- 1Department of Chemical Engineering, Institute of Technology, Federal Rural University of Rio de Janeiro, Seropédica, Brazil
- 2Department of Mechanical Engineering, Technology Sector, Federal University of Paraná, Curitiba, Brazil
- 3Brazilian Air Force – Curitiba Health Squad (ES-CT), Curitiba, Brazil
- 4Federal University of Paraná, Postgraduate Program in Sports Education, Curitiba, Brazil
As consumption and use increased, the accumulation of urban waste of polymeric origin drew the attention of several sectors, especially that of the organized civil society. Through mobilizations and activism, environmental became more restricted regarding the use and disposal of polymer materials. Plastic bags, tires, disposable cups, plastic straws, PET bottles are some examples of how polymers have had a negative impact to the environment generating pressures around the world to rethink their uses. However, the pandemic crisis that emerged in January, 2020 has reinforced the importance of polymers for contemporary society. If, in the past, consumerism was the driving force behind the application of polymers, nowadays health and medical emergencies are the new forces. The reduction in stocks of medical-hospital supplies and personal protective equipment for health professionals and for the general public caused by the pandemic led to the emergence of alternative production movements based on polymers. Because of those alternatives, which have helped a lot to save and preserve lives, the present work aims to highlight the types of polymers most used during this pandemic period, such as polycarbonate (PC), poly(ethylene terephthalate) (PET) and polypropylene (PP). For this purpose, scientific articles related to the production of masks and other devices having some type of polymer as raw material were analyzed. The present research was based on the first half of 2020, highlighting the countries, the polymer used, and the final product it is intended to.
Introduction
The importance of Chemistry in everyday life has been observed for a long time now. Many are the cases – even emblematic – in which this branch of Science has greatly contributed to our well-being. Now and then, however, questions arise – even if shyly – about its benefits to contemporary society. Environmental or social activism carried out without due reflection have called into question the leading role of this Science and of all those who exercise it and must promote a healthy and thoughtful debate about the legacy of Chemistry.
Countless are the examples in which chemists have left their marks on the history of technical and technological evolution. Since the manipulation of radioactive elements by the Curie couple (Curie, 1903) till the development of rubber formulations by Goodyear (Korman, 2002) – which would later be used for tire manufacturing – through the development of catalysts used in polymerization by professors Ziegler and Natta (Boor, 1979), Chemistry has always been present. And, in all those examples, it has left its mark: that of a Science capable of transforming the world. From this point of view, polymer chemistry has also contributed positively to contemporary society. Through sophisticated techniques of organic syntheses, many polymers have been developed and/or modified, getting adapted to various applications and situations. The pandemic crisis initiated in 2020 has proved that polymers are relevant for everyday life, going far beyond consumerism (Mitra and Wiesweg, 2020). Considering that many disposable masks for medical use are made of polypropylene (PP) and polyamides (PA), and also considering that since February 2020 China – its largest producer in the world – started to produce more than 200 million units of it a day (Park et al., 2020), it is reasonable to expect that the demand for those polymers will also increase. The Japanese government raised investments in mask companies, guaranteeing a supply of more than 600 million masks per month (Park et al., 2020). As if those initiatives were not enough, organizations whose business area is not centered on the production of Personal Protective Equipment (PPE) have directed their industrial plants to manufacture masks and other hospital medical equipment. This is the case of SAIC-GM-Wuling, a venture by the General Motors Co, which built 14 production lines for masks, with a daily production of 1.7 million units (Park et al., 2020). Many Italian industries have also dedicated themselves to the production of masks, allocating part of their industrial park for this new application (Amendola et al., 2020). As Dargaville et al. (2020) well pointed out, the current moment requires coordinated action among doctors, physiotherapists, materials engineers, and the industrial sector to rethink ways of production from already available supplies.
It is indisputable that the current lifestyle leads society to scenarios where pollution and environmental degradation are evident. No wonder, conferences and forums around the world involving the main global powers (politicians and the private sector) discuss the environment. But the current crisis scenario facing humanity has brought to light an aspect of polymers that, until then, had been marginalized (at least by lay people): the potential of those materials in the diversification of their use, adjusting as necessary. Many examples prove that, due to their very particular characteristics, polymers have contributed to safeguard lives in numerous battle fronts against the invisible enemy, the coronavirus, as pretty well discussed by Czigány and Ronkay (2020). The objective of the present work is to illustrate, through practices already carried out, applications of polymers for making personal protective equipment and swabs for laboratory tests.
Methodology
The present work is based on a survey of types of polymers used in three devices, the demand of which increased in the present pandemic crisis: disposable masks, face shields, and swabs. The former two are protection items, and the latter is used to collect fluid samples for testing COVID-19. The present study analyzed articles submitted and published during the 2020 period, the peak of the COVID-19 pandemic. For that purpose, the Science Direct data base was used, due to its relevance in the production of academic materials. The Google search engine was also used in order to collect information on the alternative use of materials in making PPEs. This investigation was chosen since many practices used in hospital centers have not been publishes in massive media, but only reported in scientific journals. Keywords were used that could convert to the theme of polymers used in the manufacture of masks and PPE, which are supplies with high global demand in the evaluated period.
Results
The COVID-19 pandemic has impacted, to different degrees, all productive sectors. Due to the scarcity of PPE, especially masks (UNICEF, 2020) – which were previously mandatory for health professionals, and now indispensable items to the rest of the population as a primary means to contain the advance of the virus – initiatives are being taken to produce this equipment from alternative materials. Companies and volunteers strive to meet the demand for such products by using unconventional supplies, generating a movement with strong evidence of economic circularity. In a previous work, Corrêa and Corrêa (2020) analyzed some of those initiatives focusing on face shields and masks. In all of them, there was a common element: the use of polymer material utilized in their virgin form (as a raw material not yet processed) or as recycled or reused material.
Non-certified Masks
After the rapid spread of the new coronavirus and recommendations of the European Centre for Disease Prevention and Control, 2020 and those of the Centers for Disease Control and Prevention-2020 (Centers for Disease Control and Prevention [CDC], 2020) regarding the use of masks by the population as a means of controlling contagion, many cities adopted the use of homemade masks – and, therefore, non-certified masks – as a control tool. For the circulation of people in public areas, the use of such masks has become mandatory, as it had already been the case in China, South Korea, and the Czech Republic. Because of this, many companies and individuals have resorted to means of making their own masks, looking for the best way of manufacturing those (Rubio-Moreno et al., 2020). According to a survey carried out by Rubio-Moreno and co-authors, homemade masks fall into the category of masks made from clothing, fabrics, and other materials – such as paper – not intended for use in hospital environments. They are produced based on non-standard methods, except for those manufactured according to the AFNOR SPEC S76-001 (French Association for Standardization) or the UNE 0064-1:2020, UNE 0064-2:2020, and UNE 0065:2020 specifications (Spanish Association for Standardization), which are also known as “barrier masks” or “sanitary masks”. It is worth pointing out that it is not within the scope of the present work to encourage the use of non-certified masks for aerodispersoids containment, but to demonstrate that, when properly used, polymers are useful for preserving lives.
Certified Masks
Unlike non-certified masks, the certified ones undergo tests that, among other properties, analyze their barrier capacity to particles and aerodispersoids, as well as their sealing characteristics. This type of equipment is intended for environments with potential contagion, such as hospital environments (Centers for Disease Control and Prevention [CDC], 2010; Agência Nacional de Vigilância Sanitária, 2020). In European territory, the manufacture of these masks is regulated according to Regulation (EU) 2016/425. This document is strict as to the requirements that manufacturers must have to guarantee the conformity of PPE, including respiratory protection (The European Parliament and of the Council, 2020). Since the beginning of the uncontrolled spread of the new coronavirus around the world, the demand for this item has increased. China, the world’s largest producer of masks, has adopted measures to expand its production capacity hiring more employees and facilitating the purchase of supplies, besides granting tax benefits to manufacturers (Park et al., 2020).
Polymers Used
Polypropylene (PP)
Those masks classified as FFP1, FFP2, FFP3, as well as the surgical masks usually use PP obtained by blowing. Although China – the world’s largest producer of hospital masks – is expanding its production capacity, there is still an important bottleneck: the installation of blow-molding units. According to a survey carried out by Park et al. (2020), one of the greatest challenges since the pandemic is the installation of new factories to supply non-woven blown PP since simple units take up to 6 months, at least, to be installed.
Aiming to circumvent the lack of blown PP, Solvay directed two products capable of replacing this polymer in the manufacture of masks. They are: Solef PVDF and Algoflon PTFE, both can be obtained in the form of microporous membranes with high purity content. Initially developed to meet the demand of lithium-ion batteries for electric vehicles (Solvay, 2019), such membranes are compatible and resistant to sterilization treatments based on hydrogen peroxide and water vapor in autoclaves, which would enhance their use in masks for hospital purposes (Solvay, 2020b), whose requirement is to act as a physical barrier. In this sense, in their studies related to obtaining PVDF membranes from a β structure, Cao et al. (2020) produced membranes with 300 nm pores.
Polyvinylidene Fluoride
Polyvinylidene fluoride (PVDF) is a semicrystalline thermoplastic polymer with numerous applications due to its unique properties such as chemical and thermal stability, UV radiation, oxidation resistance (Lederle et al., 2020), biological resistance, and durability (Cao et al., 2020). It has five crystalline phases (α, β, γ, δ, ε). Phases β and γ are polar phases that present conditions to favor the piezo, pyro, and ferroelectric properties of the polymer material (Cao et al., 2020). The alpha phase is apolar and easily obtained by polymerization. However, for the beta phase fractions to be generated, additional stages to polymerization are necessary, including electrospinning (Ribeiro et al., 2010).
Polytetrafluoroethylene
Polytetrafluoroethylene (PTFE) is a semicrystalline polymer with a low coefficient of friction, high thermal stability, good electrical insulation, hydrophobicity, and biocompatibility, making it attractive for many applications (Guenoun et al., 2020). Unlike most thermoplastics, PTFE cannot be processed in a conventional manner. Due to its high viscosity when melted (10 GPa.s at 380°C) (Kerbow and Sperati, 2003), injection molding is not feasible. Thus, powders of this polymer can be cold pressed, extruded with the aid of lubricants or cast molded (Ebnesajjad, 2014), and there is usually a need for subsequent sintering (Guenoun et al., 2020). Generally speaking, the PTFE membranes are produced by the biaxial stretching method. Through this process, however, it is difficult to control pore size and geometry (Cheng et al., 2020). PTFE hollow fiber membranes can be obtained from paste extrusion followed by stretching and sintering. The drawback in this process is the excessive use of lubricants during extrusion (Vavlekas et al., 2016). In this case, an alternative that has proven to be attractive for the manufacture of PTFE fibers is the use of near-field electrospinning (NFES). Through it, layers of nanomaterials are superimposed on top of one another, on a flat substrate, under the action of an electric field (Chang et al., 2008; Cheng et al., 2020). In their studies related to the development of PTFE membranes for separating water/oil, Cheng et al. (2020) obtained porous structures with various geometries. Figure 1 shows the different geometries generated by the NFES process and a membrane obtained through the method.

Figure 1. Different geometries obtained by PTFE electrospinning: (A) triangle, (B) diamond, (C) square, (D) hexagon. (Adapted from Cheng et al., 2020).
Although the membranes had not been developed for application in hospital masks, their microporous structures can be useful as barriers to aerodispersoids, giving a new use to a polymer material. Even presenting average market values of up to 10 times the value of PP, whose quotation for the current year was 1,200 euros/t, the PTFE and PDVF polymers demonstrate technical potential for use in the production of masks (Hodakel, 2020; Plastics Information Europe, 2020).
Electrospinning Process
Manufacturing polymer nanofibers can be performed using the electrospinning technique. Through it, by the action of electrical charges, polymers in solution are converted into fibers with diameters that can vary from micrometers to nanometers. This method does not require either high temperatures or chemical coagulation. The polymer nanofibers obtained by this process show a high contact area and can be presented under different structures, such as core-sheath and porous, among others (Reneker and Chun, 1996; Zhu et al., 2017; Qin et al., 2018; Bagbi et al., 2019). Its filtration power is excellent, as pointed by Molnár and Mészáros (2020). The nanofibers obtained by this process can be randomly distributed or oriented. Figure 2 shows some examples of polymer nanofibers produced by electrospinning.
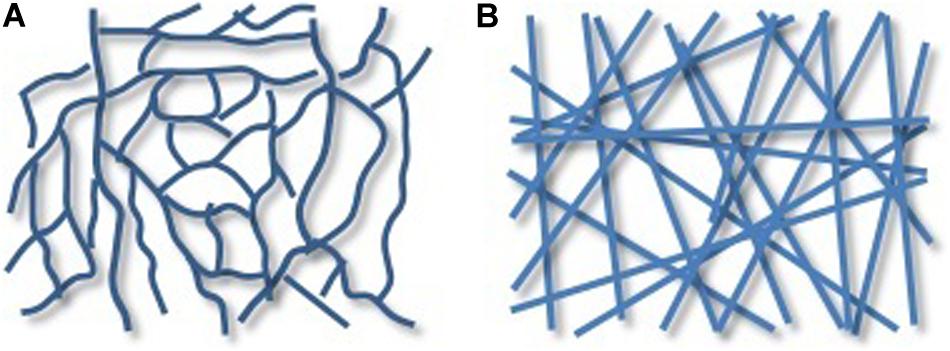
Figure 2. Examples of microstructures of polymer membranes obtained by electrospinning: (A) commercial PTFE membrane (Adapted from Huang et al., 2018); (B) lactic polyacid membrane (LPM) (Adapted from Huang and Thomas, 2018).
Compared to other methods of obtaining nanofibers – such as vapor-phase, solution-liquid-solution and hydrothermal synthesis – electrospinning becomes more attractive because it is less complex, low cost, and with a greater capacity to control the morphology of nanofibers (Qin et al., 2018). For a mass-producing electrospun fibers, the equipments can cost from 170,000 to 300,00 USD, for example (Barraza et al., 2016).
Face Shields
Considered as protective equipment in environments contaminated by coronavirus, face shields are manufactured with thermoplastic polymers resistant to heat, impact, and chemicals. Polycarbonate (PC) and poly(ethylene terephthalate) (PET) sheets are preferably used for this purpose as they combine all the properties already mentioned with a high degree of transparency (Piedmont Plastics, 2020).
Aiming to adopt alternatives that may guarantee the supply of those PPEs to health professionals wherever the supply is scarce, volunteers have proposed accessible methods of production. From PET bottles, for example, simple recycling processes are able to generate sheets of this polymer that, after finishing, become face shields. Figure 3 shows an example of the steps involved in the process.
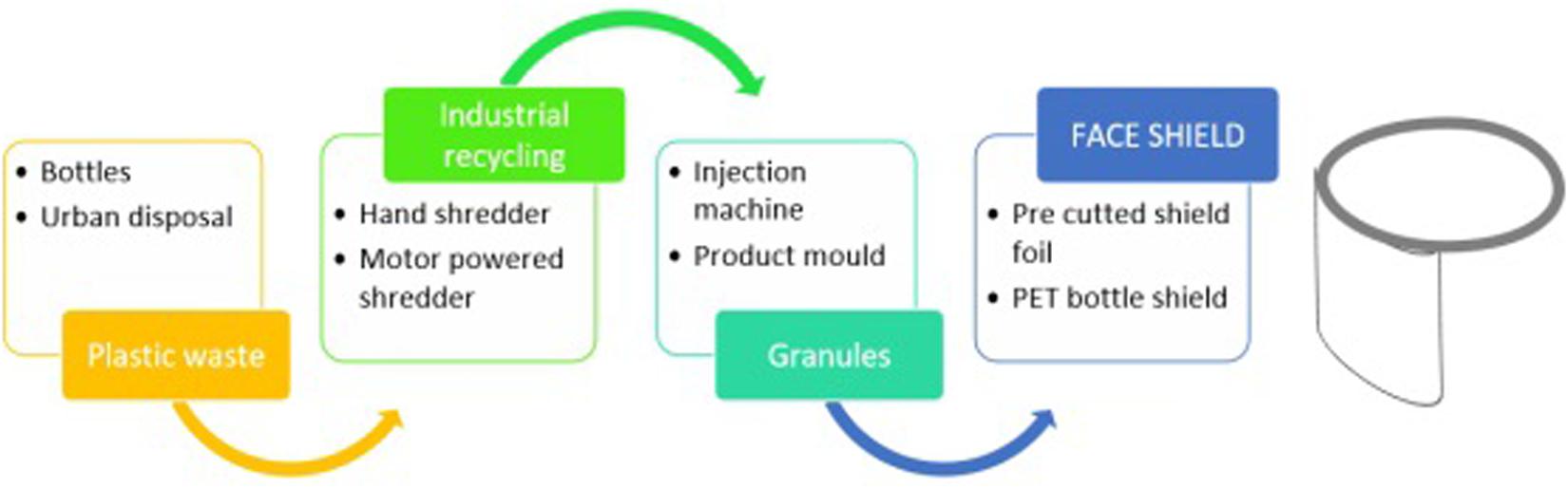
Figure 3. Steps involved in recycling PET bottles to produce face shields. (Adapted from Southern African Polymer Technology, 2020).
Depending on the pace and work conditions, there can be a daily disposal of face shields of up to 50 units per patient (Solvay, 2020a). In order to increase the reuse of this equipment in traditional hospitals and to circumvent the shortage of PC, PET, and polyacetate – materials usually used for making face shields – Solvay proposed the use of transparent films made from two of its products: Radel PPSU and Udel PSU – special polymers already used to manufacture reusable medical devices. Thus, those two lines of polymers have the advantage of guaranteeing a PPE capable of being reusable, increasing its lifetime and reducing the environmental impact of its disposal. Figure 4 shows the prototype of a face-shield obtained from Radel PPSU.
Through a consortium involving doctors, engineers, academicians, and students, the University Hospital of Paris evaluated the feasibility of producing face shields to protect radiologists from any droplets from patients diagnosed with COVID-19. The PPEs were made of poly(vinyl chloride) (PVC) sheets and headbands produced in a 3D-printer using ABS or PLA. The acceptability of the equipment by radiologists was assessed by a questionnaire based on the Likert scale. Issues related to visual quality, musculoskeletal tolerance and the ability to perform the usual functions were included in that questionnaire. Although studies on virus protection have not been carried out, a PPE can be produced in less than 2 h (Sapoval et al., 2020).
Swabs
Clinical analysis laboratories are essential in this pandemic period, contributing to fast and accurate results and allowing infection control, in addition to promoting public health guidelines (Leblanc et al., 2020; Pasomsub et al., 2020; Wu et al., 2020). Like PPE, testing has also been hampered due to shortage of supplies, including that of nasopharyngeal swabs (Leblanc et al., 2020). Copan, one of the most active companies in this segment, manufactures flocked swabs for collection and transfer of biological samples (Copan Group, 2020). Swabs are made from short nylon fibers arranged perpendicularly at the end of an applicator shaft molded in plastic. Nylon are polyamides with varied applications, including in the form of fibers and nanofibers. Depending on the type of diamines and diacids participating in the polymerization process, the produced nylons may have different properties, such as melting point, glass transition temperature, water absorption and mechanical properties (Misra et al., 2015), in addition to chemical resistance to solvents such as alcohols, aldehydes, alkalis, ethers, detergents, etc. (Goswami et al., 2004). As there is no absorbent core, the flocked type of swab prevents encapsulation of the collected samples, facilitating their elution and analysis (Indevuyst et al., 2012; Ambers et al., 2018). Figure 5 shows the applicator shaft of a flocked swab.
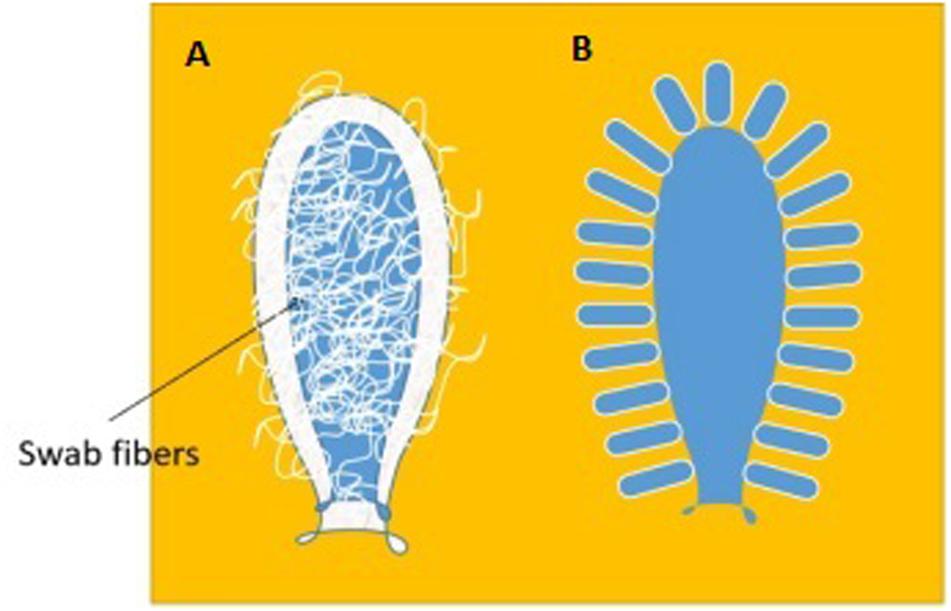
Figure 5. Drawings of swab applicators: (A) conventional swab, in which biological samples are absorbed; (B) flocked swab, made of a non-absorbent core. (Adapted from: Copan Group, 2020).
Conclusion
Despite the questionable efficiency of non-certified masks regarding the aerodispersoid barrier – and even for larger particles – these devices will most likely have their use extended for months. Countries where there have been no tradition regarding their use will now incorporate them into the routines of large cities. And for that, alternative materials must be thought of to guarantee present and future demands. In this sense, polymer materials have the advantage of being used because they are available in great quantity, they are easy to process and adapt to a particular need, and can be recycled. As for the recent pandemic crisis – which began in 2020 – initiatives by volunteers, companies, and the public sector have demonstrated the relevance polymers have in society. Due to their versatility and other very specific properties, polymers have allowed hospitals and health centers around the world to have quick and safe access to PPE produced with unconventional supplies.
Author Contributions
HC and DC performed material preparation, data collection, and analysis. HC wrote the first draft of the manuscript. Both authors commented on previous versions of the manuscript, read and approved the final manuscript, and contributed to the study conception and design.
Conflict of Interest
The authors declare that the research was conducted in the absence of any commercial or financial relationships that could be construed as a potential conflict of interest.
References
Agência Nacional de Vigilância Sanitária (2020). Cartilha de Proteção Respiratória Contra Agentes Biológicos Para Trabalhadores de Saúde. Brasilia: ANVISA.
Ambers, A., Wiley, R., Novroski, N., and Budowle, B. (2018). Direct PGR amplification of DNA from human bloodstains, saliva and touch samples collected with microFLOQ swabs. Foren. Sci. Int. Gen. 32, 80–87. doi: 10.1016/j.fsigen.2017.10.010
Amendola, L., Saurini, M., Di Girolamo, F., and Arduini, F. (2020). A rapid screening method for testing the efficiency of masks in breaking down aerosols. Microchem. J. 157:104928. doi: 10.1016/j.microc.2020.104928
Bagbi, Y., Pandey, A., and Solanki, P. (2019). “Electrospun nanofibrous filtration membranes for heavy metals and dye removal,” in Nanoscale Materials in Water Purification. Micro and Nanotechnologies, eds S. Thomas, D. Pasquini, S.-Y. Leu, and D. A. Gopakumar (Cambridge, MA: Elsevier), 75–288. doi: 10.1016/B978-0-12-813926-4.00015-X
Barraza, R., Suarez, A., Gómez, L., González, J., Iglesias, A., and Graziano, R. (2016). Design a low cost electrospinning device for practical learning in a bioengineering biomaterials course. Rev. sta Mex. Ingin. Bioméd. 37, 7–16.
Cao, P., Shi, J., Zhang, J., Wang, X., Jung, J., Wang, Z., et al. (2020). Piezoelectric PVDF membranes for use in anaerobic membrane bioreactor (AnMBR) and their antifouling performance. J. Memb. Sci. 603:118037. doi: 10.1016/j.memsci.2020.118037
Centers for Disease Control and Prevention [CDC] (2010). Interim Guidance on Infection Control Measures for 2009 H1N1 Influenza in Healthcare Settings, Including Protection of Healthcare Personnel. Atlanta, GA: CDC.
Centers for Disease Control and Prevention [CDC] (2020). Use of Cloth Face Coverings to Help Slow the Spread of COVID-19. Atlanta, GA: CDC.
Chang, C., Limkrailassiri, K., and Lin, L. (2008). Continuous near-field electrospinning for large area deposition of olderly of nanofibers patterns. Appl. Phys. Lett. 93:123111. doi: 10.1063/1.2975834
Cheng, J., Huang, Q., Huan, Y., Luo, W., Hu, Q., and Xiao, C. (2020). Study on a novel PTFE membrane with regular geometric pore structures fabricated by near-field electrospinning and its applications. J. Memb. Sci. 603:118014. doi: 10.1016/j.memsci.2020.118014
Copan Group (2020). FloqSwabs, Patented Original Technology for Optimal Sample Collection and Diagnostics. Brescia: Copan Group.
Corrêa, H. L., and Corrêa, D. G. (2020). The COVID-19 pandemic crisis stimulate circular economy practices? A brief reflection. Braz. J. Health Rev. 3, 3820–3832. doi: 10.34119/bjhrv3n2-205
Czigány, T., and Ronkay, F. (2020). Editorial corner - a personal view. The coronavirus and plastics. Exp. Poly. Lett. 14, 510–511. doi: 10.3144/expresspolymlett.2020.41
Dargaville, T., Spann, K., and Celina, M. (2020). Opinion to address the personal protective equipment shortage in the global community during the Covid-19 outbreak. Poly. Degrad. Stab. 176:109162. doi: 10.1016/j.polymdegradstab.2020.109162
Ebnesajjad, S. (2014). Fluoroplastics: Non-Melt Processible Fluoropolymers - The Definitive User’S Guide and Data Book Plastics Design Library. Amsterdam: Elsevier.
European Centre for Disease Prevention and Control (2020). Using Face Masks in the Community. Solna: ECDC.
Guenoun, G., Faou, J., Régnier, G., Schmitt, N., and Roux, S. (2020). PTFE crystallization mechanisms: insight from calorimetric and dilatometric experiments. Polymer 193:122333. doi: 10.1016/j.polymer.2020.122333
Hodakel, B. (2020). What is Polytetrafluoroethylene (PTFE) Fabric: Properties, How its Made and Where. London: Sewport.
Huang, C., and Thomas, N. (2018). Fabricating porous poly(lactic acid) fibres via electrospinning. Eur. Poly. J. 99, 464–476. doi: 10.1016/j.eurpolymj.2017.12.025
Huang, Y., Xiao, C., Huang, Q., Liu, H., Guo, Z., and Sun, K. (2018). Robust preparation of tubular PTFE/FEP ultrafine fibers-covered porous membrane by electrospinning for continuous highly effective oil/water separation. J. Memb. Sci. 568, 87–96. doi: 10.1016/j.memsci.2018.09.062
Indevuyst, C., Beuselinck, K., and Lagrou, K. (2012). ESwab flocked swabs unfit for viral culture. J. Clin. Virol. 55, 282–283. doi: 10.1016/j.jcv.2012.07.006
Kerbow, D., and Sperati, C. (2003). “Physical constants of fluoropolymers,” in Polymer Handbook, 4th Edn, eds J. Brandrup, E. H. Immergut, and E. A. Grulke (New York, NY: Wiley), V31–V58.
Korman, R. (2002). The Goodyear Story: An Inventor’S Obsession and the Struggle for a Rubber Monopoly. New York, NY: Encounter Books.
Leblanc, J., Heinstein, C., MacDonald, J., Pettibas, J., Hatchette, T., and Patricquin, G. (2020). A combined oropharyngeal/nares swab is a suitable alternative to nasopharyngeal swabs for the detection of SARS-CoV-2. J. Clin. Virol. 128:104442. doi: 10.1016/j.jcv.2020.104442
Lederle, F., Härter, C., and Beuermann, S. (2020). Inducing beta phase crystallinity of PVDF homopolymer, blends and block copolymers by anti-solvent crystallization. J. Fluor. Chem. 234:109522. doi: 10.1016/j.jfluchem.2020.109522
Misra, M., Pandey, J., and Mohanty, A. (2015). Biocomposites: Design and Mechanical Performance. Cambridge: Woodhead Publishing.
Mitra, K., and Wiesweg, M. (2020). How is Polymer Demand Impacted by the COVID-19 Pandemic?. London: IHS Markit.
Molnár, K., and Mészáros, L. (2020). Editorial corner – a personal view. The role of electrospun nanofibers in the fight against the COVID-19. Exp. Poly. Lett. 14:605. doi: 10.3144/expresspolymlett.2020.49
Park, C., Kim, K., Roth, S., Beck, S., Kang, J., Tayag, M., et al. (2020). Global Shortage of Personal Protective Equipment Amid Covid-19: Supply Chains, Bottlenecks and Policy Implications. Available online at: https://www.adb.org/sites/default/files/publication/579121/ppe-covid-19-supply-chains-bottlenecks-policy.pdf (accessed May 20, 2020).
Pasomsub, E., Watcharananan, S., Boonyawat, K., Janchompoo, P., Wongtabtim, G., Suksuwan, W., et al. (2020). Saliva sample as a non-invasive specimen for the diagnosis of coronavirus disease-2019 (COVID-19): a cross-sectional study. Clinical Microbiol. and Infect. [Epub ahead of print]. doi: 10.1016/j.cmi.2020.05.001
Piedmont Plastics (2020). Surgical Face Shields - Polycarbonate and Polyester Sheets. Available online at: https://www.piedmontplastics.com/applications/surgical-face-shield (accessed May 20, 2020).
Plastics Information Europe (2020). Polymer Prices. Available online at: https://pieweb.plasteurope.com/default.aspx?pageid=2000
Qin, L., Zhu, J., Zhang, L., and Qiu, Y. (2018). Recent advances in energy materials by electrospinning. Renew. Sustain. Energy Rev. 81, 1825–1858. doi: 10.1016/j.rser.2017.05.281
Reneker, D., and Chun, I. (1996). Nanometre diameter fibres of polymer, produced by electrospinning. Nanotechnology 7, 216–223. doi: 10.1088/0957-4484/7/3/009
Ribeiro, C., Sencadas, V., Ribelles, J., and Lanceros-Méndez, S. (2010). Influence of processing conditions on polymorphism and nanofiber morphology of electroactive poly(vinylidene fluoride) electrospun membranes. Soft Mater. 8, 274–287. doi: 10.1080/1539445x.2010.495630
Rubio-Moreno, J. C., Pardo-Ferreira, M., García, J. A., and Calero-Castro, S. (2020). Disposable masks: desinfection and sterilization for reuse and non-certified manufacturing in the face of shortages during the Covid-19 pandemic. Saf. Sci. 129:104830. doi: 10.1016/j.ssci.2020.104830
Sapoval, M., Gaultier, A., Giudice, C., Pellerin, O., Cassis-Chikhani, N., Lemarteleur, V., et al. (2020). 3-D printed face protective shield in interventional radiology: evaluation of an immediate solution in the era of COVID-19 pandemic. Diag. Intervent. Imag. 101, 413–415. doi: 10.1016/j.diii.2020.04.004
Solvay (2019). Solvay to More Than Double its SOLEF PVDF Capacity in China to Meet Booming Demand in Lithium Batteries. Brussels: Solvay.
Southern African Polymer Technology (2020). “One for One” Face Shields. Available online at: https://sapt.co.za/one-for-one-faces-shield/ (accessed May 20, 2020).
The European Parliament, and of the Council (2020). Regulation (EU) 2016/425. Oficial Journal of the European Union. Available online at: https://eur-lex.europa.eu/eli/reg/2016/425/oj (accessed May 21, 2020).
UNICEF (2020). COVID-19 Impact Assessment and Outlook on Personal Protective Equipment. Supply Division. New York, NY: UNICEF.
Vavlekas, D., Ansari, M., Hao, H., Fremy, F., McCoy, J., and Hatzikiriakos, S. (2016). Zero Poisson’s ratio PTFE in unixial extension. Poly. Test. 55, 143–151. doi: 10.1016/j.polymertesting.2016.08.014
Wang, H., and Ziegler, G. (2019). Electrospun nanofiber mats from aqueous starch-pullulan dispersions: optimizing dispersion properties for electrospinning. Int. J. Biol. Macromol. 133, 1168–1174. doi: 10.1016/j.ijbiomac.2019.04.199
Wu, J., Liu, J., Li, S., Peng, Z., Xiao, Z., Wang, X., et al. (2020). Detection and analysis of nucleic acid in various biological samples of Covid-19 patients. Travel Med. Infect. Dis. [Epub ahead of print]. doi: 10.1016/j.tmaid.2020.101673
Keywords: polymers, thermoplastics, SARS-CoV-2, applications, PPEs
Citation: Corrêa HL and Corrêa DG (2020) Polymer Applications for Medical Care in the COVID-19 Pandemic Crisis: Will We Still Speak Ill of These Materials? Front. Mater. 7:283. doi: 10.3389/fmats.2020.00283
Received: 26 June 2020; Accepted: 27 July 2020;
Published: 21 August 2020.
Edited by:
Alessandro Pegoretti, University of Trento, ItalyReviewed by:
Gonzalo Martinez-Barrera, Autonomous University of the State of Mexico, MexicoFrancesco Paolo La Mantia, University of Palermo, Italy
Copyright © 2020 Corrêa and Corrêa. This is an open-access article distributed under the terms of the Creative Commons Attribution License (CC BY). The use, distribution or reproduction in other forums is permitted, provided the original author(s) and the copyright owner(s) are credited and that the original publication in this journal is cited, in accordance with accepted academic practice. No use, distribution or reproduction is permitted which does not comply with these terms.
*Correspondence: Harrison Lourenço Corrêa, aGFycnkubG91LmNvcnJlYUBnbWFpbC5jb20=