- 1College of Materials Science and Engineering, Jilin University, Changchun, China
- 2International Center of Future Science, Jilin University, Changchun, China
- 3G.V. Kurdyumov Institute for Metal Physics, Kyiv, Ukraine
Titanium–titanium boride (Ti/TiB) metal matrix composites have been widely identified as promising materials for various applications. The traditional ingot metallurgy processing strategies used to fabricate these materials are energy intensive and have fallen short of their perceived mass production potentials. Powder metallurgy processing, especially that aimed at in-situ synthesis of Ti/TiB composites from titanium and TiB2 powder blends, is currently widely used for the cost-efficient production of such composites. However, this approach usually results in excessive sintered porosities and associated mechanical property degradation. Therefore, further thermomechanical or hot isostatic pressing steps are required for porosity reduction. In the present study, low-porosity Ti/TiB composites were synthesized using TiH2 and TiB2 powders via a simple press-and-sinter hydrogen-assisted blended elemental powder metallurgy route. The manufacturing route included two stages. Compaction and vacuum sintering of the noted blended powders was followed by hydrogenation and ball milling of the pre-sintered product to produce a hydrogenated, pre-alloyed powder. This was followed by compaction and final sintering. X-ray diffraction, light microscope, and scanning electron microscope were employed to investigate the powder morphology and material microstructures after various processing steps. The role of temporary alloying with hydrogen was established in tailoring the microstructure. When an optimized particle size distribution that was carefully controlled using a Malvern Mastersizer laser analyzer was combined with optimized hydrogenated pre-alloyed Ti/TiB powder compaction and sintering parameters, a nearly dense, uniform composite was formed. The above approach can be considered a promising solution for economical manufacturing of Ti/TiB parts with improved properties, such as a high performance-to-cost ratios.
Introduction
Titanium alloys have been thoroughly investigated and are used in intensive aerospace, military, biomedicine, and automotive materials applications because of their superior intrinsic properties, such as high specific strengths, excellent corrosion resistance, and high-temperature characteristics. Nevertheless, inferior hardness, poor wear resistance, and unaffordable final-product prices have limited the commercial success of these materials. Ceramic-reinforced titanium matrix composites may offset the physical property shortcomings of conventional titanium alloys (Abkowitz et al., 2004; Morsi and Patel, 2007; Hayat et al., 2019).
Of the various hard reinforcement materials available, such as TiB2, Al2O3, SiC, and TiC, in-situ-formed titanium boride (TiB) is considered the most compatible because it offers a chemically stable composition and its density is similar to that of the titanium matrix. It also exhibits distinctive metallurgical bonding with the titanium matrix (Hu et al., 2017). In addition, since the thermal expansion coefficients of TiB and the matrix are similar, little residual stress forms at their interface. This further enhances the mechanical properties of the material (Yamamoto et al., 1997; Huang et al., 2015).
TiB-reinforced, titanium-based metal matrix composites can be produced via a traditional ingot metallurgy (IM) approach (Chandravanshi et al., 2011; Prasad et al., 2011; Sarkar et al., 2013). A mixture of titanium and boron sources in titanium diboride (TiB2) or elemental forms dissolves and transforms into a titanium-boron alloy during the melt heating cycle. The in-situ TiB phase precipitates in the matrix during solidification via a eutectic reaction at elevated temperatures. Usually, secondary thermal work, such as rolling or extrusion, is introduced to help modify the inevitable as-cast defects in the cast products and convert coarse as-cast grains into finer microstructures.
Powder technologies are effective alternative manufacturing methods. However, pre-alloyed (PA) powder technology involves a melting stage during powder fabrication and subsequent complex powder consolidation operations. Thus, this processing route is relatively complicated. For example, the Ti-B alloy melt can be fast-cooled to obtain PA Ti-B powders via inert gas atomization (Tamirisakandala et al., 2004). Thus, the TiB phase forms and is evenly distributed among the particles. After outgassing to remove volatile impurities, the PA powders can be pressed into green parts and subjected to the abovementioned thermo-mechanical processes to produce wrought products. Advanced alloy production technologies could also be candidates in the fabrication of Ti/TiB composites with enhanced mechanical properties. Selective laser melting (SLM) is proven to be able to fabricate biomedical materials with a superb anti-corrosion ability, while spark plasma sintering (SPS) is time-saving, taking advantage of combining sintering and post treatment with the assistance of current and pressure (Zhang and Chen, 2019). With melt filling into clearance in between the reinforcements and the matrix, semi-solid sintering (SSS) can be adopted to tailor the composite densification (Yang et al., 2017).
However, the abovementioned technologies all face the same dilemma between property and cost efficiency, resulting in the limitation of industrial acceptance. Moreover, there are problematic metallurgical issues. The application of hot deformation is a key problem in ingot metallurgy (IM) processing. The growth of coarse primary TiB phases in hypereutectic compounds is the main obstacle that restricts both the IM and PA approaches (Tamirisakandala et al., 2010).
Unlike conventional IM and PA powder routes for Ti/TiB composite fabrication, blended elemental powder metallurgy (BEPM) is well known to provide a large processing “window” for microstructure control, improved TiB particle distribution uniformity in the metallic matrix, and better cost efficiency because of the lack of melting operations.
To produce composites via the BEPM route, TiB2, boron, and boron carbide (B4C) (Gorsse and Miracle, 2003; Saito, 2004; Tamirisakandala et al., 2004; Tjong and Mai, 2008; Tamirisakandala et al., 2010; Kumar et al., 2012; Huang et al., 2015; Li et al., 2016; Baglyuk et al., 2017; Іvasishin et al., 2017; Ivasishin et al., 2019) powders are used as starting materials. They are blended with either titanium or titanium hydride (Saito, 2004; Baglyuk et al., 2017; Іvasishin et al., 2017; Ivasishin et al., 2019) powders to form monoboride TiB particles via a high-temperature reaction between titanium and the abovementioned powders (Tjong and Mai, 2008). However, solid-state reactive sintering of such blends with the in-situ formation of Titanium–titanium boride (Ti/TiB) composites generally leads to excessive porosity, which is detrimental to mechanical behavior. Thus, BEPM processing routes always include complex hot deformation operations designed to reduce porosity and produce nearly dense Ti/TiB materials with an improved set of properties. Abkowitz et al. (2004) included hot isostatic pressing (HIP), forging, or extrusion of sintered products in the processing scheme, while Saito (2004) extruded, forged, and annealed sintered semi products to produce materials with properties sufficient for practical application. Li used hot extrusion to eliminate the massive pores that formed during sintering between the Ti matrix and boron powder at the expense of reinforcement aggregation (Li et al., 2016). Kumar compared HIP, spark plasma sintering, and vacuum sintering when making high-density Ti/TiB composites. The denser sintered compacts were acquired by following the first two expensive fabrication techniques; however they could not meet application requirements (Kumar et al., 2012). In the study by Gorsse and Miracle (2003), heat treatment after HIP was conducted for up to 100 h to improve the microstructure and reinforcement distribution of Ti/TiB composites.
The state-of-the-art strategies designed to reduce Ti/TiB composite porosity in most published papers typically required tedious post-thermal mechanical work or long-term heat treatment. These processes are not ideal with respect to economic factors and actual engineering demands. Only studies by Abkowitz et al. (2004) and Saito (2004) were directly aimed at the practical application of titanium-based composites.
Undoubtedly, if residual porosity can be abated, simple compaction and sintering of elemental powder blends could be one of the most fundamental and industrially viable approaches to cost-efficient fabrication of near-net-shape Ti/TiB composites. Such a process could overcome the financial obstacles driven by high material waste and the complex, expensive thermomechanical procedures that other methods require (Geng et al., 2004).
Titanium hydride TiH2 powders have been demonstrated to be substantial substitutes for conventional CP-Ti powders that do not suffer from the abovementioned severe problems associated with press-and-sinter BEPM fabrication of titanium alloys (Ivasishin and Moxson, 2015). Because of the temporary presence of hydrogen in titanium powder, residual pores can be reduced up to 1%–2% and the contents of interstitials, such as oxygen and chlorine, can be decreased to acceptable levels via dehydrogenation and sintering (Savvakin et al., 2012). However, unlike with titanium alloys, the titanium hydride approach is less effective in producing in-situ Ti/TiB and Ti-6Al-4V/TiB composites via the BEPM route (Baglyuk et al., 2017; Іvasishin et al., 2017). Better densification of TiH2-based blends than Ti-based blends has been observed only at low TiB-phase contents. However, because of the significant porosity induced by the Ti + TiB2 → 2TiB reaction, its overall value increases by 7%–9%, as observed in Ti powder-based blends with reasonable TiB contents. Such poor results require that researchers develop a better understanding of factors that affect the densification of BEPM compacts with boride powder additions in order to more effectively use the positive potential of hydrogenated powders.
The objective of this study was to develop a manufacturing approach for in-situ production of nearly dense Ti/TiB composites via hydrogen-assisted BEPM using an economically friendly cold compaction and sintering approach. Sintering of TiH2 and TiB2 blends was investigated to establish a better understanding of the role of hydrogen in microstructure evolution during the formation of a nearly dense Ti/TiB composite.
Peculiarities of Densification of TiH2 + TiB2 Blends and the Microstructures of the Resulting Ti/TiB Composites
Powder blends of TiH2 with 5 and 10 wt% TiB2 corresponding to Ti/8.4 vol% TiB and Ti/16.8 vol% TiB composites, respectively, were used in the present investigation to elucidate the general peculiarities of in-situ formation of Ti/TiB materials via BEPM. TiB inclusions were expected during the sintering process due to the reaction TiB2 + Ti → 2TiB.
As the dominant starting component, single-phase titanium hydride TiH2 (3.5 wt% H) powder was sieved to less than 100 µm and blended with corresponding amounts of fine TiB2 powder less than 25 µm in size. Figure 1 shows the particle size distributions of the initial powders, as determined using a Malvern Mastersizer 3,000 laser analyzer. The maximum size of titanium hydride particles sieved through an 100 µm cell sieve is approximately 120 µm because the particles are not spherical. The peak of the TiH2 powder size distribution curve appears at approximately 40 µm. The average TiB2 particle is approximately 8 µm in size. The powders were blended in a drum container for 6 h. Once the elemental blends were prepared, cold pressing (600 MPa) was used to fabricate cylindrical (10 mm in diameter, 10 mm long) and prismatic (60 × 9 × 9 mm) preforms. Sintering was performed in vacuum at 1,250°C (heating rate 10°C/min), followed by 4 h of isothermal exposure. Vacuum heating up to sintering temperature resulted in hydrogen emission from TiH2 and formation of dehydrogenated titanium powder particles. The negative Gibbs free energy ensures that the TiB formation reaction occurs with the development of boron diffusion into the Ti matrix (Singh et al., 2019).
The microstructure of sintered Ti/8.4% TiB material is shown in Figure 2 (TESCAN VEGA3). Images of the sintered samples indicate the presence of local microstructural inhomogeneity and substantial residual porosity. The porosity level was determined to be 7.5% via analysis of polished cross sections of the material. This is similar to early residual porosity values obtained in Іvasishin et al. (2017). The density of the sintered compact as determined via Archimedes’s technique is 4.16 g/cm3. The phase composition of the powder blends and sintered materials (Figures 3A,B) was analyzed using an “Ultima IV” diffractometer (Rigaku, Japan) that used monochromatic CuKα radiation. The sintered material consists of completely dehydrogenated α titanium matrix with orthorhombic TiB as the main boride phase and trace amounts of unreacted TiB2 phase (Figure 3B). Figure 2 clearly reveals that the reaction of TiB2 particles with titanium and the diffusion of boron inside the matrix during high-temperature sintering forms boride crystals with various morphologies. The in-situ nucleated TiB phase exhibits coarse needle-like or lamellar crystals that are located mainly between and inside large titanium grains. Some irregularly-shaped gatherings of disperse boride particles exist locally, as shown in Figure 2B. Relatively large equiaxed boride particles, like those presented in Figure 2C, are identified as intermediate reaction products consisting of a mixture of TiB2 and TiB phases (Ivasishin et al., 2019). Inhomogeneous boride redistribution within the titanium matrix produces relatively large areas (up to 60–80 µm in size) that are free of boride precipitation. The sizes of such areas correlate with that of the initial titanium hydride powder. This implies that finer starting titanium hydride powders might achieve better sintered composite microstructural homogeneity. Considerable porosity appears near boride crystals. Most pores form and aggregate directly alongside large boride clusters at the locations of initial TiB2 particles and intermediate Ti-B reaction products.

FIGURE 2. Microstructures of Ti/8.4 vol% TiB samples fabricated via sintering at 1,250°C for 4 h (A,B) and typical morphology of boride inclusions showing not completely transformed equiaxed TiB2 particle (C). SEM.
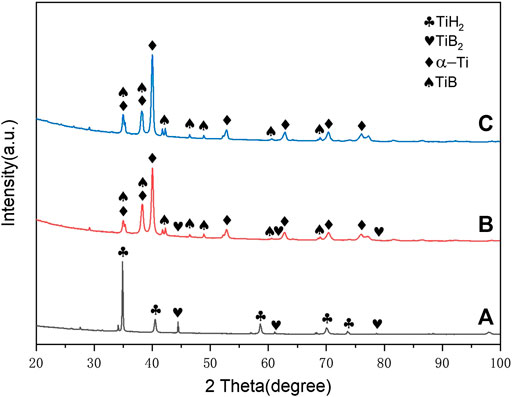
FIGURE 3. X-ray diffraction patterns of initial TiH2 + 10% TiB2 powder blends (A), material after first sintering (B) and after second hydrogenation and sintering stage (C).
To investigate the sintering kinetics and to understand the reasons for increased Ti/TiB composite porosities, in-situ shrinkage curves (Figure 4) were measured during vacuum heating (rate of 10°C/min) of powder compacts using a special dilatometric complex (Ivasishin et al., 2010). It is clearly seen (Figure 4) that the densification kinetics of the TiH2 + 5% TiB2 (curve 2) blend are worse than those of a pure TiH2 compact (curve 1). This indicates that excess porosity forms during the heating stage. When the TiB2 content is further increased to 10% in the powder blend (curve 3), less shrinking occurs. This indicates that there is an inverse relationship between the amount of TiB2 used and the extent of densification. Most TiH2 densification occurs during the dehydrogenation period. Starting when the vacuum heating process has reached approximately 300°C, the release of hydrogen atoms results in the reconstruction of the crystal lattice and significant shrinkage of each powder particle and of the entire sample due to a specific compaction mechanism that is exhibited between the particles (Ivasishin and Savvakin, 2010). Dehydrogenation is nearly complete for all samples at around 600–650°C. Phase transformations δ-TiH2 to β-Ti and then to α-Ti creates a large number of crystalline defects (Ivasishin et al., 2011). This factor activates an overall diffusion that is accompanied by intensive powder sintering and ∼10% linear reduction in total. However, as seen when comparing curve 1 with curves 2 and 3, the addition of TiB2 particles to the titanium hydride strongly affects the shrinkage processes of the corresponding compacts, retarding densification. The presence of TiB2 particles results in the loss of compact integrity during dehydrogenation, as well as the formation of additional gaps and voids between compacted particles at 300–650°C. When the temperature exceeds 650°C, the boride blend shrinkage intensity decreases substantially. Minor swelling even occurs when the temperature exceeds 1,000°C. These differences can be attributed to the presence of titanium diboride particles in the blend, which, unlike hydride particles, are not subject to dehydrogenation-related shrinkage. Reactions between dehydrogenated Ti particles and TiB2 are another reason for poor densification. Although calculations based on the densities of reacting materials indicate minor volume reductions (∼1%) during in-situ formation of the TiB phase, swelling occurs because of increased porosity formation at higher boride contents. As shown in Ivasishin et al. (2019), the interfaces between TiB2 particles and the Ti matrix are important sintering-related pore formation locations. The swelling effect observed due to this reaction strongly hinders the overall densification upon powder sintering, decreasing overall linear shrinkage from ∼10% for TiH2 to ∼4% for TiH2 admixtures that contain 5% TiB2 and to 2% for blends that contain 10% TiB2.
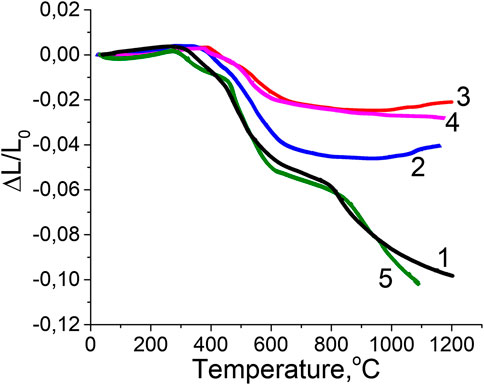
FIGURE 4. Dilatometric heating curves for (1) compacted TiH2 powder; (2) TiH2 + 5% TiB2 powder blend; (3,4) TiH2 + 10% TiB2 powder blends; and (5) hydrogenated, pre-alloyed Ti/TiB powder compacts. The TiB2 particles are (2, 3) <25 µm and (4) <8 µm in size.
Bulk shrinkage of TiH2 powder particles upon hydrogen release during heating cycles creates extra interstitial spaces between the dehydrogenated titanium matrix and TiB2 particles. These spaces further impede direct contact between the reactants, diminishing the TiB formation rate and sometimes stopping the reaction during its intermediate stages. Two more reasons for the noted excess porosity are the gap between the diffusion capabilities of titanium and boron at elevated temperatures (Baglyuk et al., 2017) and the difference between the boron diffusion velocities in TiB and TiB2 phases. These factors can cause the formation of Kirkendall porosity during boron redistribution (Panda et al., 2003). The TiB crystals grow to form needle-like shapes via unidirectional diffusion of atomic boron. This creates a flux of vacancies in the opposite direction and forms pores, which also contribute to the swelling of the compact and the formation of residual porosity.
The presence of a particular boride cluster structure surrounded by a number of pores (Figure 2C) and the remnants of TiB2 phase in the sintered material prove that titanium diboride is not completely reacted to single-phase titanium monoboride even after treatment at 1,250°C for 4 h. Similar effects were observed in Ivasishin et al. (2019). Incomplete transformation of TiB2 powder to the TiB phase can also be induced via occasional formation of relatively coarse TiB2 aggregates during powder blending. This also promotes the porous structure developed during heating.
Increased porosity, remnants of borides that are not fully transformed into TiB, and boride particle distribution irregularities in the titanium matrix harm the mechanical properties of the resulting composites. For example, Ti/8.4 vol% TiB with 7.5% porosity has a moderate Vickers hardness (260–270 HV) and moderate tensile characteristics (UTS = 770 MPa, elongation 2.4%). The Ti/16.8% TiB composite is completely brittle without the expected hardness increase due to its higher (∼9%) porosity. For comparison, commercially pure titanium (CP-Ti) produced by sintering TiH2 powder exhibits a hardness of 220 HV–230 HV, UTS of 570–600 MPa, and elongation of 16%–22% at a low (1.5%) residual porosity. Excessive porosity of Ti/TiB material is the main cause of premature fracture because pores serve as stress concentrators during tensile loading and hide the strengthening effect of boride particles during hardness testing. The strengthening potential of TiB particles cannot be used when the resulting composites exhibit excessive porosities.
Efforts to Reduce Porosities by Varying Blended Elemental Powder Metallurgy Processing Parameters
Since high porosity of sintered Ti/TiB composite porosities, incomplete TiB2 → TiB transformation, and non-uniform distribution of TiB crystals in the titanium matrix all contribute to property degradation, significant efforts were dedicated to improving as-sintered microstructures by varying press-and-sinter BEPM parameters. Smaller starting powders, higher temperatures, and longer sintering durations were tested. All such efforts are summarized in Table 1, taking Ti/8.4% TiB composite as an example. A basic set of parameters was taken, as described above.

TABLE 1. Microstructural characteristics of Ti/8.4% TiB composites produced with various press-and-sinter BEPM parameters.
Changing the types and sizes of starting powders did not result in a noticeable microstructural improvement. Since TiB2 powder is responsible for compromised densification, a finer starting TiB2 powder (<8 µm) was tested via dilatometric experiments (Figure 4, curve 4). Although the decreased boride powder size leads to some better shrinkage behavior at high temperatures (compare curves 3 and 4 in Figure 4), the final porosity is not considerably reduced (Table 1, #2). A minor decrease in as-sintered porosity is also observed in Stasiuk (2019) when smaller TiH2 powder particles are used (Table 1, #3). These experiments cannot reduce the average residual porosity below 5%–6%. As expected, the use of HDH titanium powder sieved to less than 100 µm (i.e., with a particle size distribution similar to that of the TiH2 powder presented in Figure 1) results in even worse densification, similar to that observed in Baglyuk et al. (2017), and an increase in residual porosity to 9% for the Ti/8.4% TiB composite (Table 1, #6).
Increasing the temperature to 1,350°C and extending the sintering cycle duration to 8 h has a minor effect on porosity reduction (Table 1, #4–#5), while completion of TiB formation improves only slightly. To conclude, substantial improvement of Ti/TiB composite microstructures requires a different technique that includes more revolutionary changes to the manufacturing process.
Production of Low-Porosity Composites via the Blended Elemental Powder Metallurgy + pre-alloyed Double Hydrogenation/Double Sintering Method
The idea for this process modification comes from the relatively good Ti/TiB composite PA powder metallurgy results in Tamirisakandala et al. (2004). It has already been mentioned that the disadvantage of the PA approach is that it requires melting for powder fabrication and further complex operations to consolidate hard, crystallized powders. In contrast, processing can be simplified significantly if the above-described BEPM solid-state sintered Ti/TiB composites are used as a specific grade of PA material for further production of PA powders and these resulting PA powders are then used in a second press-and-sinter stage.
In two-stage BEPM + PA processing, the non-uniform Ti/TiB obtained during the first sintering stage is further mixed via crushing. This promotes better boride-phase distribution uniformity in the resulting PA powder. Moreover, the absence of the TiB2 → TiB reaction during subsequent sintering of the PA powder can improve densification as compared to the initial TiH2 + TiB2 powder blends. However, the problem with this processing route is the insufficient sintered Ti/TiB composite crushing ability. This hinders the production of PA powders of desirable sizes. Despite the considerable porosities of the Ti/TiB composites produced during the first sintering stage and the presence of brittle boride particles, the titanium matrix plasticity allows the material to be deformed instead of crushed. Transformation of bulk as-sintered product into PA powders smaller than 100 µm requires long, intensive milling processes that lead to excessive contamination of the powders.
Hydrogenation of the Ti/TiB composite obtained during the first sintering stage was proposed to overcome the problems described above. This operation was intended to be the main feature of the modified process. Hydrogenation would make the Ti/TiB composite material brittle and reduce its strength, just as it affects titanium. Non-uniform, porous composite materials saturated with hydrogen would be crushed easily into composite powders of desirable sizes. Utilization of a hydrogenated, pre-alloyed powder in a second press-and-sinter stage would promote a positive influence of hydrogen on densification and hydrogen cleaning of powder once more to produce uniform, low-porosity composite structures. This approach is validated via the experimental results described below.
The Ti/TiB material hydrogenation process was thoroughly investigated and optimized based on Sieverts method, which demonstrated active hydrogen consumption above 425°C. The Ti/TiB composite obtained by sintering of the TiH2 + 5 wt% TiB2 blends (1,250°C for 4 h) was saturated with hydrogen at 600°C and 0.6 MPa. Thus, the titanium matrix reverts to a δ-TiHX lattice structure according to the X-ray data. The substantial volume change associated with this leads to stress accumulation and crack nucleation in the bulk sintered composites. As shown in Figure 5, wide cracks extend throughout the sintered compacts and fractures form and grow along intergranular positions.
Because of the brittle, low-strength nature of the hydride composite and ceramic reinforcement of the titanium boron compound, the sintered compacts were readily broken up and ground into powders with desirable dimensions after quick (10 s) milling in a planetary mill. Figure 6 shows the resulting hydrogenated pre-alloyed powders after milling. The particles of irregular morphologies are fractured during further compaction and mechanically locked to each other with the formation of dense compacts via close powder stacking. Furthermore, large TiB whiskers and incompletely reacted remnants of the initial TiB2 powders are crushed and blended with the matrix phases, creating a prerequisite for the complete formation and homogeneous distribution of the titanium monoboride phase during the second sintering stage. The resulting PA powder was pressed into compacts at 600 MPa and sintered again using the same parameters (1,250°C for 4 h) to form the final Ti/TiB composite.
Neither TiB2 nor other Ti-B phases were identified after the second sintering step (Figure 3). The intensities of the TiB peaks are enhanced after the second sintering step. This indicates that transformation to TiB is complete. Titanium hydride phases are not found in the composite after the second sintering step. This demonstrates that hydrogen has completely escaped from the base material during heating. The above X-ray findings are in accordance with our microstructure observations.
As shown in Figure 7, after hydrogenation of pre-sintered material and the second press-and-sinter operation, porosity is reduced from over 7.5% to nearly 2.2%, which is acceptable. The density improvement from 4.16 to 4.41 g/cm3 corroborates this observation. The average pore size also decreases. This promising result is in line with dilatometric studies where hydrogenated, pre-alloyed powder compacts (Figure 4, curve 5) exhibit shrinkage trends similar to those for pure TiH2 (curve 1). Hydrogen desorption from hydrogenated, pre-alloyed Ti/TiB compacts is observed at the same temperature range as for titanium hydride powder (300–700°C) and results in analogous compact shrinkage during dehydrogenation (curves 5 and 1 in Figure 4). The apparent shrinkage difference between curve 5 and curves 2–4 demonstrates that the considerably more intense densification of the hydrogenated pre-alloyed powder compact naturally results in low residual porosities after isothermal exposure at 1,250°C. The presence of boron mainly as a TiB phase embedded into hydrogenated titanium powder provides better densification kinetics than those observed with the TiB2 + TiH2 powder blend during dehydrogenation (curves 5 and 2 in Figure 4). The absence of a pronounced Ti + TiB2 → 2TiB reaction above 900°C in the pre-alloyed Ti/TiB compact minimizes factors that negatively affect densification and reduce porosity.
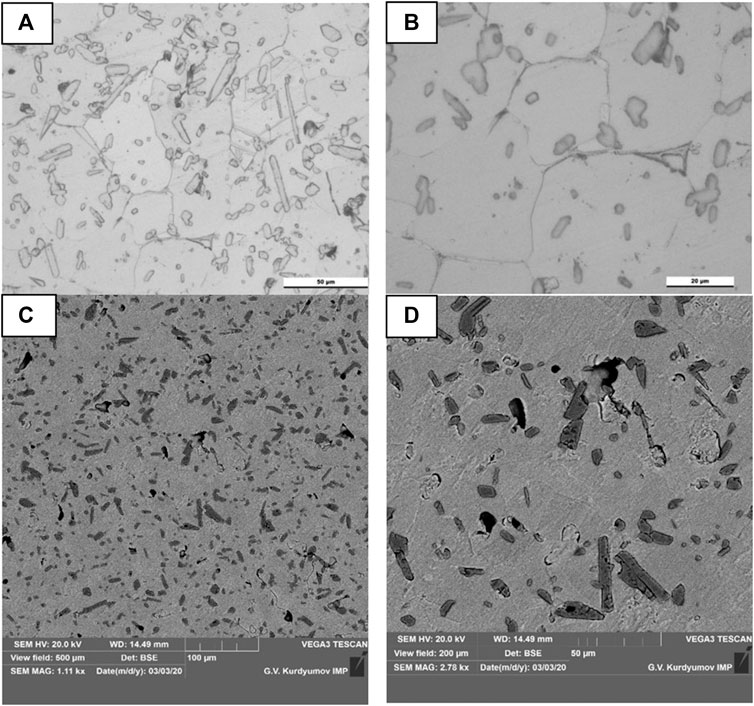
FIGURE 7. Low-porosity microstructure of the Ti/8.4 vol% TiB composite after a second sintering stage performed at 1,250°C for 4 h.
The second sintering stage improves the TiB reinforcement distribution uniformity in the Ti matrix considerably and produces a grain size of approximately 40 µm (Figure 7). Finer TiB particles are attained and uniformly distributed among the α-Ti grains in equiaxial or whisker morphologies, as shown in Figure 7. The markedly reduced residual porosity is observed with few voids near single TiB particulates (Figure 7D). The two-stage hydrogen-assisted processing schematically summarized in Figure 8 significantly contributes to the tailored microstructures and composite homogeneity.
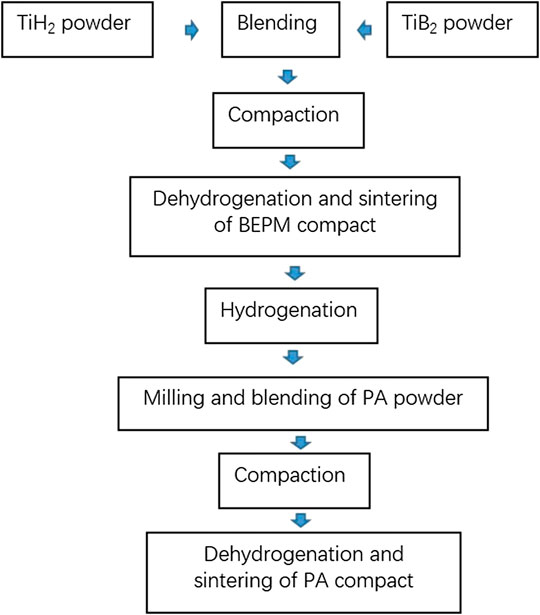
FIGURE 8. Scheme of the two-stage BEPM + PA press-and-sinter manufacturing process used to make Ti/TiB composites.
Vickers hardness tests were carried out using a Wolpert Wilson 452 SVD hardness meter in order to provide preliminary evaluations of the mechanical properties of the Ti/8.4 vol% TiB composites fabricated using the present approach. The hardness values obtained demonstrate that the proposed hydrogen-assisted two-stage BEPM + PA approach contributes to a nearly 50% increase in hardness (390–410 HV) relative to the traditional one-step BEPM press-and-sinter route (260–270 HV). This is a clear reflection of the finer grain size, minimized residual porosity, and better TiB redistribution uniformity in Ti/TiB composites fabricated via the hydrogen-assisted BEPM + PA technique. The Ti/TiB composite hardness values suggest the feasibility of this manufacturing approach for practical use.
Conclusions
(1) BEPM press-and-sinter manufacturing of Ti/TiB composites using TiH2 + TiB2 powder blends results in highly porous structures, non-uniform distribution of borides throughout the titanium matrix, and incomplete in-situ transformation of TiB2 into the TiB phase. Addition of TiB2 particles to TiH2 powder hinders densification kinetics because of the loss of compact integrity that results from differences in the powder constituent volume changes that occur during the hydrogen emission stage. Development of a high-temperature in-situ Ti + TiB2 → TiB reaction is another reason for poor densification.
(2) The microstructures of BEPM-produced Ti/TiB composites could not be markedly improved via optimization of press-and-sinter processing parameters, such as powder size or the sintering time-temperature regime.
(3) A new approach was developed based on the hydrogen-assisted two-stage press-and-sinter BEPM + PA method. The microstructurally and chemically non-uniform, highly porous Ti/TiB composite received after the first sintering stage was hydrogenated again to produce PA powder. The second stage of processing focuses on sintering the hydrogenated PA powder. This finally produces a Ti/TiB composite with improved densification kinetics, as well as the desired chemistry and microstructure.
Data Availability Statement
The raw data supporting the conclusions of this article will be made available by the authors, without undue reservation.
Author Contributions
YS and OS conceived and designed the study and experiment plan and performed the experiments. YS wrote the paper. YS and SD analyzed the experiment result. DS and OI reviewed and edited the manuscript. All authors read and approved the manuscript.
Funding
This study was funded by Jilin University, China and the National Academy of Sciences of Ukraine.
Conflict of Interests
The authors declare that the research was conducted in the absence of any commercial or financial relationships that could be construed as a potential conflict of interest.
The handling editor declared a past co-authorship with one of the authors OI.
References
Abkowitz, S., Abkowitz, S. M., Fisher, H., and Schwartz, P. J. (2004). CermeTi discontinuously reinforced Ti-matrix composites: manufacturing, properties, and applications. J. Mater. Sci. 56, 37–41. doi: 10.1007/s11837-004-0126-2. CrossRef Full Text
Baglyuk, G. A., Ivasyshyn, O. M., Stasyuk, O. O., and Savvakin, D. G. (2017). The effect of charge component composition on the structure and properties of titanium matrix sintered composites with high-modulus compounds. Powder Metall. Met. Ceram. 56, 45–52. doi: 10.1007/s11106-017-9870-z. CrossRef Full Text
Chandravanshi, V. K., Sarkar, R., Kamat, S. V., and Nandy, T. K. (2011). Effect of boron on microstructure and mechanical properties of thermomechanically processed near alpha titanium alloy ti-1100. J. Alloys Compd. 509, 5514. doi: 10.1016/j.jallcom.2011.02.114. CrossRef Full Text
Geng, K., Lu, W., Qin, Y., and Zhang, D. (2004). In situ preparation of titanium matrix composites reinforced with TiB whiskers and Y2O3 particles. Mater. Res. Bull. 39, 873–879. doi: 10.1016/j.materresbull.2003.11.008. CrossRef Full Text
Hayat, M. D., Singh, H., He, Z., and Cao, P. (2019). Titanium metal matrix composites: an overview. Compos. Appl. Sci. Manuf. 121, 418–438. doi: 10.1016/j.compositesa.2019.04.005. CrossRef Full Text
Hu, Y., Ning, F., Wang, X., Wang, H., Zhao, B., Cong, W., et al. (2017). Laser deposition-additive manufacturing of in situ TiB reinforced titanium matrix composites: TiB growth and part performance. Int. J. Adv. Manuf. Technol. 93, 3409–3418. doi: 10.1007/s00170-017-0769-0. CrossRef Full Text
Huang, L. J., Geng, L., and Peng, H.-X. (2015). Microstructurally inhomogeneous composites: is a homogeneous reinforcement distribution optimal? Prog. Mater. Sci. 71, 93–168. doi: 10.1016/j.pmatsci.2015.01.002. CrossRef Full Text | Google Scholar
Ivasishin, O. M., Bagliuk, G. A., Stasiuk, O. O., and Savvakin, D. G. (2017). The peculiarities of structure formation upon sintering of TiH2+TiВ2 powder blends. Phys. Chem. Solid State. 18, 15–20 | Google Scholar.
Ivasishin, O. M., Cherepin, V. T., Kolesnik, V. N., and Gumenyak, N. M. (2010). An automated dilatometric system. Instrum. Exp. Tech. 53, 457–460. doi: 10.1134/s0020441210030255. CrossRef Full Text
Ivasishin, O. M., Markovsky, P. E., Savvakin, D. G., Stasiuk, O. O., Rad, M. N., and Prikhodko, S. V. (2019). Multi-layered structures of Ti-6Al-4V alloy and TiC and TiB composites on its base fabricated using blended elemental powder metallurgy. J. Mater. Process. Technol. 269, 172–181. doi: 10.1016/j.jmatprotec.2019.02.006. CrossRef Full Text
Ivasishin, O. M., and Moxson, V. S. (2015). Low-cost titanium hydride powder metallurgy. Titanium Powder Metall. 2015, 117–148. doi: 10.1016/b978-0-12-800054-0.00008-3. CrossRef Full Text
Ivasishin, O. M., Savvakin, D. G., and Gumenyak, N. M. (2011). Dehydrogenation of powder titanium hydride and its role in the activation of sintering. Metallofiz. Noveish. Tekhnol. 33, 899–917 | .
Ivasishin, O. M., and Savvakin, R. G. (2010). The impact of diffusion on synthesis of high-strength titanium alloys from elemental powder blends. Key Eng. Mater. 436, 113–121. doi: 10.4028/www.scientific.net/kem.436.113. CrossRef Full Text
Morsi, K., and Patel, V., V. (2007). Processing and properties of titanium–titanium boride (TiBw) matrix composites—a review. J. Mater. Sci. 56, 42–48 | .
Kumar, M. S., Chandrasekar, P., Chandramohan, P., and Mohanraj, M. (2012). Characterisation of titanium–titanium boride composites processed by powder metallurgy techniques. Mater. Char. 73, 43–51 | .
Li, S., Kondoh, K., Imai, H., Chen, B., Jia, L., and Umeda, J. (2016). Strengthening behavior of in situ -synthesized (TiC-TiB)/Ti composites by powder metallurgy and hot extrusion. Mater. Des. 95, 127–132. doi: 10.1016/j.matdes.2016.01.092. CrossRef Full Text
Panda, K. B., and Chandran, K. S. R. (2003). Synthesis of ductile titanium-titanium boride (Ti-TiB) composites with a beta-titanium matrix: the nature of TiB formation and composite properties. Metall. Mater. Trans., 34, 1371–1385. doi: 10.1007/s11661-003-0249-z. CrossRef Full Text
Prasad, K., Sarkar, R., Ghosal, P., Satyanarayana, D. V. V., Kamat, S. V., and Nandy, T. K. (2011). Tensile and creep properties of thermomechanically processed boron modified timetal 834 titanium alloy. Mater. Sci. Eng. A 528, 6733–6741. doi: 10.1016/j.msea.2011.05.069. CrossRef Full Text
Saito, T. (2004). The automotive application of discontinuously reinforced TiB-Ti composites. J. Mater. Sci. 56 (5), 33–36. doi: 10.1007/s11837-004-0125-3. CrossRef Full Text
Sarkar, R., Ghosal, P., Nandy, T. K., and Ray, K. K. (2013). Structure-property correlation of a boron and carbon modified as castβtitanium alloy. Phil. Mag. 93, 1936–1957. doi: 10.1080/14786435.2013.765979. CrossRef Full Text
Savvakin, D. H., Humenyak, M. M., Matviichuk, M. V., and Molyar, O. H. (2012). Role of hydrogen in the process of sintering of titanium powders. Mater. Sci. 47 (5), 651–661. doi: 10.1007/s11003-012-9440-y. CrossRef Full Text
Gorsse, S., and Miracle, D. B. (2003). Mechanical properties of Ti-6Al-4V/TiB composites with randomly oriented and aligned TiB reinforcements. Acta Mater. 51, 2427–2442. doi: 10.1016/s1359-6454(02)00510-4. CrossRef Full Text
Singh, H., Hayat, M., Zhang, H., Das, R., and Cao, P. (2019). Effect of TiB2 content on microstructure and properties of in situ Ti-TiB composites. Int. J. Miner. Metall. Mater. 26, 915–924. doi: 10.1007/s12613-019-1797-6. CrossRef Full Text
Stasiuk, О. О. (2019). The general laws of high-modulus refractory compounds influence on structure and properties of sintered titanium alloys. Dissertation (Kyiv: National Technical University of Ukraine, Ihor Sikorsky Kyiv Polytechnical Institute) | .
Tamirisakandala, S., Bhat, R. B., Ravi, V. A., and Miracle, D. B. (2004). Powder metallurgy Ti-6Al-4V-xB alloys: processing, microstructure, and properties. J. Mater. Sci. 56 (5), 60–63. doi: 10.1007/s11837-004-0131-5. CrossRef Full Text
Tamirisakandala, S., and Miracle, D. B. (2010). Microstructure engineering of titanium alloys via small boron additions. Int. J. Adv. Eng. Sci. Appl. Math. 2, 168–180. doi: 10.1007/s12572-011-0033-z. CrossRef Full Text
Tjong, S. C., and Mai, Y.-W. (2008). Processing-structure-property aspects of particulate- and whisker-reinforced titanium matrix composites. Compos. Sci. Technol. 68, 583–601. doi: 10.1016/j.compscitech.2007.07.016. CrossRef Full Text
Yamamoto, T., Otsuki, A., Ishihara, K., and Shingu, P. H. (1997). Synthesis of near net shape high density TiB/Ti composite. Materials Science and Engineering: A, 239-240, 647–651. doi: 10.1016/s0921-5093(97)00643-6. CrossRef Full Text
Yang, C., Kang, L. M., Li, X. X., Zhang, D. T., Fu, Z. Q., et al. (2017). Bimodal titanium alloys with ultrafine lamellar eutectic structure fabricated by semi-solid sintering. Acta Mater. 132, 491–502. doi: 10.1016/j.actamat.2017.04.062. CrossRef Full Text
Zhang, L. C., and Chen, L. Y. (2019). A review on biomedical titanium alloys: recent progress and prospect. Adv. Eng. Mater. 21, 1801215. doi: 10.1002/adem.201801215. CrossRef Full Text
Keywords: titanium matrix composite, titanium boride, blended elemental powder metallurgy, hydrogenation, densification, microstructure
Citation: Song Y, Dong S, Stasiuk O, Savvakin D and Ivasishin O (2020) Synthesis of Ti/TiB Composites via Hydrogen-Assisted Blended Elemental Powder Metallurgy. Front. Mater. 7:572005. doi: 10.3389/fmats.2020.572005
Received: 15 June 2020; Accepted: 30 September 2020;
Published: 11 November 2020.
Edited by:
Chao Yang, South China University of Technology, ChinaReviewed by:
Liang-Yu Chen, Jiangsu University of Science and Technology, ChinaDeliang Zhang, Northeastern University, China
Copyright © 2020 Song, Dong, Stasiuk, Savvakin and Ivasishin. This is an open-access article distributed under the terms of the Creative Commons Attribution License (CC BY). The use, distribution or reproduction in other forums is permitted, provided the original author(s) and the copyright owner(s) are credited and that the original publication in this journal is cited, in accordance with accepted academic practice. No use, distribution or reproduction is permitted which does not comply with these terms.
*Correspondence: Yuchao Song, c29uZ3ljMTlAbWFpbHMuamx1LmVkdS5jbg==