- National Engineering Laboratory of Highway Maintenance Technology, Changsha University of Science & Technology, Changsha, China
The objective of this research was to improve the scientificity of the design method of the cold patching asphalt mixture (CPAM). Firstly, the curing temperature for CPAM was optimized. In addition, based on the traditional Marshall mix design method, the volume parameters of CPAM were converted, and the low-temperature workability index was added. This is the modified Marshall mix design method to determine the optimal asphalt aggregate ratio of CPAM. Then, the initial strength, forming strength, storage stability, water stability, and high-temperature stability of CPAM were tested. The properties of CPAM designed by using the modified Marshall mix design method were compared with those of CPAM designed by using the traditional Marshall mix design method and the empirical formula method. The test results show that the optimal asphalt aggregate ratio of CPAM is 5.38%. The recommended oven curing temperature for the CPAM specimen is 90°C. The initial strength and forming strength of CPAM meet the requirements, and the forming strength can reach about twice the initial strength. The stability of CPAM increases with an increase in storage time. High-temperature performance is good. These properties of CPAM designed by using the modified Marshall mix design method were all superior to those of the CPAM designed by using the traditional Marshall mix design method and the empirical formula method, and the water stability is similar to that of the CPAM designed by the traditional Marshall mix design method. The CPAM designed by using the modified Marshall mix design method shows better road performance, which shows that the modified procedure in this study is feasible and can be recommended as the mix design method for CPAM.
Introduction
Hot mix asphalt is widely used in road paving and repair because of its excellent performance as pavement (Yang et al., 2011). However, in the process of mixing, transportation, and placement of hot mix asphalt, the temperature required and its control are relatively high and strict, respectively (Li et al., 2017). High temperature causes not only great energy consumption but also severe environmental pollution (Diaz, 2016). Poor temperature control will cause aging of the asphalt mixture, which affects its fatigue performance and service life (Khan et al., 2016; Liu et al., 2020). Hot mix asphalt mixture cannot be produced at low temperature and in rainy weather. The damage to pavement in winter can only be repaired after April of the next year, which not only aggravates the damage to the road but also affects its comfort and safety (Ling et al., 2007). In view of these problems, cold patching asphalt mixture (CPAM) is very popular in pavement repair due to its excellent characteristics such as environmentally friendliness, low energy cost, convenient placement procedure, and sustainability and the fact that is is almost always ready to be used.
At present, there are many kinds of CPAM on the market. According to the type of solution, they can be divided into three types: solvent type, emulsion type, and reaction type (Doyle et al., 2013). In the existing research on CPAM at home and abroad, the main focus is on performance improvement. Approaches include designing moisture-resistant CPAM, high-strength CPAM, and crack-resistant CPAM. Bentonite (a kind of nano clay with strong water absorption) or microbial carbonate precipitation (MCP) has been added to CPAM with the objective of improving its capacity for moisture resistance. Moreover, these additives enhance the dehumidification and water damage prevention characteristics related to CPAM (Ling et al., 2016; Dong et al., 2018; Alenezi et al., 2019; Attaran Dovom et al., 2019). Besides, the use of cementing material instead of the emulsion can achieve the same effect. Generally, cement is added to CPAM when high strength is needed from this asphalt mixture (Shanbara et al., 2018). Fiber is added to CPAM with the goal of enhancing its tensile modulus significantly (Gómez-Meijide and Pérez, 2014). The improvement of tensile properties plays a vital role in slowing down crack growth in asphalt mixture, and permanent deformation is also significantly reduced. Cold patching asphalt mixture has been widely used in actual pavement repair and has achieved some results (Guo et al., 2014; Ma et al., 2016). However, research related to CPAM is not as mature as that associated with hot patching asphalt mixture. The early performance of CPAM is worse than that of hot patching asphalt mixture. The mechanical properties of the mixture are greatly affected by the mixing sequence and the interface formed. The stability of the aggregate skeleton and the bond strength between aggregate and binder are positively related to the rutting resistance (Ma et al., 2018; Zhang et al., 2019; Chen et al., 2020). There is not an mature method for designing a set of mix proportions for CPAM (Song et al., 2014; Saadoon et al., 2017). At present, the majority of research has used the mix proportion design method of hot mix asphalt mixture (Marshall mix design method) to design CPAM (Li et al., 2010; Dash and Panda, 2018). Additionally, the empirical formula methods of California and Tongji University are also used to calculate the amount of cold asphalt binder (Song and Lv, 1998). Cold patching asphalt mixture is different from hot mix asphalt mixture, as it need not be heated during construction. The Marshall mix design method is not suitable for designing CPAM, and the parameters of Marshall mix design (stability and flow value) have a weak correlation with the road performance of CPAM (Xu et al., 2018). The empirical formula method is greatly influenced by gradation and local climate, and the design method lacks volume index control, so the durability of the mixture is difficult to guarantee (Meng et al., 2011).
Based on the characteristics of CPAM, the Marshall mix design method was modified in this study. The road performance of three kinds of CPAM designed by using the modified Marshall mix design method, the Marshall mix design method, and the empirical formula method were tested. The comparative analysis verified the usefulness of the modified Marshall mix design method, which provides a reference for designing CPAMs.
Materials and Methods
Raw Materials
The research object of this study is the solvent used in CPAM, which is composed of neat asphalt or modified asphalt, diluent, additive, and aggregate.
Neat Asphalt
The neat asphalt used in this research is Sinopec Donghai 70PG# road petroleum asphalt; its main technical characteristics were obtained, and the results are shown in Table 1.
Diluent
The diluent can reduce the viscosity of asphalt so that CPAM has good workability under low temperature. The diluent should have good solubility in asphalt. Considering safety, volatility, and economy, the diluent used in this study was diesel oil.
Additive
The cold patching additives are generally patented by the manufacturer. In this research, the additive PR-JW03A was optimized. PR-JW03A was produced by Shenzhen Jiashengwei Chemical Technology Co., Ltd. This additive is a special polymer chemical product composed of a variety of polymers that can improve the properties of asphalt when added to ordinary road asphalt. Its technical indicators are shown in Table 2.
Coarse Aggregate
The coarse aggregate plays an important supporting role in the mixture skeleton and is the main part of the pavement bearing load. Limestone was used as a coarse aggregate in this study. According to the requirements of the specification, the relevant technical indices of the coarse aggregate were obtained; the test results are shown in Table 3.
Fine Aggregate
The fine aggregate fills the gaps formed by the coarse aggregate to achieve a dense skeleton structure, improving the durability of the pavement. The fine aggregate used in this research was limestone.
Mineral Filler
The mineral filler can not only fill the gap between aggregates but also improves the water stability of CPAM. Furthermore, the addition of mineral filler increases the proportion of structural asphalt, which enhances the strength of CPAM. In this study, the selected mineral filler was obtained by grinding limestone, and its main properties met the specification requirements, as shown in Table 4.
Preparation of Cold Patching Asphalt
The main instrument used in the preparation of cold patching asphalt is a high-speed disperser, with a speed range equal to 0–10,000 r/min. The electric furnace, thermometer, oven, electronic scale, and other auxiliary tools were also utilized.
The best ratio for cold patching asphalt finally determined in this research was additive:asphalt:diluent = 1.8:100:25. The preparation steps were as follows.
1) Heat the neat asphalt in an oven at 135°C for 2 h, then take it out and heat it in an electric furnace to maintain the temperature around 135°C.
2) Add the additive into (1), start the disperser, rotate at 200 r/min, and mix for half an hour.
3) Add diesel oil into (2), control the temperature at about 110°C, and mix for 30 min.
4) The preparation is completed.
The preparation of cold patching asphalt and the principle involved are shown in Figure 1.
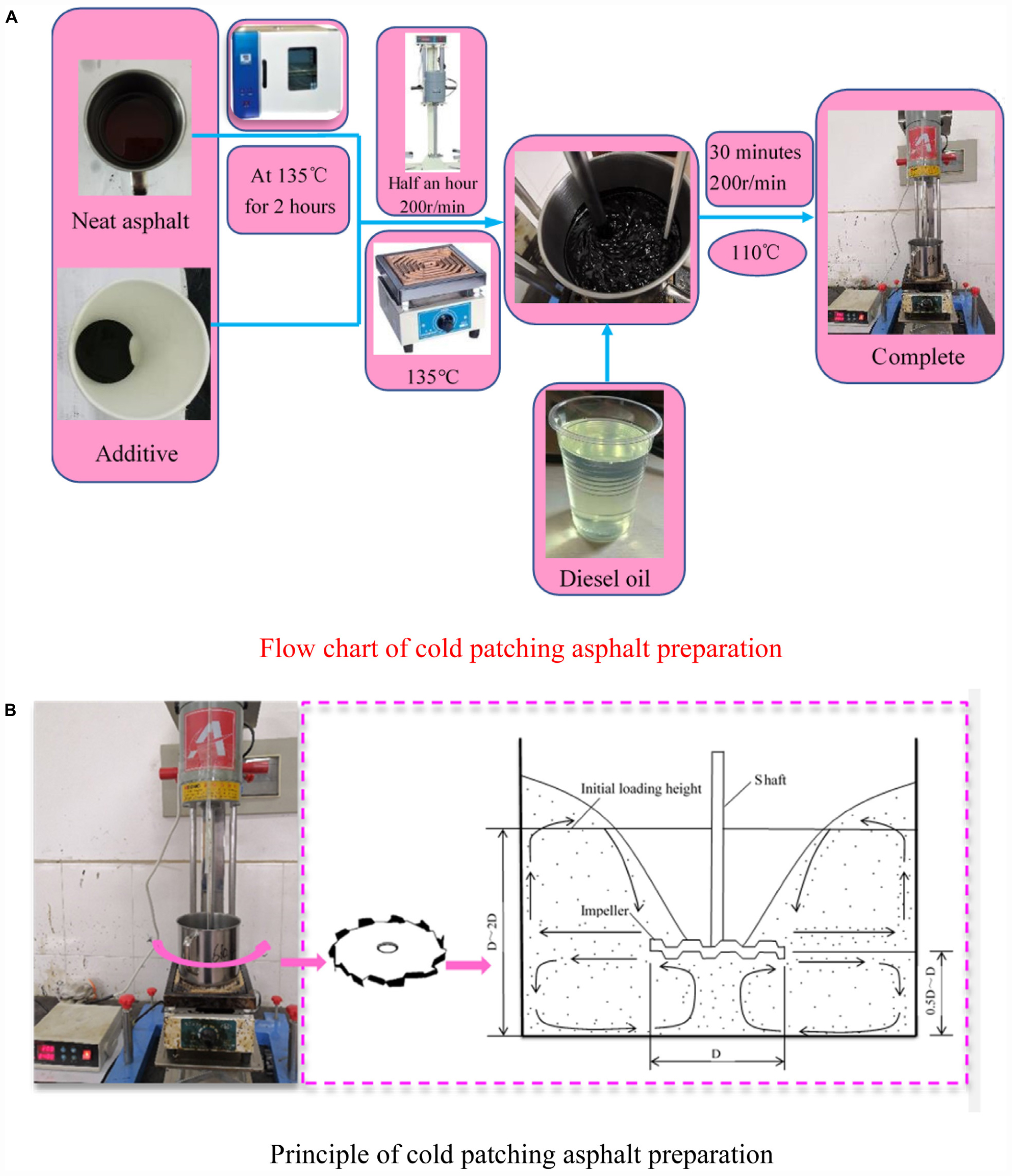
Figure 1. Preparation of cold patching asphalt by disperser and the principle involved. (A) Flow chart of cold patching asphalt preparation. (B) Principle of cold patching asphalt preparation.
Mix Design of CPAM
The Marshall mix design method was used to obtain the proportion of each element that composes hot mix asphalt mixture. By utilizing this method, researchers have accumulated a rich body of practical experience and data. Cold patching asphalt mixture should not only have good road performance in the later stage but also have excellent low-temperature workability. Based on the Marshall mix design method, the Marshall test indices of CPAM were tested. In addition, given the performance requirements of CPAM, the low-temperature workability index was considered. The volume parameters of the finished specimen were converted into those related to the initial specimen. According to the relationship between each index and the asphalt aggregate ratio, the best asphalt aggregate ratio of CPAM was determined.
Gradation
Generally, the ratio of pavement disease depth h and the maximum size D of aggregate is used to determine the nominal maximum aggregate size of CPAM. Usually, it is considered that h/D should be greater than or equal to 2. The thickness of the upper layer of asphalt pavement is designed as 4 cm, and the nominal maximum grain size of the top layer is generally 13.2 mm. Considering the interface characteristics of the new and old mixture, and according to the calculation of h/D, the nominal maximum aggregate size was determined to be 13.2 mm.
According to the Technical Specifications for Construction of Highway Asphalt Pavements (JTG F40–2004,2004), LB-13 gradation was adopted in this study. The grading is shown in Table 5.
Marshall Specimen Preparation
In this research, the second compaction method was used to form the specimen. This involves first compacting both sides 50 times. The specimen is then put in a test mold in the oven at a certain temperature for 24 h, standing on its side. After taking the sample out from the oven, both sides are compacted 25 times immediately, and it is demolded. The height of the specimen is measured by using a vernier caliper and should meet the criterion 63.5 ± 1.3 mm. According to the Technical Specifications for Construction of Highway Asphalt Pavements (JTG F40–2004,2004), the initial curing temperature of the specimen in this research was equal to 110°C, but it was found that the specimen was loose and peeled after curing. This fact shows that the curing temperature of 110°C was too high, and it was not suitable for solvent-type CPAM. Therefore, considering the volatilization rate of diluent inside the specimen, and the integrity of the specimen, four different curing temperatures were preliminary selected: 60, 75, 90, and 100°C. After curing, the Marshall stability of the specimen was obtained, and the results are shown in Figure 2.
As can be seen from Figure 2, the stability increases with the increase in temperature. The value rapidly increases from 60 to 90°C and then slowly increases from 90 to 100°C. According to the Technical Specifications for Construction of Highway Asphalt Pavements (JTG F40–2004,2004), the Marshall stability of CPAM should not be less than 3 kN, and the specimen can meet this requirement when the curing temperature is above 90°C. Considering the Marshall stability growth rate with temperature, the integrity of the test piece, and the economic and energy-cost factors, the final curing temperature adopted in this study was equal to 90°C.
Determination of Asphalt Aggregate Ratio
According to the volatilization level of diluent in CPAM, the forming stage of CPAM can be divided into two states: the initially and finally formed states. The diluent inside the CPAM in the finally formed state has basically evaporated. However, the diluent in CPAM in the initially formed state has not yet begun to volatilize, so the CPAM in this state can be regarded as a typical hot mix. With the gradual volatilization of diluent, the volume parameters of the CPAM in the finally formed state can be obtained by using all of the volume parameters of the initially formed specimen. Therefore, the optimal binder content of CPAM can not only be determined according to the parameters of the final formed specimen. The volume parameter that should be used is that of the initially formed specimen, which can be regarded as an ordinary hot mix (Gu, 2017).
The most obvious characteristic of CPAM is that it can be elaborated under normal and low-temperature conditions. Therefore, the CPAM is required to be loose at low temperature, which is convenient for spreading and compaction. In this research, low temperature and workability indices were considered in the process of mix design.
Volume Parameter Conversion
All of the measured volume parameters of the finally formed specimen were converted into the volume parameters of the initially formed specimen. Before compacting, the quality mp of the mixture in each test mold was recorded.
The bulk specific gravityrpf of the initially formed specimen was calculated according to formula (1),
where mf and mw are the surface dry mass of the specimen and the water mass of the specimen, respectively, g.
The theoretical maximum specific gravity rpt of the initially formed specimen was calculated according to formula (2),
where ma is the air mass of the specimen, g and rt is theoretical maximum specific gravity.
According to formulas (3)–(5), the percentage of voids in mineral aggregatepvma, percent air voids pvv, and percent voids in mineral aggregate filled with asphalt pvfa are calculated,
where rsb is synthetic bulk density, g/cm3 and ps is proportion of mineral aggregate quality to total asphalt mixture quality,%.
The volume parameters of the initially formed specimen are obtained based on the above formula. The relationship between each volume parameter and the asphalt aggregate ratio was obtained. According to the determination method of the optimal asphalt aggregate ratio of hot mix asphalt mixture, the optimal asphalt aggregate ratio of CPAM was determined.
Determination of the Optimal Asphalt Aggregate Ratio
The Marshall test results of the finished formed specimens are shown in Table 6.
Keeping the stability unchanged, the volume parameters of the final formed specimen were converted into the volume parameters of the initially formed specimen. The calculation results are shown in Table 7.
Figure 3 shows the relationship between the asphalt aggregate ratio and each index of the initially formed specimen.
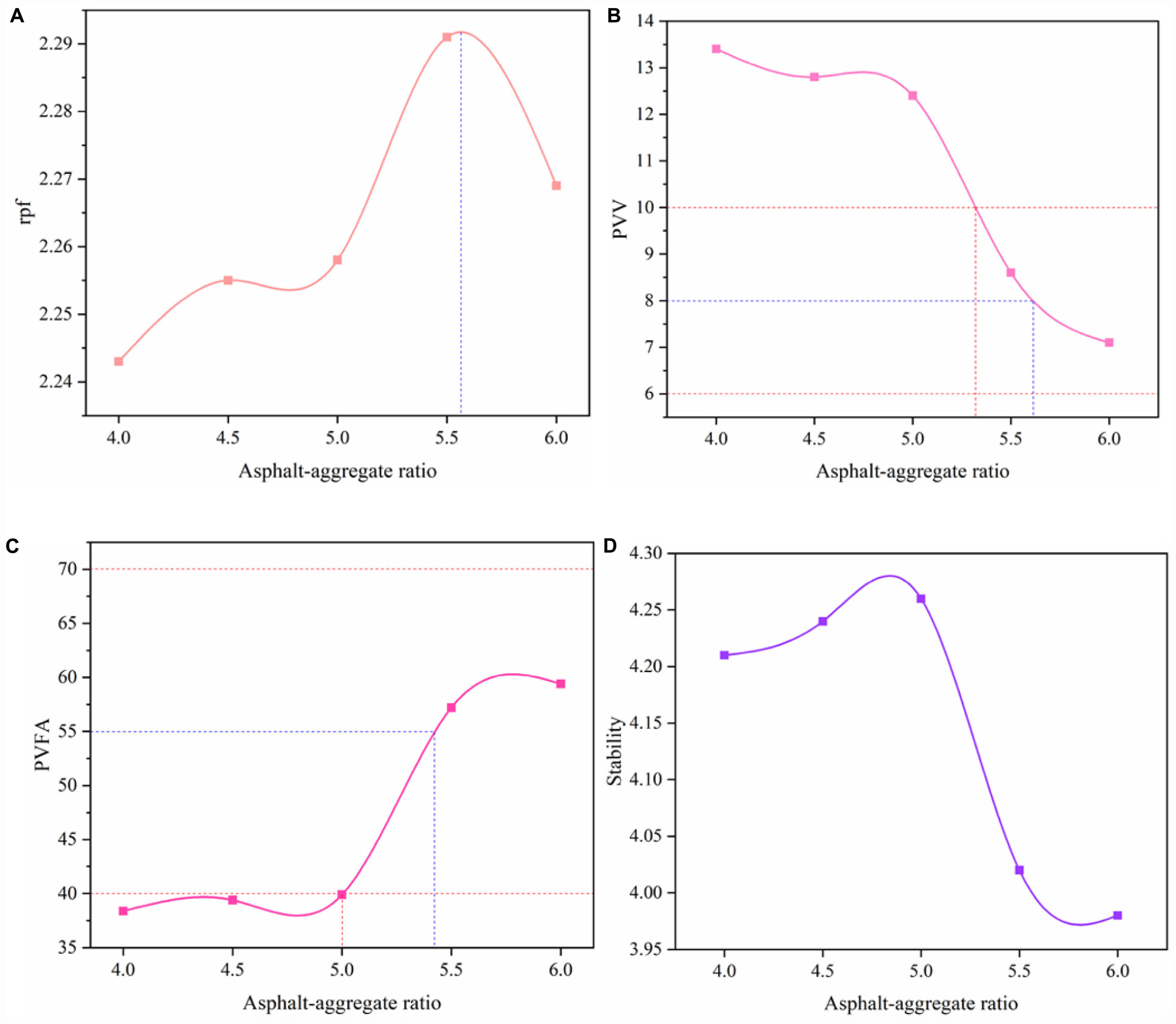
Figure 3. (A) Relationship between asphalt aggregate ratio and rpf; (B) relationship between asphalt aggregate ratio and PVV; (C) relationship between asphalt aggregate ratio and PVFA; (D) relationship between asphalt aggregate ratio and stability.
To sum up, the asphalt aggregate ratio a1, a2,a3, a4 corresponding to the maximum stability, the maximumrpf, the median design range ofpvv, and the median range of pvfa were determined from Figure 3. According to formula (6), the average value of the four asphalt aggregate ratios is the initial value OAC1 of the optimal asphalt aggregate ratio.
On the basis of the test results of each index, the range of asphalt content that meets the technical standards was determined. According to the Technical Specifications for Construction of Highway Asphalt Pavements (JTG F40–2004,2004), Marshall stability should be not less than 3 kN. pvma and pvfa refer to the Marshall test standard of hot mix asphalt mixture. Therefore, the asphalt aggregate ratio is required to be higher than 5.3% for pvv. The asphalt aggregate ratio needs to be higher than 5% for pvfa.
CPAM should have excellent workability at room temperature. Therefore, this research focuses on workability under low-temperature conditions. Cold patching asphalt mixture was prepared with variations of 0.2% in the asphalt aggregate ratio. According to the Technical Specifications for Construction of Highway Asphalt Pavements (JTG F40–2004,2004), the CPAM was placed in a refrigerator at -10°C for 24 h. If the mixture has no obvious agglomeration phenomenon, it can be easily mixed with a shovel. Cold patching asphalt mixture was taken out from the refrigerator and showed good workability at low temperatures. The test results are shown in Table 8.
According to the test results shown in Table 8, the asphalt aggregate ratio should be 5.2–5.4% for low-temperature workability. The initial value of the optimal asphalt aggregate ratio OAC2 was calculated from Eq. (7).
The optimal asphalt aggregate ratio of CPAM is calculated according to formula (8),
The optimal asphalt aggregate ratio of CPAM obtained by using the modified Marshall mix design method was equal to 5.38%.
Road Performance Verification
In this study, the optimal asphalt aggregate ratio of CPAM obtained by using the tradition Marshall mix design method was equal to 5.52%. In addition, the empirical formula proposed by LV Weimin of Tongji University was used to find the optimal asphalt aggregate ratio of CPAM. The calculation formula is as follows.
where P is the asphalt aggregate ratio,%, a is the mass percentage of aggregate with particle size greater than 2.36 mm,%, b is the mass percentage of aggregate with particle size between 0.3and 2.36 mm,%, c is the mass percentage of aggregate with particle size between 0.075and 0.3 mm,%, and d is the mass percentage of aggregate with particle size less than 0.075 mm,%.
According to Eq. (9), the asphalt aggregate ratio designed by using the empirical formula was equal to 4.5%.
In order to verify the usefulness of the modified Marshall mix design method proposed in this study, road performance tests of CPAM designed by the different methods were carried out. The test flow chart is shown in Figure 4.
Test Method
Initial Strength
In the early stage of CPAM, the diluent has not volatilized, and the cohesion among minerals is small. The initial strength is mainly supported by the intercalation and friction among aggregates (Nassar et al., 2016). In order to ensure that the pavement can resist the loose damage caused by the rolling of vehicles at the initial stage of repair, it should be ensured that the initial strength of CPAM reaches a specific value.
The test method of initial strength was as follows: take about 1100 g of CPAM (subject to the height of the specimen conforming to 63.5 ± 1.3 mm) and put it into a Marshall test mold. Compact the upper and lower sides respectively 75 times by using an automatic Marshall compactor. Stability can be tested after demolding.
Forming Strength
The method for testing the forming strength is as follows. Take 1100 g of CPAM (subject to the height of the specimen conforming to 63.5 ± 1.3 mm) and put it into a Marshall test mold. Compact the upper and lower sides respectively 75 times by using an automatic Marshall compactor. After that, the specimen with the test mold is kept in an oven at 90°C for 24 h, and then it is removed from the oven and compacted on both sides 25 times. A Marshall stability test is conducted after demolding.
Storage Stability
The CPAM can be divided into hot mix CPAM and cold mix CPAM according to mixing conditions. Hot mix CPAM can be stored for about two years (Dulaimi et al., 2017). During the storage process, it should be ensured that the CPAM does not experience a high degree of agglomeration to facilitate its placement and compaction during construction. In this research, the CPAM was stored and sealed for 0, 3, 7 and 28 days at normal temperature. The initial strength was then tested, and the method described above was used to judge the workability at 28 days.
Water Stability
The water stability of CPAM was evaluated by conducting an immersion Marshall test and freeze-thaw splitting test. The test should be carried out according to Standard Test Methods of Bitumen and Bituminous Mixtures for Highway Engineering (JTG E20–2011,2011).
High-Temperature Performance
In this study, the Hamburg rutting test was used to evaluate the high-temperature performance of CPAM. According to the formation method of a hot mix asphalt rutting specimen, combined with the characteristics of CPAM, the formation of a rutting specimen was carried out as follows.
Take the CPAM and put it into the test mold and first conduct manual compaction. Then, roll down the CPAM two times in one direction and 12 times in the other direction using a hydraulic rutting machine. Put the CPAM with the test mold into an oven at 90°C for 24 h and then take it out and carry out a second rolling according to the first rolling method. The Hamburg rutting test should be carried out according to Standard Test Methods of Bitumen and Bituminous Mixtures for Highway Engineering (JTG E20–2011,2011).
Results and Discussion
Initial Strength
The initial strength of the three kinds of CPAM (empirical formula method design, Marshall mix design method, and modified Marshall mix design method) was tested. The test results are shown in Figure 5.
It can be seen from Figure 5 that the CPAM with a 5.38% asphalt aggregate ratio has the largest initial strength. The initial strength of the 4.5% asphalt aggregate ratio is the lowest. This is because there is a small amount of binder and the strength of the mixture is mainly supported by the friction among the aggregates. There is no specificated requirement for the initial strength of CPAM. The United States and Song Jiansheng, China, require an initial strength greater than 2 kN. The initial strengths of CPAM with asphalt aggregate ratios of 5.38 and 5.52% are equal to 2.84 and 2.53 kN, respectively, which meet this requirement. The asphalt aggregate ratio obtained by the empirical formula method is too low, so that the initial strength is too low and fails to meet the requirement.
Forming Strength
The forming strengths of the three kinds of CPAMs were measured according to the test method in section“Forming Strength”. In this section, the initial strength and the forming strength are compared; the results are shown in Figure 6.
The forming strength consists of cohesion and internal friction. It can be noticed from Figure 6 that the forming strength of the three CPAMs is basically twice the initial strength. This fact is because the viscosity of the binder increases and the cohesion of CPAM increases as a result of diluent volatilization. The forming strength of CPAM with a 5.38% asphalt aggregate ratio achieves the highest value, which is equal to 6.13 kN. The forming strength of CPAM with a 4.5% asphalt aggregate ratio has the lowest value because the amount of binder is too small, and the cohesion is not sufficient. When the asphalt aggregate ratio is equal to 5.52%, the binder content of CPAM is too high, and there is a large amount of free asphalt. A larger or smaller asphalt aggregate ratio is not advantageous to the forming strength of CPAM. Compared with the other two methods, the forming strength of CPAM designed by using the modified Marshall mix design method formed faster.
Storage Stability
Three CPAMs were prepared by using the three different design methods. Then, the elaborated CPAM specimens were stored and sealed for a period of time, and afterward, their initial strength and workability were tested. The test results are shown in Table 9.
According to Table 9, the relationship between the initial strength and storage time of the three CPAM is consistent. The initial strength increases with an increase in storage time in all cases. After 28 days of storage, the strength of the three kinds of CPAM changes little; the variation is lower than 0.2 kN. The initial strength is relatively stable. The workability grade of CPAM designed by using the Marshall mix design method was equal to 4, meaning that its low-temperature workability was poor. The results show that the asphalt content of CPAM designed by using the Marshall mix design method is too high and it easily agglomerates. However, the low-temperature workability of CPAM designed by using the modified Marshall mix design method was acceptable.
Water Stability
The immersion Marshall test and freeze-thaw splitting test were carried out with the objective of testing the three kinds of CPAM with different asphalt aggregate ratios. The water damage resistance of CPAM with different asphalt aggregate ratios was studied and compared with that of hot asphalt mixture. The results of the immersion Marshall test are shown in Figure 7, and the results of the freeze-thaw split test are shown in Figure 8.
It can be seen from Figure 7 that the residual stability of the CPAM specimens with asphalt aggregate ratios of 5.38 and 5.52% meets the requirements of the residual stability for hot asphalt mixture. The residual stability of the CPAM with a 4.5% asphalt aggregate ratio is low. This is due to the lack of binder and the large percentage of air voids. It can be noticed from Figure 8 that the freeze-thaw splitting strength ratio of the three CPAMs meets the requirements for hot asphalt mixture. The order of the freeze-thaw splitting strength ratios is as follows: 5.38% CPAM > 5.52% CPAM > 4.5% CPAM. This shows that CPAM designed by the modified Marshall mix design method has the best water stability. The residual stabilities and the freeze-thaw splitting strength ratios of the three kinds of CPAM are lower than that of the hot asphalt mixture. Because the diluent has not been completely volatilized, the CPAM has not been fully formed, and, consequently, its performance is poor.
High-Temperature Performance
Track boards were formed according to the method in section“High-Temperature Performance”. The Hamburg rutting test was carried out to test the three kinds of CPAM, and the results are shown in Figure 9.
It can be seen from Figure 9 that the dynamic stability of CPAM designed with the modified Marshall mix design method was slightly higher than that of CPAM designed with the other two methods. The dynamic stability of the CPAM with a 4.5% asphalt aggregate ratio shows the smallest value because the amount of binder is too small and the cohesion is poor, which causes the mixture to have a dry texture. The dynamic stability of CPAM with a 5.52% asphalt aggregate ratio is lower than that of CPAM with a 5.38% asphalt aggregate ratio. This may be because the former CPAM has a larger amount of binder and thick asphalt film. The increase in free asphalt leads to move and plastic deformation at high temperature. The overall dynamic stability of CPAM is low because the strength of the mixture has not been fully formed. The rutting resistance under this condition does not represent the final performance of CPAM.
Conclusion
The Marshall mix design method was modified with the objective of designing CPAMs. A series of road performance tests of CPAM designed by using the Marshall mix design method, the empirical formula method, and the modified Marshall mix design method were carried out. The tests included an initial strength test, forming strength test, storage stability test, water stability test, and high-temperature stability test. The results of comparative analysis verified the usefulness and feasibility of the modified Marshall mix design method. Based on the results of this limited laboratory investigation, the following conclusions can be drawn.
• In this paper, the recommended curing temperature for a CPAM specimen was 90°C. The optimal asphalt aggregate ratio of CPAM obtained by using the modified Marshall mix design method was equal to 5.38%. This value was between the optimal asphalt aggregate ratio obtained by using the traditional Marshall mix design method and that obtained by using the empirical formula method.
• The road performance of CPAM designed by using the modified Marshall mix design method was better than that of CPAM designed by using the traditional Marshall mix design method and empirical formula method. The modified Marshall mix design method is feasible.
• The strength of CPAM increases with time. The forming strength was about twice the initial strength.
• The mix design of CPAM should consider its own characteristics. In this paper, volume parameter conversion and the addition of the low-temperature workability requirement enable better CPAM design. It is recommended that the modified Marshall mix design method be utilized as the mix design procedure for CPAM.
Data Availability Statement
All datasets generated for this study are included in the article/supplementary material.
Author Contributions
SL directed the entire process of the manuscript. SW, CX, and CL carried out the experiments and data analysis. All authors analyzed the results and contributed in writing the manuscript.
Conflict of Interest
The authors declare that the research was conducted in the absence of any commercial or financial relationships that could be construed as a potential conflict of interest.
Funding
This work was supported by the National Natural Science Foundation of China (51578081, 51608058), the Scientific and Technological Innovation Project of Hunan Province for University Graduate Students (CX2019B∗∗∗), the National Engineering Laboratory Open Fund Project (kfh160102), Hunan Province-Transport Construction Projects of Science and Technology (201701), Inner Mongolia Autonomous Region Transportation and Transportation Department Transportation Projects of Science and Technology (NJ-2016-35, HMJSKJ-201801), the National Key R&D Program of China (2018YFB1600100), the Natural Science Foundation of Hunan Province (2018JJ3550), the Education Department of Hunan Province (18B144), and the Science and Technology Project of Henan Provincial Department of Transportation (2016Z2).
Acknowledgments
We wish to thank the reviewers and editors for their advice on this article.
References
Alenezi, T., Norambuena-Contreras, J., Dawson, A., and Garcia, A. (2019). A novel type cold mix pavement material made with calcium-alginate and aggregates. J. Clean. Product. 212, 37–45. doi: 10.1016/j.jclepro.2018.11.297
Attaran Dovom, H., Mohammadzadeh Moghaddam, A., Karrabi, M., and Shahnavaz, B. (2019). Improving the resistance to moisture damage of cold mix asphalt modified by eco-friendly Microbial Carbonate Precipitation (MCP). Constr. Build. Mater. 213, 131–141. doi: 10.1016/j.conbuildmat.2019.03.262
Chen, T., Luan, Y., Ma, T., Zhu, J., Huang, X., and Ma, S. (2020). Mechanical and microstructural characteristics of different interfaces in cold recycled mixture containing cement and asphalt Emulsion. J. Clean. Product. 258:120674. doi: 10.1016/j.jclepro.2020.120674
Dash, S. S., and Panda, M. (2018). Influence of mix parameters on design of cold bituminous mix. Construct. Build. Mater. 191, 376–385. doi: 10.1016/j.conbuildmat.2018.10.002
Diaz, L. G. (2016). Creep performance evaluation of Cold Mix Asphalt patching mixes. Int. J. Pavement Res. Technol. 9, 149–158. doi: 10.1016/j.ijprt.2016.04.002
Dong, Q., Yuan, J., Chen, X., and Ma, X. (2018). Reduction of moisture susceptibility of cold asphalt mixture with Portland cement and bentonite nanoclay additives. J. Clean. Product. 176, 320–328. doi: 10.1016/j.jclepro.2017.12.163
Doyle, T. A., McNally, C., Gibney, A., and Tabakoviæ, A. (2013). Developing maturity methods for the assessment of cold-mix bituminous materials. Construct. Build. Mater. 38, 524–529. doi: 10.1016/j.conbuildmat.2012.09.008
Dulaimi, A., Al Nageim, H., Ruddock, F., and Seton, L. (2017). High performance cold asphalt concrete mixture for binder course using alkali-activated binary blended cementitious filler. Construct. Build. Mater. 141, 160–170. doi: 10.1016/j.conbuildmat.2017.02.155
Gómez-Meijide, B., and Pérez, I. (2014). A proposed methodology for the global study of the mechanical properties of cold asphalt mixtures. Mater. Design 57, 520–527. doi: 10.1016/j.matdes.2013.12.079
Gu, C. (2017). Structural Characteristics and Test Evaluation of Cold Patching Asphalt Mixture. Master thesis, Southeast University, Nanjing.
Guo, M., Tan, Y., and Zhou, S. (2014). Multiscale test research on interfacial adhesion property of cold mix asphalt. Construct. Build. Mater. 68, 769–776. doi: 10.1016/j.conbuildmat.2014.06.031
JTG E20–2011 (2011). Standard Test Methods of Bitumen and Bituminus Mixture for Highway Engineering. Beijing: China Communications Press.
JTG F40–2004 (2004). Technical Specifications for Construction of Highway Asphalt Pavements. Beijing: China Communications Press.
Khan, A., Redelius, P., and Kringos, N. (2016). Evaluation of adhesive properties of mineral-bitumen interfaces in cold asphalt mixtures. Construct. Build. Mater. 125, 1005–1021. doi: 10.1016/j.conbuildmat.2016.08.155
Li, F., Huang, S. C., Xu, J., and Qin, Y. C. (2010). Research on composition design of cold patching asphalt mixture. J. Wuhan Univ. Sci. Technol. 32, 79–82.
Li, J. X., Nan, B. Z., and Gao, J. T. (2017). Study on composition and performance of cold patching asphalt mixture. Highway Transp. Technol. 13, 199–200,227.
Ling, C., Hanz, A., and Bahia, H. (2016). Measuring moisture susceptibility of Cold Mix Asphalt with a modified boiling test based on digital imaging. Construct. Build. Mater. 105, 391–399. doi: 10.1016/j.conbuildmat.2015.12.093
Ling, J. M., Zhou, Z. F., and Peng, J. C. (2007). Preparation and performance of storage asphalt mixture for pavement repair. J. Build. Mater. 10, 195–200.
Liu, C. C., Lv, S. T., Peng, X. H., Zheng, J. L., and Yu, M. (2020). Analysis and comparison of different impacts of aging and loading frequency on fatigue characterization of asphalt concrete. J. Mater. Civ. Eng. 32:04020240. doi: 10.1061/(ASCE)MT.1943-5533.0003317
Ma, Q. H., Xing, X. T., Xu, X. S., Li, J. Z., and Feng, X. H. (2016). Preparation and performance analysis of cold patching asphalt mixture. J. S. Univ. 46, 594–598.
Ma, T., Zhang, D., Zhang, Y., Wang, S., and Huang, X. (2018). Simulation of wheel tracking test for asphalt mixture using discrete element modeling. Road Mater. Pavement Design 19, 367–384. doi: 10.1080/14680629.2016.1261725
Meng, W. Z., Yang, L., Xia, Z., Wang, X. Y., Xue, J., Wu, J. Y., et al. (2011). Preparation and properties of cold patching asphalt mixture. J. Wuhan Univ. Eng. 33, 49–53.
Nassar, A. I., Thom, N., and Parry, T. (2016). Optimizing the mix design of cold bitumen emulsion mixtures using response surface methodology. Construct. Build. Mater. 104, 216–229. doi: 10.1016/j.conbuildmat.2015.12.073
Saadoon, T., Garcia, A., and Gómez-Meijide, B. (2017). Dynamics of water evaporation in cold asphalt mixtures. Mater. Design 134, 196–206. doi: 10.1016/j.matdes.2017.08.040
Shanbara, H. K., Ruddock, F., and Atherton, W. (2018). A laboratory study of high-performance cold mix asphalt mixtures reinforced with natural and synthetic fibres. Construct. Build. Mater. 172, 166–175. doi: 10.1016/j.conbuildmat.2018.03.252
Song, J. S., and Lv, W. M. (1998). Study on composition design of storage asphalt mixture. J. Tongji Univ. 26, 664–668.
Song, X. F., Fan, Z. H., and Wang, Y. F. (2014). Study of the same curing condition of large volume concrete based on maturity methods. Adv. Mater. Res. 893, 593–596. doi: 10.4028/www.scientific.net/AMR.893.593
Xu, W., Mei, H., Luo, R., Guo, X. L., and Wang, X. (2018). Material design and mixture performance of cold patching asphalt. J. Wuhan Univ. Sci. Technol. 42, 1049–1054.
Yang, L., Meng, W. Z., Wang, X. H., Xia, Z., Wang, X. Y., Xue, J., et al. (2011). Effect of inorganic filler on strength of cold patching asphalt mixture. J. Wuhan Univ. Eng. 33, 47–51.
Keywords: Cold patching asphalt mixture, mix design, modified marshall mix design method, volume parameters, low-temperature workability, road performance
Citation: Lv S, Wang S, Xia C and Liu C (2020) A New Method of Mix Design for Cold Patching Asphalt Mixture. Front. Mater. 7:182. doi: 10.3389/fmats.2020.00182
Received: 29 February 2020; Accepted: 18 May 2020;
Published: 14 August 2020.
Edited by:
Yiqiu Tan, Harbin Institute of Technology, ChinaReviewed by:
Tao Ma, Southeast University, ChinaGilda Ferrotti, Marche Polytechnic University, Italy
Haryati Yaacob, University of Technology Malaysia, Malaysia
Ahmad Kamil Arshad, MARA University of Technology, Malaysia
Copyright © 2020 Lv, Wang, Xia and Liu. This is an open-access article distributed under the terms of the Creative Commons Attribution License (CC BY). The use, distribution or reproduction in other forums is permitted, provided the original author(s) and the copyright owner(s) are credited and that the original publication in this journal is cited, in accordance with accepted academic practice. No use, distribution or reproduction is permitted which does not comply with these terms.
*Correspondence: Shuangshuang Wang, MTMxNDIxNjQzODBAMTYzLmNvbQ==