- 1Key Laboratory of Fluid and Power Machinery, Ministry of Education, School of Material Science and Engineering, Xihua University, Chengdu, China
- 2Materials Research and Education Center, Auburn University, Auburn, AL, United States
- 3North Sichuan Nitrocellulose Co, Ltd., Luzhou, China
Corrosion of metal products can seriously affect their reliability. The application of coatings is the most widely used method of corrosion protection due to the desire for easy application and low cost. Most of the present corrosion-resistant coatings are solvent coatings. Due to the high content of volatile organic compounds, the use of solvent coatings is restricted. Currently, the corrosion resistance of waterborne coatings is much lower than that of solvent coatings, so research and development of waterborne corrosion-resistant coatings are necessary and valuable. A corrosion-resistant waterborne polyurethane modified epoxy (WPUME) emulsion was prepared and characterized by Fourier transform infrared (FTIR) spectra, transmission electron microscopy, and thermal gravimetric analysis. The particle size, dispersion, and solid content of the emulsion were tested by laser-scattering equipment and a weighing method. Coatings were prepared based on the emulsion, and the properties (i.e., water absorption rate, salt spray resistance, and flexibility) of the coatings were tested by the standard method, respectively. Results show that the synthesis reaction accords well with the molecule design, and the average diameter of the particles in the emulsion is 100 nm approximately. The cured coating, which is coated on tinplate sheets, has good flexibility and can withstand the salt spray test for more than 60 days (i.e., 1,440 h). The emulsion has many potential practical applications in the protection of metal materials.
Introduction
Corrosion is a process by which materials, especially metals (i.e., carbon steel, galvanized steel, and, cast iron), are worn away by electrochemical and chemical actions. Metals have anodic and cathodic areas, and corrosion results from the presence of oxygen, water, and the conducting medium. The impact of metal corrosion on operational safety and product reliability may lead to the loss of valuable products, major accidents, personnel deaths, and plant shutdowns, so the consequences of the corrosion of metal structures are vast. The application of coatings is the most widely used method of corrosion protection due to the desired advantage of slowing down water, ions, and other corrosive media penetrating through the organic film, along with the ease of application.
Most of the present corrosion-resistant coatings are solvent coatings. In the last decade, waterborne coatings have attracted attention for metal protection because the environmental standard requirements legislate the limit to the removal or control of volatile organic compounds to the lowest possible levels (Wang et al., 2013; Abdolahi et al., 2014; Yilmaz et al., 2014; Liu et al., 2016; Zhang et al., 2017).
However, the anticorrosion properties of waterborne coatings are far inferior to solvent coatings because the hydrophilic groups are often retained in the coating during the film formation process, decreasing the shield's ability for vapor diffusion and moisture resistance (Ai et al., 2014; Wang Z. et al., 2014; Rahman et al., 2015). Thus, the addition of corrosion inhibitors or fillers is necessary to improve the corrosion resistance of the waterborne coatings, and micro/nano inorganic particles (i.e., inorganic additives) are often applied as corrosion inhibitors or fillers (Hao et al., 2012; Ma et al., 2012b; Cheek et al., 2013; Liang et al., 2013; Suleiman et al., 2014; Das et al., 2017).
Many inorganic particles that include graphene (Mittal, 2014; Kausar et al., 2016; Qiu et al., 2017; Shahabadi et al., 2017; Zhu et al., 2017), Ni-Fe(Ti,W)C nanocomposite (Khorsand et al., 2018), nano-ZnO (Dhoke and Khanna, 2009; Rasool et al., 2018), SiO2 (Khademian et al., 2015; Wang N. et al., 2016), TiO2 (Montesinos et al., 2015; Wang N. et al., 2016), Al (Deflorian et al., 2011), Al2O3 (Chen et al., 2014), Ag (Rahman, 2017), micaceous iron oxide (Kakaei et al., 2013), and carbon nanotube (Zhuo et al., 2016) have been investigated by researchers, and the results show that the corrosion resistance of composite coatings has improved significantly.
A composite coating is composed of organic polymers and inorganic additives. The polymers act as a matrix and hold the inorganic additives. Water-based polymers are used due to their popularity in coating formulations, and these that include acrylic (Singh et al., 2017), polyurethane (PU) (Alagi et al., 2017), alkyd (Pathan and Ahmad, 2013), epoxy (Cao et al., 2015), polyester (Kumar et al., 2017), and their combinations because of their complementary performance.
Waterborne organic–inorganic hybrid coatings will be the development trend in the future (Boubakri et al., 2010; Huang et al., 2012). However, due to the addition of inorganic additives, certain properties (i.e., transparency, etc.) of the composite coatings are reduced obviously, and the applications of the coatings are limited in some special fields that require high transparency and showing the natural colors of the substrate covered by the coatings. Therefore, research and development of corrosion-resistant coating, without inorganic additives, are essential.
Among various waterborne polymers used in coatings, polyurethane is known for its excellent durability and resistance mainly against chemical and thermal degradation, ultraviolet (UV) radiation, scratch, and hydrophobicity (Boubakri et al., 2010; Huang et al., 2012; Ma et al., 2013; Mohammad and Han, 2015; Kausar, 2016).
Epoxy resins, owing to their excellent chemical properties, corrosion resistance, outstanding adhesion properties, low shrinkage, and low price, are widely used in various coating applications. In addition, the properties of cured epoxy coating depend on the curing agent and curing process, and these properties can be adjusted widely (Muhammad et al., 2014; Pradhan et al., 2016; Kumar et al., 2017). However, due to the poor outdoor durability of epoxy resins, acrylics, and polyurethane hybrids are finding increasing use.
When exposed to aggressive media, metal or alloy stability depends upon the protective properties of the surface coatings formed. Chemical composition, conductivity, adherence, solubility, hygroscopicity, and morphological characteristics determine the film's capacity to work as a corrosion barrier (Stratmant et al., 1983). If the polyurethane and epoxy segments are synthesized in a polymer molecule, the properties (i.e., chemical composition, adherence, hygroscopicity, and morphological characteristics) of the resins can be regulated widely. Therefore, the corrosion resistance of the polymer can be improved.
In this investigation, a waterborne polyurethane modified epoxy (WPUME) emulsion was prepared and characterized, and the emulsion showed good corrosion resistance properties.
Materials and Methods
Materials
Epoxy resin (E-44) was bought from Lanxing Advanced Material Co. (Wuxi, China). Isophorone diisocyanate (IPDI), dimethylolbutyric acid (DMBA), triethylamine (TEA), acetone, butanone, and polyethylene glycol 2000 (PEG-2000) were purchased from Kelong Co. (Chengdu, China). The catalyst with organotin (i.e., dibutyltin dilaurate) as the main active ingredient, named DY-20, was a product of Deyin Chemical Co. (Shanghai, China). The waterborne curing agent with modified primary amine as the main active ingredient, named GCA 02, was bought from BASF Co. The active hydrogen equivalent of GC 02 is 320. All the materials were analytical grade, besides epoxy resin, the curing agent, and DY-20. IPDI, DMBA, and PEG-2000 were dried in a vacuum oven (100°C) for at least 5 h before the experiment, and the other materials were applied as received without further treatments.
Preparation of the Polyurethane Modified Epoxy Emulsion
Polyurethane modified epoxy emulsion was synthesized by a reaction using IPDI, PEG, DMBA, epoxy resin, and TEA. In a four-necked round-bottom flask, 5 g DMBA was dissolved in 10 g acetone, and the flask was equipped with a thermometer, a stirrer, an inlet of dry nitrogen, a condenser, and a heat jacket. Then, 15 g IPDI and 5 g acetone were added slowly under moderate stirring (300 rpm), and the mixture was allowed to react at 70°C until the theoretical NCO content was reached. The change of NCO content during the reaction was determined using a standard dibutylamine back-titration method (David and Staley, 1969). As the theoretical NCO value was obtained, the reactant was heated to 90°C, and the solution (i.e., 41.8 g epoxy resin, 37.1 g PEG-2000, 0.3 g DY-20, and 40 g acetone) was added and stirred at 300 rpm for 2.5 h while maintaining the temperature at 90°C. Then the reactant was cooled to 40°C, and 3.5 g TEA was added slowly and stirred for 30 min while maintaining the temperature at 40°C. After the reaction, 120 g deionized water was added into the flask under fast stirring (800 rpm) at room temperature for 15 min. Finally, the acetone was removed under vacuum to obtain the WPUME resin emulsion. The WPUME molecule contained hydrophilic groups (i.e., the carboxylate group and the ether bond) and an epoxy group, so it could be self-emulsified (i.e., depending on carboxyl group and ether bond) in water to form a stable emulsion. The emulsion was cured to a stable film depending on the reaction between the epoxy group and amino group in GC 02. The scheme of the preparation process for WPUME is shown in Scheme 1, and the main functional groups are encircled.
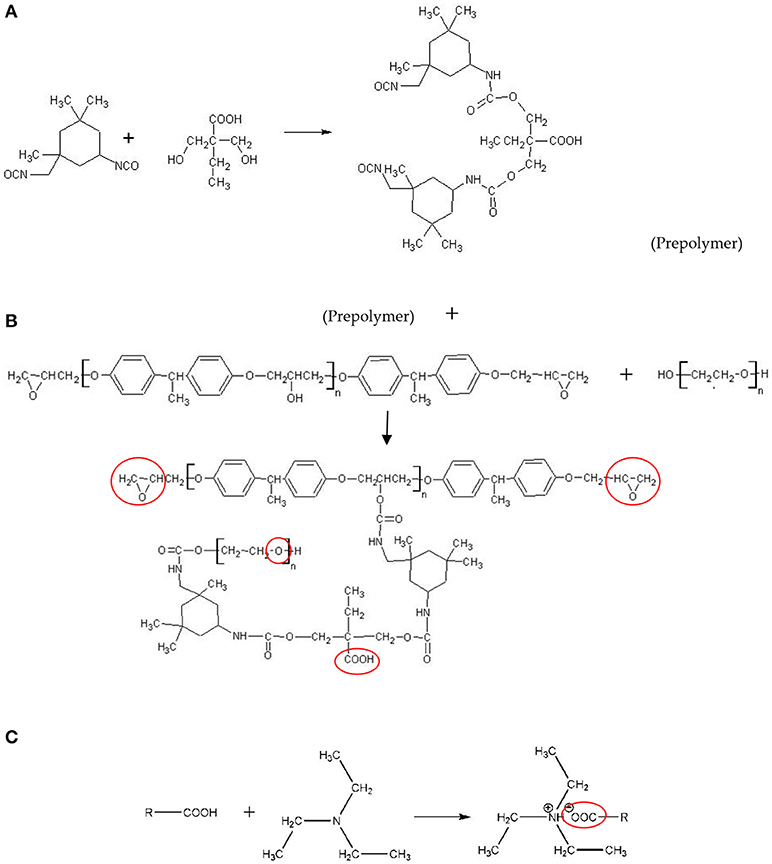
Scheme 1. Preparation process of the WPUME molecule. (A) Reaction between IPDI and DMBA. (B) Reaction among prepolymer, epoxy resin and PEG-2000. (C) Reaction between carboxylic acid and TEA.
Preparation of Cured and Pristine WPUME Film
About 100 g WPUME emulsion was well mixed with 7.5 g of curing agent (i.e., GCA 02), and the mixture was cast on several 8 × 15 cm tinplate sheets. The curing process was implemented at 120°C for 15 min followed by 140°C for 15 min to form the film. Another surface of the tinplate sheet was cast to form an additional cast film. A spiral micrometer measured the obtained film thickness of 15–25 μm. The curing response occurred between the epoxy group in the WPUME molecule and the amine group in the GC 02, and the response is shown in Scheme 2.
As the pristine film was prepared, no curing agent was added to the emulsion, and all the other procedures were the same as in the preparation method of the cured film.
Water Resistance
The water resistance test was characterized by the water absorption rate and determined by the weighing method as follows (Ma et al., 2012a). The cured WPUME film samples were cut into 3 cm × 3 cm pieces and dried in a vacuum oven at 60°C for 24 h to determine their dry weight (Wd). Then, the film was immersed in distilled water for 72 h, followed by wiping off the surface water with a piece of filter paper to determine its weight (Wt). The water absorption rate (W%) was then calculated by Formula (1).
Stability of the Emulsion
Storage Stability
The emulsion sample was filled into a covered glass bottle of 50 ml, and the sample was placed in an oven for 20 h at 50 ± 2°C. Then, the bottle was taken out of the oven and placed at room temperature (i.e., 23 ± 2°C) for 3 h. If the emulsion was not stratified, the stability was good.
Freezing and Thawing Stability
The emulsion sample froze at −10°C and was placed at room temperature (i.e., 23 ± 2°C) for some time until the frozen emulsion was thawed. If the sample was not stratified, the process of the freezing–thawing cycles continued until five cycles were carried out to complete the freezing and thawing stability test.
Centrifugation Stability
The emulsion sample was centrifuged at 5,000 rpm for 5 min in a centrifuge (TGK-16, Xiangyi Co., China). If the emulsion was not stratified, the stability was good.
Characterization
FTIR
Fourier transform infrared (FTIR) spectra of the pristine and cured film sample were recorded respectively in the range of 400–4,000 cm−1 using an FTIR spectrometer (VERTEX 70, BRUKER Co., Germany) on a KBr disk at a resolution of 4 cm−1 for 32 scans.
Solid Content
An emulsion sample of 2 g was weighed precisely to get the weight of W1, and then, the emulsion was dried to a constant weight to get the weight of W2, and the solid content (sc%) was calculated by Formula (2).
Particle Size and the Dispersion of the Emulsion
Laser-scattering equipment (Autosizer, Melvern Co., UK) was used to determine the particle size and dispersion. The sample was first diluted in distilled water to 0.5%, followed by an ultrasonic wave treatment to homogenize the emulsion.
Microscopic Observation
A microscopic observation was performed on a transmission electron microscope (TEM, JEM-200CX, Japan Electronics Co., Japan) operating at 120 kV. In order to view the morphology, the pristine film was floated off from the mica substrates into distilled water and collected on the TEM grids.
Thermal Gravimetric Analysis
Thermal gravimetric analysis (TGA) was carried out on a thermal analyzer (STA 449 F3, NETZSCH Co., Germany). The TGA instrument was calibrated with calcium oxalate from 30 to 500°C at a heating rate of 10°C/min in a static nitrogen atmosphere.
Electrochemical Measurement
Electrochemical measurements of the cured and pristine WPUME films on the tinplates (the plating was polished by sandpaper before the film was coated) were carried out using a ParStat 2273 potentiostat (Ametec, Berwyn, PA, USA). A classical three-electrode system was applied. The samples, a saturated calomel electrode (SCE), and a platinum plate, were used as a working electrode, reference electrode, and auxiliary electrode, respectively. The polarization curves were obtained on an exposed area of 1 cm2 at a constant voltage scan rate of 0.5 mV s−1 after an initial delay of 300 s. An immersion test was performed according to GB 10124-88 of China (GB 10124-88, 2008). The electrochemical measurements were conducted in NaCl solution of 3.5%.
Salt Spray Test
The salt spray test was performed in a YW/R-150 salt mist corrosion testing box (Tianjin, China) on tinplate sheets with a cured WPUME sample to simulate environment corrosion according to ASTM B117-09 (natural salt spray test).
Flexibility Test
The WPUME emulsion was cured on the tinplate, and the flexibility of the samples was tested according to ASTM 4145-2010 (coating flexibility).
Results and Discussion
Chemical Characterization
An FTIR spectroscopy study was performed for a structural comparison between the cured and pristine films that were prepared by the WPUME emulsion (Figure 1). In general, there was no major structural difference between the spectra of the cured and pristine film.
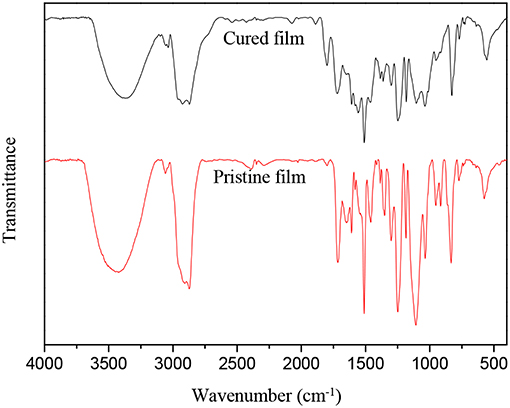
Figure 1. Fourier transform infrared spectra of pristine and cured film prepared by the WPUME emulsion.
The FTIR spectrum for the pristine film showed an absorption band at 3,406 cm−1 and absorption peaks at 1,718 and 1,250 cm−1, corresponding to the characteristic absorption of N-H, C = O, and C-O in -NH-COO-, respectively. No absorption peak was found at 2,270 cm−1 (i.e., absorption peak of -NCO), which means the -NCO almost completely reacts to the -OH in the reactant. An analysis of these spectra reveals absorption peaks at 1,400 and 1,107 cm−1, which can be assigned as the characteristic absorption of -OH in the primary alcohol and ether bond, respectively. It means that the PEG is induced in the polymeric chain segment, and a certain amount of primary alcohol remained. The results of the characteristic peak at 955 cm−1 are from the absorption of -COOH, which means the DMBA reacts with the other materials, and the -COOH is induced in the polymeric chain segment. Hydrophilic groups (i.e., ether bond and carboxyl) in the WPUME molecule endues good stability to the emulsion. The characteristic absorption peaks of the epoxy group at 913 and 830 cm−1 are easily found in the pristine film sample, which means the epoxy group is retained and can result in the curing reaction later. These FTIR spectra show that the synthesis reaction among DMBA, IPDI, PEG, and epoxy resin to synthesize WPUME may occur corresponding to Scheme 1.
With regard to the spectrum of the cured film sample in Figure 1, the absorption peak of the epoxy group, primary hydroxyl, and -COOH at 913, 1,400, and 955 cm−1, respectively, disappears, and a new absorption bank of a tertiary amino group at 1,125 cm−1 is found, which means the curing agent (i.e., modified amine) may react with the oxygen group, and the epoxy group may react with the active amine, so the amino group can be formed. The disappearance of the epoxy group, primary hydroxyl, and -COOH implies that the curing reaction is carried out thoroughly, and the cured film may have good properties of corrosion resistance, low water absorption rate, and good heat resistance; therefore, the properties correspond well with the results of the later investigation.
Solid Content
The solid content of the emulsion prepared with the typical method was 44.5%, which corresponds well with the theoretical value (i.e., 46%). The difference may be attributed to the volatilization of the materials in the reaction.
Water Resistance
The transparent samples of pristine and cured films were all immersed in distilled water to determine their water resistance performance. The transparent pristine film of WPUME turned white and then opaque after it was immersed into distilled water for about 30 min at room temperature, and it gradually split into small pieces for about 2 h. However, the cured WPUME film had no apparent changes even after it was immersed into distilled water for 72 h at room temperature. The average water absorption rate was 2.8%, which was calculated according to Formula (1). The low water absorption rate illustrates that the cured film is not sensitive to water, and it has good water resistance.
Particle Size and the Dispersion of the Emulsion
Figure 2 shows the particle size and the dispersion of the WPUME. It can be seen that the average particle size of the emulsion is 102.82 nm, and it accords well with the TEM. The small particle size of the emulsion leads to the good stability of the emulsion.
Stability
The WPUME emulsion shows good stabilities (i.e., storage stability, freezing and thawing stability, centrifugation stability). The stabilities can be attributed to the introduction of the hydrophilic groups in the WPUME polymeric chain and small particle size of the emulsion.
Microscopic Observation
The typical TEM images of the WPUME emulsion particles are shown in Figure 3. It is found that the particles are regularly spherical with a diameter of 100–200 nm, and it has some regular boundaries. The morphology of particles is an approximate core-shell structure, in which hydrophilic groups (i.e., carboxyl group and ether bond) constitute the shell and a hydrophobic component constitutes the core. Encapsulated by a hydrophilic group, the original hydrophobic segment in the polymeric chain is dispersed in water. The core-shell structure appears to be more visible when the particles are amplified to bigger sizes, as shown in Figure 3b.
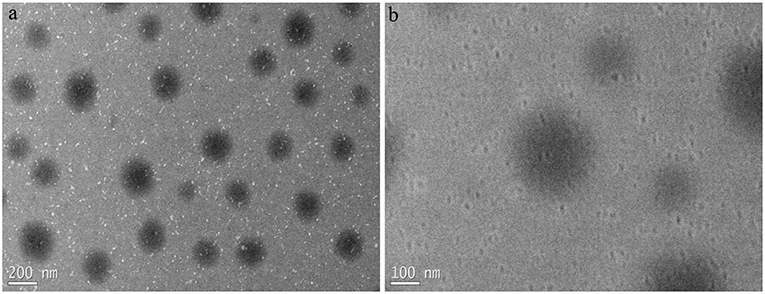
Figure 3. TEM images of the emulsion samples with different magnification (i.e., 2500× in a and 5000× in b).
Thermal Gravimetric Analysis
TGA results of the pristine and cured WPUME film samples are shown in Figure 4. The temperatures correspond to a 5, 10, 20, 50, and 80% weight loss, which are listed in Table 1.
The main weight loss of the samples is caused by the thermal decomposition of the polymer molecule segment. By the addition of the curing agent, the cured WPUME film sample displays better thermal resistance than the pristine one. For typical samples, the temperature corresponding to a 5% weight loss for the pristine and the cured film is 270 and 335°C, respectively, which is 65°C higher for the cured film sample than the pristine one. The curing and cross-linking between polymeric chains limit the free-chain movement of polymers (Charles and Carraher, 2007), so the cured WPUME film shows a better thermal resistance. The better thermal resistance indicates that polymeric chains of the WPUME sample are cross-linked and cured effectively. The cured WPUME film can offer relatively greater corrosion resistance properties, which is verified in the following section.
Electrochemical Measurement
The polarization curves of cured and pristine films on the polished tinplates are shown in Figure 5. It can be seen in Figure 5 that the hydrogen evolution rate on the cathodic side and metallic dissolution rate on the anodic side both decrease significantly as the cured film is coated on the substrate compared with the pristine film. In addition, the anodic sides of the two curves are also different. The anodic side of the sample with pristine film on it is much smoother than that of the cured one. In the curve of the cured film sample, the corrosion current density (J) increases much more slowly with increasing anodic potential in the passive tendency region. The corrosion current density of the sample coated with a cured film is 0.002551 μA·cm−2, which is much lower than that of the sample coated with a pristine film (1.905 μA cm−2). The result indicates that the tinplate with cured film on it can dramatically improve the corrosion resistance of the substrate compared to the pristine one.
Salt Spray Test
Figure 6 shows photographs of the WPUME sample cured on the tinplate sheets after different exposure times (0, 30, 60, and 65 days) in a neutral salt spray chamber, respectively.
No corrosion is observed before the salt spray tests. The images in Figure 6 after 30, 60, and 65 days of exposure reveal the presence of corrosion activity. Yellow rust and coating blistering are observed near the scratches of the samples, which means a corrosion attack. However, the image of the sample after 30 days of exposure does not show blistering, and there is no evidence of an apparent localized corrosion attack. The coating blisters with diameters of about 1 mm and larger than 1 mm are observed near the scratches of the sample after 60 and 65 days of exposure, respectively, which indicates the good anticorrosion performance of the WPUME coating prepared in the investigation. However, some previous waterborne coatings can endure a neutral salt spray test about 480 h (Wang et al., 2014), 720 h (Li et al., 2018), 600 h (Wang N. et al., 2016), and 288 h (Zhang et al., 2019), etc. before localized corrosion appeared, which are all much shorter than the samples prepared in this investigation.
Flexibility Test
The flexibility of the prepared coating is bent to the diameter of 2 mm, which is the highest flexibility in ASTM 4145-2010.
Conclusions
A WPUME emulsion was successfully prepared with the reaction of epoxy resin (E-44), IPDI, DMBA, organotin catalyst, and PEG-2000, and the curing agent to form the corrosion resistance coating could cure the emulsion. The coating has good flexibility (i.e., can be bent at a diameter of 2 mm) and corrosion resistance properties (i.e., can endure the salt spray corrosion test for about 60 days on tinplate sheets). The coating has many potential applications in some special fields that require high flexibility and corrosion resistance abilities.
Data Availability
The raw data supporting the conclusions of this manuscript will be made available by the authors, without undue reservation, to any qualified researcher.
Author Contributions
All authors listed have made a substantial, direct and intellectual contribution to the work, and approved it for publication.
Funding
This work was financially supported by the Sichuan Science and Technology Program (No. 2019JDTD0024 and No. 2019ZHCG0048), the military and civilian integration project of Sichuan province (No. zyf-2018-089), the Yibin Science and Technology Program (No. 2018YG05 and No. 2017YG02), the Chunhui Project from the Education Ministry of China (No. Z2017066), the Scientific Research Fund of the Sichuan Education Department, China (No. 18ZA0445), and the Xihua Scholars program of Xihua University.
Conflict of Interest Statement
JM was employed by the company North Sichuan Nitrocellulose Co., Ltd.
The remaining authors declare that the research was conducted in the absence of any commercial or financial relationships that could be construed as a potential conflict of interest.
References
Abdolahi, E., Ibrahim, Z., and Hashim, S. (2014). Application of environmentally-friendly coatings toward inhibiting the microbially influenced corrosion (MIC) of steel: a review. Polym. Rev. 54, 702–745. doi: 10.1080/15583724.2014.946188
Ai, L., Liu, Y., Zhang, X., Ouyang, X., and Ge, Z. (2014). A facile and template-free method for preparation of polythiophene microspheres and their dispersion for waterborne corrosion protection coatings. Synth. Met. 191, 41–46. doi: 10.1016/j.synthmet.2014.02.004
Alagi, P., Ghorpade, R., Choi, Y., Patil, U., Kim, I., Baik, J., et al. (2017). Carbon dioxide–based polyols as sustainable feedstock of thermoplastic polyurethane for corrosion-resistant metal coating. ACS Sustain. Chem. Eng. 5, 3871–3881. doi: 10.1021/acssuschemeng.6b03046
Boubakri, A., Guermazi, N., Elleuch, K., and Ayedi, H. (2010). Study of UV-aging of thermoplastic polyurethane material. Mat. Sci. Eng. A 527, 1649–1654. doi: 10.1016/j.msea.2010.01.014
Cao, M., Wang, H., Cai, R., Ge, Q., Jiang, S., Zhai, L., et al. (2015). Preparation and properties of epoxy-modified tung oil waterborne insulation varnish. J. Appl. Polym. Sci. 132:42755. doi: 10.1002/app.42755
Charles, E., and Carraher, J. (2007). Seymour/Carraher's Polymer Chemistry. 7th Edn. New York, NY: Marcel Dekker Press.
Cheek, J., Steele, A., Bayer, I., and Loth, E. (2013). Underwater saturation resistance and electrolytic functionality for super hydrophobic nanocomposites. Colloid Polym. Sci. 291, 2013–2016. doi: 10.1007/s00396-013-2933-x
Chen, X., Yuan, J., Huang, J., Ren, K., Liu, Y., Lu, S., et al. (2014). Large-scale fabrication of superhydrophobic polyurethane/nano-Al2O3 coatings by suspension flame spraying for anti-corrosion applications. Appl. Surf. Sci. 311, 864–869. doi: 10.1016/j.apsusc.2014.05.186
Das, S., Pandey, P., Mohanty, S., and Nayak, S. (2017). Insight on castor oil based polyurethane and nanocomposites: recent trends and development. Polym. Plast. Technol. 56, 1556–1585. doi: 10.1080/03602559.2017.1280685
David, D. J., and Staley, H. B. (1969). “High Polymer Series,” in Analytical Chemistry of Polyurethanes, Vol. 16 (New York, NY: Wiley Interscience Press, 45–46.
Deflorian, F., Rossi, S., and Fedel, M. (2011). Aluminium components for marine applications protected against corrosion by organic coating cycles with low environmental impact. Corros. Eng. Sci. Technol. 46, 237–244. doi: 10.1179/147842209X12489567719545
Dhoke, S., and Khanna, A. (2009). Study on electrochemical behavior of nano-ZnO modified alkyd-based waterborne coatings. J. Appl. Polym. Sci. 113, 2232–2237. doi: 10.1002/app.30276
GB 10124-88 (2008). Standard Practice for Laboratory Immersion Corrosion Testing of Metals. Beijing: Standardization Administration of the People's Republic of China.
Hao, Y., Liu, F., and Han, E. (2012). Mechanical and barrier properties of epoxy/ultra-short glass fibers composite coatings. J. Mater. Sci. Technol. 28, 1077–1084. doi: 10.1016/S1005-0302(12)60176-5
Huang, T., Wang, Y., Hsieh, K., and Lin, J. (2012). Molecular-level dispersion of phosphazene–clay hybrids in polyurethane and synergistic influences on thermal and UV resistance. Polymer 53, 4060–4068. doi: 10.1016/j.polymer.2012.07.049
Kakaei, M., Danaee, I., and Zaarei, D. (2013). Investigation of corrosion protection afforded by inorganic anticorrosive coatings comprising micaceous iron oxide and zinc dust. Corros. Eng. Sci. Technol. 48, 194–198. doi: 10.1179/1743278212Y.0000000060
Kausar, A. (2016). Waterborne polyurethane-coated polyamide/fullerene composite films: mechanical, thermal, and flammability properties. Int. J. Polym. Anal. Charact. 21, 275–285. doi: 10.1080/1023666X.2016.1147729
Kausar, A., Rafique, I., Anwar, Z., and Muhammad, B. (2016). Perspectives of epoxy/graphene oxide composite: significant features and technical applications. Polym. Plast. Technol. 55, 704–722. doi: 10.1080/03602559.2015.1098700
Khademian, M., Eisazadeh, H., Shakeri, A., and Ghorbani, M. (2015). Effect of HPC-PANI/SiO2 emulsion nanocomposite in poly (vinyl acetate) for corrosion-resistant coatings. Polym. Plast. Technol. 54, 1051–1056. doi: 10.1080/03602559.2014.986801
Khorsand, S., Karbasi, M., Sayyedan, F., Eshaghian, M., and Razavi, M. (2018). Development of electro-co-deposited Ni-Fe (Ti,W) C nanocomposite coatings. Surf. Eng. 34, 433–439. doi: 10.1080/02670844.2017.1370880
Kumar, S., Krishnan, S., Samal, S., Mohanty, S., and Nayak, S. (2017). Itaconic acid used as a versatile building block for the synthesis of renewable resource–based resins and polyesters for future prospective: a review. Polym. Int. 66, 1349–1363. doi: 10.1002/pi.5399
Li, J., Li, X., Zhu, K., Wang, H., and Fei, G. (2018). Reinforcement of phosphorylated graphene oxide on the anticorrosive properties of waterborne acrylate–epoxy resin coatings. J. Macromol. Sci. A 55, 649–657. doi: 10.1080/10601325.2018.1504611
Liang, Y., Liu, F., Nie, M., Zhao, S., Lin, J., and Han, E. (2013). Influence of nano-Al concentrates on the corrosion resistance of epoxy coatings. J. Mater. Sci. Technol. 29, 353–358. doi: 10.1016/j.jmst.2013.01.014
Liu, S., Gu, L., Zhao, H., Chen, J., and Yu, H. (2016). Corrosion resistance of graphene-reinforced waterborne epoxy coatings. J. Mater. Sci. Technol. 32, 425–431. doi: 10.1016/j.jmst.2015.12.017
Ma, C., Xu, L., Xu, W., and Zhang, G. (2013). Degradable polyurethane for marine anti-biofouling. J. Mater. Chem. B 1, 3099–3106. doi: 10.1039/c3tb20454e
Ma, S., Song, G., and Feng, N. (2012a). Preparation and characterization of self-emulsified waterborne nitrocellulose. Carbohydr. Polym. 89, 36–40. doi: 10.1016/j.carbpol.2012.02.029
Ma, S., Song, G., Feng, N., and Zhao, P. (2012b). Corrosion protection of mild steel with nanofibrous polyaniline-based coatings. J. Appl. Polym. Sci. 125, 1601–1605. doi: 10.1002/app.35643
Mittal, V. (2014). Functional polymer nanocomposites with graphene: a review. Macromol. Mater. Eng. 299, 906–931. doi: 10.1002/mame.201300394
Mohammad, M., and Han, D. (2015). Waterborne polyurethane/oil fly ash composite: a new environmentally friendly coating material. J. Adhes. Sci. Technol. 29, 2709–2718. doi: 10.1080/01694243.2015.1087252
Montesinos, R., Reynoso, R., Álvarez, F., and Vázquez, C. (2015). Assessment of novel water-borne coatings obtained from composite latex particles and reinforced with TiO2 nanotubes. Polym. Plast. Technol. 54, 730–740. doi: 10.1080/03602559.2014.974273
Muhammad, R., Mohammad, D., and Saidatul, S. (2014). Development of vegetable-oil–based polymers. J. Appl. Polym. Sci. 131, 1–13. doi: 10.1002/app.40787
Pathan, S., and Ahmad, S. (2013). s-Triazine ring–modified waterborne alkyd: synthesis, characterization, antibacterial, and electrochemical corrosion studies. ACS Sustain. Chem. Eng. 1, 1246–1257. doi: 10.1021/sc4001077
Pradhan, S., Pandey, P., Mohanty, S., and Nayak, S. (2016). Insight on the chemistry of epoxy and its curing for coating applications: a detailed investigation and future perspectives. Polym. Plast. Technol. 55, 862–877. doi: 10.1080/03602559.2015.1103269
Qiu, S., Li, W., Zheng, W., Zhao, H., and Wang, L. (2017). Synergistic effect of polypyrrole-intercalated graphene for enhanced corrosion protection of aqueous coating in 3.5% NaCl solution. ACS Appl. Mater. Interfaces 9, 34294–34304. doi: 10.1021/acsami.7b08325
Rahman, M. (2017). Improvements of antimicrobial and barrier properties of waterborne polyurethane containing hydroxyapatite–silver nanoparticles. J. Adhes. Sci. Technol. 31, 613–626. doi: 10.1080/01694243.2016.1228744
Rahman, O., Kashif, M., and Ahmad, S. (2015). Nanoferrite dispersed waterborne epoxy–acrylate: anticorrosive nanocomposite coatings. Prog. Org. Coat. 80, 77–86. doi: 10.1016/j.porgcoat.2014.11.023
Rasool, K., Nasrallah, G., Younes, N., Pandey, R., Rasheed, P., and Mahmoud, K. (2018). “Green” ZnO-interlinked chitosan nanoparticles for the efficient inhibition of sulfate-reducing bacteria in inject seawater. ACS Sustain. Chem. Eng. 6, 3896–3906. doi: 10.1021/acssuschemeng.7b04248
Shahabadi, S., Kong, J., and Lu, X. (2017). Aqueous-only, green route to self-healable, UV-resistant, and electrically conductive polyurethane/graphene/lignin nanocomposite coatings. ACS Sustain. Chem. Eng. 5, 3148–3157. doi: 10.1021/acssuschemeng.6b02941
Singh, A., Alam, S., and Rani, N. (2017). Preparation and characterization of acrylic–polyurethane–based waterborne anticorrosion coating on galvanised steel. Trans. Inst. Met. Finish. 95, 165–172. doi: 10.1080/00202967.2017.1237759
Stratmant, M., Bohnenkamp, K., and Engell, H. J. (1983). An electrochemical study of phase-transitions in rust layers. Corros. Sci. 23, 969–985. doi: 10.1016/0010-938X(83)90024-0
Suleiman, R., Khaled, M., Wang, H., Smith, T., Gittens, J., Akid, R., et al. (2014). Comparison of selected inhibitor doped sol–gel coating systems for protection of mild steel. Corros. Eng. Sci. Technol. 49, 189–196. doi: 10.1179/1743278213Y.0000000113
Wang, N., Fu, W., Sun, M., Zhang, J., and Fang, Q. (2016). Effect of different structured TiO2 particle on anticorrosion properties of waterborne epoxy coatings. Corros. Eng. Sci. Technol. 51, 365–372. doi: 10.1080/1478422X.2015.1117267
Wang, N., Wu, Y., Cheng, K., and Zhang, J. (2014). Investigation on anticorrosion performance of polyaniline–mesoporous MC-41 composites in new water-based epoxy coating. Mater. Corros. 65, 968–976. doi: 10.1002/maco.201307458
Wang, X., Wang, J., Li, Q., and Li, S. (2013). Synthesis and characterization of waterborne epoxy–acrylic corrosion-resistant coatings. J. Macromol. Sci. B 52, 751–761. doi: 10.1080/00222348.2012.730351
Wang, Z., Han, E., Liu, F., Qian, Z., and Zhu, L. (2014). Waterborne epoxy nanocoatings modified by nanoemulsions and nanoparticles. J. Mater. Sci. Technol. 30, 1036–1042. doi: 10.1016/j.jmst.2014.01.004
Yilmaz, O., Karesoja, M., Adiguzel, C., Zengin, G., and Tenhu, H. (2014). Nanocomposites based on crosslinked polyacrylic latex/silver nanoparticles for waterborne high-performance antibacterial coatings. J. Appl. Polym. Sci. A 52, 1435–1447. doi: 10.1002/pola.27130
Zhang, J., Li, Y., Hu, C., Huang, W., and Su, L. (2019). Anti-corrosive properties of waterborne polyurethane/poly (o-toluidine)–ZnO coatings in NaCl solution. J. Adhes. Sci. Technol. 33, 1047–1065. doi: 10.1080/01694243.2018.1529881
Zhang, K., Huang, C., Fang, Q., and Lu, Q. (2017). Synthesis of a self-emulsifiable waterborne epoxy curing agent based on glycidyl tertiary carboxylic ester and its cure characteristics. J. Appl. Polym. Sci. 134:44246. doi: 10.1002/app.44246
Zhu, K., Li, X., Wang, H., Li, J., and Fei, G. (2017). Electrochemical and anti-corrosion behaviors graphene/acrylic modified alkyd resin latex composites carbon steel. J. Appl. Polym. Sci. 134:44445. doi: 10.1002/app.44445
Keywords: waterborne, corrosion resistance, polyurethane modified, epoxy, emulsion
Citation: Zhang J, Huang H, Ma J, Huang L, Huang L, Chen X, Zeng H and Ma S (2019) Preparation and Properties of Corrosion-Resistant Coatings From Waterborne Polyurethane Modified Epoxy Emulsion. Front. Mater. 6:185. doi: 10.3389/fmats.2019.00185
Received: 05 March 2019; Accepted: 17 July 2019;
Published: 13 August 2019.
Edited by:
Alessandra Vitale, Polytechnic University of Turin, ItalyReviewed by:
Lin Gu, Ningbo Institute of Industrial Technology (CAS), ChinaMisbah Sultan, University of the Punjab, Pakistan
Copyright © 2019 Zhang, Huang, Ma, Huang, Huang, Chen, Zeng and Ma. This is an open-access article distributed under the terms of the Creative Commons Attribution License (CC BY). The use, distribution or reproduction in other forums is permitted, provided the original author(s) and the copyright owner(s) are credited and that the original publication in this journal is cited, in accordance with accepted academic practice. No use, distribution or reproduction is permitted which does not comply with these terms.
*Correspondence: Sude Ma, bWFzdWRlMjAwN0AxNjMuY29t