- 1Department of Civil Engineering, Hubei Urban Construction Vocational and Technological College, Wuhan, China
- 2State Key Laboratory of Silicate Materials for Architectures, Wuhan University of Technology, Wuhan, China
- 3School of Materials Science and Engineering, Wuhan University of Technology, Wuhan, China
The effects of pre-dispersing metakaolin (MK) in water on the properties and hydration of mortar and distribution of MK particles in mortar were characterized by analytical techniques. Zeta-potential of MK-water dispersion significantly decreased with the increase of pH of solution, resulting in a stable dispersion at pH of 8 with zeta-potential of −40 mV. The bulk density of MK-water slurry rapidly increased with water/MK ratio due to the surface tension force of water and filling of spaces by water, resulting in a maximum bulk density of 665.2 kg/m3 at water/MK ratio of 1.0. Comparing to that of powder MK, pre-dispersing MK in water did not alter hydration products, slightly improved compressive strength, and pore structure, but further reduced shrinkage and significantly improved the uniformed distribution of MK particles in mortar.
Introduction
Concrete is one of the most used man-made materials for construction, due to its availability, suitable workability, properties, and durability. However, concrete has been criticized in recent decades for its contribution to CO2 footprint, which is mainly from one of its components, Portland cement (Scrivener and Kirkpatrick, 2008). To reduce the CO2 footprint of construction industry, mineral additives have been introduced to concrete in the aim to reduce the amount of Portland cement required. Mineral additives include fly ash, silica fume, slag, and metakaolin (MK). Mineral additives are usually amorphous in nature with high silicate/aluminate content, which can react with calcium hydroxide formed during hydration of Portland cement through pozzolanic reaction (Taylor, 1997).
MK attracted much attention among mineral additives recently due to its high contribution to strength and durability when introduced to concrete (Frias and Cabrera, 2000; Aquino et al., 2001; Gueneyisi et al., 2008; Goncalves et al., 2009; Shui et al., 2010; Fernandez et al., 2011; Rashad, 2013), resulting from its effect of acceleration of hydration of Portland cement and refinement of pore structure of concrete or mortar (Buchwald et al., 2007; Lagier and Kurtis, 2007; Cassagnabere et al., 2010; Li et al., 2010; Kadri et al., 2011). MK is manufactured by calcining kaolin at 650–800°C to remove interlayer water and OH− resulting in the deterioration of long-range order of silicon-aluminum layer structure (Murat and Comel, 1983; He et al., 1995; Badogiannis et al., 2005; Rashad, 2013). Amorphous MK with pozzolanic activity was obtained with formula of Al2O3·2SiO2 (Coleman and McWhinnie, 2000; Sabir et al., 2001; Love et al., 2007; Bich et al., 2009; Fernandez et al., 2011). When MK was added into concrete, the compressive strength could be improved, permeability, and porosity could be decreased and pore structure could be refined due to the filler effect, acceleration of hydration, and pozzolanic reaction with CH to form C-S-H (Wild et al., 1996; Aquino et al., 2001; Lagier and Kurtis, 2007; Gueneyisi et al., 2008; Shui et al., 2010; Fernandez et al., 2011; Kadri et al., 2011). The compressive strength increased with the content of MK, and the maximum effect was reached at 28 days as observed by many researchers previously (Justice and Kurtis, 2007; Khatib, 2008, 2009; Arikan et al., 2009; Johari et al., 2011; Kadri et al., 2011; Antoni et al., 2012; Li et al., 2015). The early age (before 24 h) autogenous shrinkage of concrete decreased with the increase of content of MK due to the dilution effect of MK, although the long-term autogenous shrinkage of concrete containing MK could be higher than that of control specimen, due to the acceleration of Portland cement hydration, and pozzolanic reaction by MK with calcium hydroxide (Kinuthia et al., 2000; Brooks and Johari, 2001). With the increase of MK addition, the drying shrinkage of concrete could be significantly reduced by 50%, comparing to the control specimen, due to the reduced amount of evaporable water as a result of hydration, and pozzolanic reaction (Brooks and Johari, 2001).
Due to the high specific surface area and small particle size, there is a high tendency for MK particles to agglomerate, resulting in the non-uniform properties of concrete when MK was introduced as SCMs. The low stacking density of MK, which is ~1,500 kg/m3, reduced the capacity and efficiency of transportation. Approximately over 40% of MK particles is under the size of 2.5 μm, which could pollute the environment and be harmful to the respiratory system of human. The authors' preliminary study suggested non-uniform hydration products, mechanical properties, and durability of concrete specimens with MK addition, resulted from the uneven distribution of MK particles after introducing into concrete due to the agglomeration of MK particles. Some previous research also reported that the agglomeration of MK reduced the pozzolanic activity of MK, together with a lower compressive strength, different microstructure and macrostructure of paste, and geopolymer (Medri et al., 2010; Ilic et al., 2018).
In this study, aiming to improve the capacity and efficiency of transportation, prevent the air pollution caused by MK powder, reduce the agglomeration and improve the uniform distribution of MK particles in mortar matrix and the properties of mortar, MK was pre-dispersed in water as slurry before being added in mortar to increase the density and homogeneity. A range of analytical techniques was employed to characterize the effect of pH of solution and water/MK ratio on the physical properties and stability of dispersion of MK-water slurry, and the effect of pre-dispersed MK slurry on the properties and hydration of cement mortar was evaluated, together with the improvement of distribution of MK particles in mortar after pre-dispersing.
Materials and Experimental
Materials
In this study, ordinary Portland cement (OPC) (Huaxin Cement Co. Ltd., China) was used MK was provided by Maoming Kaolin Science and Technology Co. Ltd., China, with a specific surface area of 2,800 m2/kg. Table 1 shows the chemical composition and properties of OPC and MK. The particle size distribution of MK is shown in Figure 1, which was analyzed with Malvern Mastersizer 2000 particle size analyser (Malvern, UK) by dispersing in sodium hexametaphosphate solution. According to X-ray diffraction (XRD) pattern in Figure 2, MK is mainly amorphous. Fine aggregate is natural sand with an apparent density of 2,640 kg/m3, stacking density of 1,458 kg/m3 and fineness modulus of 2.91. The grading of fine aggregate is shown in Table 2.
Experimental Details
Zeta Potential Test
MK-water colloidal dispersion was prepared with water/MK ratio of 1,500 for zeta potential test under various pH value of solution. The pH value of the MK-water dispersion was varied by addition of HNO3 and NaOH. The pH value of MK-water dispersion was measured by Inesa PHSJ-3F pH Meter (China). Zeta potentials of MK particles in solution with various pH value were conducted by Zeta-Meter System 3.0+ (USA). All measurement was conducted under room temperature.
Bulk Density and Viscosity of MK-Water Slurry Test
The bulk density of MK-water slurry was measured by adding water into MK powder with various water/MK ratio, mechanically mixing the slurry with a ball miller for 30 min, then measuring the weight, and volume of slurry. The viscosity of MK-water slurry with various water/MK ratio was evaluated by Brookfield R/S-SST (USA) with shear rate of 60 r/min. The VANE rotor for the test was V40-20, the container used was Griffin beaker of 600 ml and the temperature was constant at room temperature of 25 ± 5°C.
Stability of MK-Water Slurry With Time
The stability of MK-water slurry with water/MK ratio of 1.86 was evaluated by the differences of viscosity at 0 h and 24 h after mixing and the segregation of water from the slurry at 24 and 48 h after mixing. The segregation of water was measured as follows.
One hundred milliliter of slurry was put in the measuring cylinder after mixing. The volume of water segregated from slurry was recorded from the top of slurry after 24 and 48 h. The measurement was performed under room temperature and no vibration was applied.
Mix Design and Curing Conditions
The pre-dispersed MK slurry used in this study was with water/MK ratio of 1.86. The mix design of mortar and paste is shown in Table 3. OPC was substituted by 5 or 10 wt% powder MK or pre-dispersed MK slurry in mortar and paste. The water/binder ratio was 0.5 for all mortar and paste mixes. Specimens were demoulded at 1 day and cured in a fog room under standard moist curing condition with temperature of 20°C and relative humidity above 90%.
Compressive Strength and Porosity Test
For compressive strength test, the mortar and paste specimens were cast into the size of 40 × 40 × 160 mm. Nine specimens from each mix were used for compressive strength test. The compressive strength test was performed at 3, 7, and 28 days for all mixes according to Chinese standard GB/T 50081-20021. The results from all specimens were included for the calculation of compressive strength and standard deviation. Porosity test was conducted on paste specimens according to ASTM C642-132.
Phase Assemblage
XRD analysis was conducted on the paste specimens at 3 and 28 days. Crystalline minerals in freshly ground paste specimens was characterized by Bruker D8 Advance with Cu Kα = 1.5406 Å, step size of 0.019°, measuring time of 141.804 s/step, start position 5° and end position 70°. The obtained XRD pattern was analyzed by PANalytical X'pert Highscore Plus software with PDF2004 database.
Shrinkage
The shrinkage of mortar specimens was evaluated according to Chinese standard JGJ/T70-20093. Mortar specimens were cast into the size of 40 × 40 × 160 mm and cured under standard moist conditions for 7 days before demoulding, where cement mortar without MK addition, cement mortar with 10 wt% MK addition as dry powder and cement mortar with 10 wt% MK addition as dispersed slurry were named as M0, MMK10, and MDMK10, respectively. Then the initial length of specimens were recorded and the specimens were cured under temperature of 20 ± 2°C and relative humidity of 60 ± 5%. The lengths of specimens were measured at 7, 14, 21, 28, 35, and 42 days after demoulding. Three measurement were performed on each age. The shrinkage was calculated by the following equation.
Where εt is the shrinkage of mortar at t days, L0 is the length of specimen at demoulding (mm), L is the standard length of 160 mm, Ld is the length of test head in the mortar (mm), and Lt is the length of specimen at t days (mm).
Coefficient of Variation of Compressive Strength
The coefficient of variation (Cv) is a standardized measure of dispersion of a probability distribution. It is defined as the ratio of the standard deviation (SD) to the mean (μ), as follows.
In this study, the coefficient of variation was used to express the distribution of compressive strength test results of mortar specimens of M0, MMK10, and MDMK10 at 28 days. Eighteen specimens were tested for each mix. The mean value, standard deviation and coefficient of variation were calculated to assess the distribution of MK particles in mortar matrix. The results from all specimens were included for the calculation of mean value, standard deviation, and coefficient of variation, to evaluate the homogeneity.
Results and Discussion
Stability of MK-Water Dispersion Under Various pH
Zeta potential is a key indicator of the stability of colloidal dispersion. The magnitude of zeta potential indicates the electrostatic repulsion between adjacent, similarly charged particles in the dispersion, with a higher zeta potential indicating better stability, and less aggregation. According to the relationship between zeta potential and pH value of MK-water dispersion with water/MK ratio of 1,500 observed in this study (Figure 3 and Table 4), zeta potential of MK-water dispersion significantly decreased with the increase of pH of solution, from 16.4 to −48.2 mV when pH increased from 1.5 to 10. The concentration of OH− increases with pH value, providing more OH− available to attach to the surface of metakaolin particles, resulting in the continuous decrease of zeta potential to ~-40 mV at pH of 8, indicating that the MK-water dispersion was stably dispersed. In solution of pH over 10, pozzolanic reaction of MK will take place, which is not beneficial for the purpose of storage and dispersion of metakaolin for construction. Severe aggregation was observed when pH was more than 10 in this study, indicating the activation of MK due to the pozzolanic reaction (He et al., 1995). Considering the stability of dispersion of MK slurry, dispersing MK with water, which has a pH value of 7, should result in a stable dispersion without pozzolanic reaction. In this study, de-ionized water was used for dispersing at pH of 7.
Bulk Density and Viscosity Under Various Water/MK Ratio
To improve the bulk density of MK slurry and distribution of MK in mortar, MK-water slurry with water/MK ratio of 0–2.5 were prepared and the bulk density and viscosity were evaluated. According to the results shown in Figure 4, the bulk density of MK slurry rapidly increased with the addition of water due to the decrease of distance between particles by surface tension force of water and filling of water between particles, reaching the maximum of 665.2 kg/m3 at water/MK weight ratio of 1.0, where the packing of MK particles reached the closest packing. Then the bulk density of MK slurry gradually decreased with the increase of water/MK ratio, due to the increase of distance between MK particles by continuous addition of water.
The viscosity was measured at water/MK ratio over 1.3, where the bulk density of MK slurry started to decrease (Figure 4 and Table 5). The viscosity decreased rapidly with the increase of water/MK ratio, from 693.5 mPa·s at water/MK ratio of 1.25 to 30.0 mPa·s at water/MK ratio of 1.85. To obtain a low viscosity and relative high MK content, water/MK ratio of 1.86 was chosen to evaluate the effect of pre-dispersed MK slurry on the properties and hydration of cement mortar in this study.
The stability of MK-water slurry with water/MK ratio of 1.86 was evaluated. The viscosity of MK slurry increased from 28.6 mPa·s at 0 h after mixing to 49.3 mPa·s at 24 h after mixing. The water segregation of MK slurry was 4.7 ml water per 100 ml slurry at 24 h after mixing and 8.2 ml water per 100 ml slurry at 48 h after mixing.
Compressive Strength
The compressive strength of specimen M0, MMK10, MDMK10 at 3, 7 and 28 days were shown in Figure 5 and Table 6. For MDMK10 specimens, the pre-dispersed MK slurry was added in mortar after preparing or settling for 1, 2, and 4 days, respectively. Comparing to the compressive strength of M0 specimen, by addition of 10 wt% powder MK, the compressive strength increased by 29.4, 51.6, and 24.7% at 3, 7, and 28 days, respectively. Comparing the compressive strength of mortar with pre-dispersed MK with those with powder MK, pre-dispersing of MK did not hinder the effect of MK on the compressive strength of mortar. At 28 days, the compressive strength of mortar with pre-dispersed MK was slightly higher than that with powder MK. With a pH value of 7, water could not activate MK, which was activated later by calcium hydroxide formed during the hydration of cement in mortar. The improvement of compressive strength of mortar by MK was due to the accelerated hydration of cement, filler effect, and pore structure refinement by MK, as reported in previous studies (Li et al., 2015).
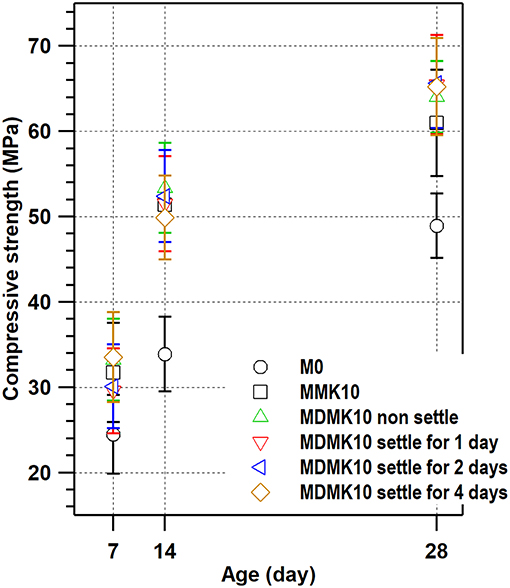
Figure 5. Compressive strength of mortars with powder MK, pre-dispersed MK, and per-dispersed MK settled for 1, 2, and 4 days before addition.
Comparing with the compressive strength of mortar with non-settled pre-dispersed MK specimen, the settlement of pre-dispersed MK up to 4 days did not alter the effect of MK on the compressive strength of mortar with pre-dispersed MK, indicating that there was no reaction between water and MK during settlement up to 4 days and MK particles were stably dispersed in water as being suggested by results from zeta-potential test under various pH values.
Porosity
The porosity of paste specimens is shown in Figure 6 and Table 7, together with the relationship between porosity and compressive strength. For the pastes with powder or pre-dispersed MK addition, the compressive strength and porosity did not alter much at 3 days, comparing to that of the control specimen P0. However, at 7 and 28 days, while the porosity was slightly lower than that of the control specimen at the same age, the compressive strength greatly increased with ages, comparing to those of the control specimen P0. There is a linear relationship between the compressive strength and porosity of mortar for each group, where the compressive strength increased with the decrease of porosity, which is similar to previous studies (Frias and Cabrera, 2000). Although the relationship between porosity and compressive strength kept linear for the control, powder MK and pre-dispersed MK specimens, these results indicate that the pore structure was refined through addition of powder or pre-dispersed MK while the porosity did not change much. The relationships between porosity and compressive strength of powder and pre-dispersed MK specimens were similar, indicating that the pore structure refinement effect of MK was not affected by pre-dispersing MK in water. It is notable that the relationship is valid in the porosity range of 28–46% in this study. When the porosity is close to 0, the relationship could be invalid.
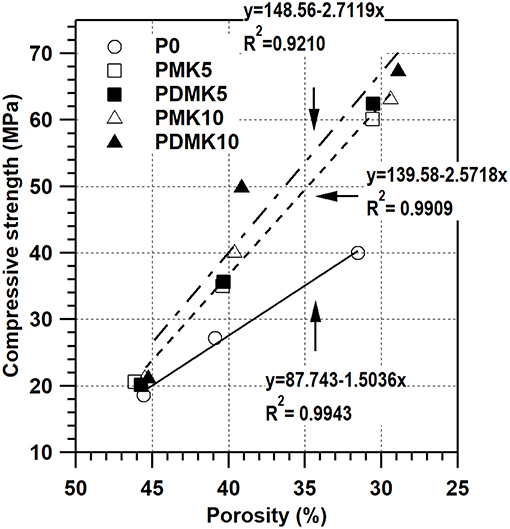
Figure 6. Relationship between the compressive strength and porosity of cement paste, pastes with powder MK, and pre-dispersed MK. Specimens with a porosity of ~45% were cured for 3 days, those with a porosity of 35–42% were cured for 7 days and those with a porosity of 25–35% were cured for 28 days.
Hydration Products
The crystalline phases of paste specimens were characterized by XRD (Figure 7). According to these results, the hydration products of ettringite, Portlandite, calcite, hemicarboaluminate (Hc), and monocarboaluminate (Mc) were identified for P0, PMK10, and PDMK10 specimens at 3 and 28 days, except for P0 at 3 days, where monocarboaluminate was not identified. The hydration products identified were similar to those from previous studies (Frias et al., 2012; Gameiro et al., 2012; Tironi et al., 2013). The intensity of peaks attributed to monocarboaluminate increased with age for P0, PMK10, and PDMK10 specimens, indicating the increase of content of monocarboaluminate with age. The intensity of peaks of these hydration products was similar in PMK10 and PDMK10 specimens at the same age, indicating that the effects of powder MK and pre-dispersed MK on the hydration of cement were similar and the effects of MK on cement hydration were not hindered by dispersing in water, as being indicated by the compressive strength and porosity tests. The reason is that MK was not activated by water, with a pH value of 7. There was no reaction between water and MK observed.
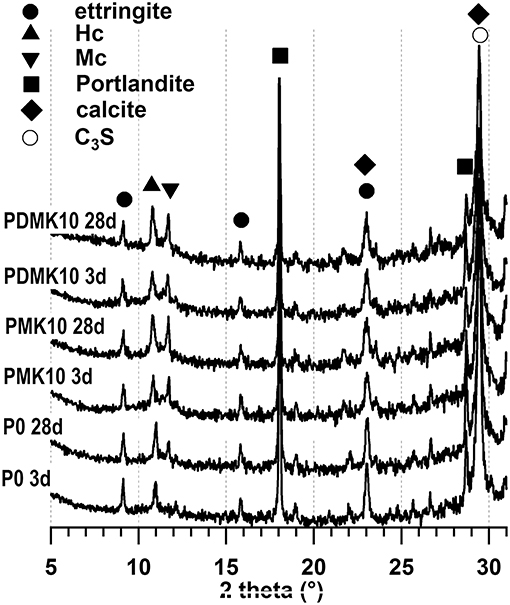
Figure 7. XRD patterns of cement paste, pastes with powder or pre-dispersed MK at 3 and 28 days. Tricalcium silicate, calcite, Portlandite, monocarboaluminate (Mc), hemicarboaluminate (Hc), and ettringite were identified from these specimens.
Shrinkage
The shrinkage of mortar was evaluated and the results are shown in Figure 8 and Table 8. The shrinkage of mortar was reduced at all ages through addition of powder MK, due to the refined pore structure of mortar by addition of MK, as indicated by previous studies (Li and Yao, 2001), which suggested that the reduced shrinkage by MK addition can be attributed to the lower amount of evaporable water available due to the hydration and pozzolanic reaction of cement and MK. At 28 days, the shrinkage was reduced by 21%, which was similar to previous studies (Brooks and Johari, 2001; Khatib, 2008; Guneyisi et al., 2010, 2012; Cheng et al., 2016). Pre-dispersing of MK reduced the shrinkage of mortar by 41% at 28 days, due to the internal curing effect by water stored in the interlayer of MK during the pre-dispersing process.
Distribution of MK in Mortar Matrix
Preliminary study showed that the agglomeration of MK in mortar or concrete matrix resulted in the non-uniform properties or hydration degree of mortar or concrete. In this study, the distribution of MK particles of powder or pre-dispersed MK were evaluated by coefficient of variation of compressive strength results of 18 specimens from each mortar mix at 28 days. The variation of coefficient is unit-less and represents the distribution of results. The variation of coefficient of results with different mean value can be compared, unlike the standard deviation. The compressive strengths with the range of results, standard deviation, and coefficient of variation were shown in Figure 9 and Table 9 for M0, MMK10, and MDMK10 at 28 days. According to these results, the compressive strength of mortar improved by MK addition, and pre-dispersing of MK further improved the compressive strength, as discussed above. Comparing to that of the control specimen, the range of compressive strength of specimens from the same mix significantly increased by addition of powder MK and slightly increased by addition of pre-dispersed MK. Similar to the range of compressive strength, standard deviation (SD) of compressive strength was greatly increased by powder MK and slightly increased by pre-dispersed MK, comparing to that of control specimen. The coefficient of variation (Cv), which indicates the evenness of distribution of MK particles, shown as the size of circle in Figure 9, significantly increased by powder MK addition and approximately doubled by pre-dispersing MK addition, comparing to that of M0 specimens. These results suggest that the particle of powder MK distributed unevenly in the mortar and pre-dispersing of MK by water improved the uniformness of distribution of MK particles in mortar. As indicated by the zeta-potential of dispersed MK slurry, pre-dispersing improved the distribution of MK particles in slurry, and formed a stable dispersing system. Viscosity was also significantly improved through dispersing in water, so as to improve the uniformness of distribution of MK particles in mortar during mixing, although the hydration of cement and MK was not affected by pre-dispersing, as indicated by XRD results.
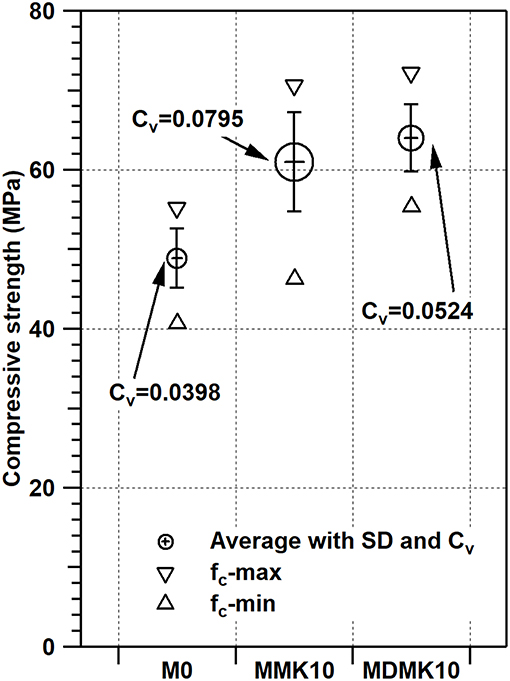
Figure 9. Compressive strength of cement mortar, and mortar with powder or pre-dispersed MK. The results are shown as mean value of 18 specimens of each mix, range of results (fc-max and fc-min), standard deviation and coefficient of variation (size of circle).

Table 9. Average value, standard deviation, range, and coefficient of deviation of compressive strength at 28 days by calculating 18 specimens.
Conclusions
The effects of dispersing MK in water on the properties of MK, the properties and hydration of mortar and the distribution of MK particles in mortar were characterized by a range of analytical techniques. According the results, the following conclusions can be drawn.
Zeta-potential of MK-water dispersion significantly decreased with the increase of pH of solution, with zeta-potential of ~-40 mV at pH of 8, indicating a stable dispersion, due to more OH− attachment on the surface of MK particles without activation of MK.
During the addition of water, the bulk density of MK-water slurry firstly rapidly increased with water/MK ratio, due to the decrease of distance between MK particles by surface tension force of water and filling of spaces between particles by water. The maximum bulk density was 665.2 kg/m3 at water/MK ratio of 1.0, indicating the closest packing of MK particles. Then the bulk density gradually decreased with the increase of water/MK ratio, due to the increase of distance between MK particles by continuous addition of water. Viscosity of MK-water slurry decreased rapidly with the increase of water/MK ratio.
Both powder MK and pre-dispersed MK increased the compressive strength of mortar. There was linear relationship between the compressive strength and porosity of mortar. Neither pre-dispersing MK in water nor settlement of pre-dispersed MK slurry hindered the effect of MK on the compressive strength. Pre-dispersing MK in water slightly decreased the porosity of mortar, comparing to that with powder MK. The hydration products were not affected by pre-dispersing MK in water. Addition of powder MK reduced the shrinkage of mortar, which was reduced further by pre-dispersing MK in water.
Comparing to powder MK, pre-dispersed MK improved the uniformed distribution of MK particles in mortar according to the range, standard deviation, and coefficient of variation of compressive strength results, due to the stable dispersing of MK particle in pre-dispersed MK slurry.
Author Contributions
HG, WC, QL, and ZS contributed conception and design of the study. BY performed the properties tests. HG, WC, and QL performed the microstructure and statistical analysis. HG wrote the first draft of the manuscript. WC, QL, ZS, and BY wrote sections of the manuscript. All authors contributed to manuscript revision, read, and approved the submitted version.
Conflict of Interest Statement
The authors declare that the research was conducted in the absence of any commercial or financial relationships that could be construed as a potential conflict of interest.
Acknowledgments
Thanks to Dr. Jian Huang (Wuhan University of Technology) for beneficial discussion on the viscosity test. This research was financially supported by the Natural Science Foundation of China (project 51611530545, 51672199), the YangFan Innovative and Entrepreneurial Research Team Project (No. 201312C12) and the Research Fund of State Key Laboratory of Silicate Materials for Architectures (Wuhan University of Technology).
Footnotes
1. ^Standard for Test Method of Mechanical Properties on Ordinary Concrete. Ministry of Construction of the People's Republic of China (2002).
2. ^ASTM C642-13: Standard Test Method for Density, Absorption, and Voids in Hardened Concrete. West Conshohocken, PA: ASTM International (2013).
3. ^JGJ/T70-2009: Standard for Test Method of Performance on Building Mortar. Beijing: Ministry of Housing and Urban-Rural Development of People's Republic of China (2009).
References
Antoni, M., Rossen, J., Martirena, F., and Scrivener, K. (2012). Cement substitution by a combination of metakaolin and limestone. Cement Concrete Res. 42, 1579–1589. doi: 10.1016/j.cemconres.2012.09.006
Aquino, W., Lange, D. A., and Olek, J. (2001). The influence of metakaolin and silica fume on the chemistry of alkali-silica reaction products. Cement Concrete Compos. 23, 485–493. doi: 10.1016/S0958-9465(00)00096-2
Arikan, M., Sobolev, K., Ertuen, T., Yeginobali, A., and Turker, P. (2009). Properties of blended cements with thermally activated kaolin. Constr. Build. Mater. 23, 62–70. doi: 10.1016/j.conbuildmat.2008.02.008
Badogiannis, E., Kakali, G., and Tsivilis, S. (2005). Metakaolin as supplementary cementitious material - Optimization of kaolin to metakaolin conversion. J. Thermal Anal. Calorimetry. 81, 457–462. doi: 10.1007/s10973-005-0806-3
Bich, C., Ambroise, J., and Pera, J. (2009). Influence of degree of dehydroxylation on the pozzolanic activity of metakaolin. Appl. Clay Sci. 44, 194–200. doi: 10.1016/j.clay.2009.01.014
Brooks, J. J., and Johari, M. A. M. (2001). Effect of metakaolin on creep and shrinkage of concrete. Cement Concrete Compos. 23, 495–502. doi: 10.1016/S0958-9465(00)00095-0
Buchwald, A., Hilbig, H., and Kaps, C. (2007). Alkali-activated metakaolin-slag blends - performance and structure in dependence of their composition. J. Mater. Sci. 42, 3024–3032. doi: 10.1007/s10853-006-0525-6
Cassagnabere, F., Mouret, M., Escadeillas, G., Broilliard, P., and Bertrand, A. (2010). Metakaolin, a solution for the precast industry to limit the clinker content in concrete: mechanical aspects. Constr. Build. Mater. 24, 1109–1118. doi: 10.1016/j.conbuildmat.2009.12.032
Cheng, S. K., Shui, Z. H., Li, Q., Sun, T., and Yang, R. H. (2016). Properties, microstructure and hydration products of lightweight aggregate concrete with metakaolin and slag addition. Constr. Build. Mater. 127, 59–67. doi: 10.1016/j.conbuildmat.2016.09.135
Coleman, N. J., and McWhinnie, W. R. (2000). The solid state chemistry of metakaolin-blended ordinary Portland cement. J. Mater. Sci. 35, 2701–2710. doi: 10.1023/A:1004753926277
Fernandez, R., Martirena, F., and Scrivener, K. L. (2011). The origin of the pozzolanic activity of calcined clay minerals: a comparison between kaolinite, illite and montmorillonite. Cement Concrete Res. 41, 113–122. doi: 10.1016/j.cemconres.2010.09.013
Frias, M., and Cabrera, J. (2000). Pore size distribution and degree of hydration of metakaolin-cement pastes. Cement Concrete Res. 30, 561–569. doi: 10.1016/S0008-8846(00)00203-9
Frias, M. R., Vigil de la Villa, M. I., Sanchez de Rojas Medina, C., and Juan Valdes, A. (2012). Scientific aspects of kaolinite based coal mining wastes in pozzolan/Ca(OH)2 system. J. Am. Ceram. Soc. 95, 386–391. doi: 10.1111/j.1551-2916.2011.04985.x
Gameiro, A., Santos Silva, A., Veiga, R., and Velosa, A. (2012). Hydration products of lime-metakaolin pastes at ambient temperature with ageing. Thermochim. Acta. 535, 36–41. doi: 10.1016/j.tca.2012.02.013
Goncalves, J. P., Tavares, L. M., Toledo Filho, R. D., and Fairbairn, E. M. R. (2009). Performance evaluation of cement mortars modified with metakaolin or ground brick. Constr. Build. Mater. 23, 1971–1979. doi: 10.1016/j.conbuildmat.2008.08.027
Gueneyisi, E., Gesoglu, M., and Mermerdas, K. (2008). Improving strength, drying shrinkage, and pore structure of concrete using metakaolin. Mater. Struct. 41, 937–949. doi: 10.1617/s11527-007-9296-z
Guneyisi, E., Gesoglu, M., Karaoglu, S., and Mermerdas, K. (2012). Strength, permeability and shrinkage cracking of silica fume and metakaolin concretes. Constr. Build. Mater. 34, 120–130. doi: 10.1016/j.conbuildmat.2012.02.017
Guneyisi, E., Gesoglu, M., and Ozbay, E. (2010). Strength and drying shrinkage properties of self-compacting concretes incorporating multi-system blended mineral admixtures. Constr. Build. Mater. 24, 1878–1887. doi: 10.1016/j.conbuildmat.2010.04.015
He, C., Osbaeck, B., and Makovicky, E. (1995). Pozzolanic reactions of six principal clay minerals: activation, reactivity assessments and technological effects. Cement Concrete Res. 25, 1691–1702. doi: 10.1016/0008-8846(95)00165-4
Ilic, B., Mitrovic, A., Radonjanin, V., Malesev, M., and Zdujic, M. (2018). “Compressive strength improvements of cement-based composites achieved with additional milling of metakaolin,” in Calcined Clays for Sustainable Concrete, eds F. Martirena, A. Favier, and K. Scrivener (Dordrecht: Springer), 212–218. doi: 10.1007/978-94-024-1207-9_;34
Johari, A. M., Brooks, J. J., Kabir, S., and Rivard, P. (2011). Influence of supplementary cementitious materials on engineering properties of high strength concrete. Constr. Build. Mater. 25, 2639–2648. doi: 10.1016/j.conbuildmat.2010.12.013
Justice, J. M., and Kurtis, K. E. (2007). Influence of metakaolin surface area on properties of cement-based materials. J. Mater. Civil Eng. 19, 762–771. doi: 10.1061/(ASCE)0899-1561(2007)19:9(762)
Kadri, E.-H., Kenai, S., Ezziane, K., Siddique, R., and De Schutter, G. (2011). Influence of metakaolin and silica fume on the heat of hydration and compressive strength development of mortar. Appli. Clay Sci. 53, 704–708. doi: 10.1016/j.clay.2011.06.008
Khatib, J. M. (2008). Metakaolin concrete at a low water to binder ratio. Constr. Build. Mater. 22, 1691–1700. doi: 10.1016/j.conbuildmat.2007.06.003
Khatib, J. M. (2009). Low temperature curing of metakaolin concrete. J. Mater. Civil Eng. 21, 362–367. doi: 10.1061/(ASCE)0899-1561(2009)21:8(362)
Kinuthia, J. M., Wild, S., Sabir, B. B., and Bai, J. (2000). Self-compensating autogenous shrinkage in Portland cement-metakaolin-fly ash pastes. Adv. Cement Res. 12, 35–43. doi: 10.1680/adcr.2000.12.1.35
Lagier, F., and Kurtis, K. E. (2007). Influence of Portland cement composition on early age reactions with metakaolin. Cement Concrete Res. 37, 1411–1417. doi: 10.1016/j.cemconres.2007.07.002
Li, C., Sun, H., and Li, L. (2010). A review: the comparison between alkali-activated slag (Si plus Ca) and metakaolin (Si plus Al) cements. Cement Concrete Res. 40, 1341–1349. doi: 10.1016/j.cemconres.2010.03.020
Li, J. Y., and Yao, Y. (2001). A study on creep and drying shrinkage of high performance concrete. Cement Concrete Res. 31, 1203–1206. doi: 10.1016/S0008-8846(01)00539-7
Li, Q., Geng, H., Shui, Z., and Huang, Y. (2015). Effect of metakaolin addition and seawater mixing on the properties and hydration of concrete. Appl. Clay Sci. 115, 51–60. doi: 10.1016/j.clay.2015.06.043
Love, C. A., Richardson, I. G., and Brough, A. R. (2007). Composition and structure of C-S-H in white Portland cement-20% metakaolin pastes hydrated at 25 degrees C. Cement Concrete Res. 37, 109–117. doi: 10.1016/j.cemconres.2006.11.012
Medri, V., Fabbri, S., Dedecek, J., Sobalik, Z., Tvaruzkova, Z., and Vaccari, A. (2010). Role of the morphology and the dehydroxylation of metakaolins on geopolymerization. Appli. Clay Sci. 50, 538–545. doi: 10.1016/j.clay.2010.10.010
Murat, M., and Comel, C. (1983). Hydration reaction and hardening of calcined clays and related minerals III. Influence of calcination process of kaolinite on mechanical strengths of hardened metakaolinite. Cement Concrete Res. 13, 631–637. doi: 10.1016/0008-8846(83)90052-2
Rashad, A. M. (2013). Metakaolin as cementitious material: history, scours, production and composition - a comprehensive overview. Constr. Build. Mater. 41, 303–318. doi: 10.1016/j.conbuildmat.2012.12.001
Sabir, B. B., Wild, S., and Bai, J. (2001). Metakaolin and calcined clays as pozzolans for concrete: a review. Cement Concrete Compos. 23, 441–454. doi: 10.1016/S0958-9465(00)00092-5
Scrivener, K. L., and Kirkpatrick, R. J. (2008). Innovation in use and research on cementitious material. Cement Concrete Res. 38, 128–136. doi: 10.1016/j.cemconres.2007.09.025
Shui, Z., Sun, T., Fu, Z., and Wang, G. (2010). Dominant factors on the early hydration of metakaolin-cement paste. J. Wuhan Univ. Technol. Mater. Sci. Edn. 25, 849–852. doi: 10.1007/s11595-010-0106-z
Taylor, H. F. W. (1997). Cement Chemistry, 2 Edn. London: Thomas Telford Services Ltd. doi: 10.1680/cc.25929
Tironi, A., Trezza, M. A., Scian, A. N., and Irassar, E. F. (2013). Assessment of pozzolanic activity of different calcined clays. Cement Concrete Compos. 37, 319–327. doi: 10.1016/j.cemconcomp.2013.01.002
Keywords: zeta-potential, viscosity, hydration products, compressive strength, shrinkage, coefficient of variation
Citation: Geng H, Chen W, Li Q, Shui Z and Yuan B (2019) Effect of Pre-dispersing Metakaolin in Water on the Properties, Hydration, and Metakaolin Distribution in Mortar. Front. Mater. 6:99. doi: 10.3389/fmats.2019.00099
Received: 09 February 2019; Accepted: 17 April 2019;
Published: 03 May 2019.
Edited by:
Maria Juenger, University of Texas at Austin, United StatesReviewed by:
Maria Stefanidou, Aristotle University of Thessaloniki, GreeceZehra Canan Girgin, Yildiz Technical University, Turkey
Copyright © 2019 Geng, Chen, Li, Shui and Yuan. This is an open-access article distributed under the terms of the Creative Commons Attribution License (CC BY). The use, distribution or reproduction in other forums is permitted, provided the original author(s) and the copyright owner(s) are credited and that the original publication in this journal is cited, in accordance with accepted academic practice. No use, distribution or reproduction is permitted which does not comply with these terms.
*Correspondence: Qiu Li, cWl1LWxpQHdodXQuZWR1LmNu