- 1Faculty of Mechanical and Manufacturing Engineering, University Tun Hussein Onn Malaysia (UTHM), Parit Raja, Malaysia
- 2Al Muthana Water Directorate, General Directorate of Water, Ministry of Municipalities and Public Works, Baghdad, Iraq
- 3Faculty of Maritime Studies, Universiti Malaysia Terengganu, Terengganu, Malaysia
- 4Faculty of Mechanical and Manufacturing Engineering Technology, Universiti Teknikal Malaysia Melaka, Melaka, Malaysia
- 5Structural Integrity and Monitoring Research Group (SIMReG), Universiti Tun Hussein Onn Malaysia, Parit Raja, Malaysia
- 6Center of Excellence Geopolymer and Green Technology (CeGeoGTech), Universiti Malaysia Perlis (UniMAP), Kangar, Malaysia
- 7Department of Aerospace Engineering, Faculty of Engineering, Universiti Putra Malaysia, Serdang, Malaysia
- 8Laboratory of Biocomposite Technology, Institute of Tropical Forestry and Forest Products (INTROP), Universiti Putra Malaysia, UPM Serdang, Malaysia
- 9Aerospace Malaysia Innovation Centre (944751-A), Prime Minister's Department, MIGHT Partnership Hub, Jalan Impact, Cyberjaya, Malaysia
The use of metallic materials in automotive industry leads to increasing fuel consumption and cost, so trends are starting to use lighter and cheaper materials. In automotive applications, fibers are used in composites because they are stronger, stiffer, and lighter than bulk materials, and they can achieve higher energy absorbing compared to metallic materials. The purpose of this work is to study the potential utilization of natural fibers in the crash energy absorbing applications. The experimental procedures (the principle of a combination of manual layup and vacuum bladder technique) were applied to search the influence of utilizing jute fiber mat on crashworthiness parameters of composite materials with other kinds of fibers such as woven glass fiber reinforced epoxy composites. The study involved corrugated composite tubes with three layers of jute and hybrid glass-jute/epoxy material have been tested in uniaxial quasi-static crush conditions at the speed 10 mm/min. The results exhibit that the tube of jute fiber was somewhat lower than synthetic fibers, but the substitution of one layer of jute fiber with one layer of glass fiber resulted in an improvement in the crashworthiness parameters. As hybrid jute-glass was used, the best result was obtained, where energy absorption and specific energy absorption are improved by 17.75% and 25.122%, respectively.
Introduction
Synthetic fibers such as carbon and glass fibers reinforced plastics composites (FRPc) have been vastly applied in industries and transportation field due to their properties such as low density and good mechanical characteristics (Okubo et al., 2004; Summerscales et al., 2010). However, these fibers are neither recycled nor naturally decomposed; therefore, the researchers and manufactures have been trended to find natural materials as alternative due to increased ecological consciousness (Okubo et al., 2004). In recent years, focus has been on studying fibers based on natural sources. To name a few, hemp, Kenaf, flax, and jute have been well known for their mechanical properties (Summerscales et al., 2010). Apart from that, natural fibers possess lower weight, good specific strength, and lower cost, and most of all, they are available in abundance (Abosbaia et al., 2003; Mahdi et al., 2003b; Ismail et al., 2007; Lau, Said, and Yaakob 2012; Ismail and Che Abdul Aziz, 2015; Ismail, 2016; Ismail and Mohd Tobi, 2016).
In axial crushing of composites, less research on the use of natural fiber reinforced plastics has been performed. Meanwhile, carbon and glass fiber reinforced plastics are extensively investigated (Lau et al., 2012). Various shapes, geometries of structure, and kinds of failure modes that led to the different energy absorbing have been studied. According to Abosbaia et al. (2003) who have investigated the influence of segmented composites on the collapse behavior of cotton/epoxy composite structures, the filament winding method and different stacking sequences were adopted. As a result, the cotton/epoxy composite specimens showed a progressive failure under axial compression test with SEA value of 2.501 kJ/kg. Similar works were also studied in the literature by Mahdi et al. (2003a). Furthermore, a work by Ghoushji et al. (2017) tested the natural square ramie fibers/epoxy composite structures by applying various lengths. The study concluded that, with the increasing specimen length, an increase in the energy absorption capacity is produced. The maximum SEA value gained from the test was 4.841 kJ/kg. The report by Said et al. (2017) was on square-shaped kenaf/epoxy composite specimens. In their work, it was revealed that unidirectional fibers showed a better energy absorbing performance compared to the random orientation of the fibers. Besides, most of the unidirectional plies’ specimens exhibited stable crushing through progressive failure and recorded the highest of SEA by 22.4 kJ/kg. However, to this date, very limited researches have been done on the crashworthiness characterization of jute FRC tubes (Sivagurunathan et al., 2018b). Jute has caught a great attention to scientists and manufacturers due to its novel mechanical properties and environmentally friendly characteristics (Raghavendra et al., 2014). Besides, jute has been used in making intermediate and finishing goods such as clothing, souvenirs, and mats (Mishra & Biswas, 2013). Although jute possesses several great mechanical properties, it is rarely used in crashworthiness studies on composite structures.
From literature review, the type of fibers used in the tests affects the crashworthiness parameters. In spite of all the above tubes crushed progressively, specific energy absorption (SEA) of natural fiber reinforced composites was relatively low compared to carbon and glass fiber reinforced plastics which for cotton, ramie, and kenaf reinforced plastics composite were at 2.501, 4.841, and 22.400 kJ/kg, respectively. Therefore, to solve this problem, hybridization is considered the best option. The main idea is to make a balance between the high modulus fibers such as synthetic fibers that contribute to load bearing and stiffens and the materials with low modulus fibers such as natural fibers, which contribute to damage tolerance. This approach makes a balancing in stiffness, toughness, and strength with weight reduction. Then get a new specimen with best specification compared to both materials, which can absorb high EA. Through the synergistic effect of the fibers, a new material can be obtained with characteristics that differ from both of them and an improvement in the ability of the structure to absorb energy and the behavior of crashing during axial loading (Reddy et al., 2016).
In the current study, the use of bidirectional jute and hybrid glass-jute fiber in three layers was investigated to determine which is the most effective configuration in terms of SEA. Moreover, since many works have proven that tulip trigger (Palanivelu et al., 2010; Palanivelu et al., 2011; Sivagurunathan et al., 2018a) and corrugated tubes (Abdewi et al., 2008; Lau et al., 2012; Al-Qrimli et al., 2015) have highest effect on crashworthiness parameters values, they have been determined as constant.
Experimental Procedure
Specimen Geometry
Two kinds of specimens have been studied, hollow corrugated composite tubes. The two specimens were fabricated one by pure jute/epoxy and the other by hybrid jute-glass/epoxy. All specimens were made in the same conditions with a constant number of laminate layers equal to three. Details on the height (h), upper diameter (dup), and lower diameter (dlw) are given in Table 1 (please refer to Figure 1 for the notations utilized).
Materials and Configuration
Two kind of fibers were used in present work: the woven jute (plain weave, 1.44 g/cm3) was procured from Innovative Pultrusion Sdn. Bhd, Seremban, Malaysia, while woven glass fibers (plain weave, 2.55 g/cm3) were provided by University Tun Hussein Onn Malaysia (UTHM). Both kinds of fibers come in mat form with bidirectional fibers orientation of 0° and 90°.
In order to strengthen the fibers reinforcement, a resin matrix was utilized in current work. The catalyst used was a combination of Auto-Fix 1710-A epoxy resin and Auto-Fix 1345-B as hardener. The epoxy and hardener were supplied by Chemibond Corporation, Malaysia.
Two configurations were manufactured and tested in the same conditions in order to provide a means of comparison.
Preparation of the Mandrel
After the materials were prepared, the second phase began with the preparation of the mandrels. Corrugated geometry of mandrel has been used, which was made from aluminum metal in the workshop by CNC machine with height of 150 mm and external diameter of 50 mm as depicted in Figure 1. The mandrel was then wrapped by a layer of plastic to prevent the epoxy from sticking to the mandrel, which might affect the specimens through extraction.
Fabrication Process
The novel principle of a combination of manual layup and vacuum bladder technique was employed. Through the compression vacuum-bagging technique is used in present work. "Vacuum-bagging" is an advanced composite molding technique that used a pump to draw a vacuum over the composite laminate, allowing even atmospheric pressure to compact the laminate against the mold face and improve its performance. However, both specimens were fabricated with the fiber volume fraction of 60% (Shibata, Cao, and Fukumoto 2005). For facilitating the removal of the specimen from the mold, wiping the releasing agent on the surface of the mandrel was applied. The reinforced materials were trimmed to the proper size of the mold and then weighed for equivalent epoxy use of the layers. Epoxy and hardener were mixed at ratio 1:1 as per the supplier's instructions by an electric mixer. The electric mixer was used in order to prevent air bubble formation in a mixture. The epoxy resin was poured and spread by using a brush onto the jute layers and then wrapping the fibers around the mandrel. A steel roller was moved over each jute-epoxy layer under a mild press down to dispose air bubbles from the laminate and to obtain the required thickness. The peel/release ply, release film, and bleeder film were cut as per the mold size and placed on the surface of layers. The whole specimen was sealed by using a vacuum bag under constant vacuum pressure of 6 bars. Under vacuum, air bubbles were eliminated and the resin was distributed into composite laminate equally. The fabricated specimens were left to cure for 24 h at laboratory temperature (30°C ± 2%). After that, the specimens were extracted from the vacuum-bagging and mold. The postcuring was carried out by placing samples into a heat oven at 60°C for 8 h and 100 °C for 4 h. Finally, all tubes were cut into the required specimen size with a height of 100 mm by using bench saw; a tulip trigger was done by using an angle grinder for each one. This process was repeated four times for each specimen.
Weighing and Labeling
The specimens were weighed, and then nominations were used for the specimens before and after the crush to classify them, where (J) represents jute fibers mat, the (G) represents the woven glass fibers, and (H) represents hybrid fiber of (2 Jute + 1 Glass). As only one epoxy form was used, the matrix (epoxy) was not symbolized. Two kinds of composite constituents’ specimens have been studied, jute composite specimens (JCS) and hybrid composite specimens (HCS).
Testing Procedure
The samples tests were carried out by applying quasi-static uniaxial compression forces using an Autograph AG-X plus Shimadzu Universal Testing System with a loading of 100 kN at UTeM University, Melaka, Malaysia. The measurements were done based on ASTM: D7336M-16 with a stroke of 80 mm. The speed of the crosshead was 10 mm/min. Each specimen was placed on the lower fixed platen and the parallel platen started to crush axially. To ensure that the collected findings are consistent and accurate, five replicate tests were done for each configuration. Load and displacement test data were obtained by the automatic acquisition system to determine the crashworthiness parameters and absorb the energy of the designed specimens.
Characterization Methods
Crashworthiness Parameters
Crashworthiness is an important key parameter that must be taken into consideration when assessing the safety factor of structures. Besides, the collision energy is absorbed in a controlled failure mechanism by the gradual decay of the specimen under a compressive load. However, different indicators are available to assess the absorbing energy and crush characteristics of various structures (Mahdi and Sebaey, 2014b). These indicators will be computed and analyzed mathematically based on a load– (kN) displacement (mm) which is illustrated in Figure 2:
1. The peak load is the maximum sustained load that a particular specimen can endure before it undergoes failure during the elastic phase, which can be determined directly from the load-displacement diagram. Besides, peak load also determines how long the specimen can withstand before it completely fails.
2. The energy absorbing (EA) of a structure or body refers to its capability to do the work done and resistance to an external load. Within this context of the definition, the high-energy structure will be capable of deforming widely to dissipate the impact load (Sun et al., 2017). Total absorbed energy, EA, represents the area underneath the load-deformation diagram until the compaction region. It can be computed as follows:
where (δ) represent the displacement distance (mm) and p is the axial average load.
3. The mean load rate is one of the important indicators by which the energy absorption measuring of the tested specimen can be determined. It plays a main role in defining the characteristics of crashworthiness because the crushing efficiency represents the ratio of the mean load to the maximum peak load and therefore it is closely related to the increase or decrease of acceleration that will face the vehicle’s passengers in a collision event (Roslan et al., 2017). Pm can be computed by total energy absorption divided by deformation distance as follows:
4. The specific energy absorption (SEA) is due to the difference in material and weight of each specimen used in study. The evaluation through total energy absorption to determine the structure’s capability to dissipate energy stably may be misleading. Therefore, to make a more realistic comparison among the geometric specimens, it is based on the SEA (Mahdi and Sebaey, 2014b). SEA can be computed as follows:
where (W) represent crushed weight of tested specimen.
5. Crush efficiency (ɳc) is another significant indicator that needs to be taken into consideration in assessing the energy dissipation performance of the designed structure. It is calculated mathematically by dividing the average load over the maximum peak load, which is usually from zero to one. Therefore, the closer the efficiency is to a unit, it indicates that the performance is close to the ideal value. Thus it leads to an increase in deceleration during the collision event and increases safety probability to the object (Boria, Scattina and Belingardi 2018).
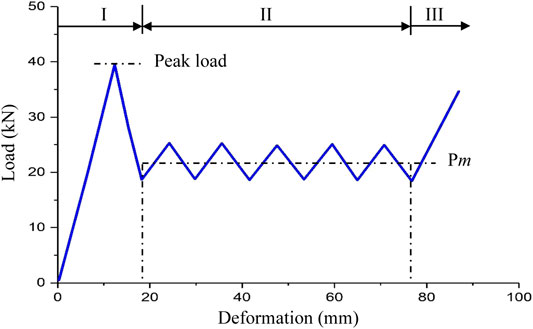
FIGURE 2. Typical force-displacement graph (Rabiee and Ghasemnejad, 2017).
Results and Discussion
Load vs. Deformation Response and Failure Mode
Details of crashworthiness characteristics of the composite specimen include the peak load (Pmax), mean deformation load (Pm), energy absorption (EA), specific energy absorption (SEA), and crushing efficiency (ɳc) (Roslan et al., 2017).
From the test results, the typical force-displacement graph can be distributed into three regions as in Figure 2 (Abdewi et al., 2006). The first region (I) represents the precrushing phase, in which the load (p) increases dramatically and reaches an initial maximum load Pmax within elastic failure behavior before dropping. In the second region (II), the load fluctuated about a mean load over the crushing process in the plastic failure region and it is associated with the postcrushing phase. The force-displacement graph exhibited the Pmax, Pm, and the displacement of the final failure. In the third region (III), known as the compaction phase, the load increases drastically and nonlinearly because of debris accumulations at the end of the tube. This region was not taken into account due to its small absorbing energy compared with the postcrushing region. The tests results have been mentioned in detail in the next section. These findings are matching with McGregor et al. (2016) and Said et al. (2017).
Crushing Behavior of JCS
The load vs. displacement diagram and deformation trace for corrugated JCS with three layers are shown in Figure 3. In the precrushing phase, the load escalated nonlinearly up to attaining an initial peak load of 13.101 kN at 20.277 mm displacement and then started to fluctuate and progressively around mean load with the stable manner during the postcrushing phase. The longitudinal cracks were noted only at the curvature locations from the top and along its length due to the stress concentration at the curvature of the corrugated surface composite pattern. A splaying manner is characterized by very long cracks. The lamina bundles were not fractured as they underwent bending deformation. At this postcrushing phase, the maximum peak load was 14.399 kN at 59.323 mm displacement. This was owing to hoop constraint resulting from the axial crack opening along its length of the specimen wall due to the concentration of stress at the curvature of the corrugated composite specimen. Besides, geometry plays a serious role in the influence on the failure mechanism. As a result, the tube contributed a substantial amount of crushing energy absorption (mode I) showing steady and progressive deformation throughout the test. When the load exceeded 80 mm displacement, it began to increase dramatically due to crushed materials that accumulated during axial loading applying as it reached the compaction phase. The principal energy absorption was through cracks developed along the axial specimen wall, bending of lamina bundles, and contribution of friction effect between the steel platen surface, fronds, adjacent lamina, debris wedge, and delamination. This phenomenon is in the same line as stated by Lau et al. (2012) and Rabiee and Ghasemnejad (2017).
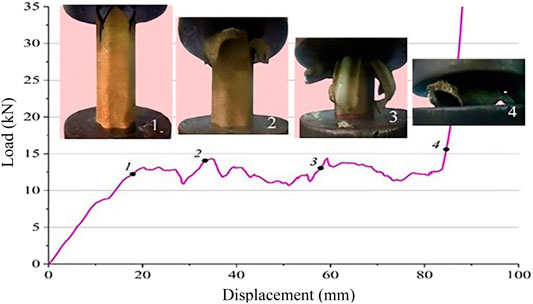
FIGURE 3. Representative load vs. displacement and collapse history of corrugated JCS with three layers.
Crushing Behavior of HCS
Typical load vs. displacement graph and collapse history of the corrugated hybrid composite specimen with three layers are depicted in Figure 4. In the first phase, the load increases nonlinearly up to attaining an initial peak value of 20.838 kN at 18.358 mm displacement, which represents the end of the tube trigger. However, during a short distance of displacement, stable fluctuating loads were established around the mean load as plotted in bottom of figure mentioned above. This was indicating the lamina-splaying mode intralaminar, long interlaminar, and parallel to the fibers bundle slits as illustrated in Figure 4 (Top). These mechanisms led to the formation of fronds that spread outwards and inwards continuously. On the other hand, friction and intra/interlaminar fractures control the energy absorbing amount of bundle bending manner. During the postcrushing phase, the maximum load recorded 24.151 kN at 54.546 mm displacement. It is noted that the lamina bending deformation mode contributes to the largest energy absorption compared to other modes. This large energy absorption (EA) was caused by a higher collapse area and thus a bigger potential to dissipate higher energy by splaying or bending accompanied with peel-off effects resulting from friction between the platen and specimen wall interface (refer to Figure 4, top No. 6).
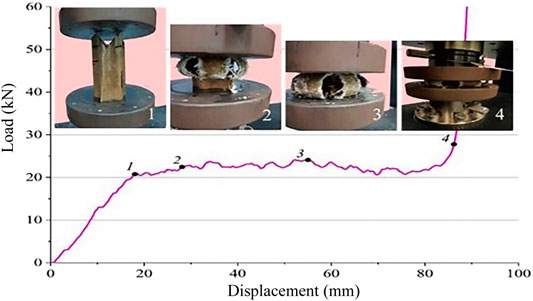
FIGURE 4. Representative load vs. displacement and collapse history of the corrugated HCS with three layers.
Hybridization Influence on Peak Load, Mean Load, and Crush Efficiency
Due to the strong correlation among peak load (Pmax), average load (Pm), and crushing efficiency (ɳc) and their effect on the load curve behavior, it is advisable to discuss all these parameters together. On the other hand, a growth in acceleration is caused by peak load value (Pmax) exceeding the average load (Pm), thus leading to structural damage or reducing passengers’ safety factor. However, to demonstrate the hybrid influence on the Pmax value in this section, a comparison must be made between the hybrid and nonhybrid samples tested under the same conditions. Figure 5 shows Pmax behavior under quasi-static loading for hybrid and nonhybrid specimens. This comparison showed that the hybridization by replacing one layer of jute mat with one layer of glass achieved a higher peak load compared to the nonhybrid jute specimen. From the results obtained, it is observed that fiber’s content of specimen has effectively influenced the maximum peak load under quasi-static loading condition. The main reason for the occurrence of this phenomenon is attributed to the high tensile strength of glass material compared to jute material (Albahash and Ansari, 2017). This result is consistent with the study by Hu et al. (2010).
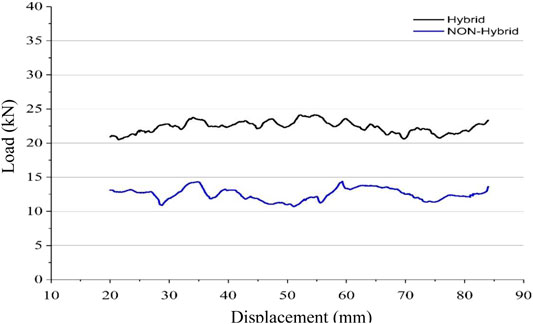
FIGURE 5. A comparison of sustained load between hybrid and nonhybrid composite specimens at postcrushing stage.
Concerning mean load (Pm), as compared to the overall mean load result of nonhybrid with hybrid composite tube, the mean load for the pure composite of the corrugated tube made of bidirectional JRFP with three layers is the lower value (i.e., Pm = 11.209 kN), while the mean load of hybrid of the corrugated tube made from (2-layer Jute + 1-layer glass) was 19.613 kN as shown in Table 2. By reviewing Figure 5, it appears that the largest value of the average load contributes to obtaining the greatest energy absorption capacity, as it has been discussed with details in the next section of the research. This conclusion was consistent with the published report by Ghasemnejad et al. (2010). However, comparing the current experimental result by the Pareto chart as depicted in Figure 6, it can be seen that the mean crush load (Pm) of the hybrid with one layer of glass was higher than those of nonhybrid by about 43%, which contributed with more stability as well.
For crushing efficiency (ɳc), another significant indicator that needs to be taken into consideration in assessing the energy dissipation performance of the designed structure is the ɳc. It is calculated mathematically by dividing the average load over the maximum peak load, which is usually from zero to one. Therefore, the closer the efficiency is to a unit, it indicates that the performance is close to the ideal value (Sivagurunathan et al., 2018a). Figure 5 shows that the bigger crush efficiency value indicated stability and progressive collapsing during displacement under the crush loading test that usually yielded a higher SEA, in contrast to the catastrophic failure during crushing that shows a decrease in the value of ɳc. On the other hand, the high value of crushing efficiency occurs in the event of the slight difference between the peak and average load (Roslan et al., 2017). However, it is obvious that the larger and the best stability results were recorded by the hybrid (jute + glass) fibers compared to the nonhybrid specimens in this experiment as shown in Figure 7
Hybrid Influence on Energy Absorption Characteristic
The energy absorption, EA, represents the total work done during the uniaxial crush loading of a specimen, which is equal to the area between the crushing curve path and the x-axis. Therefore, the total absorbed energy is the sum of the areas of the crushing stages except the area of the compaction stage because of its small value compared to pre- and postcrushing phase (Mahdi and Sebaey, 2014b). As depicted above in Table 2 and Figure 8, the greatest energy absorption was noticed in the corrugated tube with hybrid (two jute + one glass) fibers layers compared to the pure jute fibers epoxy composite, which attained 1.5687 kJ. This cues that the hybridization composite, in case that low modulus fibers are combined with the high modulus fibers compared to each other, has a larger effect on the energy absorption capacity of the composite tubes. On the other hand, the flexural, tensile, and strength properties of jute fibers reinforced epoxy composites are improved by the enhancement of one layer of glass fibers in this composite, demonstrating the positive hybrid influence. The TEA by this hybrid mechanism was about 1.8 times larger than pure jute/epoxy composite specimen at the same geometry configuration. The same conclusion was reached by Reddy et al. (2016).
However, the energy absorption is a function that represents an area under the curve resulting from the computing of the applied load multiplied by the displacement of the crushed specimen, which depends on the area of the cross-section and the mass of the structure crushed (Mahdi and Sebaey, 2014a). Therefore, using the different cross-section and mass for each specimen might be misleading for the evaluation of the EA. For a realistic comparison, when assessing the energy absorbing ability of structures, it is necessary to use the specific absorbed energy, SEA, which represents the area under the load-deformation curve divided by the mass of the specimen (Jimenez et al., 2000; Alkbir et al., 2014). Therefore, the SEA is defined as a significant factor to compare the TEA capabilities. From Figure 9, it is clear that a significant improvement in the ability to absorb energy can be found through the hybridization mechanism of different types of brittle fibers, taking into account optimization of the production cost. The SEA of the hybrid specimen was 44.82 J/g which was about 1.45 times higher than the nonhybrid specimen used in the current study. Besides, it was about 5.24–9.64 and 2.1–5 times higher than square and circle of (two Jute + one glass) specimens, respectively, in the previous study by Albahash and Ansari (2017). This indicates that even though the same materials are used, the geometrical shape and dimension of the structure play a significant role in the effect of the energy absorption capability. On the other hand, the current result of SEA for the hybrid composite specimen is higher than the metal structure value mentioned in the comparison part (Table 3). Therefore, based on the test results, the energy absorption capacity of the composite structure could be improved by hybridization using reasonable fibers; this conclusion is matched as reported by Albahash and Ansari (2017) and Hu et al. (2010).
Comparison With Previously Reported Works
To assess the current results, they are compared with other previous works reports which were using different material and geometric shapes as shown in Table 3. However, because each work presented different geometrical shape and material, the evaluation of energy absorption (EA) might be misleading. Therefore, a more realistic comparison can be made using a specific energy absorption (SEA) which was taking into account the mass of materials.
From table 3, it can be seen that replacing one jute fiber layer by one layer of woven glass for corrugated tube achieved the highest SEA compared to natural, synthetic, and metallic materials. In addition, it exhibited more stability and less potential to buckle under a quasi-static crushing test, due to its failure in brittle mode with a progressive crushing. Thus, it can be considered that hybrid jute-glass/epoxy corrugated specimen is good choice to substitute the tubular metal, synthetic composite, and natural composite in terms of energy absorption capability.
Conclusion
The hybrid composite tube based on jute and glass fiber was manufactured using epoxy resin. Composites with jute/epoxy were also prepared for purposes of comparison. However, for hybrid specimens, it can be concluded that using materials of low modulus fibers combined with the high modulus fibers compared to each other caused significant differences in the crashworthiness parameters and failure patterns of composite tubes. Based on the experimental results, the following can be drawn:
1. It was observed that the energy absorber performance of a corrugated hybrid composite tube with three layers was significantly improved by replacing one of three jute mat layers by glass mat layer in consideration of crashworthiness optimization. The hybrid specimen considered superior as it recorded the highest Pm, EA, SE, and ɳc values compared to nonhybrid specimens.
2. Hybridization is a good option in terms of finding a balance in the material properties, where the choice of fibers with high modulus contributes to the stiffness and load bearing, while the fibers with low modulus make the compound more damage tolerant, thus obtaining a design with specifications superior to both materials at a low cost.
3. The design of a hybrid fibers/epoxy specimen, in the tubes chosen for this research, has a SE of 44.82 J/g and a ɳc of 81.21%, which is superior to conventional metallic energy absorber and it is closer to that of carbon and glass fibers reinforced polymers composites which are reported in the previous studies.
Data Availability Statement
The raw data supporting the conclusions of this article will be made available by the authors, without undue reservation.
Author Contributions
SH performed experiments, investigation, methodology, and data analysis and drafted the manuscript. AI performed project supervision, funding acquisition, formal analysis, and drafting the manuscript. YY performed methodology and experimental analyses and wrote and reviewed and edited the manuscript. AA reviewed and edited the manuscript. MS reviewed funding acquisition and edited the manuscript. All authors contributed to the article and approved the submitted version.
Conflict of Interest
The authors declare that the research was conducted in the absence of any commercial or financial relationships that could be construed as a potential conflict of interest.
Acknowledgments
The authors gratefully thank the Faculty of Mechanical and Manufacturing Engineering, University Tun Hussein Onn Malaysia (UTHM), and Centre for Composites, (UTeM) Universiti Teknikal Malaysia Melaka, so much for their support in this research, as well as the Ministry of Construction, Housing and Public Municipalities/Al-Muthanna Water Directorate, Iraq, for their financial and moral support in accomplishing this work.
References
Abdewi, E. F., Sulaiman, S., Hamouda, A. M. S., and Mahdi, E. (2006). Effect of geometry on the crushing behaviour of laminated corrugated composite tubes. J. Mater. Process. Technol. 172 (3), 394–399. doi:10.1016/j.jmatprotec.2005.07.017
Abdewi, E. F., Sulaiman, S., Hamouda, A. M. S., and Mahdi, E. (2008). Quasi-static axial and lateral crushing of radial corrugated composite tubes. Thin-Walled Struct. 46 (3), 320–332. doi:10.1016/j.tws.2007.07.018
Abosbaia, A. A. S., Mahdi, E., Hamouda, A. M. S., and Sahari, B. B. (2003). Quasi-static axial crushing of segmented and non-segmented composite tubes. Compos. Struct. 60 (3), 327–343. doi:10.1016/s0263-8223(02)00341-0
Al-Qrimli, H. F., Mahdi, F. A., Ismail, F. B., and Alzorqi, I. S. (2015). Thin-walled composite tubes using fillers subjected to quasistatic axial compression. IOP Conf. Ser.: Mater. Sci. and Eng., 78 (7), 1012024. doi:10.1088/1757-899X/78/1/012024
Albahash, Z. F., and Ansari, M. N. M. (2017). Investigation on energy absorption of natural and hybrid fiber under axial static crushing. Compos. Sci. Technol. 151, 52–61. doi:10.1016/j.compscitech.2017.07.028
Alkbir, M. F. M., Sapuan, S. M., Nuraini, A. A., and Ishak, M. R. (2014). Effect of geometry on crashworthiness parameters of natural kenaf fibre reinforced composite hexagonal tubes. Mater. Des. 60, 85–93. doi:10.1016/j.matdes.2014.02.031
Balaji, G., and Annamalai, K. (2017). An experimental and numerical scrutiny of crashworthiness variables for square column with V-notch and groove initiators under quasi-static loading. Cogent Eng. 4 (1), 1364118. doi:10.1080/23311916.2017.1364118
Boria, S., Scattina, A., and Belingardi, G. (2018). Axial crushing of metal-composite hybrid tubes: experimental analysis. Procedia Struct. Integrity 8, 102–117. doi:10.1016/j.prostr.2017.12.012
Esnaola, A., Ulacia, I., Aretxabaleta, L., Aurrekoetxea, J., and Gallego, I. (2015). Quasi-static crush energy absorption capability of E-glass/polyester and hybrid E-glass-basalt/polyester composite structures. Mater. Des. 76, 18–25. doi:10.1016/j.matdes.2015.03.044
Ghasemnejad, H., Hadavinia, H., and Aboutorabi, A. (2010). Effect of delamination failure in crashworthiness analysis of hybrid composite box structures. Mater. Des. 31 (3), 1105–1116. doi:10.1016/j.matdes.2009.09.043
Ghoushji, M. J., Eshkoor, R. A., Zulkifli, R., Sulong, A. B., Abdullah, S., and Azhari, C. H. (2017). Energy absorption capability of axially compressed woven natural ramie/green epoxy square composite tubes. J. Reinf. Plast. Compos. 36 (14), 1028–1037. doi:10.1177/0731684417700482
Hu, D. Y., Luo, M., and Yang, J. L. (2010). Experimental study on crushing characteristics of brittle fibre/epoxy hybrid composite tubes. Int. J. Crashworthiness 15 (4), 401–412. doi:10.1080/13588261003647402
Ismail, A. E. (2016). Crushing mechanisms of cylindrical winding kenaf fiber reinforced composites. Jurnal Teknologi 78 (6), 45–50. doi:10.11113/jt.v78.5258
Ismail, A. E., Awang, M. K., and Sa’at, M. H. (2007). Tensile strength of natural fiber reinforced polyester composite. AIP Conf. Proc. 909, 174–179. doi:10.1063/1.2739848
Ismail, A. E., and Che Abdul Aziz, M. A. (2015). IOP Conf. Ser. Mater. Sci. Eng. 100 (1), 012037. doi:10.1088/1757-899x/100/1/012037
Ismail, A. E., and Mohd Tobi, A. L. (2016). Axial energy absorption of woven kenaf fiber reinforced composites. ARPN J. Eng. Appl. Sci. 11 (14), 8668–8672.
Jimenez, M. A., Miravete, A., Larrode, E., and Revuelta, D. (2000). Effect of trigger geometry on energy absorption in composite profiles. Compos. Struct. 48 (1-3), 107–111. doi:10.1016/s0263-8223(99)00081-1
Lau, S. T. W., Said, M. R., and Yaakob, M. Y. (2012). On the effect of geometrical designs and failure modes in composite axial crushing: a literature review. Compos. Struct. 94 (3), 803–812. doi:10.1016/j.compstruct.2011.09.013
Mahdi, E., Hamouda, A. M. S., Sahari, B. B., and Khalid, Y. A. (2003a). Experimental quasi-static axial crushing of cone-tube-cone composite system. Compos. B Eng. 34 (3), 285–302. doi:10.1016/s1359-8368(02)00102-6
Mahdi, E., Hamouda, A. M. S., Sahari, B. B., and Khalid, Y. A. (2003b). On the collapse of cotton/epoxy tubes under axial static loading. Appl. Compos. Mater. 10 (2), 67–84. doi:10.1023/a:1022890104728
Mahdi, E., and Sebaey, T. A. (2014a). An experimental investigation into crushing behavior of radially stiffened GFRP composite tubes. Thin-Walled Struct. 76, 8–13. doi:10.1016/j.tws.2013.10.018
Mahdi, E., and Sebaey, T. A. (2014b). Crushing behavior of hybrid hexagonal/octagonal cellular composite system: aramid/carbon hybrid composite. Mater. Des. 63, 6–13. doi:10.1016/j.matdes.2014.06.001
Mamalis, A. G., Manolakos, D. E., Ioannidis, M. B., and Papapostolou, D. P. (2004). Crashworthy characteristics of axially statically compressed thin-walled square CFRP composite tubes: experimental. Compos. Struct. 63 (3-4), 347–360. doi:10.1016/s0263-8223(03)00183-1
McGregor, C., Vaziri, R., Poursartip, A., and Xiao, X. (2016). Axial crushing of triaxially braided composite tubes at quasi-static and dynamic rates. Compos. Struct. 157, 197–206. doi:10.1016/j.compstruct.2016.08.035
Mishra, V., and Biswas, S. (2013). Physical and mechanical properties of bi-directional jute fiber epoxy composites. Procedia engineering 51, 561–566. doi:10.1016/j.proeng.2013.01.079
Okubo, K., Fujii, T., and Yamamoto, Y. (2004). Development of bamboo-based polymer composites and their mechanical properties. Compos. Appl. Sci. Manuf. 35 (3), 377–383. doi:10.1016/j.compositesa.2003.09.017
Palanivelu, S., Paepegem, W. V., Degrieck, J., Vantomme, J., Kakogiannis, D., Ackeren, J. V., et al. (2011). Crushing and energy absorption performance of different geometrical shapes of small-scale glass/polyester composite tubes under quasi-static loading conditions. Compos. Struct. 93 (2), 992–1007. doi:10.1016/j.compstruct.2010.06.021
Palanivelu, S., Van Paepegem, W., Degrieck, J., Kakogiannis, D., Van Ackeren, J., Van Hemelrijck, D., et al. (2010). Parametric study of crushing parameters and failure patterns of pultruded composite tubes using cohesive elements and seam, Part I: central delamination and triggering modelling. Polym. Test. 29 (6), 729–741. doi:10.1016/j.polymertesting.2010.05.010
Rabiee, A., and Ghasemnejad, H. (2017). Progressive crushing of polymer matrix composite tubular structures: review. Open J. Compos. Mat. 7 (1), 14–48. doi:10.4236/ojcm.2017.71002
Raghavendra, G., Ojha, S., Acharya, S., and Pal, S. (2014). Jute fiber reinforced epoxy composites and comparison with the glass and neat epoxy composites. J. Compos. Mater. 48 (20), 2537–2547. doi:10.1177/0021998313499955
Reddy, T. S., Subba Reddy, P. R., and Madhu, V. (2016). Influence of hybridization on the performance of glass composites under low and high velocity impact. Adv. Mater. Lett. 7 (6), 491–496. doi:10.5185/amlett.2016.6316
Roslan, M. N., Yahya, M. Y., Ahmad, Z., and Azrin Hani, A. R. (2017). Energy absorption behaviour of braided basalt composite tube. Adv. Compos. Mater. 27 (5), 467–481. doi:10.1080/09243046.2017.1405604
Said, M. R., Lau, S. T., and Yaakob, M. Y. (2017). Quasi static axial crushing of kenaf fibre reinforced epoxy composite fabricated by VARTM method. ARPN J. Eng. Appl. Sci 12, 4804–4808.
Shibata, S., Cao, Y., and Fukumoto, I. (2005). Press forming of short natural fiber-reinforced biodegradable resin: effects of fiber volume and length on flexural properties. Polym. Test. 24 (8), 1005–1011. doi:10.1016/j.polymertesting.2005.07.012
Sivagurunathan, R., Lau Tze Way, S., Sivagurunathan, L., and Yaakob, M. Y. (2018a). The effects of triggering mechanisms on the energy absorption capability of circular jute/epoxy composite tubes under quasi-static axial loading. Appl. Compos. Mater. 25 (6), 1401–1417. doi:10.1007/s10443-018-9673-5
Sivagurunathan, R., Way, S. L. T., Sivagurunathan, L., and Yaakob, M. Y. (2018b). Effects of triggering mechanisms on the crashworthiness characteristics of square woven jute/epoxy composite tubes. J. Reinf. Plast. Compos. 37 (12), 824–840. doi:10.1177/0731684418763218
Summerscales, J., Dissanayake, N. P. J., Virk, A. S., and Hall, W. (2010). A review of bast fibres and their composites. Part 1 - fibres as reinforcements. Compos. Appl. Sci. Manuf. 41 (10), 1329–1335. doi:10.1016/j.compositesa.2010.06.001
Keywords: hybrid composites, jute fiber, quasi-static, crashworthiness parameters, fabrication
Citation: Salim Hamza S, Ismail AE, Yuhazri MY, Ariffin AH and Hameed Sultan MT (2021) Hybridization Effect on Crashworthiness Parameters of Natural Composite. Front. Mater. 8:619245. doi: 10.3389/fmats.2021.619245
Received: 19 October 2020; Accepted: 07 January 2021;
Published: 11 February 2021.
Edited by:
Andreas J. Brunner, Swiss Federal Laboratories for Materials Science and Technology, SwitzerlandReviewed by:
Wesley Cantwell, Khalifa University, United Arab EmiratesBamber Blackman, Imperial College London, United Kingdom
Copyright © 2021 Salim Hamza, Ismail, Yuhazri, Ariffin and Hameed Sultan. This is an open-access article distributed under the terms of the Creative Commons Attribution License (CC BY). The use, distribution or reproduction in other forums is permitted, provided the original author(s) and the copyright owner(s) are credited and that the original publication in this journal is cited, in accordance with accepted academic practice. No use, distribution or reproduction is permitted which does not comply with these terms.
*Correspondence: Al Emran Ismail, ZW1yYW5AdXRobS5lZHUubXk=, YWxfZW1yYW5AaG90bWFpbC5jb20=