- Advanced Steel Processing and Products Research Center, Metallurgical and Materials Engineering Department, Colorado School of Mines, Golden, CO, United States
Forming operations are known to be complex, involving many strain states, strain rates, temperatures, strain paths, and friction conditions. Material properties, such as strength and ductility, are large drivers in determining if a material can be formed into a specific part, and for selecting the equipment required for the forming operation. Predicting yielding behavior in situations such as these has been done using yield surfaces to describe material yielding in specific stress states. These models typically use initial mechanical properties, and will require correction if the material has experienced previous straining. Here, we performed interrupted uniaxial tensile testing of a 304 stainless steel to observe the effects of unloading and subsequent reloading on yielding and tensile properties. An increase in yield point developed, in which a higher yield was observed prior to returning to the bulk work hardening behavior, and the magnitude of the yield point varied with unloading conditions and strain imposed. The appearance of a yield point is attributed to strain aging or dislocation trapping at obstacles within the matrix. These results suggest that both strain aging and dislocation trapping mechanisms may be active in the matrix, which may present challenges when forming austenitic stainless and new advanced high strength steels that likely show a similar behavior. These results provide a potential area for refinement in the calculation of yielding criteria that are currently used to predict forming behavior.
1 Introduction
As multi-phase, complex microstructures are increasingly used to achieve strength and ductility targets, the deformation response of advanced high strength steels becomes more complicated and may deviate from expected with respect to temperature (Tsuchida et al., 2011; Coryell et al., 2013), strain rate (Zou et al., 2017), and strain state (Zou et al., 2018). Further, complex operations often involve varying strain states, strain rates, friction conditions, temperatures, and multiple, non-linear deformation steps. The newest generation of advanced high strength steels are increasingly difficult to form, because the higher strength requires presses with higher tonnages, and decreased ductility may cause the part to fail during a forming operation (Billur and Altan, 2012).
The yielding response of metals has been defined using criteria, such as the Hill (1948), Tresca (1864), or Mises (1913), that allow engineers to predict when a material will yield based on the stress state. These criteria focus largely on material that has not experienced straining in various directions prior to deformation. The criteria for yielding have been adapted for the Bauschinger effect and changing the strain path of the test (Naghdi et al., 1957; Holmedal, 2019) showing that prior deformation will change the shape and location of the yield surface. The presence of path-dependent yield behavior requires an in-depth analysis of the yield surface to be used in operations in which material undergoes multiple stages of deformation. This is further complicated by yielding behavior tied to experimental variables, such as testing temperature and strain rate.
In experiments done by Mendiguren et al., the loading/unloading mechanical behavior was observed for a TRIP700 steel (Mendiguren et al., 2015). During testing, an upper yield point was observed and explained by strain aging and the Snoek phenomenon, which is the stress induced redistribution of interstitial atoms in a body centered cubic lattice. Similar yielding behavior was also observed by Rathbun et al. and Lichtenfeld et al. in metastable austenitic stainless steels, which was explained by strain aging (Rathbun et al., 2000) and adiabatic heating of the samples (Lichtenfeld et al., 2006). Haasen and Kelly also observed this behavior in face centered cubic materials, and explained the phenomena by the pinning and unpinning of dislocations at short range barriers in the microstructure (Haasen and Kelly, 1957).
304 stainless-steel is a metastable austenitic stainless-steel; during deformation the austenite may transform to martensite due to a deformation induced transformation. This transformation is characterized by the TRansformation Induced Plasticity (TRIP) effect, which is known to increase the work hardening rate while accommodating strain thereby, delaying necking and improving the strength and ductility. TRIP is influenced by many factors, including the imposed strain state, as well as the direction of straining (Streicher et al., 2002; Alturk et al., 2018; Zou et al., 2018). In a study done by Streicher et al., a TRIP780 steel exhibited differing amounts of retained austenite transformation during straining in different strain states relative to the rolling direction, showing an increase in amount of martensite formed as a function of strain (Streicher et al., 2002). In a recent study by Finfrock et al., the amount of retained austenite transformation was dependent on the strain state relative to the rolling direction (Finfrock et al., 2020). The amount of transformation from austenite to martensite has also been shown to be dependent on strain state in 304 stainless-steel, with biaxial tension transforming more austenite than uniaxial tension (Hecker et al., 1982).
2 Materials and Methods
A 0.90 mm sheet of 304 stainless-steel that was cold rolled and fully annealed to develop a fully austenitic equiaxed microstructure with an average austenite grain size of 13 μm (Lewis, 1999). The 304 stainless-steel was waterjet cut into ASTM E8 subsize tensile specimens with a 25.4 mm gauge length. The composition of the steel is given in Table 1.
Specimens were removed from both the rolling direction (RD) and transverse direction (TD). After cutting, samples were used for interrupted tensile testing. The interrupted testing consisted of deforming the sample in tension at a strain rate of 0.001 s−1 on an MTS® Alliance® 20 kip uniaxial electromechanical load frame. Two samples were pulled to failure in both the TD and RD to establish baseline properties. Additional samples from each direction were used for interrupted tensile testing. Interrupted tests were performed with incremental cross-head displacements of nominally 1.5 mm (3 pct strain) below 15 pct total strain, and 3 mm (7 pct strain) above 15 pct total strain. Samples were then either unloaded and removed from the frame for a room temperature isothermal hold, unloaded and immediately reloaded to start the next straining increment, or unloaded partially and immediately reloaded to the next straining increment.
3 Results
The 304 stainless steel exhibited a difference in monotonic tensile properties along the RD and TD, as shown in the true stress-true strain and instantaneous strain hardening exponent (ni) plots presented in Figure 1. The instantaneous strain hardening rate was evaluated until the onset of necking using Equation 1 (Dieter, 1976)
where σ is the true stress and ϵ is the true strain. The instantaneous strain hardening rate increasing with strain indicates the TRIP effect active. After establishing the properties of the steel under monotonic loading, one sample in each direction was interrupted during tensile testing at various strains.
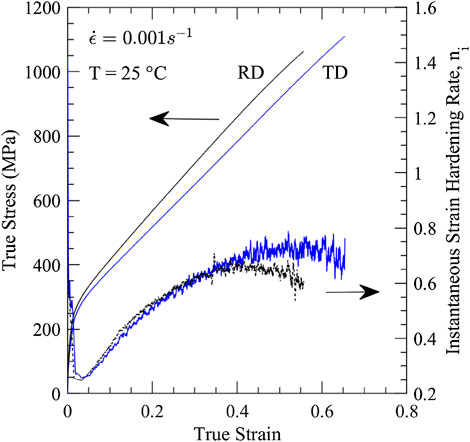
FIGURE 1. Baseline mechanical properties of a 304 stainless-steel in the rolling (RD) and transverse (TD) directions of the sheet with instantaneous strain hardening exponent (ni) plotted to the onset of necking. The mechanical properties of the steel vary with orientation relative to the rolling direction, and there is significant strain hardening in the samples due to the TRIP effect.
Figure 2 shows the engineering stress vs. strain results of the samples interrupted in the RD (Figure 2A) and TD (Figure 2B) with respect to the baseline mechanical properties. For the interrupted tests, a yield point begins to develop with increasing strain. This behavior is characterized by an initially higher yield stress, followed by a constant or negative strain hardening rate, and then finally a return to the flow behavior associated with the monotonically loaded sample. The change in stress was measured as the difference between the stress value observed during reloading and the value that is observed at the same total strain in a monotonic test.
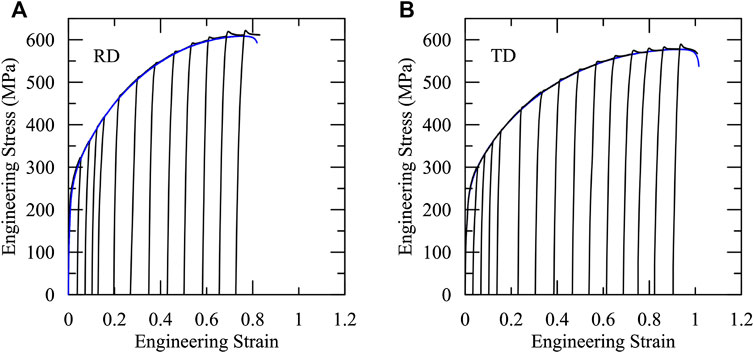
FIGURE 2. Engineering stress vs engineering strain of a 304 stainless-steel in the (A) rolling direction and (B) transverse direction from monotonic and interrupted tests. Tests were performed at room temperature and a strain rate of 0.001 s−1. The interrupted tests were fully unloaded and held at room temperature prior to reloading.
The difference in yielding behavior is defined as
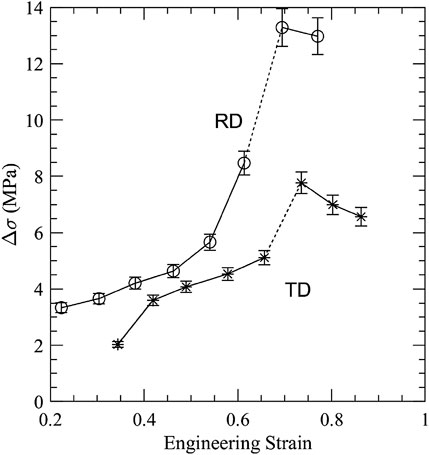
FIGURE 3. Change in yielding (
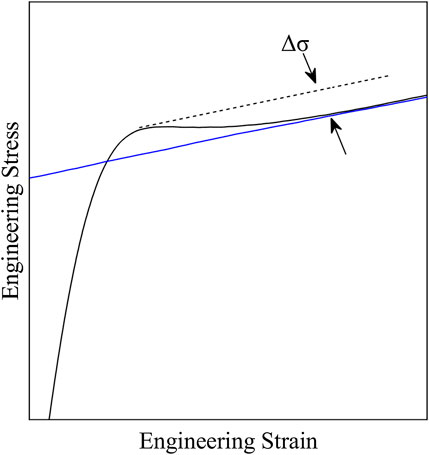
FIGURE 4. Change in yielding (
This calculation was also performed for the samples that were fully unloaded with no hold time before reloading (Figure 5), and samples that were partially unloaded (45 kg, less than 2 pct of the max load) and immediately reloaded with no isothermal room temperature hold (Figure 6).
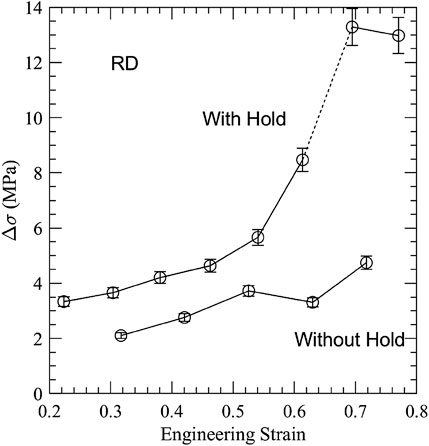
FIGURE 5. Change in yielding of a 304 stainless steel during interrupted tensile testing performed at room temperature and a strain rate of 0.001 s−1, with and without an isothermal hold between straining steps.
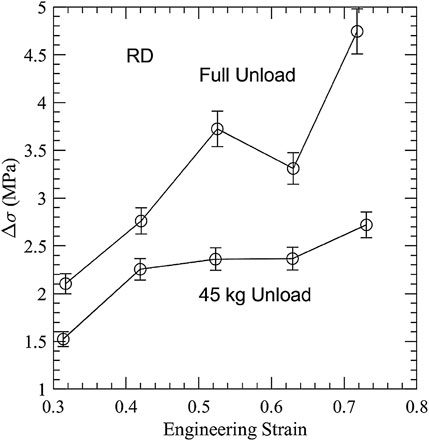
FIGURE 6. Change in yielding of a 304 stainless steel during interrupted tensile testing performed at room temperature and a strain rate of 0.001 s−1, with a full unload and partial unload between straining steps without an isothermal hold at room temperature.
4 Discussion
The 304 stainless-steel exhibited similar mechanical properties when subjected to interrupted straining, demonstrating strength and ductility levels equivalent to the properties when tested monotonically, with the exception of the yield point that occurred during some interrupted tests.
Interrupted straining showed that a yield point developed as strain increased, and increased in magnitude as strain increased. This yield point was similar to the phenomena reported by Haasen et al. during interrupted testing of pure single crystal face center cubic aluminum and nickel (Haasen and Kelly, 1957). Likewise, yield points bore resemblance to those presented by Rathbun et al. and Lichtenfeld et al. for 301, 302 (Rathbun et al., 2000), and 304 (Lichtenfeld et al., 2006) stainless steel. Rathbun et al. indicated that strain aging occurred at ambient temperature in 301 and 302 stainless steels and exhibited similar behaviors during straining, however strain aging was only present when deformation induced martensite existed in the microstructure (Rathbun et al., 2000). Lichtenfeld et al. attributed the yield point phenomena seen in 304 stainless steels at strain rates of 0.125 s−1 and 1.25 × 10−4 s−1 to a testing artifact (Lichtenfeld et al., 2006), and indicated that the actuator used for testing applied an anomalously high strain rate for a short period of time, which caused a temporary loss in the closed loop control, resulting in an artificially high strain rate, and therefore yield stress. The authors also claimed that strain aging did not occur; rather, any potential yield points were attributed to the thermal softening of austenite due to deformation induced heating, causing the yield stress to be higher upon reloading than it would be in a monotonic test in which heat was not dissipated (Lichtenfeld et al., 2006). In this study, the samples that were reloaded immediately at a rate of 0.001 s−1 exhibited a yield point which was comparable to the yield points of samples that were held at room temperature. This suggest that thermal softening due to specimen heating was not a valid explaination for the yield points observed here. This temperature increase is negligible, therefore the samples likely did not see significant heating during straining. It should be noted that the samples immediately reloaded exhibited
A model of the amount of work converted to heat during deformation was used to calculate the expected temperature of the samples. This model does not account for any heating due to the exothermic austenite to martensite transition. The predicted temperature of the sample is given by Andrade-Campos et al. (2010).
where TRT is the ambient temperature (21.4°C), ρ is the density of the steel and has the value of 7,860 kg m−3 (Callister, 2007), C is the specific heat of the steel and has the value of 495 J°C−1 kg−1 (Callister, 2007), and
Both a change in properties due to a hold and due to an unload are relevant to forming operations, as they may be designed to be multi-step, or to vary the load at specific locations within the part to allow for material flow. Though, an increase in yielding may cause higher local stresses needed for a part to be plastically deformed after initial straining. The stresses observed in interrupted testing were up to a 3 pct increase in stress required for deformation, which may cause the strain distribution of the part to vary from what it was intended due to local flow stress changes.
5 Conclusion
Interrupting and changing strain path in an austenitic stainless-steel introduces a yield point that has been attributed to strain aging and adiabatic heating in literature and resembles the Haasen-Kelly effect. Based on a model from literature, the samples were expected to accumulate less than 2°C during interrupted straining, which does not support the yield point being due to sample heating during deformation. The samples did show a time dependence on the magnitude of the yield point exhibited, as well as a dependence on the amount of unloading that occurred during testing. Based on the results shown, the yield point may be due to a combination of the Haasen-Kelly effect and strain aging of the sample. The increase in yield stress observed can cause up to a 3 pct increase in stress required for deformation, which may have implications during multi-step forming operations. This behavior provides a potential area of improvement for yield criteria, because sequential loading and unloading changes the subsequent deformation behavior in a way that has not been accounted for in existing yield criteria.
Data Availability Statement
The raw data supporting the conclusions of this article will be made available by the authors, without undue reservation.
Author Contributions
MT conceptualization, formal analysis, investigation, writing - original draft, visualization. CF investigation, writing - review and editing. AC writing - review and editing, supervision. KC writing - review and editing, supervision.
Funding
This program is supported by NSF Award 1752530, Career: Controlling Austenite Stability and Response During Deformation of Advanced High Strength Steels, through the Division of Civil, Mechanical and Manufacturing Innovation and the Advanced Steel Processing and Products Steel Center at the Colorado School of Mines.
Conflict of Interest
The authors declare that the research was conducted in the absence of any commercial or financial relationships that could be construed as a potential conflict of interest.
Acknowledgments
The authors would like to acknowledge Trevor Ballard and Kayla Molnar for their input and aid in mechanical testing as well as the Advanced Steel Processing and Products Research Center at the Colorado School of Mines for their support.
References
Alturk, R., Hector, L. G., Enloe, C. M., Abu-Farha, F., and Brown, T. W. (2018). Strain rate effect on tensile flow behavior and anisotropy of a medium-manganese trip steel. JOM. 70, 894–905. doi:10.1007/s11837-018-2830-3
Andrade-Campos, A., Teixeira-Dias, F., Krupp, U., Barlat, F., Rauch, E., and Grácio, J. (2010). Effect of strain rate, adiabatic heating and phase transformation phenomena on the mechanical behaviour of stainless steel. Strain. 46, 283–297. doi:10.1111/j.1475-1305.2008.00572.x
Billur, E., and Altan, T. (2012). Challenges in forming advanced high strength steels. Proc. New Develop. Sheet Met. Form., 285–304.
Callister, W. D. (2007). Materials science and engineering an introduction. New York, NY: John Wiley.
Coryell, J., Savic, V., Hector, L., and Mishra, S. (2013). Temperature effects on the deformation and fracture of a quenched-and-partitioned steel. Tech. rep. [Equb ahead of print].doi:10.4271/2013-01-0610
Finfrock, C. B., Clarke, A. J., Thomas, G. A., and Clarke, K. D. (2020). Austenite stability and strain hardening in c-mn-si quenching and partitioning steels. Metall. Mater. Trans. 51, 2025–2034. doi:10.1007/s11661-020-05666-8
Haasen, P., and Kelly, A. (1957). A yield phenomenon in face-centered cubic single crystals. Acta Metall. 5, 192–199. doi:10.1016/0001-6160(57)90165-7
Hecker, S., Stout, M., Staudhammer, K., and Smith, J. (1982). Effects of strain state and strain rate on deformation-induced transformation in 304 stainless steel: part i. magnetic measurements and mechanical behavior. Metall. Trans. A. 13, 619–626. doi:10.1007/BF02644427
Hill, R. (1948). A theory of the yielding and plastic flow of anisotropic metals. Proc. Roy. Soc. Lond. Math. Phys. Sci. 193, 281–297. doi:10.1098/rspa.1948.0045
Holmedal, B. (2019). Bauschinger effect modelled by yield surface distortions. Int. J. Plast. 123, 86–100. doi:10.1016/j.ijplas.2019.07.009
Lewis, D. T. (1999). Influence of compositional variation on deformation induced martensite formation in type 304 stainless steels. PhD thesis. Golden, CO: Colorado School of Mines, Arthur Lakes Library.
Lichtenfeld, J. A., Van Tyne, C. J., and Mataya, M. C. (2006). Effect of strain rate on stress-strain behavior of alloy 309 and 304l austenitic stainless steel. Metall. Mater. Trans. 37, 147–161. doi:10.1007/s11661-006-0160-5
Mendiguren, J., Cortés, F., Gómez, X., and Galdos, L. (2015). Elastic behaviour characterisation of trip 700 steel by means of loading–unloading tests. Mat. Sci. Eng. A. 634, 147–152. doi:10.1016/j.msea.2015.03.050
Mises, R. v. (1913). Mechanics of solid bodies in the plastically-deformable state. Göttin Nachr. Math. Phys. 1, 582–592.
Naghdi, P. M., Essenburg, F., and Koff, W. (1957). An experimental study of initial and subsequent yield surfaces in plasticity. Technical Report. (Accessed August 27, 2020).
Rathbun, R., Matlock, D., and Speer, J. (2000). Strain aging behavior of austenitic stainless steels containing strain induced martensite. Scripta Materialia. 42, 887–891. doi:10.1016/S1359-6462(00)00308-0
Streicher, A. M., Speer, J. G., and Matlock, D. K. (2002). Forming response of retained austenite in a c-si-mn high strength trip sheet steel. Steel Res. 73, 287–293. doi:10.1002/srin.200200210
Tresca, H. (1864). Memoire sur l’écoulement des solides à de forte pressions. Acad. Sci. Paris. 2, 59.
Tsuchida, N., Morimoto, Y., Tonan, T., Shibata, Y., Fukaura, K., and Ueji, R. (2011). Stress-induced martensitic transformation behaviors at various temperatures and their trip effects in sus304 metastable austenitic stainless steel. ISIJ Internat. 51, 124–129. doi:10.2355/isijinternational.51.124
Zou, D., Li, S., He, J., Gu, B., and Li, Y. (2018). The deformation induced martensitic transformation and mechanical behavior of quenching and partitioning steels under complex loading process. Mat. Sci. Eng.: A. 715, 243–256. doi:10.1016/j.msea.2018.01.011
Keywords: sheet forming, strain path, yield point, advanced high strength steel, deformation behavior, yield surface
Citation: Thrun M, Finfrock C, Clarke A and Clarke K (2021) Effects of Unloading on Subsequent Yielding Behavior in 304 Stainless Steel. Front. Mater. 7:615361. doi: 10.3389/fmats.2020.615361
Received: 08 October 2020; Accepted: 16 November 2020;
Published: 22 January 2021.
Edited by:
Lijia Zhao, ArcelorMittal USA LLC, United StatesCopyright © 2021 Thrun, Finfrock, Clarke and Clarke. This is an open-access article distributed under the terms of the Creative Commons Attribution License (CC BY). The use, distribution or reproduction in other forums is permitted, provided the original author(s) and the copyright owner(s) are credited and that the original publication in this journal is cited, in accordance with accepted academic practice. No use, distribution or reproduction is permitted which does not comply with these terms.
*Correspondence: Melissa Thrun, bXRocnVuQG1pbmVzLmVkdQ==