscopy. Synthesis and Reactivity in Inorganic, Metal-Organic. Nano-Metal Chem (2005) 35(10):733–42. doi:10.1080/15533170500359794
64. Wan F, Liu Q, Kong W, Luo Z, Gao S, Wang Y, et al. High-sensitivity lithium-ion battery thermal runaway gas detection based on fiber-enhanced Raman spectroscopy. IEEE Sensors J (2023) 23(7):6849–56. doi:10.1109/jsen.2023.3243213
65. Zhang J, Lei E, Luo W, Jin L, Ma K. Fault diagnosis method for lithium-ion battery based on multi-algorithm fusion. Guangdong Electric Power (2024) 37(7):50–7.
66. Bernhard R, Meini S, Gasteiger HA. On-line electrochemical mass spectrometry investigations on the gassing behavior of Li4Ti5O12 electrodes and its origins. J The Electrochem Soc (2014) 161(4):A497–505. doi:10.1149/2.013404jes
67. Aiken CP, Xia J, Wang DY, Stevens DA, Trussler S, Dahn JR. An apparatus for the study of in situ gas evolution in Li-ion pouch cells. J The Electrochem Soc (2014) 161(10):A1548–54. doi:10.1149/2.0151410jes
68. Aiken CP, Self J, Petibon R, Xia X, Paulsen JM, Dahn JR. A survey of in situ gas evolution during high voltage formation in Li-ion pouch cells. J The Electrochem Soc (2015) 162(4):A760–7. doi:10.1149/2.0941504jes
69. Ellis LD, Allen JP, Thompson LM, Harlow JE, Stone WJ, Hill IG, et al. Quantifying, understanding and evaluating the effects of gas consumption in lithium-ion cells. J The Electrochem Soc (2017) 164(14):A3518–28. doi:10.1149/2.0191714jes
70. Lundström R, Berg EJ. Design and validation of an online partial and total pressure measurement system for Li-ion cells. J Power Sourc (2021) 485:229347. doi:10.1016/j.jpowsour.2020.229347
71. Misiewicz C, Lundström R, Ahmed I, Lacey MJ, Brant WR, Berg EJ. Online electrochemical mass spectrometry on large-format Li-ion cells. J Power Sourc (2023) 554:232318. doi:10.1016/j.jpowsour.2022.232318
72. Zheng T, Muneeswara M, Bao H, Huang J, Zhang L, Hall DS, et al. Gas evolution in Li-ion rechargeable batteries: a review on operando sensing technologies, gassing mechanisms, and emerging trends. ChemElectroChem (2024) 11(15):e202400065. doi:10.1002/celc.202400065
73. He M, Fic K, Fra E, Novák P, Berg EJ. Ageing phenomena in high-voltage aqueous supercapacitors investigated by in situ gas analysis. Energy and Environ Sci (2016) 9(2):623–33. doi:10.1039/C5EE02875B
74. Ma L, Li Q, Ying Y, Ma F, Chen S, Li Y, et al. Toward practical high-areal-capacity aqueous zinc-metal batteries: quantifying hydrogen evolution and a solid-ion conductor for stable zinc anodes. Adv Mater (2021) 33(12):2007406. doi:10.1002/adma.202007406
75. Chen H, Buric M, Ohodnicki PR, Nakano J, Liu B, Chorpening BT. Review and perspective: sapphire optical fiber cladding development for harsh environment sensing. Appl Phys Rev (2018) 5(1). doi:10.1063/1.5010184
76. Lee BH, Kim YH, Park KS, Eom JB, Kim MJ, Rho BS, et al. Interferometric fiber optic sensors. Sensors (2012) 12(3):2467–86. doi:10.3390/s120302467
77. Wu J, Yin MJ, Seefeldt K, Dani A, Guterman R, Yuan J, et al. In situ μ-printed optical fiber-tip CO2 sensor using a photocrosslinkable poly (ionic liquid). Sensors Actuators B: Chem (2018) 259:833–9. doi:10.1016/j.snb.2017.12.125
78. Chen X, Gan L, Guo X. Optical fiber-based gas sensing for early warning of thermal runaway in lithium-ion batteries. Adv Sensor Res (2023) 2(12):2300055. doi:10.1002/adsr.202300055
79. Zhou Z, Xu Y, Qiao C, Liu L, Jia Y. A novel low-cost gas sensor for CO2 detection using polymer-coated fiber Bragg grating. Sensors Actuators B: Chem (2021) 332:129482. doi:10.1016/j.snb.2021.129482
80. Su YD, Preger Y, Burroughs H, Sun C, Ohodnicki PR. Fiber optic sensing technologies for battery management systems and energy storage applications. Sensors (2021) 21(4):1397. doi:10.3390/s21041397
81. Dong R, Shen Z, Li H, Cheng J, Fu Y. Research progress in fluorescent gas sensors based on MOFs. J Mater Chem C (2024) 12:12692–707. doi:10.1039/d4tc02491e
82. Mejia Quintero SM, Guedes Valente LC, de Paula Gomes MS, Gomes da Silva H, Caroli de Souza B, Morikawa SR. All-fiber CO2 sensor using hollow core PCF operating in the 2 µm region. Sensors (2018) 18(12):4393. doi:10.3390/s18124393
83. Chong X, Kim KJ, Li E, Zhang Y, Ohodnicki PR, Chang CH, et al. Near-infrared absorption gas sensing with metal-organic framework on optical fibers. Sensors Actuators B: Chem (2016) 232:43–51. doi:10.1016/j.snb.2016.03.135
84. Kim KJ, Lu P, Culp JT, Ohodnicki PR. Metal–organic framework thin film coated optical fiber sensors: a novel waveguide-based chemical sensing platform. ACS sensors (2018) 3(2):386–94. doi:10.1021/acssensors.7b00808
85. Cao R, Yang Y, Wang M, Yi X, Wu J, Huang S, et al. Multiplexable intrinsic Fabry–Perot interferometric fiber sensors for multipoint hydrogen gas monitoring. Opt Lett (2020) 45(11):3163–6. doi:10.1364/ol.389433
86. Perrotton C, Javahiraly N, Slaman M, Dam B, Meyrueis P. Fiber optic surface plasmon resonance sensor based on wavelength modulation for hydrogen sensing. Opt Express (2011) 19(S6):A1175–A1183. doi:10.1364/oe.19.0a1175
87. Wei W, Nong J, Zhang G, Tang L, Jiang X, Chen N, et al. Graphene-based long-period fiber grating surface plasmon resonance sensor for high-sensitivity gas sensing. Sensors (2016) 17(1):2. doi:10.3390/s17010002
88. Cubillas AM, Lazaro JM, Conde OM, Petrovich MN, Lopez-Higuera JM. Gas sensor based on photonic crystal fibres in the 2 ν 3 and ν 2+ 2 ν 3 vibrational bands of methane. Sensors (2009) 9(8):6261–72. doi:10.3390/s90806261
89. Hu L, Zheng C, Yao D, Yu D, Liu Z, Zheng J, et al. A hollow-core photonic band-gap fiber based methane sensor system capable of reduced mode interference noise. Infrared Phys and Tech (2019) 97:101–7. doi:10.1016/j.infrared.2018.12.023
Keywords: gas detection, lithium-ion battery, thermal runaway, optical fiber, spectroscopy
Citation: Qian Y, Zhao Y, Li Z, Wang Q and Zhao Y (2025) Gas detection technology for thermal runaway of lithium-ion batteries. Front. Phys. 13:1615872. doi: 10.3389/fphy.2025.1615872
Received: 22 April 2025; Accepted: 22 May 2025;
Published: 23 June 2025.
Edited by:
Xukun Yin, Xidian University, ChinaReviewed by:
Qiang Wang, Chinese Academy of Sciences (CAS), ChinaWeilin Ye, Shantou University, China
Ruyue Cui, Shanxi University, China
Copyright © 2025 Qian, Zhao, Li, Wang and Zhao. This is an open-access article distributed under the terms of the Creative Commons Attribution License (CC BY). The use, distribution or reproduction in other forums is permitted, provided the original author(s) and the copyright owner(s) are credited and that the original publication in this journal is cited, in accordance with accepted academic practice. No use, distribution or reproduction is permitted which does not comply with these terms.
*Correspondence: Yaohong Zhao, a2Vubnlhb29AMTI2LmNvbQ==