- 1State Key Laboratory of Special Surface Protection Materials and Application Technology, Wuhan Research Institute of Materials Protection, Wuhan, China
- 2National United Engineering Laboratory for Advanced Bearing Tribology, Henan University of Science and Technology, Luoyang, China
- 3Luoyang Bearing Science and Technology Co., Ltd, Luoyang, China
G95Cr18 stainless bearing steel is used to manufacture rolling bearings widely used in aviation and navigation fields. Twin carbide structure often appears in G95Cr18 stainless bearing steel structure and affects its material properties. This study adopts ball-block friction pairs to qualitatively discuss the influence of twin carbide structure of different degrees on the friction and wear performance of G95Cr18 stainless bearing steel under dry sliding conditions at room temperature and atmospheric environment. The results show that a slight twin carbide structure has only a little influence on the friction coefficient but can reduce the wear rate slightly, while a severe twin carbide structure can significantly increase the friction coefficient and wear rate. Thus, the existence of an optimal value for twin carbide structure was confirmed. The wear mechanism is mainly oxidation wear and abrasive wear, and the oxide produced by oxidation reaction during friction consists mainly of Fe2O3.
Introduction
G95Cr18 stainless bearing steel has high hardness, high wear resistance, and corrosion resistance, and tempering stability (Kun and Dong, 2012; Zhao et al., 2012). Thus, it is often used to manufacture high-end bearings for the military industry, aviation, aerospace and navigation. However, its disadvantages are poor thermal conductivity, narrow forging temperature, and it easily develops a thick forging structure with twin structure because the forging temperature is too high and the heat preservation time is too long. Furthermore, the twin carbide structure seriously affects the impact toughness. And is strictly controlled by both the materials standards GB/T3086-20081 and the heat treatment standard JB/T1460-20112 (Initial forging temperature 1120–1150°C, final forging temperature850-900°C,quenching temperature:1000–1050°C, Tempering temperature 200–300°C).Hence, it is necessary to thoroughly understand the formation mechanism of twin structure and its effect on material properties.
Twin structure has two crystals (or two parts of a crystal) along a common crystal surface forming a mirror symmetry of the directional relationship. These two crystals are called twin structure and the common crystal surface is called the twin plane. The formation of twins is closely related to the stacking fault of atoms inside the metal, which can be divided into deformation twins, growth twins and annealing twins based on the different causes of formation of twins. Because twins are closely related to fault formation, crystals with high fault energy generally do not easily produce twins. However, stainless steel such as G95Cr18 martensitic stainless steel have crystals with low dislocation energy and consequently a twin boundary is easily formed. Once the twin boundary is formed, due to its low energy, carbide easily precipitates into a point chain at the twin boundary during the annealing process. This is twin carbide. On the formation of twins, in the literature (Wang, 2011) it is believed that the twin substructure formed during martensite phase transition is that of phase transition twins. Wang et al. (2006) believe that twins are divided into linear twins and chain twins, while linear twins are formed by grain boundary migration, chain twins are essentially reticular carbides. Influence of twin structure on material properties has been studied in the literature. Xu et al. (2012) studied the influence of wafer thickness on the fatigue performance of nano-twin Cu. They concluded that both the fatigue life and fatigue endurance limit of samples increased with a decrease in the twin layer thickness under stress fatigue. Li et al. (2000) studied the influence of twin size in twin copper on fatigue dislocation configuration. They found that the fatigue dislocation configuration in twin structure is related to the width of the twins. There are studies in the literature (Guo et al., 2005; Luan and Lei, 2009) on the influence of surface nitriding on surface properties and tribological behaviors. There are also research literatures (Xu et al., 2006; Ying et al., 2007; Fan et al., 2010; Liu et al., 2013) on surface friction and wear performance using coating technology and ion implantation. However, the influence of twin carbide structure (linear twins)of different degrees on friction and wear properties of G95Cr18 stainless steel is still unknown. Meanwhile, wear is one of the important failure modes of rolling bearing made of 9Cr18 Material. As mentioned earlier, twin microstructure is strictly controlled by current standards. And research results (Xu et al., 2017a,b) show that the size and distribution of carbides affect the friction and wear properties of materials. The author draws a conclusion that VC(carbide) with high hardness was mainly attributed to excellent wear, which can resist micro-cutting of abrasive particles (Xu et al., 2017a). Hence, it is necessary to explore the influence of twin carbide structure on friction and the wear properties of G95Cr18 stainless steel.
In this study, friction couple, including G95Cr18 stainless steel block and GCr15 steel ball, are adopted under dry sliding conditions at room temperature (RT) and atmospheric environment. The G95Cr18 stainless steel was successively obtained as twin free carbide structure, slight twin carbide structure, and severe twin carbide structure through different heat treatment processes. The influences of twin carbide structure on friction and the wear properties of G95Cr18 stainless steel were analyzed qualitatively.
Experimental Procedures
Sample Preparation
The same batch(ϕ30 mm) of stainless bearing steel is selected. The chemical composition is presented in Table 1. Twin carbide structures of different degrees were obtained and grouped according to different heat treatment processes, as shown in Table 2. Linear twin carbide microstructure was observed using metallographic microscopy. Group 1# had twin free carbide microstructure, group 2# had slight twin carbide microstructure, and group 3# had severe twin carbide microstructure. As shown in Figure 1, the structure of G95Cr18 stainless bearing steel includes tempered martensite, fine dispersed carbide and a small amount of residual austenite. And the alloy carbide particles in the three groups are similar in size and uniformly distributed. Although the size of carbide particles is similar between them. The microstructure of Figures 1B,C are not up to standard requirements. There are many slight linear twins with length of 2–5 um in Figure 1B and severe linear twins with a larger length of 6–10 um appear in Figure 1C. In order to clearly observe the twins carbide structure, field emission electron microscope was used, shown in Figure 2. It can be seen that carbides are straight lines and the length is about 10 um(red arrows). In the process of grain growth, stacking happened accidentally during grain boundary migration and the linear twins was formed. In the subsequent annealing process, the carbide precipitates along the austenitic twin boundary. Hence, Linear twin microstructure is essentially twin carbide (Wang et al., 2006). The EDS results that the main elements of twin carbides includes Fe, Cr and C. The surface hardness of the samples was measured using a 200HRS-150 Rockwell hardness tester. The results are presented in Table 3. Table 3 shows that the surface hardness of the three sample groups are similar. Therefore, the effect of hardness in the experiment can be ignored.
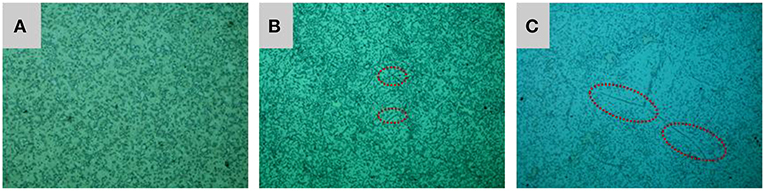
Figure 1. Linear Twin structure (red dashed line) of different degrees at optical microscopy (500×magnification): (A) twin free microstructure; (B) slight twin microstructure; (C) severe twin microstructure.
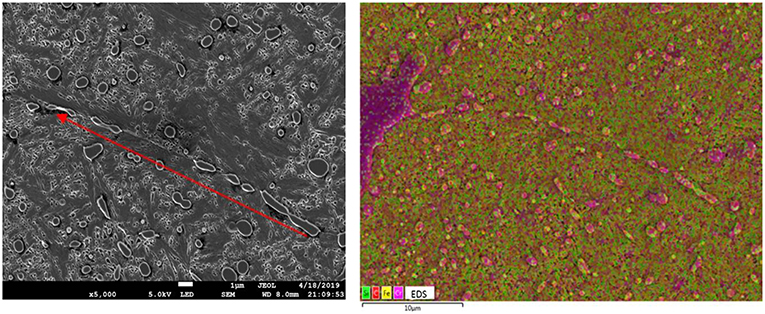
Figure 2. SEM of linear Twin carbide structure (The length of the linear twin is 10 um, marked in red) and the EDS result of element distribution.
Experimental Method
Friction and wear tests were carried out on a UMT-2 reciprocating wear tester with ball-block configuration under the condition of dry friction at room temperature. Before the experiment, each group sample was pre-ground for 3s under the conditions of load 5N and at speed 9 mm/s. All the friction and wear tests were run at an applied load of 25 N, sliding speed of 9 mm/s, reciprocating distance 5 mm, and duration of 20 min. Friction coefficient was automatically recorded by the computer of the friction and wear tester. Three dimensional surface profilers were used to measure the cross-sectional area of wear marks of the test block and to calculate the cross-sectional area of the wear marks. The cross-sectional area of the wear marks of the samples is the average value obtained after 4 successive measurements. The wear volume of the test block was obtained by multiplying the cross-sectional area of the wear mark by the sliding displacement (5 mm). The bulk wear rate of the test block was obtained by dividing the wear volume by the product of the sliding distance and loading. The friction coefficient and wear rate of each group of samples are the average values of the friction and wear test results repeated at least 2–3 times.
Scanning electron microscopy (SEM, JSM-6380lv) was used to analyze the wear morphology, profile morphology and chip morphology of the samples. While, energy-dispersive X-ray spectroscopy (EDS) was used to analyze the chemical composition of grinding chips. The wear profile was analyzed using Nanofocus AG three-dimensional surface profiler. Raman spectroscopy (LRS, Invia, Renishaw) was used to detect the phase composition of the worn surface and the laser wavelength was 532 nm.
Results and Discussion
Figure 3 shows a profile of the wear track of samples with severe twin carbide microstructure. Figure 4 shows a three-dimensional morphology of the wear surface of twin samples at different degrees. Figures 4A–C show the three-dimensional surface profile of twin free, slight twin, and severe twin samples, respectively. The maximum depth of worn tracks can be obtained with the embedded software. For each wear track, three locations were measured to determine the mean cross-sectional area, as shown in Table 4. From Figure 4, all the worn surfaces of the three sample groups had deep worn tracks. As can be seen from Table 4, the depth of the average worn tracks of the three groups was more than 4 μm. The depth of the worn tracks of the slight twin sample was slightly less than that of twin free sample, and that of the severe twin sample was the deepest.
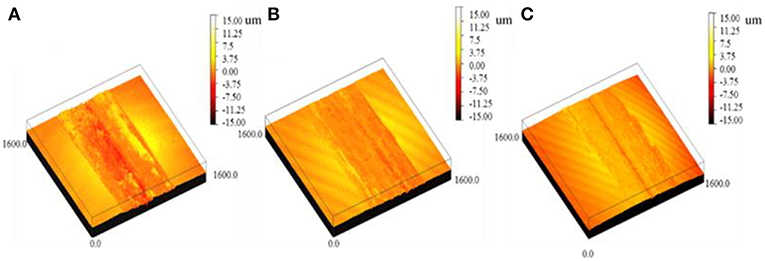
Figure 4. Three-dimensional morphology of the wear surface of twin samples: (A) twin free samples, (B) slight twin samples, (C) severe twin samples.
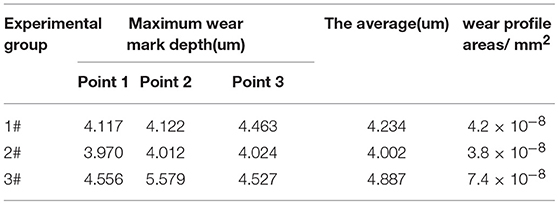
Table 4. Statistical of the depth of wear marks on the worn surface of twin specimens at different degrees.
Figure 5 shows the friction coefficient and wear rate of twin samples with different degrees. As can be seen from Figure 5A, the friction coefficients of three sample groups (with or without twin carbide structure) at the initial stage of the test are similar but fluctuate slightly, which may be because it is an initial test. After running the test for about 300 s, the friction coefficients of the three sample groups are relatively stable, but the friction coefficient of the severe twin sample (about 0.8) is significantly higher than the other two. The friction coefficient of twin free samples and slight twin samples is similar (between 0.65 and 0.7), but the friction coefficient of the slight twin samples decreases slightly. As can be seen from Figure 5B, the wear rate of the sample with slight twin carbide structure is slightly lower than that with twin free carbide structure at the same time (20 min), while that of the severe twin carbide structure is the highest. It can be seen that the slight twin carbide structure has only a little influence on the friction coefficient during the whole test process, but it can reduce the wear rate slightly. However, the severe twin carbide structure increases the friction coefficient and wear rate noticeably.
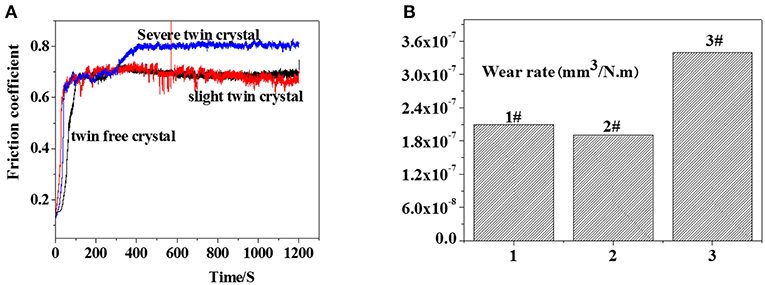
Figure 5. Friction coefficient and wear rate of twin carbide structures of different degrees: (A) friction coefficient, (B) wear rate.
Figure 6 shows the typical SEM morphology of the worn surfaces of twin samples with varying degrees. Among them, Figures 5A,B, and c present the morphology of twin free samples, slight twin samples, and severe twin samples, respectively. Under the same experimental conditions, there are many small pits in Figure 6.There are dark black irregular flaky substances locally. In Figure 6A, there are a few dark and irregular flake materials and these materials are not connected. The proportion of black materials is the highest and these materials are connected. It can be seen from the surface distribution of major elements that O elements are concentrated mainly in the area of wear marks, which indicates that oxidation took place during friction. Meanwhile, the Cr and Fe elements are evenly distributed in the matrix.
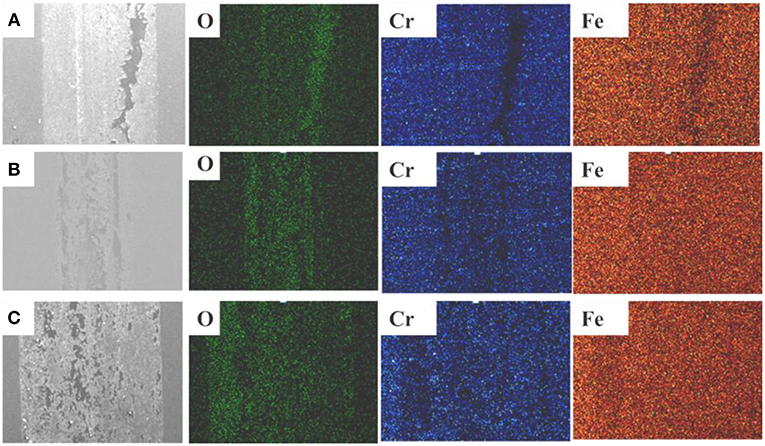
Figure 6. Typical SEM morphology of the worn surface of twin samples with varying degree and corresponding surface distribution of major elements: (A) twin free samples, (B) slight twin samples, (C) severe twin samples.
Figure 7 shows the SEM morphology of the wear debris. According to a research (Shogrin et al., 1996), there are four kinds of particles generated by wear: microspall (micropit) particles, layer/thin particles (laminar particles), chunky particles, and spherical particles. Three sample groups all produce granular wear debris, which accumulate loosely. To a certain extent, some of the samples have thin flakes of wear debris, the accumulation of thin chip wear debris can isolate the friction pair. As the friction goes on, the chip wear debris breaks up and produces new wear debris, and so on. Compared with the twin free samples, the slightly twin samples have more chip abrasions, which may be the reason why the friction coefficient is lower than that of the twin free samples. The grinding chips of the severe twin samples are mostly granular, with uneven size. The soft granular particles are compacted into flakes, while the hard-granular particles remain on the contact surface and play the role of fine plow, which aggravates the wear of the friction surface. Energy spectrum analysis was carried out on the grinding chips of three sample groups, and the results are presented in Figures 8–10. The main chemical components of the three sample groups were O, Fe, and Cr, indicating that the grinding debris generated by friction was oxidized. To further study the oxidation products of abrasive debris, the phase composition of the worn surfaces of three sample groups were analyzed.
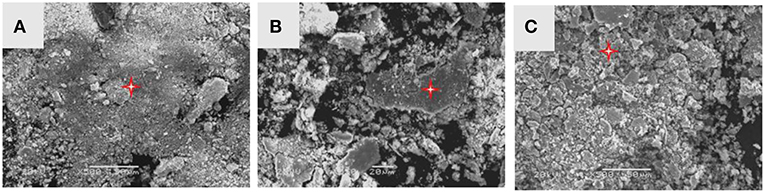
Figure 7. SEM morphology of abrasive debris of twin samples at different degrees: (A) twin free samples, (B) slight twin samples, (C) severe twin samples.
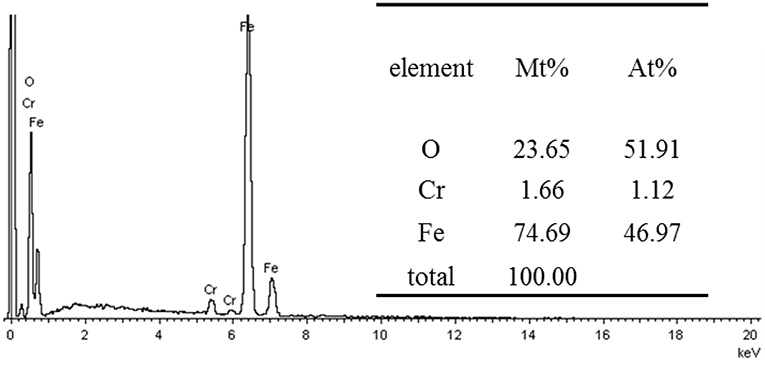
Figure 8. Typical EDS spectra of the worn tracks in Figure 6A.
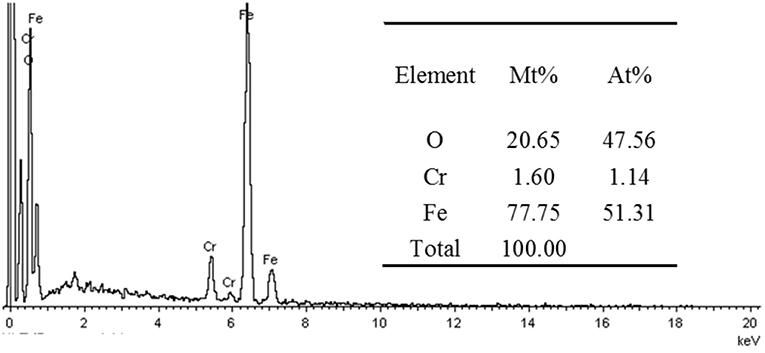
Figure 9. Typical EDS spectra of the worn tracks in Figure 6B.
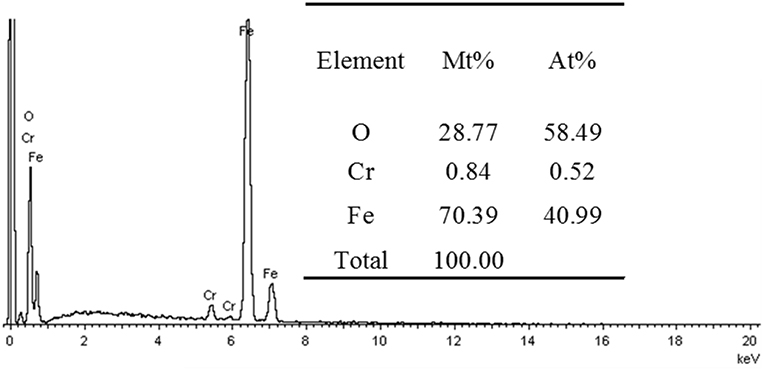
Figure 10. Typical EDS spectra of the worn tracks in Figure 6C.
Figure 11 shows the Raman spectra of the worn surface of twin samples at different degrees. As can be seen from Figures 10A–C, no oxide formation was found in the unworn area of the sample surface, while oxide formation was found in the worn area, indicating that oxidation reaction occurred on the contact surface during the friction process. It can be seen from Figure 10D that the Raman spectrum shapes of the wear area of the three sample groups are the same, and the Raman spectrum peak strength of the twin free samples and the slight twin samples is similar. However, the Raman spectrum peak strength of the severe twin samples is significantly higher than that of the former, indicating that the severe oxidation of the contact area of the severe twin samples means that more oxides were generated. Raman spectral analysis shows that the oxide generated by friction is mainly Fe2O3, which is consistent with the conclusion in the literature (Symonds et al., 2015). According to studies in the literature (Sullivan and Athwal, 1983), the predominant oxides are Fe2O3 for contact temperature of friction pairs up to 200°C, and Fe3O4 for temperatures between 200 and 570°C. This shows that the maximum temperature of the friction interface in this test was about 200°C.
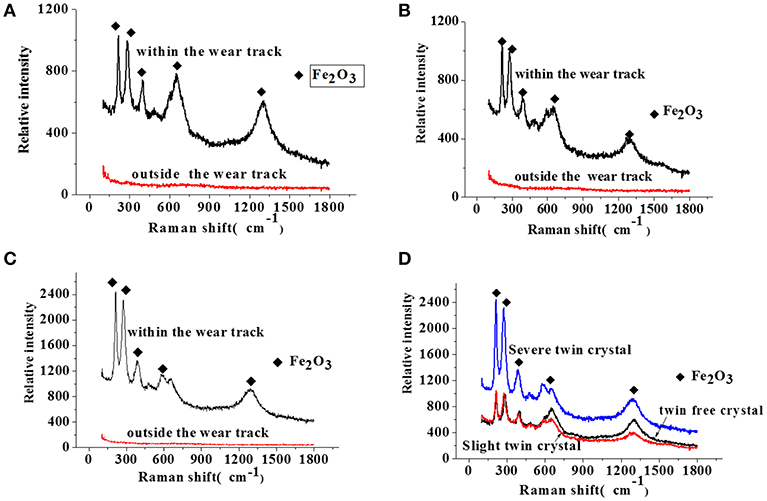
Figure 11. Raman spectra of the worn surface of twin samples at different degrees: (A) twin free samples, (B) slight twin samples, (C) severe twin samples, (D) three sample groups.
Figure 12 shows the vertical section SEM morphology of the wear mark of the twin samples with varying degrees and the corresponding surface distribution of major elements. The depth of the wear marks is relatively shallow, which can hardly be observed from the vertical section, corresponding to the results in Table 4. Meanwhile, there is no obvious plastic deformation of the section due to the factors such as test load and test time. Furthermore, carbides in the cross section is evenly distributed in the matrix. Furthermore, elements of O, Cr and Fe are also uniformly distributed. The element O, it may occur during mechanical polishing.
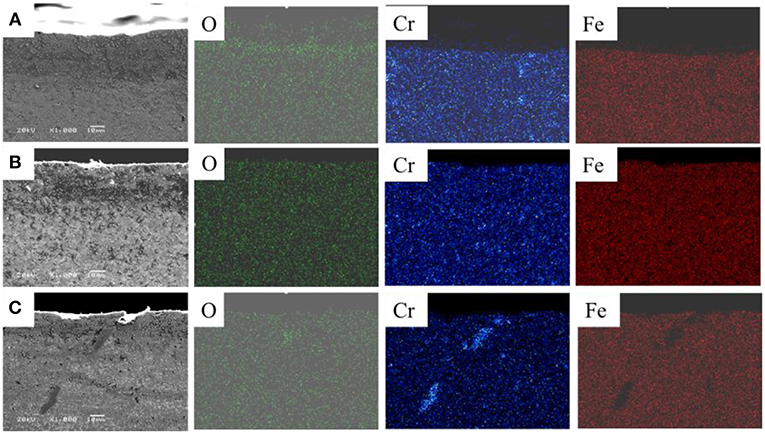
Figure 12. The vertical section SEM morphology of the wear mark of twin samples with varying degree and corresponding surface distribution of major elements: (A) twin free samples, (B) slight twin samples, (C) severe twin samples.
From what has been discussed above, it is concluded that slight twins have little influence on the friction coefficient but can reduce the wear rate slightly, while severe twins significantly increase the friction coefficient and wear rate under the conditions of a dry friction test at room temperature. The SEM morphology, the abrasive debris morphology and the energy spectrum analysis show that oxidation reaction occurs during the friction process, and part of the abrasive debris remains between the friction contact surfaces. Flakes or soft granular oxide flakes are compacted and rubbed repeatedly between the friction contact surfaces to form large flakes. The linked flakes accumulate enough to isolate the friction pair. As the friction continues, the large flakes are broken down and new oxide flakes accumulate. Thus, the oxidation wear is formed repeatedly. Concurrently, the hard granular abrasive particles play the role of plow cutting between the friction contact surfaces, and this is also the main reason why the friction coefficient and wear rate of the severe twin increases noticeably. Further, twin structure refers to carbides in crystals. It is well known that fine dispersed carbides can pin dislocations and strengthen the matrix, while hard carbides can destroy the continuity of the matrix and reduce material properties (Kang and Rivera Díaz del Castillo, 2013; Xu et al., 2017a). In this study, the severe twin structure is linear carbides in grains. Carbides are relatively rare around them (Figure 2), and thus the pinning dislocation effect is weakened. Meanwhile, chain carbides destroy the continuity of matrix. And the material properties are ultimately reduced. Hence, it can be concluded that there is an optimal value or range of the influence of twin structure on the friction and wear performance of G95Cr18 bearing steel.
In brief,the influence of twin structure on friction and wear properties of G95Cr18 stainless steel has been analyzed qualitatively. This study presents only a qualitative test and G95Cr18 stainless steel is mainly used in harsh conditions which result in effects such as corrosion. Therefore, it is of great significance to study the influence of twin structure on the friction and wear performance of G95Cr18 bearing steel in harsh conditions.
Conclusion
1. The qualitative test shows that slight twinning has little influence on the friction coefficient but can reduce the wear rate slightly, while severe twinning can significantly increase the friction coefficient and wear rate, and there is an optimal value or range of values of twin under the conditions of dry friction at room temperature.
2. The wear mechanism of the three sample groups is oxidative wear and abrasive wear, of which the twin free samples and the slight twinning samples are mainly oxidative wear and the severe twin samples are mainly abrasive wear.
3. Oxidation reaction occurred in the friction process on the worn surface of the three sample groups, and the main oxide was Fe2O3.
Data Availability
The raw data supporting the conclusions of this manuscript will be made available by the authors, without undue reservation, to any qualified researcher.
Author Contributions
YZ directs this article. LH is responsible for heat treatment test. This article is written by HG, JL, and SD.
Conflict of Interest Statement
HG, JL, and LH were employed by company Luoyang Bearing Science & Technology Co., Ltd.
The remaining authors declare that the research was conducted in the absence of any commercial or financial relationships that could be construed as a potential conflict of interest.
Acknowledgments
This work was supported by the National Key R&D Program of China [no.2018YFB2000300] and the National United Engineering Laboratory for Advanced Bearing Tribology, Henan University of Science and Technology under grant [no. 201807].
Footnotes
1. ^GB/T3086-2008. High carbon chromium stainless bearing steels [S]. 2008.09.
2. ^JB/T1460-2011. Rolling bearing-bearing parts made from high-carbon chromium stainless steel. 2011.08.
References
Fan, X. S., Yang, Z. G., and Xia, Z. X. (2010). The microstructure evolution of VC coatings on AISI H13 and 9Cr18 steel by thermo-reactive deposition process. J. Alloys Comp. 505, L15–L18. doi: 10.1016/j.jallcom.2010.06.064
Guo, L. X., Li, S., and Li, S. S. (2005). Effect of twin size on the dislocation configuration during cyclic deformation of polycrystalline twin copper. Acta Metall. Sinica 41, 23–27.
Kang, J. H., and Rivera Díaz del Castillo, P. E. J. (2013). Carbide dissolution in bearing steels. Computat. Mater. Sci. 67, 364–372. doi: 10.1016/j.commatsci.2012.09.022
Kun, S., and Dong, X. (2012). Mild quenching of 9Cr18 martensitic stainless steel. Heat Treat. Techn. Equip. 3, 19–22.
Li, S., Liu, X., and Chen, C. (2000). Microstructure analysis of cryogenic decomposition products of twin martensite. Mechan.Eng. Mater. 24, 15–17.
Liu, F., Li, J., and Jie, J. (2013). Surface structure and mechanical properties of 9Crl8Mo stainless steel with nitrogen ion implantation. Rare Metal Mater. Eng. 42, 1838–1842.
Luan, S., and Lei, C. (2009). Effect of twin lamellar thickness on the fatigue properties of nano-twinned cu. Acta Metall. Sinica 45, 808–814.
Shogrin, B., William, P. J., Jones, Jr. W. R., and Herrera-Fierro, P. (1996). The effects of ion implantation on the tribology of perfluoropolyether-lubricated 440C Stainless steel couples. Tribol. Transact. 39, 507–516. doi: 10.1080/10402009608983561
Sullivan, J. L., and Athwal, S. S. (1983). Athwal. Mild wear of low alloy steel at temperatures up to 500?C. Tribol. Int. 16, 123–131. doi: 10.1016/0301-679X(83)90053-1
Symonds, N., Corni, I., Wood, R. J. K., Wasenczuk, A., and Vincent, D. (2015). Observing early stage rail axle bearing damage. Eng. Fail. Analys. 56, 216–232. doi: 10.1016/j.engfailanal.2015.02.008
Wang, H. (2011). Study on twin carbide of high carbon chromium stainless bearing steel. Spec. Steel Techn. 17, 9–15.
Wang, S., Yu, Z., and Yao, Y. (2006). Eliminate heat treatment technology of 9Cr18Mo forging twin structure. Bearing. 5, 11–13.
Xu, L., Fan, X., Wei, S., Liu, D., Zhou, H., Zhang, G., et al. (2017b). Microstructure and wear properties of high-speed steel with high molybdenum content under rolling-sliding wear. Tribol. Int. 116, 39–46. doi: 10.1016/j.triboint.2017.07.002
Xu, L., Wei, S., Xiao, F., and Zhou, H. (2017a). Effects of carbides on abrasive wear properties and failure behaviours of high speed steels with different alloy element content. Wear 376–377, 968–974. doi: 10.1016/j.wear.2017.01.021
Xu, X., Xu, J., and Bao, M. (2006). Influence of nitriding on tribological properties of 9Crl8. Mater. Heat Treatt. 55, 50–53.
Xu, Y., Liu, Z., and Ren, H. (2012). “Twin substructure and formation mechanism of martensite in steel,” in Tenth National Conference on Solid State Transformation Solidification and Application (Suzhou), 106–107.
Ying, L. X., Wang, L. Q., Jia, X., and Gu, L. (2007). Laser alloyed coatings of TiB2/Graphite on 9Cr18 stainless steel surface. J. Iron Steel Res. 14, 69–72. doi: 10.1016/S1006-706X(07)60046-6
Keywords: twin structure, carbide, G95Cr18 stainless bearing steel, friction, wear
Citation: Guo H, Du S, Lei J, Zhang Y and Hu L (2019) Influence of Twin Carbide Structure on Friction and Wear Properties of G95Cr18 Stainless Bearing Steel. Front. Mater. 6:162. doi: 10.3389/fmats.2019.00162
Received: 26 April 2019; Accepted: 24 June 2019;
Published: 10 July 2019.
Edited by:
Shengqiang Ma, Xi'an Jiaotong University, ChinaReviewed by:
Shengyu Zhu, State Key Laboratory of Solid Lubrication, Lanzhou Institute of Chemical Physics, Chinese Academy of Sciences, ChinaLe GU, Harbin Institute of Technology, China
Jinjun Lu, Northwest University, China
Copyright © 2019 Guo, Du, Lei, Zhang and Hu. This is an open-access article distributed under the terms of the Creative Commons Attribution License (CC BY). The use, distribution or reproduction in other forums is permitted, provided the original author(s) and the copyright owner(s) are credited and that the original publication in this journal is cited, in accordance with accepted academic practice. No use, distribution or reproduction is permitted which does not comply with these terms.
*Correspondence: Sanming Du, ZHNtaW5nXzAwMUAxNjMuY29t; Yongzhen Zhang, eXp6aGFuZ0BoYXVzdC5lZHUuY24=