- 1Department of Mining and Petroleum Engineering, Faculty of Engineering, Chulalongkorn University, Bangkok, Thailand
- 2Division of Sustainable Resources Engineering, Faculty of Engineering, Hokkaido University, Sapporo, Japan
- 3Department of Materials and Resources Engineering Technology, College of Engineering and Technology, Mindanao State University-Iligan Institute of Technology, Iligan City, Philippines
We developed a technique called the reverse hybrid jig, an advanced physical separation technique that combines the principles of jig and flotation to separate floating plastics. This technique is a promising green technology that is more economical and environmentally friendly compared with the conventional flotation. Although the applicability of this technique to separate PP/PE have been reported, the index to illustrate the possibility of separation for the reverse hybrid jig is still not available. In this study, a reverse apparent concentration criterion (CCRA) is proposed to estimate reverse hybrid jig separation efficiency. This modified concentration criterion can be calculated using the specific gravity (SG) of particle with attached bubbles called the apparent specific gravity (SGA). To determine the volume of attached bubbles on plastic surfaces under water pulsation, a laser-assisted apparatus was used under various conditions, including plastic type, air flow rate, dosage, and type of wetting agent. The results of attached bubble volume measurements were used to calculate the SGA and CCRA. The estimated values were then compared with the results of reverse hybrid jig separation. It was found that higher CCRA resulted in better separation efficiency. In addition, an empirical linear equation for estimating the reverse hybrid jig separation efficiency is proposed.
1 Introduction
Management of municipal solid wastes (MSW) is a big global challenge particularly because of the increasing amount of their associated plastic waste fraction (Geyer et al., 2017). During the Coronavirus disease (COVID-19) pandemic, the situation with plastic wastes worsened as consumption of single-use plastics in households skyrocketed. Various types of single-used plastics (e.g., surgical mask, plastic glove, and packaging from food delivery) are not treated properly and often mixed with MSW. Prata et al. (2020), for example, estimated that the monthly use of personal protective equipment (PPE) worldwide was approximately 129 billion face masks and 65 billion gloves. Furthermore, lockdowns in many countries around the world due to the pandemic led to the growth of e-commerce and food delivery services that increased plastic packaging waste generation by 53% in 2021 (Filho et al., 2021).
Almost half of plastics produced worldwide (46%) and more than half of plastic used in the global packaging industry (69.5%) is made up of polyolefin (Rabnawaz et al., 2017). Polyolefin—floating plastics like polypropylene (PP) and polyethylene (PE)—is the most widely produced and consumed type of thermoplastics due to its low cost, light weight, easy processability, and good recyclability (Gopanna et al., 2019). Moreover, PP is one of the most important plastics used to fabricate medical face masks (Irez et al., 2022).
Resources recovery, the concept of waste reduction by extracting valuable materials from waste streams, is a promising strategy for the management of plastic wastes in MSW. Recovered plastic wastes can be recycled to generate new plastic materials (i.e., resources recycling) and/or used as supplementary fuel for cement production, pyrometallurgical operations and electricity generation (i.e., energy recovery) (Tabelin et al., 2021). Compared with landfilling, incineration, and energy recovery, resources recycling is a more sustainable approach because plastic materials are recirculated back into the economy (Demirbas, 2011). Therefore, resources recycling is an important way of minimizing the amounts of plastic wastes disposed of in landfills or burned in incinerators. It means that recycling of mixed plastic wastes is critical to limit the negative environmental impacts of plastics as well as to conserve finite natural resources. It is also included in the United Nation Sustainable Development Goals (UN-SDGs): Goal 12 “Responsible production and consumption” (United Nations, 2015). To effectively recycle plastics, separation of various plastic types in mixed-plastic wastes is essential. Sink-float separation in water is commonly used to separate polyolefins from other mixed plastics because they have lower densities than water causing them to float while other types of plastics sink with their heavier density. The sink-float separation of various polyolefins like PP and PE, however, is expensive because it requires the use of water-ethanol mixtures as medium (Mumbach et al., 2019).
An alternative to sink-float separation for the separation of mixed-plastics is the use of jig, a gravity concentration technique that uses vertical expansion and contraction of a bed of particles by a pulse of fluid to separate the particle based on difference of specific gravity (SG) and settling velocity (v). It is one of the oldest mineral processing methods and still used due to its simple operation, low cost, and high efficiency. Among the many types of jigs, four advanced jig separation technology—RETAC jig, reverse jig, hybrid jig, and reverse hybrid jig (Figure 1)—were developed in the Laboratory of Mineral Processing and Resources Recycling, Hokkaido University, Japan for plastic-plastic separation. First, the RETAC jig, modified from coal cleaning TACUB (Tsunekawa Air Chamber Under Bed) jig (commercially called as BATAC jig) (Hori et al., 2009a; Tsunekawa et al., 2012; Phengsaart et al., 2020, 2021), was successfully applied to recover plastics and other valuable materials from copy machines (Tsunekawa et al., 2005), automobile shredded residues (ASR) (Kuwayama et al., 2014), small home appliances (Phengsaart et al., 2018), mobile phones (Jeon et al., 2019) in both laboratory- and pilot-scales. Second, the reverse jig, which is the RETAC jig with top screen, was developed to separate plastics lighter than water (e.g., PP and high-density polyethylene (HDPE) from packaging containers) by their difference in levitating velocity (Ito et al., 2010). Third, the hybrid jig was developed to separate plastics with similar SGs but different surface wettabilities by combining density- and surface-based separation concepts. In this type of jig, an aeration tube is installed under the screen to generate air bubbles introduced into the jig separation chamber. Separation occurs when the SG of one type of plastic is reduced and changed into apparent specific gravity (SGA) due to the attachment of bubbles. This causes stratification during water pulsation, so the lower SGA (more hydrophobic) plastic is recovered on top while that with higher SGA (more hydrophilic) is recovered at the bottom. The hybrid jig effectively separated various types of mixed-plastics like polyethylene terephthalate (PET)/polyvinyl chloride (PVC) (Hori et al., 2009b; Ito et al., 2019a, 2020), polypropylene with glass fiber (PPGF)/high impact polystyrene (HIPS) (Ito et al., 2019b, 2020), and PVC/polyamide (nylon-66 or PA) (Ito et al., 2019b). Finally, the reverse hybrid jig—a combination of reverse and hybrid jigs—was developed to separate floating plastics having similar SGs like PE/cross-linked polyethylene (XLPE) mixtures (Ito et al., 2021).
For separation to occur, less selectivity of bubble attachment is required for hybrid and reverse hybrid jigs compared with flotation. Very high bubble attachment selective is crucial in flotation because bubbles are used to separate and carry hydrophobic particles to froth products while hydrophilic particles are left in suspension. Because of this, the high consumption of chemical reagents (e.g., wetting agents and frothers) are required for high selectivity and efficiency (Aikawa et al., 2020; Hornn et al., 2020, 2021). In contrast, only few bubbles with low selectivity are needed for effective separation in hybrid and reverse hybrid jigs because their main role is only to change the SG of more hydrophobic plastics. Meanwhile, water pulsations are introduced to stratify the particles into different layers in the separation chamber, so little consumption of chemical reagents is required (Ito et al., 2019b). Therefore, advanced jigs are both green and sustainable technologies.
To obtain high quality recycled plastics with similar physical/chemical properties of virgin resins, high separation efficiency is required. In the previous studies of the authors about advanced jig separation efficiency, the concentration criterion (CC)—an index illustrates the possibility of gravity separation—was modified to estimate the separation efficiency of the RETAC jig, reverse jig, and hybrid jig. However, the estimation of CC for floating plastics using the reverse hybrid jig separation is still lacking in the literature.
In this study, a laser-assisted measurement apparatus was used to measure attached-bubble volume on plastics during water pulsation and determine the SGA of plastics under various conditions (i.e., plastic type, air flow rate, dosage and type wetting agents). Finally, a new index based on CC is proposed to estimate the separation efficiency of reverse hybrid jig separation.
2 Concentration criteria for advanced jig separation
The concentration criterion (CC) is an index used to determine the possibility of separation by gravity concentrators like conventional jigs. The higher the value of CC, the easier it is to separate materials in the sample (Wills and Finch, 2015; Gupta and Yan, 2016). It is calculated using the following equation (Wills and Finch, 2015; Gupta and Yan, 2016):
where ρH and ρL are the mass density of heavy (H) and light (L) materials, respectively while ρF is the mass density of fluid medium used for separation.
In terms of SG, Eq. 1 can be rewritten as
where SGH and SGL are the specific gravities of H and L materials, respectively while SGF is the specific gravity of fluid medium.
In gravity separation, particles with different densities are separated by the difference of their settling velocities (v) in fluid usually water. The settling of a particle in water is strongly influenced by three forces—gravity force (FG; Eq. 3), buoyancy force (FB; Eq. 4) and drag force (FD; Eq. 5)—while its v is determined by the balance between these three forces (Eq. 6).
where m is the mass of the particle [kg], v is the velocity of particle [m/s], t is time [s], g is gravitational acceleration [m/s2], ρP is density of particle [kg/m3], ρF is density of fluid [kg/m3], CD is drag coefficient, and A is the projection area of particle [m2].
where V = volume of particle [m3].
When a particle reaches terminal velocity (v∞), its acceleration (dv/dt) becomes zero and Eqs 6, 7 can be simplified to the following equation:
If the particle is a sphere (*), its projection area (A*) and volume (V*) are given by Eqs 9, 10.
The drag coefficient (CD) in Eqs 5, 6 could also be expressed as a function of the Reynolds number (Rep) assuming a laminar flow regime during particle settling (Rep < 1) (Eqs 11, 12).
where µ is the viscosity of fluid [Pa,s].
In a laminar or Stokes’ flow regime, the terminal velocity of a sphere (v∞*) could be calculated and is given as Eq. 13 by substituting Eqs 9–12 to Eq. 8.
Using Stokes’ law (Eq. 13), CC (Eq. 1) can be expressed by the ratio of v∞ of heavy and light particles.
where v∞*H and v∞*L are the terminal velocities of heavy and light materials with spherical shape, respectively.
The equations of conventional CC (Eqs 1, 2 and Eq. 14), however, are not applicable for non-spherical particles. To modify the CC and capture the effects of particle shape, a dynamic shape factor called shape settling factor (SSF) was introduced (Eq. 15) (Gupta and Yan, 2016).
The SSF is defined as the ratio of the terminal velocity in static water of a non-spherical particle (v∞) and the terminal velocity in static water of a spherical particle having the same D (v∞*). Using SSF (Eq. 15), the modified concentration criterion for non-spherical particles (CCS) were obtained as follows (Pita and Castilho, 2016):
where SSFH and SSFL are the shape settling factor of heavy and light materials, respectively.
Then,
where v∞H is the terminal velocity in static water of a heavy, non-spherical particle, v∞L is the terminal velocity in static water of a light, non-spherical particle, v∞*H is the terminal velocity in static water of heavy, spherical particle having the same D as the heavy, non-spherical particle, and v∞*L is the terminal velocity in static water of a light, spherical particle having same D as a light, non-spherical particle.
Finally,
However, CC and CCS are suitable for estimate the separation efficiency of sinking plastics using conventional and RETAC jigs. To estimate the results of reverse jig separation that separate the particles based on levitation velocity difference, Eqs 1, 2 were modified into reverse concentration criterion (CCR) as shown in Eq. 19 (Ito et al., 2010).
Similarly, for hybrid jig separation, since the apparent specific gravity (SGA)—SG changed by bubble attachment—affects the separation efficiency more than the inherent SGs of plastics therefore, SGA (Eq. 20) calculated from the inherent specific gravity of materials (SGP) and volume of attached bubbles on particles during water pulsation (V0*) need to be considered (Ito et al., 2020).
From Eqs 2, 20, the apparent concentration criterion (CCA) —modified CC based on SGA—was proposed as Eq. 21 to determine the efficiency of hybrid jig separation (Ito et al., 2020).
where SGAH and SGAL are the SGA of H and L materials, respectively.
These CC, CCS, CCR, and CCA have been successfully applied to estimate the separation efficiency of various jig separation of plastics (Ito et al., 2010, 2020; Pita and Castilho, 2016). However, an index to illustrate the possibility of separation for reverse hybrid jig is still not available. In this study, reverse apparent concentration criterion (CCRA)—modified CC combining the principles of reverse jig and hybrid jig (Eqs 19, 21)—was proposed to estimate reverse hybrid jig separation efficiency (Eq. 22) The experiments to confirm this proposed equation were carried out as explained in the next section.
3 Materials and methods
3.1 Samples
The samples used in this study are virgin plastic pellets about 3.5–4.0 mm in size, spherically shaped and without additives. Two types of polyolefins, PP (PP1100NK, POLIMAXX, IRPC Public Co., Ltd., Thailand) with SG of 0.90 and PE, which is further subdivided into low-density polyethylene (LDPE; LDJJ4324, POLENE, TPI Polene Public Co. Ltd., Thailand) with SG of 0.92 and high-density polyethylene (HDPE; HD2308J, InnoPlus, PTT Global Chemical Public Co., Ltd., Thailand) with SG of 0.96.
3.2 Reagents
Four types of wetting agents were used: 1) docusate sodium salt (Aerosol OT; AOT), 2) calcium lignosulfonate (CaLS), 3) sodium lignosulfonate (NaLS), and 4) tannic acid (TA). Methyl isobutyl carbinol (MIBC), a reagent widely utilized in flotation as a frother, was used to stabilize bubbles in solution. All chemicals used in the experiments are reagent grade obtained from Sigma-Aldrich Co., United States .
3.3 Measurements of attached-bubble volume
Because SGA (Eq. 20) is an important factor to estimate the reverse hybrid jig separation efficiency, determination of attached-bubble volume on plastic surfaces during water pulsation (V0*) were carried out under various conditions using the apparatus shown in Figure 2 (Ito et al., 2020, 2021).
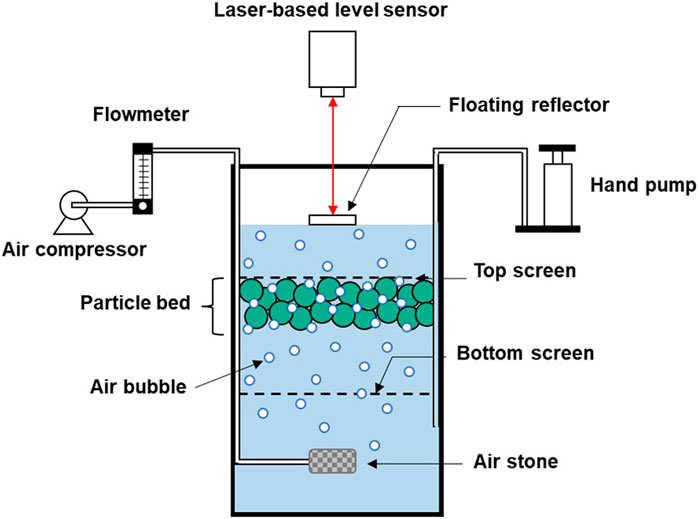
FIGURE 2. A schematic diagram of the laser-assisted measurement setup for the determination of attached-bubble volume.
In these tests, a reverse hybrid jig with a separation chamber 60 mm long, 60 mm wide, and 150 mm high were used. A hand-pump connected to the air chamber was used for water pulsation while an air pump introduces air into the jig through a tube connected to porous rock for creating air bubbles under the separation chamber. Air bubbles are introduced under the particle bed, and when bubbles attached to particles, an equivalent water level rise is recorded. This water level rise is accurately measured and recorded by a laser-based level sensor (HG-C1050, Panasonic Corporation, Japan) with a floating reflector on top of the water surface. The attached-bubble volume can then be calculated from changes in water level inside the separation chamber before and after bubble introduction (Ito et al., 2020, 2021).
Supplementary Figure S1 shows the procedure of this measurement in which 50 g of a single-type plastic sample (i.e., PP, LDPE, or HDPE) was fed into a separate chamber then, 1.2 L of water containing 20 ppm of MIBC were added. The experiments were carried out with wetting agents (i.e., AOT, CaLS, NaLS, or TA) at concentrations of 0, 50, and 100 ppm. The water pulsation was controlled by hand-pump at a displacement of 20 mm and frequency equal to 30 cycles/min with air bubbles generated using an air pump at flow rates of 0.5, 1, and 1.5 L/min for 3 min. The measurement was carried out by following the procedure in the published paper of Ito et al. (2020, 2021). After finished the aeration with water pulsation, the change in water height were recorded using a laser-based level sensor. Then, four more water pulsation were introduced to remove air bubbles that were trapped in the void between plastic pallets and the height of the water surface of each pulsation were also recorded. These data were used to determine the V0* (Ito et al., 2020).
3.4 Reverse hybrid jig separation experiments
The reverse hybrid jig separation experiments were carried out using the same reverse hybrid jig used in the attached-bubble volume measurements. 60 g of PP/LDPE, and PP/LDPE mixtures with 1:1 mixing ratio (by weight) were used for the experiments. All conditions were the same as that of the attached-bubble volume measurements. Experiments were carried out under two different methods below (Supplementary Figure S2) (Ito et al., 2021):
3.4.1 Reverse hybrid jig separation experiments with continuous bubble generation
In these tests, air bubbles were introduced for 5 min as a kind of “conditioning” process. This was followed by water pulsation for 3 min with continuous bubble generation bubble. After the separation, products were collected into three layers from the top. The products in each layer were then separated by sink-float separation using 50 wt% ethanol (prepared using 99.9% C2H6O, AR grade, Qchemical Co. Ltd., Thailand) solution (SG: ∼0.91) as medium to determine the purity of each layer.
3.4.2 Reverse hybrid jig separation experiments without bubble generation during pulsation
Similar to the tests in Section 3.4.1, air bubbles were introduced for 5 min, but after conditioning, air introduction was stopped and water pulsation was introduced for 3 min. For the determination of purity of products in each layer, the same sink-float separation method was used as outlined previously.
4 Results and discussion
4.1 Effects of air flow rate and wetting agents on the apparent specific gravity.
Figure 3 shows the SGA of plastics measured using the laser-assisted measurement apparatus without wetting agent at air flow rates of 0, 0.5, 1.0, and 1.5 L/min. HDPE had the highest SGA regardless of the air flow rate and was followed by LDPE and PP. It was also found that the SGA of all types of plastics decreased with increasing air flow rate, which could be attributed to the higher volume of bubbles attached to plastic surfaces (Eq. 20).
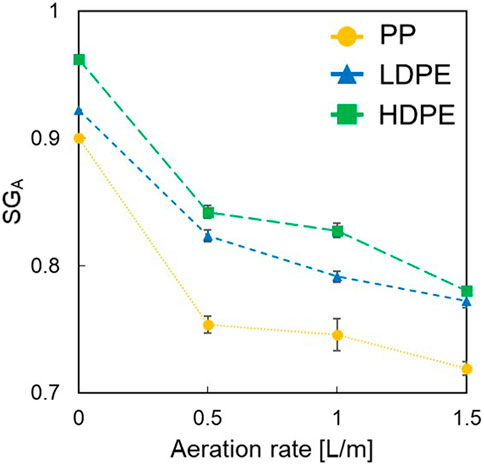
FIGURE 3. Apparent specific gravities of PP, LDPE, and HDPE at different air flow rates (i.e., 0, 0.5, 1.0, and 1.5 L/min) in water (i.e., without wetting agent).
After determining the values of SGA, these were used to calculate CCRA using Eq. 22, and the results are presented in Table 1. The plastic mixtures of PP/HDPE showed higher CCRA compared with that of PP/LDPE because of larger differences in SGA of the former than the latter. It is also interesting to note was also found that the CCRA were higher when lower air flow rate was used. These results indicate that the conditions with lower air flow rate should achieve higher separation efficiency if the proposed equation (Eq. 22) is correct as well as the separation of PP/HDPE should be better than that of PP/LDPE.
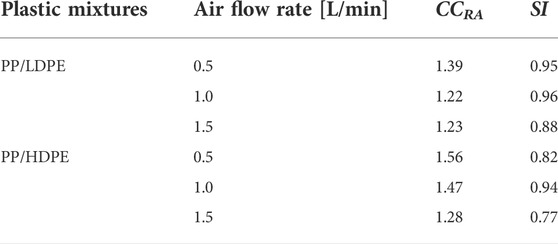
TABLE 1. Reverse apparent concentration criterion (CCRA) of each plastic mixtures (i.e., PP/LDPE and PP/HDPE) and sharpness index (SI) of reverse hybrid jig separation experiments without bubble generation during pulsation at air flow rate (i.e., 0.5, 1.0, and 1.5 L/min) and wetting agent of 0 ppm.
Figure 4 shows the SGA of PP, LDPE, and HDPE at air flow rate of 1.0 L/min in the solution with wetting agent (i.e., AOT, CaLS, NaLS, and TA) of 0, 50, and 100 ppm. HDPE shows the highest SGA in all conditions followed by LDPE and PP, a trend similar to the SGA results in water (Figure 3). It was also found that SGA of HDPE drastically changed with the concentration and type of wetting agents but those of LDPE and PP changed only slightly. To explore these discrepancies more, CCRA were calculated from SGA of each condition as shown in Table 2. The PP/HDPE mixtures always had higher CCRA compared with the PP/LDPE mixtures under the same conditions due to their higher SGA difference. Also, most conditions with wetting agents had higher CCRA than without wetting agents when the same air flow rate (i.e., 1.0 L/min) was used, indicating that the addition of wetting agents could improve the reverse hybrid jig separation efficiency if this proposed index (Eq. 22) is correct.
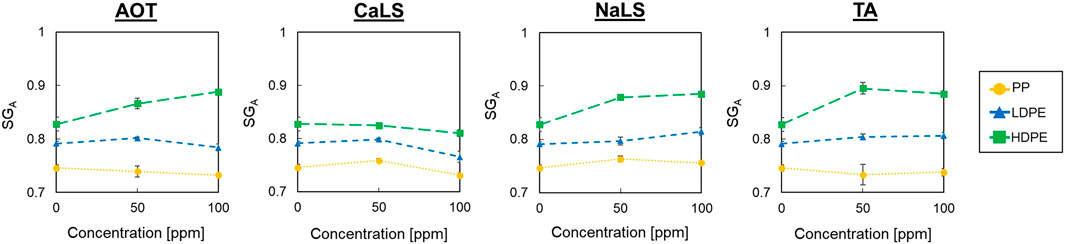
FIGURE 4. Apparent specific gravities of PP, LDPE, and HDPE at air flow rate of 1.0 L/min with AOT, CaLS, NaLS, and TA at concentrations of 0, 50, and 100 ppm.
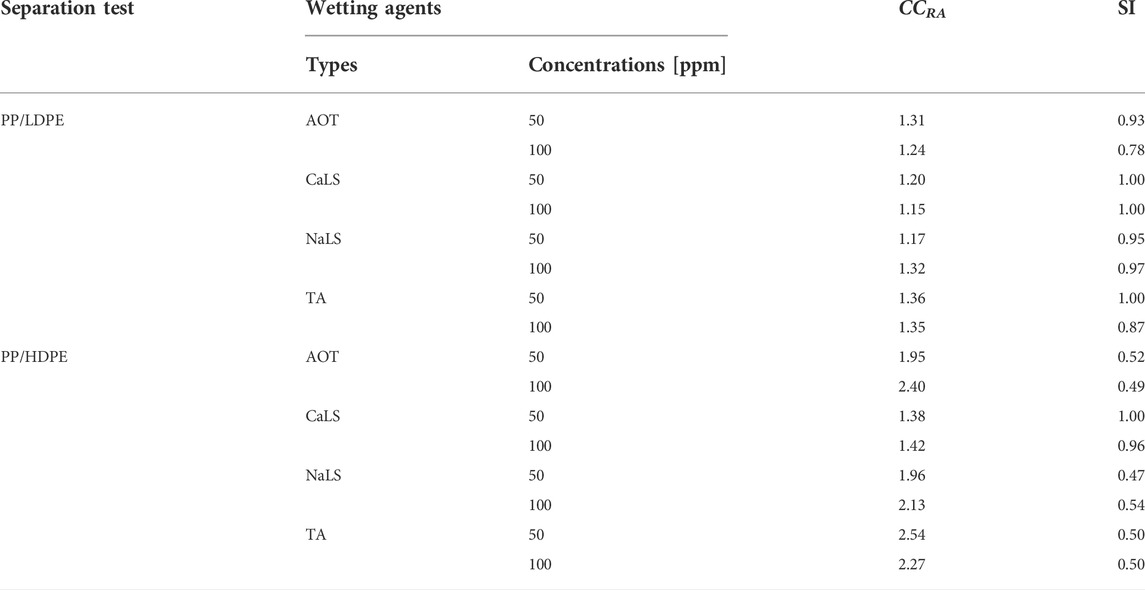
TABLE 2. Reverse apparent concentration criterion (CCRA) of each plastic mixtures (i.e., PP/LDPE and PP/HDPE) and sharpness index (SI) of reverse hybrid jig separation experiments without bubble generation during pulsation at different air flow rate of 1.0 L/min and wetting agents (i.e., AOT, CaLS, NaLS, and TA) of 50 and 100 ppm.
The SGA of HDPE increased with the addition of AOT with the highest SGA difference and CCRA value between PP and HDPE obtained at 100 ppm. This means that 100 ppm AOT could achieve better separation efficiency than pure water or lower AOT concentrations. For NaLS and TA, the SGA of HDPE only increased until 50 ppm. After this dosage, the SGA like that of AOT remained constant. Meanwhile, contrast, CaLS had negligible effects on the SGA of HDPE. Also, because this agent has very low effect influence on the apparent density of the three plastics. It can be said that it does not change the hydrophobicity of the three plastics. These results indicate that AOT, NaLS, and TA are capable of selectively modifying the hydrophobic surface of HDPE to become more hydrophilic. It follows that surface modification using wetting agents like AOT, NaLS, and TA could enhance the separation of PP/HDPE since CCRA could be increased.
In the case of PP/LDPE mixtures, the results are still unclear and difficult to interpret due to the unnoticeable changes of SGA. Based on the CC guide for gravity separation of Gupta and Yan (2016), PP/LDPE separation might not because particles with 3.5–4.0 mm size requires CC to be larger than 1.7. To confirm these hypothesis, the reverse hybrid jig separation experiments with the condition above were carried out.
4.2 Effects of air flow rate and wetting agents on reverse hybrid jig separation
The results of reverse hybrid jig separation experiments with continuous bubble generation of PP/HDPE and PP/LDPE plastic mixtures using various air flow rates as well as different wetting agent types and concentrations are presented in Figure 5. It was found that after separation, each layers contained similar amounts of PP and PE (i.e., LDPE or HDPE), indicating that separation did not occur. Visual observations suggest that separation was disturbed by the rising motion of air bubbles, which influence the fluidization behavior of the particle bed during water pulsation. However, there were slight improvements in PP/HDPE separation when wetting agents, particularly in TA, were added (Figure 6). These results confirmed that wetting agents could change the surface wettability of HDPE particles and improve the efficiency of reverse hybrid jig separation.
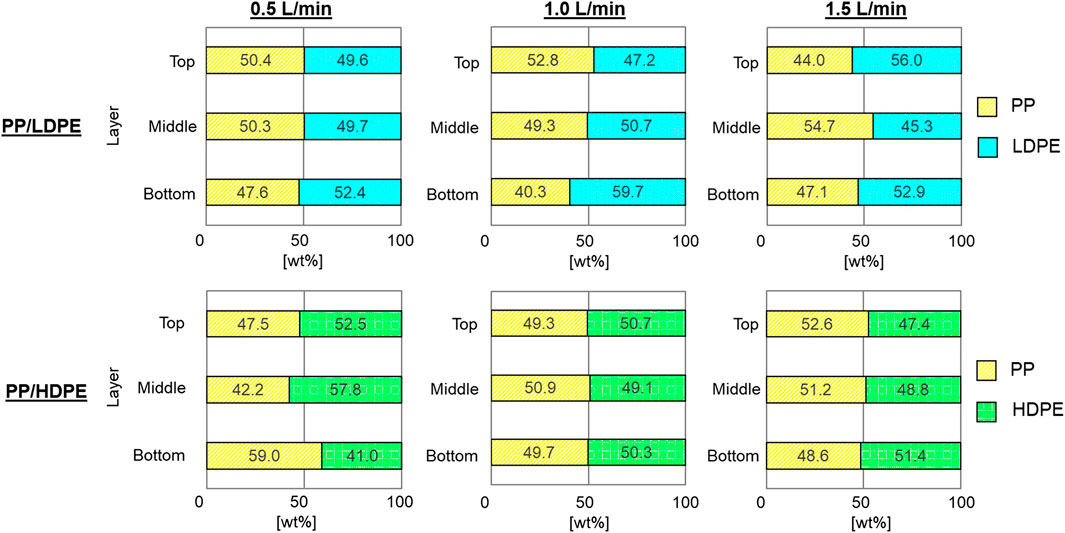
FIGURE 5. The proportion of plastics in each layer after reverse hybrid jig separation of PP/LDPE and PP/HDPE with continuous bubble generation at different air flow rate of 0.5, 1.0, and 1.5 L/min in water (i.e., without wetting agent).
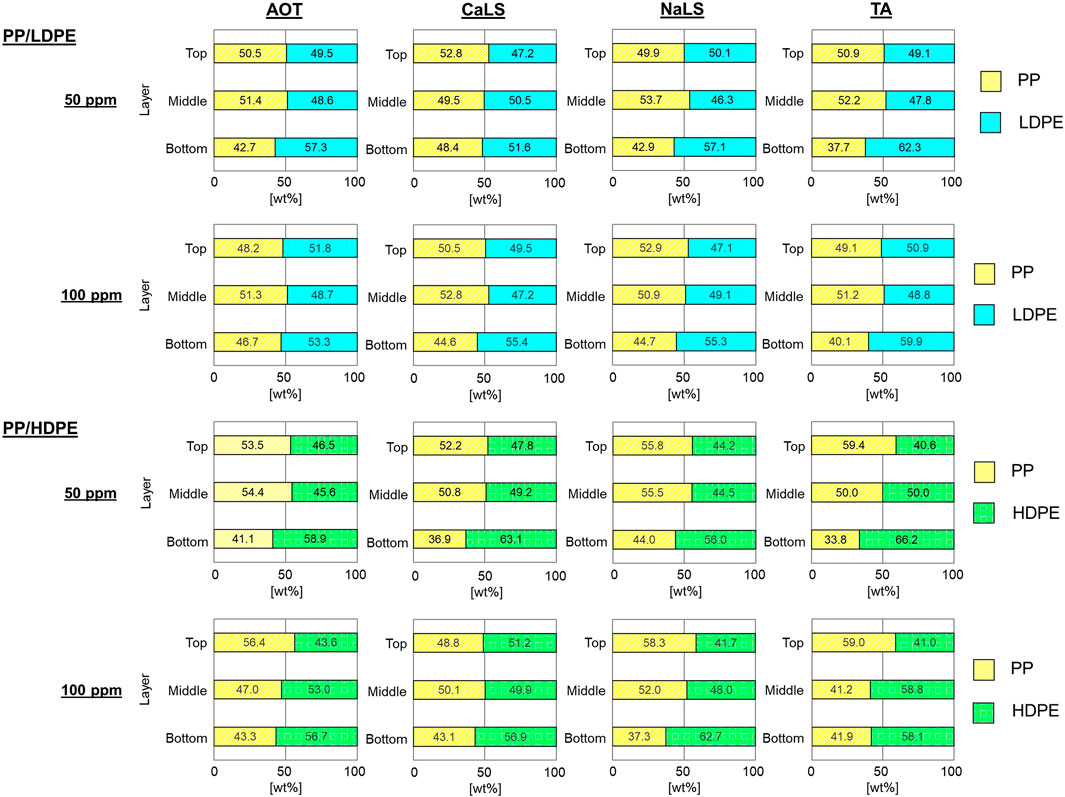
FIGURE 6. The proportion of plastics in each layer after reverse hybrid jig separation of PP/LDPE and PP/HDPE with continuous bubble generation at air flow rate of 1.0 L/min in the solution with AOT, CaLS, NaLS, and TA at concentration of 50 and 100 ppm.
In contrast, the separation could occur for reverse hybrid jig separation experiments without bubble generation during pulsation (Figure 7). Compared with that of continuous bubble generation, the particle layer expanded more freely when bubbles were not introduced during pulsation. The particles with attached bubbles also stratified based on their SGA without excess bubbles. Moreover, separation was possible even when CCRA are less than 1.7 (Table 1). This improvement to the CC guide of Gupta and Yan (2016) could be attributed to the high precision control of water pulsation in advanced jig (Phengsaart et al., 2021). It was found that PP was concentrated in the top layers while PE (i.e., LDPE or HDPE) was concentrated in bottom layers. The results confirmed that separation of PP and HDPE was more effective than that of PP and LDPE in all air flow rates and was consistent with the results discussed previously (Figure 3 and Table 1). While air flow rate did not have significant effect on the separation. These indicate that SGP was important for the separation. However, to prove that SGA has more influence on gravity-wettability hybrid separation, more reverse hybrid jig separation experiments without bubble generation during pulsation were done with surface modification using wetting agents at air flow rate of 1.0 L/min (Figure 8 and Table 2). Similarly, PP and PE (i.e., LDPE or HDPE) were concentrated in the top and bottom layers, respectively. The results showed that the separation of PP and HDPE using AOT, NaLS, and TA improved but not for CaLS. While for PP/LDPE mixtures, the separation could not be improved. These reverse hybrid jig separation results were in line with the results of SGA obtained from attached-bubbles volume measurements, indicating that separation efficiency has a stronger relationship with SGA than SGP. Also, the CCRA could be used to estimate the efficiency of reverse jig separation.
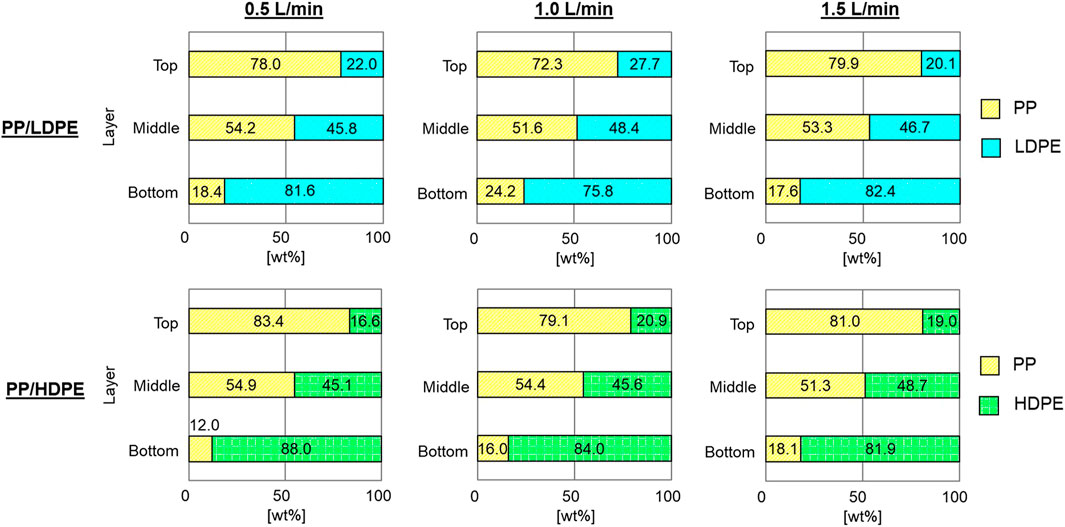
FIGURE 7. The proportion of plastics in each layer after reverse hybrid jig separation of PP/LDPE and PP/HDPE without bubble generation during pulsation at different air flow rates of 0.5, 1.0, and 1.5 L/min in water (i.e., without wetting agent).
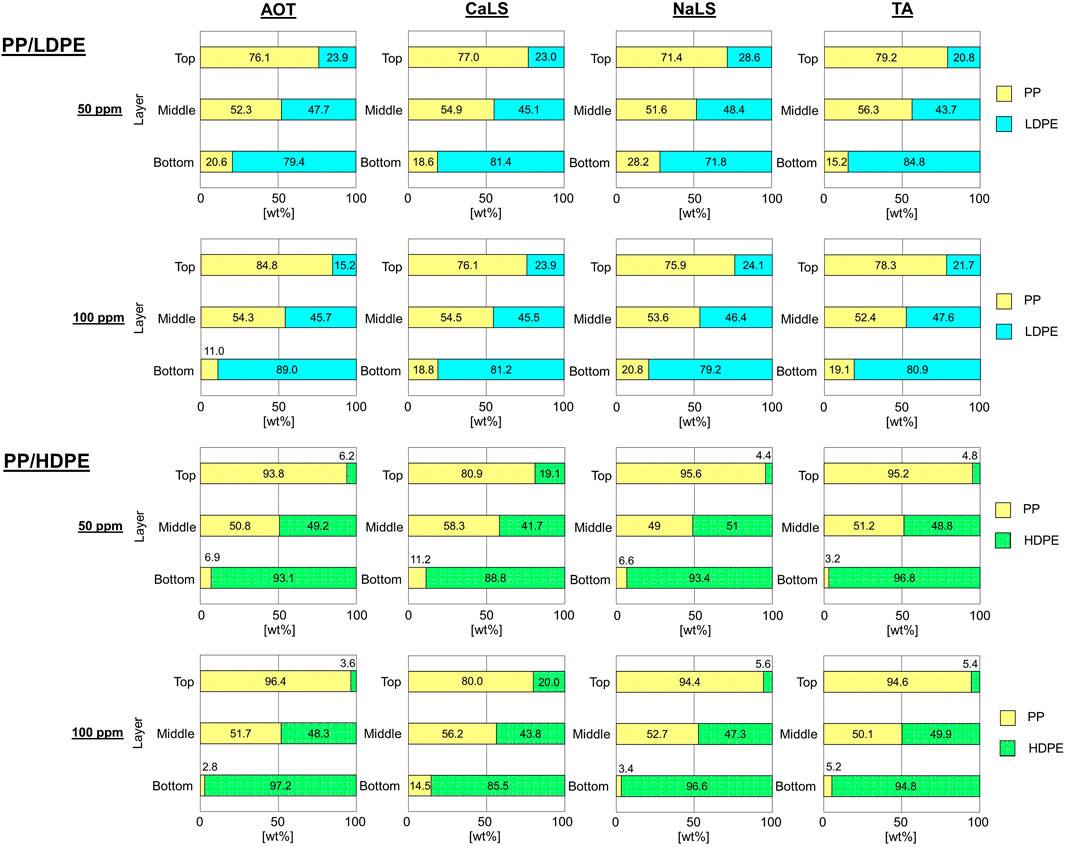
FIGURE 8. The proportion of plastics in each layer after reverse hybrid jig separation of PP/LDPE and PP/HDPE without bubble generation during pulsation at air flow rate of 1.0 L/min with AOT, CaLS, NaLS, and TA at concentrations of 50 and 100 ppm.
4.3 Relationship of sharpness index of reverse hybrid jig separation without bubble generation during pulsation and reverse apparent concentration criterion.
To determine the separation efficiency, purity distribution curves (Supplementary Figure S3, S4) were plotted from the results of Figure 7 and Figure 8, respectively. The horizontal axis (X) refers to the height (distance between the center position of each product layer and the lowest point of particle bed) and the vertical axis is the purity of PP while the horizontal axis (Y) refers to the purity of lighter plastic (i.e., PP) of each layer products.
From these purity distribution curves, the sharpness index (SI) could be calculated by Eq. 23 (Ito et al., 2020).
where X84.13 and X50 are the heights when purities of PP are 84.13 and 50%, respectively.
The value of CCRA and SI under various conditions of air flow rate and surface modifications using wetting agents are shown in Table 1 and Table 2. It was found that the SIs were low (high separation efficiency) when CCRA were high.
To understand the relationship of CCRA and SI more clearly, the data in Table 1 and Table 2 were plotted into Figure 9. An empirical linear equation (Eq. 24) as a function of CCRA and SI was obtained using least-squares method with a coefficient of determination (R2) of 0.81.
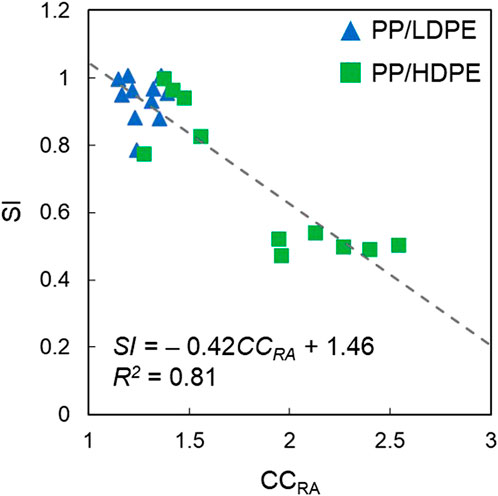
FIGURE 9. Relationship between sharpness index (SI) and reverse apparent concentration criterion (CCRA).
This relationship showed that the higher the values of CCRA, the lower are the values of SI, which means that higher separation efficiency and CCRA as well as attached-bubble volume measurement could be used to estimate the reverse jig separation efficiency when air bubbles are not introduced during water pulsation.
5 Conclusions
In this study, a new index called the reverse apparent concentration criterion (CCRA) is proposed to estimate the efficiency of reverse jig separation at various air flow rates and surface modifications using wetting agents. The findings of this study are summarized as follows:
• Higher air flow rate deceased the SGA of plastics because more air bubbles were generated and attached on plastic surfaces.
• Reverse hybrid jig separation with continuous bubble generation could not be used to separate mixed plastics because the rising motion of air bubbles disturbed particle fluidization. By stopping bubble generation during pulsation, separation occurred because the particle bed could expand more freely.
• Except for CaLS, AOT, NaLS, and TA could selectively modify the surface of HDPE from hydrophobic to become more hydrophilic that improved the separation of PP/HDPE plastic mixtures.
• CCRA, a modified CC for reverse hybrid jig, obtained using SGA and V0* from the attached-bubble volume measurement could be used to estimate the efficiency of reverse hybrid jig separation.
Data availability statement
The original contributions presented in the study are included in the article/Supplementary Material, further inquiries can be directed to the corresponding author.
Author contributions
TP: conceptualization, methodology, validation, formal analysis, investigation, data curation, writing—original draft, writing editing, visualization, project administration. CM: methodology, validation, formal analysis, investigation, data curation, writing—original draft, writing—editing, visualization. PS: validation, writing—editing. OJ: methodology, supervision. KM: supervision. SJ: supervision. IP: supervision. CT: writing—editing, supervision. NH: supervision. MI: conceptualization, validation, writing—editing, supervision.
Funding
This work (Grant No. RGNS 64-009) was supported by the Office of the Permanent Secretary, Ministry of Higher Education, Science, Research, and Innovation (OPS MHESI), Thailand Science Research and Innovation (TSRI) and Chulalongkorn University.
Acknowledgments
The authors wish to thank the editor and reviewers for their valuable inputs to this paper.
Conflict of interest
The authors declare that the research was conducted in the absence of any commercial or financial relationships that could be construed as a potential conflict of interest.
Publisher’s note
All claims expressed in this article are solely those of the authors and do not necessarily represent those of their affiliated organizations, or those of the publisher, the editors and the reviewers. Any product that may be evaluated in this article, or claim that may be made by its manufacturer, is not guaranteed or endorsed by the publisher.
Supplementary material
The Supplementary Material for this article can be found online at: https://www.frontiersin.org/articles/10.3389/fchem.2022.1014441/full#supplementary-material
References
Aikawa, K., Ito, M., Segawa, T., Jeon, S., Park, I., Tabelin, C. B., et al. (2020). Depression of lead-activated sphalerite by pyrite via galvanic interactions: Implications to the selective flotation of complex sulfide ores. Min. Eng. 152, 106367. doi:10.1016/j.mineng.2020.106367
Demirbas, A. (2011). Waste management, waste resource facilities and waste conversion processes. Energy Convers. Manag. 52 (2), 1280–1287. doi:10.1016/j.enconman.2010.09.025
Filho, W. L., Voronova, V., Kloga, M., Paço, A., Minhas, A., Salvia, A. L., et al. (2021). COVID-19 and waste production in households: A trend analysis. Sci. Total Environ. 777, 145997. doi:10.1016/j.scitotenv.2021.145997
Geyer, R., Jambeck, J. R., and Law, K. L. (2017). Production, use, and fate of all plastics ever made. Sci. Adv. 3, e1700782. doi:10.1126/sciadv.1700782
Gopanna, A., Rajan, K. P., Thomas, S. P., and Chavali, M. (2019). “Polyethylene and polypropylene matrix composites for biomedical applications,” in Materials for biomedical engineering. Editors V. Grumezescu, and A. M. Grumezescu, 175–216. doi:10.1016/B978-0-12-816874-5.00006-2
Gupta, A., and Yan, D. (2016). “Gravity separation,” in Mineral processing design and operations. Editors A. Gupta, and D. Yan, 563–628. doi:10.1016/B978-0-444-63589-1.00016-2
Hori, K., Tsunekawa, M., Hiroyoshi, N., and Ito, M. (2009a). Optimum water pulsation of jig separation for crushed plastic particles. Int. J. Min. Process. 92 (3–4), 103–108. doi:10.1016/j.minpro.2009.01.001
Hori, K., Tsunekawa, M., Ueda, M., Hiroyoshi, N., Ito, M., and Okada, H. (2009b). Development of a new gravity separator for plastics —A hybrid-jig. Mater. Trans. 50 (12), 2844–2847. doi:10.2320/matertrans.M-M2009825
Hornn, V., Ito, M., Shimada, H., Tabelin, C. B., Jeon, S., Park, I., et al. (2020). Agglomeration-flotation of finely ground chalcopyrite and quartz: Effects of agitation strength during agglomeration using emulsified oil on chalcopyrite. Minerals 10, 380. doi:10.3390/min10040380
Hornn, V., Park, I., Ito, M., Shimada, H., Suto, T., Tabelin, C. B., et al. (2021). Agglomeration-flotation of finely ground chalcopyrite using surfactant-stabilized oil emulsions: Effects of co-existing minerals and ions. Min. Eng. 171, 107076. doi:10.1016/j.mineng.2021.107076
Irez, A. B., Okan, C., Kaya, R., and Cebe, E. (2022). Development of recycled disposable mask based polypropylene matrix composites: Microwave self-healing via graphene nanoplatelets. Sustain. Mater. Technol. 31, e00389. doi:10.1016/j.susmat.2022.e00389
Ito, M., Tsunekawa, M., Ishida, E., Kawai, K., Takahashi, T., Abe, N., et al. (2010). Reverse jig separation of shredded floating plastics — separation of polypropylene and high density polyethylene. Int. J. Min. Process. 97 (1–4), 96–99. doi:10.1016/j.minpro.2010.08.007
Ito, M., Saito, A., Murase, N., Phengsaart, T., Kimura, S., Tabelin, C. B., et al. (2019a). Development of suitable product recovery systems of continuous hybrid jig for plastic-plastic separation. Min. Eng. 141, 105839. doi:10.1016/j.mineng.2019.105839
Ito, M., Takeuchi, M., Saito, A., Murase, N., Phengsaart, T., Tabelin, C. B., et al. (2019b). Improvement of hybrid jig separation efficiency using wetting agents for the recycling of mixed-plastic wastes. J. Mater. Cycles Waste Manag. 21, 1376–1383. doi:10.1007/s10163-019-00890-w
Ito, M., Saito, A., Murase, N., Phengsaart, T., Kimura, S., Kitajima, N., et al. (2020). Estimation of hybrid jig separation efficiency using a modified concentration criterion based on apparent densities of plastic particles with attached bubbles. J. Mater. Cycles Waste Manag. 22, 2071–2080. doi:10.1007/s10163-020-01090-7
Ito, M., Saito, A., Takeuchi, M., Murase, N., Phengsaart, T., Tabelin, C. B., et al. (2021). Development of the reverse hybrid jig: Separation of polyethylene and cross-linked polyethylene from eco-cable wire. Min. Eng. 174, 107241. doi:10.1016/j.mineng.2021.107241
Jeon, S., Ito, M., Tabelin, C. B., Pongsumrankul, R., Tanaka, S., Kitajima, N., et al. (2019). A physical separation scheme to improve ammonium thiosulfate leaching of gold by separation of base metals in crushed mobile phones. Min. Eng. 138, 168–177. doi:10.1016/j.mineng.2019.04.025
Kuwayama, Y., Ito, M., Hiroyoshi, N., and Tsunekawa, M. (2014). Jig separation of crushed automobile shredded residue and its evaluation by float and sink analysis. J. Mater. Cycles Waste Manag. 13, 240–246. doi:10.1007/s10163-011-0008-y
Mumbach, G. D., de Sousa Cunha, R., Machado, R. A. F., and Bolzan, A. (2019). Dissolution of adhesive resins present in plastic waste to recover polyolefin by sink-float separation processes. J. Environ. Manage. 243, 453–462. doi:10.1016/j.jenvman.2019.05.021
Phengsaart, T., Ito, M., Hamaya, N., Tabelin, C. B., and Hiroyoshi, N. (2018). Improvement of jig efficiency by shape separation, and a novel method to estimate the separation efficiency of metal wires in crushed electronic wastes using bending behavior and “entanglement factor”. Min. Eng. 129, 54–62. doi:10.1016/j.mineng.2018.09.015
Phengsaart, T., Ito, M., Azuma, A., Tabelin, C. B., and Hiroyoshi, N. (2020). Jig separation of crushed plastics: The effects of particle geometry on separation efficiency. J. Mater. Cycles Waste Manag. 22, 787–800. doi:10.1007/s10163-019-00967-6
Phengsaart, T., Ito, M., Kimura, S., Azuma, A., Hori, K., Tanno, H., et al. (2021). Development of a restraining wall and screw-extractor discharge system for continuous jig separation of mixed plastics. Min. Eng. 168, 106918. doi:10.1016/j.mineng.2021.106918
Pita, F., and Castilho, A. (2016). Influence of shape and size of the particles on jigging separation of plastics mixture. Waste Manag. 48, 89–94. doi:10.1016/j.wasman.2015.10.034
Prata, J. C., Silva, A. L. P., Walker, T. R., Duarte, A. C., and Rocha-Santos, T. (2020). COVID-19 pandemic repercussions on the use and management of plastics. Environ. Sci. Technol. 54 (13), 7760–7765. doi:10.1021/acs.est.0c02178
Rabnawaz, M., Wyman, I., Auras, R., and Chenga, S. (2017). A roadmap towards green packaging: The current status and future outlook for polyesters in the packaging industry. Green Chem. 1920, 4737–4753. doi:10.1039/C7GC02521A
Tabelin, C. B., Park, I., Phengsaart, T., Jeon, S., Villacorte-Tabelin, M., Alonzo, D., et al. (2021). Copper and critical metals production from porphyry ores and E-wastes: A review of resource availability, processing/recycling challenges, socio-environmental aspects, and sustainability issues. Resour. Conserv. Recycl. 170, 105610. doi:10.1016/j.resconrec.2021.105610
Tsunekawa, M., Naoi, B., Ogawa, S., Hori, K., Hiroyoshi, N., Ito, M., et al. (2005). Jig separation of plastics from scrapped copy machines. Int. J. Min. Process. 76 (1-2), 67–74. doi:10.1016/j.minpro.2004.12.001
Tsunekawa, M., Kobayashi, R., Hori, K., Okada, H., Abe, N., Hiroyoshi, N., et al. (2012). Newly developed discharge device for jig separation of plastics to recover higher grade bottom layer product. Int. J. Min. Process. 114-117, 27–29. doi:10.1016/j.minpro.2012.09.003
United Nations (2015). Transforming our world: the 2030 agenda for sustainable development, Available at: https://sustainabledevelopment.un.org/post2015/summit (Accessed July 28, 2022).
Keywords: recycling, plastic, polyolefin, gravity separation, bubble attachment
Citation: Phengsaart T, Manositchaikul C, Srichonphaisarn P, Juntarasakul O, Maneeintr K, Jeon S, Park I, Tabelin CB, Hiroyoshi N and Ito M (2022) Reverse hybrid jig separation efficiency estimation of floating plastics using apparent specific gravity and concentration criterion. Front. Chem. 10:1014441. doi: 10.3389/fchem.2022.1014441
Received: 08 August 2022; Accepted: 09 September 2022;
Published: 28 September 2022.
Edited by:
Mohd Hazwan Hussin, Universiti Sains Malaysia (USM), MalaysiaCopyright © 2022 Phengsaart, Manositchaikul, Srichonphaisarn, Juntarasakul, Maneeintr, Jeon, Park, Tabelin, Hiroyoshi and Ito. This is an open-access article distributed under the terms of the Creative Commons Attribution License (CC BY). The use, distribution or reproduction in other forums is permitted, provided the original author(s) and the copyright owner(s) are credited and that the original publication in this journal is cited, in accordance with accepted academic practice. No use, distribution or reproduction is permitted which does not comply with these terms.
*Correspondence: Theerayut Phengsaart, dGhlZXJheXV0LnBAY2h1bGEuYWMudGg=